DOI:
10.1039/C9RA10741J
(Paper)
RSC Adv., 2020,
10, 8244-8254
Improving the corrosion resistance of micro-arc oxidation coated Mg–Zn–Ca alloy
Received
20th December 2019
, Accepted 11th February 2020
First published on 26th February 2020
Abstract
Four additives (Na2WO4, nano-hydroxyapatite, K2TiF6 and NaF) were added into the Na5P3O10 + NaOH + C3H8O3 base electrolyte according to the orthogonal design of four factors three levels (L9 (34)). Nine different micro-arc oxidation (MAO) coatings were fabricated on Mg–2Zn–0.5Ca alloys through orthogonal experiments. The effects of four additives on the microstructure, mechanical properties, corrosion resistance and biocompatibility of MAO coatings were investigated through X-ray diffraction (XRD), scanning electron microscopy (SEM) with energy dispersive X-ray spectroscopy (EDS), electrochemical corrosion test and in vitro degradation test. The addition of nano-hydroxyapatite and K2TiF6 showed self-sealing effects and contributed to the corrosion resistance of the samples significantly. The addition of 0.5 g L−1 Na2WO4 markedly elevated the bonding strength of the coatings with the substrate. The optimal combination of factors and levels considering both mechanical properties and corrosion resistance was: 0.5 g L−1 Na2WO4, 0 g L−1 NaF, 5 g L−1 n-HAp, 5 g L−1 K2TiF6. The growth mechanism of MAO coatings combining with the visual phenomenon was discussed as well.
1 Introduction
Magnesium alloys have drawn extensive attention as biodegradable orthopedic implant materials in recent years. Magnesium alloys possess low specific density (1.74–1.84 g cm−3) and Young's modulus (41–45 GPa) close to those of natural bone tissues (1.8–2.1 g cm−3, 15–25 GPa).1 Magnesium naturally exists in bone tissues and its corrosion products generated in vivo can be easily excreted by human bodies.2,3 Furthermore, magnesium alloys avert a second surgery of removing the implant and relieve the patients' pain compared to conventional permanent metallic biomaterials (e.g. stainless steels, titanium alloys, cobalt chromium alloys, etc.).4 However, the widespread use of magnesium alloys for biomedical applications is still limited due to its rapid biodegradation rate when exposed to the physiological environment,5,6 thereby losing mechanical integrity before the host tissues sufficiently heal.7,8 Furthermore, the large amount of hydrogen gas generated from the degradation of implants is not conducive to the tissue healing process. The shifting pH values are pernicious to cell viability.9
The addition of alloying elements can improve mechanical properties and corrosion resistance of pure magnesium.10 The alloying elements must be nontoxic and safe to human bodies.11 The addition of zinc (Zn) element helps to improve the mechanical properties of magnesium alloy by grain refining.12 In addition, Zn element promotes bone formation, whilst inhibits bone resorption.13,14 Therefore, Zn is chosen as the alloying element of magnesium alloys due to its biocompatibility, osteogenic activity, antibacterial ability and grain refining effect.15,16 Calcium (Ca) is a biocompatible element owing to its natural existence in bones.17 And the calcium addition elevates the corrosion resistance of magnesium alloys in chloride containing solutions.18 Based on previous studies and experiments,19–21 we chose Mg–2Zn–0.5Ca alloys as our substrate metal.
Numerous surface treatments have been elaborated to improve the corrosion properties and biocompatibility of magnesium based alloys, such as chemical conversion coating, electrochemical treatment, organic coating and micro-arc oxidation (MAO).22–24 Micro-arc oxidation is an environment friendly technique to prepare uniform coatings with excellent adhesion and corrosion resistance.25,26 The micro-pores formed in the MAO coatings could contribute to the growth of bone tissues.27 The nature of substrate metals, composition and concentration of electrolyte, and applied electrical parameters plays a crucial role in the properties of coatings.28–31 The composition of electrolytes can change the properties of coatings significantly by altering the microstructure and composition of the coating. The addition of sodium tungstate (Na2WO4) increases the electrolytic conductivity and enlarges the size of micro-pores generated in MAO coatings on AZ91HP magnesium alloys.32 Hydroxyapatite (HA, Ca10(PO4)6(OH)2) is the major mineral component of bone and teeth.33 Therefore, HA is a promising candidate for preparing coatings on magnesium alloys in terms of its outstanding biocompatibility, bioactivity and corrosion resistance.34,35 NaF additives decrease the energy consumption of MAO process and contribute to the growth of the coating. The addition of K2TiF6 in the electrolytes helps to seal the micro-pores and improve the corrosion resistance of MAO coatings.36–38 Moreover, F− participates in the arc discharge during the micro-arc oxidation process and forms dense ceramic containing MgF2.39
In this paper, we chose sodium tripolyphosphate (Na5P3O10), sodium hydroxide (NaOH) and glycerine (C3H8O3) as our base electrolyte. Na2WO4, nano-hydroxyapatite, K2TiF6 and NaF was added as extra additives. Nine different ceramic coatings were fabricated on Mg–2Zn–0.5Ca alloys by orthogonal design of four factors three levels to optimize the electrolyte solution. The microstructure, phase and elemental composition, corrosion resistance, biocompatibility of these samples were discussed.
2 Experimental
2.1 Materials and coating preparation
Mg–2Zn–0.5Ca alloy was cast using commercial purity Mg (99.99%), Zn blocks (99.99%) and Mg–20Ca master alloys. The ingot was cut into rectangular specimens with size of 10 mm × 10 mm × 12 mm. Prior to the MAO treatment, every sample was ground with SiC papers up to 1000 grit, rinsed with distilled water, degreased with acetone and dried with a blower. The base electrolyte contained 10 g L−1 Na5P3O10 + 2 g L−1 NaOH + 10 mL L−1 C3H8O3 in distilled water. Four additives Na2WO4, nano-hydroxyapatite (n-HAp), K2TiF6 and NaF were added into the base electrolyte according to orthogonal design of four factors three levels (as shown in Table 1). The specimens were numbered A1–A9 in terms of different combination of additives. All solutions were prepared using analytical grade reagents and distilled water. The MAO treatment was performed using a constant pressure control mode. During the MAO process, the applied positive voltage, pulse frequency, applied negative voltage, positive duty ratio, negative duty ratio and ratio of positive and negative pulses were 350 V, 600 HZ, 30 V, 30%, 20%, 1
:
1 respectively. The oxidation process was carried out for 10 min under 30 °C.
Table 1 The composition and concentration of extra additives by orthogonal design
Sample codes |
Additives |
Na2WO4 (g L−1) |
NaF (g L−1) |
n-HAp (g L−1) |
K2TiF6 (g L−1) |
A1 |
— |
— |
— |
— |
A2 |
— |
2.5 |
5.0 |
5.0 |
A3 |
— |
5.0 |
10.0 |
10.0 |
A4 |
0.5 |
— |
5.0 |
10.0 |
A5 |
0.5 |
2.5 |
10.0 |
— |
A6 |
0.5 |
5.0 |
— |
5.0 |
A7 |
1.0 |
— |
10.0 |
5.0 |
A8 |
1.0 |
2.5 |
— |
10.0 |
A9 |
1.0 |
5.0 |
5.0 |
— |
2.2 Coating characterization
The thickness of MAO coatings was measured by MiniTest 600B FN2 microprocessor coating thickness gauge (Elektrophysik Koln). The final value obtained was the average value of six replicate measurements. WS-20004 Scratch Tester was used to evaluate the adhesion strength of MAO coatings. The morphology and element distribution was investigated using scanning electron microscopes (SEM, Hitachi S-3400N) combined with energy dispersive spectrum (EDS, Horiba EMAX X-act). The phase composition of the coatings before and after immersion was detected using X-ray diffractometer (SHIMADZU XRD-6100) with Cu-Kα radiation at a scanning speed of 4° min−1.
2.3 Electrochemical corrosion test
Electrochemical behavior of MAO treated samples and bare Mg alloy substrate was studied in simulated body fluid (SBF). The SBF was prepared by dissolving the analytical grade reagents following the sequence of NaCl, NaHCO3, KCl, K2HPO4·3H2O, MgCl2·6H2O, 1.0 mol L−1 HCl, CaCl2, Na2SO4 and tris(hydroxymethyl)aminomethane ((CH2OH)3CNH2) in distilled water at 36.5 ± 0.5 °C. The pH was adjusted to 7.2–7.3 with 1.0 mol L−1 HCl. A conventional three electrode electrochemical cell was employed to assess the electrochemical behavior, which contained a platinum wire counter electrode, a saturated calomel reference electrode, and one 10 mm × 10 mm side of specimen as the working electrode. Potentiodynamic polarization tests were performed at a scan rate of 1 mV s−1 from −2500 mV to 1000 mV.
2.4 In vitro degradation test
The MAO treated samples and bare Mg alloy substrate was immersed in SBF for 28 days. Each sample was submerged in 45 mL SBF separately, and three parallel samples were evaluated to minimize contingency. The ratio of the samples' surface area to SBF volume is 8 mm2
:
1 mL. The SBF was renewed every the other day to keep it fresh and stable whilst avoiding sediment during the immersion process. The pH values were tested and recorded every the other day to evaluate the degradation stability by pH meter. The samples were picked out from the SBF after the immersion, cleaned in distilled water and dried in a drying oven.
3 Results and discussions
The addition of four additives in the electrolyte plays an important role in the microstructure, mechanical properties, corrosion resistance and biocompatibility of MAO coated Mg–2Zn–0.5Ca alloys. The orthogonal experiment is an efficient and economical way to obtain the results. The four additives Na2WO4, NaF, n-HAp and K2TiF6 are defined as factors j (j = A, B, C, D respectively). Each factor possesses three levels i (i = 1, 2, 3), representing three different concentrations. kji is defined as the average value of the evaluation indexes of all levels i in each factor j, which is used to evaluate the optimal combination of factors and levels. Rj is the difference value between the maximum kji and minimum kji. Rj value is used for assessing the influence degree of the factors, a larger Rj value means a greater impact on the results.40 The calculation methods of factor B is shown below:
|
Rj = max(kBi) − min(kBi);
| (1) |
where kBi is the k value of factor B with i level; and Yz (z = 1–9) is the value of evaluation indexes Ecorr (V per SCE), Icorr (A cm−2), Wl (%) and Bs (N) of nine samples respectively. Higher Ecorr (V per SCE) value indicates the samples are harder to corrode while lower Icorr (A cm−2) value means a slower corrosion rate. Meanwhile, lower Wl (%) value promises better corrosion resistance. Table 2 shows the visual analysis of the samples' corrosion potential (Ecorr (V per SCE)), corrosion current density (Icorr (A cm−2)), weight loss percentage after 28 days' immersion (Wl (%)) and bonding strength (Bs (N)). As shown in the Table 2, the addition of Na2WO4 has a greater impact on the bonding strength of the samples, thus, the optimal addition of Na2WO4 is 0.5 g L−1. Three evaluation indexes show that the best concentration of NaF is 0 g L−1. Furthermore, the addition of 0 g L−1 and 5 g L−1 NaF leads to similar Icorr value. In consequence, the addition of 0 g L−1 NaF is the best choice. The addition of n-HAp influences greater on the Icorr (A cm−2) of the samples and the optimal concentration is 5 g L−1. The addition of K2TiF6 has obvious impact on the Icorr (A cm−2), Wl (%) and Bs (N) of the samples. The concentration of 5 g L−1 K2TiF6 promises slow degradation rate as well as strong bonding strength. Therefore, the optimal combination of factors and levels is: 0.5 g L−1 Na2WO4, 0 g L−1 NaF, 5 g L−1 n-HAp and 5 g L−1 K2TiF6.
Table 2 The visual analysis of corrosion potential (Ecorr (V per SCE)), corrosion current density (Icorr (A cm−2)), weight loss percentage after 28 days' immersion (Wl (%)) and bonding strength (Bs (N)) of the samples
Ecorr (V per SCE) |
Na2WO4 |
NaF |
n-HAp |
K2TiF6 |
Icorr (A cm−2) |
Na2WO4 |
NaF |
n-HAp |
K2TiF6 |
k1 |
−1.588 |
−1.598 |
−1.658 |
−1.703 |
k1 |
6.73 × 10−6 |
7.32 × 10−6 |
9.37 × 10−6 |
1.69 × 10−5 |
k2 |
−1.713 |
−1.662 |
−1.671 |
−1.704 |
k2 |
1.01 × 10−5 |
1.24 × 10−5 |
3.98 × 10−6 |
4.16 × 10−6 |
k3 |
−1.692 |
−1.733 |
−1.664 |
−1.585 |
K3 |
1.02 × 10−5 |
7.31 × 10−6 |
1.37 × 10−5 |
5.99 × 10−6 |
Rj |
0.125 |
0.135 |
0.013 |
0.119 |
Rj |
3.45 × 10−6 |
5.1 × 10−6 |
9.71 × 10−6 |
1.27 × 10−5 |
Sequence of factors |
B > A > D > C |
|
D > C > B > A |
Optimal combination |
A1 |
B1 |
C1 |
D3 |
|
A1 |
B3 |
C2 |
D2 |
Wl (%) |
Na2WO4 |
NaF |
n-HAp |
K2TiF6 |
Bs (N) |
Na2WO4 |
NaF |
n-HAp |
K2TiF6 |
k1 |
3.731 |
3.277 |
3.824 |
5.159 |
k1 |
16.27 |
25.39 |
17.77 |
16.11 |
k2 |
3.791 |
3.758 |
3.618 |
3.002 |
k2 |
25.92 |
20.98 |
18.73 |
25.57 |
k3 |
3.327 |
3.815 |
3.407 |
2.688 |
k3 |
20.50 |
16.32 |
26.19 |
21.01 |
Rj |
0.464 |
0.538 |
0.418 |
2.471 |
Rj |
9.65 |
9.07 |
8.42 |
9.46 |
Sequence of factors |
D > B > A > C |
|
A > D > B > C |
Optimal combination |
A3 |
B1 |
C3 |
D3 |
|
A2 |
B1 |
C3 |
D2 |
3.1 Coating appearance, thickness and bonding strength
The MAO coatings presented different degrees of white and blue color as the composition and concentration of the electrolyte solutions changed (as shown in Fig. 1). The samples without the addition of K2TiF6 (A1, A5, A9) all presented white color, thus, the addition of K2TiF6 led to the appearance of blue color. Moreover, as the concentration of K2TiF6 increased, the color of the coatings grew darker. Li et al.41 proved that MgF2 coating reflected red and blue light under the white light. The combination of different volume MgF2 phases and Ti element on the coating surface presented various degrees of blue with different saturation via light scattering. The samples A2, A6, A7 showed light grey blue with the addition of 5 g L−1 K2TiF6, while samples A3, A4, A8 presented darker steel blue with more addition of 10 g L−1 K2TiF6.
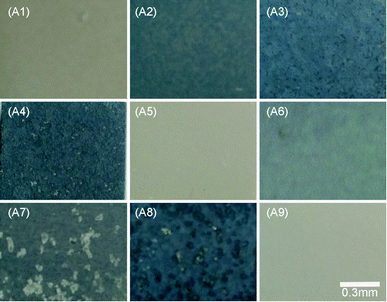 |
| Fig. 1 Appearance of MAO coatings prepared by nine different electrolytes (samples A1–A9). | |
The thickness and adhesion of nine different MAO coatings was shown in Fig. 2. The thickness of MAO coatings had no direct relations to the corrosion resistance of the samples. The corrosion properties of the samples mainly depended on the configuration and size of the defects (micro-pores and micro-cracks). The adhesion strength of MAO coatings to the substrate was crucial properties to identify the mechanical integrity of the samples, and it was closely related to the corrosion properties of MAO coated samples.42 According to the range analysis of orthogonal experiments (as shown in Table 2), the addition of K2TiF6 and NaF influenced the thickness of the MAO coatings significantly. The addition of K2TiF6 could elevate the electrolyte conductivity and decrease the melting point of the components in the anode/electrolyte interface which lower the breakdown voltage.43 Thus, the increase of K2TiF6 concentration improved the formation rate of the coatings and raised the thickness of the coatings evidently. The addition of 5 g L−1 K2TiF6 exhibited the best bonding strength. With the increase of NaF additives, the MAO coatings grew much thicker, but the adhesion of MAO coatings with the substrate decreased. The better bonding strength was more conducive to mechanical properties of MAO coatings, thus the addition of NaF was harmful to the samples. Na2WO4 additives possessed greater impact on the bonding strength of the samples than the others. And 0.5 g L−1 addition of Na2WO4 showed strongest bonding strength. The addition of n-HAp hardly had any effect on the thickness of the coatings, but the increase of n-HAp additives elevated the adhesion of MAO coatings to a big extent. Fig. 2 showed that there are no direct connections between the thickness and adhesion of MAO coatings. The samples A4 and A7 exhibited higher adhesion strength than the others.
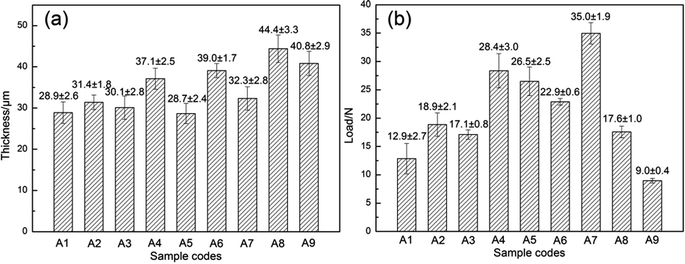 |
| Fig. 2 Thickness (a) and bonding strength (b) of nine different MAO coatings. | |
3.2 Surface morphologies of MAO coatings
Fig. 3 showed the surface morphologies and EDS profiles of nine different MAO coatings (sample A1–A9). All the samples displayed crater-like and island-like morphologies. The micro-pores' diameters of A3, A6, A9 samples were obviously bigger than the others. And the micro-cracks of A6, A9 were easily observed, which all indicated the addition of NaF increased the occurrence of micro-cracks and size of micro-pores caused by enlarged discharge sparks.44,45 Most of the micro-pores of samples A2, A3, A4, A7 were filled and sealed with a medley of particles due to the addition of K2TiF6. The elements O, Ti, F, Ca, P were detected in these particles due to the absorption of K2TiF6 into the discharge channel under high temperature and pressure.46 Reactions TiF62− + 4OH− = TiO2 + 6F− + 2H2O took place in the discharge channel.47 Therefore, TiO2 and fluoride were left in the discharge channel and the pores were sealed. The n-HAp was incorporated into the coatings under strong electric field and absorbed into the pores of the coatings. The existence of C element in the coatings was due to the generated CO32− coming from CO2 atmosphere during MAO treatment. The porosity and pore configuration influenced the corrosion resistance of MAO coatings significantly.48 The sealed pores and cracks helped to improve the corrosion resistance of samples evidently due to the blocking of corrosive media's access with substrate. Therefore, the addition of n-HAp or K2TiF6 generated the self-sealing effects on micro-pores and micro-cracks existing in MAO coatings, as a result, improved the corrosion resistance of the samples.
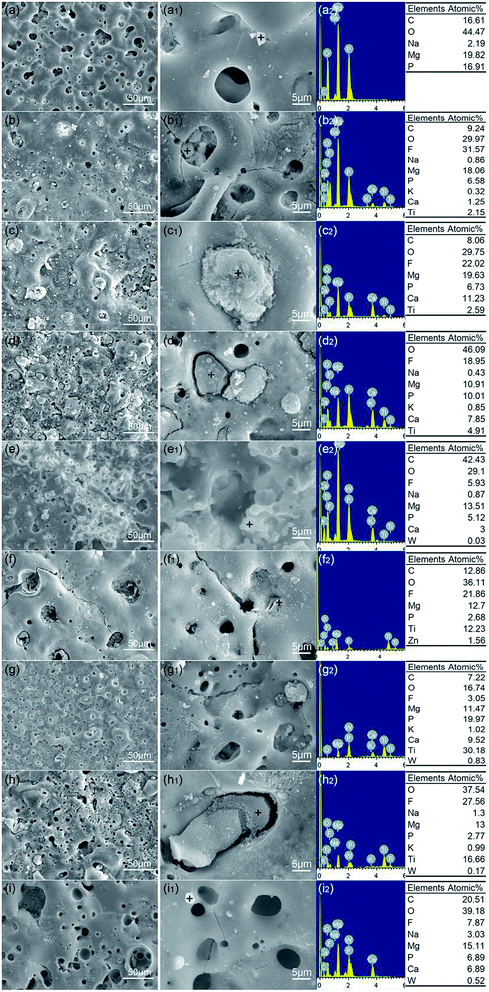 |
| Fig. 3 Surface morphologies and EDS profiles of nine different MAO coatings (a, a1 and a2) sample A1, (b, b1 and b2) sample A2, (c, c1 and c2) sample A3, (d, d1 and d2) sample A4, (e, e1 and e2) sample A5, (f, f1 and f2) sample A6, (g, g1 and g2) sample A7, (h, h1 and h2) sample A8, (i, i1 and i2) sample A9. | |
Cross-sectional morphologies and elemental distribution of samples A3, A4, A5 were shown in Fig. 4. The interface of MAO coatings and the substrate showed a compact and coherent appearance which indicated the good adhesion between MAO coatings and the substrate. The compact inner configuration could effectively prevent the contact of the corrosive medium with the substrate and slow down the corrosion rate. Elements Mg, P, O, F, Ca, Ti were detected in the MAO coatings. The detection of Ca, Ti elements showed the active participation of n-HAp or K2TiF6 additives during MAO. Surface morphologies combining with cross-sectional morphologies showed that considerable micro-pores existing in MAO coatings were interconnected. Smaller pores could be observed through the bigger pores from the top layer (as shown in Fig. 3(a1, b1 and g1)).
 |
| Fig. 4 Cross-sectional morphologies and elemental distribution of samples (a) A3, (b) A4, (c) A5. | |
3.3 Phase composition of MAO coatings
The XRD patterns of MAO coatings prepared by nine different electrolytes (samples A1–A9) were shown in Fig. 5. Metal oxides (MgO, TiO2, WO2), fluorides (MgF2), phosphate (Mg3(PO4)2, Ca2P2O7), CaCO3 and Mg distributed in nine different MAO coatings. The addition of NaF and K2TiF6 led to the formation of MgF2 phase. And the MgO, MgF2, Mg3(PO4)2 phases were dominant and stable phases that could protect the substrate from corrosion in corrosive environments.49 The dehydration of Mg(OH)2 led to the formation of MgO. The TiO2 phase possessed catalytic activity and highly antibacterial properties.50–52 Furthermore, the free radicals on TiO2 can induce the formation of apatite that subsequently promoted the adhesion of osteoblast.53,54 The formation of calcium salts indicated that the incorporation of n-HAp occurred by reactive way during MAO process.55 Although inert incorporation might take place, the content of the original n-HAp was too minimal to detect.
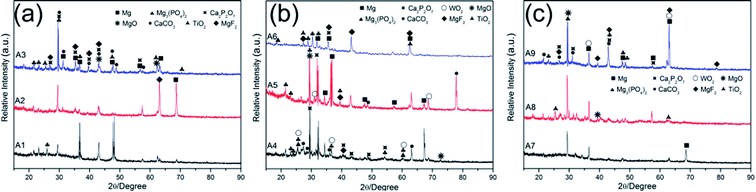 |
| Fig. 5 XRD patterns of MAO coatings prepared by nine different electrolytes (samples A1–A9). | |
3.4 Corrosion resistance of MAO coatings
Typical potentiodynamic polarization curves of samples A1–A9 and substrate in SBF were shown in Fig. 6. The corrosion potential (Ecorr) and corrosion current density (Icorr) were also displayed in Fig. 6. Table 3 displayed detailed potentiodynamic polarization data of MAO coated samples. The MAO coatings prevented the direct contact of corrosive ions with the substrate. Therefore, the MAO-treated samples had lower corrosion current density and higher polarization resistance comparing to the bare substrate. The range analysis of orthogonal experiments indicated that the addition of K2TiF6 had much more effects on the corrosion resistance of samples than the other additives (as shown in Table 2). The addition of 5 g L−1 K2TiF6 achieved better corrosion resistance with higher Ecorr (V vs. SCE) and lower Icorr (A cm−2). It was due to the addition of K2TiF6 promoted the formation of MgF2 phases, which acted as a barrier to protect the substrate from being further corroded.56 The addition of K2TiF6 helped to improve the corrosion resistance of samples, which was in accordance with the observation and deduction of surface morphologies of MAO coatings above. Adding n-HAp also evidently improved the corrosion resistance of the samples, and the concentration of 5 g L−1 brought the best effects. But the addition of Na2WO4 and NaF had no obvious impact on the corrosion properties of the samples.
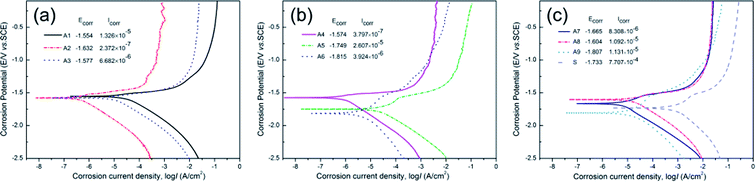 |
| Fig. 6 Potentiodynamic polarization curves of samples A1–A9 and substrate in SBF. | |
Table 3 Potentiodynamic polarization data of MAO coated samples
Sample codes |
Icorr (A cm−2) |
Ecorr (V vs. SCE) |
ba (mV) |
bc (mV) |
Rp (Ω cm2) |
A1 |
1.326 × 10−5 |
−1.554 |
5.376 |
17.864 |
1410.9 |
A2 |
2.372 × 10−7 |
−1.632 |
8.702 |
2.456 |
164261.5 |
A3 |
6.682 × 10−6 |
−1.577 |
4.788 |
18.544 |
2789 |
A4 |
3.797 × 10−7 |
−1.574 |
4.246 |
27.468 |
36101.1 |
A5 |
2.607 × 10−5 |
−1.749 |
5.236 |
5.043 |
1622.3 |
A6 |
2.184 × 10−6 |
−1.501 |
4.574 |
7.043 |
17134.2 |
A7 |
8.308 × 10−6 |
−1.665 |
4.052 |
7.006 |
4732.7 |
A8 |
1.092 × 10−5 |
−1.604 |
4.637 |
19.209 |
1669.2 |
A9 |
1.131 × 10−5 |
−1.807 |
5.844 |
4.796 |
3613.4 |
S |
7.707 × 10−4 |
−1.733 |
4.596 |
4.939 |
59.2 |
The weight loss percentage of samples A1–A9 and substrate immersed in SBF for 7, 14, 21, 28 days was shown in Fig. 7. Comparing to the substrate, the weight loss percentage of A1–A9 samples was obviously lower, which proved the superior corrosion resistance of MAO coatings. After 28 days of immersion, samples without the addition of K2TiF6 (A1, A5, A9) corroded more severely than the other samples. The data in Table 2 showed that the increase of K2TiF6 could retard the corrosion rate of samples markedly. The addition of n-HAp also helped to reduce the degradation rate. However, the increase of NaF additives impaired the corrosion resistance of samples due to more micro-cracks and larger micro-pores caused by enlarged discharge sparks.
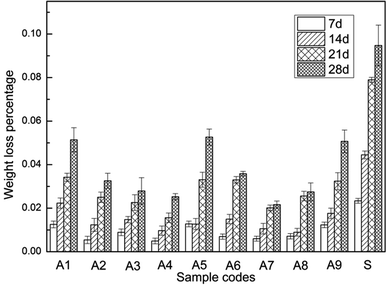 |
| Fig. 7 Weight loss percentage of samples A1–A9 and substrate immersed in SBF for 7, 14, 21, 28 days respectively. | |
3.5 Coating biocompatibility
Fig. 8 showed the pH values of samples A1–A9 and substrate immersed in SBF for 28 days. MAO coatings helped to decrease the pH values during the degradation process comparing to the substrate. Liu et al.57 demonstrated that the weak alkaline physiological environment promoted the differentiation of osteoblasts while inhibited the formation of osteoclast. And the weak alkaline condition accelerated the repairing process of the damaged bones. As shown in Fig. 8, the pH values of A2, A4, A7 samples were steady and ranged from 7.32–7.65, 6.91–7.58, 7.18–7.65 respectively, which was close to the physiological environment. Shen et al.58 proved that the optimal pH values for the viability of osteoblast ranged from 8 to 8.5. The pH values of the substrate ranged from 7.88 to 8.62. Therefore, even though the MAO coatings would degrade, the exposed substrate could offer a favorable environment for the growth of the osteoblast.
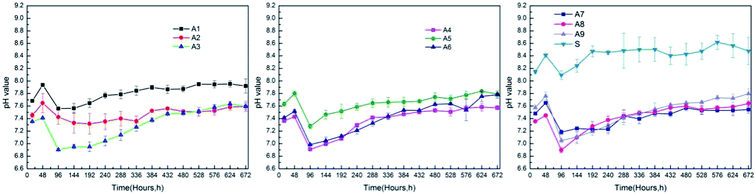 |
| Fig. 8 pH values of samples A1–A9 and substrate immersed in SBF for 28 days. | |
The surface morphologies and elemental composition of samples A1–A9 and substrate after immersed in SBF for 28 days were shown in Fig. 9. Typical spherical clusters with honeycomb like constructions appeared on the surface of A1 and A5 samples. In addition, numerous spherical, lamellar and blocky particles with different size generated on the surface of samples A1–A9 and substrate after the immersion. The elements C, O, Ca, P, F, Mg, Cl, Ti were detected in the particles or surface of samples. The elemental composition of samples A1–A9 and substrate atomic percentage and molar ratio of Ca and P on the surface of samples A1–A9 and substrate was shown in Table 4. It indicated that the proportion of Ca and P in some of the new generated products was pretty high, which demonstrated the surfaces' ability of inducing the precipitation of calcium phosphates. The results indicated that samples with and without MAO coatings all possessed excellent biocompatibility and bioactivity.
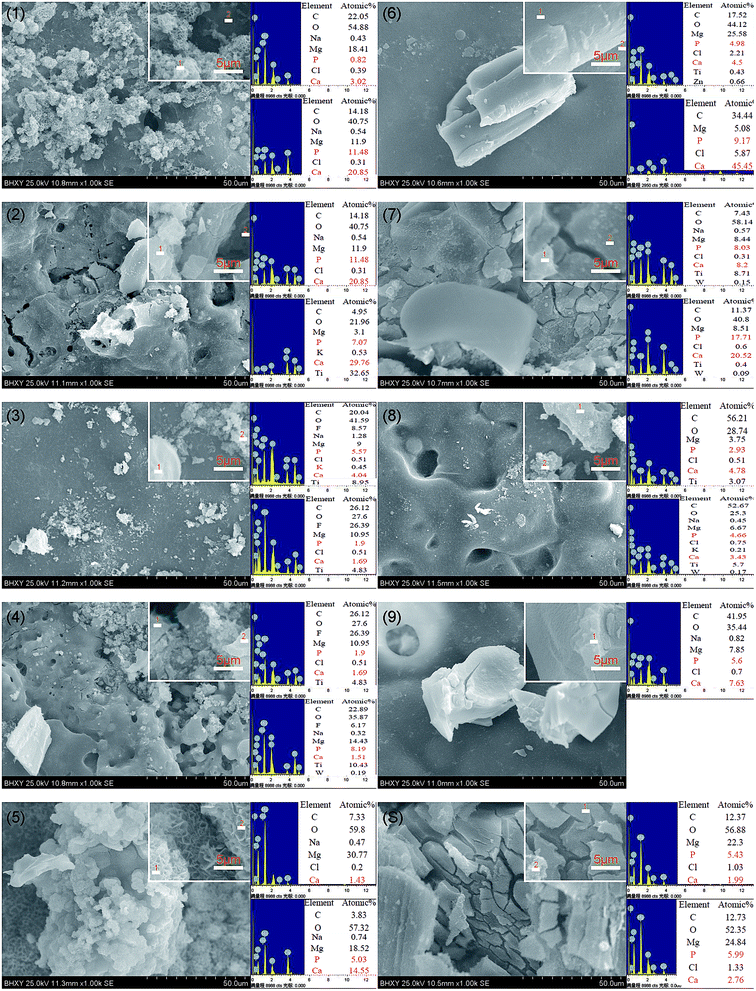 |
| Fig. 9 Surface morphologies and elemental composition of samples A1–A9 and substrate after immersed in SBF for 28 days. | |
Table 4 The atomic percentage and molar ratio of Ca and P on the surface of samples A1–A9 and substrate
Sample codes |
A1-1 |
A1-2 |
A2-1 |
A2-2 |
A3-1 |
A3-2 |
A4-1 |
A4-2 |
A5-1 |
A5-2 |
Ca (atomic%) |
3.02 |
20.85 |
8.48 |
29.76 |
4.04 |
1.69 |
3.82 |
1.51 |
1.43 |
14.55 |
P (atomic%) |
0.82 |
11.48 |
7.15 |
7.07 |
5.57 |
1.9 |
3.12 |
8.19 |
— |
5.03 |
Ca/P |
3.68 |
1.82 |
1.19 |
4.21 |
0.73 |
0.89 |
1.22 |
0.18 |
— |
2.89 |
Sample codes |
A6-1 |
A6-2 |
A7-1 |
A7-2 |
A8-1 |
A8-2 |
A9-1 |
S-1 |
S-2 |
Ca (atomic%) |
4.5 |
45.45 |
3.02 |
20.52 |
4.78 |
3.43 |
7.63 |
12.2 |
16.11 |
P (atomic%) |
4.98 |
9.17 |
0.82 |
17.71 |
2.93 |
4.66 |
5.6 |
10.66 |
13.97 |
Ca/P |
0.90 |
4.96 |
3.68 |
1.16 |
1.63 |
0.74 |
1.36 |
1.14 |
1.15 |
The XRD patterns of samples A1–A9 and substrate immersed in SBF for 28 days were shown in Fig. 10. The abundant existence of Cl− in SBF accelerated the pitting corrosion of samples, but the presence of HPO42−/PO42−, HCO3−/CO32−, Ca2+ contributed to the formation and precipitation of calcium phosphate and carbonate salt which may seal the micro-pores and prevent further corrosion of the samples.1,59,60 Hydroxyapatite (Ca10(PO4)6(OH)2) was detected in the immersed samples which demonstrated the excellent biocompatibility of these MAO coated samples.
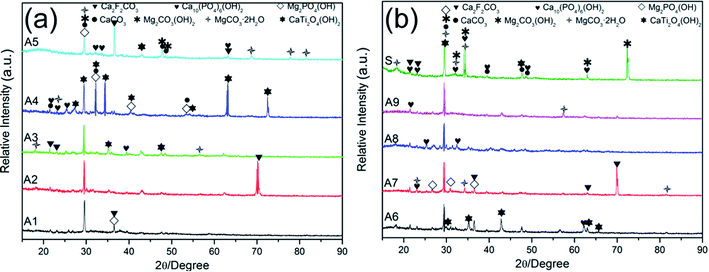 |
| Fig. 10 XRD patterns of samples A1–A9 and substrate immersed in SBF for 28 days. | |
3.6 Growth mechanism of MAO coatings
The electrolytes composition of samples A4 and A7 were relatively close to the optimal combination. It could be observed that white bumps distributed unevenly on samples A4 and A7 (as shown in Fig. 1 (A4, A7)). On the contrary, the micro-morphologies of samples A4 and A7 showed that the micro-pores distributed uniformly on the MAO coatings. The micro-pores of samples A4 and A7 were small and almost the same size. Furthermore, almost all the micro-pores and micro-cracks were sealed by different particles (as shown in Fig. 3(A4 and A7)). Without the addition of NaF, the MAO coatings of samples A4 and A7 were relatively thin, but the adhesion and corrosion resistance of samples A4 and A7 was excellent. The steady pH values during the immersion in SBF as well as the calcium phosphate generated on MAO coatings after immersion all demonstrated the fabulous biocompatibility of samples A4 and A7.
Fig. 11 showed the schematic cross-sectional illustrations of MAO coatings on the Mg–2Zn–0.5Ca substrate which was summarized by surface and cross-sectional morphologies of MAO coatings. The interface of the substrate and MAO coatings presented a wavy-jagged and integrated appearance. Electrochemical reactions, plasma electrolysis reactions and thermal diffusion went on simultaneously during the process of coating growth.61,62 First, in the stage of high pressure anodization, a compact and uniform inner layer grew promptly to 1.7 ± 0.6 μm by ion migration.63 As the substrate was been covered by insulated oxide coatings, the voltage increased rapidly and exceeded the breakdown threshold which leads to electron avalanches. The electrons attaching to the gas bubbles triggered off plasma activities.64 The microscopic localized plasma discharge broke the coating and generated numerous discharge channels, with the potential to impair the corrosion resistance of coatings.60 And the micro-pores formed by plasma discharges were more vulnerable for next electron avalanches on account of its lower breakdown voltage.65 This was reflected as a great deal of small sparks moving rapidly and circuitously over the surface of the sample. Therefore, a series of interconnected pores formed in the coating of the sample. In the following stage, the coating grew tougher to break, the voltage increased slower and the sparks grew more intensive and extended. The more concentrated discharges caused the formation of through pores which might jeopardize the corrosion resistance of the coatings.61 But the plasma discharge locating at the coating/electrolyte interface induced the deposition of electrolyte composition in the inner discharge channel. Therefore, the micro-pores existing in surface coatings were partially self-sealed by electrolyte deposition combing with migration of Mg2+ from the substrate.66,67 In addition, the sediments formed in micro-pores were unconsolidated instead of an integral chunk (as shown in Fig. 3), the phase composition was complex after a series of “breakdown–melting–ion migration–deposition”. The formation of micro-cracks attributed to two reasons: one was the lattice distortion among the hexagonal closet-packed (HCP) lattice of Mg and various crystal structures of different phases generated in the coatings, led to the internal stress differential; the other was the Pilling–Bedworth ratios (PBR) of the oxides, fluorides, phosphates, carbonates exiting in coatings were different.60 These mismatches led to the formation of micro-cracks which impaired the corrosion resistance of the coatings.
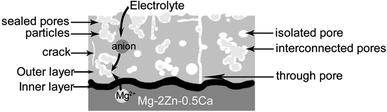 |
| Fig. 11 Schematic cross-sectional illustrations of MAO coatings on the Mg–2Zn–0.5Ca substrate. | |
4 Conclusion
Nine different micro-arc oxidation coatings with different colors were fabricated on Mg–2Zn–0.5Ca alloys to improve the mechanical properties, corrosion resistance and biocompatibility of the magnesium alloy substrate. The following conclusions can be drawn:
(1) The addition of 0.5 g L−1 Na2WO4 markedly elevated the bonding strength of the coatings with the substrate. Additives n-HAp participated in the MAO process and improved the adhesion strength of the coatings with the substrate. The participation of n-HAp helped the self-sealing of the coatings and enhanced the corrosion resistance of the samples.
(2) The addition of K2TiF6 promoted the formation of MgF2 phase and increased the thickness of the coatings. The MgF2 phase combining with Ti element led to the blue color of MAO coatings. The corrosion resistance of the samples was significantly improved due to the sealing effects of K2TiF6 additives on the micro-pores and micro-cracks in MAO coatings.
(3) The addition of NaF increased the thickness of the coatings, whilst increased the occurrence of micro-cracks and enlarged the micro-pores on account of enlarged discharge sparks. Therefore, the samples with NaF additives possessed lower corrosion resistance than the other samples.
(4) Large amount of micro-pores formed in MAO coatings were interconnected. The A4, A7 samples exhibited the best performance in terms of mechanical properties, corrosion resistance and biocompatibility. According to the orthogonal experiments, the optimal combination of additives is: 0.5 g L−1 Na 2WO4, 0 g L−1 NaF, 5 g L−1 n-HAp, 5 g L−1 K2TiF6, considering good mechanical properties, corrosion resistance and biocompatibility.
Data availability statement
All relevant data are within the paper.
Conflicts of interest
The authors declare that they have no competing interests.
Acknowledgements
This work was financially supported by the Key R&D Project of Shandong Province (Grant no. 2018CXGC0811), China Postdoctoral Science Foundation Funded Project (Grant no. 2019M652184) and China Postdoctoral Science Foundation Special Funded Project (Grant no. 2019T120589).
References
- S. Agarwal, J. Curtin, B. Duffy and S. Jaiswal, Mater. Sci. Eng., C, 2016, 68, 948–963 CrossRef CAS PubMed.
- H. Tang, Y. Han, T. Wu, W. Tao, X. Jian, Y. Wu and F. Xu, Appl. Surf. Sci., 2017, 400, 391–404 CrossRef CAS.
- M. Carboneras, M. C. García-Alonso and M. L. Escudero, Corros. Sci., 2011, 53, 1433–1439 CrossRef CAS.
- H. Ma, Y. Gu, S. Liu, J. Che and D. Yang, Surf. Coat. Technol., 2017, 331, 179–188 CrossRef CAS.
- Y. Xin, K. Huo, H. Tao, G. Tang and P. K. Chu, Acta Biomater., 2008, 4, 2008–2015 CrossRef CAS PubMed.
- S. Durdu and M. Usta, Appl. Surf. Sci., 2012, 261, 774–782 CrossRef CAS.
- F. Witte, J. Fischer, J. Nellesen, H. Crostack, V. Kaese, A. Pisch, F. Beckmann and H. Windhagen, Biomaterials, 2006, 27, 1013–1018 CrossRef CAS PubMed.
- Y. Pan, S. He, D. Wang, D. Huang, T. Zheng, S. Wang, P. Dong and C. Chen, Mater. Sci. Eng., C, 2015, 47, 85–96 CrossRef CAS PubMed.
- J. Fischer, M. H. Prosenc, M. Wolff, N. Hort, R. Willumeit and F. Feyerabend, Acta Biomater., 2010, 6, 1813–1823 CrossRef CAS PubMed.
- B. A. Shaw, Corrosion Resistance of Magnesium Alloys, ASM International, 2003, vol. 13, pp. 692–696 Search PubMed.
- X. Gu, Y. Zheng, Y. Cheng, S. Zhong and T. Xi, Biomaterials, 2009, 30, 484–498 CrossRef CAS PubMed.
- S. Cai, T. Lei, N. Li and F. Feng, Mater. Sci. Eng., C, 2012, 32, 2570–2577 CrossRef CAS.
- M. Yamaguchi, J. Trace Elem. Exp. Med., 1998, 11, 119–135 CrossRef CAS.
- G. Jin, H. Qin, H. Cao, S. Qian, Y. Zhao, X. Peng, X. Zhang, X. Liu and P. K. Chu, Biomaterials, 2014, 35, 7699–7713 CrossRef CAS PubMed.
- W. L. Yu, D. Y. Chen, Z. Y. Ding, M. Qiu, Z. Zhang, J. Shen, X. Zhang, S. Zhang, Y. He and Z. Shi, RSC Adv., 2016, 6, 45219–45230 RSC.
- G. Jin, H. Qin, H. Cao, Y. Qiao, Y. Zhao, X. Peng, X. Zhang, X. Liu and P. K. Chu, Biomaterials, 2015, 65, 22–31 CrossRef CAS PubMed.
- M. B. Kannan and R. K. S. Raman, Biomaterials, 2008, 29, 2306–2314 CrossRef CAS PubMed.
- G. Wu, Y. Fan, H. Gao, C. Zhai and Y. P. Zhu, Mater. Sci. Eng., A, 2005, 408, 255–263 CrossRef.
- D. Zander and N. A. Zumdick, Corros. Sci., 2015, 93, 222–233 CrossRef CAS.
- Y. Lu, A. R. Bradshaw, Y. L. Chiu and I. P. Jones, Mater. Sci. Eng., C, 2015, 48, 480–486 CrossRef CAS PubMed.
- B. Zhang, Y. Hou, X. Wang, Y. Wang and L. Geng, Mater. Sci. Eng., C, 2011, 31, 1667–1673 CrossRef CAS.
- N. Nashrah, M. P. Kamil, D. K. Yoon, Y. G. Kim and Y. G. Ko, Appl. Surf. Sci., 2019, 497, 143772 CrossRef.
- Y. Li, Y. Guan, Z. Zhang and S. Ynag, Appl. Surf. Sci., 2019, 478, 866–871 CrossRef CAS.
- Q. Du, D. Wei, S. Wang, S. Cheng, Y. Wang, B. Li, D. Jia and Y. Zhou, Appl. Surf. Sci., 2019, 487, 708–718 CrossRef CAS.
- D. Luo, Y. Liu, X. Yin, H. Wang, Z. Han and L. Ren, J. Alloys Compd., 2018, 731, 731–738 CrossRef CAS.
- H. F. Guo, M. Z. An, H. B. Huo, S. Xu and L. J. Wu, Appl. Surf. Sci., 2006, 252, 7911–7916 CrossRef CAS.
- R. Zhou, D. Wei, H. Yang, S. Cheng, W. Feng, B. Li, Y. Wang, D. Jia and Y. Zhou, J. Mater. Sci.: Mater. Med., 2014, 25, 1307–1318 CrossRef CAS PubMed.
- Y. K. Pan, C. Z. Chen, D. G. Wang and T. G. Zhao, Colloids Surf., B, 2013, 109, 1–9 CrossRef CAS PubMed.
- L. Xu, C. Wu, X. Lei, K. Zhang, C. Liu, J. Ding and X. Shi, Surf. Coat. Technol., 2018, 342, 12–22 CrossRef CAS.
- Y. Jang, Z. Tan, C. Jurey, Z. Xu, Z. Dong, B. Collins, Y. Yun and J. Sankar, Mater. Sci. Eng., C, 2015, 48, 28–40 CrossRef CAS PubMed.
- H. Tang, Y. Han, T. Wu, W. Tao, X. Jian, Y. Wu and F. Xu, Appl. Surf. Sci., 2017, 400, 391–404 CrossRef CAS.
- F. Zhao, A. Liao, R. Zhang, S. Zhang, H. Wang, X. Shi, M. Li and X. He, Trans. Nonferrous Met. Soc. China, 2010, 20, s683–s687 CrossRef CAS.
- L. Lei, L. Li, L. Zhang, D. Chen and W. Tian, Polym. Degrad. Stab., 2009, 94, 1494–1502 CrossRef CAS.
- S. Chen, J. Tu, Q. Hu, X. Xiong, J. Wu, J. Zou and X. Zeng, J. Non-Cryst. Solids, 2017, 456, 125–131 CrossRef CAS.
- A. R. Ribeiro, F. Oliveira, L. C. Boldrini, P. E. Leite, P. Falagan-Lotsch, A. B. R. Linhares, W. F. Zambuzzi, B. Fragneaud, A. P. C. Campos, C. P. Gouvêa, B. S. Archanjo, C. A. Achete, E. Marcantonio, L. A. Rocha and J. M. Granjeiro, Mater. Sci. Eng., C, 2015, 54, 196–206 CrossRef CAS PubMed.
- L. Song, Y. Kou, Y. Song, D. Shan, G. Zhu and E. H. Han, Mater. Corros., 2011, 62, 1124–1132 CrossRef CAS.
- W. Yang, J. Wang, D. Xu, J. Li and T. Chen, Surf. Coat. Technol., 2015, 283, 281–285 CrossRef CAS.
- M. Tang, G. Li, W. Li, H. Liu and L. Zhu, J. Alloys Compd., 2013, 562, 84–89 CrossRef CAS.
- Y. H. Xia, B. P. Zhang, C. X. Lu and L. Geng, Mater. Sci. Eng., C, 2013, 33, 5044–5050 CrossRef CAS.
- X. Wu and D. Y. C. Leung, Appl. Energy, 2011, 88, 3615–3624 CrossRef CAS.
- H. Li, H. Guan, P. Han, Y. Li and C. Zhang, Opt. Commun., 2013, 287, 162–166 CrossRef CAS.
- H. Tang, Y. Han, T. Wu, W. Tao, X. Jian, Y. Wu and F. Xu, Appl. Surf. Sci., 2017, 400, 391–404 CrossRef CAS.
- M. Tang, Z. Feng, G. Li, Z. Zhang and R. Zhang, Surf. Coat. Technol., 2015, 264, 105–113 CrossRef CAS.
- H. Chen, G. Lv, G. Zhang, H. Pang, X. Wang, H. Lee and S. Yang, Surf. Coat. Technol., 2010, 205, S32–S35 CrossRef CAS.
- L. Zhang, J. Zhang, C. Chen and Y. Gu, Corros. Sci., 2015, 91, 7–28 CrossRef CAS.
- W. Yang, D. Xu, Q. Guo, T. Chen and J. Chen, Surf. Coat. Technol., 2018, 349, 522–528 CrossRef CAS.
- X. Lin, X. Wang, L. Tan, P. Wan, X. Yu, Q. Li and K. Yang, Ceram. Int., 2014, 40, 10043–10051 CrossRef CAS.
- L. Zhang, J. Zhang, C. Chen and Y. Gu, Corros. Sci., 2015, 91, 7–28 CrossRef CAS.
- H. Duan, C. Yan and F. Wang, Electrochim. Acta, 2007, 52, 3785–3793 CrossRef CAS.
- B. Arora, B. Arora, M. Murar and V. Dhumale, J. Exp. Nanosci., 2015, 10, 819–827 CrossRef CAS.
- R. Michal, E. Dworniczek, M. Caplovicova, O. Monfort, P. Lianos, L. Caplovic and G. Plesch, Appl. Surf. Sci., 2016, 371, 538–546 CrossRef CAS.
- C. Chung, H. Lin, C. Chou, P. Hsieh, C. Hsiao, Z. Shi and J. He, Surf. Coat. Technol., 2009, 203, 1081–1085 CrossRef CAS.
- T. Yang, H. Shu, H. Chen, C. Chung and J. He, Surf. Coat. Technol., 2014, 259, 185–192 CrossRef CAS.
- C. M. Lin and S. K. Yen, Mater. Sci. Eng., C, 2006, 26, 54–64 CrossRef CAS.
- X. Lu, C. Blawert, Y. Huang, H. Ovri, M. L. Zheludkevich and K. U. Kainer, Electrochim. Acta, 2016, 187, 20–33 CrossRef CAS.
- L. Rama Krishna and G. Sundararajan, JOM, 2014, 66, 1045–1060 CrossRef CAS.
- W. Liu, T. Wang, C. Yang, B. W. Darvell, J. Wu, K. Lin, J. Chang, H. Pan and W. W. Lu, Osteoporosis Int., 2016, 27, 93–104 CrossRef CAS PubMed.
- Y. Shen, W. Liu, C. Wen, H. Pan, T. Wang, B. W. Darvell, W. W. Lubc and A. W. Huange, J. Mater. Chem., 2012, 22, 8662 RSC.
- M. B. Kannan, R. K. Singh Raman, F. Witte, C. Blawert and W. Dietzel, J. Biomed. Mater. Res., Part B, 2011, 96B, 303–309 CrossRef PubMed.
- L. Cui, R. Zeng, S. Guan, W. Qi, F. Zhang, S. Li and E. Han, J. Alloys Compd., 2017, 695, 2464–2476 CrossRef CAS.
- R. O. Hussein, X. Nie and D. O. Northwood, Electrochim. Acta, 2013, 112, 111–119 CrossRef CAS.
- R. O. Hussein, X. Nie, D. O. Northwood, A. Yerokhin and A. Matthews, J. Phys. D: Appl. Phys., 2010, 43, 105203 CrossRef.
- D. Veys-Renaux, E. Rocca and G. Henrion, Electrochem. Commun., 2013, 31, 42–45 CrossRef CAS.
- M. P. Kamil, M. Kaseem, Y. H. Lee and Y. G. Ko, J. Alloys Compd., 2017, 707, 167–171 CrossRef CAS.
- H. Nasiri Vatan, R. Ebrahimi-kahrizsangi and M. Kasiri-asgarani, J. Alloys Compd., 2016, 683, 241–255 CrossRef CAS.
- L. Zhu, X. Ke, B. Zhang, Y. Zhang and M. Sui, J. Alloys Compd., 2018, 766, 88–94 CrossRef CAS.
- L. Zhu, Z. Guo, Y. Zhang, Z. Li and M. Sui, Electrochim. Acta, 2016, 208, 296–303 CrossRef CAS.
|
This journal is © The Royal Society of Chemistry 2020 |
Click here to see how this site uses Cookies. View our privacy policy here.