DOI:
10.1039/C9RA09990E
(Paper)
RSC Adv., 2020,
10, 2786-2790
Heat transfer properties of Morpho butterfly wings and the dependence of these properties on the wing surface structure†
Received
29th November 2019
, Accepted 7th January 2020
First published on 15th January 2020
Abstract
The heat transfer properties of a material strongly rely on its surface structure. The wings of the Morpho butterfly have a unique surface structure with features of order and disorder. In this work, the surface temperature and radiative heat flux of Morpho butterfly wings with structural colour when a ceramic heater attached to the opposite surface of the wings was heated to 250 °C were evaluated in terms of their heat transfer properties. Morpho menelaus butterfly (MM) wings and Cithaerias (CE) wings with no periodic structure on their surface, were used as samples. The MM wings had higher surface temperature and radiative heat flux than the CE wings, which is the first report of heat transfer properties of the wings. The surface structure of the MM wings was changed by heat treatment in order to investigate the effect of the surface structural change on their heat transfer properties. The treatment changed the colour of the wings to red and brown, distorting the periodic structure. The radiative heat flux increased due to the change in the structure on their surface. XPS spectra revealed that the treatment leads to a slight change in the chemical structure of the wings. The spectral analyses results showed there was no obvious change in the mid-infrared absorbance. The heat radiative properties of the MM wings were strongly influenced by the surface structural changes due to the heat treatment.
Introduction
Thermal management through the fabrication of various structures on the surface of materials to enhance their heat transfer properties has been investigated over a wide range of industries, such as semiconductors,1,2 electronics,3,4 and photovoltaic cell applications.5,6 Two types of surface structure have been suggested for the enhancement of heat transfer properties. The periodic microscopic roughness on the material's surface causes an increase in surface area, leading to the improvement of radiative heat flux from the surface.7 The periodic layered structures called photonic crystals control the reflectance or absorbance of infrared light.8,9 Meanwhile, Maire et al. demonstrated that heat conductive properties of a Si surface with nanoscale-disordered holes increase compared with surfaces with periodic holes.10 Similar to this report, studies about disordered surfaces have been gradually emerging.11
Recently, the field of engineering, which was inspired by the characteristic features of living organisms, has attracted many researchers.12–14 There are functional surface structures in nature, which can possess various heat transfer properties. Pachliopta aristolochiae butterflies have been reported to control the transmittance and absorbance in the solar spectrum by holes of random size on their wing surfaces.15 Bitis gabonia snakes have high solar absorbing properties due to the disordered shape projections on their scale surfaces.16 Saharan silver ants have triangle-shaped skin hair distributed randomly on their body to control infrared solar absorbance and reflectance.17 We assume that the control of both the order and disorder structure of material surfaces would be the key to the regulation of the heat transfer properties.
Morpho butterflies have roof tile-shaped scales on their wings surface, which are arranged in periodic lines called “ridges” with approximately 1 μm between two ridges. These ridges have shelf-like structures on their side surface, which are called “lamellae” structures, with 200–300 nm between individual shelves (Fig. S1†). Although there have been many optical studies about Morpho butterfly wings inspired by their structural colouration,18–20 the actual heat transfer properties has not been experimentally demonstrated. It has been reported that the nano- and microscale asperities behave as heat conductive paths to transfer the heat to the surrounding environment.21 Didari et al. suggested a way to design original and modified structures of Morpho didius wings using algorithms.22 This report revealed that the heat flux within the atmospheric window (8–13 μm bandwidth) of the simulated structures varied by changing the distance between the shelves and their sizes. We speculate that the ridges and lamellae structures of Morpho butterfly wings would act as effective paths for heat transfer, and changes in the surface structure would affect the radiative heat flux. Pris et al. reported that the visible reflectance of the wings showed a reduction of 5.4% by heating to ΔT = 30 °C.23 The heat treatment is thought to change the surface structure of the Morpho butterfly wings. In this study, the heat transfer properties of Morpho butterfly wing surfaces were investigated to clarify the effect of surface structural changes due to heat treatment on the heat transfer properties.
Experimental
Small pieces with dimensions of 10 × 10 mm2 were collected from three types of butterfly wings: two types of Morpho (M.) menelaus (MM) obtained from Brazil and M. adonis (MA) from Giana and Cithaerias (CE) with no periodic structure on their surface from Peru (Fig. S2†). The thickness of MM, MA and CE wings measured by a micrometer were 0.26 mm, 0.25 mm and 0.23 mm, respectively. The weight of MM, MA and CE wings with the size were 0.53, 0.47 and 0.37 mg, respectively. The ventral surface of the wings was attached to a ceramic heater (10 × 10 mm) using a thermally conductive tape (Z5008, HIOKI) to change from room temperature to 250 °C. The temperature change in the opposite surface, which has the structural colour, due to the heating was monitored by using a thermocouple (ST-51-100-C, RKC Instrument). The radiative heat flux of the wings surface was also measured by a radiation sensor (10 × 10 mm RF series, Captec), which was 10 mm from the wings and connected to a chiller (MC-02, Advanced Thermal Science) to maintain the thermal difference between the wings and the sensor. In the measurement of the radiative heat flux, surface temperature of the dorsal wings with the structural colour were monitored by an infrared camera (CPA-E6, FLIR systems). ε of the camera was set as 0.95, which was the closest to surface temperature of the wings measured by the thermocouple. The measured wavelength of this infrared camera was 7.5–14 μm. The heat transfer property measurements were carried out at least three times for each wing, and the uncertainly was evaluated as the standard deviation of the measurements.
In our preliminary experiment, treatment at over 250 °C for 10 minutes caused surface structural changes of the wings. Therefore, the wings were heated at 250 and 300 °C for 10 minutes on a hot plate to change their surface structure. The surface morphology of the wings was observed by an optical microscope (VHX2000, Keyence) and a field emission-scanning electron microscope (SEM, JSM-6301, JEOL). The transmittance and reflectance properties of the wings in the near infrared (NIR) range were evaluated by UV/VIS/NIR spectrometer (V770, JASCO) with an integrated sphere. The mid-infrared (MIR) absorbance of the dorsal surface with the inherent structure of the MM, MA and CE wings was evaluated by Fourier transform infrared spectrophotometer (FT-IR 4100, JASCO).
Results and discussion
Heat transfer properties of the Morpho butterfly wings
Fig. 1(a) shows the time dependence of surface temperature changes of the MM wings and CE wings when the heater temperature increased to 100 °C. This result reveals that the increased rate of the surface temperature of the MM wings was higher than that of CE wings, which is fit to the heat equation as follows. |
 | (1) |
where α is the coefficient of thermal diffusion (m2 s−1) and T is the surface temperature of the sample (K). Each wing surface shows almost constant temperature after 40 minutes. It seems that surface temperature of the both wings becomes the steady state after heating for 40 minutes. These results imply that the MM wings have a higher coefficient of thermal diffusion than that of CE wings. Fig. 1(b) shows the relationships between the surface temperature of the wings after 40 minutes of the heating and the heater temperature. It is clear that MM wings had higher surface temperature than that of CE wings. The MA wings, which have a similar surface structure to that of the MM wings (shown in Fig. S3†), had almost the same surface temperature as that of the MM wings (Fig. S4†). From these results, the surface structure of Morpho butterfly wings has the ability to enhance their heat conductive properties.
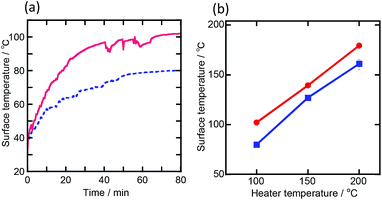 |
| Fig. 1 (a) Surface temperature changes of the MM (solid line) and CE (dashed line) wings during heating them from room temperature to 100 °C for 80 minutes. (b) Relationship between the surface temperature of the MM (●) and CE (■) wings and the heater temperature. | |
Fig. 2 shows the dependence of the radiative heat flux on the surface temperature of the wings. The radiative heat flux of MM wings exceeded that of the CE wings under this experimental condition. The heat radiative property of a material depends on the emissivity, surface temperature, and surface area based on the Stefan–Boltzmann law as follows,
where
σ is Stefan–Boltzmann constant (=5.67 × 10
−8 W (m
2 K
4)
−1),
ε is emissivity (—),
A is the surface area (m
2) and
T is the surface temperature of sample (K). The surface area of a material can be a projection area in horizontal plane.
24 This implies that the surface area of the MM and the CE wings is determined to be the same value. The radiative heat transfer property of a material is strongly affected by its emissivity and surface temperature. The MM wings had higher radiative heat flux with lower surface temperature than that of the CE wings. Absorptivity and emissivity of a material can be equal at a given surface temperature based on the Kirchhoff's law.
Fig. 3 shows MIR absorbance spectra of the MM and the CE wings. The wavelength with the highest spectral-radiance characteristics in the range of surface temperature of the wings is determined to be 5.5–7.0 μm by Planck's radiation law. The absorbance properties of the MM wings were higher than those of the CE wings in the wavelength attributed to the surface temperatures of the wings. This suggests that the higher radiative heat flux of the MM wings compared with the CE wings is caused by the higher emissivity. The calculated emissivity of the wings by using the
eqn (2) showed less than 0.1, which is smaller than the emissivity obtained from the MIR spectra. The convective heat transfer under the atmospheric experiments would lead to decline of the heat flux. In addition, the MA wings showed similar values in radiative heat flux as that of the MM wings (Fig. S5 and S6
†). These results imply that the emissivity of the
Morpho butterfly wings contributes to enhance their heat radiative properties.
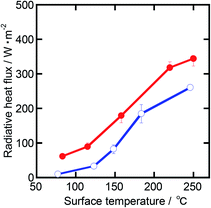 |
| Fig. 2 Relationship between the radiative heat flux of MM (●) and CE wings (○) and their surface temperature. | |
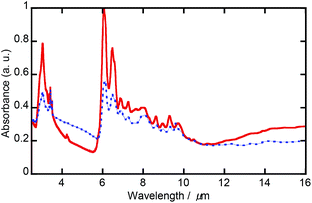 |
| Fig. 3 MIR absorbance spectra of the MM (solid line) and the CE (dashed line) wings. | |
Relationships between the surface structure change and the heat transfer properties of the wing
The heat treatment of the MM wings was conducted to explore the relationships between the surface structural change and heat radiative properties of the Morpho butterfly wings. Fig. 4 shows the colour changes of the MM surface before and after the heat treatments. The colour of the wing surfaces changed from blue to red-purple due to treatment at 250 °C and became brown due to the treatment at 300 °C.
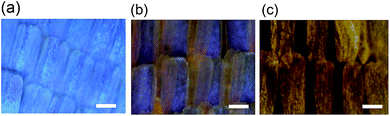 |
| Fig. 4 Optical images of the MM wings before (a) and after the heat treatment at 250 °C (b) and 300 °C (c). Scale bar shows 50 μm. | |
The SEM observation (Fig. 5) reveals that the heat treatment changes in the ridge structure. The treatment at 250 °C caused distortion of the ridge structure. In the case of the wings treated at 300 °C, some ridges on the wings surface disappeared. The average scale size of the wings calculated from the SEM images and an image analysis soft (ImageJ) was 66.3 μm before the treatment, 65.1 μm after the treatment at 250 °C and 70.4 μm after the treatment at 300 °C, which indicates almost the same size before and after the treatment. The width between the two shelves in the lamellae structure of the wings surface also seems not to be changed dramatically under this experimental conditions (Fig. S7†). These results show that the heat treatment changes the colour of the MM wings due to the surface structural changes. The heat treatment at 300 °C led to a decline in the surface area.
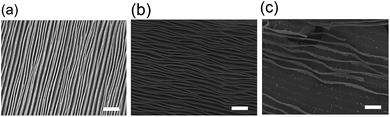 |
| Fig. 5 SEM images of the MM wings before (a) and after the heat treatment at 250 °C (b) and 300 °C (c). Scale bar shows 5 μm. | |
Fig. 6 shows the XPS C1s spectra of the MM wings before and after the heat treatment. The peak was fitted by two peaks using Gaussian functions; one peak at approximately 284 eV (peak 1), assigned to the carbon of glucosamine that composes the framework of chitin, and the other peak at approximately 287 eV (peak 2), assigned to the carbon that is connected with amino groups of the side chain of chitin.25,26 The peak position of peak 1 shifted slightly to the lower energy, indicating decline of the binding energy attributable to chitin due to the heat treatment. The integrals ratio of peak 2/peak 1 for the wings before and after heat treatment at 250 and 300 °C were determined to be 0.86, 1.08 and 0.68. It has been already proposed that the side chains of organic materials, such as proteins27 and polysaccharides,28 prevent the heat conductive property of a material. However, all the wings showed similar trends in surface temperature change, as shown in Fig. S8.† Fig. 7 shows MIR absorbance spectra of the MM wings before and after the heat treatment. There was almost the same spectra before and after the heat treatment. These imply that the chemical structural changes due to the heat treatment have little effect on the heat transfer properties of the wings.
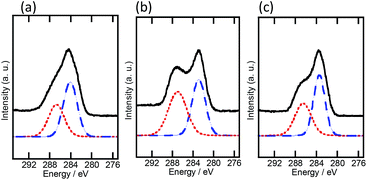 |
| Fig. 6 XPS spectra of the C1s of the MM wings before (a) and after the heat treatment at 250 °C (b) and 300 °C (c). Solid and dashed lines represent original and fitted spectra. | |
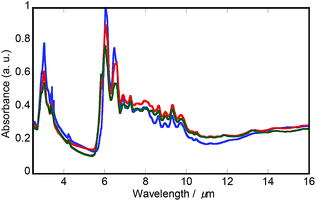 |
| Fig. 7 MIR absorbance spectra of the MM wings before (blue line) and after the heat treatment at 250 °C (red line) and 300 °C (green line). | |
Fig. 8 shows the relationships between the radiative heat flux and the surface temperature of the MM wings before and after the heat treatment. The wings treated at 250 °C have the highest radiative heat flux among the wings under this experimental condition. Radiative heat flux of the wings tends to enhance due to the treatment, although the emissive properties of the wings were almost the same. This implies that the enhancement of the radiative heat flux was mainly derived from the surface structural change. We suppose that surface design for enhancement of their heat radiative properties of the material is to maintain the periodic structure and introduce a distortion into it.
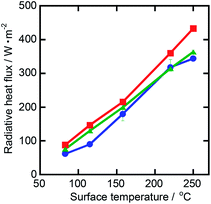 |
| Fig. 8 Dependence of the radiative heat flux of the MM wings before (●) and after the heat treatment at 250 °C (■) and 300 °C (▲) on the surface temperature. | |
Conclusions
The surface temperature and radiative heat flux of Morpho butterfly wings before and after the heat treatment were investigated to clarify the effects of surface structure on the heat transfer properties. The time dependence of surface temperature measurement showed that the heat conductive properties of Morpho menelaus and Morpho adonis wings were higher than those of Cithaerias wings, which have almost the same thickness and main components as the Morpho butterfly wings, due to their surface structure. The wings of Morpho menelaus and Morpho adonis had higher heat radiative properties than those of the Cithaerias wings due to their emissivity. The heat treatment of the Morpho butterfly wings caused surface structural changes, leading to the enhancement of the radiative heat flux. Understanding the structural effects of Morpho butterfly wings on the heat transfer properties is a potential approach to develop a new surface design for thermal management applications.
Author contributions statement
H. M. conceived the experiments. H. M. and M. K. conducted the experiments and analyzed the results. All authors reviewed the manuscript.
Conflicts of interest
The authors declare no competing interests.
Acknowledgements
This work was supported in a part by a research funding granted by NITech President.
References
- J. Lee, D. Kim, C.-H. Choi and W. Chung, Nano Energy, 2017, 31, 504–513 CrossRef CAS.
- J. Park, J.-H. Kang, X. Liu, S. J. Maddox, K. Tang, P. C. Mclntyre, R. B. Seth and L. Brongersma, Sci. Adv., 2018, 4, eaat3163 CrossRef CAS PubMed.
- B. Liu, W. Gong, B. Yu, P. Li and S. Shen, Nano Lett., 2017, 17, 666–672 CrossRef CAS PubMed.
- M. Mecklenburg, W. A. Hubbard, E. R. White, R. Dhall, S. B. Cronin, S. Aloni and B. C. Regan, Science, 2015, 347, 629–632 CrossRef CAS PubMed.
- V. E. Ferry, M. A. Verschuuren, H. B. T. Li, E. Verhagen, R. J. Walters, R. E. I. Schropp, H. A. Atwater and A. Polman, Opt. Express, 2010, 18, A239 CrossRef PubMed.
- Z. Yao, Y. Ma, S. N. David, D. Zhao, R. Lou, G. Tan, R. Yang and X. Yin, Science, 2017, 355, 1062–1066 CrossRef PubMed.
- H. Sai, Y. Kanamori and H. Yugami, J. Micromech. Microeng., 2005, 15, S243–S249 CrossRef CAS.
- S. Y. Lin, J. G. Fleming, D. L. Hetherington, B. K. Smith, R. Biswas, K. M. Ho, M. M. Sigalas, W. Zubrzycki, S. R. Kurtz and J. Bur, Nature, 1998, 394, 251–253 CrossRef CAS.
- S.-Y. Lin, J. G. Flemming, E. Chow and J. Bur, Phys. Rev. B: Condens. Matter Mater. Phys., 2000, 62, R2243–R2246 CrossRef CAS.
- J. Maire, A. Roman, R. Yanagisawa, A. Ramiere, A. Volz and M. Nomura, Sci. Adv., 2017, 3, e1700027 CrossRef PubMed.
- M. N. Lackyanova, J. Mendoza, H. Lu, B. Song, S. Huang, J. Zhou, J. Garlow, L. Wu, B. J. Kirby, A. J. Grutter, A. A. Puretzky, Y. Zhu, M. S. Dresselhaus, A. Gossard and G. Chen, Sci. Adv., 2018, 4, eaat9460 CrossRef PubMed.
- G. Arregui, N. D. Lanzillotti-Kimura, C. M. Sotomayor-Torres and P. D. García, Phys. Rev. Lett., 2019, 122, 043903 CrossRef CAS PubMed.
- Z. Han, J. Xu, X. Liu, H. Zhang, D. Wang, Z. Chen, D. Zhang and T. Fan, Adv. Funct. Mater., 2018, 28, 1705309 CrossRef.
- H. Lee, D.-S. Um, Y. Lee, S. Lim, H.-j. Kim and H. Ko, Adv. Mater., 2016, 28, 7457–7465 CrossRef CAS PubMed.
- R. H. Siddique, Y. J. Donie, G. Gomard, S. Yalamanchili, T. Merdzhanova, U. Lemmer and H. Hölscher, Sci. Adv., 2017, 3, e1700232 CrossRef PubMed.
- M. Spinner, K. Alexander, S. N. Gorb and G. Westhoff, Sci. Rep., 2013, 3, 1846 CrossRef PubMed.
- N. N. Shi, C.-C. Tsai, F. Camino, G. D. Bernard, N. Yu and R. Wehner, Science, 2015, 349, 298–301 CrossRef CAS PubMed.
- K. Chung, S. Yu, C.-J. Heo, J. W. Shim, S.-M. Yang, M. G. Han, H.-S. Lee, Y. Jin, S. Y. Lee, N. Park and J. H. Shin, Adv. Mater., 2012, 24, 2375–2379 CrossRef CAS PubMed.
- R. Ahmed, X. Ji, R. M. H. Atta, A. A. Rifat and H. Butt, RSC Adv., 2018, 8, 27111–27118 RSC.
- J. He, N. S. Villa, Z. Luo, S. An, Q. Shen, P. Tao, C. Song, J. Wu, T. Deng and W. Shang, RSC Adv., 2018, 8, 32395–32400 RSC.
- H. Huang, C. Liu, Y. Wu and S. Fan, Adv. Mater., 2005, 17, 1652–1656 CrossRef CAS.
- A. Didari and M. Pinar Mengüç, Sci. Rep., 2018, 8, 16891 CrossRef PubMed.
- A. D. Pris, Y. Utturkar, C. Surman, W. G. Morris, A. Vert, S. Zalyubovskiy, T. Deng, H. T. Ghiradella and R. A. Potyrailo, Nat. Photonics, 2012, 6, 195–200 CrossRef CAS.
- Y. Tan, B. Liu, S. Shen and Z. Yu, Enhancing radiative energy transfer through thermal extraction, Nanophotonics, 2016, 5, 22–30 Search PubMed.
- Q. Yan, S. Chena, L. Ying, H. Suna, S. Jia, J. Shi, C. M. Pedersen, Y. Wang and X. Hou, Carbohydr. Polym., 2015, 133, 163–170 CrossRef PubMed.
- M. R. Weatherspoon, Y. Cai, M. Crne, S. Mohan and K. H. Sandhage, Angew. Chem., Int. Ed., 2008, 47, 7921–7923 CrossRef CAS PubMed.
- X. Yu and D. M. Leitner, Chem. Phys., 2005, 122, 054902 Search PubMed.
- S. Lepri, R. Livi and A. Politi, Phys. Rev. Lett., 1997, 78, 1896–1899 CrossRef CAS.
Footnote |
† Electronic supplementary information (ESI) available. See DOI: 10.1039/c9ra09990e |
|
This journal is © The Royal Society of Chemistry 2020 |
Click here to see how this site uses Cookies. View our privacy policy here.