DOI:
10.1039/C9RA09069J
(Paper)
RSC Adv., 2020,
10, 1261-1270
A high-performance trace level acetone sensor using an indispensable V4C3Tx MXene†
Received
3rd November 2019
, Accepted 18th December 2019
First published on 8th January 2020
Abstract
The development of a stringent sensor to detect low levels of acetone, yielding the potential for the point-of-care clinical diagnosis of diabetes, is still a great challenge but is urgently required. Most studies have focused on Ti3C2Tx, yet other types of MXenes with good performance are rare. Herein, an emerging kind of MXene, V4C3Tx, has been prepared from V4AlC3 via the selective etching of the Al layer using aqueous HF at room temperature (RT), and its performance as an acetone sensor is presented. A V4C3Tx based acetone sensor delivers good performance, as demonstrated by its low working temperature of 25 °C, low detection limit of 1 ppm (lower than the 1.8 ppm diabetes diagnosis threshold), and high selectivity towards acetone in a mixed gas of acetone and water vapor, hopefully showing promise for application in the much faster and earlier diagnosis of diabetes. V4C3Tx MXene is used for the first time in the field of acetone detection in this work, hopefully opening up a path for the investigation of applications of MXene in gas sensors, and such exciting findings distinguish V4C3Tx as a comparable material to the well-known Ti3C2Tx. In addition, we used DFT calculations to explore the mechanisms that result in the superior selectivity for acetone with respect to water vapor. Hopefully, the proposed mechanisms combining experimental results and theoretical study will shed light on the design and production of new high-performance acetone sensors.
1. Introduction
Recent years have seen an enormous amount of research highlighting oxygenated volatile organic compounds (OVOCs) owing to their threats to human health and the environment.1–4 Among various OVOCs, acetone is one of the most promising research candidates for various industrial and medical applications, not least towards diabetes diagnosis5–7 in human exhaled breath. Clinical analysis has shown that the acetone concentration in the exhaled breath of healthy people is 300–900 ppb, while it will increases to more than 1.8 ppm for diabetic patients.8 Although similar work has been done relating to a highly selective trace-level acetone sensor,9 in the face of a lower diagnosis threshold and complex physiological environment, a stringent sensor which possesses high selectivity towards acetone at the sub-ppm level still needs urgently to be addressed.
A new class of two-dimensional (2D) transition metal carbides or carbonitrides (MXenes),10–14 with the formula Mn+1XnTx, where M is an early transition metal (Sc, Ti, V, Cr, Zr, Nb, Mo, Ta), X is C and/or N, T is the surface termination (O, OH, and/or F) and x represents the number of termination groups, have recently received considerable interest owing to their promising applications in many diverse fields, e.g., energy storage,13,15–21 water purification,22 electromagnetic shields,23,24 photothermal cancer therapy,25,26 and gas separation.12 MXenes are fabricated by the exfoliation of ternary layered carbides and nitrides, known as MAX phases with the formula Mn+1AXn, where n = 1, 2, or 3, M represents a transition metal, A represents the A-group element27,28 in the periodic table of the elements, and X represents carbon and/or nitrogen. The exfoliation process is carried out by selectively etching the A-group element using concentrated hydrofluoric acid (HF) or hydrochloric acid (HCl) and fluoride salts or potassium hydroxide to obtain 2D carbides or carbonitrides called MXenes, which are typically functionalized with a hydroxyl (OH), oxygen (O) or fluorine (F) group.29,30 Until now, only the following MXenes have been discovered: M2X type,31–34 M3X2 type,30,35,36 and M4X3 type.29,36 As the above list shows, it should be noted that most M2X- and M3X2-types of MXenes have been obtained, but of the M4X3-type MXenes, only Ta4C3Tx,10 Nb4C3Tx,29 and Mo2Ti2C3Tx36 have been reported. Therefore, the development of M4X3-type MXenes is necessary and of great importance for expanding the application of the MXene family.
Currently, the most studied V-based MXene is V2CTx MXene, which has been demonstrated to be a promising electrode material for Li and Na-ion batteries according to theoretical37,38 and experimental results.32,39,40 Nevertheless, there are still many challenges for V2CTx, such as the difficulty in synthesizing the pure phase and poor stability. After studying the structure of V2CTx carefully, the instability of V2CTx can be ascribed to the fact that a three-atom-thick V2CTx monolayer is too thin. When the weak metallic V–Al bonds are broken in the etching process, the V–C bonds as the basic composition units of V2CTx are also removed, resulting in the easy decomposition of V2CTx. In order to overcome the problem of the thinness of V-based MXene, it is feasible to increase the thicknesses via the fabrication of the much thicker V3C2Tx/V4C3Tx instead of the thinner V2CTx.32,37,41 Previously, V4AlC3 MAX was reported in 2007,42 boosting our confidence in the feasibility of transforming V4AlC3 MAX into V4C3Tx MXene. However, we also notice that, unlike other MXenes, V4AlC3 cannot be produced by simple ball milling and high-temperature reaction, making it harder to synthesize V4C3Tx MXene.
Herein, an emerging kind of MXene, V4C3Tx, is prepared by the synthesis of V4AlC3 with the help of Al and Co as fluxes and catalysts, while the subsequent selective etching of the Al layer from V4AlC3 is performed by using aqueous HF at room temperature. V4C3Tx MXene is used in the field of acetone detection for the first time in this work. Interestingly, we found that V4C3Tx MXene became semiconducting from the metallic V4AlC3 after the HF treatment. It is worth noting that V4C3Tx MXene shows great acetone sensing performance with a low working temperature of 25 °C and a low detection limit of 1 ppm. Good acetone sensing performance makes V4C3Tx MXene one of the few acetone sensors meeting two prerequisite conditions (high sensitivity for low concentration (sub-ppm) and high selectivity for a mixed gas), opening up a path for the investigation of applications of MXene in gas sensors.
2. Materials and methods
2.1 Chemicals
Vanadium powder (99.99%), graphite powder (99.9%), aluminum pellets (99.995%), cobalt powder (99.995%), HCl solution (30% conc.), and HF solution (48% conc.) were purchased from Sigma-Aldrich (Germany). A corundum crucible was purchased from Charslton Technologies Pte Ltd. (Singapore).
2.2 Preparation of V4AlC3
Originally, as with the synthesis of most MAX phases, the methods of ball milling and direct reaction of stoichiometric amounts of high-purity V, Al and C were used to obtain the V4AlC3 in the pure phase, but only ternary V2AlC phase could be obtained. After many attempts, we found that Co is important for obtaining V4AlC3 from the reaction. At last, an optimal way was found to synthesize the V4AlC3 phase by using Co and Al as the catalysts and fluxes. The amounts of high-purity V, Al, Co and C in a molar ratio of 4
:
28
:
6
:
3 with a weight of 20 g were placed in a corundum crucible, and heated to 1500 °C over 10 h under flowing argon (Ar) in a tube furnace, held at 1500 °C for 30 h, then cooled to 900 °C over 30 h, and finally cooled to room temperature over 20 h. In order to obtain the V4AlC3 in the pure phase, the mixture was immersed in aqueous HCl to remove the excess metal of the solidified melt (the chart is shown in Fig. 1), and the possible reaction could be:
2CoxAly + 2(2x + 3y)HCl = 2xCoCl2 + 2yAlCl3 + (2x + 3y)H2↑ |
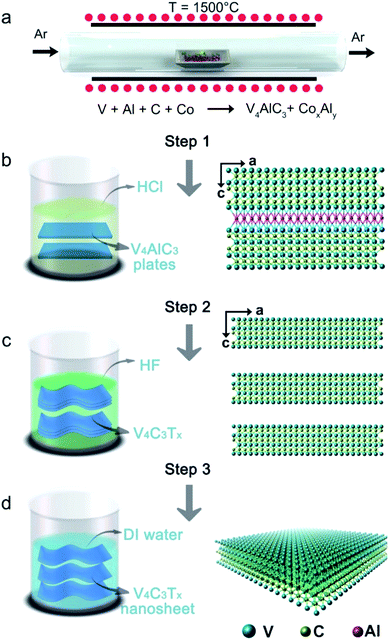 |
| Fig. 1 The synthesis, structure, and geometrical engineering of two-dimensional V4C3Tx. (a) The setup used for the growth of a single crystal of V4AlC3 with the help of metal fluxes. (b) An as-synthesized V4AlC3 single crystal with excess metal fluxes is treated with 30% HCl solution in order to remove the metal fluxes and produce pure V4AlC3. (c) V4AlC3 powder is immersed in 48% HF solution to destroy the metallic bonds of V–Al to prepare 2D V4C3Tx nanosheets. (d) The exfoliated V4C3Tx nanosheets are separated via the sonication of V4C3Tx powder in DI water. Step 1: HCl treatment, step 2: HF treatment, step 3: filtration, washing, sonication, and centrifugation. | |
The mixed solution was centrifuged at 2000 rpm for 10 min, and the supernatant was removed, then the bottom samples were washed with deionized (DI) water. The washing step was repeated many times until the pH of the top liquid was close to the pH of DI water. Finally, after the washed samples were dried in an oven, V4AlC3 pure phase with metallic platelets (Fig. 2a, b and S1d†) was obtained, as confirmed by the powder XRD pattern (Fig. 2c).
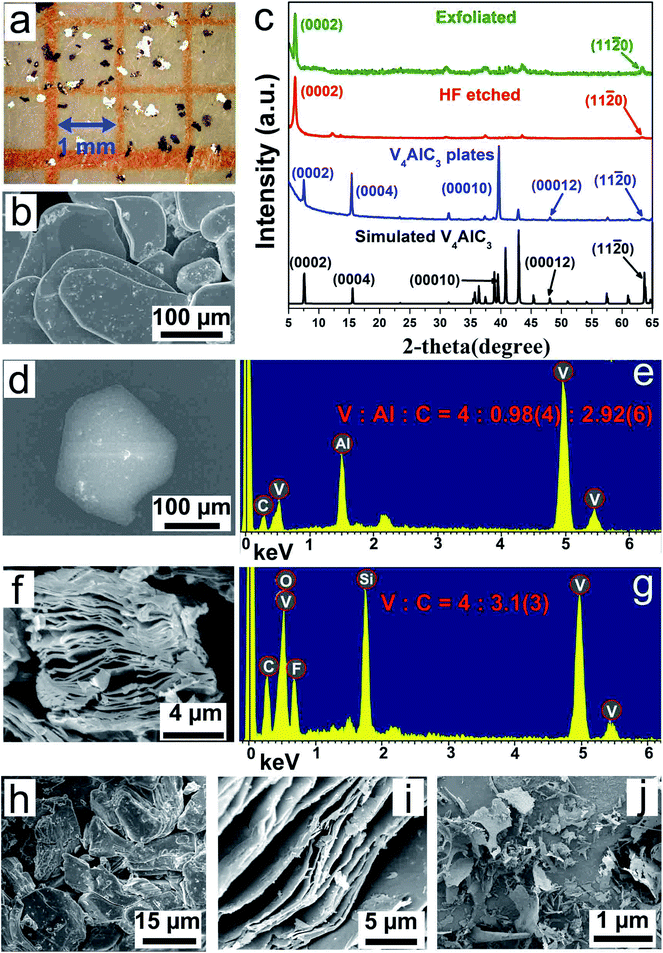 |
| Fig. 2 The characterization and analysis of V4AlC3 before and after HF treatment. Optical (a) and SEM images (b) of as-synthesized V4AlC3 plates. (c) XRD patterns of V4AlC3 before and after HF (48% conc.) treatment, and exfoliated nanosheets produced via sonication compared to the simulated XRD pattern of V4AlC3. An SEM image (d) and the corresponding EDS results from a piece of V4AlC3 with a V : Al : C atomic ratio of 4 : 0.98 : 2.92 (e). EDS measurements taken from visibly clean surfaces of V4C3Tx on a SiO2/Si (280 nm oxide layer) substrate (f) prove that the V : C atomic ratio is 4 : 3.13 (g). Different-magnification SEM images of HF-treated V4AlC3 showing the obvious exfoliated grains (h and i). (j) An SEM image of exfoliated V4C3Tx sheets obtained via sonication. | |
2.3 Preparation of V4C3Tx MXene
Firstly, 6 g of V4AlC3 single crystals was ground into a powder using a mortar, and then immersed in 110 mL of 48% concentrated HF solution at room temperature for 5 days. The resulting solution was then vacuum filtered, followed by washing with DI water until the pH reached 6. Finally, V4C3Tx powder was obtained by filtration and freeze drying at temperature: −20 °C and vacuum: 5 Pa, for use in further characterization and experimental usage. Powder XRD patterns (Fig. 2c) and EDS spectra (Fig. 2g and Table S2†) of V4C3Tx powder confirmed that 6 g of V4AlC3 had been completely transformed into 5.5 g of V4C3Tx after HF etching for 5 days.
2.4 Fabrication of V4C3Tx nanosheets
The V4C3Tx powder was dispersed in DI water, and was then sonicated in an ice-bath for 5 h using an ultrasonic machine at a power of 200 W. The mixture was centrifuged for 20 min at 3000 rpm and the obtained suspension was then freeze-dried at temperature: −20 °C and vacuum: 5 Pa to obtain the final product, i.e. V4C3Tx nanosheets, which were collected for further characterization and experimental usage. In addition, it should be noted that, if V4C3Tx powder was just treated by simple sonication and centrifugation, the yield of V4C3Tx nanosheets was less than 20%. In order to improve the rate of production, tetrabutylammonium hydroxide (TBAOH) was used to intercalate V4C3Tx powder for delamination. Firstly, 3 g of V4C3Tx powder was treated for 6 h with a 30% concentrated TBAOH solution. Secondly, the TBAOH treated V4C3Tx was obtained by centrifugation for 20 min at 10
000 rpm. Thirdly, the TBAOH treated MXene was mixed with DI water and then hand-shaken for 3 minutes. Finally, the whole mixture was centrifuged for 20 min at 3000 rpm to separate the black supernatant from non-delaminated MXenes and the obtained suspension was then freeze-dried at temperature: −20 °C and vacuum: 5 Pa to obtain about 2.4 g of V4C3Tx nanosheets. Interestingly, we found that the yield of V4C3Tx nanosheets was improved from 25% to 80% by using the delamination agent: TBAOH.
2.5 Fabrication of V4C3Tx quantum dots
Firstly, 2 g of V4AlC3 single crystals was ground into a powder using a mortar, and then immersed in 80 mL of 48% concentrated HF solution at room temperature for 10 days. The resulting solution was then filtrated and washed using DI water by turns until the pH reached 6. Secondly, the mixture was mixed with DI water and was then sonicated in an ice-bath for 2 h with a sonication power of 200 W. After centrifugation for 20 min at 10
000 rpm, the suspension was then freeze-dried at temperature: −20 °C and vacuum: 5 Pa and finally 1.0 g of V4C3Tx nanodots was obtained, whose TEM images (Fig. 3d–f) and EDX spectra (Fig. S9†) confirmed that the V–C framework in the nanodots was retained.
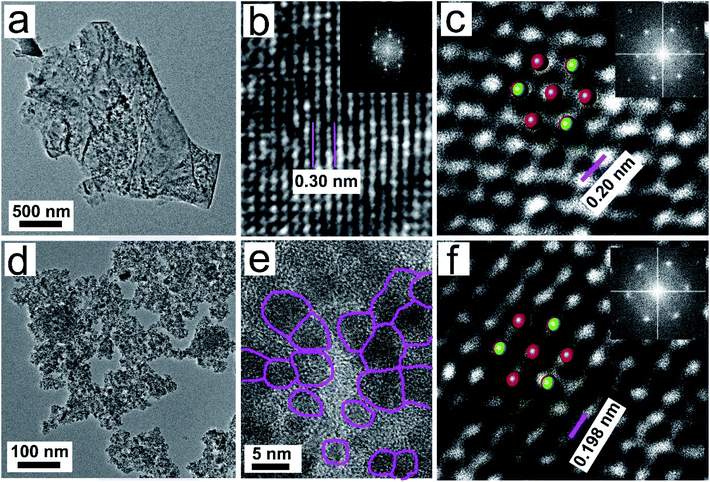 |
| Fig. 3 TEM characterization of few-layer exfoliated V4C3Tx nanosheets and quantum dots. Low-magnification (a) and high-resolution (b) TEM and atomic resolution Z-contrast STEM (c) images of V4C3Tx nanosheets and the corresponding FFT patterns. Low-magnification (d) and high-resolution (e) TEM and atomic resolution Z-contrast STEM (f) images of V4C3Tx quantum dots; the corresponding FFT pattern is shown in the inset. STEM images show the hexagonal crystal structures of V4C3Tx nanosheets (c) and quantum dots (f). C atoms are in green and V atoms are in red. | |
2.6 Sensing measurements
For the sensing experiments and characterizations, the films obtained by vacuum filtration (Fig. S8a and S10†) were processed by freeze drying, stripping and cutting to produce the desired pieces, and two copper wires were connected by silver colloid to both ends of the V4C3Tx film as the electrodes. A DC voltage was applied between the two electrodes, and the resistance of the V4C3Tx film was collected as the sensing signal. The sheet resistance of the V4C3Tx film was calculated to be ∼100 MΩ, enabling a low-power operation of the sensor to meet the requirement of ultra-low-power sensor nodes for IoT applications. The sensor device was placed in a sealed chamber, where acetone vapors at different concentrations in a nitrogen (N2) background were fed in.
3. Results and discussion
3.1 Fabrication and characterization of V4C3Tx nanosheets
The bulk V4AlC3 crystallizes in the hexagonal space group P63/mmc with a = b = 2.9302(4) Å, c = 22.745(5) Å, α = β = 90°, γ = 120°, and V = 166.187 Å3.42 The structure of V4AlC3 is characterized as a 3D V–Al–C framework consisting of seven atomic V–C–V–C–V–C–V layers connected by Al atoms with V–Al metallic bonding to form a 3D structure, as shown in Fig. S1a.† The length of the V–Al metallic bond is around 2.757 Å, longer than those of the V–C covalent bonds in the range 1.994–2.089 Å (Fig. S1b and c†). Metallic V4AlC3 plates of a size of several hundreds of micrometers and CoxAly compounds were synthesized using a solid-state reaction (Fig. 1a, S1d and S2;† for details see the Experimental section in ESI†). After the aforementioned products were treated with HCl solution, pure V4AlC3 plates were obtained (Fig. 1b, step 1). In order to prepare V4C3Tx, the V4AlC3 plates were first ground and then treated with aqueous HF (Fig. 1c, step 2). The obtained supernatant was filtrated and washed with deionized (DI) water by turn until its pH reached 6. Finally, the V4C3Tx nanosheets were obtained after sonication and centrifugation of the aforementioned solution (Fig. 1d, step 3).
All the synthesized V4AlC3 plates with a metallic luster (Fig. 2a) have a flat surface perpendicular to the c axis (Fig. 2b), whose pure phase was confirmed by the X-ray powder diffraction (XRD) pattern (Fig. 2c). The energy dispersive X-ray (EDX) result proved that the molar ratio of V
:
Al
:
C is 4
:
0.98
:
2.92 (Fig. 2d and e), which is consistent with the stoichiometric ratio of V4AlC3. In addition, the XRD pattern of single-crystal V4AlC3 gave strong peaks of (0002), (0004), (00010), and (00012), arising from the strong grain orientation along the c axis. After the treatment of V4AlC3 with HF, most of the diffraction peaks became much weaker or even disappeared, but the (0002) peak became quite strong (Fig. 2a), indicating that the MAX phase of V4AlC3 was transformed to the new MXene phase of V4C3Tx.
The shift of the (0002) peak from 7.76° to 6.04° means that the c lattice parameter shifts from 22.75 Å to 29.23 Å, which is consistent with previous reports.29,32,37 The expansion of about 6.48 Å along the crystallographic axis c can be attributed to the intercalation of water between the MXene sheets during treatment. Furthermore, the domain size of ∼5.6 nm along [0001] in V4C3Tx was estimated with Scherrer's formula, revealing that the shrinkage occurs after HF treatment, which has also been reported in other MXene phases.29,32 In addition, we also noted that, when tetrabutylammonium hydroxide (TBAOH) was used as the delamination agent to intercalate V4C3Tx powder, the yield of V4C3Tx nanosheets increased from 25% to 80%. The XRD patterns for V4C3Tx before and after 6 h of TBAOH treatment (Fig. S3†) show that the (0002) peak of V4C3Tx shifted from 6.04° to 4.2° corresponding to the c lattice parameter increasing from 29.23 Å to 32.72 Å, implying that, like other MXenes,34,43 the delamination agent can also be intercalated into V4C3Tx to improve the yield of V4C3Tx nanoflakes.
EDX and X-ray photoelectron (XPS) spectroscopy were used to identify whether the V–C framework remained in V4C3Tx after HF treatment. Five elements were identified in the EDX spectrum of V4C3Tx (Fig. 2f and g): V, C and F are from the samples, while O and Si are mainly from the SiO2 substrate. The V
:
C ratio is ∼4
:
3.13, consistent with the expected stoichiometric ratio of 4V
:
3C, indicating that the V–C framework is well preserved. This is also supported by XPS analysis where the V
:
C atomic ratio is ∼4
:
3.24 (Fig. S4 and S5†). Notably, small amounts of F and O elements are found in the XPS spectra (Fig. S5†), which possibly come from the surface termination (e.g. O, OH and F) in MXene. Also, a strong signal from O is observed in the XPS, which should be from the oxygen-containing surface terminations (O or OH) or water physically absorbed between the layers, and it was also found in Nb2CTx, Nb4C3Tx and V2CTx MXenes.29,33,44 Based on our experimental data, and the reported reaction principles for other MXenes, such as V2C, Nb2C, Ti3C2, Ti2C and Ta4C3,10,17,32,33 the chemical reaction for the production of V4C3 can be written as:
2V4AlC3 + 6HF = 2V4C3 + 2AlF3 + 3H2↑ |
After the main reaction, the vanadium atoms will react with the solution species in the interface between V4C3 and the solution, resulting in the formation of O, OH and F terminations in the surface of MXene, which was confirmed by the XPS results (Fig. S4 and S5†) and has also been observed in other MXenes.10,32
Scanning electron microscopy (SEM) images (Fig. 2f and h–j) show the layered structure of V4C3Tx, similar to other MXenes. The low-magnification transmission electron microscope (TEM) image shows the exfoliated V4C3Tx nanosheets (Fig. 3a). The lattice structures of the V4C3Tx nanosheets were examined by high-resolution TEM imaging (HRTEM, Fig. 3b and S6a†). They confirmed the single-crystalline nature of the V4C3Tx nanosheets with a lattice spacing of ∼0.30 nm (Fig. 3b). The lattice spacing agrees with the (11
0) planes of the V4AlC3 crystal. The atomic resolution Z-contrast STEM image (Fig. 3c) shows that the V4C3Tx nanosheets maintain a hexagonal crystal structure consisting of V and C atomic columns, which is also supported by the fast Fourier transform (FFT) diffraction patterns. We also observed the formation of V4C3Tx quantum dots after immersing V4AlC3 powder in aqueous HF (48% conc.) for 10 days at room temperature (Fig. 3d), which could be ascribed to the etching of the V atoms in the thinnest nanosheets or defects in V4AlC3 nanosheets by long-running HF treatment.
The lateral size of the V4C3Tx quantum dots is in the range of 1–7 nm (Fig. 3e). Such quantum dots remained the hexagonal basal structure of V4AlC3, as confirmed by HRTEM (Fig. S6b†) and STEM (Fig. 3f) images. In addition, the specific surface area of the sample was further characterized by the Brunauer–Emmett–Teller (BET) method and N2 adsorption/desorption isotherm analyses (Fig. S7†), showing that as-exfoliated V4C3Tx have a high BET surface area of 156 m2 g−1, which can compare with those of other MXenes, such as Ti3C2Tx of 98 m2 g−1,45 Ti3C2Tx of 4.74 m2 g−1,46 Ti3C2Tx/TiO2 nanowires of 56.45 m2 g−1,46 etc.
3.2 Electrical transport properties of V4C3Tx film
The electrical performance of V4C3Tx was then evaluated. A thick film consisting of as-exfoliated V4C3Tx nanosheets (Fig. S8a and b†) was prepared by vacuum filtration. The sheet electrical resistivity is ∼3 Ω cm at room temperature measured by the four-probe method (Fig. S8c†). The sheet electrical resistivity increases exponentially at low temperature, which suggests that V4C3Tx MXene becomes a semiconductor, presumably due to surface functionalization. The activation energy Ea for the conduction can be evaluated using the Arrhenius equation:
where σ is the electrical conductivity, A is the conductivity constant, T is the absolute temperature, Ea is the activation energy, and k is the Boltzmann constant. The activation energy Ea for conduction, calculated from the slope of the Arrhenius plot (Fig. S8d†), is ∼3.7 meV for V4C3Tx. Such a phase transition from metallic to semiconducting V4C3Tx MXene reveals that the fully functionalized V4C3Tx MXenes will become semiconductors with non-zero energy gaps, which was also found for its analogue MXene: V2CTx.47
Due to the large surface area and unique atomic structure of the V4C3Tx film, it shows great potential for ultra-sensitive and highly selective gas sensing. A resistive-type V4C3Tx film sensing device was fabricated, as shown in Fig. 4a. A DC voltage was applied between the two Cu electrodes. The resistance of the V4C3Tx film was collected as the sensing signal. The sheet resistivity of the V4C3Tx film was calculated to be ∼1000 MΩ sq−1, making it possible for ultra-low-power consuming sensor nodes for internet of things (IoT) applications. The sensor device was placed in a sealed chamber, where acetone vapors of different concentrations were fed in with nitrogen (N2) as a carrier gas through a standing gas stream mixing method, as reported in our previous work.48 Accordingly, this shows that acetone is sensitive to V4C3Tx film here and can be detected accurately. More details about the experimental setup can be found in the Experimental section.
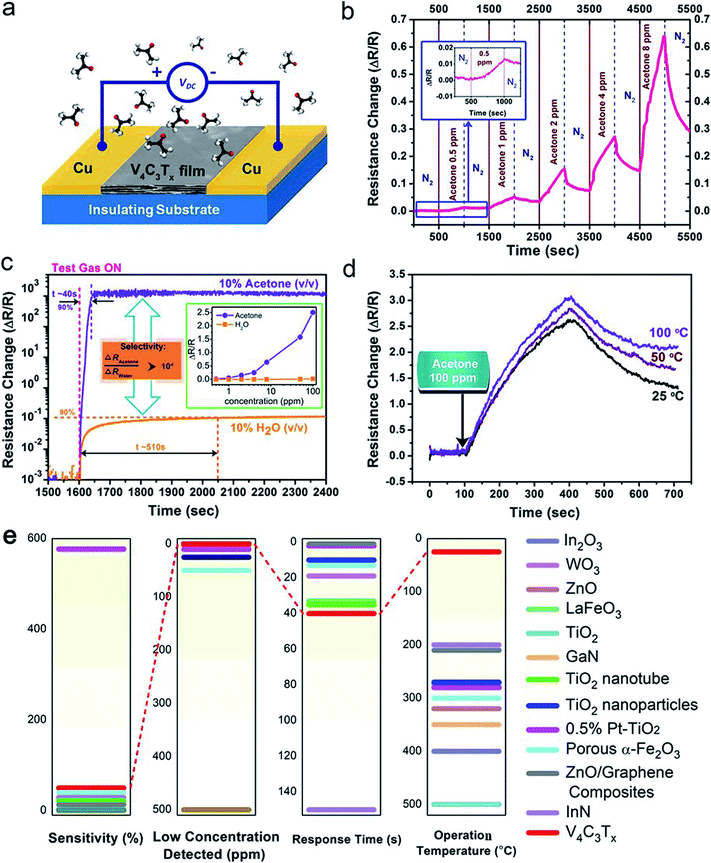 |
| Fig. 4 The acetone sensing performance of an as-fabricated V4C3Tx device. (a) A schematic diagram of the V4C3Tx film sensor fabricated on an insulating substrate for mechanical support and with Cu electrodes. (b) The sensor responses of V4C3Tx film to different concentrations of acetone from 0.5 ppm to 8 ppm at room temperature; the inset is the response to 0.5 ppm acetone. (c) A comparison of the gas sensing responses of V4C3Tx film to 10% acetone (v/v) and 10% H2O (v/v); the inset is the selectivity between acetone and water vapor at low concentrations, implying the excellent selectivity toward acetone over water molecules at a low detection limit. (d) The gas sensing responses of V4C3Tx film at different temperatures of 25 °C, 50 °C, and 100 °C, respectively. (e) A comparison of various gateless acetone gas sensors with V4C3Tx (this work) according to sensitivity, lowest concentration detected, response time, and operating temperature. | |
3.3 Acetone sensing properties of a V4C3Tx based device
Good sensitivity detection of acetone down to sub-ppm has been demonstrated using V4C3Tx film at room temperature (25 °C), as shown in Fig. 4b. It is notable that there is ∼5% change in the total resistance for 1 ppm acetone, which is better than that of other reported state-of-the-art of solid-state acetone sensors at room temperature.49–52 The selectivity of the acetone sensor toward water molecules was also characterized, as shown in Fig. 4c. At the same concentration, i.e. 10% v/v, the resistance change for acetone vapor is >104 higher than that for water vapor. This is much better than the recently reported high selectivity between acetone and water vapor based on protonic current measurement.53 The inset of Fig. 4c shows the selectivity between acetone and water vapor at low concentrations from 1 ppm to 100 ppm. This shows the significant response of the sensor to acetone over a wide range, while almost no detectable signal of water vapor could be observed, suggesting the excellent selectivity towards acetone over water molecules at the low detection limit. In addition, the rise time (defined as achieving 90% of the maximum sensor response) of the acetone response (∼40 s) is also much shorter than that of water vapor (∼510 s). In order to evaluate the optimal operating temperature for the acetone sensor, the response of the acetone sensing at elevated temperature was characterized (Fig. 4d), showing that the response gradually increases as the temperature rises, which is similar to other nanostructured solid-state nanostructure acetone sensors. However, we also noticed that the acetone sensing response of the V4C3Tx device at room temperature (25 °C) was large enough to meet practical applications for detecting acetone, combined with it being a rare RT acetone sensor, making the V4C3Tx sensor a promising RT acetone sensor.
Fig. 4e shows a comparison of various unbiased acetone gas sensors based on metal oxides and nitrides, i.e., In2O3,54 WO3,55 ZnO,56 LaFeO3,57 TiO2,58 GaN,59 InN,60 TiO2 nanotubes,61 TiO2 nanoparticles,62 0.5% Pt–TiO2,63 porous α-Fe2O3,64 and ZnO/graphene composites,65 which shows that our fabricated V4C3Tx sensor possesses the best comprehensive performance, such as good sensitivity, low concentration detected, fast response time and optimal working temperature (RT), making the V4C3Tx sensor a promising practical acetone sensor. Therefore, V4C3Tx film based detectors have great potential to offer a room-temperature solution for the noninvasive detection of diabetes. We hope that our results will bring more attention to MXene products for use in gas sensing detection applications.
3.4 Discussion
Our results have demonstrated that V4C3Tx film shows high selectivity towards acetone (sub-ppm) over water vapor at room temperature, where V4C3Tx yields superior sensing performance to previous work.53 Yet it is natural to ask what causes the sensitivity of V4C3Tx film towards acetone?
To provide insights into the mechanisms that result in superior selectivity to acetone with respect to water vapor, we first evaluated the influence of the molecule itself. It is obvious that the molecular size of acetone is much bigger than that of a water molecule. Thus the contact performance of V4C3Tx films will be hindered (d1 > d2) due to the steric effect resulting from the bigger acetone molecule (a diagram is shown in Fig. 5a and b), yielding a bigger change in resistance (ΔR/R) than the smaller water molecule.
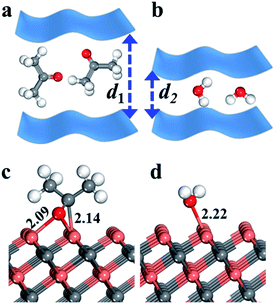 |
| Fig. 5 A schematic diagram of the sensor responses of V4C3Tx film to (a) acetone and (b) H2O molecules. The DFT optimized structures of the most favourably adsorbed (c) acetone and (d) H2O states on a V4C3 monolayer. | |
In addition, we also calculated the adsorption energy of acetone and H2O on a V4C3 monolayer with density functional theory (DFT) packages. In the DFT calculations, we first optimized many possible adsorption states and the most favourable optimized structures of acetone and H2O are shown in Fig. 5c and d. As shown in Fig. 5, for acetone adsorption, acetone adsorbs on the surface three-coordinated V (V3c) atoms via its middle C and end O atoms, forming V–C and V–O bonds, while water adsorbs on a surface V3c atom, yielding an O–V3c bond which is parallel with the surface V–C bond. The adsorption energy (ΔEads) per molecule (X) on the surface is defined by ΔEads = E[X/sur] − E[X] − E[sur], where E is the energy of the system based on DFT periodic calculations. Our DFT calculations show that the adsorption energies of acetone and H2O on the V4C3 monolayer are −1.11 and −1.97 eV, respectively, which are consistent with the order of V–O bond lengths (2.22 Å and 2.09 Å). The large difference in adsorption behaviours (0.86 eV) corresponds to the sensitivity of V4C3Tx film towards acetone. Similarly, an “assistive binding model” is proposed to explain the enhanced acetone sensing performance, where it is also attributed to the adsorption between target molecules and adsorbed Oδ− species.9 It is hoped that the DFT calculations presented here will shed light on predictions of new high-performance acetone sensors.
4. Conclusions
In summary, assisted by catalysts and the metallic fluxes of indispensable Al and Co elements, we have synthesized a high-quality V4AlC3 single crystal using a solid-state reaction. An emerging MXene phase, V4C3Tx, has been obtained via aluminum extraction from V4AlC3 using aqueous HF, as confirmed by XRD, XPS and EDX. We also found that the V4C3Tx sheets become a semiconductor after HF treatment. It is worth noting that a V4C3Tx based acetone sensor possesses a low working temperature of 25 °C, a low detection limit of 1 ppm and high selectivity toward acetone in a mixed gas of acetone and water vapor, making it possible to diagnose diabetes. In addition, we used DFT calculations to explore the mechanisms that result in the superior selectivity toward acetone with respect to water vapor, which is due to the molecule size and adsorption behaviors. The excellent acetone sensing performance of V4C3Tx makes it a promising material for application as a sensor for type I diabetes. The proposed mechanisms combining experimental results with theoretical study will hopefully shed light on the design and production of new high-performance acetone sensors.
Conflicts of interest
There are no conflicts to declare.
Acknowledgements
This work was supported by the National Natural Science Foundation of China (No. 21607029, 21777033), the Guangdong Natural Science Foundation (NO. 501190141), and the Science and Technology Planning Project of Guangdong Province (No. 2017B020216003). We also thank the Innovation Team Project of Guangdong Provincial Department of Education (No. 2017KCXTD012).
References
- B. Liu, W. Zhao, Q. Jiang, Z. Ao and T. An, Sustainable Mater. Technol., 2019, 21, e00103 CrossRef CAS.
- M. Wen, G. Li, H. Liu, J. Chen, T. An and H. Yamashita, Environ. Sci.: Nano, 2019, 6, 1006–1025 RSC.
- Y. Su, Z. Ao, Y. Ji, G. Li and T. An, Appl. Surf. Sci., 2018, 450, 484–491 CrossRef CAS.
- Y. Su, W. Li, G. Li, Z. Ao and T. An, Chin. J. Catal., 2019, 40, 664–672 CrossRef CAS.
- W. Liu, X. Zhou, L. Xu, S. Zhu, S. Yang, X. Chen, B. Dong, X. Bai, G. Lu and H. Song, Nanoscale, 2019, 11, 11496–11504 RSC.
- W. Liu, L. Xu, K. Sheng, X. Zhou, B. Dong, G. Lu and H. Song, NPG Asia Mater., 2018, 10, 293–308 CrossRef CAS.
- S.-J. Choi, I. Lee, B.-H. Jang, D.-Y. Youn, W.-H. Ryu, C. O. Park and I.-D. Kim, Anal. Chem., 2013, 85, 1792–1796 CrossRef CAS PubMed.
- S. Park, J. Alloys Compd., 2017, 696, 655–662 CrossRef CAS.
- S. Dey, S. Santra, P. K. Guha and S. K. Ray, IEEE Trans. Electron Devices, 2019, 66, 3568–3572 CAS.
- M. Naguib, O. Mashtalir, J. Carle, V. Presser, J. Lu, L. Hultman, Y. Gogotsi and M. W. Barsoum, ACS Nano, 2012, 6, 1322–1331 CrossRef CAS PubMed.
- Y. C. Dong, S. S. K. Mallineni, K. Maleski, H. Behlow, V. N. Mochalin, A. M. Rao, Y. Gogotsi and R. Podila, Nano Energy, 2018, 44, 103–110 CrossRef CAS.
- L. Ding, Y. Y. Wei, L. B. Li, T. Zhang, H. H. Wang, J. Xue, L. X. Ding, S. Q. Wang, J. Caro and Y. Gogotsi, Nat. Commun., 2018, 9, 155 CrossRef PubMed.
- B. Anasori, M. R. Lukatskaya and Y. Gogotsi, Nat. Rev. Mater., 2017, 2, 16098 CrossRef CAS.
- H. Kim, B. Anasori, Y. Gogotsi and H. N. Alshareef, Chem. Mater., 2017, 29, 6472–6479 CrossRef CAS.
- Z. F. Lin, D. Barbara, P. L. Taberna, K. L. Van Aken, B. Anasori, Y. Gogotsi and P. Simon, J. Power Sources, 2016, 326, 575–579 CrossRef CAS.
- M. Q. Zhao, C. E. Ren, Z. Ling, M. R. Lukatskaya, C. F. Zhang, K. L. Van Aken, M. W. Barsoum and Y. Gogotsi, Adv. Mater., 2015, 27, 339–345 CrossRef CAS PubMed.
- M. R. Lukatskaya, O. Mashtalir, C. E. Ren, Y. Dall'Agnese, P. Rozier, P. L. Taberna, M. Naguib, P. Simon, M. W. Barsoum and Y. Gogotsi, Science, 2013, 341, 1502–1505 CrossRef CAS PubMed.
- M. Ghidiu, M. R. Lukatskaya, M.-Q. Zhao, Y. Gogotsi and M. W. Barsoum, Nature, 2014, 516, 78–81 CrossRef CAS PubMed.
- C. Cedric, A. Mohamed, L. V. A. Katherine, K. Narendra, G. Luisa, M. N. S. Adriana, A. Babak, N. A. Husam and G. Yury, Adv. Electron. Mater., 2018, 4, 1700339 CrossRef.
- B. Anasori, M. R. Lukatskaya and Y. Gogotsi, Nat. Rev. Mater., 2017, 2, 16098 CrossRef CAS.
- Y. Xia, T. S. Mathis, M.-Q. Zhao, B. Anasori, A. Dang, Z. Zhou, H. Cho, Y. Gogotsi and S. Yang, Nature, 2018, 557, 409–412 CrossRef CAS PubMed.
- L. Ding, Y. Y. Wei, Y. J. Wang, H. B. Chen, J. Caro and H. H. Wang, Angew. Chem., Int. Ed., 2017, 56, 1825–1829 CrossRef CAS PubMed.
- F. Shahzad, M. Alhabeb, C. B. Hatter, B. Anasori, S. M. Hong, C. M. Koo and Y. Gogotsi, Science, 2016, 353, 1137–1140 CrossRef CAS PubMed.
- Y. Qian, H. W. Wei, J. D. Dong, Y. Z. Du, X. J. Fang, W. H. Zheng, Y. T. Sun and Z. X. Jiang, Ceram. Int., 2017, 43, 10757–10762 CrossRef CAS.
- P. Zhao, H. Jin, X. S. Lv, B. B. Huang, Y. D. Ma and Y. Dai, Phys. Chem. Chem. Phys., 2018, 20, 16551–16557 RSC.
- H. Lin, S. S. Gao, C. Dai, Y. Chen and J. L. Shi, J. Am. Chem. Soc., 2017, 139, 16235–16247 CrossRef CAS PubMed.
- R. Kötz and M. Carlen, Electrochim. Acta, 2000, 45, 2483–2498 CrossRef.
- M. D. Stoller, S. Park, Y. Zhu, J. An and R. S. Ruoff, Nano Lett., 2008, 8, 3498–3502 CrossRef CAS PubMed.
- M. Ghidiu, M. Naguib, C. Shi, O. Mashtalir, L. M. Pan, B. Zhang, J. Yang, Y. Gogotsi, S. J. L. Billinge and M. W. Barsoum, Chem. Commun., 2014, 50, 9517–9520 RSC.
- M. Naguib, V. N. Mochalin, M. W. Barsoum and Y. Gogotsi, Adv. Mater., 2014, 26, 992–1005 CrossRef CAS PubMed.
- J. Come, M. Naguib, P. Rozier, M. W. Barsoum, Y. Gogotsi, P.-L. Taberna, M. Morcrette and P. Simon, J. Electrochem. Soc., 2012, 159, A1368–A1373 CrossRef CAS.
- M. Naguib, J. Halim, J. Lu, K. M. Cook, L. Hultman, Y. Gogotsi and M. W. Barsoum, J. Am. Chem. Soc., 2013, 135, 15966–15969 CrossRef CAS PubMed.
- O. Mashtalir, M. R. Lukatskaya, M.-Q. Zhao, M. W. Barsoum and Y. Gogotsi, Adv. Mater., 2015, 27, 3501–3506 CrossRef CAS PubMed.
- O. Mashtalir, M. Naguib, V. N. Mochalin, Y. Dall'Agnese, M. Heon, M. W. Barsoum and Y. Gogotsi, Nat. Commun., 2013, 4, 1716 CrossRef PubMed.
- M. Naguib and Y. Gogotsi, Acc. Chem. Res., 2015, 48, 128–135 CrossRef CAS PubMed.
- B. Anasori, Y. Xie, M. Beidaghi, J. Lu, B. C. Hosler, L. Hultman, P. R. C. Kent, Y. Gogotsi and M. W. Barsoum, ACS Nano, 2015, 9, 9507–9516 CrossRef CAS PubMed.
- Y. Xie, Y. Dall'Agnese, M. Naguib, Y. Gogotsi, M. W. Barsoum, H. L. Zhuang and P. R. C. Kent, ACS Nano, 2014, 8, 9606–9615 CrossRef CAS PubMed.
- J. Hu, B. Xu, C. Ouyang, S. A. Yang and Y. Yao, J. Phys. Chem. C, 2014, 118, 24274–24281 CrossRef CAS.
- Y. Dall'Agnese, P.-L. Taberna, Y. Gogotsi and P. Simon, J. Phys. Chem. Lett., 2015, 6, 2305–2309 CrossRef PubMed.
- J. Zhou, S. Gao, Z. Guo and Z. Sun, Ceram. Int., 2017, 43, 11450–11454 CrossRef CAS.
- L. M. Azofra, N. Li, D. R. MacFarlane and C. Sun, Energy Environ. Sci., 2016, 9, 2545–2549 RSC.
- J. Etzkorn, M. Ade and H. Hillebrecht, Inorg. Chem., 2007, 46, 7646–7653 CrossRef CAS PubMed.
- X. Jinnan, W. Zhiqiang, C. Yuyan, L. Dujuan, C. Liang, Y. Xiaojing, L. Zhuang, M. Renzhi, S. Takayoshi and G. Fengxia, Angew. Chem., Int. Ed., 2016, 128, 14789–14794 CrossRef.
- J. Feng, X. Sun, C. Wu, L. Peng, C. Lin, S. Hu, J. Yang and Y. Xie, J. Am. Chem. Soc., 2011, 133, 17832–17838 CrossRef CAS PubMed.
- Y. Dall'Agnese, M. R. Lukatskaya, K. M. Cook, P. L. Taberna, Y. Gogotsi and P. Simon, Electrochem. Commun., 2014, 48, 118–122 CrossRef.
- M. J. Cao, F. Wang, L. Wang, W. L. Wu, W. J. Lv and J. F. Zhu, J. Electrochem. Soc., 2017, 164, A3933–A3942 CrossRef CAS.
- M. Khazaei, M. Arai, T. Sasaki, C.-Y. Chung, N. S. Venkataramanan, M. Estili, Y. Sakka and Y. Kawazoe, Adv. Funct. Mater., 2013, 23, 2185–2192 CrossRef CAS.
- K. Zhang, J. P. Zou and Q. Zhang, Nanotechnology, 2015, 26, 455501 CrossRef PubMed.
- M. Righettoni, A. Tricoli, S. Gass, A. Schmid, A. Amann and S. E. Pratsinis, Anal. Chim. Acta, 2012, 738, 69–75 CrossRef CAS PubMed.
- L. L. Deng, C. X. Zhao, Y. Ma, S. S. Chen and G. Xu, Anal. Methods, 2013, 5, 3709–3713 RSC.
- Q. Fengdong, Y. Yao, G. Rohiverth and Y. Minghui, Small, 2016, 12, 3128–3133 CrossRef PubMed.
- S. J. Kim, H.-J. Koh, C. E. Ren, O. Kwon, K. Maleski, S.-Y. Cho, B. Anasori, C.-K. Kim, Y.-K. Choi, J. Kim, Y. Gogotsi and H.-T. Jung, ACS Nano, 2018, 12, 986–993 CrossRef CAS PubMed.
- J. P. Zou, K. Zhang and Q. Zhang, IEEE Sens. J., 2016, 16, 8884–8889 CAS.
- A. Vomiero, S. Bianchi, E. Comini, G. Faglia, M. Ferroni and G. Sberveglieri, Cryst. Growth Des., 2007, 7, 2500–2504 CrossRef CAS.
- Z.-G. Wang, M.-R. Zhang, H.-D. Peng, Q.-M. Jiang, F. Hou, Z.-L. Zhu and G.-B. Pan, Chem. Lett., 2018, 47, 518–519 CrossRef CAS.
- D. Manish and A. Anil, Indian J. Pure Appl. Phys., 2018, 56, 367–372 Search PubMed.
- P. A. Murade, V. S. Sangawar, G. N. Chaudhari, V. D. Kapse and A. U. Bajpeyee, Curr. Appl. Phys., 2011, 11, 451–456 CrossRef.
- A. Teleki, S. E. Pratsinis, K. Kalyanasundaram and P. I. Gouma, Sens. Actuators, B, 2006, 119, 683–690 CrossRef CAS.
- Y. S. Lin, K. H. Lin, Y. M. Chang and J. A. Yeh, Surf. Sci., 2012, 606, L1–L4 CrossRef CAS.
- K. W. Kao, M. C. Hsu, Y. H. Chang, S. Gwo and J. A. Yeh, Sensors, 2012, 12, 7157–7168 CrossRef CAS PubMed.
- B. Bhowmik, A. Hazra, K. Dutta and P. Bhattacharyya, IEEE Trans. Device Mater. Reliab., 2014, 14, 961–967 CAS.
- S. T. Navale, Z. B. Yang, C. Liu, P. J. Cao, V. B. Patil, N. S. Ramgir, R. S. Mane and F. J. Stadler, Sens. Actuators, B, 2018, 255, 1701–1710 CrossRef CAS.
- X. Xinxin, C. Nan, Y. Yue, Z. Rongjun, W. Zhezhe, W. Zidong, Z. Tong and W. Yude, Phys. Status Solidi A, 2018, 215, 1800100 CrossRef.
- H. Fu, X. Wang, P. Wang, Z. Wang, H. Ren and C.-C. Wang, Dalton Trans., 2018, 47, 9014–9020 RSC.
- H. Zhang, Y. Cen, Y. Du and S. Ruan, Sensors, 2016, 16, 1876 CrossRef PubMed.
Footnote |
† Electronic supplementary information (ESI) available. See DOI: 10.1039/c9ra09069j |
|
This journal is © The Royal Society of Chemistry 2020 |
Click here to see how this site uses Cookies. View our privacy policy here.