DOI:
10.1039/C9RA05278J
(Paper)
RSC Adv., 2020,
10, 719-723
The synthesis of calcium arsenate@iron arsenate coating materials and their application for arsenic-containing wastewater treatment†
Received
10th July 2019
, Accepted 16th December 2019
First published on 2nd January 2020
Abstract
The current method of treating arsenic-containing wastewater is mainly to use a calcium method to synthesize stable calcium arsenate. It is easy to cause reverse dissolution by rain or other erosion, releasing arsenic into the natural world and polluting soil and groundwater. So, calcium arsenate is not an ideal material for removing and immobilizing arsenic. Iron arsenate (FeAsO4) is much better than calcium arsenate because of its stability and acid resistance. In this study, calcium arsenate@iron arsenate coating materials were synthesized. From the results of the XRD and SEM analyses, it was shown that calcium arsenate was coated by an iron arsenate shell which consisted of nanoparticles. The stability of the coating materials was determined using the Toxicity Characteristic Leaching Procedure (TCLP). The results showed that the concentrations of As for CaHAsO4 and Ca3(AsO4)2 were 744 mg L−1 and 302.2 mg L−1, respectively. Arsenic was not detected through the TCLP tests for CaHAsO4@FeAsO4 and Ca3(AsO4)2@FeAsO4 coating materials, and the best coating condition was confirmed to be an Fe/As molar ratio of 4
:
1, pH of 4, and temperature of 50 °C. The stability of the materials showed a significant improvement. The results indicated that calcium arsenate materials could be converted to coating materials by using ferric salts. The coating materials had excellent stability in an aqueous solution. Thus, the coating was suitable for the removal and immobilization of arsenic in industrial applications. This work provided a new way to treat arsenic-containing wastewater, which was simple and economical. This method has potential for use in the field of wastewater treatment containing arsenic.
1. Introduction
At present, the most common method for removing and immobilizing arsenic in industrial applications is the calcium arsenate (Ca3(AsO4)2) precipitation method.1–3 The arsenic-containing wastewater is treated by using calcium oxide or calcium hydroxide to form a calcium arsenate precipitate.4 However, calcium arsenate is not stable, it easily reacts with carbon dioxide in the air and cannot exist stably in nature for very long.5 It is easy for reverse dissolution to occur from rain or other erosion, releasing arsenic into the natural world and polluting soil and groundwater.6 So calcium arsenate is not an ideal material for removing and immobilizing arsenic. The calcium arsenate can be stabilized using a treatment to make it more stable overall and resist external erosion.7 This is the best way to retain the economic advantages of calcium arsenate and avoid secondary pollution. Using iron arsenate (FeAsO4) is much better than using calcium arsenate because of its stability and acid resistance.8–10 It is also used to remove and immobilize arsenic.11 However, the cost of the calcium salt to treat arsenic-containing wastewater is much lower than the iron salt. So most non-ferrous metal smelting companies choose the calcium arsenate method.12 However, iron arsenate has obvious advantages in terms of the efficiency of arsenic removal and the safety of arsenic.13 The solubility of iron arsenate (Ksp = 10−21 to 10−24) is about 1 million times smaller than that of calcium arsenate (Ksp = 10−18 to 10−21) in water.14,15 Calcium arsenate can react with carbon dioxide to produce calcium carbonate and water-soluble arsenic acid, resulting in the re-dissolution of arsenic.16 In this study, the advantages and disadvantages of these two arsenates are considered. The calcium arsenate is stabilized using treatment with ferric chloride. In this research, the iron arsenate is synthesized and then calcium arsenate is coated with the synthesized iron arsenate. The iron–arsenic ratio is studied to achieve the best stabilization of calcium arsenate. Calcium hydrogen arsenate (CaHAsO4) and calcium arsenate (Ca3(AsO4)2) are the two most common calcium arsenate phases. In this research, they are synthesized and coated with iron arsenate. The Fe/As ratio, reaction time and pH are studied for the stabilization of the calcium arsenate. Furthermore, the stability of the synthesized samples was measured using the Toxicity Characteristic Leaching Procedure (TCLP), and its application properties were also evaluated.17
2. Material and methods
2.1 Reagents
Leaching liquid of smelting dust was used as the As(V) source. The components of the dust and leaching liquid are shown in Table 1. Analytical reagent grade calcium hydroxide (Ca(OH)2) was used as the calcium source. Analytical reagent grade ferric chloride (FeCl3) was used as the iron source. Analytical reagent grade nitric acid (HNO3), and sodium hydroxide (NaOH) were used only for pH adjustment.
Table 1 Components of dust and leaching liquid
|
As |
K |
Zn |
Na |
Pb |
Dust (%) |
46.8 |
0.9 |
0.7 |
0.4 |
14.7 |
Leaching liquid (g L−1) |
20.1 |
0.5 |
0.1 |
0.2 |
— |
2.2 Calcium arsenate synthesis
A portion of arsenic-containing solution (800 mL) was taken and the pH value was adjusted to 5 using NaOH. Next, 0.75 mol of Ca(OH)2 was dissolved ultrasonically in 200 mL of deionized water. To obtain a Ca(OH)2 suspension, the pH value of the Ca(OH)2 solution was adjusted to 5 using HNO3. Then, the Ca(OH)2 suspension was poured into the arsenic-containing solution, and the pH was adjusted to 5 with stirring. The reaction was maintained at 50 °C for 24 h. Finally, the product was washed, with suction, and dried at 60 °C. The product was named sample 1.
The synthesis process of sample 2 was same as for sample 1 except the reaction pH value was 10.
Sample 1 or sample 2 was dispersed in deionized water. A certain amount of FeCl3 was added into the solution and then dissolved. The Fe/As molar ratios were 0.5
:
1, 1
:
1, 2
:
1, 3
:
1, 4
:
1, and 5
:
1. Then the pH of solution was adjusted to 4, 6, 7, 8, 10, or 12 using NaOH, and the reaction was left to occur for 12 h at room temperature, with stirring. Finally, the precipitations were washed with deionized water and dried at 60 °C. The products obtained were stabilized calcium arsenate@iron arsenate coated samples.
2.3 Characterization
The morphology of the synthesized products were observed using field emission scanning electron microscopy (FESEM, Hitachi S-4800, Japan). The X-ray diffraction (XRD) patterns were collected using a diffraction instrument with Cu Kα radiation (Bruker D8, 40 kV, 40 mA).
2.4 Stability evaluation of the products
Leaching tests were conducted, to examine the leach ability of the precipitates, according to the Toxicity Characterization Leaching Procedure (TCLP) tests (EPA, 1994).17 Glacial acetic acid (HAc, 5.7 mL) and NaOH solution (64.3 mL, 1 mol L−1) were sequentially added to 500 mL of distilled water and then diluted to 1 L to give a pH of 4.93 ± 0.05 to prepare the leaching agent.
The operating procedures of the leaching tests are briefly described here. The samples were each placed in PTFE bottles with extraction liquor at a liquid to solid (L/S) mass ratio of 20
:
1. The leaching tests were conducted for 16 ± 2 h for the HAc solution. The temperature was maintained at 25 °C during the leaching tests. After leaching, the supernatant was collected using 0.8 μm quantitative filter paper and the concentrations of arsenic and iron in the leaching solutions of the stability tests were determined using inductively coupled plasma optical emission spectroscopy (ICP-OES, PerkinElmer Optima 5300 DV, USA). The determination wavelength of As was 188.98 nm, and the detection limit of As was 0.01 mg L−1.
3. Results and discussion
3.1 Characterization of samples
The synthesized samples were identified by XRD. Fig. 1(a) shows that CaHAsO4 was synthesized successfully using the method of a previous report. As is known, the main peaks of scorodite (FeAsO4·2H2O) are located at approximately 30.1°, 27.8°, 16.9° and 10.9°, which can be indexed as the (221), (220), (101) and (020) lattice planes of scorodite (JCPDS no. 18-0288), respectively.18 The diffraction peak intensity was strong, and the CaHAsO4 had excellent crystallinity. Fig. 1(b) shows that Ca3(AsO4)2 was synthesized successfully by the method of the previous report. As is known, the main peaks of scorodite located at approximately 30.8° and 31.7°, can be indexed as the (020) and (021) lattice planes of Ca3(AsO4)2 (JCPDS no. 01-0933).19 Sample 1 and sample 2 were the two most common calcium arsenate phases in the arsenic-containing wastewater treatment.
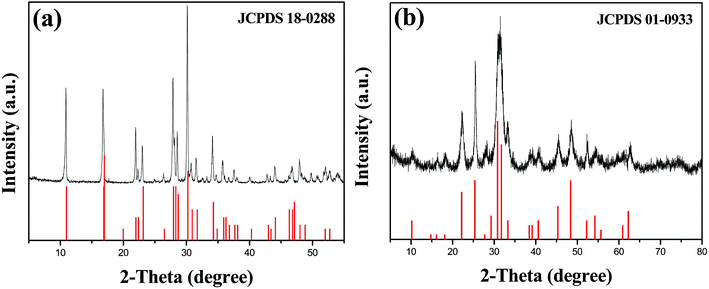 |
| Fig. 1 The XRD patterns of (a) sample 1, (b) sample 2. | |
3.2 Analysis of calcium arsenate@iron arsenate coated samples
3.2.1 Stability analysis of CaHAsO4@FeAsO4. Fig. 2 shows the concentrations of arsenic found by TCLP test after sample 1 was treated by FeCl3 to give it stability. Because of the design of the experiment, the products should be CaHAsO4@FeAsO4, and the synthesized CaHAsO4 was coated by FeAsO4. Fig. 2(a) shows the TCLP test results of the products which were reacted with different molar ratios of Fe/As at 25 °C. The concentration of arsenic was 744 mg L−1 without stability treatment. This indicated that CaHAsO4 was not stable in the solution. The concentrations of arsenic decreased when the Fe/As molar ratio was increased. The results indicated that the stability treatment by FeCl3 obviously increased the stability of CaHAsO4. The concentrations of arsenic were 1.075 mg L−1 and 0.982 mg L−1 when the Fe/As molar ratios were 4
:
1 and 5
:
1, respectively. These two results were below the standard value of TCLP (1.5 mg L−1). 1.075 mg L−1 and 0.982 mg L−1 of the concentration were little difference. The reason for this was because the CaHAsO4 could be completely coated when the Fe/As molar ratio was more than 4
:
1, and then the FeAsO4 shell would prevent the continued reaction between the internal CaHAsO4 and the FeCl3 solution. However, it was more economical when the Fe/As molar ratio was 4
:
1, so the best Fe/As molar ratio should be 4
:
1.
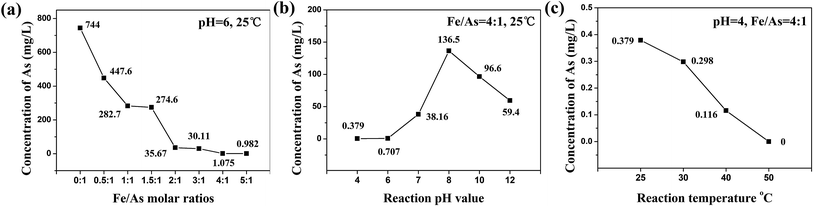 |
| Fig. 2 Concentrations of arsenic obtained using the TCLP test after sample 1 was treated with FeCl3. (a) Different Fe/As molar ratios, (b) different reaction pH values, (c) different reaction temperatures. | |
Fig. 2(b) shows the TCLP test results of products which were reacted at different pH values at 25 °C. The Fe/As molar ratio of the reaction was 4
:
1, and the reaction pH was 2. However, there was no precipitation because CaHAsO4 and FeCl3 were both dissolved completely when the pH was 2. The concentrations of arsenic obtained from the TCLP test increased when the pH value was 4 to 8. The reason for this was that CaHAsO4 could react with Fe3+ and the FeAsO4 shell formed when the solution was acidic. The concentrations of arsenic decreased when the pH value was 8 to 12. The reason for this was that Fe3+ would react with OH− and form Fe(OH)3 preferentially when the solution was alkaline, and so FeAsO4 could not form. So, the products were a CaHAsO4/Fe(OH)3 mixture. The solution of TCLP test was acetic acid solution (HAc, pH = 4.93 ± 0.05). The Fe(OH)3 reacted with H+ preferentially in the TCLP test, this caused the pH value of the TCLP solution to increase. The newly produced Fe3+ ions reacted with CaHAsO4 and formed FeAsO4, and this process made the materials more stable. The best pH of the stability treatment was 4, and the concentration of arsenic was 0.379 mg L−1.
Fig. 2(c) shows the TCLP test results of the products which were reacted at pH = 4 at different temperatures. The Fe/As molar ratio of the reaction was 4
:
1. The results indicated that the reaction rate increased as the temperature of the reaction increased. When the temperature was 50 °C, the CaHAsO4 could be coated perfectly by FeAsO4. Arsenic was not detected by TCLP test.
3.3 Morphology of samples
Sample 3 was CaHAsO4@FeAsO4 which was obtained by the FeCl3 stability treatment of sample 1 (Fe/As = 4
:
1, pH = 4, 50 °C). Sample 4 was Ca3(AsO4)2@FeAsO4 which was obtained by the FeCl3 stability treatment of sample 2 (Fe/As = 4
:
1, pH = 4, 50 °C).
As shown in Fig. 4, the SEM images show the morphology of samples 1, 2, 3 and 4. Fig. 4(a) and (b) show that the synthesized CaHAsO4 and Ca3(AsO4)2 were both layered structures. The thickness of the layers was about 30 nm. This structure corresponded to previous reports of calcium arsenate.1 The surface of the layers was smooth without particles. Sample 3 and sample 4 were the CaHAsO4 and Ca3(AsO4)2, respectively, which had been stability treated with FeCl3. As shown in Fig. 4(c) and (d), the layered structure remained, and the layer was coated by nanoparticles. According to the XRD and TCLP results, the particles were FeAsO4. The FeAsO4 nanoparticles could prevent the internal calcium arsenate contacting with the solution, so the dissolution of calcium arsenate stopped. Fig. 4(d) shows the schematic diagram of the stability treatment process. The CaHAsO4 or Ca3(AsO4)2 dissolved into the aqueous solution, released Ca2+ and AsO43− ions. The AsO43− ions reacted with the Fe3+ ions and formed FeAsO4 particles. These particles were deposited on the surface of calcium arsenate until the calcium arsenate was coated completely. Because the solubility of FeAsO4 was much less than the solubility of CaHAsO4 or Ca3(AsO4)2, the FeAsO4 was insoluble material and could not react with H+ and OH−. The FeAsO4 shell could protect the internal CaHAsO4 and Ca3(AsO4)2. They would not be corroded by the external solution. This structure was more stable after the stability treatment with FeCl3.
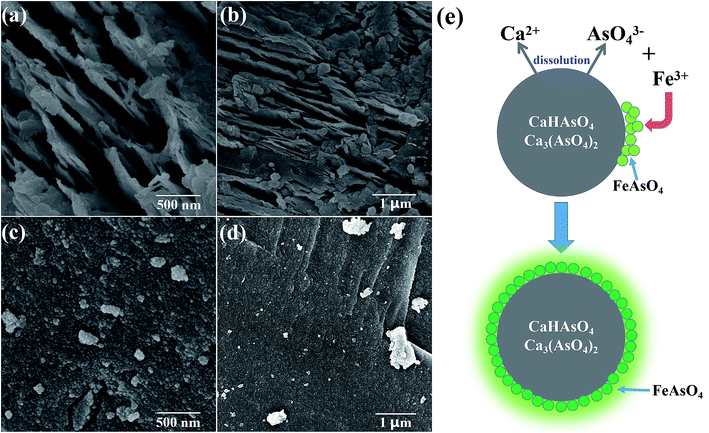 |
| Fig. 4 The SEM images of (a) sample 1, (b) sample 2, (c) sample 3, (d) sample 4; (e) schematic diagram of the stability treatment process. | |
The XRD pattern is shown in Fig. S1 (ESI).† The EDS analysis results of sample 1 and 3 are shown in Fig. S2 and S3 (ESI).†
4. Conclusion
The leaching liquid of smelting dust was used as the As(V) source. Layered CaHAsO4 and Ca3(AsO4)2 were synthesized. The CaHAsO4 and Ca3(AsO4)2 were stability treated with FeCl3 because the FeAsO4 formed has a lower solubility and higher stability. From the XRD and SEM analyses, it can be seen that the CaHAsO4@FeAsO4 and Ca3(AsO4)2@FeAsO4 were synthesized successfully. The layered calcium arsenate was coated by a FeAsO4 shell which consisted of nanoparticles. The stability of the coating materials was determined by the TCLP tests. The results showed that the concentrations of As for CaHAsO4 and Ca3(AsO4)2 were 744 mg L−1 and 302.2 mg L−1, respectively. The concentration of As for CaHAsO4@FeAsO4 and Ca3(AsO4)2@FeAsO4 were both 0 mg L−1, and the best coating conditions were confirmed as a Fe/As molar ratio of 4
:
1, a pH of 4, and a temperature of 50 °C. The stability of the materials showed a significant improvement. The results indicated that calcium arsenate materials could be converted to coating materials by the ferric salts. The coating materials had excellent stability in aqueous solution. It was suitable for the removal and immobilization of arsenic in industrial applications. This work provided a new way to treat the arsenic-containing wastewater, which was simple and economical. This method has potential applications in the field of arsenic-containing wastewater treatment.
Conflicts of interest
There are no conflicts to declare.
Acknowledgements
This work was supported by National Natural Science Foundation of China (21476268, and 21808170) and Shandong Provincial Natural Science Foundation (ZR201807260006).
References
- J. V. Bothe and P. W. Brown, Environ. Sci. Technol., 1999, 33, 3806–3811 CrossRef CAS.
- T. S. Choong, T. Chuah, Y. Robiah, F. G. Koay and I. Azni, Desalination, 2007, 217, 139–166 CrossRef CAS.
- G. Ungureanu, S. Santos, R. Boaventura and C. Botelho, J. Environ. Manag., 2015, 151, 326–342 CrossRef CAS PubMed.
- C. Sullivan, M. Tyrer, C. R. Cheeseman and N. J. Graham, Sci. Total Environ., 2010, 408, 1770–1778 CrossRef CAS PubMed.
- Y. Zhu, X. Zhang, Q. Xie, D. Wang and G. Cheng, Water Air Soil Pollut., 2006, 169, 221–238 CrossRef CAS.
- E. O. Kartinen Jr and C. J. Martin, Desalination, 1995, 103, 79–88 CrossRef.
- J. Camacho, H.-Y. Wee, T. A. Kramer and R. Autenrieth, J. Hazard Mater., 2009, 165, 599–603 CrossRef CAS PubMed.
- K. Leetmaa, F. Guo, L. Becze, M. A. Gomez and G. P. Demopoulos, J. Chem. Technol. Biotechnol., 2016, 91, 408–415 CrossRef CAS.
- S. Vega-Hernandez, J. Weijma and C. J. Buisman, J. Hazard Mater., 2019, 368, 221–227 CrossRef CAS PubMed.
- P.-c. Ke and Z.-h. Liu, Trans. Nonferrous Metals Soc. China, 2019, 29, 876–892 CrossRef CAS.
- Z. Yuan, D. Zhang, S. Wang, L. Xu, K. Wang, Y. Song, F. Xiao and Y. Jia, Hydrometallurgy, 2016, 164, 228–237 CrossRef CAS.
- L. Yao, X. Min, H. Xu, Y. Ke, Y. Liang and K. Yang, Int. J. Environ. Res. Public Health, 2018, 15, 1863 CrossRef PubMed.
- M. Edwards, J. Am. Water Work. Assoc., 1994, 86, 64–78 CrossRef CAS.
- E. Woolson, J. Axley and P. Kearney, Soil Sci. Soc. Am. J., 1973, 37, 254–259 CrossRef.
- J. Fei, J. Ma, J. Yang, Y. Liang, Y. Ke, L. Yao, Y. Li, D. Liu and X. Min, Environ. Geochem. Health, 2019, 1–12 Search PubMed.
- M. Stachowicz, T. Hiemstra and W. H. van Riemsdijk, J. Colloid Interface Sci., 2008, 320, 400–414 CrossRef CAS PubMed.
- Test Methods for Evaluating Solid Waste Physical/Chemical Methods, SW-846/Method 1311-Toxicity Characteristic Leaching Procedure, USEPA, 1992 Search PubMed.
- T. Nishimura and R. Robins, Mineral Processing and Extractive Metallurgy Review, 1998, 18, 283–308 CrossRef CAS.
- Y. Fan, Q. Weng, Y. Zhuo, S. Dong, P. Hu and D. Li, Materials, 2019, 12, 677 CrossRef CAS PubMed.
Footnote |
† Electronic supplementary information (ESI) available. See DOI: 10.1039/c9ra05278j |
|
This journal is © The Royal Society of Chemistry 2020 |
Click here to see how this site uses Cookies. View our privacy policy here.