DOI:
10.1039/C9MH00851A
(Communication)
Mater. Horiz., 2020,
7, 164-172
Multi-stimuli responsive chromism with tailorable mechanochromic sensitivity for versatile interactive sensing under ambient conditions†
Received
2nd June 2019
, Accepted 12th August 2019
First published on 13th August 2019
Abstract
Multi-stimuli responsive (MSR) chromic materials which can exhibit a color change when exposed to external stimuli demonstrate huge potential in developing new intelligent devices. However, they commonly require complicated synthesis processes that are not suitable for mass production. To facilitate the fabrication of MSR devices, for the first time, we propose a facile 3D integration strategy to rationally assemble various commercial chromic materials, light shielding layers, and a stretchable substrate into a set of MSR devices equipped with thermo-/photo-/mechanochromic characteristics with negligible cross-interferences. Notably, the mechanochromic sensitivity can be readily adjusted to multiple levels via facile pre-stretching methods. Moreover, two types of MSR units are integrated into an interactive electronic device, which exhibits thermo-/photo-/electrochromic responses, and two levels of mechanochromic responses with color changes at 100% and 200% strain, respectively. In addition, another highly sensitive MSR unit is applied to a wearable motion/environmental monitoring chromic device, which can detect finger bending within 30% strain, and monitor environmental stimuli (UV, temperature) with thermal mapping capability. A smartphone-based colorimetric analysis app was also developed for finger bending detection. Comprehensive quantitative characterization and finite element analysis are used to elucidate the performance and intrinsic mechanisms of these MSR responses.
New concepts
We pioneer to develop a 3D integration strategy to rationally assemble various commercial photo-/thermochromic materials, light shielding layers, and a stretchable substrate into a set of multi-stimuli responsive (MSR) materials, equipped with thermo-/photo-/mechanochromic characteristics. The design is optimized based on the physical characteristics of the chromic materials, structural assembly requirement, and color change styles. Notably, the mechanochromic effect is created by the micro-constructed crack opening/closing of light shielding layers, and the mechanochromic sensitivity can be readily adjusted to various levels via a facile pre-stretching method. The resulting system can achieve different color changing processes for different stimuli with negligible cross-interference. All the chromic color changes can be directly visualized by the naked eye under ambient environment. We also demonstrate that these new MSR materials can be smoothly applied in human motion/environmental condition monitoring and stretchable interactive electronics. The same conceptual design was also successfully demonstrated in thermochromic based temperature mapping. Overall, this work provides a new, versatile, and facile fabrication strategy for MSR materials without the need for complicated synthesis processes, and is thus highly suitable for mass production. It also offers guidance for a wider spectrum of applications for stretchable sensors/electronics, dynamic optoelectronics, and related areas.
|
1. Introduction
Stimuli-responsive chromic materials are becoming increasingly attractive owing to their unique capabilities to exhibit visual color change when exposed to external stimuli (e.g., mechanical strain, heat, light, voltage, etc.). As a result, they have shown great promise for developing new generation intelligent devices, such as smart windows,1–3 optical switches,4–6 displays,7–9 sensors,10,11 and so on.12–14 These chromic materials commonly undergo interconversions of isomeric molecular structures with associated reflective color changes when exposed to external stimuli.13,15 These visual signals can be directly discerned with the naked eye, providing a straightforward sensing/mapping approach for people to perceive the change of materials or environmental conditions. Also, a variety of interactive photonics and electronics are exploited to probe various stimuli, like mechanical strain,16–21 temperature,22,23 UV radiation,24,25 or human body/finger motion.26,27 However, very few devices possess multi-stimuli responsive (MSR) capabilities in one single system. Lab-scale synthetic MSR chromic materials are widely considered as promising colorimetric sensory units28–31 for these applications. However, they commonly require highly demanding and complicated synthesis processes that are not suitable for mass production. As colorimetric sensors, they also usually present similar or the same color change styles for different stimuli, which makes it difficult to distinguish different stimuli sources.28,32–35 Due to the limitation of the reaction chemistry, it is usually very difficult to change these color change styles for better stimuli sensing performance. Since there are various levels of stretching strain in different applications of interactive/stretchable electronics,2,21,29,36,37 to achieve better monitoring/sensing capabilities for different devices, it will be ideal if the sensitivities of mechanochromic performance can be tunable. For example, it usually requires a mechanochromic sensitivity within 30% strain to sense finger bending motion.37 While it will require a lower mechanochromic sensitivity for some highly stretchable electronics up to 100% strain or even 300% strain.36 Thus, it is crucial to develop an alternative facile approach imparting the MSR devices to exhibit different color changing styles to each individual stimulus and possess tunable mechanochromic sensitivities.
In this research, we fabricated a set of intriguing MSR chromic devices via a newly developed three-dimensional (3D) integration approach. Various commercial chromic materials and/or light shielding layers were assembled through facile vertical layer stacking and/or planar assembly methods. The resulting prototypes can clearly demonstrate thermo-/photochromic responses originating from the incorporated chromic materials. The mechanochromic effect, which is inspired by the skin color change mechanism of Cephalopods,2 is attributed to the crack opening of the light shielding layers as the prototype stretched. All these MSR performances exhibit different color changing styles with negligible cross-interferences. Notably, the mechanochromic response can be further modulated into three levels of strain sensitivity (denoted as low, normal, and high) by distinct “pre-stretching” methods. The system can clearly demonstrate the capabilities for sensing different levels of stretching strain from 30%, to 100% to 300% range. Such versatile and tunable mechanochromic performance has not been reported in previous references. In the first application, two MSR units with normal and low mechanochromic sensitivity are integrated into highly stretchable (up to 300% strain) interactive electronics equipped with an electrochromic ability to indicate bias direction. Besides the thermo-/photochromic responses, the two MSR units can manifest evident color change to red as stretched at 100% and 200% strain, respectively, demonstrating an enhanced strain coding accuracy. In the second application, an MSR unit with high mechanochromic sensitivity showing color change within 30% strain is applied to a finger motion/environment monitoring device containing a thermal mapping unit. A smartphone-based colorimetric analysis app for finger bending degree is also demonstrated. Thus, this 3D integration approach leads to a series of versatile MSR devices, for the first time, by only using commercial materials without the need for extra demanding synthesis requirements. Furthermore, these chromism-based color changes can be directly captured by the naked eye under ambient environment without the need for an extra observing device/environment which is necessary for fluorescence-based materials.26 Comprehensive quantitative characterization and the Finite Element Analysis (FEA) are used to evaluate the MSR performance and elucidate the intrinsic mechanisms of these responses.
2. Results
2.1 The general design strategy for the MSR units
The general design strategy for the MSR units is shown in Fig. 1a. The thermochromic and photochromic effects can be achieved simultaneously by homogenously mixing these powders with appropriate color changing style selection and proper mass ratio. Similarly, a colorimetric thermal mapping unit can be prepared by suitably mixing different thermochromic pigments. The introduction of mechanochromic characteristic can be realized by fabricating a rigid thermochromic/photochromic film atop a light shielding layer, which is tightly attached atop a stretchable substrate with a different color. When the MSR unit is stretched, distributed cracks occur and opened on the top rigid layers, which act as “shutters” to adjust the exposure of the underlying soft substrate, imparting the system with strain-dependent color variations (also see Fig. S1–S3, ESI†).
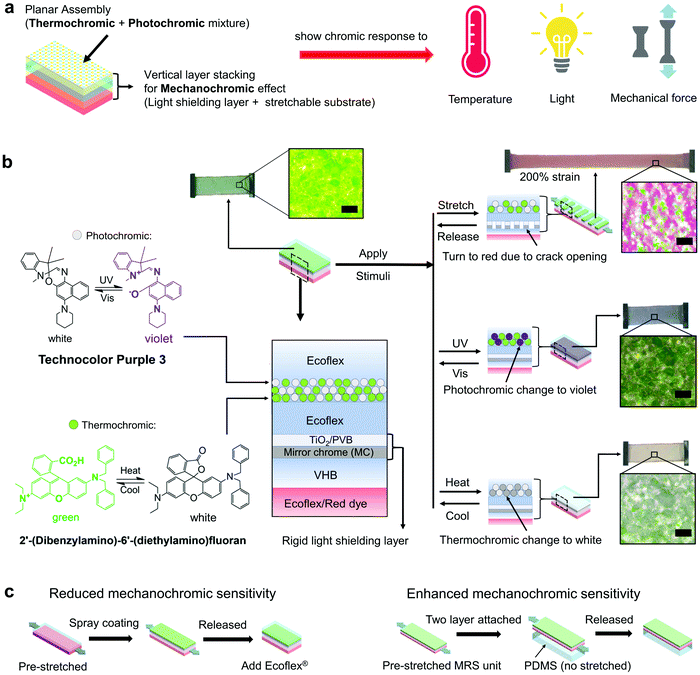 |
| Fig. 1 (a) General strategies for preparing the MSR device via the 3D integration approach. (b) Schematic showing the preparation of the MSR chromic units (including the microscopic and digital images of the top surfaces) (scale bar = 50 μm). (c) Illustration of the mechanochromic sensitivity modulation for the MSR units. | |
In the real MSR unit, we selected a photochromic leuco pigment containing Technocolor Purple 3, which shows a white color under visible light but changes to dark violet when exposed to UV at 365 nm. A minimum UV output power intensity (OPI) of 17 μW cm−2 is required to generate a visible photochromic effect, and the standard OPI of the UV source used in this work is 536 μW cm−2 unless otherwise mentioned (see Fig. 1b and Fig. S4, ESI†). To impart a thermochromic response, a leuco pigment containing 2′-(dibenzylamino)-6′-(diethylamino) fluoran is chosen, which displays a green color at temperatures (T) < 33 °C and switches to white at T > 33 °C (Fig. 1b and Fig. S4, ESI†). Thus, as evident in the optical microscopic (OM) and digital images of the real MSR unit (see Fig. 1b), the binary mixture with a mass ratio of 1
:
1 demonstrates green color at T < 33 °C (all the tests labeled as T < 33 °C were conducted at 25 °C unless otherwise specified) and under visible light (this environment denoted as (Vis, <33 °C)). When the MSR unit is heated above 33 °C under visible light (denoted as (Vis, >33 °C)), the sample changes to white. When exposed to UV at T < 33 °C and at T > 33 °C (denoted as (UV, <33 °C) and (UV, >33 °C), respectively), the photochromic effect induces a mixture of color changes to violet and pink violet (combined with thermochromic effect), respectively. It should be noted that the color exhibited from the digital images of the real MSR unit might look different from that under OM. The reason is that the macro-scale color is the result of the combination of all different color units in micro-scale (<0.1 mm), which cannot be perceived by the naked eye.
To achieve the mechanochromic effect, a silicone rubber (Ecoflex®)/red dye and a transparent double-sided adhesive (3M™ VHB™ tape) bilayer structure are used as the stretchable substrate. A light shielding layer (consisting of an 890 nm thick polyvinyl butyral (PVB)/TiO2 composite and a 40 nm thick metal-like mirror chrome (MC) layer; see Fig. 1b, Fig. S4 and S5, ESI†) was then sprayed atop the substrate. Subsequently, a layer of thermochromic/photochromic homogenous binary mixture was sprayed atop the light shielding layer. This rigid chromic pigment layer was then encapsulated by a layer of Ecoflex®. The unit was then stretched to a 300% pre-strain prior to release to generate sufficient distributed cracks for the mechanochromic effect. Note that the thickness of the thermo-/photochromic pigment mixture is carefully tuned to be ca. 3.3 μm, so that it is sufficient to block the visibility of the underlying light shielding layer in the released state and thus can achieve the optimal MSR performance. Upon re-stretching over the threshold strain value, the device instantaneously switches from green to red color under the (Vis, <33 °C) condition, owing to the distributed crack opening of the rigid layer (see Fig. 1b using 200% strain as a sample). Notably, the mechanochromic response can be further modulated into enhanced or reduced strain sensitivity levels by two different “pre-stretching” methods shown in Fig. 1c. To reduce the sensitivity, the Ecoflex®/red and VHB substrate are pre-stretched to the predetermined strain (such as 150% strain) followed by adding the light shielding, chromic, and Ecoflex® layers. To enhance the sensitivity, the as-prepared MSR unit is pre-stretched to a predetermined strain (such as 29% strain) followed by attaching to the PDMS substrate and released.
2.2 The MSR performance of normal strain sensitivity unit (NSSU)
The macro-scale digital photos of the real MSR unit performance are demonstrated in Fig. 2a. Under the (Vis, <33 °C) condition, the unit requires ca. 100% strain to create sufficient crack opening width to change from green into red. And this unit is denoted as the normal strain sensitivity unit (NSSU). To determine the correlation between the applied deformation and the color change, this unique mechanochromism was further analyzed through a 3D Finite Element (FE) model using the commercial software ABAQUS (see Fig. 2a). In the FE model, the thin rigid light shielding layer was tied on the VHB substrate by enforcing the displacement continuity at the interface. Modeling details are given in the ESI† and Fig. S1. The key to capturing the mechanochromic effect is to introduce distributed cracks that not only penetrate through the thin rigid layer but also evolve into the VHB substrate. Fig. 2b shows the computed total crack width as a function of the strain on a 600 μm long NSSU, which is correlated well with the experimental measurement.
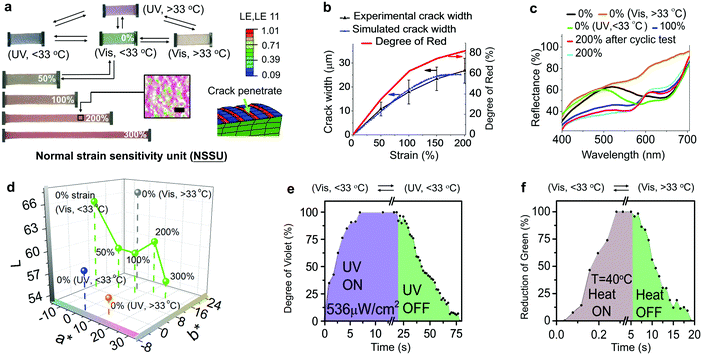 |
| Fig. 2 (a) MSR performance of the NSSU and the 3D FE simulation for the distributed cracks (scale bar = 50 μm). (b) Experimental and simulated crack width and degree of red (DR) as a function of the applied strain for NSSU under (Vis, <33 °C). (c) Reflectance spectra of the MSR performance for the NSSU (all unlabeled conditions are under (Vis, <33 °C) and the samples have been stretched/released for over 1000 times between 0% and 100% strain in the cyclic test). (d) 3D La*b* coordinates for MSR performance of the NSSU. (e) Photochromic responsive dynamic of the NSSU. (f) Thermochromic responsive dynamic of the NSSU. | |
In Fig. 2c, the reflectance spectra (see Fig. S6(a), for testing set-up, ESI†) show that the peak originally located at 520 nm under (Vis, <33 °C) at 0% strain and shifts to 496 nm as exposed to UV under (UV, <33 °C). And the peak at 614 nm corresponding to the red color of the substrate becomes increasingly intensive as stretched under (Vis, <33 °C). The spectra also indicate that the mechanochromic response has an excellent reversibility after the cyclic test, because the rigid layers are well encapsulated and protected by Ecoflex®. When the unit was heated to (Vis, >33 °C), the 520 nm peak disappeared without other evident peaks shown, indicating a white color. The corresponding absorbance spectra converted from the above reflectance spectra based on the Kubelka–Munk functions are shown in Fig. S6(b) (ESI†). The MSR behaviors were further quantitatively characterized by the CIE La*b* color coordinate. CIE La*b* is a color space describing all the visible colors by a combination of L (lightness, value ranging from 0 to 100), a* channel (indicating the level of green to red, ranging from −128 to 127) and b* channel (indicating the level of blue to yellow, ranging from −128 to 127) (see Fig. S7 for definition diagram, ESI†). Thus, a higher a* value indicates a higher red extent. As shown in Fig. 2d, the a* value increases from −13.3 at 0% strain to 9 at 100% strain under (Vis, <33 °C). For three other conditions under UV and/or heating, similar mechanochromic effects can all be visualized but with different initial colors at 0% strain (see Fig. S8 for the La*b* color coordinates change and Fig. S9 for digital photos, ESI†). The degree of red (DR) (see ESI† for definition) of MSR is also used to quantitatively characterize the extent of the mechanochromic effect. And it increases proportionally to the applied strain and crack width (see Fig. 2b and Fig. S10, ESI†) and reaches 62.5% at 100% strain under (Vis, <33 °C), matching the clear red present at this strain. The dynamic of photochromic response was quantitatively analyzed based on the degree of violet (DV) (see ESI† for definition) (see Fig. 2e). When the unit is activated from (Vis, <33 °C) and exposed to a UV OPI of 536 μW cm−2, it takes 6.9 s to reach the maximum DV (DVmax) and 55 s to recover back to green. Note that the time to reach DVmax increases with a decreased OPI (see Table S1, ESI†). Similarly, the thermochromic dynamic is characterized by the reduction of green (RG) (see ESI† for definition) in Fig. 2f. When the unit is 25 °C and contacted to a heat source of 40 °C, the time for reaching the maximum RG is rather rapid (t ∼ 0.27 s), and the recovery time is ca. 15 s. Both thermochromic and photochromic characteristics demonstrate a good reversibility as evident in the cyclic tests (see Fig. S11, ESI†).
2.3 Applying the NSSU and low strain sensitivity unit (LSSU) in an interactive electronic device
The mechanochromic sensitivity of the MSR unit can be reduced by simply applying a pre-stretch of 150% strain on the substrate before spray coating the rigid light shielding layers (see Fig. 3a). Therefore, the threshold tensile strain to achieve an evident red color becomes ca. 200% strain, due to the reduced crack opening response. This device is denoted as a low stain sensitivity unit (LSSU). The characterization of the LSSU, including the reflectance spectra, crack width and DR evolution, OM images, La*b* coordinates and digital photos for MSR behaviors are shown in Fig. S11–S16, ESI.† Based on the different activation strains of NSSU and LSSU, we integrated both units along with a stretchable conductor and LED set into a stretchable electronic device with an electrochromic unit (see Fig. 3b for the device design layout). The LSSU and NSSU are used to monitor the stretching strain level of the stretchable conductor. In our design, the LED lamp is connected in parallel with an electrochromic cell made by polymer gel electrolyte atop two separated PEDOT:PSS electrodes. The electrochromic cell displays blue color under a negative bias <−1.8 V38,39 (see Fig. S17–S19 for the design layout and characterizations for the electrochromic unit, ESI†). Thus, when the LED lamp is on (need a bias >2 V with a correct direction), the “check mark” side exhibits a blue color. While the LED lamp is off with an opposite bias direction larger than 1.8 V, the “cross mark” side exhibits blue color, indicating a wrong bias direction. Additionally, the LED lamp is connected to two highly stretchable conductors on both sides (R ≈ 30 Ω, stretchability >300% strain), which are fabricated from a conductive thread with spun stainless steel fiber and VHB™ tapes (see Fig. S20 and S21 for fabrication details, ESI†). The resulting device demonstrates instantaneous and reversible MSR properties as well as high stretchability (see Fig. 3c, Movies S1 and S2, ESI†). The NSSU and LSSU are used as the strain level indicator with additional chromic responses to heat and UV light. Notably, they can collectively exhibit impressive mechanochromic response covering a large stretching strain range from 50% to 300%. For example, when stretched to 110% strain, the NSSU (right side) changes into evident red from green, while the LSSU (left side) maintains green color. If further stretched to 250% strain, the LSSU finally switches to red. Also, the electrochromic device is used as a bias/current direction indicator.
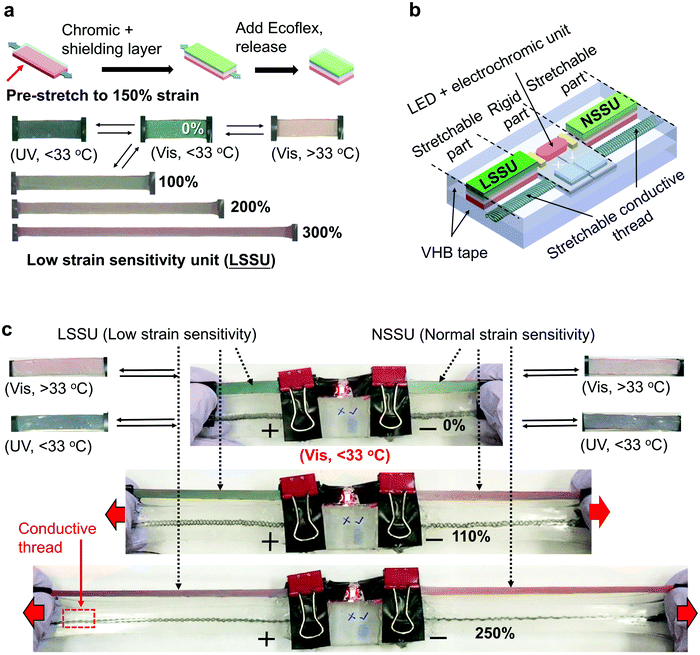 |
| Fig. 3 (a) Preparation and MSR performance of the LSSU. (b) Schematic design of the interactive electronics and (c) its MSR performance. | |
2.4 The MSR performance of the high strain sensitivity unit (HSSU)
To obtain a higher mechanochromic sensitivity, the NSSU is pre-stretched to 29% strain (with green color maintained) followed by adhere to the PDMS substrate to lock the pre-strain level (see Fig. 4a). The resulting sample demonstrates a curved shape which can be re-flattened by clamping or attaching it onto a rigid substrate (see Fig. 4b). The curvature of the sample results from the mismatch of the mechanical properties of the NSSU and PDMS, which is also analyzed through a 3D FE model (see Fig. 4b, Fig. S2 and ESI† for model details including the predefined stress field and interaction between the NSSU and PDMS). Since the NSSU is pre-stretched to 29%, the stored elastic energy is redistributed between the NSSU and PDMS, resulting in different bending curvatures to keep the material interface bonded together. The resulting new MSR unit, denoted as the high strain sensitivity unit (HSSU), exhibits a much more sensitive mechanochromic performance with an evident color change around 20% strain (see Fig. 4c and Fig. S22 and S23 reflectance spectra, La*b* coordinate, ESI†). The simulated crack opening response of the HSSU is correlated well with the experiment, as shown in Fig. 4d (also see Fig. S24, ESI†). Fig. 4e shows the strain evolution of a* values in La*b* of the HSSU, NSSU and LSSU under the (Vis, <33 °C) condition, indicating the different mechanochromic sensitivity. The HSSU response shows the sharpest slope and highest strain sensitivity as it reaches the a* value of 11 at 50% strain. However, to reach the same value, NSSU and LSSU require ca. 100% and 250% strains, respectively (also see Fig. S25 for the evolution of a* value with crack width, ESI†).
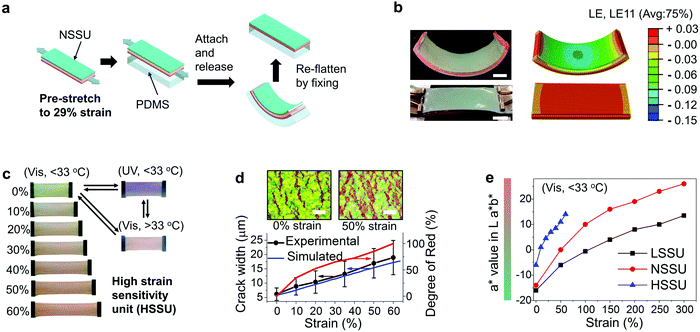 |
| Fig. 4 (a) Schematic of the preparation of the HSSU. (b) Digital image and 3D FE model of the bent and re-flattened HSSU. (c) MSR performance of the HSSU. (d) Simulated and experimental results of the strain-dependent crack width of HSSU and the strain evolution of the degree of red of the HSSU under (Vis, <33 °C) (inset: optical microscopic images of the distributed cracks at 0% and 50% strain, scale bar = 50 μm). (e) Comparison of the strain evolution of the a* value in La*b* coordinates for the HSSU, NSSU and LSSU, indicating the different mechanochromic sensitivities. | |
2.5 HSSU's application in a wearable motion/environmental monitoring device
The HSSU is further integrated into a wearable motion/environmental monitoring (WMEM) device to measure the finger bending motion and examine circumambient conditions. The deformation is localized on the joint when a finger is bent (a dummy finger is used in this work). To maximize the colorimetric sensitivity of HSSU, the middle part of HSSU is placed right atop the dorsal side (back side) of the middle finger joint without adhesion, while the two ends of HSSU are bonded to the non-bendable/stretchable finger segments adjacent to the joint. As a result, evident crack opening and color change are shown in the middle free part while the two-end parts exhibit negligible changes (see Fig. 5a), maximizing the visibility and sensitivity of the mechanochromic coding. In addition, the WMEM also includes a thermal mapping unit containing three types of thermochromic pigments with different critical transition temperatures attached to the finger's palmar side (front side). This unit can demonstrate different colors in four different temperature ranges (blue at T < 15 °C, green at 15 °C < T < 33 °C, red at 33 °C < T < 65 °C, and white T > 65 °C, see Fig. 5b, Fig. S26, S27 for pigment details and Movie S3, ESI†). It also demonstrates an accurate mapping capability that the thermochromic contour can perfectly match the shape of a target object. Note that the contour measured by the thermal camera exhibits significant shape distortion due to the circumferentially diffused thermal radiations (see Fig. 5b and Fig. S28, ESI†).
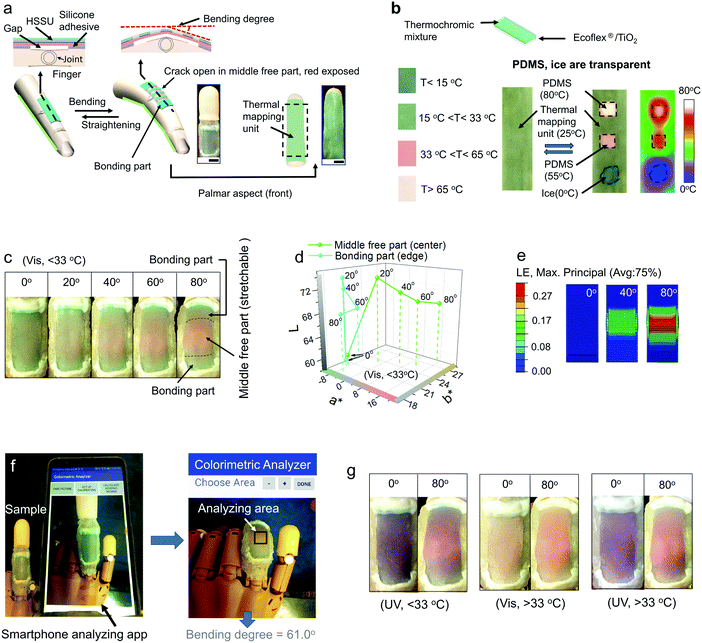 |
| Fig. 5 (a) Schematic and images of the wearable motion/environmental monitoring device (WMEM) (scale bar = 1 cm) containing a HSSU on a finger's dorsal side (back side) and the thermal mapping unit on a finger's palmar side (front side) (both digital photos for the HSSU and thermal mapping unit were taken under condition (Vis, 15 °C < T < 33 °C) with the finger straightened.) (b) Structure and performance of the thermal mapping unit. (c) Mechanochromic responses of the HSSU on WMEM bending from 0° to 80° under (Vis, <33 °C). (d) La*b* coordinates of the HSSU on WMEM as a function of bending degree under (Vis, <33 °C). (e) 3D FE modeling of the strain distribution of the HSSU on WMEM under 0°, 40° and 80° of bending. (f) Smartphone-based colorimetric analysis for monitoring finger bending behavior. (g) Mechanochromic responses of the HSSU on WMEM under (UV, <33 °C), (Vis, >33 °C), and (UV, >33 °C). | |
The mechanochromic response of the HSSU on WMEM to monitor finger bending under (Vis, <33 °C) is shown in Fig. 5c. As the finger is bent to 40°, the middle free part of HSSU becomes red and distinguishable from the ends that remain green, and the middle part reaches the maximum red intensity when the finger is bent to ca. 80° (see Movie S4, ESI†). The corresponding variation in the La*b* coordinates is shown in Fig. 5d, and the a* value of the middle part changes from −7 at 0° to 17 at 80° while the a* value of the bonding part remains virtually unchanged. Fig. 5e shows the predicted strain evolution of WMEM using a full 3D FE model (see Fig. S3 and ESI† for model detail), and the results are correlated well with the experimental mechanochromic color distribution in the HSSU as bent. We further introduced a smartphone-based colorimetric analysis app for monitoring the finger bending behavior. The color change of the middle free part of HSSU as bent can be captured by a smartphone app, and then converted into the corresponding bending degree displayed on the screen (see Fig. 5f and Movie S5, ESI†). The evolution of the simulated strain levels and the experimental DR on the middle part of the HSSU on WMEM with different bending degrees are shown in Fig. S29 (ESI†). They both increase proportionally to the bending degree, and a maximum strain of 26.9% and DR of 100% are observed when the finger is bent to 80°. Similar mechanochromic responses under the (UV, <33 °C), (Vis, >33 °C) and (UV, >33 °C) conditions are also observed (see Fig. 5g and Fig. S30–S33 for the La*b* coordinates and digital photos, ESI†).
3. Conclusion
In summary, we invented a facile 3D integration method to rationally assemble various commercial chromic materials, light shielding layers, and stretchable substrate into a set of reversible MSR units equipped with thermo-/photo-/mechanochromic responses. The designs are optimized at the discretion of the physical characteristics of materials (powder or polymer film), structural assembling requirement (stacking or planar deposition), and chromic color change style to minimize the cross-interference. Notably, the mechanochromic sensitivity based on crack opening mechanism can be readily customized by altering the pre-stretching methods. Thus, we fabricated three MSR units identified as HSSU, NSSU, and LSSU, which demonstrate evident mechanochromic color change at 20%, 100%, and 200% strains, respectively. Thus, the NSSU, LSSU, a smart electrochromic unit and stretchable conductor constitute an interactive electronic device, which exhibits thermochromic and photochromic characteristics, electrochromic response indicating bias direction and two levels of mechanochromic effects. And the HSSU can be integrated into a wearable device sensing finger bending within 30% strain and monitoring environmental stimuli. Comprehensive quantitative characterization was carried out to evaluate the MSR performances and FE simulations are applied to elucidate intrinsic mechanisms of the mechanochromic effects, the preparation process of HSSU, and the bending deformation of HSSU on WMMD. This proposed strategy also demonstrates high design flexibility and wide applicability: (1) color changing styles for various chromic responses can be readily customized; holding huge advantages as compared to the traditional synthesis method which is limited by the reaction chemistry. (2) All materials are commercially available without the need of extra synthesis and thus enabling the applicability for large-scale production. (3) All the chromic color changes can be directly visualized by the naked eye under ambient environment. (4) This 3D integration strategy can also be useful for obtaining new functionalities in the other optoelectronics and sensors. For example, the electrochromic bias indicators for the LED set and the thermochromic based thermal mapping unit are shown in this paper. Thus, this 3D integration strategy demonstrates great potential for mass production of future versatile interactive sensory devices, which have immediate and reversible color change feedback to human motion and/or external stimuli.
Conflicts of interest
There are no conflicts to declare.
Acknowledgements
We acknowledge the polyvinyl butyral samples provided by Kuraray. S. Z. acknowledges the GE Graduate Fellowship for Innovation for the 2015 calendar year and A. S. acknowledges the GAANN Fellowship (No. P200A150330).
References
- P. Kim, Y. Hu, J. Alvarenga, M. Kolle, Z. Suo and J. Aizenberg, Adv. Opt. Mater., 2013, 1, 381–388 CrossRef.
- S. Zeng, D. Zhang, W. Huang, Z. Wang, S. G. Freire, X. Yu, A. T. Smith, E. Y. Huang, H. Nguon and L. Sun, Nat. Commun., 2016, 7, 11802 CrossRef CAS.
- E. Lee, M. Zhang, Y. Cho, Y. Cui, J. Van der Spiegel, N. Engheta and S. Yang, Adv. Mater., 2014, 26, 4127–4133 CrossRef CAS.
- S. G. Lee, D. Y. Lee, H. S. Lim, D. H. Lee, S. Lee and K. Cho, Adv. Mater., 2010, 22, 5013–5017 CrossRef CAS.
- D. Ge, E. Lee, L. Yang, Y. Cho, M. Li, D. S. Gianola and S. Yang, Adv. Mater., 2015, 27, 2489–2495 CrossRef CAS.
- K. Bange and T. Gambke, Adv. Mater., 1990, 2, 10–16 CrossRef CAS.
- S. Zeng, R. Li, S. G. Freire, V. M. M. Garbellotto, E. Y. Huang, A. T. Smith, C. Hu, W. R. T. Tait, Z. Bian, G. Zheng, D. Zhang and L. Sun, Adv. Mater., 2017, 29, 1700828 CrossRef.
- K. Itaya, K. Shibayama, H. Akahoshi and S. Toshima, J. Appl. Phys., 1982, 53, 804–805 CrossRef CAS.
- P. Andersson, R. Forchheimer, P. Tehrani and M. Berggren, Adv. Funct. Mater., 2007, 17, 3074–3082 CrossRef CAS.
- L. Wang, K. Wang, B. Zou, K. Ye, H. Zhang and Y. Wang, Adv. Mater., 2015, 27, 2918–2922 CrossRef CAS.
- J. Yoon, S. K. Chae and J.-M. Kim, J. Am. Chem. Soc., 2007, 129, 3038–3039 CrossRef CAS.
- C. Niu, Y. You, L. Zhao, D. He, N. Na and J. Ouyang, Chem. – Eur. J., 2015, 21, 13983–13990 CrossRef CAS.
- C. Reus and T. Baumgartner, Dalton Trans., 2016, 45, 1850–1855 RSC.
- C. M. Rodd and R. Agarwal, Nano Lett., 2011, 11, 3460–3467 CrossRef CAS.
- K. Motoyama, H. Li, T. Koike, M. Hatakeyama, S. Yokojima, S. Nakamura and M. Akita, Dalton Trans., 2011, 40, 10643–10657 RSC.
- C. Wang, D. Hwang, Z. Yu, K. Takei, J. Park, T. Chen, B. Ma and A. Javey, Nat. Mater., 2013, 12, 899 CrossRef CAS PubMed.
- G. Kim, S. Cho, K. Chang, W. S. Kim, H. Kang, S.-P. Ryu, J. Myoung, J. Park, C. Park and W. Shim, Adv. Mater., 2017, 29, 1606120 CrossRef.
- C. Wu, S. Zeng, Z. Wang, F. Wang, H. Zhou, J. Zhang, Z. Ci and L. Sun, Adv. Funct. Mater., 2018, 28, 1803168 CrossRef.
- Y. Jiang, S. Zeng, Y. Yao, S. Xu, Q. Dong, P. Chen, Z. Wang, M. Zhang, M. Zhu, G. Xu, H. Zeng and L. Sun, Polymers, 2019, 11, 103 CrossRef.
- W.-H. Yeo, Y.-S. Kim, J. Lee, A. Ameen, L. Shi, M. Li, S. Wang, R. Ma, S. H. Jin, Z. Kang, Y. Huang and J. A. Rogers, Adv. Mater., 2013, 25, 2773–2778 CrossRef CAS.
- X. Wang, L. Dong, H. Zhang, R. Yu, C. Pan and Z. L. Wang, Adv. Sci., 2015, 2, 1500169 CrossRef.
- T. Q. Trung, S. Ramasundaram, B.-U. Hwang and N.-E. Lee, Adv. Mater., 2016, 28, 502–509 CrossRef CAS.
- S. Wang, X. Liu, M. Yang, Y. Zhang, K. Xiang and R. Tang, Packag. Technol. Sci., 2015, 28, 839–867 CrossRef CAS.
- H. Araki, J. Kim, S. Zhang, A. Banks, K. E. Crawford, X. Sheng, P. Gutruf, Y. Shi, R. M. Pielak and J. A. Rogers, Adv. Funct. Mater., 2017, 27, 1604465 CrossRef.
- E. Orgiu and P. Samorì, Adv. Mater., 2014, 26, 1827–1845 CrossRef CAS.
- T. Bu, T. Xiao, Z. Yang, G. Liu, X. Fu, J. Nie, T. Guo, Y. Pang, J. Zhao, F. Xi, C. Zhang and Z. L. Wang, Adv. Mater., 2018, 30, 1800066 CrossRef.
- K. Szendrei, P. Ganter, O. Sànchez-Sobrado, R. Eger, A. Kuhn and B. V. Lotsch, Adv. Mater., 2015, 27, 6341–6348 CrossRef CAS.
- Y. Lei, Y. Liu, Y. Guo, J. Chen, X. Huang, W. Gao, L. Qian, H. Wu, M. Liu and Y. Cheng, J. Phys. Chem. C, 2015, 119, 23138–23148 CrossRef CAS.
- D. Wang, C. Capel Ferrón, J. Li, S. Gámez-Valenzuela, R. Ponce Ortiz, J. T. López Navarrete, V. Hernández Jolín, X. Yang, M. Peña Álvarez, V. García Baonza, F. Hartl, M. C. Ruiz Delgado and H. Li, Chem. – Eur. J., 2017, 23, 13776–13783 CrossRef CAS.
- W. Li, P.-P. Yang, L. Wang and H. Wang, J. Mater. Chem. C, 2015, 3, 3783–3789 RSC.
- G. Fan and D. Yan, Sci. Rep., 2014, 4, 4933 CrossRef CAS.
- H. Wang, W. Wang, J. Guan, M.-S. Yuan and J. Wang, J. Lumin., 2017, 192, 925–931 CrossRef CAS.
- S.-J. Yoon, J. W. Chung, J. Gierschner, K. S. Kim, M.-G. Choi, D. Kim and S. Y. Park, J. Am. Chem. Soc., 2010, 132, 13675–13683 CrossRef CAS.
- P. K. Kundu, G. L. Olsen, V. Kiss and R. Klajn, Nat. Commun., 2014, 5, 3588 CrossRef.
- Q. Chen, X. Yu, Z. Pei, Y. Yang, Y. Wei and Y. Ji, Chem. Sci., 2017, 8, 724–733 RSC.
- C. Larson, B. Peele, S. Li, S. Robinson, M. Totaro, L. Beccai, B. Mazzolai and R. Shepherd, Science, 2016, 351, 1071–1074 CrossRef CAS PubMed.
- M. Amjadi, A. Pichitpajongkit, S. Lee, S. Ryu and I. Park, ACS Nano, 2014, 8, 5154–5163 CrossRef CAS PubMed.
- J. Kawahara, P. A. Ersman, I. Engquist and M. Berggren, Org. Electron., 2012, 13, 469–474 CrossRef CAS.
- R. Sydam, M. Deepa and A. K. Srivastava, RSC Adv., 2012, 2, 9011–9021 RSC.
Footnote |
† Electronic supplementary information (ESI) available. See DOI: 10.1039/c9mh00851a |
|
This journal is © The Royal Society of Chemistry 2020 |
Click here to see how this site uses Cookies. View our privacy policy here.