DOI:
10.1039/D0MA00291G
(Review Article)
Mater. Adv., 2020,
1, 1575-1601
What triggers dye adsorption by metal organic frameworks? The current perspectives
Received
9th May 2020
, Accepted 6th July 2020
First published on 10th July 2020
Abstract
Coordination chemistry has always been the most important tool to envisage the material importance of metal–organic systems. The chemistry involved plays a key role in determining structural features, which are responsible for tuning the properties of materials. In the present review, the current trends of metal organic frameworks (MOFs), their structural properties and dye adsorption related to their structural architecture together with other parameters affecting adsorption phenomena are discussed. The content of hazardous dyes such as methylene blue, rhodamine B, and methyl orange has been continuously increasing in wastewater, and therefore, considering environmental safety, their removal is urgent. The present survey demonstrates the important role of MOFs in dye adsorption and separation. Their structure activity relationship, which is the most important factor, is elaborated through the current scenario. The mechanisms involved in the adsorption are also illustrated and explained. The mechanisms support that, besides the porous nature of MOFs, various non-covalent interactions also play a significant role in enhancing the adsorption of dyes. This review presents the modern trends of dye adsorption by MOFs and opens new doors for the further tuning of their structural features to modulate the adsorption/separation of hazardous materials, which will definitely guide the future endeavors of coordination chemists.
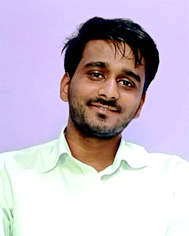
M. Shahnawaz Khan
| Shahnawaz was born in 1994 in Lakhimpur-Kheri, India. He did his graduation (2014) and post-graduation (2016) in chemistry from Aligarh Muslim University, India. He was then admitted in PhD under the supervision of Dr Mohd Khalid in the same department in 2016. The topic of his PhD Thesis is “Synthesis and spectral characterization of metal chelates of N and O donor ligands.” He has published more than ten papers in international reputed journals. Currently, he is working on the project “Inorganic functional material as an adsorbent for hazardous substances in an aqueous medium.” He works on designing metal organic frameworks and their functional applications in dye adsorption and degradation. He is a team member of the Functional Inorganic Materials Lab (FIML). |
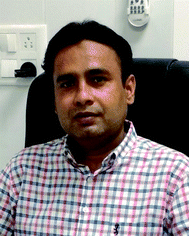
Mohd Khalid
| Dr Mohd Khalid was born in Jaunpur, Uttar Pradesh India. He completed his BSc, MSc and PhD degrees in Chemistry from Aligarh Muslim University, Aligarh, India. He is an Assistant Professor in Department of Chemistry, AMU, Aligarh. He has been teaching Inorganic Chemistry to undergraduate and postgraduate students since last 10 years. He has published more than forty papers in international journals of repute. He is actively involved in design and X-ray crystallographic investigations of novel polynuclear clusters and metal organic frameworks (MOFs), and their material applications in sensing and dye adsorption. He has also got the UGC Start-Up Grant to work on such molecules of functional importance. He has also participated in various national and international conferences and symposia to present his work. He is a part of the Functional Inorganic Materials Lab (FIML). |
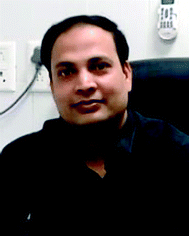
M. Shahid
| Dr Shahid is an Assistant Professor at Department of Chemistry, Aligarh Muslim University, Aligarh, India. He has been teaching Inorganic Chemistry to the under and post graduate students since 2010. He received his BS and MS degrees from CSJM University, Kanpur. He holds a PhD degree in Inorganic Chemistry from Aligarh Muslim University, Aligarh. After completing PhD, he worked as a Fast Track Young Scientist in the same department. He received many fellowships and awards given by various agencies of Govt. of India. He is a part of the Functional Inorganic Materials Lab (FIML). His research group is actively involved in development of cages, clusters and MOFs to serve as magnets, coolers, sensors and adsorbent materials. He has successfully completed many research projects funded by SERB (DST), UGC and ICMR and is currently involved in some major projects on developing inorganic functional materials. He has more than 80 research papers to his credit and filed one Indian Patent in July 2020. |
1. Introduction
Currently, the treatment of wastewater is challenging due to increasing amount of pollutant species from various sources.1 Water pollution has expanded in the last few decades, and has become the most challenging subject globally. It is predicted that by the end of 2025, people residing in desert regions will face a water shortage.1,2 Although gathering freshwater or groundwater from saltwater is an easy way to overcome this serious issue, this is impossible for communities with scarce resources2 and those living in remote territories. The concern of water pollution is still ongoing, where each year a high volume of wastewater is released into fresh and running water in the aquatic environment.3 Thus, water purification, water reuse, and drinkable water have attracted much attention (Fig. 1). However, they face several hurdles, such as potential chronic toxicity, operational cost, and public recognition.4,5 Scientifically, the establishment of sharing systems with centralized pieces of equipment has to occur, and diverse technologies can be installed depending on the restricted conditions and requirements. Thus, the ultimate management of water and water quality must be maintained at a good standard.6 Separate from all the other types of wastewater, dye wastewater has attracted considerable recognition. In the last century, the discharge of dyes into the atmosphere from the printing and dyeing industries has progressed significantly.7 Organic dyes are everyday compounds and are used enormously in numerous fields for coloring textiles, paper, rubber, leather, printing, plastic, etc.8 Mainly, the textile industry utilizes more than 700,000 tons of dye, and is one of three principal pollutants in modern times. Most of the utilized dyes are organic compounds, which are teratogenic and carcinogenic.9–12 The traditional approaches used for the remediation of wastewater include sedimentation, coagulation, and chemical and membrane technologies. However, although they are most extensively used, these methods do not eliminate contaminants effectively from wastewater and they produce secondary pollutants (Fig. 2).13 Industrial wastewater comprises a full spectrum of organic pollutants, oil, detergents, and other carcinogenic organic compounds,14 which have different harmful effects on humans and animals.15 These carcinogenic pollutants in wastewater cannot be fully degraded using the abovementioned conservative methods, which can be lethal and harmful to biological processes. Thus, two approaches have attracted much interest in treating organic pollutants in wastewater as follows: (1) The use of an appropriate adsorbent for the adsorption of organic pollutants from wastewater using polymeric resins, biomaterials, activated carbon, clay minerals, zeolites and industrial solid waste (Fig. 3).16–18 The adsorption process is very simple and cost effective.19 In this field, activated carbon is the most widely accepted adsorbent because of its efficacy in the adsorption process.20 However, its application is restricted due to its high cost and very difficult use.21 Accordingly, many new methods have been explored to replace the conventional activated carbon for the adsorption process. (2) The second approach involves removing organic pollutants via degradation through advanced oxidation processes. The degradation process involves the generation of highly reactive species, which oxidize toxic organic compounds into simple compounds with lower toxicity or fully degrade them to form CO2 and water.
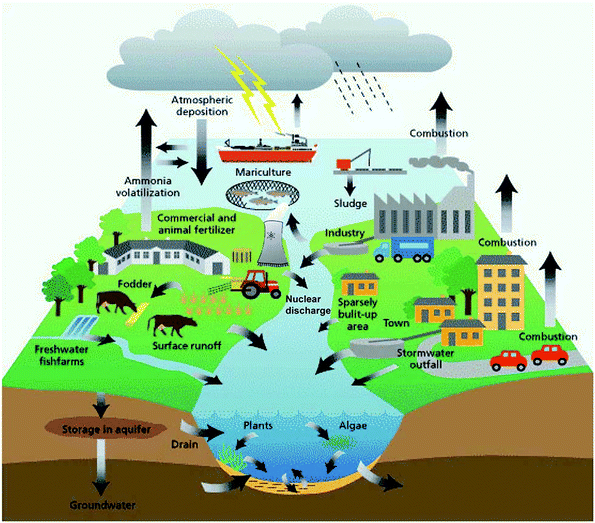 |
| Fig. 1 Sources of groundwater contamination in the hydrologic cycle.4 Reproduced from ref. 4 with permission from the Royal Society of Chemistry. | |
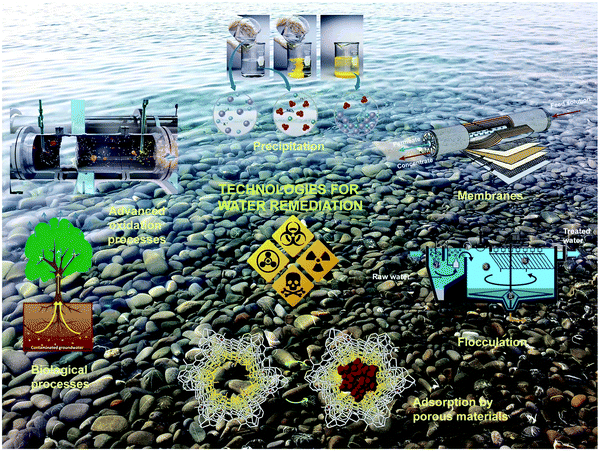 |
| Fig. 2 Current technologies and processes for water decontamination.4 Reproduced from ref. 4 with permission from the Royal Society of Chemistry. | |
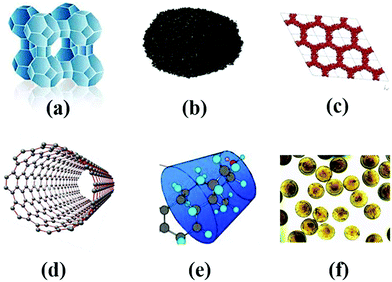 |
| Fig. 3 Different types of adsorbents used for the removal of ECs: (a) zeolites, (b) Activated carbon, (c) mesoporous silica, (d) carbon nanotubes, (e) cyclodextrins, and (f) chitosan beads.31 Reproduced from ref. 31 with permission from Elsevier. | |
One of the most common organic pollutants is aromatic organic dyes in the wastewater from industries. Since becoming aware of the hazardous nature of dyeing materials, scientists have worked hard to defeat this obstacle, and accordingly, have developed numerous chemical, biological and physical methods for the treatment of wastewater. These techniques include flocculation, adsorption, photocatalysis, biodegradation, coagulation, electrochemical process, membrane separation, advanced oxidation processes and ion-exchange. The main advantages and disadvantages of these techniques are shown in Table 1. The utilization of biological methods is comprehensive due to its eco-friendly and simple procedures compared to other methods. In the biological process, many microorganisms are used for the decolourization of dyes under varying conditions. However, there are various disadvantage associated with the biological process, which requires a strict external environment and suitable conditions such as temperature and pH. The principle limitation of the biological method is that it requires a bioreactor to be established, which demands a specific amount of land, makes the process more intricate, and requires much more time.22 Furthermore, the biological method does not have exceptional efficiency in degrading dyes due to the stability and rigid structure of these synthetic dyes. The main concern with biological processes is that there will be a lot of sludge to be disposed. On the other hand, the chemical process is beneficial and practical, but the deposition of mud adds increase the cost of the process. The main downside of chemical technology is that it needs an ample amount of chemicals and electric energy.23 Recently, the advancement in the field of advanced oxidation has gained much attention because of its tremendous oxidizing property. However, although this technique is quite impressive, it is costly, and the generation of oxide intermediates is toxic to organisms.24,25 Thus, the abovementioned reasons make it clear that these methods are economically unpleasant. In the physical method, the traditional techniques used include membrane separation and adsorption technologies. The process of membrane separation is very effective, which includes nanofiltration, ultrafiltration, microfiltration, and reverses osmosis.26 However, membrane technology in wastewater remediation is not a standard technique, and although the use of membranes is economical, they can be polluted.27 Based on the literature, it can be presumed that the process of adsorption is the most regularly used technique for the remediation of dye wastewater due to its flexible and low-cost treatment and full effectiveness.28 Also, although there are many problems that need to be resolved, the adsorption mode does not form any hazardous materials29 (Tables 2 and 3).
Table 1 The advantages and disadvantages of different dye removal technologies
Technology |
Disadvantages |
Advantages |
Biodegradation |
Occupy a certain area of land, requires strict external environmental conditions, and slow process. |
Economically attractive and simple. |
Membrane separation |
Short lifetime and economically unfeasible. |
High efficiency and reuses salts. |
Electrochemical process |
High electricity consumption and economically unfeasible. |
High efficiency and rapid. |
Ion exchange |
Economically unattractive and ineffective for certain dyes. |
No loss of sorbents. |
Coagulation/Flocculation |
High sludge production and disposal issues. |
Simple and economically attractive. |
Photochemical process |
Formation of by-products and power consumption. |
No sludge production and rapid. |
Adsorption |
Ineffective for certain dyes, regeneration is costly, disposal of adsorbent residue and loss of adsorbents. |
High efficiency, simple operation process, low cost, and does not form hazardous substances. |
Table 2 Adsorption of veterinary drugs over MOFs from aquatic systems
Veterinary drug |
MOF |
Metals/organic linkers |
Q
max (mg g−1) |
Interaction/mechanism |
Ref. |
Roxarsone |
MIL-100(Fe) |
Iron/trimesic acid |
387 |
Coordination unsaturated sites |
106
|
Phenylarsonic acid |
MIL-101(Cr) |
Chromium/terephthalic acid |
57 |
Electrostatic |
107
|
OH-MIL 101(Cr) |
Chromium/terephthalic acid |
84 |
H-bonding |
107
|
(OH)3-MIL 101(Cr) |
Chromium/terephthalic acid |
139 |
H-bonding |
107
|
p-Arsanilic acid |
ZIF-8 |
Zinc/2-methylimidazole |
730 |
Electrostatic |
108
|
Mesoporous ZIF-8 |
Zinc/2-methylimidazole |
791 |
Electrostatic |
108
|
MIL-100(Fe) |
Iron/trimesic acid |
366 |
Coordination unsaturated sites |
106
|
MIL 101(Cr) |
Chromium/terephthalic acid |
67 |
Electrostatic |
107
|
OH-MIL 101(Cr) |
Chromium/terephthalic acid |
163 |
H-bonding |
107
|
(OH)3-MIL 101(Cr) |
Chromium/terephthalic acid |
238 |
H-bonding |
107
|
UiO-67-NH2 |
Zirconium/4,40 biphenyl-aminodicarboxylate |
|
π–π interaction |
109
|
NH2-MIL-68(In) |
Indium/terephthalic acid |
401 |
H-bonding and π–π |
110
|
Table 3 Recently reported adsorption capacities of clays, zeolites and their composites
Adsorbents |
Dye |
Adsorption capacity (mg g−1) |
Ref. |
Smectite rich natural clays |
Basic yellow 28 |
77 |
111
|
Zeolite/chitosan composite |
Methylene blue |
199 |
112
|
Mesoporous zeolite |
Basic fuchsin |
238 |
113
|
Porous clay heterostructures with silica–zirconia (SiZrePCH) |
Acid Blue 25 |
266 |
114
|
Cellulose/clay composite hydrogel |
Methylene blue |
277 |
115
|
Magnesium phyllosilicates |
Red RB |
344 |
116
|
Activated organo-bentonite/sodium alginate composite |
Methylene blue |
414 |
117
|
Kaolin-based mesoporous silica |
Methylene blue |
653 |
118
|
Montmorillonite/graphene oxide composite |
Crystal violet |
746 |
119
|
Natural clay (Turkey) |
Acid Red 88 |
1133 |
120
|
Mesoporous zeolite |
Crystal violet |
1217 |
121
|
Magnesium phyllosilicates |
Blue RN |
1286 |
122
|
Magnesium phyllosilicates |
Yellow GR |
1343 |
123
|
Metal–organic frameworks (MOFs) are basically infinite crystalline structures composed of metal clusters bonded with organic ligands.30,31 The characteristic feature of MOFs is that they are generally porous and flexible due to their structure and chemical tunability. MOF materials have also been used as adsorbents for gas-phase and liquid-phase separations.32 MOFs have also been employed in the adsorption of organics,33 H234 and CO2.35–37 Recently, MOF materials showed good catalytic, and particularly, photocatalytic properties because their optical characteristics can be easily tuned to enhance their light harvesting properties, and thus employed as alternatives to other more photosensitive molecules.38–40 However, coordination compounds and most MOFs are potentially unstable in aqueous media. The stability of MOFs can be tuned in water after understanding the coordination between their metal and organic ligands. Over the years, great advancement have been achieved in the design of water-stable MOFs, which is a new class. This class of MOF materials can be immersed in water for a long period and at different pH.41 Thus, MOFs are promising candidates for the treatment of wastewater due to their high porosity and specific interactions between adsorbates and adsorbents. Moreover, their catalytic behavior can be tuned for the degradation of organic pollutants. Thus, in this review, we mainly discus the recent advancements in different topological and structural MOFs as good agents for dye adsorption and photocatalytic degradation of organic dyes. Research in the area of optimizing, modifying and introducing defects in MOFs can improve their adsorption performance. The optimized MOF materials having novel features such as one-dimensional (1D) linear molecules, two-dimensional coordination polymeric (2D) sheets and three-dimensional metal organic systems (3D) have attracted significant consideration. Mixed-metal complexes with functionalized linkers are the major forms of the modified MOFs. Defective MOFs are also involved in the formation of defect active sites. MOF-based composites obtained from the arrangement of MOFs with other functional materials have also been designed to enhance their surface area, adsorption capability and straightforward separation. The direct carbonization of MOFs as raw materials yields derived MOFs. Accordingly, we hope that MOF-based materials will be better used for the adsorption of organic pollutants and new prospects in this direction featuring their structure–activity relationship based on structural modifications should be elaborated by coordination chemists to enhance the material importance of MOFs.
In this review, the characteristic features of metal organic frameworks (MOFs) and their structural tuning triggering the capture of hazardous organic contaminants especially organic dyes are elaborated. This review features the types of adsorption, together with their mechanism and the factors promoting dye adsorption by a particular MOF. Our desire to work on functional materials especially MOFs and their dye adsorption properties led some important conclusions, which spurred us write this review as an informative paper to readers and scientists working in the field of dye adsorption.
2. Metal organic frameworks (MOFs): structural features and types
Hybrid materials consisting of organic and inorganic solids have an infinite and consistent crystalline nature created by metal ions or clusters with organic ligands.42 In 1995, the first MOFs having permanent porosity were described.43 At that time, there was no conventional nomenclature introduced for this class of molecules, and thus there were numerous names in practice, such as microporous coordination polymers,44 porous coordination polymers,45 and zeolite-like MOFs.46 In an MOF, the organic linker and metal ions are linked through coordination bonds. The metal ion can be present in cluster form with organic linkers in multidentate organic ligands such as carboxylates and other organic anions such as sulfonate heterocyclic and phosphonate compounds.47 Recently, MOF-based materials have attracted great attention from researchers due to their versatile and potential applications.48,49 The characteristics features of MOFs that make them so popular are: (1) they are easy to synthesize compared with zeolites, (2) they can easily expand their surface area with tunable porosities having coordinative unsaturated sites,50 and (3) their ability to function without breaking their framework.51–54 The most interesting feature of MOFs is that they can be easily synthesized with diverse topologies, unusual structures and neutral skeletons. The first parameter to observe in the synthesis of MOFs is their solvent. The solvent acts as the first template, which is favorably correlated in the construction of zeolite-based materials, in which organic or inorganic templates are normally needed. Additionally, the solvent has limited interaction with the framework, which is an essential parameter for understanding the final framework with accessible pores, at comparatively low temperatures. On the other hand, the various metal ions in their mono-, di-, tri-, and tetravalent form can coordinate with the organic linker, whereas in traditional zeolites, only a small number of cations (such as P, Si and Al) can form these architectures. Thus, MOFs can be easily tuned to obtain a desired product with an improved functional application. The surface area, pore size and shape of MOFs can be easily tuned from the microporous to mesoporous scale.55,56 For instance, three MOFs comprising a zirconium metal ion, namely, UiO-66 (Zr-benzene dicarboxylate, Zr-BDC), UiO-68 (Zr-terphenyldicarboxylate, Zr-TPDC) and UiO-67 (Zr-biphenyldicarboxylate, Zr-BPDC) possessed surface areas of 1187, 4170 and 3000 m2 g−1, respectively. The different organic linkers56 with different metal ions or clusters in MOFs form different frameworks, having diverse topological and physicochemical features. The CUSs or OMSs, stability, and Lewis acidities and their reaction with related organic linkers55 such as CPO-27 (Me-DHTP) (2,5-dihydroxy terephthalate), where Me = Co2+, Ni2+, Fe2+, Mn2+, and Zn2+,57–59 MIL-100 (Me-BTC (benzenetricarboxylate), where Me = Fe3+ Cr3+, and Al3+),60–62 and MIL-96 (Me-BTC; Al3+, Cr3+, Ga3+, and In3+).63–66 After the formation of crystalline materials, the physicochemical properties of MOFs can be easily tuned.67–70 Various reported MOFs have a robust nature, and their porous quality allows their post-synthetic modification (PSM) without affecting their original structure and topology.67–70 Various techniques can be adopted to anchor the effect of acid or base on MOFs via PSM, i.e., post-functionalization of amine groups with sulfones,70 post-synthetic framework sulfonation,69 grafting of cysteamine or ethylenediamine (ED)70 and amendment with different acid anhydrides.71 On the other hand, there are various ways in which MOFs can be easily tuned by loading active metals (such as Pd, Cu and Ag) or by forming composites.72 Further, the thermal and mechanical stability of MOFs are crucial and much attention has been given to the stability of MOFs in aqueous media.73 The common limitation for the utilization of MOFs in numerous applications is their instability in water both in the liquid and vapor phase.74 Numerous MOFs such as MOF-5 and MIL-101-V can be degraded through ligand displacement or hydrolysis, which has been confirmed by multiple experimental and computational investigations.75 On the other hand, MOFs (MIL-100) (Al, Cr, and Fe),76,77 MIL-101-Cr,78 and UiO-66, ZIF-879 with high water stability and can be employed for water purification through the adsorption process. Various techniques such as composite formation,80 incorporating water repellent functional groups,81 and fluorination82 can be used for enhancing the stability of MOFs in aqueous media. In last few decades, MOFs have been widely developed due to their exceptional chemistry and unusual characteristics, and their great potential applications in diverse research areas (Fig. 4).83 Finally, MOFs have been recognized as suitable substances for the liquid-phase adsorption of different compounds, including the compounds having sulfur84 and nitrogen,85 in different media. This review focuses on the MOF-based adsorptive removal of hazardous compounds, particularly from aqueous media.
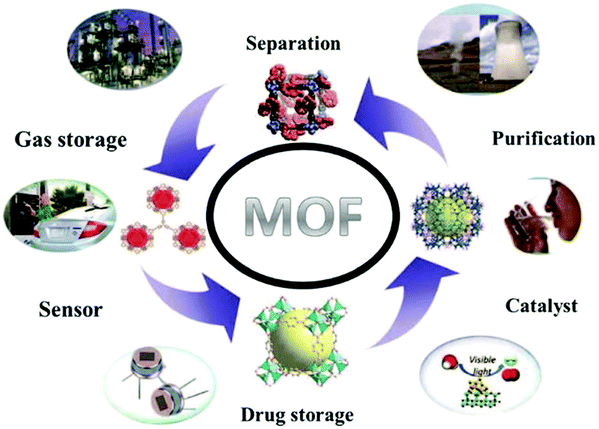 |
| Fig. 4 Wide-ranging applications of MOFs.49 Reproduced from ref. 49 with permission from the Royal Society of Chemistry. | |
The issue of water pollution has gained much consideration due to the industrial expansion globally, which has become the principal threat to the environment.86–88 Heavy metal ions and organic pollutants are mainly responsible for water pollution.86–92 A huge amount of organic pollutants is present in natural water, which pose a risk to living bodies and also make purifying wastewater difficult (Table 4).89 The United States Environmental Protection Agency has listed the poisonous organic pollutants that should be separated from wastewater before it is released into the atmosphere.90 The list is comprised of organic compounds such as benzene, benzenes (chlorinated), phenols (chlorinated phenols), nitrobenzene and phthalates, which are used in very toxic industries and threaten human life and the environment.91–95 Furthermore, it contains various hazardous materials such as dyes, spilled oils, and pharmaceuticals and personal care products (PPCPs).86–90 Nowadays, the most critical threat to the environment is dye molecules because of their organic nature and stability in aqueous medium, making them tough to degrade. Essentially, dye materials are used in the plastic, textile, painting, leather, and paper industries. Recently, it was reported that approximately 100
000 dyes are produced every year and 2% of them released into the atmosphere.91 Regularly, synthetic dyes are carcinogenic and teratogenic in nature when flashed to the aquatic system, and thus may cause severe diseases such as acute or chronic disease.92 These impurities in water are very difficult to degrade because they absorb sunlight.94,95 Currently, PPCPs are also considered as contaminants, which consist of the chemical materials used in cosmetics, veterinary drugs, agrochemicals, medicines, fragrances, fungicides, and disinfectants.96–98 Due to their stability, they are tough to degrade or convert in wastewater processing plant, and thus enter the aquatic system.96 The discovery of PPCPs in the atmosphere was investigated in the late 1980s.97,98 A previous study suggested that the liquid waste from water treatment plants, lakes, rivers, and occasionally groundwater and their demand increase with time.99 Meeting the requirements of customers, PPCPs have long shelf-lives, and thus endure in the atmosphere even after the product has been used.98,100,101 However, the effects of PPCPs on living organisms have rarely been investigated, although it has been documented that these poisonous pollutants can cause endocrine disruptions and further change in hormonal effects.102,103 As in known, in oil spills, the liquid is released into the environment unintentionally due to anthropogenic actions, together with storage, transporting, drilling and manufacturing. Presently, oil spills are very common, for example the Korean (2007, Yellow Sea), Deepwater Horizon (2010, Gulf of Mexico), and Mayflower (2013) oil spills. Due to the severe effect of oil spills on the marine and aquatic systems, during the Deepwater Horizon oil spill, many marine animals died, spanning an area of around 1300 km of beaches and shoreline.104 The investigation into numerous terrible oil spills and their impact on the atmosphere has spurred researcher to design ecological and effective methods for the remediation of wastewater.105 Organic dyes, which are organic moieties and can be easily found in wastewater, are very dangerous to human health (Fig. 5). Different dyes and their structures and absorption peaks are listed in Table 5. Metal organic frameworks (MOFs) or coordination polymers (CPs) have been employed recently for the adsorption of these dyes in aqueous media. This new class of organic–inorganic porous materials have a high surface area, tunable pore geometry, and different topological properties, making them a suitable candidates for the treatment of wastewater through dye adsorption106–123 (Tables 2 and 3).
Table 4 Classification, sources and hazards of PTS
PTS |
Sources |
Hazards |
Synthetic dyes |
Food industry, dye wastewater, papermaking wastewater, textile and printing wastewater |
High chromaticity, carcinogenesis, and toxicity |
Plasticizers |
Chemical industry and plastics industry |
Inhibition of human central nervous system, and strong stability |
Polycyclic aromatic hydrocarbons (PAHs) |
Petrochemical industry and coking industry |
Strong stability and strong carcinogenicity |
Organic cyanogen compounds |
Petrochemical industry, artificial fiber industry, and coking industry |
Acute toxicity |
Heterocyclic compounds |
Heterocyclic organisms |
Carcinogenesis, Strong stability, Mutagenicity, and Bioconcentration |
Polychlorinated biphenyl (PCB) |
Lubricating oil industry, chemical wastewater, mechanical industry, and plastics industry |
Acute toxicity and carcinogenesis |
Synthetic detergents |
Food industry, textile industry, tannery industry, and papermaking industry |
Solubilization of carcinogenic polycyclic aromatic hydrocarbons |
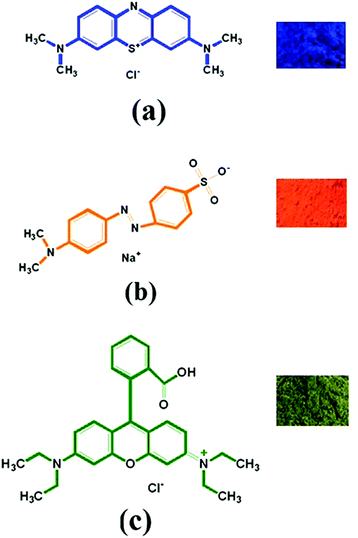 |
| Fig. 5 Powdered forms of some hazardous aromatic dyes: MB (a), MO (b) and Rh-B (c) and their structures. | |
Table 5 The classifications, chemical structures and absorption wavelengths of some commonly used organic dyes
Name of dye |
Chemical structure |
Nature |
Absorption λmax (nm) |
Methylene blue (MB) |
|
Cationic |
664 |
Methyl orange (MO) |
|
Anionic |
467 |
Rhodamine B (RhB) |
|
Cationic |
552 |
Methyl violet |
|
Cationic |
Variable |
Alizarin |
|
Neutral |
Variable |
Crystal violet (CV) |
|
Cationic |
Variable |
Congo red (CR) |
|
Anionic |
Variable |
Acid chrome blue K (AC) |
|
Neutral |
Variable |
3. Characteristics of MOFs as adsorbents
In the last few decades, there many studies have been performed in the field of designing adsorbent materials for wastewater remediation. Accordingly, metal–organic frameworks (MOFs) have been reported as solid adsorbent materials due to their high stability. Furthermore, MOFs exhibit some added peculiarities that make them promising candidates for the adsorption process (Fig. 6). The main features of MOFs are their extensive surface area, porosity, high thermal and mechanical stability, and excellent functionality. For an adsorbent, a wide surface area and especially high porosity make it very efficient because the adsorption sites become accessible and the diffusion of hazardous substances can occur easier. Accordingly, MOFs can be constructed with better porosity, where the pores of the material are guaranteed due to the crystallinity of MOFs. Synthesized MOFs with better porosity can be easily tuned by changing the organic spacers and their coordination with different metal ions. Currently, the in situ adjustment of the post-synthetic structure of MOFs has attracted much interest because it does not change the internal topology of the MOFs.124 The tuning of the topology and properties of MOFs can be easily done simultaneously with their organic and inorganic components. Furthermore, their pore size and chemical environment may trigger synergy between the adsorbates and adsorbent. Additionally, the spontaneous synthesis, large surface area, functionalized organic linkers and thermal stability of MOF make them better candidates than regular adsorbents compounds, e.g., carbonaceous solid, zeolites and silica. The pores in MOFs are effective space for the adsorption of guest molecules, which depends on the structural characteristics of the MOF. Ultimately, the unique features, wide range of structural qualities and their inorganic–organic hybrid features of MOFs make them beneficial for efficiently adsorbing hazardous materials. Recently, M. Shahid et al., reported a porous metal organic framework, [Cu(Metet)]n (MOF-1), which was synthesized via a solvothermal method employing NaN3 and 2-amino-4-picoline.125 The porous MOF, which was formed in situ during the autoclave, reaction showed a tremendous adsorption performance towards methylene blue dye. The adsorption process was carried by adsorbing the dye into the pores of MOF-1, as shown in Fig. 7.
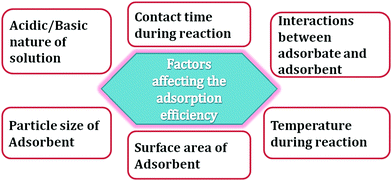 |
| Fig. 6 Factors affecting the adsorption process using MOFs as adsorbents. | |
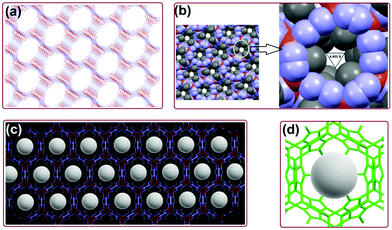 |
| Fig. 7 (a) Expanded 3D model of MOF-1. (b) Space filled model of MOF-1 showing a single unit of the expanded MOF-1. (c) and (d) Space occupied by the MB structure in the 3D MOF-1.125 Reproduced from ref. 125 with permission from Springer. | |
Although it is evident from the above discussion on the structural features of MOFs that they are better candidates for various functional applications, there are some specific requirements in the structure of their framework that cause the dye adsorption to occur effectively. Porosity is the most common factor according to the size of the dye, e.g., linear dyes such as methylene blue easily enter the porous network, thus enhancing the adsorption phenomenon. However, not only porous materials, but also non-porous MOFs have been found to absorb dyes owing to their special structural features such as the presence of suitable free functional groups like –NH2 and –OH, which form stronger H-bonding interactions with dye molecules. The HSAB principle has also been applied in MOFs for interaction of hard donor sites such as nitrogen with their hard functional groups, thus providing hard-hard (ionic) interactions. Also, the planar aromatic rings present in the skeleton of MOFs are an added advantage for the interaction of dye molecules through π–π and C–H⋯π interactions.126 Numerous other suitable functions can also be used to consolidate the binding of dye molecules on the surface of MOFs through various non-covalent interactions.
To enhance the adsorption process, the dimensionality of MOFs also plays a key role. Thus, the synthetic method to obtain MOFs with suitable dimensionality is also important to enhance the adsorption process. Specifically, 3D (porous or non-porous materials) followed by 2D MOFs are suitable candidates depending on the reactants and the reaction type and conditions. Thus, when considering the synthesis of MOFs for dye adsorption applications, these factors should be the focus when choosing reactants to trigger the effective adsorption of dye molecules by the resulting product. Therefore, a proper understanding of the structural features and their tuning becomes necessary in designing adsorbent MOFs.
3.1 Stability of MOFs in water
The water stability of MOFs is essential for their adsorption of organic pollutants. MOFs have been applied in diverse fields, i.e., catalysis, gas adsorption and separation, where their water stability is not necessary, unlike the adsorption process (Fig. 8). Thus, the feeble stability of MOFs in water restricts their application as adsorbents for the treatment of wastewater.127 The synthesis of water-stable MOFs is challenging, but several articles on water-stable MOFs such as MOF-74, MIL-101 (Cr, Fe, Al), ZIF-8, and MIL-53 (Cr, Al) have been published.128 The deficiency in the water stability of MOFs is due to the weak bonding between their metal ions and organic spacers. The functionality of several MOFs has been observed in varying humid atmospheres such as water vapor, water, and acid/base aqueous media. By following the characteristic features of a series of different MOFs, implementing high-throughput steam treatment demonstrated that the stability of MOFs can be efficiently tuned via the formation of metal and organic ligand coordination bonds and modifying the oxidation state of the metal ions.127 Accordingly, MOFs such as MOF-74 (Mg–O bond), ZIF-8 (Zn–N bond), Cr-MIL-101 (Cr–O bond) and Al-MIL-53 (Al–O bond) have been seen to exhibit sufficient stability in contrast to that of Cu–O (HKUST-1) and Zn–O (MOF-5 and MOF-508).127 Various studies have demonstrated that ZIF-8 MIL-101 and MIL-100(Fe) are stable in aqueous media. An additional study by Schoenecker et al., on water vapor adsorption suggested that the MOFs HKUST-1, Mg MOF-74, and UiO-66(–NH2) remained stable, while DMOF-1, DMOF-1-NH2, and UMCM-1 were unstable under 90% relative humidity.129 According to the observations to date, the zirconium MOFs, i.e., UiO-66 and UiO-66–NH2, are the stable MOFs in the water. An MOF (CAU-10-H) employing aluminum hydroxide isophthalate was studied under humid multi-cycling conditions, and it was observed that it was remarkably stable.130 The properties of different MOFs have been investigated in water. For instance, two zinc-based MOFs such as MOF-177 and MOF-5 has been observed to be moisture sensitive. Due to the hydrolysis of the framework, the porosity and surface area of the MOFs were reduced.131 The investigation by Greathouse and Allendorf using molecular dynamic simulation also suggests that MOF-5 is unstable.132 Another MOF reported by DeCoste et al., underwent complete distortion after one-day exposure to water, and third material was named Mg-MOF-74.133 The identical decomposition of the framework of HKUST-1 was observed when it was exposed to 90% humidity under ambient conditions. Further, Cychosz et al., carried out PXRD analysis to justify the stability of various MOFs, including UMCM-150, MOF-177, ZIF-8, MOF-505, MOF-5, HKUST-1 and MIL-100 (Cr), in aqueous media, and observed that among them, MIL-100 (Cr) and ZIF-8 were stable in pure water solution for up to 1 month.134 The excellent stability of MOFs of chromium is because of the inertness of the chromium metal ion.134,135 On the other hand, due to the higher coordination sites of their secondary building units, MIL-125 and UiO-66 were observed to have better stability.136 Individual MOFs were also investigated for their stability in acidic or basic medium or buffer medium. Zirconium-based MOFs such as PCN 224 and 222 were stable, even under harsh conditions.137,138 These MOFs exhibited significant stability in acidic and basic medium (pH 1–11).137,138 On the contrary, Al-based MOFs are structurally stable in aqueous medium, but some of them dissolve in acidic conditions.139 The durability of V, Cr, and Al-BDC have also been investigated at room temperature, and among them, Cr-BDC was established to be the most stable.140 Besides, Kandiah et al., investigated the effect of acid and base on some Zr-based MOFs, and all of them maintained their stability in aqueous medium under acidic conditions (pH = 1). On the other hand, in NaOH solution (pH = 14), MOF UiO-66-NO2 retained its structural identity, while other MOFs such as UiO-66 and UiO-66-Br inappreciably changed their identity within only 2 h at pH = 14.141 Park et al., described the stability of ZIFs in water, aqueous sodium hydroxide, benzene and methanol for almost a week at different temperatures, which were found to be stable. ZIF-8 maintained its composition for seven days in all the warm organic solvents and water for up to 24 h in 0.1 M and 8 M NaOH at 100 °C.142 Furthermore, the stability of MOF materials in buffer medium is also an essential parameter, which has been reported in a few articles. In phosphate buffer solution, Cunha et al., investigated the stability of seven carboxylate-based MOFs at 7.4 pH and at 37 °C. The stability of the MOFs followed the order of Fe-MIL-100/-127 > Fe-MIL-53, UiO-66-NH2 > Fe-MIL-53-Br UiO-66 > UiO-66-Br.143 Jung et al., explained the stability of IRMOF-3 in PBS buffer at a pH value of 7.3. Powder XRD was employed to investigate the stability of IRMOF-3 after 1 h incubation in the buffer, and it was found that an increase in the incubation time (6 h) modified its XRD pattern.144 Understanding the stability of MOFs in aqueous media is imperative for the formation of water stable and water sensitive MOFs for practical utilization. Distinct theoretical studies have also been conducted, such as molecular dynamics and quantum mechanical calculations, to provide knowledge about the interaction of MOFs with water.132,145,146 MOF-5 can be readily protonated due to the appearance of water in its formation, where the oxygen in the water molecule attacks the tetrahedral ZnO, and frees its linker.131,132 De Toni recommended that the development of a water cluster at the Zn4O section is due to the displacement of a ligand, which maintains the water coordination in the MOF structure.146 An accurate study of the hydrolysis of MOF-74, IRMOF-1 and IRMOF-10 utilizing reactive force field investigation was performed,145 in which it was assumed that when water molecules are introduced in the framework of IRMOF-1, they attack the Zn–O moiety. The water molecules dissociate into H+ and OH−, and subsequently the OH− anion coordinates with the Zn site, while H+ coordinates with the organic part, causing the structure to become distorted and deflated.145 Low et al. so estimated with the help of computational and experimental studies that ligand displacement and hydrolysis are the principal causes of the low stability of MOFs in water.127 There are several review article on the degradation mechanism of MOFs in aqueous media.126,147,148 To obtain MOFs with excellent stability, different procedures have been reported, such as ligand fictionalization, metal cation exchange, and hydrophobicity enhancement.149 The diffusion of water protective groups on the ligand is the most accepted method for increasing the stability of MOFs.150,151 The synthesis of Banasorb-22 by Wu et al., with a water protecting group on the organic linker endowed the MOF with tremendous sorption capability and better stability.152 By applying a tetraethyl-1,3,6,8-pyrenetetraphosphonate linker, which has a good monoester phosphonate ligand, a new porous barium-based MOF material named CALF-25 was synthesized, exhibiting hydrophobicity due to the presence of ethyl ester groups.150 MOFs based on naphthyl, anthracene, and tetramethyl-BDC preserve their crystalline form even after water exposure.153 By varying the organic linkers, different chemically stable MOFs can be designed, such as PCN-600 (M), where M = Mn, Fe, Co, Ni and Cu derived with a porphyrin ring as the organic ligand.154 Wang et al., elaborated two water-stable MOFs, which were isostructural, using the flexible ligand [Zr6O4(OH)8(H2O)4(CTTA)8/3] (BUT-12, H3CTTA = 50-(4-carboxyphenyl)-20,40,60-trimethyl-[1,10:30,100-terphenyl]-4,400 dicarboxylic acid).155 These two MOFs showed very good efficiency in detecting particular antibiotics and organic explosives in aqueous media.155 The fundamental nature of the ligand plays a critical role in the stability of MOFs in aqueous media because the bond between metal–ligand becomes powerful. The hydrophobic Cu-MOF Cu2L, where L = 3,30,5,50-tetraethyl-4,40-bipyrazolate, has been reported, which showed tremendous thermal mechanical and water stability.156 The PXRD pattern of this MOF was examined in acidic and basic medium, and there were no changes in the intensity of its PXRD pattern after 24 h.156 Similar MOF materials have also been synthesized, such as azolate-based MOFs with better stability in water than that based on the carboxylate ligand due to the basicity of the ligand.157,158 To further improve the water stability of MOFs in water, Li et al., incorporated the hydrophobic C60 in a c-cyclodextrin MOF and used it for drug delivery.159 The addition of different metals to MOF materials has gained significant attention due to the stronger metal–ligand bond, which enhances their water stability. A nickel-doped MOF-5 was synthesized by Li et al., which retained it crystallinity against humidity and possessed a higher surface area than that of its parent MOF-5.160 Catenated MOFs are also attracting attention due to their thermal stability and low water-loading in their frameworks. Chen et al., reported MOF-14, where 4,40,400 benzene-1,3,5-triyl-tribenzoic acid is the organic ligand with copper(II) nitrate in DMF solvent via a catenation process, which is quite robust in nature. MOF-14 was stable at room temperature, but exhibited low solubility in water and other organic solvents.161 Also, MOF-508 was constructed employing BTTB (4,40,400,4000-benzene-1,2,4,5-tetrayltetrabenzoic acid) and a pillared ligand such as bipyridyl, which was stable up to 90% moisture due to the catenation in its framework.162 Further, a tetravalent zirconium-based network was designed, Zr6O4(OH)4(CO2)12 (UiO-66), which was stable in water.136 MOFs with Zr and Cr metal ions are quite robust in nature due to the higher coordination sites of their secondary unit and their inertness.
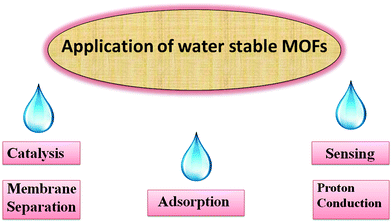 |
| Fig. 8 Various applications of water-stable MOFs. | |
3.2 Defective MOFs as adsorbents
Defective MOFs have developed as an enthusiastic topic due to their promising strategy to improve the structure of MOFs to achieve a better adsorption process.162 A defect is a disturbance in the structure and heterogeneity of MOFs, which conclusively destroys the arrangement of the atoms and surface properties of the final MOFs.163 Various defects have been introduced in structure of MOFs such as acid modulators, mixed linkers and post-synthetic modification of MOFs with inorganic acids. The introduction of acetic acid in UiO-66 was investigated to enhance the adsorption process. The defective MOF showed a selective adsorption property with a positive zeta potential, large surface area and better adsorption capacity.164 The role of acetic acid in the modulation of UiO-66 was studied for the enhanced adsorption of dichloromethane. The adsorption capacity changed due to the missing linker defect, as demonstrated by the change in surface area from 980 to 1470 m2 g−1.165 The introduction of defects in MOFs makes them more porous in nature.166 The reaction of MIL-101 (Cr) crystals with a high molar ratio of formic acid/CrCl3 resulted in a better shape, larger surface area and effective adsorption performance in the MOF.167–169 During the course of the synthesis, the addition of trifluoroacetic and HCl increased the adsorption capacity of the crystalline material.170 Thus, it can be concluded that defects increase the surface area, expand the pore size and enhance the chemical stability of MOFs.171 It can be seen in Fig. 9 that the change in the BET surface area of the MOFs is mainly due to acetic acid, benzoic acid and formic acid.172 Accordingly, a missing linker defect was synthesized using an acid modulator to construct an MOF with enhanced hydrophobicity, which provided various possibilities for the adsorption of dyes.173
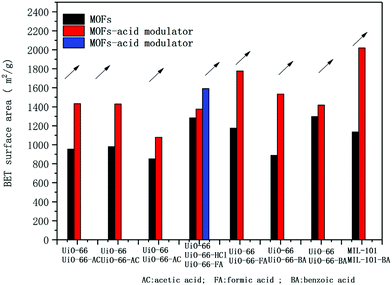 |
| Fig. 9 Change in the BET surface area of MOFs based on modulator.172 Reproduced from ref. 172 with permission from Elsevier. | |
3.3 Functionalized MOFs as adsorbents
MOF materials can be used as precursors for the synthesis of several nanostructure materials, e.g., heteroatom-doped carbons, transition metal oxide–carbon (TMO@C) composites and transition metal oxides (TMOs).174 Nanostructure-derived MOFs exhibit various special features as follows: (1) unique ability due to their chemical features compared to other MOFs; (2) expanded surface areas; and (3) inexpensive and easy to modify. For a better adsorption performance, MOF-5 was employed to obtain hierarchically porous carbon (HPC) via pyrolysis and graphitization. The HPC showed better adsorption of aromatic contaminants due to its characteristics feature and π–π interactions.175 Further MOF-1 was applied to derive HPC containing oxygen and nitrogen at 100 °C, which resulted in the efficient adsorption of PPCPs.176 Using MAF-6, porous carbon was derived as a probable adsorbent for non-natural sweeteners due to its expanded porosity, surface functionality, hydrophobicity and thermal stability. The pyrolysis temperature is the critical factor to achieve enhanced adsorption, and 6 h was considered a suitable time.177 Additionally, ZIF-8 templated with carbons via the polymerization of ZIF-8 using furfuryl alcohol (FA) and a supplementary carbon source resulted in an excellent adsorption performance.178 ZIF-8 was also employed as a precursor because of its high thermal stability, sodalite-like structure, and mild product conditions.179 Further, the carbonated ZIF-8 was employed as an adsorbent at 100 °C, which exhibited a better adsorption performance toward MB (186.3 mg g−1) compared with that of ZIF-8 (19.5 mg g−1).180 There are rare MOF-derived carbon materials with unprecedented structure–property that necessitate special consideration. An MOF acquired using multi-walled carbon nanotubes (MWCNTs) exhibited an adsorption performance toward CR of 1600 mg g−1.181 Multiple 1D carbon nanorods and 2D graphene nanoribbons were also employed in the adsorption method. The 1D carbon nanorods were derived via the self-sacrificial and morphology-preserved thermal transmutation of MOF-74. With the assistance of the sonochemical method, the thermal activation of robust carbon nanorods resulted in the construction of graphene nanoribbons with two- to six-layer stiffness. The synthetic characteristics of porous carbon materials can be easily modified using heteroatoms, such as O, S and N. Porous carbon was doped nitrogen through the carbonization of ZIF-8/urea composites, exhibiting a high adsorption performance due to its Lewis acid–base, electrostatic and hydrogen bonding interactions.182 Thermolysis of MOFs can yield nanoscale materials with a metal matrix due to the coordination of the metal ion with organic linkers.183 Co-doped hierarchically porous carbon (Co/HPC) was effectively used for the adsorption of MB.184 Also, bimetallic compounds such as Zn/Co ZIFs were applied as precursors for the preparation of porous carbon doped by Co.185 Ni-doped porous carbon is also known to exhibit a good adsorption performance such as Ni@C and Ni/PC-CNT.186,187 In comparison with the traditional methods, MOF materials derived from metal oxides exhibit unique advantages as follows: (1) the simple synthetic procedures can expedite their large-scale use; (2) the morphology, size, and elemental arrangement of the metal oxides form various MOFs; and (3) the porous structure of the resulting MOFs facilitates the adsorption of distinct precursors such as mesoporous silica and molecular sieves. After the calcination of Ce-BTC in a green solvent, CeO2 nanofibers were derived with a good adsorption capacity (86.6 mg g−1). The adsorption performance of the CeO2 nanofibers is due to their π–π interactions and electrostatic interactions.188 On the other hand, NiO resulted in excellent adsorption capability due to the thermolysis of the precursor at 350 °C.189 In comparison with C3N4 and 3D graphene, the resulting hierarchical meso/microporous structural composites displayed extraordinary adsorption ability190 (Table 6).
Table 6 Some reports on MOFs, defective MOFs and functionalized MOFs and their adsorption performance
MOF |
Ligand |
Q
0
|
Adsorption kinetics |
Mechanism |
Adsorption thermodynamics |
Ref. |
MIL-53 |
H2BDC |
MR 183.5 |
Pseudo second-order kinetic model |
Electrostatic interaction, π–π interaction, the breathing effect |
|
191
|
MOF-235 |
H2BDC |
MO 477 |
Pseudo second-order kinetic model |
Electrostatic interaction, π–π interaction |
|
192
|
MIL-100 (Fe) |
H3BTC |
MB 1045.2 |
Pseudo second-order kinetic model |
Electrostatic interaction |
|
193
|
Cu-BTC |
H3BTC |
MB 200 |
Pseudo second-order kinetic model |
Electrostatic forces, π–π interactions, hydrogen bonding |
|
194
|
NMIL-100 (Fe) |
H3BTC |
RB 68.69 |
Pseudo second-order kinetic model |
Electrostatic interaction, hydrogen bonding |
|
195
|
Cd-based MOF |
INA and ISB |
MO 166.7 |
Pseudo second-order kinetic model |
Electrostatic interaction |
|
196
|
Mn-BTB |
H3BTB |
MB 62.5 |
Pseudo second-order kinetic model |
Electrostatic interaction, π–π interaction |
|
197
|
TMU-39 |
H2oba |
CR 53 |
Pseudo second-order kinetic model |
Electrostatic interaction, π–π interaction |
|
198
|
Al-based MOF |
Succinic acid |
AO7 559.28 |
Pseudo second-order kinetic model |
Electrostatic interaction, hydrogen bonding |
|
199
|
2D Cu(II)-5N3IP |
H25N3IP |
MB > CR > RhB > MO |
|
Hydrogen-bonding, π–π Interaction |
|
200
|
2D Zn-based MOF |
H4L |
MB 139.6 MO 116.9 |
|
Electrostatic interaction, π–π interaction |
|
201
|
3D Zn-based MOF |
OH-bim and D-H2Cam |
|
|
Electrostatic interaction, π–π interaction |
|
202
|
3D Co-based MOF |
H2BPDC and ligand |
MO 53.3 Q0 |
|
π–π interaction |
|
203
|
3D Cu-based MOF |
1,4-H2ndc and L |
MB 7.34 |
|
Electrostatic interaction, π–π interaction |
|
204
|
3D Zn-based MOF |
H3BTB and bbis |
MB 348 |
|
Electrostatic interaction |
|
205
|
3D Cd-based MOF |
Ppda and abpy |
MB 315.2 |
|
Electrostatic interaction |
|
206
|
3D Co-based MOF |
H2oba and bpe |
MO 61.67 |
|
π–π interactions, hydrogen bonding |
|
207
|
2D Cd-based MOF |
L(NH2)2 and ipaH2 |
CV 221 |
|
Electrostatic interaction, π–π interaction, Lewis acid–base interaction |
|
208
|
2D BUC-17 |
Tib |
CR 4923.7 |
Pseudo second-order kinetic model |
Electrostatic interaction, ion-exchange, hydrogen-bonding, π–π interaction |
|
209
|
2D Ni-based MOF |
D-H2cam and bpzpip |
MB 185.5 |
Pseudo second-order kinetic model |
Electrostatic interaction, π–π interaction |
|
210
|
2D Zn-based MOF |
H3BTC and L |
RhB 24.36 MB 21.55 |
|
Electrostatic interaction, π–π interaction |
|
211
|
MIL-101 (Al) |
H2BDC |
MB 195 |
Pseudo-second order model |
Electrostatic interaction, Lewis acid–base interaction |
|
212
|
TMU-16 |
H2BDC and 4-bpdh |
MO 350 |
Pseudo-second order model |
Electrostatic interaction, hydrogen bonding |
Langmuir isotherm |
213
|
TMU-16-NH2 |
NH2-H2BDC and 4-bpdh |
MO 393.7 |
|
|
|
213
|
UiO-66 |
H2BDC |
MB 90.98 |
Pseudo-second order model |
Electrostatic interaction |
Langmuir isotherm |
214
|
UiO-66-NH2 |
|
MB 96.45 |
|
|
|
214
|
MIL-125 |
H2BDC |
MB 321.39 |
Pseudo-second order model |
Electrostatic interaction, p–p interaction |
Langmuir isotherm |
215
|
NH2-MIL-125 |
NH2-H2BDC |
MB 405.61 |
|
|
|
215
|
MIL-125 |
H2BDC |
|
|
Electrostatic interaction, p–p interaction, hydrogen bonding |
|
216
|
|
NH2-H2BDC |
BB 41 1257 MB 862 |
|
|
|
216
|
ZIF-8 |
2Methylimidazole |
RDB 133.76 |
Pseudo second-order kinetic mode |
p–p interaction, the hydrophobic bonds |
Langmuir isotherm |
217
|
Fe/ZIF-8 |
|
RDB 193.56 |
|
|
|
217
|
Ni-BTC |
H3BTC |
CR 828.50 |
Pseudo second-order kinetic mode |
Electrostatic interaction, p–p interaction, hydrogen bonding |
Langmuir isotherm |
218
|
Ni–Cu BTC |
|
CR 999.20 |
|
|
|
218
|
Ni-BTC |
H3BTC |
MB 765.5 |
Pseudo second-order kinetic mode |
Electrostatic interaction, p–p interaction, hydrogen bonding |
Langmuir isotherm |
219
|
Ni–Cu BTC |
|
|
|
|
|
219
|
UiO-66 |
H2BDC |
CR 251 |
Pseudo second-order kinetic mode |
Electrostatic interaction |
Langmuir isotherm |
220
|
Ti-UiO-66 |
|
CR 979 |
|
|
|
220
|
UiO-66 |
H2BDC |
MB 24.5 MO 172.5 |
Pseudo second-order kinetic mode |
p–p interaction |
Langmuir isotherm |
221
|
Ce–UiO-66 |
|
MB 145.3 MO 639.6 |
|
|
|
221
|
ZJU-24 |
H4TPTC and H6TPHC |
|
|
Electrostatic interaction |
|
222
|
ZJU-24-COOH |
|
MB 902 |
|
|
|
222
|
MIL-101 |
H3BTC |
FS 297.5 |
|
Electrostatic interaction, ion exchange |
|
223
|
MIL-101-SO3H |
2-Sulfoterephthalic acid |
FS 422.5 |
|
|
|
223
|
MIL-101 |
H3BTC |
|
Pseudo second-order kinetic mode |
Electrostatic interaction |
Langmuir isotherm |
224
|
UiO-66 |
H2BDC |
MB 73.5 |
Pseudo second-order kinetic mode |
hydrogen ions, missing-linker defects |
|
225
|
UiO-66 |
H2BDC |
DCM 510.3 |
Pseudo-second order model |
Missing-linker defects |
Langmuir–Freundlich |
226
|
UiO-66-acetic acid |
H2BDC and acetic acid |
DCM 346.4 |
|
(L–F) isotherm |
|
226
|
MIL-101 |
H2BDC |
|
|
Missing-linker defects |
|
227
|
MIL-101-formic acid |
H2BDC and formic acid |
|
|
|
|
227
|
UiO-66 |
H2BDC |
ST 39 |
|
Missing-linker defects, size-exclusion effect |
|
228
|
UiO-66-benzoic acid |
H2BDC and benzoic acid |
ST 366 |
|
|
|
228
|
UiO-66 |
H2BDC |
UiO-66 < BA-UiO-66 < FA-UiO-66 |
|
Missing-linker defects |
|
229
|
4. Possible adsorption mechanisms
The adsorption of deadly pollutants from wastewater using MOFs as adsorbents has attracted significant attention. The adsorption can occur via distinct mechanisms, i.e., interactions between acid and base, electrostatic interactions between adsorbates and adsorbent, H-bonding, hydrophobic interactions and π–π stacking (Fig. 10).230 It is well documented in the literature that more than one interaction is possible during the adsorption process.
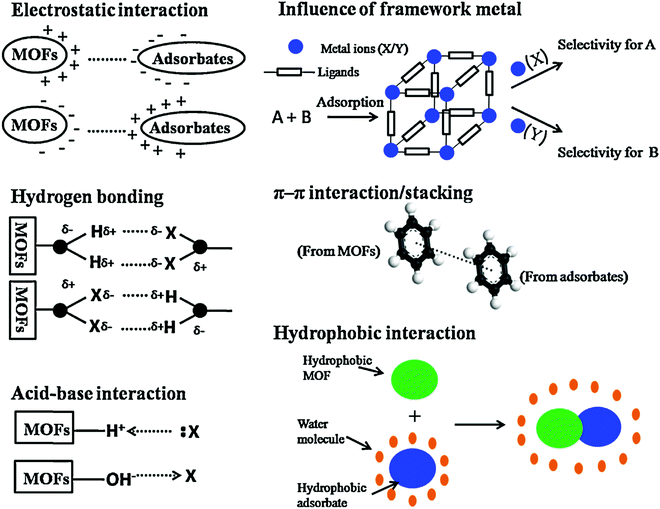 |
| Fig. 10 Schematic diagram of the possible mechanisms for the adsorptive removal of hazardous materials over MOFs.230 Reproduced from ref. 230 with permission from Elsevier. | |
4.1 Electrostatic interactions
The most often recognized phenomenon is electrostatic interactions throughout the course of the adsorption process for the elimination of hazardous substances from wastewater. The surface charge is the electric charge formed when the MOF adjusts its net surface charge at the interface and upon dispersion in polar media, i.e., water, which depends on the pH of the medium. Using the protonation and deprotonation process, the net charge of an MOF can also be changed.231,232 Thus, the charge (cationic or anionic) of MOFs can comfortably interact with various charged adsorbates, which is known as electric interactions. In 2010, Haque et al., first reported the adsorption of organic pollutants employing MOFs as adsorbents.231 In their study, they synthesized two porous Cr-based MOFs, i.e., MIL-101-Cr and MIL-53-Cr, where MIL stands for Material of Institute Lavoisier. These two MOFs efficiently adsorbed the dangerous anionic methyl orange (MO) dye from wastewater, and their capacity was much higher than that of activated carbon. Furthermore, the adsorption performance of MIL-101-Cr was much better than that of MIL-53-Cr, which additionally supports the importance of the porosity of MOFs in their adsorption characteristic. Also, after the grafting of ED and protonated ED, the adsorption performance of MIL-101-Cr was further enhanced. The anionic dye MO possessing a sulfate ion exhibits electrostatic interaction with cationic MOFs, which are very robust in nature. Using a functionalized MOF, Haque et al., reported the adsorption of methylene blue (MB) and methyl orange (MO) in wastewater.233 They attached an amino group on the MOF, and the resulting NH2-MIL-101-Al exhibited a superior adsorption capacity for MB of 762 ± 12 mg g−1, which is much higher than that of other reported MOFs and materials (Fig. 11).
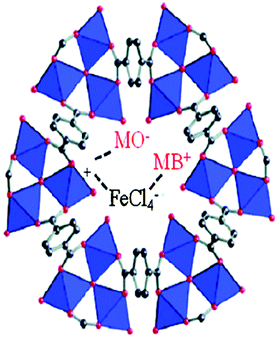 |
| Fig. 11 Electrostatic interaction between MO and MB dyes and the counter positive charge (frameworks) and negative charge (charge-balancing anion) of MOF-235.234 Reproduced from ref. 234 with permission from Elsevier. | |
In the non-functionalized MOF, the adsorption capacity reported for MIL-101-Al is 195 mg g−1, which indicates that the electrostatic interaction is singularly responsible for the high adsorption capacity of NH2-MIL-101-Al. Moreover, Haque et al., fabricated an iron terephthalate-based MOF denoted as MOF-235, which could promptly adsorb MB and MO dye from wastewater.234 Subsequently, the adsorption capability of uranine over MIL-101-Cr was also calculated, which was observed to be 126.9 mg g−1. This high capacity of over MIL-101-Cr is due to the electrostatic interaction between the MOF material and dye molecules. Lin et al., also constructed a Cu-BTC MOF, which showed a good adsorption performance towards MB.235 Khushboo et al., reported two coordination polymers based on Co(II) and Cu(II) ions, which showed a good adsorption performance towards the cationic dye MB. However, the Co-MOF showed a superior adsorption towards MB dye due to interaction between the cation and aromatic system, i.e. cation–π interaction, which is a strong interaction and plays a key role in molecular recognition (Fig. 12).236
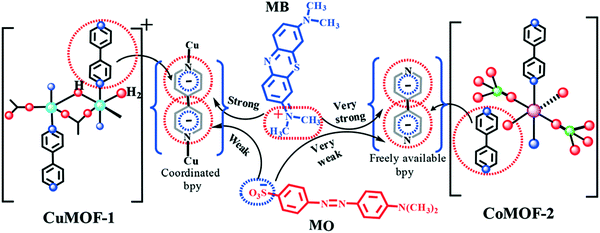 |
| Fig. 12 Plausible mechanism of dye adsorption showing the cation/anion–π interaction between cationic/anionic dyes and MOFs.236 Reproduced from ref. 236 with permission from the Royal Society of Chemistry. | |
4.2 Interactions between acid and base
The interactions between acids and bases are rarely exist in the adsorption of dangerous pollutants from wastewater. However, the acid–base interaction was observed in the adsorption of an organic pollutant by an MOF. Hasan et al., reported the adsorption of naproxen and clofibric acid on an MIL-101-Cr-functionalized MOF possessing acidic and basic groups.237 MIL-101-Cr is an outstanding adsorbent for the elimination of clofibric and naproxen,238 but when the acidic SO3H and primary NH2 groups were introduced, this increased the acid–base interaction between the MOF and pollutant. Thus, the MOF functionalized with primary NH2 groups exhibited a higher adsorption capacity than that of the pristine MOF, and the opposite was established for the MOFs having SO3H groups; therefore, these results are in good agreement with previous reports.239
4.3 Hydrogen bonding
During the adsorption of hazardous materials, the adsorption mechanism due to hydrogen bonding between the MOF and pollutants seldom occurs. H-bonding is mainly plausible in organic compounds. Liu et al., investigated the aqueous medium adsorption process of p-nitrophenol in phenol on MOFs with various architectures and topologies such as MIL-100-Fe, Cr, and NH2-MIL-101-Al.240 All the reported MOFs exhibited comparable and poor adsorption capabilities, but NH2-MIL-101-Al showed a tremendous adsorption capacity, which was 4.3 and 1.9 times higher than that of MIL-100-Fe and MIL-100-Cr, respectively. The adsorption capability in the case of PNP was much higher for NH2-MIL-101-Al in phenol than that of AC. This is due to the hydrogen bonding between PNP and the existence of the amino group in NH2-MIL-101-Al (Fig. 13). In an exceptional publication, Xie et al., illustrated the adsorption capacity of two aluminum-based MOFs, CAU-1 and MIL-68-Al, for nitrobenzene from wastewater, where their adsorption capacities were 970 ± 10 and 1130 ± 10 mg g−1, respectively, which are much higher than the experimental values for the porous materials summarized so far.241 Due to the presence of –OH groups in Al–O–Al units, both MOFs exhibited a very high adsorption capacity via the creation of H-bonding between the –OH of the MOF and nitrogen atom of nitrobenzene (Fig. 13).
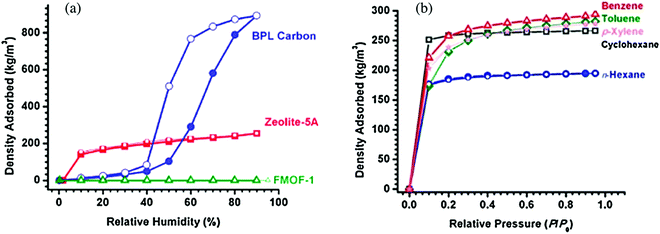 |
| Fig. 13 (a) Water adsorption isotherms over FMOF-1, zeolite-5A, and BPL carbon and (b) adsorption of oil components in FMOF-1 using vapors of cyclohexane, n-hexane, benzene, toluene, and p-xylene. Open symbols indicate desorption.242 Reproduced from ref. 242 with permission from the American Chemical Society. | |
Subsequently, H-bonding in the adsorption of carbon dioxide and ammonia with MOFs or functionalized MOFs242,243 was reported in the literature, even when the adsorption was performed in gaseous media. Recently, Mantasha et al., reported two 2-D MOFs [M(ox)(bpy)]n [H2ox = oxalic acid and bpy = 4,4′-bipyridine] based on Co(II) and Cu(II) ions, which showed tremendous selective adsorption towards methylene blue even in the presence of methylene orange dye. The mechanism was proposed to occur via electrostatic, π–π and H-bonding interactions (Fig. 14).244
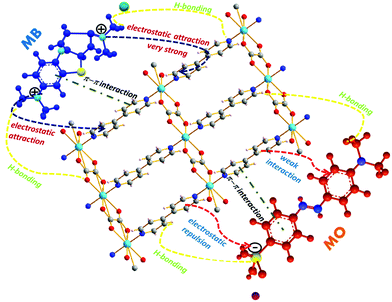 |
| Fig. 14 Plausible mechanism of dye adsorption between cationic/anionic dyes and MOFs (1 or 2).244 Reproduced from ref. 244 with permission from Elsevier. | |
4.4 π–π interactions
π–π interaction is also responsible for the adsorption of organic pollutants over MOFs,245,246 but in wastewater adsorption, π–π interactions/stacking mainly rather than complexation. Qin et al., reported the removal of bisphenol-A (BPA) using two highly porous MOF materials, MIL-101-Cr and MIL-100-Fe, and the results were analogous to that with AC.247 The kinetic parameters obtained in this case followed the order of AC < MIL-100-Fe < MIL-101-Cr. It was speculated that this trend may be attributed to the average pore diameter of the materials. Nevertheless, the adsorption mechanism was not been reported, but the most favorable reason for the high adsorption of BPA over MIL-101-Cr is due to the interactions between the benzene rings of BPA and MIL-101, together with partial H-bonding. Analogous interactions were also proposed in the adsorption of BPA over MIL-53248 and malachite green over MIL-100-Fe.249 Recently, Khalid et al., reported the synthesis of a Cu(II)-based coordination polymer named CP (1), which exhibited a tremendous adsorption performance for cationic and anionic dyes in aqueous media (Fig. 15).250 CP (1) adsorbed almost 98%, 92.8% and 95% of MB, MO and Rh-B organic dye in only 240 min. The mechanism is attributed to the strong π–π interactions between the aromatic backbones of the organic dyes with the benzene ring of CP (1).250
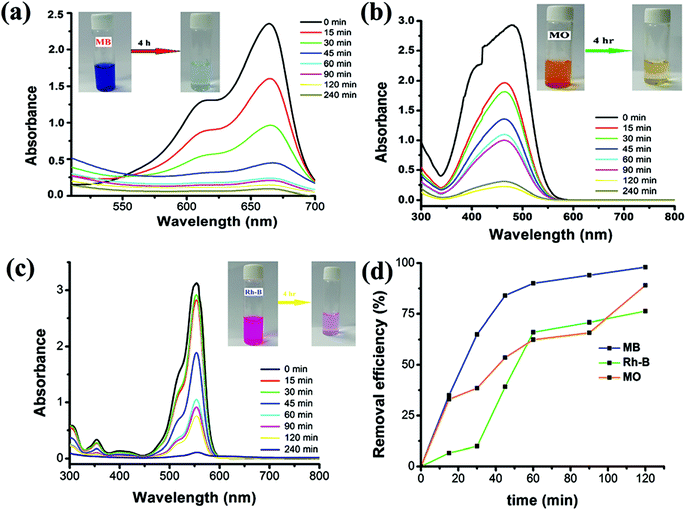 |
| Fig. 15 Change in absorption spectrum of CP (1) in the presence of different dyes: MB (a), MO (b), and Rh-B (c) at different time intervals and (d) efficiency of CP (1) to remove different dyes.250 Reproduced from ref. 250 with permission from the Royal Society of Chemistry. | |
4.5 Hydrophobic interactions
Generally, hydrophobes are non-polar and low soluble molecules with long carbon chains. Hydrophobic interactions are generally observed when adsorption occurs in the aqueous phase. For the adsorption of spilled oil, MOF materials have been used as adsorbents. In 2011, Yang et al., reported a fluorous MOF (FMOF-1) design by utilizing silver(I) 3,5-bis((trifluoromethyl)-1,2,4-triazolate) for the adsorption of oil spills.251 Because of its perfluorinated inner surface, FMOF-1 is a hydrophobic environment, and thus it exhibited high capacity for C6–C8 hydrocarbons although it has no noticeable hydrocarbons. Lin et al., reported the high extraction of oil droplets (soybean oil) from water over Cu-BTC.252 This high adsorption is attributed to the hydrophobic interactions between soybean oil and the benzene rings of the Cu-BTC MOF.
4.6 Photocatalytic degradation of dyes
Besides adsorption, sometimes organic pollutant dyes can be removed from wastewater through degradation via the mechanism of oxidation by specially employing photocatalysts.253,254 The degradation of organic pollutants via the oxidation method, which includes ozonation, Fenton reaction, and photocatalysis, is applied due to its high efficiency, better recyclability, low coast, and safe handling.254–259 The advance oxidation process is more advantageous than other processes because it transforms of organic pollutants into less harmful ions. Photocatalysis for the treatment of wastewater via the advance oxidation process involves the use of semiconductors such as TiO2, ZnS, GaP, ZnO, and Fe2O3 as catalysts to effectively degrade organic dyes into less toxic ions. In most cases, the photocatalyst even mineralizes these less toxic molecules into H2O and CO2.259–262 The advantages of photocatalytic reactions are as follows: (a) these reactions occur at ambient temperature and pressure; (b) they almost mineralize the initial and intermediate compounds without producing other toxic pollutants and (c) they are inexpensive to perform.253,254 However, the disadvantage of this method is that the semiconductors employed as catalysts are not very photostable, resulting in the corrosion of the catalyst in aqueous media, and further the movement of metal ions into water and dissolution of the solid catalysts. To date, many semiconductors have been explored for the photocatalytic degradation of organic pollutants, but TiO2 remains the best one due to its low toxicity, exceptional stability, and economical cost.263,264 However, it also involves some drawbacks such as low photocurrent quantum yield and reduced solar energy utilization efficiency. Henceforth, the development of new materials as photocatalysts with better degradation performances and stability is crucial.253,254 Recently, MOF materials have been reported as a new class of photocatalysts for the degradation of organic dyes under UV and visible irradiation. Due to their abundant metal-containing nodes, various organic linkers and controllable synthetic process, it is effortless to design MOFs with better degradation capableness and tailored dimensions to absorb light. Consequently, the photocatalytic application of MOFs has an promising future, although they have not been exploited much compared to traditional metal oxides and sulfides. MOF-5 was the first reported MOF to function as a photocatalyst,265 which was composed of clusters of Zn4O situated at the edge of the framework, joined by 1,4-bdc organic ligands.
The photodegradation mechanism is directly related to the band gap energy and other structural features supporting the degradation process. The MOF exhibited broadband adsorption in the range of 500–800 nm, which is attributed to the delocalized electron existing on the microsecond time scale remaining on its conduction band (CB). MOF-5 resulted in the enhanced degradation of phenol in wastewater comparable to that of TiO2 semiconductors. Encouraged by the photocatalytic activity of MOF-5, Chen et al., designed a porous MOF, [Zn4O(2,6ndc)3(DMF)1.5(H2O)0.5]·4DMF·7.5H2O, which was named UTSA-38, having a bandgap energy of 2.85 eV for the photodegradation of MO in aqueous phase.266 It was established that this appropriate MOF degraded the MO dye in the visible region. However, under UV light, the degradation of MO occurred rapidly within only 120 min, suggesting that UV light may more effectually degrade organic dyes than visible light (Fig. 16).255 The plausible mechanism for the degradation of the organic dye by the MOF is shown in Fig. 16, which indicates that initially electron–hole pairs are formed in UTSA-38. The subsequent absorption of light and the promotion of the electrons from the valence band (VB) to the conduction band (CB) result in the formation of holes in the VB. The holes and electrons move to the surface of UTSA-38 and the electrons reduce oxygen (O2) to its radical (˙O2), which is further transformed into hydroxyl radicals (˙OH), and in turn, the holes oxidize the hydroxyl (H2O) to hydroxyl radicals (˙OH). Hydroxyl radicals (˙OH) were proven to be responsible for the decomposition of MO efficiently.267
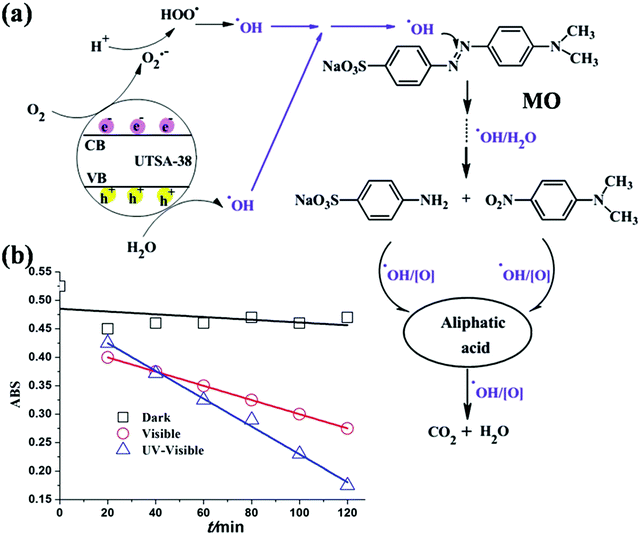 |
| Fig. 16 (a) Main pathways proposed for the photodegradation of methyl orange by UTSA-38 under UV-visible or visible light irradiation. (b) Plots of absorbance of methyl orange solution degraded by UTSA-38 as a function of irradiation time under UV-visible light, visible light and dark. Reproduced from ref. 255 with permission from the Royal Society of Chemistry. | |
Recently, Cui et al., designed six coordination polymers by employing Ni(II) and Co(II) ions. The photocatalytic degradation capacity of complexes 1–6 for methylene blue (MB) was investigated, and surprisingly complexes 1–4 exhibited a better photocatalytic degradation effect for MB (Fig. 17).268 The degradation follows the first order rate equation and complex 6 showed an enhanced degradation property with an increase in the pH of the reaction.268 Kaur et al., reported a Cd(II)-based metal–organic framework (MOF) formulated as {[Cd(PA)(4,4′ bpy)2](H2O)}n employing pamoic acid and bipyridine ligands. This photocatalyst reduced organic dyes, such as methyl orange (MO) and rhodamine B (Rh-B). Moreover, a Cd(II)-based MOF under visible light irradiation was also explored in the literature [q]. It can be seen in Fig. 18 that the Cd(II)-based MOF showed a better degradation property in the presence of H2O2. Moreover, the kinetics of the reaction was also investigated, which suggests a pseudo-first-order process for the degradation of RhB and MO.269 Furthermore, two designed porous materials, x and y, also showed better degradation of methylene blue in the UV region. Fig. 19 shows the control experiments under different reaction conditions to reduce the Cr(VI) to Cr(III), confirming that the pH value was indispensable for the reduction of Cr(VI).270 Henceforth, together with dye adsorption, the degradation of dyes also results in the overall removal of pollutants from waste, involving the mechanism of electron–hole availability and the band gap of the CB and VB in MOFs. Thus, by suitable designing MOFs, hazardous aromatic dyes can be adsorbed (by degradation), controlling the mechanism of photocatalysis.
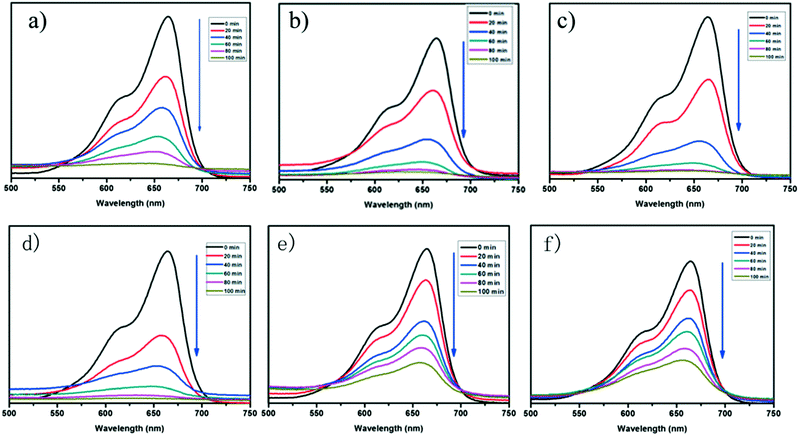 |
| Fig. 17 (a)–(f) Absorption spectra of MB dye solution in the presence of complexes 1–6. Reproduced from ref. 268 with permission from the Royal Society of Chemistry. | |
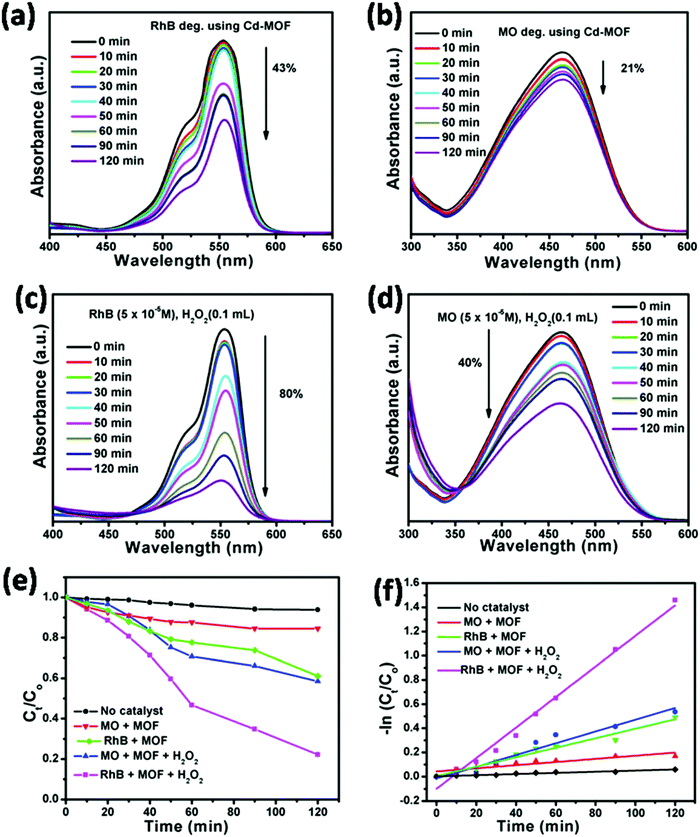 |
| Fig. 18 UV-vis spectra for the photocatalytic degradation of RhB and MO (a) and (b) over Cd-MOF and (c) and (d) with the addition of H2O2. Kinetic plots for the photocatalytic degradation of RhB and MO under various parameters (e) and (f). Reproduced from ref. 269 with permission from the Royal Society of Chemistry. | |
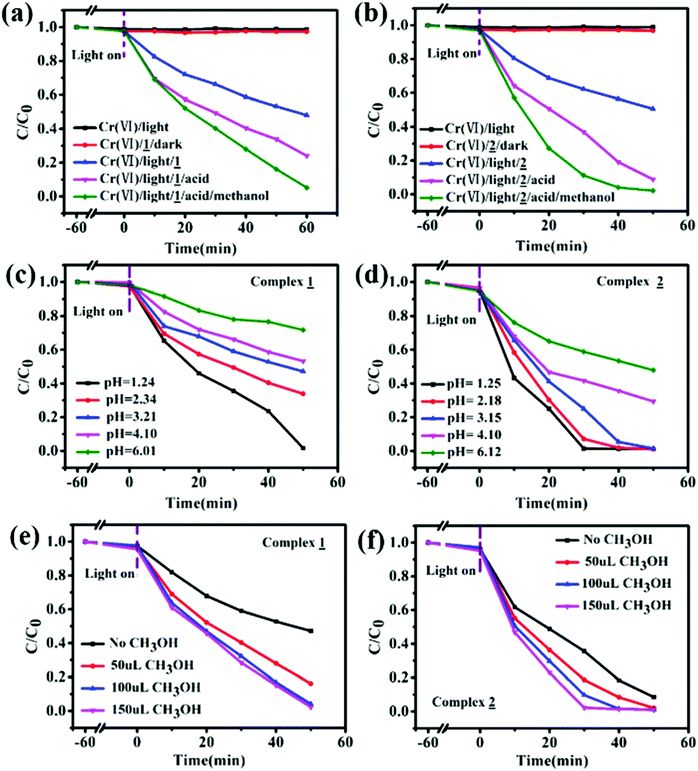 |
| Fig. 19 Control experiments for the reduction of Cr(VI) over complexes 1 (a) and 2 (b) under different conditions; photocatalytic reduction of Cr(VI) over complexes 1 (c) and 2 (d) at different pH values; and photocatalytic reduction of Cr(VI) complexes 1 (e) and 2 (f) with different methanol addition. Reproduced from ref. 270 with permission from the Royal Society of Chemistry. | |
4.7 Role of the theoretical approach (DFT) in the host–guest chemistry of MOFs
Density functional theory together with other theoretical tools such as molecular dynamic (MD) simulations have become an intriguing part in the study of MOFs for functional applications. The dynamic and kinetic aspects of substrate binding within porous MOFs are important to understand the host–guest interaction properly.271 In particular, theoretical chemists have focused on studying host–guest interactions, which consider the open metal sites or pendant functional groups in the pore as the primary binding sites for incoming guest entities. In the field of gas storage, separation and purification, special emphasis has been placed on the interactions between MOF hosts and the adsorbed substrate molecules, leading to the discovery of new functional materials with higher storage capacities and stronger binding energies. Owing to their importance, the investigation of the guest–host binding interactions involved in the adsorption becomes significant to determine how these materials (MOFs) function, and to elaborate the mechanisms for their sensing and discrimination of guest molecules such as dyes.
Computational modelling, including density functional theory (DFT) and molecular dynamics (MD), linked to experimental data has played an important role in visualizing the molecular motions and diffusion of guest molecules within the pores of MOFs. The combination of these static, dynamic and kinetic approaches offers a comprehensive understanding of the guest–host binding processes, which ultimately govern the properties of MOFs. The nature of the host–guest interactions is often related to weak supramolecular mechanisms (e.g., hydrogen bonds, π–π interactions, van der Waals, electrostatic and dipole interactions). These supramolecular interactions often involve hydrogen atoms and undergo dynamic processes. The dynamics of these interactions are difficult to probe directly by conventional spectroscopic experiments such as infrared (IR) and Raman spectroscopy, which are the most common methods to study molecular vibrations. However, it is easy to understand these interactions using DFT analysis.
Considering dyes as guest molecules, exact theoretical insights into their adsorption have not been established; however, the mechanism for the degradation of dyes has been detailed by some theoretical chemists, for example Abhinav et al. This group established a plausible mechanistic pathway for the photodegradation of aromatic dyes in the presence of an MOF by performing band structure calculations for the MOF under investigation. This calculation was based on the DFT method.272 For example, they demonstrated the density of states (DOS) and partial density of states (pDOS) for the MOF, as shown in Fig. 20. The pDOS plots show that the valence band in the MOF originates mainly from the aromatic carbon centers and oxygen centers of the carboxylate groups with a small contribution from the zinc centers. In addition, the conduction band in the range of −0.35 to 0.87 eV is attributed to the carbon centers with an additional contribution by the oxygen centers. Therefore, DOS and pDOS plots disclosed that the electronic transitions in the MOF occur from the aromatic to aromatic center (ligand-to-ligand) with an additional contribution from the carboxylate oxygen centers. Referring to this, it is established (in this case) that during photo-excitation, charge transfer occurs from the HOMO to the LUMO to generate holes, and the HOMO strongly needs one electron to return to its stable state. Thus, one electron taken from a water molecule is converted to the ˙OH active species, which decompose the dye effectively to complete the photocatalytic process.272
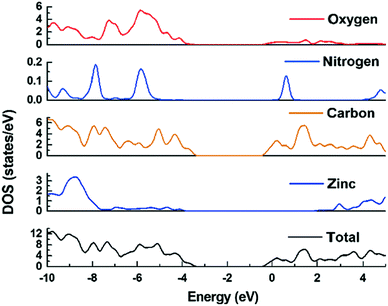 |
| Fig. 20 DOS and partial DOS plots (obtained from DFT) for Zn-MOF. Reproduced from ref. 272 with permission from the Royal Society of Chemistry. | |
The theoretical studies described herein for the elucidation of the binding sites, host–guest interactions and photodegradation of dyes with MOFs can enable and assist the design and optimization of functional materials, in which high adsorption capacity, selectivity and stability may be achieved simultaneously.
5. Conclusions and future prospects
In summary, we focused the current perspectives of the properties of MOFs and their dye adsorption capacities together with the factors and mechanisms influencing their material properties. Metal–organic frameworks (MOFs) are a different class of strong materials having a highly expanded structure and are probable candidates as adsorbents for the removal of organic pollutants from wastewater. Currently, there are various review articles in the literature on the removal of organic dyes from wastewater using MOF materials. These review articles indicate the strong interest shown by the research community in the treatment of wastewater using MOFs as adsorbents. MOFs show improved and enhance adsorption capacity and kinetics in comparison to that of the conventional used adsorbents such as AC and zeolites due to their easier tunability than that of conventional methods. Due to their large surface area, tunable porosity and ability for functional integration, MOFs are high quality materials compared with conventional adsorbents. The adsorption of organic dyes on MOFs is due to various electrostatic interactions, hydrogen bonding, π–π interactions and acid–base interactions between the adsorbent and adsorbates. The adsorption mechanism mainly follows a specific interaction depending on the target dye and structure or chemistry of the MOF. MOFs can be easily tuned for their functional application via the specific selection of the organic linker in the synthetic and post-synthetic process. In addition, the methodology for the synthesis of MOFs influences their surface area, size, shape, expansion of pores, chemical environment and dimensions. Besides, the advantages and the critical factors to employ MOF-based materials as dye adsorbents including their high efficiency, water stability, simple operation process, cost effectiveness, less amount of hazardous side products, they also suffer from some drawbacks, which need to be overcome. These drawbacks include their inability to adsorb certain dyes (either owing to the complex structures of the dye molecules or the absence of appropriate porous sites to interact with the dye moiety), their costly regeneration, disposal of the adsorbent residue, and loss of adsorbent. These issues need to be addressed to make MOFs more suitable for use in effective dye adsorption in future endeavors. Thus, it can be concluded that advance research is necessary to understand the interactions between MOFs and organic pollutants to enhance the properties of MOFs and apply them as adsorbents for the removal of organic dyes from wastewater. In addition, we hope that the scientific community will focus on the various technologies for designing water-stable MOFs with the aim of incorporating water resistance into MOFs.
Conflicts of interest
There are no conflicts to declare.
References
- D. Seckler, R. Barker and U. Amarasinghe, Int. J. Water Resour. D, 1999, 15, 29–42 CrossRef.
- S. Malato, P. Fernandez-Ibanez, M. I. Maldonado, J. Blanco and W. Gernjak, Catal. Today, 2009, 147, 1–59 CrossRef CAS.
- M. Rafatullah, O. Sulaiman, R. Hashim and A. Ahmad, J. Hazard. Mater., 2010, 177, 70–80 CrossRef CAS PubMed.
- M. Marta, R. Bruno, J. S. Ferrando-Soria, D. Armentano and E. Pardo, J. Mater. Chem. A, 2018, 6(12), 4912–4947 RSC.
- S. Casani, M. Rouhany and S. Knochel, Water Res., 2005, 39(6), 1134–11346 CrossRef CAS PubMed.
-
V. Lazarova, B. Levine and P. Renaud, Wastewater reclamation in Africa: assessment of the reuse applications and available technologies. Proc IXème Congrès de l’Union Africaine des Distributeurs d’Eau; 1998 16–20 Feb; Casablanca.
- V. Sivakumar and P. G. Rao, Ultrason. Sonochem., 2003, 85–94 CrossRef CAS.
- J. S. Gajda, H. S. Freeman and A. Reife, Dyes Pigm., 1996, 30, 1–20 CrossRef.
- G. Zeng, M. Chen and Z. Zeng, Science, 2013, 340, 1403 CrossRef CAS PubMed.
- S.-F. Yang, C.-G. Niu, D.-W. Huang, H. Zhang, C. Liang and G.-M. Zeng, Environ. Sci.: Nano, 2017, 4, 585–595 RSC.
- J.-H. Deng, X.-R. Zhang, G.-M. Zeng, J.-L. Gong, Q.-Y. Niu and J. Liang, Chem. Eng. J., 2013, 226, 189–200 CrossRef CAS.
- X. Ren, G. Zeng, L. Tang, J. Wang, J. Wan, Y. Liu, J. Yu, H. Yi, S. Ye and R. Deng, Sci. Total Environ, 2018, 610, 1154–1163 CrossRef.
- M. N. Chong, B. Jin, C. W. K. Chow and C. Saint, Water Res., 2010, 44(10), 2997–3027 CrossRef CAS PubMed.
- I. Ali, M. Asim and T. A. Khan, J. Environ. Manage., 2012, 113, 170–183 CrossRef CAS PubMed.
- M. Yang, J. Environ. Sci. Health, Part C: Environ. Carcinog. Ecotoxicol. Rev., 2011, 29(3), 223–249 CrossRef CAS PubMed.
- S. B. Wang and Y. L. Peng, Chem. Eng. J., 2010, 156, 11–24 CrossRef CAS.
- I. Ali, Chem. Rev., 2012, 112, 5073–5091 CrossRef CAS PubMed.
- M. S. Khan, M. Khalid, M. S. Ahmad, M. Shahid and M. Ahmad, Res. Chem. Intermed., 2020, 46, 2985–3006 CrossRef CAS.
- M. Saleem, T. Pirzada and R. Qadeer, Colloids Surf., A, 2007, 292, 246–250 CrossRef CAS.
- F. Deniz and R. A. Kepekci, J. Mol. Liq., 2016, 219, 194 CrossRef CAS.
- V. K. Gupta, P. J. M. Carrott, M. M. L. Ribeiro Carrott and Suhas, Crit. Rev. Environ. Sci. Technol., 2009, 39, 783 CrossRef.
- T. Ngulube, J. R. Gumbo, V. Masindi and A. Maity, J. Environ. Manage, 2017, 191, 35–57 CrossRef CAS PubMed.
- M. A. Jamal, M. Muneer and M. Iqbal, Chem. Int., 2015, 1, 2–6 Search PubMed.
- M. Ismail, W. Zheng, L. Zhang, J. Ma, Y. Jia, Y. Hu and Y. Wang, Chemosphere, 2019, 228, 212–218 CrossRef CAS.
- Y. Zhou, X. Liu, Y. Xiang, P. Wang, J. Zhang, F. Zhang and L. Tang, Bioresour. Technol., 2017, 245, 266–273 CrossRef CAS PubMed.
- U. Shamraiz, R. A. Hussain, A. Badshah, B. Raza and S. Saba, J. Photochem. Photobiol., B, 2016, 159, 33–41 CrossRef CAS PubMed.
- X. Jiang, J. Shen, S. Lou, Y. Mu, N. Wang, W. Han and L. Wang, Bioresour. Technol., 2016, 216, 645–652 CrossRef CAS PubMed.
- G. Crini, Bioresour. Technol., 2006, 97, 1061–1085 CrossRef CAS PubMed.
- J. R. Long and O. M. Yaghi, Chem. Soc. Rev., 2009, 38, 1201–1507 RSC.
- M. S. Khan, M. Khalid, M. S. Ahmad, M. Shahid and M. Ahmad, J. Struct. Chem., 2019, 60, 1833–1841 CrossRef CAS.
- S. Dhaka, R. Kumar, A. Deep, M. B. Kurade, S. W. Ji and B. H. Jeon, Coord. Chem. Rev., 2019, 380, 330–352 CrossRef CAS.
- J. R. Li, J. Sculley and H. C. Zhou, Chem. Rev., 2012, 112(2), 869–932 CrossRef CAS PubMed.
- Z. Hasan and S. H. Jhung, J. Hazard. Mater., 2015, 283, 329–339 CrossRef CAS PubMed.
- M. P. Suh, H. J. Park, T. K. Prasad and D. W. Lim, Chem. Rev., 2012, 112(2), 782–835 CrossRef CAS PubMed.
- A. R. Millward and O. M. Yaghi, J. Am. Chem. Soc., 2005, 127(51), 17998–17999 CrossRef CAS PubMed.
- J. R. Li, Y. G. Ma, M. C. McCarthy, J. Sculley, J. M. Yu and H. K. Jeong, Coord. Chem. Rev., 2011, 255, 1791–1823 CrossRef CAS.
- K. Sumida, D. L. Rogow, J. A. Mason, T. M. McDonald, E. D. Bloch and Z. R. Herm, Chem. Rev., 2012, 112(2), 724–781 CrossRef CAS PubMed.
- J. E. Mondloch, M. J. Katz, W. C. Isley, P. Ghosh, P. Liao and W. Bury, Nat. Mater., 2015, 14, 512–516 CrossRef CAS PubMed.
- M. A. Nasalevich, M. van der Veen, F. Kapteijn and J. Gascon, CrystEngComm, 2014, 16(23), 4919–4926 RSC.
- M. S. Khan, M. Khalid, M. S. Ahmad, M. Ahmad, M. Ashafaq, Rahisuddin, R. Arif and M. Shahid, J. Mol. Struct., 2019, 1175, 889 CrossRef CAS.
- K. K. Wang, H. L. Huang, W. J. Xue, D. H. Liu, X. D. Zhao and Y. Xiao, CrystEngComm, 2015, 17, 3586–3590 RSC.
- H. Furukawa, K. E. Cordova, M. O’Keeffe and O. M. Yaghi, Science, 2013, 341, 1230444 CrossRef.
- O. M. Yaghi, G. Li and H. Li, Nature, 1995, 378, 703–706 CrossRef CAS.
- K. A. Cyshosz, A. G. Wong-Foy and A. J. Matzger, J. Am. Chem. Soc., 2008, 130, 6938–6939 CrossRef PubMed.
- S. Kitagawa, R. Kitaura and S. Noro, Angew. Chem. Int. Ed., 2004, 43, 2334–2375 CrossRef CAS PubMed.
- S. Ma and H.-C. Zhou, J. Am. Chem. Soc., 2006, 128, 11734–11735 CrossRef CAS PubMed.
- Y. Liu, V. Ch Kravtsov, R. Larsen and M. Eddaoudi, Chem. Commun., 2006, 8–1490 Search PubMed.
- J. Kim, N. Rosi, D. Vodak, J. Wachter, M. O’Keeffe and O. M. Yaghi, Science, 2002, 295, 469–472 CrossRef.
- S. Chaemchuen, N. A. Kabir, K. Zhou and F. Verpoort, Chem. Soc. Rev., 2013, 42, 9304–9332 RSC.
- J. Juan-Alcaniz, R. Gielisse, A. B. Lago, E. V. Ramos-Fernandez, P. Serra-Crespo, T. Devic, N. Guillou, C. Serre, F. Kapteijn and J. Gascon, Catal. Sci. Technol., 2013, 3, 2311–2318 RSC.
- Y. K. Hwang, D.-Y. Hong, J.-S. Chang, S. H. Jhung, Y.-K. Seo, J. Kim, A. Vimont, M. Daturi, C. Serre and G. Férey, Angew. Chem. Int. Ed., 2008, 47, 4144–4148 CrossRef CAS PubMed.
- J. D. Evans, C. J. Sumby and C. J. Doonan, Chem. Soc. Rev., 2014, 43, 5933–5951 RSC.
- J. Juan-Alcaniz, J. Gascon, F. Kapteijn and J. Mater, Chem, 2012, 22, 10102–10118 CAS.
- S. H. Jhung, N. A. Khan and Z. Hasan, CrystEngComm, 2012, 14, 7099–7109 RSC.
- O. M. Yaghi, M. O’Keeffe, N. W. Ockwig, H. K. Chae, M. Eddaoudi and J. Kim, Reticular, Nature, 2003, 423, 705–714 CrossRef CAS PubMed.
- J. H. Cavka, S. Jakobsen, U. Olsbye, N. Guillou, C. Lamberti, S. Bordiga and K. P. Lillerud, J. Am. Chem. Soc., 2008, 130, 13850–13851 CrossRef PubMed.
- P. D. C. Dietzel, P. A. Georgiev, J. Eckert, R. Blom, T. Strässle and T. Unruh, Chem. Commun., 2010, 46, 4962–4964 RSC.
- D. Yu, A. O. Yazaydin, J. R. Lane, P. D. C. Dietzel and R. Q. Snurr, Chem. Sci., 2013, 4, 3544–3556 RSC.
- S. M. Chavan, G. C. Shearer, E. Bloch and S. Bordiga, ChemPhysChem, 2012, 13, 445–448 CrossRef CAS PubMed.
- C. Volkringer, D. Popov, T. Loiseau, G. Férey, M. Burghammer, C. Riekel, M. Haouas and F. Taulelle, Chem. Mater., 2009, 21, 5695–5697 CrossRef CAS.
- G. Férey, C. Serre, C. M. Draznieks, F. Millange, S. Surblé, J. Dutour and I. Margiolaki, Angew. Chem. Int. Ed., 2004, 43, 6296–6301 CrossRef PubMed.
- P. Horcajada, S. Surblé, C. Serre, D.-Y. Hong, Y.-K. Seo, J. S. Chang, J.-M. Grenèche, I. Margiolaki and G. Férey, Chem. Commun., 2007, 2820–2822 RSC.
- T. Loiseau, L. Lecroq, C. Volkringer, J. Marrot, G. Férey, M. Haouas, F. Taulelle, S. Bourrelly, P. L. Llewellyn and M. Latroche, J. Am. Chem. Soc., 2006, 128, 10223–10230 CrossRef CAS PubMed.
- P. Long, H. Wu, Q. Zhao, Y. Wang, J. Dong and J. Li, Microporous Mesoporous Mater., 2011, 142, 489–493 CrossRef CAS.
- C. Volkringer, T. Loiseau, G. Férey, C. M. Morais, F. Taulelle, V. Montouillout and D. Massiot, Microporous Mesoporous Mater., 2007, 105, 111–117 CrossRef CAS.
- C. Volkringer and T. Loiseau, Mater. Res. Bull., 2006, 41, 948–954 CrossRef CAS.
- Z. Wang and S. M. Cohen, Chem. Soc. Rev., 2009, 38, 315–1329 Search PubMed.
- D.-Y. Du, J.-S. Qin, S.-L. Li, Z.-M. Su and Y.-Q. Lan, Chem. Soc. Rev., 2014, 43, 4615–4632 RSC.
- M. G. Goestena, J. Juan-Alcaniz, E. V. Ramos-Fernandez, K. B. S. S. Gupta, E. Stavitski, H. V. Bekkum, J. Gascon and F. Kapteijn, J. Catal., 2011, 281, 177–187 CrossRef.
- D. Britt, C. Lee, F. J. Uribe-Romo, H. Furukawa and O. M. Yaghi, Inorg. Chem., 2010, 49, 6387–6389 CrossRef CAS.
- M. Kandiah, S. Usseglio, S. Svelle, U. Olsbye, K. P. Lillerud and M. Tilset, J. Mater. Chem., 2010, 20, 9848–9851 RSC.
- I. Ahmed, Z. Hasan, N. A. Khan and S. H. Jhung, Appl. Catal., B, 2013, 129, 123–129 CrossRef CAS.
- J. M. Taylor, R. Vaidhyanathan, S. S. Iremonger and G. K. H. Shimizu, J. Am. Chem. Soc., 2012, 134, 14338–14340 CrossRef CAS PubMed.
- J. Canivet, A. Fateeva, Y. Guo, B. Coasne and D. Farrusseng, Chem. Soc. Rev., 2014, 43, 5594–5617 RSC.
- J. J. Low, A. I. Benin, P. Jakubczak, J. F. Abrahamian, S. A. Faheem and R. R. Willis, J. Am. Chem. Soc., 2009, 131, 15834–15842 CrossRef CAS PubMed.
- F. Jeremias, A. Khutia, S. K. Henninger and C. Janiak, J. Mater. Chem., 2012, 22, 10148–10151 RSC.
- K. A. Cychosz and A. J. Matzger, Langmuir, 2010, 26, 17198–17202 CrossRef CAS PubMed.
- J. Ehrenmann, S. K. Henninger and C. Janiak, Eur. J. Inorg. Chem., 2011, 471–474 CrossRef CAS.
- K. S. Park, Z. Ni, A. P. Cote, J. Y. Choi, R. Huang, F. J. Uribe-Romo, H. K. Chae, M. O’Keeffe and O. M. Yaghi, Proc. Natl. Acad. Sci. U. S. A., 2006, 103, 10186–10191 CrossRef CAS PubMed.
- D.-D. Zu, L. Lu, X.-Q. Liu, D.-Y. Zhang and L.-B. Sun, J. Phys. Chem. C, 2014, 118, 19910–19917 CrossRef CAS.
- T. Wu, L. Shen, M. Luebbers, C. Hu, Q. Chen, Z. Ni and R. I. Masel, Chem. Commun., 2010, 46, 6120–6122 RSC.
- K. Sumida, D. L. Rogow, J. A. Mason, T. M. McDonald, E. D. Bloch, Z. R. Herm, T.-H. Bae and J. R. Long, Chem. Rev., 2012, 112, 724–778 CrossRef CAS PubMed.
- J.-R. Li, Y. Ma, M. C. McCarthy, J. Sculley, J. Yu, H.-K. Jeong, P. B. Balbuena and H.-C. Zhou, Coord. Chem. Rev., 2011, 255, 1791–1823 CrossRef CAS.
- N. A. Khan and S. H. Jhung, J. Hazard. Mater., 2013, 260, 1050–1056 CrossRef CAS PubMed.
- I. Ahmed, N. A. Khan and S. H. Jhung, Inorg. Chem., 2013, 52, 14155–14161 CrossRef CAS PubMed.
- C. Bao and C.-L. Fang, Water Resour. Manage. Ser., 2012, 26, 531–552 CrossRef.
- X.-J. Zhang, C. Chen, P.-F. Lin, A.-X. Hou, Z.-B. Niu and J. Wang, Environ. Sci. Technol., 2011, 45, 161–167 CrossRef CAS PubMed.
- I. Michael, L. Rizzo, C. S. McArdell, C. M. Manaia, C. Merlin, T. Schwartz, C. Dagot and D. Fatta-Kassinos, Water Res., 2013, 47, 957–995 CrossRef CAS PubMed.
- Q. Bu, B. Wang, J. Huang, S. Deng and G. Yu, J. Hazard. Mater., 2013, 262, 189–211 CrossRef CAS PubMed.
-
http://water.epa.gov/scitech/methods/cwa/pollutants.cfm
.
- L. Xie, D. Liu, H. Huang, Q. Yang and C. Zhong, Chem. Eng. J., 2014, 246, 142–149 CrossRef CAS.
- X. K. Zhao, G. P. Yang and X. C. Gao, Chemosphere, 2003, 52, 917–925 CrossRef CAS PubMed.
- J. Fawell and C. N. Ong, Int. J. Water Resour. D, 2012, 28, 247–263 CrossRef.
- Y. M. Slokar and M. L. Marechal, Dyes Pigm., 1998, 37, 335–356 CrossRef CAS.
- M. Asgher and H. N. Bhatti, Waste biomass, Ecol. Eng., 2010, 36, 1660–1665 CrossRef.
- D. Inthorn, S. Singhtho, P. Thiravetyan and E. Khan, Bioresour. Technol., 2004, 94, 299–306 CrossRef CAS PubMed.
- C. G. Daughton, Environ. Impact Assess., 2004, 24, 711–732 CrossRef.
- C. G. Daughton, Renew. Resour. J., 2005, 23, 6–23 Search PubMed.
- E. M. Cuerda-Correaa, J. R. Domínguez-Vargas, F. J. Olivares-Marín and J. B. Heredia, J. Hazard. Mater., 2010, 177, 1046–1053 CrossRef PubMed.
- O. A. H. Jones, N. Voulvoulis and J. N. Lester, Environ. Sci. Technol., 2005, 35, 401–427 CAS.
- J. L. Packer, J. J. Werner, D. E. Latch, K. McNeill and W. A. Arnold, Aquat. Sci., 2003, 65, 342–351 CrossRef CAS.
- J. K. Fawell, D. Sheahan, H. A. James, M. Hurst and S. Scott, Water Res., 2001, 35, 1240–1244 CrossRef CAS PubMed.
- M. Carballa, F. Omil and J. M. Lema, Electron. J. Environ., Agric. Food Chem., 2003, 2, 309–313 Search PubMed.
- A. A. Al-Majed, A. R. Adebayo and M. E. Hossain, J. Environ. Manage., 2012, 113, 213–227 CrossRef PubMed.
- A. Sarkar and S. Mahapatra, J. Mater. Chem. A, 2014, 2, 3808–3818 RSC.
- J. W. Jun, M. Tong, B. K. Jung, Z. Hasan, C. Zhong and S. H. Jhung, Chem. – Eur. J., 2015, 21, 347–354 CrossRef CAS PubMed.
- M. Sarker, J. Y. Song and S. H. Jhung, J. Hazard. Mater., 2017, 335, 162–169 CrossRef CAS PubMed.
- B. K. Jung, J. W. Jun, Z. Hasan and S. H. Jhung, Chem. Eng. J., 2015, 267, 9–15 CrossRef CAS.
- C. Tian, J. Zhao, X. Ou, J. Wan, Y. Cai, Z. Lin, Z. Dang and B. Xing, Environ. Sci. Technol., 2018, 52, 3466–3475 CrossRef CAS PubMed.
- Y. Lv, R. Zhang, S. Zeng, K. Liu, S. Huang, Y. Liu, P. Xu, C. Lin, Y. Cheng and M. Liu, Chem. Eng. J., 2018, 339, 359–368 CrossRef CAS.
- I. Chaari, E. Fakhfakh, M. Medhioub and F. Jamoussi, J. Mol. Struct., 2019, 1179, 672–677 CrossRef CAS.
- M. A. Islam, M. J. Ahmed, W. A. Khanday, M. Asif and B. H. Hameed, J. Environ. Manage., 2017, 203, 237–244 CrossRef CAS PubMed.
- G. V. Brião, S. L. Jahn, E. L. Foletto and G. L. Dotto, Colloids Surf., A, 2018, 556, 43–50 CrossRef.
- G. P. S. Aguiar, B. D. Arcari, L. M. Chaves, C. D. Magro, D. L. Boschetto, A. L. Piato and J. V. Oliveira, Ind. Crops Prod., 2018, 112, 1–5 CrossRef CAS.
- M. Ismail, Z. Wu, L. Zhang, J. Ma, Y. Jia, Y. Hu and Y. Wang, Chemosphere, 2019, 228, 212–218 CrossRef CAS PubMed.
- A. S. Moscofian, C. T. Pires, A. P. Vieira and C. Airoldi, RSC Adv., 2012, 2(8), 3502–3511 RSC.
- N. Belhouchat, H. Zaghouane-Boudiaf and C. Viseras, Appl. Clay Sci., 2017, 135, 9–15 CrossRef CAS.
- Y. Li, A. R. Zimmerman, F. He, J. Chen, L. Han, H. Chen, X. Hu and B. Gao, Sci. Total Environ, 2020, 10, 137972 CrossRef PubMed.
- C. Puri and G. Sumana, Appl. Clay Sci., 2018, 166, 102–112 CrossRef CAS.
- S. T. Akar and R. Uysal, Chem. Eng. J., 2010, 162, 591–598 CrossRef CAS.
- S. Bhasin, J. P. Brito, G. R. Cunningham, F. J. Hayes, H. N. Hodis, A. M. Matsumoto and M. A. Yialamas, J. Clin. Endocrinol. Metab., 2018, 103(5), 1715–1744 CrossRef.
- A. S. Moscofian, C. T. Pires, A. P. Vieira and C. Airoldi, RSC Adv., 2012, 2, 3502–3511 RSC.
- A. S. P. Moscofian, C. T. G. V. M. T. Pires, A. P. Vieira and C. Airoldi, RSC Adv., 2012, 2(8), 3502–3511 RSC.
- W. Lu, Z. Wei, Z.-Y. Gu, T.-F. Liu, J. Park, J. Park, J. Tian, M. Zhang, Q. Zhang and T. Gentle III, Chem. Soc. Rev., 2014, 43, 5561–5593 RSC.
- A. Mariyam, M. Shahid, I. Mantasha, M. S. Khan and M. Ahmad, J. Inorg. Organomet. Polym. Mater., 2020, 30, 1935–1943 CrossRef CAS.
-
(a) Mantasha I., M. Shahid, H. A. M. Saleh, K. M. A. Qasem and M. Ahmad, CrystEngComm, 2020, 22, 3891–3909 RSC;
(b) Mantasha I., H. A. M. Saleh, K. M. A. Qasem, M. Shahid and M. Ahmad, Inorg. Chim. Acta, 2020, 511, 119787 CrossRef CAS.
- K. Tan, N. Nijem, Y. Gao, S. Zuluaga, J. Li, T. Thonhauser and Y. J. Chabal, CrystEngComm, 2015, 17, 247–260 RSC.
- X. Lan, H. Zhang, P. Bai and X. Guo, Microporous Mesoporous Mater., 2016, 231, 40–46 CrossRef CAS.
- P. M. Schoenecker, C. G. Carson, H. Jasuja, C. J. Flemming and K. S. Walton, Ind. Eng. Chem. Res., 2012, 51, 6513–6519 CrossRef CAS.
- D. Fröhlich, S. K. Henninger and C. Janiak, Dalton Trans., 2014, 43, 15300–15304 RSC.
- L. Huang, H. Wang, J. Chen, Z. Wang, J. Sun, D. Zhao and Y. Yan, Microporous Mesoporous Mater., 2003, 58, 105–114 CrossRef CAS.
- J. A. Greathouse and M. D. Allendorf, J. Am. Chem. Soc., 2006, 128, 10678–10679 CrossRef CAS PubMed.
- J. B. DeCoste, G. W. Peterson, B. J. Schindler, K. L. Killops, M. A. Browe and J. J. Mahle, J. Mater. Chem. A, 2013, 1(1932), 11922–11932 RSC.
- K. A. Cychosz and A. J. Matzger, Langmuir, 2010, 26, 17198–17202 CrossRef CAS PubMed.
- G. Férey, C. Mellot-Draznieks, C. Serre, F. Millange, J. Dutour, S. Surblé and I. Margiolaki, Science, 2005, 309, 2040–2042 CrossRef PubMed.
- J. H. Cavka, S. Jakobsen, U. Olsbye, N. Guillou, C. Lamberti, S. Bordiga and K. P. Lillerud, J. Am. Chem. Soc., 2008, 130, 13850–13851 CrossRef PubMed.
- D. Feng, Z. Y. Gu, J. R. Li, H. L. Jiang, Z. Wei and H. C. Zhou, Angew. Chem., 2012, 124, 10453–10456 CrossRef.
- D. Feng, W.-C. Chung, Z. Wei, Z.-Y. Gu, H.-L. Jiang, Y.-P. Chen, D. J. Darensbourg and H.-C. Zhou, J. Am. Chem. Soc., 2013, 135, 17105–17110 CrossRef CAS PubMed.
- C. Volkringer and S. M. Cohen, Angew. Chem. Int. Ed., 2010, 49, 4644–4648 CrossRef CAS PubMed.
- I. J. Kang, N. A. Khan, E. Haque and S. H. Jhung, Chem. – Eur. J., 2011, 17, 6437–6442 CrossRef CAS PubMed.
- M. Kandiah, M. H. Nilsen, S. Usseglio, S. Jakobsen, U. Olsbye, M. Tilset, C. Larabi, E. A. Quadrelli, F. Bonino and K. P. Lillerud, Chem. Mater., 2010, 22, 6632–6640 CrossRef CAS.
- K. S. Park, Z. Ni, A. P. Côté, J. Y. Choi, R. Huang, F. J. Uribe-Romo, H. K. Chae, M. O’Keeffe and O. M. Yaghi, Proc. Natl. Acad. Sci. U. S. A., 2006, 103, 10186–10191 CrossRef CAS PubMed.
- D. Cunha, M. Ben Yahia, S. Hall, S. R. Miller, H. Chevreau, E. Elkaïm, G. Maurin, P. Horcajada and C. Serre, Chem. Mater., 2013, 25, 2767–2776 CrossRef CAS.
- S. Jung, Y. Kim, S.-J. Kim, T.-H. Kwon, S. Huh and S. Park, Chem. Commun., 2011, 47, 2904–2906 RSC.
- S. S. Han, S.-H. Choi and A. C. van Duin, Chem. Commun., 2010, 46, 5713–5715 RSC.
- M. De Toni, R. Jonchiere, P. Pullumbi, F. X. Coudert and A. H. Fuchs, ChemPhysChem, 2012, 13, 3497–3503 CrossRef CAS PubMed.
- J. Canivet, A. Fateeva, Y. Guo, B. Coasne and D. Farrusseng, Chem. Soc. Rev., 2014, 43, 5594–5617 RSC.
- N. C. Burtch, H. Jasuja and K. S. Walton, Chem. Rev., 2014, 114, 10575–10612 CrossRef CAS PubMed.
- M. G. Goesten, F. Kapteijn and J. Gascon, CrystEngComm, 2013, 15, 9249–9257 RSC.
- J. M. Taylor, R. Vaidhyanathan, S. S. Iremonger and G. K. Shimizu, J. Am. Chem. Soc., 2012, 134, 14338–14340 CrossRef CAS PubMed.
- J. Yang, A. Grzech, F. M. Mulder and T. J. Dingemans, Chem. Commun., 2011, 47, 5244–5246 RSC.
- T. Wu, L. Shen, M. Luebbers, C. Hu, Q. Chen, Z. Ni and R. I. Masel, Chem. Commun., 2010, 46, 6120–6122 RSC.
- H. Jasuja and K. S. Walton, J. Phys. Chem. C, 2013, 117, 7062–7068 CrossRef CAS.
- K. Wang, D. Feng, T.-F. Liu, J. Su, S. Yuan, Y.-P. Chen, M. Bosch, X. Zou and H.-C. Zhou, J. Am. Chem. Soc., 2014, 136, 13983–13986 CrossRef CAS PubMed.
- B. Wang, X.-L. Lv, D. Feng, L.-H. Xie, J. Zhang, M. Li, Y. Xie, J.-R. Li and H.-C. Zhou, J. Am. Chem. Soc., 2016, 138, 6204–6216 CrossRef CAS PubMed.
- J. H. Wang, M. Li and D. Li, Chem. – Eur. J., 2014, 20, 12004–12008 CrossRef CAS PubMed.
- S. Galli, N. Masciocchi, V. Colombo, A. Maspero, G. Palmisano, F. LopezGarzon, M. Domingo-García, I. Fernandez-Morales, E. Barea and J. Navarro, Chem. Mater., 2010, 22, 1664–1672 CrossRef CAS.
- V. Colombo, S. Galli, H. J. Choi, G. D. Han, A. Maspero, G. Palmisano, N. Masciocchi and J. R. Long, Chem. Sci., 2011, 2, 1311–1319 RSC.
- H. Li, M. R. Hill, R. Huang, C. Doblin, S. Lim, A. J. Hill, R. Babarao and P. Falcaro, Chem. Commun., 2016, 52, 5973–5976 RSC.
- H. Li, W. Shi, K. Zhao, H. Li, Y. Bing and P. Cheng, Inorg. Chem., 2012, 51, 9200–9207 CrossRef CAS PubMed.
- B. Chen, M. Eddaoudi, S. Hyde, M. O’Keeffe and O. Yaghi, Science, 2001, 291, 1021–1023 CrossRef CAS PubMed.
- D. M. Driscoll, D. Troya, P. M. Usov, A. J. Maynes, A. J. Morris and J. R. Morris, J. Phys. Chem. C, 2018, 122, 14582–14589 CrossRef CAS.
- W. Liang, C. J. Coghlan, F. Ragon, M. Rubio-Martinez, D. M. D’Alessandro and R. Babarao, Dalton Trans., 2016, 45, 4496–4500 RSC.
- J. Qiu, Y. Feng, X. Zhang, M. Jia and J. Yao, J. Colloid Interface Sci., 2017, 499, 151–158 CrossRef CAS PubMed.
- L. Zhou, X. Zhang and Y. Chen, Mater. Lett., 2017, 197, 167–170 CrossRef CAS.
- H. Wu, Y. S. Chua, V. Krungleviciute, M. Tyagi, P. Chen, T. Yildirim and W. Zhou, J. Am. Chem. Soc., 2013, 135, 10525–10532 CrossRef CAS PubMed.
- S. Hu, M. Liu, X. Guo, K. Li, Y. Han, C. Song and G. Zhang, Cryst. Growth Des., 2017, 17, 6586–6595 CrossRef CAS.
- J. Ren, N. M. Musyoka, H. W. Langmi, T. Segakweng, B. C. North, M. Mathe and X. Kang, Int. J. Hydrogen Energy, 2014, 39, 12018–12023 CrossRef CAS.
- K. Wang, C. Li, Y. Liang, T. Han, H. Huang, Q. Yang, D. Liu and C. Zhong, Chem. Eng. J., 2016, 289, 486–493 CrossRef CAS.
- F. Vermoortele, B. Bueken, G. L. Bars, B. Van de Voorde, M. Vandichel, K. Houthoofd, A. Vimont, M. Daturi, M. Waroquier, V. Van Speybroeck, C. Kirschhock and D. E. De Vos, J. Am. Chem. Soc., 2013, 135, 11465–11468 CrossRef CAS PubMed.
- P. Ghosh, Chem. Commun., 2014, 50, 11329–11331 RSC.
- D. Jiang, M. Chen, H. Wang, G. Zeng, D. Huang, M. Cheng, Y. Liu, W. Xue and Z. W. Wang, Coord. Chem. Rev., 2019, 380, 471–483 CrossRef CAS.
- Y. Li, Y. Liu, W. Gao, L. Zhang, W. Liu, J. Lu, Z. Wang and Y.-J. Deng, CrystEngComm, 2014, 16, 7037–7042 RSC.
- Z. Xie, W. Xu, X. Cui and Y. Wang, ChemSusChem, 2017, 10, 1645–1663 CrossRef CAS PubMed.
- W. Teng, N. Bai, Z. Chen, J. Shi, J. Fan and W.-X. Zhang, Chem. Eng. J., 2018, 346, 388–396 CrossRef CAS.
- B. N. Bhadra and S. H. Jhung, Microporous Mesoporous Mater., 2018, 270, 102–108 CrossRef CAS.
- J. Y. Song, B. N. Bhadra, N. A. Khan and S. H. Jhung, Microporous Mesoporous Mater., 2018, 260, 1–8 CrossRef CAS.
- A. Almasoudi and R. Mokaya, J. Mater. Chem., 2012, 22, 146–152 RSC.
- R. R. Salunkhe, Y. V. Kaneti, J. Kim, J. H. Kim and Y. Yamauchi, Acc. Chem. Res., 2016, 49, 2796–2806 CrossRef CAS PubMed.
- Z. Abbasi, E. Shamsaei, S. K. Leong, B. Ladewig, X. Zhang and H. Wang, Microporous Mesoporous Mater., 2016, 236, 28–37 CrossRef CAS.
- H. Y. Lin, J. Zhao, G. Song, J. Luan, X. X. Liu and G. C. Liu, Dalton Trans., 2017, 46, 17067–17073 RSC.
- S. Xu, Y. Lv, X. Zeng and D. Cao, Chem. Eng. J., 2017, 323, 502–511 CrossRef CAS.
- Z. Song, W. Liu, N. Cheng, M. N. Banis, X. Li, Q. Sun, B. Xiao, Y. Liu, A. Lushington, R. Li, L. Liu and X. Sun, Mater. Horiz., 2017, 4, 900–907 RSC.
- N. L. Torad, M. Hu, S. Ishihara, H. Sukegawa, A. A. Belik, M. Imura, K. Ariga, Y. Sakka and Y. Yamauchi, Small, 2014, 10, 2096–2107 CrossRef CAS PubMed.
- L. Jin, X. Zhao, X. Qian and M. Dong, J. Colloid Interface Sci., 2018, 509, 245–253 CrossRef CAS PubMed.
- J. Zhang, X. Yan, X. Hu, R. Feng and M. Zhou, Chem. Eng. J., 2018, 347, 640–647 CrossRef CAS.
- Y. Song, T. Qiang, M. Ye, Q. Ma and Z. Fang, Appl. Surf. Sci., 2015, 359, 834–840 CrossRef CAS.
- E. Abdelillah Ali Elhussein, S. Sahin and S. S. Bayazit, J. Mol. Liq., 2018, 255, 10–17 CrossRef CAS.
- S. Ru, L. Xu, H. Xiao and X. Li, Mater. Res. Express, 2016, 3, 115006 CrossRef.
- Y. Gu, K. Cheng, Y.-N. Wu, Y. Wang, C. Morlay, F. Li and A. C. S. Sust, Chem. Eng., 2016, 4, 6744–6753 CAS.
- E. Yılmaz, E. Sert and F. S. Atalay, J. Taiwan Inst. Chem. Eng., 2016, 65, 323–330 CrossRef.
- E. Haque, J. W. Jun and S. H. Jhung, J. Hazard. Mater., 2011, 185, 507–511 CrossRef CAS PubMed.
- M. Tong, D. Liu, Q. Yang, S. Devautour-Vinot, G. Maurin and C. Zhong, J. Mater. Chem. A, 2013, 1, 8534 RSC.
- S. Lin, Z. Song, G. Che, A. Ren, P. Li, C. Liu and J. Zhang, Microporous Mesoporous Mater., 2014, 193, 27–34 CrossRef CAS.
- S. Duan, J. Li, X. Liu, Y. Wang, S. Zeng, D. Shao and T. Hayat, ACS Sustainable Chem. Eng., 2016, 4, 3368–3378 CrossRef CAS.
- A. C. Tella, M. D. Olawale, M. Neuburger and J. A. Obaleye, J. Solid State Chem., 2017, 255, 157–166 CrossRef CAS.
- D. M. Driscoll, D. Troya, P. M. Usov, A. J. Maynes, A. J. Morris and J. R. Morris, J. Phys. Chem. C, 2018, 122, 14582–14589 CrossRef CAS.
- W. Liang, C. J. Coghlan, F. Ragon, M. Rubio-Martinez, D. M. D’Alessandro and R. Babarao, Dalton Trans., 2016, 45, 4496–4500 RSC.
- K.-W. Jung, B. H. Choi, C. M. Dao, Y. J. Lee, J.-W. Choi, K.-H. Ahn and S.-H. Lee, J. Ind. Eng. Chem., 2018, 59, 149–159 CrossRef CAS.
- Y. Zhou, S. Yao, Y. Ma, G. Li, Q. Huo and Y. Liu, Chem. Commun., 2018, 54, 3006–3009 RSC.
- J. He, J. Li, W. Du, Q. Han, Z. Wang and M. Li, J. Alloys Compd., 2018, 750, 360–367 CrossRef CAS.
- Y. H. Tang, F. Wang and J. Zhang, Dalton Trans., 2018, 47 Search PubMed.
- Y. Deng, Y. Zhao, P. Wang, Z.-Y. Yao, X.-D. Zhang and W.-Y. Sun, Microporous Mesoporous Mater., 2017, 241, 192–201 CrossRef CAS.
- L. Yang, X. Li, C.-Y. Sun, H. Wu, C.-G. Wang and Z.-M. Su, New J. Chem., 2017, 41, 3661–3666 RSC.
- M. Guo, S. Liu, H. Guo, Y. Sun, X. Guo and R. Deng, Dalton Trans., 2017, 46, 14988–14994 RSC.
- G. G. Sezer, M. Arıcı, I. Erucar, O. Z. Yesilel, H. U. Özel, B. T. Gemici and H. Erer, J. Solid State Chem., 2017, 255, 89–96 CrossRef CAS.
- S. Phengthaisong, A. Cheansirisomboon, J. Boonmak and S. Youngme, Inorg. Chim. Acta, 2018, 479, 172–178 CrossRef CAS.
- S. Chand, S. M. Elahi, A. Pal and M. C. Das, Dalton Trans., 2017, 46, 9901–9911 RSC.
- N. Ahmad, H. A. Younus, A. H. Chughtai, K. V. Hecke, Z. A. K. Khattak, Z. Gaoke, M. Danish and F. Verpoort, Catal. Sci. Technol., 2018, 8, 4010–4017 RSC.
- M.-J. Tsai and J.-Y. Wu, Polymers, 2017, 9, 661 CrossRef PubMed.
- Y. Rachuri, S. Subhagan, B. Parmar, K. K. Bisht and E. Suresh, Dalton Trans., 2018, 47, 898–908 RSC.
- E. Haque, V. Lo, A. I. Minett, A. T. Harris and T. L. Church, J. Mater. Chem. A, 2014, 2, 193–203 RSC.
- M. Roushani, Z. Saedi and T. M. Beygi, J. Taiwan Inst. Chem. Eng., 2016, 66, 164–171 CrossRef CAS.
- Q. Chen, Q. He, M. Lv, Y. Xu, H. Yang, X. Liu and F. Wei, Appl. Surf. Sci., 2015, 327, 77–85 CrossRef CAS.
- R. Bibi, L. Wei, Q. Shen, W. Tian, O. Oderinde, N. Li and J. Zhou, J. Chem. Eng. Data, 2017, 62, 1615–1622 CrossRef CAS.
- M. Oveisi, M. A. Asli and N. M. Mahmoodi, J. Hazard. Mater., 2018, 347, 123–140 CrossRef CAS PubMed.
- D. Jiang, M. Chen, H. Wang, G. Zeng, D. Huang, M. Cheng, Y. Liu, W. Xue and Z. Wang, Coord. Chem. Rev., 2019, 380, 471–483 CrossRef CAS.
- J. Hu, H. Yu, W. Dai, X. Yan, X. Hu and H. Huang, RSC Adv., 2014, 4, 35124–35130 RSC.
- H. M. Abd El Salam, S. A. Younis, H. R. Ali and T. Zaki, Microporous Mesoporous Mater., 2017, 241, 210–217 CrossRef CAS.
- Y. Han, M. Liu, K. Li, Q. Sun, W. Zhang, C. Song, G. Zhang, Z. C. Zhang and X. Guo, Inorg. Chem. Front., 2017, 4, 1870–1880 RSC.
- J. M. Yang, R. J. Ying, C. X. Han, Q. T. Hu, H. M. Xu, J. H. Li, Q. Wang and W. Zhang, Dalton Trans., 2018, 47, 3913–3920 RSC.
- J. Y. Song, I. Ahmed, P. W. Seo and S. H. Jhung, ACS Appl. Mater. Interfaces, 2016, 8, 27394–27402 CrossRef CAS PubMed.
- X. Zhao, K. Wang, Z. Gao, H. Gao, Z. Xie, X. Du and H. Huang, Ind. Eng. Chem. Res., 2017, 56, 4496–4501 CrossRef CAS.
- X.-P. Luo, S.-Y. Fu, Y.-M. Du, J.-Z. Guo and B. Li, Microporous Mesoporous Mater., 2017, 237, 268–274 CrossRef CAS.
- J. Qiu, Y. Feng, X. Zhang, M. Jia and J. Yao, J. Colloid Interface Sci., 2017, 499, 151–158 CrossRef CAS PubMed.
- L. Zhou, X. Zhang and Y. Chen, Mater. Lett., 2017, 197, 167–170 CrossRef CAS.
- J. Ren, N. M. Musyoka, H. W. Langmi, T. Segakweng, B. C. North, M. Mathe and X. Kang, Int. J. Hydrogen Energy, 2014, 39, 12018–12023 CrossRef CAS.
- K. Wang, C. Li, Y. Liang, T. Han, H. Huang, Q. Yang, D. Liu and C. Zhong, Chem. Eng. J., 2016, 289, 486–493 CrossRef CAS.
- P. Ghosh, Chem. Commun., 2014, 50, 11329–11331 RSC.
- Z. Hasan and S. H. Jhung, J. Hazard. Mater., 2015, 283, 329–339 CrossRef CAS PubMed.
- E. Haque, J. E. Lee, I. T. Jang, Y. K. Hwang, J.-S. Chang, J. Jegal and S. H. Jhung, J. Hazard. Mater., 2010, 181, 535–542 CrossRef CAS PubMed.
- A. A. Adeyemo, I. O. Adeoye and O. S. Bello, Toxicol. Environ. Chem., 2012, 94, 1846–1863 CrossRef CAS.
- E. Haque, V. Lo, A. I. Minett, A. T. Harris and T. L. Church, J. Mater. Chem. A, 2014, 2, 193–203 RSC.
- E. Haque, J. W. Jun and S. H. Jhung, J. Hazard. Mater., 2011, 185, 507–511 CrossRef CAS PubMed.
- S. Lin, Z. Song, G. Che, A. Ren, P. Li, C. Liu and J. Zhang, Microporous Mesoporous Mater., 2014, 193, 27–34 CrossRef CAS.
- K. Iman, M. Shahid, M. S. Khan, M. Ahmad and F. Sama, CrystEngComm, 2019, 21, 5299–5309 RSC.
- Z. Hasan, E.-J. Choi and S. H. Jhung, Chem. Eng. J., 2013, 219, 537–544 CrossRef CAS.
- Z. Hasan, J. Jeon and S. H. Jhung, J. Hazard. Mater., 2012, 209–210, 151–157 CrossRef CAS PubMed.
- I. Ahmed, Z. Hasan, N. A. Khan and S. H. Jhung, Appl. Catal., B, 2013, 129, 123–129 CrossRef CAS.
- B. Liu, F. Yang, Y. Zou and Y. Peng, J. Chem. Eng. Data, 2014, 59, 1476–1482 CrossRef CAS.
- L. Xie, D. Liu, H. Huang, Q. Yang and C. Zhong, Chem. Eng. J., 2014, 246, 142–149 CrossRef CAS.
- C. Petit and T. J. Bandosz, Adv. Funct. Mater., 2010, 20, 111–118 CrossRef CAS.
- N. Planas, A. L. Dzubak, R. Poloni, L.-C. Lin, A. McManus, T. M. McDonald, J. B. Neaton, J. R. Long, B. Smit and L. Gagliardi, J. Am. Chem. Soc., 2013, 135, 7402–7405 CrossRef CAS PubMed.
- Mantasha I., S. Hussain, M. Ahmad and M. Shahid, Sep. Purif. Technol., 2020, 238, 116413 CrossRef.
- N. A. Khan and S. H. Jhung, Angew. Chem. Int. Ed., 2012, 51, 1198–1201 CrossRef CAS PubMed.
- I. Ahmed and S. H. Jhung, Chem. Eng. J., 2014, 251, 35–42 CrossRef CAS.
- F.-X. Qin, S.-Y. Jia, Y. Liu, H.-Y. Li and S.-H. Wu, Desalin. Water Treat., 2014, 54, 93–102 CrossRef.
- E. Y. Park, Z. Hasan, N. A. Khan and S. H. Jhung, J. Nanosci. Nanotechnol., 2013, 13, 2789–2794 CrossRef CAS.
- S.-H. Huo and X.-P. Yan, J. Mater. Chem., 2012, 22, 7449–7455 RSC.
- M. S. Khan, M. Khalid, M. S. Ahmad, M. Shahid and M. Ahmad, Dalton Trans., 2019, 48, 12918–12932 RSC.
- C. Yang, U. Kaipa, Q. Z. Mather, X. Wang, V. Nesterov, A. F. Venero and M. A. Omary, J. Am. Chem. Soc., 2011, 133, 18094–18097 CrossRef CAS PubMed.
- K.-Y. A. Lin, H. Yang, C. Petit and F.-K. Hsu, Chem. Eng. J., 2014, 249, 293–301 CrossRef CAS.
- U. I. Gaya and A. H. Abdullah, J. Photochem. Photobiol., C, 2008, 9, 1–12 CrossRef CAS.
- H. Yang and H. Cheng, Sep. Purif. Technol., 2007, 56, 392–396 CrossRef CAS.
- M. C. Das, H. Xu, Z. Wang, G. Srinivas, W. Zhou, Y.-F. Yue, V. N. Nesterov, G. Qian and B. Chen, Chem. Commun., 2011, 47, 11715–11717 RSC.
- G. Li, M. Yu, Z. Wang, J. Lin, R. Wang and J. Fang, J. Nanosci. Nanotechnol., 2006, 6, 1416–1422 CrossRef CAS PubMed.
- J. Lu, J.-X. Lin, X.-L. Zhao and R. Cao, Chem. Commun., 2012, 48, 669–671 RSC.
- M. R. Hoffmann, S. T. Martin, W. Choi and D. W. Bahnemann, Chem. Rev., 1995, 95, 69–96 CrossRef CAS.
- T. L. Thompson and J. T. Yates, Chem. Rev., 2006, 106, 4428–4453 CrossRef CAS PubMed.
- A. Mills and S. Le Hunte, J. Photochem. Photobiol., A, 1997, 108, 1–35 CrossRef CAS.
- K. Ayoub, E. D. van Hullebusch, M. Cassir and A. Bermond, J. Hazard. Mater., 2010, 178, 10–28 CrossRef CAS PubMed.
- U. Akpan and B. Hameed, J. Hazard. Mater., 2009, 170, 520–529 CrossRef CAS PubMed.
- A. Janczyk, E. Krakowska, G. Stochel and W. Macyk, J. Am. Chem. Soc., 2006, 128, 15574–15575 CrossRef CAS PubMed.
- A. Y. Nosaka, E. Kojima, T. Fujiwara, H. Yagi, H. Akutsu and Y. Nosaka, J. Phys. Chem. B, 2003, 107, 12042–12044 CrossRef CAS.
- M. Alvaro, E. Carbonell, B. Ferrer, F. X. Llabrés i Xamena and H. Garcia, Chem. – Eur. J., 2007, 13, 5106–5112 CrossRef CAS PubMed.
- M. C. Das, H. Xu, Z. Wang, G. Srinivas, W. Zhou, Y.-F. Yue, V. N. Nesterov, G. Qian and B. Chen, Chem. Commun., 2011, 47, 11715–11717 RSC.
- J. M. Joseph, H. Destaillats, H.-M. Hung and M. R. Hoffmann, J. Phys. Chem. A, 2000, 104, 301–307 CrossRef CAS.
- L. S. Cui, X. M. Meng, Y. G. Li, K. R. Huang, Y. C. Li, J. Q. Long and P. F. Yao, CrystEngComm, 2019, 21, 3798–3809 RSC.
- H. Kaur, R. Kumar, A. Kumar, V. Krishnan and R. R. Koner, Dalton Trans., 2019, 48, 915–927 RSC.
- T. Zeng, L. Wang, L. Feng, H. Xu, Q. Cheng and Z. Pan, Dalton Trans., 2019, 48, 523–534 RSC.
- T. L. Easun, F. Moreau, Y. Yan, S. Yang and M. Schröder, Chem. Soc. Rev., 2017, 46, 239–274 RSC.
-
(a) J.-C. Jin, J. Wu, Y.-X. He, B.-H. Li, J.-Q. Liu, R. Prasad, A. Kumar and S. R. Batten, CrystEngComm, 2017, 19, 6464–6472 RSC;
(b) Y. Pan, Q. Ding, H. Xu, C. Shi, A. Singh, A. Kumar and J. Liu, CrystEngComm, 2019, 21, 4578–4585 RSC.
|
This journal is © The Royal Society of Chemistry 2020 |