DOI:
10.1039/D0GC02058C
(Critical Review)
Green Chem., 2020,
22, 6258-6287
Plasma-driven catalysis: green ammonia synthesis with intermittent electricity
Received
17th June 2020
, Accepted 8th September 2020
First published on 8th September 2020
Abstract
Ammonia is one of the most produced chemicals, mainly synthesized from fossil fuels for fertilizer applications. Furthermore, ammonia may be one of the energy carriers of the future, when it is produced from renewable electricity. This has spurred research on alternative technologies for green ammonia production. Research on plasma-driven ammonia synthesis has recently gained traction in academic literature. In the current review, we summarize the literature on plasma-driven ammonia synthesis. We distinguish between mechanisms for ammonia synthesis in the presence of a plasma, with and without a catalyst, for different plasma conditions. Strategies for catalyst design are discussed, as well as the current understanding regarding the potential plasma-catalyst synergies as function of the plasma conditions and their implications on energy efficiency. Finally, we discuss the limitations in currently reported models and experiments, as an outlook for research opportunities for further unravelling the complexities of plasma-catalytic ammonia synthesis, in order to bridge the gap between the currently reported models and experimental results.
1. Introduction – the need for electrification and energy storage
Renewable energy sources, such as wind energy and solar power, increasingly penetrate the electrical power grid, spurring the electrification of the energy landscape.1 However, these energy sources are intermittent and energy storage is required. For short-term energy storage (up to a few days), a wide range of technologies is available, including batteries and thermo-mechanical storage.2 In contrast, chemical energy storage is one of the few alternatives for long-term, seasonal energy storage,2,3 the other main option being pumped hydropower.4 Even though pumped hydropower may be a potential solution for low-cost energy storage in some naturally suited areas,4 the energy density of such systems is low, and pumped hydropower heavily depends on the availability of large natural water formations.
Chemical energy storage in the form of hydrogen is often proposed to solve the intermittency challenge. Hydrogen can be produced from water via electrolysis using renewable electricity, producing oxygen as a by-product. Hydrogen can be combusted to water in a fuel cell or gas turbine, producing electricity again. However, hydrogen is not easily stored over longer timespans due to temperature fluctuations over the different seasons, considering the severe storage conditions. Therefore, hydrogen carriers are required and ammonia is one of the options available.3,5 Ammonia can be used for stationary energy storage, as well as for fuel applications.3,6,7 Ammonia is a carbon-free hydrogen carrier, which can be produced from air and water. The current ammonia supply accounts for about 170 Mt per year.
Currently, ammonia (NH3) is produced mostly as a synthetic fertilizer via thermochemical conversion of hydrogen (H2) and nitrogen (N2), which is crucial to produce sufficient food via agriculture to sustain the current world population of almost 8 billion people.8,9 Hydrogen for this purpose is mostly produced via steam reforming of methane, contributing significantly to global warming caused by emission of CO2. Alternative methods to produce ammonia are being researched, both for the purpose of energy storage and/or fertilizer production by using electrical power rather than fossil energy carriers like methane. The goal of this review is to put one specific solution, i.e. plasma-catalytic synthesis of ammonia, in perspective of existing and other innovative routes. The reader is introduced to the concepts of plasma chemistry and plasma catalysis, followed by the state of the art of plasma-driven ammonia synthesis.
2. Ammonia synthesis processes
We discuss the current ammonia synthesis processes and non-conventional technologies, starting with the industrial Haber–Bosch process and its modifications for greener ammonia production at milder conditions, after which sustainable and novel ammonia synthesis methods are presented, such as electrochemical, photochemical and homogeneous ammonia synthesis, as well as chemical looping approaches. This provides the background for the core of this review: plasma-driven ammonia synthesis.
2.1. The Haber–Bosch process
This section serves as an introduction to commercial ammonia synthesis processes via the Haber–Bosch process. We present the basics of the hydrogen production, nitrogen production, and ammonia synthesis loop. Conventional ammonia production processes are extensively discussed in ref. 10–13. We also elaborate on scale-down and intermittency issues,6 providing a rationale for research on novel technologies.
2.1.1. Brief history of the Haber–Bosch process.
The Haber–Bosch process was developed in the early 20th century as the first industrial large-scale process for fixating nitrogen in the form of ammonia.11,14 In 1908, the chemist Fritsch Haber and his co-worker Robert Le Rossignol demonstrated that the ammonia synthesis reaction from nitrogen and hydrogen was industrially viable.15 Using Le Châtelier's principle, they found that significantly increasing the pressure shifts the equilibrium of the reaction towards the product side (eqn (1)). |  | (1) |
The high-pressure, industrial ammonia synthesis process was developed by Carl Bosch and co-workers. The first plant in Oppau (Germany) was operational by 1913, with a production capacity of 30 t-NH3 d−1. Since then, the Haber–Bosch process and catalysts have undergone only gradual changes.11,12 Hydrogen and nitrogen react in a H2
:
N2 molar ratio of 2
:
1 to 3
:
1 over a multiple-promoted iron catalyst at 400–500 °C and 100–450 bar.16 The Haber–Bosch process has outcompeted other nitrogen fixation processes, such as NOx production using electrical arcs (the Birkeland–Eyde process)17,18 and the cyanamide process (the Frank–Caro process).18,19 The development and evolution of nitrogen fixation processes is shown in Fig. 1, from which it follows that the best Haber–Bosch plants have energy consumptions close to the lower heating value of 18.6 GJ t-NH3−1.
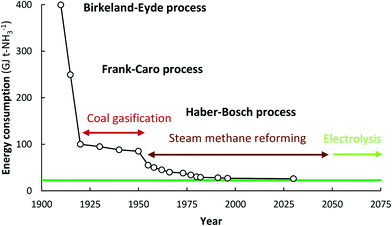 |
| Fig. 1 Energy consumption of synthetic nitrogen fixation processes, and the theoretical minimum energy consumption (green line). Adapted and modified from ref. 20. | |
2.1.2. Process description.
Nearly all ammonia is currently produced from fossil fuels, such as natural gas, naphtha, heavy fuel oil, and coal.14,21 This ammonia is termed brown ammonia, while ammonia produced from fossil fuels with carbon capture and storage (CCS) is termed blue ammonia. Ammonia produced with essentially zero carbon footprint from electrolysis-based or biomass-based hydrogen is termed green ammonia. A process flow diagram of a steam methane reforming-based Haber–Bosch process is shown in Fig. 2.
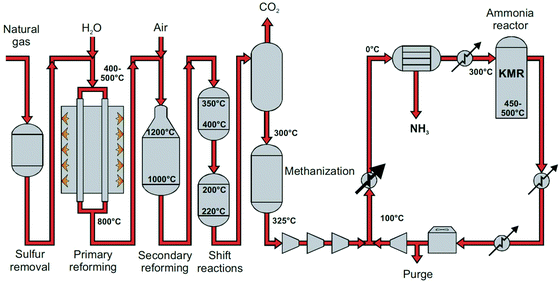 |
| Fig. 2 Process flow diagram of steam methane reforming-based Haber–Bosch process. KMR is a commercial multiple promoted iron-based ammonia synthesis catalyst. Reproduced from ref. 22. | |
The ammonia production process starts with hydrogen production, usually through stream methane reforming (SMR), with >70% of the ammonia currently produced (eqn (2)).11,12,21 Other processes for hydrogen production include coal or biomass gasification and electrolysis.14,20 In the primary reforming section (the tubular reformer), natural gas and water react at 400–800 °C. Nitrogen is usually introduced by adding air at the second stage of the reforming process (the autothermal reformer), in which part of the oxygen is burned to overcome the endothermicity of the steam methane reforming reaction.11 In both reforming stages, a nickel-based catalyst is used. The residual CH4 concentration is below 0.5 vol%.12
|  | (2) |
|  | (3) |
Subsequently, the produced gas mixture is subjected to a series of water gas shift (WGS) reactors to maximize the hydrogen yield and to remove the bulk of CO present in the gas stream (eqn (3)). A decrease in temperature is favoured to push the conversion to H2 and CO2 production, due to the exothermicity of the reaction. A two-stage shift conversion is usually applied to optimize the efficiency of the reactor and catalyst usage. First, the gas mixture is fed to a high-temperature-shift catalyst bed of Fe2O3/Cr2O3 at 350–400 °C, after which the gas mixture is fed to a low-temperature-shift catalyst bed of CuO/ZnO/Al2O3 at 200–220 °C.23 The residual CO concentration after the low-temperature-shift reactor is below 0.3 vol%.12
Gas cleaning is required before ammonia synthesis. Firstly, the CO2 is scrubbed out using a caustic scrub, either based on amines like MEA or MDEA, or alkali hydroxides like potash.11,12 The added benefit is that any remaining sulfur or nitrous oxide compounds are also removed. Secondly, any remaining CO is reactively removed through methanation (reverse of eqn (2)) at 250–350 °C and 25 bar, using a nickel catalyst.12
Alternative methods for nitrogen generation include cryogenic air separation, pressure swing adsorption, and membrane permeation.11,24,25 While cryogenic air separation is usually the preferred technology at industrial scale, small-scale operation may be facilitated by nitrogen production by pressure swing adsorption.6,25
After gas purification, the reaction mixture is compressed to 100–450 bar for the ammonia synthesis loop (see Fig. 2). High temperature (400–500 °C) is required because of the limited activity of the iron catalyst for breaking the triple nitrogen–nitrogen bond (N
N), which is the rate-determining step for ammonia synthesis.26,27 High pressure is required to shift the thermodynamic equilibrium towards ammonia, achieving typically 25 vol% ammonia at the reactor outlet.10,12 The product mixture is cooled to near-ambient temperatures (−20 °C to 30 °C) to separate the bulk of the produced ammonia from the reaction mixture via condensation.12 The remaining gasses are compressed back up to reaction pressures, mixed with fresh make-up gas and sent back into the reactor. Furthermore, a purge is required in the recycle to prevent the accumulation of inert gases, i.e. mainly CH4 and Ar.
2.1.3. Catalyst.
The catalyst used in the ammonia synthesis loop is arguably one of the most important aspects of the whole process. The activity of the catalyst determines the required operating temperature for the reactor. This determines the operational pressure to achieve sufficient conversion, and consequently the required compression, as well as the cooling requirement for condensation. Also, the catalyst lifetime is an important factor in determining the run time of the process before a new catalyst is required, which is determined by the catalyst resistance to chemical parameters such as poisons and physical parameters in the process such as a high temperature.11,12
The most widely used catalyst for ammonia synthesis is a multiple promoted iron-catalyst, containing a mix of Al2O3, MgO and SiO2 for mechanical strength and as structural promoters, as well as some electronic promoters such as CaO and K2O.28 Iron-based catalysts typically have a typical lifetime of at least 10 years.29–31
The reaction mechanisms for ammonia synthesis from H2 and N2 over the industrial iron-catalyst have been heavily debated over the past century.32–37 Only in the late 1970s, Ertl et al.33 were able to construct a free energy diagram for gas phase ammonia synthesis and ammonia synthesis over the industrial iron-catalyst. The reaction mechanism for ammonia synthesis is listed in Table 1.
Table 1 Reaction mechanism for ammonia synthesis over the industrial iron-catalyst
|
Reaction |
Note |
H2 dissociation |
H2 + 2* ⇌ 2H* |
|
N2 dissociation |
N2 + 2* ⇌ 2N* |
Rate-determining step |
Hydrogenation reactions |
N* + H* ⇌ NH* + * |
|
NH* + H* ⇌ NH2* + * |
NH2* + H* ⇌ NH3* + * |
NH3 desorption |
NH3* ⇌ NH3 + * |
|
In the 1910s, Mittasch et al.38,39 put a tremendous effort into finding a suitable catalyst for ammonia synthesis by scanning a large part of the periodic table and mixtures thereof. Only decades later, it was consolidated that the binding strength of nitrogen is a descriptor for ammonia synthesis activity.22 Furthermore, electronic promoters can substantially change the activity by altering the barrier for breaking the triple N
N bond.40,41 A so-called volcano curve was developed, with the binding strength of nitrogen as a descriptor for the ammonia synthesis rate (see Fig. 3). Materials that bind nitrogen too strongly (i.e., on the left-hand side of the volcano curve), easily dissociate nitrogen. However, the ammonia is also strongly bound to the surface of these catalysts, causing desorption limitations, or the N-atoms on the surface are too stable, converting slowly to ammonia. On the other hand, materials that bind nitrogen too weakly (i.e., on the right-hand side of the volcano curve), have limitations for nitrogen dissociation due to a high nitrogen dissociation barrier. An optimum is achieved at intermediate binding strength of nitrogen. As follows from Fig. 3, osmium and ruthenium are more active than iron among metal catalysts.42–45 Among bimetallic catalysts, CoMo nitrides have also been researched, which show activities similar to ruthenium (Ru) catalysts.46,47 The latter have been used in various industrial plants,48 but due to the high cost, these have mostly been replaced by the newest generation of iron-catalysts.28,31,49 Osmium on the other hand cannot be used because it is highly poisonous. Current research focuses on developing catalysts which break the N
N bond easily, resulting in hydrogenation of N as the rate determining step on the surface.44,50,51
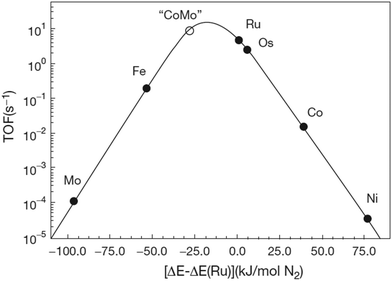 |
| Fig. 3 Calculated turnover frequencies for ammonia synthesis as a function of the adsorption energy of nitrogen (at 400 °C, 50 bar, H2 : N2 = 3 : 1 and 5% NH3). Reproduced from ref. 47. | |
2.1.4. Scale-down and intermittency.
The current trend for large-scale Haber–Bosch plants is further upscaling for minor improvements in energy consumption and minor gains in the capital expenditures.52 Even though modern, large-scale Haber–Bosch plants operate at a low energy consumption of 27–36 GJ t-NH3−1 (see Fig. 1) close to the theoretical minimum of 20.1 GJ t-NH3−1, these plants are only feasible for continuous, large-scale production up to 3300 t-NH3 d−1 nowadays.53,54 Large-scale brown ammonia production allows for relatively low capital investments per tonne of ammonia produced due to the economy of scale. However, such large-scale plants have limited operational flexibility and decarbonisation of current Haber–Bosch plants with intermittent electricity from solar and wind resources coupled with electrolysers is not straightforward.
Another trend for the conventional technology is downscaling to 3–60 t-NH3 d−1 for coupling with electrolysers for hydrogen production, which allows for scaling the technology to the size of wind and solar electricity.6,55 Furthermore, small-scale plants can be installed more easily, and the ammonia can be produced and used locally, saving transportation costs. However, downscaling leads to an increased cost of ammonia production due to the relatively higher capital expenditure.
Thus, there is a need for operation under milder temperatures and pressures as compared to the current Haber–Bosch process to allow for intermittent operation and lower capital expenditures.14 Furthermore, Haber–Bosch processes suffer from energy losses upon downscaling below 1 t-NH3 d−1,6 which is due to the high temperatures and temperature fluctuations within the process (see Fig. 4). Alternative technologies may allow for sufficiently energy-efficient ammonia production with a low carbon footprint.18,66
 |
| Fig. 4 Energy consumption of various electrolysis-based Haber–Bosch processes (academic and industrial estimates). The bold line represents the thermodynamic minimum energy consumption (20.1 GJ t-NH3−1). 100 kg h−1 ammonia corresponds to approximately 1 MW. Original references.56–65 Reproduced from ref. 20. | |
2.2. Sustainable ammonia synthesis
Ammonia is one of the most produced bulk chemicals, with a high carbon footprint.14,20 For this reason, ammonia synthesis receives much attention, in the transition towards a more environmentally friendly chemical industry. Making ammonia synthesis more sustainable revolves around two main aspects dictating the process energy consumption: (i) hydrogen production, and (ii) the ammonia synthesis loop, which includes both modifying the Haber–Bosch process and novel ammonia synthesis methods.20,67 These various aspects are discussed in the next sections. Typically, hydrogen production accounts for 90–95% of the energy consumed for ammonia production. Furthermore, operating ammonia synthesis under milder conditions may allow for scale-down and intermittent operation.6,68
2.2.1. Hydrogen production.
Hydrogen production is a prime candidate for electrification in the chemical industry,69,70 since it can be produced via electrolysis from water at a reasonable efficiency of 70–80%. Historically, electrolysis has been a major production method for hydrogen in ammonia synthesis, second only to coal gasification up till the 1950s–1960s. Afterwards, the emergence of low-cost natural gas decreased the share of hydrogen from electrolysis.
Alkaline electrolysis is the most mature technology71 and therefore used for producing green hydrogen at large scale (10–100 MWs). On the other hand, proton–exchange membrane (PEM) electrolysis has recently received attention for hydrogen production, due to its ability to follow intermittent electrical loads from renewables such as solar and wind.71,72 In terms of production capacity, both electrolysis techniques are comparable. However, PEM electrolyzers currently have a higher capital cost due to the use of noble metals. Energy consumptions of 3.8–6.6 kW h NmH2−3 are reported for both alkaline electrolyzers and PEM electrolyzers, with a current trend towards lower energy consumption (at elevated pressure).71,73 A major benefit of PEM is that it can produce hydrogen at up to 200 bar pressure, which alleviates the need for energy intensive hydrogen compression.72
Further methods for improving the sustainability of hydrogen production are modification of the conventional technology. Examples include electrical heating during SMR1,74 and carbon-capture and -storage of the produced CO2.75,76 Lastly, biomass can be used as a sustainable source of hydrogen, directly through gasification, or indirectly through anaerobic digestion or fermentation followed by steam reforming.77
2.2.2. Ammonia synthesis loop.
New developments in the ammonia synthesis loop focus on two main aspects. The first focus is on modifying the Haber–Bosch process by decreasing the operating temperature and pressure, by using more active catalysts and highly efficient separation of ammonia with sorbents, which is coined the absorbent-enhanced Haber–Bosch process.6,68 The second focus is on novel ammonia synthesis methods, such as electrochemical ammonia synthesis,78,79 photochemical ammonia synthesis,80,81 plasma-driven ammonia synthesis,82–84 homogeneous ammonia synthesis,66,85 and chemical looping approaches.86,87 Novel ammonia synthesis methods were recently reviewed by various authors.14,18,66,88 The current status of alternative ammonia synthesis methods is listed in Table 2.
Table 2 Comparison of alternative ammonia synthesis methods. The reported energy requirement refers to the best available technology (BAT) or the best reported value in literature. The potential energy requirement refers to the energy requirement of such a process if the technology is successfully improved, and additional separation steps are included. The theoretical minimum refers to the theoretical minimum energy consumption for the reaction based on thermodynamics (separation steps are not included). Estimates based on ref. 55, 65, 66 and 89–95
|
Energy requirement (GJ tNH3−1) |
TRL |
Reported |
Potential |
Theoretical minimum |
The energy requirement is for large-scale plants. Upon scale-down, the energy efficiency will be lower (see Fig. 4).
Electrolysis for hydrogen production, nitrogen production, plasma-catalysis and recycling of the synthesis gas are included in the consideration. The potential energy requirement is based on an energy consumption of about 35 GJ tNH3−1 for H2 production via low temperature electrolysis and N2 purification. Plasma-activation of N2 can lower the N2 dissociation barrier by about 70 kJ mol−1 over Ru catalysts.96 We assume that this is the energy input of the plasma. This results in an energy consumption of 2.1 GJ tNH3−1, the ammonia separation amounts to about 10 GJ tNH3−1 with a metal halide or zeolite material. At ammonia outlet concentrations above 1 mol%, the recycle cost is negligible.95 Additional details can be found in ref. 97.
The theoretical energy consumption is based on the heat of reaction for the formation of ammonia from H2O and N2via electrolysis of H2O to H2 and O2, with subsequent hydrogenation of N2 with H2. Furthermore, additional energy is required for mild excitation of N2 by the plasma, which is assumed to be 2.1 GJ tNH3−1 (see foornote b). This results in a total energy of 22.3 GJ tNH3−1 for the mild excitation case. When N2 and H2 are fully dissociated in the plasma, this requires 66.1 GJ tNH3−1. Combined with the 21.3 GJ tNH3−1 required in the base case, this results in a total energy consumption of 87.4 GJ tNH3−1 for the N2 & dissociation in plasma case.
|
Benchmark electrolysis-based Haber–Bosch process
|
33
|
26
|
21.3
|
7–9
|
|
Electrolysis-based Haber–Bosch processes with
|
Absorbent-enhanced synthesis loop |
47–50 |
30–35 |
— |
4–5 |
Non-thermal plasma technology with mild excitation |
155 |
50–65b |
22.3c |
1–3 |
Non-thermal plasma technology, N2 & H2 dissociation in plasma |
— |
— |
87.4c |
1–3 |
|
Electrochemical & photochemical synthesis
|
Electrochemical synthesis |
135 |
27–29 |
18.6 |
1–3 |
Photochemical synthesis |
— |
200 |
— |
1–3 |
|
Other technologies
|
Electro-thermochemical looping |
64 |
— |
55 |
1–3 |
Homogeneous catalysis |
900 |
— |
159 |
1–3 |
Modifying the Haber–Bosch process.
The first strategy towards ammonia production from nitrogen and hydrogen under milder conditions is the development of more active catalysts. Over the past five years, substantially more active Ru-based catalysts were developed,44,45,98–100 which can lower the minimum reaction temperature from about 350 °C to 200–250 °C.88 This is especially relevant for small-scale ammonia production, as the reaction heat in small-scale plants is usually not heat-integrated with the hydrogen production. Thus, operating under mild conditions decreases heat losses.
Even though milder temperatures can be achieved by using better catalysts, the condensation process is limited by the partial pressure of ammonia in the gas phase for separation at −20 °C to 30 °C.6 This leads to a minimum feasible pressure of about 100 bar.95 Operation at lower pressure is only feasible by using alternative methods for ammonia removal. A wide variety of sorbents have been researched, among which metal halides and zeolites are most promising.101,102 These solid sorbents allow for complete ammonia removal from the reactor effluent under milder pressures of 10–30 bar and at temperatures close to the temperature of the ammonia synthesis reactor, which is coined the absorbent-enhanced Haber–Bosch process.68,103,104 This may allow for operating the hydrogen and nitrogen production at the same pressure as the ammonia synthesis loop.6 Furthermore, ammonia may also be stored on the sorbents.105,106 The conditions for various ammonia separation technologies are listed in Table 3.
|
Condensation |
Metal halides |
Zeolites |
Separation temperature (°C) |
−20 to 30 |
150–250 |
20–100 |
Desorption temperature (°C) |
— |
350–400 |
200–250 |
Pressure (bar) |
100–450 |
10–30 |
10–30 |
Energy consumption (GJ tNH3−1) |
3–5 |
6–11 |
8 |
Ammonia at outlet (mol%) |
2–5 |
0.1–0.3 |
0.1–0.3 |
Ammonia capacity (wt%) |
100 |
5–30 |
5–15 |
Ammonia density (kg m−3) |
680 |
100–600 |
30–90 |
Chemical stability |
- |
Low/medium |
High |
TRL |
9 |
4–5 |
4–5 |
Novel ammonia synthesis methods.
In academia, research is being pursued into alternative methods for nitrogen fixation. The main research tracks involve electrochemical & photochemical ammonia synthesis,78–81 plasma-driven ammonia synthesis,82–84 homogeneous ammonia synthesis,66,85 and chemical looping approaches.86,87 Plasma-driven ammonia synthesis is discussed from section 3 onward and will not be discussed further in this section.
By far, most research has been conducted on electrochemical ammonia synthesis.78,79,110–112 This is due to the promise of reducing nitrogen directly from water and air (eqn (4)–(6)). Electrochemical ammonia synthesis only requires a relatively simple electrolysis setup, and both reactants can be generated in the same cell as the two opposing half-reactions.112 However, electrochemical ammonia synthesis remains an unsolved scientific challenge,112 due to the formation of hydrogen at lower overpotentials than ammonia over transition metals (see Fig. 5).113,114 Electrochemical ammonia synthesis suffers from the high bond strength of the dinitrogen molecule (941 kJ mol−1), as well as the large difference between the HOMO and LUMO in the molecule (1044 kJ mol−1),115 meaning that dissociation on the electrode surface is difficult. Furthermore, the solubility of nitrogen in aqueous electrolytes is limited, further favouring the formation of H2 rather than ammonia.14 The reported activities are so low, that ammonia impurities in the surroundings sometimes lead to false positives.116,117 Current strategies include the use of three-dimensional materials and bio-inspired materials, as well as the use of non-aqueous electrolytes.92,118,119
| H2O → 2H+ + ½ O2 + 2e− | (4) |
 |
| Fig. 5 Limiting potential for the nitrogen reduction reaction (NRR) and hydrogen evolution reaction (HER) over different transitions metals. Reproduced from ref. 113. | |
Photochemical ammonia synthesis has also gained interest in recent years, due to the potential simplicity of directly converting photons via electrochemical activation of N2 and H2O to ammonia.80 However, photochemical ammonia synthesis suffers from similar challenges as electrochemical ammonia synthesis, with the additional difficulty of supplying electrons by light.120 So far, research on photocatalytic ammonia synthesis has not yielded any promising results.81
Research has been conducted on homogeneously catalysed ammonia synthesis, which is mostly aimed at understanding and intensifying nitrogenase (the nitrogen fixation method of plants).66,85 The potential for practical application is limited for homogeneously catalysed ammonia synthesis (see Table 2). However, nitrogenase-like complexes may find applications for on-site fertilizer production on the seeds of plants.121
Chemical looping approaches have also been researched,86,87 inspired by the industrial Frank–Caro process in the early 20th century.18,19 Sometimes chemical looping approaches are used in electrochemical systems.122 By separating the nitrogen reduction, hydrogen oxidation and ammonia synthesis steps, it is possible to operate the individual steps at the optimal conditions to boost conversion and selectivity to ammonia. The main drawback is that every step occurs at different conditions, implying temperature sweeps within a cycle. Switching between these conditions decreases the energy efficiency of the full process.
3. Plasma catalysis
As discussed in section 2, decarbonizing and decentralizing ammonia synthesis requires novel methods for the conversion of nitrogen and hydrogen. Although electrochemical (and to a lesser degree photochemical) ammonia synthesis have received substantial attention in recent years, this remains a scientific challenge. Plasma activation of the stable N2 molecule is another alternative for electron-driven ammonia synthesis,83,123–126 inspired by the Birkeland–Eyde process of the early 20th century.17,18 Next to nitrogen fixation, plasma-driven conversion has attracted recent attention for CO2 conversion and methane coupling.83,125,127 In the current section, plasma technology is introduced, with a focus on nitrogen fixation to ammonia. Afterwards, reported activities, mechanisms and prospects for plasma-driven ammonia synthesis are discussed in sections 4–6.
3.1. Plasma properties
Plasma can be considered as the fourth state of matter, in which electrons, various types of ions, molecules and their derived radicals and excited species show collective behaviour, which is strongly determined by the influence of electrodynamics due to the charged particles.82,83,123 This state of matter is typically reached by adding energy to a gas. However, the transition is far more complex than the transitions between solids, liquids and gases.
Plasmas exist in a large variety. The type of plasmas used in plasma catalysis operate near room temperature up to several thousand K, and are typically partially ionized with ionization degrees of 10−4 to 10−6. The latter type of plasmas find many industrial applications, e.g. in microelectronics, coating deposition and lighting, as well as emerging applications in green chemistry, pollution control, gas conversion and medical applications.128
One important parameter identifying a plasma, certainly for applications of plasma catalysis as discussed in this review, is the so-called reduced electric field (E/N), i.e., the electric field strength (E, in V m−1) over the total gas number density (N, in m−3). E/N is mostly expressed in Townsend (Td), where 1 Td corresponds to 10−21 V m2. The reduced electric field determines the electron energy distribution function (EEDF), which gives the likelihood of finding an electron with a certain energy in the plasma.
Partially ionized plasmas, generated from a gas breakdown upon application of an electric field, are classified as non-thermal plasmas, because only the electron temperature is elevated far above room temperature. Furthermore, the gas molecules in the plasma can be rotationally, vibrationally or electronically excited, and the degree of excitation can be expressed by rotational, vibrational and electronic excitation temperatures. The electronic excitation temperature is typically comparable to the electron temperature, while the gas (translational) temperature, ion temperature and rotational temperature are also typically equal to each other. The vibrational temperature, however, can be elevated in a plasma above the gas temperature, i.e., when the vibrational levels are overpopulated compared to a Boltzmann distribution at the gas temperature. It is this concept which is often exploited in gas conversion applications to increase process efficiencies and yields.83,129,130
The various electron impact processes occurring in the plasma, and their corresponding rates, depend on the EEDF and the electron density, which in turn depend on the reduced electric field in the plasma. Next to rotational, vibrational and electronic excitation, ionization and dissociation of the gas molecules can occur as well. In Fig. 6, we plot the fraction of electron energy lost to those various processes in an N2/H2 (25/75%) gas mixture, as a function of the reduced electric field (bottom x-axis) and mean electron energy (top x-axis). Based on the electron impact collisions with N2 (Fig. 6(a)), we can identify three different plasma regimes:
• Regime I: Below 20 Td, where vibrational excitation of N2 is dominant.
• Regime II: Between 20 and 200 Td, where electronic excitation of N2 is most significant.
• Regime III: Above 200 Td, where ionization (mainly from N2 ground state to N2+) and dissociation are the most important N2 electron impact processes.
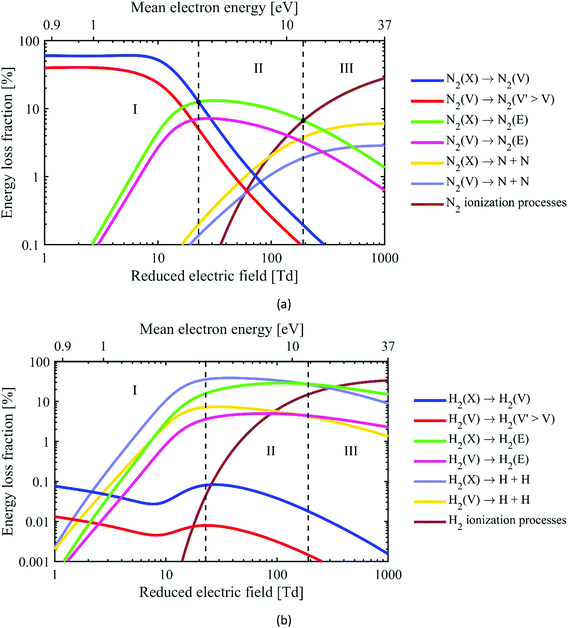 |
| Fig. 6 Fraction of electron energy transferred to various important electron impact collisions (i.e. vibrational excitation, electronic excitation, dissociation and ionization) in an N2/H2 25/75% mixture at 400 K and a vibrational temperature of 3000 K,131,132 as a function of the reduced electric field (bottom x-axis) and the corresponding mean electron energy (top x-axis), both for N2 (a) and H2 (b). Note the different y-axis between (a) and (b). The notations (X), (V) and (E) denote the ground state, vibrational levels and electronically excited levels of the molecules, respectively. | |
Note that this figure specifically applies to this gas mixture, and to a fixed gas temperature of 400 K and vibrational temperature of 3000 K; other assumptions lead to somewhat different borders between the different regimes, so they only give an indication, but are no hard numbers.
For the sake of information, we plot in Fig. 6(b) the same processes for H2. Note that vibrational excitation of H2 has a contribution less than 0.1%, in spite of its higher fraction in the gas mixture. On the other hand, electronic excitation and dissociation of H2 start to be important from much lower E/N values, because the H2 bond dissociation energy is much lower than for N2.
3.2. Feedstocks
Various feedstocks have been used for plasma-driven ammonia synthesis, but most research focuses on H2 and N2 as feedstocks. Furthermore, various authors researched plasma-driven ammonia synthesis from CH4 and N2 (e.g., the feedstock for the SMR-based Haber–Bosch process),133–136 as well as H2O and N2 (e.g., the feedstock for the electrolysis-based Haber–Bosch process).137–142 The challenge with using CH4, and even more with using H2O, is that the ammonia synthesis becomes endergonic. Although such a reaction can be driven by plasma, the energetically favourable reverse reaction is likely to compromise efficiency.
On the other hand, plasma technology may be a pathway to provide the energy required to form ammonia from H2O and N2, as the reaction is highly endothermic. Furthermore, H2O is a sustainable H2 source. However, a drawback of using H2O and CH4 as a hydrogen source is the presence of carbon or oxygen, implying that ammonia is not the only product of the reaction. In the case of CH4 and N2 as reactants, C
N-compounds such as hydrogen cyanide (HCN) are potentially formed, which are extremely poisonous and flammable. For the H2O and N2 as feedstock, other reaction products include NO2−, NO3−, and NH4+ in the aqueous phase and H2O2, NOx, O3 and H2 in the gas phase.137,138 The lowest energy consumption reported for NH3 from H2O and N2 is about 5600 GJ t-NH3−1.137 As follows from electrochemical ammonia synthesis, finding a catalyst selective for ammonia synthesis as compared to H2 production is an unsolved scientific challenge.116
3.3. Plasma reactors
Throughout the years, different kinds of plasmas have been studied for the plasma-catalytic synthesis of ammonia from N2/H2 feedstocks. In addition, N2/H2O non-catalytic plasma–liquid systems have recently been investigated for ammonia synthesis. In Fig. 7 we depict the accumulation of approximate number of publications on the various plasma sources through time.
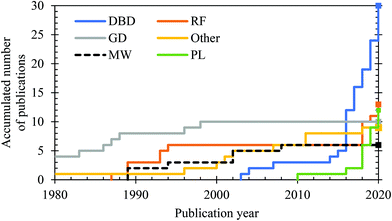 |
| Fig. 7 Approximate accumulated number of publications on ammonia formation from N2/H2 in the various plasma reactors studied throughout time, as well as from N2/H2O non-catalytic plasma–liquid systems. The listed plasma reactors are dielectric barrier discharge (DBD),96,131,142,143–149,150–159,160–169 (low pressure) glow discharge (GD),170,171,172–179,180 microwave plasma (MW),181–186 (low pressure) radio frequency discharges (RF),181–183,187–193,194–196 miscellaneous plasma reactors and devices (other),197–204 and plasma–liquid systems (PL).87,137,138–140,205–209,210,211 | |
A general consideration for the material choice of the plasma reactor is the corrosive nature of ammonia. Thus, carbon–steel and Cu-containing alloys should not be used. Stainless steel equipment is used for industrial ammonia synthesis, at partial ammonia pressures of up to 75 bar. In case of plasma-catalysis, partial ammonia pressures are substantially lower (typically in the order 0.01 bar). Thus, corrosion due to ammonia should not be a critical issue in plasma reactors.
Glow discharges (GDs; in direct current (DC) mode) are the simplest form of self-sustained gas discharges. They are created between two electrodes, i.e. a cathode and anode, to which a constant high potential difference is applied. Electrons are emitted from the cathode and accelerated towards the anode, causing collisions with the gas in the discharge tube. Electron impact excitation creates excited species, which emit photons upon decay to lower levels. This explains the name of these “glow” discharges. Electron impact ionization creates ions and new electrons. The combination of electron emission at the cathode and ionization in the bulk of the gas makes the discharge self-sustained. Such glow discharges are characterised by a well-defined plasma structure and the emission of light, i.e. a glow, at specific locations of the discharge. GDs can be created at low pressure, but also at atmospheric pressure.
Radio-frequency (RF) plasmas, typically operating at low pressure, can exist in capacitively coupled (CC) or inductively coupled plasma (ICP) mode. CC RF plasmas are in their simplest form also created by applying a potential difference between two electrodes, just like in low pressure GDs. The important difference is that the potential difference is not constant (direct current, DC), but alternating current (AC), with a frequency in the RF range (typically 13.56 MHz). In ICP RF plasmas, an electric current flows through a coil, which can be wound over the plasma reactor or placed on top of it, and it induces an RF electric field in the plasma. The ions only experience a time-averaged electric field, as their characteristic plasma frequency is typically lower than the applied RF frequency, while the light electrons can follow the fluctuating electric field, so they can be more accelerated, giving rise to more electron impact (electronic) excitation, ionization and dissociation of the gas molecules. Vibrational excitation is less important, because of high values of the reduced electric field.
Microwave (MW) discharges are another type of high frequency discharge, typically operating in the GHz regime. In contrast to GDs and CC RF discharges, the plasma reactor is electrode-less, and the power to break down the gas is delivered by the microwaves. Most common is a setup where the microwaves are transferred with waveguides to a quartz discharge tube through which the gas flows, but also other MW-based plasma setups are possible.212,213 MW discharges can operate from low pressure212 to atmospheric pressure.213 Upon increasing the operational pressure, the plasma becomes increasingly more thermal.
A dielectric barrier discharge (DBD) consists of two opposing electrodes with at least one electrode covered by a dielectric material (e.g., quartz or alumina). An alternating voltage is applied on the electrodes. Common voltage amplitudes are in the order of a few kV and the frequency is typically in, but not limited to, the kHz range.
DBDs for gas conversion applications operate in the filamentary regime with strong, temporally and spatially isolated small discharges throughout the gaseous discharge gap. The complexity of this filamentary behaviour leads to confusing nomenclature in literature. Section 3.4 provides an overview of the most common terms and the types of discharges that are observed in (packed) DBDs. In recent years, most plasma-based ammonia synthesis is performed in DBD reactors (see Fig. 7), because they operate at atmospheric pressure, they are very flexible and easily allow the integration of catalysts.
Besides plasma-catalytic ammonia synthesis, carried out in the above-described gas-phase plasma reactors, ammonia synthesis has recently also been realized in plasma–liquid systems, without using catalysts. This is usually accomplished by plasma jets, as typically used for plasma medicine applications.214 A plasma jet can operate in argon or helium, but also directly in air or N2 gas. The plasma is created inside a tube, consisting of (usually) two electrodes, through which the gas flows. Many different designs and geometries are possible, e.g., the powered electrode can be a ring-shape, needle, etc. The counter-electrode can be a ring, but the target to be treated (e.g., liquid in this case) can also act as counter-electrode. Due to the gas flow, the plasma can exit through a nozzle, creating an effluent, or jet. The jet comes into contact with the ambient atmosphere, causing the creation of various reactive oxygen and nitrogen species, or with a more controlled environment, e.g. pure N2, which is more interesting for ammonia synthesis. Due to the gas flow, the plasma effluent can reach the liquid, located at a distance of several mm from the tip of the plasma device, and the reactive plasma species can be transferred to the liquid phase. The reactive plasma species react with H2O molecule forming ammonia, but also NO3− and NO2−, among others, limiting the selectivity of the ammonia synthesis.
3.4. Discharge types
As mentioned above, DBDs relevant for plasma catalysis (and gas conversion applications in general) operate in the filamentary regime. The plasma exhibits small discharges, or micro-discharges, that do not encompass the complete discharge reactor, and which are often called filaments, i.e. thin conducting wires. Sometimes they are also called streamers. However, streamer discharges are not specific to occur in DBD systems alone.215,216 Wang et al. also described a micro-discharge between two packing beads as a local discharge,217 while Kim et al. used the term partial discharges218–221 after Mizuno et al.,222 and Butterworth et al. used the term point-to-point discharges.223
Surface streamers, surface discharges or surface ionization waves are terms used for micro-discharges that are observed after a streamer or filament reaches a surface, such as a packing bead. Once the micro-discharge reaches the surface, the discharge continues in a lateral expansion across the surface. This lateral expansion is facilitated by strong electric fields and the ionization processes taking place in the growth direction of the discharge.224,225
An afterglow normally describes the effluent of a plasma reactor. However, the term is sometimes used more broadly to indicate that (plasma) species are no longer exposed to plasma conditions corresponding to micro-discharges. Liu et al. described those two usages as a spatial and temporal definition, respectively.226
Homogeneous plasma or uniform plasma are terms that have been seen in relation to the filamentary regime of DBDs. This can be confusing because a DBD can operate in either a homogenous or in a filamentary regime. Still, the filamentary plasmas have been described as becoming more uniform, or more homogeneous when a packing is introduced.156 In addition, such a description has been used when the micro-discharges are still present, but of lower importance.163
Partial surface discharging, as used by Peeters et al.227 refers to the fact that not the whole surface area of the electrodes in a DBD reactor has to actively contribute to the discharge. This is due to the charge deposited on the electrode or dielectric surfaces being non-uniform or spatially isolated, due to the overall discharge consisting of small micro-discharges. This influences some electrical characteristics of the DBD.227 This effect is generally important in packed bed DBDs due to the obstructions in the plasma.
3.5. Coupling of plasma and catalyst
Coupling plasma and catalysis is complex. Previously, such mutual influences of the plasma and the catalyst were extensively discussed by Neyts et al.125,228,229 and Kim et al.219 Recent modelling investigations and characterization have provided novel insights.230,231 This subsection sets the stage for the assessment of plasma-catalytic ammonia synthesis.
Plasma-catalytic reactors are classified as in-plasma catalysis reactors or post-plasma catalysis reactors.90,219 In case of in-plasma catalytic reactors, also termed plasma-driven catalytic reactors, the plasma and the catalyst are located in the same position in the reactor.219 In case of post-plasma catalytic reactors, also termed plasma-assisted catalytic reactors, the plasma generation and the catalyst bed are separated in space.219 While in-plasma catalysis can be used to activate short-lived plasma-activated species over a catalyst, post-plasma catalysis is only relevant for long-lived species.219 Thus, plasma catalysis can benefit from the mutual influence of the plasma and the catalyst on one another.
3.5.1. Synergy and mutual influence.
Plasma catalysis sometimes leads to synergistic effects, in which the result of combining the plasma and the catalyst is larger than the sum of the individual contributions of the plasma and the catalyst.232 Synergy may be defined in terms of conversion, reaction rate or selectivity. It should be noted that in the case of ammonia synthesis, selectivity is not relevant because there are no by-products. However, plasma-catalyst interactions and synergies thereof are not trivial to uncover, as the underlying principles of plasma catalysis are not fully understood.231,233,234 Various possible plasma-catalyst interactions have been proposed for ammonia synthesis, as shown in Fig. 8.
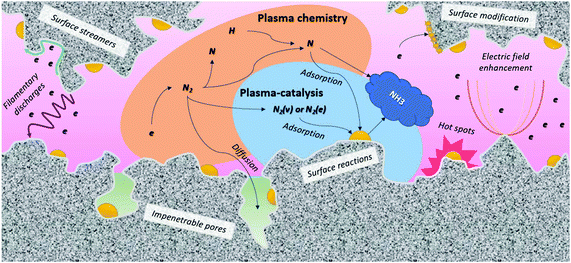 |
| Fig. 8 Plasma-catalyst interactions. Inspired by ref. 228. | |
A multidisciplinary approach is required to understand the mutual influence of the plasma and the catalyst,219 covering various time-scales and length-scales.90,231,235,236 So far, most information is obtained by macroscopic performance testing of plasma catalysis reactors. Van Durme et al.237 were the first to systematically categorize the mutual influence of a plasma and a catalyst, a topic heavily discussed thereafter.125,219,228,229,231,233,234 Possible mutual influences of a plasma and a catalyst have been reviewed by Kim et al.,219 Neyts et al.125,228,229 and Whitehead.231,233,234 The complexity is even more severe, as any change in the catalyst will induce changes in the plasma, which again influence the catalyst. Thus, effects in plasma-catalytic interactions can generally not be isolated.233,238
The various species present in the plasma environment include electrons, positive and negative ions, photons, radicals, and neutral atoms and molecules in ground state or excited in vibrational or electronic modes.90 These species may interact with the catalyst in various manners, and catalyst may influence the conversion of N2 and/or H2 in the presence of a plasma in three manners, namely (1) by modifying the plasma characteristics, (2) by exploiting the radicals from the plasma environment for reaction pathways other than simple recombination, or (3) via surface reactions of plasma-activated species on the catalyst surface.
The first mechanism, i.e. modifying the plasma characteristics, may influence the plasma chemistry far from the surface, when the catalyst is applied on dielectric packing material. A commonly encountered effect is the electric field enhancement and consequently a decreased plasma onset voltage, as was substantiated by simulations.230,239–241 The electric field enhancement will also enhance the electron temperature,230,239–241 which may shift the importance of various electron impact reactions, and thus affect the plasma chemistry. In addition, micro-discharges may form on the surface of the catalytic packing, or even the discharge may entirely move from the gas phase to the catalyst surface, depending on the dielectric constant of the packing beads.217,234
The second mechanism, i.e. exploiting the plasma radicals for reactions other than recombination, proceeds via facile adsorption on catalyst surfaces,90 without any barrier. In case of noble metals, all further reactions proceeding on the catalyst surface are downhill and the surface has either limited or no activating effect on the hydrogenation reactions. On the other hand, surface reactions can have a strong effect on the dominant reaction pathways and thus on the product distribution. This can even lead to increased conversion when the surface indeed favours reaction pathways to products over recombination reactions, forming back the reactants. The production of radicals and ions may also open alternative surface reaction pathways,228,242 that are not accessible in thermal catalysis. It should also be noted that radicals and ions in the plasma may react on the surface with other surface species which are formed via dissociative adsorption of non-activated molecules. This mechanism is discussed in more detail in section 5.2.
The third mechanism, i.e. surface reactions of plasma-activated species, is complex and often not well understood. Dissociative chemisorption can be enhanced via vibrational or electronic excitation of a molecule,123,243 decreasing the apparent activation barrier and increasing the reaction rate in case the dissociative adsorption step is rate limiting in thermal catalysis.96,244 A recent study also showed that vibrational excitation could enhance Eley–Rideal reactions of molecular species.245 Such reactions are typically negligible under thermal conditions and it is not fully understood to what extent they contribute to the total conversion under plasma conditions. These mechanisms and how they impact the total conversion and energy efficiency will be discussed in more detail in section 5.3.
Besides effects from the presence of reactive plasma species, the surface properties of the catalyst such as the work function and consequently the activity of the surface might be altered due to the presence of plasma, e.g., by the electric fields or surface charging.246–248 Physical modifications of the catalyst surface may also occur due to bombardment with energetic plasma species, causing reduction of the catalyst, coke formation, changes in the physicochemical properties of the catalyst (such as the catalyst work function), and the formation of hot spots. Furthermore, it was reported that surface cracking and peeling of metal nanoparticles can occur in DBD reactors.249 Similarly, changes in the surface morphology of a metal oxide catalyst after plasma treatment were reported after plasma-illumination in a DBD reactor.250
A pre-requisite for effective interaction between the plasma and the catalyst is that the plasma-activated species reach the catalytic surface before recombining or decaying to the ground state molecules.234 Plasma-activated species have a limited lifetime, and thus a limited traveling distance by diffusion, before recombining into neutral molecules, or decaying to the ground state.219 A direct interaction between the plasma and the catalyst surface is attained when the distance between the plasma and the catalyst surface is smaller than the maximum traveling distance of plasma-activated species.219 This is especially relevant when the catalyst is porous, as shown in Fig. 8. Large pores allow the generation of plasma inside the pores, but this is only possible for pores in the (sub-)micron range.230,251–253 Indeed, a prerequisite is that the pore size must be larger than the Debye length, which is defined by the electron density and temperature in the plasma. In helium, characterized by homogenous plasma, computer simulations revealed that plasma can only be formed in pores with diameters typically above 10 μm.252,254,255 On the other hand, molecular plasmas typically exhibit streamers, with higher electron density and smaller Debye length. Hence, computer modelling predicts that plasma streamers can propagate in pores of several 100 nm diameter, depending e.g., on the applied voltage.253,256 It should be noted that the majority of the pores in a typical support material are smaller than 50 nm. Therefore, only plasma-activated species with a sufficiently long lifetime can penetrate into the pores, while most other species recombine or decay to the ground state before reaching the active catalyst surface within the pores. Thus, the contribution of the external surface area is likely to dominate in most cases.
3.5.2. Catalyst selection considerations.
Depending on the plasma conditions and the chosen catalyst material, different plasma-activated species can determine the catalytic reactions (see Fig. 6). In order to optimize the plasma-catalyst synergy, it is crucial to couple the right catalyst to the right plasma.
In plasmas with a low degree of dissociation and a high degree of excitation (vibrational or electronic), plasma-activation is used to decrease the operating temperature for processes that are limited by dissociative adsorption. Typically, the optimal active metal is a more noble metal than the optimum for thermal catalysis, which desorbs reaction products easily and thus the operating temperature can be low. Dissociative adsorption of reactants is usually limiting the reaction rate for noble metals. Part of the activation barrier of dissociative adsorption may be overcome through vibrational or electronic excitation of molecules, explaining the plasma-enhanced catalytic activity over a noble metal. The catalyst still has an activating role in this case, as N2 is not fully dissociated in the plasma environment. Apart from metallic catalysts, metal nitrides have also been reported for ammonia synthesis.47,257 Plasma-activation of metals with nitrogen plasmas may yield metal nitride catalysts.258 Hargreaves46 recently reviewed metal nitride catalysts active for ammonia synthesis.
In plasmas with a higher degree of dissociation, the ideal catalysts will usually be very different from those used in thermal catalysis. Plasma-generated radicals do not need to be dissociated over a surface, as dissociation already occurs in the plasma. Thus, the surface influences recombination reactions, as well as consecutive reactions with e.g. H atoms on the catalyst surface. Plasma activation of reactants via formation of radicals often opens pathways that are thermodynamically impossible for ground state reactants; in that case the use of traditional catalysts is likely to be counterproductive as these will catalyse the reverse reaction, back to reactants. Several materials may enhance reaction pathways, such as consecutive reactions with H atoms forming ammonia, instead of recombination of radicals to N2. Transition metals may be used to hydrogenate the adsorbed NHx (x = 0–2) radicals. For these catalysts, efficient plasma-activation of reactants towards radicals is required.259 Therefore, the choice of the catalyst is less determined by chemical properties and more by properties influencing the discharge characteristics (e.g. dielectric properties and morphology), thereby influencing the plasma-phase dissociation of activated molecules. A method to modify the plasma by radicals was proposed by Akay et al.,152,168,260 who used a mix of a dielectric material with a supported transition metal catalyst in the plasma reactor. The dielectric material acts as a plasma catalyst promoter (PCP), which modifies the plasma characteristics, whereas the transition metal catalyst performs the catalytic function.
Apart from the choice of the active metal, the choice of the support and promoter composition affect the activity in some cases.96 As plasmas can only be generated in (sub)-micron pores (cf. previous section), oxides with highly porous structures with pore sizes below 1 μm and large internal surface areas are not beneficial for maximum interaction between the active metal catalyst and the plasma (see Fig. 8).230 This is very different form thermal catalysis, requiring an as high as possible active surface area and therefore support materials with high surface area, in order to maximize the productivity per unit of volume of chemical reactors.
4. Assessment of plasma-driven ammonia synthesis
This section provides an overview of the most significant developments in plasma-driven ammonia synthesis, with a focus on the coupling between fundamentals from heterogeneous catalysis and plasma catalysis. This forms a framework for plasma-driven ammonia synthesis, and the mechanisms involved. Extensive historical accounts can be found in other reviews.82,84,90,141,261 The aim of this section is to show how recent insights in mechanisms can aid in the development of the field. The energy efficiency and conversion for various plasma reactor types are compared, describing the state of the art. The discussion on the mechanisms and catalyst selection is coupled with the energy efficiency.
4.1. Performance in various types of plasma reactors
Plasma-driven ammonia synthesis was first independently reported by Morren and Perrot in a DBD reactor in 1859,262 two years after the first report of plasma-driven conversions with a DBD reactor by Werner von Siemens.263 In the late 19th century, various authors attempted plasma-driven ammonia synthesis, among whom Berthelot.262 Furthermore, ammonia was first synthesized in a glow discharge by Donkin in 1973.264 In general, however, plasma-driven ammonia synthesis was sporadically researched until the 1980s.262,265,266 Between 1980 and 2000, low pressure glow discharges (LPGDs) received a lot of attention.170,171,173–180,181–183,267–272 In these publications, the surface (both catalytic and non-catalytic) was often related to the ammonia formation. Ions, more specifically N2+ and N2H+, were often mentioned to play an important role in the formation of ammonia. Nowadays, atmospheric pressure DBDs are studied most, although some papers also describe low pressure MW and RF discharges.181–183,187,190–192,194–196
A summary of quantified plasma-driven conversions to ammonia in various plasma reactors under a wide variety of conditions is shown in Fig. 9. An energy yield of 100–200 g-NH3 kW h−1 is required to be competitive with alternative technologies for small-scale ammonia synthesis.90 Furthermore, an ammonia concentration of about 1.0 mol% (10
000 ppm) is required to minimize the energy cost of separation and recycling in case of an atmospheric synthesis loop,95 as an ammonia partial pressure of 0.01 bar is required for effective ammonia removal in solid sorbents.103,273–275 Therefore, low pressure plasma reactors such as MW and RF plasmas require a near complete conversion at an energy yield of 100–200 g-NH3 kW h−1, because separation of ammonia is not feasible. The highest energy yield reported so far is 37.9 g-NH3 kW h−1.165 Hereafter, plasma reactors for ammonia synthesis from H2 and N2 are discussed.
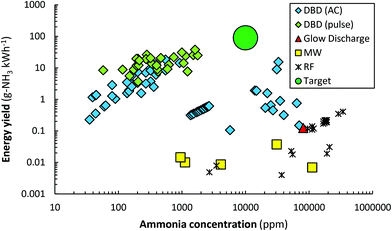 |
| Fig. 9 Reported energy yield vs. ammonia concentration. Constructed and extended from ref. 96. Original references: DBD (AC),144,146–148,151–153,159,164–166,169,276,277 DBD (pulse),158,165 Glow Discharge,174 MW186,278,279 and RF.182,187,188,190–192,194 In some cases, the reported units have been converted to g-NH3 kW h−1 for the energy yield, and ppm for the ammonia concentration. We refer the reader to the recent review of Carreon261 for the reported energy efficiency for specific metals. | |
4.1.1. DBD reactors.
Most literature is available on plasma-driven ammonia synthesis in a DBD reactor. Already in 1859, Morren and Perrot reported experiments with a DBD reactor.262 Modern attempts at plasma-driven ammonia synthesis in DBD reactors date from the 1950s, 1960s and beyond.265,266 Especially since 2000, research on plasma-catalytic ammonia synthesis is mostly performed in DBD reactors.82,84,261 Various reactor configurations without and with packed bed have been attempted. An overview of the energy yield vs. ammonia concentration for various packing materials is shown in Fig. 10.
Electrode materials.
Various authors have researched either ammonia synthesis, or ammonia decomposition, with various electrode materials.150,153,174,266,280 Iwamoto et al.153 attributed a trend in ammonia synthesis rate for wool-like electrodes to the binding strength of Nads on the metal surface. On the other hand, Yin et al.174 reported that the ammonia yield increases with increasing electron work function of the electrode material. An increased electron work function implies that the electrons released upon discharging have a higher energy, making dissociation of N2 in the gas phase more likely.
Oxides.
A drawback of a DBD reactor without a packing is the high ratio between plasma volume and surface area for catalytic reactions. Therefore, most authors introduced packing materials, such as oxides,143,146,155,161,162,167,199,281 dielectric materials,146,149,161,166 and ferro-electrics.147 Introducing a packing material can lower the discharge power required to ignite the plasma. Furthermore, the presence of a packing material can alter the plasma discharge characteristics.149,161 Surface functionalization of the oxide can also alter the plasma discharge characteristics.149 The capacitive and discharge regimes can be modified by the dielectric constant of the material.161
Ru-Catalysts.
The presence of supported metal particles may introduce hydrogenation sites for atomic nitrogen and/or molecular N2. Ru-Catalysts have been studied most among supported metal catalysts.90,96,131,144,145,148,151,159,160,165,169,282 Ru-Catalysts are known to have a high activity for ammonia synthesis under mild conditions.41,283 The rate-limiting step for thermos-catalytic ammonia synthesis over Ru-catalysts is usually the dissociation of N2.41 Ru-Catalysts were first used in a membrane-like DBD reactor by Mizushima et al.144,145 Afterwards, various authors attempted to disentangle the complexity of reactions in plasma-driven ammonia synthesis in a DBD reactor packed with Ru-catalysts.90,96,148,151,159,160,165,169,282
In order to distinguish between the rate of homogenous plasma-chemical ammonia synthesis, and the rate of heterogeneous plasma-catalytic ammonia synthesis over the Ru-catalyst, it is important that the rate in a DBD reactor packed with the bare support is low. For this reason, various authors reported conversions for the bare support, as well as the supported Ru-catalysts (sometimes with promoters).148,151,282 Furthermore, various authors reported that the ammonia synthesis rate depends on the temperature.90,96,165,282 Catalytic hydrogenation of nitrogen is possible only at sufficient high temperature, allowing for ammonia desorption. Below this onset temperature, plasma-driven ammonia synthesis must be attributed to plasma chemistry rather than catalysis.282
Various authors introduced alkali promoters,96,148,151,165 which are known to enhance N2 dissociation by lowering the N2 dissociation barrier, as well as to enhance ammonia desorption for thermal-catalytic ammonia synthesis.40,41,284–286 The highest reported energy yield for such a system is 37.9 g-NH3 kW h−1,165 which is overall the highest reported energy yield to date (see Fig. 10). In case of plasma catalysis with molecular plasma-activated N2, promoters can enhance the N2 dissociation rate and thereby the ammonia synthesis rate.96 However, in case the reaction proceeds via adsorption of NHx (x = 0–2) radicals, the introduction of alkali promoters does not influence the conversion, apart from less desorption limitation of ammonia in the low temperature regime.282
Other metal catalysts.
Next to Ru-catalysts, other supported metal catalysts were tested for plasma-catalytic ammonia synthesis (and ammonia decomposition).131,152,156,157,159,168,276,277,279,280,287–292 In most cases, supported Co, Ni, and Rh catalysts are found to be most active among the tested catalysts.131,156,159,276,277 Such metals have less ammonia desorption limitations than the classical Fe and Ru catalysts for thermal-catalytic ammonia synthesis. Mehta et al.131,293 proposed that plasma-activation of N2via vibrational excitation leads to a lower barrier for N2 dissociation, resulting in an enhancement for late-transition metals which are typically rate-limited by N2 dissociation. On the other hand, Wang et al.156 proposed that the introduction of metal nanoparticles on γ-Al2O3 changes the acid site strength, and thereby the ammonia synthesis rate on γ-Al2O3 acid sites. Herrera et al.157 reported that the introduction of metal nanoparticles on γ-Al2O3 has a statistically insignificant difference in macroscopic discharge characteristics in the charge voltage characteristics compared to bare γ-Al2O3. Akay et al.152,168 reported increased ammonia yield on introduction of dielectric materials in a physical mixture with supported Co and Ni catalysts, altering the plasma discharge characteristics.
Other packings.
Solid sorbents have also been used for plasma-driven ammonia synthesis.158,164 The ammonia is removed in situ, lowering the ammonia content in the plasma zone, thereby increasing the chance of activating the H2 and N2 reactants rather than the ammonia product. Metal halides, such as MgCl2, can absorb ammonia in a solid solution, forming Mg(NH3)xCl2.294 Peng et al.158 reported an energy yield of 20.5 g-NH3 kW h−1 in the presence of a MgCl2 sorbent. However, from XRD it was confirmed that Mg3N2 was primarily formed, rather than Mg(NH3)xCl2. Zeolites are also proposed as a solid sorbent for ammonia.105,109,274 Shah et al.164 reported an ammonia concentration of 3.3% at 15.5 g-NH3 kW h−1 energy yield in the presence of zeolite 5A, which is among the highest energy yields reported so far and the only reported energy yield above 10 g-NH3 kW h−1 in combination with an ammonia concentration above 1.0% (see Fig. 10). A chemical looping system based on MgO and Mg3N2 was also proposed by Zen et al.295,296 Membrane reactors have also been proposed to either remove the ammonia or to feed the H2 from the other side of the membrane.144,145,297
4.1.2. Radiofrequency plasma reactors.
Reactors operating under radiofrequency (RF) plasma excitation have been researched to a lesser extent, as compared to DBD reactors,261 but have recently gained substantial attention in several research groups.190–196,298 In the late 1980s and early 1990s, Uyama et al. and Tanaka et al. used zeolite182,187 as well as Fe183,188 and Mo183 wires as catalyst in the downstream of their low pressure (650 Pa) RF plasma apparatus. Fe catalysts resulted in the highest product yield. They are the only authors to report the formation of both ammonia and hydrazine182,183,188 and speculated that the H and NHx radicals formed in the discharge are the main adsorbates.183
Recently, Ben Yaala et al.193,195 placed W and stainless steel catalysts in their low pressure (2 Pa) RF plasma reactor. They reported the thermal decomposition of ammonia at high temperature (above 830 K on W) and the creation of stables nitrides (starting at 650 K on stainless steel), inhibiting ammonia formation.195
Shah et al.190–192,194 placed a catalyst bed very close to the plasma electrodes in a low pressure (40 Pa) RF plasma setup. They studied various transition metal based catalysts,191,194 Ga alloys192,194 and a Ni–MOF (metal organic framework).190 Within the metals, Ni and Sn based catalysts were the most active.194 However, the Ni–MOF performed better than pure Ni, which was attributed to the porosity.190 Ga alloys, both Ga–In192,194 and Ga–Pd,194 gave the best results.192 The ammonia synthesis rate was directly correlated to the H atom radical density.192,196 Shah et al.191 also reported on modelling work, from which the mechanism for plasma-catalytic ammonia synthesis in RF reactors was disentangled. Both N2 and H2 dissociate in the plasma, after which N adsorbs on the surface. Subsequently, the adsorbed N atoms are hydrogenated by H atoms on the surface or in the gas phase, i.e., the model revealed that both Langmuir–Hinshelwood reactions and Eley–Rideal-reactions play a role.191
4.1.3. Microwave plasma reactors.
Low pressure (60–600 Pa) plasmas ignited with microwaves (MWs, i.e., GHz frequency range) have received considerably less attention for ammonia synthesis compared to both RF discharges and DBDs.261 Uyama et al.181–183,189 studied MW plasmas with catalyst downstream. They found the performance of their MW plasma to be superior to their RF discharge.182,183 Unlike the RF discharge, there was no significant hydrazine yield. This was attributed to a difference in plasma radicals created in the discharge. The RF discharge caused the adsorption of H and NHx radicals, while the MW plasma caused the adsorption of N radicals.183 Kiyooka et al.198 explored an electron cyclotron resonance plasma, which also operates within a GHz frequency range and at low pressure (600 Pa). They found that N and NH radicals adsorb onto the stainless steel reactor walls and report further hydrogenation on the surface due to H radicals in the plasma (i.e., Eley–Rideal mechanism) until the desorption of ammonia.198
Siemsen279 performed experiments and simulations for a MW plasma reactor with downstream Rh catalyst bed. Due to the long distance between MW plasma and catalyst, the excited N2 molecules do not reach the catalytic surface, and only atomic radicals remain. Simulations revealed that the atoms account for the formed ammonia. Ammonia was not formed without catalyst.279 Jauberteau et al.184 reports that the adsorption of NH onto the stainless steel reactor walls is the first reaction step towards ammonia, from which either ammonia or adsorbed NH2 is formed.
To date, only two studies considered ammonia synthesis in atmospheric pressure MW plasmas,186,278 despite the more beneficial process conditions for industrial application. However, the highest energy yields, i.e., 0.4 g-NH3 kW h−1 (see Fig. 9), have been reported for pressures as low as 10−4 bar. In addition, the reported energy yields of MW plasma reactors are orders of magnitude lower than for DBD reactors (see also Fig. 9). The reason may be that the temperatures, even downstream in the afterglow of a MW plasma, are too high for adsorption on a catalyst surface, due to (i) catalytic stability problems, but also (ii) a fundamental limitation, because adsorption always leads to loss in entropy and therefore is exothermic, implying that the equilibrium is unfavourable at very high temperatures.
4.1.4. Glow discharges.
Various authors have researched glow discharges for ammonia synthesis over the past one and a half centuries.170,171,173–177,264,299,300,301 Donkin reported ammonia synthesis in glow discharges as early as 1873,264 after which Brewer et al. published more systematic studies with a batch process in 1929 and 1930.170,171,299 Most research has been conducted on low-pressure glow discharges (LPGDs). In 1968 and 1969, Eremin et al.300,301 considered that the wall may have an effect for ammonia synthesis, and they were the first to deliberately add catalytic materials on the reactor wall. From 1980 onward, various authors investigated a wide range of transition metals, alloys and metal oxides.173–176,302 Coupling with catalysts is possible in glow discharges, both in a packed bed and on the walls of the reactor or the electrode.
The mechanism for ammonia synthesis from H2 and N2 in glow discharges has been debated over the years. Brewer et al.170 proposed that ammonia is primarily formed in the plasma phase. On the other hand, Eremin et al.300,301 and Venugopalan et al.173,174,176 proposed that ammonia is primarily formed on the reactor wall, which acts as a catalytic surface, as substantiated by experimental data. Venugopalan et al.173,174,176 and Sugiyama et al.175 proposed that N atoms are the relevant species for ammonia formation, rather than plasma-activated molecular N2 species.
4.1.5. Arc discharges.
Arc reactors such as static arc discharges and gliding arc reactors can also be used for ammonia synthesis, inspired by the commercial Birkeland–Eyde process for NOx production.17 An advantage of gliding arcs is the scalability.277 However, research conducted on ammonia synthesis in this type of reactor is limited.197,201,202,303,304 Brewer et al.197 first published on the application of low voltage arcs for ammonia synthesis in 1931. A detailed study on ammonia synthesis in an arc plasma was conducted by van Helden et al.201,202 Implementing catalysts in arc reactors, for in-plasma catalysis, is not feasible, due to the excessive temperatures. However, post-plasma catalysis is possible, as demonstrated for other reactions, but has not yet been explored for ammonia synthesis in this type of plasma reactors.219
4.1.6. Plasma–liquid systems.
Besides plasma-catalytic ammonia synthesis, ammonia has recently also been generated in plasma–liquid systems, albeit without using catalysts. In 2010, Kubota et al.210 first reported ammonia synthesis in a plasma–liquid system. It is obvious that using H2O as a feedstock is more energy demanding than H2.67 On the other hand, these very simple plasma setups allow the immediate accumulation and potential storage of ammonia in H2O, the most benign solvent.
A combined plasma-electrolytic system was proposed for ammonia formation from H, generated from either H2O molecules or H+ ions, by Kumari et al.,205 Hawtof et al.,139 Haruyama et al.206–209,211 and Peng et al.138,140 Ammonia was formed by direct interaction of air or N2 plasma with H2O, allowing simpler reactors, i.e., no need for counter electrodes in liquids and additional electrolysis. Gorbanev et al.137 used an atmospheric pressure plasma jet with N2 containing H2O vapour, in contact with liquid H2O. The system offers a selectivity to ammonia of up to 96%, at energy yields up to 0.65 g-NH3 kW h−1.137 Experiments without direct plasma–liquid interaction and with isotopically labelled water revealed the major role of H2O vapour in the feed gas, rather than liquid H2O, as H-source for the ammonia synthesis.137 There was some interaction of plasma effluent with the plasma-exposed liquid H2O, but the latter decreased dramatically when H2O vapour was introduced in the N2 feed gas.137
5. Mechanisms of plasma-driven ammonia synthesis
Various mechanisms are conceivable for plasma-driven ammonia synthesis, in the absence and in the presence of a catalyst. A distinction is made between plasma chemistry pathways with N atoms generated in the plasma, either reacting in the plasma phase or over the catalytic surface,154,191 and the catalytic dissociation of excited nitrogen molecules.96,131 This distinction is made to assess the role of the catalyst. The energy requirement of various pathways is assessed, from which we suggest that only dissociation over a catalyst (and not beforehand in the plasma phase) has the potential to become sufficiently energy efficient for practical applications. Plasma chemistry mechanisms with experimental validation are discussed. The optimal H2
:
N2 ratio for various mechanisms is discussed from both plasma chemistry and heterogeneous catalysis perspectives.
5.1. Plasma phase ammonia synthesis
The plasma phase ammonia synthesis is defined by the conversion taking place in the bulk plasma, away from the surface. In this case, the packing material does not behave as a catalyst (i.e., actively contributing to the conversion process), and merely alters plasma characteristics and flow patterns in the reactor. The ammonia is formed through hydrogenation of nitrogen dissociated by the plasma.
In practice, plasma phase ammonia synthesis is difficult to disentangle from reactions on a surface, as even in the absence of packing material, the reactor walls may play a role in converting plasma-generated species on the wall.
Even though ammonia synthesis is exergonic at ambient conditions,285 the reaction does not proceed spontaneously. Both the bonds in molecular hydrogen and molecular nitrogen need to be ruptured for ammonia formation in the gas phase. This can be accomplished by high-energy electrons in the plasma, but at the same time, these high input powers do not only affect the N2 molecules but can also decompose the produced ammonia. The minimum energy requirement for ammonia formation from plasma chemistry is 66.1 MJ kg-NH3−1 (equivalent to 54.4 g-NH3 kW h−1), which is due to the energy required for rupturing the N2 and H2 bonds by the plasma (27.7 MJ kg-NH3−1 and 38.4 MJ kg-NH3−1, respectively, see Table 4). As discussed in section 4.1, the energy yield of 54.4 g-NH3 kW h−1 is too low for practical applications. This clearly shows the need for a catalyst. As shown in Table 4, only partial activation of N2 by vibrational or electronic excitation may allow for a lower energy requirement. In this case, both the plasma and the catalyst have a role in the N2 dissociation reaction (see section 5.3).
Table 4 Energy requirements for various plasma-activations of N2 and H2. Partially adapted from ref. 82
|
Reaction |
N2/H2-based |
NH3-based |
kJ mol−1 (eV) |
MJ kg−1 |
kW h kg−1 |
g kW h−1 |
Dissociation
|
N2 dissociation |
N2 + e → 2N + e |
945 (9.79) |
27.7 |
7.7 |
129.8 |
H2 dissociation |
H2 + e → 2H + e |
436 (4.52) |
38.4 |
10.7 |
93.7 |
N
2
& H
2
dissociation
|
|
|
66.1
|
18.4
|
54.4
|
Ionization
|
N2 ionization |
N2 + e → N2+ + e |
1505 (15.6) |
44.2 |
12.3 |
81.5 |
H2 ionization |
H2 + e → H2+ + e |
1485 (15.4) |
130.8 |
36.3 |
27.5 |
N
2
& H
2
ionization
|
|
|
175.0
|
48.6
|
20.6
|
Excitation
|
N2 vibrational excitation |
N2(X) → N2(X v = 1) |
28.0 (0.29) |
0.8 |
0.2 |
— |
N2 electronic excitation |
N2(X) → N2(A3) |
595.1 (6.17) |
17.5 |
4.9 |
— |
5.2. Surface-enhanced plasma-driven ammonia synthesis
In the presence of a surface, ammonia may be produced from molecular N2 and H2, or from plasma-generated radicals, depending on the plasma conditions and the catalytic properties of the material at a given temperature and pressure. In the current section, we discuss the conversion of plasma-generated radicals to ammonia over a catalyst, which is coined surface-enhanced plasma-driven ammonia synthesis (SEPDAS).96 In section 5.3, we elaborate on the conversion of plasma-activated molecular N2 to ammonia over a catalyst, which is coined plasma-enhanced catalytic ammonia synthesis (PECAS).96
If plasma-generated radicals adsorb on the catalyst surface, they can react to form ammonia. However, N, NH, and NH2 radicals can also recombine to N2 and H2. The rate of ammonia synthesis versus recombination reactions towards H2 and N2 depends on the barriers of the relevant surface reactions on the catalyst surfaces. The number of possible surface reactions is much greater than the reactions listed in Table 1 for thermal catalysis, as these also include the reactions of all the different unique species generated in the plasma. The possible surface reactions in case of surface-enhanced plasma-driven ammonia synthesis are listed in Table 5.
Table 5 Possible surface reactions for surface-enhanced plasma-catalytic ammonia synthesis and plasma-enhanced catalytic ammonia synthesis. The * denotes an adsorption site on the catalyst
|
Reaction |
Note |
Hydrogen adsorption |
H2 + 2* ⇌ 2H* |
|
H + * ⇌ H* |
Nitrogen adsorption |
N2 + 2* ⇌ 2N* |
Dominant for PECAS |
N + * ⇌ N* |
Dominant for SEPDAS |
NHx adsorption |
NH + * ⇌ NH* |
Dominant for SEPDAS |
NH2 + * ⇌ NH2* |
NH3 desorption |
NH3* ⇌ NH3 + * |
|
Surface hydrogenation reactions |
N* + H* ⇌ NH* + * |
|
NH* + H* ⇌ NH2* + * |
NH2* + H* ⇌ NH3* + * |
Eley–Rideal-reactions |
N* + H ⇌ NH* |
|
NH* + H ⇌ NH2* |
NH2* + H ⇌ NH3* |
H* + N ⇌ NH* |
H* + NH ⇌ NH2* |
H* + NH2 ⇌ NH3* |
It should be noted that this scheme presents a case of the second mechanism explained in section 3.5.1, i.e., exploiting the plasma radicals for surface reactions other than recombination. Engelmann et al.305 developed a microkinetic model for plasma-catalytic ammonia synthesis including plasma-produced N atoms, radical NHx species and vibrationally excited N2. From various models it follows that the N2 dissociative adsorption is no longer rate-limiting for ammonia formation. The hydrogenation reactions on the surface become rate-limiting for the ammonia formation rate, as substantiated with DFT calculations,131,191,305 and experimental data.191,282 In principle, the hydrogenation rate increases with decreasing nitrogen binding strength (i.e., nobler catalysts). However, the N2 recombination rate is also enhanced for noble catalysts.305 This is due to a decrease in the barrier for N2 recombination from 2N* for catalysts with a decreased nitrogen binding energy (EN).306 Thus, the measured activity is the result of competition between hydrogenation on the catalyst to form ammonia and recombination reactions of 2N* to form N2. However, the density of H atoms in the plasma phase is typically higher than the density of N atoms, which results in a build-up of adsorbed H atoms, promoting the hydrogenation reactions. It should be noted that most transition metals do not have a barrier for H2 dissociation, resulting in a high coverage of hydrogen for thermal catalysis, unless N2 is dissociated at sufficient rates.306
DFT calculations show that Eley–Rideal-type reactions (N* + H → NH* or H* + N → NH*) may also be relevant for surface-enhanced plasma-driven ammonia synthesis,305 due to low enthalpy barriers for these reactions (<30 kJ mol−1).194 In thermal catalysis, Eley–Rideal reactions are typically not considered because of entropic reasons. Stable reactant molecules would not only have to overcome the appropriate reaction barrier, they would also need to approach the active site in the right orientation and direction. In the case of plasma-generated N and H atoms, incoming angles are less important, and Engelmann et al.,305 suggested by means of DFT calculations that the reactions are barrierless on all transition metals. Shah et al.191 combined modelling work and experimental work, from which the authors concluded that the Eley–Rideal-like reaction H + N* → NH* is important for ammonia synthesis over an Fe catalyst in a low pressure RF plasma. The subsequent hydrogenation steps primarily occur over the Fe catalyst via a Langmuir–Hinshelwood mechanism,191 while the contribution of Eley–Rideal-like mechanisms may increase with increasing plasma power and pressure. Ben Yaala et al.193 performed a series of chemical looping experiments to gain insight in the mechanisms of ammonia synthesis in low pressure RF plasma on a W catalyst. They reported the highest yields for the H2
:
N2 = 1
:
1 gas fraction and concluded that the Eley–Rideal reaction H + N* → NH* is a crucial step for the formation of ammonia under these circumstances. It should be noted that W binds nitrogen strongly, which means that the hydrogenation steps are strongly uphill, implying it is not a typical catalyst considered for ammonia synthesis.
Hong et al.82 also studied the plasma-catalytic ammonia synthesis for different plasma regimes. Their models include significantly more plasma-generated species, but with approximated values that make quantitative evaluation difficult. They concluded that mechanistically the pathways are determined by the abundant amount of H atoms adsorbed to the surface, and they propose that Eley–Rideal reactions are essential in plasma catalysis. They proposed the formation of NH in the plasma, with a subsequent NH + H* → NH2* reaction, followed by hydrogenation of NH2* via a Langmuir–Hinshelwood mechanism over the surface.
A DBD typically operates in the filamentary regime (i.e., characterized by micro-discharges) when used for ammonia synthesis. Therefore, Van ‘t Veer et al.307 developed a model explicitly considering the role of the micro-discharges and their afterglows, i.e. the weaker plasma in between the micro-discharges, in the ammonia formation mechanisms; see definitions in section 3.4. The calculations revealed that, while dissociative adsorption initially determines the major adsorbate, the plasma radicals, and especially the N atoms, actually determine the ammonia formation rate. Thus, electron impact dissociation of N2 in the plasma, followed by N adsorption, and not N2 dissociative adsorption at the catalyst surface, was identified as the rate-limiting step for ammonia formation in the DBD plasma at the conditions under study. Eley–Rideal type reactions played an overall important role, especially in the formation of NH(s). Further hydrogenation at the catalyst surface yielded ammonia. The afterglows in between the micro-discharges were found to be responsible for the net ammonia production, because during the micro-discharges ammonia is destroyed more (by electron impact dissociation) than it is formed. It should be noted that the mechanism in a DBD highly depends on the plasma and catalyst properties, as Rouwenhorst et al.96 showed experimentally that the dissociative adsorption of plasma-activated N2 is dominant in DBD plasmas at low energy input, while dissociation of N2 in the plasma dominates at high energy input.96,282
Summarizing, the fraction of N, H, and NHx radicals depends on the specific energy input (SEI). In turn, the density of these plasma-generated radicals appears to determine whether Langmuir–Hinshelwood mechanisms, or Eley–Rideal-like reactions, or even plasma phase reactions are dominant.
Similar to plasma phase ammonia synthesis, the minimum energy requirement is 66.1 MJ kg−1 in case of surface reactions with N and H atoms generated in the plasma (equivalent to 54.4 g-NH3 kW h−1, see Table 4). It should be noted that some catalysts are not able to dissociate N2 at sufficient rates, while H2 is readily dissociated on many metals. The minimum energy requirement in that case is 27.7 MJ kg−1 (equivalent to 129.8 g-NH3 kW h−1, see Table 4). This is above the minimum required energy yield of 100 g-NH3 kW h−1, and potentially interesting for practical applications. It should be noted, however, that both H2 and N2 are activated when co-feeding both reactants, so that plasma reactor designs with primarily N2 activation are required. Strategies for catalyst design for surface-enhanced plasma-driven ammonia synthesis were discussed in section 3.5.2.
5.3. Plasma-enhanced catalytic ammonia synthesis
Energetically, it is beneficial to prevent full dissociation of the reactants by the plasma (see Table 4). Therefore, research has recently focused on enhancing the dissociative N2 adsorption on catalysts via vibrational or electronic excitation, following the modelling work of Mehta et al.131 The authors postulated that dissociative N2 adsorption is enhanced upon vibrational excitation, while the subsequent hydrogenation steps and ammonia desorption are not affected by plasma activation.131 The authors predicted that the ammonia synthesis can be enhanced for metals that bind atomic nitrogen weakly on the catalyst surface (high EN in Fig. 11),131 given that N2 activation is usually the rate-limiting step for ammonia synthesis. This is based on microkinetic models that incorporate the potential influences of vibrational excitations in N2, based on density functional theory (DFT) data available in literature (see Fig. 11). The vibrational energy is often not sufficient for dissociation in plasma phase, due to the large amount of energy needed to break the N2 triple bond (9.79 eV), although vibrationally induced dissociation is reported for some types of plasmas.308,309 Conversely, the energy barrier for the catalytic dissociation of N2 on transition metals is considerably lower, e.g. 1.5 eV on Ru(111),310 and vibrational excitation will have relatively more impact on dissociation on these metals.
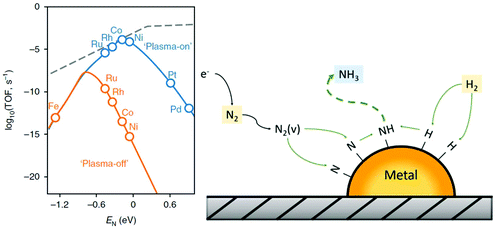 |
| Fig. 11 Left: Proposed effect of plasma-induced N2 activation on the catalytic activity at T = 200 °C and 1 bar over step sites. The dashed line represents the maximum possible hydrogenation rate. Reproduced from ref. 131. Right: Proposed mechanism for plasma-enhanced catalytic ammonia synthesis via plasma-activated N2 dissociation. Reproduced from ref. 96. | |
Rouwenhorst et al.96 substantiated this claim with a kinetic analysis for Ru-based catalysts in a DBD reactor. In case of thermal catalysis (i.e., without a plasma), the apparent activation barrier of ammonia synthesis is about 60–115 kJ mol−1, which can be attributed to the dissociation of N2.42,283 Upon plasma activation, the authors found that the apparent activation barrier for ammonia synthesis decreased to about 20–40 kJ mol−1, which was attributed to a lower barrier for N2 dissociation.96 It is observed that the ammonia synthesis rate increases upon addition of an alkali promoter, both in thermal catalysis as well as in plasma catalysis.96 This can be attributed to a decrease in the transition state barrier for N2 dissociation in the presence of an alkali promoter due to electrostatic attractions,40 confirming that N2 dissociation is also kinetically relevant in plasma catalysis.
Proving that the catalytic activity enhancement is due to plasma-activated N2 rather than plasma-generated radicals is difficult and no definitive experimental proof has been provided for transition metals other than Ru so far. Rouwenhorst et al.282 found that Ru metal becomes active for ammonia synthesis below the thermal onset temperature (typically 300–400 °C
41–43,283,311). The onset temperature for plasma catalysis is due to the desorption temperature of ammonia from Ru (typically 150–200 °C
160,312), substantially lower than the temperature required for N2 dissociation at sufficient rates (typically 300–400 °C
41–43,283,311). Given that sufficient radicals are available for adsorption, ammonia can be formed over the metal without the need for N2 dissociation on the catalyst. Rouwenhorst et al.282 found that plasma-activated, molecular N2 also contributes to the plasma-catalytic conversion at temperatures above 300 °C. Furthermore, the plasma-catalytic conversion to ammonia increases with the specific energy input (SEI),165 which is due to increased plasma-activation of N2.131,282
Another effect observed for plasma-enhanced catalytic ammonia synthesis is ammonia yields beyond the thermodynamic equilibrium limit.282,293 Mehta et al.293 developed a model for plasma-enhanced ammonia synthesis, which estimates the activities for ammonia synthesis and ammonia decomposition. The N2 activation barrier is the key descriptor, while the hydrogenation steps are lumped in the model. The plasma-activation is assumed to decrease the barrier for N2 dissociation and therefore increase the rate of N2 dissociation. The final state of surface-adsorbed N* is assumed to be unaffected by plasma-activation of N2. Upon varying the N2 activation barrier, it was shown that plasma-activation can lead to ammonia synthesis beyond the thermal equilibrium. This model was experimentally validated for Ru/MgO and Ru–K/MgO catalysts.282 Coupling the model of Mehta et al.293 with experimental data, allows for distinguishing between regimes where plasma-generated radicals are dominant and regimes where plasma-activated molecular N2 is dominant.282
As shown in Fig. 12(a), Mehta et al.131 lumped the N2 dissociation reaction in a single activation barrier to atomic N* on the catalyst surface, which leads to the prediction of enhancing the ammonia synthesis rate for noble catalysts with high N2 activation barriers (see Fig. 11). However, N2 dissociation is more complex in practice with various intermediates towards 2N* (see Fig. 12).40,313,314 Furthermore, molecule–surface interactions may lead to energy losses upon adsorption of plasma-activated N2.315
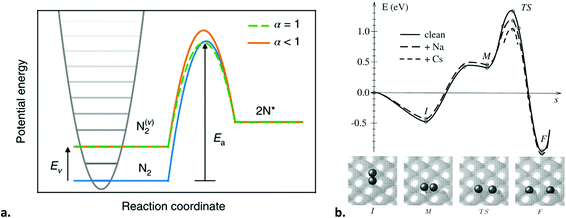 |
| Fig. 12 (a) Proposed impact of vibrational excitation on dissociation barrier of N2. Reproduced from ref. 131. (b) Minimum energy path for N2 dissociation over Ru(0001), without and with alkali promoters. Reproduced from ref. 40. | |
It remains an open question to what degree plasma-activation can lower the N2 dissociation barrier for metals with a substantial barrier for N2 dissociation. To account for these effects, Mehta et al. introduced an alpha parameter that represents the efficacy of vibrational excitation to lower the energy barrier. This alpha parameter is obtained from the Fridman–Macheret equation.129 In reality the efficacy of vibrational excitation also depends on the degree of excitation316–318 and it is unclear how accurate the Fridman–Macheret approximation is. To the best of our knowledge, more accurate models to describe the vibrational efficacy do not exist yet.
6. Plasma-catalytic ammonia synthesis: the complexity ahead
As discussed in the previous section, plasma catalysis could become an alternative for small-scale ammonia synthesis only in two scenarios: (1) N2 is dissociated by the plasma, while H2 remains unaffected by the plasma, and (2) N2 is only partially activated by the plasma. Some general strategies for catalyst design and for effective plasma-catalyst coupling were discussed in section 3.5. Furthermore, the possible mechanisms leading to plasma-catalytic ammonia synthesis, as well as the complexity of dissociative N2 adsorption were discussed in section 5. Hereafter, we aim to shed light on potential avenues that may be relevant for the development of the field.
We want to stress that there are several known unknowns, as well as multiple unknown unknowns in plasma catalysis.231,233 The mutual interactions between the plasma and catalyst imply that a large number of interactions may affect the plasma-driven conversions. Only recently, kinetic models were introduced in an attempt to understand plasma-catalytic ammonia synthesis in terms of the catalytic cycle.131,191,293,305 These models have provided guidelines and concepts to interpret experimental results, but it remains difficult to link the experimental results to highly simplified models. For instance, plasma-excitations in molecular N2 are predicted to shift the volcano curve to more noble metals (see Fig. 11). However, a shift to more noble metals is also to be expected for NHx radicals adsorbing and hydrogenating via Langmuir–Hinshelwood reactions, due to an increased hydrogenation rate over more noble metals, as well as less desorption limitations.305 This implies both options are still open to explain catalytic trends observed in experiments. Secondly, these first models are simplifications in which not all the complexity of plasma-catalysis is incorporated, because we simply do not yet comprehend all the important contributions to plasma-catalyst interactions.231,233 This sometimes results in disagreement between modelling results and trends observed in experiments, as discussed in section 5.3.
Specifically, the studies by Mehta et al.131 and Engelmann et al.305 assume specific plasma conditions that are unaffected by the catalytic reactions. Indeed, while increased TOFs were obtained by Mehta for vibrational excitations and by Engelmann for radical contributions, it is yet to be investigated whether the plasma can sustain a high vibrational temperature and high radical densities while the catalyst consumes these reactive plasma species. This, potentially, imposes limitations on the ratio of the amount of catalyst to plasma volume.
Thus, it is often difficult to distinguish between the relevant plasma species responsible for the activity enhancement in the presence of a plasma, although a few studies have strong indications for a specific pathway.96,191,282 Based on a combined experimental and modelling study, Shah et al.191 proposed that the plasma-catalytic conversion over Fe-catalysts in a low pressure RF reactor is due to dissociation of N2 by the plasma, with subsequent adsorption and hydrogenation to ammonia over the surface. Based on experiments with various Ru-catalysts, Rouwenhorst et al.282 showed that the plasma-enhancement over Ru-catalysts in a DBD reactor is due to reactions with NHx radicals at low temperatures (<300 °C), while plasma-activated N2 with subsequent hydrogenation over the surface may also become increasingly relevant at temperatures where the activity in the absence of plasma is also substantial. Even if the activity enhancement can be proven to be due to plasma-activated N2 rather than plasma-generated NHx species, it remains unresolved which plasma-activated N2 species, e.g. with different levels of vibrational of electronic excitation, is responsible for the activity enhancement over Ru-catalysts observed in various reports.90,96,165
Various authors have reported an improvement in the energy efficiency for ammonia formation when using pulsed plasmas rather than AC plasmas.158,165 For plasma-enhanced catalytic ammonia synthesis, the enhanced efficiency can be understood from the lower overall plasma power, and therefore reduced heat losses.319 Furthermore, vibrational–translational relaxation is suppressed for pulsed plasmas,320 thereby limiting the gas heating losses. Lastly, the electron energy distribution is different for pulsed plasmas.321
Jafarzadeh, Bal et al.246,248,322 recently reported computational studies on enhanced surface binding of CO2 on various metal cluster surfaces in case of a polarized surface; similar behavior may occur for N2 binding. Surface polarization may also affect surface reactions in case of ammonia synthesis over metals, but there have not been any studies confirming or ruling out the relevance of such effects. For thermal catalysis and plasma catalysis, electrostatic attraction of alkali metals with N2 cause an enhancement in N2 dissociation rates.40,96 This shows that the electronic characteristics of the catalyst are very relevant for ammonia synthesis.
Furthermore, the effect of periodic discharges and capacitive regimes is not fully understood, both on the catalytic properties of the surface323,324 and on the plasma characteristics near the catalyst.225,230,325 For instance, Ardagh et al.323,324 reported that oscillatory surface binding strengths, induced by for instance electric fields, may enhance the catalytic activity by orders of magnitude. Furthermore, the waveform and the frequency of the oscillation can determine the catalytic activity.323,324 As the plasma frequency and waveform is a design parameter which alters both the electron density and electron energy for N2 activation in the plasma zone, as well as the catalyst surface properties, this potentially adds a new dimension to the complexity of plasma-catalytic systems.
7. Outlook
Over the past decades, research on plasma-catalytic ammonia synthesis has transitioned from exploratory and trial-and-error approaches to more fundamental understanding based on experimental and modelling work, as described in detail in this review paper. Operando plasma and catalyst diagnostics, such as surface techniques such as XPS and FTIR,193,195 isotopic labelling326 and spectroscopy194,327 will aid in further improving our understanding of how plasma and catalyst interact at the molecular level, rather than on the macroscopic level.
Open questions remain, such as which plasma-activated species are dominant for the conversion to ammonia, and under which conditions. For instance, which plasma-activated N2 species is dominant for plasma-enhanced catalytic ammonia synthesis: electronically excited N2 or vibrationally excited N2? Furthermore, to what degree have we uncovered the complexity of plasma catalysis for plasma-driven ammonia synthesis, i.e. what is the role of plasma-generated radicals, and the importance of Langmuir–Hinshelwood versus Eley–Rideal reactions, and which unknown unknowns remain? How does the plasma environment behave very close to a metal nanoparticle on a solid surface? Additional modelling efforts may aid in enhancing the understanding.230
Secondly, to which degree can our understanding of plasma catalysis aid in developing sufficiently energy-efficient plasma-catalytic ammonia synthesis? Which combination of plasma reactor and catalyst leads to the highest productivity at the lowest energy cost? For now, the highest energy yields are reported for atmospheric pressure DBD reactors (see Fig. 9). On the other hand, low pressure plasma reactors such as MW and RF reactors lead to a higher degree of vibrational excitation, which may be beneficial for mild N2 activation before catalytic N2 dissociation. However, it should be noted that plasma activation is not the only process step for ammonia synthesis from air and water, as H2 production, N2 purification and ammonia separation and storage should be considered as well. The most suitable plasma reactor and catalyst are to a high degree linked to the process conditions, such as temperature and pressure for H2 production, N2 purification and ammonia separation and storage.
Finally, it is not yet clear whether plasma technology will be the most feasible alternative for decentralized ammonia production in the future (see Table 2). In heterogeneous catalysis, ammonia synthesis has been a guide reaction, due to the perceived simplicity of the reaction and the absence of by-products.22,34 Thus, plasma-catalytic ammonia synthesis can certainly aid in improving our understanding of the emerging research field of plasma catalysis. Currently, plasma technology is already used for ozone production and acetylene at large scale.328,329 Further experimental and modelling research will tell whether plasma catalysis will become a feasible alternative for green ammonia production, and whether plasma-catalytic processes will become industrially viable for other processes, like CO2 and CH4 conversions.328
Author contributions
A. B., K. H. R. R., K. v. t. V., L. L. and Y. E. wrote section 1. A. B., K. H. R. R., K. v. t. V., L. L., R. S. P. and Y. E. co-wrote section 2. A. B., K. H. R. R., K. v. t. V., L. L. and Y. E. co-wrote section 3. A. B., K. H. R. R., K. v. t. V., L. L. and Y. E. co-wrote section 4. A. B., K. H. R. R., K. v. t. V., L. L. and Y. E. co-wrote section 5. A. B., K. H. R. R., K. v. t. V., L. L. and Y. E. co-wrote section 6. All authors reviewed the document.
Conflicts of interest
There are no conflicts to declare.
References
- K. M. Van Geem, V. V. Galvita and G. B. Marin, Making chemicals with electricity, Science, 2019, 364, 734–735 CrossRef CAS.
-
E. Simon, Green ammonia, in REFUEL Kickoff meeting, 2017 Search PubMed.
- A. Valera-Medina, H. Xiao, M. Owen-Jones, W. I. F. David and P. J. Bowen, Ammonia for power, Prog. Energy Combust. Sci., 2018, 69, 63–102 CrossRef.
- J. D. Hunt,
et al., Global resource potential of seasonal pumped hydropower storage for energy and water storage, Nat. Commun., 2020, 11, 947 CrossRef CAS.
- J. Guo and P. Chen, Catalyst: NH3 as an Energy Carrier, Chem, 2017, 3, 709–712 CAS.
- K. H. R. Rouwenhorst, A. G. J. Van Der Ham, G. Mul and S. R. A. Kersten, Islanded ammonia power systems: Technology review & conceptual process design, Renewable Sustainable Energy Rev., 2019, 114, 109339 CrossRef CAS.
- S. Giddey, S. P. S. Badwal, C. Munnings and M. Dolan, Ammonia as a Renewable Energy Transportation Media, ACS Sustainable Chem. Eng., 2017, 5, 10231–10239 CrossRef CAS.
- V. Smil, Detonator of the population explosion, Nature, 1999, 400, 415 CrossRef CAS.
- J. W. Erisman, M. A. Sutton, J. Galloway, Z. Klimont and W. Winiwarter, How a century of ammonia synthesis changed the world, Nat. Geosci., 2008, 1, 636–639 CrossRef CAS.
- M. Appl, Ammonia, 1. Introduction, Ullmann's Encycl. Ind. Chem., 2011 DOI:10.1002/14356007.a02_143.pub3.
- M. Appl, Ammonia, 2. Production Processes, Ullmann's Encycl. Ind. Chem., 2012, 295–338, DOI:10.1002/14356007.o02_o11.
- M. Appl, Ammonia, 3. Production Plants, Ullmann's Encycl. Ind. Chem., 2012, 295–338, DOI:10.1002/14356007.o02_o12.
- V. Pattabathula, Ammonia, Kirk-Othmer Encycl. Chem. Technol., 2019 DOI:10.1002/0471238961.0113131503262116.a01.pub4.
-
K. H. R. Rouwenhorst, P. M. Krzywda, N. E. Benes, G. Mul and L. Lefferts, Green Ammonia Production, in Techno-Economic Challenges of Green Ammonia as Energy Vector, ed. R. Bañares-Alcántara and A. Valera-Medina, 2020 Search PubMed.
-
V. Smil, Enriching the Earth: Fritz Haber, Carl Bosch, and the Transformation of World Food Production, 2004 Search PubMed.
- H. Liu, Ammonia synthesis catalyst 100 years: Practice, enlightenment and challenge, Chin. J. Catal., 2014, 35, 1619–1640 CrossRef CAS.
- B. S. Patil, Q. Wang, V. Hessel and J. Lang, Plasma N2-fixation: 1900–2014, Catal. Today, 2015, 256, 49–66 CrossRef CAS.
- B. S. Patil,
et al., Nitrogen Fixation, Ullmann's Encycl. Ind. Chem., 2017 DOI:10.1002/14356007.a17_471.pub2.
-
F. A. Ernst, Industrial Chemical Monographs: Fixation of Atmospheric Nitrogen, Chapman & Hall, Ltd., 1928 Search PubMed.
-
K. H. R. Rouwenhorst, P. M. Krzywda, N. E. Benes, G. Mul and L. Lefferts, Ammonia, 4. Green Ammonia Production, Ullmann's Encycl. Ind. Chem. Search PubMed, In preparation.
- Y. Bicer, I. Dincer, C. Zamfirescu, G. Vezina and F. Raso, Comparative life cycle assessment of various ammonia production methods, J. Cleaner Prod., 2016, 135, 1379–1395 CrossRef CAS.
-
A. Hellman, K. Honkala, S. Dahl, C. H. Christensen and J. K. Nørskov, Ammonia Synthesis: State of the Bellwether Reaction, in Comprehensive Inorganic Chemistry (II), Elsevier Ltd, 2013. DOI:10.1016/B978-0-08-097774-4.00725-7.
- R. Reimert,
et al., Gas Production, 2. Processes, Ullmann's Encycl. Ind. Chem., 2011, 1–60, DOI:10.1002/14356007.o12_o01.
- T. L. Hardenburger and M. N. Ennis, Nitrogen, Kirk-Othmer Encycl. Chem. Technol., 2005, 1–23, DOI:10.1002/0471238961.1409201808011804.a01.pub2.
- A. Sánchez and M. Martín, Scale up and scale down issues of renewable ammonia
plants: Towards modular design, Sustainable Prod. Consumption, 2018, 16, 176–192 CrossRef.
- P. Stoltze and J. K. Nørskov, The surface science based ammonia kinetics revisited, Top. Catal., 1994, 1, 253–263 CrossRef CAS.
- P. Stoltze and J. K. Nørskov, A description of the high–pressure ammonia synthesis reaction based on surface science, J. Vac. Sci. Technol., A, 1987, 5, 581–585 CrossRef CAS.
- H. Liu and W. Han, Wüstite-based catalyst for ammonia synthesis: Structure, property and performance, Catal. Today, 2017, 297, 276–291 CrossRef CAS.
-
J. M. Jennings, Catalytic Ammonia Synthesis: Fundamentals and Practice, Plenum Press, 1991 Search PubMed.
-
A. Nielsen, Ammonia: Catalysis and Manufacture, Springer-Verlag, 1995 Search PubMed.
-
H. Liu, Ammonia Synthesis Catalysts: Innovation and Practice, World Scientific, 2013. DOI:10.1142/8199.
- A. Ozaki, H. Taylor and M. Boudart, Kinetics and Mechanism of the Ammonia Synthesis, Proc. R. Soc. A, 1960, 258, 47–62 CAS.
- G. Ertl, Surface Science and Catalysis—Studies on the Mechanism of Ammonia Synthesis: The P. H. Emmett Award Address, Catal. Rev., 1980, 21, 201–223 CrossRef CAS.
- M. Boudart, Ammonia synthesis: The bellwether reaction in heterogeneous catalysis, Top. Catal., 1994, 1, 405–414 CrossRef CAS.
- J. J. Mortensen,
et al., Nitrogen adsorption on Fe (111), (100), and (110) surfaces, Surf. Sci., 1999, 422, 8–16 CrossRef CAS.
- J. J. Mortensen, L. B. Hansen, B. Hammer and J. K. Nørskov, Nitrogen Adsorption and Dissociation on Fe(111), J. Catal., 1999, 182, 479–488 CrossRef CAS.
- N. D. Spencer, R. C. Schoonmaker and G. A. Somorjai, Iron single crystals as ammonia synthesis catalysts: Effect of surface structure on catalyst activity, J. Catal., 1982, 135, 129–135 CrossRef.
- A. Mittasch and W. Frankenburg, Early Studies of Multicomponent Catalysts, Adv. Catal., 1950, 2, 81–104 Search PubMed.
- E. Farber, From Chemistry to Philosophy: The Way of Alwin Mittasch (1869–1953), Chymia, 1966, 11, 157–178 CrossRef CAS.
- J. J. Mortensen, B. Hammer and J. K. Nørskov, Alkali promotion of N2 dissociation over Ru(0001), Phys. Rev. Lett., 1998, 80, 4333–4336 CrossRef CAS.
- K.-I. Aika, Role of alkali promoter in ammonia synthesis over ruthenium catalysts—Effect on reaction mechanism, Catal. Today, 2017, 286, 14–20 CrossRef CAS.
- K.-I. Aika, A. Ohya, A. Ozaki, Y. Inoue and I. Yasumori, Support and promoter effect of ruthenium catalyst: II. Ruthenium/alkaline earth catalyst for activation of dinitrogen, J. Catal., 1985, 92, 305–311 CrossRef CAS.
- K.-I. Aika,
et al., Support and promoter effect of ruthenium catalyst. I. Characterization of alkali-promoted ruthenium/alumina catalysts for ammonia synthesis, J. Catal., 1985, 92, 296–304 CrossRef CAS.
- M. Kitano,
et al., Self-organized Ruthenium-Barium Core-Shell Nanoparticles on a Mesoporous Calcium Amide Matrix for Efficient Low-Temperature Ammonia Synthesis, Angew. Chem., Int. Ed., 2018, 57, 2648–2652 CrossRef CAS.
- M. Hara, M. Kitano and H. Hosono, Ru-Loaded C12A7:e− Electride as a Catalyst for Ammonia Synthesis, ACS Catal., 2017, 7, 2313–2324 CrossRef CAS.
- J. S. J. Hargreaves, Nitrides as ammonia synthesis catalysts and as potential nitrogen transfer reagents, Appl. Petrochem. Res., 2014, 4, 3–10 CAS.
- C. J. H. Jacobsen,
et al., Catalyst Design by Interpolation in the Periodic Table: Bimetallic Ammonia Synthesis Catalysts, J. Am. Chem. Soc., 2001, 123, 8404–8405 CrossRef CAS.
- D. E. Brown, T. Edmonds, R. W. Joyner, J. J. McCarroll and S. R. Tennison, The genesis and development of the commercial BP doubly promoted catalyst for ammonia synthesis, Catal. Lett., 2014, 144, 545–552 CrossRef CAS.
- H. Liu, W. Han, C. Huo and Y. Cen, Development and application of wüstite-based ammonia synthesis catalysts, Catal. Today, 2019, 1–18 Search PubMed.
- Y. Kobayashi, M. Kitano, S. Kawamura, T. Yokoyama and H. Hosono, Kinetic evidence: The rate-determining step for ammonia synthesis over electride-supported Ru catalysts is no longer the nitrogen dissociation step, Catal. Sci. Technol., 2017, 7, 47–50 RSC.
- Y. Inoue,
et al., Highly Dispersed Ru on Electride [Ca24Al28O64]4+(e−)4 as a Catalyst for Ammonia Synthesis, ACS Catal., 2014, 4(2), 674–680 CrossRef CAS.
-
J. B. Hansen and P. A. Han, Roadmap to All Electric Ammonia Plants, in NH3 Fuel Conference, 2018 Search PubMed.
- J. R. Brightling, Ammonia and the fertiliser industry: The development of ammonia at Billingham, Johnson Matthey Technol. Rev., 2018, 62, 32–47 CrossRef CAS.
-
European Fertilizer Manufacturers’ Association, Production of Ammonia. Best available techniques for pollution prevention and control in the European fertilizer industry, 2000 Search PubMed.
- Proton Ventures B. V., Sustainable ammonia for food and power, Nitrogen + Syngas, 2018, 1–10.
-
H. Vrijenhoef, Dutch initiatives to store sustainable energy in the form of ammonia, in NH3 Fuel Conference, 2017 Search PubMed.
- M. Reese,
et al., Performance of a Small-Scale Haber Process, Ind. Eng. Chem. Res., 2016, 55, 3742–3750 CrossRef CAS.
-
T. Brown, Ammonia technology portfolio: optimize for energy efficiency and carbon efficiency, 2018 Search PubMed.
- E. R. Morgan, J. F. Manwell and J. G. McGowan, Sustainable Ammonia Production from U.S. Offshore Wind Farms: A Techno-Economic Review, ACS Sustainable Chem. Eng., 2017, 5, 9554–9567 CAS.
- P. H. Pfromm, Towards sustainable agriculture: Fossil-free ammonia, J. Renewable Sustainable Energy, 2017, 9, 034702 Search PubMed.
-
M. Will, Realisation of Large-Scale Green Ammonia Plants, in NH3 Fuel Conference, 2018 Search PubMed.
-
M. Will and L. Lüke, Realisation of large-scale Green Ammonia plants, in NH3 Event, 2018 Search PubMed.
-
J. P. Vrijenhoef, Opportunities for small scale ammonia production, in International Fertiliser Society, 2017, pp. 1–16 Search PubMed.
-
J. Schmuecker and D. Toyne, Making demonstration amounts of renewable ammonia and using it to fuel a farm tractor, in NH3 Event, 2019 Search PubMed.
-
J. B. Hansen and P. Han, The SOC4NH3 Project in Denmark, in NH3 Event, 2019 Search PubMed.
- N. Cherkasov, A. O. Ibhadon and P. Fitzpatrick, A review of the existing and alternative methods for greener nitrogen fixation, Chem. Eng. Process., 2015, 90, 24–33 CAS.
- J. G. Chen,
et al., Beyond fossil fuel–driven nitrogen transformations, Science, 2018, 360(6391), eaar6611 Search PubMed.
- M. Malmali, Y. Wei, A. McCormick and E. L. Cussler, Ammonia Synthesis at Reduced Pressure via Reactive Separation, Ind. Eng. Chem. Res., 2016, 55, 8922–8932 CAS.
- C. Philibert, Direct and indirect electrification of industry and beyond, Oxford Rev. Econ. Policy, 2019, 35, 197–217 Search PubMed.
- Z. J. Schiffer and K. Manthiram, Electrification and Decarbonization of the Chemical Industry, Joule, 2017, 1, 10–14 Search PubMed.
- A. Buttler and H. Spliethoff, Current status of water electrolysis for energy storage, grid balancing and sector coupling via power-to-gas and power-to-liquids: A review, Renewable Sustainable Energy Rev., 2018, 82, 2440–2454 CAS.
- M. Carmo, D. L. Fritz, J. Mergel and D. Stolten, A comprehensive review on PEM water electrolysis, Int. J. Hydrogen Energy, 2013, 38(12), 4901–4934 CrossRef CAS.
-
L. Bertuccioli, et al., Development of water electrolysis in the european union: Final report, 2014 Search PubMed.
- S. T. Wismann,
et al., Electrified methane reforming: A compact approach to greener industrial hydrogen production, Science, 2019, 364, 756–759 CrossRef CAS.
- C. D. Demirhan, W. W. Tso and J. B. Powell, Sustainable Ammonia Production Through Process Synthesis and Global Optimization, AIChE J., 2019, 65(7), e16498 Search PubMed.
- D. Frattini,
et al., A system approach in energy evaluation of different renewable energies sources integration in ammonia production plants, Renewable Energy, 2016, 99, 472–482 CAS.
- A. Sánchez, M. Martín and P. Vega, Biomass Based Sustainable Ammonia Production: Digestion vs Gasification, ACS Sustainable Chem. Eng., 2019, 7, 9995–10007 Search PubMed.
- S. Giddey, S. P. S. Badwal and A. Kulkarni, Review of electrochemical ammonia production technologies and materials, Int. J. Hydrogen Energy, 2013, 38, 14576–14594 CAS.
- I. J. McPherson, T. Sudmeier, J. Fellowes and S. C. E. Tsang, Materials for electrochemical ammonia synthesis, Dalton Trans., 2019, 48, 1562–1568 CAS.
- A. J. Medford and M. C. Hatzell, Photon-Driven Nitrogen Fixation: Current Progress, Thermodynamic Considerations, and Future Outlook, ACS Catal., 2017, 7, 2624–2643 CAS.
- X. Chen, N. Li, Z. Kong, W. J. Ong and X. Zhao, Photocatalytic fixation of nitrogen to ammonia: State-of-the-art advancements and future prospects, Mater. Horiz., 2018, 5, 9–27 RSC.
- J. Hong, S. Prawer and A. B. Murphy, Plasma Catalysis as an Alternative Route for Ammonia Production: Status, Mechanisms, and Prospects for Progress, ACS Sustainable Chem. Eng., 2018, 6, 15–31 CrossRef CAS.
- A. Bogaerts and E. C. Neyts, Plasma Technology: An Emerging Technology for Energy Storage, ACS Energy Lett., 2018, 3, 1013–1027 CrossRef CAS.
- P. Peng,
et al., A review on the non-thermal plasma-assisted ammonia synthesis technologies, J. Cleaner Prod., 2018, 177, 597–609 CrossRef CAS.
- T. A. Bazhenova and A. E. Shilov, Nitrogen fixation in solution, Coord. Chem. Rev., 1995, 144, 69–145 CAS.
-
J. Nørskov, et al., Sustainable Ammonia Synthesis Exploring the scientific challenges associated with discovering alternative, sustainable processes for ammonia production, in DOE Roundtable Report, 2016. DOI:10.2172/1283146.
- W. Gao,
et al., Production of ammonia via a chemical looping process based on metal imides as nitrogen carriers, Nat. Energy, 2018, 3, 1067–1075 CAS.
- R. Shi, X. Zhang, G. I. N. Waterhouse, Y. Zhao and T. Zhang, The Journey toward Low Temperature, Low Pressure Catalytic Nitrogen Fixation, Adv. Energy Mater., 2020, 10(19), 2000659 CAS.
- F. Jiao and B. Xu, Electrochemical Ammonia Synthesis and Ammonia Fuel Cells, Adv. Mater., 2018, 1–5, DOI:10.1002/adma.201805173.
- H.-H. Kim, Y. Teramoto, A. Ogata, H. Takagi and T. Nanba, Plasma Catalysis for Environmental Treatment and Energy Applications, Plasma Chem. Plasma Process., 2016, 36, 45–72 CrossRef CAS.
-
J. Hu, et al., Microwave Catalysis for Ammonia Synthesis Under Mild Reaction Conditions, in NH3 Fuel Conference, 2018 Search PubMed.
- A. R. Singh,
et al., Strategies Toward Selective Electrochemical Ammonia Synthesis, ACS Catal., 2019, 9, 8316–8324 CrossRef CAS.
- L. Wang,
et al., Greening Ammonia toward the Solar Ammonia Refinery, Joule, 2018, 1–20, DOI:10.1016/j.joule.2018.04.017.
-
CEFIC, European chemistry for growth: Unlocking a competitive, low carbon and energy efficient future, 2013 Search PubMed.
- C. Smith, A. K. Hill and L. Torrente-Murciano, Current and future role of Haber–Bosch ammonia in a carbon-free energy landscape, Energy Environ. Sci., 2020, 13(2), 331–344 CAS.
- K. H. R. Rouwenhorst, H.-H. Kim and L. Lefferts, Vibrationally excited activation of N2 in plasma-enhanced catalytic ammonia synthesis: a kinetic analysis, ACS Sustainable Chem. Eng., 2019, 7, 17515–17522 CAS.
- K. H. R. Rouwenhorst and L. Lefferts, Feasibility study of plasma-catalytic ammonia synthesis for energy storage applications, Catalysts, 2020, 10(9), 999 Search PubMed.
- P. Wang,
et al., Breaking scaling relations to achieve low-temperature ammonia synthesis through LiH-mediated nitrogen transfer and hydrogenation, Nat. Chem., 2017, 9, 64–70 CAS.
- W. Gao,
et al., Barium Hydride-Mediated Nitrogen Transfer and Hydrogenation for Ammonia Synthesis: A Case Study of Cobalt, ACS Catal., 2017, 7, 3654–3661 CrossRef CAS.
- P. Wang,
et al., The Formation of Surface Lithium–Iron Ternary Hydride and its Function on Catalytic Ammonia Synthesis at Low Temperatures, Angew. Chem., Int. Ed., 2017, 56, 8716–8720 CrossRef CAS.
- T. Zhang, H. Miyaoka, H. Miyaoka, T. Ichikawa and Y. Kojima, Review on Ammonia Absorption Materials: Metal Hydrides, Halides, and Borohydrides, ACS Appl. Energy Mater., 2018, 1, 232–242 CrossRef CAS.
- J. W. Makepeace,
et al., Reversible ammonia-based and liquid organic hydrogen carriers for high-density hydrogen storage: Recent progress, Int. J. Hydrogen Energy, 2019, 44, 7746–7767 CrossRef CAS.
- M. Malmali,
et al., Better Absorbents for Ammonia Separation, ACS Sustainable Chem. Eng., 2018, 6(5), 6536–6546 CrossRef CAS.
- M. S. Huberty, A. L. Wagner, A. McCormick and E. Cussler, Ammonia Absorption at Haber Process Conditions, AIChE J., 2012, 58, 3526–3532 CrossRef CAS.
- C. Y. Liu and K.-I. Aika, Ammonia Adsorption on Ion Exchanged Y-zeolites as Ammonia Storage Material, J. Jpn. Pet. Inst., 2003, 46, 301–307 CAS.
- C. Y. Liu and K. Aika, Ammonia Absorption on Alkaline Earth Halides as Ammonia Separation and Storage Procedure, Bull. Chem. Soc. Jpn., 2004, 77, 123–131 CAS.
- C. Y. Liu and K. Aika, Effect of the Cl/Br Molar Ratio of a CaCl2-CaBr2 Mixture Used as an Ammonia Storage Material, Ind. Eng. Chem. Res., 2004, 43, 6994–7000 CAS.
-
J. D. Beach, J. D. Kintner and A. W. Welch, Removal of gaseous NH3 from an NH3 reactor product stream, US Patent, 20180339911A1, 2018 Search PubMed.
- C. Y. Liu and K. Aika, Modification of active carbon and zeolite as ammonia separation materials for a new de-NOx process with ammonia on-site synthesis, Res. Chem. Intermed., 2002, 28, 409–417 CAS.
- V. Kyriakou, I. Garagounis, E. Vasileiou, A. Vourros and M. Stoukides, Progress in the Electrochemical Synthesis of Ammonia, Catal. Today, 2017, 286, 2–13 CAS.
- K. Wang, D. Smith and Y. Zheng, Electron-driven heterogeneous catalytic synthesis of ammonia: Current states and perspective, Carbon Resour. Convers., 2018, 1, 2–31 CrossRef.
- G. Soloveichik, Electrochemical synthesis of ammonia as a potential alternative to the Haber – Bosch process, Nat. Catal., 2019, 2, 377–380 CrossRef CAS.
- J. H. Montoya, C. Tsai, A. Vojvodic and J. K. Nørskov, The challenge of electrochemical ammonia synthesis: A new perspective on the role of nitrogen scaling relations, ChemSusChem, 2015, 8, 2180–2186 CrossRef CAS.
- A. R. Singh,
et al., Electrochemical Ammonia Synthesis - The Selectivity Challenge, ACS Catal., 2017, 7, 706–709 CrossRef CAS.
- X. Cui, C. Tang and Q. Zhang, A Review of Electrocatalytic Reduction of Dinitrogen to Ammonia under Ambient Conditions, Adv. Energy Mater., 2018, 8, 1800369 CrossRef.
- J. Kibsgaard, J. K. Nørskov and I. Chorkendorff, The Difficulty of Proving Electrochemical Ammonia Synthesis, ACS Energy Lett., 2019, 2986–2988 CAS.
- S. Z. Andersen,
et al., A rigorous electrochemical ammonia synthesis protocol with quantitative isotope measurements, Nature, 2019, 570, 504–508 CAS.
- A. R. Singh,
et al., Computational Design of Active Site Structures with Improved Transition-State Scaling for Ammonia Synthesis, ACS Catal., 2018, 8, 4017–4024 CAS.
- S. L. Foster,
et al., Catalysts for nitrogen reduction to ammonia, Nat. Catal., 2018, 1, 490–500 Search PubMed.
- M. Vu, M. Sakar, S. A. Hassanzadeh-tabrizi and T. Do, Photo(electro)catalytic Nitrogen Fixation: Problems and Possibilities, Adv. Mater. Interfaces, 2019, 6, 1900091 Search PubMed.
-
U.S. Department of Energy, Sustainable Ammonia Synthesis, 2016 Search PubMed.
- J. M. McEnaney,
et al., Ammonia synthesis from N2 and H2O using a lithium cycling electrification strategy at atmospheric pressure, Energy Environ. Sci., 2017, 10, 1621–1630 CAS.
- P. Mehta, P. Barboun, D. B. Go, J. C. Hicks and W. F. Schneider, Catalysis Enabled by Plasma Activation of Strong Chemical Bonds: a Review, ACS Energy Lett., 2019, 4(5), 1115–1133 CAS.
- R. Brandenburg,
et al., White paper on the future of plasma science in environment, for gas conversion and agriculture, Plasma Processes Polym., 2018, e1700238 Search PubMed.
- E. C. Neyts, K. Ostrikov, M. K. Sunkara and A. Bogaerts, Plasma Catalysis: Synergistic Effects at the Nanoscale, Chem. Rev., 2015, 115, 13408–13446 CrossRef CAS.
- A. Bogaerts,
et al., The 2020 Plasma Catalysis Roadmap, J. Phys. D: Appl. Phys., 2020, 53, 1–51 CrossRef.
- R. Snoeckx and A. Bogaerts, Plasma technology - a novel solution for CO2 conversion?, Chem. Soc. Rev., 2017, 46, 5805–5863 RSC.
- A. Bogaerts, E. Neyts, R. Gijbels and J. Van Der Mullen, Gas discharge plasmas and their applications, Spectrochim. Acta, Part B, 2002, 57, 609–658 CrossRef.
-
A. Fridman, Plasma chemistry, 2008 Search PubMed.
- R. Snoeckx and A. Bogaerts, Plasma technology – a novel solution for CO2 conversion?, Chem. Soc. Rev., 2017, 46, 5805–5863 RSC.
- P. Mehta,
et al., Overcoming ammonia synthesis scaling relations with plasma-enabled catalysis, Nat. Catal., 2018, 1, 269–275 CrossRef.
- Y. Uchida, K. Takaki, U. K. Urashima and J.-S. Chang, Atmospheric pressure of nitrogen plasmas in a ferro-electric packed-bed barrier discharge reactor part II: Spectroscopic measurements of excited nitrogen molecule density and its vibrational temperature, IEEE Trans. Dielectr. Electr. Insul., 2004, 11, 491–497 CrossRef CAS.
- M. Bai, Z. Zhang, M. Bai, X. Bai and H. Gao, Synthesis of Ammonia using CH4/N2 plasmas based on micro-gap discharge under environmentally friendly condition, Plasma Chem. Plasma Process., 2008, 28, 405–414 CrossRef CAS.
- M. Bai, Z. Zhang, M. Bai, X. Bai and H. Gao, Conversion of methane to liquid products, hydrogen, and ammonia with environmentally friendly condition-based microgap discharge, J. Air Waste Manage. Assoc., 2008, 58, 1616–1621 CrossRef CAS.
-
M. Bai, X. Bai, N. Wang, D. Zhang and K. Zhan, Synthesis of ammonia and liquid fuel by CH4 and N2 plasmas without catalyst at ambient pressure and temperature, in IEEE International Conference on Plasma Science, 2004, p. 413 Search PubMed.
- G. Horvath,
et al., Packed bed DBD discharge experiments in admixtures of N2 and CH4, Plasma Chem. Plasma Process., 2010, 30, 565–577 CrossRef CAS.
- Y. Gorbanev, E. Vervloessem, A. Nikiforov and A. Bogaerts, Nitrogen fixation with water vapor by non-equilibrium plasma: Towards sustainable ammonia production, ACS Sustainable Chem. Eng., 2020, 8(7), 2996–3004 CrossRef CAS.
- P. Peng,
et al., Plasma in situ gas-liquid nitrogen fixation using concentrated high-intensity electric field, J. Phys. D: Appl. Phys., 2019, 52, 494001 CrossRef CAS.
- R. Hawtof,
et al., Catalyst-free, highly selective synthesis of ammonia from nitrogen and water by a plasma electrolytic system, Asian J. Chem., 2019, 31, 1–10 CrossRef.
- P. Peng,
et al., In situ plasma-assisted atmospheric nitrogen fixation using water and spray-type jet plasma, Chem. Commun., 2018, 54, 2886–2889 RSC.
- P. Peng,
et al., Sustainable non–thermal plasma–assisted nitrogen fixation – Synergistic catalysis, ChemSusChem, 2019, 1–12, DOI:10.1002/cssc.201901211.
- D. Xie,
et al., Ammonia synthesis and by-product formation from H2O, H2 and N2 by dielectric barrier discharge combined with an Ru/Al2O3 catalyst, RSC Adv., 2016, 6, 105338–105346 RSC.
- M. Bai, Z. Zhang, X. Bai, M. Bai and W. Ning, Plasma Synthesis of Ammonia With a Microgap Dielectric Barrier Discharge at Ambient Pressure, IEEE Trans. Plasma Sci., 2003, 31, 1285–1291 CrossRef CAS.
- T. Mizushima, K. Matsumoto, J. I. Sugoh, H. Ohkita and N. Kakuta, Tubular membrane-like catalyst for reactor with dielectric-barrier-discharge plasma and its performance in ammonia synthesis, Appl. Catal., A, 2004, 265, 53–59 CrossRef CAS.
- T. Mizushima, K. Matsumoto, H. Ohkita and N. Kakuta, Catalytic effects of metal-loaded membrane-like alumina tubes on ammonia synthesis in atmospheric pressure plasma by dielectric barrier discharge, Plasma Chem. Plasma Process., 2007, 27, 1–11 CrossRef CAS.
- J. Hong, S. Prawer and A. B. Murphy, Production of ammonia by heterogeneous catalysis in a packed-bed dielectric-barrier discharge: Influence of argon addition and voltage, IEEE Trans. Plasma Sci., 2014, 42, 2338–2339 Search PubMed.
- A. Gómez-Ramírez, J. Cotrino, R. M. Lambert and A. R. González-Elipe, Efficient synthesis of ammonia from N2 and H2 alone in a ferroelectric packed-bed DBD reactor, Plasma Sources Sci. Technol., 2015, 24, 065011 CrossRef.
- P. Peng,
et al., Atmospheric Pressure Ammonia Synthesis Using Non-thermal Plasma Assisted Catalysis, Plasma Chem. Plasma Process., 2016, 36, 1201–1210 CrossRef CAS.
- J. Hong,
et al., Plasma Catalytic Synthesis of Ammonia Using Functionalized-Carbon Coatings in an Atmospheric-Pressure Non-equilibrium Discharge, Plasma Chem. Plasma Process., 2016, 36, 917–940 CrossRef CAS.
- K. Aihara,
et al., Remarkable catalysis of a wool-like copper electrode for NH3 synthesis from N2 and H2 in non-thermal atmospheric plasma, Chem. Commun., 2016, 52, 13560–13563 RSC.
- P. Peng,
et al., Ru-based multifunctional mesoporous catalyst for low-pressure and non-thermal plasma synthesis of ammonia, Int. J. Hydrogen Energy, 2017, 42, 19056–19066 CrossRef CAS.
- G. Akay and K. Zhang, Process intensification in ammonia synthesis using novel coassembled supported microporous catalysts promoted by nonthermal plasma, Ind. Eng. Chem. Res., 2017, 56, 457–468 CrossRef CAS.
- M. Iwamoto, M. Akiyama, K. Aihara and T. Deguchi, Ammonia Synthesis on Wool-Like Au, Pt, Pd, Ag, or Cu Electrode Catalysts in Nonthermal Atmospheric-Pressure Plasma of N2 and H2, ACS Catal., 2017, 6924–6929 CrossRef CAS.
- J. Hong,
et al., Corrigendum: Kinetic modelling of NH3 production in N2–H2 non-equilibrium atmospheric-pressure plasma catalysis, J. Phys. D: Appl. Phys., 2018, 51, 109501 CrossRef.
- Q. Xie,
et al., Hydrogenation of plasma-excited nitrogen over an alumina catalyst for ammonia synthesis, Int. J. Hydrogen Energy, 2018, 43, 14885–14891 CrossRef CAS.
- Y. Wang,
et al., Plasma-Enhanced Catalytic Synthesis of Ammonia over a Ni/Al2O3 Catalyst at Near-Room Temperature: Insights into the Importance of the Catalyst Surface on the Reaction Mechanism, ACS Catal., 2019, 9, 10780–10793 CrossRef CAS.
- F. Herrera,
et al., The impact of transition metal catalysts on macroscopic dielectric barrier discharge (DBD) characteristics in an ammonia synthesis plasma catalysis reactor, J. Phys. D: Appl. Phys., 2019, 52, 224002 CrossRef CAS.
- P. Peng,
et al., Atmospheric Plasma-Assisted Ammonia Synthesis Enhanced via Synergistic Catalytic Absorption, ACS Sustainable Chem. Eng., 2019, 7, 100–104 CrossRef CAS.
- P. M. Barboun,
et al., Distinguishing Plasma Contributions to Catalyst Performance in Plasma-Assisted Ammonia Synthesis, ACS Sustainable Chem. Eng., 2019, 7(9), 8621–8630 CrossRef CAS.
- Q. Xie, S. Zhuge, X. Song and M. Lu, Non-thermal atmospheric plasma synthesis of ammonia in a DBD reactor packed with various catalysts, J. Phys. D: Appl. Phys., 2019, 53, 064002 CrossRef.
- B. S. Patil,
et al., Deciphering the synergy between plasma and catalyst support for ammonia synthesis in a packed dielectric barrier discharge reactor, J. Phys. D: Appl. Phys., 2020, 53, ab6a36 CrossRef.
- X. Zhu,
et al., Ammonia synthesis over y-Al2O3 pellets in a packed-bed dielectric barrier discharge reactor, J. Phys. D: Appl. Phys., 2020, 53, 164002 CrossRef CAS.
- K. van ‘t Veer, F. Reniers and A. Bogaerts, Zero-dimensional modelling of unpacked and packed bed dielectric barrier discharges: The role of vibrational kinetics in ammonia synthesis, Plasma Sources Sci. Technol., 2020, 29, 045020 CrossRef.
- J. R. Shah, F. Gorky, J. Lucero, M. A. Carreon and M. L. Carreon, Ammonia synthesis via atmospheric plasma- catalysis: Zeolite 5A a case of study, Ind. Eng. Chem. Res., 2020, 59, 5167–5176 CAS.
- H.-H. Kim, Y. Teramoto, A. Ogata, H. Takagi and T. Nanba, Atmospheric-pressure nonthermal plasma synthesis of ammonia over ruthenium catalysts, Plasma Processes Polym., 2017, 14, 1–9 Search PubMed.
- A. Gómez-Ramírez, A. M. Montoro-Damas, J. Cotrino, R. M. Lambert and A. R. González-Elipe, About the enhancement of chemical yield during the atmospheric plasma synthesis of ammonia in a ferroelectric packed bed reactor, Plasma Processes Polym., 2017, 14, 1–8 Search PubMed.
- Y. Nie,
et al., Effect of CaO-modified Al2O3 on the synthesis of ammonia by DBD plasma, Mod. Chem. Ind., 2016, 36, 127–130 Search PubMed.
- G. Akay, Sustainable Ammonia and Advanced Symbiotic Fertilizer Production Using Catalytic Multi-Reaction-Zone Reactors with Nonthermal Plasma and Simultaneous Reactive Separation, ACS Sustainable Chem. Eng., 2017, 5, 11588–11606 CrossRef CAS.
- S. Li, T. van Raak and F. Gallucci, Investigating the operation parameters for ammonia synthesis in dielectric barrier discharge reactors, J. Phys. D: Appl. Phys., 2020, 53, 014008 CrossRef CAS.
- A. K. Brewer and J. W. WestHaver, The Synthesis of Ammonia in the Glow Discharge, J. Phys. Chem., 1929, 33, 883–895 CrossRef CAS.
- A. K. Brewer and J. W. Westhaver, Chemical Action in the Glow Discharge II. Further Investigation on the Synthesis of Ammonia, J. Phys. Chem., 1930, 34, 153–164 CrossRef.
- E. Tiede and E. Hey, Über aktiven Stickstoff und Ammoniak-Bildung im Glimmstrom in Abhängingkeit vom Elektroden-Material unter Berücksichtigung katalytischer Probleme, Ber. Dtsch. Chem. Ges. B, 1933, 66, 85–94 CrossRef.
- G. Y. Botchway and M. Venugopalan, Plasma Synthesis of Ammonia in Presence of an Iron Catalyst, Z. Phys. Chem., 1980, 120, 103–110 CrossRef CAS.
- K. S. Yin and M. Venugopalan, Plasma Chemical Synthesis. I. Effect of Electrode Material on the Synthesis of Ammonia, Plasma Chem. Plasma Process., 1983, 3, 343–350 CrossRef CAS.
- K. Sugiyama,
et al., Ammonia synthesis by means of plasma over MgO catalyst, Plasma Chem. Plasma Process., 1986, 6, 179–193 CrossRef CAS.
- M. Touvelle, J. L. M. Licea, M. Venugopalan, J. L. Mufioz Licea and M. Venugopalan, Plasma Chemical Synthesis. II. Effect of Wall Surface on the Synthesis of Ammonia, Plasma Chem. Plasma Process., 1987, 7, 101 CrossRef CAS.
- H. Miura,
et al., The Formation of Ammonia in the After-Glow Region of N2 Plasma, Electrochem. Ind. Phys. Chem., 1988, 56, 656–657 CAS.
- J. Amorim, G. Baravian and G. Sultan, Absolute density measurements of ammonia synthetized in N2–H2 mixture discharges, Appl. Phys. Lett., 1996, 68, 1915–1917 CrossRef CAS.
- B. Gordiets, C. M. Ferreira, M. J. Pinheiro and A. Ricard, Self-consistent kinetic model of low-pressure N2-H2 flowing discharges: I. Volume processes, Plasma Sources Sci. Technol., 1998, 7, 363–378 CrossRef CAS.
- B. Gordiets, C. M. Ferreira, M. J. Pinheiro and A. Ricard, Self-consistent kinetic model of low-pressure N2-H2 flowing discharges: II. Surface processes and densities of N, H, NH3 species, Plasma Sources Sci. Technol., 1998, 7, 379–388 CrossRef CAS.
- H. Uyama and O. Matsumoto, Synthesis of Ammonia in High-Frequency Discharges. II. Synthesis of Ammonia in a Microwave Discharge Under Various Conditions, Plasma Chem. Plasma Process., 1989, 9, 421–432 CrossRef CAS.
- H. Uyama and O. Matsumoto, Synthesis of ammonia in high-frequency discharges, Plasma Chem. Plasma Process., 1989, 9, 13–24 CrossRef CAS.
- S. Tanaka, H. Uyama and O. Matsumoto, Synergistic effects of catalysts and plasmas on the synthesis of ammonia and hydrazine, Plasma Chem. Plasma Process., 1994, 14, 491–504 CrossRef CAS.
- J. L. Jauberteau, I. Jauberteau and J. Aubreton, NH3 and NHx < 3 radical downstream a microwave discharge sustained in an Ar-N2-H2 gas mixture. Study of surface reactive processes and determination of rate constants, J. Phys. D: Appl. Phys., 2002, 35, 665–674 CrossRef CAS.
- T. Fujii, K. Iwase and P. C. Selvin, Mass spectrometric analysis of a N2/H2 microwave discharge plasma, Int. J. Mass Spectrom., 2002, 216, 169–175 CrossRef CAS.
- J. Nakajima and H. Sekiguchi, Synthesis of ammonia using microwave discharge at atmospheric pressure, Thin Solid Films, 2008, 516, 4446–4451 CrossRef CAS.
- H. Uyama, T. Uchikura, H. Niijima and O. Matsumoto, Synthesis of Ammonia
with RF Discharge. Adsorption of Products on Zeolite, Chem. Lett., 1987, 16, 555–558 CrossRef.
- H. Uyama, T. Nakamura, S. Tanaka and O. Matsumoto, Catalytic effect of iron wires on the syntheses of ammonia and hydrazine in a radio-frequency discharge, Plasma Chem. Plasma Process., 1993, 13, 117–131 CrossRef CAS.
- H. Uyama and O. Matsumoto, Reaction Scheme of Ammonia Formation in Microwave Discharge from Quenching Reactions of NH Radicals by Hydrogen, Electrochem. Ind. Phys. Chem., 1993, 61, 925–926 CAS.
- J. Shah, T. Wu, J. Lucero, M. A. Carreon and M. L. Carreon, Nonthermal Plasma Synthesis of Ammonia over Ni-MOF-74, ACS Sustainable Chem. Eng., 2019, 7, 377–383 CrossRef CAS.
- J. Shah, W. Wang, A. Bogaerts and M. L. Carreon, Ammonia Synthesis by Radio Frequency Plasma Catalysis: Revealing the Underlying Mechanisms, ACS Appl. Energy Mater., 2018, 1, 4824–4839 CrossRef CAS.
- J. Shah, J. Harrison and M. Carreon, Ammonia Plasma-Catalytic Synthesis Using Low Melting Point Alloys, Catalysts, 2018, 8, 437 CrossRef.
- M. Ben Yaala,
et al., Plasma-assisted catalytic formation of ammonia in N2-H2 plasma on tungsten surface, Phys. Chem. Chem. Phys., 2019, 21(30), 16623–16633 RSC.
- M. Carreon, J. Shah, F. Gorky, P. Psarras and B. Seong, Ammonia yield enhancement by hydrogen sink effect during plasma catalysis, ChemCatChem, 2019, 12(4), 1200–1211 Search PubMed.
- M. Ben Yaala,
et al., Plasma-activated catalytic formation of ammonia from N2–H2: influence of temperature and noble gas addition, Nucl. Fusion, 2020, 60, 016026 CAS.
- M. L. Carreon, D. F. Jaramillo-Cabanzo, I. Chaudhuri, M. Menon and M. K. Sunkara, Synergistic interactions of H2 and N2 with molten gallium in the presence of plasma, J. Vac. Sci. Technol., A, 2018, 36, 021303 CrossRef.
- A. K. Brewer and R. R. Miller, The Synthesis of Ammonia in the Low Voltage Arc, J. Am. Chem. Soc., 1931, 53, 2968–2978 CrossRef CAS.
- H. Kiyooka and O. Matsumoto, Reaction scheme of ammonia synthesis in the ECR plasmas, Plasma Chem. Plasma Process., 1996, 16, 547–562 CAS.
- M. D. Bai,
et al., Synthesis of ammonia in a strong electric field discharge at ambient pressure, Plasma Chem. Plasma Process., 2000, 20, 511–520 CrossRef.
- P. Vankan, T. Rutten, S. Mazouffre, D. C. Schram and R. Engeln, Absolute density measurements of ammonia produced via plasma-activated catalysis, Appl. Phys. Lett., 2002, 418, 2000–2003 Search PubMed.
- J. H. Van Helden,
et al., Detailed study of the plasma-activated catalytic generation of ammonia in N2-H2 plasmas, J. Appl. Phys., 2007, 101, 043305 CrossRef.
- J. H. Van Helden,
et al., Production Mechanisms of NH and NH2 Radicals in N2-H2 Plasmas, J. Phys. Chem. A, 2007, 3, 11460–11472 CrossRef.
- E. Carrasco, M. Jiménez-Redondo, I. Tanarro and V. J. Herrero, Neutral and ion chemistry in low pressure dc plasmas of H2/N2 mixtures: routes for the efficient production of NH3 and NH4+, Phys. Chem. Chem. Phys., 2011, 13, 19561–19572 RSC.
- T. Body, S. Cousens, J. Kirby and C. Corr, A volume-averaged model of nitrogen – hydrogen plasma chemistry to investigate ammonia production in a plasma-surface- interaction device, Plasma Phys. Controlled Fusion, 2018, 60, 075011 CrossRef.
- S. Kumari, S. Pishgar, M. E. Schwarting, W. F. Paxton and J. M. Spurgeon, Synergistic plasma-assisted electrochemical reduction of nitrogen to ammonia, Chem. Commun., 2018, 54, 13347–13350 RSC.
- T. Haruyama,
et al., Non-catalyzed one-step synthesis of ammonia from atmospheric air and water, Green Chem., 2016, 18, 4536–4541 RSC.
- T. Sakakura,
et al., Excitation of H2O at the plasma/water interface by UV irradiation for the elevation of ammonia production, Green Chem., 2018, 20, 627–633 RSC.
- T. Sakakura, N. Murakami, Y. Takatsuji, M. Morimoto and T. Haruyama, Contribution of Discharge Excited Atomic N, N2*, and N2+ to a Plasma/Liquid Interfacial Reaction as Suggested by Quantitative Analysis, ChemPhysChem, 2019, 20, 1467–1474 CAS.
- T. Sakakura, Y. Takatsuji, M. Morimoto and T. Haruyama, Nitrogen Fixation through the Plasma/Liquid Interfacial Reaction with Controlled Conditions of Each Phase as the Reaction Locus, Electrochemistry, 2020, 88, 190–194 CrossRef CAS.
- Y. Kubota, K. Koga, M. Ohno and T. Hara, Synthesis of Ammonia through Direct Chemical Reactions between an Atmospheric Nitrogen Plasma Jet and a Liquid, Plasma Fusion Res., 2010, 5, 042–042 CrossRef.
- T. Sakakura, N. Murakami, Y. Takatsuji and T. Haruyama, Nitrogen Fixation in a Plasma/Liquid Interfacial Reaction and Its Switching between Reduction and Oxidation, J. Phys. Chem. C, 2020, 124, 9401–9408 CrossRef CAS.
- H. Conrads and M. Schmidt, Plasma generation and plasma sources, Plasma Sources Sci. Technol., 2000, 9, 441–454 CrossRef CAS.
- C. Tendero, C. Tixier, P. Tristant, J. Desmaison and P. Leprince, Atmospheric pressure plasmas: A review, Spectrochim. Acta, Part B, 2006, 61, 2–30 CrossRef.
- M. Laroussi and T. Akan, Arc–Free Atmospheric Pressure Cold Plasma Jets: A Review, Plasma Processes Polym., 2007, 4, 777–788 CrossRef CAS.
- U. Ebert,
et al., Review of recent results on streamer discharges and discussion of their relevance for sprites and lightning, J. Geophys. Res., 2010, 115, 1–13 CrossRef.
- U. Ebert,
et al., The multiscale nature of streamers, Plasma Sources Sci. Technol., 2006, 15, S118–S129 CrossRef.
- W. Wang, H. Kim, K. Van Laer and A. Bogaerts, Streamer propagation in a packed bed plasma reactor for plasma catalysis applications, Chem. Eng. J., 2018, 334, 2467–2479 CrossRef CAS.
- H.-H. Kim and A. Ogata, Nonthermal plasma activates catalyst: From current understanding and future prospects, Eur. Phys. J.: Appl. Phys., 2011, 55, 13806 CrossRef.
- H.-H. Kim, Y. Teramoto, N. Negishi and A. Ogata, A multidisciplinary approach to understand the interactions of nonthermal plasma and catalyst: A review, Catal. Today, 2015, 256, 13–22 CrossRef CAS.
- H.-H. Kim, Y. Teramoto, T. Sano, N. Negishi and A. Ogata, Effects of Si/Al ratio on the interaction of nonthermal plasma and Ag/HY catalysts, Appl. Catal., B, 2015, 166–167, 9–17 CAS.
- H.-H. Kim, Y. Teramoto and A. Ogata, Time-resolved imaging of positive pulsed corona-induced surface streamers on TiO2 and γ-Al2O3 supported Ag catalysts, J. Phys. D: Appl. Phys., 2016, 49, 415204 CrossRef.
- A. Mizuno and H. Ito, Basic performance of an electrostatically augmented filter consisting of a packed ferroelectric pellet layer, J. Electrostat., 1990, 25, 97–107 CrossRef CAS.
- T. Butterworth and R. W. K. Allen, Plasma-catalyst interaction studied in a single pellet DBD reactor: Dielectric constant effect on plasma dynamics, Plasma Sources Sci. Technol., 2017, 26, 065008 CrossRef.
- J. Kruszelnicki, K. W. Engeling and J. E. Foster, Propagation of negative electrical discharges through 2-dimensional packed bed reactors, J. Phys. D: Appl. Phys., 2017, 50, 25203 CrossRef.
- K. W. Engeling, J. Kruszelnicki and M. J. Kushner, Time-resolved evolution of micro- discharges, surface ionization waves and plasma propagation in a two-dimensional packed bed reactor, Plasma Sources Sci. Technol., 2018, 27, 085002 CrossRef.
- S. Liu, L. R. Winter and J. G. Chen, Review of Plasma-Assisted Catalysis for Selective Generation of Oxygenates from CO2 and CH4, ACS Catal., 2020, 10(4), 2855–2871 CrossRef CAS.
- F. J. J. Peeters and M. C. M. Van de Sanden, The influence of partial surface discharging on the electrical characterization of DBDs, Plasma Sources Sci. Technol., 2015, 24, 015016 CrossRef CAS.
- E. C. Neyts and A. Bogaerts, Understanding plasma catalysis through modelling and simulation—a review, J. Phys. D: Appl. Phys., 2014, 47, 1–18 Search PubMed.
- E. C. Neyts, Plasma-Surface Interactions in Plasma Catalysis, Plasma Chem. Plasma Process., 2016, 36, 185–212 CrossRef CAS.
- A. Bogaerts, Q. Zhang, Y. Zhang, K. Van Laer and W. Wang, Burning questions of plasma catalysis : Answers by modeling, Catal. Today, 2019, 337, 3–14 CrossRef CAS.
- J. C. Whitehead, Plasma-catalysis: Is it just a question of scale?, Front. Chem. Sci. Eng., 2019, 13, 264–273 CrossRef.
- J. C. Whitehead, Plasma catalysis: A solution for environmental problems, Pure Appl. Chem., 2010, 82, 1329–1336 CAS.
- J. C. Whitehead, Plasma-catalysis: The known knowns, the known unknowns and the unknown unknowns, J. Phys. D: Appl. Phys., 2016, 49, 243001 CrossRef.
-
J. C. Whitehead, Plasma-catalysis: Introduction and history, in Plasma Catalysis: Fundamentals and Applications, ed. X. Tu, T. Nozaki and J. C. Whitehead, Springer International Publishing AG, 2018 Search PubMed.
- K. Ostrikov, Plasma-nano-interface in perspective: From plasma-for-nano to nano-plasmas, Plasma Phys. Controlled Fusion, 2019, 61, 014028 CrossRef CAS.
- E. C. Neyts and P. Brault, Molecular Dynamics Simulations for Plasma-Surface Interactions, Plasma Processes Polym., 2017, 14, 1–18 Search PubMed.
- J. Van Durme, J. Dewulf, C. Leys and H. Van Langenhove, Combining non-thermal plasma with heterogeneous catalysis in waste gas treatment: A review, Appl. Catal., B, 2008, 78, 324–333 CrossRef CAS.
- B. Wang,
et al., The Mechanism of Non-thermal Plasma Catalysis on Volatile Organic Compounds Removal, Catal. Surv. Asia, 2018, 22, 73–94 CrossRef CAS.
- K. Van Laer and A. Bogaerts, Fluid modelling of a packed bed dielectric barrier discharge plasma reactor, Plasma Sources Sci. Technol., 2015, 25, 015002 CrossRef.
- K. Van Laer and A. Bogaerts, Influence of Gap Size and Dielectric Constant of the Packing Material on the Plasma Behaviour in a Packed Bed DBD Reactor: A Fluid Modelling Study, Plasma Processes Polym., 2017, 14, 1600129 CrossRef.
- K. Van Laer and A. Bogaerts, How bead size and dielectric constant affect the plasma behaviour in a packed bed plasma reactor: a modelling study, Plasma Sources Sci. Technol., 2017, 26, 085007 CrossRef.
- M. Liu, Y. Yi, L. Wang, H. Guo and A. Bogaerts, Hydrogenation of Carbon Dioxide to Value-Added Chemicals by Heterogeneous Catalysis and Plasma Catalysis, Catalysts, 2019, 9, 275 CrossRef.
- C. T. Rettner and H. Stein, Effect of vibrational energy on the dissociative chemisorption of N2 on Fe(111), J. Chem. Phys., 1987, 87, 770–771 CrossRef CAS.
- J. Kim, D. B. Go and J. C. Hicks, Synergistic effects of plasma-catalyst interactions for CH4 activation, Phys. Chem. Chem. Phys., 2017, 19, 13010–13021 RSC.
- J. Quan,
et al., Vibration-driven reaction of CO2 on Cu surfaces via Eley–Rideal-type mechanism, Nat. Chem., 2019, 11, 722–729 CrossRef CAS.
- A. Jafarzadeh, K. M. Bal, A. Bogaerts and E. C. Neyts, Activation of CO2 on Copper Surfaces: The Synergy between Electric Field, Surface Morphology, and Excess Electrons, J. Phys. Chem. C, 2020, 124(12), 6747–6755 CrossRef CAS.
- K. M. Bal, S. Huygh, A. Bogaerts and E. C. Neyts, Effect of plasma-induced surface charging on catalytic processes: Application to CO2 activation, Plasma Sources Sci. Technol., 2018, 27, 024001 CrossRef.
- K. M. Bal and E. C. Neyts, Overcoming Old Scaling Relations and Establishing New Correlations in Catalytic Surface Chemistry: Combined Effect of Charging and Doping, J. Phys. Chem. C, 2019, 123, 6141–6147 CrossRef CAS.
- C. J. Lee, D. H. Lee and T. Kim, Modification of catalyst surface from interaction between catalysts and dielectric barrier discharge plasma, J. Nanosci. Nanotechnol., 2017, 17, 2707–2710 CrossRef CAS.
- Y. Guo, D. Ye, K. Chen, J. He and W. Chen, Toluene decomposition using a wire-plate dielectric barrier discharge reactor with manganese oxide catalyst in situ, J. Mol. Catal. A: Chem., 2006, 245, 93–100 CrossRef CAS.
- U. Roland, F. Holzer and F. D. Kopinke, Improved oxidation of air pollutants in a non-thermal plasma, Catal. Today, 2002, 73, 315–323 CrossRef CAS.
- Y. R. Zhang, K. Van Laer, E. C. Neyts and A. Bogaerts, Can plasma be formed in catalyst pores? A modeling investigation, Appl. Catal., B, 2016, 185, 56–67 CrossRef CAS.
- Q. Z. Zhang and A. Bogaerts, Propagation of a plasma streamer in catalyst pores, Plasma Sources Sci. Technol., 2018, 27, 035009 CrossRef.
- Y. R. Zhang, E. C. Neyts and A. Bogaerts, Influence of the material dielectric constant on plasma generation inside catalyst pores, J. Phys. Chem. C, 2016, 120, 25923–25934 CrossRef CAS.
- Y. R. Zhang, E. C. Neyts and A. Bogaerts, Enhancement of plasma generation in catalyst pores with different shapes, Plasma Sources Sci. Technol., 2018, 27, 055008 CrossRef.
- Q.-Z. Zhang, W.-Z. Wang and A. Bogaerts, Importance of surface charging during plasma streamer propagation in catalyst pores, Plasma Sources Sci. Technol., 2018, 27, 065009 CrossRef.
- R. Kojima and K.-I. Aika, Cobalt molybdenum bimetallic nitride catalysts for ammonia synthesis, Chem. Lett., 2000, 29, 514–515 CrossRef.
- T. Czerwiec, H. Michel and E. Bergmann, Low-pressure, high-density plasma nitriding: mechanisms, technology and results, Surf. Coat. Technol., 1998, 108–109, 182–190 CrossRef CAS.
- B. Ashford and X. Tu, Non-thermal plasma technology for the conversion of CO2, Curr. Opin. Green Sustainable Chem., 2017, 3, 45–49 CrossRef.
- E. Chiremba, K. Zhang, C. Kazak and G. Akay, Direct Nonoxidative Conversion of Methane to Hydrogen and Higher Hydrocarbons by Dielectric Barrier Discharge Plasma with Plasma Catalysis Promoters, AIChE J., 2017, 63, 4418–4429 CrossRef CAS.
- M. L. Carreon, Plasma catalytic ammonia synthesis: state of the art and future directions, J. Phys. D: Appl. Phys., 2019, 52, 483001 CrossRef CAS.
- M. Alsfeld and E. Wilhelmy, Über die Bildung von Ammoniak aus seinen Elementen durch elektrische Gasentladungen, Ann. Phys., 1931, 400, 89–123 CrossRef.
- W. von Siemens, Ueber die elektrostatische Induction und die Verzögerung des Stroms in Flaschendrähten, Ann. Phys., 1857, 178, 66–122 CrossRef.
- W. F. Donkin, On the direct synthesis of ammonia, London, Edinburgh Dublin Philos. Mag. J. Sci., 1873, 21, 281–282 Search PubMed.
- J. C. Devins and M. Burton, Formation of Hydrazine in Electric Discharge Decomposition of Ammonia, J. Am. Chem. Soc., 1954, 76, 2618–2626 CrossRef CAS.
- E. N. Eremin, A. N. Maltsev and V. L. Syaduk, Catalytic synthesis of ammonia in a barrier discharge, Russ. J. Phys. Chem., 1971, 45, 635–636 Search PubMed.
- L. Petitjean and A. Ricard, Emission spectroscopy study of N2-H2 glow discharge for metal surface nitriding, J. Phys. D: Appl. Phys., 1984, 17, 919–929 CrossRef CAS.
- J. Loureiro and A. Ricard, Electron and vibrational kinetics in an N2-H2 glow discharge with application to surface processes, J. Phys. D: Appl. Phys., 1993, 163 CrossRef CAS.
- J. Amorim, G. Baravian and A. Ricard, Production of N, H, and NH Active Species in N2-H2 dc Flowing Discharges, Plasma Chem. Plasma Process., 1995, 15, 721–731 CrossRef CAS.
- P. Bletzinger and B. N. Ganguly, High fractional dissociation efficiency in H2 and H2-N2 gas mixtures in a helical resonator discharge, Chem. Phys. Lett., 1995, 247, 584–588 CAS.
- R. Nagpal, B. N. Ganguly, P. Bletzinger and A. Garscadden, Power deposition in H and H2-N2 glow discharges, Chem. Phys. Lett., 1996, 257, 386–392 CrossRef CAS.
- J. Amorim, G. Baravian, S. Bockel, A. Ricard and G. Sultan, Laser and Emission Spectroscopy in H2 and H2-N2 dc Discharges, J. Phys. III, 1996, 6, 1147–1155 CrossRef CAS.
- J. Helminen, J. Helenius, E. Paatero and I. Turunen, Adsorption Equilibria of Ammonia Gas on Inorganic and Organic Sorbents at 298.15 K, J. Chem. Eng. Data, 2001, 46, 391–399 CrossRef CAS.
- J. Helminen, J. Helenius, E. Paatero and I. Turunen, Comparison of sorbents and isotherm models for NH3-gas separation by adsorption, AIChE J., 2000, 46, 1541–1555 CrossRef CAS.
- C. Y. Liu and K. Aika, Ammonia Absorption into Alkaline Earth Metal Halide Mixtures as an Ammonia Storage Material, Ind. Eng. Chem. Res., 2004, 43, 7484–7491 CrossRef CAS.
-
N. V. Srinath, Plasma catalytic ammonia synthesis at atmospheric pressure in a dielectric barrier discharge reactor, Eindhoven University of Technology, 2017 Search PubMed.
-
B. S. Patil, Plasma (catalyst) - assisted nitrogen fixation: reactor development for nitric oxide and ammonia production, Eindhoven University of Technology, 2017 Search PubMed.
- X. Bai,
et al., Microwave catalytic synthesis of ammonia from methane and nitrogen, Catal. Sci. Technol., 2018, 8, 6302–6305 RSC.
-
L. G. Siemsen, The synthesis of ammonia from hydrogen and atomic nitrogen on the Rh(110) surface, Iowa State University, 1990 Search PubMed.
- M. Akiyama, K. Aihara, T. Sawaguchi, M. Matsukata and M. Iwamoto, Ammonia decomposition to clean hydrogen using non-thermal atmospheric-pressure plasma, Int. J. Hydrogen Energy, 2018, 43, 14493–14497 CAS.
- M. Bai, Z. Zhang, H. Han, Y. Wang and X. Bai, Studies of ammonia synthesis in a strong ionization discharge at ambient pressure, Conf. Rec. Ind. Appl. Soc. IEEE-IAS Annu. Meet., 2001, 2, 1103–1107 Search PubMed.
- K. H. R. Rouwenhorst,
et al., Plasma-Catalytic Ammonia Synthesis beyond Thermal Equilibrium over Ru-based Catalysts, ChemCatChem, 2021 Search PubMed , under review.
- M. Muhler, F. Rosowski, O. Hinrichsen, A. Hornung and G. Ertl, Ruthenium as catalyst for ammonia synthesis, Stud. Surf. Sci. Catal., 1996, 101, 317–326 CrossRef CAS.
- B. Hammer and J. K. Norskov, Theoretical Surface Science and Catalysis—Calculations and Concepts, Adv. Catal., 2000, 45, 71–129 CAS.
- A. Vojvodic,
et al., Exploring the limits: A low-pressure, low-temperature Haber-Bosch process, Chem. Phys. Lett., 2014, 598, 108–112 CrossRef CAS.
-
G. Ertl, Mechanisms of Heterogeneous Catalysis, in Reactions at Solid Surfaces, John Wiley & Sons, Inc., 2009, pp. 123–139 Search PubMed.
- Y. Yi, L. Wang, Y. Guo, S. Sun and H. Guo, Plasma-assisted ammonia decomposition over Fe–Ni alloy catalysts for COx-Free hydrogen, AIChE J., 2019, 65, 691–701 CAS.
- L. Wang,
et al., Highly Dispersed Co Nanoparticles Prepared by an Improved Method for Plasma-Driven NH3 Decomposition to Produce H2, Catalysts, 2019, 9, 107 CrossRef.
- S. Q. Sun, Y. H. Yi, L. Wang, J. L. Zhang and H. C. Guo, Preparation and performance of supported bimetallic catalysts for hydrogen production from ammonia decomposition by plasma catalysis, Acta Phys.-Chim. Sin., 2017, 33, 1123–1129 CAS.
- L. Wang,
et al., Synergy of DBD plasma and Fe-based catalyst in NH3 decomposition: Plasma enhancing adsorption step, Plasma Processes Polym., 2017, 14, e1600111 Search PubMed.
- L. Wang, Y. Zhao, C. Liu, W. Gong and H. Guo, Plasma driven ammonia decomposition on a Fe-catalyst: Eliminating surface nitrogen poisoning, Chem. Commun., 2013, 49, 3787–3789 RSC.
- L. Wang,
et al., NH3 Decomposition for H2 Generation: Effects of Cheap Metals and Supports on Plasma-Catalyst Synergy, ACS Catal., 2015, 5, 4167–4174 CrossRef CAS.
- P. Mehta,
et al., Plasma-Catalytic Ammonia Synthesis Beyond the Equilibrium Limit, ACS Catal., 2020, 10(12), 6726–6734 CrossRef CAS.
- H. H. Himstedt, M. S. Huberty, A. V. McCormick, L. D. Schmidt and E. L. Cussler, Ammonia synthesis enhanced by magnesium chloride absorption, AIChE J., 2015, 61, 1364–1371 CrossRef CAS.
- S. Zen, T. Abe and Y. Teramoto, Indirect Synthesis System for Ammonia from Nitrogen and Water Using Nonthermal Plasma Under Ambient Conditions, Plasma Chem. Plasma Process., 2018, 38, 347–354 CrossRef CAS.
- S. Zen, T. Abe and Y. Teramoto, Atmospheric Pressure Nonthermal Plasma Synthesis of Magnesium Nitride as a Safe Ammonia Carrier, Plasma Chem. Plasma Process., 2019, 39, 1203–1210 CrossRef CAS.
- Y. Hayakawa,
et al., Hydrogen production system combined with a catalytic reactor and a plasma membrane reactor from ammonia, Int. J. Hydrogen Energy, 2019, 44, 9987–9993 CrossRef CAS.
- A. R. Hanna, T. L. Van Surksum and E. R. Fisher, Investigating the impact of catalysts on N2 rotational and vibrational temperatures in low pressure plasmas, J. Phys. D: Appl. Phys., 2019, 52, 345202 CrossRef CAS.
- A. K. Brewer and J. W. Westhaver, Chemical Action in the Glow Discharge. IV, J. Phys. Chem., 1930, 34, 1280–1293 CrossRef CAS.
- E. N. Eremin and A. N. Maltsev, Behaviour of a catalyst in a glow-discharge plasma, Russ. J. Phys. Chem., 1969, 3, 43 Search PubMed.
- A. N. Maltsev and E. N. Eremin, Activity of heterogeneous catalysts in the synthesis of ammonia in the glow discharge, Russ. J. Phys. Chem., 1968, 9, 1235–1237 Search PubMed.
- A. de Castro and F. L. Tabarés, Role of nitrogen inventory and ion enhanced N-H recombination in the ammonia formation on tungsten walls. A DC glow discharge study, Vacuum, 2018, 151, 66–72 CrossRef CAS.
- Y. Zhao, L. Wang, J. Zhang and H. Guo, Enhancing the ammonia to hydrogen (ATH) energy efficiency of alternating current arc discharge, Int. J. Hydrogen Energy, 2014, 39, 7655–7663 CrossRef CAS.
- Y. Zhao, L. Wang, J. L. Zhang and H. C. Guo, Influence of non-thermal plasma discharge mode and reactor structure on ammonia decomposition to hydrogen, Acta Phys.-Chim. Sin., 2014, 30, 738–744 CAS.
- Y. Engelmann, K. van ‘t Veer, E. C. Neyts, W. F. Schneider and A. Bogaerts, Plasma catalysis for ammonia synthesis: the importance of Eley-Rideal reactions, ACS Catal., 2021 Search PubMed , under revision.
- S. Wang,
et al., Universal transition state scaling relations for (de)hydrogenation over transition metals, Phys. Chem. Chem. Phys., 2011, 13, 20760–20765 RSC.
- K. Van ‘t Veer, Y. Engelmann, F. Reniers and A. Bogaerts, Plasma-catalytic ammonia synthesis in a DBD plasma: Role of the micro-discharges and their afterglows, J. Phys. Chem. C, 2021 Search PubMed , under review.
- W. Wang, B. Patil, S. Heijkers, V. Hessel and A. Bogaerts, Nitrogen Fixation by Gliding Arc Plasma: Better Insight by Chemical Kinetics Modelling, ChemSusChem, 2017, 10, 2145–2157 CrossRef CAS.
- E. Vervloessem, M. Aghaei, F. Jardali, N. Hafezkhiabani and A. Bogaerts, Plasma-based N2 fixation into NOx: Insights from modeling toward optimum yields and energy costs in a gliding arc plasmatron, ACS Sustainable Chem. Eng., 2020, 8(26), 9711–9720 CrossRef CAS.
- J. S. Hummelshøj, F. Abild-pedersen, F. Studt, T. Bligaard and J. K. Nørskov, CatApp: A web application for surface chemistry and heterogeneous catalysis, Angew. Chem., Int. Ed., 2012, 51, 272–274 CrossRef.
- K. Aika,
et al., Support and promoter effect of ruthenium catalyst. III. Kinetics of ammonia synthesis over various Ru catalysts, Appl. Catal., 1986, 28, 57–68 CrossRef CAS.
- R. Pandya, R. Mane and C. V. Rode, Cascade dehydrative amination of glycerol to oxazoline, Catal. Sci. Technol., 2018, 8, 2954–2965 CAS.
- S. Dahl,
et al., Role of Steps in N2 Activation on Ru(0001), Phys. Rev. Lett., 1999, 83, 1814–1817 Search PubMed.
- M. J. Murphy, J. F. Skelly, A. Hodgson and B. Hammer, Inverted vibrational distributions from N2 recombination at Ru(001): Evidence for a metastable molecular chemisorption well, J. Chem. Phys., 1999, 110, 6954–6962 CrossRef CAS.
- L. Diekhöner, H. Mortensen and A. Baurichter, N2 dissociative adsorption on Ru(0001): The role of energy loss, J. Chem. Phys., 2001, 115, 9028–9035 CrossRef.
- L. B. F. Juurlink, R. R. Smith, D. R. Killelea and A. L. Utz, Comparative study of C-H stretch and bend vibrations in methane activation on Ni(100) and Ni(111), Phys. Rev. Lett., 2005, 94, 208303 CrossRef CAS.
- L. B. F. Juurlink, R. R. Smith and A. L. Utz, The role of rotational excitation in the activated dissociative chemisorption of vibrationally excited methane on Ni(100), Faraday Discuss., 2000, 117, 147–160 RSC.
- L. B. F. Juurlink, P. R. Mccabe, R. R. Smith, C. L. Dicologero and A. L. Utz, Eigenstate-resolved studies of gas-surface reactivity: CH4(ν3) Dissociation on Ni(100), Phys. Rev. Lett., 1999, 83, 868–871 CrossRef CAS.
- Y. Teramoto and H.-H. Kim, Effect of vibrationally excited N2(v) on atomic nitrogen generation using two consecutive pulse corona discharges under atmospheric pressure N2, J. Phys. D: Appl. Phys., 2019, 52, 494003, DOI:10.1088/1361-6463/ab3f83.
- S. Van Alphen,
et al., Power Pulsing to Maximize Vibrational Excitation Efficiency in N2 Microwave Plasma: A Combined Experimental and Computational Study, J. Phys. Chem. C, 2019, 124(3), 1765–1779 CrossRef.
- G. Colonna, A. Laricchiuta and L. D. Pietanza, Time dependent selfconsistent electron energy distribution functions during nano-second repetitive discharges in reacting N2/H2 mixtures, Plasma Phys. Controlled Fusion, 2020, 62, 014003 CrossRef.
- A. Jafarzadeh, K. M. Bal, A. Bogaerts and E. C. Neyts, CO2 Activation on TiO2-Supported Cu5 and Ni5 Nanoclusters: Effect of Plasma-Induced Surface Charging, J. Phys. Chem. C, 2019, 123, 6516–6525 CrossRef CAS.
- M. A. Ardagh, O. A. Abdelrahman and P. J. Dauenhauer, Principles of Dynamic Heterogeneous Catalysis: Surface Resonance and Turnover Frequency Response, ACS Catal., 2019, 9, 6929–6937 CrossRef CAS.
- M. A. Ardagh, T. Birol, Q. Zhang, O. A. Abdelrahman and P. J. Dauenhauer, Catalytic resonance theory: SuperVolcanoes, catalytic molecular pumps, and oscillatory steady state, Catal. Sci. Technol., 2019, 9, 5058–5076 RSC.
- Z. Mujahid, J. Kruszelnicki, A. Hala and M. J. Kushner, Formation of surface ionization waves in a plasma enhanced packed bed reactor for catalysis applications, Chem. Eng. J., 2020, 382, 123038 CrossRef.
- P. Navascués, J. M. Obrero-Pérez, J. Cotrino, A. R. González-Elipe and A. Gómez-Ramírez, Isotope labelling for reaction mechanism analysis in DBD plasma processes, Catalysts, 2019, 9, 1–12 CrossRef.
- A. Fateev,
et al., Plasma Chemistry in an Atmospheric Pressure Ar/NH3 Dielectric Barrier Discharge, Plasma Processes Polym., 2005, 2, 193–200 CrossRef CAS.
- U. Kogelschatz, Dielectric Barrier Discharge: Their History, Discharge Physic, and Industrial Applications, Plasma Chem. Plasma Process., 2003, 23, 1–46 CrossRef CAS.
- P. Pässler,
et al., Acetylene, Ullmann's Encycl. Ind. Chem., 2011, 1–50, DOI:10.1002/14356007.a01_097.pub4.
|
This journal is © The Royal Society of Chemistry 2020 |
Click here to see how this site uses Cookies. View our privacy policy here.