DOI:
10.1039/C9GC04457D
(Critical Review)
Green Chem., 2020,
22, 1019-1037
Strategies for structuring diverse emulsion systems by using wood lignocellulose-derived stabilizers
Received
31st December 2019
, Accepted 30th January 2020
First published on 30th January 2020
Abstract
Wood biomass is an abundant renewable source of materials, but due to the accelerating depletion of natural resources, it is important to explore new ways to use it in a more sustainable manner. Modern technologies enable the recovery and valorization of the main components of wood—namely, cellulose, lignin, and hemicelluloses—contributing to sustainability. However, the method of isolation and resulting structure and purity of lignocellulosic materials determine their functionality and applicability. This review discusses the properties of all three main wood-based compounds that can stabilize emulsions, a class of industrial dispersions that are widely used in life science applications and chemicals. Due to the multi-billion-dollar annual market for hydrocolloids, the food, pharmaceutical, cosmetic, coating, and paint industries are actively seeking new sustainable emulsion stabilizers that fulfill the demanding requirements regarding safety and functionality. Wood-derived stabilizers facilitate various mechanisms involved in emulsion stabilization: (1) development of amphiphilic structures that decrease interfacial tension, (2) stabilization of interfaces by particles according to the Pickering theory, and (3) increase in the viscosity of emulsions’ continuous phase. This review presents pathways for treating cellulose, lignin, and hemicelluloses to achieve efficient stabilization and provides suggestions for their broad use in emulsions.
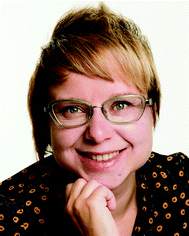 Kirsi S. Mikkonen | Dr Kirsi S. Mikkonen is Assistant Professor in Food Sciences at the Department of Food and Nutrition, University of Helsinki. She also works as an Academy of Finland Research Fellow. Assist. Prof. Mikkonen leads the Food Materials Science research group (http://www.helsinki.fi/food-materials-science). Her research interests include valorization of industrial side streams for food and packaging materials, focusing on wood and grain hemicelluloses and fungal biomass. Assist. Prof. Mikkonen has more than 15 years research experience on hemicelluloses. She also develops active packaging materials to prevent food waste, and teaches food technology to undergraduate students. |
1. Introduction
On average, the Earth is covered by about 200 trees per ha, totaling an estimated 3.04 trillion.1 Forests are important, acting as a carbon sink and maintaining vital oxygen levels in the atmosphere via photosynthesis. In addition, forest ecosystems foster biological diversity and serve as sources of valuable commodities to meet the demands of modern society. When managed conservatively and used economically, forests can be viewed as a major renewable and sustainable resource.
The forest industry, which has a long tradition of exploiting and processing wood, is currently undergoing a transition from pulp and paper mills to biorefineries.2 These establishments provide new, diverse, and refined bio-based products to replace those that were typically derived from fossil fuels in addition to manufacturing more traditional fiber-based products.3 Within the circular (bio)economy vision, all material streams are fully utilized and recycled, reducing industrial waste and saving resources. However, the traditional forest industry was based on the refinement of cellulose—the main constituent of wood—and the other constituents, most importantly lignin and hemicelluloses, were partly lost with the process water, degraded, or burned for energy. To overcome this problem, extensive research and development have been performed within the past few decades, resulting in the invention and application of methods to upgrade wood-based compounds into various types of chemicals, precursors, particles, and fuel in addition to traditional cellulosic fibers.4–6
Cellulose, lignin, and hemicelluloses are distinguished by their chemical structures, physical attributes, methods for recovery from woody biomass, further derivatization treatments, and functional properties. Their unique characteristics are beneficial for specific applications. For example, regular-structured, high-molecular mass cellulose can form strong materials,4 and the complex polyphenolic composition of lignin enables multiple pathways for its modification into chemical reagents.5 Hemicelluloses, on the other hand, are intermediate in size, which compromises their performance in materials for which high stiffness or strength is required. They may be hydrolyzed into monosaccharides and fermented to produce ethanol, or they may be converted into furfural.6–8 The variation in their properties enables bio-based raw materials to play a large role in manufactured products, including emulsions, a class of industrial dispersions widely used in food and other life science products, paints, coatings, and adhesives. As there is currently a multi-billion-dollar annual market for hydrocolloids,9 industries are actively seeking new sustainable emulsion stabilizers that fulfill the demanding requirements regarding safety and functionality. For example, the global consumption of emulsion stabilizers for beverages alone was foreseen to surpass 210
000 MT in 2018, and it continues to grow annually by 4%.10 The global surfactant market for detergent formulations is more than 18 MT, which is worth 19 $ billion per year.11 The market value of food hydrocolloids is about 4.4 $ billion.9 Large quantities of surfactants are continuously released into the environment, where they may or may not be degraded, depending on their structure.11
In contrast to starch, the production and utilization of wood-based stabilizers does not compete with food production. Wood-based stabilizers may replace non-renewable chemicals, provide clean-label alternatives to synthetic additives, and/or serve as non-toxic, biocompatible, and biodegradable structuring agents in dispersed systems. Various methods are used to convert wood or pulp into efficient stabilizers. For example, optimized aqueous extraction of hemicelluloses yields native functional emulsifiers;12–15 cellulose may be disintegrated into nanoparticles16,17 or modified to become a water-soluble derivative;18 and lignin may be transformed into amphiphilic molecules via grafting with other building blocks.19,20 Subsequently, emulsion stability is achieved through interfacial activity of the amphiphilic surfactants, Pickering stabilization with insoluble particles, or an increase in the viscosity of the continuous phase. This review discusses these conversion methods and the functionality they achieve, emphasizing the design of new safe green materials.
2. Emulsions as diverse modern industrial systems
Emulsions are dispersions of at least two immiscible liquids, typically oil and water, in which one of the liquids forms the dispersed phase (i.e., droplets that are surrounded by the other liquid) and the other forms the continuous phase.21 Oil-in-water (o/w) emulsions feature oil droplets immersed in water, water-in-oil (w/o) emulsions consist of aqueous droplets immersed in oil, and oil-in-water-in-oil (o/w/o) or water-in-oil-in-water (w/o/w) compositions are multiple emulsions that can be applied in certain cases that require their good encapsulation and protection capacity.22 These morphologies result in a large interfacial area between the different phases, causing interfacial tension at the oil–water interface. Therefore, emulsion formation requires energy. During storage, emulsions seek to minimize the energy used by reducing the interfacial area, which is why emulsion structures tend to break down during time.21,23
The energy required for emulsion formation can be reduced by using emulsifiers.21,23 Typically, these are relatively low-molar mass amphiphilic compounds that can be rapidly assembled at the interface at which droplets are formed during liquid flow in emulsion mixing. Surface-active emulsifiers lower the interfacial tension between the dispersed and continuous phases and thus decrease droplet size. In most cases, emulsifiers provide only short-term stability. Long-term kinetic stability is achieved by applying stabilizing agents, which may function by lowering interfacial tension, forming a mechanical barrier between the droplets and the continuous phase, or increasing viscosity of the continuous phase.23 A stabilizer may reinforce the interfacial layer between the emulsion phases, forming a film and causing steric hindrance, which separates droplets and prevents them from coalescing. Interfacial layers can be formed by amphiphilic molecules or insoluble particles. The sides of these molecules or particles exhibit different polarities, and the nonpolar side is drawn towards oil while the polar side is drawn towards water. Depending on the morphology and electrostatic properties of the interfacial layer, droplets can be protected against coalescence and flocculation.24 Furthermore, the mobility of droplets can be regulated by adjusting the viscosity of the continuous phase.21 In o/w emulsions, this can be done with macromolecular hydrocolloids; entangling them in an aqueous environment entraps the droplets and prevents them from creaming/undergoing sedimentation and collision. Viscosity and droplet mobility in w/o emulsions are most influenced by the lipid structure and flow properties of the oil.
The physical stability of emulsions requires the maintenance of evenly dispersed droplets with constant size distribution. However, physical stabilization alone is not sufficient to preserve the quality of emulsions, especially those containing polyunsaturated lipids, as the double bonds in lipids are prone to oxidization through a radical chain mechanism. Lipid oxidation deteriorates life science products by decreasing the lipids’ nutritional or pharmacological value, leading to the development of rancid flavors and, possibly, the formation of toxic reaction products. Emulsification accelerates the oxidation rate by increasing the total surface area of oil droplets, which exposes them to reactions with oxygen.25–27 Consequently, there is considerable interest in the development of effective strategies for retarding the oxidation of unsaturated lipids in emulsions.28,29
Emulsions are utilized in numerous products to protect sensitive ingredients, control dosage, make application easier, or conceal or adjust taste. The culinary field contains many classical examples of emulsions, including milk, beverages, mayonnaise, chocolate, and sausages. Life science products with emulsion structures include pharmaceutical and cosmetic creams, lotions, microencapsulated drugs, and bioactive compounds, some of which may have designated release points in the gastrointestinal tract.30 Technical emulsions are applied in paints, where the dispersal of binders decreases viscosity and facilitates spreading and drying of the coating layer.14,31 Emulsions are also applied in chemicals, such as those involved in polymerization reactions, as a way of controlling the contact between reagents.32
Emulsions have multiple uses, numerous alternative ingredients, and diverse physicochemical and functional properties. Thus, the requirements regarding emulsifiers and stabilizing agents vary. Lipid phase, pH, and the ionic strength of the aqueous phase play a major role in emulsions’ stability. For amphiphilic stabilizers, the size and proportion of the polar and nonpolar parts determines the position at which the stabilizer is anchored at the droplet interface (i.e., hydrophilic–lipophilic balance, HLB).21 This, in turn, determines whether the stabilizer is applicable to o/w or w/o emulsions. The size, shape, and surface chemistry of particles define their ability to assemble at an interface, and the macromolecular properties of hydrocolloids, such as hydrodynamic volume and polymer entanglement, determine the associations between stabilizer molecules and emulsion droplets.23
Food emulsions are commonly stabilized with starch derivatives,9 phospholipids (e.g., soy lecithin), or synthetic emulsifiers (e.g., polysorbates).21 However, the abundance of allergies among consumers and demand for “clean-label” food is increasing consumers’ interest in new stabilizers. Synthetic emulsifying and stabilizing agents with HLBs optimized for various products can be manufactured from either petroleum-derived or bio-based alkyls. Wood biomass is an attractive material that can lead to an increase in the share of bio-based emulsifiers and stabilizers and replacement of non-renewable ones, exploration of new alternatives for green chemicals, and the achievement of good functional properties without compromising environmental and human safety. In addition, production of wood biomass does not compete with food production.
3. Lignocellulosic materials – bioresources and structural characteristics
Wood biomass is mainly composed of lignocellulosics, generally containing 40–50% cellulose, 20–35% lignin, and 20–35% hemicelluloses (Fig. 1).33,34 However, the composition of a tree varies depending on its species, age, growing conditions, and harvesting season. To release and recover individual components, wood biomass is commonly subjected to pretreatment, which can take the form of mechanical milling, extrusion, acid, alkaline, or organosolv treatments, oxidation, ionic liquids, or hot water extraction.35–38 Green biomass treatment methods include deep eutectic solvents, steam explosion, supercritical fluids, and microbial degradation, and emerging lignocellulose pretreatment methods include microwave irradiation, ultrasound, gamma radiation, electron beam irradiation, pulsed-electric field, high hydrostatic pressure, and high pressure homogenization.39 Also, we recently presented centrifugation as a solvent-free method of separating lignin- and hemicellulose-rich fractions in softwood extracts.40
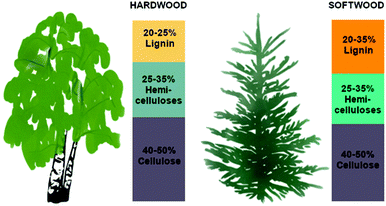 |
| Fig. 1 The main components of wood: Cellulose, lignin, and hemicelluloses. The lignin and hemicellulose composition varies depending on the wood species. In addition to the three main components, wood also contains extractives, usually less than 10 wt%.33 | |
3.1. Cellulose
At the molecular level, cellulose consists of long and linear β-(1 → 4)-linked glucopyranosyl chains (Fig. 2). Industrially prepared wood-based cellulose samples from acid sulfite process showed molar mass up to 1.5 × 106 g mol−1.32 Due to the large molar mass and regularity of the structure, numerous hydroxyl groups cause hydrogen bonding and van der Waals forces between the individual chains.41 Cellulose is organized into repeated crystalline structures and forms microfibrils in the wood cell wall, which in turn form larger macroscopic fibers.42 Native cellulose is practically insoluble in water, but it can be dissolved in other solvents, such as acids. Treatment of dissolved cellulose with a non-solvent, such as water, results in regeneration of cellulose in solid form.43 Cellulose pulp can also be dispersed in an alkaline solution and then treated with appropriate reagents to substitute the anhydroglucosyl monomers of the cellulose chain and yield water-soluble derivatives. The products of chloromethane, propylene oxide, mixed chloromethane and propylene oxide, mixed chloromethane and chloroethane, and monochloracetic acid are methyl cellulose (MC), hydroxypropyl cellulose (HPC), hydroxypropyl methyl cellulose (HPMC), methylethyl cellulose (MEC), and carboxymethyl cellulose (CMC), respectively (Fig. 3).18 These are the chemical derivatives of cellulose that are most widely used as emulsion stabilizers. However, numerous other pathways for cellulose modification have been reviewed by others.44,45
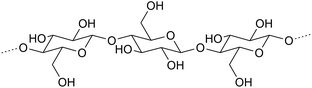 |
| Fig. 2 Partial chemical structure of cellulose. | |
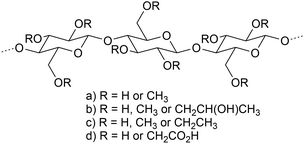 |
| Fig. 3 Partial structures of cellulose derivatives with (a) methyl, (b) hydroxypropyl methyl, (c) methyl ethyl, and (d) carboxymethyl groups. | |
A hierarchical cell wall structure is the basis of cellulose fibers, microcrystalline and microfibrillated celluloses (MCC and MFC, respectively), nanofibrils (CNF), and nanocrystals (CNC). Preparation of MCC, MFC, CNF, and CNC involves breaking down the hierarchy into individualized micro- or nanostructures with high crystallinity, therefore reducing the amount of amorphous material present.4,46 CNF is prepared by extracting fine nano-sized fibrils from pulp via mechanical processing and/or homogenization. Oxidation by (2,2,6,6-tetramethylpiperidin-1-yl)oxyl (TEMPO) or enzymatic pretreatment may be used to facilitate fibrillation and reduce the amount of mechanical energy needed to disintegrate structures. CNC is even more crystalline than CNF and is commonly obtained after amorphous parts are removed by acid hydrolysis. The size and aspect ratio of CNF and CNC determine their properties. The length of CNC generally ranges between 100 and 300 nm, while CNF may be up to one μm in length. The width of individual CNC and CNF nanoparticles ranges from a few nanometers to tens of nanometers, and they may appear in bundles of several particles.4 CNC and CNF grades also differ in cellulose purity, as residual hemicelluloses may be present up to 25% in hardwood pulp used as starting material for nanocellulose preparation.47
3.2. Lignin
Lignin is a complex aromatic polymer located mainly in the secondary cell walls of wood.33 In contrast to cellulose, the structure of lignin is not uniform and lacks a repetitive polymeric pattern. The structure of lignin varies remarkably between wood species, and even between parts of individual trees, so there is a low probability that two lignin macromolecules will be identical.48 Furthermore, lignin is highly reactive and tightly bound with cellulose and hemicelluloses in the cell wall. Thus, its structure is often altered during isolation, which complicates efforts to define its native formulation in detail. Lignin is composed of 4-hydroxyphenylpropanoid units that polymerize to form a netlike structure. Three different phenylpropanoid molecules are known to function as major precursors to lignin polymers: p-coumaryl alcohol, coniferyl alcohol, and sinapyl alcohol. These precursors polymerize via radical oxidative coupling and form p-hydroxyphenyl, guaiacyl, and syringyl units (Fig. 4).48
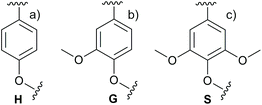 |
| Fig. 4 The (a) p-hydroxyphenyl, (b) guaiacyl, and (c) syringyl units that comprise lignin. For a comprehensive description of lignin structure, a review by Ralph et al.48 is recommended. | |
For analytical purposes, lignin can be isolated from pretreated, disrupted wood biomass by removing carbohydrates after hydrolyzation or by extraction. Lignin is nonpolar and shows low solubility in common solvents.33 Chemical derivatization introduces functional groups and solubilizes lignin, after which it can be separated from solid cellulose and hemicelluloses. In industrial scale, large quantities of lignin are released in the spent liquor of sulfite and Kraft pulping processes (40–50%49 and 30–35%50 of the spent liquor, respectively). Sulfite pulping is performed in the presence of sulfur dioxide and sulfite ions33 and it produces lignosulfonic acids and salts in the spent liquor.51 Lignosulfonates are anionic polymers in which the essentially hydrophobic lignin backbone is rendered hydrophilic by substitution of sulfonate groups. Lignosulfonates are highly crosslinked and contain some carboxylate groups. The polyelectrolyte nature of lignosulfonates gives them dispersive and adhesive properties.51,52 In Kraft pulping, wood is treated at elevated temperature with a mixture of sodium hydroxide and sodium sulfide.33 Phenolic hydroxyl and carboxyl groups as well as sulfur are introduced in the lignin structure,53 and simultaneously, side chains and substructures may be slightly altered.54 Other variations of pulping processes yielding lignin are also used and developed. For example, one type of biorefinery concept applies hot water extraction of wood to recover hemicelluloses, and sequential alkaline extraction to separate lignins from the pulp.55
Traditionally, lignin was treated as waste and used for low-value applications, such as energy production. However, advances in lignin modification chemistry have produced a number of functional lignin-derived polymers that exploit both the intrinsic features of lignin and the properties of grafted functional groups. Current applications of lignin-derived biopolymers include reinforcement fillers, antioxidants, UV adsorbents, antimicrobial agents, carbon precursors, biomaterials for tissue engineering and gene therapy, and smart materials, which were recently reviewed by Kai et al.5
3.3. Hemicelluloses
Hemicelluloses are heteropolysaccharides that are closely associated with cellulose and lignin in wood cell walls. The most abundant hemicelluloses in hardwoods are xylans (25–35% of wood mass), and mannans are most abundant in softwoods (about 20% of wood mass). Softwoods contain 5–10% xylan, and hardwoods contain a minor quantity of glucomannan (2–5%) (Fig. 5).33,34
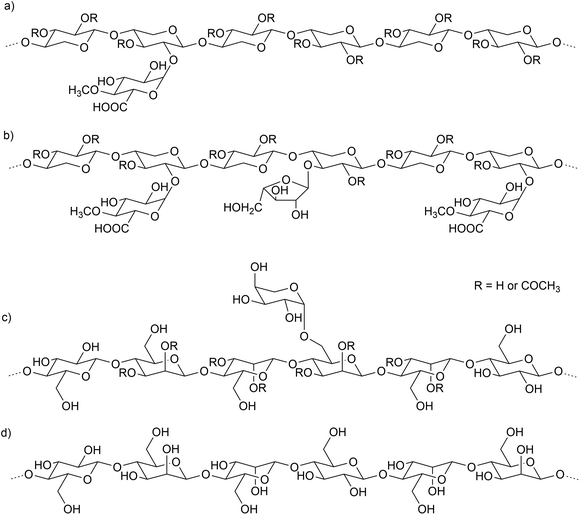 |
| Fig. 5 Partial structure of (a) glucuronoxylan, (b) arabinoglucuronoxylan, (c) galactoglucomannan, and (d) glucomannan. | |
Hardwood xylans consist of β-D-xylopyranosyl units linked by (1 → 4)-bonds and substituted with (1 → 2)-linked 4-O-methyl-α-D-glucopyranosyl uronic acid and acetyl groups (glucuronoxylans, GX).33,34 Xylans from softwoods are substituted with (1 → 2)-linked 4-O-methyl-α-D-glucopyranosyl uronic acid and (1 → 3)-linked α-L-arabinofuranosyl units (arabinoglucuronoxylans; AGX).56 On average, seven of ten xylopyranosyl residues derived from hardwood GX carry an O-acetyl group at the C-2 and/or C-3 position. Softwood xylans are not acetylated.34 The molar mass of pressurized hot water extracted (PHWE) birch GX is about 6500 g mol−1.12
The backbones of GGM and glucomannan consist of alternating β-D-glucopyranosyl and β-D-mannopyranosyl units attached with (1 → 4)-bonds. Softwood GGM contains α-D-galactopyranosyl units (1 → 6)-linked to the backbone mannosyl units. The C-2 and C-3 positions of mannosyl units are partially substituted by O-acetyl groups, on the average one group per 3–4 backbone hexopyranosyl units.33,57 The molar mass of GGM from thermomechanical pulping process water of spruce is approximately 30
000 g mol−1 (ref. 58) and that from PHWE is about 10
000 g mol−1.12
However, the composition of isolated GX and GGM extracts is more complex than that described above, as the extracts often contain co-components, such as lignin fragments or other wood-derived extractives.59–61 Pressurized hot water-extracted hemicelluloses are characterized by up to 70 mg gallic acid equivalent per g hemicelluloses,14 indicating presence of lignin.61 Covalent bonding may occur between the polysaccharide chains and lignin residues, creating lignin–carbohydrate complexes (LCC).61–63 These may either originate from native structures in wood or form through reactions that occur during the extraction process.
Hot-water-extracted hemicelluloses are largely water-soluble, but they may exhibit macromolecular assemblies or aggregates in aqueous environments.64 The aggregation phenomenon is time- and pH-dependent.65 Alkali treatment of hardwood pulp removes side groups from xylans and decreases their water solubility. Due to their intermediate molar mass, the viscosity of aqueous GX and GGM solutions is low, even at high concentrations.12
4. Strategies for achieving emulsion stability
4.1. Amphiphilic surfactants
To introduce surface activity to wood cellulose and lignin, they are functionalized with nonpolar groups in cellulose18 and either charged groups66,67 or alkyl chains68 in lignin, which bring amphiphilic properties to their structures (Fig. 6). Tailored amphiphilic stabilizers may contain various proportions of polar and nonpolar structures, and they have capacity to assemble into an oil–water interface and reduce interfacial tension. Hemicellulose-rich aqueous extracts exhibit native surface activity without chemical derivatization.12
 |
| Fig. 6 Amphiphilic surfactants adsorb at the emulsion droplet interface and decrease interfacial tension between phases. | |
4.1.1. Cellulose derivatives.
Cellulose derivatives are attractive as hydrocolloids since the fact that they are produced by chemical modification of cellulose ensures that they have uniform properties.69 Numerous methods for cellulose modification have been explored,44,45 but the most common methods for producing emulsion stabilizers are the etherification reactions of cellulose into MC, HPC, HPMC, MEC, and CMC (Fig. 3).18 After these reactions, cellulose ethers can be further hydrophobized through the attachment of alkyl chains of different lengths.70 The properties of modified cellulose are determined by the type of substitution, the degree of polymerization (DP) of the cellulose chains, and the degree of substitution (DS) with functional groups.71 For example, the above-mentioned cellulose ethers are soluble in cold water, and CMC is also soluble in hot water.
MC and HPMC exhibit some surface activity.18 HPC has high surface activity compared to most hydrocolloids, and MEC shows very high surface activity and the capacity to decrease the surface tension of water.18 CMC is not surface-active,72 and its effects on emulsion stability are related to regulation of the viscosity of the continuous phase, as discussed further in section 4.3.
Many cellulose ethers are commonly used to stabilize o/w emulsions.73,74 However, ethylcellulose (EC), which is water-insoluble, can stabilize w/o emulsions.75 HPC, HPMC, and hydrophobically modified hydroxyethyl cellulose (HMHEC) adsorb at the oil–water interface and form a solid film that prevents coalescence of the droplets.76–78 Camino et al. compared several grades of HPMC with varying methyl and hydroxypropyl content, methyl/hydroxypropyl ratio, molar mass, and DS and found that the highest surface activity were achieved with the HPMC sample with the highest content of methyl groups and lowest molar mass.77 Low molar mass has also been correlated with small emulsion droplet size, which is related to high stability.79 The self-assembly of HPMC in a solution is driven by hydrophobic interactions between the hydrophobic substituents, mainly methyl groups.77 However, at pH 3, adsorption at the droplet surface and interfacial film formation was hindered. At low pH values, there are a higher number of hydrogen bonds between the protons of the solvent and the HPMC. Thus, because of the interactions between the molecules and the surrounding medium, the hydrophobic interactions and interfacial film formation were weaker.79,80 Controlling emulsion stability with cellulose derivatives therefore requires an understanding of the structural proportions and molecular interactions between the polar cellulose chain and the nonpolar functional groups introduced to it.
4.1.2. Lignin derivatives.
To stabilize emulsions, the stabilizer is commonly dissolved or dispersed in the continuous phase. Kraft lignin shows tendency to form aggregates in aqueous environment,53 whereas lignosulfonates are readily dispersible in water.81 Both can be viewed as spherical polyelectrolytic microgels.81,82 Due to the ionizable groups, both lignosulfonates and Kraft lignin act as polyelectrolytes and may stabilize emulsions through repulsion via an electrical double layer.66,67,83,84 Unsubstituted regions of lignin remain nonpolar and hydrophobic, and they are likely to induce adsorption at dispersion interfaces.85 Notably, Kraft lignin exhibits higher surface-activity, which can be explained by its lower polyelectrolytic expansion and degree of sulfonation compared to lignosulfonates.66 The former implies that the swollen core of lignosulphonates is more amenable to the ionization of acidic groups, so lignosulfonates may be richer of ionizable groups in the interior of the molecular matrix.66 However, the surface activity is not directly linked to efficient emulsion stabilization capacity86 and the molar mass of the lignin fraction also plays a role. For example, high-molar-mass lignosulfonates and Kraft lignin can act via multilayer adsorption to provide both steric and electrokinetic stabilization.83
Lignosulfonates can be combined with other surfactants to achieve higher stability. For example, lignosulfonates engage with cationic surfactants and adsorb at the oil phase through hydrophobic interactions.52 Changes in pH and presence of multivalent cations may affect the colloidal behavior by causing coagulation of sulfonated lignins.82 Surfactants and other designed additives, such as sodium salts and bile acids, may enhance the colloidal stability of lignins under challenging conditions, such as alkaline solutions, elevated temperatures, and high ionic strengths.87
To utilize sulfur-free industrial lignins, such as those recovered from pre-hydrolysis, as emulsifying agents, they can be modified by, for example, alkylation to improve their surface activity.69 The surface tension of alkylated lignins is associated with their capacity to emulsify and stabilize paraffin o/w emulsion, as can be observed by monitoring the formation of a creaming layer.68 Another approach is to introduce polar groups via carboxymethylation to make lignins water-soluble, adjust the balance of affinity between the oil and water phases, and optimize their surface activity.19,20 The solution-related properties of carboxymethylated lignins are dependent upon DS and pH. In one study, the droplet size of carboxymethyl lignin-stabilized kerosene o/w emulsion remained relatively constant for one month.19 The complexity of lignins’ structure and the numerous possibilities for further derivatization makes lignins a challenging, but versatile, raw material for producing effective emulsion stabilizers.
4.1.3. Native hemicellulose-rich extracts.
The polysaccharide structure of wood hemicelluloses is composed of chains of monosaccharides with short branches and some backbone monosaccharides partially substituted with acetyl groups. The carbohydrates are polar in nature, whereas the acetyl groups are slightly nonpolar. However, the plain polysaccharide structure of hemicelluloses lacks considerable amphiphilicity that would make them interfacially active.
The water-solubility of hemicelluloses is dependent upon their molar mass and the presence of side groups, which hinder close packing and association of adjacent hemicellulose chains. Additionally, the alkaline conditions under which extraction is performed remove a major part of the side groups and make hemicelluloses water-insoluble. The first studies to report the use of wood hemicelluloses in emulsions performed hydrophobic modification by grafting insoluble beech GX, its sulfoethyl derivative, and viscose effluents with alkyl or p-carboxybenzyl groups.88,89 After treatment, the samples showed water solubility, moderate surface activity, and the ability to form and stabilize paraffin o/w emulsions.88,89 This experiment was conducted simply using a laboratory mixer and observed visually by monitoring the level of the cream layer or separated oil.88,89 In a different study, controlled etherification of Kraft GX and GGM into water-soluble hydroxypropylated and butylated derivatives was performed to tune the amphiphilicity of hemicelluloses for emulsifying octane.90
Water-extracted hemicellulose samples are largely water-soluble, but they are rarely composed of pure polysaccharides. Depending on the lignocellulosic raw material and isolation method, the amounts and types of lignin residues and extractives accompanying the carbohydrate structure may vary.40 These provide hemicellulose samples with amphiphilic properties and the capacity to lower the surface tension of water.12 For example, native beech GX isolates that contained residual lignin showed the capacity to stabilize emulsions.91 In addition, spruce GGM extracts often contain varying amounts of lignin residues,61 and they have been shown to stabilize colloidal wood resin emulsions92 as well as orange o/w emulsions.93 Furthermore, GGM adsorbed at the rapeseed o/w emulsion droplet interface and stabilized it.12,13 Rheological characterization of GGM- and GX-stabilized emulsions indicated that stability was at least partially due to the steric mechanism.12 Most work on hemicellulose-stabilized emulsions has been performed with o/w emulsions, but Xu et al. prepared and stabilized w/o emulsions using carboxymethylated GGM.94
In addition to surface activity and the physical capacity to stabilize emulsions, phenolic compounds such as lignin fragments introduce antioxidant properties to hemicelluloses.60,61,91,95 This was shown by Wrigstedt et al., who synthesized ferulic acid and sinapic acid esters on birch GX and testing the antioxidant and emulsification properties.96 In a different study, spruce GGM containing phenolic residues efficiently inhibited lipid oxidation of rapeseed oil o/w emulsions, as indicated by the resulting peroxide values, volatile oxidation products, and analysis of polymerized lipids.29 Naturally associated lignin residues in GGM are believed to anchor polysaccharide structures at the oil droplet interface and enable stabilization of emulsions.97 Lehtonen et al. suggested that the native interactions of GGM and phenolic residues could be retained by adjusting the isolation methods, and that this could achieve efficient physical stabilization and extended protection against lipid oxidation.97 Indeed, water-extracted hemicelluloses are exceptionally attractive emulsion stabilizers due to their multifunctionality, which is obtained through environmentally advantageous and safe aqueous isolation without further derivatization.
4.2. Pickering stabilization by particles
In contrast to amphiphilic compounds and dissolved macromolecules, Pickering emulsions are physically stabilized by solid colloidal particles that are wetted partly by oil and partly by water (Fig. 7).98,99 The position of such particles at the oil–water interface depends on their relative affinity for both phases; their interface bends toward the phase for which their affinity is lower. Particles that are preferentially wetted by water are suitable for forming o/w emulsions, whereas particles that are preferentially wetted by oil are suitable for forming w/o emulsions.99
 |
| Fig. 7 Particle-stabilized emulsion interface. | |
4.2.1. Micro- and nanocelluloses.
MCC has been employed by the food industry as an emulsion and foam stabilizer for over 40 years.46 It functions as an emulsion stabilizer and thickener because it has a strong affinity for both oil and water, resulting in its orientation at the o/w interface.100 MCC particles form a three-dimensional network structure, developing viscosity and thickening the continuous water phase between oil droplets, thus preventing collision and subsequent coalescence. The combined functional effects of interfacial adsorption and thickening can be utilized to stabilize emulsions under challenging process and storage conditions.46,100,101 Multiple w/o/w emulsions in which both of the interfaces were stabilized using MCC in the external and internal aqueous phases have been prepared.102–104 In addition to physically stabilizing emulsions, MCC reduced the rate of lipid oxidation in sunflower o/w emulsions.105
Cellulose nanoparticles have gained increasing attention as Pickering stabilizers.16,17 Chemically unmodified CNF, TEMPO-oxidized CNF, and CNC can act as Pickering stabilizers of o/w emulsions against droplet coalescence, but not against creaming or flocculation.106 The performance of CNC prepared to become Pickering stabilizers by various methods of conversion, including oxidative reaction and deep eutectic solvents, was comparable.107 Near-critical water treatment and high-shear homogenization of MCC produced nanocellulose particles that acted as Pickering stabilizers.108 CNC can also be combined with CNF, the former acting as a Pickering stabilizer at the o/w interface and the latter inducing depletion stabilization.109
Hydrophobization of CNF by surface silylation functionalized it as a w/o emulsion stabilizer.101,110 CNF occurred as single, dispersed fibrils or formed large, network-like aggregates at the o/w interface. Fibrils that were insufficiently hydrophobized did not stabilize emulsions, as they were only partially deposited, and formed small, compact aggregates. Network formation by CNF was identified as the main mechanism preventing coalescence of oil droplets.111 Treatment of CNF with octadecylamine or poly(styreneco-maleic anhydride) also resulted in hydrophobic fibrils, which were tested by Lif et al. for their ability to stabilize w/o emulsions in combination with nonionic surfactants.112 Anionic CNC was combined with cationic surfactants to tailor Pickering emulsions to have the capacity for phase-inversion.113 Dried, water-redispersable emulsions were obtained by combining tannic acid and water-soluble cellulose derivatives (i.e., MC or HEC) with CNC. Tannic acid formed complexes with the cellulose derivatives, leading to the condensing of a protective “shell” around the oil droplets.114
Chemical modification of CNF and CNC with lauroyl chloride resulted in nonpolar nanofibers that were able to stabilize w/o emulsions. Combining lauroyl chloride-modified and native nanocelluloses led to new surfactant-free o/w/o double emulsions that could be stabilized by nanocelluloses at both interfaces. High nanofiber length was associated with high emulsion stability.115
In summary, versatile cellulose nanoparticles can be prepared and functionalized into designed stabilizers.
4.2.2. Regenerated cellulose.
Another method for preparing cellulose nanoparticles that can stabilize emulsions is regeneration of dissolved cellulose in a non-solvent. The hydrophobic cellulose derivative hypromellose phthalate (HP) is dissolved in acetone, an ethanol/water mixture, or acetate buffer with a pH of >5, and then it is sheared in aqueous non-solvent media to produce micron-sized particles.116 During coagulation, the HP particles are deformed into far-from-equilibrium shapes because of the low interfacial tension and turbulent flow in the blender after solvent attrition.116 The particles, which have intermediate hydrophobicity, adsorb at the oil–water interfaces and stabilize them.116 Dissolution of cellulose into phosphoric acid causes esterification, and subsequent regeneration in water yields amorphous cellulose particles that efficiently stabilize o/w emulsions through a combination of Pickering and network mechanisms.117,118 Regenerated cellulose particles prepared with phosphoric acid also showed stabilization capacity in combination with sodium caseinate.119
Cellulose derivative particles may be a type of regenerated cellulose when they form dispersions in emulsions’ continuous phase instead of solutions. EC and HPMC were characterized as Pickering stabilizers in o/w and w/o emulsions. The average particle sizes D[3,2] of HPMC and EC dispersed were 22 and 0.7 μm, respectively, in oil and 0.2 and 110 μm, respectively, in water. Particles’ size was further reduced by sonication. Emulsification of sunflower oil with EC particles resulted in small water droplet size in w/o emulsions, while HPMC was a more effective stabilizer for o/w emulsions.120
4.2.3. Lignin particles.
There are numerous possibilities for converting lignin into chemicals and derivatives. One interesting approach to developing new materials is preparation of lignin particles, as reviewed by Beisl et al.121 and Bai et al.122 For example, alkaline lignin extracted from the residues resulting from furfural production is soluble in basic water. In acidic conditions, lignin becomes insoluble and forms particles that are an effective emulsifier for o/w Pickering emulsions.123,124 Combination of acid precipitation of alkaline lignin with sonication is a rapid method to produce nanoparticles that provide extended emulsion stability.125 Control over the regeneration of solubilized lignin enables reducing the particle size to nanoscale (Fig. 8).126 Interestingly, small angle X-ray scattering revealed that the morphology of lignin nanoparticles may be heterogenous, as they can form clusters of aggregated sub-particles (Fig. 9).125 This corresponds with earlier observations of the microgel-like morphology of lignin.81,82
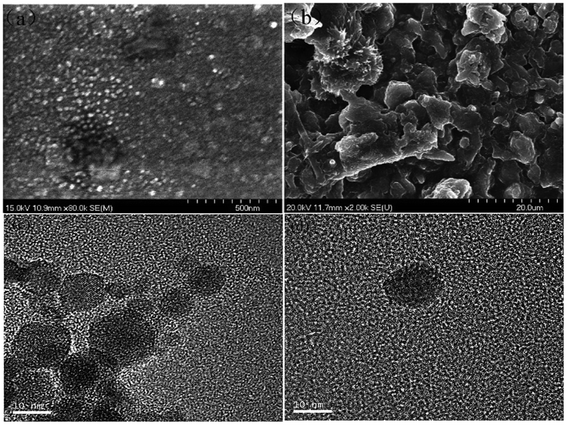 |
| Fig. 8 (a) Scanning electron micrographs of lignin nanoparticles and the (b) alkaline lignin used as raw material for nanoparticle preparation. (c and d) Transmission electron micrographs of lignin nanoparticles. The scale bar in A is 500 nm, in B 20 μm, and in c and d 10 nm. Reproduced from ref. 126 with permission from the Royal Society of Chemistry. | |
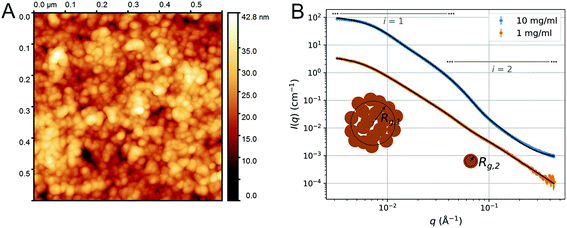 |
| Fig. 9 (A) Atomic force micrograph of lignin nanoparticles. (B) Small-angle X-ray scattering intensities of lignin nanoparticles in aqueous solution, with fits of the unified exponential/power-law model with two levels of structural hierarchy (i = 1, 2) drawn with solid lines. Based on the fitting, the samples consisted of mass fractal aggregates of smaller subunits. Reprinted with permission from M. Agustin, P. Penttilä, M. Lahtinen, K. S. Mikkonen, Rapid and direct preparation of lignin nanoparticles from Alkaline pulping liquor by mild ultrasonication, ACS Sustainable Chem. Eng., 2019, 7, 19925–19934. Copyright 2019 American Chemical Society. | |
Composite nanoparticles for Pickering stabilization can be prepared by acid precipitation of alkaline lignin together with sodium dodecyl sulfate.127 Lignin can also be cross-linked to produce Pickering stabilizer particles.128 Particles grafted from a lignin macroinitiator with hydrophilic polymers using reversible addition–fragmentation chain transfer polymerization have structural features similar to those of the nanoparticles used in Pickering emulsions, but the former are surface-active. In addition, those particles have the capacity to stabilize w/o emulsions.129,130 Fully bio-based Kraft lignin nanoparticles were surface-treated by adsorbing cationic lignin, to extend the emulsion stabilization array.131 Kraft lignin nanoparticles were also coated with chitosan, used as emulsifiers, and further crosslinked with sodium triphosphate to achieve a strong stability against emulsion coalescence.132 Recent efforts in lignin nanoparticle research tackle the challenge of their continuous production by using a microchannel126 and a potentially scalable preparation by spray-freezing.133
4.2.4. Hemicellulose particles.
In contrast to PHWE, alkali extraction of hemicelluloses modifies (i.e., deacetylates) polysaccharides, resulting in reduced water solubility and concomitant extraction of some lignin.134 In fact, alkali-treated polymeric hemicelluloses, such as those recovered from Kraft pulp, are not water-soluble without chemical derivatization. We suspended alkali-extracted xylan from beech and birch (sigma) in 25 mM sodium citrate buffer at a pH of 4.5 and used the suspension as the continuous phase of rapeseed o/w emulsions with 1 wt% xylan and 5% oil (previously unpublished data). The emulsions were prepared and their droplet size distributions were characterized by static light scattering according to Lehtonen et al.97 The D[3,2] surface average droplet size of beech xylan-stabilized emulsions was 0.49 μm immediately after preparation and 0.54 μm after a one-month accelerated storage test at 40 °C. The D[3,2] values of birch xylan-stabilized emulsions were 0.43 μm fresh and 0.42 μm after one month. The results showed that the water-insoluble xylan particles acted as efficient emulsifiers and stabilizers. Fig. 10 illustrates the droplet size distributions of beech and birch xylan-stabilized emulsions immediately after preparation and after storage for one month. A narrow distribution of small droplets was detected, with little indication of large droplets. Optical microscopy was performed according to Lehtonen et al.'s method for visualizing droplets, and the microscopy images (Fig. 11) supported the findings of the droplet size distribution analysis.97
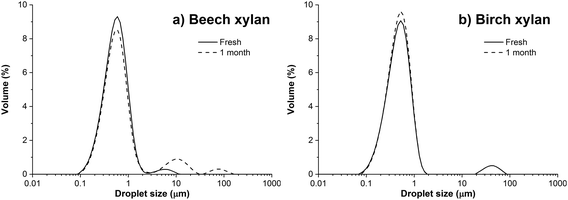 |
| Fig. 10 Droplet size distributions of 5 wt% rapeseed o/w emulsions stabilized by 1% alkali-extracted (a) beech and (b) birch xylan immediately after preparation and after storage for one month at 40 °C. | |
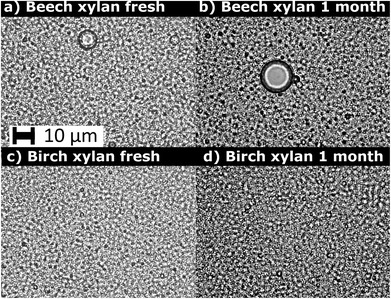 |
| Fig. 11 Optical microscopy images of emulsions with 5 wt% rapeseed oil stabilized with 1 wt% alkali-extracted (a) beech xylan immediately after preparation, (b) beech xylan after storage for one month at 40 °C, (c) birch xylan immediately after preparation and (d) birch xylan after storage for one month at 40 °C. All images were taken at the same magnification. | |
According to our results, insoluble hemicelluloses, such as xylans obtained from alkaline processes, can be used as efficient emulsion stabilizers. It is hypothesized that xylan particles act as Pickering stabilizers, adsorb at the droplet interface, and form a protective film that prevents coalescence.
4.3. Control over the viscosity of the continuous phase
The shelf life of emulsions can be remarkably extended by increasing the viscosity of the continuous phase (Fig. 12). Of the wood-based stabilizers, CNF is particularly suited for increasing the viscosity of water, as it consists of long, flexible, and entangled fibrils that form a gel network that can entrap emulsified droplets and prevent them from undergoing creaming and coalescence. An ionic surfactant, sodium dodecyl sulfate, was used to prepare o/w and w/o emulsions, and then the emulsions were further co-stabilized by addition of CNF or less polar aqueous counter collision-treated CNF.135
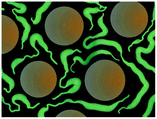 |
| Fig. 12 Macromolecules and cellulose nanofibrils can stabilize emulsions by increasing the viscosity of the continuous phase. | |
The solution viscosity of cellulose derivatives depends on DP and, to some extent, on DS. CMC is not surface-active and does not show an emulsifying capacity as such,73 so its effects on stability are related to controlling the viscosity. It has been found that 1% aqueous solutions of CMC show viscosity of up to 5000 mPa s at ambient temperatures.18 CMC solutions exhibit a reversible reduction of viscosity upon heating, but they do not gel alone or with other hydrocolloids.18 The stabilizing capacity of other cellulose derivatives results from combined effects of interfacial activity and viscosity increase.71,75
5. Potential of lignocellulosic stabilizers
5.1. Stabilization mechanisms and performance
Current literature presents clear evidence of the functionality of lignocellulose-derived compounds and particles as emulsion stabilizers. However, quantitative comparison and evaluation of their performance is complicated due to high variation in emulsion composition, preparation, and characterization methods used in different studies (Table 1). The oil type and polarity, content and ratio of stabilizer and oil, and the intensity of the emulsification process affect the emulsion formation and resulting oil droplet size. Furthermore, the emulsion stability assessment is subject to storage time and conditions as well as characterization methods, such as visual inspection or droplet size analysis (Table 1). The envisioned application determines whether emulsification and short-term stability is sufficient,123 or whether long-time stability against coalescence and creaming, for example, is needed.14 To compare the performance of lignocellulosic emulsion stabilizers, systematic studies at standardized conditions are needed.
Table 1 Comparison of lignocellulosic stabilizers’ performance in o/w emulsions
Stabilizer type (and content) |
Oil type and content |
Emulsification method |
Stability evaluation |
Stabilization mechanism |
Hydrophobically modified HEC76 (0.2–1%) |
Paraffin |
Mixing at 6000 rpm for 10 min |
Droplet size 10–30 μm, stable for at least one month |
Thickening effect |
Φ 0.5 |
Adsorption at interface |
Lignosulfonate67 (0.0625–0.5%) |
Geisum |
Mixing at 1200 rpm for 15 min |
Visual observation, stable for at least 3 days |
Surface activity, electrostatic interactions |
70% |
Kraft lignin83 (0.5–2%) |
Exxsol D80 |
Mixing at 8000 rpm for 2 min |
Visual observation, phase separation in 25–240 min |
Adsorption, steric and electrokinetic stabilization |
48% |
Etherified Kraft GGM or GX90 (1%) |
Octane |
Mixing with Ultra-Turrax T8 at speed 6 for 2 min |
Droplet size below 100 μm for at least 22 days |
Amphiphilic structures |
Up to Φ 60 |
GGM-rich spruce extract97 (1%) |
Rapeseed oil |
High-pressure homogenization, three passes at 800 bar |
Droplet size |
Adsorption, amphiphilic hemicellulose-lignin structures |
5% |
Stable for at least 6 weeks |
CNF, TEMPO-oxidized CNF, or CNC106 (0.1–1.5%) |
Dodecane |
Mixing at 24 000 rpm for 90 s |
Droplet size 10–40 μm, stable against coalescence for at least one month |
Adsorption, electrostatic interactions |
20–35% |
CNC and/or CNF109 (0–1%) |
Sunflower oil |
Ultrasonication for 90 s at a power level set at 40% strength |
Visual inspection and microscopy for 7 days, stability dependent on component ratios |
CNC: Adsorption |
1–10% |
CNF: Depletion stabilization |
Regenerated cellulose particles118 (0.1–1.25%) |
Kerosene |
Mixing at 10 000 rpm for 3 min |
Visual inspection; stable after 1 day |
Combination of adsorption and network formation |
Φ 30 |
Nanoparticles from alkaline lignin125 (0.15–0.6%) |
Rapeseed oil |
High-pressure homogenization, four passes at 88 bar |
Turbiscan analysis and visual inspection; stable for at least 22 days |
Adsorption, electrostatic interactions |
10% |
Nanoparticles from black liquor lignin with sodium dodecyl sulfate127 0.6% |
Cyclohexane |
Mixing at 11 000 rpm for 3 min |
Droplet size 10–20 μm for 2 months |
Adsorption, electrostatic interactions |
Φ 10 |
Insoluble beech and birch xylan |
Rapeseed oil |
High-pressure homogenization, three passes at 800 bar |
Droplet size 0.4–0.5 μm for at least one month |
Adsorption |
5% |
Sodium dodecyl sulfate (0.01–1.2%) and CNF (0–0.5%)135 |
Toluene |
Mixing at 9000 rpm for 5 min |
Visual inspection for stability against creaming |
Viscosity modification and electrostatic interactions |
Φ 50 |
Lignocellulose-derived components, either soluble molecules or insoluble particles, stabilize emulsion systems via different mechanisms depending on their colloidal properties (Table 1). Cellulose derivatives,76 lignosulfonates,67 Kraft lignin,83 native97 and modified90 hemicelluloses, as well as insoluble nanoparticles from cellulose,106,109 lignin,125,127 and hemicelluloses (please see section 4.2.4) adsorb at oil droplet interface either through amphiphilic structures or the Pickering mechanism. The amphiphilic structures may be derived from natural associations between hemicelluloses and lignin97 or they can be achieved by modification during the pulping process67,83 or by derivatization of the isolated lignocellulosics.90 The emulsion stabilization mechanisms of amphiphilic lignocellulose-derived molecules resemble those of abundant surfactants, such as polysorbates and lechitin.12,21 Even though the interfacial activity of lignocellulosic stabilizers may not compare to that of small-molecular amphiphilic surfactants, their higher molecular mass brings additional functionality through steric stabilization.12
Pickering particles can be formed from each: cellulose,117 lignin,125,127 and hemicelluloses through solubilization and regeneration, and they show capacity to adsorb at oil–water interfaces and stabilize them. Pickering particles are well known for emulsion stabilization.99 To compete with inorganic particles or starch granules,99 lignocellulose-derived particles should provide at least comparable performance, price, and availability.
Cellulose derivatives76 and CNF135 may also stabilize emulsions by increasing the viscosity of the continuous emulsion phase, inhibiting droplet coalescence and emulsion creaming/sedimentation. A surface active emulsifier is usually first needed to reduce droplet size.122 Viscosity optimization is essential for many common industrial applications. To facilitate processing of certain products, such and paints14 and heavy crude oil,67 low viscosity is desired, so interfacial stabilization of emulsions is preferred over viscosity increase. Thickening agents are abundantly used in other products, including cosmetic creams and certain foods.21 The combination of price and performance determines whether lignocellulosic stabilizers will find use in these products.
5.2. Applications in technical emulsions
Lignocellulosic stabilizers are an attractive option for technical dispersions as their bio-based nature and, in many cases, biodegradability are favored over the less sustainable characteristics of non-renewable stabilizers. One type of technical dispersion in which they might be used is petroleum-based emulsions. Heavy crude o/w emulsions have been emulsified with sodium lignin sulfonates to decrease their viscosity for pipeline transportation.85 In addition, the stabilizing capacity of lignosulfonates has been compared with that of more surface-active Kraft lignin in an emulsion model with dispersed bituminous crude oil containing large amounts of polar asphaltenes.66
Decreasing the viscosity of crude bitumen and refined oil were achieved by emulsification with carboxymethylated Kraft and organosolv lignins.20 Overall, the complex structure of lignins makes them complicated to use, but they are inexpensive, and their numerous reactive groups enable derivatization and upgrading for functional stabilizers.20
Di Marino et al. exploited the emulsification capacity of Kraft lignin during in situ extraction in an electrochemical depolymerization system to obtain monomers for further reactions.136 Prior studies have also found that lignin-derived fragments32 or lignin nanoparticles123 can be applied to surfactants for emulsion polymerization of latexes. In a different study, hemicelluloses derived from pre-hydrolysis of Kraft-based dissolving pulp were used to aid the creation of a stable latex with enhanced capacity for absorbing dyes and to improve the biodegradability of the latex.137 Further, softwood GGM and hardwood xylans have been tested as stabilizers of alkyd-based paint emulsions to decrease viscosity and ensure easy application on painted surfaces.14 Examples of technical emulsions stabilized with cellulose include o/w emulsion droplets characterized as a substrate for cellulose hydrolysis for advanced conversion processes.138 Svagan et al. crosslinked hexadecane o/w emulsions stabilized by a mixture of CNC and CNF using aromatic polyurea to produce a protective mechanical barrier for liquid-core microcapsules.139
5.3. Food and other life science applications
Cellulose derivatives are widely used and well-known as food emulsion stabilizers.18 Recent research on the topic has applied them as fat replacers in biscuits,140,141 muffins,142 and stabilizers and texturing agents in emulsion-type sausages.143,144 Cellulose derivatives are also suitable for pharmaceutical applications, such as HPMC-stabilized emulsion for treatment of dry eye syndrome.79
MCC, nanocelluloses, and hemicelluloses are of interest for their ability to naturally emulsify and stabilize ingredients and additives in food products, including salad dressings, whipped toppings, sauces, foams, soups, puddings, dips, and many others.145–147 The use of MCC and MFC in food was first suggested in Japanese and US patents developed by Turbak et al.148–150 in the 1980s, as noted by Gómez et al.146 Later, application of CNF as a stabilizer for frozen dessert was proposed in a patent application by Yano et al.151 In addition, Mikulcová et al. proposed emulsification and stabilization of antimicrobial oils (i.e., cinnamaldehyde, eugenol, and limonene) by CNF and CNC as a way to achieve a longer shelf life for perishable food.152 Multiple w/o/w emulsions stabilized with MCC may be of interest for drug release applications,103 such as carriers of isoniazid for tuberculosis therapy.104
Hu et al.43 characterized regenerated cellulose particles as sausage emulsion stabilizers when combined with sodium caseinate. Use of soybean oil as a lipid phase enabled the authors to reduce the saturated fat content of pork sausages. Substitution of 50% pork fat with emulsified soybean oil resulted in products that were acceptable by a sensory panel.43 In other studies, regenerated cellulose153 and softwood GGM93 functioned as stabilizers of citrus o/w beverage model emulsions. GGM-stabilized rapeseed o/w emulsions have also been proposed for use in food applications.12,13 Vegan and dairy beverages stabilized with GGM were characterized as model product prototypes.154 Additionally, GGM-stabilized emulsions in which α-tocopherol (a model hydrophobic core compound) is the dispersed phase were lyophilized to produce edible microcapsules that could be applied to a variety of foods.155
Various wood-derived compounds are used as food additives or ingredients, including MCC and several types of cellulose derivatives, vanillin aroma, glycerol esters of wood rosins, xylitol, and steryls/stanols.147 Cellulose, hemicelluloses, and lignins are present in all terrestrial plants and thus in common diet, and they are classified as dietary fibers. However, food-grade assessment and related safety evaluation of isolated wood lignins and hemicelluloses has not been conducted. According to legislation, the risk assessment and safety evaluation considers the preparation method and toxicity of novel foods, taking account of the anticipated intake.147
Pitkänen et al. highlighted the safety of softwood GGM as a food ingredient or additive as major safety hazards were not identified in their literature review; on the contrary, successful animal feeding tests indicated the non-toxicity of GGM.147 A study using an in vitro digestion model suggests that birch pulp xylan is slowly fermented in colon.156 Pressurized hot water extraction of hemicelluloses is advantageous, because hazardous chemicals are avoided.157 The presence of process chemicals in Kraft lignin and lignosulfonates33 raise concern regarding their use in life-science products, unless they are carefully purified. Alkali-extracted birch lignin from the residual solids after hot water extraction is free from sulfur, so it is advantageous compared to Kraft lignin and lignosulfonates.55 However, the latter are still extensively studied for their beneficial effects on human health.158 Those effects include the capacity of lignin's complex polyphenolic structure to bind bile acids in the intestine, inhibit tumor growth, and act as antioxidant, for examples.158
Physical modifications (e.g., particle size reduction) and chemical derivatization (e.g., introducing charged groups) may affect the function of lignocellulosic materials in digestion.159 The interactions of nano-sized materials with their biological surroundings can be unpredictable.160 The nanosized structure of CNC has raised concern due to its capacity to pass through the cell membrane and cause cell death. However, the cytotoxicity of CNC is strongly dependent on the nanoparticle concentration.159
6. Future perspectives
Due to depletion of non-renewable resources, increasing greenhouse gas emissions, and extremes of weather becoming more frequent than before, the need for sustainable technologies and green materials is urgent.161 Since forests play a key role as a carbon sink, their cutting and industrial exploitation should be balanced with their growth rate. This emphasizes the need to use the wood mass economically, so that all fractions of harvested wood are valorized. Ideally, lignocellulosic components can be used in various upgraded materials to replace fossil resources or other biomass types, such as those that could be preferably used as energy nutrients. To realize this aim, both the price and performance of lignocellulose-derived materials should match or outperform those of conventional alternatives.162 A key parameter to determine the price of wood biomass fractions is scale of production. The fact that forest industries operate at scale of thousands of tonnes of forest biomass fractions per year162 causes a bottleneck for commercialization of new products, since small-scale production is rarely profitable, and large-scale production is challenged to find markets at early stages of development. Small- and medium-sized players and start-ups may find opportunities to develop new types of operations besides or in conjunction with established forest industries.
Lignocellulosic biomass treatment can target obtaining highly pure fractions.55 Alternatively, certain processes result in heterogeneous mixtures of lignin and hemicelluloses, whose purification would require extra process steps.40 On the other hand, less pure multicomponent fractions may exhibit additional functionality compared to pure lignocellulosics.14,61,97 A new interesting opportunity would be to use whole wood particles as stabilizers, after dissolving wood in water163 or ionic liquids.164
Safety aspects of novel products are of utmost importance before commercialization. On the other hand, legislative matters often slow down the route of new products to market. Thus rapid development of reliable safety assessment methods is needed to evaluate emerging technologies, including lignocellulosic stabilizers.160 Acceptance of novel products further requires a dialogue between researchers, authorities, industries, and consumers. For example, different grades of nanocelluloses are gradually appearing to market after decades of research and development. Questions still remain on their upscaling, practical applications, markets and business models, toxicity and environmental issues, characterization, and fundamental features.165
7. Conclusions
The three unique types of biopolymers that form the vast majority of wood mass—namely, cellulose, lignin, and hemicelluloses—can be recovered from forest industry processes and valorized into bio-based emulsion stabilizers. Functionalization of cellulose and lignin provides them with amphiphilic properties and the capacity to assemble at the oil–water interface, whilst hemicellulose-rich aqueous extracts exhibit native surface activity derived from the associations between polysaccharides and phenolic structures. Many wood-derived materials are poorly soluble in water, but they can be used as insoluble particles ranging in size from nanometers to micrometers that have capacity to stabilize oil–water interfaces. Cellulose nanofibrils and carboxymethyl cellulose form viscous aqueous suspensions and solutions, respectively, that restrict the mobility of oil droplets and extend emulsions’ stability. The properties of lignocellulosic stabilizers make them particularly suitable for technical emulsions, such as those made from crude oil, as they can decrease the emulsions’ viscosity. In addition, food and other life science industries have long used cellulose derivatives in their products. There is the potential for broad use of sustainable and functional wood-based stabilizers in life sciences after performing the necessary safety evaluations of novel ingredients.
Conflicts of interest
There are no conflicts to declare.
Acknowledgements
I thank Satu Kirjoranta for providing technical assistance with preparation and analysis of emulsions created with water-insoluble birch and beech xylans. In addition, I am grateful to Julia Varis for drawing the graphical abstract and Fig. 1, 5, 7 and 10 as well as Dr Maarit Lahtinen for drawing the chemical structures in Fig. 2, 3, 4 and 6. Finally, I thank Prof. Maija Tenkanen for our fruitful discussions.
References
- T. W. Crowther, H. B. Glick, K. R. Covey, C. Bettigole, D. S. Maynard, S. M. Thomas, J. R. Smith, G. Hintler, M. C. Duguid, G. Amatulli, M.-N. Tuanmu, W. Jetz, C. Salas, C. Stam, D. Piotto, R. Tavani, S. Green, G. Bruce, S. J. Williams, S. K. Wiser, M. O. Huber, G. M. Hengeveld, G.-J. Nabuurs, E. Tikhonova, P. Borchardt, C.-F. Li, L. W. Powrie, M. Fischer, A. Hemp, J. Homeier, P. Cho, A. C. Vibrans, P. M. Umunay, S. L. Piao, C. W. Rowe, M. S. Ashton, P. R. Crane and M. A. Bradford, Mapping tree density at a global scale, Nature, 2015, 525, 201–207 CrossRef CAS PubMed.
- A. J. Ragauskas, G. T. Beckham, M. J. Biddy, R. Chandra, F. Chen, M. F. Davis, B. H. Davison, R. A. Dixon, P. Gilna, M. Keller, P. Langan, A. K. Naskar, J. N. Saddler, T. J. Tschaplinski, G. A. Tuskan and C. E. Wyman, Lignin valorization: improving lignin processing in the biorefinery, Science, 2014, 344, 1246843 CrossRef PubMed.
-
E. K. Ackom, Integrated forest biorefineries: industrial sustainability, in Industrial Sustainability: Challenges and Opportunities, ed. L. Christopher, The Royal Society of Chemistry, London, 2012, vol. 5, pp. 117–133 Search PubMed.
- S. J. Eichhorn, A. Dufresne, M. Aranguren, N. E. Marcovich, J. R. Capadona, S. J. Rowan, C. Weder, W. Thielemans, M. Roman, S. Renneckar, W. Gindl, S. Veigel, J. Keckes, H. Yano, K. Abe, M. Nogi, A. N. Nakagaito, A. Mangalam, J. Simonsen, A. S. Benight, A. Bismarck, L. A. Berglund and T. Peijs, Review: current international research into cellulose nanofibers and nanocomposites, J. Mater. Sci., 2010, 45, 1–33 CrossRef CAS.
- D. Kai, M. J. Tan, P. L. Chee, Y. K. Chua, Y. L. Yap and X. J. Loh, Towards lignin-based functional materials in a sustainable world, Green Chem., 2016, 18, 1175–1200 RSC.
- Y. Luo, Z. Li, X. Li, X. Liu, J. Fan, J. H. Clark and C. Hu, The production of furfural directly from hemicellulose in lignocellulosic biomass: a review, Catal. Today, 2019, 319, 14–24 CrossRef CAS.
- C. M. Cai, T. Zhang, R. Kumar and C. E. Wyman, THF co-solvent enhances hydrocarbon fuel precursor yields from lignocellulosic biomass, Green Chem., 2013, 15, 3140–3145 RSC.
- C. M. Cai, N. Nagane, R. Kumar and C. E. Wyman, Coupling metal halides with a co-solvent to produce furfural and 5-HMF at high yields directly from lignocellulosic biomass as an integrated biofuels strategy, Green Chem., 2014, 16, 3819–3829 RSC.
-
A. Nussinovitch and M. Hirashima, Cooking Innovations: Using Hydrocolloids for Thickening, Gelling, and Emulsification, CRC Press, Boca Raton, FL, 2014 Search PubMed.
-
https://www.prnewswire.com/news-releases/emulsion-stabilizer-for-beverages-market-remains-highly-fragmented-global-consumption-to-grow-1–4x-through-2028-finds-fact-mr-826932777.html
, accessed 30. Dec 2019.
- A. Fernández Cirelli, C. Ojeda, M. J. L. Castro and M. Salgot, Surfactants in sludge-amended agricultural soils: a review, Environ. Chem. Lett., 2008, 6, 135–148 CrossRef.
- K.
S. Mikkonen, D. Merger, P. Kilpeläinen, L. Murtomäki, U. S. Schmidt and M. Wilhelm, Determination of physical emulsion stabilization mechanisms of wood hemicelluloses via rheological and interfacial characterization, Soft Matter, 2016, 12, 8690–8700 RSC.
- K. S. Mikkonen, C. Xu, C. Berton-Carabin and K. Schroën, Spruce galactoglucomannans in rapeseed oil-in-water emulsions: efficient stabilization performance and structural partitioning, Food Hydrocolloids, 2016, 52, 615–624 CrossRef CAS.
- K. S. Mikkonen, S. Kirjoranta, C. Xu, J. Hemming, A. Pranovich, M. Bhattarai, L. Peltonen, P. Kilpeläinen, N. Maina, M. Tenkanen, M. Lehtonen and S. Willför, Environmentally-compatible alkyd paints stabilized by wood hemicelluloses, Ind. Crops Prod., 2019, 133, 212–220 CrossRef CAS.
- M. Bhattarai, L. Pitkänen, V. Kitunen, R. Korpinen, H. Ilvesniemi, P. Kilpeläinen, M. Lehtonen and K. S. Mikkonen, Functionality of spruce galactoglucomannans in oil-in-water emulsions, Food Hydrocolloids, 2019, 86, 154–161 CrossRef CAS.
- A. Salas, T. Nypelö, C. Rodriguez-Abreu, C. Carrillo and O. J. Rojas, Nanocellulose properties and applications in colloids and interfaces, Curr. Opin. Colloid Interface Sci., 2014, 19, 383–396 CrossRef.
- S. Fujisawa, E. Togawa and K. Kuroda, Nanocellulose-stabilized Pickering emulsions and their applications, Sci. Technol. Adv. Mater., 2017, 18, 959–971 CrossRef CAS PubMed.
-
J. C. F. Murray, Cellulosics, in Handbook of Hydrocolloids, ed. G. O. Phillips and P. A. Williams, Woodhead Publishing, Cambridge, 2nd edn, 2009, vol. 25, pp. 710–722 Search PubMed.
- S. Li, J. A. Willoughby and O. J. Rojas, Oil-in-water emulsions stabilized by carboxymethylated lignins: properties and energy prospects, ChemSusChem, 2016, 9, 2460–2469 CrossRef CAS PubMed.
- S. Li, D. Ogunkoya, T. Fang, J. Willoughby and O. J. Rojas, Carboxymethylated lignins with low surface tension toward low viscosity and highly stable emulsions of crude bitumen and refined oils, J. Colloid Interface Sci., 2016, 482, 27–38 CrossRef CAS PubMed.
-
D. J. McClements, Food Emulsions: Principles, Practices, and Techniques, CRC Press, Boca Raton, FL, 2015 Search PubMed.
- T. Schmidts, D. Dobler, P. Schlupp, C. Nissing, H. Garn and F. Runkel, Development of multiple W/O/W emulsions as dermal carrier system for oligonucleotides: effect of additives on emulsion stability, Int. J. Pharm., 2010, 398, 107–113 CrossRef CAS PubMed.
- E. Dickinson, Hydrocolloids at interfaces and the influence on the properties of dispersed systems, Food Hydrocolloids, 2003, 17, 25–39 CrossRef CAS.
- C. C. Berton-Carabin, L. Sagis and K. Schroën, Formation, structure, and functionality of interfacial layers in food emulsions, Annu. Rev. Food Sci. Technol., 2018, 9, 551–587 CrossRef CAS PubMed.
- C. C. Berton-Carabin, M.-H. Ropers and C. Genot, Lipid oxidation in oil-in-water emulsions: Involvement of the interfacial layer, Compr. Rev. Food Sci. Food Saf., 2014, 13, 945–977 CrossRef CAS.
- D. J. McClements and E. A. Decker, Lipid oxidation in oil-in-water emulsions: impact of molecular environment on chemical reactions in heterogeneous food systems, J. Food Sci., 2000, 65, 1270–1282 CrossRef CAS.
- T. Waraho, D. J. McClements and E. A. Decker, Mechanisms of lipid oxidation in food dispersions, Trends Food Sci. Technol., 2011, 22, 3–13 CrossRef CAS.
- D. J. McClements, E. A. Decker and J. Weiss, Emulsion-based delivery systems for lipophilic bioactive components, J. Food Sci., 2007, 72, R109–R124 CrossRef CAS PubMed.
- M. Lehtonen, S. Teräslahti, C. Xu, M. P. Yadav, A.-M. Lampi and K. S. Mikkonen, Spruce galactoglucomannans inhibit lipid oxidation in rapeseed oil-in-water emulsions, Food Hydrocolloids, 2016, 58, 255–266 CrossRef CAS.
- C. P. Champagne and P. Fustier, Microencapsulation for the improved delivery of bioactive compounds into foods, Curr. Opin. Biotechnol., 2007, 18, 184–190 CrossRef CAS PubMed.
- D. J. Watson and M. R. Mackley, The rheology of aqueous emulsions prepared by direct emulsification and phase inversion from a high viscosity alkyd resin, Colloids Surf., A, 2002, 196, 121–134 CrossRef CAS.
- B. V. K. J. Schmidt, V. Molinari, D. Esposito, K. Tauer and M. Antonietti, Lignin-based polymeric surfactants for emulsion polymerization, Polymer, 2017, 112, 418–426 CrossRef CAS.
-
E. Sjöström, Wood Chemistry Fundamentals and Applications, Academic Press, San Diego, CA, 1993 Search PubMed.
- T. E. Timell, Recent progress in the chemistry of wood hemicelluloses, Wood Sci. Technol., 1967, 1, 45–70 CrossRef CAS.
- N. Mosier, C. Wyman, B. Dale, R. Elander, Y. Y. Lee, M. Holtzapple and M. Ladisch, Features of promising technologies for pretreatment of lignocellulosic biomass, Bioresour. Technol., 2005, 96, 673–686 CrossRef CAS PubMed.
- C. E. Wyman, V. Balan, B. E. Dale, R. T. Elander, M. Falls, B. Hames, M. T. Holtzapple, M. R. Ladisch, Y. Y. Lee, N. Mosier, V. R. Pallapoluh, J. Shi, S. R. Thomas and R. E. Warner, Comparative data on effects of leading pretreatments and enzyme loadings and formulations on sugar yields from different switchgrass sources, Bioresour. Technol., 2011, 102, 11052–11062 CrossRef CAS PubMed.
-
C. E. Wyman, B. E. Dale, V. Balan, R. T. Elander, M. T. Holtzapple, R. S. Ramirez, M. R. Ladisch, N. S. Mosier, Y. Y. Lee, R. Gupta, S. R. Thomas, B. R. Hames, R. Warner and R. Kumar, Comparative Performance of Leading Pretreatment Technologies for Biological Conversion of Corn Stover, Poplar Wood, and Switchgrass to Sugars, in Aqueous Pretreatment of Plant Biomass for Biological and Chemical Conversion to Fuels and Chemicals, ed C. E. Wyman, John Wiley & Sons, Ltd., 2013, p. 239 Search PubMed.
- T. Y. Nguyen, C. M. Cai, O. Osman, R. Kumar and C. E. Wyman, CELF pretreatment of corn stover boosts ethanol titers and yields from high solids SSF with low enzyme loadings, Green Chem., 2016, 18, 1581–1589 RSC.
- S. S. Hassan, G. A. Williams and A. K. Jaiswal, Emerging technologies for the pretreatment of lignocellulosic biomass, Bioresour. Technol., 2018, 262, 310–318 CrossRef CAS PubMed.
- F. Valoppi, M. Lahtinen, M. Bhattarai, S. Kirjoranta, V. Juntti, L. Peltonen, P. O. Kilpeläinen and K. S. Mikkonen, Centrifugal fractionation of softwood extracts improves biorefinery workflow and yields functional emulsifiers, Green Chem., 2019, 21, 4691–4705 RSC.
- T. Schult, T. Hjerde, O. I. Optun, P. J. Kleppe and S. Moe, Characterization of cellulose by SEC-MALLS, Cellulose, 2002, 9, 149–158 CrossRef CAS.
- C. Somerville, S. Bauer, G. Brininstool, M. Facette, T. Hamann, J. Milne, E. Osborne, A. Paredez, S. Persson, T. Raab, S. Vorwerk and H. Youngs, Toward a systems approach to understanding plant cell walls, Science, 2004, 306, 2206–2211 CrossRef CAS PubMed.
- H. Hu, J. Pereira, L. Xing, Y. Hu, C.-L. Qiao, G. Zhou and W. Zhang, Effects of regenerated cellulose emulsion on the quality of emulsified sausage, LWT–Food Sci. Technol., 2016, 70, 315–321 CrossRef CAS.
- S. C. Fox, B. Li, D. Xu and K. J. Edgar, Regioselective esterification and etherification of cellulose: a review, Biomacromolecules, 2011, 12, 1956–1972 CrossRef CAS PubMed.
- K. Jedvert and T. Heinze, Cellulose modification and shaping – a review, J. Polym. Eng., 2017, 37, 845–860 CAS.
-
G. Krawczyk, A. Venables and D. Tuaso, Microcrystalline cellulose, in Handbook of Hydrocolloids, ed. G. O. Phillips and P. A. Williams, Woodhead Publishing, Cambridge, 2nd edn, 2009, vol. 27, pp. 740–758 Search PubMed.
- T. Pääkkönen, K. Dimic-Misic, H. Orelma, R. Pönni, T. Vuorinen and T. Maloney, Effect of xylan in hardwood pulp on the reaction rate of TEMPO-mediated oxidation and the rheology of the final nanofibrillated cellulose gel, Cellulose, 2016, 23, 277–293 CrossRef.
- J. Ralph, K. Lundquist, G. Brunow, F. Lu, H. Kim, P. F. Schatz, J. M. Marita, R. D. Hatfield, S. A. Ralph, J. H. Christensen and W. Boerjan, Lignins: natural polymers from oxidative coupling of 4-hydroxyphenylpropanoids, Phytochem. Rev., 2004, 3, 29–60 CrossRef CAS.
-
R. Alén, Pulp Mills and Wood-Based Biorefineries, in Industrial Biorefineries & White Biotechnology, ed. A. Pandey, R. Höfer, M. Taherzadeh, K. M. Nampoothiri and C. Larroche, Elsevier, 2015, vol. 3A, pp. 91–126 Search PubMed.
- G. Gebremeskel and F. Aldaeus, Determination of lignin content in kraft black liquors by capillary zone electrophoresis (CZE), Holzforschung, 2013, 67, 887–890 CAS.
- J. L. Gardon and S. G. Mason, Physicochemical studies of ligninsulphonates: II. Behavior as polyelecytolytes, Can. J. Chem., 1955, 33, 1491–1501 CrossRef CAS.
- K. M. Askvik, S. Hetlesæther, J. Sjöblom and P. Stenius, Properties of the lignosulfonate–surfactant complex phase, Colloids Surf., A, 2001, 182, 175–189 CrossRef CAS.
- V. Nyman and G. Rose, The colloidal behaviour of Kraft lignin and lignosulfonates, Colloids Surf., 1986, 21, 125–147 CrossRef CAS.
- D. Ibarra, M. I. Chávez, J. Rencoret, J. C. Del Río, A. Gutiérrez, J. Romero, S. Camarero, M. J. Martínez, J. Jiménez-Barbero and A. T. Martínez, Lignin modification during eucalyptus globulus Kraft pulping followed by totally chlorine-free bleaching: a two-dimensional nuclear magnetic resonance, Fourier transform infrared, and pyrolysis−gas chromatography/mass spectrometry study, J. Agric. Food Chem., 2007, 55, 3477–3490 CrossRef CAS PubMed.
- L. Lagerquist, A. Pranovich, A. Smeds, S. von Schoultz, L. Vähäsalo, J. Rahkila, I. Kilpeläinen, T. Tamminen, S. Willför and P. Eklund, Structural characterization of birch lignin isolated from a pressurized hot water extraction and mild alkali pulped biorefinery process, Ind. Crops Prod., 2018, 111, 306–316 CrossRef CAS.
-
A. Ebringerová, Z. Hromádková and T. Heinze, Hemicellulose, in Advances in Polymer Science, ed. T. Heinze, Springer, Berlin, 2005, vol. 186, pp. 1–67 Search PubMed.
- S. Willför, K. Sundberg, M. Tenkanen and B. Holmbom, Spruce derived mannans – a potential raw material for hydrocolloids and novel advanced natural materials, Carbohydr. Polym., 2008, 72, 197–210 CrossRef.
- K. S. Mikkonen, M. Heikkilä, S. Willför and M. Tenkanen, Films from glyoxal-crosslinked spruce galactoglucomannans plasticized with sorbitol, Int. J. Polym. Sci., 2012, 482810 Search PubMed.
- N. Giummarella and M. Lawoko, Structural insights on recalcitrance during hydrothermal hemicellulose extraction from wood, ACS Sustainable Chem. Eng., 2017, 5, 5156–5165 CrossRef CAS.
- Y. Zhang, S. Wang, W. Xu, F. Cheng, A. Pranovich, A. Smeds, S. Willför and C. Xu, Valorization of lignin−carbohydrate complexes from hydrolysates of Norway spruce: efficient separation, structural characterization, and antioxidant activity, ACS Sustainable Chem. Eng., 2019, 7, 1447–1456 CrossRef CAS.
- M. Lahtinen, F. Valoppi, V. Juntti, S. Heikkinen, P. Kilpeläinen, N. Maina and K. S. Mikkonen, Lignin-rich PHWE hemicellulose extracts responsible for extended emulsion stabilization, Front. Chem., 2019, 7, 871 CrossRef PubMed.
- H. Nishimura, A. Kamiya, T. Nagata, M. Katahira and T. Watanabe, Direct evidence for α ether linkage between lignin and carbohydrates in wood cell walls, Sci. Rep., 2018, 8, 6538 CrossRef PubMed.
- N. Giummarella, Y. Pu, A. J. Ragauskas and M. Lawoko, A critical review on the analysis of lignin carbohydrate bonds, Green Chem., 2019, 21, 1573–1595 RSC.
- S. Kishani, F. Vilaplana, W. Xu, C. Xu and L. Wågberg, Solubility of softwood hemicelluloses, Biomacromolecules, 2018, 19, 1245–1255 CrossRef CAS PubMed.
- M. Bhattarai, F. Valoppi, S.-P. Hirvonen, S. Hietala, P. Kilpelainen, V. Aseyev and K. S. Mikkonen, Time-dependent self-association of spruce galactoglucomannans depends on pH and mechanical shearing, Food Hydrocolloids, 2020, 102, 105607 CrossRef.
- S. A. Gundersen, M.-H. Ese and J. Sjöblom, Langmuir surface and interface films of lignosulfonates and Kraft lignins in the presence of electrolyte and asphaltenes: correlation to emulsion stability, Colloids Surf., A, 2001, 182, 199–218 CrossRef CAS.
- N. N. Zaki, N. S. Ahmed and A. M. Nassar, Sodium lignin sulfonate to stabilize heavy crude oil-in-water emulsions for pipeline transportation, Pet. Sci. Technol., 2000, 18, 1175–1193 CrossRef CAS.
- B. Košíková, M. Ďuriš and V. Demianová, Conversion of lignin biopolymer into surface-active derivatives, Eur. Polym. J., 2000, 36, 1209–1212 CrossRef.
- C. Onyango, G. Unbehend and M. G. Lindhauer, Effect of cellulose-derivatives and emulsifiers on creep-recovery and crumb properties of gluten-free bread prepared from sorghum and gelatinised cassava starch, Food Res. Int., 2009, 42, 949–955 CrossRef CAS.
- L. M. Landoll, Nonionic polymer surfactants, J. Polym. Sci., Polym. Chem. Ed., 1982, 20, 443–455 CrossRef CAS.
- E. Akiyama, T. Yamamoto, Y. Yago, H. Hotta, T. Ihara and T. Kitsuki, Thickening properties and emulsification mechanisms of new derivatives of polysaccharide in aqueous solution 2. The effect of the substitution ratio of hydrophobic/hydrophilic moieties, J. Colloid Interface Sci., 2007, 311, 438–446 CrossRef CAS PubMed.
- R. Y. Z. Hu, A. T. A. Wang and J. P. Hartnett, Surface tension measurement of aqueous polymer solutions, Exp. Therm. Fluid Sci., 1991, 4, 723–729 CrossRef CAS.
- R. E. M. Davies and J. M. Rowson, Water-soluble cellulose derivatives: uses as primary emulsifying agents. Part I, J. Pharm. Pharmacol., 1960, 12, 154–162 CrossRef CAS PubMed.
- R. E. M. Davies and J. M. Rowson, Water-soluble cellulose derivatives: uses as primary emulsifying agents. Part II, J. Pharm. Pharmacol., 1960, 12, 237–244 CrossRef CAS PubMed.
- E. Melzer, J. Kreuter and R. Daniels, Ethylcellulose: a new type of emulsion stabilizer, Eur. J. Pharm. Biopharm., 2003, 56, 23–27 CrossRef CAS PubMed.
- W. Sun, D. Sun, Y. Wei, S. Liu and S. Zhang, Oil-in-water emulsions stabilized by hydrophobically modified hydroxyethyl cellulose: adsorption and thickening effect, J. Colloid Interface Sci., 2007, 311, 228–236 CrossRef CAS PubMed.
- N. A. Camino, C. Sánchez, J. M. Rodríguez Patino and A. M. R. Pilosof, Hydroxypropylmethylcellulose at the oil-water interface. Part I. Bulk behaviour and dynamic adsorption as affected by pH, Food Hydrocolloids, 2011, 25, 1–11 CrossRef CAS.
- S. Mezdour, A. Lepine, P. Erazo-Majewicz, F. Ducept and C. Michon, Oil/water surface rheological properties of hydroxypropyl cellulose (HPC) alone and mixed with lecithin: contribution to emulsion stability, Colloids Surf., A, 2008, 331, 76–83 CrossRef CAS.
- M. B. Schulz and R. Daniels, Hydroxypropylmethylcellulose (HPMC) as emulsifer for submicron emulsions: influence of molecular weight and substitution type on the droplet size after high-pressure homogenization, Eur. J. Pharm. Biopharm., 2000, 49, 231–236 CrossRef CAS PubMed.
- J. Tritt-Goc and N. Pislewski, Magnetic resonance imaging study of the swelling kinetics of hydroxypropylmethylcellulose (HPMC) in water, J. Controlled Release, 2002, 80, 79–86 CrossRef CAS PubMed.
- A. Rezanowich and D. A. I. Goring, Polyelectrolyte expansion of a lignin sulfonate microgel, J. Colloid Sci., 1960, 15, 452–471 CrossRef CAS.
- S. A. Gundersen, Ø. Sæther and J. Sjöblom, Salt effects on lignosulfonate and Kraft lignin stabilized O/W-emulsions studied by means of electrical conductivity and video-enhanced microscopy, Colloids Surf., A, 2001, 186, 141–153 CrossRef CAS.
- S. A. Gundersen and J. Sjöblom, High- and low-molecular-weight lignosulfonates and Kraft lignins as oil/water-emulsion stabilizers studied by means of electrical conductivity, Colloid Polym. Sci., 1999, 277, 462–468 CrossRef CAS.
-
E. J. W. Verwey and J. T. G. Overbeek, Theory of the Stability of Lyophobic Colloids, Elsevier, New York, 1948 Search PubMed.
- J. C. Le Bell, The relation between the structure of lignosulphonates and their effect as stabilizers for latex particulate dispersions, Colloids Surf., 1984, 9, 237–261 CrossRef CAS.
- L. I. Tolosa, A. J. Rodríguez-Malaver, A. M. González and O. J. Rojas, Effect of Fenton's reagent on O/W emulsions stabilized by black liquor, J. Colloid Interface Sci., 2006, 294, 182–186 CrossRef CAS PubMed.
- M. Norgren and H. Edlund, Stabilisation of kraft lignin solutions by surfactant additions, Colloids Surf., A, 2001, 194, 239–248 CrossRef CAS.
- A. Ebringerová, I. Sroková, P. Talába, M. Kačuráková and Z. Hromádková, Amphiphilic beechwood glucuronoxylan derivatives, J. Appl. Polym. Sci., 1998, 67, 1523–1530 CrossRef.
- A. Ebringerová, Z. Hromádková, A. Malovíková, V. Sasinková, J. Hirsch and I. Sroková, Structure and properties of water-soluble p-carboxybenzyl polysaccharide derivatives, J. Appl. Polym. Sci., 2000, 78, 1191–1199 CrossRef.
- T. Nypelö, C. Laine, M. Aoki, T. Tammelin and U. Henniges, Etherification of wood-based hemicelluloses for interfacial activity, Biomacromolecules, 2016, 17, 1894–1901 CrossRef PubMed.
- Z. Hromádková, A. Ebringerová and A. Malovíkova, The structural, molecular and functional properties of lignin-containing beechwood glucuronoxylan, Macromol. Symp., 2006, 232, 19–26 CrossRef.
- T. Hannuksela and B. Holmbom, Stabilization of wood-resin emulsions by dissolved galactoglucomannans and galactomannans, J. Pulp Pap. Sci., 2004, 30, 159–164 CAS.
- K. S. Mikkonen, M. Tenkanen, P. Cooke, C. Xu, H. Rita, S. Willför, B. Holmbom, K. B. Hicks and M. P. Yadav, Mannans as stabilizers of oil-in-water beverage emulsions, LWT–Food Sci. Technol., 2009, 42, 849–855 CrossRef CAS.
- A. Xu, C. Eckerman, A. Smeds, M. Reunanen, P. C. Eklund, R. Sjöholm and S. Willför, Carboxymethylated spruce galactoglucomannans: preparation, characterisation, dispersion stability, water-in-oil emulsion stability, and sorption on cellulose surface, Nord. Pulp Pap. Res. J., 2011, 26, 167–178 Search PubMed.
- A. Ebringerová, Z. Hromádková, V. Hříbalová, C. Xu, B. Holmbom, A. Sundberg and S. Willför, Norway spruce galactoglucomannans exhibiting immunomodulating and radical-scavenging activities, Int. J. Biol. Macromol., 2008, 42, 1–5 CrossRef PubMed.
- P. Wrigstedt, P. Kylli, L. Pitkänen, P. Nousiainen, M. Tenkanen and J. Sipilä, Synthesis and antioxidant activity of hydroxycinnamic acid xylan esters, J. Agric. Food Chem., 2010, 58, 6937–6943 CrossRef CAS PubMed.
- M. Lehtonen, M. Merinen, P. O. Kilpeläinen, C. Xu, S. M. Willför and K. S. Mikkonen, Phenolic residues in spruce galactoglucomannans improve stabilization of oil-in-water emulsions, J. Colloid Interface Sci., 2018, 512, 536–547 CrossRef CAS PubMed.
- S. U. Pickering, Emulsions, J. Chem. Soc. Trans., 1907, 91, 2001–2021 RSC.
- C. C. Berton-Carabin and K. Schroën, Pickering emulsions for food applications: background, trends, and challenges, Annu. Rev. Food Sci. Technol., 2015, 6, 263–297 CrossRef CAS PubMed.
- K. P. Oza and S. G. Frank, Microcrystalline cellulose stabilized emulsions, J. Dispersion Sci. Technol., 1986, 7, 543–561 CrossRef CAS.
- M. Andersen and P. Stenius, Water-in-oil emulsions stabilized by hydrophobized microfibrillated cellulose, J. Dispersion Sci. Technol., 2007, 28, 837–844 CrossRef.
- K. P. Oza and S. G. Frank, Multiple emulsions stabilized by colloidal microcrystalline cellulose, J. Dispersion Sci. Technol., 1989, 10, 163–185 CrossRef CAS.
- K. P. Oza and S. G. Frank, Drug release from emulsions stabilized by colloidal microcrystalline cellulose, J. Dispersion Sci. Technol., 1989, 10, 187–210 CrossRef CAS.
- A. J. Khopade and N. K. Jain, A stable multiple emulsion system bearing isoniazid: preparation and characterization, Drug Dev. Ind. Pharm., 1998, 24, 289–293 CrossRef CAS PubMed.
- M. Kargar, K. Fayazmanesh, M. Alavi, F. Spyropoulos and I. T. Norton, Investigation into the potential ability of Pickering emulsions (food-grade particles) to enhance the oxidative stability of oil-in-water emulsions, J. Colloid Interface Sci., 2012, 366, 209–215 CrossRef CAS PubMed.
- M. Gestranius, P. Stenius, E. Kontturi, J. Sjöblom and T. Tammelin, Phase behaviour and droplet size of oil-in-water Pickering emulsions stabilised with plant-derived nanocellulosic materials, Colloids Surf., A, 2017, 519, 60–70 CrossRef CAS.
- O. Laitinen, J. Ojala, J. A. Sirviö and H. Liimatainen, Sustainable stabilization of oil in water emulsions by cellulose nanocrystals synthesized from deep eutectic solvents, Cellulose, 2017, 24, 1679–1689 CrossRef CAS.
- J. Buffiere, Z. Balogh-Michels, M. Borrega, T. Geiger, T. Zimmermann and H. Sixta, The chemical-free production of nanocelluloses from microcrystalline cellulose and their use as Pickering emulsion stabilizer, Carbohydr. Polym., 2017, 178, 48–56 CrossRef CAS PubMed.
- L. Bai, S. Huan, W. Xiang and O. J. Rojas, Pickering emulsions by combining cellulose nanofibrils and nanocrystals: phase behavior and depletion stabilization, Green Chem., 2018, 20, 1571–1582 RSC.
- K. Xhanari, K. Syverud and P. Stenius, Structure of nanofibrillated cellulose layers at the o/w interface, J. Dispersion Sci. Technol., 2011, 32, 447–452 CrossRef CAS.
- K. Xhanari, K. Syverud, G. Chinga-Carrasco, K. Paso and P. Stenius, Emulsions stabilized by microfibrillated cellulose: The effect of hydrophobization, concentration and o/w ratio, J. Colloid Interface Sci., 2011, 356, 58–62 CrossRef CAS PubMed.
- A. Lif, P. Stenstad, K. Syverud, M. Nydén and K. Holmberg, Fischer–Tropsch diesel emulsions stabilised by microfibrillated cellulose and nonionic surfactants, J. Colloid Interface Sci., 2010, 352, 585–592 CrossRef CAS PubMed.
- Z. Hu, S. Ballinger, R. Pelton and E. D. Cranston, Surfactant-enhanced cellulose nanocrystal Pickering emulsions, J. Colloid Interface Sci., 2015, 439, 139–148 CrossRef CAS PubMed.
- Z. Hu, H. S. Marway, H. Kasem, R. Pelton and E. D. Cranston, Dried and redispersible cellulose nanocrystal Pickering emulsions, ACS Macro Lett., 2016, 5, 185–189 CrossRef CAS.
- A. G. Cunha, J.-B. Mougel, B. Cathala, L. A. Berglund and I. Capron, Preparation of double Pickering emulsions stabilized by chemically tailored nanocelluloses, Langmuir, 2014, 30, 9327–9335 CrossRef CAS PubMed.
- H. A. Wege, S. Kim, V. N. Paunov, Q. Zhong and O. D. Velev, Long-term stabilization of foams and emulsions with in situ formed microparticles from hydrophobic cellulose, Langmuir, 2008, 24, 9245–9253 CrossRef CAS PubMed.
- X. Jia, R. Xu, W. Shen, M. Xie, M. Abid, S. Jabbar, P. Wang, X. Zeng and T. Wu, Stabilizing oil-in-water emulsion with amorphous cellulose, Food Hydrocolloids, 2015, 43, 275–282 CrossRef CAS.
- Z. Li, H. Wu, M. Yang, D. Xu, J. Chen, H. Feng, Y. Lu, L. Zhang, Y. Yu and W. Kang, Stability mechanism of O/W Pickering emulsions stabilized with regenerated cellulose, Carbohydr. Polym., 2018, 181, 224–233 CrossRef CAS PubMed.
- H. Y. Hu, L. J. Xing, Y. Y. Hu, C. L. Qiao, T. Wu, G. H. Zhou and W. G. Zhang, Effects of regenerated cellulose on oil-in-water emulsions stabilized by sodium caseinate, Food Hydrocolloids, 2016, 52, 38–46 CrossRef CAS.
- L. J. Duffus, J. E. Norton, P. Smith, I. T. Norton and F. Spyropoulos, A comparative study on the capacity of a range of food-grade particles to form stable O/W and W/O Pickering emulsions, J. Colloid Interface Sci., 2016, 473, 9–21 CrossRef CAS PubMed.
- S. Beisl, A. Friedl and A. Miltner, Lignin from micro- to nanosize: applications, Int. J. Mol. Sci., 2017, 18, 2367 CrossRef PubMed.
- L. Bai, L. G. Greca, W. Xiang, J. Lehtonen, S. Huan, R. W. N. Nugroho, B. L. Tardy and O. J. Rojas, Adsorption and assembly of cellulosic and lignin colloids at oil/water interfaces, Langmuir, 2019, 35, 571–588 CrossRef CAS PubMed.
- Z. Wei, Y. Yang, R. Yang and C. Wang, Alkaline lignin extracted from furfural residues for pH-responsive Pickering emulsions and their recyclable polymerization, Green Chem., 2012, 14, 3230–3236 RSC.
- Y. Yang, Z. Wei, C. Wang and Z. Tong, Lignin-based Pickering HIPEs for macroporous foams and their enhanced adsorption of copper(II) ions, Chem. Commun., 2013, 49, 7144–7146 RSC.
- M. Agustin, P. Penttilä, M. Lahtinen and K. S. Mikkonen, Rapid and direct preparation of lignin nanoparticles from alkaline pulping liquor by mild ultrasonication, ACS Sustainable Chem. Eng., 2019, 7, 19925–19934 CrossRef CAS.
- T. Ju, Z. Zhang, Y. Li, X. Miao and J. Ji, Continuous production of lignin nanoparticles using a microchannel reactor and its application in UV-shielding films, RSC Adv., 2019, 9, 24915 RSC.
- Y. Pang, S. Wang, X. Qiu, Y. Luo, H. Lou and J. Huang, Preparation of lignin/sodium dodecyl sulfate composite nanoparticles and their application in Pickering emulsion template-based microencapsulation, J. Agric. Food Chem., 2017, 65, 11011–11019 CrossRef CAS PubMed.
- T. E. Nypelö, C. A. Carrillo and O. J. Rojas, Lignin supracolloids synthesized from (W/O) microemulsions: use in the interfacial stabilization of Pickering systems and organic carriers for silver metal, Soft Matter, 2015, 11, 2046–2054 RSC.
- A. Gupta and N. R. Washburn, Polymer-grafted lignin surfactants prepared via reversible addition–fragmentation chain-transfer polymerization, Langmuir, 2014, 30, 9303–9312 CrossRef PubMed.
- K. S. Silmore, C. Gupta and N. R. Washburn, Tunable Pickering emulsions with polymer-grafted lignin nanoparticles (PGLNs), J. Colloid Interface Sci., 2016, 466, 91–100 CrossRef CAS PubMed.
- M. H. Sipponen, M. Smyth, T. Leskinen, L.-S. Johansson and M. Österberg, Monika, All-lignin approach to prepare cationic colloidal lignin particles: stabilization of durable Pickering emulsions, Green Chem., 2017, 19, 5831–5840 RSC.
- T. Zou, M. H. Sipponen and M. Österberg, Natural
shape-retaining microcapsules with shells made of chitosan-coated colloidal lignin particles, Front. Chem., 2019, 7, 370 CrossRef CAS PubMed.
- P. K. Mishra and A. Ekielski, A simple method to synthesize lignin nanoparticles, Colloids Interfaces, 2019, 3, 52 CrossRef CAS.
- K. S. Mikkonen, C. Laine, I. Kontro, R. A. Talja, R. Serimaa and M. Tenkanen, Combination of internal and external plasticization of hydroxypropylated birch xylan tailors the properties of sustainable barrier films, Eur. Polym. J., 2015, 66, 307–318 CrossRef CAS.
- S. Huan, S. Yokota, L. Bai, M. Ago, M. Borghei, T. Kondo and O. J. Rojas, Formulation and composition effects in phase transitions of emulsions costabilized by cellulose nanofibrils and an ionic surfactant, Biomacromolecules, 2017, 18, 4393–4404 CrossRef CAS PubMed.
- D. Di Marino, V. Aniko, A. Stocco, S. Kriescher and M. Wessling, Emulsion electro-oxidation of kraft lignin, Green Chem., 2017, 19, 4778–4784 RSC.
- J. Zhang, H. Xiao and Y. Yang, Preparation of hemicellulose-containing latex and its application as absorbent toward dyes, J. Mater. Sci., 2015, 50, 1673–1678 CrossRef CAS.
- G. Alfassi, D. M. Rein and Y. Cohen, Cellulose emulsions and their hydrolysis, J. Chem. Technol. Biotechnol., 2019, 94, 178–184 CrossRef CAS.
- A. J. Svagan, A. Musyanovych, M. Kappl, M. Bernhardt, G. Glasser, C. Wohnhaas, L. A. Berglund, J. Risbo and K. Landfester, Cellulose nanofiber/nanocrystal reinforced capsules: a fast and facile approach toward assembly of liquid-core capsules with high mechanical stability, Biomacromolecules, 2014, 15, 1852–1859 CrossRef CAS PubMed.
- P. Tarancón, M. J. Hernández, A. Salvador and T. Sanz, Relevance of creep and oscillatory tests for understanding how cellulose emulsions function as fat replacers in biscuits, LWT–Food Sci. Technol., 2015, 62, 640–646 CrossRef.
- T. Sanz, A. Quiles, A. Salvador and I. Hernando, Structural changes in biscuits made with cellulose emulsions as fat replacers, Food Sci. Technol. Int., 2017, 23, 480–489 CrossRef CAS.
- S. Martínez-Cervera, A. Salvador and T. Sanz, Cellulose ether emulsions as fat replacers in muffins: rheological, thermal and textural properties, LWT–Food Sci. Technol., 2015, 63, 1083–1090 CrossRef.
- V. Schuh, K. Allard, K. Herrmann, M. Gibis, R. Kohlus and J. Weiss, Impact of carboxymethyl cellulose (CMC) and microcrystalline cellulose (MCC) on functional characteristics of emulsified sausages, Meat Sci., 2013, 93, 240–247 CrossRef CAS PubMed.
- M. Gibis, V. Schuh, K. Allard and J. Weiss, Influence of molecular weight and degree of substitution of various carboxymethyl celluloses on unheated and heated emulsion-type sausage models, Carbohydr. Polym., 2017, 159, 76–85 CrossRef CAS PubMed.
- A. F. Turbak, F. W. Snyder and K. R. Sandberg, Microfibrillated cellulose, a new cellulose product: properties, uses, and commercial potential, J. Appl. Polym. Sci.: Appl. Polym. Symp., 1983, 37, 815–827 CAS.
- C. Gómez, A. Serpa, J. Velásquez-Cock, P. Gañán, C. Castro, L. Vélez and R. Zuluag, Vegetable nanocellulose in food science: a review, Food Hydrocolloids, 2016, 57, 178–186 CrossRef.
- L. Pitkänen, M. Heinonen and K. S. Mikkonen, Safety considerations of plant polysaccharides for food use: case study on phenolic-rich softwood galactoglucomannan extract, Food Funct., 2018, 9, 1931–1943 RSC.
-
A. F. Turbak, F. W. Snyder and K. R. Sandberg, US Pat, 4341807, 1982 Search PubMed.
-
A. F. Turbak, F. W. Snyder and K. R. Sandberg, US Pat, 4378381, 1983 Search PubMed.
-
A. F. Turbak, F. W. Snyder and K. R. Sandberg, US Pat, 4487634, 1984 Search PubMed.
-
G. Yano, K. Abe, Y. Kase, S. Kikkawa and Y. Onishi, US Pat, 20140342075A1, 2012 Search PubMed.
- V. Mikulcová, R. Bordes and V. Kašpárková, On the preparation and antibacterial activity of emulsions stabilized with nanocellulose particles, Food Hydrocolloids, 2016, 61, 780–792 CrossRef.
- W. Shen, L. Guo, T. Wu, W. Zhang and M. Abid, Stabilizing beverage emulsions by regenerated celluloses, LWT–Food Sci. Technol., 2016, 72, 292–301 CrossRef CAS.
- F. Valoppi, N. Maina, M. Allen, R. Miglioli, P. O. Kilpeläinen and K. S. Mikkonen, Spruce galactoglucomannan-stabilized emulsions as essential fatty acid delivery systems for functionalized drinkable yogurt and oat-based beverage, Eur. Food Res. Technol., 2019, 245, 1387–1398 CrossRef CAS.
- P. Laine, A.-M. Lampi, M. Peura, J. Kansikas, K. Mikkonen, S. Willför, M. Tenkanen and K. Jouppila, Comparison of microencapsulation properties of spruce galactoglucomannans and arabic gum using a model hydrophobic core compound, J. Agric. Food Chem., 2010, 58, 981–989 CrossRef CAS PubMed.
- N. Rosa-Sibakov, T. K. Hakala, N. Sözer, E. Nordlund, K. Poutanen and A.-M. Aura, Birch pulp xylan works as a food hydrocolloid in acid milk gels and is fermented slowly in vitro, Carbohydr. Polym., 2016, 154, 305–312 CrossRef CAS PubMed.
- P. O. Kilpeläinen, S. S. Hautala, O. O. Byman, L. J. Tanner, R. I. Korpinen, M. K.-J. Lillandt, A. V. Pranovich, V. H. Kitunen, S. M. Willför and H. S. Ilvesniemi, Pressurized hot water flow-through extraction system scale up from the laboratory to the pilot scale, Green Chem., 2014, 16, 3186–3194 RSC.
- M. P. Vinardell and M. Mitjans, Lignins and their derivatives with beneficial effects on human health, Int. J. Mol. Sci., 2017, 18, 1219 CrossRef PubMed.
- R. Koshani and A. Madadlou, A viewpoint on the gastrointestinal fate of cellulose nanocrystals, Trends Food Sci. Technol., 2018, 71, 268–273 CrossRef CAS.
-
H. Kangas and M. Pitkänen, Nanomaterials in industry—How to assess the safety? in Industrial applications of nanomaterials: micro and nano technologies, ed. S. Thomas, Y. Grohens and Y. B. Pottathara, Elsevier, 2019, pp. 1–27 Search PubMed.
-
J. Delbeke and P. Vis, EU Climate Policy Explained, 2016, European Union.
- L. Dessbesell, Z. Yuan, S. Hamilton, M. Leitch, R. Pulkki and C. C. Xu, Bio-based polymers production in a kraft lignin biorefinery: techno-economic assessment, Biofuels, Bioprod. Biorefin., 2018, 12, 239–250 CrossRef CAS.
- Z. Fang and C. Fang, Complete dissolution and hydrolysis of wood in hot water, AIChE J., 2008, 54, 2741–2758 CrossRef.
-
J. Xu, Q. Zhou, X. Wang, X. Lu and S. Zhang, Fundamentals of ionic liquids, in Production of biofuels and chemicals with ionic liquids, ed. Z. Fang, R. L. Smith Jr., X. Qi, Springer, 2014, pp. 3–28 Search PubMed.
- T. Lindström, Research needs for nanocellulose commercialization and applications, Tappi J., 2019, 18, 308–311 Search PubMed.
|
This journal is © The Royal Society of Chemistry 2020 |
Click here to see how this site uses Cookies. View our privacy policy here.