DOI:
10.1039/C9GC02963J
(Paper)
Green Chem., 2020,
22, 219-229
Rapid synthesis and NH3-SCR activity of SSZ-13 zeolite via coal gangue
Received
22nd August 2019
, Accepted 19th November 2019
First published on 19th November 2019
Abstract
Coal gangue is a typical waste produced during coal mining and washing. Synthesis of zeolites via coal gangue can contribute to resource recycling and environmental protection. In this study, high-silica SSZ-13 was synthesized by one-step hydrothermal synthesis from coal gangue without the traditional pretreatment methods of high-temperature roasting and alkali melting, making it more convenient and energy efficient. The synthesis time, gel silicon–aluminum ratio and silicon source were systematically studied to optimize the synthesis of SSZ-13. Experimental results indicated that the nucleation time of SSZ-13 could be shortened to 7 h, which was half the synthesis time by using chemicals. Tetrahedral aluminum was the main factor for rapid synthesis, which also accelerated the transformation of octahedral aluminum and further accelerated the synthesis of SSZ-13. The DeNOx activity of the synthesized Cu-SSZ-13 was over 90% across a broad range from 180 to 400 °C, and it remained over 85% in this temperature range even after hydrothermal treatment for 12 h. It also demonstrated good water resistance (over 95% DeNOx in the range of 200 to 400 °C) and sulfur resistance (over 95% DeNOx in the presence of 100 ppm SO2).
Introduction
Coal is the main energy source worldwide. In China, coal-fired thermal power accounts for more than 70% of China's electricity.1 Coal gangue is a type of by-product generated from the process of coal excavation and washing, accounting for 10–15% of China's total coal production.2,3 The quantity of China's coal gangue has reached 4.5 billion tons in 2011, and is generated at a rate of more than 600 million tons per year.4,5 Massive accumulation of coal gangue would occupy vast tracts of farmland, damage the ecological environment, cause geological disasters, and even threaten human health.6,7 Coal gangue has been widely utilized in power generation, cement production, highway roadbeds, concrete production and ceramic manufacturing, and those applications were lower added value.2,8,9 The content of SiO2 and Al2O3 in coal gangue exceeded 68 wt%,10 which are the main elements of zeolites. Therefore, using coal gangue to synthesize zeolites might be environmentally friendly and have value-added applications.11,12 However, the main mineral components of coal gangue are kaolinite, quartz, illite, pyrite, calcite, and carbonaceous materials.13 In order to activate Si and Al, researchers always used high temperature calcination, alkali fusion and submolten salt,14–17 which were energy inefficient and unsafe in practical applications.
As a silica–alumina zeolite with a chabazite structure, SSZ-13 has lots of proton acid sites, excellent hydrothermal stability and orderly pore structure, and it exhibits excellent performance in removing NOx of diesel exhaust, the methanol to olefin (MTO) process and gas separation.18–20 However, the long synthesis time limited its industrial application. It was reported that SSZ-13 was first synthesized in 6 d.21 Although adding F− to the gel could reduce the synthesis time of SSZ-13, it is harmful to the environment.22 The addition of seed crystals could promote nucleation of SSZ-13 zeolite, thus shortening its synthesis time to 2–3 d.23 However, the Si/Al ratios of the samples were lower than 6.1, which was unfavorable to the hydrothermal stability of SSZ-13. The conversion of structures between zeolites could also shorten the synthesis time.24–27 However, those zeolite precursors were cost-prohibitive. The reason for rapid synthesis was that the decomposition of the parent zeolites produced dissolved Si–O–Al fragments, which promoted the crystal growth kinetics.27 Coal gangue contains lots of silica–alumina structures, which as raw materials may promote the rapid synthesis of zeolites.
In this study, high silica SSZ-13 zeolite was rapidly synthesized via coal gangue by a one-step hydrothermal method. The Cu loaded SSZ-13 zeolite exhibits excellent activity, hydrothermal stability and resistance to sulfur and water. Compared with the traditional chemical synthesis, this method shortened the nucleation and synthesis time, enabled energy conservation and environmental protection, and converted the waste of coal gangue into value-added zeolites, which have greater application prospects. The synthesis mechanism of zeolites was systematically investigated and analyzed, which has great significance to the study of rapid synthesis of zeolites.
Materials and methods
Materials
The major mineral composition of coal gangue used in this experiment was tested by X-ray fluorescence (XRF) (Table 1). The XRF results showed that SiO2 and Al2O3 accounted for 80 wt% and the Si/Al mole ratio was about 1.21. All reagents were of analytical grade and used without further purification. KOH and Al2(SO4)3·18H2O were purchased from Tianjin Kermal Chemical Reagent Co. Ltd. TMAdaOH (20 wt% in water) was purchased from Sachem Inc. Kaolin was purchased from Shanghai Titanchem Co. Ltd.
Table 1 Elemental composition of raw coal gangue
Composition |
Si |
Al |
S |
Fe |
O |
Other |
Wt% |
20.29 |
16.10 |
2.0 |
2.54 |
54.76 |
4.31 |
Synthesis of SSZ-13
In this synthetic experiment, the gel molar ratio was n(H2O
:
K
:
Al
:
Si
:
TMAdaOH) = 1250
:
2
:
1
:
15
:
6.5. The silica–alumina ratios discussed in this paper were all atomic ratios. The synthesis process was as follows: coal gangue powder (Al2(SO4)3·18H2O, kaolin, CBV400 or a combination of them) was mixed with KOH solution and stirred for 1 h. Then, aqueous solution of TMAdaOH was mixed and stirred for 1 h. Finally, cabosil-M5 (or silica sol) was mixed to the above solution and stirred for 2 h. The obtained solution precursor was dried at 160 °C for 0–36 h to fully crystallize the samples. After hydrothermal synthesis, the samples were washed three times and dried at 100 °C overnight. Template removal was conducted at 550 °C for 8 h in air.
Cu-SSZ-13 was prepared by a two step ion-exchange method.28 First, the zeolite was mixed with NH4NO3 solution (1 M) and stirred at 80 °C for 8 h. Then the solid was filtered and dried to obtain NH4-SSZ-13. Second, NH4-SSZ-13 was added to Cu(CH3COO)2 solution and stirred at 80 °C for 1 h. It was then filtered and dried again to obtain Cu-SSZ-13. Finally, the Cu-SSZ-13 was calcined at 550 °C for 6 h for further tests.
Characterization
Powder X-ray diffraction (XRD) patterns were recorded on a Bruker D8 Focus XRD diffractometer with a Cu Kα radiation source operating at 40 kV and 40 mA. The relative crystallinity was evaluated by comparing the sum of the peak areas (at 2θ = 9.7°, 13.1°, 14.2°, 16.3°, 18.1°, 20.9°, 25.3°, 26.4°, 31.1° and 31.6°) of the synthesized samples with that of the highest crystallinity (synthesized from chemicals with a synthesis time of 60 h). Scanning electron microscopy and energy dispersive X-ray spectroscopy were performed on a NOVA NanoSEM430 instrument. The samples had to be sprayed before the SEM test. X-ray fluorescence was conducted on a Panalytical Axios X-ray fluorometer. The N2 adsorption isotherms were measured using N2 at 77 K using a Beishide 3H-2000PS4 analyzer. The samples were degassed at 300 °C for 5 h before measurement. 27Al magic angle spinning (MAS) NMR spectra were recorded at 78.13 MHz, on a Varian Infinity plus 300 WB solid NMR spectrometer at a rotation speed of 8 kHz.
Catalytic reaction test
A fixed-bed quartz reactor was used for NH3-SCR activity tests. The gas concentrations were measured by using a gas analyzer (NOVA PLUS Multifunctional German MRU) and an FTIR spectrometer (Bruker TENSOR II). The total flow rate was 300 ml min−1 for all tests, resulting in a space velocity of 100
000 h−1. The reaction gases were as follows: [NO] = [NH3] = 500 ppm, [O2] = 10%, N2 balance, [SO2] = 100 ppm, [H2O] = 5% or 10% when used. The NOx conversion and N2 selectivity were calculated as follows: |  | (1) |
|  | (2) |
Results and discussion
Rapid synthesis of SSZ-13 via coal gangue
The synthesis parameters of SSZ-13 were optimized, and the corresponding XRD results are shown in Fig. 1. Fig. 1-a1 shows the XRD pattern of SSZ-13 synthesized via coal gangue + cabosil-M5. It could be seen that after crystallization for 12 h, the peaks were consistent with the characteristic peak of SSZ-13, which indicated that the synthesized sample was SSZ-13. There were no obvious changes in the position of peaks of synthesized SSZ-13 when the synthesis time was extended, which indicated that the crystal phase of SSZ-13 was not affected by the synthesis time. Fig. 1-a2 shows the relative crystallinity of SSZ-13 synthesized via coal gangue + cabosil-M5. It could be seen that the relative crystallinity gradually increased as the synthesis time prolonged, and it reached about 95% at a crystallization time of 36 h, indicating that the crystallinity of samples was greatly affected by the synthesis time. The SEM images of samples synthesized via coal gangue + cabosil-M5 are shown in Fig. 2. Fig. 2 shows that the synthesized samples have good cubic structures at a synthesis time of 12 h, which was typical of SSZ-13. With the synthesis time prolongation, the amorphous matter on the surface of the synthesized SSZ-13 gradually decreased, which also indicated that the crystallinity of the samples gradually improved. This is consistent with the results of XRD analysis. The crystal size of the synthesized SSZ-13 was approximately 2 μm.
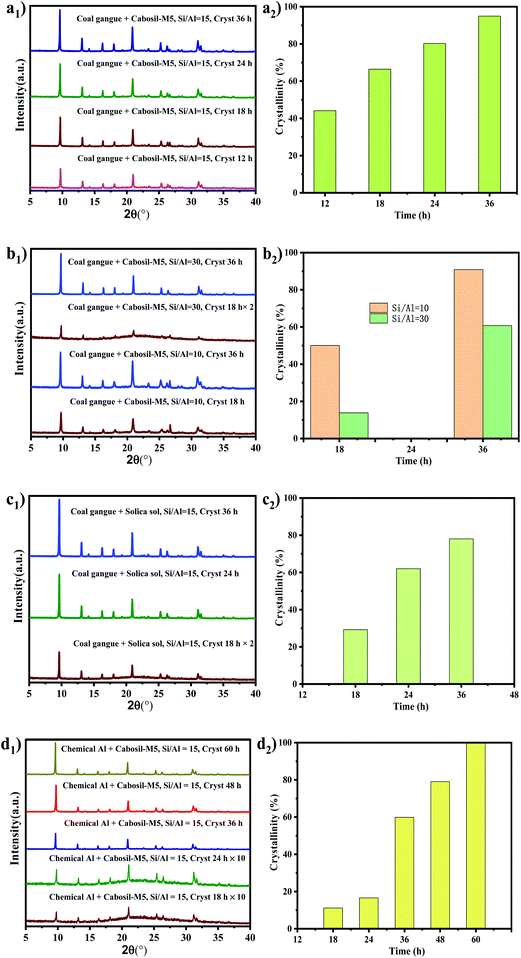 |
| Fig. 1 XRD patterns and relative crystallinity of SSZ-13 synthesized under different synthesis conditions: XRD patterns (a1) and relative crystallinity (a2) of SSZ-13 at different synthesis times with a Si/Al gel ratio of 15 via coal gangue + cabosil-M5. XRD patterns (b1) and relative crystallinity (b2) of SSZ-13 at different synthesis times with different gel Si/Al radios via coal gangue + cabosil-M5. XRD patterns (c1) and relative crystallinity (c2) of SSZ-13 at different synthesis times via coal gangue + silica sol. XRD patterns (d1) and relative crystallinity (d2) of SSZ-13 at different synthesis times with a Si/Al gel ratio of 15 via chemical Al + cabosil-M5. | |
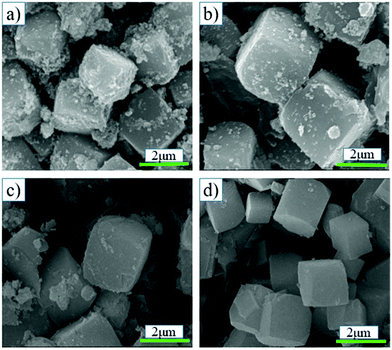 |
| Fig. 2 SEM images of the as-synthesized SSZ-13 at different synthesis times with a Si/Al gel ratio of 15 via coal gangue + cabosil-M5 synthesis: (a) Cryst 12 h, (b) Cryst 18 h, (c) Cryst 24 h, and (d) Cryst 36 h. | |
The hydrothermal resistance of Cu-SSZ-13 was greatly affected by the silica–alumina ratio, while the silica–alumina ratio of the gel affected the silica–alumina ratio of the samples.29,30 The effect of the gel silica–alumina ratio and synthesis time on the silica–alumina ratio of the synthesized samples was investigated. The XRD pattern, relative crystallinity and SEM images of the samples synthesized via coal gangue are shown in Fig. 1-b1, b2 and 3, respectively. As depicted in Fig. 1b1, when the synthesis time was 18 h, the sample prepared with a gel silica–alumina ratio of 10 had sharp SSZ-13 peaks. However, the XRD pattern of the synthesized SSZ-13 at a synthesis time of 18 h and a silica–alumina ratio of 30 had a large arch, which indicated that the sample had a large amount of amorphous matter under these conditions. It could also be confirmed in Fig. 1-b2 that the relative crystallinity of the sample with a gel silica–alumina ratio of 30 was less than 15% at a synthesis time of 18 h, while the relative crystallinity of the sample with a silica–alumina ratio of 10 was more than 50% at the same synthesis time. With the synthesis time increasing to 36 h, it could be found that the relative crystallinity of the sample with a gel silica–alumina ratio of 30 was more than 60%, and the arch in the XRD pattern disappeared, which could be confirmed by the corresponding SEM images in Fig. 3. This indicated that a high gel Si/Al ratio was not conducive to the growth of SSZ-13 crystals.29
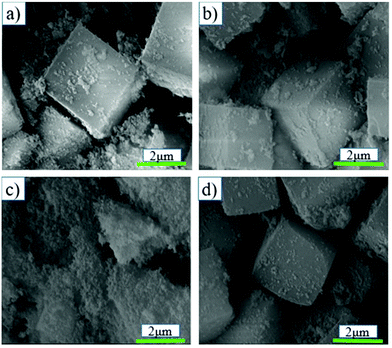 |
| Fig. 3 SEM images of SSZ-13 at different synthesis times with different gel Si/Al radios via coal gangue + cabosil-M5 synthesis: (a) Si/Al = 10, Cryst 18 h, (b) Si/Al = 10, Cryst 36 h, (c) Si/Al = 30, Cryst 18 h, and (d) Si/Al = 30, Cryst 36 h. | |
The silica–alumina ratio of the synthesized SSZ-13 was tested by using an energy dispersive spectrometer (EDS). The data are summarized in Table 2a and b. As shown in Table 2a, the silica–alumina ratio of the synthesized crystal was 9.95 at a gel silica–alumina ratio of 15 when the synthesis time was 12 h. With the synthesis time increasing, the ratio of silica–alumina increased first and then decreased, eventually reaching 13.26 when the synthesis time was 36 h. Through the EDS results of the samples in Table 2b, it could be found that the silica–alumina ratio was only 6.72 at a gel silica–alumina ratio of 10, while the silica–alumina ratio increased to 33 at a gel silica–alumina ratio of 30. Studies showed that the catalyst showed better performance when the silica–alumina ratio was about 15; when the Si/Al ratio was too low (Si/Al = 6), Cu-SSZ-13 was prone to collapse and deactivation due to dealuminization during high temperature hydrothermal treatment; when the Si/Al ratio was too high (Si/Al = 30), the catalyst showed low catalytic activity due to fewer active sites.31 As mentioned above, the silica–alumina ratio of the synthesized SSZ-13 was about 13 with a gel silica–alumina ratio of 15, which was close to the optimal silica–alumina ratio of a catalyst. Therefore, the gel silica–alumina ratio of 15 was a better choice for synthesizing SSZ-13.
Table 2 Elemental and structural analysis of the synthesized SSZ-13 zeolite: (a) EDS analysis of SSZ-13 at different synthesis times with a Si/Al gel ratio of 15 via coal gangue + cabosil-M5 synthesis. (b) EDS analysis of SSZ-13 at different synthesis times with different gel Si/Al ratios via coal gangue + cabosil-M5 synthesis. (c) BET analysis of textural properties of SSZ-13 at different synthesis times with a gel Si/Al ratio of 15 via coal gangue + cabosil-M5 synthesis. (d) EDS analysis of Cu content of Cu-SSZ-13 after Cu ion exchange at a synthesis time of 36 h via coal gangue + cabosil-M5 synthesis
a |
Samples |
Si/Al ratio of gel |
Si/Al ratio of sample |
Cryst 12 h |
15 |
9.95 |
Cryst 18 h |
15 |
15.42 |
Cryst 24 h |
15 |
13.68 |
Cryst 36 h |
15 |
13.26 |
b |
Samples |
Si/Al ratio of gel |
Si/Al ratio of sample |
Cryst 18 h |
10 |
6.72 |
Cryst 36 h |
10 |
6.54 |
Cryst 18 h |
30 |
33.12 |
Cryst 36 h |
30 |
33.02 |
c |
Samples |
Si/Al ratio of gel |
S
BET (m2 g−1) |
V
t (cm3 g−1) |
V
M (cm3 g−1) |
Cryst 18 h |
15 |
511 |
0.38 |
0.21 |
Cryst 24 h |
15 |
565 |
0.34 |
0.23 |
Cryst 36 h |
15 |
535 |
0.31 |
0.22 |
d |
Samples |
Cu ion-change concentration (mol l−1) |
0.002 |
0.01 |
0.05 |
Cryst 36 h |
Cu content (wt%) |
— |
3.97 |
— |
The silicon source was one of the main factors affecting zeolite synthesis.32,33 The effects of the silica source was investigated for the synthesis of SSZ-13 zeolite. The XRD pattern, relative crystallinity and SEM images of SSZ-13 synthesized with different synthesis times via coal gangue + silica sol are shown in Fig. 1-c1, c2 and 4, respectively. Fig. 1-c1 shows that all samples exhibited the typical characteristic peaks of SSZ-13. Fig. 1-c2 shows that the relative crystallinity of the samples increased with the increase of synthesis time, and the relative crystallinity of the synthesized sample was less than 30% at a synthesis time of 18 h. It could be confirmed by the SEM images in Fig. 4 that the amorphous matter was continuously present at a synthesis time of 18 h, and the amorphous matter disappeared gradually as the synthesis time increased to 36 h. By comparing with the synthesized SSZ-13 via cabosil-M5 as the silica source, the use of silica sol as the silica source led to a longer synthesis time. Therefore, cabosil-M5 was an excellent raw material for synthesizing SSZ-13 under these conditions.
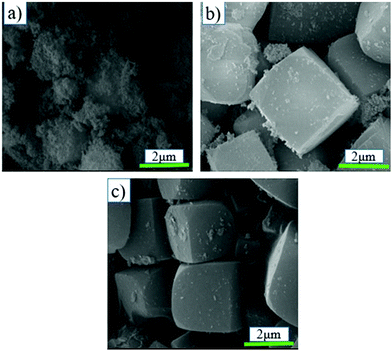 |
| Fig. 4 SEM images of SSZ-13 at different synthesis times with a gel Si/Al ratio of 15 via coal gangue + silica sol synthesis: (a) Cryst 18 h, (b) Cryst 24 h, and (c) Cryst 36 h. | |
The XRD pattern, relative crystallinity and SEM results of SSZ-13 synthesized at different synthesis times via chemical Al + cabosil-M5 are shown in Fig. 1d1, d2 and 5, respectively. Fig. 1-d1 shows that all samples exhibited the typical characteristic peaks of SSZ-13. Fig. 1-d2 shows that the relative crystallinity of samples synthesized from chemicals is poor and increases slowly when the synthesis time is less than 24 h. When the synthesis time exceeded 24 h, the crystallinity of the samples increases rapidly, and it reaches 100% at a synthesis time of 60 h. This could be confirmed by the SEM images in Fig. 5. The samples exhibited cubic structures with good crystallinity and the crystal size was approximately 7 μm at an extended synthesis time of 48 h. The literature showed that smaller crystal sizes were more conducive to mass transfer and led to better catalytic performance.28,34 Compared with chemicals, using coal gangue to synthesize SSZ-13 required less synthesis time and resulted in a smaller crystal size, indicating that coal gangue was a better synthetic material.
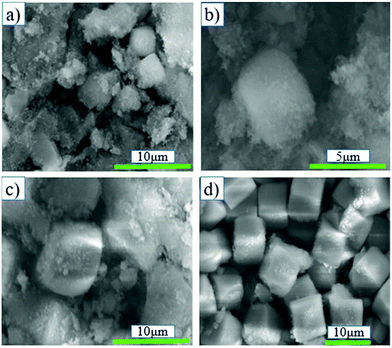 |
| Fig. 5 SEM images of the as-synthesized SSZ-13 at different synthesis times with a Si/Al gel ratio of 15 via chemicals + cabosil-M5 synthesis: (a) Cryst 18 h, (b) Cryst 24 h, (c) Cryst 36 h, and (d) Cryst 48 h. | |
Synthesis mechanism analysis
Fig. 6a shows the XRD patterns of SSZ-13 throughout the synthesis procedure via coal gangue + cabosil-M5. It could be seen that after pretreatment, the characteristic peaks of kaolinite almost disappeared and the characteristic peaks of quartz also decreased obviously. As the synthesis time increased, the characteristic peaks of quartz gradually decreased. When the synthesis time was 7 h, the SSZ-13 peaks formed. Fig. 6b shows the XRD patterns of SSZ-13 throughout the nucleation process via chemicals + cabosil-M5. It could be seen that only the characteristic peak of silica dioxide appeared at the initial stage of synthesis. The SSZ-13 formed when the synthesis time reached 14 h, which was approximately 7 h longer than that when the coal gangue was used as the raw material.
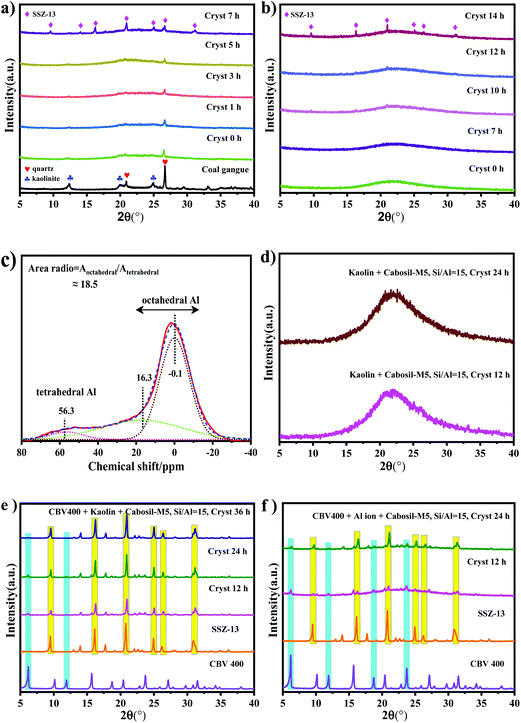 |
| Fig. 6 Characterization of the nucleation process of the synthesis of SSZ-13 via coal gangue. (a) XRD patterns of coal gangue and the nucleation process of SSZ-13 via coal gangue + cabosil-M5 with a Si/Al gel ratio of 15. (b) XRD patterns of the nucleation process of SSZ-13 via chemical Al + cabosil-M5 with a Si/Al gel ratio of 15. (c) 27Al MAS NMR spectra of raw coal gangue. (d) XRD patterns of the nucleation process of SSZ-13 via kaolin + cabosil-M5 with a Si/Al gel ratio of 15. (e) XRD patterns of SSZ-13 via CBV400 + kaolin + cabosil-M5 at different synthesis times with a Si/Al gel ratio of 15. (f) XRD patterns of SSZ-13 via CBV400 + Al ions + cabosil-M5 at different synthesis times with a Si/Al gel ratio of 15. | |
The silica–alumina atomic ratio of the coal gangue was approximately 1.21. Compared with the silica–alumina ratio of the gel (15), coal gangue was mainly used as the aluminum source. The Al NMR results of the coal gangue are shown in Fig. 6c. It indicated that Al in the coal gangue consisted of octahedral aluminum and tetrahedral aluminum. As seen above in the XRD of coal gangue, octahedral aluminum should be present in kaolinite. The SSZ-13 synthesized from kaolin with different synthesis times is studied, and the corresponding XRD patterns are shown in Fig. 6d. Fig. 6d shows that the SSZ-13 peaks still did not appear when the synthesis time was 24 h, which indicated that only octahedral aluminum as the aluminum source could not rapidly synthesize SSZ-13. In order to simulate the Al structure composition of coal gangue, both CBV400 and kaolin were used as aluminum sources to synthesize SSZ-13. And the corresponding XRD pattern is shown in Fig. 6e. Fig. 6e shows that the SSZ-13 peaks formed without the arch when the synthesis time was 12 h, indicating that the synthesized samples had good crystallinity at this time. There were a few characteristic peaks of CBV400 in Fig. 6e; the reason may be that the structure of CBV400 was relatively stable and not completely dissolved in the aging stage of synthesized SSZ-13. Since the Al structure of CBV400 aluminum was tetrahedral aluminum, it could be inferred that the existence of tetrahedral aluminum was the main reason for promoting nucleation of SSZ-13.
Both CBV400 and Al ions were also used as aluminum sources to synthesize SSZ-13. And the corresponding XRD pattern is shown in Fig. 6f. Fig. 6f shows that the SSZ-13 peaks formed with a large arch when the synthesis time was 12 h, indicating that the synthesized samples had poor crystallinity at this time. By comparing Fig. 6e and f at the same synthesis time, it could be found that in the presence of CBV400, the synthesis rate of kaolin was faster than that of aluminum ions. The literature indicated that in the process of synthesizing zeolite via kaolin as the raw material, kaolin would be converted into metakaolin; the main reason was that metakaolin contained a large amount of tetrahedral aluminum, which was more reactive than octahedral aluminum in the synthesis of zeolites.35–38 The previous work of our research team has also verified that the kaolin in coal gangue decomposed and converted into some structural units such as Si–O–Si and Si–O–Al after pretreatment, and those structural units were beneficial to the nucleation and synthesis of SSZ-13.39 It was inferred that tetrahedral aluminum promotes the transformation of octahedral aluminum into tetrahedral aluminum structural units such as Si–O–Al, which further promoted the nucleation and synthesis of the SSZ-13. Therefore, it was further inferred that the presence of tetrahedral aluminum was the main reason for promoting the rapid synthesis of SSZ-13, and it also promoted the transformation of octahedral aluminum into tetrahedral aluminum structural units, which further accelerated the synthesis of SSZ-13. The comparison schematic of the SSZ-13 synthesis path is shown in Fig. 7.
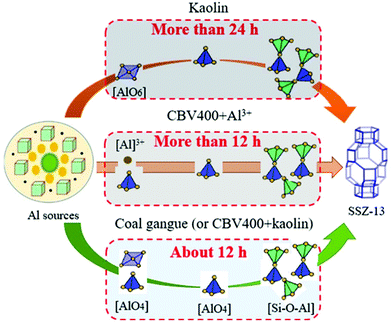 |
| Fig. 7 Schematic representation of the synthesis mechanism of SSZ-13 from coal gangue. | |
NH3-SCR performance
BET analysis
The N2 adsorption–desorption isotherms under different synthesis times of synthesized SSZ-13 are shown in Fig. 8. As shown in Fig. 8a, all the N2 adsorption–desorption isotherm curves of the synthesized samples showed typical I adsorption with a H4 hysteresis according to the classification of IUPAC, which indicated that the samples were microporous zeolites.40 The corresponding pore size distribution curves are shown in Fig. 8b, calculated by the DFT method. A relatively narrow pore size of about 0.5 nm was measured, suggesting the uniform size of the synthesized SSZ-13 zeolite, which was consistent with the conclusion that the synthesized samples were microporous. The textural properties of the samples are summarized in Table 2c. It indicated that after the synthesis time exceeded 18 h, the synthesis time had a slight effect on the textural properties of the synthesized samples. And the synthesized samples showed similar surface areas (511–565 m2 g−1), micropore volumes (0.21–0.23 cm3 g−1) and total pore volumes (0.31–0.38 cm3 g−1).
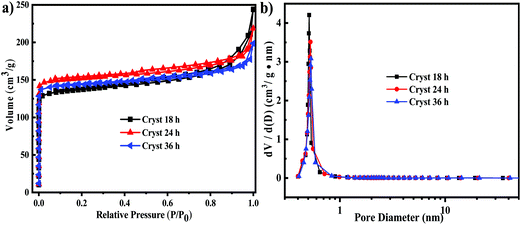 |
| Fig. 8 N2 adsorption–desorption isotherms (a) and pore size distribution (b) of SSZ-13 with a gel Si/Al ratio of 15 via coal gangue + cabosil-M5 synthesis at different synthesis times; pore size distributions were calculated using the DFT method. | |
Synthesis time optimization
The DeNOx activity of Cu-SSZ-13 synthesized with different synthesis times is studied, which is shown in Fig. 9a. It indicated that the higher the synthesis time, the better the NOx conversion performance, especially at low temperatures. The DeNOx activity of the catalyst with a synthesis time of 36 h was optimal, and the activity of the catalyst was more than 90% at 180–400 °C. According to the SEM images in Fig. 2, the crystallinity of SSZ-13 improved with the extension of synthesis time. Therefore, it was inferred that crystallinity was the main factor affecting the DeNOx activity of Cu-SSZ-13.
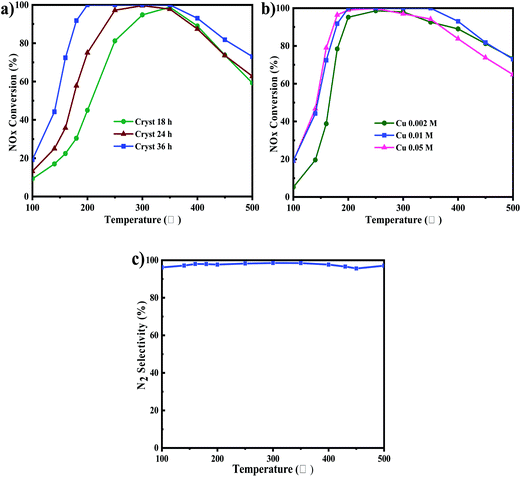 |
| Fig. 9 Study on the optimal activity parameters of Cu-SSZ-13 with a Si/Al gel ratio of 15 via coal gangue + cabosil-M5. (a) NOx conversion of Cu-SSZ-13 after 0.01 M Cu ion exchange at different synthesis times. (b) NOx conversion of Cu-SSZ-13 with a synthesis time of 36 h with different Cu ion exchange concentrations. (c) N2 selectivity of Cu-SSZ-13 with a synthesis time of 36 h and 0.01 M Cu ion exchange. Reaction conditions: [NO] = [NH3] = 500 ppm, [O2] = 10%, N2 balance, total flow rate 300 ml min−1 and GHSV = 100 000 h−1. | |
Cu ion exchange concentration optimization
Fig. 9b shows the DeNOx activity of the synthesized catalysts with different copper exchange concentrations. As shown in Fig. 9b, it could be seen that with the increase of Cu exchange concentration, the DeNOx activity of Cu-SSZ-13 increased gradually at low temperatures (≤200 °C). As the temperature exceeded 350 °C, the DeNOx activity of Cu-SSZ-13 decreased significantly, especially that of the catalyst with 0.05 M Cu exchange. The optimum Cu exchange concentration was 0.01 M, and the NOx conversion reached 90% in the range of 180 °C to 400 °C. The reason might be that at low temperatures (≤250 °C), the density of Cu ions had enormous influence on the DeNOx activity of Cu-SSZ-13; however, with the temperature further increasing (≥350 °C), non-selective NH3 oxidation by O2 became the dominant reaction, which deprived the NH3 reductant of the SCR reaction.41–43 In addition, CuO particles formed at high Cu loadings of Cu-SSZ-13, and these particles tended to oxidize NH3 instead of reducing NOx in NH3-SCR.42 As shown in Fig. 9c the N2 selectivity of the catalyst with 0.01 M Cu ion exchange was more than 95% in the entire test temperature. Table 2d shows that the optimum copper mass concentration in synthesized Cu-SSZ-13 was about 3.97 wt%, which was tested by EDS. Therefore, the catalyst of 0.01 M Cu ion exchange concentration was used for further studies.
NOx conversion and H2O resistance
Fig. 10a shows the comparison with and without water on Cu-SSZ-13 synthesized from coal gangue + cabosil-M5 and chemical Al + cabosil-M5. As shown in Fig. 10a, NOx conversion on Cu-SSZ-13 synthesized from chemical Al was slightly higher than that from coal gangue, but the DeNOx activity of the two catalysts was more than 90% in the range of 180 to 400 °C, and the activities became similar in the presence of water. By comparing the DeNOx activity with (5 vol%) and without H2O on the Cu-SSZ-13 synthesized from coal gangue, it could be seen that when the temperature was below 200 °C, the presence of H2O significantly inhibited the catalyst activity, and NOx conversion decreased by about 10%. When the temperature was between 200 and 350 °C, the NOx conversion was less affected by water vapor. As the temperature continued to raise to 400 °C, the DeNOx activity was slightly higher in the presence of H2O than in the absence of H2O. This result indicated that H2O had an inhibitory effect on the DeNOx activity of Cu-SSZ-13 at low temperatures, while slightly promoting the DeNOx activity of the catalyst at high temperatures. The reason might be that the water showed competitive adsorption with NH3 at low temperatures, resulting in decreasing NOx conversion activity of the catalyst at low temperature, while decreased NH3 oxidation in the presence of H2O resulted in increasing NOx conversion at high temperature.44,45
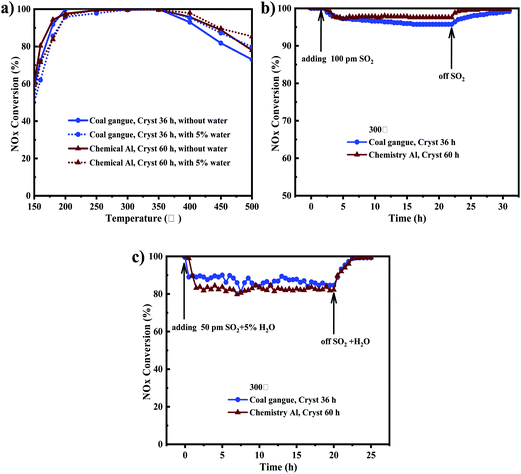 |
| Fig. 10 NOx conversion comparison of H2O, SO2 and SO2 + H2O resistance on Cu-SSZ-13 synthesized with 0.01 M copper ion exchange from coal gangue + cabosil-M5 and chemical Al + cabosil-M5. (a) NOx conversion comparison with and without water on Cu-SSZ-13 synthesized from coal gangue + cabosil-M5 and chemical Al + cabosil-M5. (b) NOx conversion comparison of SO2 resistance on Cu-SSZ-13 synthesized from coal gangue + cabosil-M5 and chemical Al + cabosil-M5. (c) NOx conversion comparison of SO2 + H2O resistance on Cu-SSZ-13 synthesized from coal gangue + cabosil-M5 and chemical Al + cabosil-M5. Reaction conditions: [NO] = [NH3] = 500 ppm, [O2] = 10%, [SO2] = 50 or 100 ppm when used, [H2O] = 5% when used, N2 balance, total flow rate 300 ml min−1 and GHSV = 100 000 h−1. | |
SO2 resistance
Fig. 10b shows the comparison of 100 ppm SO2 resistance on Cu-SSZ-13 synthesized at 300 °C from coal gangue + cabosil-M5 and chemical Al + cabosil-M5. As shown in Fig. 10b, SO2 resistance on Cu-SSZ-13 synthesized from chemical Al was slightly higher than that from coal gangue, but the activity change trends of the two catalysts were similar. It was shown that the SCR activity of the catalysts remained at 100% before SO2 was injected. The catalyst activity began to gradually decrease and then remained above 95% in the presence of SO2 for 22 h. Upon stopping the injection of SO2, the SCR activity gradually recovered to more than 99%. It is reasonable to speculate that SO2 may react directly with NH3 to form (NH3)2SO4 and (NH3)2SO3 and deposit on the surface of the catalyst, resulting in a decrease in NOx conversion. And as SO2 was ceased, the formed species gradually decomposed, resulting in recovery of NOx conversion. This indicated that the effect of sulfur dioxide on the catalyst was reversible inactivation.
SO2 + H2O resistance
Fig. 10c shows the comparison of 50 ppm SO2 + 5% H2O resistance on Cu-SSZ-13 synthesized at 300 °C from coal gangue + cabosil-M5 and chemical Al + cabosil-M5. As shown in Fig. 10c, the SO2 + H2O resistance on Cu-SSZ-13 synthesized from coal gangue was slightly higher than that from chemical Al, but the activity fluctuation trends of the catalysts with the introduction of SO2 + H2O were basically similar. After injection of SO2 + H2O at the same time, the NOx conversion of the two catalysts decreased rapidly and then remained stable. The NOx conversion of the two catalysts remained above 80% in the presence of H2O + SO2 for 20 h. The catalyst activity gradually recovered to more than 99% after stopping the injection of H2O + SO2, indicating that the influence of sulfur and water on the catalyst was reversible inactivation.
Hydrothermal stability
The comparison of NOx conversion before and after hydrothermal treatment on Cu-SSZ-13 synthesized from coal gangue + cabosil-M5 and chemical Al + cabosil-M5 is presented in Fig. 11. As shown in Fig. 11, the activity of Cu-SSZ-13 synthesized from chemical Al before and after hydrothermal treatment was slightly higher than that from coal gangue, but the hydrothermal stability of Cu-SSZ-13 from coal gangue was also excellent. Comparing the NOx conversion of catalysts before and after hydrothermal treatment, it could be seen that after hydrothermal treatment for 12 h, the activity of the catalyst decreased slightly (<200 °C), while it decreased significantly at high temperatures (>300 °C). The reason for these results may be that hydrothermal treatment could cause the aggregation of copper ions and form CuO clusters.46 As the active center of the Cu-SSZ-13, the decrease in copper ions will directly lead to a decrease in catalyst SCR activity at low temperatures. In addition, the CuO generated by hydrothermal aging will lead to the non-selective ammoxidation by O2 at high temperatures.46 However, the DeNOx activity of the synthesized catalyst remained above 85% in the range of 180 to 400 °C after hydrothermal treatment.
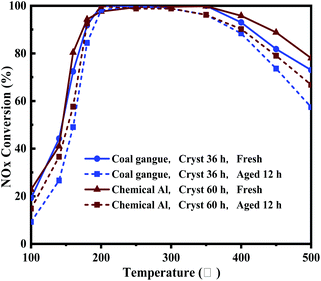 |
| Fig. 11 NOx conversion comparison before and after hydrothermal aging on Cu-SSZ-13 with 0.01 M copper ion exchange from coal gangue + cabosil-M5 and chemical Al + cabosil-M5. Reaction conditions: [NO] = [NH3] = 500 ppm when used, [O2] = 10%, [H2O] = 10% when used, N2 balance, total flow rate 300 ml min−1 and GHSV = 100 000 h−1. | |
Conclusions
SSZ-13 zeolite was synthesized by a one-step hydrothermal method via coal gangue. The results showed that the formation time of SSZ-13 via coal gangue was shortened by 7 h compared with chemical synthesis. Further research found that the optimal silica–alumina ratio was 15 and the optimum silicon source was cabosil-M5. The DeNOx activity of the Cu-SSZ-13 synthesized with a crystallization time of 36 h from coal gangue was over 90% in the range of 180 to 400 °C, and the DeNOx activity remained over 85% in this temperature range even after hydrothermal treatment of 12 h. Moreover, it also had good water resistance (over 95% DeNOx activity in the range of 200 to 400 °C), sulfur resistance (over 95% DeNOx activity with 100 ppm SO2), and water + sulfur resistance (over 85% DeNOx activity with 50 ppm SO2 + 5% water). These performances were slightly lower than the activities of the catalyst synthesized from chemicals with a crystallization time of 60 h. Thus, the Cu-SSZ-13 synthesized from coal gangue has a bright future in industrial applications because of the lower cost and shorter crystallization time. In addition, it was found that the presence of tetrahedral aluminum was the main factor contributing to the rapid synthesis, which also promoted the transformation from octahedral aluminum to tetrahedral aluminum structural units and further accelerated the formation of SSZ-13. This indicated that using coal gangue to synthesize SSZ-13 could be a potential alternative to achieve its value-added and environmentally friendly utilization.
Conflicts of interest
The authors declare no competing financial interest.
Acknowledgements
This work was supported by the National Key R&D Program of China (No. 2016YFC0205300), the National Engineering Laboratory for Mobile Source Emission Control Technology of China (NELMS2017A03), the Natural National Science Foundation of China (No. 21503144 and 21690083), the Tianjin Research Program of Ecological Environmental Treatment (No. 18ZXSZSF00210 and 18ZXSZSF00060) and the Tianjin Research Program of Application Foundation and Advanced Technique (No. 16JCQNJC05400).
References
- X. W. Lu, X. D. Jia and F. L. Wang, Curr. Sci., 2006, 91, 1508–1511 CAS.
- H. B. Liu and Z. L. Liu, Resour., Conserv. Recycl., 2010, 54, 1331–1340 CrossRef.
- Z. C. Dong, J. W. Xia, C. Fan and J. C. Cao, Constr. Build. Mater., 2015, 100, 63–69 CrossRef.
- Y. Yun, R. Gao, H. F. Yue, X. F. Liu, G. K. LI and N. Sang, Sci. Total Environ., 2017, 580, 632–640 CrossRef CAS PubMed.
- H. Wu, Q. B. Wen, L. M. Hu, M. Gong and Z. L. Tang, Waste Manage., 2017, 63, 161–171 CrossRef CAS.
- J. F. Li, C. S. Yue, M. Zhang, X. D. Wang and Z. T. Zhang, Energies, 2015, 8, 7428–7440 CrossRef CAS.
- B. W. Liu, Z. H. Tang, S. G. Dong, L. X. Wang and D. W. Liu, Int. Biodeterior. Biodegrad., 2018, 128, 134–140 CrossRef CAS.
- L. J. Yu, Y. L. Feng and W. Yan, Adv. Mater. Res., 2012, 524–527, 915–918 CAS.
- J. M. Wang, Q. Qin, S. J. Hu and K. N. Wu, J. Cleaner Prod., 2016, 112, 631–638 CrossRef.
- D. X. Li, X. Y. Song, C. C. Gong and Z. H. Pan, Cem. Concr. Res., 2006, 36, 1752–1759 CrossRef CAS.
- T. T. Qian and J. H. Li, Adv. Powder Technol., 2015, 26, 98–104 CrossRef CAS.
- J. L. Chen and X. W. Lu, J. Mater. Cycles Waste Manage., 2018, 20, 489–495 CrossRef CAS.
- C. C. Zhou, G. J. Liu, Z. C. Yan, T. Fang and R. W. Wang, Fuel, 2012, 97, 644–650 CrossRef CAS.
- J. L. Chen and X. W. Lu, J. Water Reuse Desalin., 2018, 8, 94–101 CrossRef CAS.
- X. W. Lu, D. Q. Shi and J. L. Chen, Environ. Earth Sci., 2017, 76, 591 CrossRef.
- Y. Y. Yue, H. Y. Liu, Y. N. Zhou, Z. S. Bai and X. J. Bao, Appl. Clay Sci., 2016, 126, 1–6 CrossRef CAS.
- Y. Y. Yue, X. X. Guo, T. Liu, H. Y. Liu, T. H. Wang, P. Yuan, H. B. Zhu, Z. S. Bai and X. J. Bao, Microporous Mesoporous Mater., 2019 DOI:10.1016/j.micromeso.2019.109772.
- Y. H. Zheng, N. Hu, H. M. Wang, N. Bu, F. Zhang and R. F. Zhou, J. Membr. Sci., 2015, 475, 303–310 CrossRef CAS.
- B. H. Chen, R. N. Xu, R. D. Zhang and N. Liu, Environ. Sci. Technol., 2014, 48, 13909–13916 CrossRef CAS PubMed.
- Y. W. Ji, M. A. Deimund, Y. Bhawe and M. E. Davis, ACS Catal., 2015, 5, 4456–4465 CrossRef CAS.
-
S. I. Zones, US Patent4544538, 1985 Search PubMed.
- E. A. Eilertsen, B. Arstad, S. Svelle and K. P. Lillerud, Microporous Mesoporous Mater., 2012, 153, 94–99 CrossRef CAS.
- Z. C. Zhao, R. Yu, R. R. Zhao, C. Shi, H. Gies, F. S. Xiao, D. D. Vos, T. Yokoi, X. H. Bao, U. Kolb, M. Feyen, R. Mcguire, S. Maurer, A. Moini, U. Müller and W. P. Zhang, Appl. Catal., B, 2017, 217, 421–428 CrossRef CAS.
- B. N. Bhadra, P. W. Seo, N. A. Khan, J. W. Jun, T. W. Kim, C. U. Kim and S. H. Jhung, Catal. Today, 2017, 298, 53–60 CrossRef CAS.
- H. L. Geng, G. Li, D. Liu and C. Y. Liu, J. Solid State Chem., 2018, 265, 193–199 CrossRef CAS.
- Y. P. Li, Y. Zhang, A. D. Lan, H. M. Bian, R. Liu, X. F. Li, P. D. Han and T. Dou, Microporous Mesoporous Mater., 2019, 279, 1–9 CrossRef CAS.
- L. X. Tang, K. G. Haw, Y. Y. Zhang, Q. R. Fang, S. L. Qiu and V. Valtchev, Microporous Mesoporous Mater., 2019, 280, 306–314 CrossRef CAS.
- T. Zhang, F. Qiu and J. H. Li, Appl. Catal., B, 2016, 195, 48–58 CrossRef CAS.
- E. A. Eilertsen, M. H. Nilsen, R. Wendelbo, U. Olsbye and K. P. Lillerud, Stud. Surf. Sci. Catal., 2008, 174, 265–268 CrossRef.
- F. Gao, N. M. Washton, Y. L. Wang, M. Kollár, J. Szanyi and C. H. F. Peden, J. Catal., 2015, 331, 25–38 CrossRef CAS.
- C. Fan, Z. Chen, L. Pang, S. J. Ming, X. F. Zhang, K. B. Albert, P. Liu, H. P. Chen and T. Li, Appl. Catal., A, 2018, 550, 256–265 CrossRef CAS.
- N. Kumar and L. E. Lindfors, Appl. Catal., A, 1996, 147, 175–187 CrossRef CAS.
- S. Askari, R. Halladj and M. Sohrabi, Rev. Adv. Mater. Sci., 2012, 32, 83–93 CAS.
- N. Nishiyama, M. Kawaguchi, Y. Hirota, D. V. Vu, Y. Egashira and K. Ueyama, Appl. Catal., A, 2009, 362, 193–199 CrossRef CAS.
- A. A. B. Maia, R. N. Dias, R. S. Angelica and R. F. Neves, J. Mater. Res. Technol., 2019, 8, 2924–2929 CrossRef CAS.
- S. H. Silva Filho, L. Bieseki, A. R. Silva, A. A. B. Maia, R. A. S. San Gil and S. B. C. Pergher, Ceramica, 2015, 61, 409–413 CrossRef.
- E. A. Hildebbrando, C. G. B. Andrade, C. A. F. Rocha Junior, R. S. Angélica, F. R. Valenzuela-Diaz and R. F. Neves, Mater. Res., 2014, 17, 174–179 CrossRef.
- A. Á. B. Maia, R. F. Neves, R. S. Angélica and H. Pöllmann, Appl. Clay Sci., 2015, 108, 55–60 CrossRef CAS.
- J. F. Han, Y. Ha, M. Y. Guo, P. P. Zhao, Q. L. Liu, C. X. Liu, C. F. Song, N. Ji, X. B. Lu, D. G. Ma and Z. G. Li, Ultrason. Sonochem., 2019, 59 DOI:10.1016/j.ultsonch.2019.104703.
- T. D. Pham, Q. L. Liu and R. F. Lobo, Langmuir, 2013, 29, 832–839 CrossRef CAS PubMed.
- J. H. Park, H. J. Park, J. H. Baik, I. S. Nam, C. H. Shin, J. H. Lee, B. K. Cho and S. H. Oh, J. Catal., 2006, 240, 47–57 CrossRef CAS.
- J. H. Kwak, D. Tran, J. Szanyi, C. H. F. Penden and J. H. Lee, Catal. Lett., 2012, 142, 295–301 CrossRef CAS.
- F. Gao, E. D. Walter, E. M. Karp, J. Y. Luo, R. G. Tonkyn, J. H. Kwak, J. Szanyi and C. H. F. Peden, J. Catal., 2013, 300, 20–29 CrossRef CAS.
- J. H. Li, H. Z. Chang, L. Ma, J. M. Hao and R. T. Yang, Catal. Today, 2011, 175, 147–156 CrossRef CAS.
- T. Zhang, F. Qiu, H. Z. Chang, X. Li and J. H. Li, Catal.: Sci. Technol., 2016, 6, 6294–6304 RSC.
- J. Song, Y. L. Wang, E. D. Walter, N. M. Washton, D. H. Mei, L. B. Kovarik, M. H. Engelhard, S. Prodinger, Y. Wang, C. H. F. Peden and F. Gao, ACS Catal., 2017, 7, 8214–8227 CrossRef CAS.
|
This journal is © The Royal Society of Chemistry 2020 |
Click here to see how this site uses Cookies. View our privacy policy here.