pH universal Ru@N-doped carbon catalyst for efficient and fast hydrogen evolution†
Received
17th December 2019
, Accepted 10th June 2020
First published on 11th June 2020
1. Introduction
The hydrogen evolution reaction (HER) is a key step in overall water splitting; it stores energy by producing H2 gas which is a green and sustainable alternative to fossil fuels.1–3 Therefore, the employment of H2 as an energy source in our real life has been attracting more and more attention in these years. Compared to the traditional H2 production by steam reforming of natural gas, electrochemical reduction of water is much cleaner and more sustainable because the electricity consumed can be obtained from renewable energy sources such as solar, wind, river and so on.4,5 Platinum (Pt) is known to be the most efficient electrocatalyst for HER in both acidic and alkaline solutions6–8 owing in part to its appropriate Pt–H bond strength,9 but the large-scale application of Pt HER electrocatalysis is impractical due to the high cost and low natural abundance of Pt.10 Therefore, the search for more economical candidates is desirable. Much effort has been made to develop earth-abundant Pt-free HER catalysts.11–15 Although the HER activity of some of these catalysts is comparable to that of Pt in acidic media, they are generally susceptible to corrosion in acid. In addition, most catalysts exhibit much lower activity and stability in alkaline media. Since many commercial water electrolysers operate in alkaline solutions, it is necessary to develop more stable and efficient catalysts under alkaline conditions.16
Recently, much attention has been paid to the use of ruthenium as HER electrocatalysts, since the metal–hydrogen bond strength of Ru is similar to that of Pt (∼65 kcal mol−1), but it is around 25 times cheaper than Pt.17 There have been several reports suggesting that Ru is a promising and attractive alternative to Pt in achieving excellent HER performance.16–24 In particular, a number of electrocatalysts based on Ru nanoparticles (NPs) have been recently shown to exhibit similar or even better HER performance compared to the Pt/C benchmark.25–30 However, the preparation of Ru NPs usually requires a strong reducing reagent such as NaBH4, and the direct loading of Ru NPs on the surface of the supports may be not enough to guarantee the sufficient interactions with the supports. Thermolysis of a Ru precursor with a carbon source seems to be a potential way for the in situ generation of Ru NPs embedded in a carbon matrix, though it is still a challenge to control the uniform particle size and the homogenous distribution of NPs during the high temperature pyrolysis process. Herein, we report the design of a series of Ru-based HER electrocatalysts composed of uniform Ru nanoparticles embedded in N-doped carbon (NC) (Ru@NC). These electrocatalysts are prepared by pyrolysis of mixtures of a Ru precursor and various ratios of a carbon-containing ligand, and they are found to exhibit excellent activity and stability in alkaline solution as well as good performance in acidic media.
The synthetic route for Ru@NC is illustrated in Scheme 1. Bu4N[Ru(N)Cl4] and Na4EDTA (H4EDTA = ethylenediamine tetraacetic acid) were chosen as the precursors because the chloro ligands of [Ru(N)Cl4]− are relatively labile and can be readily substituted by EDTA to give [Ru(N)(EDTA)x]n−.31 Thermolysis of [Ru(N)(EDTA)x]n− at 850 °C under inert atmosphere affords Ru@NC. Various samples of Ru@NC were prepared by adjusting the mole ratio of Bu4N[Ru(N)Cl4] and Na4EDTA (1
:
2, 1
:
5, 1
:
10 and 1
:
20). N-Doped carbon without Ru as obtained by direct thermolysis of Na4EDTA under similar conditions.
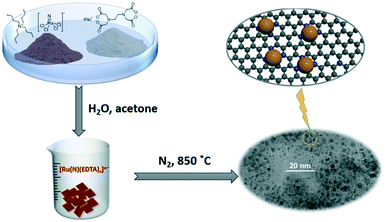 |
| Scheme 1 Schematic illustration of the synthesis and the structure of the Ru@NC electrocatalysts. | |
2. Experimental
2.1. Reagents
All chemicals were of reagent grade and used as received unless otherwise noted. [Bu4N[Ru(N)Cl4] was prepared according to a literature method.31 Water for the experiments was distilled twice from alkaline permanganate. Ethylenediaminetetraacetic acid tetrasodium (Na4EDTA) and commercial Pt/C (20 wt%) catalyst were purchased from Sigma-Aldrich. Nafion solution (5% wt in water and 1-propanol) was purchased from Alfa Aesar.
2.2. Preparation of Ru@NC
The synthesis of Ru@NC electrocatalysts follows the same procedure. Take Ru@NC(1
:
5) for example. Typically, 500 mg [Bu4N[Ru(N)Cl4] (1 mmol) and 1.9 g Na4EDTA (5 mmol) were dissolved in a mixed solvent containing water (50 mL) and acetone (20 mL) and the solution was stirred for 15 min at room temperature. Then, the solution was evaporated under vacuum. The remaining solid was triturated followed by carbonization at 850 °C under N2 atmosphere for 2 h. The final black powder was soaked in 0.5 M H2SO4 solution for one night followed by washing with water and absolute ethanol, and dried at vacuum for 12 h. Ru@NC(1
:
2, 1
:
10 and 1
:
20) were prepared by the similar procedure. N-Doped carbon without Ru was obtained by direct thermolysis of Na4EDTA under the same conditions.
2.3. Physical characterization
The X-ray diffractometer (X'Pert PRO MPD) with Cu-Kα radiation was employed to obtain the X-ray powder diffraction (XRD) with the 2-theta range from 10° to 90°. Scanning electron microscopy (SEM) images were recorded on a field-emission scanning electron microscope (JEM-2100F) with an accelerating voltage of 5 kV. The elemental mapping was analysed by the energy dispersion X-ray spectroscopy (EDS). Transmission electron microscopy (TEM) images were obtained on a SU8020 microscope. The surface area was obtained by nitrogen adsorption–desorption isotherms using the Brunauer–Emmett–Teller (BET) method on Autosorb-IQ3 sorption analyzer based on N2 adsorption/desorption. The chemical elements and valence states of samples were investigated by X-ray photoelectron spectroscopy with an ESCALAB250Xi spectrometer and all data were corrected by employing the C 1s peak at 284.8 eV as an internal standard. Raman spectra were measured on a LabRAM HR Evolution in the range from 700 to 3000 cm−1. The Ru contents of Ru@NC were determined by ICP-MS (ICAPQ).
2.4. Electrochemical measurements
The electrochemical experiments were performed on a CHI 660E instrument with a three-electrode configuration using glassy carbon (GC) electrode as working electrode, graphite rod as counter electrode and saturate calomel electrode (SCE) as reference electrode, respectively, at room temperature. For the preparation of working electrode, the GC electrode of 3 mm diameter was initially polished with a 0.05 mm alumina powder followed by washing with water and acetone. Then, 3.1 mg of catalyst and 100 μL of 5 wt% Nafion solution were dispersed in 0.9 mL methanol followed by 10 min sonication to obtain a homogeneous ink. Finally, 5 μ L of the catalyst ink was loaded onto the cleaned glassy carbon electrode and dried at room temperature, which led to a catalyst loading of 0.22 mg cm−2. The potentials of HER in all figures were regulated by reversible hydrogen electrode (RHE) using the equation: ERHE = ESCE + 0.24 + 0.059 pH. The electrochemical stability tests were carried out by performing 3000 CV cycles in the potential range of 0.1 to −0.2 V vs. RHE at a scan rate of 50 mV s−1. The electrochemical impedance spectroscopy (EIS) analyses were measured in the frequency range from 0.01 to 100
000 Hz and with an amplitude of 10 mV. Faradaic efficiency was calculated by the equation: Faradaic efficiency = 2nF/Q, where n is the amount of H2 collected by the water drainage method and calculated using the gas laws; Q is the amount of charge calculated from the corresponding i–t curve.
2.5. Determination of the active site density of Ru@NC(1
:
5)
The active site density was measured by the Cu under-potential deposition method (UPD), which means that the active sites responsible for the proton reduction, are same to those for the reduction of Cu2+ at an underpotential.32 The detailed procedure is as follows. Initially, the CVs of the prepared electrode containing NC or Ru@NC(1
:
5) were measured in 0.1 M H2SO4 as baseline. Then the electrodes were polarized at 0 V vs. RHE for 100 s in a solution containing 0.1 M H2SO4 and 20 mM CuSO4 to deposit Cu. After that, the CV measurements of the electrodes with deposited copper were performed in the same mixed solution (0.1 M H2SO4 and 20 mM CuSO4) from the initial 0 V vs. RHE to a point where all of the deposited copper had been oxidized at a scan rate of 0.01 V s−1. The observation of only one reduction peak or oxidation peak indicates the overlap of UPD Cu and overpotential deposition (OPD) Cu. Therefore, chloride ion was employed to separate the UPD and OPD peaks.28 The procedure of the CV measurements is similar except that the electrolyte contains 0.1 M H2SO4, 20 mM CuSO4 and 60 mM NaCl (Fig. S18, ESI†). Charges of oxidative copper stripping were corrected by subtracting the charge obtained for the same electrode in 0.1 M H2SO4. The active site density of the prepared electrode was calculated by the equation: active site density = QL/(2FA), where Q is amount of charges of copper stripping from the current–potential curve; L is Avogadro constant; F is Faraday‘s constant and A is the surface area of the working electrode. The active site density is calculated to be 8.26 × 1016 cm−2.
3. Results and discussion
3.1. Morphology and structure characterization
The morphology and detailed structures of Ru@NC catalysts were initially investigated by scanning electron microscopy (SEM) and transmission electron microscopy (TEM). The SEM image of Ru@NC(1
:
5) (Fig. 1a) shows that the catalyst consists of many small sheets. The corresponding energy dispersive spectroscopy (EDS) reveals the presence and homogeneous distribution of Ru, C and N elements and the Ru content was further detected to be 36% wt% by SEM-EDS (Fig. S4, ESI†), which is in good agreement with the value of 36.3% wt% obtained by ICP-MS. The Ru contents of Ru@NC(1
:
2, 1
:
10, 1
:
20) were also investigated by ICP-MS and were found to be 21.7% wt%, 19.2% wt% and 9.4% wt%, respectively (Table 1). The TEM image of Ru@NC(1
:
5) in Fig. 1b clearly shows that the Ru nanoparticles are homogeneously distributed on the carbon skeleton as dark spots with uniform size distribution (average diameter ca. 2.1 nm) (Fig. 1c). The particle size of Ru@NC(1
:
2, 1
:
10 and 1
:
20) were found to be the 4.2 nm, 3.8 nm and 4.5 nm, respectively (Fig. S1–S3, ESI†). Intriguingly, Ru@NC(1
:
5) has the most abundant Ru content but smallest particle size. The high resolution TEM (HRTEM) image of Ru@NC(1
:
5) (Fig. 1d) further reveals the embedding of Ru NPs on the carbon skeleton. The spacing of the crystal lattices 0.205 nm, 0.214 nm and 0.234 nm can be attributed to the (101), (002) and (100) planes of hexagonal Ru, respectively.
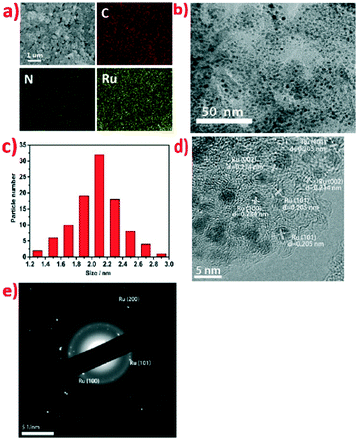 |
| Fig. 1 Morphology and physical characterization of Ru@NC(1 : 5). a) SEM image and corresponding EDS mapping images of C, N and Ru. b) TEM image. c) The corresponding particle size distribution of the Ru nanoparticles. d) HRTEM image. e) Selected-area electron diffraction (SAED) pattern. | |
Table 1 Ru content by ICP analysis and average particle diameter of Ru@NC catalysts
Catalysts |
Ru content/wt% |
Average diameter/nm |
Ru@NC(1 : 5) |
36.3 |
2.1 |
Ru@NC(1 : 2) |
21.7 |
4.2 |
Ru@NC(1 : 10) |
19.2 |
3.8 |
Ru@NC(1 : 20) |
9.4 |
4.5 |
The structures of the Ru@NC samples were further confirmed by X-ray powder diffraction (XRD). For Ru@NC(1
:
5), the indicated peaks in Fig. 2a can be attributed to hexagonal Ru (PCPDF no. 06-0663), while a small diffraction peak of graphite (002) plane was observed at 26.7°. The XRD patterns of Ru@NC(1
:
2, 1
:
10 and 1
:
20) suggest the same compositions (Fig. S8, ESI†). X-ray photoelectron spectroscopy (XPS) was also performed to identify the binding states and quantitative chemical compositions of Ru@NC. The XPS spectra of Ru@NC(1
:
5) (Fig. 2) and Ru@NC(1
:
2, 1
:
10 and 1
:
20) (Fig. S9–S11, ESI†) clearly indicate the presence of C, N, O and Ru elements. The occurrence of the O peak is presumably due to the physically adsorbed oxygen or edge oxygen of carbon matrix. For Ru@NC(1
:
5), the bonding configurations of N and Ru in the sample were further studied. The N 1s XPS spectrum (Fig. 2b) reveals three peaks at 398.4, 399.5 and 400.9 eV, which can be assigned to pyridinic N (N3), pyrrolic N, (N2) and graphitic N (N1), respectively. Furthermore, 90% N belongs to graphitic N which is reported to be able to activate the adjacent C atoms to increase the density of active sites.33 Although pyridinic N and pyrrolic N can coordinate to metal, they can also block active sites of metal NPs.26 Therefore, too many pyridinic N and pyrrolic N are not desirable. The binding energies of Ru 3d, Ru 3p3/2 and Ru 3p1/2 are observed at 280.5 eV, 462.1 and 484.1 eV, respectively, indicating the presence of metallic Ru0 and Run+ species (Fig. 2c and d). Because Ru 3d3/2 at 284.5 eV is overlapped with C 1s signal, the composition of Ru was only investigated by the Ru 3d5/2 XPS signal. The peak located at 280.3 eV is assigned to Ru0 and the rest is assigned to electron-deficient Run+ species.34 The Ru0/Run+ ratio was calculated from the integral peaks area of fitted Ru0 and Run+ species which are found to be 1.26, 1.31, 1.35 and 1.71 for Ru@NC(1
:
2, 1
:
5, 1
:
10, 1
:
20), respectively. Based on the overall Ru contents of ICP analysis, the Ru0 contents of Ru@NC(1
:
2, 1
:
5, 1
:
10, 1
:
20) are 12.1% wt, 20.6% wt, 11.0% wt and 5.9% wt, respectively. The carbon component of Ru@NC(1
:
5) was further investigated by Raman spectroscopy (Fig. S12, ESI†). A typical D-band at 1358 cm−1 and a typical G-band at 1600 cm−1 are observed with the intensity ratio (ID/IG) of 0.978, indicating a highly disordered and defective graphitic carbon component.35
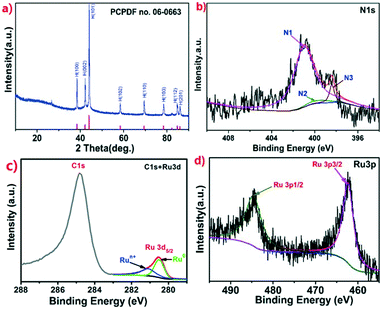 |
| Fig. 2 XRD and XPS analysis of Ru@NC(1 : 5). a) XRD pattern. b) High-resolution XPS spectrum of N 1s. c) High-resolution XPS spectrum of C 1s and Ru 3d. (d) High-resolution XPS spectrum of Ru 3p. | |
3.2. Electrocatalytic performance of Ru@NC for HER
The electrocatalytic activity for HER by Ru@NC was initially investigated in alkaline solution (1.0 M KOH). For comparison, catalysis by the commercial Pt/C (20 wt%) benchmark was also measured under the same conditions.36 The HER catalytic activity of Pt catalysts is excellent in alkaline electrolytes because the energy barrier of the Volmer step is so low that the rate of HER process is determined by a fast Tafel step.24,37 Similarly, Ru has been shown to have good water dissociation ability,38 which may also make the Volmer step of electrocatalytic HER facile in alkaline solutions.39 As shown by the polarization curves of Ru@NC catalysts without iR correction in Fig. 3a, all the catalysts exhibit distinctly positive electrocatalytic HER performance. Among the prepared catalysts, Ru@NC(1
:
5) shows the best activity, which is comparable to that of the Pt/C benchmark, probably owing to its smallest particle size. Although the other Ru@NC catalysts also contain a few of small Ru NPs, it is insufficient due to the much lower Ru content than that of Ru@NC(1
:
5) as aforementioned. Both Ru@NC(1
:
5) and Pt/C show very small onset overpotentials (η) with η0 = 0 mV. When the current density reaches 10 mA cm−2, the overpotential for Ru@NC(1
:
5) is only 29 mV, which is very close to that of the Pt/C benchmark (η10 = 27 mV). Furthermore, Tafel plots obtained from the corresponding polarization curves were used to examine the kinetics during the HER process. The Tafel slope for Ru@NC(1
:
5) is approximately 27 mV per decade (Fig. 3b), which is similar to that of Pt/C benchmark (25 mV per decade), suggesting that the HER process occurs via Volmer–Tafel mechanism (30 mV per decade) in which the combination of two chemisorbed hydrogen atoms is the rate-determining step. Overall, the above results clearly indicate that Ru@NC(1
:
5) is a highly efficient electrocatalyst for HER in alkaline media and is comparable to the other excellent Ru-based electrocatalysts (Table 2).19,21,23,26–30,39
 |
| Fig. 3 a) HER polarization curves of Ru@NC (1 : 2, 1 : 5, 1 :10, 1:20), NC and Pt/C in 1.0 M KOH at a scan rate of 5 mV s−1. b) Corresponding Tafel plots. c) HER polarization curves recorded before and after 3000 CV cycles for Ru@NC(1 : 5). d) Time-dependent current density curve for Ru@NC(1 : 5) in 0.5 M H2SO4 at a constant potential of −0.088 V vs. RHE for 30 h. | |
Table 2 Recently reported HER electrocatalysts in alkaline and acidic electrolytes
Catalyst |
Loading amount/mg cm−2 |
Electrolyte |
Current density/mA cm−2 |
Overpotential at corresponding j/mV |
Tafel slope/mV per decade |
References |
Ru@NC |
0.22 |
1 M KOH |
10 |
29 |
27 |
This work |
0.5 M H2SO4 |
62 |
40 |
R–TiO2:Ru |
0.255 |
1 M KOH |
10 |
150 |
95 |
19
|
Ru@C2N |
0.285 |
1 M KOH |
10 |
17 |
38 |
21
|
0.5 M H2SO4 |
22 |
30 |
RuP2@NPC |
1.0 |
1 M KOH |
10 |
52 |
69 |
23
|
0.5 M H2SO4 |
38 |
38 |
Ru@GnP |
0.25 |
1 M KOH |
10 |
22 |
28 |
26
|
0.5 M H2SO4 |
13 |
30 |
Ru@NC |
— |
1 M KOH |
10 |
26 |
36 |
27
|
Ru@CN |
0.247 |
1 M KOH |
10 |
32 |
53 |
28
|
0.5 M H2SO4 |
126 |
— |
Ru/MWCNTs |
0.28 |
1 M KOH |
10 |
39 |
28 |
29
|
Ru/C-300 |
— |
1 M KOH |
10 |
14 |
32.5 |
30
|
RuCo alloy |
0.275 |
1 M KOH |
10 |
28 |
31 |
39
|
Ru-CCS |
0.285 |
0.5 M H2SO4 |
10 |
27.3 |
33 |
40
|
Ni@Ni2P–Ru |
0.283 |
0.5 M H2SO4 |
10 |
51 |
35 |
41
|
Ru0/CeO2 |
0.197 |
0.5 M H2SO4 |
10 |
47 |
41 |
42
|
P–W2C@NC |
3.5 |
0.5 M H2SO4 |
10 |
89 |
53 |
44
|
The other important criterion of a good catalyst is the stability during the catalytic process. Therefore, we carried out a long-term durability test of Ru@NC(1
:
5) using cyclic voltammetry (CV) initially. The linear sweep voltammetry (LSV) curves were measured before and after 3000 CV cycles at a scan rate of 50 mV s−1 (Fig. 3c), and the LSV of 3000th cycle remains almost the same as that of the first cycle. Then, we further evaluated the durability of the Ru@NC(1
:
5) electrocatalyst by electrolysis at a fixed potential of −0.074 V vs. RHE. As shown in Fig. 3d, although the current density reaches up to ca. 32 mA cm−2 at this potential, it is maintained for 30 h with negligible decrease. These results reveal the excellent stability of Ru@NC(1
:
5) which is better than that of Pt/C (Fig. S15, ESI†). The TEM image of the catalyst after the durability test (Fig. S13, ESI†) shows that the morphology and structure are similar to that of the fresh catalyst. The EDS image reveals a 34.86 wt% Ru content (Fig. S14, ESI†), which is very close to 36 wt% of the fresh catalyst, suggesting little metal loss after the long term test, which may account for the excellent stability of Ru@NC(1
:
5). Furthermore, the amount of H2 generated in the cathodic compartment matches well with the theoretical value, suggesting nearly a 100% Faradaic efficiency for Ru@NC(1
:
5) (Fig. S16, ESI†). Due to the high content of Ru@NC(1
:
5), the mass activity at an overpotential of 50 mV was found to be only 0.32 A mgRu−1. To reach to the same mass activity, the overpotentials of Ru@NC(1
:
2, 1
:
10, 1
:
20) have to be 312 mV, 370 mV and 148 mV, respectively. Furthermore, the active site density of Ru@NC(1
:
5) was estimated to be as large as 8.26 × 1016 sites per cm2 by the Cu under-potential deposition method (UPD) (Fig. S18, ESI†). The high active site density of Ru@NC(1
:
5) is probably due to its high Ru content and its small particle size. Finally, the H2 turnover frequency (TOF = the number of H2 molecules generated per second per active site), was found to be a 0.96 s−1 at an overpotential of 50 mV.
In view of the fact that other types of electrolytic cells such as proton exchange membrane electrolytic cell may work in acidic electrolyte during water splitting, we also investigated the HER electrocatalytic performance of the Ru@NC catalysts in acidic media (0.5 M H2SO4). Similarly, Ru@NC(1
:
5) exhibits the best HER activity in acidic electrolytes as shown in Fig. 4a. Under acidic conditions, both Ru@NC(1
:
5) and Pt/C show very small onset overpotentials (η) with η0 = 17 mV and 8 mV, respectively. The overpotential η10 of Ru@NC(1
:
5) is 62 mV and the Tafel slope is approximately 40 mV per decade, slightly larger than that of the Pt/C benchmark (Fig. 4b). However, the LSV curve of Ru@NC(1
:
5) measured after 3000 CV cycles (Fig. 4c) is very similar to that of the first cycle suggesting the good stability of Ru@NC(1
:
5) in acidic media. The long-term durability test of Ru@NC(1
:
5) (Fig. 4d) shows negligible degradation for over 30 h under acidic conditions, superior to that of Pt/C (Fig. S15, ESI†). In addition, the Faradic efficiency is found to be almost 100% as well (Fig. S17, ESI†) and the H2 TOF is found to be a 0.64 s−1 at an overpotential of 50 mV. These results reveal that Ru@NC(1
:
5) possesses remarkable HER activity and stability in acidic media, which are close to some excellent examples of Ru-based catalysts and better than non-noble metal catalysts (Table 2).20,21,23,26,28,40–43 More importantly, it suggests Ru@NC(1
:
5) can function well in both alkaline and acidic conditions.
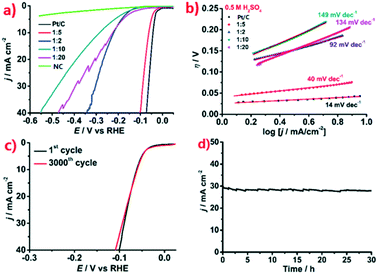 |
| Fig. 4 a) HER polarization curves of Ru@NC (1 : 2, 1 : 5, 1 : 10, 1 : 20), NC and Pt/C in 0.5 M H2SO4 at a scan rate of 5 mV s−1. b) Corresponding Tafel plots. c) HER polarization curves recorded before and after 3000 CV cycles for Ru@NC(1 : 5). d) Time-dependent current density curve for Ru@NC(1 : 5) in 0.5 M H2SO4 at a constant potential of −0.088 V vs. RHE for 30 h. | |
In order to get more insight into the high electrocatalytic activity of Ru@NC in HER, the electrochemically active surface area (ECSA) of Ru@NC(1
:
2, 1
:
5, 1
:
10 and 1
:
20) was evaluated by the double-layered capacitance (Cdl) at non-Faraday area using the cyclic voltammetry (CV) method (Fig. S19, ESI†). Obviously, Ru@NC(1
:
5) exhibits a larger Cdl of 25.3 mF cm−2 than Ru@NC(1
:
2) (13.7 mF cm−2), Ru@NC(1
:
10) (21.3 mF cm−2) and Ru@NC(1
:
20) (22.5 mF cm−2), indicating Ru@NC(1
:
5) benefits from the more exposed active sites. EIS measurements were also carried out to investigate the charge transfer between the interfaces of catalysts and electrolytes. As simulated with the equivalent circuits in Fig. 5, the obtained charge transfer resistances (Rct) of Ru@NC(1
:
5) by Nyquist plots are found to be 38 Ω and 37 Ω in acidic and alkaline solutions, respectively, which are even smaller than that of Ru@NC (43.7 Ω)21 and that of Ru-NGC (70 Ω),45 indicating that the charge-transfer during the HER process is fast and favourable. This high electrochemical conductivity may be owing to the synergistic effects between the Ru NPs and the carbon support that facilitates the electron transfer between the catalyst and electrolyte interfaces. On the other hand, the support material is known to play an important role in stabilizing the metal nanoparticles. Carbon with a high degree of graphitization is a very stable and robust kind of support.46 The strong interaction of Ru NPs with N-doped carbon can avoid either the detachment or the agglomeration of the Ru nanoparticles and thus improves the stability of the whole catalyst. Additionally, N2 adsorption–desorption analysis was carried out to investigate the texture structure of Ru@NC(1
:
5). As shown in Fig. 6, Ru@NC(1
:
5
) has a typical type II N2 adsorption isotherm revealing a large specific surface area (298.69 m2 g−1) and a pore volume of 0.2295 cm3 g−1 with an average pore diameter of 3.07 nm. The large specific surface area and the hierarchical pores can play a key role in ensuring the efficient dispersion of Ru NPs and contributing to the high active site density of the catalyst.
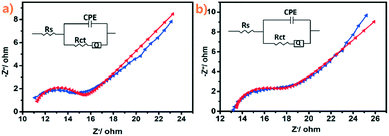 |
| Fig. 5 a) Measured (blue) and fitted (red) Nyquist plots of Ru@NC(1 : 5) in 0.5 M H2SO4 at a constant potential of −0.088 V vs. RHE. b) Measured (blue) and fitted (red) Nyquist plots of Ru@NC(1 : 5) in 1.0 M KOH at a constant potential of −0.074 V vs. RHE. | |
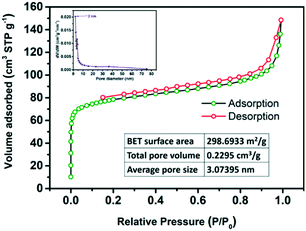 |
| Fig. 6 N2 adsorption/desorption isotherms of Ru@NC(1 : 5). Top inset: Corresponding pore size distribution. | |
Conclusions
In summary, we have successfully synthesized a series of HER electrocatalysts composed of Ru nanoparticles embedded in N-doped carbon by a simple process using Bu4N[Ru(N)Cl4] and Na4EDTA as precursors. By varying the molar ratio, Ru@NC(1
:
5) with particle size of ca. 2.1 nm diameter was found to exhibit the best HER activity in both acidic and alkaline media, which are comparable to the state-of-the-art Pt/C catalysts. Furthermore, this catalyst exhibits excellent stability during electrocatalytic HER in both strongly acidic and alkaline conditions. The experimental results suggest that the suitable particle size of Ru NPs, the high active site density and its synergistic effects with N-doped carbon support all contribute to the high electrocatalytic activity and stability.
Conflicts of interest
There are no conflicts to declare.
Acknowledgements
The work described in this paper was supported by the National Natural Science Foundation of China (Grant No. 21801058), the Anhui Provincial Natural Science Foundation (Grant No. 1808085QB28) and the Research Grants Council of Hong Kong (CityU 11301618). Partial financial support to M. R. from the Institut Universitaire de France (IUF) is gratefully acknowledged.
Notes and references
- N. S. Lewis and D. G. Nocera, Proc. Natl. Acad. Sci. U. S. A., 2006, 103, 15729–15735 CrossRef CAS PubMed.
- J. Turner, G. Sverdrup, M. K. Mann, P.-C. Maness, B. Kroposki, M. Ghirardi, R. J. Evans and D. Blake, Int. J. Energy Res., 2008, 32, 379–407 CrossRef CAS.
- G. W. Crabtree, M. S. Dresselhaus and M. V. Buchanan, Phys. Today, 2004, 57, 39–44 CrossRef CAS.
- M. S. Dresselhaus and I. L. Thomas, Nature, 2001, 414, 332–337 CrossRef CAS PubMed.
- J. A. Turner, Science, 2004, 305, 972 CrossRef CAS PubMed.
- E. J. Popczun, J. R. McKone, C. G. Read, A. J. Biacchi, A. M. Wiltrout, N. S. Lewis and R. E. Schaak, J. Am. Chem. Soc., 2013, 135, 9267–9270 CrossRef CAS PubMed.
- X. Bao, Y. Gong, Y. Chen, H. Zhang, Z. Wang, S. Mao, L. Xie, Z. Jiang and Y. Wang, J. Mater. Chem. A, 2019, 7, 11038–11043 RSC.
- X. Bao, J. Wang, X. Lian, H. Jin, S. Wang and Y. Wang, J. Mater. Chem. A, 2017, 5, 16249–16254 RSC.
-
A. Gross, S. Schnur, E. Santos and W. Schmickler, Catalysis in Electrochemistry:From Fundamental Aspects to Strategies for Fuel Cell Development, Wiley, 2011 Search PubMed.
- R. B. Gordon, M. Bertram and T. E. Graedel, Proc. Natl. Acad. Sci. U. S. A., 2006, 103, 1209–1214 CrossRef CAS PubMed.
- J. Shan, T. Ling, K. Davey, Y. Zheng and S.-Z. Qiao, Adv. Mater., 2019, 31, 1900510 CrossRef PubMed.
- T. Tian, L. Huang, L. H. Ai and J. Jiang, J. Mater. Chem. A, 2017, 5, 20985–20992 RSC.
- L. Liao, S. Wang, J. Xiao, X. Bian, Y. Zhang, M. D. Scanlon, X. Hu, Y. Tang, B. Liu and H. H. Girault, Energy Environ. Sci., 2014, 7, 387–392 RSC.
- X. Feng, H. Wang, X. Bo and L. Guo, ACS Appl. Mater. Interfaces, 2019, 11, 8018–8024 CrossRef CAS PubMed.
- P. Jiang, Q. Liu, Y. Liang, J. Tian, A. M. Asiri and X. Sun, Angew. Chem., Int. Ed., 2014, 53, 12855–12859 CrossRef CAS PubMed.
- J. Chen, H. Wang, Y. Gong and Y. Wang, J. Mater. Chem. A, 2019, 7, 11038–11043 RSC.
- Z.-F. Huang, J. Song, K. Li, M. Tahir, Y.-T. Wang, L. Pan, L. Wang, X. Zhang and J.-J. Zou, J. Am. Chem. Soc., 2016, 138, 1359–1365 CrossRef CAS PubMed.
- Y. Zheng, Y. Jiao, Y. Zhu, L. H. Li, Y. Han, Y. Chen, M. Jaroniec and S.-Z. Qiao, J. Am. Chem. Soc., 2016, 138, 16174–16181 CrossRef CAS PubMed.
- S. Nong, W. Dong, J. Yin, B. Dong, Y. Lu, X. Yuan, X. Wang, K. Bu, M. Chen, S. Jiang, L.-M. Liu, M. Sui and F. Huang, J. Am. Chem. Soc., 2018, 140, 5719–5727 CrossRef CAS PubMed.
- J. Yang, B. Chen, X. Liu, W. Liu, Z. Li, J. Dong, W. Chen, W. Yan, T. Yao, X. Duan, Y. Wu and Y. Li, Angew. Chem., Int. Ed., 2018, 57, 9495–9500 CrossRef CAS PubMed.
- J. Mahmood, F. Li, S.-M. Jung, M. S. Okyay, I. Ahmad, S.-J. Kim, N. Park, H. Y. Jeong and J.-B. Baek, Nat. Nanotechnol., 2017, 12, 441–446 CrossRef CAS PubMed.
- J. Xu, T. Liu, J. Li, B. Li, Y. Liu, B. Zhang, D. Xiong, I. Amorim, W. Li and L. Liu, Energy Environ. Sci., 2018, 11, 1819–1827 RSC.
- Z. Pu, I. S. Amiinu, Z. Kou, W. Li and S. Mu, Angew. Chem., Int. Ed., 2017, 56, 11559–11564 CrossRef CAS PubMed.
- J. Creus, J. De Tovar, N. Romero, J. Garcia-Anton, K. Philippot, R. Bofill and X. Sala, ChemSusChem, 2019, 12, 2493–2514 CrossRef CAS PubMed.
- J. Creus, S. Drouet, S. Surinach, P. Lecante, V. Colliere, R. Poteau, K. Philippot, J. Garcia-Anton and X. Sala, ACS Catal., 2018, 8, 11094–11102 CrossRef CAS.
- F. Li, G.-F. Han, H.-J. Noh, I. Ahmad, I.-Y. Jeon and J.-B. Baek, Adv. Mater., 2018, 1803676 CrossRef PubMed.
- Z.-L. Wang, K. Sun, J. Henzie, X. Hao, C. Li, T. Takei, Y.-M. Kang and Y. Yamauchi, Angew. Chem., Int. Ed., 2018, 57, 5848–5852 CrossRef CAS PubMed.
- J. Wang, Z. Wei, S. Mao, H. Li and Y. Wang, Energy Environ. Sci., 2018, 11, 800–806 RSC.
- W. Gou, J. Li, W. Gao, Z. Xia, S. Zhang and Y. Ma, ChemCatChem, 2019, 11, 1970–1976 CrossRef CAS.
- C. Xu, M. Ming, Q. Wang, C. Yang, G. Fan, Y. Wang, D. Gao, J. Bi and Y. Zhang, J. Mater. Chem. A, 2018, 6, 14380–14386 RSC.
- W. L. Man, T. M. Tang, T. W. Wong, T. C. Lau, S. M. Peng and W. T. Wong, J. Am. Chem. Soc., 2004, 126, 478–479 CrossRef CAS PubMed.
- C. L. Green and A. Kucernak, J. Phys. Chem. B, 2002, 106, 1036–1047 CrossRef CAS.
- Y. Zheng, Y. Jiao, L. H. Li, T. Xing, Y. Chen, M. Jaroniec and S. Z. Qiao, ACS Nano, 2014, 8, 5290–5296 CrossRef CAS.
- J. Ftouni, A. Munoz-Murillo, A. Goryachev, J. P. Hofmann, E. J. M. Hensen, L. Lu, C. J. Kiely, P. C. A. Bruijnincx and B. M. Weckhuysen, ACS Catal., 2016, 6, 5462–5472 CrossRef CAS.
- X.-H. Li, S. Kurasch, U. Kaiser and M. Antonietti, Angew. Chem., Int. Ed., 2012, 51, 9689–9692 CrossRef CAS PubMed.
- R. Subbaraman, D. Tripkovic, D. Strmcnik, K.-C. Chang, M. Uchimura, A. P. Paulikas, V. Stamenkovic and N. M. Markovic, Science, 2011, 334, 1256–1260 CrossRef CAS.
- J. L. C. Fajin, M. N. D. S. Cordeiro and J. R. B. Gomes, J. Phys. Chem. A, 2014, 118, 5832–5840 CrossRef CAS.
- Y. Zheng, Y. Jiao, A. Vasileff and S.-Z. Qiao, Angew. Chem., Int. Ed., 2018, 57, 7568–7579 CrossRef CAS PubMed.
- J. Su, Y. Yang, G. Xia, J. Chen, P. Jiang and Q. Chen, Nat. Commun., 2017, 8, 16029–16038 CrossRef CAS PubMed.
- D. Luo, B. Zhou, Z. Li, X. Qin, Y. Wen, D. Shi, Q. Lu, M. Yang, H. Zhou and Y. Liu, J. Mater. Chem. A, 2018, 6, 2311–2317 RSC.
- Y. Liu, S. Liu, Y. Wang, Q. Zhang, L. Gu, S. Zhao, D. Xu, Y. Li, J. Bao and Z. Dai, J. Am. Chem. Soc., 2018, 140, 2731–2734 CrossRef CAS PubMed.
- E. Demir, S. Akbayrak, A. M. Onal and S. Ozkar, ACS Appl. Mater. Interfaces, 2018, 10, 6299–6308 CrossRef CAS PubMed.
- J. Yu, Q. He, G. Yang, W. Zhou, Z. Shao and M. Ni, ACS Catal., 2019, 9, 9973–10011 CrossRef CAS.
- G. Yan, C. Wu, H. Tan, X. Feng, L. Yan, H. Zang and Y. Li, J. Mater. Chem. A, 2017, 5, 765–772 RSC.
- Q. Song, X. Qiao, L. Liu, Z. Xue, C. Huang and T. Wang, Chem. Commun., 2019, 55, 965–968 RSC.
- L. Castanheira, W. O. Silva, F. H. B. Lima, A. Crisci, L. Dubau and F. Maillard, ACS Catal., 2015, 5, 2184–2194 CrossRef CAS.
Footnote |
† Electronic supplementary information (ESI) available. See DOI: 10.1039/c9cy02552a |
|
This journal is © The Royal Society of Chemistry 2020 |
Click here to see how this site uses Cookies. View our privacy policy here.