DOI:
10.1039/D0CS00179A
(Review Article)
Chem. Soc. Rev., 2020,
49, 6329-6363
Biomass-derived chemical substitutes for bisphenol A: recent advancements in catalytic synthesis†
Received
28th February 2020
First published on 4th August 2020
Abstract
Bisphenol A is an oil-derived, large market volume chemical with a wide spectrum of applications in plastics, adhesives and thermal papers. However, bisphenol A is not considered safe due to its endocrine disrupting properties and reproductive toxicity. Several functional substitutes of bisphenol A have been proposed in the literature, produced from plant biomass. Unless otherwise specified, the present review covers the most significant contributions that appeared in the time span January 2015–August 2019, describing the sustainable catalytic synthesis of rigid diols from biomass derivatives. The focus is thereupon on heterogeneous catalysis, use of green solvents and mild conditions, cascade processes in one-pot, and continuous flow setups. More than 500 up-to-date references describe the various substitutes proposed and the catalytic methods for their manufacture, broken down according to the main biomass types from which they originate.
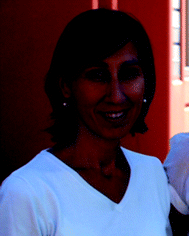
Francesca Liguori
| Francesca Liguori got her PhD in Chemistry in 2005 from the University of Florence. After several collaborations as a grant-holder at the Consiglio Nazionale delle Ricerche (CNR, Italy), in 2011 she became a Permanent Researcher at the Istituto di Chimica dei Composti Organo Metallici – CNR. Currently her research interests mainly concern green chemistry, flow chemistry, catalysis for the synthesis of value-added chemicals from renewable sources and the synthesis of materials as supports for catalysts. She was a co-author of several peer reviewed papers on ISI journals and an investigator in research and industrial projects in the field of heterogeneous catalysis. |
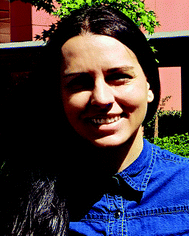
Carmen Moreno-Marrodan
| Carmen Moreno-Marrodan studied Chemistry in the University of La Rioja, Spain. In 2008 she won a Leonardo da Vinci European Programme Fellowship in the chemical industry in Cork, Ireland. In 2009 she was awarded a Marie Sklodowska Curie Fellowship and joined the ITN Nano-HOST in the Institute of Chemistry of OrganoMetallic Compounds (ICCOM), Florence, Italy. In 2013 she received her PhD in Chemistry from the University of Florence. Currently, she is a Permanent Researcher in the Italian National Research Council (ICCOM) in Florence. Her research interests focus on biomass valorisation through the development of heterogeneous catalysis and flow technologies. |
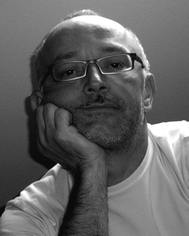
Pierluigi Barbaro
| Pierluigi Barbaro was born in 1962 in Firenze. He obtained his PhD in Chemistry from the University of Firenze, then he spent a two-year post-doctorate fellowship at ETH Zurich. Presently he is the Researcher Director at the Istituto di Chimica dei Composti Organo Metallici, Consiglio Nazionale delle Ricerche (Italy). He was a member of the Network of Excellence IDECAT and a Coordinator of the Initial Training Network NANO-HOST (European Commission VII FP). He is a member of the Board of Directors of the European Research Institute of Catalysis, Brussels. His activities are in the fields of green chemistry, catalysis and flow processes for biomass valorisation. |
1. Introduction
There is no doubt that plastic materials are central to our society. Plastics are widespread in everyday products that we use for housing, personal care, packaging, clothing, transport, adhesives and electronics.1 There is equally no doubt that, just because of their versatility and ubiquity, today plastics are also a source of concern. Multiple issues relate to plastics.2,3
Plastics are usually synthetic polymers recalcitrant to biodegradation. They accumulate in the environment if discarded, thus representing important pollutants.4,5 Plastics may contain or release toxic components or volatile organic compounds dangerous to human health and the habitat.6,7 Most plastics are manufactured from oil, which contributes to the carbon footprint of the process industry and to the depletion of exhaustible raw materials.8,9 Not all plastics can be recovered and reused, or have significant recycling economic value; therefore, they are liable to end up in landfills or the environment.10,11
To overcome, at least in part, these problems, considerable efforts have been devoted in recent years to the development of compostable and bio-based polymers,12,13 and to the synthesis of alternative monomers.14,15 Transnational strategies have been launched to this aim,16,17 including the United Nation Sustainable Development Goals (SDG 13 Climate Action, SDG 12 Responsible Consumption and Production),18 the European Strategy for Plastics in a Circular Economy,19 and the United States Sustainable Materials Management Program Strategic Plan.20 Research agendas21,22 and position papers23,24 have been made available from European Technology Platforms and Consortia.25
Bisphenol A (2,2-bis(4-hydroxyphenyl)propane, BPA) is a component of several plastic materials, from which it may leach under certain circumstances. Unfortunately, BPA is considered a hazardous compound.26 A number of chemicals have thus been proposed as substitutes for BPA, some of them obtainable from plant biomass derivatives.
The present manuscript reviews the most significant contributions that appeared in the last five years’ literature, describing the catalytic synthesis of functional monomer substitutes of BPA, which are manufactured from biomass or from biomass-derived compounds. The synthetic processes are illustrated according to the raw materials used and the corresponding value chains. The topic was partially covered by previous surveys,27,28 particularly in relation to the synthesis of epoxy monomers.29,30 The aim of the present review is to provide the reader with the basic concepts behind chemical substitution, and with an analysis of the advancements proposed for the sustainable synthesis of BPA replacements from renewable feedstock. The focus is thereupon on heterogeneous catalysts enabling multistep reaction sequences in one-pot, use of green solvents, mild conditions and continuous flow setups. Strategies, challenges and prospects in the field are discussed. No functional substitutes other than diols are considered (e.g. epoxides, amines), neither petroleum-derived chemicals, nor biocatalytic processes will be detailed.31,32
2. BPA
2.1. Properties and uses
BPA (CAS No. 80-05-7) is a diphenylmethane derivative bearing two hydroxy groups in the para positions. The chemical structure of BPA is reported in Scheme 1. BPA is industrially produced by the acid-catalysed condensation reaction of phenol with acetone, using an excess of phenol.33 All by-products of the BPA synthesis, including unreacted phenol, are toxic.34,35 An environmental profile associated with the production of BPA as a monomer is available from plastic manufacturers.36 Lab-scale yields up to 96% were reported for this process.37 A purity greater than 98% is required for most uses of BPA.38,39
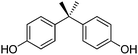 |
| Scheme 1 Structure of bisphenol A (BPA). | |
BPA is largely incorporated as a monomer in a variety of polymers, namely polycarbonates, epoxy resins, polyethers, polysulphones and polyesters.40 Representative structures are shown in Scheme 2. End-user applications of polycarbonates include food and beverage containers, optical lenses, electronic and household appliances, safety helmets, telephones, automotive components, construction parts, medical equipment and toys. Epoxy resins are primarily used for the production of consumer and industrial coatings, paints and adhesives.
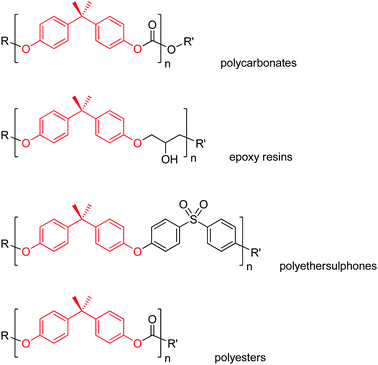 |
| Scheme 2 Representative structures of some BPA-based polymers. | |
The extensive use of BPA justifies for a global BPA market above 6 million tons in 2017, with an expected compound annual growth rate of ca. 6% over the period 2019–2024.41,42 This makes BPA one of the highest volume chemicals produced worldwide. To date, the manufacture of polycarbonates and epoxies accounts for about 68% and 30% of the production capacity of BPA, respectively.43 The remaining market is shared among other polymers and the components of antioxidants, flame retardants, colour agents and thermal papers. In 2018, the amount of BPA used for thermal papers in the EU market was around 3 ktons.44
In addition to its double functionality and intrinsic stability,45,46 one other reason for the massive use of BPA in polymer manufacture is its rigid structure. The limited degrees of freedom associated with the BPA molecule are believed to endow the resulting polymers with excellent thermal and mechanical properties, including stiffness, toughness and hardness.47,48 Indeed, BPA-based plastics usually feature high flexural strength,49 glassy moduli, glass transition temperatures (Tg),50,51 tensile moduli,52,53 and tensile and impact strength.54,55 A detailed description of the synthesis and properties of the resulting polymers is outside the scope of the present review. The reader may refer to the above cited specialised reviews for this purpose.
BPA's physico-chemical properties, potentially relevant to toxicological and exposure aspects, are its low solubility in water (300 mg L−1)56 and volatility (5.3 × 10−6 Pa),57 and its significant octanol/water partition coefficient (log
Kow 3.42).58 These parameters result in a high tendency for BPA sorption to soil and sediments, which ultimately controls the fate of BPA in aquatic and terrestrial environments.59,60
BPA-derived resins and polycarbonates are sensitive to hydrolysis61,62 and temperature.63,64 Together with the presence of monomer residues, due to incomplete polymerization,65,66 or the incorporation of BPA as an additive,67 this may cause the release of BPA from BPA-containing materials and related plasticware, including bottles,68,69 dental sealants,70,71 textiles,72 papers,73,74 food packaging75,76 and cans.77,78 Consequently, significant levels of BPA are detected in air, dust, wastewater, drinking water, food,79,80 and human fluids and tissues,81,82 particularly in infants.83
2.2. Health and environmental effects
A plethora of studies have been carried out on the diverse effects of BPA on human health. Several reviews are available in the literature.84,85 Exposure to BPA occurs mainly through ingestion, although inhalation and dermal absorption may contribute significantly.86,87 BPA is recognised as an endocrine disrupting and estrogenic chemical.88,89 Data have indicated BPA as potentially responsible for a variety of health problems, such as obesity,90,91 diabetes,92,93 carcinogenesis,94,95 neurobehavioral and neurological disorders (autism, anxiety, cognitive deficits, hyperactivity),96,97 and reproductive98,99 and developmental impairment.100,101
The risk associated with BPA exposure was assessed in the aquatic, sediment and terrestrial compartments,102,103 suggesting significant toxic potential for vertebrates, invertebrates and algae.104,105 The need for further information and testing was highlighted, however.106,107
On the above basis, several regulations have therefore been enforced worldwide on the production and use of BPA.108
Use of BPA in the manufacturing of baby bottles has been banned in Europe since 2011.109 The marketing of any packaging, container and utensil containing BPA, intended to come into direct contact with food, has been prohibited in France since 2015.110 In 2017, following the European Union Registration, Evaluation, Authorisation and Restriction of Chemicals (REACH) regulation,111 the European Chemical Agency (ECHA) placed BPA on the Candidate List of Substances of Very High Concern (SVHC),112 classifying it as toxic for reproduction (Article 57c) and endocrine disrupting (Article 57f).113 In December 2016, the EU published a new regulation stating that BPA “shall not be placed on the market in thermal paper in a concentration equal to or greater than 0.02% by weight after 2 January 2020”.114 In July 2019, the General Court of the European Union confirmed “the inclusion of Bisphenol A as a substance of very high concern on account of its properties as a substance toxic for reproduction”.115
BPA is on the List of Chemicals Known to the State of California to Cause Cancer or Reproductive Toxicity (Proposition 65), because it is considered harmful to the female reproductive system.116 Since July 2013, the manufacture, sale or distribution of bottles or cups that contain BPA above 0.1 ppb has been prohibited in California, if they are designed as containers for food and beverages used by children.117 Other twelve US states and the District of Columbia have enacted law restrictions on BPA since 2009.118 According to the U.S. Food and Drug Administration, the use of BPA-based polycarbonates and epoxy resins in baby bottles, sippy cups and infant formula packaging has been abandoned since 2012.119,120 In 2014, the U.S. Environmental Protection Agency released a report on BPA alternatives in thermal paper, for stakeholders interested in chemical substitution.121
Starting from 2010, baby bottles containing BPA polycarbonate have no longer been manufactured advertised, sold and imported in Canada.122
3. Chemical substitutes of BPA from biomass
3.1. Principles of chemical substitution
The increasingly restrictive rules concerning the use of chemicals of risk to human health and the environment have become a major driver for their substitution in both research and industry.123,124
Chemical substitution is “the replacement or reduction of hazardous substances in products or processes by less hazardous or non-hazardous substances, or by achieving an equivalent functionality via technological or organisational measures”.125,126 Therefore, chemical substitution is considered as a primary prevention strategy, rather than a mere reduction of the risk associated with a hazard.127,128 Research in chemical substitution is “solution-oriented”: the target is not the replacement with a specific compound (e.g. drop-in chemicals),129,130 but the functions that the chemicals may provide.131,132 Whenever structure–activity data are available, “safety-by-design” chemicals may be proposed for substitution.133,134 In case that large volume chemicals are targeted for substitution, economic assessment attributes, other than hazard and functional performance, shall be considered for optimal replacement: capital investment, costs, technical feasibility, environmental impact of manufacture, life-cycle of chemicals.135,136 Substitution using non-fossil feedstock is certainly a preferred option and a priority from a circular economy perspective.137,138 Support and assessment tools are available online for chemical substitution.139,140
3.2. Proposed substitutes for BPA
A number of “bisphenol analogues” have been produced to replace BPA in various applications.141,142 The largest market shares are held by BPF (4,4′-methylenediphenol), BPS (bis(4-hydroxyphenyl)sulfone) and BPAF (2,2-bis(4-hydroxyphenyl)hexafluoropropane), whose structures are shown in Scheme 3. However, they are neither considered safer than BPA,143,144 nor synthesized from renewable sources.145,146 Therefore, they will not be discussed further in the present review. Reports and databases are available on the viability of these monomers as BPA substitutes.147,148
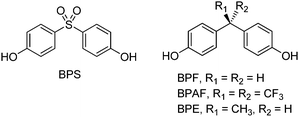 |
| Scheme 3 Structures of BPF, BPS, BPE and BPAF. | |
Lignocellulose, together with cellulose, hemicellulose and lignin, accounts for around 80% (non-edible portion) of plant biomass (Fig. 1).149,150 Terpenes, terpenoids and triglycerides account for ca. 10%.151 These matters can be used as alternative carbon sources for the manufacture of most materials currently obtained from oil. In contrast to biofuels, the estimated amount of feedstock available from biomass is enough to produce high value-added chemicals that we need in everyday life,152,153 including solvents, pharmaceutical building blocks, agrochemicals, food additives, hygiene and cosmetic components, and monomers for bio-plastics.154,155 A limited number of functional molecules, called platform chemicals,156 can be produced through biomass conversion and usable as bulk chemicals in this direction.157,158 Examples include 5-hydroxymethylfurfural (HMF), sorbitol, furfural, and xylitol.159,160 The upgrade of these intermediates usually requires multi-step sequences of dehydration, isomerisation, esterification, oxidation or hydrogenation reactions that, for their economic feasibility, each should be performed with high selectivity and a safe environmental profile.161,162 In practice, the best way to achieve this goal is through catalysis: chemical and biocatalysis each have their role to play.163,164 Excellent reviews are available covering most aspects of catalytic valorisation of lignocellulosic biomass.165,166 From an industrial point of view, heterogeneous catalysts are preferred due to the easier catalyst/product separation, catalyst reuse and integration in existing reactor equipment.167,168 This, however, often requires the immobilisation of tailored catalysts onto appropriate insoluble support materials.169,170 On the other hand, multi-step processes are most efficiently achieved in one-pot by using truly bifunctional catalysts, i.e. a combination of well-defined supported acid and metal sites acting under the same reaction conditions, notably metal catalysts immobilized onto solid acids.171,172 The strategy has been successfully applied to the upgrade of bio-derived platform molecules.173,174 A step forward in sustainability and process intensification is provided by performing catalysis under continuous flow conditions, because of the considerable advantages compared to conventional batch operations: increased safety and reactor volume productivity, simpler downstream processing, smaller hold-up volumes, improved heat transfer and process control.175,176 Continuous refreshes of the catalyst surface may also reduce active site inhibition due to the adsorption of (by)products.177 Facilities integrating “biomass conversion processes and equipment to produce fuels, power, heat and value-added chemicals from biomass” are called biorefineries.178,179 A 4th generation of biorefineries, focusing on economically feasible technologies, production of unconventional platforms and use of advanced catalysts, is currently under development.180,181
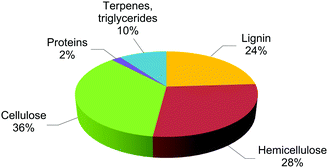 |
| Fig. 1 Composition of plant biomass. | |
Several studies have been devoted to the catalytic synthesis of alternative monomers for plastics from renewable resources, particularly from lignocellulose.182,183 The finished polymers are often referred to as “sustainable polymers” or “renewable polymers”.184,185 Metrics to evaluate the sustainability of bio-derived polymers are available.186,187 Functional substitutes of BPA from biomass and its derivatives have also been proposed, mainly from cellulose and lignin and a few from terpenoids and hemicellulose.188 Schematic representations of the main BPA substitutes from biomass found in the literature are reported in Fig. 2.
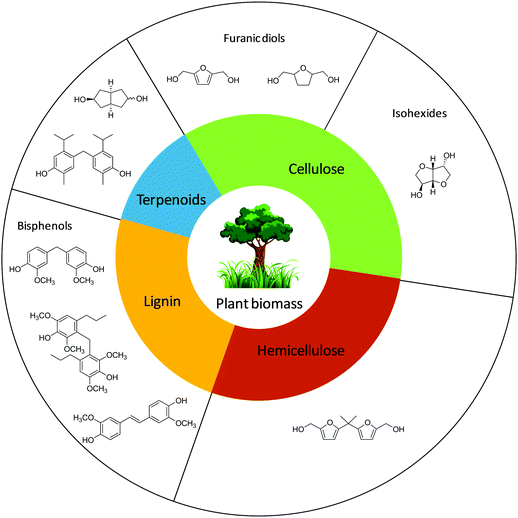 |
| Fig. 2 Sketches of the main BPA substitute types recently proposed from biomass. | |
Cellulose is a linear-chain homopolysaccharide consisting of a well-defined sequence of D-glucose units linked by β(1,4) glycosidic bonds.189 Cellulose is the main component of the cell walls of green plants and many algae, and the most abundant organic polymer in nature.190 Unlike cellulose, lignin is a very complex, cross-linked polymer reducible to three main methoxylated 4-hydroxycinnamyl alcohol building blocks, known as monolignols (Scheme 4).191 They form a variety of structural and functional motifs, whose composition depends on the plant from which lignin is extracted.192,193 Lignin is considered a waste material from the paper and forestry industries, with a production of around 100 million tons per year.194,195
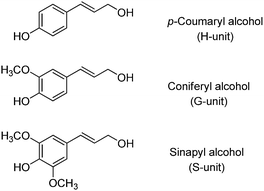 |
| Scheme 4 Structures of H, G and S monolignol subunits of lignin. | |
It is generally agreed that the proposed monomer BPA substitutes from biomass shall be bifunctional and have a rigid structure, either due to a ring scaffold or due to the inhibition of rotational flexibility.196,197 The present paper reviews the substitutes based on rigid diol units which are obtained by catalytic methods. No linear diols will therefore be considered.198 The syntheses of these compounds will be reviewed in the following sections, according to the main biomass feeds from which they originate: cellulose, lignin or others.
4. Substitutes from the cellulose depolymerisation chain
Cellulose is a source of C6 carbohydrate platform molecules. Upon full acid-catalysed hydrolytic depolymerisation, cellulose affords glucose,199,200 from which two important platform molecules can be obtained via catalysis: sorbitol201 and HMF.202,203 These materials are the starting materials used in industry to produce a variety of useful chemicals, including isosorbide and furanic diols, also through catalytic methods.204,205 The overall value chain is outlined in Scheme 5. Isosorbide, as well as isohexides in general, and bis(hydroxymethyl)furans have been investigated as BPA replacements. Routes to these compounds from glucose (or cellulose) involve sequences of two or more acid-catalysed dehydration (hydrolysis) and metal-catalysed reduction steps. Use of upstream substrates, other than sorbitol or HMF, is clearly more attractive owing to the intensification,206 reduced complexity and cost of the overall process.207 However, its drawbacks are the high pressures and temperatures usually needed, and the significant amounts of mineral acids reported to overcome the recalcitrance of glucose, cellulose and the non-edible biomass in general.208 Process selectivity under such harsh conditions is often moderate, leading to variable quantities of (humin) by-products, partly because of the suboptimal catalysis used, whose stability may be an issue as well.209
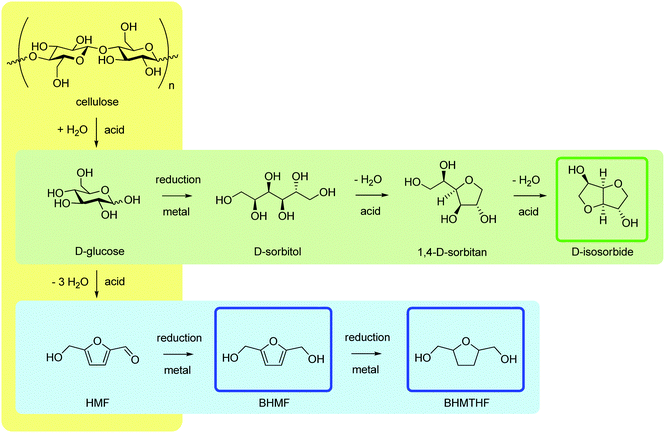 |
| Scheme 5 Simplified reaction pathways for the catalytic conversion chain of cellulose to isosorbide and furanic diols. | |
Therefore, improved catalysts and processes shall be developed, in order to convert efficiently and selectively original cellulose-derived feeds to the desired bio-based building blocks.
4.1. Isohexides
Isohexides are chiral V-shaped diols consisting of two fused tetrahydrofuran units, with secondary hydroxyl groups in endo/endo (isomannide), exo/endo (isosorbide) and exo/exo (isoidide) configurations (Scheme 6). Their very low toxicity (Table S1, ESI†), rigid bicyclic structure, acceptable chemical stability, different stereochemistries and potential for selective functionalizations make them very attractive for several applications, including synthesis of pharmaceutical intermediates (e.g. isosorbide dinitrate);210 synthesis of fuel additives, surfactants, chiral auxiliaries;211,212 and bio-based plastics.183 The preparation and properties of polymers (polycarbonates, polyesters or polyamides) based on isohexides,213 particularly isosorbide,214,215 scaffolds have been reviewed earlier. The exo/exo configuration of the least sterically hindered isoidide results in polymers with the highest molecular weights, whereas the endo/endo configuration of isomannide provides polymers with higher thermal stability, compared to the other isomers. Importantly, biodegradable polymers based on isohexide units have been developed.216,217
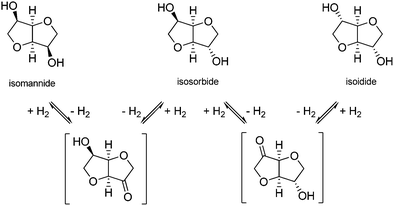 |
| Scheme 6 Structures and epimerization of isosorbide, isomannide and isoidide. | |
Synthetic methods and applications of isomannide and isoidide are yet limited. Due to the poor availability of their sugar alcohol precursors (L-iditol for isoidide, D-mannitol for isomannide), and the low selectivity of the associated dehydration processes, they are still produced on a bench scale.182,218 Recently, an unprecedented 63% yield of isomannide from mannitol was achieved over solid acid Hβ zeolite catalysts having a Si/Al ratio of 75.219 The efficiency of the catalysts was attributed to the structural properties of the zeolite and to the balanced acid loading and hydrophobicity of Hβ-75. Based on density functional theory calculations, it was suggested that a challenging selective 1,4-dehydration path can be achieved, thanks to the inhibition of a bulkier 2,5-dehydation transition state within the zeolite micropores (Scheme 7). The catalyst could be reused with a slight activity decrease (ca. 10%) over four cycles. The synthesis of isomannide in 92% yield was also reported in the homogeneous phase, using the basic catalyst 1,8-diazabicyclo[5.4.0]undec-7-ene (DBU) and dimethyl carbonate (DMC), via a mechanism analogous to that described below for isosorbide (Scheme 10).220 Isomannide could be isolated after evaporation of the excess of DMC and methanol solvent, without a chance of catalyst reuse, however.
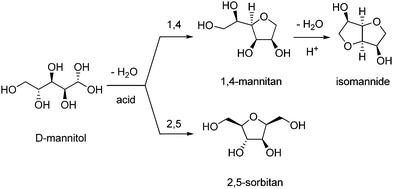 |
| Scheme 7 Pathways of acid-catalyzed dehydration of mannitol to isomannide. | |
The most efficient strategy for the synthesis of isoidide is the catalytic epimerization of the other isohexides. After the first approaches of Fletcher and Wright,221,222 a detailed study was reported in 2013 by Le Nôtre, wherein the process was achieved in water over heterogeneous Ru@C catalysts and in the presence of H2 (40 bar, 220 °C).223,224 It was demonstrated that epimerization occurs through a dehydrogenation–hydrogenation path (Scheme 6). The catalyst could be reused once with a moderate loss of activity (20%), whereas >99% pure starting isosorbide was required. More recently, epimerization of an “impure isosorbide” feed (i.e. an isosorbide-rich mixture containing up to 10% of sorbitans) was conveniently achieved over Ni RANEY® catalysts at 230 °C, using various hydrogen flows.225 99% pure isoidide was obtained after chromatographic separation and crystallization. The advantages of the methods are the reduction of costs and isosorbide loss, usually caused by prior heat-sensitive isosorbide distillation.
Due to the large availability of bio-based precursors (sorbitol, glucose or cellulose), isosorbide is by far the most important of isohexides. The synthesis182,212 and applications183,215 of isosorbide have been reviewed up to 2016. Hence, only the most recent achievements in catalytic synthesis will be described herein. Table 1 summarises the most significant reaction parameters (solvent, temperature, H2 pressure) for the catalytic processes described in the present review which lead to isohexides from biomass-derived sources. Catalyst productivity to the products specified, as mmolprod gcat−1 h−1, is also reported aimed at providing a significant and quantitative estimate of catalyst efficiency.
Table 1 Summary of recent catalytic systems for proposed BPA monomeric replacements from isohexidesa
Catalyst |
Biomass-derived substrate |
Product |
Reaction conditions |
Conv.c (%) |
Sel.d (%) |
Prod.e (mmolprod gcat−1 h−1) |
Ref. |
Solventb (M) |
T (°C) |
H2 (bar) |
See Section 4.1 for labelling and abbreviations.
Reaction solvent, substrate concentration (M) in brackets.
Substrate conversion.
Selectivity to the product indicated.
Catalyst productivity to the product indicated.
Nafion–silica composite.
Sorbitol 70 wt%.
Two-stage process.
Mechanical mixture.
Calculated with respect to Ru@C.
|
Hβ-75 |
Mannitol |
Isomannide |
Free |
140 |
— |
99 |
65 |
4.3 |
219
|
DBU |
Mannitol |
Isomannide |
Methanol (2.7) |
Reflux |
— |
100 |
92 |
5.1 |
220
|
DBU |
Mannitol |
Isosorbide |
Methanol (2.5) |
Reflux |
— |
100 |
98 |
2.5 |
220
|
Ru@C |
Isosorbide |
Isoidide |
H2O (6.9) |
220 |
— |
100 |
51 |
22.3 |
224
|
Amberlyst-36 |
Sorbitol |
Isosorbide |
H2O (13.5) |
150 |
— |
100 |
69 |
12.7 |
232
|
Hβ-75 |
Sorbitol |
Isosorbide |
H2O (0.5) |
200 |
— |
100 |
77 |
n.a. |
235
|
Hβ-75 |
Sorbitol |
Isosorbide |
Free |
127 |
— |
100 |
76 |
7.6 |
236
|
Glu-Fe3O4-SO3H |
Sorbitol |
Isosorbide |
Free |
140 |
— |
100 |
94 |
25.8 |
237
|
SAC-13f |
Sorbitol |
Isosorbide |
Free |
130 |
— |
100 |
83 |
0.6 |
239
|
Dowex-50WX2 |
Sorbitol |
Isosorbide |
Free |
130 |
— |
100 |
78 |
1.5 |
239
|
Amberlyst-15 |
Sorbitol |
Isosorbide |
Free |
130 |
— |
100 |
67 |
1.3 |
239
|
Deloxan |
Sorbitol |
Isosorbide |
Free |
130 |
— |
100 |
68 |
2.3 |
239
|
SHTC |
Sorbitol |
Isosorbide |
Free |
130 |
— |
100 |
80 |
2.7 |
239
|
SiO2-SO3H |
Sorbitol |
Isosorbide |
Free |
120 |
— |
100 |
84 |
23.1 |
241
|
SBA15-PrSO3H |
Sorbitol |
Isosorbide |
Free |
150 |
— |
90 |
78 |
3.2 |
242
|
SBA15-ArSO3H |
Sorbitol |
Isosorbide |
Free |
170 |
— |
100 |
71 |
46.7 |
245
|
B phosphate |
Sorbitol |
Isosorbide |
H2Og |
250 |
— |
99 |
80 |
n.a. |
248
|
Zr phosphate |
Sorbitol |
Isosorbide |
Free |
210 |
— |
100 |
73 |
20.0 |
249
|
MST-450 |
Sorbitol |
Isosorbide |
Free |
180 |
— |
100 |
70 |
96.1 |
250
|
BIL-5 |
Sorbitol |
Isosorbide |
Free |
130 |
— |
99 |
85 |
95.6 |
251
|
Bi(OTs)3 |
Sorbitol |
Isosorbide |
Free |
145 |
— |
100 |
67 |
23.1 |
257
|
Hβ-20 |
Sorbitol |
Isosorbide |
MIBK (0.4) |
170 |
— |
100 |
93 |
25.1 |
258
|
CH3ONa |
Sorbitol |
Isosorbide |
Methanol |
Reflux |
— |
100 |
98 |
0.6 |
260
|
Ru@Dowex |
Glucose |
Isosorbide |
H2O (0.1) |
190 |
30 |
100 |
85 |
0.1 |
261
|
RuOx@C-SO3H |
Cellulose MCC |
Isosorbide |
H2O (0.04) |
170 + 200h |
40 |
100 |
56 |
2.1 |
266
|
Ru@C + Amberlyst-70i |
Milled cellulose |
Isosorbide |
H2O (0.05) |
190 |
50 |
78 |
72 |
0.35j |
267
|
Ru@C + Amberlyst-70i |
Cellulose |
Isosorbide |
H2O (0.002) |
190 |
50 |
38 |
67 |
0.01j |
268
|
Ru/Fe3O4@PMO-SO3H |
Cellulose |
Isosorbide |
H2O (0.12) |
220 |
60 |
98 |
59 |
17.9 |
269
|
Ru@mNbPO |
Cellulose |
Isosorbide |
H2O (0.12) |
220 |
60 |
100 |
40 |
24.7 |
270
|
4.1.1. Sorbitol dehydration.
Isosorbide is a monomer for several bioplastics, including poly-(ethylene-co-isosorbide) terephthalate (PEIT), poly(isosorbide carbonate) (PIC) and poly(isosorbide oxalate). The isosorbide volume demand for PEIT production was around 3 ktons in 2012, while the global isosorbide market is expected to reach 300 million Euros by 2023.226 The conventional route to isosorbide synthesis involves a sequence of metal-catalysed hydrogenation of glucose to sorbitol, followed by twofold acid-catalysed dehydration of sorbitol through 1,4-sorbitan (Scheme 5). The latter steps are slowed down in the presence of water, thus requiring much higher reaction temperatures.227 On an industrial scale, isosorbide is currently produced in high purity via a three-stage process, comprising enzymatic depolymerisation of starch, hydrogenation over Ni catalyst and H2SO4-catalysed dehydration,228,229 however after a complex purification procedure.230,231 The world's largest manufacturer of isosorbide, the French company Roquette with a production capacity of 20
000 tons year−1, has recently patented an isosorbide process based on acidic ion-exchange resin dehydration under vacuum, whose yield based on sorbitol is around 94%.232 On the other hand, sorbitol itself is largely used in the food and pharmaceutical industries due to its low-calorie sweetener, laxative and humectant properties, as well as in the preparation of several other chemicals, including vitamin C, besides isosorbide.201,233 As a matter of fact, sorbitol has the biggest market share among the sugar alcohols.234
As mentioned above for the synthesis of isomannide, several zeolites were used in the solid acid-catalyzed dehydration of sorbitol and, among them, Hβ-75 showed the highest activity, which was attributed to its appropriate Brønsted/Lewis acidic site ratio, hydrophobicity and three-dimensional porous structure, favorable for the diffusion of sorbitol. A constant 87% isosorbide yield was observed in water at 200 °C over Hβ-75, wherein the catalyst could be reused three times, with no significant efficiency decay, after calcination at 550 °C.235 Solvent-free conditions resulted in 76% yield at 127 °C.236
Sulfonic acid heterogeneous catalysts, inorganic, silica-based or polymeric, have also been successfully used in sorbitol dehydration reaction. Excellent isosorbide yields (94%) were obtained at 140 °C, using a large amount (20 wt%) of magnetically-recoverable Glu–Fe3O4–SO3H catalysts under neat conditions.237,238 The Nafion–silica composite SAC-13 showed up to 83% isosorbide yield under solvent-free conditions, 130 °C and high vacuum, better than those obtained using the comparable catalysts Amberlyst-15 (67%), Deloxan (68%), Dowex 50WX2 (78%), Purolite CT269 (75%) or Sulfonated Hydrothermal Carbon (SHTC, 80%).239,240 This finding was tentatively attributed to the better site-accessibility of silica under catalytic conditions, compared to polymeric support materials, and to the higher acidic strength of the perfluorosulfonic groups. Indeed, similar catalytic performances were observed using sulfonic acid-functionalized silica catalysts. For instance, an 84% isosorbide yield was obtained over micro-bead silica catalysts, having different acid densities (120 °C, solvent-free), and obtained by reacting silica with variable amounts of (3-mercaptopropyl)trimethoxysilane (MPTS).241 The yield of isosorbide increased by increasing the acid density (up to 60% MPTS loading). The catalyst was reused ten times, showing no activity loss, but significant selectivity decrease (ca. 10%). The excellent catalytic performance was attributed to the appropriate combination of acidity, pore size (ca. 8 nm) and high surface hydrophilicity of the silica support, favoring the adsorption of feed, in that case. The effect of acid density/hydrophilicity balance on the catalytic efficiency of sorbitol dehydration was studied over mesostructured SBA-15 silica, functionalized with different amounts of hydrophilic propyl sulfonic acid groups and hydrophobic silyl moieties.242 The results indicated that an increase in the acid content slowed down the sorbitol to sorbitan step, but increased the rate of the sorbitan to isosorbide dehydration. On the other hand, an increase in surface hydrophobicity reduced the affinity of sorbitol for the catalyst, but increased the accessibility of sulfonic groups, thus slowing down the first step, but enhancing the second one. The best compromised results (70% yield at 150 °C) were obtained over 10% propyl sulfonic silica catalysts bearing trimethylsilane substituents. The catalyst lost most of its activity after the first run, which was ascribed to (by)-product adsorption, although decomposition of silica-bound propyl sulfonic groups cannot be ruled out.243,244 Comparable results (71% isosorbide yield at 170 °C) were obtained using an arenesulfonic acid-functionalized SBA-15 catalyst.245
Metal phosphates have been shown to be convenient dehydration catalysts, due to their nontoxicity, thermal stability and strong acidity.246,247 A series of phosphates were tested in the dehydration of 70 wt% aqueous sorbitol and their activity was found to increase in the order Al < Zr < Fe < La < Ce < B.248 At 250 °C a yield of 79.9 mol% of isosorbide was achieved using boron-phosphate. Quantitative sorbitol conversion, with 73% isosorbide selectivity, was obtained over porous zirconium phosphate (ZrP) at 210 °C without solvents.249 ZrP reusability was examined, showing quantitative sorbitol conversion up to the fifth run, with only a slight selectivity decrease (5%). A similar performance, though at a lower reaction temperature (180 °C), was observed using a mesoporous sulfated titania catalyst calcined at 450 °C (MST-450).250
Brønsted acidic ionic liquids (BILs) were recently explored as catalysts, due to their inherent advantages, compared to conventional mineral acids, in terms of reduced volatility and corrosivity.251 A series of ionic liquids bearing diverse acidic substituents and counterions was synthesized, and their efficiency rationalized in terms of the Gutmann acceptor number,252 rather than inherent acidity. Kinetic studies indicated that the ionic liquids have diverse abilities in forming adducts with sorbitol and the intermediate 1,4-sorbitan. The best results were achieved using BIL-5 catalyst (Scheme 8), which resulted in 85% isosorbide yield at 130 °C. The catalytic efficiency compared favourably with that of the homogeneous catalysts H2SO4 and CF3SO3H under the same reaction conditions. Despite the increasing interest and use of BILs in catalysis, some questions still remain to be addressed, particularly in relation to toxicity,253,254 reaction kinetics,255 and reusability.256 In the cited work, catalyst recycling experiments were performed by vacuum distillation of the product at 170 °C, well below the TGA decomposition temperature of ca. 300 °C, followed by addition of a fresh amount of substrate, showing pretty constant catalytic efficiency over five consecutive runs.
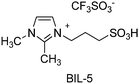 |
| Scheme 8 BIL-4 Brønsted acidic ionic liquid catalyst for sorbitol dehydration. | |
Metal tosylate salts were also explored as homogeneous-phase acidic catalysts. Thus, use of Bi(OTs)3 resulted in full conversion and 67% isosorbide yield, under solvent-free conditions, 145 °C and vacuum (40 mbar).257 Heterogenization onto Amberlyst 70 resin, although enabling effective removal of catalyst, resulted in their substantial deactivation.
Recently, a 93% isosorbide yield was achieved under mild conditions (170 °C, solvent-free), thanks to a new strategy based on sorbitol ketalization by methyl isobutyl ketone (MIBK), followed by double intramolecular etherification over Hβ-20 zeolite catalysts (Scheme 9).258 The approach allowed reducing the number of etherification active sites, thus controlling cyclisation selectivity and minimizing byproduct formation (humins, 2,5-sorbitan). Intramolecular etherification was facilitated by the ketone, as a better leaving group than water. After regeneration at 550 °C, the solid catalyst could be used three times without loss of activity.
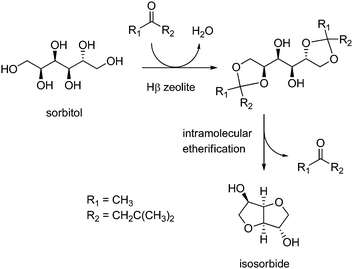 |
| Scheme 9 One-pot synthesis of isosorbide via sorbitol ketalization. | |
Although sorbitol dehydration to isosorbide mostly occurs by acid catalysis, in a few cases it was achieved in the presence of strong (i.e. sodium methoxide)259,260 or nitrogen bicyclic (i.e. DBU) bases.220 Thus, using dimethyl carbonate as both a carboxymethylating agent and a leaving group, the double intramolecular cyclization of sorbitol yielded isosorbide almost quantitatively (98%) (Scheme 10). However, the reaction was performed in the homogeneous phase and details on the fate of soluble catalysts were not provided. Carboxymethyl derivatives of isosorbide may be observed as by-products.
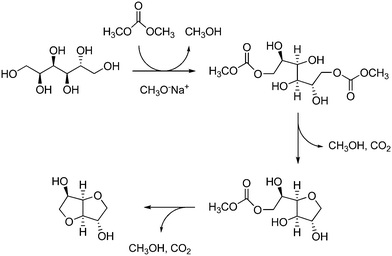 |
| Scheme 10 Mechanism of sorbitol dehydration in dimethyl carbonate under basic conditions. Adapted with permission from ref. 260 (F. Aricò, P. Tundo, Beilstein J. Org. Chem., 2016, 12, 2256–2266). Copyright 2016, Aricò and Tundo, Open Access article under the terms of Creative Commons Attribution License. (https://creativecommons.org/licenses/by/4.0/deed.it) license Beilstein-Institut. | |
4.1.2. Glucose conversion.
The one-pot, one-stage synthesis of isosorbide, directly from glucose and in water, was recently reported using a bifunctional (hydrogenation/acid) heterogeneous catalyst comprising Ru nanoparticles (1.3 nm) immobilized onto commercial sulfonic-acid ion-exchange resin Dowex 50WX2 (Ru@Dowex-H).261 Selection of the appropriate reaction conditions (190 °C, 30 bar H2, 48 h) allowed obtaining isosorbide in a remarkable 85% yield (based on glucose) at full substrate conversion, with the only significant by-product being 1,4-sorbitan. Interestingly, the process outcomes could be selectivity tuned to the intermediate sorbitol (>99% yield), by a simple modulation of the reaction conditions (i.e. 120 °C, 30 bar H2, 7 h). The effect of the reaction temperature on the reaction products, at fixed time and H2 pressure, is reported in Fig. 3. The high selectivity of the catalyst was attributed to the combination of appropriate swelling of the gel-type resin support in water and to the balanced loading of Ru-hydrogenation and Brønsted acid-dehydration sites (rate-determining).262,263
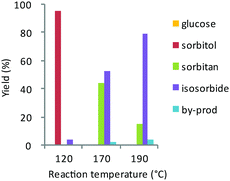 |
| Fig. 3 Effect of reaction temperature at 24 h reaction time on the direct, catalytic conversion of glucose over bifunctional Ru@Dowex-H (0.2% w/w Ru, water, 30 bar H2). Adapted with permission from ref. 261. Copyright 2016, Royal Society of Chemistry. | |
4.1.3. Cellulose conversion.
Methods for the direct, catalytic conversion of aqueous lignocellulosic biomass to isosorbide (Scheme 5) are receiving increasing attention, though only a few articles describe real improvements in terms of yields and catalyst reusability. Selectivity in such processes is an usual drawback, as several (poisoning) by-products may form and the carbon balance of the final products is often moderate.264,265 A new efficient catalyst, based on Ru oxide on sulfonated carbon, showed high catalytic activity in an optimized two-stage isosorbide synthesis from lignocellulosic substrates, whether containing lignin (bagasse pulp, yield 49 wt%) or not (microcrystalline cellulose, yield 56 wt%).266 The first stage involved the hydrolysis of cellulose to glucose and hydrogenation of glucose into sorbitol (170 °C), whereas the acid-catalysed dehydration to isosorbide was accomplished in the second stage (200 °C). A carbon balance in the range 85–92% was observed, wherein the only products detected, besides isosorbide, were unreacted intermediate glucose, sorbitol and 1,4-sorbitan, and the partial dehydration isomers 1,5- and 2,5-sorbitan. A reasonable selectivity of 56% to isosorbide was measured. Compared to conventional Ru@C/H2SO4 catalytic mixtures, the system showed constant activity over four consecutive runs (although with slight changes in the distribution of products) and superior recyclability, even for lignin-containing substrates. This was ascribed to the oxidative treatment of the catalyst, which increased the amount of carboxylic acid groups on the carbon support and reduced the adsorption of oligomer by-products (e.g. glucose) on the catalyst surface.
The one-pot, single-stage conversion of milled cellulose in water was performed using a mechanical mixture of commercial Ru@C and sulfonated resin Amberlyst-70 catalyst at 190 °C.267 A 56% isosorbide yield was observed in the first run, which decreased to 11% in the second run, due to the adsorption of by-products on the ruthenium surface (including 1,4-sorbitan, isomannide and various amounts of unidentified soluble materials). The same catalyst was used, under the same conditions, to convert lignocellulosic biomass from Japanese cedar (ca. 40 wt% cellulose content). However, the isosorbide yield was less than 30%.268
A sophisticated bifunctional catalyst featuring a core@void@shell structure (Ru/Fe3O4@void@PMO-SO3H) was recently developed and used in the direct conversion of cellulose to isosorbide, for the first time.269 By tailoring the size of Ru nanoparticles (2.2 nm), on a yolk–shell nanostructure containing an Fe3O4 core and a sulfonated periodic mesoporous organosilica (PMO) shell, an almost complete conversion of cellulose (98 wt%) was achieved at 220 °C, with a carbon efficiency of around 80%. A selectivity to isosorbide of 59% was observed, due to the significant formation of a variety of by-products, including sorbitol, mannitol, xylitol, erythritol and ethylene glycol originating from several side-reactions. The isosorbide productivity was 2.19 molisosorb h−1 gRu−1, higher than that obtained using previously reported ruthenium-based bifunctional catalysts, e.g. Ru@mNbPO.270 No significant decrease in the yield and conversion after four runs was observed.
4.2. Furanic diols
5-Hydroxymethylfurfural (HMF) is an important platform molecule obtainable from cellulose depolymerisation, via three-fold acid-catalyzed dehydration reaction of glucose (or fructose).271,272 HMF is usable to produce several value-added chemicals, including monomers for polymers (Scheme 5).273,274 Reduction of HMF provides a “family” of rigid cyclic diols, namely 2,5-bis(hydroxymethyl)furan (BHMF) and 2,5-bis(hydroxymethyl)tetrahydrofuran (BHMTHF), that have been proposed as BPA replacements. The topic has been partially covered by previous reviews.275,276 Actually, given the double functionality susceptible of reduction within HMF (C–O and C
C), its reduction is prone to significant selectivity issues, due to the complex network of potential reduction products that can be generated (Scheme 11),277,278 in addition to those usually observed in the processing of sugar-derived compounds (oligomers, humins, levulinates).279,280 As for any other partial reduction process, the challenge in BHMF and BHMTHF synthesis is to achieve the reduction of one specific group at full substrate conversion, which strongly depends on a subtle combination of metal catalyst, reaction conditions and, in the case of heterogeneous systems, properties of the support material.281,282 Continuous flow catalysis can be particularly useful in this regard, as it allows the fine tuning of reaction conditions and contact times, while enabling fast removal of intermediate products before further reduction.283,284Table 2 summarises the main features of the catalytic processes hereinafter described leading to furanic diols from biomass-derived sources.
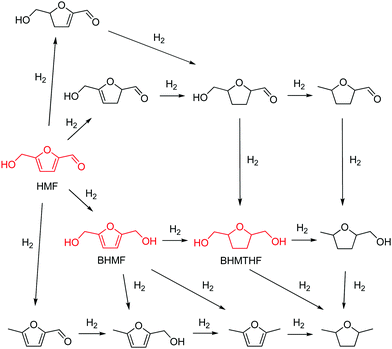 |
| Scheme 11 Simplified network of hydrogenation products originating from HMF. | |
Table 2 Summary of recent catalytic systems for proposed BPA monomeric replacements from furanic diolsa
Catalyst |
Biomass-derived substrate |
Product |
Reaction conditions |
Conv.c (%) |
Sel.d (%) |
Prod.e (mmolprod gcat−1 h−1) |
Ref. |
Solventb (M) |
T (°C) |
H2 (bar) |
See Section 4.2 for labelling and abbreviations.
Reaction solvent, substrate concentration (M) in brackets.
Substrate conversion.
Selectivity to the product indicated.
Catalyst productivity to the product indicated.
Homogeneous-phase catalysts.
Calculated with respect to the amount of Ru.
Under continuous flow conditions.
First of a two-step process.
Mechanical mixture.
Calculated with respect to the Ir catalysts.
Calculated with respect to the amount of Ru@SiO2 catalyst.
Calculated with respect to the amount of HT-Cu@ZnO@Al2O3 catalyst.
Catalytic transfer hydrogenation.
Reduction by silanes.
Calculated with respect to the amount of KF.
|
Ru complexf |
HMF |
BHMTHF |
Toluene (0.08) |
120 |
10 |
100 |
79 |
10.8g |
285
|
Ru complexf |
HMF |
BHMF |
Toluene (0.08) |
120 |
10 |
100 |
98 |
30.1g |
285
|
Ru@C |
HMF |
BHMTHF |
H2O (0.25) |
100 |
50 |
100 |
95 |
9.5 |
287
|
Ru@C |
HMF |
BHMF |
H2O (0.25) |
50 |
30 |
100 |
93 |
9.2 |
287
|
Ru@C |
HMF |
BHMF |
H2O (0.25) |
100 |
50 |
100 |
73 |
7.2 |
287
|
Ru@CNF |
HMF |
BHMF |
2-Butanol (0.08) |
150 |
20 |
86 |
95 |
810.4g |
288
|
Ru(OH)x@ZrO2 |
HMF |
BHMF |
1-Butanol (0.329) |
120 |
15 |
100 |
99 |
10.7 |
289
|
Pd@MIL-101(Al)-NH2 |
HMF |
BHMTHF |
H2O (0.13) |
30 |
10 |
100 |
96 |
4.0 |
293
|
Pd@mpg-C3N4 |
HMF |
BHMTHF |
H2O (0.17) |
60 |
10 |
100 |
96 |
4.0 |
294
|
Cu–ZnO |
HMF |
BHMF |
1,4-Dioxane (0.34) |
100 |
15 |
100 |
99 |
11.8 |
295
|
Cu–Zn nanoalloy |
HMF |
BHMF |
Ethanol (0.2) |
120 |
70 |
100 |
95 |
12.5 |
296
|
Ni–Al@LDH |
HMF |
BHMTHF |
H2O (0.04) |
80 |
20 |
100 |
99 |
4.8 |
297
|
Ni-Fe@CNT |
HMF |
BHMF |
1-Butanol (0.2) |
110 |
30 |
100 |
96 |
4.3 |
298
|
Ni–Al2O3 |
HMF |
BHMTHF |
1,4-Dioxane (0.34) |
60 |
60 |
100 |
96 |
9.5 |
299
|
RANEY® Cuh |
HMF |
BHMF |
H2O (0.08) |
90 |
90 |
94 |
92 |
1.48i |
300
|
Pd@SiO2 + Ir-ReOx@SiO2h,j |
HMF |
BHMTHF |
H2O/THF (0.08) |
100 |
30 |
100 |
77 |
0.37k |
301
|
K-Cu@Al2O3h |
HMF |
BHMF |
Ethanol (0.24) |
120 |
20 |
99 |
99 |
0.30 |
302
|
Ru@SiO2 + Nb2O5–PO4h,j |
Fructose |
BHMTHF |
Cyclohexane (0.17) |
160 |
40 |
98 |
41 |
3.3l |
304
|
Ru@SiO2 + Nb2O5–PO4h,j |
Glucose |
BHMTHF |
Cyclohexane (0.17) |
160 |
40 |
32 |
63 |
1.68l |
304
|
Ru@SiO2 + Nb2O5–PO4h,j |
Inulin |
BHMTHF |
Cyclohexane (0.17) |
160 |
40 |
96 |
33 |
2.6l |
304
|
Cu–SiO2 |
HMF |
BHMTHF |
1-Butanol (0.79) |
100 |
15 |
95 |
98 |
20.2 |
307
|
HY + HT-Cu@ZnO@Al2O3h,j |
HMF |
BHMF |
GBL/H2O (0.19) |
140 |
10 |
n.a. |
48 |
0.002m |
308
|
NiO |
HMF |
BHMF |
2-Propanol (0.1) |
150 |
—n |
77.9 |
94 |
3.1 |
311
|
Ru@Co3O4 |
HMF |
BHMF |
2-Propanol (0.03) |
170 |
—n |
94 |
85 |
0.19 |
312
|
Zr-Ba oxide |
HMF |
BHMF |
2-Propanol (0.06) |
150 |
—n |
98 |
92 |
2.9 |
313
|
Al7Zr3@Fe3O4 |
HMF |
BHMF |
2-Propanol (0.2) |
180 |
—n |
83 |
86 |
4.4 |
315
|
Hf-TPA |
HMF |
BHMF |
2-Butanol (0.13) |
130 |
—n |
99 |
98 |
3.8 |
316
|
K2CO3 |
HMF |
BHMF |
2-MeTHF (0.25) |
25 |
—o |
100 |
94 |
17.7 |
317
|
KF |
HMF |
BHMF |
DMSO (0.25) |
25 |
—o |
99 |
99 |
5.4 |
318
|
Amberlyst-15 + KFj |
Fructose |
BHMF |
DMSO (0.25) |
25 |
—o |
99 |
89 |
7.3p |
318
|
The hydrogenation of HMF has been recently reported by Hashmi et al. using homogeneous-phase catalysts in toluene solution.285,286 A screening study was performed through a variety of ligands and metals, wherein the best BHMF (98%) and BHMTHF (79%) yields were obtained at full HMF conversion with Ru bispyridine and DTBM–SEGPHOS complexes, respectively, at 120 °C and 10 bar H2 (Scheme 12). However, despite its fundamental interest and good yields, the system suffers from limitations that hamper its use for real applications: high catalyst loading, cost of chiral ligands, non-reusability of catalysts, and toxic toluene solvent.
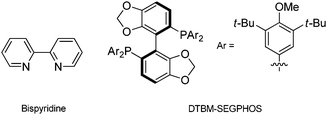 |
| Scheme 12 Structures of bipyridine and DTBM–SEGPHOS ligands. | |
Several heterogeneous catalysts have been reported in recent years for the hydrogenation of HMF. Use of commercial Ru@C gave BHMF and BHMTHF from aqueous HMF in 93% and 95.3% yield, respectively, by a simple change in the reaction temperature (from 50 °C to 100 °C) and hydrogen pressure (from 30 bar to 50 bar).287 The same catalyst gave BHMF in 73% (100 °C and 50 bar H2) using a crude HMF-rich hydrolyzate mixture from fructose dehydration as a substrate. Ru nanoparticles immobilized onto carbon nanofibers (CNF) were used in the hydrogenation of HMF in 2-butanol.288 BHMF was obtained in 82% yield at 86% HMF conversion at 150 °C and 20 bar H2. On the other hand, Ru(OH)x@ZrO2 in 1-butanol gave BHMF in 99% yield at full HMF conversion at 120 °C and 15 bar H2.289 A turnover frequency (TOF) of 304 h−1 was calculated, in that case. The catalyst could be recovered and reused five times with no significant loss of activity, after acetone/NaOH washings. Heterogeneous catalysts based on noble metals other than Ru (Pd, Pt) were reported for the synthesis of BHMTHF with high selectivity.290 This approach can be rationalized in terms of the different affinities toward C–O (Pt, Ru), rather than C
C bond hydrogenation (Pd, Rh).291,292 In a recent study, a palladium catalyst immobilized onto amine-functionalized metal–organic frameworks [Pd@MIL-101(Al)-NH2] was used to obtain a 96% yield of BHMTHF, at full conversion of aqueous HMF, under mild reaction conditions (30 °C, 10 bar H2). The choice of metal–organic framework supports was motivated by their tunable physicochemical properties. In that case, amine group functionalization resulted in the modification of the nanoparticle dispersion and acidity/basicity of the catalyst, hence in its selectivity, due to the stronger hydrogen bonding interaction between MIL-101(Al)-NH2 and the intermediate BHMF, instead of HMF (Scheme 13).293 Comparable results in terms of conversion (>99%) and BHMTHF selectivity (96%) were obtained using Pd catalysts immobilized onto mesoporous graphitic carbon nitride (Pd@mpg-C3N4) under similar reaction conditions (water, 60 °C, 10 bar H2).294
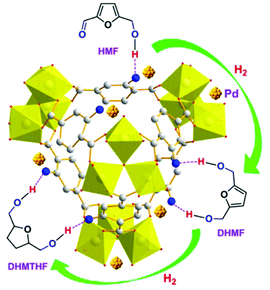 |
| Scheme 13 Molecular interactions in the hydrogenation of HMF over Pd/MIL-101(Al)-NH2. Gray and blue balls represent carbon and nitrogen atoms, respectively. The palladium nanoparticles are golden in color. Reprinted with permission from ref. 293. Copyright (2015) American Chemical Society. | |
Use of non-noble catalysts (Cu, Ni) was investigated due to their low cost and higher hydrogenation activity toward C–O than C
C bonds. Thus, mineral-derived Cu/ZnO catalysts (malachite, rosasite and aurichalcite) provided BHMF in 99% yield from HMF at 100 °C, whereas an increase in the reaction temperature to 220 °C afforded the fully C–O hydrogenated product 2,5-dimethylfuran.295 A sharp decrease of the catalytic efficiency was observed after the first run, which was attributed to the deposition of the carbonaceous material on the catalyst surface. Cu/Zn nanoalloys with particle sizes <150 nm were employed to synthesize BHMF from HMF with an excellent yield (95%), at 120 °C and a high hydrogen pressure of H2 (70 bar).296
A Ni–Al layered double hydroxide (LDH) bearing supported Ni nanoparticles (8–10 nm) was tested in the liquid-phase hydrogenation of HMF in water (0.4 M) at 80 °C and 20 bar H2.297 Complete conversion (96%) was achieved after 6 h, yielding a mixture of BHMF (25%) and BHMTHF (71%), however. Higher BHMTHF yields (>99%) were obtained upon increasing the reaction time to 12 h, whereas an increase of the reaction temperature promoted the formation of by-products via ring opening-cyclization (to 3-hydroxymethylcyclopentanone) and cross-polymerisation. Better BHMF yields (96%) were achieved using a carbon-nanotube (CNT)-supported bimetallic Ni–Fe catalyst at 110 °C, wherein 2,5-dimethylfuran formed preferentially at 200 °C (91% yield).298 Hydrotalcite-derived Ni–Al2O3 catalysts were scrutinized in the hydrogenation of HMF to 2,5-dimethylfuran, BHMF and BHMTHF. Selectivity was found to be dependent on the calcination temperature, which was ascribed to the different dispersion of the surface metallic sites. The best results were obtained for BHMTHF (96% selectivity at full conversion) using catalysts calcined at 450 °C, 60 °C reaction temperature and 60 bar H2.299
In a few studies, the catalytic hydrogenation of HMF was examined using continuous flow setups. A BHMTHF yield of 98% was obtained in two-stages, wherein two different catalysts were used sequentially, under the same reaction conditions: RANEY® Cu for the hydrogenation of HMF to BHMF, and RANEY® Ni for further hydrogenation to BHMTHF (90 °C, 90 bar H2, water solution rate 0.05 mL min−1).300 The calculated productivity of BHMTHF was 1.45 mmol gcatalyst−1 h−1 (based on BHMF, yield 98%). The intermediate BHMF stream showed an average 94% HMF conversion and 92% selectivity. Unfortunately, the catalytic activity decreased significantly after 32 h time-on-stream, due to RANEY® Ni deactivation. Lower BHMTHF yields (77%) were previously reported using double layered catalyst Pd@SiO2/Ir-ReOx@SiO2, 100 °C, 50 bar H2 and THF solvent.301 HMF in ethanol (0.24 M) was also hydrogenated by flowing through a potassium-doped Cu@Al2O3 catalyst at 120 °C, using a concurrent stream of H2 (20 bar, 50 mL min−1), to give BHMF in 98.9% yield.302 The high efficiency was tentatively attributed to the fact that the addition of appropriate amounts of potassium improved the dispersion of copper and reduced the acidity of the catalyst, thus enhancing the catalytic activity, while suppressing unwanted side reactions. A totally selective hydrogenation of HMF to BHMF was achieved in the gas phase over Au-Cu@CeO2 catalyst, using in situ generated hydrogen by dehydrogenation of 2-butanol.303
The synthesis of furanic diols was also sought by direct conversion of carbohydrates. Thus, a heterogeneous catalyst based on the combination of acid-treated Nb2O5 (HF and H3PO4) and hydrophobic Ru@SiO2 catalyst (treated with trimethylchlorosilane) was used for the one-pot dehydration–hydrogenation reaction of diverse carbohydrates (mono-, di- and polysaccharides) (Scheme 5).304 Niobic acid and its derivatives are well-known strong solid acids, featuring high tolerance to water and catalytic activity.305,306 The best results in terms of conversion (98%) and selectivity to BHMTHF (41%) were obtained using fructose as a substrate (160 °C, 40 bar H2, in cyclohexane.) Under the same conditions, the selectivity for glucose was 63%, at 32% conversion, however. Conversions and selectivities around 30–40% were achieved using disaccharides (sucrose, maltose, cellobiose). A high conversion value (96%), but lower selectivity (33%), was obtained using inulin polysaccharides. In order to foster the production of BHMF directly from fructose, an integrated batch process, consisting of dehydration over Amberlyst-15 and a further hydrogenation over a Cu–SiO2 nanocomposite in 1-butanol, was developed.307 Highly concentrated fructose (15 wt%) gave HMF in 95% yield at 100 °C. The HMF feed obtained after extraction was hydrogenated with Cu–SiO2 (50% Cu), to give BHMF in 88% yield. A continuous process for the direct conversion of fructose to BHMF was recently engineered, combining two catalysts in the same reactor: HY zeolite for the conversion of fructose to HMF, and hydrotalcite HT-Cu@ZnO@Al2O3 for the hydrogenation of HMF to BHMF.308 The tandem dehydration–hydrogenation of fructose was achieved by pumping a fructose solution (3 wt%) in γ-butyrolactone/water, together with a H2 stream. The effects of the water content, the reaction temperature and the fructose weight-hourly-space-velocity (WHSV) were examined, to give 48.2% yield of BHMF under optimized conditions (15 wt% water, 140 °C, 15 mL min−1 H2 flow and of 0.02 h−1 WHSV).
Other approaches than H2 hydrogenation were used to reduce HMF to BHMF or BHMTHF. For instance, catalytic transfer hydrogenation (CTH) is a conventional method previously applied to diverse biomass-derived substrates.309,310 The strategy proved to be particularly useful in the selective synthesis of BHMF. The most successful heterogeneous systems recently reported include 3D-nanostructured NiO catalysts with a sea urchin-like morphology, yielding 74% BHMF at 150 °C,311 and Ru@Co3O4, yielding 80% BHMF at 170 °C,312 both using 2-propanol as a hydrogen source. Better BHMF yields (91%) were obtained in 2-propanol at 150 °C using a mixed Zr-Ba oxide catalyst supported on SBA-15 mesoporous silica.313 The efficiency of the mixed catalyst was attributed to the negligible amount of Brønsted acidic sites, usually favoring etherification side-reactions, and to the content of Lewis acidic sites, promoting the reduction of HMF via a Meerwein–Ponndorf–Verley mechanism.314 Despite its moderate BHMF yield (71%), the magnetically recoverable catalyst Al7Zr3@Fe3O4 was particularly interesting in terms of ease of separation from the reaction mixture and reuse.315 Recently, an excellent (96.8%) yield of BHMF was achieved in 2-propanol at 130 °C, using a large amount of Hf-TPA catalyst (50 wt%) prepared from hafnium tetrachloride and diethylene triamine penta(methylene)phosphonic acid (TPA).316 The high catalytic efficiency was attributed to the synergistic effect of Hf4+ Lewis acidic sites and O2− Lewis basic sites, in that case. The catalyst could be easily recovered and reused for five successive recycles, without activity drops.
Silanes were used as cheap and easy-to-handle reducing agents. A K2CO3-catalyzed conversion of HMF to BHMF in 94% yield was reported at room temperature, using diphenyl silane as reagent and bio-based 2-methyltetrahydrofurane as solvent.317 Although an irritant and a high-boiling point liquid, Ph2SiH2 avoids usual noble metal-based hydrogenation catalysts and high H2 pressures. A mechanism was speculated in which a carbonate-promoted hydride transfer from silane to the aldehyde group occurs, to afford a siloxane intermediate that gives BHMF after reaction quenching with methanol (Scheme 14). Use of potassium fluoride as a catalyst and polymethylhydrosiloxane (PMHS) as a hydrogen donor was described, providing BHMF in 95% yield with a TOF of 4.2 h−1 at room temperature.318 The catalyst could be reused over five runs, without activity loss. An increase of the reaction temperature to 80 °C resulted in 98% yield. A two-step, one-pot process for the direct conversion of fructose to BHMF in 88% yield was also achieved, combining Amberlyst-15 for the dehydration of the sugar to HMF at 120 °C, and KF/PMHS, for the hydrogenation step at room temperature.
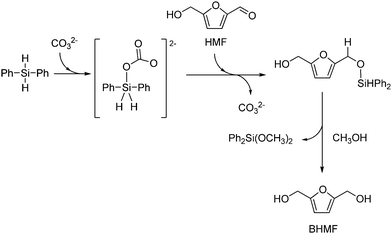 |
| Scheme 14 Proposed mechanism for carbonate-catalyzed reduction of HMF by Ph2SiH2. | |
4.3. Other compounds
The synthesis of other alicyclic compounds, potential functional substitutes of BPA, such as 3-hydroxymethylcyclopentanol (HCPO) which is currently produced from petrochemicals,319,320 has recently been reported using HMF as a substrate in water. Use of a catalyst composed of a mechanical mixture of Pt@SiO2and Nd2O3 gave HCPO in 88% yield, through a multi-step, one-pot process based on Pt-catalyzed hydrogenation of HMF to BHMF, Lewis acid-catalyzed Piancatelli ring-rearrangement to 4-hydroxy-4-(hydroxymethyl)-cyclopenten-2-one (HHCPEN), and successive acid-catalyzed hydrodeoxygenation and hydrogenation to HCPO, at 140 °C and 30 bar H2 (Scheme 15).321 Similarly, HCPO was obtained in higher yield (94%) using Co@Al2O3 as a bifunctional catalyst at 140 °C and 20 bar H2.322
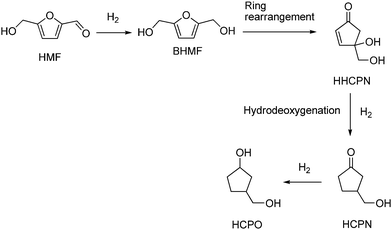 |
| Scheme 15 Catalytic synthesis of HCPO from HMF. | |
In a different approach, homo- or cross-coupling of HMF with furfural (see Section 6) was catalyzed to give furoin-type difuranics, usable in the synthesis of polyurethanes and polyesters.323,324 Thus, organocatalytic homocoupling of HMF using TPT-OMe (5-methoxy-1,3,4-triphenyl-4,5-dihydro-1H-1,2,4-triazoline) gave the triol DHMF shown in Scheme 16 (95% yield), which could then be oxidized (MnO2 or air, 95–86% yield)325,326 or reduced (NaBH4, 63% yield),327 to give the diol BHF and the tetraol BHMH, respectively. Furfural–HMF cross-coupling, catalyzed by N-heterocyclic carbene (NHC) in the presence of a base, gave C11 furoins in around 60% yield.328 The production of C10 and C12 furoins could be significantly improved to 97% yield by using an azolium catalyst grafted onto either silica or Merrifield resin.329
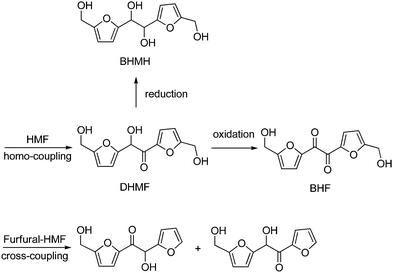 |
| Scheme 16 Catalytic coupling syntheses of bis-furanic diols. | |
It must be mentioned that p,p′-diphenolic acid (DPA) was previously proposed as a BPA substitute from biomass. DPA can be produced from levulinic acid and phenol using mineral acids (HCl, H2SO4),330 Brønsted acidic ionic liquids,331 heteropolyacids332 and sulfonated polymer333 catalysts (Scheme 17). Levulinic acid and alkyl levulinates are obtainable from woody raw materials, particularly non-edible agricultural wastes, and from biorefinery side-streams.334 Technologies are nowadays available for the production of levulinic acid on a tons per day scale by acid-catalysed dehydration of cellulose sugars.335,336 Polyether ketones containing DPA units,337 as well as polyethers bearing DPA pendant groups,338 have been synthesized.
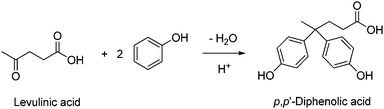 |
| Scheme 17 Synthesis of DPA. | |
Table 3 summarises the main features of the catalytic processes detailed in the present review which lead to proposed BPA substitutes from other cellulose-derived sources.
Table 3 Summary of recent catalytic systems for proposed BPA monomeric replacements from other cellulose-derived sourcesa
Catalyst |
Biomass-derived substrate |
Product |
Reaction conditions |
Conv.c (%) |
Sel.d (%) |
Prod.e (mmolprod gcat−1 h−1) |
Ref. |
Solventb (M) |
T (°C) |
H2 (bar) |
See Section 4.3 for labelling and abbreviations.
Reaction solvent, substrate concentration (M) in brackets.
Substrate conversion.
Selectivity to the product indicated.
Catalyst productivity to the product indicated.
Mechanical mixture.
Calculated with respect to the Pt catalyst.
Calculated with respect to NEt3.
|
Pt@SiO2 + Nd2O3f |
HMF |
HCPO |
H2O (0.07) |
140 |
30 |
100 |
88 |
0.6g |
321
|
Co@Al2O3 |
HMF |
HCPO |
H2O (0.04) |
140 |
20 |
100 |
94 |
1.8 |
322
|
TPT-OMe |
HMF |
DHMF |
CH2Cl2 (3.2) |
40 |
— |
100 |
95 |
573.6 |
327
|
MnO2 |
DHMF |
BHF |
THF (0.1) |
r.t. |
— |
100 |
95 |
0.27 |
327
|
DBU |
DHMF |
BHF |
THF (0.1) |
60 |
— |
100 |
86 |
4.7 |
327
|
NHC + NEt3 |
Furfural-HMF |
C11 furoin |
Free |
80 |
— |
95.2 |
34 |
2.6h |
328
|
5. Substitutes from the lignin depolymerisation chain
Lignin is extracted from biomass using different processes that greatly influence its structure and composition.339,340 Methods have then been developed to depolymerise and fragment lignin into a huge variety of smaller aromatic molecules, usually referred to as lignin-derived platforms, whose nature depends on the native biomass and the deconstruction method used.341,342 Selected examples are shown in Scheme 18. These lignin platforms may be categorised according to the monolignol G, H and S units from which, at least formally, they are derived (Scheme 4).343,344 A detailed description of the several strategies, techniques and processes to extract, fraction (particularly via reductive catalysis)345,346 and depolymerise lignin is outside the scope of the present review and can be found elsewhere.347,348 As lignin is by far the most abundant renewable source of aromatic platforms,349,350 exploding interest has been recorded in recent years toward lignin valorisation.351,352 The lignin biorefinery concept has equally become of increasing importance.353,354
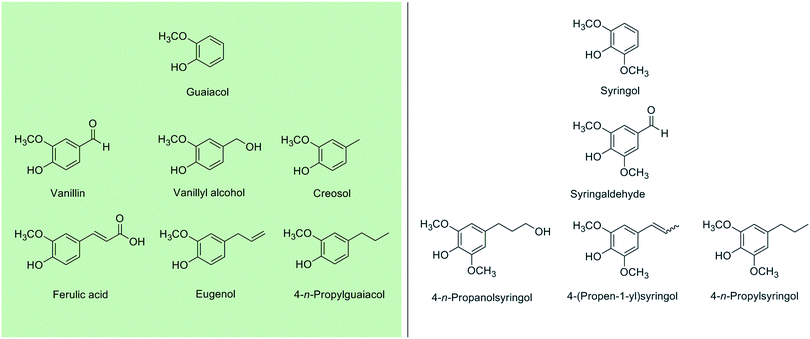 |
| Scheme 18 Some aromatic molecules obtained from lignin deconstruction processes and used in the production of monomeric substitutes of BPA. | |
Several possibilities exist to convert lignin platforms into building blocks for polymers, taking advantage of the multiple functionalities that they feature: phenolic, aromatic and side-chain.355,356 Catalytic methods for the synthesis of diol building blocks will be considered in the present review. Other compounds (e.g. epoxies, esters, ethers) can then be obtained by further functionalisation.357,358 It must be underlined, however, that most proposed BPA substitutes from lignin are based on bis-phenolic moieties that, with few notable exceptions, are still obtained by means of classical organic processes using noxious reagents and/or solvents, e.g. coupling reactions by carcinogenic formaldehyde. The development of innovative scaffolds and synthetic strategies is thus strongly desirable, including improved heterogeneous catalysts.
5.1. Substitutes from coniferyl-derived compounds
5.1.1. Vanillin-derived substitutes.
One of the most important lignin-derived platforms is vanillin and its direct derivatives (vanillic acid, vanillyl alcohol, 2-methoxyhydroquinone, creosol), together referred to as “vanillin platforms”.359
A reason for that lies in the usual difficulty of separating and recovering aromatic compounds, with purities and yields attractive for commercial applications, from lignin-depolymerisation streams.360 Indeed, vanillin is the highest volume, and one of the few, aromatic molecules currently produced on an industrial scale from lignin. To date, the vanillin obtained from lignosulfonates has accounted for around 15% of the total vanillin market (ca. 20
000 tons year−1).361,362 The remaining amount is still produced from oil, through the catechol–guaiacol process.363,364 Lignin-to-vanillin processes have been detailed in a recent account.365
The building blocks prepared from vanillin platforms, and the bio-polymers thereof, have been exhaustively reviewed up to 2017.366,367 These building blocks include divanillin (by enzymatic catalysis)368,369 and the corresponding methylated diol,370meso-hydrovanilloin,371 vanillin acetals (1 and 2),372,373 polyaromatic Schiff-bases374,375 and C1-bridged376,377 and C2-bridged diphenols (4 and 5)378 shown in Scheme 19. Catalytic steps in the syntheses of these compounds from platform molecules were limited to C
C side-chain hydrogenation, over conventional PtO2 catalysts,377 and acid-catalysed acetalisations (by p-toluenesulfonic acid). The various coupling methods leading to these building blocks have been described in a recent survey.379 It is worth mentioning, however, that the synthesis of bisguaiacol F (BGF) isomers has recently been reported via the acid-catalysed condensation of vanillyl alcohol with guaiacol, as safer alternatives to formaldehyde, with the preferential formation of the p,p′-BGF isomer (70% yield, 82% purity, Scheme 20). Use of the solid acid resin catalyst Dowex DR2030 adds significant benefits to the method.380 A later study showed that the estrogenic activity of these BGF isomers was lower than that of BPA, thus suggesting their potential as viable alternatives to BPA.381,382 A number of vanillin-based bis-epoxides,383,384 polycarbonates and polyesters385,386 have been made available from the above mentioned scaffolds.
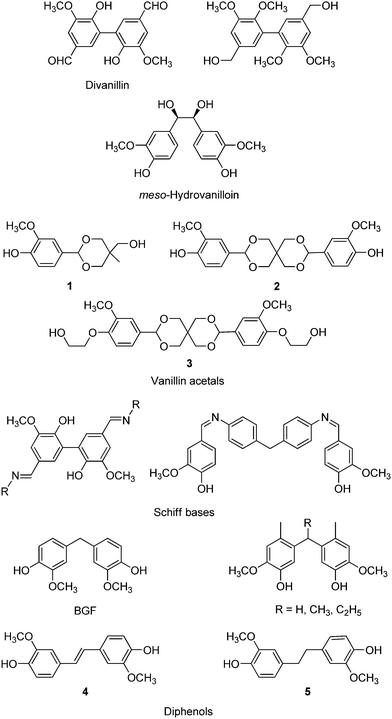 |
| Scheme 19 Some diol building blocks prepared from vanillin platforms. | |
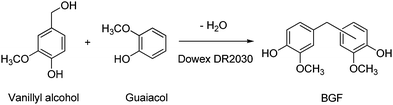 |
| Scheme 20 Synthesis of BGF isomers from vanillyl alcohol and guaiacol. | |
More recently, a diol with a spirocyclic acetal structure (3) was obtained by alkali treatment of 2 with ethylene carbonate.387 Therein, the greenhouse gas emissions generated by the production of 3 were evaluated to be around one-half of those related to BPA. Copolymerization of 3 with 1,6-hexanediol and dimethyl terephthalate resulted in copolyesters showing improved glass transition temperature and thermal stability, upon incorporation of the spiroacetal unit. The synthesis of the bisphenol carbonate BHMC shown in Scheme 21 was also reported, however using an un-catalysed reaction sequence, chlorinated and THF solvents and toxic phosgene reagent.388
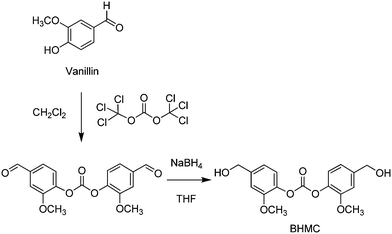 |
| Scheme 21 Synthesis of BHMC from vanillin. | |
5.1.2. Substitutes from ferulic acid.
Ferulic acid is the second monophenolic compound produced from lignin by volume.389,390 It is highly abundant (predominantly the trans isomer) in the cell walls of flowering plants, as well as in sugar beet and sugar cane.391,392
Ferulic acid was previously reported as a substrate in the synthesis of homopolymers mimicking the thermal properties of polyethylene terephthalate (PET), i.e. poly(dihydroferulic acid), via Pd@C hydrogenation, followed by Zn(OAc)2 polymerisation (Scheme 22).393 More recently, a ferulic acid-derived bisphenol containing an isosorbide core (Section 4.1), namely bis-o-dihydroferuloyl isosorbide (IDF), was reported via two-step acid-catalysed esterification and Pd@C-catalysed hydrogenation of ferulic acid in ethanol, followed by lipase-mediated transesterification with isosorbide (Scheme 23).394 The as-prepared macromonomer was used in the synthesis of polyesters.197
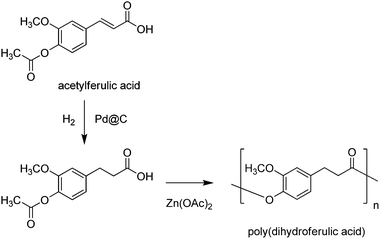 |
| Scheme 22 Synthetic pathway to poly(dihydroferulic) acid. | |
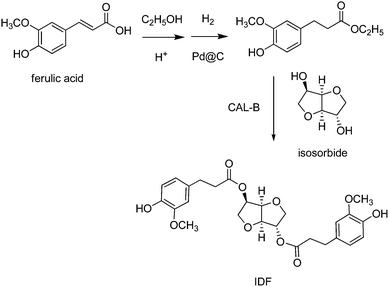 |
| Scheme 23 Synthetic pathway to IDF from ferulic acid. | |
5.1.3. 4-n-Propylguaiacol.
A valuable product of softwood lignin catalytic depolymerisation is 4-n-propylguaiacol.395 Brønsted acid-catalysed condensation of 4-n-propylguaiacol with formaldehyde, by either homogeneous HCl396 or heterogeneous zeolites (FAU-40),397 afforded the bisguaiacol 5,5′-methylenebis(4-n-propylguaiacol) (m,m′-BGF-4P) represented in Scheme 24, in moderate yield and high purity (minor amounts of o,m′ and o,o′ regioisomers were detected). As for other condensation or dehydration processes (Section 4.1.1), the rationale for the use of acidic zeolite catalysts is to avoid unrecoverable mineral acids (e.g. HCl, H2SO4) or thermolabile sulfonated resins (e.g. Dowex, Amberlyst) often used to this aim. The benefits of zeolites include their thermal stability, high Brønsted acidic-site density and ease of recovery. Indeed, the zeolite catalyst could be easily separated and reused, unfortunately showing a significant loss of activity, which can be regenerated by coke burn-off. Common shortcomings of zeolites are the limited site accessibility and mass transfer of large substrates, due to their intrinsic microporous structure, that can be partially circumvented by the introduction of additional mesoporosity. Noteworthily, m,m′-BGF-4P showed reduced estrogenic receptor activity compared to BPA. This finding, together with the similar one previously reported for BGF, suggests that the presence of methoxy groups in the ortho position strongly decreases the ability to bind and/or activate estrogen receptors in alkylphenols, which was attributed to steric hindrance.398,399 Polycarbonates (Tg 99 °C), cyanate ester (Tg 193 °C)396 and a variety of epoxy resins were prepared from m,m′-BGF-4P.400,401 The increase of the length of the phenolic side-chain did not affect significantly the yield of polycarbonates (around 60% for the n-propyl, ethyl and methyl monomers), whereas it lowered their tendency to crystallize and their glass transition temperature and improved their solubility in common organic solvents.
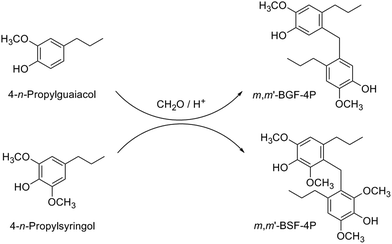 |
| Scheme 24 Synthesis of C1-bridged diphenols from propylguaiacol and propylsyringol. | |
5.1.4. Eugenol.
Eugenol (and iso-eugenol) can be isolated from lignin and, in higher amounts, from the essential oils of several plants.402,403 About 2000 tons of eugenol are produced yearly from clove oil.404 These molecules may be used in the synthesis of polymer building blocks.405
Thus, the dihydroxystilbene 4 and its di(hydroxyphenyl)ethane 5 analogue were prepared from eugenol, via a catalytic process involving isomerising metathesis and C
C bond hydrogenation, respectively (Scheme 25).406 A combination of Pd isomerisation ([Pd(μ-Br)(t-Bu3P)]2) and Ru metathesis (Hoveyda–Grubbs type) homogeneous catalysts was required for the first step, whereas the second step was accomplished over conventional Pd@C. Compared to the previously reported synthesis from vanillin,378 the benefits of the approach are use of safer solvents (ethanol), a simpler purification procedure, an entirely catalytic protocol, potential for a one-pot process, and use of a less expensive hydrogenation catalyst (Pd vs. Pt). As for most homogeneous-phase catalysts, the drawbacks include the non-reusability of expensive metal complexes. Both 4 and 5 were found to be non-estrogenic. Polycarbonate and thiol–ene polymers were prepared from these monomers. Polycarbonates were obtained in ca. 80% yield by reacting the monomers with diphenyl carbonate and catalytic LiOH at 180 °C, showing lower molecular weights compared to the BPA analogue and Tg 127 °C and 81 °C, respectively.
 |
| Scheme 25 Catalytic metathesis-hydrogenation pathway to C2-bridged diphenols. | |
Table 4 summarises the main features of the catalytic processes described in the present review leading to proposed BPA substitutes from coniferyl-derived compounds.
Table 4 Summary of recent catalytic systems for proposed BPA monomeric replacements from coniferyl-derived compoundsa
Catalyst |
Biomass-derived substrate |
Product |
Reaction conditions |
Conv.c (%) |
Sel.d (%) |
Prod.e (mmolprod gcat−1 h−1) |
Ref. |
Solventb (M) |
T (°C) |
H2 (bar) |
See Section 5.1 for substrate and product numbering and labelling.
Reaction solvent, substrate concentration (M) in brackets.
Substrate conversion.
Selectivity to the product indicated.
Catalyst productivity to the product indicated.
Homogeneous-phase catalysts.
|
Dowex DR2030 |
Vanillyl alcohol |
p,p′-BGF |
Free |
60 |
— |
70 |
82 |
0.5 |
380
|
K2CO3 |
Vanillin acetal 2 |
3
|
DMF (0.4) |
160 |
— |
100 |
90 |
9.1 |
387
|
Pd@C + CAL-B |
Ferulic acid |
IDF |
Ethanol (1.4) |
r.t. + 75 |
1 |
100 |
72 |
n.a. |
197
|
FAU-40 |
4-n-Propylguaiacol |
m,m′-BGF-4P |
Toluene (0.5) |
100 |
— |
40 |
80 |
4.3 |
397
|
Pd + Ru complexes f |
Eugenol |
4
|
Ethanol (0.3) |
70 |
— |
100 |
81 |
n.a. |
406
|
Pd@C |
4
|
5
|
Ethanol (0.3) |
50 |
7 |
100 |
95 |
19.1 |
406
|
5.2. Substitutes from sinapyl-derived compounds
Various sinapyl-derived molecules (including syringaldehyde, 4-n-propylsyringol, 4-n-propanolsyringol, and 4-propenylsyringol) can be obtained with remarkable selectivity by lignin depolymerisation through catalytic oxidation or reduction processes,407,408 particularly hydrogen-free fractionation of woody biomass over Pd@C catalysts409 and lignin-first strategies.410,411
Enzymatic oxidative dimerization of sinapyl alcohol, either from lignin degradation or by chemical reduction of sinapic acid, affords syringaresinol (SYR) in very high yield.412 SYR is a naturally occurring phenol that can be found is small quantities in some flowering plants.413,414 It can also be obtained by chemical methods from sinapyl alcohol via multistep reaction processes and using stoichiometric amounts of peracids or potassium ferricyanide, however.415,416 The structure of SYR consists of a rigid cis-fused bis-tetrahydrofuranic ring and two pendant syringol units (Scheme 26). Its rigid core makes it a good functional substituent candidate for BPA. Compared to IDF, featuring a similar bisfuran core (Scheme 23), SYR lacks the flexibility of the aliphatic ester side-chain. Indeed, poly(hydroxy)urethanes417 and epoxy-amine resins were synthesized based on the epoxy derivative SYR-EPO, showing better thermal properties compared to parent IDF-based resins.418 Syringaresinol showed no endocrine disruption activity.
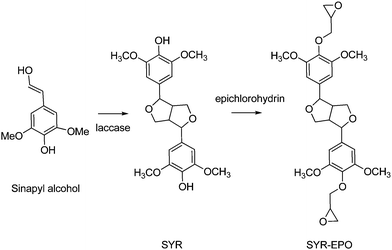 |
| Scheme 26 Catalytic synthesis of SYR and the structure of the epoxy derivative SYR-EPO. | |
5.2.1. Syringaldehyde.
Bisphenols having structures with diverse flexibilities were synthesized from syringaldehyde, via a two-step process comprising uncatalysed Wittig olefination (step 1), followed by either HCl treatment or acid-catalysed (p-TsOH) addition of di(trimethylolpropane) (DTMP) (step 2), to give the annulated-HS and the bis-acetal DTMP-HS products shown in Scheme 27, respectively.419 These compounds could also be obtained directly from lignin after selective degradation in methanolic H2SO4, in much lower yields, however. The corresponding bis-epoxy based resins were also synthesized, showing glass transition temperatures of 130 °C and 67 °C, respectively.
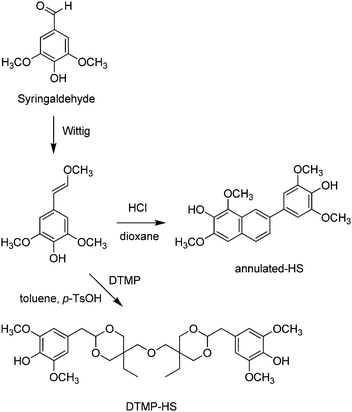 |
| Scheme 27 Two-step synthesis of bisphenols from syringaldehyde. | |
A series of highly rigid triphenylmethane polyphenols (TPs), bearing a various number of methoxy and alkyl substituents, were prepared by conventional acid-catalysed condensation of lignin-derived aldehydes (including syringaldehyde and vanillin) and bio-based phenols (guaiacol, syringol, catechols).420,421 Their structures are reported in Scheme 28. The benefits of the method include the use of aromatic aldehydes as bridging reagents, thus avoiding toxic formaldehyde usually employed for this purpose. However, an excess of concentrated H2SO4 (ca. 3
:
1) was required to achieve yields in the range 5–69%, which decreased upon increasing the number of methoxy substituents. This clearly reduces the feasibility of bulkier TPs as precursors for polymers. Indeed, epoxy thermosets were prepared using TPs with up to four methoxy groups, which exhibited excellent glassy moduli and glass transition temperatures, which was attributed to the rigidity of the TP scaffold. An increase in the number of methoxy groups decreased the Tg value (132–118 °C) and the glassy modulus (2.7–2.2 GPa), in this case.
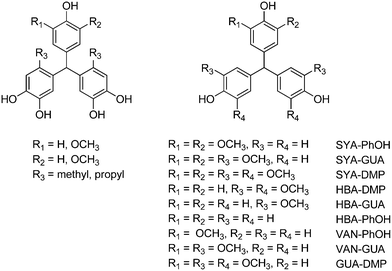 |
| Scheme 28 Structures of triphenol TPs. | |
5.2.2. 4-n-Propylsyringol.
Similar to that described above for 4-n-propylguaiacol, the bissyringol 5,5′-methylenebis(4-n-propylsyringol) (m,m′-BSF-4P) was isolated in 60% yield and 99% purity, by condensation of 4-n-propylsyringol (obtained by catalytic hydrogenolysis of hardwood lignin over Ru@C; a detailed study was provided) with formaldehyde using HCl as a catalyst (Scheme 24).422 Compared to BPA, the bissyringyl scaffold showed lower potency and efficacy toward human estrogen receptor α. The presence of the bulky methoxy substituents in the 2,6-positions and the para-propyl side chain had two significant consequences: reduced tendency to form oligomers and high thermal resistance of the resulting polymers, which may be tentatively attributed to the hindered rotation. Indeed, m,m′-BSF-4P-based aromatic polyesters were synthesized in >90 wt% yield, showing glass-transition (157 °C) and degradation temperature (Td,5% 345 °C) values among the highest reported for lignin-based thermoplastics.
Table 5 summarises the main features of the catalytic processes detailed in the present review which lead to proposed BPA substitutes from sinapyl-derived compounds.
Table 5 Summary of recent catalytic systems for proposed BPA monomeric replacements from sinapyl-derived compoundsa
Catalyst |
Biomass-derived substrate |
Product |
Reaction conditions |
Conv.c (%) |
Sel.d (%) |
Prod.e (mmolprod gcat−1 h−1) |
Ref. |
Solventb (M) |
T (°C) |
See Section 5.2 for substrate and product numbering and labelling.
Reaction solvent, substrate concentration (M) in brackets.
Substrate conversion.
Selectivity to the product indicated.
Catalyst productivity to the product indicated.
Buffer.
Two-step reaction sequence, the first is an uncatalysed Wittig olefination.
Yield (%).
|
Laccase |
Sinapyl alcohol |
Syringaresinol |
CH3CN/H2Of |
50 |
100 |
93 |
30.4 |
412
|
p-TSAg |
Syringaldehyde |
DTMP-HS |
Toluene/methanol (n.a.) |
70 |
100 |
58 |
n.a. |
419
|
H2SO4 |
Syringaldehyde |
SYA-PhOH |
Ethanol (0.6) |
65 |
100 |
64 |
0.05 |
421
|
H2SO4 |
Syringaldehyde |
SYA-GUA |
Ethanol (0.6) |
65 |
100 |
46 |
0.03 |
421
|
H2SO4 |
Syringaldehyde |
SYA-DMP |
Ethanol (0.6) |
65 |
|
5h |
n.a. |
421
|
HCl |
4-n-Propylsyringol |
m,m′-BSF-4P |
H2O |
100 |
100 |
60 |
n.a. |
422
|
6. Substitutes from the hemicellulose depolymerisation chain
Hemicellulose is a group of branched heteropolysaccharides containing mainly pentose (xylose, arabinose), as well as hexose units (galactose, glucose, mannose).423,424 Hemicellulose is an amorphous polymer, hence more easily solubilised and attacked than cellulose. It represents a natural source of C5 carbohydrate platform molecules (xylose, xylitol, furfural), which are accessible by hydrolytic depolymerisation,425,426 followed by acid-catalysed dehydration or metal-catalysed reduction.427,428 In particular, furfural is obtainable from hemicellulose-derived xylose via challenging threefold acid-catalyzed dehydration, at high temperatures.429,430 Current production methods rely on aqueous phase mineral acid (H2SO4) treatment.431,432 Several key industrial intermediates and consumer chemicals are then available through further furfural processing.433,434
Thus, a bis-furanic diol was reported earlier, having a structure resembling that of BPA, and obtained by classical organic reaction from furoic acid and acetone, via mineral acid-mediated coupling and unviable LiAlH4 reduction (Scheme 29).435 The parent epoxy derivatives were synthesized.
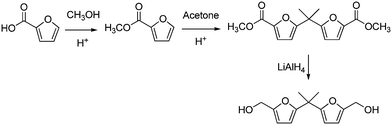 |
| Scheme 29 Synthesis of diols from furoic acid. | |
7. Substitutes from other biomass-derived sources
The catalytic synthesis of rigid diols has been described from naturally occurring, renewable raw materials other than lignocellulosic biomass. Table 6 summarises the main features of the catalytic processes hereinafter described leading to proposed BPA replacements from other biomass-derived sources.
Table 6 Summary of recent catalytic systems for proposed BPA monomeric replacements from other biomass-derived sourcesa
Catalyst |
Biomass-derived substrate |
Product |
Reaction conditions |
Conv.c (%) |
Sel.d (%) |
Prod.e (mmolprod gcat−1 h−1) |
Ref. |
Solventb (M) |
T (°C) |
H2 (bar) |
See Section 7 for substrate and product numbering and labelling.
Reaction solvent, substrate concentration (M) in brackets.
Substrate conversion.
Selectivity to the product indicated.
Catalyst productivity to the product indicated.
|
HCl |
Carvacrol |
6
|
H2O (0.9) |
80 |
— |
100 |
55 |
0.9 |
440
|
Oxalic acid |
Cardanol |
7
|
Free |
100 |
— |
n.a. |
n.a. |
n.a. |
449
|
Pd@C |
trans-Resveratrol |
Dihydroresveratrol |
THF |
r.t. |
0.5 |
100 |
98 |
n.a. |
450
|
Cu/Zn/Al |
4-Formylcyclohex-3-enecarboxylate |
CHDM |
Ethanol (0.6) |
240 |
40 |
100 |
76 |
2.3 |
460
|
Cyclic terpenes and terpenoids are other important sources of non-petrochemical phenols. They are obtained on a thousands of tons per year scale from trees, from essential oils or as by-products of the food and paper industries.436 Besides being extracted from plants, terpenoids may also be produced via chemical synthesis from terpenes. In particular, carvacrol is obtained from the essential oils of thyme and origanum,437,438 and synthetically from bio-sourced limonene (found in citrus fruit oils).439 The p,p′-isomer of the methylene-bridged bisphenol 6 shown in Scheme 30 was synthesized in high yields, by the HCl-catalyzed coupling of carvacrol with 1,3,5-trioxane.440 The bisphenol was used as building block for polycarbonates, cyanate ester and epoxy resins441 whose thermomechanical properties were evaluated, showing Tg values around 120 °C.
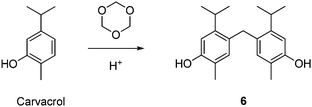 |
| Scheme 30 Synthesis of carvacrol-derived bisphenol 6. | |
Cashew nut shell liquid (CNSL) is a non-edible waste product of the cashew nut industry, whose yearly production is around 450 ktons.442,443 Crude CNSL consists of a mixture of phenol, resorcinol, 2,6-xylenol and salicylic acid derivatives having C-15 aliphatic side chains, with different unsaturation degrees.444,445 The main component of refined CNSL is cardanol.446 Several polymer and surfactant building blocks were prepared from cardanol. The topic has been reviewed in detail up to 2018.447,448
Lately, the cardanol-derived bisphenol 7 was prepared by conventional formaldehyde condensation using oxalic acid as a catalyst (Scheme 31).449 This was used in the synthesis of thermosetting epoxy resins that showed higher tensile strength and impact strength compared to the BPA-based congener.
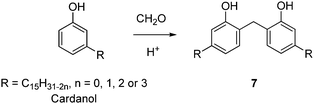 |
| Scheme 31 Synthesis of 7 from cardanol. | |
trans-Resveratrol, as well as its congeners cis-resveratrol and dihydroresveratrol, was used as a basis for cyanate ester thermosettings, showing very high Tg (>350 °C) and decomposition temperature (>400 °C), which are significantly higher than those of the BPA and BPE parents.450trans-Resveratrol is found in remarkable amounts in the skin of grapes, peanuts and Japanese knotweed.451,452 The structure of trans-resveratrol, shown in Scheme 32, consists of a stilbene scaffold bearing three hydroxyl groups, from which the cis isomer and the dihydro-derivative can be obtained by UV irradiation453 and usual Pd@C hydrogenation,454 respectively.
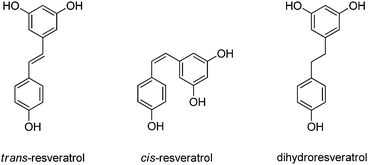 |
| Scheme 32 Structures of resveratrols. | |
Recently, several homo- and co-polymers were described containing the octahydro-2,5-pentalenediol (OPD) unit, which features a rigid bicyclic skeleton of fused cyclopentane rings (Scheme 33).455,456 This scaffold was aimed at increasing the thermal stability of the isosorbide core (Section 4.1), while retaining a similar rigidity. OPD can be prepared from naturally occurring citric acid, via dimethyl-1,3-acetonedicarboxylate and glyoxal, through a multiple reaction sequence of classical, un-catalysed organic reactions.457,458 Co-polycarbonates containing OPD, CHDM (see below) and diphenyl carbonate were synthesized, showing an increase in tensile modulus and glass transition temperature upon increasing the OPD content.459
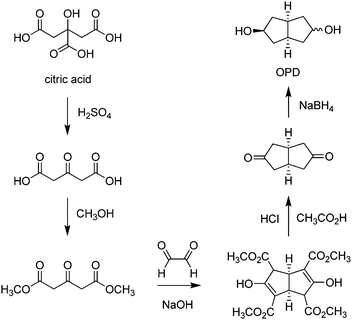 |
| Scheme 33 Synthesis of OPD from citric acid. | |
It is worth mentioning that cyclohexane oxygenates, such as 1,4-cyclohexanedimethanol (CHDM) and 1,4-cyclohexanedicarboxylic acid (CHDA), were obtained from biomass-derived raw materials and used in the synthesis of copolyesters.460 These monomers are usually prepared by hydrogenation of oil-based phthalic acids under harsh reaction conditions. A mild two-step procedure using crotonaldehyde, formaldehyde and ethyl acrylate, from biomass fermentation/gasification processes, afforded CHDM in 76% yield, as sketched in Scheme 34. In the first step, a one-pot proline-catalyzed [3+1+2] cycloaddition gave 4-formylcyclohex-3-enecarboxylate, which was then hydrogenated over commercial Cu/Zn/Al catalysts (240 °C, 4.0 MPa H2). An alternative hydrogenation, oxidation, and hydrolysis reaction sequence yielded 78% CHDA.
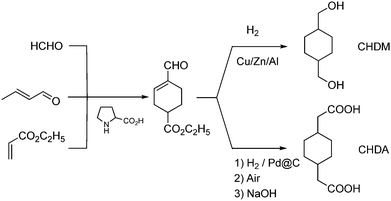 |
| Scheme 34 Biomass-derived synthesis of CHDM. | |
Although outside the timespan covered by the present review, it must be mentioned that BPA substitutes were also proposed from bio-sourced gallic acid (from hydrolyzable tannins found in several flowering plants),461 hydroxytyrosol (from oleuropein found in argan oil, olive oil and olive leaves),462 anethole and other substrates.
Anethole, predominantly in the trans form, is a flavouring aromatic compound found in the essential oils of several plants, including anise, fennel liquorice and star anise. The latter oil contains more than 90% anethole and it is produced on a hundreds of tons per year scale.463 A peculiar rigid monomer has been reported based on a cis-fused ring diphenol (8) obtained from anethole in two steps: strong acid treatment, followed by demethylation (Scheme 35). Low overall yields were, however, observed, wherein stoichiometric use of dangerous reagents (H2SO4, pyridine, phosphorus oxychloride) was required.464
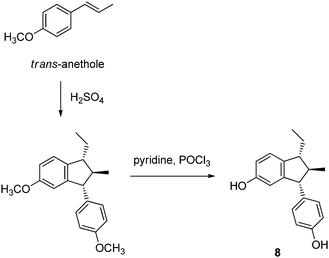 |
| Scheme 35 Synthesis of diphenol 8. | |
The bisphenols shown in Scheme 36 were obtained in good yields by the acid-catalysed condensation of phenol with lactic acid-derived 2,3-pentanedione.465,466 In turn, lactic acid can be produced catalytically from bio-sourced polysaccharides.467,468 Interestingly, homogeneous and heterogeneous sulfonic acid catalysts could be used for this purpose, wherein the reusability of insoluble ones (e.g. Nafion NR50) was demonstrated. The as-prepared bisphenols were coupled with PET to afford polyesters with improved thermal properties, compared to the BPA analogues.
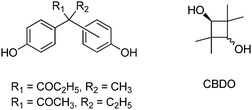 |
| Scheme 36 Structures of 2,3-pentanedione-derived bisphenols and CBDO. | |
2,2,4,4-Tetramethylcyclobutan-1,3-diol (CBDO, Scheme 36) and its derivatives have been recently used to replace BPA in commercial copolyesters, including Tritan™, PETF,469 PPTF, PBTF470 and PECTF.471 The incorporation of these cyclic diols resulted in the improved thermal and mechanical properties of the polymers. However, CBDO is obtained from petroleum derived isobutyric anhydride.472 In 2012 a synthesis of CBDO was proposed via Meldrum's acid, starting from bio-based malonic acid, through a complex eight-step procedure, wherein a catalytic C
C hydrogenation was achieved over Pd@C.473
Finally, it is worth mentioning that, while submitting the present review, at least two notable contributions appeared describing the selective hydrogenation of HMF to BHMF over a bimetallic Ni–Re@TiO2474 catalyst and the continuous flow hydrogenation of vanillin to vanillyl alcohol over Ni@porous nitrogen-doped carbon,475 respectively. Further, the synthesis of the unconventional m,p′-BGF and o,p′-BGF isomers was achieved by condensation of guaiacol with bio-derived isovanillyl and ortho-vanillyl alcohol, respectively.476 The oestrogenic activity of p,p′-BGF was also shown to be two orders of magnitude lower than that of the p,p′-BPF homologue, thus confirming the beneficial effect of ortho-methoxy substituents on the toxicity of bis-phenols. The readers may refer to the relevant literature for details.
8. Conclusions and future perspectives
Polymers are an important component of our society, contributing to the improvement of the quality of our life. Yet, they pose severe environmental issues.477,478 Most commercial polymers are produced from fossil sources and disposed within relatively short periods, compared to the long time required for their biodegradation, if any. Still, they may contain or release components toxic to human health and the environment. An alternative and renewable supply of carbon feedstock is embedded in polysaccharides, lignin, terpenes, and other small molecules available from plants. From these matters it is possible to produce a large part of the chemicals currently manufactured form oil, including polymers. A clear industrial example is 2,5-furandicarboxylic acid, used to replace noxious terephthalic acid in plastic bottles, and obtained from biomass via glucose conversion.479,480 Significant improvements are needed in the identification of abundant crops not competing with the food industry, including a better use of agricultural and forestry waste, and in the conversion of these crops into useful platforms through sustainable and safer processes.
Synthetic strategies for BPA replacements from biomass
A perusal of the literature highlights the great potential of catalysis, and the significant advancements achieved, in the synthesis of building blocks for polymers manufactured from biomass and its derivatives. A variety and a number of potential BPA substitutes have been made available through catalytic methods, using platform raw materials mostly originating from cellulose and lignin deconstruction processes. While cellulose is the source of furanic and alicyclic rigid diols, a spectrum of bis-phenols featuring hindered rotation is accessible from lignin. These bio-based diols have been demonstrated to be key building blocks in the design and synthesis of high-performance plastic materials, characterised by improved thermal and mechanical stabilities.
Since cellulose is a regular, monosaccharide-based polymer, a variety of catalysts and strategies have been developed allowing for the upgrade of cellulose-derived sugars to specific building blocks based on these units, each with its own advantages. Significant advancements were recently offered in the engineering of heterogeneous catalysts, often sophisticated, featuring high efficiency in the conversion of cellulose-derived platforms (sugar alcohols, HMF) to rigid diols, sometimes using concentrated aqueous solution feeds. Several catalytic systems have been demonstrated, enabling dehydration and hydrogenation steps. Still, by surveying the recent literature, a number of major challenges may be identified in this field. Challenge one: in order to be transferred from the bench to the industrial scale, catalysts should be available in appropriate amounts at competitive costs and, possibly, implemented into existing reactor plants. Therefore, a desirable achievement is the sustainable manufacture of heterogeneous catalysts based on non-critical support raw materials and non-noble metals.481,482 Moreover, besides costs and efficiency, catalyst resistance is also considered as a crucial issue. Most reports claim catalyst recyclability; however, parameters such as selectivity drop, changes in reaction kinetics upon catalyst reuse, metal leaching, long-term productivity and the need for catalyst regeneration are not always evaluated quantitatively.483,484 Challenge two: a major weakness of the above processes, particularly if intermediate conversion products are targeted, is selectivity under mild reaction conditions.485 This is critical for industrial applications, wherein minimisation of energy inputs shall couple with reduced downstream processing (i.e. separation, purification). Use of organic solvents often used for this purpose,486,487 as well as for the enhancement of substrate/product solubility, should also be avoided in favour of (concentrated) original water solutions. Great potential for selectivity improvement may be provided by catalysis under continuous flow conditions, because of the possibility for a careful control of reaction conditions, namely contact time with the catalyst and homogeneous heating.488 Challenge three: design of novel catalysts enabling efficient multistep cascade processes in one-pot. This would open up the possibility for process intensification via direct conversion of cellulose to target chemicals, while avoiding intermediate conventional mineral acid depolymerisation protocols.489 The engineering of truly heterogeneous bifunctional catalysts, wherein acidic and metal functionalities are comprised in a single catalytic body, will be both critical and intriguing to this aim. The efficiency of such catalysts is ruled by the fine tuning of diverse factors and their interplay: nature of metal, type and strength of acidic sites, balance of acid and metal loading, and site accessibility. Actually, examples have already been reported for the direct upgrade of cellulose without isolation of intermediate streams, for instance in the case of isosorbide synthesis (Section 4.1.3). However, these systems underperform with respect to carbon balance, mostly due to the significant formation of cellulose acidic depolymerisation by-products (humins, levulinates, oligomers) and dehydration isomers. This is partially due to the mixtures of supported metals and soluble acid catalysts often used to this aim.490,491 Therefore, the development of innovative solid acid catalysts will be of utmost importance in the biorefinery industry,492,493 provided that high acidic-site density and tolerance to water and to medium to high temperatures are ensured. Indeed, the conventional sulfonated resin catalysts used in the acid-catalysed depolymerisation steps suffer from limited thermal resistance. This may be circumvented, for example, using inorganic niobia or polymeric perfluorosulfonic acids.494,495 Further, the engineering of single (continuous flow) processing lines, in which specialised molecules are directly obtained from upstream substrates, would be highly desirable, e.g. combining supported enzymatic catalysis (for depolymerisation) and inorganic catalysis (for the upgrade of the intermediate platforms).496,497 Innovative solid support materials, with improved stability, mass transport properties and efficient processing, are thus required. This may be the case of unconventional, inorganic monoliths featuring interconnected dual porosities (meso, macro).498,499 Finally, the existing gap in catalysis between the laboratory scale and the validation scale at the industrial readiness level shall be bridged in most cases.
By contrast, lignin is a very complex polymer which results in a variety of chemicals by deconstruction, depending on the biomass source and the method, and hardly reducible to single platform molecules. As a consequence, despite the huge amount of lignin available, its potential for chemical synthesis is still underutilised. Despite the recent remarkable advancements, e.g. reductive catalytic fractionation or catalytic oxidative depolymerization methods,410,500 here the bottleneck is the immature technology for the selective depolymerisation of lignin and the conversion to the desired platforms.501,502 The further step is the upgrade of lignin platforms to potential BPA substitutes, which at present is often available through unexceptional organic methods, however. Indeed, recent advancements, although significant, restrict to the adoption of zeolite or enzyme catalysts for the synthesis of diphenolic scaffolds from monolignol units.397 Herein some challenges can be identified. Challenge one: development of improved technologies for the selective conversion of lignin to chemicals, economically and sustainably. These new solutions shall optimise the utilisation of heterogeneously composed raw materials, while enabling the large-scale production of bulk chemicals for the process industry. Challenge two: development of catalytic deconstruction technologies affording novel building blocks, other than monolignol-derived monomers, directly from lignin, i.e. bis-phenols as in the case of naturally occurring BPF,503 SYR and lignans.504,505 Challenge three: most proposed BPA replacements from lignin are based on bis-phenol moieties. However, with the few notable exceptions outlined above, they are usually synthesized via conventional, sometimes uncatalysed, organic reactions. Typical is the case of C1-bridged bis-phenols obtained by formaldehyde coupling, using soluble mineral acids (H2SO4 and HCl) and, often, noxious or unstable solvents (see Tables 4–6). Thus, inventive solutions are needed, which avoid use of toxic reagents and media and which comply with the principles of green and sustainable chemistry. Novel rigid scaffolds have to be designed, for instance mimicking natural molecules and built upon C0-linked phenols or fused rings.504 Use of Brønsted acid solid catalysts would be, once again, highly beneficial in this case too.
As emerged from the literature, several other BPA replacements may be produced from the catalytic conversion of other biomass sources. Some specific challenges may be envisaged. Challenge one: to increase the scenario of available platforms and production of BPA replacements, featuring structure alternatives to monosaccharide or phenol-based ones. High-throughput screening methods are expected to be particularly useful to this aim. Herein, possibilities are plenty, provided that the amount of raw material is suitable for industrial use. From that, a second challenge is closely related: to improve the uptake of unconventional, non-edible biomass sources, such as algae, biorefinery side-streams and waste (food, agricultural). The role of catalysis will be crucial in developing flexible and sustainable conversion routes in this direction.
Properties of BPA monomer replacements and derived polymers
Although the present review does not explicitly cover the specific properties of monomers aiming at the manufacture of polymers with improved performances, rather the catalytic synthesis of the monomers themselves, some challenges may be inferred from the literature targeting a rational design of effective BPA replacements. They can be briefly summarised herein. Challenge one: are the proposed BPA replacements really safe? Before evaluating the potential for use in sustainable polymer synthesis, novel building blocks should undergo preliminary (endocrine) toxicity tests. This particularly concerns phenolic scaffolds, due to the known adverse health effects.506,507 The absence of relevant data is not proof for safety. Hence, caution must be exercised whenever replacing chemicals of known toxicity, with others of unknown toxicity. We scrutinized the data available from ECHA for all BPA substitutes described in the present review. The Harmonised Classification and Labelling of Hazardous Substances reported at the time of publication are collected in the ESI,† Tables S1 and S2. With very few exceptions, a perusal of these tables shows that very little is known about the toxicity of most of the proposed BPA replacements. Indeed, no hazards have been classified in the REACH register only for isosorbide and isomannide. All other chemicals are not registered (mostly), pre-registered or registered in Annex III (i.e. substances predicted or suspected to meet hazard criteria). This means that most of the claimed BPA substitutes are actually “potential” substitutes, at least from a hazard point of view, and that this gap must be filled by further data.508,509 On the other hand, additional issues shall be considered in this regard. In some cases, e.g. cashew nutshell phenols,510,511 processable feedstock is toxic, which complicates their effective use on the industrial scale. Also, the endocrine activity of most replacement candidates was shown to be ruled by a combination of subtle factors. For instance, evidence indicates that the presence of ortho methoxy substituents in bis-phenols reduces their activity.476 Further screenings are thus highly recommended, eventually extended to various receptors. Challenge two: are the suggested BPA replacements viable? As outlined in Section 3.1, once safety criteria are met, chemical substitution at large should be offered at competitive costs, compared to existing technologies. From a catalysis point of view, this includes evaluation of the cost of catalysts, the long term productivity and selectivity of catalysts, the cost of feedstock pre-treatment (if any) and downstream processing, and the availability of raw materials. This requires a techno-economic analysis which is seldom performed.186,387 Other relevant parameters are the sustainability and environmental impact of production. Key enabling technologies, such as bifunctional or continuous flow catalysis, the use of concentrated water solutions and mild reaction conditions, would contribute substantially to this end, but still underutilised for the synthesis of monomers from biomass, see e.g.Tables 1–6. Challenge three: are the proposed replacements equally relevant to the synthesis of polymers? What is offered by the present overview is a panorama of suitable monomers for BPA substitutions. It is then the duty of polymer chemists to make a selection of appropriate scaffolds and strategies targeted at the obtainment of polymers with the desired properties. This will end up in the identification of novel industrially relevant chemical building blocks. However, this requires a more detailed molecular level understanding of structure–function relationships. For instance, in the case of BPA replacements, a “rigid structure” is a requirement that refers to a rather vague attribute, lacking detailed molecular descriptors. Computer-aided molecular simulations may help in addressing this point. Further, in most cases, the proposed substitutes indeed have been shown to result in polymers with the desired stability and thermoplastic properties, however with very different reactivities and processabilities, which sometimes hamper their effective use in the manufacture of polymers. This may be the case of triphenylmethane polyphenols.420 Challenge four: once the toxicity, viability and effectiveness of proposed BPA substitutes are ascertained, it would be essential to perform degradation tests of the derived polymers. Deconstruction of polymers into low molecular weight, useful compounds or reusable monomers would help in addressing a circular economy of plastics, which is usually achieved (when possible) via enzymatic biocatalysis,512,513 and, more recently, via organo514,515 or metal-based catalysis.516,517
In conclusion, the results reported in the recent literature describing catalysts and approaches for the synthesis of monomers from biomass that are proposed as BPA replacements and that are collected in the present review provide a large choice of potential candidates for substitution. While quite advanced catalytic systems are available for the upgrade of cellulose-derived feeds, the conversion of platforms originating from lignin still needs significant improvements, mostly due to the inherent complexity of lignin materials. In addition, further studies should be performed aiming at a careful evaluation of compliance with the viability and effectiveness criteria of the proposed BPA replacements, whose extension to chemical substitution, in general, would contribute to a safer and more sustainable future.
List of acronyms
BGF | Bisguaiacol F |
m,m′-BGF-4P | 5,5′-Methylenebis(4-n-propylguaiacol) |
BHMC | Bisphenol hydroxy methyl carbonate |
BHMF | 2,5-Bis(hydroxymethyl)furan |
BHMTHF | 2,5-Bis(hydroxymethyl)tetrahydrofuran |
BPA | Bisphenol A |
BPAF | 2,2-Bis(4-hydroxyphenyl)hexafluoropropane |
BPF | 4,4′-Methylenediphenol |
BPS | Bis(4-hydroxyphenyl)sulfone |
BILs | Brønsted acidic ionic liquids |
m,m′-BSF-4P | 5,5′-Methylenebis(4-n-propylsyringol) |
CBDO | 2,2,4,4-Tetramethylcyclobutan-1,3-diol |
CHDA | 1,4-Cyclohexanedicarboxylic acid |
CHDM | 1,4-Cyclohexanedimethanol |
CNF | Carbon nanofibers |
CNSL | Cashew nut shell liquid |
CNT | Carbon-nanotubes |
CTH | Catalytic transfer hydrogenation |
DBU | 1,8-Diazabicyclo[5.4.0]undec-7-ene |
DMC | Dimethyl carbonate |
DMF |
N,N-Dimethylformamide |
DPA |
p,p′-Diphenolic acid |
DTMP | Di(trimethylolpropane) |
ECHA | European Chemical Agency |
GBL | γ-Butyrolactone |
HCPO | 3-Hydroxymethylcyclopentanol |
HHCPEN | 4-Hydroxy-4-(hydroxymethyl)-cyclopenten-2-one |
HMF | 5-Hydroxymethylfurfural |
HT | Hydrotalcite |
IDF | Bis-o-dihydroferuloyl isosorbide |
LDH | Layered double hydroxide |
MIBK | Methyl isobutyl ketone |
MPTS | (3-Mercaptopropyl)trimethoxysilane |
MST | Mesoporous sulfated titania |
NHC | N-Heterocyclic carbene |
OPD | Octahydro-2,5-pentalenediol |
PET | Polyethylene terephthalate |
PEIT | Poly-(ethylene-co-isosorbide)terephthalate |
PIC | Poly(isosorbide carbonate) |
PMHS | Polymethylhydrosiloxane |
PMO | Periodic mesoporous organosilica |
TGA | Thermogravimetric analysis |
TOF | Turnover frequency |
TPA | Diethylene triaminepenta(methylene)phosphonic acid |
TPT-OMe | 5-Methoxy-1,3,4-triphenyl-4,5-dihydro-1H-1,2,4-triazoline |
p-TsOH |
p-Toluenesulphonic acid |
REACH | Registration, Evaluation, Authorisation and Restriction of Chemicals |
SDG | Sustainable development goals |
SHTC | Sulfonated hydrothermal carbon |
SVHCs | Substances of very high concern |
SYR | Syringaresinol |
SYR-EPO | Diepoxy syringaresinol |
TPs | Triphenylmethane polyphenols |
WHSV | Weight-hourly-space-velocity |
ZrP | Zirconium phosphate |
Conflicts of interest
There are no conflicts to declare.
Notes and references
-
PlasticsEurope, Association of Plastics Manufacturers, Plastics – the Facts 2018, Brussels, 2018 Search PubMed.
- L. M. Heidbreder, I. Bablok, S. Drews and C. Menzel, Sci. Total Environ, 2019, 668, 1077–1093 CrossRef CAS PubMed.
- T. Narancic and K. E. O’Connor, Microbiology, 2019, 165, 129–137 CrossRef CAS PubMed.
- R. V. Moharir and S. Kumar, J. Cleaner Prod., 2019, 208, 65–76 CrossRef CAS.
- N. Raddadi and F. Fava, Sci. Total Environ, 2019, 679, 148–158 CrossRef CAS PubMed.
- S. L. Wright and F. J. Kelly, Environ. Sci. Technol., 2017, 51, 6634–6647 CrossRef CAS PubMed.
- R. Lehner, C. Weder, A. Petri-Fink and B. Rothen-Rutishauser, Environ. Sci. Technol., 2019, 53, 1748–1765 CrossRef CAS PubMed.
- J. Zheng and S. Suh, Nat. Clim. Change, 2019, 9, 374–378 CrossRef.
- A. Dormer, D. P. Finn, P. Ward and J. Cullen, J. Cleaner Prod., 2013, 51, 133–141 CrossRef CAS.
- K. Ragaert, L. Delva and K. Van Geem, Waste Manage., 2017, 69, 24–58 CrossRef CAS PubMed.
-
P. Thomas, N. P. Rumjit, C. W. Lai, M. R. B. Johan and M. P. Saravanakumar, Polymer-Recycling of Bulk Plastics in Reference Module in Materials Science and Materials Engineering, Elsevier, 2019 Search PubMed.
- For the IUPAC definition of biobased polymers, see: M. Vert, Y. Doi, K. H. Hellwich, M. Hess, P. Hodge, P. Kubisa, M. Rinaudo and F. Schué, Pure Appl. Chem., 2012, 84, 377–410 CAS.
- T. P. Haider, C. Völker, J. Kramm, K. Landfester and F. R. Wurm, Angew. Chem., Int. Ed., 2019, 58, 50–62 CrossRef CAS PubMed.
- S. Spierling, E. Knüpffer, H. Behnsen, M. Mudersbach, H. Krieg, S. Springer, S. Albrecht, C. Herrmann and H. J. Endres, J. Cleaner Prod., 2018, 185, 476–491 CrossRef.
- D. K. Schneiderman and M. A. Hillmyer, Macromolecules, 2017, 50, 3733–3749 CrossRef CAS.
-
World Economic Forum, Ellen MacArthur Foundation and McKinsey & Company, The New Plastics Economy – Rethinking the future of plastics, 2016 Search PubMed.
- Organisation for Economic Cooperation and Development, Policies for Bioplastics in the Context of a Bioeconomy, OECD Science, Technology and Industry Policy Papers, No. 10, OECD Publishing, Paris, 28 October 2013.
- United Nations General Assembly, Transforming our world: the 2030 Agenda for Sustainable Development, A/RES/70/1, 21 October 2015.
- European Commission, A European Strategy for Plastics in a Circular Economy, COM(2018) 28 final, Brussels, 16 January 2018.
- United Sates Environmental Protection Agency, Sustainable Materials Management Program Strategic Plan, Fiscal Year 2017–2022, October 2015.
- Sustainable Process Industry through Resource and Energy Efficiency, SPIRE Roadmap 2030, Brussels, 2019.
- Bio-based Industries Consortium, Strategic Innovation and Research Agenda, Brussels, May 2017.
- European Bioplastics, Industrial use of agricultural feedstock, Berlin, January 2019.
- The European Chemical Industry Council, Innovation can impact the European Strategy for Plastics, Brussels, April 2019.
- SusChem – European Technology Platform for Sustainable Chemistry, Strategic Innovation and Research Agenda, Brussels, 2017.
-
U. Gundert-Remy, J. Bodin, C. Bosetti, R. FitzGerald, A. Hanberg, U. Hass, C. Hooijmans, A. A. Rooney, C. Rousselle, H. van Loveren, D. Wölfle, F. Barizzone, C. Croera, C. Putzu and A. F. Castoldi, Bisphenol A (BPA) hazard assessment protocol, European, Food Safety Authority (EFSA), EFSA supporting publication 2017:EN-1354, 2017 Search PubMed.
- A. Llevot, E. Grau, S. Carlotti, S. Grelier and H. Cramail, Macromol. Rapid Commun., 2016, 37, 9–28 CrossRef CAS PubMed.
- A. M. Nelson and T. E. Long, Polym. Int., 2012, 61, 1485–1491 CrossRef CAS.
- F. Ng, G. Couture, C. Philippe, B. Boutevin and S. Caillol, Molecules, 2017, 22, 149–197 CrossRef PubMed.
- S. Ma, T. Li, X. Liu and J. Zhu, Polym. Int., 2016, 65, 164–173 CrossRef CAS.
- D. J. Burke, T. Kawauchi, M. J. Kade, F. A. Leibfarth, B. McDearmon, M. Wolffs, P. H. Kierstead, B. Moon and C. J. Hawker, ACS Macro Lett., 2012, 1, 1228–1232 CrossRef CAS.
- M. Habib, M. Trajkovic and M. W. Fraaije, ACS Catal., 2018, 8, 5549–5552 CrossRef CAS PubMed.
- A. de Angelis, P. Ingallina and C. Perego, Ind. Eng. Chem. Res., 2004, 43, 1169–1178 CrossRef CAS.
- F. W. Neumann and W. E. Smith, J. Org. Chem., 1966, 31, 4318–4320 CrossRef CAS.
- U.S. Department of Health and Human Services, Toxicological profile for phenol, Agency for Toxic Substances and Disease Registry, Atlanta, Georgia, September 2008.
- Eco-profiles and Environmental Product Declarations of the European Plastics Manufacturers – Bisphenol A (BPA), PlasticsEurope, Brussels, January 2019.
- K. Shimizu, S. Kontani, S. Yamada, G. Takahashi, T. Nishiyama and A. Satsuma, Appl. Catal., A, 2010, 380, 33–39 CrossRef CAS.
-
H. M. Belfadhel, J. Brouwer, M. Vieveen, C. Wold and E. Brander, WO061274A1, 2013.
-
G. M. Kissinger and N. P. Wynn, US5362900, 1994.
-
P. Czub, in Bisphenol-A in Handbook of Engineering and Specialty Thermoplastics, Volume 3: Polyethers and Polyesters, ed. T. Sabu and P. M. Visakh, Wiley, 2011, ch. 7 Search PubMed.
- Bisphenol A (BPA) Market Analysis By Application (Polycarbonates, Epoxy resins) Regional and Segment Forecasts To 2025, Report ID 978-1-68038-169-6, Grand View Research Inc., San Francisco, June 2015.
- Bisphenol A (BPA) Market – Growth, Trends, and Forecast (2019–2024), Report ID 4520075, Research and Markets, Dublin, April 2019.
- Data from http://bisphenol-a-europe.org/, accessed 18 July 2019.
- European Chemicals Agency, Use of bisphenol A and its alternatives in thermal paper in the EU – 2018 update, Helsinki, June 2019.
- X. Xua, S. Zong, W. Chen and D. Liu, Chem. Eng. J., 2019, 369, 470–479 CrossRef.
- P. V. L. Reddy, K. H. Kim, B. Kavitha, V. Kumar, N. Raza and S. Kalagara, J. Environ. Manage., 2018, 213, 189–205 CrossRef CAS PubMed.
- A. A. Jones, Macromolecules, 1985, 18, 902–906 CrossRef CAS.
- E. Can, S. Kusefoglu and R. P. Wool, J. Appl. Polym. Sci., 2002, 83, 972–980 CrossRef CAS.
- J. Wei, S. Ma, H. Yue, S. Wang and J. Zhu, Macromol. Res., 2018, 26, 529–538 CrossRef CAS.
- K. Sommer, J. Batoulis, W. Jilge, L. Morbitzer, B. Pittel, R. Plaetschke, K. Reuter, R. Timmermann, K. Binder, W. Paul, F. T. Gentile, D. W. Heermann, K. Kremer, M. Laso, U. W. Suter and P. J. Ludovice, Adv. Mater., 1991, 3, 590–599 CrossRef CAS.
- C. Berti, M. Colonna, M. Fiorini, C. Lorenzetti and P. Marchese, Macromol. Mater. Eng., 2004, 289, 49–55 CrossRef CAS.
- C. Koning, J. Wildeson, R. Parton, B. Plum, P. Steeman and D. J. Darensbourg, Polymer, 2001, 42, 3995–4004 CrossRef CAS.
- W. J. Choi, R. K. Bay and A. J. Crosby, Macromolecules, 2019, 52, 7489–7494 CrossRef CAS.
- D. Freitag, G. Fengler and L. Morbitzer, Angew. Chem., Int. Ed. Engl., 1991, 30, 1598–1610 CrossRef.
- J. Karger-Kocsis, O. Gryshchuk and N. Jost, J. Appl. Polym. Sci., 2003, 88, 2124–2131 CrossRef CAS.
- A. Shareef, M. J. Angove, J. D. Wells and B. B. Johnson, J. Chem. Eng. Data, 2006, 51, 879–881 CrossRef CAS.
-
M. Zielinska, I. Wojnowska-Baryla and A. Cydzik-Kwiatkowska, Bisphenol A Removal from Water and Wastewater, Springer, 2019, ch. 2 Search PubMed.
- S. Borrirukwisitsak, H. E. Keenan and C. Gauchotte-Lindsay, Int. J. Environ. Sci. Dev., 2012, 3, 460–464 CrossRef.
- J. Im and F. E. Löffler, Environ. Sci. Technol., 2016, 50, 8403–8416 CrossRef CAS PubMed.
- J. Corrales, L. A. Kristofco, W. B. Steele, B. S. Yates, C. S. Breed, E. S. Williams and B. W. Brooks, Dose-Response, 2015, 3, 1–29 Search PubMed.
- C. Brede, P. Fjeldal, I. Skjevrak and H. Herikstad, Food Addit. Contam., 2003, 20, 684–689 CrossRef CAS PubMed.
- P. Mercea, J. Appl. Polym. Sci., 2009, 112, 579–593 CrossRef CAS.
- J. H. Kang, K. Kito and F. Kondo, J. Food Prot., 2003, 66, 1444–1447 CrossRef CAS PubMed.
- Y. Takao, H. C. Lee, S. Kohra and K. Arizono, J. Health Sci., 2002, 48, 331–334 Search PubMed.
- C. Nerìn, C. Fernández, C. Domeňo and J. Salafranca, J. Agric. Food Chem., 2003, 51, 5647–5653 CrossRef PubMed.
- K. A. Ehlert, C. W. E. Beumer and M. C. E. Groot, Food Addit. Contam., 2008, 25, 904–910 CrossRef CAS PubMed.
- J. N. Hahladakis, C. A. Velis, R. Weber, E. Iacovidou and P. Purnell, J. Hazard. Mater., 2018, 344, 179–199 CrossRef CAS PubMed.
- E. J. Hoekstra and C. Simoneau, Crit. Rev. Food Sci. Nutr., 2013, 53, 386–402 CrossRef CAS PubMed.
- N. C. Maragou, A. Makri, E. N. Lampi, N. S. Thomaidis and M. A. Koupparis, Food Addit. Contam., 2008, 25, 373–383 CrossRef CAS PubMed.
- A. B. Paula, D. Toste, A. Marinho, I. Amaro, C. M. Marto, A. Coelho, M. Marques-Ferreira and E. Carrilho, Int. J. Environ. Res. Public Health, 2019, 16, 1627–1647 CrossRef CAS PubMed.
- A. F. Fleisch, P. E. Sheffield, C. Chinn, B. L. Edelstein and P. J. Landrigan, Pediatrics, 2010, 126, 760–768 CrossRef PubMed.
- J. Rovira and J. L. Domingo, Environ. Res., 2019, 168, 62–69 CrossRef CAS PubMed.
- S. Biedermann, P. Tschudin and K. Grob, Anal. Bioanal. Chem., 2010, 398, 571–576 CrossRef CAS PubMed.
- B. Alves Rocha, L. Ferreira Azevedo, M. Gallimberti, A. Dobal Campiglia and F. Barbosa Jr., J. Toxicol. Environ. Health, Part A, 2015, 78, 1181–1188 CrossRef PubMed.
- J. Lopez-Cervantes and P. Paseiro-Losada, Food Addit. Contam., 2003, 20, 596–606 CrossRef CAS PubMed.
- A. Ozaki, A. Yamaguchi, T. Fujita, K. Kuroda and G. Endo, Food Chem. Toxicol., 2004, 42, 1323–1337 CrossRef CAS PubMed.
- E. M. Munguía-López, S. Gerardo-Lugo, E. Peralta, S. Bolumen and H. Soto-Valdez, Food Addit. Contam., 2005, 22, 892–898 CrossRef PubMed.
- M. Lorber, A. Schecter, O. Paepke, W. Shropshire, K. Christensen and L. Birnbaum, Environ. Int., 2015, 77, 55–62 CrossRef CAS PubMed.
- A. Schecter, N. Malik, D. Haffner, S. Smith, T. R. Harris, O. Paepke and L. Birnbaum, Environ. Sci. Technol., 2010, 44, 9425–9430 CrossRef CAS PubMed.
- A. Ballesteros-Gómez, S. Rubio and D. Pérez-Bendito, J. Chromatogr. A, 2009, 1216, 449–469 CrossRef PubMed.
- L. N. Vandenberg, R. Hauser, M. Marcus, N. Olea and W. V. Welshons, Reprod. Toxicol., 2007, 24, 139–177 CrossRef CAS PubMed.
- A. N. Edginton and L. Ritter, Environ. Health Perspect., 2009, 117, 645–652 CrossRef CAS PubMed.
- A. M. Calafat, J. Weuve, X. Ye, L. T. Jia, H. Hu, S. Ringer, K. Huttner and R. Hauser, Environ. Health Perspect., 2009, 117, 639–644 CrossRef CAS PubMed.
- S. Almeida, A. Raposo, M. Almeida-González and C. Carrascosa, Compr. Rev. Food Sci. Food Saf., 2018, 17, 1503–1517 CrossRef.
- Y. Ma, H. Liu, J. Wu, L. Yuan, Y. Wang, X. Du, R. Wang, P. W. Marwa, P. Petlulu, X. Chen and H. Zhang, Environ. Res., 2019, 176, 108575 CrossRef CAS PubMed.
- T. Geens, D. Aerts, C. Berthot, J. P. Bourguignon, L. Goeyens, P. Lecomte, G. Maghuin-Rogister, A. M. Pironnet, L. Pussemier, M. L. Scippo, J. Van Loco and A. Covaci, Food Chem. Toxicol., 2012, 50, 3725–3740 CrossRef CAS PubMed.
- N. K. Wilson, J. C. Chuang, M. K. Morgan, R. A. Lordo and L. S. Sheldon, Environ. Res., 2007, 103, 9–20 CrossRef CAS PubMed.
- M. Giulivo, M. de Lopez Alda, E. Capri and D. Barceló, Environ. Res., 2016, 151, 251–264 CrossRef CAS PubMed.
- P. Alonso-Magdalena, A. B. Ropero, S. Soriano, M. García-Arévalo, C. Ripoll, E. Fuentes, I. Quesada and Á. Nadal, Mol. Cell. Endocrinol., 2012, 355, 201–207 CrossRef CAS PubMed.
- J. Apau, A. Acheampong and E. Adua, Cogent Chem., 2018, 4, 1506601 Search PubMed.
- L. A. Hoepner, Environ. Res., 2019, 173, 54–68 CrossRef CAS PubMed.
- S. Rahmani, N. P. Khalili, F. Khan, S. Hassani, E. Ghafour-Boroujerdi and M. Abdollahi, Life Sci., 2018, 214, 136–144 CrossRef CAS PubMed.
- M. H. Sowlat, S. Lotfi, M. Yunesian, R. Ahmadkhaniha and N. Rastkari, Environ. Sci. Pollut. Res., 2016, 23, 21125–21140 CrossRef CAS PubMed.
- D. D. Seachrist, K. W. Bonk, S. M. Ho, G. S. Prins, A. M. Soto and R. A. Keri, Reprod. Toxicol., 2016, 59, 167–182 CrossRef CAS PubMed.
- S. A. Hafezi and W. M. Abdel-Rahman, Curr. Mol. Pharmacol., 2019, 12, 230–238 CrossRef CAS PubMed.
- C. J. Carter and R. A. Blizard, Neurochem. Int., 2016, 101, 83–109 CrossRef CAS PubMed.
- C. S. Rosenfeld, Front. Neuroendocrinol., 2017, 47, 123–133 CrossRef CAS PubMed.
- L. Mínguez-Alarcón, R. Hauser and A. J. Gaskins, Fertil. Steril., 2016, 106, 864–870 CrossRef PubMed.
- J. S. Siracusa, L. Yin, E. Measel, S. Liang and X. Yu, Reprod. Toxicol., 2018, 79, 96–123 CrossRef CAS PubMed.
- J. R. Rochester, Reprod. Toxicol., 2013, 42, 132–155 CrossRef CAS PubMed.
- E. Matuszczak, M. D. Komarowska, W. Debek and A. Hermanowicz, Int. J. Endocrinol., 2019, 4068717 CAS.
- European Commission Joint Research Centre, Institute for Health and Consumer Protection, Updated European Risk Assessment Report, 4,4′-Isopropylidenediphenol – Part 1 Environment, Ispra, 2010.
- C. A. Staples, P. B. Dom, G. M. Klecka, S. T. O’Blook and L. R. Harris, Chemosphere, 1998, 36, 2149–2173 CrossRef CAS PubMed.
- J. H. Kang, D. Aasi and Y. Katayama, Crit. Rev. Toxicol., 2007, 37, 607–625 CrossRef CAS PubMed.
- J. Oehlmann, M. Oetken and U. Schulte-Oehlmann, Environ. Res., 2008, 108, 140–149 CrossRef CAS PubMed.
- L. Canesi and E. Fabbri, Dose-Response, 2015, 13, 1–14 CrossRef CAS PubMed.
- M. Bilal, H. M. N. Iqbal and D. Barceló, Sci. Total Environ, 2019, 689, 160–177 CrossRef CAS PubMed.
- S. Boudalia and M. Oudir, Res. J. Environ. Toxicol., 2016, 10, 189–192 CrossRef.
- Commission Implementing Regulation No. 321/2011 of 1 April 2011 amending Regulation (EU) No. 10/2011 as regards the restriction of use of Bisphenol A in plastic infant feeding bottles.
- LOI no. 2010-729 du 30 juin 2010 tendant à suspendre la commercialisation de tout conditionnement comportant du bisphénol A et destiné à recevoir des produits alimentaires. Version consolidée au 06 septembre 2019.
- Regulation (EC) No. 1907/2006 of the European Parliament and of the Council of 18 December 2006 concerning the Registration, Evaluation, Authorisation and Restriction of Chemicals (REACH), establishing a European Chemicals Agency, 2006.
- European Chemicals Agency, Inclusion of substances of very high concern in the Candidate List for eventual inclusion in Annex XIV, Helsinki, 2017.
- ECHA Substance information 4,4'-isopropylidenediphenol. https://echa.europa.eu/it/substance-information/-/substanceinfo/100.001.133, accessed 6 September 2019.
- Commission Regulation (EU) 2016/2235 of 12 December 2016 amending Annex XVII to Regulation (EC) No. 1907/2006 of the European Parliament and of the Council concerning the Registration, Evaluation, Authorisation and Restriction of Chemicals (REACH) as regards bisphenol A.
- Judgment of the General Court of 11 July 2019. Case T-185/17.
- California Office of Environmental Health Hazard Assessment (OEHHA), List of Chemicals as Known to the State of California to Cause Cancer or Reproductive Toxicity, Proposition 65 (1986). https://oehha.ca.gov/proposition-65/chemicals/bisphenol-bpa, accessed 6 September 2019.
- Assembly Bill 1319 (2011), Chapter 467.
- National Conference of State Legislatures (NCSL) Policy Update: State Restrictions on Bisphenol A (BPA) in Consumer Products. http://www.ncsl.org/research/environment-and-natural-resources/policy-update-on-state-restrictions-on-bisphenol-a.aspx, accessed 9 September 2019.
- Federal Register, Vol. 78, No. 134, July 12, 2013. Food and Drug Administration, Department of Health and Human Services, 21 CFR Part 175.
- Federal Register, Vol. 77, No. 137, July 17, 2012. Food and Drug Administration, Department of Health and Human Services, 21 CFR Part 177.
- United States Environmental Protection Agency, Bisphenol A Alternatives in Thermal Paper, Final Report, January 2014.
- Canada Gazette, Part II: Order Amending Schedule 1 to the Hazardous Products Act (Bisphenol A), March 31, 2010.
-
J. Tickner and M. Jacobs, Improving the Identification, Evaluation, Adoption and Development of Safer Alternatives: Needs and Opportunities to Enhance Substitution Efforts within the Context of REACH, University of Massachusetts, Lowell, 2016 Search PubMed.
- European Chemical Agency, Strategy to promote substitution to safer chemicals through innovation, Helsinki, 2018.
-
S. O. Hansson and C. Rudén, The Substitution Principle, Swedish Chemicals Agency, Stockholm, 2007 Search PubMed.
- R. Lofstedt, J. Risk Res., 2014, 17, 543–564 CrossRef.
-
J. M. Lohse, A. Wirts, K. Ahrens, S. Heitman, L. Lundie, A. Lissner and A. Wagner, Substitution of Hazardous Chemicals in Products and Processes. A report compiled for the Directorate General Environment, Nuclear Safety and Civil Protection of the Commission of the European Communities, Hamburg, March 2003.
- D. C. Hendershot, J. Loss Prev. Process Ind., 1997, 10, 151–157 CrossRef.
-
M. Carus, L. Dammer, Á. Puente, A. Raschka and O. Arendt, Bio-based drop-in, smart drop-in and dedicated chemicals, Nova-Institut GmbH, 2017 Search PubMed.
-
M. Sara, S. K. Brar and J. F. Blais, Platform Chemical Biorefinery – Future Green Industry, Elsevier, 2014, ch. 14 Search PubMed.
- E. T. Lavoie, L. G. Heine, H. Holder, M. S. Rossi, R. E. Lee, E. A. Connor, M. A. Vrabel, D. M. Di Fiore and C. L. Davies, Environ. Sci. Technol., 2010, 44, 9244–9249 CrossRef CAS PubMed.
-
National Research Council, A Framework to Guide Selection of Chemical Alternatives, The National Academies Press, Washington, 2014 Search PubMed.
- T. Schug, R. Abagyan, B. Blumberg, T. Collins, D. Crews, P. De Fur, S. Dickerson, T. Edwards, A. Gore and L. Guillette, Green Chem., 2013, 15, 181–198 RSC.
- N. D. Anastas, Green Chem., 2016, 18, 4325–4331 RSC.
- M. M. Jacobs, T. F. Malloy, J. A. Tickner and S. Edwards, Environ. Health Perspect., 2016, 124, 265–280 CrossRef PubMed.
- P. Marion, B. Bernela, A. Piccirilli, B. Estrine, N. Patouillard, J. Guilbot and F. Jérôme, Green Chem., 2017, 19, 4973–4989 RSC.
-
H. Cheng and L. Wang, Lignocelluloses Feedstock Biorefinery as Petrorefinery Substitutes, Biomass Now – Sustainable Growth and Use, IntechOpen, London, 2013, ch. 14 Search PubMed.
- CEFIC, Measuring bio-based raw materials use in the chemical industry, 2014.
- OECD Organisation for Economic Co-operation and Development, Substitution and Alternatives Assessment Toolbox. http://www.oecdsaatoolbox.org, accessed 16 January 2020.
- Substitution Support Portal. http://www.subsport.eu/substitution-steps, accessed 20 January 2019.
- D. Chen, K. Kannan, H. Tan, Z. Zheng, Y. L. Feng, Y. Wu and M. Widelka, Environ. Sci. Technol., 2016, 50, 5438–5453 CrossRef CAS PubMed.
- Y. Hu, Q. Zhu, X. Yan, C. Liao and G. Jiang, Environ. Res., 2019, 178, 108732 CrossRef PubMed.
- ECHA Substance Information 4,4′-sulphonyldiphenol. https://echa.europa.eu/it/substance-information/-/substanceinfo/100.001.137, accessed 22 January 2020.
- ECHA Substance Information bisphenol AF. https://echa.europa.eu/it/substance-information/-/substanceinfo/100.014.579, accessed 22 January 2020.
- N. Andújar, Y. Gálvez-Ontiveros, A. Zafra-Gómez, L. Rodrigo, M. J. Álvarez-Cubero, M. Aguilera, C. Monteagudo and A. Rivas, Nutrients, 2019, 11, 2136–2154 CrossRef PubMed.
- K. Pelch, J. A. Wignall, A. E. Goldstone, P. K. Ross, R. B. Blain, A. J. Shapiro, S. D. Holmgren, J. H. Hsieh, D. Svoboda, S. S. Auerbach, F. M. Parham, S. A. Masten, V. Walkera, A. Rooney and K. A. Thayer, Toxicology, 2019, 424, 152235 CrossRef CAS PubMed.
- Agence nationale de sécurité sanitaire, alimentation, environment, travail, Substitution du bisphénol A, March 2013.
-
https://substitution-bp.ineris.fr/en, accessed February 1st 2020.
- M. Möller and U. Schröder, RSC Adv., 2013, 3, 22253–22260 RSC.
- C. M. Welker, V. K. Balasubramanian, C. Petti, K. M. Rai, S. De Bolt and V. Mendu, Energies, 2015, 8, 7654–7676 CrossRef CAS.
-
A. Ludwiczuk, K. Skalicka-Woźniak and M. I. Georgiev, Terpenoids, Pharmacognosy – Fundamentals, Applications and Strategies, Elsevier B.V., 2017, ch. 11 Search PubMed.
-
F. Aeschelmann and M. Carus, Bio-based Building Blocks and Polymers in the World – Capacities, Production and Applications: Status Quo and Trends toward 2020, Nova-Institut GmbH, Hürth, 2015 Search PubMed.
- N. Scarlat, J. F. Dallemand, F. Monforti-Ferrario and V. Nita, Environ. Dev., 2015, 15, 3–34 CrossRef.
-
F. Cavani, S. Albonetti, F. Basile and A. Gandini, Chemicals and Fuels from Bio-Based Building Blocks, Wiley-VCH, Weinheim, 2016 Search PubMed.
- S. Santoro, F. Ferlin, L. Luciani, L. Ackermann and L. Vaccaro, Green Chem., 2017, 19, 1601–1612 RSC.
- Platform molecules are key intermediates between raw materials and final products. They are defined as “chemical compounds whose constituent elements originate wholly from biomass (material of biological origin, excluding fossil carbon sources), and that can be utilised as a building block for the production of other chemicals”. See: T. J. Farmer and M. Mascal, Introduction to Chemicals from Biomass, John Wiley & Sons, 2nd edn, 2015, ch. 4 Search PubMed.
-
Z. Fang, R. L. Smith, Jr. and X. Qi, Production of Platform Chemicals from Sustainable Resources, Springer Nature, Singapore, 2017 Search PubMed.
- L. T. Mika, E. Cséfalvay and Á. Németh, Chem. Rev., 2018, 118, 505–613 CrossRef CAS PubMed.
- B. H. Shanks and P. L. Keeling, Green Chem., 2017, 19, 3177–3185 RSC.
- J. J. Bozell and G. R. Petersen, Green Chem., 2010, 12, 539–554 RSC.
-
G. Centi and R. A. van Santen, Catalysis for Renewables, Wiley-VCH, Weinheim, 2007 Search PubMed.
-
J. H. Clark and F. Deswarte, Introduction to Chemicals from Biomass, Wiley, 2nd edn, 2015 Search PubMed.
- S. G. Wettstein, D. M. Alonso, E. I. Gürbüz and J. A. Dumesic, Curr. Opin. Chem. Eng., 2012, 1, 218–224 CrossRef CAS.
-
Catalytic Hydrogenation for Biomass Valorization, ed. R. Rinaldi, The Royal Society of Chemistry, Cambridge, 2015 Search PubMed.
-
F. S. Xiao and L. Wang, Nanoporous Catalysts for Biomass Conversion, John Wiley & Sons, 2018 Search PubMed.
- G. Gómez Millán, S. Hellsten, J. Llorca, R. Luque, H. Sixta and A. M. Balu, ChemCatChem, 2019, 11, 2022–2042 CrossRef.
- B. C. E. Makhubela and J. Darkwa, Johnson Matthey Technol. Rev., 2018, 62, 4–31 CrossRef CAS.
- P. Sudarsanam, E. Peeters, E. V. Makshina, V. I. Parvulescu and B. F. Sels, Chem. Soc. Rev., 2019, 48, 2366–2421 RSC.
-
D. J. Cole-Hamilton and R. P. Tooze, Catalyst Separation, Recovery and Recycling, Chemistry and Process Design, Springer, Dordrecht, 2006 Search PubMed.
-
P. Barbaro and F. Liguori, Heterogenized Homogeneous Catalysts for Fine Chemicals Production, Springer, London, 2010 Search PubMed.
- M. J. Climent, A. Corma and S. Iborra, Chem. Rev., 2011, 111, 1072–1133 CrossRef CAS PubMed.
- P. Barbaro, F. Liguori, N. Linares and C. Moreno-Marrodan, Eur. J. Inorg. Chem., 2012, 3807–3823 CrossRef CAS.
- H. Li, Z. Fang, Jr., R. L. Smith and S. Yang, Prog. Energy Combust. Sci., 2016, 55, 98–194 CrossRef.
- J. C. Serrano-Ruiz, R. M. West and J. A. Dumesic, Annu. Rev. Chem. Biomol. Eng., 2010, 1, 79–100 CrossRef CAS PubMed.
- R. Gérardy, R. Morodo, J. Estager, P. Luis, D. P. Debecker and J. C. M. Monbaliu, Top. Curr. Chem., 2019, 377, 1–35 CrossRef PubMed.
- R. Ricciardi, J. Huskens and W. Verboom, ChemSusChem, 2015, 8, 2586–2605 CrossRef CAS PubMed.
- N. G. Anderson, Org. Process Res. Dev., 2012, 16, 852–869 CrossRef CAS.
-
P. Bajpai, Recycling and Deinking of Recovered Paper, 2014, pp. 283–295 DOI:10.1016/B978-0-12-416998-2.00016-7.
- International Energy Agency – Bioenergy, Task 4.2 Biorefinery, Bio-based Chemicals – Value Added Products from Biorefineries. https://www.iea-bioenergy.task42-biorefineries.com, accessed 20 January 2020.
-
M. Hingsamer and G. Jungmeier, Biorefineries, The Role of Bioenergy in the Emerging Bioeconomy, Elsevier, 2019, ch. 5 Search PubMed.
- D. Esposito and M. Antonietti, Chem. Soc. Rev., 2015, 44, 5821–5835 RSC.
- R. De Clercq, M. Dusselier and B. F. Sels, Green Chem., 2017, 19, 5012–5040 RSC.
- I. Delidovich, P. J. C. Hausoul, L. Deng, R. Pfützenreuter, M. Rose and R. Palkovits, Chem. Rev., 2016, 116, 1540–1599 CrossRef CAS PubMed.
-
V. Mittal, Polymers from Renewable Resources, Renewable Polymers: Synthesis, Processing, and Technology, John Wiley & Sons, Inc., Hoboken, 2011, ch. 1 Search PubMed.
- Y. Lee, E. E. Kwon and J. Lee, Rev. Environ. Sci. Biotechnol., 2019, 18, 317–334 CrossRef CAS.
- X. Zhang, M. Fevre, G. O. Jones and R. M. Waymouth, Chem. Rev., 2018, 118, 839–885 CrossRef CAS PubMed.
- I. T. Horváth, E. Cséfalvay, L. T. Mika and M. Debreczeni, ACS Sustainable Chem. Eng., 2017, 5, 2734–2740 CrossRef.
- H. Hong, B. G. Harvey, G. R. Palmese, J. F. Stanzione III, H. W. Ng, S. Sakkiah, W. Tong and J. M. Sadler, Int. J. Environ. Res. Public Health, 2016, 13, 705–721 CrossRef PubMed.
- D. Klemm, B. Heublein, H. P. Fink and A. Bohn, Angew. Chem., Int. Ed., 2005, 44, 3358–3393 CrossRef CAS PubMed.
-
J. L. Wertz, J. P. Mercier and O. Bédué, Cellulose Science and Technology, EPFL Press, 2010 Search PubMed.
- F. G. Calvo-Flores and J. A. Dobado, ChemSusChem, 2010, 3, 1227–1235 CrossRef CAS PubMed.
- R. Vanholme, K. Morreel, C. Darrah, P. Oyarce, J. H. Grabber, J. Ralph and W. Boerjan, New Phytol., 2012, 196, 978–1000 CrossRef CAS PubMed.
- A. Shrotri, H. Kobayashi and A. Fukuoka, Adv. Catal., 2017, 60, 59–123 CAS.
- D. S. Bajwa, G. Pourhashem, A. H. Ullah and S. G. Bajwa, Ind. Crops Prod., 2019, 139, 111526 CrossRef CAS.
-
Lignin and Lignans: Advances in Chemistry, ed. C. Heitner, D. Dimmel and J. Schmidt, CRC Press, 2010 Search PubMed.
- P. M. Hergenrother, High Perform. Polym., 2003, 15, 3–45 CrossRef CAS.
- F. Pion, P. H. Ducrot and F. Allais, Macromol. Chem. Phys., 2014, 215, 431–439 CrossRef CAS.
- D. Sun, S. Sato, W. Ueda, A. Primo, H. Garcia and A. Corma, Green Chem., 2016, 18, 2579–2597 RSC.
- Y. B. Huang and Y. Fu, Green Chem., 2013, 15, 1095–1111 RSC.
- L. Hu, L. Lin, Z. Wu, S. Zhou and S. Liu, Appl. Catal., B, 2015, 174–175, 225–243 CrossRef CAS.
- J. Zhang, J. B. Li, S. B. Wu and Y. Liu, Ind. Eng. Chem. Res., 2013, 52, 11799–11815 CrossRef CAS.
- R. J. van Putten, J. C. van der Waal, E. de Jong, C. B. Rasrendra, H. J. Heeres and J. G. de Vries, Chem. Rev., 2013, 113, 1499–1597 CrossRef CAS PubMed.
- H. Xia, S. Xu, H. Hu, J. An and C. Li, RSC Adv., 2018, 8, 30875–30886 RSC.
- G. W. Huber, S. Iborra and A. Corma, Chem. Rev., 2006, 106, 4044–4098 CrossRef CAS PubMed.
- S. Chen, R. Wojcieszak, F. Dumeignil, E. Marceau and S. Royer, Chem. Rev., 2018, 118, 11023–11117 CrossRef CAS PubMed.
- A. I. Stankiewicz and J. A. Moulijn, Chem. Eng. Prog., 2000, 22–34 CAS.
- N. V. Gromov, O. P. Taran, K. N. Sorokina, T. I. Mishchenko, S. Uthandi and V. N. Parmon, Catal. Ind., 2016, 8, 176–186 CrossRef.
- F. Menegazzo, E. Ghedini and M. Signoretto, Molecules, 2018, 23, 2201–2219 CrossRef PubMed.
- H. Kobayashi, T. Komanoya, S. K. Guha, K. Hara and A. Fukuoka, Appl. Catal., A, 2011, 409–410, 13–20 CrossRef CAS.
- J. N. Cohn, G. Johnson, S. Ziesche, F. Cobb, G. Francis, F. Tristani, R. Smith, W. B. Dunkman, H. Loeb and M. Wong, N. Engl. J. Med., 1991, 325, 303–310 CrossRef CAS PubMed.
- M. Rose and R. Palkovits, ChemSusChem, 2012, 5, 167–176 CrossRef CAS PubMed.
- C. Dussenne, T. Delaunay, V. Wiatz, H. Wyart, I. Suisse and M. Sauthier, Green Chem., 2017, 19, 5332–5344 RSC.
- F. Fenouillot, A. Rousseau, G. Colomines, R. Saint-Loup and J. P. Pascault, Prog. Polym. Sci., 2010, 35, 578–622 CrossRef CAS.
- X. Feng, A. J. East, W. B. Hammond, Y. Zhang and M. Jaffe, Polym. Adv. Technol., 2011, 22, 139–150 CrossRef CAS.
- D. J. Saxon, A. M. Luke, H. Sajjad, W. B. Tolman and T. M. Reineke, Prog. Polym. Sci., 2020, 101, 101196–101210 CrossRef CAS.
- S. Chatti and H. R. Kricheldorf, J. Macromol. Sci., Part A: Pure Appl. Chem., 2006, 43, 967–975 CrossRef.
- M. Yokoe, K. Aoi and M. Okada, J. Polym. Sci., Part A: Polym. Chem., 2003, 41, 2312–2321 CrossRef CAS.
- A. Yamaguchi, O. Sato, N. Mimura and M. Shirai, RSC Adv., 2014, 4, 45575–45578 RSC.
- H. Yokoyama, H. Kobayashi, J. Hasegawa and A. Fukuoka, ACS Catal., 2017, 7, 4828–4834 CrossRef CAS.
- F. Aricò, S. Evaristo and P. Tundo, Green Chem., 2015, 17, 1176–1185 RSC.
- H. G. Fletcher and R. M. Goepp, J. Am. Chem. Soc., 1946, 68, 939–941 CrossRef CAS.
- L. W. Wright and J. D. Brandner, J. Org. Chem., 1964, 29, 2979–2982 CrossRef CAS.
-
E. Hagberg, K. Martin, J. Van Ee, J. Le Nôtre, D. S. Van Es and J. Van Haveren, WO 125950A1, 2013.
- J. Le Nôtre, J. Van Haveren and D. S. Van Es, ChemSusChem, 2013, 6, 693–700 CrossRef PubMed.
-
S. Howard, B. Smith and J. Terrian, US0044744A1, 2018.
- Grand View Research. Isosorbide Market Size, Share & Trends Analysis Report By Application, By End Use, By Region, and Segment Forecasts, 2019–2025; 2019, accessed August 2019. https://www.grandviewresearch.com/industry-analysis/isosorbide-industry.
- J. Xia, D. Yu, Y. Hu, B. Zou, P. Sun, H. Li and H. Huang, Catal. Commun., 2011, 12, 544–547 CrossRef CAS.
-
P. Fuertes, US213439A1, 2008.
-
K. M. Moore and A. J. Sanborn, US152907A1, 2004.
-
C. G. Moyers, J. K. Withrom and J. L. Stephens, US259056A1, 2009.
-
N. Fujihana, Y. Tategami and M. Mihashi, JP316025(A), 2006.
-
H. Wyart and M. Ibert, US0092782A1, 2019.
- R. P. Dash, N. R. Srinivas and R. J. Babu, Drug Dev. Ind. Pharm., 2019, 45, 1421–1429 CrossRef CAS PubMed.
- G. Diamond, A. Hagemeyer, V. Murphy and V. Sokolovskii, Comb. Chem. High Throughput Screening, 2018, 21, 616–630 CrossRef CAS PubMed.
- R. Otomo, T. Yokoi and T. Tatsumi, Appl. Catal., A, 2015, 505, 28–35 CrossRef CAS.
- H. Kobayashi, H. Yokoyama, B. Feng and A. Fukuoka, Green Chem., 2015, 17, 2732–2735 RSC.
- R. S. Thombal and V. H. Jadhav, Tetrahedron Lett., 2016, 57, 4398–4400 CrossRef CAS.
- R. S. Thombal and V. H. Jadhav, RSC Adv., 2016, 6, 30846–30851 RSC.
- J. M. Fraile and C. J. Saavedra, ChemistrySelect, 2017, 2, 1013–1018 CrossRef CAS.
- M. J. Ginés-Molina, R. Moreno-Tost, J. Santamaría-González and P. Maireles-Torres, Appl. Catal., A, 2017, 537, 66–73 CrossRef.
- J. Shi, Y. Shan, Y. Tian, Y. Wan, Y. Zheng and Y. Feng, RSC Adv., 2016, 6, 13514–13521 RSC.
- A. Cubo, J. Iglesias, G. Morales, J. A. Melero, J. Moreno and R. Sánchez-Vázquez, Appl. Catal., A, 2017, 531, 151–160 CrossRef CAS.
- K. N. Tayade and M. Mishra, Catal. Sci. Technol., 2013, 3, 1288–1300 RSC.
- A. S. Dias, M. Pillinger and A. A. Valente, J. Catal., 2005, 229, 414–423 CrossRef CAS.
- A. A. Dabbawala, J. J. Park, A. H. Valekar, D. K. Mishra and J. S. Hwang, Catal. Commun., 2015, 69, 207–211 CrossRef CAS.
- P. Bhanja, J. Na, T. Jing, J. Lin, T. Wakihara, A. Bhaumik and Y. Yamauchi, Chem. Mater., 2019, 31, 5343–5362 CrossRef CAS.
- R. Lin and Y. Ding, Materials, 2013, 6, 217–243 CrossRef CAS PubMed.
- O. A. Rusu, W. F. Hoelderich, H. Wyart and M. Ibert, Appl. Catal., B, 2015, 176–177, 139–149 CrossRef CAS.
- D. Cao, B. Yu, S. Zhang, L. Cui, J. Zhang and W. Cai, Appl. Catal., A, 2016, 528, 59–66 CrossRef CAS.
- A. A. Dabbawala, S. M. Alhassan, D. K. Mishra, J. Jegala and J. S. Hwang, Mol. Catal., 2018, 454, 77–86 CrossRef CAS.
- J. Deng, B. H. Xu, Y. F. Wang, X. E. Mo, R. Zhang, Y. Li and S. J. Zhang, Catal. Sci. Technol., 2017, 7, 2065–2073 RSC.
- K. Matuszek, A. Chrobok, F. Coleman, K. R. Seddon and M. Swadźba-Kwaśny, Green Chem., 2014, 16, 3463–3471 RSC.
- N. Abramenko, L. Kustov, L. Metelytsia, V. Kovalishyn, I. Tetko and W. Peijnenburg, J. Hazard. Mater., 2020, 384, 121429 CrossRef PubMed.
- K. S. Egorov and V. P. Ananikov, Biophys. Rev., 2018, 10, 881–900 CrossRef PubMed.
- M. Yabushita, H. Kobayashi, A. Shrotri, K. Hara, S. Ito and A. Fukuoka, Bull. Chem. Soc. Jpn., 2015, 88, 996–1002 CrossRef CAS.
- B. D. Rabideau, K. N. Westa and J. H. Davis Jr., Chem. Commun., 2018, 54, 5019–5031 RSC.
- C. Dussenne, H. Wyart, V. Wiatz, I. Suisse and M. Sauthier, Mol. Catal., 2019, 463, 61–66 CrossRef CAS.
- P. Che, F. Lu, X. Si, H. Ma, X. Niea and J. Xu, Green Chem., 2018, 20, 634–640 RSC.
- F. Aricò, P. Tundo, A. Maranzana and G. Tonachini, ChemSusChem, 2012, 5, 1578–1586 CrossRef PubMed.
- F. Aricò and P. Tundo, Beilstein J. Org. Chem., 2016, 12, 2256–2266 CrossRef PubMed.
- P. Barbaro, F. Liguori and C. Moreno-Marrodan, Green Chem., 2016, 18, 2935–2940 RSC.
- F. Liguori, C. Moreno-Marrodan and P. Barbaro, Chin. J. Catal., 2015, 36, 1157–1169 CrossRef CAS.
- V. Trombettoni, D. Lanari, P. Prinsen, R. Luque, A. Marrocchi and L. Vaccaro, Prog. Energy Combust. Sci., 2018, 65, 136–162 CrossRef.
- I. Sádaba, M. López Granados, A. Riisager and E. Taarning, Green Chem., 2015, 17, 4133–4145 RSC.
- G. Liang, C. Wu, L. He, J. Ming, H. Cheng, L. Zhuo and F. Zhao, Green Chem., 2011, 13, 839–842 RSC.
- J. Keskiväli, S. Rautiainen, M. Heikkilä, T. T. T. Myllymäki, J. P. Karjalainen, K. Lagerblom, M. Kemell, M. Vehkamäki, K. Meinander and T. Repo, Green Chem., 2017, 19, 4563–4570 RSC.
- A. Yamaguchi, O. Sato, N. Mimura and M. Shirai, Catal. Commun., 2015, 67, 59–63 CrossRef CAS.
- A. Yamaguchi, N. Mimura, M. Shirai and O. Sato, J. Jpn. Pet. Inst., 2016, 59, 155–159 CrossRef CAS.
- Y. Yang, W. Zhang, F. Yang, B. Zhou, D. Zeng, N. Zhang, G. Zhao, S. Hao and X. Zhang, Nanoscale, 2018, 10, 2199–2206 RSC.
- P. Sun, X. D. Long, H. He, C. G. Xia and F. W. Li, ChemSusChem, 2013, 6, 2190–2197 CrossRef CAS PubMed.
- P. Zhou and Z. Zhang, Catal. Sci. Technol., 2016, 6, 3694–3712 RSC.
- K. De Oliveira Vigier and F. Jérôme, Top. Curr. Chem., 2010, 295, 63–92 CrossRef PubMed.
- C. Moreau, M. N. Belgacem and A. Gandini, Top. Catal., 2004, 27, 11–30 CrossRef CAS.
- W. Fan, C. Verrier, Y. Queneau and F. Popowycz, Curr. Org. Synth., 2019, 16, 583–614 CrossRef CAS PubMed.
-
A. S. Amarasekara, 5-Hydroxymethylfurfural Based Polymers, Renewable Polymers: Synthesis, Processing, and Technology, John Wiley & Sons, Hoboken, 2011, ch. 9 Search PubMed.
- X. Kong, Y. Zhu, Z. Fang, J. A. Kozinski, I. S. Butler, L. Xu, H. Songa and X. Wei, Green Chem., 2018, 20, 3657–3682 RSC.
- K. Gupta, R. K. Rai and S. K. Singh, ChemCatChem, 2018, 10, 2326–2349 CrossRef CAS.
- Y. Nakagawa, K. Takada, M. i. Tamura and K. Tomishige, ACS Catal., 2014, 4, 2718–2726 CrossRef CAS.
- J. Wei, T. Wang, P. Tang, X. Tang, Y. Sun, X. Zeng and L. Lin, Curr. Org. Chem., 2019, 23, 2155–2167 CrossRef CAS.
- X. Tang, J. Wei, N. Ding, Y. Sun, X. Zeng, L. Hu, S. Liu, T. Lei and L. Lin, Renewable Sustainable Energy Rev., 2017, 77, 287–296 CrossRef CAS.
- L. Foppa and J. Dupon, Chem. Soc. Rev., 2015, 44, 1886–1897 RSC.
- D. Adu-Mensah, D. Mei, L. Zuo, Q. Zhang and J. Wang, Fuel, 2019, 251, 660–668 CrossRef CAS.
- C. Moreno-Marrodan, F. Liguori and P. Barbaro, Beilstein J. Org. Chem., 2017, 13, 734–754 CrossRef CAS PubMed.
- A. Hommes, H. J. Heeres and J. Yue, ChemCatChem, 2019, 11, 4671–4708 CrossRef CAS.
- A. Cadu, K. Sekine, J. Mormul, D. M. Ohlmann, T. Schaub and A. S. K. Hashmi, Green Chem., 2018, 20, 3386–3393 RSC.
-
D. Ohlmann, T. Shaub, A. Cadu and S. K. Hashmi, WO220003A1, 2018.
- S. Fulignati, C. Antonetti, D. Licursi, M. Pieraccioni, E. Wilbers, H. J. Heeres and A. M. Raspolli Galletti, Appl. Catal., A, 2019, 578, 122–133 CrossRef CAS.
- A. Jouve, S. Cattaneo, S. Capelli, M. Stucchi, C. Evangelisti, A. Villa and L. Prati, Molecules, 2019, 24, 316–329 CrossRef PubMed.
- J. Han, Y. H. Kim, H. Seok Jang, S. Y. Hwang, J. Jegal, J. Won Kim and Y. S. Lee, RSC Adv., 2016, 6, 93394–93397 RSC.
- R. Alamillo, M. Tucker, M. Chia, Y. Pagan-Torres and J. A. Dumesic, Green Chem., 2012, 14, 1413–1419 RSC.
-
A. Roucoux, A. Nowicki and K. Philippot, Rhodium and Ruthenium Nanoparticles in Catalysis, in Nanoparticles and Catalysis, ed. D. Astruc, Wiley-VCH, Weinheim, 2007, pp. 349–388 Search PubMed.
- C. Michel and P. Gallezot, ACS Catal., 2015, 5, 4130–4132 CrossRef CAS.
- J. Chen, R. Liu, Y. Guo, L. Chen and H. Gao, ACS Catal., 2015, 5, 722–733 CrossRef CAS.
- J. Chen, Y. Ge, Y. Guo and J. Chen, J. Energy Chem., 2018, 27, 283–289 CrossRef.
- Y. Zhu, X. Kong, H. Zheng, G. Ding, Y. Zhu and Y. W. Li, Catal. Sci. Technol., 2015, 5, 4208–4217 RSC.
- G. Bottari, A. J. Kumalaputri, K. K. Krawczyk, B. L. Feringa, H. J. Heeres and K. Barta, ChemSusChem, 2015, 8, 1323–1327 CrossRef CAS PubMed.
- N. Perret, A. Grigoropoulos, M. Zanella, T. D. Manning, J. B. Claridge and M. J. Rosseinsky, ChemSusChem, 2016, 9, 521–531 CrossRef CAS PubMed.
- L. Yu, L. He, J. Chen, J. Zheng, L. Ye, H. Lin and Y. Yuan, ChemCatChem, 2015, 7, 1701–1707 CrossRef CAS.
- X. Kong, R. Zheng, Y. Zhu, G. Ding, Y. Zhu and Y. W. Li, Green Chem., 2015, 17, 2504–2514 RSC.
- S. Lima, D. Chadwick and K. Hellgardt, RSC Adv., 2017, 7, 31401–31407 RSC.
- B. Xiao, M. Zheng, X. Li, J. Pang, R. Sun, H. Wang, X. Pang, A. Wang, X. Wang and T. Zhang, Green Chem., 2016, 18, 2175–2184 RSC.
- D. Hu, H. Hu, H. Zhou, G. Li, C. Chen, J. Zhang, Y. Yang, Y. Hu, Y. Zhang and L. Wang, Catal. Sci. Technol., 2018, 8, 6091–6099 RSC.
- C. Pischetola, L. Collado, M. A. Keane and F. Cárdenas-Lizana, Molecules, 2018, 23, 2905–2920 CrossRef PubMed.
- Y. Duan, J. Zhang, D. Li, D. Deng, L. F. Ma and Y. Yang, RSC Adv., 2017, 7, 26487–26493 RSC.
- K. Tanabe, Catal. Today, 2003, 78, 65–77 CrossRef CAS.
- T. Okuhara, Chem. Rev., 2002, 102, 3641–3666 CrossRef CAS PubMed.
- P. P. Upare, Y. K. Hwang and D. W. Hwang, Green Chem., 2018, 20, 879–885 RSC.
- X. Xiang, J. Cui, G. Ding, H. Zheng, Y. Zhu and Y. Li, ACS Sustainable Chem. Eng., 2016, 4, 4506–4510 CrossRef CAS.
- X. Tang, H. Chen, L. Hu, W. Hao, Y. Sun, X. Zeng, L. Lin and S. Liu, Appl. Catal., B, 2014, 147, 827–834 CrossRef CAS.
- G. Yi and Y. G. Zhang, ChemSusChem, 2012, 5, 1383–1387 CrossRef CAS PubMed.
- J. He, M. R. Nielsen, T. W. Hansen, S. Yang and A. Riisager, Catal. Sci. Technol., 2019, 9, 1289–1300 RSC.
- T. Wang, J. Zhang, W. Xie, Y. Tang, D. Guo and Y. Ni, Catalysts, 2017, 7, 92–99 CrossRef.
- J. Wei, X. Cao, T. Wang, H. Liu, X. Tang, X. Zeng, Y. Sun, T. Lei, S. Liu and L. Lin, Catal. Sci. Technol., 2018, 8, 4474–4484 RSC.
- N. J. Wise and J. M. J. Williams, Tetrahedron Lett., 2007, 48, 3639–3641 CrossRef CAS.
- J. He, H. Li, A. Riisager and S. Yang, ChemCatChem, 2018, 10, 430–438 CrossRef CAS.
- L. Hu, X. Dai, N. Li, X. Tang and Y. Jiang, Sustainable Energy Fuels, 2019, 3, 1033–1041 RSC.
- J. Long, W. Zhao, Y. Xu, H. Li and S. Yang, Catalysts, 2018, 8, 633–644 CrossRef.
- W. Zhao, W. Wu, H. Lia, C. Fang, T. Yang, Z. Wang, C. He and S. Yang, Fuel, 2018, 217, 365–369 CrossRef CAS.
- T. Akashi, S. Sato, R. Takahashi, T. Sodesawa and K. Inui, Catal. Commun., 2003, 4, 411–416 CrossRef CAS.
- M. Renz, Eur. J. Org. Chem., 2005, 979–988 CrossRef CAS.
- J. Ohyama, Y. Ohiraa and A. Satsuma, Catal. Sci. Technol., 2017, 7, 2947–2953 RSC.
- R. Ramos, A. Grigoropoulos, N. Perret, M. Zanella, A. P. Katsoulidis, T. D. Manning, J. B. Claridge and M. J. Rosseinsky, Green Chem., 2017, 19, 1701–1713 RSC.
- H. Zang, K. Wang, M. Zhang, R. Xie, L. Wang and E. Y. X. Chen, Catal. Sci. Technol., 2018, 8, 1777–1798 RSC.
- J. F. Wilson and E. Y. X. Chen, ACS Sustainable Chem. Eng., 2019, 7, 7035–7046 CrossRef CAS.
- Z. Mou and E. Y. X. Chen, ACS Sustainable Chem. Eng., 2016, 4, 7118–7129 CrossRef CAS.
- J. Donnelly, C. R. Müller, L. Wiermans, C. J. Chuck and P. Dominguez de Maria, Green Chem., 2015, 17, 2714–2718 RSC.
- Z. Mou, S. K. Feng and E. Y. X. Chen, Polym. Chem., 2016, 7, 1593–1602 RSC.
- J. F. Wilson and E. Y. X. Chen, ACS Sustainable Chem. Eng., 2016, 4, 4927–4936 CrossRef CAS.
- L. Wang and E. Y. X. Chen, ACS Catal., 2015, 5, 6907–6917 CrossRef CAS.
- J. J. Bozell, L. Moens, D. C. Elliott, Y. Wang, G. G. Neuenscwander, S. W. Fitzpatrick, R. J. Bilski and J. L. Jarnefeld, Resour., Conserv. Recycl., 2000, 28, 227–239 CrossRef.
- H. F. Liu, F. X. Zeng, L. Deng, B. Liao, H. Pang and Q. X. Guo, Green Chem., 2013, 15, 81–84 RSC.
- X. Yu, Y. Guo, K. Li, X. Yang, L. Xu, Y. Guo and J. Hu, J. Mol. Catal. A: Chem., 2008, 290, 44–53 CrossRef CAS.
- S. Van de Vyver, J. Geboers, S. Helsen, F. Yu, J. Thomas, M. Smet, W. Dehaen and B. F. Sels, Chem. Commun., 2012, 48, 3497–3499 RSC.
- L. Filiciotto, A. M. Balu, J. C. van der Waal and R. Luque, Catal. Today, 2018, 302, 2–15 CrossRef CAS.
- S. Van de Vyver, J. Geboers, P. A. Jacobs and B. F. Sels, ChemCatChem, 2011, 3, 82–94 CrossRef CAS.
- D. W. Rackemann and W. O. S. Doherty, Biofuels, Bioprod. Biorefin., 2011, 5, 198–214 CrossRef CAS.
- S. Zhou and D. Kim, Electrochim. Acta, 2012, 63, 238–244 CrossRef CAS.
- D. Foix, X. Ramis, M. Sangermano and A. Serra, J. Polym. Sci., Part A: Polym. Chem., 2012, 50, 1133–1142 CrossRef CAS.
- T. Renders, S. Van den Bosch, S. F. Koelewijn, W. Schutyser and B. F. Sels, Energy Environ. Sci., 2017, 10, 1551–1557 RSC.
- R. E. Key and J. J. Bozell, ACS Sustainable Chem. Eng., 2016, 4, 5123–5135 CrossRef CAS.
- I. Z. Awan, N. Tanchoux, F. Quignard, S. Albonetti, F. Cavani and F. Di Renzo, Stud. Surf. Sci. Catal., 2019, 178, 257–275 CrossRef CAS.
-
Recent Advances in Development of Platform Chemicals, S. Saravanamurugan, ed. A. Pandey, H. Li and A. Riisager, Elsevier, Amsterdam, 2020 Search PubMed.
- J. Zakzeski, P. C. A. Bruijnincx, A. L. Jongerius and B. M. Weckhuysen, Chem. Rev., 2010, 110, 3552–3599 CrossRef CAS PubMed.
- S. Gillet, M. Aguedo, L. Petitjean, A. R. C. Morais, A. M. da Costa Lopes, R. M. Łukasik and P. T. Anastas, Green Chem., 2017, 19, 4200–4233 RSC.
- M. V. Galkin and J. S. M. Samec, ChemSusChem, 2016, 9, 1544–1558 CrossRef CAS PubMed.
- E. M. Anderson, R. Katahira, M. Reed, M. G. Resch, E. M. Karp, G. T. Beckham and Y. Roman-Leshkov, ACS Sustainable Chem. Eng., 2016, 4, 6940–6950 CrossRef CAS.
- W. Schutyser, T. Renders, S. Van den Bosch, S. F. Koelewijn, G. T. Beckham and B. F. Sels, Chem. Soc. Rev., 2018, 47, 852–908 RSC.
- C. Li, X. Zhao, A. Wang, G. W. Huber and T. Zhang, Chem. Rev., 2015, 115, 11559–11624 CrossRef CAS PubMed.
- B. Lochab, S. Shukla and I. K. Varma, RSC Adv., 2014, 4, 21712–21752 RSC.
-
W. Schutyser, T. Renders, G. Van den Bossche, S. Van den Bosch, S. F. Koelewijn, T. Ennaert and B. F. Sels, Catalysis in Lignocellulosic Biorefineries: The Case of Lignin Conversion, Nanotechnology in Catalysis: Applications in the Chemical Industry, Energy Development, and Environment Protection, Wiley-VCH, 2017, ch. 23 Search PubMed.
- R. Rinaldi, R. Jastrzebski, M. T. Clough, J. Ralph, M. Kennema, P. C. A. Bruijnincx and B. M. Weckhuysen, Angew. Chem., Int. Ed., 2016, 55, 8164–8215 CrossRef CAS PubMed.
- C. Xu, R. A. D. Arancon, J. Labidid and R. Luque, Chem. Soc. Rev., 2014, 43, 7485–7500 RSC.
- A. Margellou and K. S. Triantafyllidis, Catalysts, 2019, 9, 43–74 CrossRef.
- Y. Cao, S. S. Chen, S. Zhang, Y. S. Ok, B. M. Matsagar, K. C. W. Wu and D. C. W. Tsang, Bioresour. Technol., 2019, 291, 121878 CrossRef PubMed.
- B. M. Upton and A. M. Kasko, Chem. Rev., 2016, 116, 2275–2306 CrossRef CAS PubMed.
- F. H. Isikgor and C. R. Becer, Polym. Chem., 2015, 6, 4497–4559 RSC.
- S. Van den Bosch, S. F. Koelewijn, T. Renders, G. Van den Bossche, T. Vangeel, W. Schutyser and B. F. Sels, Top. Curr. Chem., 2018, 376, 36–76 CrossRef CAS PubMed.
-
C. Xu and F. Ferdosian, Lignin-Based Epoxy Resins, Conversion of Lignin into Bio-Based Chemicals and Materials, Springer, Berlin, 2017 Search PubMed.
- M. Fache, E. Darroman, V. Besse, R. Auvergne, S. Caillol and B. Boutevin, Green Chem., 2014, 16, 1987–1998 RSC.
- H. Lange, S. Decina and C. Crestini, Eur. Polym. J., 2013, 49, 1151–1173 CrossRef CAS.
-
P. C. Rodrigues Pinto, E. A. Borges da Silva and A. E. Rodrigues, Lignin as Source of Fine Chemicals: Vanillin and Syringaldehyde, Biomass Conversion: The Interface of Biotechnology, Chemistry and Materials Science, Springer, Berlin, 2012, ch. 12 Search PubMed.
- I. S. Modahl, A. Brekke and C. Valente, J. Cleaner Prod., 2015, 94, 247–259 CrossRef CAS.
- W. B. Huang, C. Y. Du, J. A. Jiang and Y. F. Ji, Res. Chem. Intermed., 2013, 39, 2849–2856 CrossRef CAS.
-
B. Schaefer, Flavours and Fragrances. Natural Products in the Chemical Industry, Springer, Berlin, 2014 Search PubMed.
- M. Fache, B. Boutevin and S. Caillol, ACS Sustainable Chem. Eng., 2016, 4, 35–46 CrossRef CAS.
- M. Fache, B. Boutevin and S. Caillol, Eur. Polym. J., 2015, 68, 488–502 CrossRef CAS.
- Z. Sun, B. Fridrich, A. de Santi, S. Elangovan and K. Barta, Chem. Rev., 2018, 118, 614–678 CrossRef CAS PubMed.
- A. Llevot, E. Grau, S. Carlotti, S. Grelier and H. Cramail, J. Mol. Catal. B: Enzym., 2016, 125, 34–41 CrossRef CAS.
- R. T. Nishimura, C. H. Giammanco and D. A. Vosburg, J. Chem. Educ., 2010, 87, 526–527 CrossRef CAS.
- A. Llevot, E. Grau, S. Carlotti, S. Grelier and H. Cramail, Polym. Chem., 2015, 6, 6058–6066 RSC.
- A. S. Amarasekara and M. A. Hasan, Polym. Sci., Ser. B, 2016, 58, 307–312 CrossRef CAS.
- J. Kwon, J. Kim, S. Park, G. Khang, P. M. Kang and D. Lee, Biomacromolecules, 2013, 14, 1618–1626 CrossRef CAS PubMed.
- T. Koike, Polym. Eng. Sci., 2012, 52, 701–718 CrossRef CAS.
- L. Gu, G. Chen and Y. Yao, Polym. Degrad. Stab., 2014, 108, 68–75 CrossRef CAS.
- H. Gang, D. Lee, K. Y. Choi, H. N. Kim, H. Ryu, D. S. Lee and B. G. Kim, ACS Sustainable Chem. Eng., 2017, 5, 4582–4588 CrossRef CAS.
- H. A. Meylemans, T. J. Groshens and B. G. Harvey, ChemSusChem, 2012, 5, 206–210 CrossRef CAS PubMed.
- T. Periyasamy, S. P. Asrafali, S. Muthusamy and S. C. Kim, New J. Chem., 2016, 40, 9313–9319 RSC.
- B. G. Harvey, A. J. Guenthner, H. A. Meylemans, S. R. L. Haines, K. R. Lamison, T. J. Groshens, L. R. Cambrea, M. C. Davis and W. W. Lai, Green Chem., 2015, 17, 1249–1258 RSC.
- M. Decostanzi, R. Auvergne, B. Boutevin and S. Caillol, Green Chem., 2019, 21, 724–747 RSC.
- E. D. Hernandez, A. W. Bassett, J. M. Sadler, J. J. La Scala and J. F. Stanzione, III, ACS Sustainable Chem. Eng., 2016, 4, 4328–4339 CrossRef CAS.
- Y. Peng, K. H. Nicastro, T. H. Epps III and C. Wu, J. Agric. Food Chem., 2018, 66, 11775–11783 CrossRef CAS PubMed.
- K. H. Nicastro, C. J. Kloxin and T. H. Epps III, ACS Sustainable Chem. Eng., 2018, 6, 14812–14819 CrossRef CAS.
- J. R. Mauck, S. K. Yadav, J. M. Sadler, J. J. La Scala, G. R. Palmese, K. M. Schmalbach and J. F. Stanzione III, Macromol. Chem. Phys., 2017, 218, 1700013 CrossRef.
- E. A. Baroncini, S. K. Yadav, G. R. Palmese and J. F. Stanzione III, J. Appl. Polym. Sci., 2016, 133, 44103 CrossRef.
- S. Curia, A. Biundo, I. Fischer, V. Braunschmid, G. M. Gebitz and J. F. Stanzione III, ChemSusChem, 2018, 11, 2529–2539 CrossRef CAS PubMed.
- J. R. Mauck, A. W. Bassett, J. M. Sadler, J. J. La Scala, E. Napadensky, K. H. Reno and J. F. Stanzione III, J. Biobased Mater. Bioenergy, 2018, 12, 471–476 CrossRef CAS.
- S. V. Mankar, M. Nelly Garcia Gonzalez, N. Warlin, N. G. Valsange, N. Rehnberg, S. Lundmark, P. Jannasch and B. Zhang, ACS Sustainable Chem. Eng., 2019, 7, 19090–19103 CrossRef CAS.
- D. Bai, Q. Chen, Y. Chai, T. Ren, C. Huang, I. D. V. Ingram, M. North, Q. Zheng and H. Xie, RSC Adv., 2018, 8, 34297–34303 RSC.
- N. Kumar and V. Pruthi, Biotechnol. Rep., 2014, 4, 86–93 CrossRef PubMed.
- J. G. Linger, D. R. Vardon, M. T. Guarnieri, E. M. Karp, G. B. Hunsinger, M. A. Franden, C. W. Johnson, G. Chupka, T. J. Strathmann, P. T. Pienkos and G. T. Beckham, Proc. Natl. Acad. Sci. U. S. A., 2014, 111, 12013–12018 CrossRef CAS PubMed.
- D. Matias de Oliveira, A. Finger-Teixeira, T. Rodrigues Mota, V. H. Salvador, F. C. Moreira-Vilar, H. B. Correa Molinari, R. A. C. Mitchell, R. Marchiosi, O. Ferrarese-Filho and W. D. dos Santos, Plant Biotechnol. J., 2015, 13, 1224–1232 CrossRef PubMed.
- S. Ou and K. C. Kwok, J. Sci. Food Agric., 2004, 84, 1261–1269 CrossRef CAS.
- L. Mialon, A. G. Pemba and S. A. Miller, Green Chem., 2010, 12, 1704–1706 RSC.
- F. Pion, A. F. Reano, P. H. Ducrot and F. Allais, RSC Adv., 2013, 3, 8988–8997 RSC.
- W. Schutyser, G. Van den Bossche, A. Raaffels, S. Van den Bosch, S. F. Koelewijn, T. Renders and B. F. Sels, ACS Sustainable Chem. Eng., 2016, 4, 5336–5346 CrossRef CAS.
- S. F. Koelewijn, S. Van den Bosch, T. Renders, W. Schutyser, B. Lagrain, M. Smet, J. Thomas, W. Dehaen, P. Van Puyvelde, H. Witterse and B. F. Sels, Green Chem., 2017, 19, 2561–2570 RSC.
- P. Ferrini, S. F. Koelewijn, J. Van Aelst, N. Nuttens and B. F. Sels, ChemSusChem, 2017, 10, 2249–2257 CrossRef CAS PubMed.
- H. Fang, W. Tong, L. M. Shi, R. Blair, R. Perkins, W. Branham, B. S. Hass, Q. Xie, S. L. Dial and C. L. Moland, Chem. Res. Toxicol., 2001, 14, 280–294 Search PubMed.
- D. Miller, B. B. Wheals, N. Beresford and J. P. Sumpter, Environ. Health Perspect., 2001, 109, 133–138 CAS.
- S. Zhao and M. M. Abu-Omar, ACS Sustainable Chem. Eng., 2016, 4, 6082–6089 CrossRef CAS.
- S. Zhao and M. M. Abu-Omar, ACS Sustainable Chem. Eng., 2017, 5, 5059–5066 CrossRef CAS.
- M. V. Galkin and J. S. M. Samec, ChemSusChem, 2014, 7, 2154–2158 CrossRef CAS PubMed.
-
K. Hüsnü, C. Başer and F. Demirci, Chemistry of Essential Oils, Flavours and Fragrances, Springer, Berlin, 2007, ch. 4 Search PubMed.
- G. P. Kamatou, I. Vermaak and A. M. Viljoen, Molecules, 2012, 17, 6953–6981 CrossRef CAS PubMed.
- C. François, S. Pourchet, G. Boni, S. Fontaine, Y. Gaillard, V. Placet, M. V. Galkin, Al. Orebom, J. Samec and L. Plasseraud, RSC Adv., 2016, 6, 68732–68738 RSC.
- A. S. Trita, L. C. Over, J. Pollini, S. Baader, S. Riegsinger, M. A. R. Meier and L. J. Gooßen, Green Chem., 2017, 19, 3051–3060 RSC.
- V. E. Tarabanko and N. Tarabanko, Int. J. Mol. Sci., 2017, 18, 2421–2450 CrossRef PubMed.
- C. Liu, S. Wu, H. Zhang and R. Xiao, Fuel Process. Technol., 2019, 191, 181–201 CrossRef CAS.
- M. V. Galkin, A. T. Smit, E. Subbotina, K. A. Artemenko, J. Bergquist, W. J. J. Huijgen and J. S. M. Samec, ChemSusChem, 2016, 9, 3280–3287 CrossRef CAS PubMed.
- T. Renders, G. Van den Bossche, T. Vangeel, K. Van Aelst and B. Sels, Curr. Opin. Biotechnol., 2019, 56, 193–201 CrossRef CAS PubMed.
- S. Van den Bosch, T. Renders, S. Kennis, S. F. Koelewijn, G. Van den Bossche, T. Vangeel, A. Deneyer, D. Depuydt, C. M. Courtin, J. M. Thevelein, W. Schutyser and B. F. Sels, Green Chem., 2017, 19, 3313–3326 RSC.
- A. S. Jaufurally, A. R. S. Teixeira, L. Hollande, F. Allais and P. H. Ducrot, ChemistrySelect, 2016, 1, 5165–5171 CrossRef CAS.
- S. K. El-Desouky and A. M. Gamal-Eldeen, Pharm. Biol., 2009, 47, 872–877 CrossRef CAS.
- W. Monthong, S. Pitchuanchom, N. Nuntasaen and W. Pompimon, Am. J. Appl. Sci., 2011, 8, 1268–1271 CrossRef CAS.
- K. V. S. G. Krishna, M. P. S. M. Moses and G. S. Krishna, Asian J. Chem., 2009, 21, 11–22 Search PubMed.
-
S. Yshihide, K. Seiichi, H. Junichi, M. Hironaga and M. Hironaga, JP150152, 2010.
- M. Janvier, P. H. Ducrot and F. Allais, ACS Sustainable Chem. Eng., 2017, 5, 8648–8656 CrossRef CAS.
- M. Janvier, L. Hollande, A. S. Jaufurally, M. Pernes, R. Ménard, M. Grimaldi, J. Beaugrand, P. Balaguer, P. H. Ducrot and F. Allais, ChemSusChem, 2017, 10, 738–746 CrossRef CAS PubMed.
- A. Kaiho, D. Mazzarella, M. Satake, M. Kogo, R. Sakaia and T. Watanabe, Green Chem., 2016, 18, 6526–6535 RSC.
- S. Zhao and M. M. Abu-Omar, Macromolecules, 2017, 50, 3573–3581 CrossRef CAS.
- S. Zhao, X. Huang, A. J. Whelton and M. M. Abu-Omar, ACS Sustainable Chem. Eng., 2018, 6, 7600–7608 CrossRef CAS.
- S. F. Koelewijn, C. Cooreman, T. Renders, C. Andecochea Saiz, S. Van den Bosch, W. Schutyser, W. De Leger, M. Smet, P. Van Puyvelde, H. Witters, B. Van der Bruggen and B. F. Sels, Green Chem., 2018, 20, 1050–1058 RSC.
- F. M. Gírio, C. Fonseca, F. Carvalheiro, L. C. Duarte, S. Marques and R. Bogel-Łukasik, Bioresour. Technol., 2010, 101, 4775–4800 CrossRef PubMed.
- B. C. Saha, J. Ind. Microbiol. Biotechnol., 2003, 30, 279–291 CrossRef CAS PubMed.
- P. Mäki-Arvela, T. Salmi, B. Holmbom, S. Willför and D. Y. Murzin, Chem. Rev., 2011, 111, 5638–5666 CrossRef PubMed.
-
A. K. Chandel, F. A. F. Antunes, R. Terán-Hilares, J. Cota, S. Ellilä, M. H. L. Silveira, J. C. dos Santos and S. S. da Silva, Bioconversion of Hemicellulose into Ethanol and Value-Added Products: Commercialization, Trends, and Future Opportunities, Advances in Sugarcane Biorefinery, Elsevier, 2018, ch. 5 Search PubMed.
- T. Granstrom, K. Izumori and M. Leisola, Appl. Microbiol. Biotechnol., 2007, 74, 273–276 CrossRef PubMed.
- A. P. Tathod and P. L. Dhepe, Green Chem., 2014, 16, 4944–4954 RSC.
- B. M. Matsagar, M. K. Munshi, A. A. Kelkar and P. L. Dhepe, Catal. Sci. Technol., 2015, 5, 5086–5090 RSC.
- A. S. Mamman, J. M. Lee, Y. C. Kim, I. T. Hwang, N. J. Park, Y. K. Hwang, J. S. Chang and J. S. Hwang, Biofuels, Bioprod. Biorefin., 2008, 2, 438–454 CrossRef CAS.
-
K. J. Zeitsch, The chemistry and technology of furfural and its many by-products, Elsevier, Amsterdam, 2000, vol. 13 Search PubMed.
- C. M. Cai, T. Zhang, R. Kumar and C. E. Wyman, J. Chem. Technol. Biotechnol., 2014, 89, 2–10 CrossRef CAS.
- R. Mariscal, P. Maireles-Torres, M. Ojeda, I. Sádaba and M. López Granados, Energy Environ. Sci., 2016, 9, 1144–1189 RSC.
- K. Yan, G. Wu, T. Lafleur and C. Jarvis, Renewable Sustainable Energy Rev., 2014, 38, 663–676 CrossRef CAS.
-
K. Cho, S. Y. Kim, D. H. Lee, B. R. Kim, J. W. Jung, S. H. Lee and J. S. Lee, US0220742A1, 2012.
-
E. Breitmaier, Terpenes: Flavors, Fragrances, Pharmaca, Pheromones, Wiley-VCH, Weinheim, 2006 Search PubMed.
- M. De Vincenzi, A. Stammati, A. De Vincenzi and M. Silano, Fitoterapia, 2004, 75, 801–804 CrossRef CAS PubMed.
- E. De Falco, E. Mancini, G. Roscigno, E. Mignola, O. Taglialatela-Scafati and F. Senatore, Molecules, 2013, 18, 14948–14960 CrossRef CAS PubMed.
- V. V. Costa, K. A. da Silva Rocha, I. V. Kozhevnikov, E. F. Kozhevnikova and E. V. Gusevskaya, Catal. Sci. Technol., 2013, 3, 244–250 RSC.
- B. G. Harvey, A. J. Guenthner, T. A. Koontz, P. J. Storch, J. T. Reams and T. J. Groshens, Green Chem., 2016, 18, 2416–2423 RSC.
- M. D. Garrison and B. G. Harvey, J. Appl. Polym. Sci., 2016, 133, 43621–43633 CrossRef.
- V. S. Balachandran, S. R. Jadhav, P. K. Vemula and G. John, Chem. Soc. Rev., 2012, 42, 427–438 RSC.
- P. Campaner, D. D’Amico, L. Longo, C. Stifani Cristina and A. Tarzia, J. Appl. Polym. Sci., 2009, 114, 3585–3591 CrossRef CAS.
- J. H. P. Tyman, R. A. Johnson, M. Muir and R. Rokhgar, J. Am. Oil Chem. Soc., 1989, 66, 553–557 CrossRef CAS.
- D. Balgude and A. S. Sabnis, J. Coat. Technol. Res., 2014, 11, 169–183 CrossRef CAS.
- P. K. Jain and K. J. Sivala, J. Food Eng., 1997, 32, 339–345 CrossRef.
- S. Caillol, Curr. Opin. Green Sustainable Chem., 2018, 14, 26–32 CrossRef.
- C. Voirin, S. Caillol, N. V. Sadavarte, B. V. Tawade, B. Boutevin and P. P. Wadgaonkar, Polym. Chem., 2014, 5, 3142–3162 RSC.
- S. Huo, H. Ma, G. Liu, C. Jin, J. Chen, G. Wu and Z. Kong, ACS Omega, 2018, 3, 16403–16408 CrossRef CAS PubMed.
- J. J. Cash, M. C. Davis, M. D. Ford, T. J. Groshens, A. J. Guenthner, B. G. Harvey, K. R. Lamison, J. M. Mabry, H. A. Meylemans, J. T. Reams and C. M. Sahagun, Polym. Chem., 2013, 4, 3859–3865 RSC.
-
Resveratrol: Sources, Production and Health Benefits, ed. D. Delmas, Nova Science Publishers, Hauppauge, NY, USA, 2013 Search PubMed.
- C. Rivière, A. D. Pawlus and J. M. Mérillon, Nat. Prod. Rep., 2012, 29, 1317–1333 RSC.
- L. R. Cambrea, M. C. Davis, M. D. Garrison, T. J. Groshens, R. E. Lyon and N. Safronava, J. Polym. Sci., Part A: Polym. Chem., 2017, 55, 971–980 CrossRef CAS.
- M. Laskoski, J. S. Clarke, A. Neal, B. G. Harvey, H. L. Ricks-Laskoski, W. J. Hervey, M. N. Daftary, A. R. Shepherd and T. M. Keller, ChemistrySelect, 2016, 1, 3423–3427 CrossRef CAS.
- X. Liu, C. Pang, J. Ma and H. Gao, Macromolecules, 2017, 50, 7949–7958 CrossRef CAS.
- C. Pang, X. Jiang, Y. Yu, X. Liu, J. Lian, J. Ma and H. Gao, ACS Sustainable Chem. Eng., 2018, 6, 17059–17067 CrossRef CAS.
- S. H. Bertz, J. M. Cook, A. Gawish and U. Weiss, Org. Synth., 1986, 64, 27–38 CrossRef CAS.
- T. W. T. Muesmann, M. S. Wickleder, C. Zitzer and J. Christoffers, Synlett, 2013, 959–962 CAS.
- Y. Yu, C. Pang, X. Jiang, Z. Yang, J. Ma and H. Gao, ACS Macro Lett., 2019, 8, 454–459 CrossRef CAS.
- Y. Hu, Z. Zhao, Y. Liu, G. Li, A. Wang, Y. Cong, T. Zhang, F. Wang and N. Li, Angew. Chem., Int. Ed., 2018, 57, 6901–6905 CrossRef CAS PubMed.
- C. Aouf, H. Nouailhas, M. Fache, S. Caillol, B. Boutevin and H. Fulcran, Eur. Polym. J., 2013, 49, 1185–1195 CrossRef CAS.
- G. Rigane, M. Bouaziz, N. Baccar, S. Abidi, S. Sayadi and R. B. Salem, J. Food Sci., 2012, 77, C1077–C1083 CrossRef CAS PubMed.
-
C. K. George, Star anise, Handbook of Herbs and Spices, Woodhead Publishing, 2012, ch, 24, vol. 2 Search PubMed.
- M. C. Davis, A. J. Guenthner, T. J. Groshens, J. T. Reams and J. M. Mabry, J. Polym. Sci., Part A: Polym. Chem., 2012, 50, 4127–4136 CrossRef CAS.
- W. Schutyser, S. F. Koelewijn, M. Dusselier, S. Van de Vyver, J. Thomas, F. Yu, M. J. Carbone, M. Smet, P. Van Puyvelde, W. Dehaen and B. F. Sels, Green Chem., 2014, 16, 1999–2007 RSC.
- M. Dusselier, P. Van Wouwe, A. Dewaele, E. Makshina and B. F. Sels, Energy Environ. Sci., 2013, 6, 1415–1442 RSC.
- A. A. Marianou, C. C. Michailof, D. Ipsakis, K. Triantafyllidis and A. A. Lappas, Green Chem., 2019, 21, 6161–6178 RSC.
- Q. Guo, F. T. Fan, E. A. Pidko, W. N. P. van der Graaff, Z. C. Feng, C. Li and E. J. M. Hensen, ChemSusChem, 2013, 6, 1352–1356 CrossRef CAS PubMed.
- J. Wang, X. Liu, Z. Jia, Y. Liu, L. Sum and J. Zhu, J. Polym. Sci., Part A: Polym. Chem., 2017, 55, 3298–3307 CrossRef CAS.
- J. Wang, X. Liu, J. Zhu and Y. Jiang, Polymers, 2017, 9, 305–319 CrossRef PubMed.
- J. Wang, S. Mahmud, X. Zhang, J. Zhu, Z. Shen and X. Liu, ACS Sustainable Chem. Eng., 2019, 7, 6401–6411 CrossRef CAS.
- E. Wedekind and W. Weisswange, Ber. Dtsch. Chem. Ges., 1906, 39, 1631–1646 CrossRef CAS.
- D. J. Burke, T. Kawauchi, M. J. Kade, F. A. Leibfarth, B. McDearmon, M. Wolffs, P. H. Kierstead, B. Moon and C. J. Hawker, ACS Macro Lett., 2012, 1, 1228–1232 CrossRef CAS.
- J. J. Wiesfeld, M. Kim, K. Nakajima and E. J. M. Hensen, Green Chem., 2020, 22, 1229–1238 RSC.
- F. Brandi, M. Bäumel, V. Molinari, I. Shekova, I. Lauermann, T. Heil, M. Antonietti and M. Al-Naji, Green Chem., 2020, 22, 2755–2766 RSC.
- S. F. Koelewijn, D. Ruijten, L. Trullemans, T. Renders, P. Van Puyvelde, H. Witters and B. F. Sels, Green Chem., 2019, 21, 6622–6633 RSC.
- Y. Zhu, C. Romain and C. K. Williams, Nature, 2016, 540, 354–362 CrossRef CAS PubMed.
- M. A. Hillmyer, Science, 2017, 358, 868–870 CrossRef CAS PubMed.
- A. F. Sousa, C. Vilela, A. C. Fonseca, M. Matos, C. S. R. Freire, G. J. M. Gruter, J. F. J. Coelho and A. J. D. Silvestre, Polym. Chem., 2015, 6, 5961–5983 RSC.
-
E. Mazoyer, A. S. V. De Sousa Dias, B. Mckay, H. J. Baars, V. P. C. Vreeken, G. J. M. Gruter and D. L. Sikkenga, WO163500A1, 2014.
- M. Kaushik and A. Moores, Curr. Opin. Green Sustainable Chem., 2017, 7, 39–45 CrossRef.
- J. A. Dahl, B. L. S. Maddux and J. E. Hutchison, Chem. Rev., 2007, 107, 2228–2269 CrossRef CAS PubMed.
-
J. A. Gladysz, in Recoverable and Recyclable Catalysts, ed. M. Benaglia, John Wiley & Sons, Chichester, 2009, ch. 1 Search PubMed.
- M. J. Ndolomingo, N. Bingwa and R. Meijboom, J. Mater. Sci., 2020, 55, 6195–6241 CrossRef CAS.
- X. Luo, Y. Li, N. K. Gupta, B. Sels, J. Ralph and L. Shuai, Angew. Chem., Int. Ed., 2020, 59, 11704–11716 CrossRef CAS PubMed.
- A. H. Motagamwala, W. Won, C. Sener, D. M. Alonso, C. T. Maravelias and J. A. Dumesic, Sci. Adv., 2018, 4, eaap9722 CrossRef PubMed.
- M. A. Mellmer, C. Sener, J. M. R. Gallo, J. S. Luterbacher, D. M. Alonso and J. A. Dumesic, Angew. Chem., Int. Ed., 2014, 53, 11872–11875 CrossRef CAS PubMed.
- P. T. Witte, S. Boland, F. Kirby, R. van Maanen, B. F. Bleeker, D. A. M. de Winter, J. A. Post, J. W. Geus and P. H. Berben, ChemCatChem, 2013, 5, 582–587 CrossRef CAS.
- K. Dietrich, C. Hernandez-Mejia, P. Verschure, G. Rothenberg and N. R. Shiju, Org. Process Res. Dev., 2017, 21, 165–170 CrossRef CAS.
- B. Op de Beeck, J. Geboers, S. Van de Vyver, J. Van Lishout, J. Snelders, W. J. J. Huijgen, C. M. Courtin, P. A. Jacobs and B. F. Sels, ChemSusChem, 2013, 6, 199–208 CrossRef CAS PubMed.
- R. Palkovits, K. Tajvidi, J. Procelewska, R. Rinaldi and A. Ruppert, Green Chem., 2010, 12, 972–978 RSC.
- P. Gupta and S. Paul, Catal. Today, 2014, 236, 153–170 CrossRef CAS.
- K. Shimizu and A. Satsuma, Energy Environ. Sci., 2011, 4, 3140–3153 RSC.
- C. Moreno-Marrodan, F. Liguori, P. Barbaro, S. Caporali, L. Merlo and C. Oldani, ChemCatChem, 2017, 9, 4256–4267 CrossRef CAS.
- A. Karam, K. De Oliveira Vigier, S. Marinkovic, B. Estrine, C. Oldani and F. Jérôme, ChemSusChem, 2017, 10, 3604–3610 CrossRef CAS PubMed.
- P. N. R. Vennestrøm, C. H. Christensen, S. Pedersen, J. D. Grunwaldt and J. M. Woodley, ChemCatChem, 2010, 2, 249–258 CrossRef.
- J. H. Schrittwieser, S. Velikogne, M. Hall and W. Kroutil, Chem. Rev., 2018, 118, 270–348 CrossRef CAS PubMed.
- A. Galarneau, Z. Abid, B. Said, Y. Didi, K. Szymanska, A. Jarzebski, F. Tancret, H. Hamaizi, A. Bengueddach, F. Di Renzo and F. Fajula, Inorganics, 2016, 4, 9–34 CrossRef.
- C. Moreno-Marrodan, P. Barbaro, S. Caporali and F. Bossola, ChemSusChem, 2018, 11, 3649–3660 CrossRef CAS PubMed.
-
J. K. Mobley, in Chemical Catalysts for Biomass Upgrading, ed. M. Crocker and E. Santillan-Jimenez, Wiley-VCH, 2020, ch. 8 Search PubMed.
- R. T. Mathers, J. Polym. Sci., Part A: Polym. Chem., 2012, 50, 1–15 CrossRef CAS.
- A. Rahimi, A. Ulbrich, J. J. Coon and S. S. Stahl, Nature, 2014, 515, 249–252 CrossRef CAS PubMed.
- T. Huang, L. A. Danaher, B. J. Brüschweiler, G. E. N. Kass and C. Merten, Arch. Toxicol., 2019, 93, 1485–1490 CrossRef CAS PubMed.
-
R. S. Ward, Studies in Natural Products Chemistry, 2000, vol. 24, pp. 739–798 Search PubMed.
- J. Zhang, J. J. Chen, Z. Z. Liang and C. Q. Zhao, Chem. Biodiversity, 2014, 11, 1–54 CrossRef CAS PubMed.
- W. Qiu, Y. Zhao, M. Yang, M. Farajzadeh, C. Pan and N. L. Wayne, Endocrinology, 2016, 157, 636–647 CrossRef CAS PubMed.
- S. P. den Braver-Sewradj, R. van Spronsen and E. V. S. Hessel, Crit. Rev. Toxicol., 2020, 50, 128–147 CrossRef CAS PubMed.
- A. T. Szafran, F. Stossi, M. G. Mancini, C. L. Walker and M. A. Mancini, PLoS One, 2017, 12, e0180141 CrossRef PubMed.
- J. B. Zimmerman and P. T. Anastas, Science, 2015, 347, 1198–1199 CrossRef CAS PubMed.
- A. de Sousa Leite, A. Ferreira Dantas, G. L. da Silva Oliveira, A. L. Gomes Júnior, S. G. de Lima, A. M. das Graças Lopes Citó, R. M. de Freitas, A. A. de, C. Melo-Cavalcante and J. A. D. Lopes, BioMed Res. Int., 2015, 626835 Search PubMed.
- S. M. Morais, K. A. Silva, H. Araujo, I. G. P. Vieira, D. R. Alves, R. O. S. Fontenelle and A. M. S. Silva, Pharmaceuticals, 2017, 10, 31–41 CrossRef PubMed.
- V. M. Pathak and Navneet, Bioresour. Bioprocess., 2017, 4, 15–46 CrossRef.
- I. Taniguchi, S. Yoshida, K. Hiraga, K. Miyamoto, Y. Kimura and K. Oda, ACS Catal., 2019, 9, 4089–4105 CrossRef CAS.
- C. Jehanno, M. M. Pérez-Madrigal, J. Demarteau, H. Sardon and A. P. Dove, Polym. Chem., 2019, 10, 172–186 RSC.
- K. Fukushima, O. Coulembier, J. M. Lecuyer, H. A. Almegren, A. M. Alabdulrahman, F. D. Alsewailem, M. A. McNeil, P. Dubois, R. M. Waymouth, H. W. Horn, J. E. Rice and J. L. Hedrick, J. Polym. Sci., Part A: Polym. Chem., 2011, 49, 1273–1281 CrossRef CAS.
- S. Westhues, J. Idel and J. Klankermayer, Sci. Adv., 2018, 4, eaat9669 CrossRef CAS PubMed.
- K. Dutt and R. K. Soni, Polym. Sci., Ser. B, 2013, 55, 430–452 CrossRef CAS.
Footnote |
† Electronic supplementary information (ESI) available. See DOI: 10.1039/d0cs00179a |
|
This journal is © The Royal Society of Chemistry 2020 |
Click here to see how this site uses Cookies. View our privacy policy here.