DOI:
10.1039/C9CS00330D
(Review Article)
Chem. Soc. Rev., 2020,
49, 1109-1143
Rare-earth-containing perovskite nanomaterials: design, synthesis, properties and applications
Received
1st October 2019
First published on 15th January 2020
Abstract
As star material, perovskites have been widely used in the fields of optics, photovoltaics, electronics, magnetics, catalysis, sensing, etc. However, some inherent shortcomings, such as low efficiency (power conversion efficiency, external quantum efficiency, etc.) and poor stability (against water, oxygen, ultraviolet light, etc.), limit their practical applications. Downsizing the materials into nanostructures and incorporating rare earth (RE) ions are effective means to improve their properties and broaden their applications. This review will systematically summarize the key points in the design, synthesis, property improvements and application expansion of RE-containing (including both RE-based and RE-doped) halide and oxide perovskite nanomaterials (PNMs). The critical factors of incorporating RE elements into different perovskite structures and the rational design of functional materials will be discussed in detail. The advantages and disadvantages of different synthesis methods for PNMs will be reviewed. This paper will also summarize some practical experiences in selecting suitable RE elements and designing multi-functional materials according to the mechanisms and principles of REs promoting the properties of perovskites. At the end of this review, we will provide an outlook on the opportunities and challenges of RE-containing PNMs in various fields.
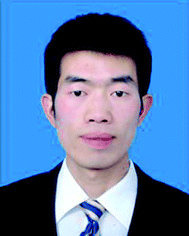
Zhichao Zeng
| Zhichao Zeng is a doctoral candidate at the School of Materials Science and Engineering, Nankai University, under the supervision of Prof. Yaping Du. His research focuses on the luminescent and electrical applications of rare-earth-containing perovskites. He received his MEng Degree (2017) from Northwest A&F University, and received his BE degree (2014) from Zhengzhou University. |
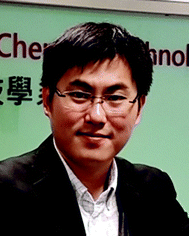
Bolong Huang
| Bolong Huang is an assistant professor at the Department of Applied Biology and Chemical Technology, The Hong Kong Polytechnic University. His main research fields are DFT calculations on rare earth functional nanomaterials and defect theory of solid functional nanomaterials. He obtained his BSc Degree from Peking University in 2007 and received his PhD Degree from The University of Cambridge in 2012. |
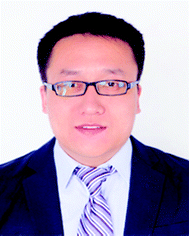
Yaping Du
| Yaping Du is a full professor at the School of Materials Science and Engineering, Nankai University, and the director of Tianjin Key Lab for Rare Earth Materials and Applications. His research interests focus on rare-earth functional materials, colloidal inorganic nanocrystals, and energy storage and conversion materials. In 2004, he received his BSc Degree from Lanzhou University, and in 2009, he received his PhD degree from Peking University. |
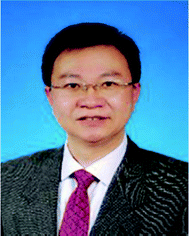
Chunhua Yan
| Chun-Hua Yan is the president of Lanzhou University and the director of the State Key Laboratory of Rare Earth Materials Chemistry and Applications at Peking University, and the Center for Rare Earth and Inorganic Functional Materials at Nankai University. He received his BSc, MSc, and PhD degrees from Peking University. He was elected as a Member of the Chinese Academy of Sciences in 2011. |
1. Introduction
Perovskites are becoming research hotspots and have been extensively studied for their variable formulae, flexible structures, numerous unique properties and broad applications.1–4 The earliest identified perovskite is CaTiO3, and later this formula was derived into a wealth of new forms, such as ABX3, A3B2X9, A2BB′X6, A2BX6, A4BX6, and so on, in which A and B are cations (A has a larger radius than B), and X is a halogen or oxygen anion. The two different anions and various metal cations form halide perovskites and oxide perovskites. These two types of perovskites have many similar crystal structures, and both of them contain BX6 octahedra in their crystal structures, and A atoms locate in the interstitial void of neighboring octahedra.5–8 The diverse compositions and structures endow perovskite materials with various properties and wide applications:4,5,9,10 luminescent perovskites have been used in the field of illumination, displays, sensing, biological imaging, etc.;11–15 some photoelectric perovskites have been applied in the areas of photovoltaics, photo-catalysis, electro-catalysis, etc.;16–21 electrical perovskites are used to prepare dielectric devices, ionic conductors, etc.;22–25 magnetic perovskites are used in magnetic refrigeration, information storage, biomedical imaging and other fields.26–28
With increasing attention on the development of nanotechnology and multi-disciplinary research, scientists have been trying to downscale the perovskite structures into the nanoregime, so as to further boost their performances and applications.1,29,30 Compared with bulk perovskite materials, perovskite nanomaterials (PNMs, including nanoparticles, nanowires, nanofilms, etc.) exhibit a series of advantages: for the fabrication of thin films and flexible devices, PNMs display high processability;31,32 for catalysis, PNMs feature rich and controllable facets and active sites;33,34 besides, benefiting from the small-size effect and quantum effect, PNMs are endowed with outstanding photo-electro-magnetic properties.35–41 All these new characteristics help enrich the performances of perovskites, and broaden their applications.
However, pristine perovskites have some inherent drawbacks, for instance, some halide PNMs have poor stability (against water, oxygen, heat, etc.) and limited adjustability of optical and electrical properties; some oxide PNMs have unsatisfactory catalytic, optical and electromagnetic performances.2,10,32,42,43 Scientists have been incorporating foreign metal ions into PNMs to overcome these shortcomings.3,5,30,44 Rare earth (RE) elements, known as ‘the vitamins of modern industry’, are extensively used as dopants or components to modulate the specific physical and chemical properties of different materials.45,46 The RE elements, including 15 lanthanides (Ln: La, Ce, Pr, Nd, Pm, Sm, Eu, Gd, Tb, Dy, Ho, Er, Tm, Yb, and Lu) and scandium (Sc) and yttrium (Y), have various multivalent ions: the RE3+ ions have the electron configurations of [Xe]4fn−1 for Ln3+ (n = 1–15), [Ar] for Sc3+ and [Kr] for Y3+; the RE2+ (Sm2+, Eu2+ and Yb2+) and RE4+ (Ce4+, Pr4+, Nd4+, Tb4+ and Dy4+) ions have the electron configurations of [Xe]4fn and [Xe]4fn−2, respectively.47,48 Their variable valence states and electronic structures endow RE ions with flexible redox properties, and unique luminous and electromagnetic characteristics.49 Therefore, REs have been widely incorporated into perovskite nanostructures to improve their performances and broaden their applications.50,51 In addition, researchers have synthesized a series of RE-based perovskite functional materials.52,53 Both RE-doped and RE-based PNMs exhibit satisfactory performances.5,54
In view of the broad attention paid to RE-containing PNMs, this review will introduce their basic compositions, variable structures, preparation methods, properties and applications (Scheme 1). The rational design and controllable syntheses of RE-containing PNMs will be discussed in detail. Furthermore, the mechanisms through which REs improve the performances of perovskites will be summarized. Also, the applications of PNMs in the fields of energy, environment, photo-electrics and electromagnetics will be reviewed. This article will also discuss the possible solutions to the problems in their application by optimizing their compositions, structures and preparation methods. At the end of this review, the emerging opportunities and challenges in the development of RE-containing PNMs are provided.
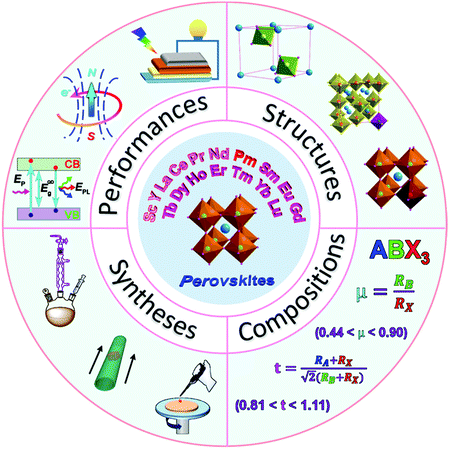 |
| Scheme 1 Schematic illustration of the structure, composition, synthesis and performance of RE-containing perovskite nanomaterials. | |
2. Design of RE-containing PNMs
In order to obtain multifunctional RE-containing PNMs with stable structure and excellent properties, their compositions and structures should be elaborately designed.6,7,55,56 Beyond the most typical metal oxide and halide compositions, many elements in the periodic table can serve as the component parts for preparing perovskite materials, yet only a limited number of them are able to construct stable perovskite structures. In addition, REs themselves can serve as the matrix element for stable perovskites. In particular, the stability of perovskites is dependent on the tolerance factor (t) and octahedral factor (μ),57,58 which strongly correlates with the difficulties of RE doping in perovskites.59 Furthermore, suitable chemical components can be selected and incorporated to construct functional perovskites according to the expected performances and applications.60–62
2.1 The diversity of perovskite crystal structures
In general, ABX3 perovskites usually display a six-coordinated B-site with X by forming an octahedral structure, surrounded by an A-site.5 According to the arrangement of the octahedron and A-site, perovskites can be divided into four types: zero-dimensional (0D), one-dimensional (1D) perovskites, two-dimensional (2D) and three-dimensional (3D) perovskites (Fig. 1).63 If the BX6 octahedra share X anions with adjacent ones in three-dimensional directions, the octahedra connect with each other, which corresponds to the 3D perovskite structure.64 In comparison, when the BX6 is connected with the shared X anions only in the 2D plane, then a 2D perovskite crystal is formed.65 It is also noted when the A-site is occupied by groups that are too large, such as the long-chain alkyl amine cations, typical lead halide perovskites would turn into 2D Ruddlesden–Popper (RP) layered structure perovskites, which can be further classified by the layer number.66 In a similar fashion, the 1D connection of BX6 octahedron represents a 1D perovskite crystal.67 In particular, if the BX6 octahedron is separated by excessive A atoms without any connections to each other, it is called a 0D perovskite crystal.68 Most oxide perovskites have a 3D structure, and only a few of them have 2D, 1D and 0D structures.2,5,19 However, halide perovskites have optional halogen elements and various coordination modes, and most of them are of 3D structure, and 2D, 1D and 0D structures are relatively uncommon.64,67,69 Owing to the varied crystal structures and multiple types of perovskites, their structures have a more powerful adjustable capacity. So the incorporation of RE ions into the structures becomes much more flexible.68,70–72 Therefore, the incorporation strategy of RE ions into perovskites opens new opportunities in designing multi-functional RE-containing perovskite materials.
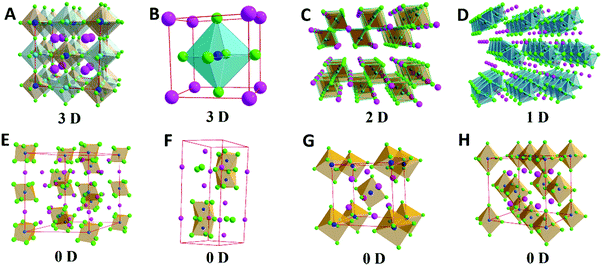 |
| Fig. 1 Various crystal structures of perovskites: (A) 3D double perovskites, (B) 3D single perovskites, (C) 2D perovskites, (D) 1D perovskites, and (E–H) 0D perovskites. | |
2.2 Tolerance factor and octahedral factor
Perovskites were first discovered as a common mineral with the chemical composition of CaTiO3, and later developed into a series of derivatives with chemical formulas of ABX3, A3B2X9, A2BB′X6, A2BX6, etc., as shown in Fig. 2.73–76 Perovskites can be divided into halides and oxides: for the halide perovskites, A is a univalent cation (K+, Na+, Rb+, Cs+, R-NH3+, etc.), B is a multivalent metal ion (Mg2+, Zn2+, Pb2/4+, Sn2/4+, Sb3+, In3+, Bi3+, etc.), and X represents a halide anion (F−, Cl−, Br−, I−); oxide perovskites (X = O2−) have the compositions of multi-valent metal cations (Ca2+, Ti4+, Fe3+, Pb4+, etc.), in which cations with a larger radius occupy the A-site while smaller ions occupy the B-site, and X is O2−.5,44,61 In an ideal perovskite of ABX3, the radii of all these cations and anions should meet the tolerance factor
and octahedral factor (μ = RB/RX); RA, RB, and RX refer to the ionic radii of A, B and X, respectively.7,57 The t value often varies from 0.81 to 1.11; otherwise, the cubic or cubic-like crystal structure would be distorted, and even destroyed.4 A smaller t value would result in lower-symmetrical tetragonal or orthorhombic structures. The t value of an ideal cubic structure varies in the range from 0.89 to 1.0.57 The value of μ ranges between 0.44 and 0.90, which determines the stability of the octahedron, and further affects the stability of the perovskite structure.77 For the most well-known perovskite, CsPbBr3, the ionic radii of Cs+, Pb2+ and Br− are about 170 pm, 119 pm and 195 pm, respectively, which derive a value of t of 0.82, and a μ value of 0.62. |  | (1) |
| 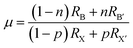 | (2) |
| 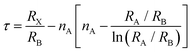 | (3) |
| 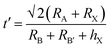 | (4) |
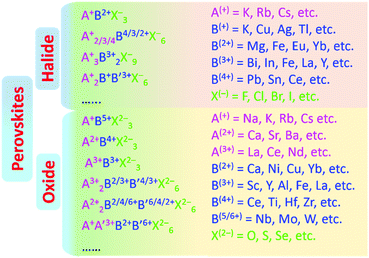 |
| Fig. 2 Various types and components of halide and oxide perovskites. | |
In polyatomic hybrid perovskite systems, such as AB1−nB′nX3, A1−mA′mBX3, A1−mA′mB1−nB′n(X1−pX′p)3, and even other complex systems, the factors of t (eqn (1)) and μ (eqn (2)) are otherwise deduced, where R is the ionic radius of different ions.6,72,78 While, as for the double perovskites of A2BX6, owing to the numerous B-site vacancies, t is not a suitable index for evaluating the stability of its structure. So a new tolerance factor τ (eqn (3)) is proposed (τ < 4.18), where R is the ionic radius, and nA is the oxide state of the A ion. As τ decreases, the probability of being a perovskite increases.58,75 The τ value is more suitable for evaluating the stability of double perovskites, according to the theoretical calculation and experimental verification.79 In addition, another tolerance factor t′ (eqn (4)) for A2BB′X6 has been reported, where R is the ionic radius, and hX represents the effective height of X in the rigid cylinder.56 Therefore, the possibility of forming double perovskites and their stability can be quantitatively described.
According to the tolerance factor and octahedral factor, we can select appropriate RE ions to replace the positions of A and B in perovskite structures, to further construct new functional perovskite materials. RE ions can replace the B-site in halide perovskites, and occupy the A-site or B-site in oxide perovskites.45,80,81 In addition, some articles reported the theoretical calculation results and experimental data to support the possibilities of incorporating RE elements into perovskite crystal structures.45,82 It is worth mentioning that Eu has been identified that acts as a redox shuttle in the perovskite to selectively oxidize Pb0 and reduce I0 defects for the long-term stability of perovskites.9 Based on the previous reports and theories, researchers can rationally design various RE-doped multifunctional perovskite materials.
2.3 Theoretical investigation
Owing to the development of theoretical calculations and simulations, we are able to carry out theoretical investigations beyond the traditional experimental characterizations, which provide insightful information on the electronic behaviours and energetic behaviours of perovskites.83 This approach supplies the possible routes to design and synthesize RE-containing perovskite materials based on the mechanistic studies. Guo and his co-workers declared that the A(B) vacancy can easily bind with the RE3+ when in the O-rich areas.6,59,84 For oxide based perovskites, such as CeAlO3, LaMnO3 and SmNiO3, other RE ions can be easily incorporated into them, because the chemical properties of different RE elements are extremely similar.85–87 By using CaTiO3 as an example, Lu et al. demonstrate the doping trend of RE ions based on systematic DFT calculations. For heavier RE ions, the substitution of Ca and Ti sites is favoured under p-type for the trivalent state and n-type growth for divalent, respectively. Meanwhile, the Ca-site doping dominates the light RE ions.88,89
As for halide perovskites, RE can be easily introduced into their structures, for instance, in CsPbBr3 perovskite, the ionic radius of divalent Pb2+ is about 119 pm, and the RE2+ (Eu2+, Yb2+, Sm2+, etc.) has a radius between 102 pm and 117 pm;45,90 as for Cs2AgBiCl6 double perovskite, the radius of Bi3+ is 103 pm, which is very similar to the radius of RE3+ (Y3+, La3+, Nd3+, etc.) (86–103 pm),91,92 indicating a lower barrier for RE doping in halide perovskite materials. Pazoki and Kullgren further demonstrated that RE-doped iodide could be used as a potential photo-absorber for photovoltaic applications, which is ascribed to the dominant contribution from the valence band maximum by the localized f-electrons.93
Theoretical calculations are also of great importance in revealing the electroactivity of RE-doped perovskites. For the high electroactivity of RE-doped perovskites, Kilner et al. reported the unique electronic configuration of RE, in which the partially occupied d-orbital of RE and the associated partial covalence instead of the complete ionization are responsible for the catalytic behaviours.94 Furthermore, Shao and co-workers demonstrated the A-site ionic electronegativity (AIE) as an indicator in perovskites to predict the HER performance. DFT studies demonstrate that an optimal AIE value of ∼2.33 indicates the optimal electronic states of active B-sites in perovskites due to the inductive effects and electron exchange interactions between the A-site and B-site.95
2.4 Evaluation of RE-incorporation
Many works have reported that the properties and performances of perovskites can be improved and promoted by RE doping.11,96 It is well known that Pb-halide-based perovskites have excellent optical and electrical properties, which are widely used in the field of perovskite solar cells (PSCs), and some of them have outstanding performances.73 However, those pristine phases of Pb-based halide perovskites have various inherent drawbacks, such as poor stability against heat, light and humidity, etc.32,97 In order to overcome these shortcomings, an RE ion pair Eu2/3+ was incorporated into the CsPbI3 perovskite, where the redox characteristics of Eu2/3+ can stabilize the structure.9,98 The Eu2/3+:CsPbI3 encapsulated solar cell not only exhibits high photoelectric conversion efficiency (PECE), but also has a durable service life. In addition, when serving as light-absorbing materials for solar cells, the absorption ability of halide perovskites is relatively limited from ultraviolet (UV) to visible light,64 which largely leaves the solar light in the infrared region unused and limits the PECE of PSCs. In this regard, RE3+ ions (Yb3+,Ce3+) were doped into perovskites showing evidently extended light absorption towards the near infrared (NIR) region, and the prepared PSCs show high PECE.96,99
Halide perovskites, such as CsPbBr3 and Cs2AgBi1−nSbnBr6 nanocrystals (NCs), have some excellent photoluminescence (PL) properties. However, because their emission wavelength can be regulated only in the visible light region, it is difficult for them to emit NIR light, and the emission peaks generally have a broad full width at half maximum (FWHM) of emission peaks and the PL decay time is very short.100–102 Beyond this, the emission spectra of PNMs can be adjusted from the UV, visible to the NIR region by doping RE3+ (Tm3+, Ce3+, Tb3+, Sm3+, Eu3+, Er3+, Ho3+, Dy3+ and Yb3+). RE ions have special luminescence properties: the emission peaks of RE ions are very narrow, with FWHM of only a few nanometers; the luminescence decay time is relatively long, which can reach several microseconds; and their emission spectra cover a wide range from UV to NIR.49,103 Some works have been reported on RE-doped perovskites, in which the RE ions greatly broaden the spectral range of perovskite materials.39,104 Furthermore, the addition of RE ions can also improve the luminescence efficiency and the stability of PNMs.11,12,105
Compared with the halide perovskites, the oxide perovskite materials display various special functions by incorporating RE ions.106–108 By doping luminescent RE ions into oxide perovskites, a series of optical materials are prepared, which can be used in lighting, displays, detection, biological imaging and other fields.15,109–111 For example, GdFeO3 oxide perovskite exhibits a highly sensitive gas response to NOx and a low detection level of 2 ppm, and show a high resistance variation in the presence of NO.112 Perovskites containing magnetic RE ions have also been studied in the fields of biomedical imaging and magnetic devices.28,113–115 For example, Gd(Tb)FeO3 has good magnetic properties, which shows great potential in the biomedical field as a T2 MRI contrast agent. In addition, excellent dielectric properties are noted in some RE-based oxide perovskites, which can serve as dielectrics in various electric devices.116
Different from the direct doping strategy, RE-based oxide perovskites are important catalyst materials with high thermal and environmental stability.5 The multivalent RE ions endow perovskite materials with excellent redox properties and further give the catalysts special catalytic activity, which is widely used in energy conversion, environmental purification, chemical industry, and other fields.19,117–119 There are numerous works about RE-based oxide perovskites as catalysts in different catalytic processes. LaNiO3 can act as an efficient electro-catalyst for the oxygen evolution reaction (OER) for new rechargeable zinc–air batteries.120 LaFeO3 has been reported as a photo-catalyst for the degradation of organic dyes;121 La0.5Ba0.5MnO3 has high stability and catalytic activity for CO and CH4 oxidation.122 La1−nCenMnO3 could catalyse NO reduction to NH3 at low temperatures.123 CeAlO3 can serve as a catalyst, promoting glycerol steam hydrogenolysis and dehydrogenation-dehydration to produce hydrogen.124 All in all, RE ions play an indispensable role in oxide perovskite catalysts, and the RE ions are remarkable dopants and important components which can improve the catalytic activity.3 Moreover, RE based perovskites can be easily functionalized by a combination of the unique perovskite structure and the specific RE ions.125–127
2.5 RE-containing PNMs
In view of both PNMs and RE ions having excellent properties, it is necessary to combine them systematically. RE-containing PNMs possess special optical, magnetic, electronic and catalytic properties. These unique properties originate from the effectively shielded electrons in the 4f subshell by the electrons in the outer 5s and 5p subshells.128 Therefore, by doping RE ions, adjusting the sizes and morphologies of PNMs can yield unprecedented and unexpected new multifunctional materials.35,129,130
Recently, various works about RE-containing PNMs have been reported. In photovoltaics, RE-doped perovskite nanofilm (NF) materials have been reported featuring high PECE and durable stability.45,131 As for light emitting diodes (LEDs), RE-containing perovskite NCs not only improve the luminescence efficiency and broaden the spectral range, but also have high stability.4,11,12,107,110 And RE-containing PNMs exhibit good optical properties in the fields of non-linear optics and lasers.1,132 Besides, in electronics, RE-containing perovskite nanopowders (NPDs) can improve the dielectric properties and expand the applications of materials in electronics.2,133 In the biomedical fields, RE-containing perovskite NCs can be used as contrast agents for bioimaging.49,134 RE-based perovskite nanocatalysts have unique catalytic properties.18,135 In the field of analysis and detection, RE-containing perovskite materials have high sensitivities and fast responses to some metal ions, gases, temperature, X-rays, and so on.14,112,136–140 Finally, with the above classical cases, we can design RE-containing PNMs catering to the different requirements in practical applications.
3. Synthetic methods
The preparation process is of pivotal importance in studying the composition, structure and performance of nanomaterials.55 Developing highly efficient and controllable synthesis strategies for RE-containing PNMs is very important to design and modulate new functional materials, and is also essential for understanding the intrinsic mechanisms of their enhanced performances in PL, catalysis, photovoltaics and ferroelectric devices.129,141–143 Presently, the major challenge of RE-containing PNM synthesis is to achieve flexible control in replacing the positions of cations (B or A) in the perovskite structures with RE ions.37,40,126,144
Over the past few years, various helpful synthesis methods have been reported on preparing RE-containing PNMs (Fig. 3).39,45,145–148 These methods have important guiding significance for the synthesis of RE-containing PNMs, and these methods have been feasible for the preparation of RE-containing PNMs with different morphologies. All of these methods can be divided mainly into three categories: wet chemical synthesis methods, high-temperature synthesis processes and other synthesis approaches.46,77,108,149 Although there are many ways to synthesize nanomaterials, all of these processes involve two core steps, nucleation and growth.150 The raw materials release abounding free atoms or ions under heating liquefaction, solution ionization and high voltage plasma. These free atoms or ions accumulate into small aggregates, namely, crystal nuclei, to complete the nucleation step.92,151,152 Then continuously released free atoms or ions bond or assemble on the surface of the nucleus, which corresponds to the growth step of NCs.149 The nanomaterials are obtained by stopping the supply of free ions or atoms via cooling or adding anti-solvents.11,39 Different preparation methods of materials have their special advantages and disadvantages, and thus it is very important to select the suitable preparation methods according to the characteristics of raw materials and target compounds.
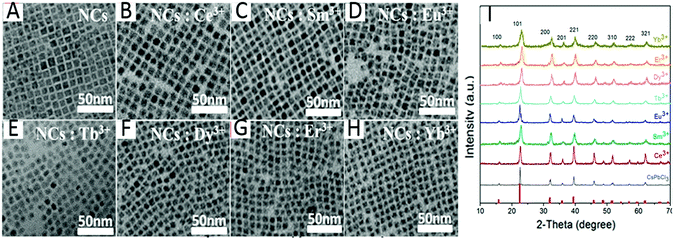 |
| Fig. 3 RE-doped CsPbCl3 NCs synthesized by the HI method. (A–H) TEM (transmission electron microscopy) images of Ln3+ doped CsPbCl3 NCs (Ln = Ce, Sm, Eu, Tb, Dy, Er, Yb). (I) XRD (X-ray diffraction) patterns of CsPbCl3 NCs doped with Ln3+. Reprinted with permission from ref. 39. Copyright 2017, American Chemical Society. | |
3.1 Wet chemical (WC) synthetic methods
Wet chemical synthesis methods have been widely used in the preparation of RE-containing nanomaterials, including the sol–gel (SG) method, thermal decomposition (TD) approach, hot injection (HI) method, solvothermal (ST) synthesis, co-precipitation (CPT) and so on.39,153–156 Among these methods, the HI, CPT and TD approaches have been demonstrated to be the most effective methods to synthesize RE-containing halide PNMs, whereas SG and ST are widely used to synthesize oxide PNMs.
3.1.1 Hot injection (HI) and thermal decomposition (TD) method.
As for the preparation of RE-containing PNMs, HI and TD have the advantages of simple operation and good repeatability. Meanwhile, the materials prepared by HI and TD methods have uniform size, controllable morphologies and excellent dispersibility (Fig. 4), which are essential requirements for achieving good performances.39 Typically, HI and TD methods require solvents or surfactants with high boiling points, such as 1-octadecene (ODE), oleic acid (OA) and oleylamine (OM), and the reactions are carried out in a flask protected by inert gases.11,149,152
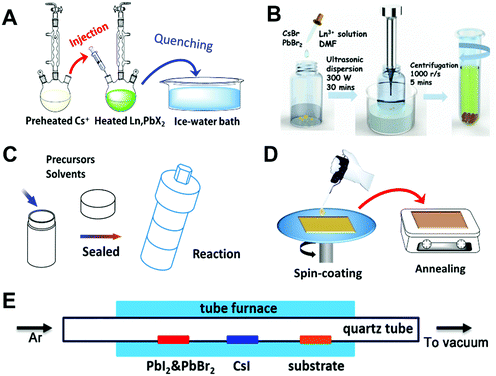 |
| Fig. 4 Various preparation methods for PNM preparation. (A) Hot-injection method, (B) ultrasonic co-precipitation method. Reprinted with permission from ref. 145. Copyright 2018, Wiley-VCH. (C) solvothermal method, (D) spin-coating technique, (E) chemical vapour deposition method. Reprinted with permission from ref. 146. Copyright 2018, Wiley-VCH. | |
The HI method is suitable for the preparation of halide RE-doped PNMs: a certain amount of preheated (100–120 °C) precursor (Cs-oleate) solution is rapidly injected into another higher temperature (150–180 °C) precursor (REX2/3, PbX2, X = Cl, Br and I) solution; after a period of reaction, the desired nanomaterials were obtained by rapid cooling and the desired nanomaterials can be obtained by washing the products with nonpolar solvents (toluene or hexane).39,105,157 In addition to injection of Cs-oleate solution, injection of halogen sources (trimethyl chlorosilane, trimethyl bromosilane, acyl chloride, etc.) is also employed in HI.158,159 In this case, metal (Pb2+,Cs+) acetates are used as metal sources. Organic halogen reagents decompose at high temperatures to form free halide ions, which combine with metal ions to form halide perovskite NCs.
Since most halide perovskite materials are ionic compounds, they have relatively poor stability in polar solvents, which easily change their morphologies and lead to degradation.158,160 In addition, the nucleation and growth processes of halide PNMs are very fast and sensitive to the reaction system such as the reaction temperature, polarity of the solvent and the ratio of the different surfactants. These factors show great influences on the size and uniformity of PNMs.159 Therefore, all the solvents used in the HI injection reaction should be anhydrous and anaerobic, and other precursor reagents used should be of high-purity. Besides, the solvents used in the post-treatment process must also be purified, for example, the solvents cyclohexane, toluene, and hexane should be purified by distillation.
The TD method is usually applied to prepare some fluoride perovskites.161,162 Metal (Zn2+, Mn2+, Na+) trifluoroacetate precursors are added to a mixed solution of OA, OM and ODE, and some small molecular impurities (O2, H2O, etc.) should be removed by heating under vacuum. The decomposition products of trifluoroacetates formed fluoride perovskite NCs at higher temperatures.163
3.1.2 Co-precipitation (CPT) method.
The co-precipitation method is another common method to fabricate PNMs (Fig. 5).147 The general process includes dissolving precursors in benign solvents, precipitation of precursor ions forming NCs by adding precipitators or changing the solubility of the reaction system. However, the morphologies of certain halide PNMs (i.e. CsPbBr(Cl)3 and Cs3Bi2Br9) are very difficult to control by using the CPT method.145,160,164 This is because a very small amount of polar solvents can promote the precursors to form bulk crystals instead of nanosized perovskites. Such nanomaterials are unstable in the dispersants in the long term, and they can easily grow larger, aggregate or even be destroyed during storage.165 Once the morphologies of NCs change, their properties decline dramatically and their performances degrade irreversibly. To suppress such a morphology change issue, surfactants can be added to stabilize NCs.164 However, additional surfactants may also hamper the properties of the materials. Yet for most oxides and fluorides, they have high stability because O2− and F− have large electronegativity, and only acidic conditions can destroy their structures.147,151,156,166
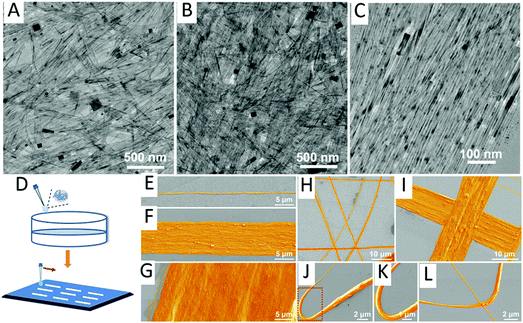 |
| Fig. 5 RE-doped KMnF3 nanowires synthesized by the CP method and TEM images of (A) KMnF3:Yb/Ho; (B) KMnF3:Yb/Tm; (C) KMnF3:Yb/Er. (D) The nanowire arrays prepared by the direct-writing method. SEM images of (E–G) the aligned, (H and I) crossed, and (J–L) curved KMnF3:Yb/Er NWs on Si substrates. Reprinted with permission from ref. 147. Copyright 2018, American Chemical Society. | |
3.1.3 Sol–gel (SG) synthesis method.
The sol–gel method is widely used to prepare oxide PNMs, and SG is rarely used for the preparation of halide perovskites. The raw materials, such as RE nitrates, transition metal (TM) nitrates, citric acid, etc., are dissolved and mixed in water, and they hydrolyse and condense to form a stable sol system, and then nanomaterials are formed after drying and sintering.167 The morphologies of nanomaterials prepared by this method lack uniformity, controllability and dispersibility (Fig. 6).167 However, this method has its unique advantages; it can be used to prepare oxide perovskites with high phase-formation temperatures.168,169 Many oxide PNMs (LaTiO3, LaFeO3, Yb/Er:La2CoMnO6, etc.) have been synthesized by the SG method, and these functional materials show excellent performances.167,170,171
 |
| Fig. 6 La1−xNaxFeO3 NPTs synthesized by the SG method. The SEM images of samples (A) LaFeO3, (B) La0.95Na0.05FeO3, (C) La0.9Na0.1FeO3 and (D) La0.85Na0.15FeO3. Reprinted with permission from ref. 167. Copyright, 2018 Author(s). | |
3.1.4 Solvothermal (ST) method.
The solvothermal method is one of the most commonly used approaches for preparing nanomaterials, and can be used to synthesize various perovskite materials, especially RE-doped Pb-based, fluoride and oxide PNMs.1,126,172 However, ST is not suitable for the synthesis of nanosized halide double perovskites.148,173 The ST method is based on the hydrothermal method, which is carried out in a closed system, such as an autoclave, with organic compounds as solvents at a certain temperature, and autogenous pressures of the reaction solution provide dynamic conditions for material generation. In order to obtain desired nanomaterials with controllable morphologies and uniform size, it is often necessary to use some surfactants in the reaction. CsPbX3 perovskite NCs were synthesized by the ST method; certain amounts of the precursor solutions (Cs-oleate in OA/ODE, PbX2 in OA/ODE/OM) were added into the autoclave, and heated to 200 °C for 50 min to form the nanomaterials.173 Eu-doped KZnF3 was synthesized by using NH4F and metal (Eu3+, Zn2+) nitrates as the raw materials, and OA and n-butyl alcohol act as the solvents. The nanoparticles (NPTs) were obtained after the reaction at 120 °C for 48 hours.174 Similarly, La-doped SrTiO3 was synthesized by using metal (La3+,Sr2+) nitrates and tetrabutyltitanate in a solution of OA and ethanol, and heating in an autoclave at 180 °C for 12 hours.175 For the post-treatment process of the ST reaction, polar or non-polar solvents (ethanol or hexane) can be used for washing oxides and fluorides, whereas chlorides and bromides must be washed with non-polar solvents (hexane or toluene).
3.2 High-temperature (HT) method
The HT method was developed and widely used to synthesize some RE-containing perovskites (oxides and fluorides) with a higher phase forming temperature, and has the merits of easy operation and mass-production processes. In addition, the materials synthesized by this method have high crystallinity, fewer defects, and high stability. Thus, some oxide perovskite materials with complex composition can be easily synthesized by the HT method. The HT method can be divided into solid state synthesis (SS) and molten salt reaction (MS). For example, La1−xSmxFeO3 perovskite was synthesized by the SS method, for which La2O3, Sm2O3 and Fe2O3 were milled and annealed in air at 1473 K for 40 hours to form micro-scale samples.176 Eu/Pr-doped CaTiO3 can be synthesized by the MS method; the raw materials were mixed and ground, then put into a muffle furnace and annealed at 820 °C for 3.5 hours, and micro-scale spheres were obtained by washing the products with distilled water and ethanol.139 These two approaches also have common shortcomings: without ligand or organic molecule protection on the surface of the particles, it is difficult to control the morphologies and size of the desired materials precisely.27
3.3 Others synthetic methods
In addition to the above-mentioned methods, there are other special synthetic processes, such as the spin coating technique (SCT),9,45 pulsed laser deposition (PLD),150,177,178 electrospinning technique (EST),179–181 and chemical vapour deposition (CVD),182 which have been widely used for the preparation of the high quality RE-containing PNMs. SCT and PLD are widely used to prepare thin film halide and oxide perovskites possessing the advantages of a few atom thickness, uniform surface, high crystallinity and fewer defects. And EST and CVD can be used to synthesise nanofiber (NFb) or nanowire (NW) oxide and halide perovskites.
3.3.1 PLD and CVD methods.
RE-containing perovskite nanofilms form an important research topic in the field of physics and materials.183,184 Thus, it is of great significance to prepare high-quality thin film materials to apply in the fields of microelectronics, magnetics and optoelectronics. PLD is also known as pulsed laser ablation, in which the active ions or atoms bombarded by laser irradiation are deposited on different substrates to obtain thin films. This method can deposit materials layer by layer on the base surface, and it is a common method for preparing thin films. This method is widely used to prepare RE-containing oxide perovskite thin films such as La0.8Sr0.2CoO3 films, YBaCo2O6 films, Sm-doped NdNiO3 films, etc.53,177,183–185 These materials show superior performances in catalysis, electronics, magnetics, photovoltaics and other fields. Moreover, h-TmFeO3 films have been successfully synthesized by the PLD method, and have large ferroelectric polarization (4.7–8.5 μC cm−2) to further inhibit the rapid recombination of the photo-induced electron–hole pairs.186 Such a material attained a better power conversion efficiency (PCE) than the typical BiFeO3. Manuel Bibes and co-workers prepared NdNiO3 films by the PLD method (Fig. 7).150 The author observed a strong resistance contrast among the metallic and the insulating regions, and a Schottky barrier formed between the sample and the tip. CVD is another effective deposition method to produce high quality and high performance based on the vacuum deposition method. Huang et al. synthesised CsPbBrxI3−x NWs by the CVD method.146 The as-prepared CsPbBrxI3−x NWs have uniform size and good crystallinity.
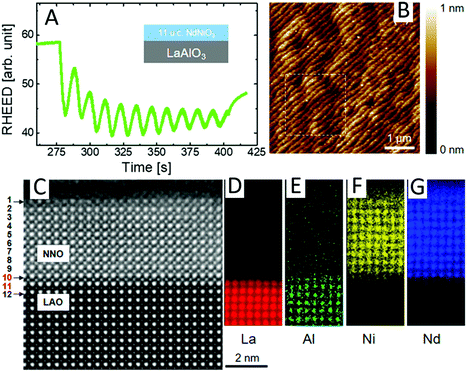 |
| Fig. 7 Growth of NdNiO3 nanofilms onto the substrates of LaAlO3 by the PLD method. (A) RHEED (reflection high-energy electron diffraction) oscillation results shown for a layer-by-layer growth process. (B) AFM (atomic force microscopy) images of the film gave a stem-and-terrace morphology. (C) HAADF-STEM (high-angle annular dark field, scanning transmission electron microscopy) images of the transverse section of NdNiO3 films and LaAlO3 substrates. (D–G) Atomic-resolution EELS (electron energy loss spectroscopy) mapping of La, Al, Ni, and Nd from the edges of the heterojunction. Reprinted with permission from ref. 150. Copyright 2018, American Chemical Society. | |
3.3.2 Spin-coating technique.
Among various methods, SCT is a relatively simple approach for preparation of RE-containing perovskite films. This method has the advantages of energy saving, low pollution, controllable thickness, massive production and high efficiencies. By adjusting the rotational speed and the viscosity of the precursor solution, the thickness of the film can be modulated easily. In order to obtain a high-quality film with uniform and smooth surface, the used salts or nanosized raw materials should be dissolved or dispersed in the colloid solution sufficiently. The last important factor for film preparation is the heating temperature and heating rate, which determine the solvent volatilization speed, and the nucleation and growth of the film on the substrate. Wang et al. prepared Eu2+/Eu3+ incorporated CsPbI3 films by SCT, and the synthesized films are highly uniform, which have good compactness and mechanical properties.9 In addition, Eu2+ was successfully introduced into the crystal structure of CsPbI2Br by SCT.45 The grains of the films were refined and uniform upon adding Eu2+, and the efficiency and the stability of the corresponding devices were improved. This method has been widely used in the preparation of solar cell films and other films.
3.3.3 Electrospinning technique.
Electrospinning technology (EST) is often used to prepare fibrous or spherical RE-containing oxide PNMs. The precursor (metal salt, polymer) solution is added to a syringe. Under a high voltage electrostatic field, the polymer carries the metal salt to form a microjet and deposits it on the substrate. The organic matter is removed by sintering and desirable nanomaterials are obtained.180 As shown in Fig. 8, La0.6Sr0.4Co0.8Mn0.2O3 NFbs were prepared by EST.181 The fibers prepared by this method have a uniform diameter and good dispersion. In recent years, this method has also been extended to prepare nanosized RE-containing oxide perovskite catalysts such as the electrode materials La0.6Sr0.4Co0.2Fe0.8O3−δ/CeO2 NFbs with a heterojunction structure, which exhibit high activity and stability in solid oxide fuel cells.179
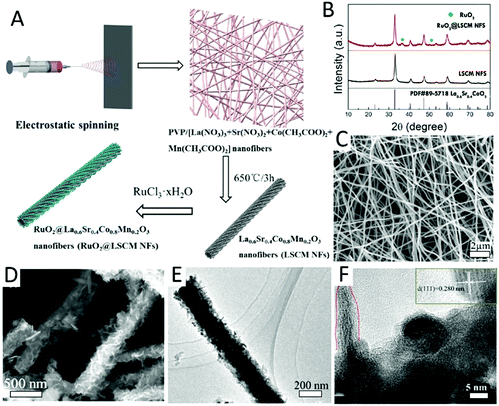 |
| Fig. 8 (A) Schematic illustration of the preparation of RuO2@ La0.6Sr0.4Co0.8Mn0.2O3 (LSCM) NFbs by the electrospinning technique. (B) The XRD patterns of LSCM and RuO2@LSCM NFbs. (C) SEM images of RuO2@LSCM NFbs. (D and E) TEM images of RuO2@LSCM NFbs. (F) HRTEM images of RuO2@LSCM NFbs. Reprinted with permission from ref. 181. Copyright 2017, American Chemistry Society. | |
4. Properties and applications
4.1 Photovoltaic properties and applications
Solar cells, as a device of directly converting abundant solar energy into electrical energy, have been regarded as one of the most promising solutions to ease the global energy crisis. Since the utilization of CH3NH3PbI3 perovskites in solar cells by Kojima in the year of 2009, the PECE of PSCs has rapidly increased to 23.7%.42,97 Such a high PECE boosts PSCs closer to practical applications, with performances similar to those of commercial single crystal silicon-based solar cells.19,73,79 The physical properties of the halide perovskites are more easily regulated by halogen, which endows the halide perovskite materials with superior photovoltaic performances over the oxide perovskites.5,97 However, the poor stability of halide perovskite materials against high temperature, humidity and oxidizing substances still severely limited their service life and industrial applications.187 Moreover, the PECE of perovskite-based solar cells is still far from their theoretical maximum value.97 To mitigate this problem, incorporating RE elements into halide perovskites has become an effective approach.46,90,188
RE elements, with various electronic configurations and sizes, have been reported as key factors in enhancing the stability, broadening the absorption range, and regulating the band gaps of perovskite materials, therefore further improving the PECE and durability of the PSCs.9,186 All these improvements are essential for the future industrialization and application of PSCs.96 There have been a significant amount of articles on RE-containing PSCs. The performances of RE-containing PSCs are summarized in Table 1, including the open-circuit voltage (Voc), short-circuit current density (Jsc), fill factor (FF), and PECE. In the following sections, current RE-containing PSCs are reviewed according to the functions of RE elements.
Table 1 RE-doped perovskite materials for solar cells
Perovskites |
RE |
Bandgap (eV) |
PECE (%) |
J
sc (mA cm−2) |
V
oc (V) |
FF (%) |
Ref. |
MAPbI3 |
Eu |
1.55 |
21.52 |
23.5 |
1.1438 |
73.2 |
9
|
CsPbI2Br |
Eu |
— |
13.71 |
14.63 |
1.22 |
76.6 |
45
|
MAPbI3 |
Eu |
— |
16.7 |
21.50 |
1.02 |
76.3 |
90
|
CsPbCl1.5Br1.5 |
Yb,Ce |
— |
21.5 |
39.8 |
0.65 |
— |
96
|
BaSnO3 |
Er/Yb |
3.64 |
4.2 |
9.69 |
0.63 |
69 |
108
|
CsPbBr3 |
La, Ce, Nd, Sm, Eu, Gd, Tb, Ho, Er, Er, Yb, and Lu |
— |
10.14 |
7.48 |
1.598 |
85.1 |
131
|
CsPbI3 |
Eu |
— |
6.8 |
11.1 |
0.898 |
68 |
188
|
MAPbI3 |
Nd |
— |
21.15 |
24.33 |
1.04 |
83.6 |
189
|
MAPbI3/TiO2 |
Sm |
1.55 |
14.10 |
18.11 |
1.032 |
68.3 |
190
|
MAPbI3 |
CeO2 |
— |
19.52 |
23.64 |
1.09 |
78.67 |
191
|
Glass-ceramic |
Sm/Ce |
— |
7.84 |
17.85 |
0.822 |
83.44 |
192
|
4.1.1 Stability enhancement.
The superior performances of Pb-based PSCs are still leading the international research hotspots. However, Pb-based perovskites suffer from easy decomposition under humid or redox environments, resulting in significant degradation of performance.134,193–195 The incorporation of RE elements can stabilize the desired phase and increase the redox, humidity, and chemical resistance of halide perovskites.9,90 Other reports also highlight that incorporating RE ions into perovskite structures can be a promising method to enhance the performance of the lead-based PSCs.45
For example, Duan et al. added RE3+ (RE = La, Ce, Nd, Sm, Eu, Gd, Tb, Ho, Er, Yb, and Lu) into CsPbBr3 films for PSCs via a multistep solution processable technique.131 The grain sizes of the films increase with the RE3+ concentration, which minimizes the grain boundaries. Meanwhile, the film becomes more and more compact with decreasing atomic number of RE3+. With RE-doping, the carrier migration time is further prolonged, and the recombination of charges and holes on the surface of perovskite film is significantly suppressed. Without metal electrodes and a hole transport layer in the solar cells, a remarkably high PECE of 10.14% is obtained, and the open-circuit voltage is also as high as 1.59 V. The batteries show high stability, with no obvious change in the PECE at 80% relative humidity for 110 days. Moreover, the cells still maintain high efficiency after working at 80 °C for 60 days. As shown in Fig. 9, the photovoltaic performances of the PSCs have been significantly improved by adding RE.131 In addition, the stability of the PSCs is also improved.
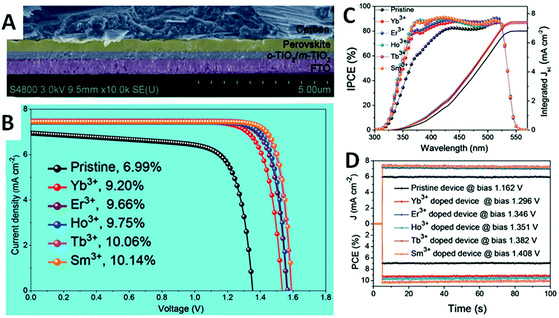 |
| Fig. 9 (A) The images of the cross section of the all-in-organic PSC. (B) The J–V curves of the PSCs with Yb3+, Er3+, Ho3+, Tb3+, Sm3+ doped CsPbBr3 perovskite absorbers. (C) The incident photon-to-current efficiency spectra of the PSCs. (D) The power output curves of the PSCs. Reprinted with permission from ref. 131. Copyright 2018, Wiley-VCH. | |
In another report, Wang et al. prepared Nd3+-doped MAPbI3 planar heterojunction films for PSCs. The Nd3+ incorporation improved the quality of the films, reduced the trap-states, inhibited the photocurrent hysteresis, prolonged the charge carrier lifetimes, and further improved the charge carrier mobilities.189 Therefore, the devices reached a high PECE of 21.15%, and the authors also demonstrated a new strategy to enhance the photoelectric performances of PSCs.
Owning to their high PECE, PSCs containing PbI2 as the starting material have been extensively studied. However, the defects of Pb0 and I0 always exist. These defects greatly reduce the PECE and shorten the service lifetime of the device. In the past few years, few efforts have been made to successfully eliminate these defects simultaneously. Wang et al. introduced Eu3+/2+ ions into the CsPbI3 perovskite, in which the Pb0 can be oxidized by Eu3+ ions and the I0 can be reduced by Eu2+ ions (Fig. 10).9 This reversible redox cycle ingeniously eliminates both Pb0 and I0 defects in the devices. As a result, the efficiency of the device is improved greatly (PECE: 21.52%, certified 20.52%), and the lifetime of the device is also prolonged. This redox shuffle strategy for eliminating defects provides a reference for stabilizing other perovskite materials.
 |
| Fig. 10 (A) Diagram of the mechanism of defect (Pb and I) elimination by Eu3+–Eu2+. (B) The PECE of (FA, MA, Cs)Pb(I,Br)3(Cl) based PSCs with different M(acac)3 (M = Eu3+, Y3+, Fe3+) incorporation. (C) The performances of Eu3+-incorporated PSCs. (D–G) are the long-term stability of the PSCs with different M(acac)3 incorporation. Reprinted with permission from ref. 9. Copyright 2019, AAAS. | |
There are two other reports on the incorporation of Eu2+ in PSCs. The doping of Eu2+ ions into the organic–inorganic MAPbI3 perovskites enhances both stability and PECE of the solar cells.90 It is also shown that EuI2 can stabilize the metastable phase of CsPbI2Br (Fig. 11).45 The corresponding devices exhibit a stable PECE of 13.34%. The electroluminescence test shows that the introduction of Eu2+ reduces the non-radiative recombination, and enlarges the Voc to 1.27 V. In addition, the initial efficiency of the device can remain at 93% for 370 hours under 100 mW cm−2 light illumination.
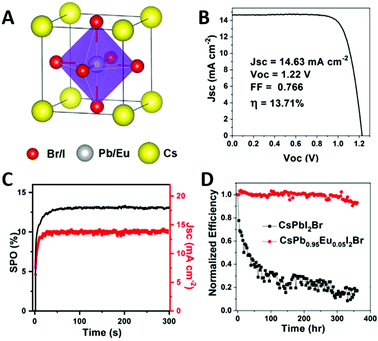 |
| Fig. 11 (A) The crystal structure of Eu2+ doped CsPbI2Br. (B) J–V curve of a CsPb0.95Eu0.05I2Br based device. (C) The stable power output of the device at maximum-power point tracking (100 mW cm−2 irradiation). (D) Normalized PECE of Eu-doped and undoped CsPbI2Br devices as a function of working time (under continuous white light irradiation). Reprinted with permission from ref. 45. Copyright 2018. Elsevier Inc. | |
4.1.2 Absorption range expansion.
The natural sunlight covers a broad frequency range from the UV to the infrared region. Oxide perovskites have high stability, but their photoelectric conversion efficiency is very low due to their weak sunlight absorption ability, which greatly limits the utilization efficiency of solar energy. The unique electronic structure of RE ions opens opportunities to extend the absorption range to infrared light for perovskites. As a result, RE-doped PSCs are capable of absorbing light covering the UV to infrared regions, which further improves the PECE.196
It is reported that when the Yb3+/Ce3+ co-doped perovskite is used as the photoabsorption layer, the efficiency of the devices is enhanced from 18.1% to 21.5%.96 In addition, LaGaO3:Cr3+/RE3+ (RE = Yb, Nd, Er) co-doped perovskites can absorb the NIR light and then transfer the energy to C-Si-based solar cells.197 The energy transfer processes between RE ions and devices were studied, and the energy transfer efficiency was as high as 77%, effectively improving the PECE of the solar cells.
4.1.3 Bandgap modulation.
PSCs consist of electrodes, a perovskite layer, hole and electron transport layers. Under illumination, the holes and carriers are effectively separated and transferred from perovskites to electrodes. Such a transfer requires the appropriate energy match between perovskites and transport layers. As a result, the large bandgap limits the fast and efficient transportation of charge carriers, and then directly affects the efficiency of PSCs. By the introduction of RE elements, the band gaps and electronic structures can be modulated for boosting the photocurrent or carrier migration rate and the PECE.
The substitution of about 10% of Ba2+ lattice sites by Yb3+/Er3+ reduces the bandgap of BaSnO3 NCs from 3.68 eV to 3.64 eV and increases the electrical conductivity.108 Moreover, the Yb3+/Er3+-doped BaSnO3 utilizes more energy from the solar spectrum, yielding a PECE of 4.2%. Compared with the undoped BaSnO3 NCs (PECE, 3%), the PECE is increased by 40%. As shown in Fig. 12, with different Yb3+ and Er3+ substitution levels, both absorption and emission spectra shift, implying a successful modulation of the bandgap, thus leading to improved Jsc and Voc.108
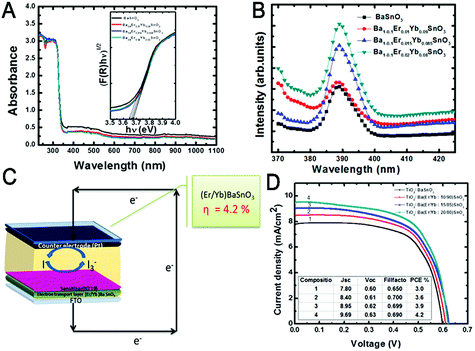 |
| Fig. 12 (A) UV-vis absorption and (B) photo-luminescence spectra of BaSnO3 and Er3+/Yb3+:BaSnO3 NCs. (C) The schematic diagram of a solar cell. (D) The J–V curves of BaSnO3 and Er3+/Yb3+:BaSnO3 NCs. Reprinted with permission from ref. 108. Copyright 2018, Elsevier Ltd. | |
ZnO/CeOx is an electron transport material (ETM) in PSCs (Fig. 13).191 The incorporation of CeOx regulates the unmatched energy levels and protects perovskite materials against UV light, high temperature and humidity. As a result, the PECE of PSCs increases from 16% (ZnO) to 19.5% (ZnO + 3% CeOx), and the service lifetime of the cell is also prolonged. All reports reviewed in this section show that RE elements play an important role in enhancing the photovoltaic performance due to the flexible modulation in different aspects, which are also a crucial contribution to the photovoltaic industry.
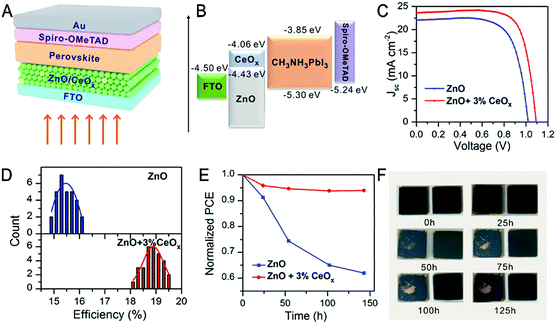 |
| Fig. 13 (A) Schematic images of the cell structure. (B) The energy band diagram of the PSCs. (C) Best J–V curves of ZnO and CeOx/ZnO based PSCs. (D) The PECEs of 30 cells with and without CeOx addition. (E) The stability of the cells at 85 °C (in an inert atmosphere). (F) The photos of CeO2 doped (right) and undoped (left) perovskite film treatment with the same conditions in (E). Reprinted with permission from ref. 191. Copyright 2019, American Chemical Society. | |
4.2 Dielectric properties and applications
Oxide perovskites are very good dielectric materials. Due to their high dielectric constant (εr), processability and stability, they are widely used in electric vehicles,198 pulse weapon systems, energy storage,199 power electronics, etc.200 Owing to the unique electronic structures and intrinsic elemental characteristics of RE elements, doping RE into perovskite structures may significantly improve their dielectric performance.201 In the future, novel perovskites will possess great potential in applications such as mobile communication, radio, television, and microwave technology, which requires new dielectric materials with low loss. This section summarizes the recent progress of RE-containing PNMs as piezoelectric, pyroelectric, and ferroelectric materials.127
4.2.1 Piezoelectric materials.
Recent studies have illustrated that RE doping improves the dielectric properties of PNMs,202 providing a promising approach to access new piezoelectric materials. RE-doping can enhance the heterogeneity of perovskite structures. The increase in atomic diffusion rate promotes the densification of perovskite ceramics, reduces the sintering temperature, and simultaneously enables the application of a higher polarization electric field.
Chen et al. demonstrated that NPTs have more advantages than microparticles in improving electrical performance.203 The CeO2 NPTs are well dispersed, with an average diameter of 20 nm. BCTS (Ba0.96Ca0.04Ti0.90Sn0.10O3)-nano CeO2 (0.03 mol%) has better piezoelectric performance than other ceramics, and the dense microstructure of BCTS ceramics with the inclusion of nano CeO2. The nano CeO2 contributes to the improvement of piezoelectric properties because of the morphotropic phase boundary (MPB) effect, which makes the domain a greater space in the rotational motion. Moreover, the improvement of dielectric properties of the ceramics is ascribed to the weakening of strain potential energy. Therefore, the inclusion of nano CeO2 elevates the piezoelectric properties of BCTS ceramics.
In addition, Chen and his co-workers further demonstrated that the piezoelectric properties of BCTS-Y (Ba0.90Ca0.10Ti0.9Sn0.1O3–xY2O3) ceramics could be improved by incorporating Y2O3.204 TEM and SEM images show that BCTS-Y ceramics have a uniform and well-distributed microstructure, with the maximum value of d33 (596 pC N−1) and Kp (0.571) obtained when 1% of nano-Y2O3 is incorporated, and this material has higher d33 and Kp than the micro-Y2O3 incorporated samples reported in the literature.205 Hence, the incorporation of nanoscale RE-containing compounds is more effective than the incorporation of micron-level RE-containing compounds for the piezoelectricity of perovskite materials.
Lead zirconate titanate [Pb(ZrxTi1−x)O3, PZT], a representative material simultaneously possessing outstanding dielectric, piezoelectric, pyroelectric, and ferroelectric properties, has already been used in high-performance electronic devices.40 However, Pb-containing materials are harmful to the environment and our health. Currently, some lead-free perovskites are being extensively investigated for environmentally friendly piezoelectric systems.133,206,207 Based on this, developing high performance, low cost and lead-free piezoelectric RE-containing perovskites is of critical significance. In particular, these materials with remarkable performances have potential applications in the fields of industrial ultrasonic testing, transducers, medical imaging and other fields.208,209
4.2.2 Ferroelectric materials.
With the development of nanotechnology, some RE-containing perovskites are widely investigated as ferroelectric materials for sensors and other devices due to their outstanding dielectric and ferroelectric properties.210 Incorporating RE elements into the lattice structure of perovskites decreases the crystal size and distortion of lattice, which optimizes the ferroelectric performance of the materials.
Liu et al. demonstrated that when La3+ or Nd3+ ions are doped in the PZT lattice, they act as donors, effectively reducing the movement of defective charges including free electrons and oxygen vacancies. Meanwhile, the appearance of a morphotropic phase boundary (MPB) greatly improves the holistic electrical properties of films. The substitution of RE-elements at the A-site also eliminates oxygen vacancies.40 In addition, Guo and his co-workers studied Nd3+-doped PZT films prepared by different deposition sequences and revealed that the BNF/PZT bilayer had better electrical properties than the corresponding PZT/BNF film.211 Moreover, the P–E (polarization-electric field) curve and the DC leakage characteristics of pure PZT film implies that BNF/PZT bilayer composite films possess better ferroelectricity than BNF/PZT. A new idea for the design of multi-layer structures is therefore provided in terms of enhancing the ferroelectricity of RE-containing PNMs. Other examples of the dielectric properties of RE-containing PNMs are shown in Table 2.
Table 2 Electrical performances of RE-containing perovskite nanomaterials
Perovskites |
RE3+ |
Methods |
Morphology |
Performances |
Application |
Ref. |
PbZr0.52Ti0.48O3 |
La/Nd |
SG |
NFs |
RT, 100 Hz, εr = 1053.36; tan δ = 0.13; LC = 8.3 × 10−9 A cm−2; d33 = 36.4 pC N−1; Pr = 64.32 μC cm−2; Ec = 57.40 kV cm−1 |
— |
40
|
Ba0.96Ca0.04Ti0.90Sn0.10O3 |
Ce |
HT |
NPTs |
RT, 1 kHz, εr = 32945.8; d33 = 512 pC N−1; kp = 0.415; Pr = 14 μC cm−2; γ= 1.44 |
— |
203
|
PbZrO3 |
Dy |
ME |
NCs |
RT, 1 GHz, εr = 16.02; tan δ = 0.275 |
High frequency memory devices |
41
|
Ba0.9Ca0.1Ti0.9Sn0.1O3 |
Y |
HT |
NPTs |
d
33 = 596 pC N−1; kp = 0.571 |
— |
204
|
La–Pb(Ni1/3Sb2/3)–PbZrTiO3 |
La |
CP |
NCs |
d
33 = 449 pC N−1; Tc = 286 °C |
Power harvesting |
218
|
Pb0.92La0.08Zr0.6Ti0.4O3 |
La |
MBM |
NPDs |
RT, 1 kHz, εr = 2293; tan δ = 1.98; Pr = 30.7 μC cm−2; Ec = 9.4 kV cm−1; Tc = 190 °C; γ = 1.98 |
Sensors, actuators, transducers |
219
|
La1−xDyxFe1−yMnyO3 |
La, Dy |
ME |
NPTs |
RT, 6 kHz, εr = 1340 |
Recording media |
220
|
BaTiO3 |
Y |
SG |
NPTs |
RT, 10 kHz, εr = 2069; tan δ = 0.05; Tc = 125 °C; γ = 1.0 |
— |
153
|
SrTiO3 |
La, Ce, Nd, Sm, Gd, Tb, Y |
ST |
NCbs |
RT, 100 Hz, εr = 1800; d33 = 380 pm V−1; kp = 0.45 |
— |
217
|
La1−xNaxFe1−yMnyO3 |
La |
PR |
NCs |
RT, 1 kHz, εr = 1256; tan δ = 1.01 |
Capacitors, resonators and memories |
210
|
Bi1−xNdxFe1−yCoyO3 |
Nd |
SG |
NPTs |
RT, 100 Hz, εr = 1050; Pr = 26 μC cm−2; Ec = 5.6 kV cm−1 |
Intelligent devices |
221
|
YCrO3 |
Y |
PR |
NCs |
T
c = 137 °C |
— |
222
|
BiFeO3 |
La/Nd |
SG |
NFs |
RT, 100 Hz, εr = 195; tan δ = 0.191; Pr = 61.21 μC cm−2; Ec = 44.86 kV cm−1 |
Device design |
143
|
Bi0.9Nd0.1FeO3 PbZr0.52Ti0.48O3 |
Nd |
SG |
NFs |
LC = 4 × 10−8 A cm−2; Pr = 11.39 μC cm−2; Ec = 87.16 kV cm−1 |
Device design |
211
|
La1−xSrxCo1−yFeyO3 |
La |
ME |
NCs |
RT, 15 MHz, εr = 103.35; tan δ = 0.57 |
Microwave devices |
223
|
CoFeO3 |
Nd |
SG |
NCs |
RT, 100 Hz, εr = 31.08; tan δ = 0.16 |
Microwave devices |
224
|
LaxSr1−xCoO3 |
La |
SG |
NPTs |
RT, 100 Hz, εr = 16 |
Sensing, memories |
225
|
LaFeO3 |
Eu |
ME |
NPTs |
RT, 30 MHz, εr = 14.18; tan δ = 0.52 |
Frequency devices |
202
|
MnFeO3 |
Gd |
SG |
NCs |
RT, 100 Hz, εr = 5.53; tan δ = 0.129 |
Microwave devices |
226
|
PbZr1−xTixO3 |
La |
SC |
NFs |
P
r = 10.14 μC cm−2; Ec = 42 kV cm−1 |
— |
227
|
CrFeO3 |
Gd, Er |
CCB |
NPTs |
P
r = 1.94 μC cm−2; Ec = 214.8 kV cm−1 |
Data storage and camera flash |
228
|
La0.05Li0.85NbO3 |
La |
HT |
NCs |
P
r = 0.15 μC cm−2; Ec = 1.31 kV cm−1 |
— |
229
|
4.2.3 Pyroelectric materials.
RE-containing PNMs are capable of exhibiting outstanding pyroelectric properties. When pyroelectric effects are present, electricity is generated under thermal stimulation, which provides an important way for energy conversion, and is also useful for temperature sensing. The pyroelectric effect is associated with the electrically charged species of the crystal structure along the direction of charge polarization displacement.211 This is usually caused by the asymmetric positive and negative charge centres, which constitute the ferroelectric dipoles and show the pyroelectric effect.212
A good thermoelectric material should have a large Seebeck coefficient, good conductivity and a low thermal conductivity coefficient.213 Kaya et al. prepared perovskite based LaNiO3–La2CuO4 layered heterojunction materials on substrates of LaSrAlO4 by the atomic layer-by-layer oxide molecular beam epitaxy technique (Fig. 14).214 The electrical conductivity decreases while the Seebeck coefficient increases with the reduced thickness of the heterojunction layers. HAADF-STEM shows that La2(CuCo)O4 solid solution is formed at the heterojunction as the thickness of the layer decreases.
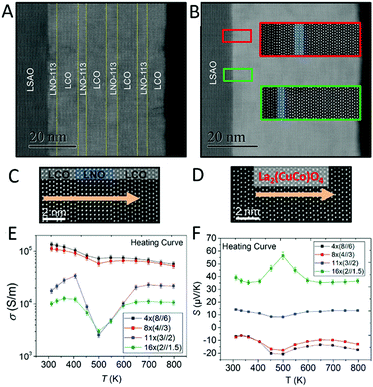 |
| Fig. 14 HAADF images of k × (n//m) heterojunctions, where k is the layer number of LaNiO3–La2CuO4 heterojunctions, n is the number of LaNiO3 unit cell, and m is the number of La2CuO4 unit cells. (A and C) 4 × (8//6) and (B and D) 16 × (2//1.5). (E and F) Temperature-dependent curves of the conductivity and Seebeck coefficient of the heterojunction layers. Reprinted with permission from ref. 214. Copyright 2018, American Chemical Society. | |
The thermopower and barrier potential of the material increase with a small amount of La3+ doping into SrTiO3 perovskites with a particle size of 20 nanometers. The results show that RE doping can modify the grain boundary and further adjust the thermoelectric properties of materials.215 The elements of Gd and W were introduced into CaMnO3 to form double substituted Ca1−xGdxMn1−xWxO3−δ. The thermoelectric properties were tested from 25 °C to 700 °C. With the amount of incorporated Gd and W increasing, the electrical conductivity of the sample improved and the thermopower reduced. When x = 0.01, the material exhibited a thermoelectric figure of merit of 0.12 at 700 °C.216 In addition, Kinemuchi Y. et al. also demonstrated that doping of RE can improve the Seebeck coefficient of Y-doped SrTiO3, and promote their pyroelectric performances.217
4.3 Luminescent properties and applications
Luminescent PNMs have various applications such as in illumination sources and anti-counterfeiting labels.132 Currently, the applications of halide perovskites are still constrained by the low stabilization energy and weak ionic bonding ability. The oxide perovskites are relative stable, but they also have some shortcomings of low luminescent efficiency and nonadjustable emission spectra. RE ions have abundant 4f levels and variable ionic valences, which show excellent optical properties and environmental stability when doped into perovskite matrix materials, and RE can also stabilize the halide perovskites.230 In addition, the spectral range of perovskites have been greatly broadened by incorporating RE elements.80,91,231–234 In what follows, we choose several representative optical mechanisms and optical applications for detailed comparison and introduction.11,35,235,236
4.3.1 Luminescent materials.
The incorporation of RE elements into perovskites greatly promoted the luminescence performances of the functional materials.237–240 Song et al. systematically studied the optical properties of Ln3+-doped CsPbCl3 NCs (Ln = Yb, Er, Dy, Tb, Eu, Sm, Ce) (Fig. 15).39 The absorption spectra of the Ln3+-doped CsPbCl3 NCs exhibit a blue shift with an increase in the atomic number of the doped Ln3+ ions, which is due to the lattice shrinkage caused by the radius of lanthanide ions shrink. Compared with the undoped CsPbCl3 NCs, Ln3+-doped samples emit characteristic peaks of each Ln3+ ions. Yb3+-doped samples exhibit a high PLQY of 143% due to the quantum tailoring effect.35,235,241 The electrons in the conduction band and the holes in the valence band reach the intermediate defect states, and then the energy is transferred to Yb3+ ions. The PLQY of Eu3+ is low for the electrons in the excited state that are transferred to the non-radiative emission level.
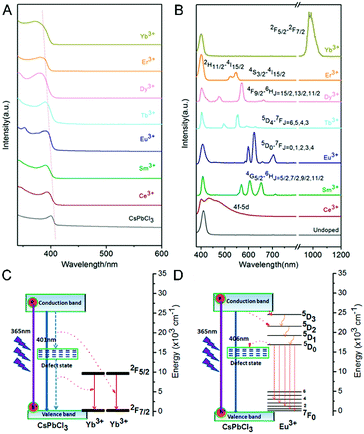 |
| Fig. 15 (A) Absorption spectra and (B) emission spectra of Ln3+-doped CsPbCl3 NCs. The energy level diagrams and possible luminescence mechanism of Ln3+-doped CsPbCsCl3 NCs: (C) doped with Yb3+; (D) doped with Eu3+. Reprinted with permission from ref. 39. Copyright 2017, American Chemical Society. | |
Zheng et al. synthesized LiYbF4:0.5%Tm@LiYF4 sensitized CsPbX3 (X = Cl, Br, I) (Fig. 16).242 Under low energy NIR (980 nm) excitation, the RE sensitizer ion (Yb3+) absorbs and transfers the energy to the luminescent centre ion (Tm3+) and emits high energy blue-violet light completing the up-conversion photoluminescence (UC PL) process.103 The energy from UC PL of RE ions can be used to stimulate the CsPbX3 quantum dots (QDs) to emit luminescence. By adjusting halide cations, perovskite QDs can be emitted from the perovskite structure sensitized by RE nanomaterials under NIR laser irradiation. This study realizes the radiative energy transfer up-conversion (RETU) system. In order to raise the NIR emission, Zhang et al. delineated Yb3+ and Yb3+/Er3+ doped CsPbCl3 NCs with the total PLQY increased from 5% to 127.8%.230 Meanwhile, the doped CsPbCl3 NCs are more stable than the undoped ones. Furthermore, Zhou and co-workers successfully synthesized Yb3+/Ce3+-doped CsPbCl1.5Br1.5 NCs by the modified HI method; the NCs exhibited a strong infrared emission peak at 980 nm with a high PL QY of 146%.96 This high PL QY belongs to the quantum cutting effect, which has been widely studied.243,244 The optical performances of some RE-doped PNMs are listed in Table 3.
 |
| Fig. 16 (A) The emission of LiYbF4:0.5% Tm@LiYF4 core/shell NPs and the NP-sensitized CsPbX3 QDs (X = Cl, Br, I) under laser excitation (980 nm). (B) The photographs of the samples (from CsPbCl3, CsPbBr3 to CsPbI3) under 980 nm illumination; adjustable colors from blue to red. (C) Upconversion tuning in CsPbX3 QDs sensitized by LiYbF4:0.5%Tm@LiYF4 nanoparticles. Reprinted with permission from ref. 242. Copyright 2018, Springer Nature. | |
Table 3 Summary of the perovskite-type, decay curves and applications of some representative RE-doped PNMs
Perovskites |
RE/emission |
PLQY % |
Decay curve |
Application |
Ref. |
CsPbBr3 |
Ce3+/515 nm |
89 |
12.69 ns |
— |
11
|
CsPbCl3 |
Ce3+/430 nm |
24.3 |
9.7 × 10−3 μs |
— |
39
|
|
Sm3+/605 nm |
14.1 |
600 μs |
|
|
|
Eu3+/620 nm |
27.2 |
714 μs |
|
|
|
Tb3+/550 nm |
31.2 |
598 μs |
|
|
|
Dy3+/572 nm |
27.6 |
583 μs |
|
|
|
Er3+/548 nm |
15.1 |
654 μs |
|
|
|
Yb3+/982 nm |
142.7 |
588 μs |
|
|
CsPbxM1−xBr3 |
Mn2+/Eu2+/492–520 nm |
75 |
5.04 ns |
— |
68
|
Cs2AgInCl6 |
Yb3+/994 nm |
100 |
2.7 ms |
— |
80
|
CsPbX3 (X = Cl, Br, I) |
Ce3+/Eu3+/398–620 nm |
50 |
— |
LEDs |
105
|
|
Ce3+/Sm3+/399–604 nm |
38 |
|
|
|
|
Bi3+/Eu3+/403–620 nm |
40 |
|
|
|
|
Bi3+/Sm3+/401–604 nm |
26 |
|
|
|
|
Ce3+/Mn3+/450–592 nm |
72 |
4.9 ns |
|
|
CsPbBr3 |
Eu3+/545 nm |
— |
0.82 ms |
— |
145
|
|
Tb3+/612 nm |
|
0.37 ms |
|
|
CsPbCl3 |
Yb3+/Er3+/986 nm |
127.8 |
941.9 μs |
— |
230
|
|
Yb3+/Er3+/1533 nm |
— |
868.2 μs |
|
|
K3InF6 |
Eu3+/615 nm |
— |
0.64 ms |
— |
148
|
Tb3+/615 nm |
0.45 ms |
Er3+/548 nm |
0.59 ms |
Er3+/656 nm |
0.57 ms |
LiNbO3 |
Er3+/543 nm |
— |
— |
Anticounterfeiting/toxicity tests |
247
|
CsYbI3 |
675 nm |
58 |
23.3 ns |
Photodetectors |
141
|
CsPbCl3 |
Yb3+/990 nm |
190 |
280 ps |
— |
250
|
KxCs1−xPbCl3 |
Y3+/410 nm |
17.6 |
12.41 ns |
— |
251
|
|
La3+/410 nm |
15.8 |
9.29 ns |
|
|
|
Eu3+/410, 438, 455, 473, 495 nm |
31.2, 38.8, 50.5, 80.8, 89.9 |
10.55 ns |
|
|
|
Lu3+/410 nm |
8.7 |
14.17 ns |
|
|
RbPbI3 |
Yb3+/Er3+/763.50 nm |
— |
4.9 ns |
Resonators |
252
|
CsSrI3 |
Yb2+/426–442 nm |
— |
10 μs |
— |
253
|
KMnF3 |
Yb3+/Er3+/660 nm |
— |
589 μs |
Biolabeling |
254
|
KMgF3 |
Eu2+/3+/360–590 nm |
30 |
3.2 ms |
RL dosimeters |
255
|
KMnF3 |
Nd/Yb/Er/668 nm |
0.023 |
100 μs |
— |
256
|
CaTiO3 |
Eu3+/619 nm |
— |
0.8 ms |
Lighting devices |
257
|
BaLaMgSbO6 |
Mn4+/700 nm |
83 |
0.90 ms |
LED |
258
|
4.3.2 Anti-counterfeiting labels.
Some RE-containing PNM composites have unique UC/downconversion (DC) PL properties and good thermal stability, such as La3+:CsPb(Cl0.7F0.3)3, RE3+:LiNbO3 (RE = Pr, Tm, Er, Yb), and 2% Yb3+(5% Mn2+, 0.01% Er3+ or Ho3+):KCdF3.245–247 These materials can only emit luminescence under UV and NIR excitation, and they cannot emit luminescence under natural light or dark conditions. This external excitation luminescence of the materials can be used for preparation of multilevel anti-counterfeiting materials. As shown in Fig. 17A, Chinese characters and image patterns were fabricated via nanoprinting on paper where the patterns printed by CsPb(Cl0.7F0.3)3:La3+ QDs would appear under 365 nm UV light.248 Moreover, Tm3+, Er3+, or Pr3+-doped LiNbO3 presents a luminescent rainbow (Fig. 17B), which meets the maximum anti-counterfeiting requirements at present.247Fig. 17C shows a printed luminescent red flower and green leaves by the inks of 2% Yb3+/5% Mn2+/0.01% Er3+-doped KCdF3 and 0.01% Ho3+-doped KCdF3, respectively.249 The intense luminescence together with multiple nanoprinting patterns shows great potential for this anti-counterfeiting technology.
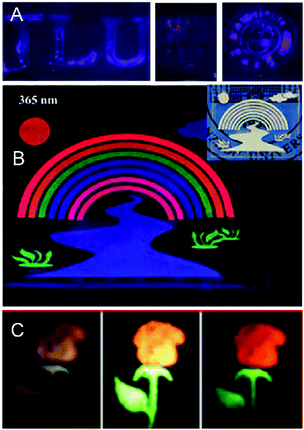 |
| Fig. 17 (A) The patterns printed by CsPb (Cl0.7F0.3)3:La3+ QD inks on paper under 365 nm UV irradiation. Reprinted with permission from ref. 248. Copyright 2019, Royal Society of Chemistry. (B) Fabrication of RE3+-doped LiNbO3 (RE = Pr, Tm, Er, Yb) luminescent rainbow river logos printed on a PDMS substrate. Reprinted with permission from ref. 247. Copyright 2019, American Chemical Society. (C) The plantlet (flowers and leaves) images printed by the inks of KCdF3:2%Yb3+,5%Mn2+,0.01%Er3+ and KCdF3:2%Yb3+,5%Mn2+,0.01%Ho3+, respectively. Reprinted with permission from ref. 249. Copyright 2019, Royal Society of Chemistry. | |
4.3.3 Lighting and display screens.
As a class of luminescent materials, perovskites have pure luminescent chroma and an adjustable spectral range, which is highly desirable in the field of the high resolution display screens.236 However, most luminescent halide perovskites emit weak blue and red spectra, which limit their practical applications as display screen materials.4,43 Owing to the RE ions that can emit narrow and sharp blue and red spectra, the RE-doped perovskites complement each other and promote the application of perovskite materials in the field of displays and LEDs.12,259
Yao et al. used Ce3+ doped CsPbBr3 NCs to encapsulate LED devices (Fig. 18).11 The devices with and without Ce3+ were evaluated with and without Ce3+ systematically. Both the CsPbBr3 and Ce3+-doped CsPbBr3 samples and the corresponding devices emit narrow and strong emission peaks. With Ce3+ doping, the brightness is enhanced with the increase of device voltage. The current density and current efficiency of the devices with Ce3+ addition are greatly improved. The external quantum efficiency (EQE) of the Ce3+ doped devices is higher than that of the Ce3+ undoped devices with different voltages, which give the highest EQE of 4.4%.
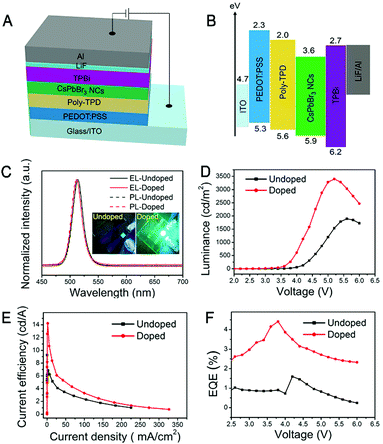 |
| Fig. 18 (A) The structure diagram of the LEDs. (B) The band distribution in each functional layer of the device. (C) PL and EL spectra of the CsPbBr3 and Ce3+ doped CsPbBr3 samples and corresponding devices. (D) The luminance changes with the driving voltage of the devices. (E) Relationship between current efficiency and current density of these devices. (F) The relationship between the driving voltage and the EQE of these devices. Reprinted with permission from ref. 11. Copyright 2018, American Chemical Society. | |
4.4 Detection and sensing
The optical, magnetic and electrical properties of RE-containing perovskites can be sensitive to various external stimuli including metal ions, gases, temperature, electromagnetic waves, etc.132,136,217,260,261 Under the stimulation of different external objects, the luminescent and electrical performances of the perovskites will be changed, and the composition and amount of analytes can be identified and determined. These specific perovskite materials can, therefore, be used to fabricate sensors, selectively detecting certain external stimulus.137,262,263 This section summarizes the applications of RE-containing PNMs as sensors (Table 4).
Table 4 Various sensors based on RE-containing PNMs
PNMs |
RE |
Morphology |
Stimulus |
Sensing performances |
Ref. |
YMnO3 |
Y |
NPTs, 50–100 nm |
NO2 |
180 °C, 30%@10 ppm, 1 min |
14
|
GdFeO3 |
Gd |
NPTs, 10–35 nm |
NO |
140 °C, 2 ppm, 1–2 min |
112
|
Yb/Er, Er:NaYF4, MeNH3PbBr3 |
Yb/Er, Er |
NWs, ∼150 nm |
NIR, 980 nm; 1532 nm |
980 nm, 2.5–17.5 W cm−2; 1532 nm, 5–30 W cm−2 |
132
|
Au/Cl, LaFeO3 |
La |
NPTs, 29 nm |
Ethanol gas |
100 ppm, Tp = 120 °C |
137
|
CsPbBr3 |
— |
QDs, ∼12 nm |
Yb3+, Cu2+ |
2 nM–2 μM |
136
|
NaMgF3 |
Eu2+, Ce |
— |
X-ray |
12 Gy |
140
|
Y0.2Sr0.8TiO3 |
Y |
NCbs, 20 nm |
Temperature |
S
bk, ∼890 μV K−1, 500 °C |
217
|
PrFeO3 |
Pr |
NPDs, 10–100 nm |
CO2 |
2.36 ppm; Tp, 200 °C; 72% RH |
264
|
EuPO4, CsPbBr3 |
Eu |
NCs, 50–300 nm |
Temperature |
303–483 K, Sa = 0.082 K−1, Sr = 1.80% K−1; 1 min |
265
|
DyFeO3 |
Dy |
NPTs, 26 nm |
H2S |
340 °C, 5 × 10−5 volume% |
266
|
DyCoO3 |
Dy |
NPTs 0.2–8 μm |
UV |
E
e = 100 mW cm−2, 2 min ∼0.5 s; ΔI, 0.027–0.1 mA |
263
|
4.4.1 Ions and gas sensing.
The detection of toxic ions and gases is pivotal for human health. Luminescent and electrochemical detection methods of toxic ions and gases are quite successful approaches due to their advantages of high sensitivity, convenience, fast response and low cost. In recent years, PNMs also show great potential in this emerging area.
One example is the selective detection of Cu2+ ions using CsPbBr3 NCs.136 As shown in Fig. 19, the addition of different metal ions induces very different responses of the PL intensities. Cu2+ effectively quenches the luminescence of CsPbBr3, whereas the response is negligible for other ions with a detection limit as low as nM. These results demonstrated the great potential of PNMs in detecting metal ions.
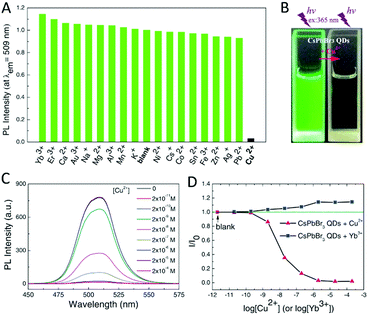 |
| Fig. 19 (A) The PL intensity of CsPbBr3 QDs (∼1.0 × 10−9 M) with addition of different metal ions (2.0 × 10−6 M). (B) The images of CsPbBr3 QDs in cyclohexane without and with Cu2+ under UV light. (C) The PL spectra of CsPbBr3 QDs with addition of different amounts Cu2+. (D) The PL intensity of CsPbBr3 QDs changing with addition of Cu2+ and Yb3+. Reprinted with permission from ref. 136. Copyright 2017, Wiley-VCH. | |
In other reports, PNMs are used to detect volatile organic compounds (VOCs) and toxic gases. PrFeO3 NPDs can be used to detect CO2 at a low concentration of 2.36 ppm, under a relative humidity of 72% at 200 °C.264 Moreover, YMnO3, GdFeO3 and DyFeO3 nanomaterials were applied to detect NO2, NO and H2S, respectively.14,112,266 LaFeO3 NPTs, surface modified by Au and Cl, have been used to detect ethanol (Fig. 20).137 The Au atom and Cl atom on the surface of the LaFeO3 NPTs inhibited the pollution of foreign carbon atoms. The oxidation of ethanol molecules on the surface of the NPTs afforded La carbonate and adsorbed the oxygen species. The calculation results showed that the Au and Cl atoms enhanced the charge transformation from ethanol to Fe–O and terminated on the surface of the LaFeO3(001) face, which were both beneficial for the response of LaFeO3 to ethanol. Thus, the detection limit reaches as low as 100 ppm at 120 °C. This method is also suitable for the detection of other gases, providing a new idea for VOC sensing.264
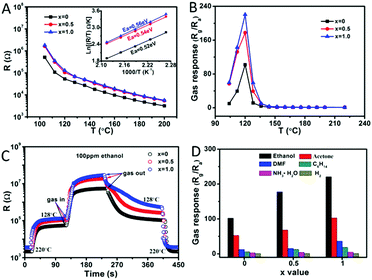 |
| Fig. 20 (A) The resistance of LaFeO3–x% HAuCl4 (x = 0, 0.5, 1.0) in air (104 A). The resistance of LaFeO3–x% HAuCl4 (x = 0, 0.5, 1.0) in air (104–200 °C); inset: the curves of ln R/T vs. 1000/T (168–200 °C). (B) Temperature dependence of ethanol (100 ppm) gas response. (C) The response curves of resistance to ethanol (120 °C, 100 ppm). (D) The response performances of different gases (120 °C, 100 ppm). Reprinted with permission from ref. 137. Copyright 2019, American Chemical Society. | |
4.4.2 Detection of heat and electromagnetic waves.
It is well-known that the optical properties of luminescent materials can be sensitive to temperature. As shown in Fig. 21(A) and (B), the emission of an EuPO4@CsPbBr3 hybrid system changed at different temperatures.265 The emission intensity of CsPbBr3 at 516 nm decreased with increasing temperature. However, the characteristic emission of Eu3+ at 593 nm, 611 nm and 700 nm showed negligible changes. The spectral change of the hybrid system as a function of temperature can be clearly read out on the chromaticity map. When the temperature increases from 303 K to 483 K, the colour of EuPO4@CsPbBr3 gradually changes from yellow-green to orange-red. Therefore, this composite structure is very suitable for thermal sensing.
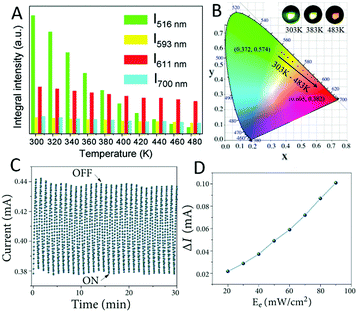 |
| Fig. 21 (A) Temperature (303–483 K) dependent PL emission intensities of CsPbBr3 and Eu3+ at different peaks (λex = 393 nm). (B) The CIE (x,y) diagram of the emission colour with different temperatures; inset: photos of the samples at different temperatures. Reprinted with permission from ref. 265. Copyright 2018, Royal Society of Chemistry. (C) The electrical current of DyCoO3 pellets under on/off cycles (30 s) of UV irradiation. (D) Quantitative current response of DyCoO3 to UV light (with different Ee values). Reprinted with permission from ref. 263. Open Access. | |
In addition, the electromagnetic waves (X-rays, UV rays, etc.) can also change some electrochemical properties of the materials. Based on such effects, a series of materials have been developed to detect electromagnetic waves.138,255,267 For example, DyCoO3 was used for UV detection (Fig. 21C and D).263 The photocurrent can clearly respond to repeated turning off–on of the UV lamp, and it is stable under repeated cyclic tests. The photocurrent shows a good linear relationship with the UV power, facilitating applications as UV sensors.
4.5 Catalysts
Oxide perovskite materials have high stability, adjustable A-site defects, oxygen vacancies and other abundant active sites.89,268 The incorporation of RE elements and reduction of the size of materials can endow RE-containing oxide PNMs with better catalytic activity not observed in other compounds.3,184,269 Halide perovskite materials have low stability (against high temperature, water, oxygen, etc.) and they are rarely used in the catalyst field.5,19,117 To date, various RE-containing PNMs have been reported as efficient catalysts for water splitting (OER, Oxygen evolution reaction, HER, Hydrogen evolution reaction), CO and CH4 transformation, NOx degradation, etc.19,54,270
4.5.1 Water splitting.
Hydrogen is a clean, and recyclable high-energy source, which attracts tremendous attention. Searching for highly efficient and stable catalysts for water splitting is essential to utilize the abundant water resources. The HER and OER are two half-reactions of water decomposition and are used to evaluate the performances of electrocatalysts.135,271 RE-containing oxide perovskite materials have been considered as promising electrocatalysts for water splitting due to their high OER activity.272 Therefore, they are also good candidates for photocatalytic water splitting.
4.5.1.1 Electrocatalysis.
There is lots of work on RE-containing oxide perovskites as electrocatalysts for water splitting, and some of them show excellent catalytic performances, which are comparable to that of noble metal catalysts. For these materials, the categories of materials,273,274 chemical compositions,18,53,116,135,275,276 microstructure and morphology,18,31,53 have important impact on the catalytic activities. In the following, we will make a detailed summary of these factors that affect the catalytic performance. Table 5 lists some electrocatalysts for water splitting.
Table 5 Experimental results of oxide perovskites and derivatives for water splitting applications
Perovskites |
RE3+ |
Overpotential (VRHE@−10 mA cm−2) |
Intrinsic activity or Tafel slope |
Ref. |
LaMn0.75Co0.25O3−δ |
La |
1.66 V (OER) |
97 mV dec−1 (Tafel slope) |
31
|
RNiO3 |
La, Nd, Sm, Gd |
1.69 V (OER) |
75 mV dec−1 (Tafel slope) |
53
|
LaNiO3 |
La |
1.45 V (OER) |
36 mV dec−1 (Tafel slope) |
18
|
LaFexNi1−xO3 |
La |
1.53 V (OER) |
50 mV dec−1 (Tafel slope) |
135
|
La0.8Sr0.2MnO3 |
La |
1.51 V (OER) |
42 mV dec−1 (Tafel slope) |
273
|
La0.5(Ba0.4Sr0.4Ca0.2)0.5Co0.8Fe0.2O3−δ/r-GO |
La |
0.28 V (OER) |
46 mV dec−1 (Tafel slope for HER) |
274
|
|
|
−0.338 V (HER) |
80 mV dec−1 (Tafel slope for OER) |
|
La0.2Sr0.8Co1−xFexO3−δ |
La |
1.53 V (OER) |
56 mV dec−1 (Tafel slope) |
275
|
La1−xSrxNi0.8Fe0.2O3−δ |
La |
1.60 V (OER) |
70 mV dec−1 (Tafel slope) |
276
|
LaCoO3 |
La |
0.47 V (OER) |
180 mV dec−1 (Tafel slope) |
277
|
(Ln0.5Ba0.5)CoO3−δ |
Pr, Sm, Gd, Ho |
1.66 V (OER) |
60 mV dec−1 (Tafel slope) |
278
|
LaCo1−xFexO3 |
La |
1.63 V (OER) |
0.27 mA cm−2oxide@1.63 VRHE (MA) |
279
|
La1−xSrxFeO3−δ |
La |
0.37 V (OER) |
60 mV dec−1 (Tafel slope) |
280
|
LaCoO3 |
La |
1.75 V (OER) |
— |
281
|
PrBaCo2O6−δ |
Pr |
1.72 V (OER) |
70 mV dec−1 (Tafel slope) |
282
|
NdNiO3 |
Nd |
1.63 V (OER) |
70 mV dec−1 (Tafel slope) |
283
|
PrBa0.5Sr0.5Co1.5Fe0.5O5+δ |
Pr |
1.62 V (OER) |
58 mV dec−1 (Tafel slope) |
284
|
Most of the oxide perovskite catalysts are composed of multiple components, and they all have good catalytic activity. La0.5(Ba0.4Sr0.4Ca0.2)0.5Co0.8Fe0.2O3−δ perovskite nanorods were adhered to reduced graphene oxide (rGO) nanosheets to prepare the hybrid material as a bifunctional electrode, showing excellent performances for the OER and HER concurrently in alkaline media. It was operated at a voltage of 1.76 V at 50 mV cm−2, which is highly close to that of the commercial IrO2/C–Pt/C couple (1.76 V@50 mA cm−2).274 A two-step calcination method was applied to obtain the LaMn0.75Co0.25O3−δ perovskite NFbs showing a highly promising OER activity that was comparable to that of the commercial RuO2 catalysts and 26.5 times higher than that of the LaMnO3 catalysts.31 By a FeCl3 post-treatment, the bulk crystalline LaNiO3 perovskite was transformed into an amorphous nickel-iron-based motif on the perovskite matrix, which exhibited superior OER activity and an ultra-low overpotential of 189 mV at 10 mA cm−2.18 In addition, La and Ni were partially substituted by Sr and Fe, respectively, to obtain the La1−xSrxNi0.8Fe0.2O3−δ. The OER results showed that the Sr and Fe co-doped perovskite exhibited excellent OER activity even above that of the benchmark RuO2, which is attributed to the promising active sites of Ni3+, O22−/O− and an optimized Ni/Fe ratio.276 Fe-doped LaFexNi1−xO3 nanorods also showed a remarkable performance for the OER with a low overpotential of 302 mV at 10 mA cm−2 and a small Tafel slope of 50 mV dec−1.135
To improve the performances of OER and HER electrocatalysts, the chemical properties of the surface and the conductivity of the material are important, both greatly affected by the electronic structure. Recently, many new perovskites have been developed as highly active electrocatalysts for water-splitting.268,269 The double perovskites (Ln0.5Ba0.5)CoO3−δ (Ln = Pr, Sm, Gd and Ho) have been reported to be a family of highly active catalysts for the OER.278 It was found that the RE-containing perovskite was much more stable than common pseudo-cubic perovskites with comparable OER activity. The high activity and stability of these double perovskites were ascribed to the appropriate distance between the O p-band center and the Fermi level modified by the RE elements’ adjustment.268 After that, the LaCoO3 film grown on the LaSr1−xMnxO3 (LSMO) film by PLD was reported to exhibit higher OER activity than that of benchmark catalysts.281 The bandgap of Co 3d–O 2p decreased due to the transfer of electrons from LSMO to the LaCoO3 film, inducing a closer distance between the O 2p band center and the Fermi level. This indicated the lower activation energy and prominent OER activity.
LaCoO3 showed remarkable performance for the oxygen evolution reaction, so it was often chosen as the substrate to study the electronic structure–function effects of single perovskites.277,279,281 By the SG method, Fe was substituted into LaCoO3 obtaining LaCo1−xFexO3 to improve the catalytic performances.279 With 10% Fe substitution, there appeared a Co3+ spin-state transition from a generally low spin state to a high spin state and enhanced Co 3d–O 2p covalency, which resulted in a transition from an insulator to a half-metal and promoted OER performance for LaCo0.9Fe0.1O3. Besides the substitution, as shown in Fig. 22A and B, lattice-orientation control growth of LaCoO3 epitaxial films was applied as a strategy to optimize the spin-state regulation of the LaCoO3 perovskite.277 A spin-state transition of cobalt from a low spin state (LS t62ge0g) to a high spin state (IS t52ge1g) was induced by different distortion degrees of the CoO6 octahedron for different lattice-oriented LaCoO3 films. Hence, the LaCoO3(100) film presented lower adsorption free energy, higher conductivity and better OER performance than the other two films.
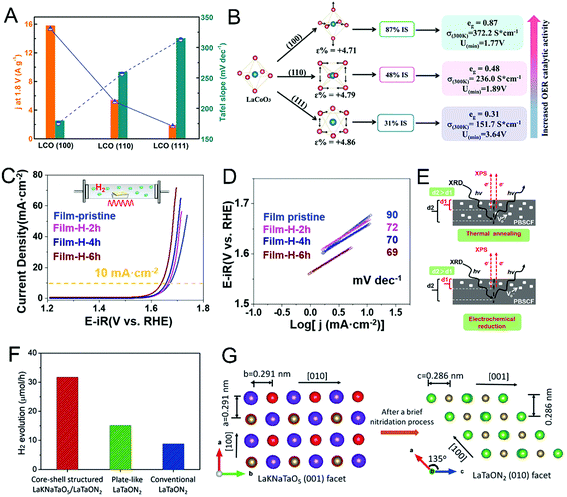 |
| Fig. 22 (A) The polarization curves and (B) Tafel plots of the OER for PrBa0.5Sr0.5Co1.5Fe0.5O5+δ (PBSCF) thin films after thermal annealing. (C) Schematic diagram of the difference in oxygen vacancy distribution in PBSCF thin films after annealing and electrochemical reduction. Reprinted with permission from ref. 277. Copyright 2017, Elsevier Inc. (D) Comparison of the reactivity (solid line) and Tafel slope (dashed line) for the obtained LCO films. (E) Schematic diagram of the relationship between spin configuration (free energy, conductivity and eg electron filling status) and OER activity of the LCO films with different orientations. Reprinted with permission from ref. 284. Copyright 2019, Wiley-VCH. (F) Direct comparison of H2 production rates for the core–shell-structured LaKNaTaO5/LaTaON2, the plate-like LaTaON2 and the conventional LaTaON2 powders. (G) The crystal structures views of the (001) facets of LaKNaTaO5 and (010) facets of LaTaON2. Reprinted with permission from ref. 34. Copyright 2019, Wiley-VCH. | |
In addition to the modulation of the electronic structure of the perovskites, the control of surface oxygen vacancies has become one of the most important issues for catalysts of water splitting. A series of Sr-doped perovskite oxides, La1−xSrxFeO3−δ, were synthesized by a bulk iodometric titration method.280 La0.2Sr0.8FeO3−δ with the optimum amount of surface oxygen vacancies and higher surface Fe valence states exhibited the best OER performance. As shown in Fig. 22C–E, Liu et al. reported that the OER performance of PrBa0.5Sr0.5Co1.5Fe0.5O5+δ was significantly improved by controlling the oxygen vacancies.284 The results indicated that the excessive oxygen defects facilitated the OH− affiliation and lowered the formation energy of O* on the surface, greatly boosting the OER kinetics. A series of RE nickelate films (RNiO3; R = La, La0.5Nd0.5, La0.2Nd0.8, Nd, Nd0.5Sm0.5, Sm, and Gd) were studied for OER performance.53 Through changing the composition of the catalysts, the partial reduction of Ni3+ to Ni2+ induced by the oxygen vacancies evidently improved the OER activity. However, the oxygen vacancies on the catalysts are not always beneficial for the catalytic process of water oxidation. The role of oxygen vacancies is still controversial. Shi et al. found that largely increasing the concentration of oxygen vacancies led to a significant reduction in the intrinsic OER activity. Structural studies revealed that oxygen vacancies tended to orderly align in PrO1−δ. This ordered structure not only lowered the cobalt oxidation states but also triggered a spin-state transition from the high-spin to low-spin states for cobalt ions, both greatly slowing the OER kinetics.282
4.5.1.2 Photocatalysis.
Besides electrocatalysis, perovskite-type materials are also promising photocatalysts for water splitting. To promote the performance of the photocatalysts for the HER, many strategies have been developed, such as interface engineering,271,285,286 energy-band engineering,287–289 and crystal structure modulation.34,118,290 Similar to electrocatalysts, surface structure and properties of the perovskite materials are extremely important for photocatalysts. It was reported that a higher surface hydrophilicity of the catalysts enhanced the photocatalytic activity of water oxidation reactions (listed in Table 6).
Table 6 Experimental results of oxide perovskites for photocatalytic water splitting or H2 generation
Perovskites |
RE3+ |
Bandgap (eV) |
Incident light |
Sacrificial reagents in solutions |
Electro-catalyst |
Activity |
Ref. |
LaSrFeO4/La2SrFe2O7 |
La |
2.16 |
>250 nm |
Neutral phosphate buffer |
1 wt% Pt |
477 μmol h−1 g−1 |
291
|
LaFeO3 |
La |
2.16 |
575 nm |
0.1 M NaOH |
— |
−0.1 mA cm−2 @1.41 V |
287
|
LaNiO3/CdS |
La |
2.4 |
420 nm |
— |
— |
3700 μmol h−1 g−1 |
290
|
LaFeO3–0.75PANI |
La |
1.92 |
>420 nm |
10% triethanolamine |
3 wt% Pt |
3080 μmol h−1 g−1 |
285
|
LaGa0.4Co0.6O3−δ |
La |
— |
>420 nm |
W/O |
1.0 at% IrOx |
470/717 μmol h−1 g−1 |
271
|
LaFeO3 |
La |
2.19 |
>420 nm |
50 mM AgNO3 |
2 wt% Au |
23 μmol/202 μmol h−1 g−1 |
118
|
LaTaON2 |
La |
1.94 |
420–620 nm |
20% methanol |
0.5 wt% Rh |
110 μmol h−1 g−1 |
34
|
LaTa0.9Zr0.1O1+yN2−y |
La |
1.99 |
λ > 420 nm |
50 mM AgNO3 |
1 wt% Pt |
110 μmol h−1 g−1 |
286
|
10%Er–K2Ta2O6 |
Er |
3.50 |
λ ≥ 270 nm |
10% formic acid |
— |
4620 μmol h−1 g−1 |
289
|
Er–KTaO3 |
Er |
3.37 |
λ ≥ 270 nm |
10% formic acid |
2% Pt |
39 528 μmol h−1 g−1 |
288
|
Pr–KTaO3 |
Pr |
— |
λ ≥ 270 nm |
10% formic acid |
2% Rh |
31 728 μmol h−1 g−1 |
288
|
Pr–K2Ta2O6 |
Pr |
4.40 |
λ ≥ 270 nm |
10% formic acid |
2% Pt |
36 134 μmol h−1 g−1 |
288
|
Er–K2Ta2O6 |
Er |
— |
λ ≥ 270 nm |
10% formic acid |
2% Rh |
44 716 μmol h−1 g−1 |
288
|
LaFeO3 was coated with a conductive polyaniline (PANI) aerogel to modify the surface hydrophilicity, showing a promoted photocatalytic performances, because of the elevated effects for water adsorption and diffusion, visible-light (photon) adsorption and photo-induced carrier transfer.285 Besides, Zr was doped into the structure of LaTaON2 to induce a better surface hydrophilicity and mesoporous microstructures, which led to a more efficient mechanism of the reaction to facilitate water oxidation.286 The redox ability of the catalysts is also important for photocatalysts. The Sr and Co co-doped La1−xSrxGa1−yCoyO3−δ perovskites exhibited much higher H2 production than the benchmark without doping, attributed to the lower activation energy.271 As shown in Fig. 22F and G, the highly active crystal phase and structure of the perovskites have been studied.34 With K and Na doping, the LaKNaTaO5 plates gradually transformed into core–shell LaTaON2, exposing more active (010) faces to promote the H2 evolution activity by 4 times. p-Type LaFeO3 and LaSrFeO4 have an ideal bandgap and band edge positions for overall solar water splitting.287,291 These oxides have been prepared and the physicochemical properties such as surface area, optical absorption and crystal structure are modified to acquire superior photocatalytic performances.
The properties and origin of the charge carriers are some of the most crucial factors for photocatalysts. The heterostructure of LaNiO3/CdS shows highly improved H2 production performance, ascribed to the effective separation and transport of photoinduced charge carriers.290 A plasmon-based Au/LaFeO3 composite photocatalyst was built to enhance the activities for water reduction and oxidation, and the complex effects of hot electrons and holes on the reaction were investigated.
4.5.2 Removal of pollutants.
Clearing up of nitrogen oxides, carbon monoxide and other pollutants has a great significance on environmental protection. RE-containing oxide perovskite materials possess excellent catalytic activity and high-temperature stability, thus can be widely used in the catalytic degradation of nitrogen oxides and other pollutants (dye molecules, phenol, etc.).
4.5.2.1 Water treatment.
Perovskites are effective photocatalysts for the degradation of various organic compounds in water. A series of perovskite-type titanate MxTiyOz (M = transition and RE metals) compounds with different structures and sizes were synthesized by the thermal decomposition method.292 The relationship between the bandgap and crystalline size was identified: smaller crystallite sizes induced lower band gaps, resulting in stronger visible light absorption and better performance of pyrocatechol degradation. New double perovskite Dy2ZnMnO6 NPTs were successfully synthesized and applied as a photocatalyst for degradation of methyl violet and methyl orange.293 Novel LaFeO3 perovskites partially substituted with Ti have been synthesized via a SG method.293 After substitution of Ti, the catalyst exhibited greatly improved stability, which is attributed to the lower Fe leaching during the reaction. The RE-doped K2Ta2O6 perovskites were successfully synthesized and exhibited greatly improved degradation efficiency under UV–vis light compared with pristine K2Ta2O6.289
To obtain materials with superior photocatalytic performance, perovskites have been modified by forming composites with other functional units. Fig. 23A and B show that the heterostructures of LaFeO3/Ag2CO3 nanocomposites are successfully constructed and show a very high electron–hole pair decoupling efficiency, resulting in greatly improved photocatalytic activity for the degradation of rhodamine B (RhB).121 Moreover, Au/La-SrTiO3 showed a superimposed effect of Au NPTs and La-doping, inducing good photocatalytic activity for photodegradation of RhB.175 The CuO/LaFeO3 nanocomposite synthesized by the SG method exhibits outstanding activity for degradation of RhB, attributed to the simultaneous effects of photocatalysis.294 RE ion (Er, Pr) doped KTaO3/K2Ta2O6 photocatalysts were decorated with monometallic NPTs (Au, Pt, Rh), resulting in boosted photocatalytic performances compared with that of pristine KTaO3/K2Ta2O6.288
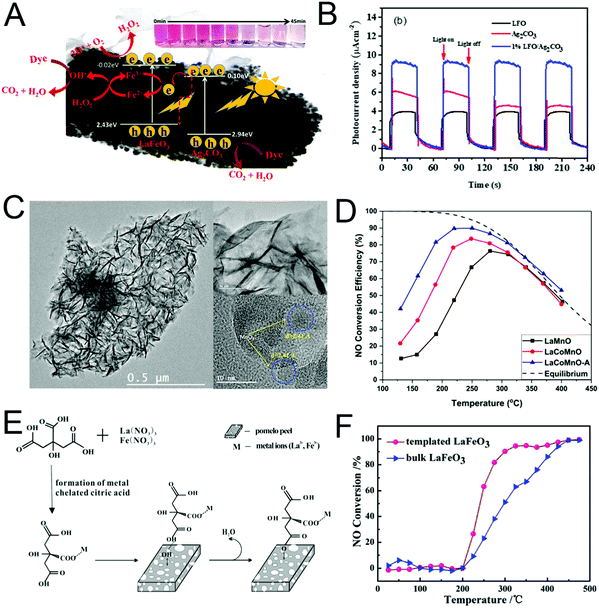 |
| Fig. 23 (A) The HRTEM image and the schematic diagram of the mechanism for the generation of different reactive oxygen species. (B) Photocurrent tests of the pure LFO, Ag2CO3, and 1% LFO/Ag2CO3 samples. Reprinted with permission from ref. 121. Copyright 2019, American Chemical Society. (C) The HRTEM of the LaCoMnO-A sample. (D) NO conversion for the studied LaMnO, LaCoMnO and LaCoMnO-A samples. Reprinted with permission from ref. 295. Copyright 2019, Elsevier B.V. (E) The proposed schematic diagrams for adsorption of metal ion precursors on the surface of pomelo peel. (F) NO conversion of template LaFeO3 and bulk LaFeO3 samples at different temperatures. Reprinted with permission from ref. 299. Copyright 2017, the Partner Organizations. | |
4.5.2.2 Automobile exhaust.
NOx, CO and CH4 from the incomplete combustion of fuels have been considered as the main pollutants in air. It is, therefore, essential to develop catalysts such as perovskite materials to eliminate these pollutants due to their high electroactivity in degradation.
For NOx degradation, both oxidation and reduction reactions have been applied. Mn-based perovskites with a porous nanostructure have been successfully synthesized and they exhibited rather good performance for NO oxidation.295,296 Furthermore, as shown in Fig. 23C and D, when La was substituted with Co, the activity of NO oxidation was further improved.295 The Cu-doped perovskite LaCoO3 that was doped with Cu showed a more prominent activity than the pristine oxide.297 The reduction of NO was performed by NH3123,144 or CO298–300 reactant gases. La1−xCexMnO3/attapulgite nanocomposites were synthesized by the SG method with different doping fractions of Ce. When the doping fraction x was 0.1, the highest activity for NO reduction was obtained.123 LaBO3/attapulgite (ATP) (B = Mn, Fe, Co, Ni) composites were prepared, and the order of NO reduction capacity was LaMnO3/ATP > LaNiO3/ATP > LaFeO3/ATP > LaCoO3/ATP.144 Pure LnFeO3 (Ln = La, Pr–Tb) perovskite porous hollow spheres and solid spheres (Ln = Dy–Yb, Y) were successfully synthesized, in which the activity of hollow spheres was obviously higher than that of the solid spheres.298 As shown in Fig. 23E and F, LaFeO3 with a hierarchical porous structure was successfully prepared and showed remarkable performance for the NO reduction reaction.299
Meanwhile, the oxidation of CH4 is crucial for green gas reduction.301 La0.5Ba0.5MnO3 nanocubes have been synthesized and presented high activity and stability for the oxidation of CO and CH4.122 A novel double perovskite La2−xSrxNiAlO6 catalyst showed excellent catalytic activity with 0.1 fraction of Sr doping for CH4 combustion.302 The RE-containing double perovskite oxide La2CoMnO6 supported on CeO2 was synthesized by three methods, and the activity of CH4 combustion was in the order CPT > SG > impregnation.170 The calcination temperature of preparation of perovskite-type LaFeO3 oxides was reported to have a great effect on the performance for CH4 oxidation.119
4.5.3 Carbon and nitrogen conversion.
The conversion of carbon-based compounds is an important chemical reaction in industry. For the special structure and chemical inertia, RE-containing oxide perovskites have very important applications in the conversion of carbon chemicals, such as the oxidative coupling of methane, oxidation of methanol or urea, conversion of carbon dioxide, etc.142 Many RE-based oxide perovskites exhibit flexible redox properties, high surface oxygen mobility, abundant surface active sites and good thermal stability, which is applicable in a wide range of applications in traditional heterogeneous catalysis for the chemical product and energy industry.142,303–309
Methane conversion to C2 hydrocarbons (ethane and ethylene) by oxidative coupling (OCM) is a promising direct methane conversion technology, which has been investigated extensively during the last three decades. Sekine et al. reported that a La0.7Ca0.3AlO3−δ catalyst exhibited a high CO2-OCM activity in an electric field with a C2 yield of 7.4% at 348 K, attributed to Ca doping.306 Jung et al. investigated the effect of pH values during LaAlO3 preparation on the OCM activity. It was found that the sample prepared at pH = 8 presented the highest C2 yield due to its well-developed oxygen vacancies and electrophilic lattice oxygen.303
Another important route of methane transformation is conversion to the syngas by the partial oxidation of methane (POM)308 or dry reforming of methane (DRM).305 Layered perovskite materials denoted as La1+xSr1−xCoO4 (x = 0; 0.25) and NdCaCoO3.96 are synthesized by the solid state method, and have better stability and higher activity in the reaction of partial oxidation of methane to syngas. This originated from the different effects of alkali metals.308 The synergistic La–Ce effect was applied to optimize the reactivity of DRM by CO2 on the supported perovskite LaxCe1−x–Fe2O3/Al2O3. With the assistance of the La–Ce effect, the reactivity of the catalysts was greatly enhanced due to the promoted lattice oxygen migration.305 As shown in Fig. 24A–D, Gao et al. prepared LaMnO3–Pt coated on a ZnO nanoarray by a simple low-temperature hydrothermal synthesis method.304 Pt was uniformly distributed on the surface of the catalyst, which greatly increased the oxidation of propane. The most effective routes for the production of hydrogen without COx by-products are methane and ammonia decomposition.307,310 Correspondingly, the conversion of COx into lower alcohols is also an important catalytic reaction. As shown in Fig. 24E, the rhodium atom can accept electrons from the reaction of LaFeO3 and La2O3, which further adjusts the amount of adsorbed CO, finally improving the selectivity and transformation rate of CO into ethanol.142 Pudukudy et al. reported the successful synthesis of a set of porous CeO2, zirconia and lanthana supported nickel catalysts for H2 generation. It was noted that the lanthana-based perovskite formed during the reaction greatly improved the reactivity.307
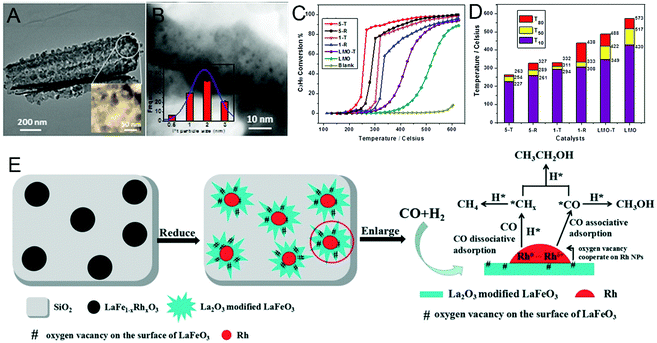 |
| Fig. 24 (A) The TEM image of a mesoporous LaMnO3 nanotube with Pt loading and (B) HAADF images of an aged LaMnO3 nanotube with Pt nanoparticles. (C) Propane conversion over all tested catalysts. (D) Bar charts of propane conversion over all samples tested at T10, T50 and T80. Reprinted with permission from ref. 304. Copyright 2018, Wiley-VCH. (E) Schematic diagram of the structure conversion of LaFe1−xRhxO3/SiO2 during the reduction process and reaction pathways over the catalysts. Reprinted with permission from ref. 142. Copyright 2019, The Royal Society of Chemistry. | |
4.6 Magnetics
The unpaired electrons in oxide perovskites containing transition metal ions (TM: Fe, Co, Ni, Mn, etc.) and RE ions (RE: Gd, Sm, Tb, Ho, etc.) can result in excellent magnetic properties. Those magnetic materials are of great significance in the application of magnetic devices and spintronic devices.311–313
4.6.1 Ferromagnetic, antiferromagnetic, and superparamagnetic materials.
Both TM and RE ions can have unpaired electrons, which endow many RE-based oxide perovskites with excellent magnetic properties. In particular, RE-based oxide perovskites combined with nickel, cobalt and iron have been extensively studied for their ferromagnetic and antiferromagnetic phase transitions. This provides both theoretical and experimental support for the development of new magnetic materials.314–316
Despite its importance, few research studies have focused on the quantum size and crystal structure effects on the magnetism of RE PMNs. Previous work has demonstrated the magnetic hysteresis (M/H) curves of bulk-phase La0.7Ca0.3MnO3 at 5, 100 and 200 K, respectively.317 In contrast, curves measured on nano La0.7Ca0.3MnO3 show no sign of saturation at all. The coercive field of a nanosample at 5 K is more than two orders of magnitude higher than that of the bulk phase. The authors attributed the results to the size effect, which led to a strong frustration of ferromagnetic ordering in nano La0.7Ca0.3MnO3 as compared to the basically stable and homogeneous ferromagnetic ground state in the bulk. The parent host PrFeO3 showed superparamagnetic behaviour.318 Through introducing Al3+ cations into the PrFeO3 (B-site) with the adjustment of different proportions, the magnetization can be greatly improved. Such an observation was likely because the introduction of the ferromagnetic component results in a weaker antiferromagnetic coupling between iron spin moments and the rearrangement in PrAlxFe1−xO3 NCs than that of PrFeO3. These results unambiguously demonstrate that quantum size and crystal structure have significant effects on the magnetism of RE host perovskite-type oxide nanomaterials.
4.6.2 Magnetocaloric materials.
The entropy changes of RE-based perovskite materials between the magnetic ordering and disordering states result in a magnetocaloric effect, suitable for magnetic refrigeration.26,329,330 The initial randomly oriented magnetic moments are aligned by a magnetic field, resulting in the heating of the magnetocaloric materials.331 This heat is removed from the material to the ambient environment by heat transfer. Upon removing the field, the magnetic moments randomize, which leads to the cooling of the material below ambient temperature. Heat from the cooling process of the system can then be extracted using a heat-transfer medium. Depending on the operating temperature, the heat-transfer medium may be water (with antifreeze), air or, for very low temperatures, helium. This technology, having the merits of high security, low energy consumption and low pollution, is expected to replace the traditional compressed liquid refrigeration. Therefore, it is of great importance to develop high performance RE-based perovskite magnetocaloric materials.
Recently, RE-containing PNMs have been demonstrated as excellent candidates for magnetic refrigeration based on an enhanced magnetocaloric effect.317,331 The intense interest in perovskite-type manganese oxides R1−xBxMnO3 (where R is a RE ion and B is a divalent alkali) is initially prompted by the observation of colossal magnetoresistance. However, they also exhibit large magnetocaloric effects associated with the transition from a second order ferromagnetic to a paramagnetic state near room temperature.26 The magnetic entropy change (−ΔSM) of 3.28 J kg−1 K−1 with a relative cooling power of 120 J kg−1 and an adiabatic temperature change (ΔTad) of 2.11 K at 310 K under 50 kOe magnetic field is already comparable to the best Gd-based clusters.26 In addition, the magnetic cooling performance of exfoliated nanosheets is even better (Table 7). With excellent processability and facile large-scale production, RE-containing PNMs have opened up a new avenue and therefore are extremely worthwhile to be explored.
Table 7 RE-based perovskite materials for superconductor, electronic, and magnetic devices
Perovskites |
RE |
Synthesis |
Morphology |
Magnetics (application) |
Ref. |
La0.7Sr0.3MnO3 |
Gd, Tb, Dy, Ho |
SG |
NCs, ∼30 nm |
T
C = 320–330 K |
319
|
LnFeO3 |
Eu, Gd, Tb |
SG |
NPTs, 30–115 nm |
T
C = 5–8 K; bioimaging |
320
|
RECrO3 |
Er, Tm, Yb, Lu |
ST |
NPTs |
T
N = 77–115 K |
321
|
YbMnO3 |
Yb |
ST |
NRs/NPLs 50–200 nm |
T
N, ∼86 K |
322
|
La0.67Ca0.33Mn1−xNixO3 |
La |
HT |
NPTs |
M
s = 34.39 emu g−1 |
323
|
LaFeO3 |
Ce |
CPT |
NPTs |
M
S = 0.56 emu g−1 |
151
|
Ce1−xEuxCrO3 |
Ce1−xEuxCrO3 |
CBs |
NPTs, 50–100 nm |
T
C = 280 K/3.5 T, TN, ∼182 K |
324
|
BiFeO3 |
Ce |
SG |
NPTs, 30–50 nm |
M
H = 1.766 emu g−1, Mr = 0.0572 emu g−1, HC = 0.1468 kOe |
325
|
Bi1−xHoxFeO3 |
Ho |
CBs |
NPTs, 60–75 nm |
H
c, ∼400 Oe, TN, ∼640 K |
326
|
SmFe0.85Mn0.15O3 |
Sm |
SG |
NPTs, 100–240 nm |
H
C = 1928 Oe, Mr = 0.064 emu g−1 |
327
|
BiFeO3 |
Ho |
SG |
NPTs |
M
s = 5.3 emu g−1, Mr = 1.5 emu g−1, HC = 140 Oe |
328
|
5. Conclusions and prospect
In this review, we summarize RE-containing PNMs with great compositional tunability, structural variability, and broad applications in optics, photovoltaics, catalysis, dielectrics, magnetics, etc. The intrinsic reasons for the property improvements induced by RE elements are briefly discussed, providing a valuable reference for the design and application of RE-containing new functional materials. Although several problems and challenges exist, the research on RE-containing perovskites is rapidly progressing. New opportunities associated with RE-containing PNMs such as high efficiency, superior stability, ease of mass production, models for fundamental research, environmental protection, and interdisciplinary studies, will be discussed in the following sections.
5.1 High efficiency and stabilities
Although lead halide (APbX3, X = Br, I) perovskites have been widely used in photovoltaics with high PECE, there is still a considerably big gap between the current PECE and its theoretical maximum. In addition, the poor stability of APbX3 leads to their easy decomposition and thus the loss of photovoltaic activity in a humid environment. Improving the PECE and stability of APbX3 perovskite materials is significant for their future applications. In addition, as the photoactive materials in solar cells, perovskites (oxides: BaSnO3, TmFeO3, etc.; halides: Cs3Bi2X9, CsSnX3, Cs2AgSbX3, etc., X = Br, I) cannot absorb NIR light. By incorporating RE into perovskite structures, it is possible to improve the absorption efficiency of solar light in the NIR range, thus enhancing the PECE. The incorporation of RE ions can also adjust the bandgap of perovskites and improve the performances of the devices. Another important strategy is to replace APbX3 with lead-free perovskites. The application of halide perovskites as illumination sources is also hindered by the low EQE and poor stability. It is therefore of both fundamental and practical importance to improve the EQE and stability of perovskite-based illumination sources. The exploration of white-light illumination sources is also desirable and current white-light perovskite-based devices are very rare.
In catalytic applications, some halide perovskites indeed show good photocatalytic activity, but with poor stability. To the best of the authors’ knowledge, there is no report regarding the catalytic performances of RE-containing halide perovskites. The exploration of RE-containing halide perovskites is, therefore, a promising area. Although oxide perovskites have been widely used in various catalytic reactions including the ORR, OER, NOx elimination, etc., the catalytic performances still need to be improved. The incorporation of RE ions with various radii and valences into perovskite structures will yield defects, strains and oxygen vacancies, and therefore enhance the catalytic performances in the reactions of ORR, carbon or nitrogen transformations.
Selective RE doping has made some breakthrough in improving the dielectric, piezoelectric, thermoelectric and ferroelectric properties of perovskites. However, from the material compositional design point of view, there are still great challenges for RE-doped perovskites to meet the requirements of high-temperature piezoelectrics and sensors in commercial applications. The development and design of perovskite materials with high transition temperatures and high dielectric and piezoelectric constants are urgently needed.
RE-based oxide perovskites are excellent electrode materials of solid oxide fuel cells with high activity and energy conversion efficiency (∼60%). However, the efficiency is still considerably lower than the theoretical value. In addition, the high operating temperature and acidic (or basic) environment pose great challenges to the stability of electrodes. All of these important issues must be resolved. In the case of metal–air batteries, although some highly active catalysts have been designed, the fabrication of high-capacity, stable and efficient batteries is still difficult. Therefore, it is essential to explore reliable battery assembly processes and find suitable electrode materials. Besides, the match between electrolyte and electrode materials is an important factor for high capacity batteries.
When used as magnetic materials and detectors, oxide perovskites have high stability but are rarely involved in biomedical magnetic resonance imaging. It may have great potential for research. In addition, the majority of magnetic devices and spin devices are still in the stage of fundamental research, requiring considerable efforts to be promoted to practical applications. Meanwhile, achieving high selectivity and sensitivity is always desirable for the detection of unknown substances. The application of perovskites in analysis and detection is a new area.
5.2 Green and mass production
The mass production of RE-containing perovskites is a prerequisite for their applications. The fabrication of solar cells requires large-scale preparation of halide perovskite thin films, with low cost and simple and efficient fabrication processes. The application of oxide perovskites as catalysts and electrolytes requires materials with tunable size, high crystallinity, adjustable catalytic active sites and good dispersion. It is a great challenge to the preparation of nanomaterials.
With the rise of wearable technology, the fabrication of flexible devices opens up great opportunities for perovskite materials. In particular, the large-scale preparation of flexible solar cells, flexible sensors, flexible capacitors and batteries has boosted the development of RE-containing PNMs. In the process of batch production, several factors including the cost, environmental protection and market demand must be balanced. All of these considerations are directly related to the commercial success of devices, and even determine the future development of this field.
5.3 Fundamental researches
Although some studies have shown that perovskite materials play important roles in the fields of luminescent materials, catalysts, dielectrics, magnetics, solid-state batteries and sensors, most of the studies are still in the preliminary stage. The details of how RE-doping improves the performances of perovskite materials, by modulating the composition, local structure and molecular orbitals, are still unclear. In particular, the studies on changes such as phases, vacancies, stress and defects induced by doping are still empirical and lack theoretical interpretations. The dependence on expensive and state-of-the-art characterization tools also limits further exploration of mechanisms. The development of new materials, especially RE-containing materials, may create new structures and therefore new functionalities, among which some have been predicted theoretically. It is essential for their synthesis and characterization.
5.4 Environmental protection
Although lead-based halide and oxide perovskites can exhibit excellent properties in applications such as luminescent materials, solar cells, and dielectric materials, Pb is harmful to both the environment and human health. Moreover, the replacement of precious element-based perovskites with RE-containing perovskites is beneficial for broad applications. Currently, lead-free perovskite materials are showing great potential to achieve similar or even better photovoltaic performances. It has been demonstrated that the incorporation of RE regulates the valence band as well as the light absorption ability of lead-free perovskite materials. On the other hand, the catalytic activity of some RE-containing perovskite materials has become comparable to that of noble metals, but the stability of these oxides is still poor. To meet the Green Chemistry criteria, the preparation and application of perovskite materials should utilize environmentally friendly raw materials, high-efficiency preparation processes, and minimal waste discharges.
5.5 Interdisciplinary studies
Perovskite materials are the focus of many disciplines. The study of RE-containing perovskite materials requires knowledge from many disciplines such as theoretical physics, chemistry, materials science, optical engineering, electromagnetics, biomedicine, etc. Interdisciplinary collaborations are therefore essential. We encourage more scientists in various fields to pay attention to this emerging field and promote the applications of perovskite materials.
Abbreviations and list of acronyms
0D | Zero-dimensional |
1D | One-dimensional |
2D | Two-dimensional |
3D | Three-dimensional |
acac | Acetylacetone |
AIE | A-site ionic electronegativity |
ATP | Attapulgite |
CCB | Citrate auto combustion method |
CPT | Co-precipitation |
CVD | Chemical vapor deposition |
CBs | Combustion method |
CB | Conduction band |
d
33
| Piezoelectric constant |
DC | Direct current |
DCL | Downconversion luminescence |
DRM | Dry reforming of methane |
E
c
| Coercive electric field |
ε
r
| Dielectric constant |
EQE | External quantum efficiency |
ES | Electrostatic spinning |
ETM | Electron transport material |
FF | Fill factor |
FWHM | Full width at half maximum |
H
C
| Coercivity |
HER | Hydrogen evolution reaction |
HI | Hot injection |
HT | High-temperature method |
J
sc
| Short-circuit current density |
K
p
| Planar electromechanical coupling coefficient |
L
C
| Leakage current |
Ln | Lanthanides |
LHPs | Lead-based halide perovskites |
MA | Methyl amine |
MBM | Mechanochemical ball milling |
ME | Micro-emulsion |
M
H
| Maximum magnetization |
MPB | Morphotropic phase boundary |
M
r
| Remanent magnetization |
MS | Molten salt reaction |
M
S
| Saturation magnetization |
NCbs | Nanocubes |
NCs | Nanocrystals |
NFs | Nanofilms |
NFbs | Nanofibers |
NIR | Near Infrared |
NPTs | Nanoparticles |
NPLs | Nanoplates |
NPDs | Nanopowders |
NRs | Nanorods |
NWs | Nanowires |
OCM | Oxidative coupling of methane |
ODE | 1-Octadecene |
OER | Oxygen evolution reaction |
OM | Oleylamine |
ORR | Oxygen reduction reaction |
PAN | Polyaniline |
PCE | Power conversion efficiency |
PECE | Photoelectric conversion efficiency |
PL | Photoluminescence |
PLD | Pulsed laser deposition |
PNMs | Perovskite nanomaterials |
POM | Partial oxidation of methane |
P
r
| Remanent polarization |
PR | Pechini method |
PSCs | Perovskite solar cells |
QD | Quantum dots |
QY | Quantum yield |
γ
| Relaxation behaviour |
RE | Rare earth |
RETU | Radiative energy transfer up-conversion |
rGO | Reduced graphene oxide |
RhB | Rhodamine B |
RP | Ruddlesden–Popper |
RT | Room temperature |
S
a
| Absolute temperature sensitivity |
S
bk
| Seebeck coefficient |
SCT | Spin coating technique |
SG | Sol–gel |
S
r
| Relative temperature sensitivity |
SS | Solid state synthesis |
ST | Solvothermal method |
t
| Tolerance factor |
tan δ | Dielectric dissipation factor |
T
c
| Curie temperature point |
TD | Thermal decomposition |
TEM | Transmission electron microscope |
TM | Transition metal |
T
N
| Néel temperature |
T
p
| Sensor working temperature |
μ
| Octahedral factor |
UCPL | Up-conversion photoluminescence |
UV | Ultraviolet |
VB | Valence band |
V
oc
| Open-circuit voltage |
VOCs | Volatile organic compounds |
WC | Wet chemical |
Conflicts of interest
The authors declare no competing financial interest.
Acknowledgements
We gratefully acknowledge the support from the China National Funds for Excellent Young Scientists (21522106) and the National Natural Science Foundation of China (21971117, 21771156), the 111 Project (B18030) from China, the Open Funds (RERU2019001) of the State Key Laboratory of Rare Earth Resource Utilization and the Functional Research Funds for the Central Universities, Nankai University (ZB19500202) and the Early Career Scheme (ECS) fund (Grant No.: PolyU 253026/16P) from the Research Grant Council (RGC) in Hong Kong.
References
- J. Shamsi, A. S. Urban, M. Imran, L. De Trizio and L. Manna, Chem. Rev., 2019, 119, 3296–3348 CrossRef CAS PubMed.
- Y. Zhang, W. Jie, P. Chen, W. Liu and J. Hao, Adv. Mater., 2018, 30, 1707007 CrossRef PubMed.
- H. Zhu, P. Zhang and S. Dai, ACS Catal., 2015, 5, 6370–6385 CrossRef CAS.
- Y. Wei, Z. Cheng and J. Lin, Chem. Soc. Rev., 2019, 48, 310–350 RSC.
- W.-J. Yin, B. Weng, J. Ge, Q. Sun, Z. Li and Y. Yan, Energy Environ. Sci., 2019, 12, 442–462 RSC.
- J. Vieten, B. Bulfin, P. Huck, M. Horton, D. Guban, L. Zhu, Y. Lu, K. A. Persson, M. Roeb and C. Sattler, Energy Environ. Sci., 2019, 12, 1369–1384 RSC.
- Z. Li, Q. Xu, Q. Sun, Z. Hou and W.-J. Yin, Adv. Funct. Mater., 2019, 29, 1807280 CrossRef.
- M. J. Cliffe, E. N. Keyzer, M. T. Dunstan, S. Ahmad, M. F. L. De Volder, F. Deschler, A. J. Morris and C. P. Grey, Chem. Sci., 2019, 10, 793–801 RSC.
- L. Wang, H. Zhou, J. Hu, B. Huang, M. Sun, B. Dong, G. Zheng, Y. Huang, Y. Chen, L. Li, Z. Xu, N. Li, Z. Liu, Q. Chen, L. D. Sun and C. H. Yan, Science, 2019, 363, 265–270 CrossRef CAS PubMed.
- R. Saha, A. Sundaresan and C. N. R. Rao, Mater. Horiz., 2014, 1, 20–31 RSC.
- J. S. Yao, J. Ge, B. N. Han, K. H. Wang, H. B. Yao, H. L. Yu, J. H. Li, B. S. Zhu, J. Z. Song, C. Chen, Q. Zhang, H. B. Zeng, Y. Luo and S. H. Yu, J. Am. Chem. Soc., 2018, 140, 3626–3634 CrossRef CAS PubMed.
- Y. Cheng, C. Shen, L. Shen, W. Xiang and X. Liang, ACS Appl. Mater. Interfaces, 2018, 10, 21434–21444 CrossRef CAS PubMed.
- J. Miao and F. Zhang, J. Mater. Chem. C, 2019, 7, 1741–1791 RSC.
- T. Addabbo, F. Bertocci, A. Fort, M. Gregorkiewitz, M. Mugnaini, R. Spinicci and V. Vignoli, Sens. Actuators, B, 2017, 244, 1054–1070 CrossRef CAS.
- M. Pellerin, E. Glais, T. Lecuyer, J. Xu, J. Seguin, S. Tanabe, C. Chanéac, B. Viana and C. Richard, J. Lumin., 2018, 202, 83–88 CrossRef CAS.
- Z. Shi, J. Guo, Y. Chen, Q. Li, Y. Pan, H. Zhang, Y. Xia and W. Huang, Adv. Mater., 2017, 29, 1605005 CrossRef PubMed.
- E. Grabowska, Appl. Catal., B, 2016, 186, 97–126 CrossRef CAS.
- G. Chen, Y. Zhu, H. M. Chen, Z. Hu, S. F. Hung, N. Ma, J. Dai, H. J. Lin, C. T. Chen, W. Zhou and Z. Shao, Adv. Mater., 2019, 31, e1900883 CrossRef PubMed.
- C. Wei, R. R. Rao, J. Peng, B. Huang, I. E. L. Stephens, M. Risch, Z. J. Xu and Y. Shao-Horn, Adv. Mater., 2019, 31, e1806296 CrossRef PubMed.
- F. Polo-Garzon and Z. Wu, J. Mater. Chem. A, 2018, 6, 2877–2894 RSC.
- A. Kostopoulou, E. Kymakis and E. Stratakis, J. Mater. Chem. A, 2018, 6, 9765–9798 RSC.
- F. Li, M. J. Cabral, B. Xu, Z. Cheng, E. C. Dickey, J. M. LeBeau, J. Wang, J. Luo, S. Taylor, W. Hackenberger, L. Bellaiche, Z. Xu, L. Q. Chen, T. R. Shrout and S. Zhang, Science, 2019, 364, 264–268 CrossRef CAS PubMed.
- T. Asano, A. Sakai, S. Ouchi, M. Sakaida, A. Miyazaki and S. Hasegawa, Adv. Mater., 2018, 30, 1803075 CrossRef PubMed.
- S. Wang, Q. Bai, A. M. Nolan, Y. Liu, S. Gong, Q. Sun and Y. Mo, Angew. Chem., Int. Ed., 2019, 58, 8039–8043 CrossRef CAS PubMed.
- A. Kostopoulou, K. Brintakis, N. K. Nasikas and E. Stratakis, Nanophotonics, 2019, 8, 1607–1640 CAS.
- B. Arun, V. R. Akshay, G. R. Mutta, C. Venkatesh and M. Vasundhara, Mater. Res. Bull., 2017, 94, 537–543 CrossRef CAS.
- Y. Cao, S. Cao, W. Ren, Z. Feng, S. Yuan, B. Kang, B. Lu and J. Zhang, Appl. Phys. Lett., 2014, 104, 232405 CrossRef.
- X. Chen, J. Song, X. Chen and H. Yang, Chem. Soc. Rev., 2019, 48, 3073–3101 RSC.
- S. Khalfin and Y. Bekenstein, Nanoscale, 2019, 11, 8665–8679 RSC.
- N. Phung and A. Abate, Small, 2018, 14, e1802573 CrossRef PubMed.
- J. Bian, Z. Li, N. Li and C. Sun, Inorg. Chem., 2019, 58, 8208–8214 CrossRef PubMed.
- Z. Wang, Z. Shi, T. Li, Y. Chen and W. Huang, Angew. Chem., Int. Ed., 2017, 56, 1190–1212 CrossRef CAS PubMed.
- K. Huang, L. Yuan and S. Feng, Inorg. Chem. Front., 2015, 2, 965–981 RSC.
- X. Wang, T. Hisatomi, Z. Wang, J. Song, J. Qu, T. Takata and K. Domen, Angew. Chem., Int. Ed., 2019, 58, 10666–10670 CrossRef CAS PubMed.
- T. J. Milstein, K. T. Kluherz, D. M. Kroupa, C. S. Erickson, J. J. De Yoreo and D. R. Gamelin, Nano Lett., 2019, 19, 1931–1937 CrossRef CAS PubMed.
- R. RameshKumar, T. Ramachandran, K. Natarajan, M. Muralidharan, F. Hamed and V. Kurapati, J. Electron. Mater., 2019, 48, 1694–1703 CrossRef CAS.
- A. Annadi, G. Cheng, H. Lee, J. W. Lee, S. Lu, A. Tylan-Tyler, M. Briggeman, M. Tomczyk, M. Huang, D. Pekker, C. B. Eom, P. Irvin and J. Levy, Nano Lett., 2018, 18, 4473–4481 CrossRef CAS PubMed.
- C. F. Pena, M. E. Soffner, A. M. Mansanares, J. A. Sampaio, F. C. G. Gandra, E. C. da Silva and H. Vargas, Phys. B, 2017, 523, 39–44 CrossRef CAS.
- G. Pan, X. Bai, D. Yang, X. Chen, P. Jing, S. Qu, L. Zhang, D. Zhou, J. Zhu, W. Xu, B. Dong and H. Song, Nano Lett., 2017, 17, 8005–8011 CrossRef CAS PubMed.
- L. Yang, D.-Y. Zheng, K.-X. Guo, W.-N. Zhao, Z.-H. Peng, G.-G. Peng and T. Zhou, J. Mater. Sci.: Mater. Electron., 2018, 29, 18011–18019 CrossRef CAS.
- M. A. Shahzad, M. Shahid, I. Bibi, M. A. Khan, M. A. Nawaz, M. F. A. Aboud, M. Asghar, R. N. Paracha and M. F. Warsi, Ceram. Int., 2017, 43, 1073–1079 CrossRef CAS.
- Z. Yi, N. H. Ladi, X. Shai, H. Li, Y. Shen and M. Wang, Nanoscale Adv., 2019, 1, 1276–1289 RSC.
- M. D. Smith, B. A. Connor and H. I. Karunadasa, Chem. Rev., 2019, 119, 3104–3139 CrossRef CAS PubMed.
- X. Zhang, L. Li, Z. Sun and J. Luo, Chem. Soc. Rev., 2019, 48, 517–539 RSC.
- W. Xiang, Z. Wang, D. J. Kubicki, W. Tress, J. Luo, D. Prochowicz, S. Akin, L. Emsley, J. Zhou, G. Dietler, M. Grätzel and A. Hagfeldt, Joule, 2019, 3, 205–214 CrossRef CAS.
- Y. Zhou, J. Chen, O. M. Bakr and H.-T. Sun, Chem. Mater., 2018, 30, 6589–6613 CrossRef CAS.
- J. Xu, X. Chen, Y. Xu, Y. Du and C. Yan, Adv. Mater., 2019, 0, 1806461 CrossRef PubMed.
- H. Zhao, J. Xia, D. Yin, M. Luo, C. Yan and Y. Du, Coord. Chem. Rev., 2019, 390, 32–49 CrossRef CAS.
- X. Qin, X. W. Liu, W. Huang, M. Bettinelli and X. G. Liu, Chem. Rev., 2017, 117, 4488–4527 CrossRef CAS PubMed.
- R. Rajeswari, N. Islavath, M. Raghavender and L. Giribabu, Chem. Rec., 2019, 19, 1–25 CrossRef.
- F. Li, D. Lin, Z. Chen, Z. Cheng, J. Wang, C. Li, Z. Xu, Q. Huang, X. Liao, L. Q. Chen, T. R. Shrout and S. Zhang, Nat. Mater., 2018, 17, 349–354 CrossRef CAS PubMed.
- A. Fuertes, Mater. Horiz., 2015, 2, 453–461 RSC.
- L. Wang, K. A. Stoerzinger, L. Chang, J. L. Zhao, Y. Y. Li, C. S. Tang, X. M. Yin, M. E. Bowden, Z. Z. Yang, H. Z. Guo, L. You, R. Guo, J. Wang, K. Ibrahim, J. S. Chen, A. Rusydi, J. L. Wang, S. A. Chambers and Y. G. Du, Adv. Funct. Mater., 2018, 28, 1803712 CrossRef.
- Q. Sun, Z. Wang, D. Wang, Z. Hong, M. Zhou and X. Li, Catal. Sci. Technol., 2018, 8, 4563–4575 RSC.
- M. C. Flemings, Annu. Rev. Mater. Sci., 1999, 29, 1–23 CrossRef CAS.
- C. Shi, C.-H. Yu and W. Zhang, Angew. Chem., Int. Ed., 2016, 55, 5798–5802 CrossRef CAS PubMed.
- W. Travis, E. N. K. Glover, H. Bronstein, D. O. Scanlon and R. G. Palgrave, Chem. Sci., 2016, 7, 4548–4556 RSC.
- C. J. Bartel, C. Sutton, B. R. Goldsmith, R. Ouyang, C. B. Musgrave, L. M. Ghiringhelli and M. Scheffler, Sci. Adv., 2019, 5, eaav0693 CrossRef CAS PubMed.
- D. H. Ji, S. L. Wang, X. Z. Ge, Q. Q. Zhang, C. M. Zhang, Z. W. Zeng and Y. Bai, Phys. Chem. Chem. Phys., 2017, 19, 17121–17127 RSC.
- S. P. Jiang, Int. J. Hydrogen Energy, 2019, 44, 7448–7493 CrossRef CAS.
- M. Askerka, Z. Li, M. Lempen, Y. Liu, A. Johnston, M. I. Saidaminov, Z. Zajacz and E. H. Sargent, J. Am. Chem. Soc., 2019, 141, 3682–3690 CrossRef CAS PubMed.
- P. K. Todd and J. R. Neilson, J. Am. Chem. Soc., 2019, 141, 1191–1195 CrossRef CAS PubMed.
- H. Lin, C. Zhou, Y. Tian, T. Siegrist and B. Ma, ACS Energy Lett., 2018, 3, 54–62 CrossRef CAS.
- F. A. Roghabadi, M. Alidaei, S. M. Mousavi, T. Ashjari, A. S. Tehrani, V. Ahmadi and S. M. Sadrameli, J. Mater. Chem. A, 2019, 7, 5898–5933 RSC.
- L. Etgar, Energy Environ. Sci., 2018, 11, 234–242 RSC.
- Y. Chen, Y. Sun, J. Peng, J. Tang, K. Zheng and Z. Liang, Adv. Mater., 2018, 30, 1703487 CrossRef PubMed.
- G. Grancini and M. K. Nazeeruddin, Nat. Rev. Mater., 2019, 4, 4–22 CrossRef CAS.
- Z. Shen, B. Qiao, Z. Xu, D. Song, D. Gao, P. Song, J. Cao, Q. Bai, Y. Wu and S. Zhao, Nanoscale, 2019, 11, 4008–4014 RSC.
- M. A. Gusowski, G. Dominiak-Dzik, P. Solarz, R. Lisiecki and W. Ryba-Romanowski, J. Alloys Compd., 2007, 438, 72–76 CrossRef CAS.
- F. U. Kosasih and C. Ducati, ChemSusChem, 2018, 11, 4193–4202 CrossRef CAS PubMed.
- Y. Zhu, W. Zhou and Z. Shao, Small, 2017, 13, 1603793 CrossRef.
- C. Moure and O. Peña, Prog. Solid State Chem., 2015, 43, 123–148 CrossRef CAS.
- Z. Xiao, Z. Song and Y. Yan, Adv. Mater., 2019, 31, 1803792 CrossRef CAS PubMed.
- A. Hossain, P. Bandyopadhyay and S. Roy, J. Alloys Compd., 2018, 740, 414–427 CrossRef CAS.
- A. E. Maughan, A. M. Ganose, M. M. Bordelon, E. M. Miller, D. O. Scanlon and J. R. Neilson, J. Am. Chem. Soc., 2016, 138, 8453–8464 CrossRef CAS PubMed.
- T. Tiittanen, S. Vasala and M. Karppinen, Chem. Commun., 2019, 55, 1722–1725 RSC.
- X. Liu, D. Yu, X. Song and H. Zeng, Small, 2018, 14, e1801460 CrossRef PubMed.
- N. Das, M. A. Nath, G. S. Thakur, M. Thirumal and A. K. Ganguli, J. Solid State Chem., 2015, 229, 97–102 CrossRef CAS.
- F. Igbari, Z. K. Wang and L. S. Liao, Adv. Energy Mater., 2019, 9, 1803150 CrossRef.
- Y. Mahor, W. J. Mir and A. Nag, J. Phys. Chem. C, 2019, 123, 15787–15793 CrossRef CAS.
- J. Bak, H. Bin Bae and S. Y. Chung, Nat. Commun., 2019, 10, 2713 CrossRef PubMed.
- G. Song, Y. Chen, G. Li and B. Gao, RSC Adv., 2019, 9, 2143–2151 RSC.
- M. R. Filip and F. Giustino, Proc. Natl. Acad. Sci. U. S. A., 2018, 115, 5397–5402 CrossRef CAS PubMed.
- B. Walker, G. H. Kim and J. Y. Kim, Adv. Mater., 2019, 31, 1807029 CrossRef PubMed.
- J. Pejchal, J. Barta, T. Trojek, R. Kucerkova, A. Beitlerova and M. Nikl, Radiat. Meas., 2019, 121, 26–31 CrossRef CAS.
- X. Liu, H. Gong, T. Wang, H. Guo, L. Song, W. Xia, B. Gao, Z. Jiang, L. Feng and J. He, Chem. – Asian J., 2018, 13, 528–535 CrossRef CAS PubMed.
- Z. Zhang, D. Schwanz, B. Narayanan, M. Kotiuga, J. A. Dura, M. Cherukara, H. Zhou, J. W. Freeland, J. Li, R. Sutarto, F. He, C. Wu, J. Zhu, Y. Sun, K. Ramadoss, S. S. Nonnenmann, N. Yu, R. Comin, K. M. Rabe, S. Sankaranarayanan and S. Ramanathan, Nature, 2018, 553, 68–72 CrossRef CAS PubMed.
- P. Yang, B. Tai, W. Wu, J. M. Zhang, F. Wang, S. Guan, W. Guo, Y. Lu and S. A. Yang, Phys. Chem. Chem. Phys., 2017, 19, 16189–16197 RSC.
- V. Celorrio, L. Calvillo, E. Dann, G. Granozzi, A. Aguadero, D. Kramer, A. E. Russell and D. J. Fermín, Catal. Sci. Technol., 2016, 6, 7231–7238 RSC.
- X. Wu, H. Li, K. Wang, X. Sun and L. Wang, RSC Adv., 2018, 8, 11095–11101 RSC.
- N. Chen, T. Cai, W. Li, K. Hills-Kimball, H. Yang, M. Que, Y. Nagaoka, Z. Liu, D. Yang, A. Dong, C. Y. Xu, R. Zia and O. Chen, ACS Appl. Mater. Interfaces, 2019, 11, 16855–16863 CrossRef CAS PubMed.
- W. Lee, S. Hong and S. Kim, J. Phys. Chem. C, 2019, 123, 2665–2672 CrossRef CAS.
- M. Pazoki, A. Röckert, M. J. Wolf, R. Imani, T. Edvinsson and J. Kullgren, J. Mater. Chem. A, 2017, 5, 23131–23138 RSC.
- J. Wu, K. Fujii, M. Yashima, A. Staykov, T. Akbay, T. Ishihara and J. A. Kilner, J. Mater. Chem. A, 2018, 6, 11819–11829 RSC.
- D. Guan, J. Zhou, Y. C. Huang, C. L. Dong, J. Q. Wang, W. Zhou and Z. Shao, Nat. Commun., 2019, 10, 3755 CrossRef PubMed.
- D. Zhou, D. Liu, G. Pan, X. Chen, D. Li, W. Xu, X. Bai and H. Song, Adv. Mater., 2017, 29, 1704149 CrossRef PubMed.
- R. Wang, M. Mujahid, Y. Duan, Z.-K. Wang, J. Xue and Y. Yang, Adv. Funct. Mater., 2019, 29, 1808843 CrossRef CAS.
- A. Bala and V. Kumar, J. Phys. Chem. C, 2019, 123, 6965–6969 CrossRef CAS.
- Y. Qiao, S. Li, W. Liu, M. Ran, H. Lu and Y. Yang, Nanomaterials, 2018, 8, 43 CrossRef PubMed.
- Q. Fan, G. V. Biesold-McGee, Q. Xu, S. Pan, J. Peng, J. Ma and Z. Lin, Angew. Chem., Int. Ed., 2020, 59, 1030 CrossRef CAS PubMed.
- K. Han, B. Yang, F. Hong, J. Chen, Y. Tang, L. Yang, Y. Sang, X. Xia, J. Guo, H. He, S. Yang and W. Deng, Angew. Chem., Int. Ed., 2018, 58, 2278–2283 Search PubMed.
- Y. Wu, X. M. Li and H. B. Zeng, ACS Energy Lett., 2019, 4, 673–681 CrossRef CAS.
- H. Dong, L.-D. Sun and C.-H. Yan, Chem. Soc. Rev., 2015, 44, 1608–1634 RSC.
- L. Zhou, T. Liu, J. Zheng, K. Yu, F. Yang, N. Wang, Y. Zuo, Z. Liu, C. Xue, C. Li, B. Cheng and Q. Wang, J. Phys. Chem. C, 2018, 122, 26825–26834 CrossRef CAS.
- G. Pan, X. Bai, W. Xu, X. Chen, D. Zhou, J. Zhu, H. Shao, Y. Zhai, B. Dong, L. Xu and H. Song, ACS Appl. Mater. Interfaces, 2018, 10, 39040–39048 CrossRef CAS PubMed.
- P. J. Deren and K. Lemanski, J. Lumin., 2014, 154, 62–67 CrossRef CAS.
- K. V. Dabre and S. J. Dhoble, J. Lumin., 2014, 150, 55–58 CrossRef CAS.
- A. A. Kumar, J. Singh, D. S. Rajput, A. Placke, A. Kumar and J. Kumar, Mater. Sci. Semicond. Process., 2018, 83, 83–88 CrossRef CAS.
- K. Ueda, T. Aoki, Y. Shimizu, F. Massuyeau and S. Jobic, Inorg. Chem., 2018, 57, 8718–8721 CrossRef CAS PubMed.
- N. Ding, Q. Liu, L. Wang, L. Zhang, Y. Feng and Q. Zhang, J. Mater. Sci.: Mater. Electron., 2018, 29, 4122–4127 CrossRef CAS.
- F. A. Rabuffetti, S. P. Culver, J. S. Lee and R. L. Brutchey, Nanoscale, 2014, 6, 2909–2914 RSC.
- C. Balamurugan, S. J. Song and D. W. Lee, Sens. Actuators, B, 2018, 272, 400–414 CrossRef CAS.
- R. B. Macedo Filho, A. Pedro Ayala and C. William de Araujo Paschoal, Appl. Phys. Lett., 2013, 102, 192902 CrossRef.
- Z. Zhou, L. Guo, H. Yang, Q. Liu and F. Ye, J. Alloys Compd., 2014, 583, 21–31 CrossRef CAS.
- J. Kang, Y. Yang, X. Qian, K. Xu, X. Cui, Y. Fang, V. Chandragiri, B. Kang, B. Chen, A. Stroppa, S. Cao, J. Zhang and W. Ren, IUCrJ, 2017, 4, 598–603 CrossRef CAS PubMed.
- Z. Wang, R. Gao, X. Deng, G. Chen, W. Cai and C. Fu, Ceram. Int., 2019, 45, 1825–1830 CrossRef CAS.
- P. Garcia-Munoz, C. Lefevre, D. Robert and N. Keller, Appl. Catal., B, 2019, 248, 120–128 CrossRef CAS.
- Y. Huang, J. Liu, D. Cao, Z. Liu, K. Ren, K. Liu, A. Tang, Z. Wang, L. Li, S. Qu and Z. Wang, Int. J. Hydrogen Energy, 2019, 44, 13242–13252 CrossRef CAS.
- B. Kucharczyk, J. Okal, W. Tylus, J. Winiarski and B. Szczygieł, Ceram. Int., 2019, 45, 2779–2788 CrossRef CAS.
- J. Bian, R. Su, Y. Yao, J. Wang, J. Zhou, F. Li, Z. L. Wang and C. Sun, ACS Appl. Energy Mater., 2019, 2, 923–931 CrossRef CAS.
- B. M. Pirzada, Pushpendra, R. K. Kunchala and B. S. Naidu, ACS Omega, 2019, 4, 2618–2629 CrossRef CAS PubMed.
- S. Liang, T. Xu, F. Teng, R. Zong and Y. Zhu, Appl. Catal., B, 2010, 96, 267–275 CrossRef CAS.
- X. Li, Y. Yin, C. Yao, S. Zuo, X. Lu, S. Luo and C. Ni, Particuology, 2016, 26, 66–72 CrossRef CAS.
- K. Kamonsuangkasem, S. Therdthianwong, A. Therdthianwong and N. Thammajak, Appl. Catal., B, 2017, 218, 650–663 CrossRef CAS.
- O. Pavlovska, I. Lutsyuk, A. Kondyr, Y. Zhydachevskyy, Y. Vakhula, A. Pieniążek and L. Vasylechko, Acta Phys. Pol., A, 2018, 133, 802–805 CrossRef CAS.
- F. A. Rabuffetti and R. L. Brutchey, Dalton Trans., 2014, 43, 14499–14513 RSC.
- Q. Choudhry, M. A. Khan, G. Nasar, A. Mahmood, M. Shahid, I. Shakir and M. F. Warsi, J. Magn. Magn. Mater., 2015, 393, 67–72 CrossRef CAS.
- X. Liu, C.-H. Yan and J. A. Capobianco, Chem. Soc. Rev., 2015, 44, 1299–1301 RSC.
- K. Lemański, B. Bondzior, D. Szymański and P. J. Dereń, New J. Chem., 2019, 43, 6242–6248 RSC.
- P. Niu, X. Liu, Z. Xie and W. Zhao, J. Lumin., 2018, 198, 34–39 CrossRef CAS.
- J. Duan, Y. Zhao, X. Yang, Y. Wang, B. He and Q. Tang, Adv. Energy Mater., 2018, 8, 1802346 CrossRef.
- B. Yang, Y. Wang, T. Wei, Y. Pan, E. Zhou, Z. Yuan, Y. Han, M. Li, X. Ling, L. Yin, X. Xie and L. Huang, Adv. Funct. Mater., 2018, 28, 1801782 CrossRef.
- J. Wu, D. Xiao and J. Zhu, Chem. Rev., 2015, 115, 2559–2595 CrossRef CAS PubMed.
- W. Lv, L. Li, M. Xu, J. Hong, X. Tang, L. Xu, Y. Wu, R. Zhu, R. Chen and W. Huang, Adv. Mater., 2019, 31, 1900682 CrossRef PubMed.
- H. Wang, J. Wang, Y. Pi, Q. Shao, Y. Tan and X. Huang, Angew. Chem., Int. Ed., 2019, 58, 2316–2320 CrossRef CAS PubMed.
- X. Sheng, Y. Liu, Y. Wang, Y. Li, X. Wang, X. Wang, Z. Dai, J. Bao and X. Xu, Adv. Mater., 2017, 29, 1700150 CrossRef PubMed.
- E. Cao, A. Wu, H. Wang, Y. Zhang, W. Hao and L. Sun, ACS Appl. Nano Mater., 2019, 2, 1541–1551 CrossRef CAS.
- L. Casillas-Trujillo, D. A. Andersson, B. Dorado, M. Nikl, K. E. Sickafus, K. J. McClellan and C. R. Stanek, Phys. Status Solidi B, 2014, 251, 2279–2286 CrossRef CAS.
- C. S. Lewis, H. Liu, J. Han, L. Wang, S. Yue, N. A. Brennan and S. S. Wong, Nanoscale, 2016, 8, 2129–2142 RSC.
- D. J. Daniel, O. Annalakshmi, U. Madhusoodanan and P. Ramasamy, J. Rare Earths, 2014, 32, 496–500 CrossRef CAS.
- B. J. Moon, S. J. Kim, S. Lee, A. Lee, H. Lee, D. S. Lee, T. W. Kim, S. K. Lee, S. Bae and S. H. Lee, Adv. Mater., 2019, 31, e1901716 CrossRef PubMed.
- H. Zhong, J. Wang, K. An, K. Fang and Y. Liu, Catal. Sci. Technol., 2019, 9, 3454–3468 RSC.
- K. Guo, R. Zhang, T. He, H. Kong and C. Deng, J. Rare Earths, 2016, 34, 1228–1234 CrossRef CAS.
- H. Shi, X. Li, J. Xia, X. Lu, S. Zuo, S. Luo and C. Yao, J. Inorg. Organomet. Polym. Mater., 2017, 27, S166–S172 CrossRef.
- Q. S. Hu, Z. Li, Z. F. Tan, H. B. Song, C. Ge, G. D. Niu, J. T. Han and J. Tang, Adv. Opt. Mater., 2018, 6, 1700864 CrossRef.
- L. Huang, Q. Gao, L. D. Sun, H. Dong, S. Shi, T. Cai, Q. Liao and C. H. Yan, Adv. Mater., 2018, 30, e1800596 CrossRef PubMed.
- S. Shi, L. D. Sun, Y. X. Xue, H. Dong, K. Wu, S. C. Guo, B. T. Wu and C. H. Yan, Nano Lett., 2018, 18, 2964–2969 CrossRef CAS PubMed.
- S. K. Saroj, P. Rawat, M. Gupta, G. V. Prakash and R. Nagarajan, Eur. J. Inorg. Chem., 2018, 4826–4833, DOI:10.1002/ejic.201801123.
- A. Heuer-Jungemann, N. Feliu, I. Bakaimi, M. Hamaly, A. Alkilany, I. Chakraborty, A. Masood, M. F. Casula, A. Kostopoulou, E. Oh, K. Susumu, M. H. Stewart, I. L. Medintz, E. Stratakis, W. J. Parak and A. G. Kanaras, Chem. Rev., 2019, 119, 4819–4880 CrossRef CAS PubMed.
- D. Preziosi, L. Lopez-Mir, X. Li, T. Cornelissen, J. H. Lee, F. Trier, K. Bouzehouane, S. Valencia, A. Gloter, A. Barthelemy and M. Bibes, Nano Lett., 2018, 18, 2226–2232 CrossRef CAS PubMed.
- P. Shikha, T. S. Kang and B. S. Randhawa, J. Alloys Compd., 2015, 625, 336–345 CrossRef CAS.
- J. M. Hodges, J. R. Morse, J. L. Fenton, J. D. Ackerman, L. T. Alameda and R. E. Schaak, Chem. Mater., 2017, 29, 106–119 CrossRef CAS.
- M. Afqir, M. Elaatmani, A. Zegzouti, A. Oufakir and M. Daoud, J. Mater. Sci.: Mater. Electron., 2019, 30, 5495–5502 CrossRef CAS.
- P. Rawat, S. K. Saroj, M. Gupta, G. V. Prakash and R. Nagarajan, J. Fluorine Chem., 2017, 200, 1–7 CrossRef CAS.
- Y. Tao, L. Wu, X. Zhao, X. Chen, R. Li, M. Chen, D. Zhang, G. Li and H. Li, ACS Appl. Mater. Interfaces, 2019, 11, 25967–25975 CrossRef CAS PubMed.
- W. Li, S. Wang and J. Li, Chem. – Asian J., 2019, 14, 2815–2821 CAS.
- D. Chen and X. Chen, J. Mater. Chem. C, 2019, 7, 1413–1446 RSC.
- M. Imran, V. Caligiuri, M. Wang, L. Goldoni, M. Prato, R. Krahne, L. De Trizio and L. Manna, J. Am. Chem. Soc., 2018, 140, 2656–2664 CrossRef CAS PubMed.
- S. E. Creutz, E. N. Crites, M. C. De Siena and D. R. Gamelin, Chem. Mater., 2018, 30, 4887–4891 CrossRef CAS.
- X. Li, Y. Wu, S. Zhang, B. Cai, Y. Gu, J. Song and H. Zeng, Adv. Funct. Mater., 2016, 26, 2435–2445 CrossRef CAS.
- Z. Quan, P. Yang, C. Li, J. Yang, D. Yang, Y. Jin, H. Lian, H. Li and J. Lin, J. Phys. Chem. C, 2009, 113, 4018–4025 CrossRef CAS.
- Y.-P. Du, Y.-W. Zhang, Z.-G. Yan, L.-D. Sun, S. Gao and C.-H. Yan, Chem. – Asian J., 2007, 2, 965–974 CrossRef CAS.
- J. E. Roberts, J. Am. Chem. Soc., 1961, 83, 1087–1088 CrossRef CAS.
- J. Zhang, Y. Yang, H. Deng, U. Farooq, X. Yang, J. Khan, J. Tang and H. Song, ACS Nano, 2017, 11, 9294–9302 CrossRef CAS PubMed.
- B. Yang, J. Chen, F. Hong, X. Mao, K. Zheng, S. Yang, Y. Li, T. Pullerits, W. Deng and K. Han, Angew. Chem., Int. Ed., 2017, 56, 12471–12475 CrossRef CAS PubMed.
- X. Yi, R. Li, H. Zhu, J. Gao, W. You, Z. Gong, W. Guo and X. Chen, J. Mater. Chem. C, 2018, 6, 2069–2076 RSC.
- E. Devi, B. J. Kalaiselvi, K. Madhan, D. Vanidha, S. S. Meena and R. Kannan, J. Appl. Phys., 2018, 124, 084102 CrossRef.
- S.-X. Chen, Y. Wang, A.-P. Jia, H.-H. Liu, M.-F. Luo and J.-Q. Lu, Appl. Surf. Sci., 2014, 307, 178–188 CrossRef CAS.
- S. Manzoor and S. Husain, J. Appl. Phys., 2018, 124, 065110 CrossRef.
- J. Li, R. Hu, J. Zhang, W. Meng, Y. Du, Y. Si and Z. Zhang, Fuel, 2016, 178, 148–154 CrossRef CAS.
- M. Rakibuddin, H. Kim and M. E. Khan, Appl. Surf. Sci., 2018, 452, 400–412 CrossRef CAS.
- M. A. Gomes, A. S. Lima, K. I. B. Eguiluz and G. R. Salazar-Banda, J. Mater. Sci., 2016, 51, 4709–4727 CrossRef CAS.
- D. Chen, G. Fang, X. Chen, L. Lei, J. Zhong, Q. Mao, S. Zhou and J. Li, J. Mater. Chem. C, 2018, 6, 8990–8998 RSC.
- K. Di, X. Li, X. Jing, S. Yao and J. Yan, J. Alloys Compd., 2016, 661, 435–440 CrossRef CAS.
- G. Wang, P. Wang, H.-K. Luo and T. S. A. Hor, Chem. – Asian J., 2014, 9, 1854–1859 CrossRef CAS PubMed.
- O. B. Pavlovska, L. O. Vasylechko, I. V. Lutsyuk, N. M. Koval, Y. A. Zhydachevskii and A. Pieniazek, Nanoscale Res. Lett., 2017, 12, 153 CrossRef CAS PubMed.
- L. Chang, L. Wang, L. You, Z. Yang, A. Abdelsamie, Q. Zhang, Y. Zhou, L. Gu, S. A. Chambers and J. Wang, ACS Appl. Mater. Interfaces, 2019, 11, 16191–16197 CrossRef CAS PubMed.
- L. Liu, W. Wang, Y. Yao, X. Wu, S. Lu and Y. Li, Appl. Surf. Sci., 2018, 439, 1034–1039 CrossRef CAS.
- W. Zhang, H. Wang, K. Guan, Z. Wei, X. Zhang, J. Meng, X. Liu and J. Meng, ACS Appl. Mater. Interfaces, 2019, 11, 26830–26841 CrossRef CAS PubMed.
- Y. Zhu, W. Zhou, Y. Zhong, Y. Bu, X. Chen, Q. Zhong, M. Liu and Z. Shao, Adv. Energy Mater., 2017, 7, 1602122 CrossRef.
- X. Zhang, Y. Gong, S. Li and C. Sun, ACS Catal., 2017, 7, 7737–7747 CrossRef CAS.
- J. Schwarzkopf, D. Braun, M. Hanke, R. Uecker and M. Schmidbauer, Front. Mater., 2017, 4, 26 CrossRef.
- N. Tsvetkov, Q. Lu, L. Sun, E. J. Crumlin and B. Yildiz, Nat. Mater., 2016, 15, 1010–1016 CrossRef CAS PubMed.
- J. Hwang, Z. Feng, N. Charles, X. R. Wang, D. Lee, K. A. Stoerzinger, S. Muy, R. R. Rao, D. Lee, R. Jacobs, D. Morgan and Y. Shao-Horn, Mater. Today, 2019, 31, 100–118 CrossRef CAS.
- T. Katayama, A. Chikamatsu, Y. Hirose, M. Minohara, H. Kumigashira, I. Harayama, D. Sekiba and T. Hasegawa, J. Mater. Chem. C, 2018, 6, 3445–3450 RSC.
- H. Han, D. Kim, S. Chae, J. Park, S. Y. Nam, M. Choi, K. Yong, H. J. Kim, J. Son and H. M. Jang, Nanoscale, 2018, 10, 13261–13269 RSC.
- E. Bi, H. Chen, F. Xie, Y. Wu, W. Chen, Y. Su, A. Islam, M. Gratzel, X. Yang and L. Han, Nat. Commun., 2017, 8, 15330 CrossRef CAS PubMed.
- A. K. Jena, A. Kulkarni, Y. Sanehira, M. Ikegami and T. Miyasaka, Chem. Mater., 2018, 30, 6668–6674 CrossRef CAS.
- K. Wang, L. Zheng, T. Zhu, X. Yao, C. Yi, X. Zhang, Y. Cao, L. Liu, W. Hu and X. Gong, Nano Energy, 2019, 61, 352–360 CrossRef CAS.
- Y. Xiang, Z. Ma, J. Zhuang, H. Lu, C. Jia, J. Luo, H. Li and X. Cheng, J. Phys. Chem. C, 2017, 121, 20150–20157 CrossRef CAS.
- R. Meng, X. Feng, Y. Yang, X. Lv, J. Cao and Y. Tang, ACS Appl. Mater. Interfaces, 2019, 11, 13273–13278 CrossRef CAS PubMed.
- P. Song, P. Zhu and C. Zhang, J. Alloys Compd., 2018, 731, 1009–1013 CrossRef CAS.
- G. E. Eperon, G. M. Paternò, R. J. Sutton, A. Zampetti, A. A. Haghighirad, F. Cacialli and H. J. Snaith, J. Mater. Chem. A, 2015, 3, 19688–19695 RSC.
- M. Kulbak, D. Cahen and G. Hodes, J. Phys. Chem. Lett., 2015, 6, 2452–2456 CrossRef CAS PubMed.
- R. E. Beal, D. J. Slotcavage, T. Leijtens, A. R. Bowring, R. A. Belisle, W. H. Nguyen, G. F. Burkhard, E. T. Hoke and M. D. McGehee, J. Phys. Chem. Lett., 2016, 7, 746–751 CrossRef CAS PubMed.
- Z. Zhang, D. Li, W. Shi, Y. Liu, Y. Zhang, Y. Liu, H. Gao and Y. Mao, Nanoscale Res. Lett., 2018, 13, 262 CrossRef PubMed.
- L. Zhang, L. Dong, B. Shao, S. Zhao and H. You, Dalton Trans., 2019, 48, 11460–11468 RSC.
- Z. Sun, C. Ma, M. Liu, J. Cui, L. Lu, J. Lu, X. Lou, L. Jin, H. Wang and C. L. Jia, Adv. Mater., 2017, 29, 1604427 CrossRef PubMed.
- G. Wang, J. L. Li, X. Zhang, Z. M. Fan, F. Yang, A. Feteira, D. Zhou, D. C. Sinclair, T. Ma, X. L. Tan, D. W. Wang and I. M. Reaney, Energy Environ. Sci., 2019, 12, 582–588 RSC.
- X. Hao, Y. Wang, L. Zhang, L. Zhang and S. An, Appl. Phys. Lett., 2013, 102, 163903 CrossRef.
- Chitra and K. C. Singh, J. Mater. Sci.: Mater. Electron., 2018, 29, 17630–17637 CrossRef CAS.
- F. Kousar, S. Nazim, M. F. Warsi, M. A. Khan, M. N. Ashiq, Z. A. Gilani, I. Shakir and A. Wadood, J. Alloys Compd., 2015, 629, 315–318 CrossRef CAS.
- T.-X. Zhao, J.-H. Qiu, M.-G. Ma, Z.-H. Chen, C.-B. Li and X.-G. Jia, J. Nanosci. Nanotechnol., 2019, 19, 5661–5666 CrossRef CAS PubMed.
- Z.-H. Chen, Z.-W. Li, J.-H. Qiu, T.-X. Zhao, K.-Q. Zhu, J.-N. Ding, W.-Q. Zhu and J.-J. Xu, Phys. Status Solidi A, 2018, 215, 1700417 CrossRef.
- M. Chen, Z. Xu, R. Chu, Z. Wang, S. Gao, G. Yu, W. Li, S. Gong and G. Li, Mater. Res. Bull., 2014, 59, 305–310 CrossRef CAS.
- M. Kroutvar, Y. Ducommun, D. Heiss, M. Bichler, D. Schuh, G. Abstreiter and J. J. Finley, Nature, 2004, 432, 81–84 CrossRef CAS PubMed.
- W. Wu, M. Chen, Y. Ding and C. Liu, J. Alloys Compd., 2014, 588, 496–501 CrossRef CAS.
- S. Zhang, F. Li, X. Jiang, J. Kim, J. Luo and X. Geng, Prog. Mater. Sci., 2015, 68, 1–66 CrossRef CAS PubMed.
- J. Roedel, W. Jo, K. T. P. Seifert, E.-M. Anton, T. Granzow and D. Damjanovic, J. Am. Ceram. Soc., 2009, 92, 1153–1177 CrossRef CAS.
- A. Rai and A. K. Thakur, J. Alloys Compd., 2017, 695, 3579–3588 CrossRef CAS.
- K. Guo, Q. Mou, T. He, H. Kong and R. Zhang, J. Mater. Sci.: Mater. Electron., 2016, 28, 1971–1975 CrossRef.
- A. Pelaiz-Barranco, J. D. S. Guerra, F. Calderon-Pinar, C. Arago, O. Garcia-Zaldivar, R. Lopez-Noda, J. A. Gonzalo and J. A. Eiras, J. Mater. Sci., 2009, 44, 204–211 CrossRef CAS.
- X. Xiao, M. Widenmeyer, W. Xie, T. Zou, S. Yoon, M. Scavini, S. Checchia, Z. Zhong, P. Hansmann, S. Kilper, A. Kovalevsky and A. Weidenkaff, Phys. Chem. Chem. Phys., 2017, 19, 13469–13480 RSC.
- P. Kaya, G. Gregori, F. Baiutti, P. Yordanov, Y. E. Suyolcu, G. Cristiani, F. Wrobel, E. Benckiser, B. Keimer, P. A. van Aken, H. U. Habermeier, G. Logvenov and J. Maier, ACS Appl. Mater. Interfaces, 2018, 10, 22786–22792 CrossRef CAS PubMed.
- Y. Kinemuchi, K.-i. Mimura and K. Kato, J. Electron. Mater., 2015, 44, 1773–1776 CrossRef CAS.
- T. Reimann and J. Toepfer, J. Alloys Compd., 2017, 699, 788–795 CrossRef CAS.
- Y. Kinemuchi, K.-I. Mimura, A. Towata and K. Kato, J. Electron. Mater., 2014, 43, 2011–2016 CrossRef CAS.
- H. H. Kumar, C. M. Lonkar and K. Balasubramanian, Appl. Phys. A: Mater. Sci. Process., 2017, 123, 615 CrossRef.
- A. Kumar, V. V. B. Prasad, K. C. J. Raju and A. R. James, J. Alloys Compd., 2016, 654, 95–102 CrossRef CAS.
- A. Mahmood, M. F. Warsi, M. N. Ashiq and M. Ishaq, J. Magn. Magn. Mater., 2013, 327, 64–70 CrossRef CAS.
- S. Das, R. C. Sahoo, K. P. Bera and T. K. Nath, J. Magn. Magn. Mater., 2018, 451, 226–234 CrossRef CAS.
- R. Jana, V. Pareek, P. Khatua, P. Saha, A. Chandra and G. D. Mukherjee, J. Phys.: Condens. Matter, 2018, 30, 335401 CrossRef.
- M. Azhar Khan, K. Khan, A. Mahmood, G. Murtaza, M. N. Akhtar, I. Ali, M. Shahid, I. Shakir and M. Farooq Warsi, Ceram. Int., 2014, 40, 13211–13216 CrossRef CAS.
- A. Aziz, E. Ahmed, M. N. Ashiq, M. A. Khan, N. Karamat and I. Ali, Prog. Nat. Sci.: Mater. Int., 2016, 26, 325–333 CrossRef CAS.
- A. Bahari, A. Ramzannezhad, D. Shajari and H. Najafi, Int. J. Mod. Phys. B, 2017, 31, 1750015 CrossRef CAS.
- A. Aziz, E. Ahmed, I. Ali, M. Athar, M. F. Ehsan and M. N. Ashiq, J. Electron. Mater., 2015, 44, 4300–4307 CrossRef CAS.
- S. Dutta, A. Antony Jeyaseelan and S. Sruthi, Thin Solid Films, 2014, 562, 190–194 CrossRef CAS.
- E. E. Ateia and F. S. Soliman, Mater. Sci. Eng., B, 2019, 244, 29–37 CrossRef CAS.
- C. A. Diaz-Moreno, Y. Ding, J. Portelles, J. Heiras, A. Hurtado Macias, A. Syeed, A. Paez, C. Li, J. Lopez and R. Wicker, Ceram. Int., 2018, 44, 4727–4733 CrossRef CAS.
- X. Zhang, Y. Zhang, X. Zhang, W. Yin, Y. Wang, H. Wang, M. Lu, Z. Li, Z. Gu and W. W. Yu, J. Mater. Chem. C, 2018, 6, 10101–10105 RSC.
- G. M. Arumugam, C. Xu, S. K. Karunakaran, Z. Shi, F. Qin, C. Zhu and F. Chen, J. Mater. Chem. C, 2018, 6, 12537–12546 RSC.
- Z. Gong, W. Zheng, Y. Gao, P. Huang, D. Tu, R. Li, J. Wei, W. Zhang, Y. Zhang and X. Chen, Angew. Chem., Int. Ed., 2019, 58, 6943–6947 CrossRef CAS PubMed.
- J. Ma, H. Wu, J. Qiu, J. Wang, Q. Wang, Y. Yang, D. Zhou and J. Han, J. Mater. Chem. C, 2019, 7, 3751–3755 RSC.
- P. D. Belsare, C. P. Joshi, S. V. Moharil and S. K. Omanwar, AIP Conf. Proc., 2015, 1675, 020015 CrossRef.
- T. J. Milstein, D. M. Kroupa and D. R. Gamelin, Nano Lett., 2018, 18, 3792–3799 CrossRef CAS PubMed.
- J. Zhong, D. Chen, S. Yuan, M. Liu, Y. Yuan, Y. Zhu, X. Li and Z. Ji, Inorg. Chem., 2018, 57, 8978–8987 CrossRef CAS PubMed.
- M. Zeng, S. Singh, Z. Hens, J. Liu, F. Artizzu and R. Van Deun, J. Mater. Chem. C, 2019, 7, 2014–2021 RSC.
- H. Wang, X. Hong, R. Han, J. Shi, Z. Liu, S. Liu, Y. Wang and Y. Gan, Sci. Rep., 2015, 5, 17088 CrossRef CAS PubMed.
- E.-H. Song, S. Ding, M. Wu, S. Ye, F. Xiao, G.-P. Dong and Q.-Y. Zhang, J. Mater. Chem. C, 2013, 1, 4209 RSC.
- Q. Li, Y. Liu, P. Chen, J. Hou, Y. Sun, G. Zhao, N. Zhang, J. Zou, J. Xu, Y. Fang and N. Dai, J. Phys. Chem. C, 2018, 122, 29044–29050 CrossRef CAS.
- R. T. Wegh, H. Donker, K. D. Oskam and A. Meijerink, Science, 1999, 283, 663–666 CrossRef CAS PubMed.
- W. Zheng, P. Huang, Z. Gong, D. Tu, J. Xu, Q. Zou, R. Li, W. You, J.-C. G. Bünzli and X. Chen, Nat. Commun., 2018, 9, 3462 CrossRef PubMed.
- X. Luo, T. Ding, X. Liu, Y. Liu and K. Wu, Nano Lett., 2019, 19, 338–341 CrossRef CAS PubMed.
- X. Li, S. Duan, H. Liu, G. Chen, Y. Luo and H. Agren, J. Phys. Chem. Lett., 2019, 10, 487–492 CrossRef PubMed.
- W. J. Mir, Y. Mahor, A. Lohar, M. Jagadeeswararao, S. Das, S. Mahamuni and A. Nag, Chem. Mater., 2018, 30, 8170–8178 CrossRef CAS.
- D. Zhang, W. Zhou, Q. Liu and Z. Xia, ACS Appl. Mater. Interfaces, 2018, 10, 27875–27884 CrossRef CAS PubMed.
- J. Sang, J. Zhou, J. Zhang, H. Zhou, H. Li, Z. Ci, S. Peng and Z. Wang, ACS Appl. Mater. Interfaces, 2019, 11, 20150–20156 CrossRef CAS PubMed.
- Y. Zhai, X. Bai, G. Pan, J. Zhu, H. Shao, B. Dong, L. Xu and H. Song, Nanoscale, 2019, 11, 2484–2491 RSC.
- X. Han, E. Song, B. Zhou and Q. Zhang, J. Mater. Chem. C, 2019, 7, 8226–8235 RSC.
- D. M. Kroupa, J. Y. Roh, T. J. Milstein, S. E. Creutz and D. R. Gamelin, ACS Energy Lett., 2018, 3, 2390–2395 CrossRef CAS.
- Y. Liu, G. Pan, R. Wang, H. Shao, H. Wang, W. Xu, H. Cui and H. Song, Nanoscale, 2018, 10, 14067–14072 RSC.
- G. M. Arumugam, C. Xu, S. K. Karunakaran, Z. Shi, C. Zhu, M. Wei and Q. Feifei, Appl. Phys. Lett., 2018, 112, 054104 CrossRef.
- M. Suta, W. Urland, C. Daul and C. Wickleder, Phys. Chem. Chem. Phys., 2016, 18, 13196–13208 RSC.
- J. Wang, F. Wang, C. Wang, Z. Liu and X. Liu, Angew. Chem., Int. Ed., 2011, 50, 10369–10372 CrossRef CAS PubMed.
- J. J. Schuyt and G. V. M. Williams, J. Lumin., 2018, 204, 472–479 CrossRef CAS.
- M. Ding, M. Xu, C. Lu, J. Xi, Z. Ji and D. Chen, J. Alloys Compd., 2017, 721, 531–537 CrossRef CAS.
- D. K. Singh and J. Manam, J. Mater. Sci.: Mater. Electron., 2016, 27, 10371–10381 CrossRef CAS.
- Q. Sun, S. Wang, B. Devakumar, L. Sun, J. Liang and X. Huang, RSC Adv., 2019, 9, 3303–3310 RSC.
- T. Xie, L. Zhang, Y. Guo, X. Wang and Y. Wang, Ceram. Int., 2019, 45, 3502–3509 CrossRef CAS.
- G. Kakavelakis, E. Gagaoudakis, K. Petridis, V. Petromichelaki, V. Binas, G. Kiriakidis and E. Kymakis, ACS Sens., 2018, 3, 135–142 CrossRef CAS PubMed.
- J. Casanova-Chafer, R. Garcia-Aboal, P. Atienzar and E. Llobet, Sensors, 2019, 19, 4563 CrossRef PubMed.
- K. Brintakis, E. Gagaoudakis, A. Kostopoulou, V. Faka, A. Argyrou, V. Binas, G. Kiriakidis and E. Stratakis, Nanoscale Adv., 2019, 1, 2699–2706 RSC.
- C. R. Michel, M. A. Lopez-Alvarez, A. H. Martinez-Preciado and G. G. Carbajal-Arizaga, J. Sens., 2019, 5682645 Search PubMed.
- Y. Chen, D. Wang, H. Qin, H. Zhang, Z. Zhang, G. Zhou, C. Gao and J. Hu, J. Rare Earths, 2019, 37, 80–87 CrossRef CAS.
- C. Wang, H. Lin, X. Xiang, Y. Cheng, Q. Huang, Y. Gao, X. Cui and Y. Wang, J. Mater. Chem. C, 2018, 6, 9964–9971 RSC.
- X. S. Niu, W. M. Du, W. P. Du and K. Jiang, Rare Met. Mater. Eng., 2005, 34, 124–127 CAS.
- C. R. Stanek, M. R. Levy, K. J. McClellan, B. P. Uberuaga and R. W. Grimes, Phys. Status Solidi B, 2005, 242, R113–R115 CrossRef CAS.
- J. Druce, H. Téllez, M. Burriel, M. D. Sharp, L. J. Fawcett, S. N. Cook, D. S. McPhail, T. Ishihara, H. H. Brongersma and J. A. Kilner, Energy Environ. Sci., 2014, 7, 3593–3599 RSC.
- M. Kubicek, A. Limbeck, T. Frömling, H. Hutter and J. r. Fleig, J. Electrochem. Soc., 2011, 158, B727 CrossRef CAS.
- M. Haneda and H. Hamada, C. R. Chim., 2016, 19, 1254–1265 CrossRef CAS.
- Z. Chen, Q. Jiang, F. Cheng, J. Tong, M. Yang, Z. Jiang and C. Li, J. Mater. Chem. A, 2019, 7, 6099–6112 RSC.
- N. Tachibana, H. Kobayashi, S. Somekawa and K. Shimanoe, Electrochemistry, 2019, 87, 193–195 CrossRef CAS.
- H. Wang, L. Yan, T. Nakotte, W. Xu, M. Zhou, D. Ding and H. Luo, Inorg. Chem. Front., 2019, 6, 1029–1039 RSC.
- B. Hua, M. Li, Y.-Q. Zhang, Y.-F. Sun and J.-L. Luo, Adv. Energy Mater., 2017, 7, 1700666 CrossRef.
- B. J. Kim, E. Fabbri, D. F. Abbott, X. Cheng, A. H. Clark, M. Nachtegaal, M. Borlaf, I. E. Castelli, T. Graule and T. J. Schmidt, J. Am. Chem. Soc., 2019, 141, 5231–5240 CrossRef CAS PubMed.
- M. Li, A. R. Insani, L. Zhuang, Z. Wang, A. U. Rehman, L. X. Liu and Z. Zhu, J. Colloid Interface Sci., 2019, 553, 813–819 CrossRef CAS PubMed.
- Y. Tong, Y. Guo, P. Chen, H. Liu, M. Zhang, L. Zhang, W. Yan, W. Chu, C. Wu and Y. Xie, Chem, 2017, 3, 812–821 CAS.
- A. Grimaud, K. J. May, C. E. Carlton, Y. L. Lee, M. Risch, W. T. Hong, J. Zhou and Y. Shao-Horn, Nat. Commun., 2013, 4, 2439 CrossRef PubMed.
- Y. Duan, S. Sun, S. Xi, X. Ren, Y. Zhou, G. Zhang, H. Yang, Y. Du and Z. J. Xu, Chem. Mater., 2017, 29, 10534–10541 CrossRef CAS.
- S. She, J. Yu, W. Tang, Y. Zhu, Y. Chen, J. Sunarso, W. Zhou and Z. Shao, ACS Appl. Mater. Interfaces, 2018, 10, 11715–11721 CrossRef CAS PubMed.
- Z. Liu, Y. Sun, X. Wu, C. Hou, Z. Geng, J. Wu, K. Huang, L. Gao and S. Feng, CrystEngComm, 2019, 21, 1534–1538 RSC.
- X. Miao, L. Wu, Y. Lin, X. Yuan, J. Zhao, W. Yan, S. Zhou and L. Shi, Chem. Commun., 2019, 55, 1442–1445 RSC.
- L. Wang, K. A. Stoerzinger, L. Chang, X. Yin, Y. Li, C. S. Tang, E. Jia, M. E. Bowden, Z. Yang, A. Abdelsamie, L. You, R. Guo, J. Chen, A. Rusydi, J. Wang, S. A. Chambers and Y. Du, ACS Appl. Mater. Interfaces, 2019, 11, 12941–12947 CrossRef CAS PubMed.
- Y. Zhu, L. Zhang, B. Zhao, H. Chen, X. Liu, R. Zhao, X. Wang, J. Liu, Y. Chen and M. Liu, Adv. Funct. Mater., 2019, 1901783, DOI:10.1002/adfm.201901783.
- Z. Chen, T. Fan, Q. Zhang, J. He, H. Fan, Y. Sun, X. Yi and J. Li, J. Colloid Interface Sci., 2019, 536, 105–111 CrossRef CAS PubMed.
- Y. Wang, S. Jin, G. Pan, Z. Li, L. Chen, G. Liu and X. Xu, J. Mater. Chem. A, 2019, 7, 5702–5711 RSC.
- G. P. Wheeler and K.-S. Choi, ACS Energy Lett., 2017, 2, 2378–2382 CrossRef CAS.
- A. Krukowska, G. Trykowski, W. Lisowski, T. Klimczuk, M. J. Winiarski and A. Zaleska-Medynska, J. Catal., 2018, 364, 371–381 CrossRef CAS.
- A. Krukowska, M. J. Winiarski, J. Strychalska-Nowak, T. Klimczuk, W. Lisowski, A. Mikolajczyk, H. P. Pinto, T. Puzyn, T. Grzyb and A. Zaleska-Medynska, Appl. Catal., B, 2018, 224, 451–468 CrossRef CAS.
- J. Xu, C. Sun, Z. Wang, Y. Hou, Z. Ding and S. Wang, Chemistry, 2018, 24, 18512–18517 CrossRef CAS PubMed.
- H. Chen, X. Sun and X. Xu, Electrochim. Acta, 2017, 252, 138–146 CrossRef CAS.
- Y. Absalan, I. G. Bratchikova and O. V. Kovalchukova, J. Mol. Liq., 2018, 268, 882–894 CrossRef CAS.
- M. Baladi, F. Soofivand, M. Valian and M. Salavati-Niasari, Ultrason. Sonochem., 2019, 57, 172–184 CrossRef CAS PubMed.
- Y. Soltanabadi, M. Jourshabani and Z. Shariatinia, Sep. Purif. Technol., 2018, 202, 227–241 CrossRef CAS.
- F. Lin, J. Shao, H. Tang, Y. Li, Z. Wang, G. Chen, D. Yuan and K. Cen, Appl. Surf. Sci., 2019, 479, 234–246 CrossRef CAS.
- Q. Wang and L. Ma, New J. Chem., 2019, 43, 2974–2980 RSC.
- C. Zhou, X. Liu, C. Wu, Y. Wen, Y. Xue, R. Chen, Z. Zhang, B. Shan, H. Yin and W. G. Wang, Phys. Chem. Chem. Phys., 2014, 16, 5106–5112 RSC.
- X. Li, C. Tang, M. Ai, L. Dong and Z. Xu, Chem. Mater., 2010, 22, 4879–4889 CrossRef CAS.
- S. Zhao, Y. Wang, L. Wang and Y. Jin, Inorg. Chem. Front., 2017, 4, 994–1002 RSC.
- A. Garbujo, M. Pacella, M. M. Natile, M. Guiotto, J. Fabro, P. Canu and A. Glisenti, Appl. Catal., A, 2017, 544, 94–107 CrossRef CAS.
- Y. Lu, K. A. Michalow, S. K. Matam, A. Winkler, A. E. Maegli, S. Yoon, A. Heel, A. Weidenkaff and D. Ferri, Appl. Catal., B, 2014, 144, 631–643 CrossRef CAS.
- R. Hu, Y. Bai, H. Du, H. Zhang, Y. Du, J. Zhang and Q. Zhou, J. Rare Earths, 2015, 33, 1284–1292 CrossRef CAS.
- Y. Sim, J. Yoo, J.-M. Ha and J. C. Jung, J. Energy Chem., 2019, 35, 1–8 CrossRef.
- S. Wang, S. Du, W. Tang, S. Hoang, X. Lu, W. Xiao, B. Zhang, J. Weng, E. Schneer, Y. Guo, J. Ding, Z. Zhang and P.-X. Gao, ChemCatChem, 2018, 10, 2184–2189 CrossRef CAS.
- M. Tang, K. Liu, D. M. Roddick and M. Fan, J. Catal., 2018, 368, 38–52 CrossRef CAS.
- T. Yabe, Y. Kamite, K. Sugiura, S. Ogo and Y. Sekine, J. CO2 Util., 2017, 20, 156–162 CrossRef CAS.
- M. Pudukudy, Z. Yaakob and M. S. Takriff, Energy Convers. Manage., 2016, 126, 302–315 CrossRef CAS.
- A. G. Dedov, A. S. Loktev, D. A. Komissarenko, K. V. Parkhomenko, A. C. Roger, O. A. Shlyakhtin, G. N. Mazo and I. I. Moiseev, Fuel Process. Technol., 2016, 148, 128–137 CrossRef CAS.
- J. Kuc, M. Neumann, M. Armbruester, S. Yoon, Y. Zhang, R. Erni, A. Weidenkaff and S. K. Matam, Catal. Sci. Technol., 2016, 6, 1455–1468 RSC.
- K. Okura, K. Miyazaki, H. Muroyama, T. Matsui and K. Eguchi, RSC Adv., 2018, 8, 32102–32110 RSC.
- D. Meng, H. Guo, Z. Cui, C. Ma, J. Zhao, J. Lu, H. Xu, Z. Wang, X. Hu, Z. Fu, R. Peng, J. Guo, X. Zhai, G. J. Brown, R. Knize and Y. Lu, Proc. Natl. Acad. Sci. U. S. A., 2018, 115, 2873–2877 CrossRef CAS PubMed.
- B.-X. Wang, S. Rosenkranz, X. Rui, J. Zhang, F. Ye, H. Zheng, R. F. Klie, J. F. Mitchell and D. Phelan, Phys. Rev. Mater., 2018, 2, 064404 CrossRef CAS.
- S. Middey, J. Chakhalian, P. Mahadevan, J. W. Freeland, A. J. Millis and D. D. Sarma, Annu. Rev. Mater. Res., 2016, 46, 305–334 CrossRef CAS.
- K. Yoshimatsu, J. Ishimaru, K. Watarai, K. Yamamoto, Y. Hirata, H. Wadati, Y. Takeda, K. Horiba, H. Kumigashira, O. Sakata and A. Ohtomo, Phys. Rev. B, 2019, 99, 235129 CrossRef CAS.
- R. Dusad, F. K. K. Kirschner, J. C. Hoke, B. R. Roberts, A. Eyal, F. Flicker, G. M. Luke, S. J. Blundell and J. C. S. Davis, Nature, 2019, 571, 234–239 CrossRef CAS PubMed.
- Q. Chen, S. Fan, K. M. Taddei, M. B. Stone, A. I. Kolesnikov, J. Cheng, J. L. Musfeldt, H. Zhou and A. A. Aczel, J. Am. Chem. Soc., 2019, 141, 9928–9936 CrossRef CAS PubMed.
- E. Rozenberg, M. I. Tsindlekht, I. Felner, E. Sominski, A. Gedanken and Y. M. Mukovskii, IEEE Trans. Magn., 2007, 43, 3052–3054 CAS.
- R. M. Khafagy and E. H. El-khawas, J. Alloys Compd., 2014, 606, 288–297 CrossRef CAS.
- P. Veverka, O. Kaman, K. Knizek, P. Novak, M. Marysko and Z. Jirak, J. Phys.: Condens. Matter, 2017, 29, 035803 CrossRef PubMed.
- S. L. C. Pinho, J. S. Amaral, A. Wattiaux, M. Duttine, M.-H. Delville and C. F. G. C. Geraldes, Eur. J. Inorg. Chem., 2018, 3570–3578 CrossRef CAS.
- S. Wang, X. Wu, T. Wang, J. Zhang, C. Zhang, L. Yuan, X. Cui and D. Lu, Inorg. Chem., 2019, 58, 2315–2329 CrossRef CAS PubMed.
- R. Das and P. Poddar, J. Phys. Chem. C, 2014, 118, 13268–13275 CrossRef CAS.
- Y. Zhou, X. Wu, W. Wu, C. Wen and Q. Wang, J. Supercond. Novel Magn., 2018, 31, 521–528 CrossRef CAS.
- M. Taheri, F. S. Razavi and R. K. Kremer, Phys. C, 2018, 553, 8–12 CrossRef CAS.
- M. Arora and M. Kumar, Ceram. Int., 2015, 41, 5705–5712 CrossRef CAS.
- S. Chaturvedi, R. Bag, V. Sathe, S. Kulkarni and S. Singh, J. Mater. Chem. C, 2016, 4, 780–792 RSC.
- W. Li, H. Shen and J. Xu, J. Sol-Gel Sci. Technol., 2015, 76, 637–643 CrossRef CAS.
- W.-L. Tang, H. Lin, S.-H. Yang, Y.-L. Zhang, Y.-X. Tong and S.-L. Xie, Ferroelectrics, 2015, 489, 65–72 CrossRef CAS.
- Z. B. Guo, Y. W. Du, J. S. Zhu, H. Huang, W. P. Ding and D. Feng, Phys. Rev. Lett., 1997, 78, 1142–1145 CrossRef CAS.
- B. F. Yu, Q. Gao, B. Zhang, X. Z. Meng and Z. Chen, Int. J. Refrig., 2003, 26, 622–636 CrossRef.
- O. Tegus, E. Brück, K. H. J. Buschow and F. R. de Boer, Nature, 2002, 415, 150–152 CrossRef CAS PubMed.
|
This journal is © The Royal Society of Chemistry 2020 |
Click here to see how this site uses Cookies. View our privacy policy here.