Influence of the aqueous solution composition on the morphology of Zn1−xMgxO films deposited by spray pyrolysis†
Received
3rd December 2018
, Accepted 22nd February 2019
First published on 13th March 2019
Abstract
Tailoring the band gap of metal oxides is an attractive property for various device applications. Zinc–magnesium-oxide (Zn1−xMgxO) is a sustainable material that allows control of the energy band gap through the Mg content. To reduce the deposition costs of Zn1−xMgxO, solution-based techniques can be employed. This study investigates spray-pyrolysis as a versatile, environment-friendly, solution-based deposition method to fabricate Zn1−xMgxO films with morphology and properties that strongly depend on the composition of the water-based precursor solution. Films that are either compact or covered with nanorods are obtained, with tunable amounts of incorporated Mg and corresponding band gap values. In order to show the applicability of these films, Zn1−xMgxO was sprayed onto transparent conducting oxide substrates that are commonly used in various devices, such as solar cells with superstrate architecture.
1. Introduction
Oxide-based wide-band gap materials are attractive for an extensive range of applications, such as photovoltaics,1–3 functional coatings,4,5 (opto)electronic devices6–8 or sensors.9,10 Among them, ZnO is one of the most investigated metal oxides, because of its facile fabrication and doping, especially by low-cost solution-based techniques.11–13 ZnO can be doped with group-13 elements to enhance the intrinsic n-type conductivity or with divalent elements such as Mg or Cd, which increase or decrease the band gap due to differences in the electron affinity.14,15 The tunability of the band gap with Mg incorporation renders Zn1−xMgxO especially interesting for semiconductor devices, as the energy band alignment at the heterojunction is of utmost importance. An example is given by Hariskos et al. who reported the application of Zn1−xMgxO as n-type buffer layer in Cu(In,Ga)(Se,S)2-based thin film solar cells16 or Minami et al. who applied a Zn1−xMgxO buffer layer in Cu2O-type solar cells.17
Although Zn1−xMgxO can be deposited by a variety of vacuum-based deposition techniques, such as pulsed laser deposition (PLD),18 sputtering,19 molecular beam epitaxy (MBE)20 or atomic layer deposition (ALD),21 solution-based methods are particularly interesting regarding deposition costs. Solution-based Zn1−xMgxO deposition includes chemical bath deposition (CBD),22 electrochemical deposition (ECD),23 and sol–gel techniques.24 The first two take place close to ambient temperature, but they have the disadvantage that the thermodynamic solubility limit of MgO in ZnO is ∼4%.25 Sol–gel techniques can achieve higher Mg incorporation up to 23%,24 but require a high temperature (>500 °C) annealing step for sufficient film quality.
Spray pyrolysis is a versatile solution-based growth technique, which yields high-quality ZnO films at temperatures below 400 °C.26–28 Further, this method is easy to upscale and, therefore, suitable for large area deposition. In spray pyrolysis a precursor solution, containing volatile metal salts, forms a mist of droplets that are directed onto a heated substrate. For the droplet generation many techniques are available. Among them, the ultrasonic atomizing system has been proven to be precise, controllable and repeatable.29
Zn1−xMgxO films deposited by spray pyrolysis have been reported frequently,15,30–41 but in the majority of the reports toxic or flammable solvents, such as methanol30–32 or ethanol,15,34,35 are used. Studies on water-based solutions are rare.36,37,40,41 Moreover, due to the unfavorable properties of water as a solvent in spray pyrolysis (such as strong hydrogen bonds and a high boiling point),27 temperatures above >400 °C are commonly employed.36,37 Among the studies using water-based solutions and temperatures below 400 °C, none achieved Mg incorporation larger than 10 mol%.40,41
For certain device applications, the use of nanostructures instead of compact films can be an advantage.42–44 For the same reasons as for compact films, it is highly desired to deposit nanostructures with a tailored band gap. A common approach to obtain Mg-doped ZnO nanorods from aqueous solutions is hydrothermal deposition, but so far the amount of incorporated Mg by this technique was limited to below 1%.45,46 Up to now, there is no report on Zn1−xMgxO nanorod deposition by a one-step spray pyrolysis process.
In this work Zn1−xMgxO was deposited by ultrasonic spray pyrolysis (USP) from water-based solutions at 360 °C, in air. Solely low-cost and environment-friendly raw materials were chosen for the precursor solution. This study elucidates the effect of the solution composition on the deposited Zn1−xMgxO films and presents a novel, one-step synthesis approach to obtain Zn1−xMgxO films that are either compact or covered with nanorods on various substrates. The Mg incorporation in the Zn1−xMgxO films was investigated and optical band gaps were determined. In order to show the applicability of these films in applications, Zn1−xMgxO was sprayed onto three different transparent conducting oxide substrates which are commonly used as electrodes in devices.
2. Experimental
2.1. Spray pyrolysis set-up
USP was carried out in a Sono-Tek Exacta Coat® system, using a Sono-Tek Impact® 120 kHz nozzle in the horizontal geometry with an applied power of 3.5 W. The solution flow rate was kept at 0.8 ml min−1 and compressed air (0.5 bar) was used as the carrier gas. The substrate-to-nozzle distance was kept at 200 mm and the scanning speed of the nozzle over the substrate was 25 mm s−1. The number of spraying cycles over the substrate was for all experiments fixed to 80 repetitions, unless otherwise stated, resulting in a film thickness between 200 and 300 nm. The substrates were heated to 360 °C using a hot plate covered with an aluminium substrate holder.
2.2. Sample preparation and precursor solutions
Borosilicate glass substrates (Schott Nexterion® D, 7.5 × 2.5 cm2) were ultrasonically cleaned at 50 °C for 30 minutes in Hellmanex® III washing solution, rinsed with deionized water (DI, 18 MΩ cm−1), then rinsed with isopropanol and finally dried in an air stream. Commercial fluorine-doped tin oxide (FTO, 2.2 mm thick, 7 Ω Sq−1, Sigma-Aldrich 735140-5EA) and indium tin oxide glass substrates (ITO, 1 mm thick, Sigma-Aldrich 703192, 8–12 Ω Sq−1) were rinsed with deionized water, rinsed with isopropanol and dried in an air stream. For the preparation of 1.8 μm-thick indium-doped ZnO (IZO) films on borosilicate glass substrates the same recipe as previously reported by our group47 was used.
In the first set of experiments Zn1−xMgxO films were deposited on clean glass substrates using precursor solutions with various concentrations of magnesium dopant and a constant concentration of zinc salt. Metal acetates were chosen as precursor salts due to their low-cost, non-toxicity and suitable properties for spray deposition. The sprayed aqueous solutions A–F contained 0.2 M of zinc acetate dihydrate (Zn(CH3COO)2 × 2H2O, Sigma-Aldrich 96459) and 0, 5, 10, 15, 20 and 30 mol% magnesium acetate tetrahydrate (Mg(CH3COO)2 × 4H2O, Sigma-Aldrich M5661) dissolved in deionized water, as summarized in Table 1. Additionally, the solutions contained 1.4 M acetic acid (CH3COOH, Sigma-Aldrich A6283) to achieve a lower surface tension, resulting in a smaller droplet size, as well as a pH value suitable for the deposition.
Table 1 Composition of the sprayed solutions
Solution |
Concentration ZnAc2 (M) |
Mg dopant (mol%) |
Acetic acid (M) |
pH value |
A |
0.2 |
0 |
1.4 |
3.60 |
B |
0.2 |
5 |
1.4 |
3.67 |
C |
0.2 |
10 |
1.4 |
3.69 |
D |
0.2 |
15 |
1.4 |
3.74 |
E |
0.2 |
20 |
1.4 |
3.78 |
F |
0.2 |
30 |
1.4 |
3.80 |
G |
0.1 |
15 |
1.4 |
3.60 |
H |
0.4 |
15 |
1.4 |
3.95 |
I |
0.8 |
15 |
1.4 |
4.10 |
J |
0.2 |
15 |
0.35 |
4.44 |
K |
0.2 |
15 |
2.8 |
3.45 |
L |
0.2 |
15 |
5.25 |
3.10 |
To investigate the influence of the zinc acetate molarity and the solution pH value, solutions G–L were prepared with a constant Mg concentration (15 mol% Mg) and varied zinc acetate molarities or acetic acid concentrations as displayed in Table 1.
For the deposition of nanorods and compact films on different TCO substrates, solutions D and I with 15 mol% Mg and different zinc acetate molarities were sprayed onto IZO, FTO and ITO.
2.3. Film characterization
The film morphology and film thickness were analysed by scanning electron microscopy (SEM, Zeiss Ultra 40), using an in-lens detector and a 5 kV acceleration voltage. The transparency of the films was obtained by Fourier transform infrared spectroscopy (FTIR, Bruker Vertex 70) in the UV/vis/IR range between 300 and 1000 nm. X-ray diffraction (XRD, ThermoFisher Scientific ARL Equinox 100) with Cu-Kα (λ = 1.5419 Å) radiation was used to determine the crystal structure of the deposited films. The elemental composition was determined by inductive coupled plasma spectroscopy (ICP-OES, PerkinElmer Optima 5300 DV). For the ICP-OES measurements liquid samples were prepared by dissolving the Zn1−xMgxO films in 1 M ultrapure HNO3 in an ultrasonic bath for 20 minutes at room temperature. The sheet resistance was measured using a 4-point probe set-up connected to a semiconductor parameter analyzer (Süss MicroTec probes, Agilent 4156 C parameter analyzer). EDX analysis was done on a scanning electron microscope (Zeiss Supra 55 VP) with an accelerating voltage of 3 kV.
3. Results and discussion
3.1. Influence of the solution composition on the deposited Zn1−xMgxO structure
3.1.1. Effect of Mg concentration.
The addition of Mg acetate to the solution causes a change in the surface morphology from a compact film to nanorods, as seen in the SEM images in Fig. 1(a)–(f). Films deposited from the undoped ZnO solution show high surface roughness and pronounced grain facets. With higher Mg content in the solution, an increasing amount of evenly distributed nanorods was observed. SEM cross sections (Fig. 2(a)–(f)) reveal that the films are composed of a first dense Zn1−xMgxO part, followed by a part with nanorods. The amount of Mg present in the deposited materials was determined by ICP OES elemental analysis and is listed in Table 2 and shown in Fig. 1.
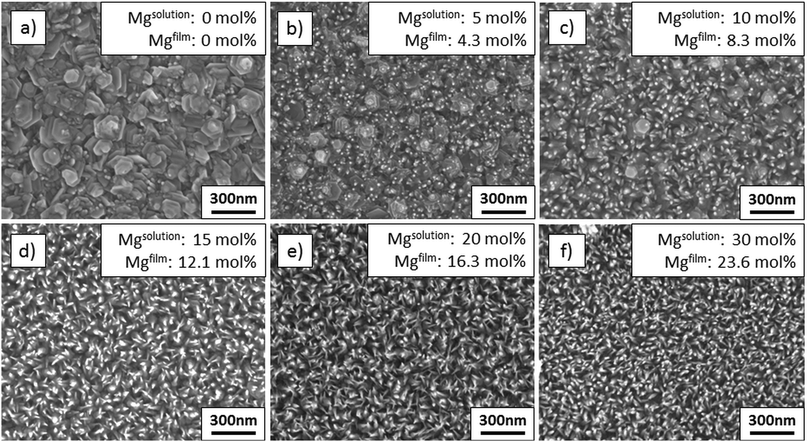 |
| Fig. 1 SEM plane views of films deposited from solutions with varied amounts of Mg: (a) undoped ZnO, (b) 5 mol% Mg, (c) 10 mol% Mg, (d) 15 mol% Mg, (e) 20 mol% Mg, and (f) 30 mol% Mg. | |
 |
| Fig. 2 SEM cross sections of films deposited from solutions with varied amounts of Mg: (a) undoped ZnO, (b) 5 mol% Mg, (c) 10 mol% Mg, (d) 15 mol% Mg, (e) 20 mol% Mg, and (f) 30 mol% Mg. | |
Table 2 (0001) ZnO 2θ position and Mg content for films obtained from solutions A–E
Solution |
Mg in solution (mol%) |
ZnAc2 molarity (M) |
(0001) ZnO 2θ position |
Mg in film from ICP OES (mol%) |
A |
0 |
0.2 |
34.304 |
0 |
B |
5 |
0.2 |
34.333 |
4.29 |
C |
10 |
0.2 |
34.363 |
8.33 |
D |
15 |
0.2 |
34.392 |
12.08 |
E |
20 |
0.2 |
34.421 |
16.27 |
Independent of the Mg concentration in the solution, X-ray diffractograms demonstrate that all Zn1−xMgxO films exhibit a preferred {0001} ZnO orientation (Fig. 3(a)). Samples deposited from solutions A–D (up to 15 mol% Mg in the solution) exhibit only the zincite phase (COD database, 96-900-4182), while solutions E (20 mol% Mg in the solution) and F (30 mol% Mg in the solution) result in segregation of a MgO periclase phase (COD database, 96-900-6463) with a preferred {111} and {200} orientation. Grain agglomerates covering the nanorod layer were observed for samples deposited from these solutions as shown in Fig. 4. The agglomerates most likely consist of a mixture of MgO and Zn1−xMgxO.
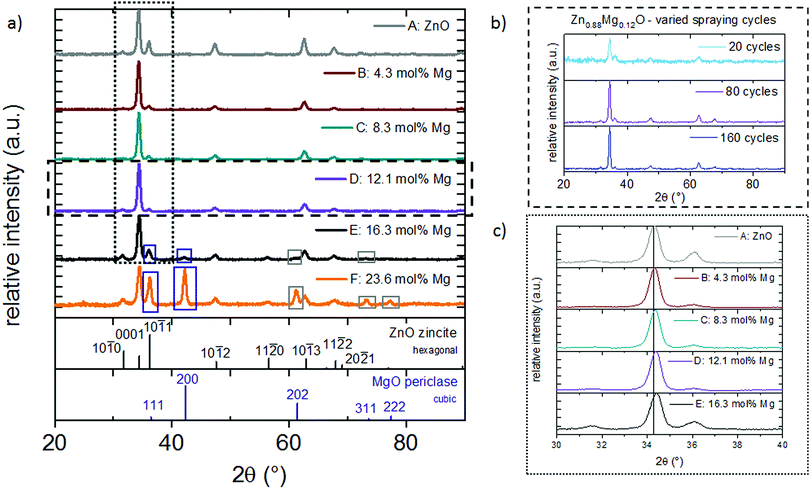 |
| Fig. 3 X-ray diffractograms of films deposited from (a) solutions A–F with varied amounts of Mg, and (b) solution D with a varied number of spraying cycles. (c) (0001) ZnO peak for films deposited from solutions A–E. | |
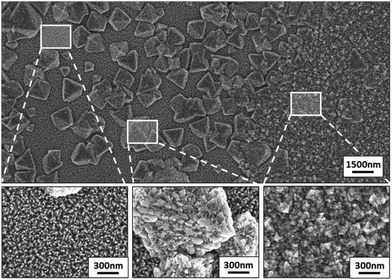 |
| Fig. 4 SEM image (top) of a film deposited from 30 mol% Mg solution F, composed of areas with different morphological features, ranging from nanorods to larger-scale agglomerates, shown in the marked zoomed-in areas (bottom). | |
Our results suggest a solubility limit of ∼20 mol% Mg in the solution (resulting in ∼16 mol% Mg in the film) for the experimental conditions of this study. Samples deposited from 30 mol% Mg solutions showed an especially high amount of Mg (23.6 mol%) in the ICP OES, which is attributed to MgO coprecipitation. A variation in spraying cycles for solution D retains the preferred {0001} ZnO crystal orientation (Fig. 3(b)) even for the thinnest film, suggesting that there is no competitive growth in the beginning of the film formation.
One important aspect of this work was the incorporation of Mg into the ZnO lattice. To verify that Mg is indeed substituting Zn atoms in the lattice and not solely occupying interstitial sites, XRD peaks were studied. Since the ionic radius of the tetrahedral Mg is slightly smaller (0.57 Å)48 compared to Zn (0.60 Å),48 a substitution by this ion results in a minor peak shift to higher 2θ angles. Fig. 3(c) and Table 2 show the {0001} reflection of zincite Zn1−xMgxO films deposited from solutions with varied Mg acetate concentrations. In comparison to undoped ZnO, films containing 16 mol% Mg cause a shift of the {0001} reflection from 34.304° to 34.421°. This indicates incorporation of the Mg atom in the ZnO lattice. Peak shifts to higher 2θ angles are commonly observed in Zn1−xMgxO prepared by spray pyrolysis and for a similar Mg incorporation range the values obtained in the present study fit well to literature data.15,40
The formation of nanorods by spray pyrolysis is not a common phenomenon. Nanorod growth is either observed if a seed layer is deposited prior to the spray deposition49 or at higher temperatures around 500–600 °C.50,51 The growth evolution of nanorods by addition of Mg can be explained by considering the aspects that influence the film growth in spray pyrolysis. According to Arca et al.,27 the main factors are: (i) the thermal properties of the solvent, (ii) the volatility/decomposition properties of the precursors and (iii) the substrate temperature.
The solvent evaporation is mainly defined by the water
:
acetic acid ratio, which was fixed for this experimental series. Therefore, this influence can be neglected.
As far as the thermal decomposition of the metal salt precursors is concerned, it is often studied by thermal analysis methods, such as thermogravimetric (TGA) or differential thermal analysis (DTA). These methods usually apply much lower heating rates compared to those that the precursors undergo in the spray pyrolysis process. Although the heating rate has a significant influence on the thermal decomposition, some conclusions could be drawn. Reports on TGA/DTA analysis of ZnAc2 and MgAc2 show that ZnAc2 decomposes completely at a much lower temperature (∼300 °C)52 compared to MgAc2 (∼400 °C),53 at an applied heating rate of 20 °C min−1. Further, for the ZnAc2 decomposition it was proposed that a volatile intermediate tetrahedral cluster of ZnO4(CH3COO)6 (I) (basic zinc acetate complex BZA) is formed, which can adsorb on the substrate surface and stepwise decompose to ZnO.54,55 Such a complex was never reported for MgAc2 decomposition and since Mg2+ prefers the octahedral over the tetrahedral complex coordination,56,57 it may not be favorable. However, there is the possibility that some zinc atoms in the BZA are substituted by magnesium atoms. It is not clear to what extent the decomposition of ZnAc2 is influenced by MgAc2 addition.
The main influence on the growth behaviour most likely arises from the substrate temperature. A possible explanation for the nanorod formation is the modified temperature at the substrate/air interface due to the Zn1−xMgxO deposition. Mg doping lowers the thermal conductivity of ZnO,58,59 resulting in a temperature gradient that favors nanorod growth (see also the schematic growth behaviour in Fig. 5(a)–(c)). At the same time, the underlying compact film acts as a seed layer for the growth of nanorods.
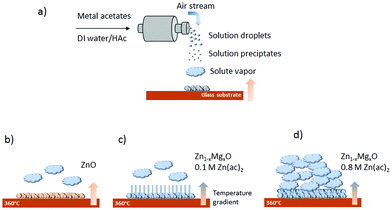 |
| Fig. 5 Schematic of (a) the general spray pyrolysis process, (b) ZnO deposition, (c) Zn1−xMgxO nanorod deposition from 0.1 M Zn(ac)2 solution, and (d) Zn1−xMgxO film deposition from 0.8 M Zn(ac)2. | |
To further investigate this behaviour, films were deposited with an increasing number of spraying cycles, namely 20, 80 and 160 cycles, from solution D (15 mol% Mg). Fig. 1(d) and 6(a) and (b) show plain view SEM images of these films and Fig. 2(d) and 7(a) and (b) cross sections. From examination of these images it is concluded that a low number of spraying cycles (fast deposition process, less substrate cooling) results in thin and compact films, while for an increasing number of spraying cycles the nanorod length remains constant, while the thickness of the compact part of the film underneath the nanorods increases. This means that nanorods evolve into a compact film as the spraying proceeds.
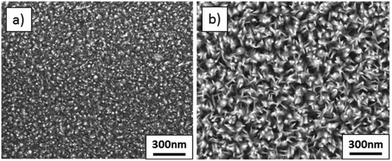 |
| Fig. 6 SEM plane views of films deposited from a 15 mol% Mg solution with a varied number of spraying cycles: (a) 20 cycles, and (b) 160 cycles. | |
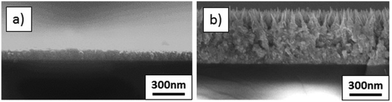 |
| Fig. 7 SEM cross sections of films deposited from a 15 mol% Mg solution with a varied number of spraying cycles: (a) 20 cycles, and (b) 160 cycles. | |
To verify that the nanorods indeed consist of Zn1−xMgxO, EDX analysis of the compact part of the film and the part with the nanorods was realized. For this, separate scans were acquired on the tilted cross section of a film deposited from solution D (with 15 mol% Mg) (see also Fig. S1, ESI†). In both scans, corresponding to the compact and nanorod part of the film, EDX showed signals from Zn and Mg (Fig. S2, ESI†).
3.1.2. Effect of zinc acetate molarity.
The zinc acetate (ZnAc2) molarity was adjusted, while maintaining 15 mol% Mg acetate in the solution. A solution containing 15 mol% Mg and 0.2 M zinc acetate resulted previously in the formation of nanorods (see also Fig. 1(d) and 2(d)). It was observed that with increasing ZnAc2 molarity denser films can be obtained, while a lower overall metal salt concentration results in thinner compact films with enlarged nanorods as displayed in Fig. 8(a)–(c) and 9(a)–(c). Independent from the Zn1−xMgxO structure, the amount of Mg determined by ICP OES remained unchanged as listed in Table 3 and Fig. 8(a)–(c). This is another indication that the nanorods and the compact film have similar compositions.
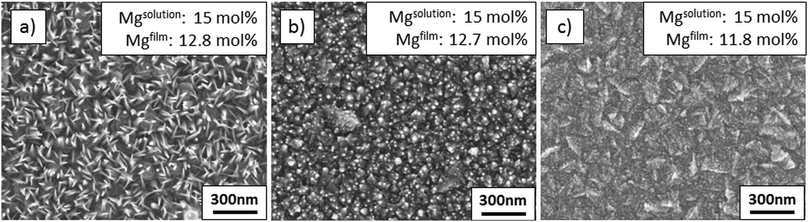 |
| Fig. 8 SEM images of films deposited from solutions with varied zinc acetate molarity (a) G: 0.1 M, (b) H: 0.4 M, and (c) I: 0.8 M. | |
 |
| Fig. 9 SEM cross sections of films deposited from solutions with varied zinc acetate molarity (a) G: 0.1 M, (b) H: 0.4 M, and (c) I: 0.8 M. | |
Table 3 (0001) ZnO 2θ position and Mg content for films obtained from solutions G–I
Solution |
Mg in solution (mol%) |
ZnAc2 molarity (M) |
(0001) ZnO 2θ position |
Mg in film from ICP OES (mol%) |
G |
15 |
0.1 |
34.392 |
12.84 |
H |
15 |
0.4 |
34.392 |
12.72 |
I |
15 |
0.8 |
34.392 |
11.78 |
Fig. 5(d) shows schematically that a high ZnAc2 molarity results in a large amount of incoming volatile zinc and magnesium species, which hinder the formation of Zn1−xMgxO nanorods and pack closely forming a compact film. Besides that, as the deposition process is accelerated, there is less surface cooling. At the same time, a higher ZnAc2 molarity increases the pH value from 3.6 to 4.1, resulting in an altered solution speciation of volatile Zn and Mg complexes, which might also affect the film growth.
Upon comparison of the compact ZnO film in Fig. 2(a) with the compact Zn1−xMgxO film in Fig. 9(c), one can observe that they possess different surface morphologies (see also plain view SEM images in Fig. 1(a) and 8(c)). Additionally, the XRD diffractograms shown in Fig. 3(a) and 10(a) reveal that they exhibit differing textures.
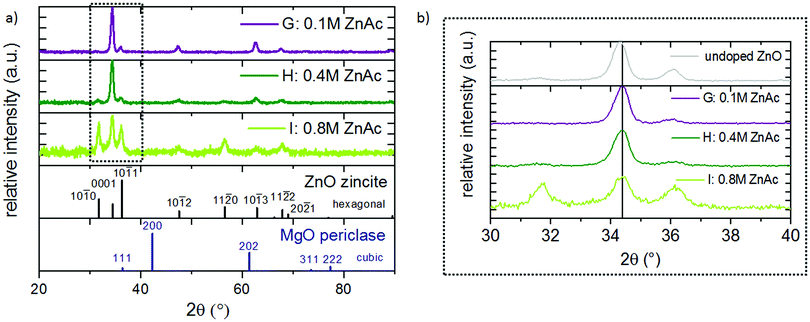 |
| Fig. 10 (a) XRD spectra of films deposited from solutions with 15 mol% Mg with varied zinc acetate molarity, and (b) zoomed in (0001) ZnO peak. | |
Zn1−xMgxO films stemming from solutions with different ZnAc2 molar concentrations (0.1–0.8 M) have distinctive structural properties. Films deposited from solutions G (0.1 M) and H (0.4 M) show a preferred {0001} ZnO orientation (Fig. 10(a)). Deposition from solution I (0.8 M) gives rise to a polycrystalline ZnO film with higher intensities of the {10
0} and {10
1} reflections. The position of the {0001} ZnO peak, as shown in Fig. 10(b) and Table 3, is not altered by a variation in the ZnAc2 molarity. This confirms, together with ICP OES, that Mg incorporation is only dependent on the Mg content in the solution.
In summary, adjustment of the ZnAc2 molarity offers a simple tool to control the film morphology and deposit films with or without nanorods, with various amounts of incorporated Mg.
3.1.3. Effect of acetic acid concentration.
The amount of acetic acid (HAc) was varied to investigate the influence of the solution pH value and of the solvent evaporation behaviour on the Zn1−xMgxO morphology. The resulting film morphologies are displayed in Fig. 11(a)–(c). With increasing pH value (lower acetic acid concentration) fewer nanorods are observed. The H2O
:
HAc ratio not only has an influence on the temperature during the deposition, it also alters slightly the mean droplet size due to a change in the surface tension.60 Further, the amounts of volatile Zn and Mg species in the solution depend on the pH value and can also influence the film growth. Compared to the influence of the Mg concentration or the zinc acetate molarity on the Zn1−xMgxO morphology, the influence of the acetic acid concentration is less pronounced.
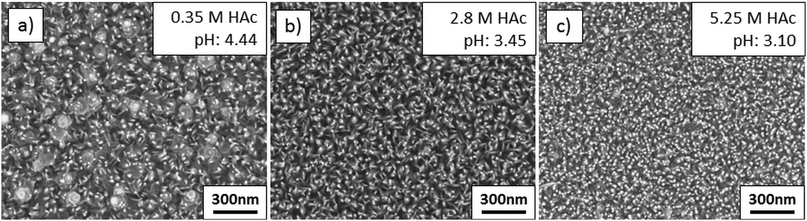 |
| Fig. 11 Films sprayed from solution with various amounts of acetic acid: (a) J: 0.35 M HAc, (b) K: 2.80 HAc, and (c) L: 5.25 M HAc. | |
XRD confirmed, as shown in Fig. 12(a), that all films are polycrystalline, with a preferred {0001} ZnO orientation. Films deposited from a solution containing a high acetic acid concentration have a reduced thickness due to the lower heat required for solvent vaporization and the consequential higher effective deposition temperature. Further, a minor {0001} peak shift to higher 2θ angles (see also Fig. 12(b)) can be observed.
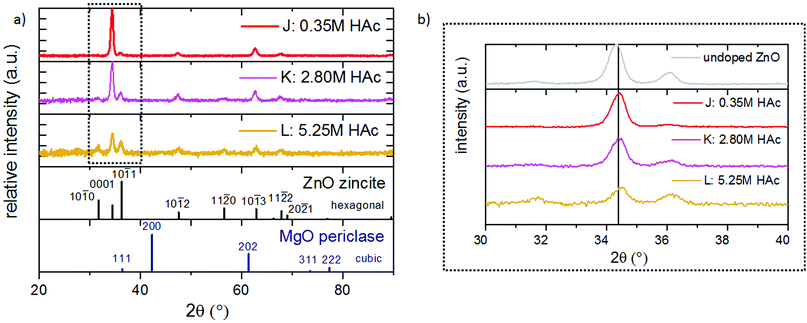 |
| Fig. 12 (a) XRD spectra of films deposited from solutions with 15 mol% Mg and varied acetic acid concentrations, and (b) zoom-in of the (0001) ZnO peak. | |
3.2. Optical and electrical Zn1−xMgxO properties
FTIR spectra (in the UV/vis/IR wavelength region) of the films obtained from all solution compositions are displayed in Fig. 13(a)–(c). For varying Mg concentration (Fig. 13(a)) higher transparencies are observed till 12.1 mol% Mg incorporation, compared to undoped ZnO. Films deposited from solutions E and F with high Mg concentrations exhibit a lower transparency, due to the presence of white MgO precipitates on the film surface. For variations in the ZnAc2 molarity (Fig. 13(b)) and the HAc concentration (Fig. 13(c)) the resulting transparency is constant, with values >80%.
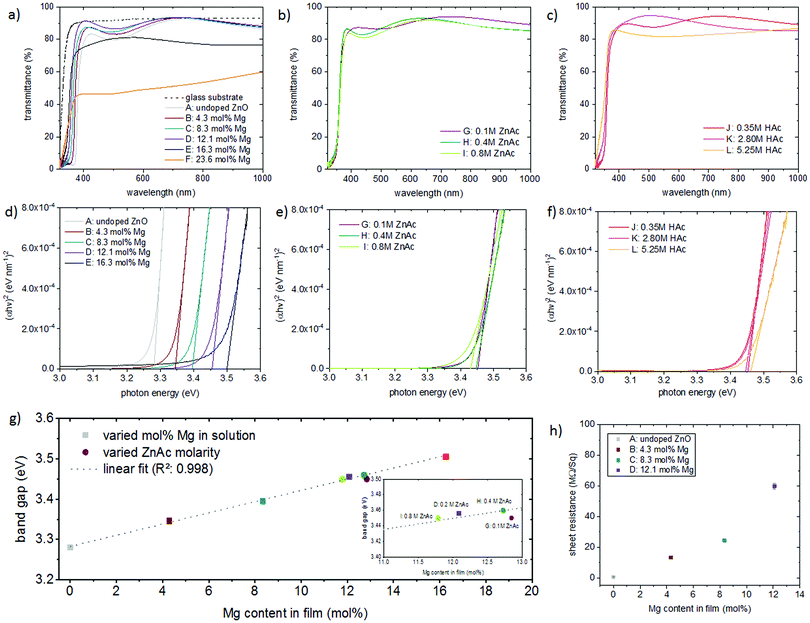 |
| Fig. 13 FTIR transmittance spectra and Tauc plots for films deposited from solutions with (a) and (d) a variation in Mg concentration, (b) and (e) a variation in zinc acetate molarity, and (c) and (f) a variation in acetic acid concentration; (g) band gap as a function of the Mg content; and (h) sheet resistance as a function of the Mg content. | |
Optical band gaps were linearly extrapolated as shown in Fig. 13(d)–(f) from transmittance data using Tauc's relation for direct band gap semiconductors,61 where α is the absorption coefficient, hν the photon energy, A a constant and Eg is the band gap (in eV):
| (α × hν)2 = A × (hν − Eg) | (1) |
Fig. 13(d) shows a gradual band edge shift to higher values with increasing amounts of incorporated Mg. It was seen that there is a linear dependence of the band gap with Mg incorporation between 0 and 16.3 mol%. For the Zn1−xMgxO films realized by variations in the zinc acetate molarity, the optical band gap remained ∼3.45 eV, as seen in Fig. 13(e). Alterations in the acetic acid concentration did not affect the band gap as well, as displayed in Fig. 13(f). Fig. 13(g) shows the dependence of the band gap on the amount of incorporated Mg for the different films.
The sheet resistance was measured for Zn1−xMgxO films (∼250 nm thick) deposited on glass (as shown in Fig. 2(a)–(d)) with different Mg content (Fig. 13(h)). While for undoped ZnO the sheet resistance is 0.52 MΩ Sq−1, it increases with an increasing amount of incorporated Mg to ∼60 MΩ Sq−1 for films with 12 mol% incorporated Mg. This behaviour is commonly observed for Zn1−xMgxO films.62
3.3. Zn1−xMgxO deposited on TCO substrates
To show the applicability of the deposition process, Zn1−xMgxO films were sprayed onto three conducting oxide substrates, namely commercial FTO, ITO and sprayed IZO. This is an important step towards device applications in which Zn1−xMgxO is applied on a transparent electrode, such as solar cells with a superstrate architecture. It is important to note that the proposed deposition process might not be applicable to devices in which the substrate properties are impaired by the temperature and/or incoming vapor of precursor solution species.
It is well known that the nature of the substrate influences the surface texture of spray deposited films.63–65 This behaviour can be attributed to the difference in surface energy and thermal properties for each substrate. As stated before, the heat conductivity of the substrate and the deposited material influences the morphology of the sprayed Zn1−xMgxO. Therefore, a lower amount of nanorods in the deposited film is expected due to the higher heat conductivity of metal oxide coated glass substrates, compared to pure borosilicate glass used in the previous experiments. To show that nanorods and dense Zn0.88Mg0.12O films can be deposited, solution D (for nanorod formation) and solution I (for dense films) were used for the deposition on the various TCO substrates.
The film morphologies are displayed in Fig. 14(a)–(f). On all three TCO substrates it was observed that low concentration solutions (solution D) still lead to the formation of nanorods, while if the ZnAc2 molarity is increased to 0.8 M compact films can be deposited. Nevertheless, deposition on ITO and FTO results in a lower amount of nanorods. This suggests that the main influence on the morphology of the deposited material stems from the solution composition and the underlying substrate has a minor effect on the film structure. The Zn0.88Mg0.12O film morphology on FTO substrates (Fig. 14(f)) appears to be rougher than on the other two substrates, which arises from the rougher morphology of the underlying FTO substrate.
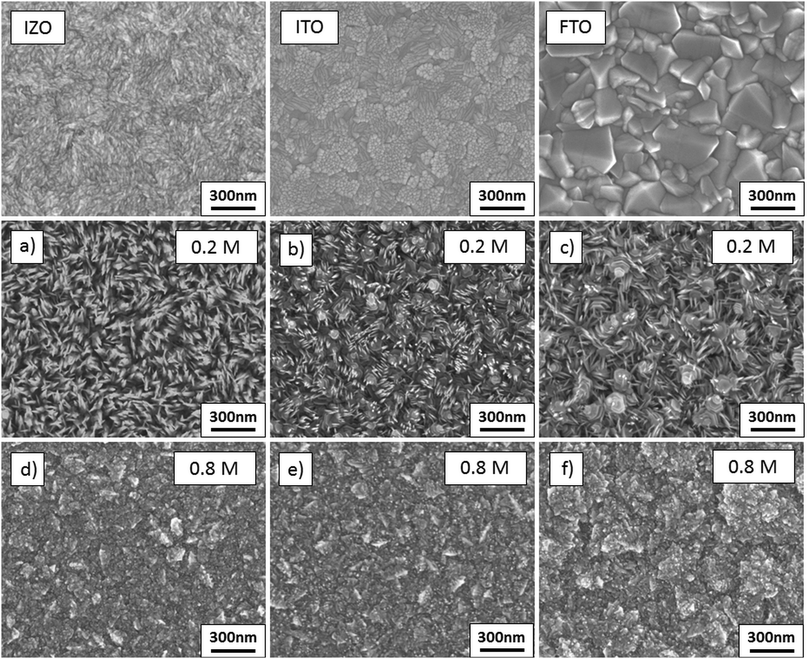 |
| Fig. 14 SEM images of films deposited from solutions D (a–c) and I (d–f) on IZO (a and d); ITO (b and e); and FTO (c and f). | |
The film structure was further analysed by XRD diffractograms of Zn0.88Mg0.12O deposited on ITO and FTO as shown in Fig. 15(a) and (b). Because of the high film thickness of the IZO electrode (1.8 μm) and the same crystal structure of IZO and Zn0.88Mg0.12O, it is not possible to assign specific peaks to Zn0.88Mg0.12O, therefore these diffractograms are not shown here.
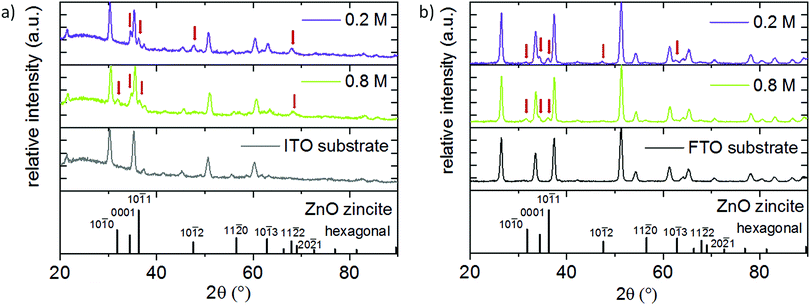 |
| Fig. 15 XRD diffractograms of films deposited from solution D and I (a) on ITO, and (b) on FTO. | |
On ITO substrates, the higher ZnAc2 molarity results in the appearance of the {10
0} Zn0.88Mg0.12O reflection additionally to {0001}, {10
1} and minor reflections of {11
2}, while the {10
2} reflection disappears. On FTO substrates the {10
0} peak becomes more prominent with higher ZnAc2 molarity, while {10
2} and {10
3} reflections could not be observed anymore. In comparison to that, on glass (Fig. 10(a)) the intensity of the {10
0}, {10
1} and {11
0} reflections increased with increasing zinc acetate molarity. This shows that the substrate has only a minor additional influence on the film orientation.
In summary, results from the deposition on glass substrates can be transferred to other substrates such as glass coated with TCOs, without altering the material properties. This indicates that the proposed deposition process of Zn1−xMgxO can further be applied in various device applications. An example is given by the application of a compact Zn0.88Mg0.12O film as a buffer layer in all-solution processed Cu2O-type all-oxide solar cells.47
4. Conclusion
This article investigates the influence of the precursor solution composition on the structure of Zn1−xMgxO obtained by ultrasonic spray pyrolysis from water-based solutions. Depending on the precursor concentrations, either dense films or nanorods can be obtained. XRD in combination with ICP OES showed that Mg is substitutionally incorporated into the ZnO lattice. It was found that solely the precursor solution defines the amount of incorporated Mg, independent from the Zn1−xMgxO morphology, which offers a valuable tool to deposit nanostructures with defined amounts of Mg and band gaps between 3.28 and 3.50 eV. The applicability of the spray deposited Zn1−xMgxO nanostructures was demonstrated by deposition on conducting metal oxide substrates.
Conflicts of interest
There are no conflicts of interest to declare.
Acknowledgements
The authors thank Dr Oskar Armbruster for valuable discussions on the Zn1−xMgxO nanorod formation, Wolfgang Obermaier for the ICP OES measurements and Stephan Puchegger for EDX analysis at the University of Vienna.
References
-
A. Pérez-Tomás, E. Chikoidze, M. R. Jennings, S. A. O. Russell, F. H. Teherani, P. Bove, E. V. Sandana and D. J. Rogers, in Oxide-based Materials and Devices IX, International Society for Optics and Photonics, 2018, vol. 10533, p. 105331Q Search PubMed.
- S. Calnan, Applications of Oxide Coatings in Photovoltaic Devices, Coatings, 2014, 4, 162–202 CrossRef.
- E. Fortunato, D. Ginley, H. Hosono and D. C. Paine, Transparent Conducting Oxides for Photovoltaics, MRS Bull., 2007, 32, 242–247 CrossRef CAS.
- Y.-J. Lee, D. S. Ruby, D. W. Peters, B. B. McKenzie and J. W. P. Hsu, ZnO Nanostructures as Efficient Antireflection Layers in Solar Cells, Nano Lett., 2008, 8, 1501–1505 CrossRef CAS PubMed.
- L. Spanhel, Colloidal ZnO nanostructures and functional coatings: A survey, J. Sol-Gel Sci. Technol., 2006, 39, 7–24 CrossRef CAS.
-
W. Fuhs, Zinc Oxide—A Material for Micro- and Optoelectronic Applications, Springer, Dordrecht, 2005, pp. 197–209 Search PubMed.
- S. J. Pearton and F. Ren, Wide Band gap Semiconductor One-Dimensional Nanostructures for Applications in Nanoelectronics and Nanosensors, Nanomater. Nanotechnol., 2013, 3, 1 CrossRef.
- A. B. Djurišić, A. M. C. Ng and X. Y. Chen, ZnO nanostructures for optoelectronics: Material properties and device applications, Prog. Quantum Electron., 2010, 34, 191–259 CrossRef.
-
B. S. Kang, H.-T. Wang, L.-C. Tien, F. Ren, B. P. Gila, D. P. Norton, C. R. Abernathy, J. Lin and S. J. Pearton, Wide Band gap Semiconductor Nanorod and Thin Film Gas Sensors, Sensors (Basel), 2006, 6, 643–666 Search PubMed.
- L. Zhu and W. Zeng, Room-temperature gas sensing of ZnO-based gas sensor: A review, Sens. Actuators, A, 2017, 267, 242–261 CrossRef CAS.
- A. Kołodziejczak-Radzimska, T. Jesionowski, A. Kołodziejczak-Radzimska and T. Jesionowski, Zinc Oxide—From Synthesis to Application: A Review, Materials, 2014, 7, 2833–2881 CrossRef PubMed.
- L. Schmidt-Mende and J. L. MacManus-Driscoll, ZnO–nanostructures, defects, and devices, Mater. Today, 2007, 10, 40–48 CrossRef CAS.
- D. P. Norton, Y. W. Heo, M. P. Ivill, K. Ip, S. J. Pearton, M. F. Chisholm and T. Steiner, ZnO: growth, doping & processing, Mater. Today, 2004, 7, 34–40 CrossRef CAS.
- A. Janotti and C. G. V. de Walle, Fundamentals of zinc oxide as a semiconductor, Rep. Prog. Phys., 2009, 72, 126501 CrossRef.
- M. Rouchdi, E. Salmani, B. Fares, N. Hassanain and A. Mzerd, Synthesis and characteristics of Mg doped ZnO thin films: Experimental and ab-initio study, Results Phys., 2017, 7, 620–627 CrossRef.
- D. Hariskos, B. Fuchs, R. Menner, N. Naghavi, C. Hubert, D. Lincot and M. Powalla, The Zn(S,O,OH)/ZnMgO buffer in thin-film Cu(In,Ga)(Se,S)2-based solar cells part II: Magnetron sputtering of the ZnMgO buffer layer for in-line co-evaporated Cu(In,Ga)Se2 solar cells, Prog. Photovoltaics, 2009, 17, 479–488 CAS.
- T. Minami, Y. Nishi, T. Miyata and S. Abe, Photovoltaic Properties in Al-doped ZnO/non-doped Zn1−XMgXO/Cu2O Heterojunction Solar Cells, ECS Trans., 2013, 50, 59–68 CrossRef.
- A. Ohtomo, M. Kawasaki, T. Koida, K. Masubuchi, H. Koinuma, Y. Sakurai, Y. Yoshida, T. Yasuda and Y. Segawa, MgxZn1−xO as a II–VI widegap semiconductor alloy, Appl. Phys. Lett., 1998, 72, 2466–2468 CrossRef CAS.
- T. Minemoto, T. Negami, S. Nishiwaki, H. Takakura and Y. Hamakawa, Preparation of Zn1−xMgxO films by radio frequency magnetron sputtering, Thin Solid Films, 2000, 372, 173–176 CrossRef CAS.
- K. Ogata, K. Koike, T. Tanite, T. Komuro, F. Yan, S. Sasa, M. Inoue and M. Yano, ZnO and ZnMgO growth on a-plane sapphire by molecular beam epitaxy, J. Cryst. Grow., 2003, 251, 623–627 CrossRef CAS.
- T. Törndahl, C. Platzer-Björkman, J. Kessler and M. Edoff, Atomic layer deposition of Zn1−xMgxO buffer layers for Cu(In,Ga)Se2 solar cells, Prog. Photovoltaics, 2007, 15, 225–235 Search PubMed.
- N. Winkler, S. Edinger, W. Kautek and T. Dimopoulos, Mg-doped ZnO films prepared by chemical bath deposition, J. Mater. Sci., 2018, 53, 5159–5171 CrossRef CAS.
- M. Wang, J. Yi, S. Yang, Z. Cao, X. Huang, Y. Li, H. Li and J. Zhong, Electrodeposition of Mg doped ZnO thin film for the window layer of CIGS solar cell, Appl. Surf. Sci., 2016, 382, 217–224 CrossRef CAS.
- M. Wang, E. J. Kim, S. Kim, J. S. Chung, I.-K. Yoo, E. W. Shin, S. H. Hahn and C. Park, Optical and structural properties of sol–gel prepared MgZnO alloy thin films, Thin Solid Films, 2008, 516, 1124–1129 CrossRef CAS.
- E. R. Segnit and A. E. Holland, The System MgO–ZnO–SiO2, J. Am. Ceram. Soc., 1965, 48, 409–413 CrossRef CAS.
- F. Paraguay D., W. Estrada L., D. R. Acosta N., E. Andrade and M. Miki-Yoshida, Growth, structure and optical characterization of high quality ZnO thin films obtained by spray pyrolysis, Thin Solid Films, 1999, 350, 192–202 CrossRef CAS.
- E. Arca, K. Fleischer and I. V. Shvets, Influence of the Precursors and Chemical Composition of the Solution on the Properties of ZnO Thin Films Grown by Spray Pyrolysis, J. Phys. Chem. C, 2009, 113, 21074–21081 CrossRef CAS.
- G. Adamopoulos, A. Bashir, W. P. Gillin, S. Georgakopoulos, M. Shkunov, M. A. Baklar, N. Stingelin, D. D. C. Bradley and T. D. Anthopoulos, Structural and Electrical Characterization of ZnO Films Grown by Spray Pyrolysis and Their Application in Thin-Film Transistors, Adv. Funct. Mater., 2011, 21, 525–531 CrossRef CAS.
- W.-N. Wang, A. Purwanto, I. W. Lenggoro, K. Okuyama, H. Chang and H. D. Jang, Investigation on the Correlations between Droplet and Particle Size Distribution in Ultrasonic Spray Pyrolysis, Ind. Eng. Chem. Res., 2008, 47, 1650–1659 CrossRef CAS.
- M. Lopez-Ponce, A. Hierro, V. Marín-Borrás, G. Tabares, A. Kurtz, S. Albert, S. Agouram, V. Muñoz-Sanjosé, E. Muñoz and J. M. Ulloa, Optical properties of ZnMgO films grown by spray pyrolysis and their application to UV photodetection, Semicond. Sci. Technol., 2015, 30, 105026 CrossRef.
- K. Hoggas, C. Nouveau, A. Djelloul and M. Bououdina, Structural, microstructural, and optical properties of Zn1−xMgxO thin films grown onto glass substrate by ultrasonic spray pyrolysis, Appl. Phys. A: Mater. Sci. Process., 2015, 120, 745–755 CrossRef CAS.
- W. S. Choi and J.-G. Yoon, Optical characterization of band gap graded ZnMgO films, Solid State Commun., 2012, 152, 345–348 CrossRef CAS.
- K. Vijayalakshmi and A. Renitta, Enhanced H2 sensing performance presented by Mg doped ZnO films fabricated with a novel ITO seed layer, J. Mater. Sci.: Mater. Electron., 2015, 26, 3458–3465 CrossRef CAS.
- M. Sahal, B. Marí, M. Mollar and F. J. Manjón, Zn1−xMgxO thin films deposited by spray pyrolysis, Phys. Status Solidi C, 2010, 7, 2306–2310 CrossRef CAS.
- T. Terasako, S. Shirakata and T. Kariya, Photoluminescence from highly oriented MgxZn1−xO films grown by chemical spray pyrolysis, Thin Solid Films, 2002, 420, 13–18 CrossRef.
- E. Diler, S. Rioual, B. Lescop, D. Thierry and B. Rouvellou, Stability of ZnMgO oxide in a weak alkaline solution, Thin Solid Films, 2012, 520, 2819–2823 CrossRef CAS.
- X. Zhang, X. M. Li, T. L. Chen, C. Y. Zhang and W. D. Yu, p-type conduction in wide-gap Zn1−xMgxO films grown by ultrasonic spray pyrolysis, Appl. Phys. Lett., 2005, 87, 092101 CrossRef.
- H. Zhang, T. Zhao, G. Hu, L. Miao and Y. Yang, Role of Mg doping on morphology and photoluminescence features of MgxZn1−xO films prepared by ultrasonic spray pyrolysis, J. Mater. Sci.: Mater. Electron., 2012, 23, 1933–1937 CrossRef CAS.
- K. Yoshino, S. Oyama and M. Yoneta, Structural, optical and electrical characterization of undoped ZnMgO film grown by spray pyrolysis method, J. Mater. Sci.: Mater. Electron., 2008, 19, 203–209 CrossRef CAS.
- A. J. Kulandaisamy, J. R. Reddy, P. Srinivasan, K. J. Babu, G. K. Mani, P. Shankar and J. B. B. Rayappan, Room temperature ammonia sensing properties of ZnO thin films grown by spray pyrolysis: Effect of Mg doping, J. Alloys Compd., 2016, 688, 422–429 CrossRef CAS.
- S. Kurtaran, S. Aldag, G. Ofofoglu, I. Akyuz and F. Atay, Transparent conductive ZnO thin films grown by chemical spray pyrolysis: the effect of Mg, J. Mater. Sci.: Mater. Electron., 2016, 27, 8478–8485 CrossRef CAS.
- P. Ravirajan, A. M. Peiró, M. K. Nazeeruddin, M. Graetzel, D. D. C. Bradley, J. R. Durrant and J. Nelson, Hybrid Polymer/Zinc Oxide Photovoltaic Devices with Vertically Oriented ZnO Nanorods and an Amphiphilic Molecular Interface Layer, J. Phys. Chem. B, 2006, 110, 7635–7639 CrossRef CAS PubMed.
- J. X. Wang, X. W. Sun, Y. Yang, H. Huang, Y. C. Lee, O. K. Tan and L. Vayssieres, Hydrothermally grown oriented ZnO nanorod arrays for gas sensing applications, Nanotechnology, 2006, 17, 4995 CrossRef CAS.
- M. Ding, Z. Guo, L. Zhou, X. Fang, L. Zhang, L. Zeng, L. Xie, H. Zhao, M. Ding, Z. Guo, L. Zhou, X. Fang, L. Zhang, L. Zeng, L. Xie and H. Zhao, One-Dimensional Zinc Oxide Nanomaterials for Application in High-Performance Advanced Optoelectronic Devices, Crystals, 2018, 8, 223 CrossRef.
- İ. Polat, S. Yılmaz, E. Bacaksız, Y. Atasoy and M. Tomakin, Synthesis and fabrication of Mg-doped ZnO-based dye-synthesized solar cells, J. Mater. Sci.: Mater. Electron., 2014, 25, 3173–3178 CrossRef.
- T.-H. Fang and S.-H. Kang, Preparation and characterization of Mg-doped ZnO nanorods, J. Alloys Compd., 2010, 492, 536–542 CrossRef CAS.
- N. Winkler, S. Edinger, J. Kaur, R. A. Wibowo, W. Kautek and T. Dimopoulos, Solution-processed all-oxide solar cell based on electrodeposited Cu2O and ZnMgO by spray pyrolysis, J. Mater. Sci., 2018, 1–13 Search PubMed.
- R. D. Shannon, Revised effective ionic radii and systematic studies of interatomic distances in halides and chalcogenides, Acta Crystallogr., Sect. A: Cryst. Phys., Diffr., Theor. Gen. Crystallogr., 1976, 32, 751–767 CrossRef.
- Y. Cai, X. Li, P. Sun, B. Wang, F. Liu, P. Cheng, S. Du and G. Lu, Ordered ZnO nanorod array film driven by ultrasonic spray pyrolysis and its optical properties, Mater. Lett., 2013, 112, 36–38 CrossRef CAS.
- U. Alver, T. Kılınç, E. Bacaksız, T. Küçükömeroğlu, S. Nezir, İ. H. Mutlu and F. Aslan, Synthesis and characterization of spray pyrolysis Zinc Oxide microrods, Thin Solid Films, 2007, 515, 3448–3451 CrossRef CAS.
- E. Kärber, T. Raadik, T. Dedova, J. Krustok, A. Mere, V. Mikli and M. Krunks, Photoluminescence of spray pyrolysis deposited ZnO nanorods, Nanoscale Res. Lett., 2011, 6, 359 CrossRef PubMed.
- T. Arii and A. Kishi, The effect of humidity on thermal process of zinc acetate, Thermochim. Acta, 2003, 400, 175–185 CrossRef CAS.
- F. Hewitt, D. E. Rhebat, A. Witkowski and T. R. Hull, An experimental and numerical model for the release of acetone from decomposing EVA containing aluminium, magnesium or calcium hydroxide fire retardants, Polym. Degrad. Stab., 2016, 127, 65–78 CrossRef CAS.
- O. F. Z. Khan and P. O’Brien, On the use of zinc acetate as a novel precursor for the deposition of ZnO by low-pressure metal-organic chemical vapour deposition, Thin Solid Films, 1989, 173, 95–97 CrossRef CAS.
- L. Hiltunen, M. Leskelä, M. Mäkelä and L. Niinistö, Crystal Structure of mu4-Oxo-hexakis(mu-acetato)tetrazinc and Thermal Studies of its Precursor, Zinc Acetate Dihydrate, Acta Chem. Scand., 1987, 41a, 548–555 CrossRef.
- C. W. Bock, A. K. Katz, G. D. Markham and J. P. Glusker, Manganese as a Replacement for Magnesium and Zinc:
Functional Comparison of the Divalent Ions, J. Am. Chem. Soc., 1999, 121, 7360–7372 CrossRef CAS.
- T. Dudev and C. Lim, Tetrahedral vs Octahedral Zinc Complexes with Ligands of Biological Interest:
A DFT/CDM Study, J. Am. Chem. Soc., 2000, 122, 11146–11153 CrossRef CAS.
- S. Shanmugan and D. Mutharasu, Thermal analysis of Mg doped ZnO nano particles as filler in epoxy for thermal interface material in led packaging, J. Optoelectron. Biomed. Mater., 2016, 8, 1–7 Search PubMed.
- T. Tsubota, M. Ohtaki, K. Eguchi and H. Arai, Transport properties and thermoelectric performance of (Zn1−yMgy)1−xAlxO, J. Mater. Chem., 1998, 8, 409–412 RSC.
- S. Edinger, J. Bekacz, M. Richter, R. Hamid, R. A. Wibowo, A. Peić and T. Dimopoulos, Influence of the acetic acid concentration on the growth of zinc oxide thin films prepared by spray pyrolysis of aqueous solutions, Thin Solid Films, 2015, 594, 238–244 CrossRef CAS.
- J. Tauc, Optical properties and electronic structure of amorphous Ge and Si, Mater. Res. Bull., 1968, 3, 37–46 CrossRef CAS.
- A. Kaushal and D. Kaur, Effect of Mg content on structural, electrical and optical properties of Zn1−xMgxO nanocomposite thin films, Sol. Energy Mater. Sol. Cells, 2009, 93, 193–198 CrossRef CAS.
- E. Bingöl, F. Bozali, E. F. Keskenler, V. Nevruzoğlu and M. Tomakin, Influence of Substrate Type on Morphology and Photoluminescence Properties of ZnO Thin Films Prepared by Ultrasonic Spray Pyrolysis Method, Turk. J. Mater., 2016, 1, 19–24 Search PubMed.
- S. M. Thahab, A. H. Omran Alkhayat and S. M. Saleh, Influence of substrate type on the structural, optical and electrical properties of CdxZn1−xS MSM thin films prepared by Spray Pyrolysis method, Mater. Sci. Semicond. Process., 2014, 26, 49–54 CrossRef CAS.
- I. Oja Acik, A. Junolainen, V. Mikli, M. Danilson and M. Krunks, Growth of ultra-thin TiO2 films by spray pyrolysis on different substrates, Appl. Surf. Sci., 2009, 256, 1391–1394 CrossRef CAS.
Footnote |
† Electronic supplementary information (ESI) available. See DOI: 10.1039/c8tc06097e |
|
This journal is © The Royal Society of Chemistry 2019 |
Click here to see how this site uses Cookies. View our privacy policy here.