Intensified ozonolysis of lignins in a spray reactor: insights into product yields and lignin structure†
Received
1st March 2019
, Accepted 26th April 2019
First published on 26th April 2019
Abstract
We demonstrate a simple spray reactor for an ozonolysis pretreatment step to cleave carbon–carbon double bonds in grass lignins to conveniently recover vanillin and p-hydroxybenzaldehyde (∼5 wt% of the lignin), two of the most value-added monomers. Lignin dissolved in an acid solution is sprayed into an ozone containing gas stream at ambient temperatures with contact times of less than 10 seconds. The production rate of these valuable species is between one to two orders of magnitude greater than that previously reported in a CSTR in which ozone is bubbled through a liquid phase containing dissolved lignin. The spray reactor thus significantly intensifies the reaction alleviating liquid-phase ozone starvation experienced in the CSTR. Gel permeation chromatography of the ozone-pretreated lignin reveals a decrease in the molecular weight distribution of macromolecular components corresponding to the recovered monomers. Scanning electron microscopy of the ozone-pretreated lignin reveals that the lignin superstructure is largely preserved as evidenced by the presence of globular assemblages in both the untreated and ozone-pretreated lignin. Thus, a mild ozone pretreatment of grass lignins in a spray reactor allows for the recovery of valuable aromatics without overoxidation of the products or unwanted bleaching of the bulk lignin.
Introduction
Lignins are biopolymers as varied as their plant sources and represent the second most abundant renewable biomass after cellulose.1 Lignin is also the most abundant renewable source of aromatics followed by tannins and phenolic lipids.2 Because of its chemical and structural diversity, lignin valorization remains a key challenge for realizing a viable biomass based economy.3,4 Accordingly, it has attracted attention from academia and industry alike to derive various products from its degradation and depolymerization.3,5–7 Lignins are typically comprised of polymerized monolignols and their derivatives.8,9 Grass lignins have an abundance of alkenes compared to hard- and softwoods and some have been demonstrated to yield up to 10–15% by weight aldehydes including vanillin (3-methoxy-4-hydroxybenzladehyde) when the lignins are oxidized using air as an oxidant.10,11 Vanillin is the main component of the vanilla aroma which commands the second highest value among flavoring agents after saffron.12–14
Ozone is a powerful non-persistent oxidant that decomposes into molecular oxygen and as such it is considered a “green” oxidant.15 It will oxidize most organic compounds, but preferentially reacts with alkenes via the Criegee mechanism.16 With some lignins, it has been shown to afford aromatic aldehydes13,17 and several methods have been reported for lignin ozonolysis and continuous ozonolysis.13,18–21 Some of these methods are aimed at structurally modifying the lignin.21,22 Alkene ozonolysis in neutral pH media follows the Criegee mechanism characterized by the presence of secondary ozonides (Fig. 1).16 The 1,2,4-trioxolane intermediates can decompose in polar and protic solvents. This exothermic decomposition of molecular ozonides can lead to reaction runaway if not properly controlled by either dilution of the reactants and/or appropriate cooling strategies.23,24 Mechanistic studies indicate that hydration of the carbonyl oxide (Criegee intermediate) can inhibit secondary ozonide formation.25,26 While industrial Kraft processes use alkaline solutions to dissolve lignin, more recent organosolv lignin extraction methods use organic solvents, such as acetic acid in the acetosolv process.3,27,28 Ozonolysis in acidic media should inhibit the formation of secondary ozonides and enhance process safety.
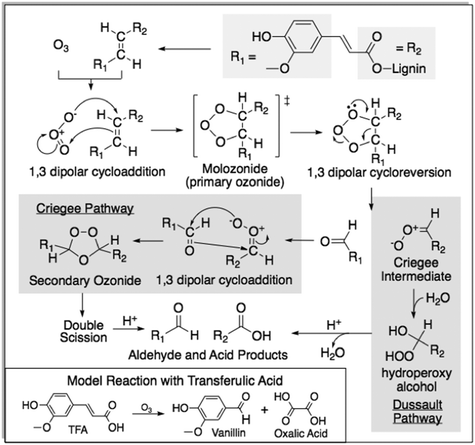 |
| Fig. 1 Reaction pathways of the Criegee intermediate from the ozonolysis of grass lignin in acid media.16,29,30 | |
Most reported lignin depolymerization techniques yield complex mixtures of small molecules that are challenging to separate or analyze.31,32 Clearly, it is desirable to deconstruct lignin in a methodical manner to sequentially strip away value-added chemicals yielding simpler product mixtures.3,33 In this context, we recently demonstrated the ozonolysis of grass lignins in a continuous stirred tank reactor (CSTR) to selectively cleave pendant aromatic groups.7 The liquid phase residence time must be limited to a few minutes in order to prevent overoxidation of the products and the bulk lignin by ozone. Given that ozonolysis reactions are relatively fast, there can be ozone starvation in the liquid phase of the CSTR due to gas-to-liquid mass transfer limitations. Herein, we develop a continuous spray reactor for the ozonolysis of grass and hardwood lignins in order to selectively yield 4-hydroxybenzaldehyde and/or vanillin while preserving the lignin superstructure. Unlike the CSTR where the ozone was sparged into the liquid phase, the lignin solution was sprayed as droplets against an air stream containing ozone in the spray reactor. This design serves two important purposes: (i) to increase the interfacial surface area between the liquid and gas phases, and thereby minimize ozone starvation in the liquid phase;34–36 and (ii) to facilitate better control of the contact time between the gas and the liquid phases to prevent both overoxidation of the value-added aldehydes (vanillin and 4-hydroxybenzaldehyde) into acids and the destruction of the remaining lignin structure via bleaching.13,37 Furthermore, it is of interest to also discern the effect of ozone pretreatment on lignin's macromolecular structure and potential implications for downstream processing and further deconstruction of lignin.38
Materials
Glacial acetic acid (99.5%), formic acid (88%), methanol (GC grade), ethyl acetate, and ethanol (HPLC grade) were purchased from TCI America. Two extracted and dried acetosolv grass lignin powders from corn stover (G1 and G2) were provided by Archer Daniels Midland (ADM) Company while alkaline (H1) and dealkaline (H2) hardwood lignins were purchased from Sigma Aldrich and TCI America respectively. Trans-ferulic acid and chromatography standards were purchased from Sigma Aldrich and used without further purification.
Methods
Ozonolysis of sprayed lignin in acids
Dry lignin (5.00 g) was added to 500 mL of 3
:
1 v
:
v mixture of glacial acetic acid and formic acid. The mixture was stirred overnight and filtered to remove any remaining particulate matter. The spray reactor consisted of an ISCO model 500D syringe pump equipped with a Teledyne ISCO D-series controller that pumps the reaction mixture through a spray nozzle (MW085 Bete MicroWhirl Nozzle, 70 μm diameter filter) located at the bottom of a 4-liter glass chamber (Fig. 2). The reactor temperature was monitored with a four-point thermocouple probe interfaced with a LabView Data Acquisition System. The mixture was sprayed at a rate between 50–125 mL min−1 into the reactor at ambient temperature (20 °C), filled with flowing ozone (150–200 std L h−1 containing 1–7.5 mol% ozone in air corresponding to 20–80% of the maximum voltage) generated from a Praxair Trailigaz Unizone Lo ozone generator. At standard operating conditions of 180 std L h−1 and 50% of the maximum voltage, the ozone is estimated to be at a four-fold molar excess compared to aldehydes in the lignin.10 The spray creates a fine mist which suspends in and fills the reactor without causing any liquid holdup at the bottom of the reactor. Below the lower limit of the flow rate range (<50 mL min−1), the spray created a stream of liquid which coated the reactor walls with a film. At higher flow rates (>125 mL min−1), the spray created a mist but also caused liquid pooling in the reactor that increased the contact time with ozone. The ozone-pretreated liquid stream exits the reactor at the bottom and is collected in 10 mL fractions for analysis. The gas stream exits at the top of the reactor avoiding further contact with the liquid stream and was vented through a solution of sodium hydroxide and hydrogen peroxide in methanol to decompose any remaining ozone to oxygen.39 The reactor was rinsed with acetic acid before and after experiments.
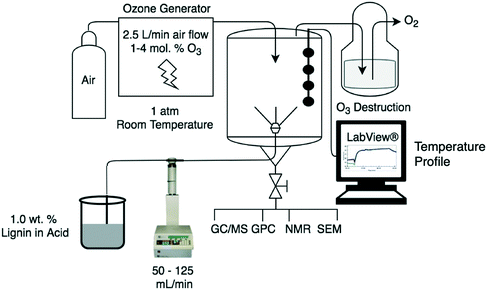 |
| Fig. 2 Schematic of the spray reactor. | |
Fractionation of ozonized lignin products
Ozonized lignin solutions were taken directly from the spray reactor and the acid solvent was removed in a rotary evaporator for reuse. The dry dark brown concentrate was washed with ethyl acetate (50 mL solvent/1 g solid product) and stirred overnight. The solution was filtered to separate a dark brown high molecular weight (HMW) solid filtrate and an orange colored mixture of low molecular weight (LMW) extracts (Fig. 3).
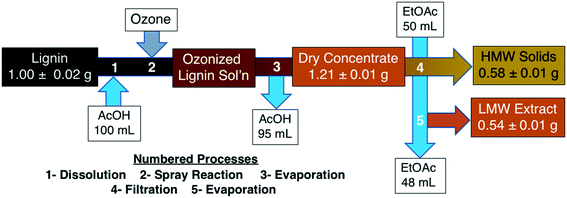 |
| Fig. 3 Schematic representation of grass lignin ozonolysis, workup, and fractionation. | |
trans-Ferulic acid model compound reactions
trans-Ferulic acid (1.00 g) was dissolved in 100 mL of a solvent (formic or acetic acid) and sprayed at 75 mL min−1 against an ozone containing stream (2.5 mol% ozone in air) flowing at 180 std L h−1. Collected effluent samples were analyzed following dilution in methanol [10
:
3 methanol
:
(reaction mixture) v/v] by gas chromatography, and solvent evaporation and redissolution in either dimethyl formamide (1 mL) for gel permeation chromatography (GPC) or dimethylsulfoxide (100 mg/700 μL DMSO) for NMR spectroscopy.
Analytical methods
Methods for gas and gel permeation chromatography (GC and GPC), along with nuclear magnetic resonance spectroscopy (NMR), scanning electron microscopy (SEM), and data processing are included in the ESI† (Methods).
Results
Spray reactor design
When ozone is dispersed in a liquid phase containing dissolved lignin (as done in the CSTR),7 ozone availability is likely to be limiting given that ozonolysis reactions are relatively fast and ozone solubility in the liquid phase is low.40 On the other hand, atomizing the liquid solution into an ozone containing gas phase increases the interfacial area between the liquid and gas phases (ESI† Table S1). Each atomized droplet may be viewed as a micro-reactor with an approximate droplet radius of 35 μm, achieved with commercial spray nozzles.37 In such a droplet comprised of the reaction solvent mixture, the diffusion time for ozone to completely permeate the droplet is approximately 1.1 seconds at 20 °C (ESI† Calc S1).37,41 The sprayed droplets eventually coalesce forming a bulk liquid phase that continuously exits the reactor. Following product separation in a rotary evaporator, the solvent (acetic and formic acid) is recycled.
At a spray rate of 75 mL min−1, the approximate residence time of the sprayed liquid phase in the reactor is determined to be 8.3 ± 3 seconds (ESI† eqn S1), of the same order as the diffusion time scale of ozone into the spray droplet. By allowing the ozone-containing gas stream to exit at the top of the reactor, side reactions such as aldehyde oxidation to an acid are minimized.
Ozonolysis reactions are exothermic. To prevent reaction runaway, low lignin concentrations (1.0 wt% in solution) were maintained to limit the rate of heat generation. The reactor temperature was effectively maintained at the operating temperatures (17–23 °C), indicating that the heat of reaction is effectively absorbed by the feed stream dominated by acetic acid (Fig. S1†). The several temporal temperature profiles in Fig. S1† show that the spray reactor system reproducibly reaches a steady state in a few minutes. At the reaction temperature (∼20 °C), the concentrations of acetic acid and the main aldehydic products in the vapor phase are below their lower flammability limits due to their low vapor pressures.42
Characterization and fractionation of various product fractions from spray ozonolysis
During the spray ozonolysis of acid solubilized lignins, the composition of the effluent stream attains a steady state in approximately one minute following start of the spray as inferred from vanillin concentrations via GC-FID (Fig. S1†). The steady state aromatic aldehyde concentrations in the reactor effluent shows an increase compared to those in the feed (Table 1). Ozone pretreatment yields approximately fourfold more vanillin from grass lignin samples G1 and G2 compared to the vanillin content in the unreacted grass lignins. As expected, the vanillin content in hardwood lignins (H1 and H2) is significantly lower than in the grass lignins. Ozonolysis of the hardwood lignins yields a ∼1.5× increase in vanillin content compared to that in the unreacted lignin. This is to be expected as the hardwood lignins do not contain the pendant aromatic groups.
Table 1 Comparison of aldehyde monomer yields (wt%) from the spray ozonolysis of acid-solubilized lignins (T ∼ 20 °C; feed flow rate = 75 mL min−1; lignin concentration in feed = 1.0 wt%; air flow rate = 180 std L min−1; O3 concentration in air = 2.5 mol%)
Lignin |
Vanillin |
4-Hydroxybenzaldehyde |
Total aromatic aldehydes |
Unreacted G1 |
0.27 ± 0.08 |
0.10 ± 0.01 |
0.38 ± 0.08 |
Ozonized G1 |
1.6 ± 0.1 |
3.2 ± 0.1 |
4.8 ± 0.1 |
Unreacted G2 |
0.28 ± 0.03 |
0.12 ± 0.03 |
0.41 ± 0.04 |
Ozonized G2 |
1.2 ± 0.1 |
3.6 ± 0.2 |
4.8 ± 0.1 |
Unreacted H1 |
0.087 ± 0.04 |
Not detected (n.d.) |
0.087 ± 0.04 |
Ozonized H1 |
0.12 ± 0.03 |
n.d. |
0.12 ± 0.03 |
Unreacted H2 |
0.56 ± 0.04 |
n.d. |
0.56 ± 0.04 |
Ozonized H2 |
0.68 ± 0.03 |
n.d. |
0.68 ± 0.03 |
The yield of a particular product aldehyde is defined as the mass ratio of the aldehyde in the product solution relative to the lignin fed. Based on this definition, the yield of 4-hydroxybenzaldehyde (4HB) is approximately two- to threefold greater than that of the vanillin yield. The total yield of aromatics from the ozonolysis of grass lignins is several fold greater than that from hardwood lignins and similar to other reports.9,11,13
It is noteworthy that similar vanillin and 4HB yields are obtained with ozonolysis in acetic acid solutions in the CSTR with contact times on the order of minutes.13 As the feed flow rates in the spray reactor (50–125 mL min−1) are several times greater than those reported for the CSTR system (0.71–14.2 mL min−1), the production rates in the spray reactor are accordingly between one to two orders of magnitude greater than those achieved in the CSTR (ESI† Calc S2). Clearly, the spray reactor intensifies the ozonolysis reaction by significantly alleviating liquid-phase ozone starvation that exists in the CSTR.
LMW aromatics from the ozone-pretreated lignin mixtures were extracted using ethyl acetate and dried alongside the filtered HMW solids insoluble in ethyl acetate. The ozonized reaction mixtures as well as the LMW and HMW fractions were characterized via GC-FID (ESI† Fig. S2, Table S2 and S3), and NMR analyses (ESI† Fig. S3–S6). GPC results (Fig. 4) indicate that LMW extract species with peaks ranging from ∼150–22 kDa are separated after solvent extraction. Further, the molecular weight distribution of the ozonized HMW lignin solids isolated from filtration display only a slight shift compared to the lignin feed solution, commensurate with the separation of the LMW species. This suggests that the original lignin structure is largely preserved and available for further valorization via catalytic depolymerization.6,43
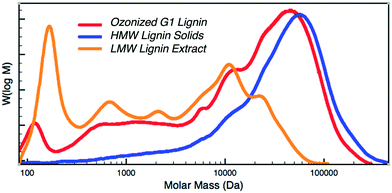 |
| Fig. 4 Gel permeation chromatograms of ozonized G1 lignin before and after fractionation highlighting a separation of low and high molecular weight species (operating conditions same as those in Table 1). | |
After separation of the HMW solids following extraction, the dissolved low molecular weight extract may be more easily separated into monomers and oligomers for the further valorization of the extract.13,44 The potential value of the vanillin and 4-hydroxybenzaldehyde thus recovered is conservatively estimated to be around $2.50 per gallon of cellulosic ethanol produced (see ESI† Calc S3). The remaining ozone-pretreated lignin can also be further valorized to make renewable materials such as polymers.45 These product streams thus have the potential to significantly improve the economics and viability of lignocellulosic (here ‘cellulose-first’) biorefineries.46
Evident in the NMR spectra of unreacted lignins are prominent guaiacolic and coumarate peaks in hardwood and grass lignin samples, respectively (Fig. 5). Ozone-pretreated lignins, LMW extracts and filtered solids (HMW) were dried and dissolved in deuterated solvent for one and two dimensional 1H/13C heteronuclear single quantum coherence (HSQC) NMR analysis. While the aldehyde products (H and V) are prominent in the spectra of the ozone-pretreated lignin solution, minor coumarate and guaiacolic peaks remain in the dried solid products (Fig. 5 and 6). While aromatic acid byproducts are not detectable by HSQC NMR, several peaks (labeled Z) corresponding to the predicted chemical shifts for secondary ozonides are observed. These observations are similar to those observed from CSTR ozonolysis reported recently.13 Evident in the 1D and 2D spectra of the LMW extracts were sharp peaks identifying the aldehydes, and the retention of prominent carbon–oxygen bonded atoms in the fractioned lignin solids (Fig. 6 and ESI† Fig. S3 and S4). This is consistent with the previous observation that the structure of the original lignin is largely preserved following ozone pretreatment.
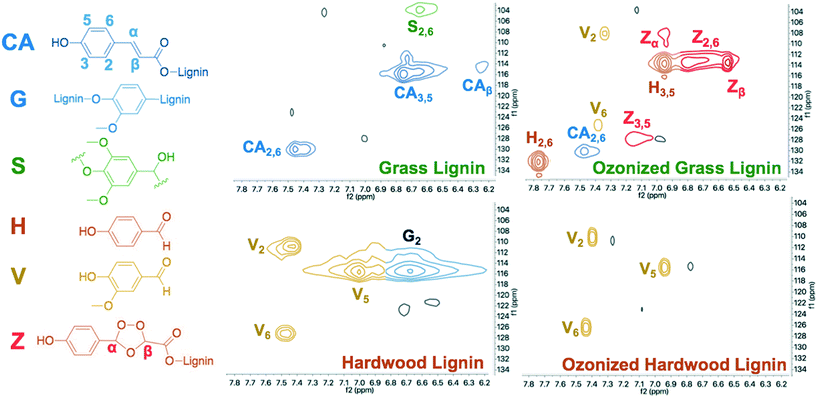 |
| Fig. 5
13C (f1) and 1H (f2) HSQC 2D NMR of grass and hardwood lignins and their reacted samples highlighting carbon-hydrogen bonded nuclei. Prominent peaks are identified for pendant reactants and aldehyde products. Weak ozonide peaks indicate the intermediate in solution (operating conditions are provided in Table 1). | |
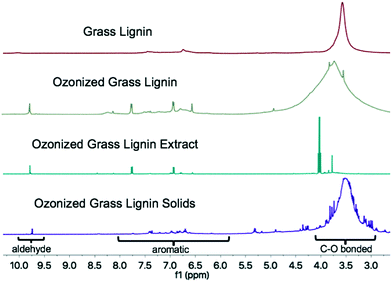 |
| Fig. 6 Comparison of 1H-NMR of grass lignin before and after ozonation and fractionation indicating the production of aldehydes and the solid fraction's retention of C–O bond character (operating conditions are provided in Table 1). | |
Insights into ozonolysis mechanism
To better understand the underlying mechanism and low formation of the secondary ozonides, trans-ferulic acid (TFA) was chosen as a model compound due to its prevalence in solubilized grass lignin mixtures. Spray ozonolysis of TFA in acetic acid, at conditions identical to those employed for grass lignins, afforded high vanillin yields with only a minor presence (<0.1 wt%) of vanillic acid byproduct (Table 2). Even though both the feeds contain 1.0 wt% substrate, the concentration of pendant groups in lignin, which contain compounds similar to TFA, is relatively small (∼10 wt%).10,11 Hence, the yield of aromatics from TFA is an order of magnitude higher compared to the observed yield from lignin. As secondary ozonides are often difficult to isolate for analysis, reaction mixture from TFA ozonolysis was first analyzed by HSQC NMR spectroscopy in DMSO to help identify and quantify ozonide peaks (Fig. 7).17 Guided by this information, spectra from grass lignin were evaluated to identify ozonide peaks that typically occur at concentrations lower than the aromatic aldehyde products (see ESI,† Fig. S7 and Table S4). The dominance of the aldehyde products and the lack of corresponding acids in stoichiometrically equivalent amounts suggest that the lignin solvent (acetic acid) reacts with the Criegee Intermediate following the Dussault pathway preventing the formation of secondary ozonides.30
Table 2 Comparison of product yields before and after ozonolysis of 1.0 wt% solutions of trans-ferulic acid and lignins in acetic acid (with all other operating conditions the same as those provided in Table 1)
Aromatic yields (wt%) |
Sample (in acetic acid) |
Vanillin |
Vanillic acid |
4-Hydroxy benzaldehyde |
4-Hydroxy benzoic acid |
Total aromatics |
TFA |
8.2 ± 0.5 |
2.2 ± 0.7 |
Not detected (n.d.) |
n.d. |
10 ± 1 |
Ozonized TFA |
79 ± 7 |
12 ± 2 |
n.d. |
n.d. |
91 ± 7 |
G1 lignin |
0.34 ± 0.04 |
0.02 ± 0.01 |
0.19 ± 0.05 |
0.04 ± 0.01 |
0.59 ± 0.07 |
Ozonized G1 lignin |
1.7 ± 0.2 |
0.04 ± 0.01 |
3.4 ± 0.1 |
0.10 ± 0.02 |
5.2 ± 0.1 |
H1 lignin |
0.12 ± 0.02 |
0.06 ± 0.01 |
n.d. |
n.d. |
0.18 ± 0.02 |
Ozonized H1 lignin |
0.16 ± 0.03 |
0.07 ± 0.02 |
n.d. |
n.d. |
0.23 ± 0.04 |
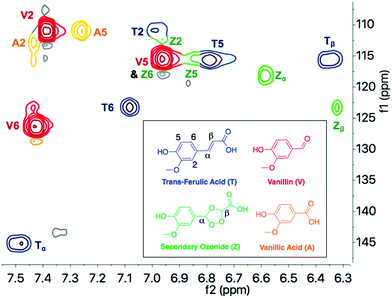 |
| Fig. 7
13C (f1) and 1H(f2) 2D HSQC NMR of the reaction mixture of ozonized trans-ferulic acid highlighting the vanillin product (red) and minor components of unreacted trans-ferulic acid (blue), secondary ozonide intermediate (green), and vanillic acid byproduct (orange). Operating conditions are the same at those in Table 1 for 1.0 wt% solutions of TFA. | |
We also performed parametric variation studies to understand the effects of the liquid feed flow rates and ozone on the product yields. At a fixed feed flow rate (75 mL min−1), increasing the ozone concentration from 2.5 to 5.0 mol% in air results in a notable downward shift in the ∼100 kDa peak to ∼50 kDa in the case of grass lignin G1 (ESI† Fig. S8). A further increase in the ozone concentration to 7.5 mol% also results in the oxidation of the desirable aldehydes as evident from GC-FID data (ESI† Table S5). At low ozone concentrations (2.0 mol% in air), decreasing the flowrate from 125 mL min−1 to 50 mL min−1 affords higher aldehyde yields (ESI† Fig. S9 and Table S6), as a result of increased residence times. Clearly, there exist optimum combinations of ozone concentration and feed flow rates at which the formation of the desired aldehydes is maximized while also preserving the lignin structure. Systematic optimization studies are essential for rational process design and scaleup.
The effect of ozonolysis on lignin macromolecules
The GPC spectra reveal a decrease in the molar mass of the constituent lignin species after ozonolysis (Fig. 8, ESI† Table S7). Gel permeation chromatography of representative grass (G1 & G2) and hardwood (H1 & H2) lignins are compared in Fig. 8A–D respectively. Peak 1 for unreacted lignin samples represents lignin unit structures or ‘globules’.47,48 G1 samples exhibit a new peak (starred in Fig. 8A) with a corresponding mass of ∼6900 Da indicative of deconstructed lignin unit.49,50 Hardwood lignin (H1 and H2) peaks shift less than those for grass lignins due to the absence of pendant alkenes. We envision that while ozone is consumed by the alkenes in grass lignin solutions, the paucity of such alkenes in the hardwood lignin samples allows ozone to attack other bonds, leading to a more drastic deconstruction of the larger lignin species as observed with peak 4 (∼100 kDa) in hardwood samples, resulting in a ∼30 kDa downward shift. The relatively mild shift in peak 1 in G1 lignin from 13.6 kDa to 11.8 kDa following ozonolysis is attributed to the liberation of pendant groups from a globular unit of lignin (intraunit scission),51,52 while the shifts in the higher molecular mass lignin components in hardwoods (peaks 4 & 5) following ozonolysis can be explained by scission involving a linkage between two lignin units (interunit scission) as well as intraunit scissions. This conceptualization is based on work reported on actual lignin and polymerized model compounds demonstrating that lignin forms globular units which chemically join to form its diverse fractal and irregular structures.53–56 It is interesting to note that magnitude of peak 1 in unreacted grass lignins is approximately 20% greater than peak 1 in hardwood species which may be due to both the prevalence of pendant groups, and differences in the abundance of monolignol components.57,58
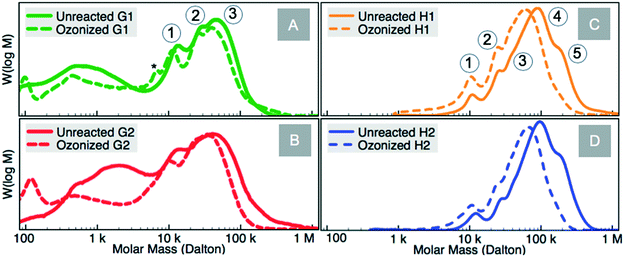 |
| Fig. 8 A–D Gel permeation chromatograms of grass and hardwood lignins before and after ozonolysis with the peaks >10 kDa labeled (conditions provided in Table 1). | |
While the ozone-pretreated lignin does undergo discernable structural changes, the foregoing GPC results are consistent with the NMR results that show that the lignin structure is largely preserved. Scanning electron micrographs of H1 and G2 lignin before and after ozonolysis also confirm this conclusion by revealing agglomerated and coalesced spheroidal structures (Fig. 9, ESI† Fig. S10). The structure of the ozonized lignin is similar to the unreacted lignin in that the assembly of smaller spheroidal structures into a macrostructure is still preserved (Fig. 9A). At increasing magnification, the lignin appears to be composed of ∼250 nm globular structures (Fig. 9B). Higher resolution SEM images reveal cracks within these globular structures and still smaller (∼10 nm diameter) globular species suggesting that the molecular weight distribution revealed by the GPC is a reflection of assemblies of the smaller components observed via GPC (Fig. 9C).47,48 While these SEM images may not reveal the smallest modular unit, the hierarchical nature of the assemblies observed from the images strongly suggest the prevalence of building blocks that organize into diverse structures.
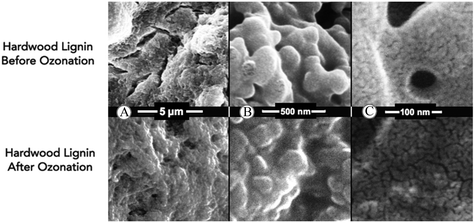 |
| Fig. 9 A–C: SEM of unreacted and ozonized H1 hardwood lignin demonstrating that mild ozone leaves pretreatment leaves behind morphologically similar lignin globule structures. | |
Conclusions
We demonstrate that intensified ozone pretreatment in a spray reactor at ambient temperatures and pressures can be an effective tool to partially deconstruct grass and hardwood lignins safely and efficiently. When acid dissolved lignins are sprayed into an ozone-laden air stream, the ozone penetrates the droplets to selectively cleave carbon–carbon double bonds associated with specific pendant groups in the grass lignins and structural linkages in hardwood samples. The products from the spray ozonolysis of grass lignin, vanillin and 4-hydroxybenzaldehyde, constitute approximately 5.0 wt% of the grass lignin may be easily extracted for further processing. Significantly, the productivity of these species is enhanced by up to an order of magnitude compared to ozonolysis in a CSTR at similar conditions. In contrast, the yield of the aldehyde monomers is low (∼1 wt%) when processing hardwood lignins, highlighting a major structural difference between these two lignins. The lack of abundant secondary ozonide intermediates and the formation of aromatic aldehyde monomers as the main products suggest that the acid solvents participate in the reaction, interrupting the commonly accepted Criegee mechanism. This hypothesis was verified by performing ozonolysis on trans-ferulic acid, a model compound present in the lignin matrix. Furthermore, gel permeation chromatography and scanning electron microscopy results reveal that the ozone-pretreated lignin is deconstructed at the micron and nanoscales while preserving modular components that make up the complex lignin structure.
Author contributions
BS and JS planned experiments and designed the spray reactor. AD and JS designed analytical methods and experiments. JS built the spray reactor and ran experiments. All authors contributed to writing and editing the manuscript.
Abbreviations
4HB | 4-Hydroxybenzaldehyde |
4HBA | 4-Hydroxybenzoic acid |
ADM | Archer Daniels Midland Company |
CSTR | Continuous stirred tank reactor |
Da | Dalton |
DMSO | Dimethylsulfoxide |
G1/G2 | Grass lignin samples |
GC | Gas chromatography |
GPC | Gel permeation chromatography |
H1/H2 | Hardwood lignin samples |
HMW | High molecular weight |
HSQC NMR | Heteronuclear single quantum correlation nuclear magnetic resonance spectroscopy |
kDa | Kilodalton |
LMW | Low molecular weight |
SEM | Scanning electron microscopy |
TCI | TCI Chemicals America |
TFA |
trans-Ferulic acid |
Conflicts of interest
There are no conflicts to declare.
Acknowledgements
This research was supported with funds from the National Science Foundation (OIA-1539105). The authors would like to thank Archer Daniels Midland for the supply of extracted organosolv lignins. JS would like to thank Michael Lundin for help interfacing the reactor with the data acquisition system, the University of Kansas Microscopy and Analytical Imaging laboratory for their help with SEM. Support for the NMR instrumentation was provided by an NIH Shared Instrumentation Grant #S10RR024664 and an NSF Major Research Instrumentation Grant #1625923.
References
-
F. E. Brauns and D. A. Brauns, The Chemistry of Lignin, Academic Press, 1960 Search PubMed.
- V. S. Balachandran, S. R. Jadhav, P. K. Vemula and G. John, Recent advances in cardanol chemistry in a nutshell: from a nut to nanomaterials, Chem. Soc. Rev., 2013, 42, 427–438 RSC.
- M. Fache, B. Boutevin and S. Caillol, Vanillin Production from Lignin and Its Use as a Renewable Chemical, ACS Sustainable Chem. Eng., 2016, 4, 35–46 CrossRef CAS.
- T. Parsell, S. Yohe, J. Degenstein, T. Jarrell, I. Klein, E. Gencer, B. Hewetson, M. Hurt, J. I. Kim, H. Choudhari, B. Saha, R. Meilan, N. Mosier, F. Ribeiro, W. N. Delgass, C. Chapple, H. I. Kenttämaa, R. Agrawal and M. M. Abu-Omar, A synergistic biorefinery based on catalytic conversion of lignin prior to cellulose starting from lignocellulosic biomass, Green Chem., 2015, 17, 1492–1499 RSC.
- E. Adler, Lignin chemistry—past, present and future, Wood Sci. Technol., 1977, 11, 169–218 CrossRef CAS.
- K. Y. Nandiwale, A. M. Danby, A. Ramanathan, R. V. Chaudhari and B. Subramaniam, Zirconium-Incorporated Mesoporous Silicates Show Remarkable Lignin Depolymerization Activity, ACS Sustainable Chem. Eng., 2017, 5, 7155–7164 CrossRef CAS.
- W. Schutyser, T. Renders, S. Van den Bosch, S.-F. Koelewijn, G. T. Beckham and B. F. Sels, Chemicals from lignin: an interplay of lignocellulose fractionation, depolymerisation, and upgrading, Chem. Soc. Rev., 2018, 47, 852–908 RSC.
- J. H. Clark, V. Budarin, F. E. I. Deswarte, J. J. E. Hardy, F. M. Kerton, A. J. Hunt, R. Luque, D. J. Macquarrie, K. Milkowski, A. Rodriguez, O. Samuel, S. J. Tavener, R. J. White and A. J. Wilson, Green chemistry and the biorefinery: a partnership for a sustainable future, Green Chem., 2006, 8, 853–860 RSC.
- M. B. Hocking, Vanillin: Synthetic Flavoring from Spent Sulfite Liquor, J. Chem. Educ., 1997, 74, 1055–1059 CrossRef CAS.
- J. Ralph, J. H. Grabber and R. D. Hatfield, Lignin-ferulate cross-links in grasses: active incorporation of ferulate polysaccharide esters into ryegrass lignins, Carbohydr. Res., 1995, 275, 167–178 CrossRef CAS.
- R. D. Hatfield, D. M. Rancour and J. M. Marita, Grass Cell Walls: A Story of Cross-Linking, Front. Plant Sci., 2017, 7, 2056 Search PubMed.
- N. Berenstein, Making a global sensation: Vanilla flavor, synthetic chemistry, and the meanings of purity, Hist. Sci., 2016, 54, 399–424 CrossRef PubMed.
- A. M. Danby, M. D. Lundin and B. Subramaniam, Valorization of Grass Lignins: Swift and Selective Recovery of Pendant Aromatic Groups with Ozone, ACS Sustainable Chem. Eng., 2018, 6, 71–76 CrossRef CAS.
- G. M. Lampman, J. Andrews, W. Bratz, O. Hanssen, K. Kelley, D. Perry and A. Ridgeway, Preparation of vanillin from eugenol and sawdust, J. Chem. Educ., 1977, 54, 776 CrossRef CAS.
- B. Subramaniam, Gas-expanded liquids for sustainable catalysis and novel materials: Recent advances, Coord. Chem. Rev., 2010, 254, 1843–1853 CrossRef CAS.
- R. Criegee, Mechanism of Ozonolysis, Angew. Chem., Int. Ed. Engl., 1975, 14, 745–752 CrossRef.
- M. D. Lundin, A. M. Danby, G. R. Akien, T. P. Binder, D. H. Busch and B. Subramaniam, Liquid CO2 as a Safe and Benign Solvent for the Ozonolysis of Fatty Acid Methyl Esters, ACS Sustainable Chem. Eng., 2015, 3, 3307–3314 CrossRef CAS.
- P. F. Vidal and J. Molinier, Ozonolysis of lignin — Improvement of in vitro digestibility of poplar sawdust, Biomass, 1988, 16, 1–17 CrossRef CAS.
- M. B. Plutschack, B. Pieber, K. Gilmore and P. H. Seeberger, The Hitchhiker's Guide to Flow Chemistry, Chem. Rev., 2017, 117, 11796–11893 CrossRef CAS PubMed.
-
French Ministry for Sustainable Development, Explosions in a pharmaceutical plant, 2003 Search PubMed.
- M. V. Bule, A. H. Gao, B. Hiscox and S. Chen, Structural Modification of Lignin and Characterization of Pretreated Wheat Straw by Ozonation, J. Agric. Food Chem., 2013, 61, 3916–3925 CrossRef CAS PubMed.
- N.-E. El Mansouri and J. Salvadó, Structural characterization of technical lignins for the production of adhesives: Application to lignosulfonate, kraft, soda-anthraquinone, organosolv and ethanol process lignins, Ind. Crops Prod., 2006, 24, 8–16 CrossRef CAS.
-
R. Sugiyama and T. Yamano, in Managing Hazardous Reactions and Compounds in Process Chemistry, American Chemical Society, 2014, vol. 1181, pp. 135–166 Search PubMed, SE–5.
-
M. Ullrich, P. Hannen and M. Roos, US Pat., 8 815 549, 2012 Search PubMed.
- Y.-T. Su, H.-Y. Lin, R. Putikam, H. Matsui, M. C. Lin and Y.-P. Lee, Extremely rapid self-reaction of the simplest Criegee intermediate CH2OO and its implications in atmospheric chemistry, Nat. Chem., 2014, 6, 477–483 CrossRef CAS PubMed.
- H. J. Tobias and P. J. Ziemann, Kinetics of the Gas-Phase Reactions of Alcohols, Aldehydes, Carboxylic Acids, and Water with the C13 Stabilized Criegee Intermediate Formed from Ozonolysis of 1-Tetradecene, J. Phys. Chem. A, 2001, 105, 6129–6135 CrossRef CAS.
-
E. Feghali and T. Cantat, US Pat., 10 081 644, 2014 Search PubMed.
- X. Pan, J. F. Kadla, E. Katsunobu, N. Gilkes and J. N. Saddler, Organosolv ethanol lignin from hybrid poplar as a radical scavenger:
relationship between lignin structure, extraction conditions, and antioxidant Activity, J. Agric. Food Chem., 2006, 54, 5806–5813 CrossRef CAS PubMed.
- O. Welz, A. J. Eskola, L. Sheps, B. Rotavera, J. D. Savee, A. M. Scheer, D. L. Osborn, D. Lowe, A. Murray Booth, P. Xiao, M. Anwar, H. Khan, C. J. Percival, D. E. Shallcross and C. A. Taatjes, Rate Coefficients of C1 and C2 Criegee Intermediate Reactions with Formic and Acetic Acid Near the Collision Limit: Direct Kinetics Measurements and Atmospheric Implications, Angew. Chem., Int. Ed., 2014, 53, 4547–4550 CrossRef CAS PubMed.
- C. E. Schiaffo and P. H. Dussault, Ozonolysis in Solvent/Water Mixtures: Direct Conversion of Alkenes to Aldehydes and Ketones, J. Org. Chem., 2008, 73, 4688–4690 CrossRef CAS PubMed.
- M. P. Pandey and C. S. Kim, Lignin depolymerization and conversion: a review of thermochemical methods, Chem. Eng. Technol., 2011, 34, 29–41 CrossRef CAS.
- J. Zakzeski, P. C. A. Bruijnincx, A. L. Jongerius and B. M. Weckhuysen, The Catalytic Valorization of Lignin for the Production of Renewable Chemicals, Chem. Rev., 2010, 110, 3552–3599 CrossRef CAS PubMed.
- Q. Liu, S. Wang, Y. Zheng, Z. Luo and K. Cen, Mechanism study of wood lignin pyrolysis by using TG–FTIR analysis, J. Anal. Appl. Pyrolysis, 2008, 82, 170–177 CrossRef CAS.
- A. Kornmüller and U. Wiesmann, Ozonation of polycyclic aromatic hydrocarbons in oil/water-emulsions: mass transfer and reaction kinetics, Water Res., 2003, 37, 1023–1032 CrossRef.
- J. P. Reid and R. M. Sayer, Heterogeneous atmospheric aerosol chemistry: laboratory studies of chemistry on water droplets, Chem. Soc. Rev., 2003, 32, 70–79 RSC.
- S. Raja and K. T. Valsaraj, Heterogeneous Oxidation by Ozone of Naphthalene Adsorbed at the Air-Water Interface of Micron-Size Water Droplets, J. Air Waste Manage. Assoc., 2005, 55, 1345–1355 CrossRef CAS.
- M. Li, F. Niu, X. Zuo, P. D. Metelski, D. H. Busch and B. Subramaniam, A spray reactor concept for catalytic oxidation of p-xylene to produce high-purity terephthalic acid, Chem. Eng. Sci., 2013, 104, 93–102 CrossRef CAS.
- J. S. Lupoi, S. Singh, R. Parthasarathi, B. A. Simmons and R. J. Henry, Recent innovations in analytical methods for the qualitative and quantitative assessment of lignin, Renew. Sustain. Energy Rev., 2015, 49, 871–906 CrossRef CAS.
- L. Forni, D. Bahnemann and E. J. Hart, Mechanism of the hydroxide ion-initiated decomposition of ozone in aqueous solution, J. Phys. Chem., 1982, 86, 255–259 CrossRef CAS.
- A. G. Khudoshin, A. N. Mitrofanova and V. V. Lunin, Lignin transformations and reactivity upon ozonation in aqueous media, Russ. J. Phys. Chem. A, 2012, 86, 360–365 CrossRef CAS.
- P. Johnson and R. A. Davis, Diffusivity of Ozone in Water, J. Chem. Eng. Data, 1996, 41, 1485–1487 CrossRef CAS.
-
Fisher Scientific and I. Global Safety Management, Acetic Acid Safety Data Sheet, https://beta-static.fishersci.com/content/dam/fishersci/en_US/documents/programs/education/regulatory-documents/sds/chemicals/chemicals-a/S25118.pdf, (accessed 18 February 2018) Search PubMed.
- J. Podschun, B. Saake and R. Lehnen, Reactivity enhancement of organosolv lignin by phenolation for improved bio-based thermosets, Eur. Polym. J., 2015, 67, 1–11 CrossRef CAS.
- M. I. F. Mota, P. C. Rodrigues Pinto, J. M. Loureiro and A. E. Rodrigues, Recovery of Vanillin and Syringaldehyde from Lignin Oxidation: A Review of Separation and Purification Processes, Sep. Purif. Rev., 2016, 45, 227–259 CrossRef CAS.
-
A. Hüttermann, A. Majcherczyk, C. Mai, A. Braun-Lüllemann, M. Fastenrath and S. Noetzold, WO Pat., 1998/031728A1, 1998 Search PubMed.
- I. Barrera, M. A. Amezcua-Allieri, L. Estupiñan, T. Martínez and J. Aburto, Technical and economical evaluation of bioethanol production from lignocellulosic residues in Mexico: Case of sugarcane and blue agave bagasses, Chem. Eng. Res. Des., 2016, 107, 91–101 CrossRef CAS.
- M. Micic, I. Benitez, M. Ruano, M. Mavers, M. Jeremic, K. Radotic, V. Moy and R. M. Leblanc, Probing the lignin nanomechanical properties and lignin–lignin interactions using the atomic force microscopy, Chem. Phys. Lett., 2001, 347, 41–45 CrossRef CAS.
- K. Radotić, M. Mićić and M. Jeremić, New Insights into the Structural Organization of the Plant Polymer Lignin, Ann. N. Y. Acad. Sci., 2005, 1048, 215–229 CrossRef PubMed.
- M. Micic, I. Benitez, M. Ruano, M. Mavers, M. Jeremic, K. Radotic, V. Moy and R. M. Leblanc, Probing the lignin nanomechanical properties and lignin–lignin interactions using the atomic force microscopy, Chem. Phys. Lett., 2001, 347, 41–45 CrossRef CAS.
- A. V. Gidh, S. R. Decker, T. B. Vinzant, M. E. Himmel and C. Williford, Determination of lignin by size exclusion chromatography using multi angle laser light scattering, J. Chromatogr. A, 2006, 1114, 102–110 CrossRef CAS PubMed.
- K. Ruel, V. Burlat and J.-P. Joseleau, Relationship Between Ultrastructural Topochemistry of Lignin and Wood Properties, IAWA J., 1999, 20, 203–211 Search PubMed.
-
S. Ralph, J. Ralph and L. Landucci, NMR Database of Lignin and Cell Wall Model Compounds, Madison, WI, 2009 Search PubMed.
- A. Karmanov and Y. Monakov, Lignin. Structural organisation and fractal properties, Russ. Chem. Rev., 2003, 72, 715–734 CrossRef CAS.
- M. Micic, K. Radotic, M. Jeremic and R. M. Leblanc, Study of Self-Assembly of the Lignin Model Compound on Cellulose Model Substrate, Macromol. Biosci., 2003, 3, 100–106 CrossRef CAS.
-
M. Micic, K. Radotic, M. Jeremic and R. M. Leblanc, Study of Self-Assembly of the Lignin Model Compound on Cellulose Model Substrate, Wiley-VCH Verlag, 2001, vol. 3 Search PubMed.
- J.-Y. Kim, E.-J. Shin, I.-Y. Eom, K. Won, Y. H. Kim, D. Choi, I.-G. Choi and J. W. Choi, Structural features of lignin macromolecules extracted with ionic liquid from poplar wood, Bioresour. Technol., 2011, 102, 9020–9025 CrossRef CAS PubMed.
- R. Hatfield and W. Vermerris, Lignin formation in plants. The dilemma of linkage specificity, Plant Physiol., 2001, 126, 1351–1357 CrossRef CAS PubMed.
- H. Chen and J. Kong, Terminal Index: A New Way for Precise Description of Topologic Structure of Highly Branched Polymers Derived from A2 + B3 Stepwise Polymerization, J. Phys. Chem. B, 2014, 118, 3441–3450 CrossRef CAS PubMed.
Footnote |
† Electronic supplementary information (ESI) available. See DOI: 10.1039/c9re00098d |
|
This journal is © The Royal Society of Chemistry 2019 |
Click here to see how this site uses Cookies. View our privacy policy here.