DOI:
10.1039/C9RA05490A
(Paper)
RSC Adv., 2019,
9, 35059-35067
Multifunctional lubricant additive based on difluoroboron derivatives of a diphenylamine antioxidant†
Received
17th July 2019
, Accepted 16th October 2019
First published on 30th October 2019
Abstract
A metal-free and phosphorus-free novel multifunctional additive (E)-4-((3-(tert-butyl)-2-((difluoroboranyl)oxy)-5-((octylthio)methyl)benzylidene)amino)-N-phenylaniline (difluoroboron derivative 4a) was synthesized and characterized. The results show that its antioxidation and tribological properties are better than those of base oil, diphenylamine and zinc dialkyldithiophosphate (ZDDP), and it can also increase the extreme pressure performance of the base oil. In addition, it can be found that the diphenylamine functional group, boron and fluorine are the main contributors to the excellent antioxidation and antiwear properties of difluoroboron derivative 4a, respectively. Finally, the results of X-ray photoelectron spectroscopy on the worn surfaces reveal that B2O3, Fe2O3, a N-containing organic compound and iron fluoride comprise the boundary films, which effectively improve the difluoroboron derivative 4a's antiwear properties.
1. Introduction
In order to reduce wear and friction and prolong the service life of mechanical systems, lubricants are widely used in industry.1 Multifunctional lubricant additives are a kind of lubricant additive with more than one property.2 Zinc dialkyldithiophosphate (ZDDP) is the most widely used multifunctional lubricant additive with excellent antioxidation, anticorrosive and antiwear abilities.3 However, SAPS (Sulfated ash, Phosphorous and Sulfur) of ZDDP are prone to reduce the life of automotive exhaust gas-treatment systems. In order to improve the compatibility of the emission system, strict laws restrict the use of ZDDP.4,5 For example, ILSAC GF-5 standards limit the phosphorous and sulfur contents in vehicle engine oil below 0.08% and 0.50%, respectively.6 Therefore, it is a progressive trend to develop new non-SAPS or low SAPS multifunctional lubricant additives without reducing the antioxidation and antiwear capabilities.7–9
Several kinds of compounds with low or zero SAPS has been studied, such as heterocyclic compounds,10–12 boron containing compounds,13–15 ionic liquids16,17 and nanoparticles.18–20 It is well known that antioxidants can improve the oxidation stability of lubricant. Modification of antioxidants with the active elements of B, S and P is a research hotspot of multifunctional lubricant additives, such as multifunctional Schiff bases (e.g. CySBE and TrBzEd),21–24 high performance multifunctional additive BHMT,10 N-containing borate ester BMEB (ref. 25) and imidazolium-based ionic liquids (e.g. (BHT-1)MIMBF4).26,27 As shown in Scheme 1, all the above works focus on the modification of hindered phenolic antioxidants. Diphenylamine has been widely used as the main free radical scavenger, but there are few multifunctional additives synthesized by modifying diphenylamine. Weimin Liu and co-authors have synthesized some novel multifunctional additives P-N compounds (Scheme 1) with better tribological behaviors than ZDDP.2 However, due to the removal of active H atom in diphenylamine, their antioxidation capacity is not significantly better than ZDDP. So, it is meaningful and challenging to synthesize a new high performance and low or zero SAPS multifunctional additive by modifying diphenylamine.
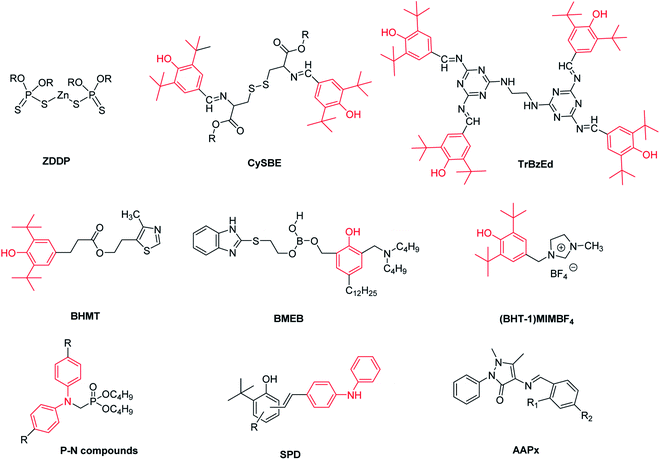 |
| Scheme 1 The structures of the related multifunctional additives and Schiff base compounds. | |
Recently, we have synthesized a series of Schiff base bridged phenolic diphenylamine (SPD, Scheme 1) antioxidants, which have better antioxidation performance than commercial antioxidants.28,29 It is interesting that synergistic antioxidation effect was found when combined with borate polyisobutylene succinimide (PIBSI) dispersant.28 Furthermore, it has been reported that the antiwear properties of lubricating oils can be greatly improved by the mixture or chemical synthesis of the Schiff bases (such as AAPx in Scheme 1) and borate esters.30–32 Thus, based on the great synergistic effect between Schiff base and borate, we designed and synthesized a new kind of coordinately saturated boron complex by combining N^O-bidentate ligands in SPD with B(III) fragment. Unlike the reported borate ester additives, BF2 was selected as the B(III) fragment due to the antiwear performance of fluorine containing compounds,26,33 facile synthesis and stable structure similar to Boranil complexes.34,35 The antioxidation and antiwear performances of the difluoroboron derivatives of SPD antioxidants as multifunctional additives were evaluated and discussed. To our delight, compared with the traditional ZDDP and the commercial antioxidant diphenylamine (DPA), the selected additive (E)-4-((3-(tert-butyl)-2-((difluoroboranyl)oxy)-5-((octylthio)methyl)benzy-lidene)amino)-N-phenylaniline (difluoroboron derivative 4a) has better wear resistance and oxidation resistance. As far as we know, this is the first time that boron, fluorine and diphenylamine antioxidants SPD have been combined to form a new non-phosphorus and non-metal compound as a potential multifunctional additive for lubricant.
2. Materials and experimental section
2.1. Materials
Solvents, reagents and DPA were bought from commercial sources. Polyisobutylene succinimide dispersant (PIBSI) was prepared according to the patent.36 And T203 (zinc diisooctyldithiophosphate) was obtained as a gift and chosen to represent ZDDP. Commercial mineral oil 150N was purchased from China National Offshore Oil Corporation. The physicochemical properties of T203 and 150N are listed in Table 1.
Table 1 Properties of T203 and 150N
Item |
T203 |
150N |
Kinematic viscosity (40 °C), mm2 s−1 |
— |
27.9 |
Kinematic viscosity (100 °C), mm2 s−1 |
— |
5.2 |
Flash point, °C |
>190 |
238.1 |
Water content, wt% |
0.03 |
0.0073 |
Sulfur content, wt% |
15.04 |
<0.0001 |
Phosphorus content, wt% |
7.61 |
— |
Zinc content, % |
9.02 |
— |
Density, 20 °C, kg m−3 |
1096.1 |
840 |
2.2. Characterization
All NMR spectra (1H, 13C, 11B, 19F) were recorded on Bruker AVANCE-400 MHz spectrometer at room temperature. High resolution mass spectra (HRMS) and element contents were analyzed by UPLC-Q-TOF mass spectrometer (AB Sciex TripleTOF 4600 system) and ICP-OES (SPECTRO ARCOS), respectively. The surface features and energy dispersive X-ray spectroscopy (EDS) of the worn scars were probed by scanning electron microscope (SEM) measurements (EVO18, Zeiss, Germany). The results of X-ray photoelectron spectroscopy (XPS) were acquired on imaging photoelectron spectrometer (AXIS ULTRA).
2.3. Synthesis and characterization of the compounds
The synthesis process is shown in Scheme 2 and ESI Section S1.1.†
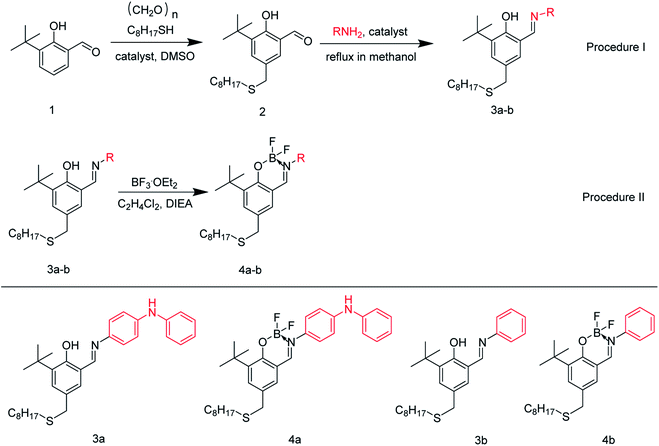 |
| Scheme 2 Synthesis processes of Schiff bases and difluoroboron derivatives. | |
2.3.1. Synthesis of (E)-2-(tert-butyl)-4-((octylthio)methyl)-6-(((4-(phenylamino)phenyl)imi-no)methyl)phenol (Schiff base 3a). Schiff base 3a as an antioxidant has been synthesized and studied in our previous works.29 As an important reaction intermediate and reference material in this study, it was synthesized according to general procedure I of Scheme 2 and ESI Section S1.1.†
2.3.2. Synthesis of (E)-4-((3-(tert-butyl)-2-((difluoroboranyl)oxy)-5-((octylthio)methyl)ben-zylidene)amino)-N-phenylaniline (difluoroboron derivative 4a). The synthesis follows general procedure II of Scheme 2 and ESI Section S1.1.† Starting material: Schiff base 3a. Product: yellow solid. Isolated yield: 85% (3 g). 1H NMR (Fig. S1,† 400 MHz, DMSO) δ 9.05 (s, 1H), 8.59 (s, 1H), 7.75–6.76 (m, 11H), 3.74 (s, 2H), 2.42 (t, J = 7.2 Hz, 2H), 1.55–1.13 (m, 21H), 0.84 (t, J = 6.5 Hz, 3H). 13C NMR (Fig. S2,† 101 MHz, DMSO) δ 163.72 (s), 156.25 (s), 144.97 (s), 142.74 (s), 138.51 (s), 136.02 (s), 133.89 (s), 131.10 (s), 130.45 (s), 129.76 (s), 124.81 (s), 121.33 (s), 118.42 (s), 116.92 (s), 116.34 (s), 34.96 (d, J = 2.4 Hz), 31.69 (s), 31.13 (s), 29.50 (s), 29.25 (s), 29.08 (s), 29.02 (s), 28.70 (s), 22.52 (s), 14.37 (s). 11B NMR (Fig. S3,† 128 MHz, DMSO) δ 94.33 (s). 19F NMR (Fig. S4,† 377 MHz, DMSO) δ −133.77 (d, J = 23.8 Hz). HRMS (Fig. S5†) found for C32H41BF2N2OS [M − H]−: 549.3001, calcd: 549.2997. Elemental analysis, S: 5.57% (calcd: 5.82%); B: 1.86% (calcd: 1.96%). The sulfur content of difluoroboron derivative 4a is lower than that of ZDDP (e.g. T203 is 15%).
2.3.3. Synthesis of (E)-1-(3-(tert-butyl)-2-((difluoroboranyl)oxy)-5-((octylthio)methyl)phen-yl)-N-phenylmethanimine (difluoroboron derivative 4b). Schiff base 3b was synthesized by substituting p-aminodiphenylamine with aniline in accordance with general procedure I and ESI Section S1.† Then difluoroboron derivative 4b was obtained by general procedure II and ESI Section S1.1.† Product: yellow oil. Isolated yield: 80% (2 g). 1H NMR (Fig. S6,† 400 MHz, DMSO) δ 9.14 (s, 1H), 7.80–7.37 (m, 7H), 3.75 (s, 2H), 2.42 (t, J = 7.3 Hz, 2H), 1.61–1.10 (m, 21H), 0.84 (t, J = 6.7 Hz, 3H). 13C NMR (Fig. S7,† 101 MHz, DMSO) δ 166.91 (s), 156.73 (s), 142.48 (s), 138.65 (s), 136.80 (s), 131.55 (s), 130.64 (s), 129.91 (s), 129.37 (s), 124.03 (s), 116.67 (s), 35.01 (s), 34.83 (s), 31.69 (s), 31.07 (s), 29.48 (s), 29.22 (s), 29.07 (s), 29.01 (s), 28.68 (s), 22.51 (s), 14.38 (s). 11B NMR (Fig. S8,† 128 MHz, DMSO) δ 0.77 (s). 19F NMR (Fig. S9,† 377 MHz, DMSO) δ −133.24 (d, J = 26.2 Hz). HRMS (Fig. S10†), calcd for C26H36BF2NOS M−: 459.2579, found 459.2603. Elemental contents, S: 7.03% (calcd: 6.98%); B: 2.40% (calcd: 2.35%).
2.4. Tribological test
The antiwear capacities, last nonseizure loads (PB values) and welding loads (PD values) were evaluated on Tianji MS-10A four-ball test machine. And all steel balls are made of GCr15 material with hardness of 59–61 HRC, surface roughness of less than 0.032 μm and ball diameter of 12.7 mm. The extreme pressure properties (PB and PD) of lubricants were evaluated by the national standard method GB/T 3142-82 (similar to ASTM D2783) at 1450 rpm and room temperature for 10 seconds. The general test conditions of antiwear capacities are as follows: test temperature, 75 °C; test duration, 60 min; test rotation rate, 1200 rpm. All results were repeated at least twice. The wear degree is expressed by the mean wear scar diameter (WSD) and the mean wear volume (WV) of the three stationary balls. After tests, the WSD was obtained by measuring the wear scar diameter of three stationary balls on the microscope and measuring device of the four-ball tester. The WV was calculated by the following equation:37
where
d equals the value of WSD and r (6.35 mm) is the radius of the steel ball.
2.5. Antioxidation behavior analysis
Pressure differential scanning calorimetry (PDSC, NETZSCH DSC 204, Germany) can be used to determine the oxidation induction time (OIT) of lubricants to quickly evaluate their antioxidation property. The experimental process and method can be referred to our previous literatures.28,29 And in this paper, PDSC tests of different lubricants were carried out in the isothermal mode at 180 °C and 500 psi oxygen pressure.
3. Results and discussion
3.1. Selection of base oil
In order to increase the solubility of additives in 150N and simulate the formulations of commercial lubricants, 150N containing 4 wt% dispersant PIBSI (PIBSI-0.04-150N) was selected as the base oil.38 The main structure of dispersant PIBSI is shown in the following structure (a). And the following tests were carried out in the base oil (PIBSI-0.04-150N).
3.2. Antioxidation behavior
As shown in Fig. 1, the antioxidation capacity of different additives in base oil was rapidly and accurately evaluated under the isothermal mode at 180 °C and 500 psi oxygen pressure. Due to the interaction between dispersant and ZDDP in base oil,39 the OIT of ZDDP in base oil (PIBSI-0.04-150N) is lower than that in 150N (15.6 min). Interestingly, compared with base oil and base oil containing ZDDP, the OIT of base oil containing difluoroboron derivative 4a increased by 2.25 and 4.76 times, respectively. Compared with DPA, difluoroboron derivative 4a exhibits superior antioxidation capacity, and its OIT increased by 32.7%. Furthermore, as expected, difluoroboron derivative 4b almost has no effect on the antioxidation capacity of base oil. The above results of the comparisons among compounds 4a, 4b and DPA show that diphenylamine was the key functional group of antioxidation property. And difluoroboron derivative 4a has better antioxidation capacity than DPA, which may be the result of the intramolecular synergism between arylamines and sulfides, which is consistent with previous research results.29,40
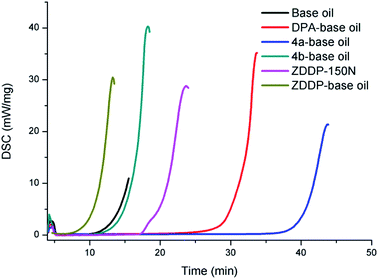 |
| Fig. 1 Antioxidation response of different additives (5 μmol g−1) in base oil. | |
3.3. Extreme pressure performance
In order to discuss the extreme pressure properties of additive and the strength of oil film, the last nonseizure loads (PB values) and welding loads (PD values) were evaluated by the national standard method GB/T 3142-82 (similar to ASTM D2783), as shown in Fig. 2. The same PD value means that additive 4a has the same extreme pressure working ability as base oil. The PB value of difluoroboron derivative 4a is 804 N, which is greater than 510 N of base oil, indicating that the oil film strength of additive is higher than that of base oil. It is clearly concluded that the strength of base oil film can be significantly improved by adding difluoroboron derivative 4a.
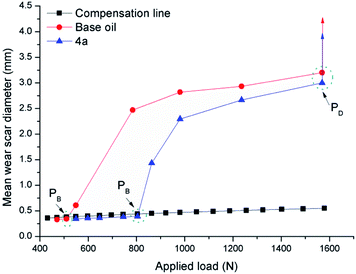 |
| Fig. 2 The plot of PB and PD values for 5 μmol g−1 difluoroboron derivative 4a and base oil. | |
3.4. Antiwear performances
3.4.1. Effects of additive concentration. Initially, the antiwear performances of base oil (PIBSI-0.04-150N) with different additive concentrations were investigated by four-ball test machine under 490 N and general test conditions. The WSD changes of the novel difluoroboron derivative 4a at different concentrations in the base oil are shown in Fig. 3. Without any additive, the WSD of base oil is as high as 0.715 mm. Adding 2.5 μmol g−1 borated Schiff base 4a to the base oil can reduce the WSD value to 0.625 mm. The maximum decrease of WSD is 30.2% at the concentration of 5 μmol g−1, but further increase of additive concentration to 7.5 and 10 μmol g−1 will increase the value of WSD, which means higher additive content would not help to improve the antiwear property. The results can be explained as follows: without additives, PIBSI is adsorbed on the steel surface to form a weak oil film. After adding the difluoroborane derivative 4a to the base oil, the PIBSI adsorption film was replaced by additives with strong polar surface adsorption ability. With the increase of additive concentration, the PIBSI adsorptive film was gradually replaced by additives. When the additive concentration is 5 μmol g−1, the best additive adsorptive film strength and the best anti-wear effect of the lubricant formulation are obtained. However, when the concentration of additive is more than 7.5 μmol g−1, the adsorptive film of lubricant may be dominated by additives. In this case, because of the high concentration, the base oil (including PIBSI) will compete with the additives to adsorb to the metal surface, resulting in the destruction of the adsorptive film of the additives and the reduction of the wear resistance of the lubricants.41–43 Considering the best wear resistance at 5 μmol g−1 concentration, all the following antiwear tests for other additives were carried out under that concentration.
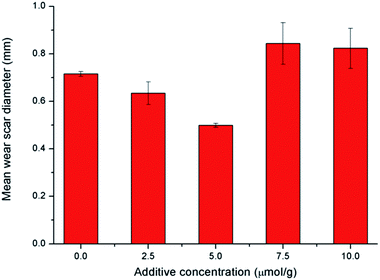 |
| Fig. 3 Variation of the WSD for difluoroboron derivative 4a at different concentrations in base oil. | |
3.4.2. Effects of applied load. As shown in Fig. 4a, the effect of applied load on antiwear performance of difluoroboron derivative 4a was discussed. Without any additive, the WSD of the base oil increases with the increase of applied load. For the 5 μmol g−1 difluoroboron derivative 4a, the WSD remained stable under the load less than 588 N. And when the applied load is 490 N, difluoroboron derivative 4a obtained the best antiwear performance with WSD of 0.499 mm. In order to explain the sudden increase of WSD at 588 N, the friction coefficient curve of difluoroboron derivative 4a under 588 N is shown in Fig. 4b. The two spikes of friction coefficient curve of difluoroboron derivative 4a indicate that the long wear under 588 N at 75 °C destroys the additive adsorption film, which results in the abrupt increase in WSD. For base oil, the spike at the beginning of the test indicates that the adsorption film of base oil is easily destroyed under 588 N, which corresponds to the PB results of base oil. Base on the change of antiwear performance under different applied load, 490 N is the selected applied load for the antiwear performance tests.
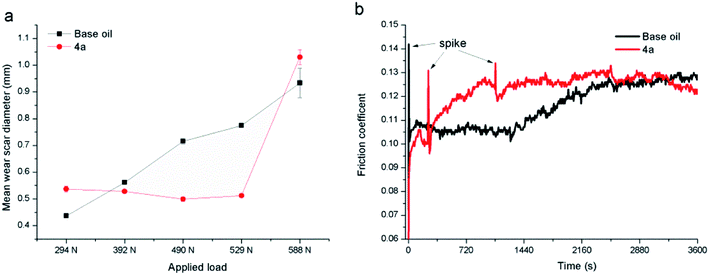 |
| Fig. 4 (a) Variation of the WSD for difluoroboron derivative 4a and base oil under different applied loads; and (b) friction coefficient under the load of 588 N. | |
3.4.3. Antiwear performance of different additives. Fig. 5a shows the variation of the friction coefficient of steel balls, which were lubricated with the base oil (PIBSI-0.04-150N) containing different additives under 490 N and general test conditions. Due to the surface adsorption ability of the nitrogen atom in PIBSI, the friction coefficient of base oil is not less than that of 5 μmol g−1 additives in base oil. The adsorption and corrosion of the fluorine make the surface of steel ball rough and increase the friction coefficients of difluoroboron derivatives 4a and 4b.
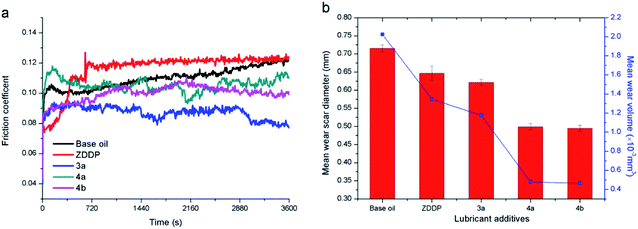 |
| Fig. 5 Variation of the friction coefficient (a) and WSD/WV (b) for different kinds of additives in base oil, additive concentration in base oil is 5 μmol g−1. | |
The antiwear performance is estimated in terms of the WSD and WV (Fig. 5b), notably, compared with the commercial ZDDP, difluoroboron derivative 4a presents a better antiwear property with reduction of 22.8% and 64.4% on WSD and WV, respectively. And compared with base oil, the WSD (or WV) of additive 3a, 4a, and 4b decreased by 12.7% (or 41.9%), 30.2% (or 76.3%) and 30.8% (or 77.1%), respectively. Moreover, compared with Schiff base 3a, the compound 4a exhibits excellent antiwear property with a reduction of WSD and WV about 20.1% and 59.2%, respectively. This strong wear resistance means that the existence of boron and fluorine elements can largely improve the antiwear performance. In order to discuss the effects of diphenylamine and boron and fluorine elements functional group, comparative experiments of difluoroboron derivative 4b were carried out. On the basis of the results, difluoroboron derivative 4a and 4b have good antiwear ability because of the influence of fluorine and boron, but have nothing to do with the structure of diphenylamine. The enhancement of the antiwear capability may be due to the participation of the boron and fluorine elements in tribological process and tribochemistry.14,33,44,45
3.5. Worn surface analysis
For better understanding the morphology and tribochemistry of worn surfaces, SEM and EDS were employed. Obviously, the metal surfaces (Fig. 6a and c) of the ball lubricated only with base oil display obvious larger wear scars and deeper furrows than those lubricated with additive 3a (Fig. 7a and c) and difluoroboron derivative 4a (Fig. 8a and c). The results show that the wear and damage of the ball lubricated only with base oil are serious during the tribological process. Compared with base oil, it can be clearly seen from the elemental mapping that Schiff base 3a is adsorbed onto the worn surface due to the surface adsorption properties of sulfur element, as shown in Fig. 7d–f. Corresponding to the better antifriction effect discussed above, Schiff base 3a lubricating ball has smooth wear scar (Fig. 7c) because of additive's strong surface adsorption and antiwear properties. Although the difluoroborane derivative 4a lubricating ball has grooves on the wear surface (Fig. 8c), the wear scar is smaller than that of the base oil and Schiff base 3a, and the wear scuffing is not sharp. In addition, in Fig. 8b, the obviously detection of B (14.46 atomic%) and F (9.07 atomic%) indicates that the strong polar boron and fluorine elements of additive 4a are transferred to the interface and formed a protective layer. Element mapping Fig. 8e and f show that B and F atoms are involved in the formation of scaly debris on wear scars, which provide intuitive evidence for the speculation of the antiwear mechanism discussed earlier. And the same wear mechanism and results are shown in the SEM images of difluoroborane derivative 4b in Fig. S11 and S12.† It is speculated that the abrasives are formed by the exfoliation of hard compounds, which are generated by the tribochemical interaction of boron and fluorine with iron.
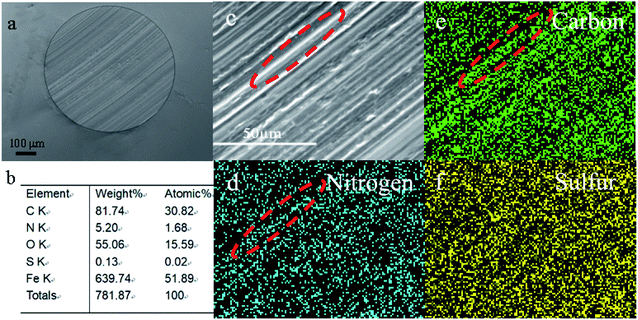 |
| Fig. 6 SEM images (a and c), elemental content (b) and elemental mapping (d–f) of the rubbing surfaces, lubricated with base oil. | |
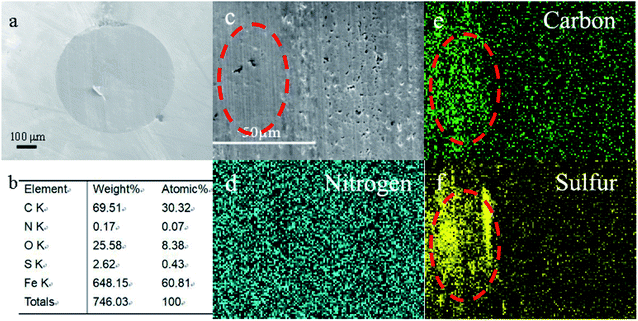 |
| Fig. 7 SEM images (a and c), elemental content (b) and elemental mapping (d–f) of the rubbing surfaces, lubricated with Schiff base 3a. | |
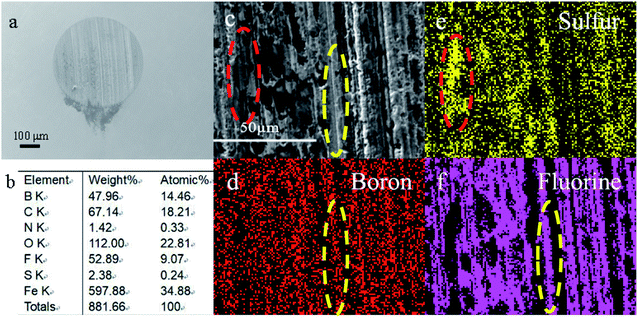 |
| Fig. 8 SEM images (a and c), elemental content (b) and elemental mapping (d–f) of the rubbing surfaces, lubricated with difluoroboron derivative 4a. | |
In order to further understand the lubrication mechanism of difluoroboron derivative 4a in base oil, XPS was used to investigate the compositions of the worn surfaces. As shown in Fig. 9, the B 1 s peak at 191.6 eV is assigned to B2O3/Fe–O–B, corresponding to the O 1s at 533.0 eV, which suggests that the difluoroboron derivative 4a is degraded and reacted with oxygen during the friction process.16,41,46,47 Fluorine peak at about 684.3 eV corresponds to iron fluorides. The Fe 2p3/2 spectra exhibit photoelectron intensity at a binding energy consistent with FeF3 and Fe2O3 at about 713.7 eV and 710.5 eV, respectively.33,47 The peak of N 1s at 399.8 eV indicates the existence of organic nitrogen compound.16,41,48 The O 1s binding energy of 529.7 eV and 531.6 eV corresponds to FeO and C–O, respectively.42,49 The composition of the boundary film, including inorganic and organic compounds, effectively improves the antiwear ability, and further confirms the participation of difluoroboron derivative 4a in tribochemical reaction.
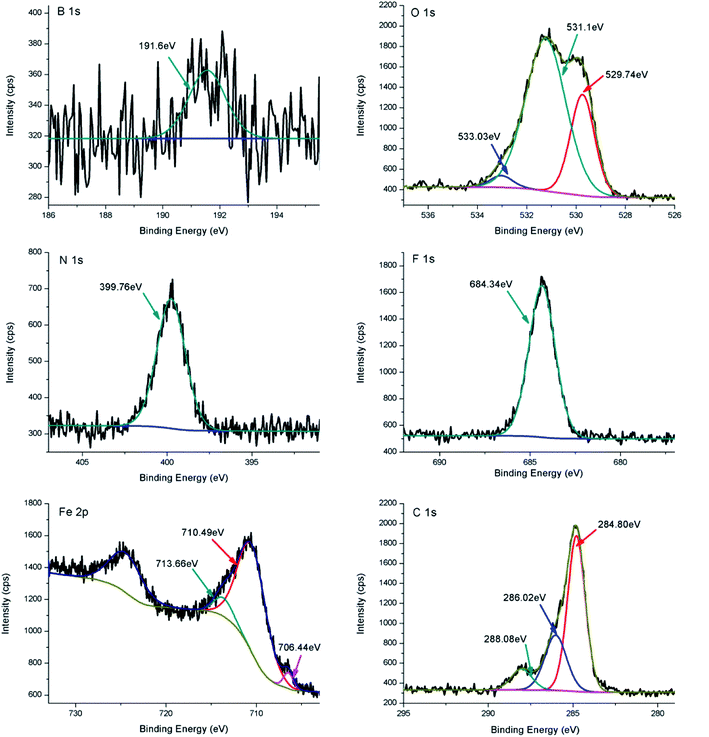 |
| Fig. 9 XPS spectra of worn surfaces on the steel balls were lubricated by 5 μmol g−1 of difluoroboron derivative 4a in base oil. | |
Base on the above results and discussions, the method of oil film formation containing difluoroboron derivative 4a has been speculated. Without additives, PIBSI adsorbs on the steel surface to form a weak oil film. When the additive is added to the base oil at a suitable concentration (5 μmol g−1), the strong polar adsorption ability of additive makes the replacement of PIBSI happens and forms a tough hybrid oil film. And then, high speed (1200 rpm) and high temperature of the contact area (higher than 150 °C) make the additive decompose and react with iron during the antiwear process.50,51 Finally, the persistent boundary film consisting of B2O3, Fe2O3, N-containing organic compounds and iron fluoride is formed.
4. Conclusions
Several metal-free and phosphorus-free compounds were synthesized, characterized and evaluated as lubricant additives. As a new multifunctional lubricant additive by modifying diphenylamine, the antioxidation, extreme pressure properties and antiwear properties of difluoroboron derivative 4a were evaluated. The additive 4a shows better antioxidation performance than base oil, traditional antioxidant DPA and ZDDP. And diphenylamine is the main source of antioxidation property of difluoroboron derivative 4a. Addition of difluoroboron derivative 4a can significantly improves the extreme pressure performance of base oil. For antiwear test, the concentration of 5 μmol g−1 and 490 N was selected as additive concentration and applied load respectively. In addition, under the selected test conditions, the antiwear property of difluoroboron derivative 4a is better, and its mean wear volume is reduced by 76.3%, 64.4% and 59.2% compared to base oil, ZDDP and Schiff base 3a, respectively. On the basis of the results, difluoroboron derivative 4a and 4b have good antiwear ability because of the influence of fluorine and boron, but have nothing to do with the structure of diphenylamine. The wear mechanism can be defined as abrasive wear according to the SEM and EDS results of the worn surfaces. XPS results show that the tribofilm is composed of B2O3, Fe2O3, N-containing organic compounds and iron fluoride such as FeF3. The composition of tribofilm reveals that difluoroboron derivative 4a is involved in complicated tribochemical reactions and effectively improves the antiwear capacity. Therefore, as a novel metal-free and phosphorus-free multifunctional additive, the difluoroboron derivative 4a has the potential application in lubricant.
Conflicts of interest
There are no conflicts to declare.
Acknowledgements
This research was supported by National Natural Science Foundation of China (Grand No. 21606247).
References
- N. J. Mosey, M. H. Müser and T. K. Woo, Science, 2005, 307, 1612–1615 CrossRef CAS.
- W. Li, Y. Wu, X. Wang and W. Liu, Lubr. Sci., 2011, 23, 363–373 CrossRef CAS.
- J. M. Martin, Tribol. Lett., 1999, 6, 1–8 CrossRef CAS.
- H. A. Spikes, Tribol. Lett., 2004, 17, 469–489 CrossRef CAS.
- H. Spikes, Lubr. Sci., 2008, 20, 103–136 CrossRef CAS.
- J. L. Maurya, V. Jaiswal and R. B. Rastogi, Proc. Inst. Mech. Eng., Part J, 2015, 230, 222–237 CrossRef.
- W. Li, C. Jiang, M. Chao and X. Wang, ACS Sustainable Chem. Eng., 2014, 2, 798–803 CrossRef CAS.
- R. B. R. Kalyani and D. Kumar, ACS Sustainable Chem. Eng., 2016, 4, 3420–3428 CrossRef CAS.
- R. K. Singh, A. Kukrety and A. K. Singh, ACS Sustainable Chem. Eng., 2014, 2, 1959–1967 CrossRef CAS.
- M. Chao, W. Li, L. Chen and X. Wang, Ind. Eng. Chem. Res., 2015, 54, 6605–6610 CrossRef CAS.
- G. Biresaw, D. Compton, K. Evans and G. B. Bantchev, Ind. Eng. Chem. Res., 2016, 55, 373–383 CrossRef CAS.
- G. Biresaw, J. A. Laszlo, K. O. Evans, D. L. Compton and G. B. Bantchev, J. Agric. Food Chem., 2014, 62, 2233–2243 CrossRef CAS.
- G. Yang, Z. Zhang, G. Li, J. Zhang, L. Yu and P. Zhang, J. Tribol., 2011, 133, 021801 CrossRef.
- R. B. Choudhary and P. P. Pande, Lubr. Sci., 2010, 14, 211–222 CrossRef.
- L. Wang, H. Wu, D. Zhang, G. Dong, X. Xu and Y. Xie, Tribol. Int., 2018, 121, 21–29 CrossRef CAS.
- Y. Zhang, T. Cai, W. Shang, L. Sun, D. Liu, D. Tong and S. Liu, Tribol. Int., 2017, 115, 297–306 CrossRef CAS.
- Y. Zhou and J. Qu, ACS Appl. Mater. Interfaces, 2017, 9, 3209–3222 CrossRef CAS.
- S. Shahnazar, S. Bagheri and S. B. Abd Hamid, Int. J. Hydrogen Energy, 2016, 41, 3153–3170 CrossRef CAS.
- M. Ye, T. Cai, W. Shang, L. Zhao, Y. Zhang, D. Liu and S. Liu, Tribol. Int., 2018, 127, 557–567 CrossRef CAS.
- M. S. Charoo and M. F. Wani, Lubr. Sci., 2017, 29, 241–254 CrossRef CAS.
- R. K. Singh, S. Pandey, R. C. Saxena, G. D. Thakre, N. Atray and S. S. Ray, J. Ind. Eng. Chem., 2015, 26, 149–156 CrossRef CAS.
- R. K. Singh, A. Kukrety, O. P. Sharma, M. K. Poddar, N. Atray, G. D. Thakre and S. S. Ray, Waste Biomass Valorization, 2016, 7, 1437–1445 CrossRef CAS.
- R. K. Singh, A. Kukrety, A. K. Chatterjee, G. D. Thakre, G. M. Bahuguna, S. Saran, D. K. Adhikari and N. Atray, Ind. Eng. Chem. Res., 2014, 53, 18370–18379 CrossRef CAS.
- R. K. Singh, S. Pandey, R. C. Saxena, G. D. Thakre, N. Atray and S. S. Ray, New J. Chem., 2015, 39, 5354–5359 RSC.
- Z. He, L. Xiong, F. Xie, M. Shen, S. Han, J. Hu and W. Xu, PLoS One, 2018, 13, e0207267 CrossRef.
- M. Cai, Y. Liang, F. Zhou and W. Liu, Wear, 2013, 306, 197–208 CrossRef CAS.
- M. Cai, Y. Liang, M. Yao, Y. Xia, F. Zhou and W. Liu, ACS Appl. Mater. Interfaces, 2010, 2, 870–876 CrossRef CAS.
- S. Yu, J. Feng, T. Cai and S. Liu, Ind. Eng. Chem. Res., 2017, 56, 4196–4204 CrossRef CAS.
- S. Yu and S. Liu, Eur. J. Org. Chem., 2018, 2018, 381–385 CrossRef CAS.
- V. Jaiswal, K. Kalyani, R. B. Rastogi and R. Kumar, J. Mater. Chem. A, 2014, 2, 10424–10434 RSC.
- K. Kalyani, V. Jaiswal, R. B. Rastogi and D. Kumar, Proc. Inst. Mech. Eng., Part J, 2016, 231, 357–365 CrossRef.
- Z. Zheng, G. Shen, Y. Wan, L. Cao, X. Xu, Q. Yue and T. Sun, Wear, 1998, 222, 135–144 CrossRef CAS.
- G. Gu, Z. Wu, Z. Zhang and F. Qing, Tribol. Int., 2009, 42, 397–402 CrossRef CAS.
- D. Frath, S. Azizi, G. Ulrich, P. Retailleau and R. Ziessel, Org. Lett., 2011, 13, 3414 CrossRef CAS.
- J. Dobkowski, P. Wnuk, J. Buczynska, M. Pszona, G. Orzanowska, D. Frath, G. Ulrich, J. Massue, S. Mosquera-Vazquez, E. Vauthey, C. Radzewicz, R. Ziessel and J. Waluk, Chemistry, 2015, 21, 1312–1327 CrossRef CAS.
- C. Huang and J. T. Loper, US Pat., US2008188385-A1, 2008.
- D. Berman, A. Erdemir and A. V. Sumant, Carbon, 2013, 59, 167–175 CrossRef CAS.
- Y. Zhang, X. Zeng, H. Wu, Z. Li, T. Ren and Y. Zhao, Tribol. Lett., 2014, 53, 533–542 CrossRef CAS.
- M. Shiomi, M. Tokashiki, H. Tomizawa and T. Kuribayashi, Lubr. Sci., 2010, 1, 131–147 CrossRef.
- J. B. He, H. Shi, Y. Wang and X. L. Gao, Molecules, 2018, 23, 1–8 Search PubMed.
- F. Jin, G. Yang, Y. Peng, S. Zhang, L. Yu and P. Zhang, Lubr. Sci., 2016, 28, 505–519 CrossRef CAS.
- V. Jaiswal, S. R. Gupta, R. B. Rastogi, R. Kumar and V. P. Singh, J. Mater. Chem. A, 2015, 3, 5092–5109 RSC.
- A. Sammaiah, K. V. Padmaja, S. S. Kaki and R. B. N. Prasad, RSC Adv., 2015, 5, 77538–77544 RSC.
- Y. Shi and J. Dong, Lubr. Sci., 2000, 12, 357–361 CrossRef CAS.
- R. B. Rastogi, J. L. Maurya and V. Jaiswal, Tribol. Trans., 2013, 56, 592–606 CrossRef CAS.
- H. Zhongyi, X. Liping, Q. Liang, H. Sheng, C. Aixi, Q. Jianwei and F. Xisheng, Lubr. Sci., 2014, 26, 81–94 CrossRef.
- D. D. Hawn and B. M. Dekoven, Surf. Interface Anal., 1987, 10, 63–74 CrossRef CAS.
- G. Yang, J. Zhao, L. Cui, S. Song, S. Zhang, L. Yu and P. Zhang, RSC Adv., 2017, 7, 7944–7953 RSC.
- Y. Liu, P. Liu, L. Che, C. Shu and X. Lu, Chin. Sci. Bull., 2012, 57, 4641–4645 CrossRef CAS.
- F. Spadaro, A. Rossi, E. Lainé, P. Woodward and N. D. Spencer, Tribol. Lett., 2016, 65, 11 CrossRef.
- S. Q. A. Rizvi, A comprehensive review of lubricant chemistry, technology, selection, and design, Library of Congress Cataloging-in-Publication Data, ASTM International, Baltimore, 2009 Search PubMed.
Footnote |
† Electronic supplementary information (ESI) available. See DOI: 10.1039/c9ra05490a |
|
This journal is © The Royal Society of Chemistry 2019 |
Click here to see how this site uses Cookies. View our privacy policy here.