DOI:
10.1039/C9RA02102G
(Paper)
RSC Adv., 2019,
9, 17016-17024
Hydrothermal-assisted shearing exfoliation for few-layered MoS2 nanosheets
Received
19th March 2019
, Accepted 17th May 2019
First published on 31st May 2019
Abstract
The exfoliation of bulk MoS2 into few layers has attracted considerable attention as 2D nanomaterials in the past decade. We developed a facile approach for producing MoS2 nanosheets by hydrothermal-assisted shearing exfoliation based on organic-free strategy. This original exfoliation was highly efficient for large-scale production and sustainable for the environment. The thickness of the as-exfoliated MoS2 nanosheets was about 4–6 layers, and the lateral size became smaller from hydrothermal processing to shearing. The hydrothermal processing with the participation of ammonium carbonate played an important role in hydrothermal-assisted shearing exfoliation. As a prospective application, the antifriction performance of the as-exfoliated MoS2 nanosheets in oil was evaluated using a ball-on-ball mode. Evidently, the average friction coefficient and wear scar diameter of 0.08 wt% MoS2-based oil dropped to about 20.66% and 47.27% relative to those of the base oil, which exhibited an excellent antifriction and antiwear ability.
1. Introduction
MoS2 nanosheets, as inorganic analogues of graphene, have excellent properties that are useful in many practical applications as catalysts,1,2 in batteries,3,4 sensors,5 nanotransistors,6 hydrogen storage devices,7 supercapacitors,8 and lubricants,9,10 due to the band gap of 1.2–1.8 eV and the layered structure with S–Mo–S monolayers interacted via van der Waals forces. At present, the bulk MoS2 has been widely used as an anti-wear additive in solid greases,11 but it cannot be used in liquid lubricants due to its unstable dispersion. The specific surface area of the bulk MoS2 was increased through nanotechnology to obtain MoS2 nanosheets and enhanced the stable dispersion in liquid lubricants. Rajendhran et al.12 exfoliated the bulk MoS2 to Ni–MoS2 nanosheets by ultrasonication and reflux techniques. The friction results revealed that the average friction coefficient (COF) and average wear scar diameter (AWSD) of 0.5 wt% Ni–MoS2-based oil decreased by 40–50% and 15–20% compared to those of the base oil due to its small size and surface modification behavior. To date, many top-down designs for preparing monolayer or multilayer MoS2 nanosheets have been successfully achieved, such as micromechanical peeling,13 electrochemical exfoliation,14 liquid-phase ultrasound,15 ion intercalation16 and shearing method.17 In contrast to bottom-up methods with high cost and serious pollution,18–20 the exfoliation method for MoS2 nanosheets was more conducive to exert its application in oil as additive due to the lateral size being of less influence on the friction of the oil. The liquid-phase exfoliation assisted with physical means such as ultrasonication and shearing is of preferable advantage for high quality and scalable output.21–23 In particular, a kitchen blender was used to exfoliate bulk MoS2 into nanosheets with a mean thickness of 4.6 nm (ref. 24) and the number of MoS2 nanosheet layers is mostly less than four layers.25 However, these liquid-phase exfoliations for nanosheets based on organic solvents were expensive and time consuming because the removal of the toxic and high boiling organic solvents after an exfoliating process accounted for an unprecedented challenge for large scale productions.26 Hence, it is urgent to develop a highly efficient method for exfoliating MoS2 nanosheets.
In this study, we adopted a facile exfoliation method based on hydrothermal-shearing exfoliation to access MoS2 nanosheets. The structure and change of the exfoliated MoS2 nanosheets were intensively determined by a series of characterizations. The tribological properties of the as-exfoliated MoS2 nanosheets were examined by adding oil as an additive. Finally, we discuss the friction reducing and forming mechanisms of the as-exfoliated MoS2 nanosheets.
2. Experimental section
2.1 Materials and methods
MoS2 nanosheets were achieved by hydrothermal-shearing exfoliation. Initially, 0.98 g of ammonium carbonate ((NH4)2CO3, AC) was dissolved in 20 mL deionized water and then 0.10 g of bulk MoS2 (Sinopharm Chemical Reagent Co., Ltd) was added into the above solution with magnetic stirring at room temperature for 2 h. Next, the suspension was transferred to a 100 mL Teflon-lined autoclave and heated at 10 rpm and 220 °C for 2 h, thus obtaining the sample denoted as MoS2-AC. Alternatively, the hydrothermal-treated MoS2 solution was swiftly added into the jug with double four-leaf rotary blades and sheared by the rotary blades at 18
000 rpm for 5 rounds at 2 min on/15 min off. Under severe centrifugal forces, the suspension rapidly diffused from the working area to the stator channel. During the diffusion process, the MoS2 suspension produced a strong shear force along the tangential direction of the blades (including the lateral shear force, the longitudinal shear force, and the collision). Finally, the upper suspension was washed by deionized water and anhydrous ethanol three times; it was then dried at 60 °C for 24 h and denoted as MoS2-AC-S. Scheme 1 shows the forming mechanism of as-exfoliated MoS2 nanosheets. A variety of anions and cations expanded the layer spacing of MoS2 in the hydrothermal process. During the shearing process, the lateral shear force overcame the weaker van der Waals forces between the MoS2 layers to obtain less or even a single layer of MoS2, the longitudinal shear force made MoS2 nanosheets fracture, and the collision had a synergistic effect.27
 |
| Scheme 1 The forming mechanism of the as-exfoliated MoS2 nanosheets. | |
2.2 Testing of tribological properties
The bulk MoS2 and as-prepared MoS2 nanosheets were added in 150 SN base oil using an ultrasonic dispersion, which was marked as MoS2-based oil, with different concentrations of MoS2 (0.02 wt%, 0.04 wt%, 0.06 wt%, 0.08 wt% and 0.10 wt%). The tribological performance was detected by a four-ball friction tester (Jinan Chenda Ltd. Co., in China). The testing parameters were set at a speed of 1200 rpm, a stable applied load of 100 N and a duration time of 2 h. Every test was repeated at least three times under the same conditions. At the end of testing, the wear scar diameter was measured using an optical microscope.
2.3 Characterization
XRD patterns, Raman, UV-vis and FTIR spectra were inspected by powder X-ray diffractometer (Bruker AXS, German), inVia Raman spectrometer (Renishaw, Britain), Cary 5000 spectrophotometer (Varian, USA) and Cary 610/670 micro infrared spectrometer (Varian, USA), respectively. The SEM, TEM and HRTEM images were recorded by a S-4800II field-emission scanning electron microscope (Hitachi, Japan), a Tecnai 12 transmission electron microscope (Philips, Netherlands) and a Tecnai G2 F30 S-TWIN field-emission transmission electron microscope (FEI, USA), respectively. The AFM analysis was conducted on a Nanoscope (Digital Instruments, USA). The wear scar micrographs were obtained using a LSM 700 3D laser scanning microscope (CARL ZEISS, Germany).
3. Results and discussion
Fig. 1 shows the XRD patterns and Raman spectra of the bulk MoS2, MoS2-AC and MoS2-AC-S. As shown in Fig. 1a, all the MoS2 samples show nine peaks at 2θ = 14.4°, 32.7°, 33.5°, 35.9°, 39.5°, 44.2°, 49.9°, 58.3° and 60.1°, corresponding to the (002), (100), (101), (102), (103), (006), (105), (110) and (008) planes of 2H MoS2 (JCPDS no. 37-1492). Every peak is assigned to the lattice of representative MoS2 and there is no extra peak corresponding to MoO3. This demonstrates that the as-exfoliated MoS2 is a single phase.28 However, all lattice planes of MoS2-AC and MoS2-AC-S show weaker peak intensities than the bulk MoS2. The possible reason is that the MoS2-AC and MoS2-AC-S have fewer layers than the bulk MoS2. In Fig. 1b, the bulk MoS2, MoS2-AC and MoS2-AC-S have two stronger characteristic peaks at about 381 cm−1 (E12g mode) and 406 cm−1 (A1g mode).29,30 However, the frequency difference between E12g and A1g peaks for the as-exfoliated MoS2 sample is less than that of the bulk MoS2. This indicates that the number of as-exfoliated MoS2 layers decreases after two exfoliation processes.31,32 In addition, MoS2-AC-S shows less frequency difference than MoS2-AC, indicating that the layer of MoS2-AC-S decreases after shearing. Furthermore, the characteristic peaks of the 1T phase are not observed after the exfoliation process, indicating that there is no phase transition.
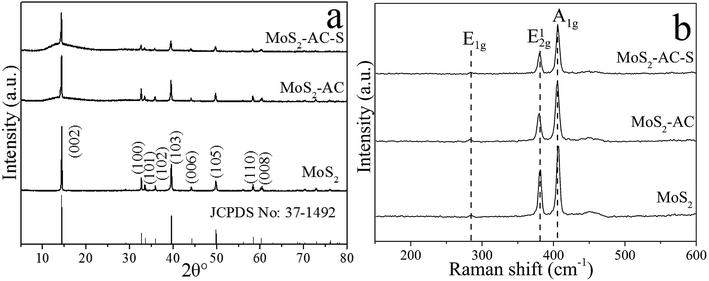 |
| Fig. 1 XRD patterns (a) and Raman spectra (b) of the bulk MoS2, MoS2-AC and MoS2-AC-S. | |
As shown in Fig. 2, the bulk MoS2 had a larger lateral size and thickness (Fig. 2a and b). Evidently, the lateral size and thickness of the MoS2-AC and MoS2-AC-S became smaller and thinner (Fig. 2c–f). More importantly, after the hydrothermal process using (NH4)2CO3, the exfoliation of bulk MoS2 into multi-layer occurred. This suggests that (NH4)2CO3 in the interlayer of MoS2 under hydrothermal processing served as the exfoliation agent. In comparison of MoS2-AC and MoS2-AC-S, the lateral size and thickness of the latter are further lessened and filmy. The result confirms that the shearing after the hydrothermal process accounts for the deep exfoliation into fewer layers and a smaller size. Accordingly, the combination of the two processes is propitious to the curling of the flake edge and prevents the secondary assembly of nanosheets.33 The surface area was measured to confirm the changes of the bulk MoS2 and MoS2-AC-S nanosheets. The results show that the surface area of MoS2-AC-S is about 62.86% larger than that of bulk MoS2, indicating that the exfoliation can increase the surface area (Table 1).
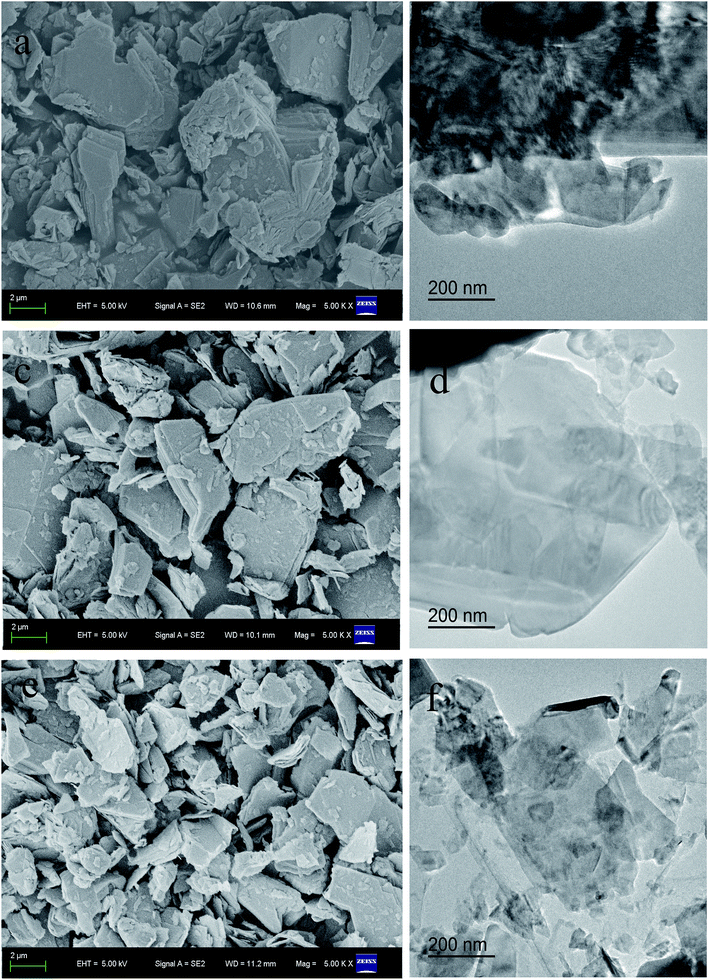 |
| Fig. 2 SEM and TEM images of the bulk MoS2 (a and b), MoS2-AC (c and d) and MoS2-AC-S (e and f). | |
Table 1 The BET surface area of bulk MoS2 and MoS2-AC-S
Samples |
Surface area (m2 g−1) |
Bulk MoS2 |
15.475 |
MoS2-AC-S |
25.203 |
In Fig. 3a and b, the edge layers of the bulk MoS2 are far more than 20, and the layers of MoS2-AC are more than 10 and less than the layers of the bulk MoS2. As displayed in the HRTEM image of Fig. 3c, the thickness of MoS2-AC-S with 0.62 nm of interlayer basal spacing is up to about 4–6 layers, which corresponds to the (002) plane for MoS2. Additionally, the 0.27 nm of (100) plane, the 0.23 nm of (103) plane and the 0.16 nm of (110) plane for MoS2-AC-S is in good agreement with the XRD spectra. The result indicates that the as-exfoliated MoS2 nanosheets still retain a good crystallinity. Fig. 3d shows the corresponding SAED pattern of MoS2-AC-S, which reveals the presence of a ring-like pattern, thus corroborating the existence of multi-layer polycrystalline nanosheets.34 The size and thickness of the as-exfoliated MoS2-AC-S was further verified by AFM (Fig. 3e). The as-exfoliated MoS2-AC-S had a larger irregular-shaped size and about 2.70–3.59 nm thickness (calculated layer number about 4–6), which is consistent with the HRTEM result.
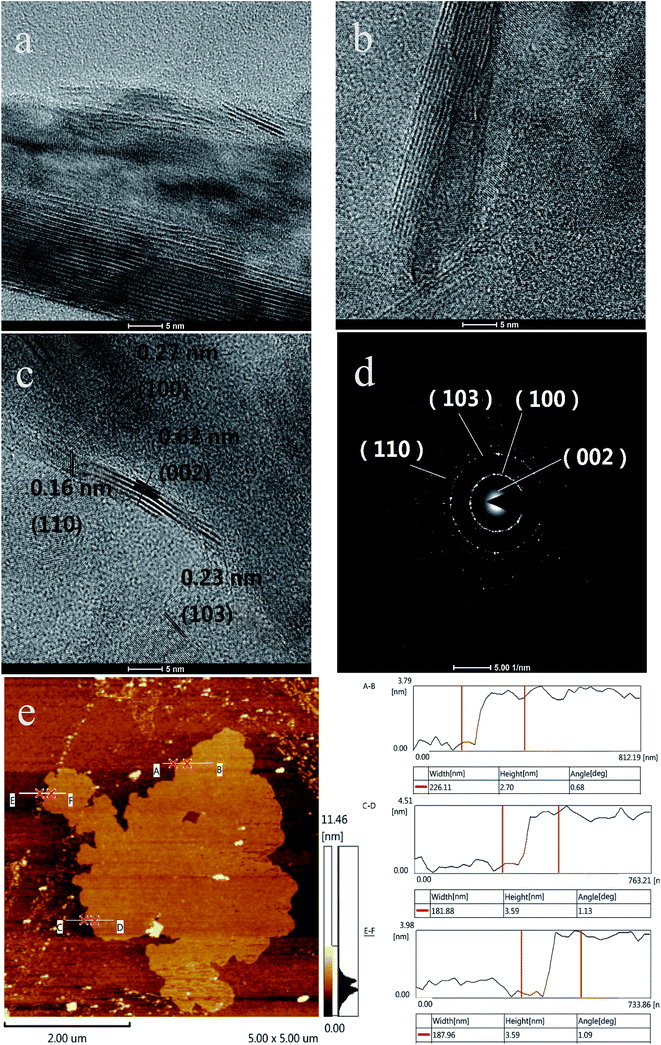 |
| Fig. 3 HRTEM images of bulk MoS2 (a) and MoS2-AC (b); HRTEM image (c); SAED pattern; (d) and AFM image and the corresponding height (e) of MoS2-AC-S. | |
Fig. 4 shows the average friction coefficients (COFs) and wear scar diameters (AWSDs) of bulk MoS2 and as-exfoliated MoS2 under a rotating speed of 1200 rpm and a load of 100 N. As disclosed in Fig. 4a, the average COFs of the bulk MoS2-based oil and MoS2-AC-S-based oil with the increase of adding content are descended prior to 0.06 wt% and 0.08%, respectively. With further increase of adding content, the COFs thereupon rise fleetly. The optimal average COFs of these two samples decreased by about 19.01% and 20.66% compared to that of the 150 SN base oil. This is because MoS2-AC-S with few layers and small size can more easily enter into the contact surface than the bulk MoS2, probably forming a tribofilm on the contact surface to reduce the friction coefficient and wear scar diameter.35 However, excessive MoS2 can result in a poor dispersion in oil, and the larger agglomerates consisting of nanosheets conversely increase the friction. Moreover, the AWSDs of the bulk MoS2 and MoS2-AC-S decrease with the increase in the content up to 0.08 wt%, but the excessive increase in the content could give rise to abrasive wear, for instance at 0.1 wt%. Furthermore, the AWSDs of the base oil containing 0.08 wt% bulk MoS2 and MoS2-AC-S are about 40.00% and 47.27% lower than the base oil, respectively.
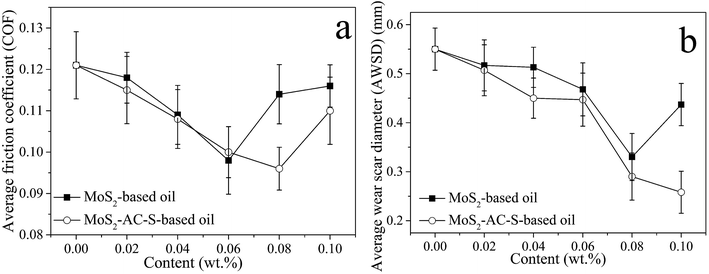 |
| Fig. 4 The average COFs (a) and AWSDs (b) of the bulk MoS2-based oil and MoS2-AC-S-based oil as a function of adding content. | |
Fig. 5a and b show the effect of the load on the average COFs and AWSDs of the steel balls lubricated by 0.08 wt% MoS2-AC-S-based oil with 2 h of friction time. As can be seen from Fig. 5a, the average COFs of MoS2-AC-S-based oil are decreasing with the increase in the applied load. Furthermore, the COF of MoS2-AC-S-based oil at 300 N is about 27.18% lower than that of MoS2-AC-S-based oil at 50 N. This demonstrates that the MoS2-AC-S-based oil under a higher applied load is more effective to improve the friction ability. On the contrary, the AWSDs of MoS2-AC-S-based oil increased in the range of testing. The AWSD of MoS2-AC-S-based oil at 50 N is about 58.33% smaller than that of MoS2-AC-S-based oil at 300 N. Overall, the MoS2-AC-S-based oil shows better anti-friction ability at higher applied load and better anti-wear ability at a lower applied load.
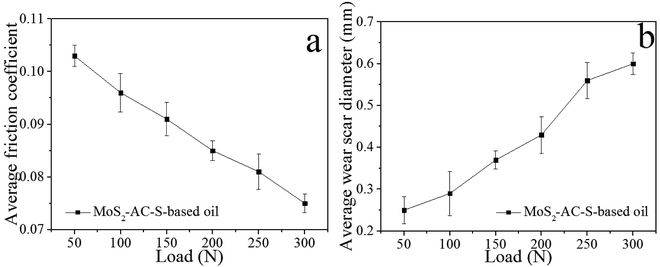 |
| Fig. 5 The average COFs (a) and AWSDs (b) of base oil with 0.08 wt% MoS2-AC-S as a function of load. | |
Fig. 6 illustrates the COF curves of the base oil, 0.08 wt% bulk MoS2-based oil and 0.08 wt% MoS2-AC-S-based oil tested for 2 h. Fig. 6a shows that the COFs of the bulk MoS2-based oil and MoS2-AC-S-based oil are lower than that of the 150 SN base oil throughout the testing time. More importantly, the COF and AWSD of the MoS2-AC-S-based oil are distinctly lower than those of the bulk MoS2-based oil. Consequently, the average COF and AWSD of MoS2-AC-S-based oil decreased to about 15.79% and 12.12% compared to those of the bulk MoS2. The result indicates that the bulk MoS2 slides difficultly onto the contact surface of the steel ball with the flow of the base oil to reduce the COF and WSD due to the bulk MoS2 with a large size, greater thickness and poor dispersibility in base oil. Owing to the MoS2-AC-S with fewer layers and smaller size, it is easy to permeate into the friction surfaces of the counterpart to form a tribofilm.36 Accidentally, the COF of MoS2 nanosheets is rising with the friction time. This suggests that the stability of MoS2 nanosheets in oil is poor in running-in period.
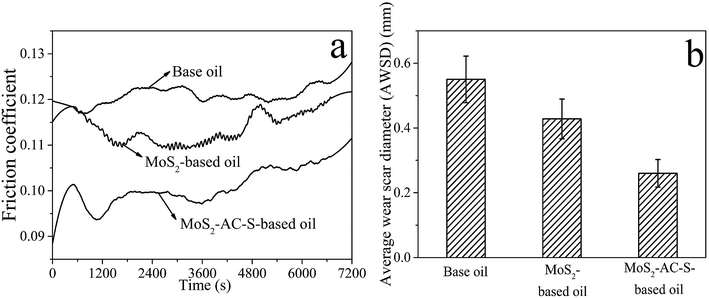 |
| Fig. 6 The COFs (a) and AWSDs (b) of base oil, base oil with 0.08 wt% MoS2 and base oil with 0.08 wt% MoS2-AC-S as a function of time. | |
The 3D laser scanning micrograph was used to measure the morphologies of the worn surface for clearly understanding the tribological behavior. Fig. 7 displays the 3D profiles of the worn surfaces of steel balls tested by the base oil, 0.08 wt% bulk MoS2-based oil and 0.08 wt% MoS2-AC-S-based oil. The contact areas of the testing balls are all severely damaged to a different degree after 2 h. For the base oil, the worn surface has a very rough wear with a deep and wide hollow along the rubbing direction. However, the worn surfaces of steel balls tested by the bulk MoS2 and MoS2-AC-S as additives are much smaller than that of the base oil because of forming the tribofilm on the contact surface, which is derived from the interaction between MoS2 and friction pairs.37 For further demonstration of the tribofilm, the worn surfaces of these steel balls were examined by Raman spectroscopy. The spectra corroborate the E12g and A1g feature peaks of MoS2 observed on the worn surfaces tested by the bulk MoS2-based oil and MoS2-AC-S-based oil. The friction reducing mechanism suggests that the MoS2 nanosheets in oil can smoothly slide onto the touching surface to avoid the wear of the tested steel ball.38,39
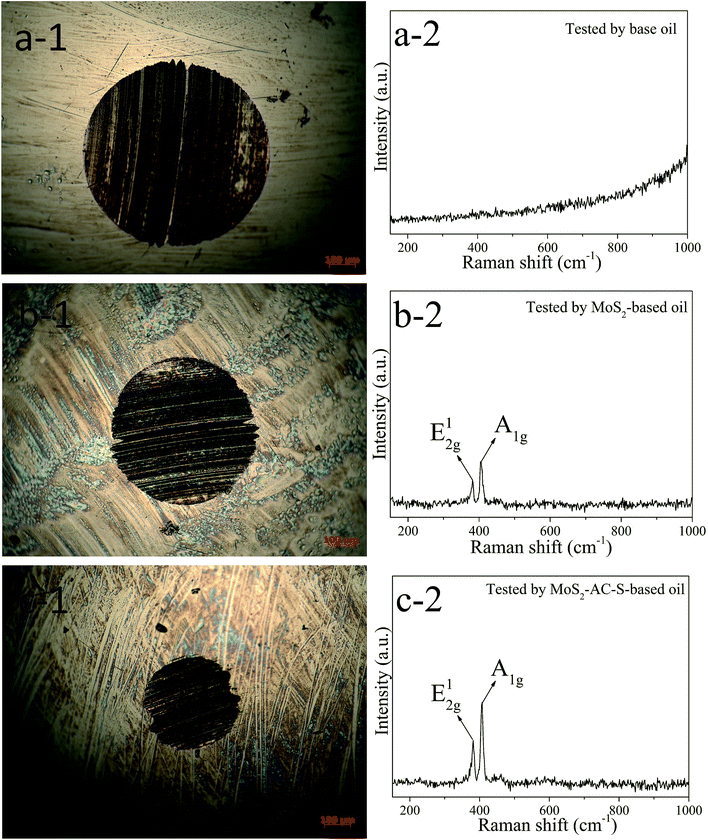 |
| Fig. 7 3D laser scanning micrographs (left) and the corresponding Raman spectra (right) of worn steel ball tested by (a-1 and a-2) base oil, (b-1 and b-2) base oil with 0.08 wt% MoS2 and (c-1 and c-2) base oil with 0.08 wt% MoS2-AC-S. | |
4. Conclusions
In summary, 2D MoS2 nanosheets with 4–6 layers were successfully prepared by the hydrothermal-assisted shearing exfoliation method. During exfoliation processing, the strategy of organic-free was thoroughly achieved. The MoS2 nanosheets as additives were applied in oil for the sake of anti-friction and anti-wear. The results revealed that the average COF and AWSD of the 150 SN base oil with 0.08 wt% MoS2 nanosheets decreased to about 20.66% and 47.27% compared to those of the base oil and exhibited better anti-friction and anti-wear performances.
Conflicts of interest
There are no conflicts to declare.
Acknowledgements
This work was funded by Jiangsu Industrial-Academic-Research Prospective Joint Project (BY2016069-02). The authors also acknowledge the Project Funded by the Priority Academic Program Development of Jiangsu Higher Education Institutions. The data of this paper originated from the Test Center of Yangzhou University.
References
- D. Voiry, M. Salehi, R. Silva, T. Fujita, M. Chen, T. Asefa, V. B. Shenoy, G. Eda and M. Chhowalla, Conducting MoS2 nanosheets as catalysts for hydrogen evolution reaction, Nano Lett., 2013, 13(12), 6222–6227 CrossRef CAS PubMed.
- Z. Cui, H. Chu, S. Gao, Y. Pei, J. Jin, Y. Ge, P. Dong, P. M. Ajayan, J. Shen and M. Ye, Large-scale controlled synthesis of porous two-dimensional nanosheets for hydrogen evolution reaction through a chemical pathway, Nanoscale, 2018, 10(13), 6168–6176 RSC.
- G. S. Bang, K. W. Nam, J. Y. Kim, J. Shin, J. W. Choi and S. Y. Choi, Effective liquid-phase exfoliation and sodium ion battery application of MoS2 nanosheets, ACS Appl. Mater. Interfaces, 2014, 6(10), 7084–7089 CrossRef CAS PubMed.
- B. Guo, F. Yu, X. Chen, B. Li and Y. Ke, Preparation of yolk-shell MoS2 nanospheres covered with carbon shell for excellent lithium-ion battery anodes, Appl. Surf. Sci., 2017, 434, 1021–1029 CrossRef.
- X. Gan, H. Zhao, K.-Y. Wong, D. Y. Lei, Y. Zhang and Q. Xie, Covalent functionalization of MoS2 nanosheets synthesized by liquid phase exfoliation to construct electrochemical sensors for Cd (II) detection, Talanta, 2018, 182, 38–48 CrossRef CAS PubMed.
- S. Bhattacharjee, K. L. Ganapathi, S. Mohan and N. Bhat, A sub-thermionic MoS2 FET with tunable transport, Appl. Phys. Lett., 2017, 111(16), 163501–163505 CrossRef.
- J. Cao, J. Zhou, Y. Zhang and X. Liu, Theoretical study of H2 adsorbed on monolayer MoS2 doped with N, Si, P, Microelectron. Eng., 2018, 190, 63–67 CrossRef CAS.
- Y. Gao, K. Huang, X. Wu, Z. Hou and Y. Liu, MoS2 nanosheets assembling three-dimensional nanospheres for enhanced-performance supercapacitor, J. Alloys Compd., 2018, 741, 174–181 CrossRef CAS.
- N. Rajendhran, S. Palanisamy, P. Periyasamy and R. Venkatachalam, Enhancing of the tribological characteristics of the lubricant oils using Ni-promoted MoS2 nanosheets as nano-additives, Tribol. Int., 2017, 118, 314–328 CrossRef.
- P. Wu, Z. Liu and Z. Cheng, Preparation and tribological properties of oleic acid-decorated MoS2 nanosheets with good oil dispersion, J. Dispersion Sci. Technol., 2018, 39, 1742–1751 CrossRef CAS.
- E. Hu, Y. Xu, K. Hu and X. Hu, Tribological properties of 3 types of MoS2 additives in different base greases, Lubr. Sci., 2017, 1–15 Search PubMed.
- N. Rajendhran, S. Palanisamy, P. Periyasamy and R. Venkatachalam, Enhancing of the tribological characteristics of the lubricant oils using Ni-promoted MoS2 nanosheets as nano-additives, Tribol. Int., 2017, 118, 314–328 CrossRef.
- K. Krishnamoorthy, P. Pazhamalai, G. Kumar Veerasubramani and S. J. Kim, Mechanically delaminated few layered MoS2 nanosheets based high performance wire type solid-state symmetric supercapacitors, J. Power Sources, 2016, 321, 112–119 CrossRef CAS.
- X. You, N. Liu, C. J. Lee and J. P. James, An electrochemical route to MoS2 nanosheets for device applications, Mater. Lett., 2014, 121(2), 31–35 CrossRef CAS.
- S. Ji, Z. Yang, C. Zhang, Z. Liu, W. W. Tjiu, I. Y. Phang, Z. Zhang, J. Pan and T. Liu, Exfoliated MoS2 nanosheets as efficient catalysts for electrochemical hydrogen evolution, Electrochim. Acta, 2013, 109(11), 269–275 CrossRef CAS.
- G. S. Bang, K. W. Nam, J. Y. Kim, J. Shin, J. W. Choi and S.-Yool Choi, Effective liquid-phase exfoliation and sodium ion battery application of MoS2 nanosheets, ACS Appl. Mater. Interfaces, 2014, 6(10), 7084–7089 CrossRef CAS PubMed.
- E. Varrla, C. Backes, K. R. Paton, A. Harvey, Z. Gholamvand, J. McCauley and J. N. Coleman, Large-scale production of size-controlled MoS2 nanosheets by shear exfoliation, Chem. Mater., 2015, 27, 1129–1139 CrossRef CAS.
- X. Wang, H. Feng, Y. Wu and L. Jiao, Controlled synthesis of highly crystalline MoS2 flakes by chemical vapor deposition, J. Am. Chem. Soc., 2013, 135(14), 5304–5307 CrossRef CAS PubMed.
- S. Kumari, R. Gusain, N. Kumar and O. P. Khatri, PEG-mediated hydrothermal synthesis of hierarchical microspheres of MoS2 nanosheets and their potential for lubrication application, J. Ind. Eng. Chem., 2016, 42, 87–94 CrossRef CAS.
- H. Huang, X. Feng, C. Du and W. Song, High-quality phosphorus-doped MoS2 ultrathin nanosheets with amenable ORR catalytic activity, Chem. Commun., 2015, 51(37), 7903–7906 RSC.
- G. S. Bang, K. W. Nam, J. Y. Kim, J. Shin, J. W. Choi and S.-Y. Choi, Effective liquid-phase exfoliation and sodium ion battery application of MoS2 nanosheets, ACS Appl. Mater. Interfaces, 2014, 6(10), 7084–7089 CrossRef CAS PubMed.
- S. Ji, Z. Yang, C. Zhang, Z. Liu, W. W. Tjiu, In Y. Phang, Z. Zhang, J. Pan and T. Liu, Exfoliated MoS2 nanosheets as efficient catalysts for electrochemical hydrogen evolution, Electrochim. Acta, 2013, 109(11), 269–275 CrossRef CAS.
- E. Varrla, C. Backes, K. R. Paton, A. Harvey, Z. Gholamvand, J. McCauley and J. N. Coleman, Large-scale production of size-controlled MoS2 nanosheets by shear exfoliation, Chem. Mater., 2015, 27, 1129–1139 CrossRef CAS.
- E. Varrla, C. Backes, K. R. Paton, A. Harvey, Z. Gholamvand, J. McCauley and J. N. Coleman, Large-scale production of size-controlled MoS2 nanosheets by shear exfoliation, Chem. Mater., 2015, 27, 1129–1139 CrossRef CAS.
- Y. Li, X. Yin and W. Wu, Preparation of few-layer MoS2 nanosheets via an efficient shearing exfoliation method, Ind. Eng. Chem. Res., 2018, 57, 2838–2846 CrossRef CAS.
- H. Yu, H. Zhu, M. Dargusch and Y. Huang, A reliable and highly efficient exfoliation method for water-dispersible MoS2 nanosheet, J. Colloid Interface Sci., 2018, 514, 642–647 CrossRef CAS PubMed.
- Y. Li, X. Yin and W. Wu, Preparation of few-layer MoS2 nanosheets via an efficient shearing exfoliation method, Ind. Eng. Chem. Res., 2018, 57, 2838–2846 CrossRef CAS.
- Y. Zhang, L. Zuo, Y. Huang, L. Zhang, F. Lai, W. Fan and T. Liu, In-situ growth of few-layered MoS2 nanosheets on highly porous carbon aerogel as advanced electrocatalysts for hydrogen evolution reaction, ACS Sustainable Chem. Eng., 2015, 3(12), 3140–3148 CrossRef CAS.
- D. Wang, X. Zhang, S. Bao, Z. Zhang, H. Fei and Z. Wu, Phase-engineering of multiphasic 1T/2H MoS2 catalyst for highly efficient hydrogen evolution, J. Mater. Chem. A, 2017, 5, 2681–2688 RSC.
- P. Wu, Y. Feng, T. Ge, Y. Kong, Z. Ma, Z. Liu and Z. Cheng, An investigation on tribological properties of the chemically capped zinc borate (ZB)/MoS2 nanocomposites in oil, J. Ind. Eng. Chem., 2018, 63, 157–167 CrossRef CAS.
- S. Wu, H. Huang, M. Shang, C. Du, Y. Wu and W. Song, High visible light sensitive MoS2 ultrathin nanosheets for photoelectrochemical biosensing, Biosens.
Bioelectron., 2016, 92, 646–653 CrossRef PubMed.
- M. Li, D. Wang, J. Li, Z. Pan, H. Ma, Y. Jiang and Z. Tian, Facile hydrothermal synthesis of MoS2 nano-sheets with controllable structures and enhanced catalytic performance for anthracene hydrogenation, RSC Adv., 2016, 6(75), 71534–71542 RSC.
- L. Chen, T. Wang, Y. Wu, F. Ma, G. Zhao and X. Hao, Fabrication of two-dimensional nanosheets via water freezing expansion exfoliation, Nanotechnology, 2014, 25, 495302 CrossRef PubMed.
- J. Wu, J. Dai, Y. Shao, M. Cao and X. Wu, Carbon dot-assisted hydrothermal synthesis of flower-like MoS2 nanospheres constructed by few-layered multiphase MoS2 nanosheets for supercapacitors, RSC Adv., 2016, 6, 77999–78007 RSC.
- P. Wu, Z. Cheng, Y. Kong, Z. Ma and Z. Liu, Templated synthesis of plate-like MoS2 nanosheets assisted with HNTs and their tribological performance in oil, J. Nanopart. Res., 2018, 20, 138 CrossRef.
- P. Wu, Z. Cheng, Y. Kong, Z. Ma and Z. Liu, Templated synthesis of plate-like MoS2 nanosheets assisted with HNTs and their tribological performance in oil, J. Nanopart. Res., 2018, 20, 138 CrossRef.
- C. Yang, X. Hou, Z. Li, X. Li, L. Yu and Z. Zhang, Preparation of surface-modified lanthanum fluoride-graphene oxide nanohybrids and evaluation of their tribological properties as lubricant additive in liquid paraffin, Appl. Surf. Sci., 2016, 388, 497–502 CrossRef CAS.
- L. Zhang, H. Yi, S. Feng, L. Zhang, L. Zhang, Z. Jiao, Y. Zhan and Y. Wang, Preparation and tribological properties of novel boehmite/graphene oxide nano-hybrid, Ceram. Int., 2016, 42, 6178–6186 CrossRef CAS.
- P. Wu, Z. Liu and Z. Cheng, Growth of MoS2 nanotubes templated by halloysite nanotubes for the reduction of friction in oil, ACS Omega, 2018, 3, 15002–15008 CrossRef CAS.
|
This journal is © The Royal Society of Chemistry 2019 |
Click here to see how this site uses Cookies. View our privacy policy here.