DOI:
10.1039/C9RA01221D
(Paper)
RSC Adv., 2019,
9, 10814-10819
Retracted Article: Fabrication of hollow CoS1.097 prisms toward supercapactior performance
Received
17th February 2019
, Accepted 1st April 2019
First published on 8th April 2019
Abstract
The controlled synthesis of a variety of microstructures is valuable for understanding the relationship between morphology and properties and exploring potential applications. In this paper, hollow CoS1.097 prisms were prepared by prismatic Co-precursors using thioacetamide (TAA) as a sulfidation treatment reagent. A plausible mechanism was proposed for the formation of the hollow prism structure. S2− comes from TAA to displace the anions in Co-precursors by adjusting temperature and pressure. The original prism morphology of the Co-precursor was maintained and a hollow prismatic structure was formed by an anion exchanging process. Interestingly, the composition of samples after sulfidation treatment can be controlled by changing the diffusion to obtain Co3O4/CoS1.097 and CoS1.097 materials. As electrode materials for supercapacitors, hollow CoS1.097 prisms revealed ideal electrochemical performance.
1. Introduction
With increasing energy consumption and environmental pollution, it is increasingly important to develop low-cost, environment friendly, high-energy and high-power alternative energy sources.1,2 Supercapacitors (SCs) have attracted a great deal of attention due to their outstanding functionality, rapid charge–discharge rates and high power densities.3–6 New electrode materials, such as transition metal chalcogenides including CoS, SnS, ZnS, and FeS have been extensively studied and have shown significant electrochemical properties.7–15 Among them, the cobalt sulfide series including Co1−xS, CoS, CoS1.097, CoS2, Co3S4 and Co9S8 are gaining great attention because of their low cost. Electro-active materials are widely used in supercapacitors.16–25
Metal sulfides, with their rich redox chemical potentials, excellent conductivity and high capacity, are considered as advanced anode materials compared with carbonaceous anodes.26–29 However, in the process of charge and discharge of supercapacitors, the redox alternates and easily causes the volume expansion of active material and detachment from matrix, thereby resulting in the fracture of particles and the loss of capacitance. To improve electrochemical activity, a typical strategy is to control the microstructure of electrode materials through optimizing morphology and size.30,31 Researchers have focused on the synthesis of cobalt sulfide with various morphologies, including nanospheres, nanowires, ellipsoids, egg yolks, shell microspheres and flower-like structures.32–36 However, CoS with other typical morphology to supply enhanced electrochemical properties is still expected. Because of good electrical conductivity and capacitance, CoS have begun to widely used in supercapacitors, especially the hollow structure of micro- and nano-materials.
Here a prismatic cobalt precursor was synthesized by reflux. Hollow prismatic Co-precursor, Co3O4/CoS1.097, and CoS1.097 were obtained hydrothermal vulcanization in thioacetamide (TAA). It is important that hydrotalcite reacted with TAA by refluxing in ethanol allows the cobalt oxyhydroxide to be transformed into a hollow prismatic Co3O4/CoS1.097 composite. The resulting Co3O4/CoS1.097 composite structure does not require additional processing. Hollow prism CoS1.097 revealed ideal electrochemical properties and high specific supercapacitance.
2. Experimental section
2.1 Synthesis of Co-precursor prisms
Co-precursor samples were synthesized by a soft refluxing process. In a typical synthesis, 0.5 g of polyvinylpyrrolidone (PVP, Sigma, MW ∼ 58
000) and 0.32 g of cobalt acetate tetrahydrate were dissolved into 200 ml of ethanol (Aik Moh Paint & Chemicals PTE LTD, 99.86%) at room temperature to form a transparent pink solution. The solution was then heated to 90 °C under refluxing for 2 hours. Afterwards, the precipitate was harvested via multiple centrifugation at 3000 rpm, rinsed thoroughly with hot ethanol (preheated at 60 °C) for at least 20 times to remove the attached PVP on the surface.
2.2 Synthesis of hollow prisms Co3O4/CoS1.097 composite
Typically, Co-precursors were re-dispersed into 40 ml of ethanol, followed by adding 0.1 g of TAA. Then, the mixture was transferred into a Teflon-lined stainless steel autoclave, which was subsequently heated at 160 °C for 6 h. After cooling to room temperature naturally, the precipitate was separated by centrifugation, washed with ethanol for several times and dried in an oven. As prepared sample was annealed at 350 °C in N2 for 2 h with a ramping rate of 2 °C min−1 to produce hollow prisms Co3O4/CoS1.097.
2.3 Synthesis of hollow prisms CoS1.097 structure
Co-precursors were re-dispersed into 40 ml of ethanol, followed by the addition of 0.3 g of TAA. Then, the mixture was transferred into a Teflon-lined stainless steel autoclave, which was subsequently heated at 160 °C for 12 h. After cooling to room temperature naturally, the precipitate was separated by centrifugation, washed with ethanol for several times and dried in an oven. Finally, the as prepared sample was annealed at 350 °C in nitrogen for 2 h with a ramping rate of 2 °C min−1 to produce hollow CoS1.097 prisms.
2.4 Characterization
The crystal structure of as-prepared precursors and target products were determined by powder X-ray diffraction (XRD, Bruker D8-Advance, Germany) instrument with the Cu Kα (λ = 0.1514 nm) as radiation source. The scanning range of 2θ was set as 10°–80° with a scanning rate of 0.02° s−1. The structural features such as morphology and size of all samples were observed by field emission scanning electron microscope (FESEM, QUANTA250 FEG, FEI, USA) and transmission electron microscope (TEM, Tecani F20, FEI). X-ray photoelectron spectroscopy (XPS) was performed using an Axis Ultra spectrometer (Kratos, UK) with an Al monochromatic source operated at 15 kV.
2.5 Electrochemical performance test
Before electrode preparation, the foam nickel was ultrasonic cleaning with HCl, water and anhydrous ethanol, respectively. The active materials (Co-precursor, Co3O4/CoS1.097 composite or Co3O4/CoS1.097, 80 wt%), conductive material (acetylene black, 10 wt%), and binder (polytetrafluoroethylene (PVDF), 10 wt%) were mixed in N-methyl-2-pyrrolidone (NMP) solvent to form a homogeneous slurry, which was then applied to the pretreated nickel foam (1 × 2 cm2). After dried at 60 °C for 12 h in vacuum stove, it was pressed into an electrode plate at 10 MPa as working electrode. Platinum plate was counter electrode and Hg/HgO was reference electrode, respectively. The electrolyte was 6 M aqueous KOH solution. Cyclic voltammetry (CV) test was performed on an electrochemical workstation (CHI 600e, CH Instruments Inc. Shanghai). The galvanostatic charge–discharge was evaluated with a LAND (LANHE CT2001A Wuhan) battery program-control test system.
3. Results and discussion
3.1 Composition and structure
The synthesis strategy of prismatic Co-precursors, hollow Co3O4/CoS1.097 prisms and hollow CoS1.097 prisms is indicated bellow. Prism-like cobalt acetate hydroxide (denoted as Co-precursor) was first prepared by a modified precipitation method and cobalt hydroxyacetate was used as a template for subsequent participation in the reaction. Through morphological observation, it was found that these highly uniform solid Co3O4-precursors have a smooth overall surface. Fig. 1 shows the SEM and TEM images as well as XRD pattern of Co-precursors. SEM and TEM images show the Co-precursor synthesized by refluxing with solid prism-like morphology. The surface of the prism is smooth. The length and width of resulting sample is about 500 and 80 nm, respectively. The XRD pattern proves the prism Co-precursor is constituted by Co3(Ac)5OH (JCPDF No. 22-0582) perfectly and the result is consistent with the previous studies.37 The formation of prism morphology is ascribed to acetate ions with hydroxyl group connected with PVP molecules. Because of selected attachment of PVP, the growth occurred along the [001] facet to form prismatic structures. The result was confirmed by XRD as shown in Fig. 1d.
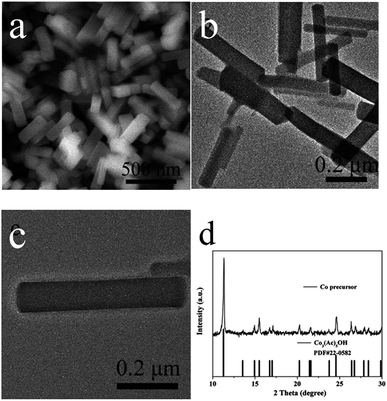 |
| Fig. 1 SEM and TEM images as well as XRD pattern of prismatic Co-precursors. (a) SEM image. (b and c) TEM image. (d) XRD pattern. | |
Because the phase composite of Co-precursor is Co3(Ac)5OH, Co-precursor was used as a template for the preparation of CoS1.097 samples. To study the composition change of Co-precursor in further sulfur treatment, CoxSy or ComOn/CoxSy composite were obtained via a rapid ion exchange method using different parameters. Co-precursors were dispersed in an ethanol solution of TAA. Furthermore, the solid structure of cobalt hydroxyacetate was converted and an internal void cavity structure formed due to the diffusion effect of different cationic and anionic substances. This is ascribed that diffusion rate inside and outside of sulfur ions and cation is different.38,39 The formation of an internal cavity is described to a diffusion-controlled ion exchange process that is widely used to create metal-centric sulfide structures.40,41
Fig. 2 shows the typical morphology and microstructure of prepared Co3O4/CoS1.097 composite samples. SEM images in Fig. 2a and b show the morphology of the entire prism is more regular. The morphological images can be clearly seen that the synthesized Co-precursor is a solid structure. The images of the Co-precursor after TAA sulfidation (Fig. 2) shows successful conversion to a hollow prismatic sulfide structure consisting of a number of interconnected subunits. TEM image in Fig. 2c clearly shows the comparison between the hollow structure and particle shell of prismatic sulfide product. In XRD pattern, all Bragg peaks were approximated to Co3O4/CoS1.097 (JCPDS card numbers 19-0366, 43-1003). The corresponding X-ray diffraction (XRD, Fig. 2d) pattern confirms that the Co-precursor crystalline has a hydroxide phase of tetragonal cobaltate without any impurities.42 Prism-like precursor under the sulfidation treatment with thioacetamide, the diffraction peak (Fig. 2d) of the obtained particles proved to be Co3O4/CoS1.097 composite structure. Because of low intensity and broad XRD peaks, as-synthesized Co3O4/CoS1.097 composite consisted of small size nanocrystals. HRTEM images in Fig. 3 clearly shows that the rupture of the vulcanized product, the thickness of the prismatic cobalt sulfide composite wall is about 20 nm. The lattice fringes of the Co3O4/CoS1.097 composite structure are calculated as 0.29 and 0.478 nm, which can be well assigned to the (100) and (101) planes of the hexagonal CoS1.097 and Co3O4 phase, respectively.
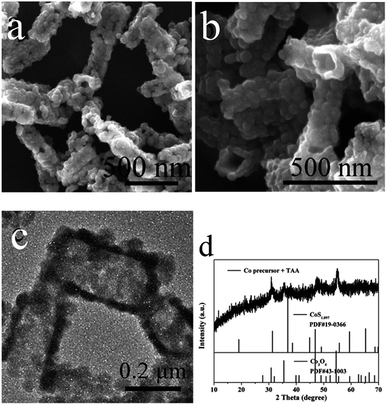 |
| Fig. 2 SEM, TEM images and XRD patterns of prismatic Co-precursors after sulfidation with TAA. (a) SEM, (b) SEM, (c) TEM, (d) XRD. | |
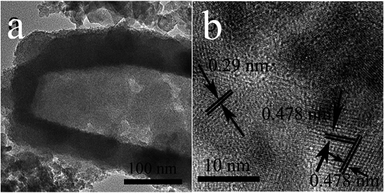 |
| Fig. 3 HRTEM images of Co3O4/CoS1.097 prisms. | |
To further investigate the elemental composition and chemical state of the composite, XPS analysis is performed and the results are presented in Fig. 4. The elements of Co, O and S can easily be identified through the characteristic peaks of Co 2p, O 1s and S 2p. C element is due to exposure to atmosphere. The high-resolution Co 2p spectrum for Co3O4/CoS1.097 composite structure in Fig. 4b can be deconvoluted into two spin–orbit doublets, corresponding to Co 2p and Co 3p, and two shake-up satellites (identified as “Sat”).43 Fig. 4c shows the high-resolution spectrum of S 2p, which the S 2p peak located at 161.4 eV and the Co 2p peak centered at 778.0 eV correspond to the characteristics of cobalt sulfide.44 Therefore, XPS spectra shows that the elements of Co3O4/CoS1.097 composite structure is related to Co 2p, Co 3p, O 1s and S 2p.
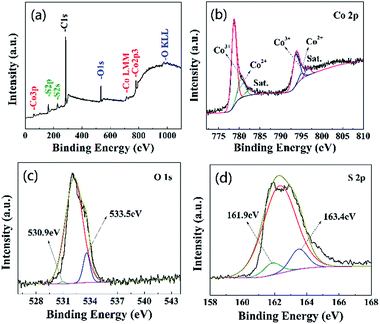 |
| Fig. 4 XPS spectra of Co3O4/CoS1.097 composites. (a) Survey spectra; (b) Co 2p; (c) S 2p; (d) O 1s. | |
The hollow prismatic Co3O4/CoS1.097 subunits uniformly grow on the surface of their upper prisms during these stratified morphological evolution based on solid Co-precursors. It is worth mentioning that temperature and TAA plays an important role in the morphology of Co3O4/CoS1.097 hollow prism. When the amount of organic ligand is not enough, only a small part of Co3O4/CoS1.097 forms on the surface of Co3O4-precursor particles. Conversely, excess reactants can cause overgrowth of reactions, formation of multistage subunits, and destruction of the prism shape. In addition, high temperature lead to the collapse of the Co3O4/CoS1.097 structure. To investigate the effect of solvent, isopropanol and methanol was used instead of ethanol. However, the morphology of precursors changed into irregular particles. Similar result was reported.37 Thus, synthesis in an ethanol solution plays an important role in creating hollow prismatic shape.
To further study the changes of the prism Co-precursor and Co3O4/CoS1.097 composite, we annealed the samples at 350 °C in nitrogen for 2 h with a ramp rate of 2 °C min−1, the XRD patterns are shown in Fig. 5. After annealed, the Co-precursor turned to Co3O4 (JCPDF no. 43-1003) (Fig. 5a), while with the TAA raising to three times more than Co3O4/CoS1.097 composite and reaction times increasing to 12 hours, the sample was changed into CoS1.097. This is confirmed from the XRD pattern in Fig. 5b. The mechanism of Co3O4/CoS1.097 composite changed into CoS1.097 is ascribed to enormous TAA offers lot of S ions for anion changing reaction. During heat-treatment, the S ions replaced O2− in Co3O4/CoS1.097 composite to form CoS1.097.
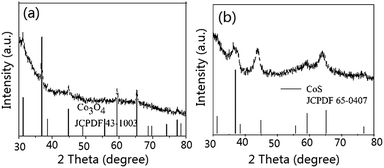 |
| Fig. 5 XRD patterns of Co-precursor calcined at 350 °C for 2 h without (a) and with (b) TAA treatment. | |
3.2 Supercapacitor property
Next, we evaluated the electrochemical properties of as prepared hollow prism Co3O4/CoS1.097 composite as an over-charged material. Since the hollow prism Co3O4/CoS1.097 with a porous structure not only provides richer redox electrochemistry and more electrochemically active sites, it also contributes to the excellent SCs electrode material properties of Co3O4 and CoS1.097.
In order to study the influence of the capacitance of the hollow prism Co3O4/CoS1.097 composite, the stability of hollow prism Co3O4/CoS1.097 composites at different scanning rates was measured. Fig. 6 depicts the CV curve of a hollow prismatic Co3O4/CoS1.097 composite at a scan rate of 10, 20, 50 and 100 mV s−1. Obviously, all composite electrodes reveal similar morphological CV plots with a pair of redox peaks in the potential range of 0–0.5 V.
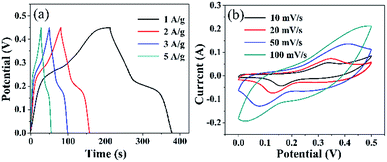 |
| Fig. 6 (a) Galvanostatic charge/discharge curves of Co3O4/CoS1.097 composites at different current densities, (b) CV curves of Co3O4/CoS1.097 composites at different scan rates. | |
The peaks were mainly due to the reversible redox reaction of the Co2+/Co3+ redox couple with OH− anion in alkaline electrolytes, such as CoS1.097.45 With the increasing of scan rate, the integrated area of the CV curve of the composite electrode increases to the maximum (at 4 cycles) and then decreases, indicating that the hollow prismatic Co3O4/CoS1.097 composite has the largest specific capacitance. With the increase of CoS1.097 content, the declining tendency of the capacitance can be explained by the surface of the Co3O4 nanosheet and the occupied space between the nanosheets is occupied or blocked by an excessive amount of CoS1.097 particles, which reduces the active surface area of Co3O4/CoS1.097 the composite electrode. Fig. 6 shows the specific capacitance of a hollow prism of Co3O4/CoS1.097 at different current densities. The longer the discharge time, the greater the specific capacitance. The trend of capacitance is the same as CV analysis.
From the CV curves of hollow prism Co3O4/CoS1.097 complexes recorded in Fig. 6, various potential scanning speeds are observed. Pairs of well-defined anode and cathode signals clearly show over the entire scan range from 10, 20, 30, 50 and 100 mV s−1. The current response increases with increasing scan. All the curves show a similar shape, indicating rapid current sensing of the electrolyte between electrode and electrode, excellent electrochemical reversibility, and high rate performance.46 In order to further evaluate the performance of the hollow prism Co3O4/CoS1.097 electrode, GCD was measured at a current density of 1, 2, 3 and 5 A g−1. All the curves have good symmetry but deviate from the flat line, indicating that the capacitance is mainly from the Faraday pseudo phase. For CoS1.097 materials, the electronic chemical test is in Fig. 7. Fig. 7a the GCD curve is almost symmetric even at current densities of 1, 2, 3 and 5 A g−1, the specific capacitance up to 965, 890, 825 and 710 F g−1, respectively. The result is better compared with that reported in literature.20 In that case, the specific capacitance is 555 F g−1 at current density of 5 A g−1. The stability of the sample is high because the specific capacitance is almost remained unchanged after 5000 cycles. Which is higher than the materials above. Their perfect properties made them promising candidates for the preparation of supercapacitors, lithium-ion batteries, and other fields. The perfect properties maybe due to the good interfacial contact between hollow prismatic CoS1.097, voids and internal cavities, fast electron transport, and equivalent series resistance is low.
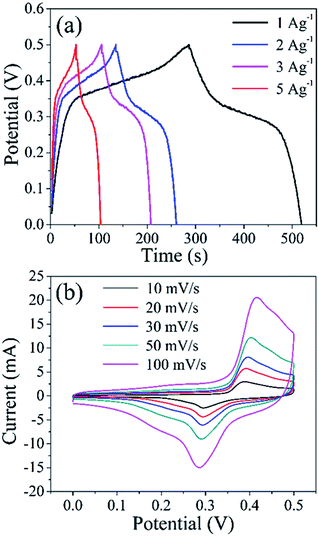 |
| Fig. 7 (a) Galvanostatic charge/discharge curves of CoS1.097 at different current densities, (b) CV curves of CoS1.097 at different scan rates. | |
4. Conclusions
In summary, we synthesized hollow prismatic Co3O4/CoS1.097 composite structure and CoS1.097 materials consisting of interconnected particles using a simple two-step adaptive approach. The first solid prismatic cobalt precursor was composed of cobalt oxyhydroxide, followed by solid cobalt hydroxyacetate as a template for further reaction to react with TAA to form a hollow prismatic CoS1.097 composite structure. Formation of hollow structure is described to a diffusion control processes. Benefit from the structural advantages, the ultimate stratified hollow prismatic CoS1.097 structure as an active material for super capacitor to enhanced electrochemical performance. In particular, these hollow prismatic CoS1.097 structures have higher specific capacity and high cycle stability.
Conflicts of interest
There are no conflicts to declare.
Acknowledgements
This work was supported by the projects from National Natural Science Foundation of China (grant no. 51572109 and 51772130).
References
- B. Dunn, H. Kamath and J. M. Tarascon, Science, 2011, 334, 928 CrossRef CAS PubMed.
- J. L. Lv, T. X. Liang and M. Yang, Colloids Surf., A, 2017, 529, 58 Search PubMed.
- M. Zhi, C. C. Xiang, J. T. Li, M. Li and N. Q. Wu, Nanoscale, 2013, 5, 72 RSC.
- P. Simon and Y. Gogotsi, Nat. Mater., 2014, 7, 848 Search PubMed.
- X. Zhang, J.-P. Veder, S. He and S. P. Jiang, Chem. Commun., 2019, 55, 1233 RSC.
- J. Jiang, Y. Y. Li, J. P. Liu, X. T. Huang, C. Z. Yuan and X. W. Lou, Adv. Mater., 2012, 24, 5178 Search PubMed.
- M. R. Gao, Y. F. Xu, J. Jiang and S. H. Yu, Chem. Soc. Rev., 2013, 42, 2994 RSC.
- Y. Wang, Y. Zhang, Y. Peng, H. Li, J. Li, B. Hwang and J. Zhao, Electrochim. Acta, 2019, 299, 489 CrossRef CAS.
- K. Krishnamoorthy, G. K. Veerasubramani and S. J. Kim, Mater. Sci. Semicond. Process., 2015, 40, 781 CrossRef CAS.
- Y. Yin, C. K. Erdonmez, A. Cabot, S. Hughes and A. P. Alivisatos, Adv. Funct. Mater., 2006, 16, 1389 CrossRef CAS.
- J. Zhang, L. Yu and X. W. Lou, Nano Res., 2017, 10, 4298 CrossRef CAS.
- M. Lao, G. Zhao, X. Li, Y. Chen, S. X. Dou and W. Sun, ACS Appl. Energy Mater., 2018, 1, 167 CrossRef CAS.
- Q. Wang, L. Jiao, Y. Han, H. Du, W. Peng, Q. Huan, D. Song, Y. Si, Y. Wang and H. Yuan, J. Phys. Chem. C, 2011, 115, 8300 CrossRef CAS.
- H. Pang, C. Z. Wei, X. X. Li, G. C. Li, Y. H. Ma, S. J. Li, J. Chen and J. S. Zhang, Sci. Rep., 2014, 4, 3577 CrossRef PubMed.
- X. Huang, Z. Y. Zeng and H. Zhang, Chem. Soc. Rev., 2013, 42, 1940 Search PubMed.
- L. F. Shen, J. Wang, G. Y. Xu, H. S. Li, H. Dou and X. G. Zhang, Adv. Energy Mater., 2015, 5, 6 Search PubMed.
- Z. Yang, C. Chen and H. Chang, J. Power Sources, 2011, 196, 7874 CrossRef CAS.
- Y. Z. Gao, Q. S. Lin, G. Zhong, Y. B. Fu and X. H. Ma, J. Alloys Compd., 2017, 704, 74 CrossRef.
- Y. Tang, S. Chen, S. Mu, T. Chen, Y. Qiao, S. Yu and F. Gao, ACS Appl. Mater. Interfaces, 2016, 8, 9721 CrossRef CAS PubMed.
- Q. Wang, L. Jiao, H. Du, J. Yang, Q. Huan, W. Peng, Y. Si, Y. Wang and H. Yuan, CrystEngComm, 2011, 13, 6960 RSC.
- S. M. Liu, J. X. Wang, J. W. Wang, F. F. Zhang, F. Liang and L. M. Wang, CrystEngComm, 2014, 16, 816 Search PubMed.
- Y. Zhao, Z. Shi, T. Lin, L. Suo, C. Wang, J. Luo, Z. Ruan, C. Wang and J. Li, J. Power Sources, 2019, 412, 321 CrossRef CAS.
- L. J. Sun, L. Lu, Y. Bai and K. N. Sun, J. Alloys Compd., 2016, 654, 198 CrossRef.
- L. Zhang, H. B. Wu and X. W. Lou, Chem. Commun., 2012, 48, 6913 Search PubMed.
- F. Cao, M. Zhao, Y. Yu, B. Chen, Y. Huang, J. Yang, X. Cao, Q. Lu, X. Zhang, Z. Zhang, C. Tan and H. Zhang, J. Am. Chem. Soc., 2016, 138, 6924 CrossRef CAS PubMed.
- B. X. Wang, X. L. Wu, Y. G. Guo, Y. T. Zhong, X. Q. Cao, Y. Ma and J. N. Yao, Adv. Funct. Mater., 2010, 20, 1684 CrossRef.
- X. D. Xu, W. Liu, Y. S. Kim and J. Cho, Nano Today, 2014, 9, 620 CrossRef.
- M. R. Gao, Y. F. Xu, J. Jiang and S. H. Yu, Chem. Soc. Rev., 2013, 42, 2995 RSC.
- X. Huang, Z. Y. Zeng and H. Zhang, Chem. Soc. Rev., 2013, 42, 1940 Search PubMed.
- F. L. Luo, J. Li, H. Y. Yuan and D. Xiao, Electrochim. Acta, 2014, 123, 185 CrossRef.
- Z. Jiang, W. J. Lu, Z. P. Li, K. H. Ho, X. Li, X. l. Jiao and D. R. Chen, J. Mater. Chem. A, 2014, 2, 8604 Search PubMed.
- Q. R. Hu, S. L. Wang, Y. Zhang and W. H. Tang, J. Alloys Compd., 2010, 491, 709 Search PubMed.
- S. Z. Li, J. Wen, T. Chen, L. B. Xiong, J. B. Wang and G. J. Fang, Nanotechnology, 2016, 27, 145401 CrossRef PubMed.
- C. K. Ranaweera, Z. Wang, E. Alqurashi, P. K. Kahol, P. R. Dvornic, B. P. Kumar Gupta, K. Ramasamy, A. D. Mohite, G. Gupta and R. K. Gupta, J. Mater. Chem. A, 2016, 4, 9016 RSC.
- D. J. Zhang, H. X. Liu, J. C. Zhang, X. Wang, R. C. Zhang and J. Y. Zhou, Int. J. Electrochem. Sci., 2016, 11, 6795 Search PubMed.
- J. Lin, J. l. Cui, F. P. Cheng, Y. F. Cui, H. L. Sun and J. C. Sun, J. Alloys Compd., 2017, 695, 2176 Search PubMed.
- L. Yu, J. F. Yang and X. W. Lou, Angew. Chem., 2016, 55, 13422 CrossRef CAS PubMed.
- Z. Q. Liu, H. Cheng, N. Li, T. Y. Ma and Y. Z. Su, Adv. Mater., 2016, 28, 37780 Search PubMed.
- X. M. Song, L. c. Tan, X. l. Wang, L. Zhua, X. Q. Yia and Q. Dong, J. Electroanal. Chem., 2017, 794, 135 CrossRef.
- Y. Li, S. T. Liu, W. Chen, S. Li, L. L. Shi and Y. Zhao, J. Alloys Compd., 2017, 712, 142 Search PubMed.
- T. Y. Huang, M. He, Y. M. Zhou, S. W. Li, B. B. Ding, W. L. Pan, S. Huang and Y. Tong, Synth. Met., 2017, 224, 50 CrossRef.
- F. Tao, Y. Q. Zhao, G. Q. Zhang and H. L. Li, Electrochem. Commun., 2007, 9, 1284 CrossRef.
- J. F. Shen, X. W. Xu, P. Dong, Z. Q. Zhang, R. Baines, J. Ji, Y. Pei and M. G. Ye, Ceram. Int., 2016, 42, 8120 CrossRef CAS.
- L. Xu and Y. Lu, RSC Adv., 2015, 5, 67518 RSC.
- J. L. Lv, T. X. Liang, M. G. Yang, K. Suzukia and H. Miura, Colloids Surf., A, 2017, 529, 57 CrossRef CAS.
- N. Li, X. Liu, G. D. Li, Y. Y. Wu, R. Q. Gao and X. X. Zou, Int. J. Hydrogen Energy, 2017, 42, 9914 CrossRef CAS.
|
This journal is © The Royal Society of Chemistry 2019 |
Click here to see how this site uses Cookies. View our privacy policy here.