DOI:
10.1039/C9RA00355J
(Paper)
RSC Adv., 2019,
9, 7314-7320
Preparation of polyimide films via microwave-assisted thermal imidization
Received
15th January 2019
, Accepted 18th February 2019
First published on 5th March 2019
Abstract
A series of polyimide (PI) films based on aromatic heterocyclic monomers of 3,3′,4,4′-biphenyltetracarboxylic dianhydride (BPDA), p-phenylenediamine (p-PDA) and 4,4′-oxydianiline (ODA) were prepared via a microwave-assisted thermal imidization and conventional thermal imidization method at different temperatures. The effects of microwave irradiation on the imidization degree, microstructures, mechanical and thermal properties of PI films were investigated. The imidization degree of the PI films treated with microwave-assisted heating reached a relatively high value at 250 °C, which was twice as much as those treated with traditional thermal imidization. The tensile strength and modulus of PI films treated with microwave-assisted imidization at 300 °C were 187.61 MPa and 2.71 GPa respectively, which were 30% higher than those of PI films treated with thermal imidization. Moreover, the order degree of polymer chains was improved by the microwave-assisted imidization method. The PI films prepared by the microwave-assisted imidization method showed excellent thermal stability with a 5% weight loss temperature of 573 °C under N2. The microwave-assisted thermal imidization proved to be a rapid and efficient way to prepare high-performance polyimide materials.
1 Introduction
As an important member in the class of high-performance polymers, polyimides (PIs) have been widely used in the aerospace industry and in microelectronics, as well as in engineering due to their excellent mechanical properties, thermal stability, chemical resistance, radiation resistance and dielectric performance.1–3 A typical two-step method is mainly adopted in preparing PI films, involving the synthesis of polyamide acid (PAA) precursors primarily and the imidization process through thermal or chemical treatment.4,5 The intermediate PAA is converted to PI by the imidization route and this process plays a decisive role on the final properties of PI products. However, during the thermal imidization process, both imidization and crystallization happen simultaneously at 150–350 °C, resulting in the brittleness of materials,6,7 and side effects including oxidation and degradation tend to occur at high temperatures.8–10 In addition, high energy cost and insufficient utilization of resources should be considered with elevated temperature. Due to these limitations, it is meaningful to exploit novel imidization method to obtain high-performance PI products efficiently.
Microwave is a nonionizing electromagnetic energy and is widely used in the chemical field recently.11–15 Compared to the conventional heating method, microwave heating can reduce the activation energy of chemical reactions and induce orientation effects of dipolar molecules.16–18 Imai et al. investigated the microwave-assisted synthesis of polyamides and PIs and indicated that microwave is a facile and rapid method in the presence of appropriate solvents.19,20 Li et al. synthesized PAAs by microwave-assisted polycondensation of aromatic dianhydrides and diamines, showing that the intrinsic viscosities of PAA solutions increased and the reaction time was shorten with microwave irradiation.21 Lin et al. used the microwave-assisted heating method to prepare a crystalline PI, and the polymerization time reduced to 10 minutes by using CuO as microwave absorber.22 Govindaraj prepared MWCNT/PI nanocomposites by microwave-assisted heating method. The nanocomposites synthesized by microwave-assisted heating exhibited a higher glass transition temperature (270 °C) than those synthesized by conventional heating (241 °C), indicating that microwave induced synchronous heating and achieved fast ensemble reaction.23,24 According to previous reports, the mechanism of energy transfer in microwave heating occurs by electric dipolar coupling of the radiation to permanent dipole moments in the polymer, rather than by thermal conductivity as in conventional processing, so that the energy can be absorbed by polymer chains more uniformly and rapidly.11,25 Meanwhile, microwave radiation may help to eliminate small molecules such as water in the polymerization and thus the equilibrium reactions shifts to higher yield.26,27 However, only a limited amount of research have focused on mechanism during the synthesis of PAAs or PIs by microwave. Seldom reference has concentrated on the structural evolutions and properties of PI products prepared by microwave-assisted thermal imidization.
Aiming at improving the imidization efficiency, a series of PI films were prepared by copolymerization of 3,3′,4,4′-biphenyltetracarboxylic dianhydride (BPDA), p-phenylenediamine (p-PDA) and 4,4′-oxydianiline (ODA), followed by microwave-assisted thermal imidization at 100–300 °C. The effects of microwave on the imidization degree, aggregation structure, mechanical and thermal property of the final PI films were discussed and the relationship between structure and properties during imidization were established. This study will provide a rapid and green production of PIs by microwave-assisted thermal imidization.
2 Experimental
2.1 Materials
The monomer BPDA was purchased from Shijiazhuang Hai Li Chemical Company and purified by sublimation prior to use. The monomers 4,4′-ODA and p-PDA were purchased from Beijing Sinmaya Chemicals Co., Ltd. and recrystallized in ethyl acetate prior to use. The solvent DMAc (analytical pure) was purchased from Tianjin Fu Chen Chemicals Reagent Factory and utilized after distillation.
2.2 Preparation of PI films
The PI films were prepared by a two-step method according to the following process. The reaction process is shown in Scheme 1. The mixture of diamines with a p-PDA/ODA molar ratio of 7/3 was firstly dispersed in DMAc solvent by stirring in the dried atmosphere. After the diamines were almost dissolved, the equimolar dianhydride BPDA was added gradually. After stirring for 5 h at low temperature, the PI films were prepared by first coating viscous PAA solution with 15 wt% solid content on glass plate and air drying, and then imidized by heating in a microwave muffle furnace with a microwave magnetron and infrared temperature control system, heating procedure was performed from 20 °C to different holding temperature at 100 °C, 150 °C, 200 °C, 250 °C and 300 °C for 10 min with a heating rate of 10 °C min−1. The samples were named as MW-PI-100, MW-PI-150, MW-PI-200, MW-PI-250, and MW-PI-300 according to the treatment temperature, respectively. To make comparison, the PI films were prepared by thermal imidization in an oven at the same temperatures, which were named as T-PI-100, T-PI-150, T-PI-200, T-PI-250 and T-PI-300. The thickness of the PI films were 20–50 μm.
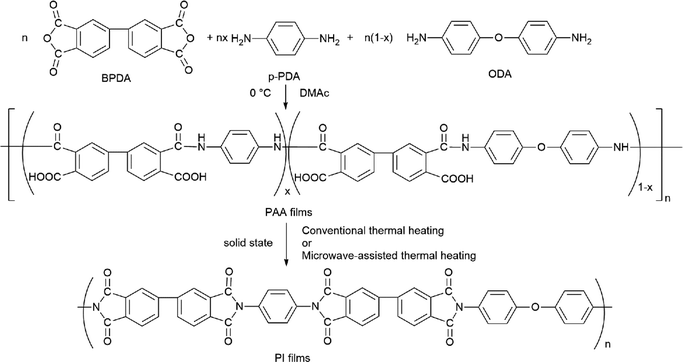 |
| Scheme 1 The process of preparation of PI films with BPDA, ODA, and p-PDA; x = 0.7. | |
2.3 Characterization
Fourier transform infrared (FTIR) spectra were obtained on Nexus 670 instrument with the scanning wavenumbers ranging from 4000 to 400 cm−1. The samples were obtained by applying attenuated total reflexion mode. The imidization degree (ID) can be calculated using the equation: |
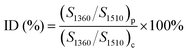 | (1) |
where S is the area of the absorption band and subscript p and c represent precursor films and the fully cured PI films respectively. Wide angle X-ray diffraction (WAXD) studies were performed using a Bruker AXS D8 ADVANCE X-ray diffractometer (Karlsruhe, Germany) in the 5–40 °C at a scanning rate of 10° min−1. The instrument employs Cu Kα radiation (λ = 0.154056 nm) and operates at 40 kV and 40 mA. The order degree X of macromolecule can be confirmed by the following equation: |
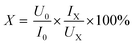 | (2) |
where U0 and UX denote to the backgrounds of the reference sample and experimental sample, and I0 and IX are integral intensities of diffraction lines of the reference sample and experimental sample, respectively. Dynamic mechanical analysis (DMA) was performed on a DMA Q800 system with a load frequency of 1 Hz and heating rate of 5 °C min−1 at the temperature ranging from 50 to 450 °C. The glass transition temperatures of the PI films were measured by a DMA Q800 system with a heating rate of 3 °C min−1 under nitrogen atmosphere. Thermo gravimetric analysis (TGA) measurements were carried out on a TGA Q50 system with a heating rate of 10 °C min−1 from 30 °C to 900 °C under nitrogen. Mechanical properties were measured with a SANS CMT-4104 universal testing instrument using a 100 newton load transducer at a rate of 10 mm min−1 according to GB/T 1040.3-2006.
3 Results and discussion
3.1 Chemical structure and imidization degree
The chemical structures of MW-PI and T-PI films prepared at different temperatures are confirmed by FTIR spectra, as shown in Fig. 2. Generally, PI exhibit four characteristic absorption bands: 1778 cm−1 for C
O asymmetrical stretching, 1715 cm−1 for C
O symmetrical stretching of imide groups, 1360 cm−1 for C–N stretching and 732 cm−1 for C
O bending of imide ring. The absorption peaks at 1658, 1552 and 1316 cm−1 are assigned to the amide-I band, amide-II band and amide CN stretching vibration of PAA, respectively.28–30 In addition, the absorption bands at 1228 and 1014 cm−1 are assigned to the C–O–C stretching vibration of the aryl ether in ODA moiety. With increasing temperature, the characteristic peaks of PI get stronger accompanied by a gradual decrease in the absorption peaks of PAA, implying the gradual conversion of CONH groups to the cycloimide rings.31 In Fig. 1(b), the CN stretching band at 1316 cm−1 disappears at temperatures higher than 250 °C, indicating that the conversation from PAA to PI is mainly completed as the film are heated by microwave-assisted method at 250 °C. However, in Fig. 1(a), the CN stretching band of PAA is still existed even as the films are thermal treated at 300 °C, demonstrating that the cyclization temperature is reduced and the imidization efficiency is improved by microwave-assisted method.32
 |
| Fig. 1 FTIR spectra of the PI films (a) treated with thermal imidization; (b) treated with microwave-assisted thermal imidization. | |
Table 1 lists the IDs of MW-PI and T-PI films with different temperatures. The ID of MW-PI-300 is set as 100%. It is obvious that the IDs of MW-PI films are higher than those of T-PI films. The ID values of T-PI-200 and WM-PI-200 films are calculated as 37.87% and 68.91%. The ID value of MW-PI-250 is 98.83%, which is in well accordance with the disappearance of PAA structure in FTIR spectra. The ID value of T-PI-300 is lower than that of MW-PI-250, indicating that the microwave-assisted heating method can accelerate the imidization process and reduce the cyclization temperature significantly.
Table 1 The imidization degree (ID) of PI films with different treatment temperatures
Temperature (°C) |
T-PI (%) |
MW-PI (%) |
100 |
0.51 |
0.74 |
150 |
17.04 |
21.37 |
200 |
37.87 |
68.91 |
250 |
65.91 |
98.83 |
300 |
91.61 |
100.00 |
3.2 Aggregation structure
The aggregation structure of the PI films are characterized by WAXD, as displayed in Fig. 2. All the PI films exhibit broad peaks, representing a typical amorphous structure. Meanwhile, the films treated with microwave-assisted heating show narrower peaks than those treated with thermal imidization, demonstrating a certain extent of ordered arrangement of the macromolecules. Table 2 shows the macromolecular order degree of MW-PI and T-PI films with different treatment temperatures. The macromolecular order degrees of both MW-PI and T-PI films increase with increasing treatment temperature, which is mainly due to the improvement of imidization degree and molecular chain rigidity.33 It should be noted that the macromolecular order degrees of the T-PI films are lower than those of MW-PI films, indicating that microwave can improve the order degree of polymer chains and promote the regular alignment of molecular chains. This phenomena is ascribed to the increment of imidization degree and the enhancement of molecular chain rigidity of MW-PI films, which is confirmed by FTIR results.
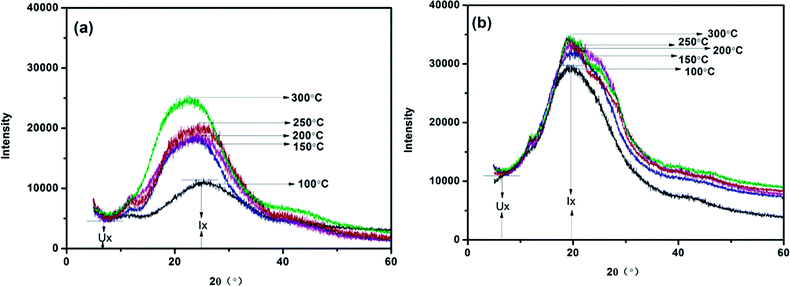 |
| Fig. 2 The WAXD profiles of the PI films (a) treated with thermal imidization; (b) treated with microwave-assisted thermal imidization. | |
Table 2 The macromolecular order degree of PI films
Temperature (°C) |
T-PI |
MW-PI |
100 |
2.37U0/I0 |
3.09U0/I0 |
150 |
3.03U0/I0 |
3.82U0/I0 |
200 |
3.21U0/I0 |
3.99U0/I0 |
250 |
3.88U0/I0 |
4.91U0/I0 |
300 |
3.95U0/I0 |
4.92U0/I0 |
3.3 Thermal properties
Fig. 3 illustrates the DMA curves of the PI films with different treatment temperatures. In Fig. 3(a), two relaxation processes at about 180 °C and 305 °C can be identified above room temperature, representing α relaxation of PAA and PI backbones respectively.34 The α relaxation of PAA backbone of T-PI-150 is obvious in Fig. 3(b), implying that a large number of PAA moieties are still existed as the films are thermal treated at 150 °C. While, the disappearance of α relaxation of PAA in MW-PI-150 demonstrates that microwave accelerate the imidization process and the PAA moieties are converted into PI ones at 150 °C. The T-PI-300 films possesses a glass transition temperature (Tg) of 306.3 and a tan
δ value of 0.437, and the MW-PI-300 films shows a Tg of 308.2 and a tan
δ value of 0.273. It should be noted that the α relaxation process corresponds to segmental motion which is attributed to a mobile amorphous region of polymer materials. The intensity of the a relaxation (tan
δ value) reflect the energy level of segmental motion of the prepared PI films which are non-crystalline.35 Thus, the higher Tg and lower tan
δ values of MW-PI films indicates that the chain movement is hindered and the inter-segment fictions decreases. As revealed by FTIR and WAXD, the imidization degree and macromolecular order degree of PI films were significantly improved by microwave-assisted heating, resulting in the improvement of chain rigidity and the decline of segmental motion. Interestingly, the DMA curves of T-PI films shows two slight peaks at about 280 °C and 320 °C, exhibiting a block structure due to the formation of BPDA/ODA and BPDA/PDA segments.36,37 While, the block structure of MW-PI films disappeared, implying the microwave-assisted heating process may have a positive effect on eliminate the block structure of co-PI films.
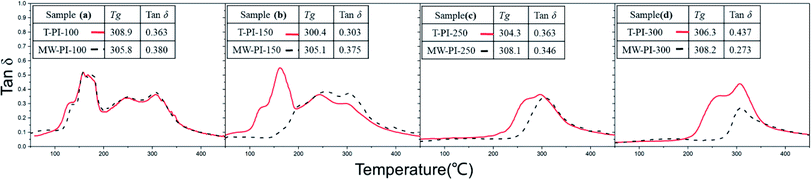 |
| Fig. 3 DMA curves of PI films treated with different temperatures (a) 100 °C; (b) 150 °C; (c) 250 °C; (d) 300 °C. | |
The thermal stabilities of the T-PI films and MW-PI films with different treatment temperatures are illustrated in Fig. 4. The weight loss in the range of 200–400 °C of PI films corresponds to the removal of the existing solvents and the elimination of H2O during cyclization process.38 Table 3 lists the weight loss between 200 °C and 400 °C of T-PI and MW-PI films with different treatment temperatures. As for T-PI films, the weight loss decreases from 13.2% to 7.5% with increasing treatment temperature, implying the improvement of imidization degree. And the weight loss in this stage can be observed as the films are thermal treated at 300 °C, which verifies the existence of PAA moieties. In Fig. 4(b), the weight loss in the range of 200–400 °C of MW-PI films decreases from 9% to 0.7% with increasing treatment temperature. The curves of MW-PI-300 shows a platform in this stage, implying the complete formation of PI structure as treated by microwave heating at 300 °C. According to previous study, the BPDA/PDA/ODA PI with a high imidization degree prepared by traditional heating process has a 5% weight loss temperature (Td5) of about 560 °C.39 The Td5 values of MW-PI-300 is 573 °C, indicating that microwave has positive effect on improving the thermal stabilities of PI films.
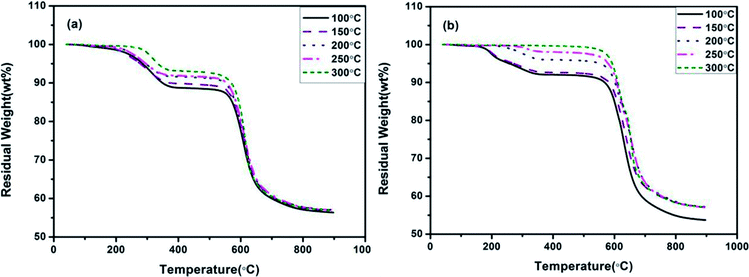 |
| Fig. 4 TGA curves of PI films (a) treated with thermal imidization at 100, 150, 200, 250, 300 °C; (b) treated with microwave-assisted imidization at 100, 150, 200, 250, 300 °C. | |
Table 3 The weight loss of PI films in the range of 200–400 °C
Temperature (°C) |
T-PI (%) |
MW-PI (%) |
100 |
13.2 |
9.0 |
150 |
10.5 |
8.8 |
200 |
8.3 |
4.7 |
250 |
8.4 |
2.6 |
300 |
7.5 |
0.7 |
3.4 Mechanical properties
Fig. 5 depicts the mechanical properties such as Young's modulus, tensile strength and elongation at break of MW-PI and T-PI films with different treatment temperatures. The tensile strength and modulus of T-PI and MW-PI films increase with rising temperature, reaching the optimum values at 300 °C. The T-PI-300 possesses tensile strength of 138.51 MPa and a modulus of 1.96 GPa. The tensile strength and modulus of MW-PI-300 are up to 187.61 MPa and 2.71 GPa, which are about 30% higher than those of T-PI-300 films. The imidization degree and macromolecular order degree are responsible for the variation of tensile strength and modulus. The MW-PI films show higher imidization and macromolecular order degrees than T-PI ones, thus resulting in preferable tensile strength and modulus. The elongation at break of PI films exhibits relatively low values in the temperature range of 150–250 °C because of the degradation of the PAA chains during imidization.40 The elongation at break of MW-PI-250 increases to 40.57%, indicating the degradation period of PAA are shorten by microwave-assisted heating.
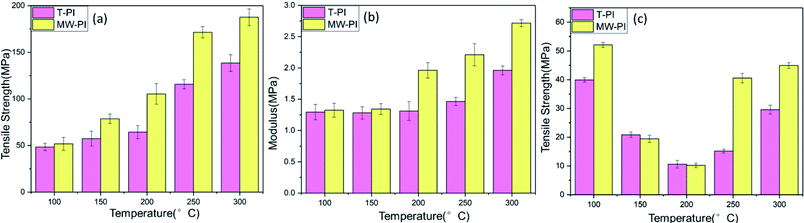 |
| Fig. 5 Mechanical properties of PI films (a) tensile strength; (b) Young's modulus; (c) elongation at break. | |
4 Conclusions
Series of PI films based on BPDA, p-PDA and ODA systems were successfully prepared by microwave-assisted thermal imidization and traditional thermal imidization method at 100–300 °C, respectively. The MW-PI films showed higher tensile strength, Young's modulus and elongation, Td5 as well as Tg values that T-PI ones. The MW-PI films prepared at 300 °C possess a high Td5 value of 573 °C and tensile strength of 187.61 MPa. The significant enhancements of mechanical and thermal properties are by microwave-assisted heating method are ascribed to the improvement of imidization and macromolecular order degrees, which are confirmed by the FTIR and WAXD results. The microwave-assisted heating method had a positive effect on improving the imidization degree and regular alignment of molecular chains, thus reducing the imidization temperature as well as uprating the overall performance of the PI films. In brief, the microwave-assisted thermal imidization proves to be a rapid and efficient way to prepare high-performance polyimide materials.
Conflicts of interest
There are no conflicts to declare.
Acknowledgements
The authors greatly thank the financial support from the National Key Research and Development Program of China (Project No. 2017YFB0307600), the National Natural Science Foundation of China (Project No. 51373008) and the Aeronautical Science Foundation of China (Project No. 201718S9001).
Notes and references
- M. Hasegawa and K. Horie, Prog. Polym. Sci., 2001, 26, 259–335 CrossRef CAS.
- H. R. Kricheldorf, Adv. Polym. Sci., 1999, 141, 325–326 CrossRef.
- L. Luo, Y. Pang, X. Jiang, X. Wang, P. Zhang, Y. Chen, C. Peng and X. Liu, J. Polym. Res., 2012, 19, 9783 CrossRef.
- H. L. Tyan, Y. C. Liu and K. H. Wei, Polymer, 1999, 40, 4877–4886 CrossRef CAS.
- H. Inoue, Y. Sasaki and T. Ogawa, J. Appl. Polym. Sci., 1996, 60, 123–131 CrossRef CAS.
- K. Vanherck, G. Koeckelberghs and I. F. J. Vankelecom, Prog. Polym. Sci., 2013, 38, 874–896 CrossRef CAS.
- F. Liu, W. Yang, J. Zhang, E. Zhang, X. Qiu and X. Ji, Eur. Polym. J., 2017, 96, 429–442 CrossRef.
- S. I. Kuroda and I. Mita, Eur. Polym. J., 1989, 25, 611–620 CrossRef CAS.
- K. H. Becker and H. W. Schmidt, Macromolecules, 1992, 25, 6784–6790 CrossRef CAS.
- S. Kunnikuruvan, P. V. Parandekar, O. Prakash, T. K. Tsotsis, S. Basu and N. N. Nair, Macromol. Theory Simul., 2015, 24, 344–351 CrossRef CAS.
- M. Komorowska-Durka, G. Dimitrakis, D. Bogdał, A. I. Stankiewicz and G. D. Stefanidis, Chem. Eng. J., 2015, 264, 633–644 CrossRef CAS.
- H. Yeganeh, B. Tamami and I. Ghazi, Eur. Polym. J., 2004, 40, 2059–2064 CrossRef CAS.
- R. S. Varma, K. P. Naicker, D. Kumar, R. Dahiya and P. J. Liesen, J. Microwave Power, 1999, 34, 113–123 Search PubMed.
- J. Olvera-Mancilla, S. López-Morales, J. Palacios-Alquisira, D. Morales-Morales, R. L. Lagadec and L. Alexandrova, Polymer, 2014, 55, 1656–1665 CrossRef CAS.
- P. González-Morones, E. Hernández-Hernández, S. Fernández-Tavizón, R. Ledezma-Rodríguez, A. Sáenz-Galindo, G. C. Pliego, C. A. Ávila-Orta and R. F. Ziolo, Polymer, 2018, 146, 73–81 CrossRef.
- R. Correa, G. Gonzalez and V. Dougar, Polymer, 1998, 39, 1471–1474 CrossRef CAS.
- L. Q. Liao, L. J. Liu, C. Zhang, F. He, R. X. Zhuo and K. Wan, J. Polym. Sci., Part A: Polym. Chem., 2002, 40, 1749–1755 CrossRef CAS.
- Y. Hu, Y. He and H. Cheng, J. Cleaner Prod., 2018, 174, 1224–1233 CrossRef CAS.
- Y. Imai, H. Nemoto, S. Watanabe and M. Kakimoto, Polym. J., 1996, 28, 256–260 CrossRef CAS.
- Y. Imai, ACS Symp. Ser., 1995, 624, 421–430 CrossRef.
- Q. Li, X. Yang, W. Chen, C. Yi and Z. Xu, Macromol. Symp., 2010, 261, 148–156 CrossRef.
- L. Lin, P. Ye, C. Cao, Q. Jin, G. Xu, Y. Shen and Y. Yuan, J. Mater. Chem. A, 2015, 3, 10205–10208 RSC.
- B. Govindaraj and M. Sarojadevi, Polym. Compos., 2016, 37, 2417–2424 CrossRef CAS.
- B. Govindaraj and M. Sarojadevi, Polym. Adv. Technol., 2018, 29, 1718–1726 CrossRef CAS.
- M. Bardts, N. Gonsior and H. Ritter, Macromol. Chem. Phys., 2010, 209, 25–31 CrossRef.
- M. Fimberger and F. Wiesbrock, Adv. Polym. Sci., 2014, 274, 149–182 CrossRef.
- J. Chen, Q. Chen and X. Yu, J. Appl. Polym. Sci., 1996, 62, 2135–2138 CrossRef CAS.
- Y. Xu and Q. Zhang, Appl. Spectrosc., 2013, 68, 657–662 CrossRef PubMed.
- Y. Zhai, Q. Yang, R. Zhu and Y. Gu, J. Mater. Sci., 2008, 43, 338–344 CrossRef CAS.
- J. S. Tao and M. Ree, Macromol. Chem. Phys., 2002, 203, 791–800 CrossRef.
- M. Sun, J. Chang, G. Tian, H. Niu and D. Wu, J. Mater. Sci., 2016, 51, 2830–2840 CrossRef CAS.
- M. Othman, H. Akil, H. Osman and Z. Ahmad, Appl. Mech. Mater., 2015, 754–755, 251–255 Search PubMed.
- M. Zhang, H. Niu, Z. Lin, S. Qi, J. Chang, Q. Ge and D. Wu, Macromol. Mater. Eng., 2015, 300, 1096–1107 CrossRef CAS.
- S. Qi, W. Wang, D. Wu, Z. Wu and R. Jin, Eur. Polym. J., 2006, 42, 2023–2030 CrossRef CAS.
- H. Niu, M. Huang, S. Qi, E. Han, G. Tian, X. Wang and D. Wu, Polymer, 2013, 54, 1700–1708 CrossRef CAS.
- H. Chung, W. Jang, J. Hwang and H. Han, J. Polym. Sci., Part B: Polym. Phys., 2001, 55, 796–810 CrossRef.
- S. Qi, D. Wu, Z. Wu, W. Wang and R. Jin, Polymer, 2006, 47, 3150–3156 CrossRef CAS.
- K. Pramoda, S. Liu and T. Chung, Macromol. Mater. Eng., 2002, 287, 931–937 CrossRef CAS.
- J. Chang, H. Niu, M. He, M. Sun and D. Wu, J. Appl. Polym. Sci., 2015, 132, 42474 CrossRef.
- R. A. Dine-Hart and W. W. Wright, J. Appl. Polym. Sci., 1967, 11, 609–627 CrossRef CAS.
|
This journal is © The Royal Society of Chemistry 2019 |
Click here to see how this site uses Cookies. View our privacy policy here.