DOI:
10.1039/C8RA09961H
(Paper)
RSC Adv., 2019,
9, 7795-7802
The study of cationic waterborne polyurethanes modified by two different forms of polydimethylsiloxane
Received
4th December 2018
, Accepted 26th February 2019
First published on 8th March 2019
Abstract
Two kinds of dimethylpolysiloxane, KF-6001 and X-22-176-DX, were used to modify polyurethane. The effects of KF-6001 and X-22-176-DX on the colloidal, physico-chemical and surface properties were studied for polydimethylsiloxane modified cationic waterborne polyurethanes (SiCWPUs). The chemical structures and the surface morphologies of the SiCWPUs are characterized via Fourier transform infrared spectrometry and scanning electron microscopy. The results showed that the addition of siloxane changes the structure and surface morphology of the polyurethane. The element distributions in the polymer films were tested via X-ray photoelectron spectroscopy, and the effect of the hydrophobicity of the surfaces of the polymer films of the cationic waterborne polyurethanes was demonstrated via water contact angle tests on the surfaces of the films. As the amount of siloxane added increases, the silicon content on the surfaces of the SiCPWU1 films increases from 0% to 17.92%, and the actual silicon content on the surfaces of the films was much larger than the theoretical value. Therefore, the hydrophobicity of the membrane surface increases sharply, and the contact angle increases from 63.0° to 105.3°. Dynamic mechanical analysis indicates that the introduction of polydimethylsiloxane into the cationic aqueous polyurethane chain increases microphase separation in the polymer films. Stress–strain data showed that the mechanical properties of SiCPWU1 films were better than those of SiCPWU2 films when the same amounts of PDMS were added.
Introduction
Waterborne polyurethanes (WPUs) have been increasingly used in coatings, elastomers, and other materials, because they are environmentally friendly and show high strength, high elasticity, and versatile performance.1–4 At present, a commonly used method is to introduce PEG or DMPA into polymers to prepare waterborne polyurethanes, but there has been little research into cationic waterborne polyurethanes (CWPUs)5,6. CWPUs exhibit many unique characteristics, such as availability under acidic conditions, adhesion properties, antibacterial properties, and dustproof effects through electrostatic repulsion.7–10 These excellent characteristics give CWPUs the great potential to become high value-added materials.11,12 Nevertheless, the introduction of cationic groups into polyurethane segments could decrease the water resistance and surface hydrophobicity of WPU films. Therefore, most research has been focused on improving the performance of waterborne polyurethanes.13–15
Polydimethylsiloxane (PDMS) has unique properties, such as a low glass-transition temperature, low surface energy, good hydrophobicity, weather resistance, high flexibility and great thermal stability.16,17 The incorporation of PDMS into polyurethane segments has been a frequently-used and effective method to improve the physical and chemical properties of WPUs.18–20 Xu et al.21 prepared a blocking polyether silicone oil with an amino group modified CWPU, which was used as the finishing agent for cashmere knitted fabric. Li et al.22 researched the effects of the N-methyldiethanolamine content, the NCO/OH ratio, the trimethylolpropane content and other factors on the properties of polydimethylsiloxane polymers with monohydroxy modified cationic WPUs. A polydimethylsiloxane end-capped CWPU and polydimethylsiloxane with an amino group modified CWPU have been studied. However, most studies introduced PDMS into the main chain of the polyurethane, and little research has been concerned with polyurethane with PDMS as a side chain. The long PDMS segment in the form of a side chain could easily migrate to the surface.
In this work, in order to compare the effects of the form of polydimethylsiloxane on the polyurethane properties, two kinds of PDMS with dihydroxy groups were used to modify cationic waterborne polyurethane. And then, the effects of different structures of silicone on the performance of cationic waterborne polyurethanes were studied. The structures of the modified polyurethanes were characterized via Fourier transform infrared (FT-IR) spectroscopy. The microstructures, mechanical properties, thermal stabilities and surface properties of the polyurethane films were also compared in detail.
Experimental
Materials
Polypropylene glycol with a molecular weight of 2000 (PPG2000), purchased from Dragon Clan. Co. Ltd (Fujian, China), was placed under vacuum at 120 °C for 2 h before use. Dibutyltin dilaurate (DBTDL) and isophorone isocyanate (IPDI) were acquired from Wanhua Polyurethane. Co. Ltd (Yantai, China). PDMS (materials: KF-6001, Mn = 1800 g mol−1; and X-22-176-DX, Mn = 3600 g mol−1) was supplied by Shin-Etsu Chemical Industry Co. Ltd. (Tokyo, Japan). The chemical structures of the PDMS samples used are shown in Scheme 1. N-Methyl diethanolamine (MDEA) was provided by Huaxia Chemical Industry Co. (Chengdu, China). Acetic acid (HAc) and 1,4-butanediol (BDO) were purchased from Kelong Reagent Co. (Chengdu, China). MDEA and BDO were dried under vacuum at 80 °C for 2 h before use. Deionized water was self-made in our laboratory.
 |
| Scheme 1 The chemical structures of polydimethylsiloxane. | |
Instrumentation
Fourier-transformed infrared (FTIR) spectra were collected using a Nicolet 560 FTIR spectrometer (Nicolet, Waltham, MA). The sizes of SiCWPU dispersions were measured via dynamic light scattering (DLS). The static contact angle of water was measured on the surfaces of films using a DSA30 contact angle system (KRUSS Co.). Dynamic mechanical analysis (DMA) was carried out using a DMA Q-800 dynamic mechanical analyzer (TA Instruments). X-ray photoelectronic spectroscopy (XPS) was performed using an XSAM 800 spectrometer (Kratos, UK). Scanning electronic microscopy (SEM) data from the SiCWPU membranes were measured with a JSM-7500F microscope (model JEOL). The mechanical properties of the SiCWPU films were measured with a material testing machine (5967, Instron, USA).
Synthesis of silicone modified cationic waterborne polyurethane
Silicone modified cationic waterborne polyurethane (SiCWPU) was synthesized based on a reaction between PPG2000, PDMS and IPDI in a 250 mL three-necked glass flask fitted with a reflux condenser, a mechanical stirrer and a digital thermometer. 25.0 g of IPDI, 0.04 g of DBTDL, and PPG2000 and PDMS at different concentrations (based on the total mass) were added into the glass flask; the reaction proceeded under constant stirring and was kept at 80 °C until the isocyanate (NCO) content reached the theoretical value. Then the temperature was cooled to 75 °C and 5.0 g of MDEA and 4.0 g of BDO were slowly introduced to the solution, which was maintained under these conditions for another 2 h. Subsequently, the solution was neutralized using HAc at 35 °C for 0.5 h to obtain the polyurethane prepolymer in the flask. Finally, deionized water was slowly dropped into the solution under vigorous stirring and the solution was maintained under these conditions for an additional 1 h. Finally, the polyurethane prepolymer was rigorously dispersed through being dropped into distilled water under stirring at a speed of 1500 rpm for 1 h to obtain cationic SiWPU dispersions. The solid content in the SiCWPU samples was 30 wt%. SiCWPU1 was synthesized when the type of PDMS added was X-22-176-DX, and SiCWPU2 was synthesized when KF-6001 was added. The reaction scheme for SiCWPU1 is shown in Scheme 2 and the synthetic formulae are tabulated in Table 1.
 |
| Scheme 2 The synthesis of SiCWPU1 prepared in this study. | |
Table 1 Compositions of the SiCWPU samples
Sample |
PPG 2000/g |
IPDI/g |
MDEA/g |
BDO/g |
HAc/g |
KF-6001/% |
X-22-176-DX/% |
CWPU |
28.8 |
25 |
5.0 |
4.0 |
3.0 |
0 |
0 |
SiCWPU1-0.5 |
28.7 |
25 |
5.0 |
4.0 |
3.0 |
0 |
0.5 |
SiCWPU1-1.0 |
28.3 |
25 |
5.0 |
4.0 |
3.0 |
0 |
1.0 |
SiCWPU1-3.0 |
27.0 |
25 |
5.0 |
4.0 |
3.0 |
0 |
3.0 |
SiCWPU1-5.0 |
25.8 |
25 |
5.0 |
4.0 |
3.0 |
0 |
5.0 |
SiCWPU2-0.5 |
28.7 |
25 |
5.0 |
4.0 |
3.0 |
0.5 |
0 |
SiCWPU2-1.0 |
28.3 |
25 |
5.0 |
4.0 |
3.0 |
1.0 |
0 |
SiCWPU2-3.0 |
27.0 |
25 |
5.0 |
4.0 |
3.0 |
3.0 |
0 |
SiCWPU2-5.0 |
25.8 |
25 |
5.0 |
4.0 |
3.0 |
5.0 |
0 |
Preparation of SiCWPU films
SiCWPU films were obtained from waterborne polyurethane dispersions on tetrafluoroethylene plates that were allowed to dry at room temperature for 5 days; then the film was dried in an oven at 50 °C for 24 h. After demolding, the SiCWPU films were kept in a desiccator for vacuum drying preservation.
Fourier-transformed infrared spectroscopy
Infrared spectra of the SiCWPU films were collected via Fourier-transformed infrared (FTIR) spectroscopy using a Nicolet 560 FTIR spectrometer (Nicolet, Waltham, MA) at ambient temperature. Thirty-two scans were averaged for the IR measurements over a range of 4000 cm−1 to 600 cm−1, with a resolution of 4 cm−1.
Particle size measurements
The average particle sizes of the SiCWPU dispersions were analyzed using dynamic light scattering apparatus (LA-960, Horiba, Japan). All samples were diluted to 0.5 wt% before analyzing the particle size.
Water contact angle assay
The static contact angle of water was measured on the surface of the films using a DSA30 contact angle system (KRUSS Co.). A 2 μL water droplet was dropped into contact with the surface and the contact angle was reported immediately. The experimental test results were the average values from at least three measurements.
X-ray photoelectron spectroscopy
X-ray photoelectronic spectroscopy (XPS) was performed using an XSAM 800 spectrometer (Kratos, UK) to analyze the SiCWPU membrane surface element compositions. The exit angle was 90° and the test depth was 10 nm from the surface.
Scanning electron microscopy
Scanning electronic microscopy (SEM) data from the SiCWPU membranes were measured with a JSM-7500F microscope (model: JEOL) operating at an acceleration voltage of 15 kV. The samples were sprayed with gold prior to observation. The specimens were magnified 1000 times to detect surface morphology changes.
Water resistance
3 cm × 3 cm SiCWPU films were taken to measure water absorption. The samples were placed in a vacuum oven at 80 °C for 24 h and then the weights of the films were measured. The dried SiCWPU films were placed in a Petri dish containing deionized water, and the water absorption of the films was measured after 1 h, 2 h, 4 h, 8 h, 12 h and 24 h. The water absorption (G%) of the films was calculated using eqn (1). |
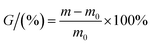 | (1) |
where m0 is the weight of the dry SiCWPU film and m is the weight of the SiCWPU film after water absorption.
Mechanical properties
Tensile testing was performed using with a 5967-model material testing machine at a speed of 50 mm min−1 and at 25 °C. The dumbbell-shaped specimens used were 25 mm in length, 4 mm in width and had a thickness of about 0.5 mm. Analysis of each sample was repeated three times.
Dynamic mechanical analysis
Dynamic mechanical analysis (DMA) was carried out using a DMA Q-800 dynamic mechanical analyzer (TA Instruments). SiCWPU membranes were tested over a temperature range of −80 °C to 100 °C with a heating rate of 3 °C min−1.
Results and discussion
FTIR characterization of the synthesis
FTIR spectra of SiCWPU1 and SiCWPU2 films are shown in Fig. 1. The characteristic peaks from WPU could be observed in Fig. 1, ranging from 4000 cm−1 to 600 cm−1. The absorption peaks at 3327 cm−1 belong to N–H stretching vibrations and the corresponding bending vibration peaks appear at 1531 cm−1. The broad absorption bands at around 1701 cm−1 correspond to C
O stretching vibrations. The peaks in the range of 2970 cm−1 to 2875 cm−1 correspond to the C–H stretching vibrations of the alkyl chains. These absorption peaks show the presence of urethane in the synthesized CWPUs. The absence of peaks at 2270 cm−1, where the characteristic peaks of –NCO groups are located, in the spectra confirmed that all isocyanates reacted during the reaction process. In addition, the asymmetric stretching vibration peaks from Si–O–Si and the C–O–C stretching vibration peaks from WPU soft segments were apparent over the wavenumber range from 1200 cm−1 to 1000 cm−1. The peaks at 806 cm−1 were attributed to Si–C telescopic vibration peaks. It has been shown that polydimethylsiloxane was successfully introduced into the cationic waterborne polyurethanes.23–25
 |
| Fig. 1 FT-IR spectra of CWPU, SiCWPU1-3.0 and SiCWPU2-3.0. | |
Characterization of the water dispersion properties of SiCWPU emulsions
The size distribution of the CWPU particles is decided by the hydrophilic properties, the chemical structure, the crosslinking, the ionic group content and the chain flexibility.26–28 Polysiloxane, as a soft segment, modified cationic aqueous polyurethane, changing the structure of polyurethane and resulting in an increase in the polyurethane particle sizes.29 The size distributions of SiCWPU1 emulsions are shown in Fig. 2a. It was observed that the size dispersion of SiCWPU1 particles increased with an increase in the content of X-22-176-DX. The hydrophilic groups and segments in the SiCWPU1 chains tended to migrate to the surfaces of the particles, which was possible as the hydrophobic ingredient X-22-176-DX tended to be packaged in the insides of particles. An increase in the content of X-22-176-DX led to an increase in hydrophobic substance content and a bigger volume in the insides of particles. Therefore, as the organosiloxane content increased, the particle size of the emulsion increased from 37 nm to 77 nm, as shown in Table 2. The size distributions of the SiCWPU2 particles are shown in Fig. 2b. The reason for the increase in the average particle size was similar to that for SiCWPU1. However, since the X-22-176-DX modified polyurethane formed a comb-like structure, the hydrophobic part occupied a larger volume inside the particle as the silicone content increased. Compared with the particle size of SiWPU1, the same content of SiCWPU2 led to a smaller increase in particle size: the specific values are listed in Table 2. Obviously, the addition of PDMS had an influence on the average particle size of the CWPU dispersions.
 |
| Fig. 2 Particle size distributions of SiCWPU dispersions: (a) SiCWPU1 and (b) SiCWPU2. | |
Table 2 Particle sizes of SiCWPU1 and SiCWPU2
Sample |
Particle size/nm |
Sample |
Particle size/nm |
CWPU |
37.55 |
CWPU |
37.55 |
SiCWPU1-0.5 |
59.12 |
SiCWPU2-0.5 |
59.40 |
SiCWPU1-1.0 |
60.06 |
SiCWPU2-1.0 |
59.68 |
SiCWPU1-3.0 |
66.43 |
SiCWPU2-3.0 |
59.92 |
SiCWPU1-5.0 |
77.63 |
SiCWPU2-5.0 |
65.84 |
X-ray photoelectron spectroscopy
XPS was used for surface element analysis of the SiCWPU films, which could provide information about the reaction between CWPU and PDMS. XPS survey spectra of SiCWPU1 and SiCWPU2 are presented in Fig. 3. The XPS measurement range for the CWPU sample shows three resolved peaks from carbon (C 1s, 285.0 eV), nitrogen (N 1s, 401.0 eV) and oxygen (O 1s, 532.0 eV).30 Comparatively, there were additional peaks from silicon (Si 2s at about 154.0 eV and Si 2p at about 102.0 eV) following the addition of organosiloxanes, which proved that silicone was incorporated into polyurethane.31 Fig. 4 displays a Si 2p XPS survey spectrum from the surface of SiCWPU1-1.0. The peak at 101.6 eV results from the binding energy of Si–O–Si and the peak at 102.1 eV results from the binding energy of Si–O–C. The Si–O–Si and Si–O–C bonds were derived from organosiloxane groups that survived during the formation of the film. The Si element percentage on the surface of the film increased with an increase in the PDMS content. The element concentrations on the surfaces of SiCWPU1 films are listed in Table 3. This shows that upon an increase in the X-22-176-DX content, the Si percentage on the film surface increased from 0% (CWPU) to 17.92% (SiCWPU1-5.0), which was much higher than the theoretical percentages of 0% (CWPU) to 2.52% (SiCWPU1-5.0); the results showed that silicon could migrate to the surfaces of the films. The driving force for migration should derive from the addition of PDMS, making the surface tension of the polymer film lower.32
 |
| Fig. 3 XPS survey spectra: (a) SiCWPU1 and (b) SiCWPU2. | |
 |
| Fig. 4 XPS narrow Si 2p spectrum on the surface of SiCWPU1-1.0. | |
Table 3 The surface chemical compositions of SiCWPU1 and SiCWPU2
Sample |
Concentration/% |
Si concentration/% |
C |
N |
O |
Experimental |
Theoretical |
CWPU |
70.39 |
6.17 |
23.44 |
0 |
0 |
SiCWPU1-0.5 |
63.27 |
2.70 |
23.10 |
10.94 |
0.04 |
SiCWPU1-1.0 |
62.72 |
3.22 |
21.24 |
12.82 |
0.36 |
SiCWPU1-3.0 |
58.79 |
2.22 |
21.72 |
17.28 |
1.80 |
SiCWPU1-5.0 |
59.55 |
1.81 |
21.72 |
17.92 |
2.52 |
SiCWPU2-0.5 |
65.81 |
3.45 |
21.79 |
8.95 |
0.04 |
SiCWPU2-1.0 |
70.49 |
2.08 |
18.43 |
9.00 |
0.36 |
SiCWPU2-3.0 |
59.69 |
3.10 |
21.71 |
15.50 |
1.80 |
SiCWPU2-5.0 |
59.15 |
2.63 |
21.78 |
16.45 |
2.52 |
Water contact angle
Fig. 5 shows the water contact angles of the SiCWPU films. As PDMS was added to the SiCWPU films, the water contact angle increased. SiCWPU1 formed from the modified polyurethane showed an increase in contact angle from 63.0° (CWPU) to 105.3° (SiCWPU1-5.0) and tended to stabilize with an increase in X-22-176-DX content. SiCWPU2 formed from the modified polyurethane showed an increase in contact angle from 63.0° (CWPU) to 100.0° (SiCWPU2-1.0) and tended to stabilize with an increase in KF-6001 content. This indicates that the SiCWPU films formed a siloxane (Si–O–Si) network structure, resulting in a hydrophobic surface.33 Moreover, upon adding the same amount of PDMS, the contact angle of SiCWPU1 was higher than that of SiCWPU2, which may be because the comb structure formed by SiCWPU1 made it easier for Si to migrate to the surfaces of the films. This was consistent with the results obtained via XPS.
 |
| Fig. 5 The water contact angles of SiCWPU films. | |
Scanning electron microscopy assays
The surface morphologies of films with different silica content values, obtained via SEM, are presented in Fig. 6. The test results show that the two different organosiloxane modified cationic waterborne polyurethanes had a certain influence on the surfaces of the polyurethane films, but X-22-176-DX had a greater influence. With the addition of siloxane, white particles appeared on the surfaces of the films, because the introduction of siloxane increased the cross-linking density.29 As the PDMS content increased, the molecules tended to agglomerate to form particles. Fig. 6a, d, b, e and c, f show the surface topography analysis of SiCWPU films formed by adding the same amounts of X-22-167-DX and KF-6001 modified cationic waterborne polyurethane, respectively. The results show that adding the same amount of X-22-167-DX was more likely to create larger white particles on the surface of the film than adding KF-6001, and when the X-22-167-DX content was increased by a certain amount, holes were formed on the surface of the film. This may be due to the fact that the comb-like structure of SiCWPU1 results in a higher silicon content on the surface of the film.
 |
| Fig. 6 SEM images of the fracture surfaces of SiCWPU films: (a) SiWPU1-1.0, (b) SiCWPU1-3.0, (c) SiCWPU1-5.0, (d) SiCWPU2-1.0, (e) SiCWPU2-3.0, and (f) SiCWPU2-5.0. | |
Water resistance of SiCWPU films
The water absorption of polyurethane film is related to the hydrophobicity and phase separation of the material.34,35 Fig. 7 shows the water absorption of the SiCWPU films. As the PDMS content increases, the water absorption of the polyurethane film increases. After the immersion of SiCWPU films in deionized water for 24 h, the water absorption of the SiCWPU2 films increased from 10.51% (CWPU) to 14.06% (SiCWPU2-5.0), and the water absorption of SiCWPU1 films increased from 10.51% to 13.82% (SiCWPU1-5.0). This was due to the phase separation of the SiCWPU films, caused by the addition of PDMS. The results showed that the water resistance of the SiCWPU2 films was more affected by phase separation.
 |
| Fig. 7 The water absorption of SiCWPU films: (a) SiCWPU1 and (b) SiCWPU2. | |
Mechanical properties
Fig. 8 shows stress–strain curves from the SiCWPU films. The results show that the elongation at break of the SiCWPU films increases with an increase in the PDMS content, and the tensile strength decreases. This is due to the fact that PDMS is very soft and has poor tensile strength.36 Since SiCWPU1 has a comb-like structure, the silicone segment was more easily stretched in the molecules; the elongation at break of the SiCWPU2 films increased from 617% to 769%, while the elongation at break of the SiCWPU1 films increased to 959%. The stress–strain values are listed in Table 4. According to the data in the table, the tensile strengths of the SiCWPU1 films were higher than the SiCWPU2 films when the same amounts of PDMS were added. This may be because the comb-like structure of SiCWPU1 increases the degree of phase separation in SiCWPU1 and increases the tensile strength. The experimental results show that the mechanical properties of SiCWPU1 are better than those of SiCWPU2.
 |
| Fig. 8 Stress–strain curves from SiCWPU films: (a) SiCWPU1 and (b) SiCWPU2. | |
Table 4 Stress–strain data from SiCWPU1 and SiCWPU2 films
Sample |
Tensile strength/MPa |
Elongation at break/% |
Young's modulus/MPa |
CWPU |
40.15 ± 3.15 |
617 ± 56 |
12.36 ± 2.41 |
SiCWPU1-0.5 |
38.06 ± 4.56 |
791 ± 95 |
8.23 ± 0.98 |
SiCWPU1-1.0 |
37.12 ± 2.32 |
799 ± 67 |
6.75 ± 1.25 |
SiCWPU1-3.0 |
32.94 ± 2.56 |
932 ± 67 |
6.60 ± 1.25 |
SiCWPU1-5.0 |
30.89 ± 3.67 |
959 ± 83 |
4.66 ± 0.65 |
SiCWPU2-0.5 |
34.05 ± 4.35 |
677 ± 45 |
8.36 ± 1.32 |
SiCWPU2-1.0 |
31.09 ± 2.78 |
744 ± 89 |
6.50 ± 2.13 |
SiCWPU2-3.0 |
30.79 ± 5.61 |
752 ± 78 |
6.46 ± 1.02 |
SiCWPU2-5.0 |
30.15 ± 1.24 |
769 ± 67 |
5.77 ± 1.54 |
Dynamic mechanical analysis
Fig. 9 shows the storage modulus values of SiCWPU films as a function of temperature. It is clear that the storage modulus values of the samples at room temperature decrease slowly with an increase in the PDMS content. This was because the addition of PDMS provided flexible Si–O–Si segments in CWPU; a certain degree of microphase separation occurred in the SiCWPU films and the high elastic modulus of the SiCWPU films decreased.37
 |
| Fig. 9 The storage modulus values of SiCWPU films: (a) SiCWPU1 and (b) SiCWPU2. | |
Fig. 10 shows the tan
δ-temperature curves for the SiCWPU films. The peak value of the tan
δ-temperature curve corresponds to the glass transition temperature of the film. It can be seen from the figure that the tan
δ curves of the films have two peaks, corresponding to the soft transition glass transition temperature (Tgs) of the CWPU film at −40.2 °C, and the glass transition temperature of the hard segment (Tgh) of the CWPU at 48.0 °C. The specific values of Tg are listed in Table 5. According to the data in the table, as the X-22-176-DX content increases, the glass transition temperature of the soft segment did not change substantially, but the glass transition temperature of the hard segment increased from 48.0 °C to 57.7 °C, indicating that the microphase separation of the film increased upon an increase in the silicon content; the degree of phase separation increased.
 |
| Fig. 10 Tan δ data from SiCWPU films: (a) SiCWPU1 and (b) SiCWPU2. | |
Table 5 DMA data from SiCWPU1 and SiCWPU2 films
Sample |
Tgs/°C |
Tgh/°C |
Sample |
Tgs/°C |
Tgh/°C |
CWPU |
−42.0 |
48.0 |
CWPU |
−42.0 |
48.0 |
SiCWPU1-0.5 |
−39.7 |
52.0 |
SiCWPU2-0.5 |
−43.1 |
48.0 |
SiCWPU1-1.0 |
−41.4 |
52.4 |
SiCWPU2-1.0 |
−42.0 |
50.3 |
SiCWPU1-3.0 |
−41.9 |
54.8 |
SiCWPU2-3.0 |
−42.0 |
50.9 |
SiCWPU1-5.0 |
−41.4 |
57.7 |
SiCWPU2-5.0 |
−43.0 |
55.4 |
Conclusions
A series of SiCWPU films were synthesized using structurally different dihydroxy dimethylpolysiloxane modified cationic waterborne polyurethane examples. The reactions were confirmed through FTIR analysis. KF-6001 and X-22-176-DX were incorporated into CWPU chains with content values increasing from 0.5 to 5.0%, and a series of silane modified CWPU dispersions were prepared using PDMS as the soft segment. The addition of both silanes had a major impact on the properties of the polymers. According to dynamic light scattering characterization, the final particle sizes of the dispersions increased with an increase in PDMS content. However, when the same amount of polysiloxane was added, the resulting SiCWPU1 dispersion was larger than the particle size of the corresponding SiCWPU2 sample. XPS data showed that the strong tendency for the migration of Si elements to the surfaces of the polymer films resulted from the lower surface free energy of silicon. The result was that CWPU coating films exhibited increased surface hydrophobicity. Compared with cationic waterborne polyurethane that was not modified with siloxane, the contact angle following the addition of 5.0% PDMS was greatly increased. Meanwhile, the contact angle of SiCWPU1 with a siloxane content of 5.0% was greater than SiCWPU2 with a siloxane content of 5.0%. The stress–strain data indicated that the mechanical properties of SiCWPU1 were better than those of SiCWPU2 when the same amount of PDMS was added. The results from DMA indicated that the glass transition temperature difference between the soft and hard segments increased following the heating of the siloxane, which proved that the addition of polysiloxane increased the phase separation in the polymer film. The results showed that the different structures of silicone modified cationic waterborne polyurethanes resulted in differences in performance. Comb-like silicone modified polyurethane performed better than linear silicone modified polyurethane. This study provided an effective route toward CWPU coating materials with advanced application performance.
Conflicts of interest
There are no conflicts to declare.
Acknowledgements
This work was funded by the National Natural Science Foundation of China (No. 51773129), the Support Plan of the Science and Technology Department of Sichuan Province, China (2017GZ0129, 2018SZ0174, 2019YFG0257), the International Science and Technology Cooperation Program of Chengdu (2017-GH02-00068-HZ) and the Postdoctoral Research Foundation of Sichuan University (2018SCU12049) and was supported by the Graduate Student's Research and Innovation Fund of Sichuan University (2018YJSY084).
References
- W. Sun, Y. Zhou, Y. Ju, L. Yang, T. Xu and Z. Chen, Macromol. Chem. Phys., 2014, 215, 96–102 CrossRef CAS.
- Y. Fang, J. Li, X. Du, Z. Du, X. Cheng and H. Wang, Polymer, 2018, 158, 166–175 CrossRef CAS.
- V. J. Tramontano, M. E. Thomas and R. D. Coughlin, in Technology for Waterborne Coatings, ed. J. E.Glass, American Chemical Society, Washington, DC, 1997, pp. 164–182 Search PubMed.
- W. He, Y. Zhang, F. Luo, J. Li, K. Wang, H. Tan and Q. Fu, RSC Adv., 2015, 5, 89763–89770 RSC.
- L. F. Wang, Q. Ji, T. E. Glass, T. C. Ward, J. E. McGrath, M. Muggli, G. Burns and U. Sorathia, Polymer, 2000, 41, 5083–5093 CrossRef CAS.
- S. Zhang, Z. Chen, M. Guo, H. Bai and X. Liu, Colloids Surf., A, 2015, 468, 1–9 CrossRef CAS.
- S. Sundar, N. Vijayalakshmi, S. Gupta, R. Rajaram and G. Radhakrishnan, Prog. Org. Coat., 2006, 56, 178–184 CrossRef CAS.
- Y. Xia, Z. Zhang, M. R. Kessler, B. Brehm-Stecher and R. C. Larock, ChemSusChem, 2012, 5, 2221–2227 CrossRef CAS PubMed.
- N. Sukhawipat, N. Saetung, J.-F. Pilard, S. Bistac and A. Saetung, J. Appl. Polym. Sci., 2018, 135, 45715 CrossRef.
- A. A. El-Sayed, F. A. Kantouch and A. Kantouch, J. Appl. Polym. Sci., 2011, 121, 777–783 CrossRef CAS.
- X. Lai, Y. Song and M. Liu, J. Polym. Res., 2013, 20, 1 CAS.
- J. Li, X. Zhang, J. Gooch, W. Sun, H. Wang and K. Wang, Polym. Bull., 2015, 72, 881–895 CrossRef CAS.
- Y. Song, Y. Gao, X. Wan, F. Luo, J. Li, H. Tan and Q. Fu, RSC Adv., 2016, 6, 17336–17344 RSC.
- F. Zhang, R. Wang, Y. He, W. Lin, Y. Li, Y. Shao, J. Li, M. Ding, F. Luo, H. Tan and Q. Fu, J. Mater. Chem. B, 2018, 6, 4326–4337 RSC.
- R. Wang, F. Zhang, W. Lin, W. Liu, J. Li, F. Luo, Y. Wang and H. Tan, Macromol. Biosci., 2018, 18, e1800054 CrossRef PubMed.
- M.-E. Vlachopoulou, P. S. Petrou, S. E. Kakabakos, A. Tserepi, K. Beltsios and E. Gogolides, Microelectron. Eng., 2009, 86, 1321–1324 CrossRef CAS.
- X. Z. Kong, D. Zou and X. Zhu, J. Polym. Res., 2014, 21, 8537 Search PubMed.
- H. Wang, Y. Shen, G. Fei, X. Li and Y. Liang, J. Colloid Interface Sci., 2008, 324, 36–41 CrossRef CAS PubMed.
- F. Yu, L. Cao, Z. Meng, N. Lin and X. Y. Liu, Polym. Chem., 2016, 7, 3913–3922 RSC.
- J. Huang, S. Wang, W. Sun, Z. Zhang, C. Cheng, Y. Ju, P. Yang, L. Ding and Z.-R. Chen, Macromol. Chem. Phys., 2015, 216, 2279–2286 CrossRef CAS.
- C. Xu, L. OuYang, H. Liu, Q. Chen, Z. Cai, J. Xing and Y. Li, Text. Res. J., 2015, 85, 2040–2050 CrossRef CAS.
- X. Li, G. Fei and H. Wang, J. Appl. Polym. Sci., 2006, 100, 40–46 CrossRef CAS.
- S. Du, Y. Wang, C. Zhang, X. Deng, X. Luo, Y. Fu and Y. Liu, J. Mater. Sci., 2018, 53, 215–229 CrossRef CAS.
- M. Li, F. Liu, Y. Li and X. Qiang, RSC Adv., 2017, 7, 13312–13324 RSC.
- J. Xiao, Z. Qiu, W. Yang, J. Qiu, T. Yang, Y. Xu, Y. Zeng, F. Wang and S. Li, Prog. Org. Coat., 2018, 116, 1–6 CrossRef CAS.
- V. García-Pacios, J. A. Jofre-Reche, V. Costa, M. Colera and J. M. Martín-Martínez, Prog. Org. Coat., 2013, 76, 1484–1493 CrossRef.
- S. K. Lee and B. K. Kim, J. Colloid Interface Sci., 2009, 336, 208–214 CrossRef CAS PubMed.
- S. Wang, Z. Du, X. Cheng, Y. Liu and H. Wang, J. Appl. Polym. Sci., 2018, 135, 46093 CrossRef.
- C. Fu, X. Hu, Z. Yang, L. Shen and Z. Zheng, Prog. Org. Coat., 2015, 84, 18–27 CrossRef CAS.
- J. Zhao, T. Zhou, J. Zhang, H. Chen, C. Yuan, W. Zhang and A. Zhang, Ind. Eng. Chem. Res., 2014, 53, 19257–19264 CrossRef CAS.
- S. Wu, J. Wang, J. Shao, L. Wei, K. Yang and H. Ren, ACS Appl. Mater. Interfaces, 2017, 9, 28887–28901 CrossRef CAS PubMed.
- Q. Li, L. Guo, T. Qiu, W. Xiao, D. Du and X. Li, Appl. Surf. Sci., 2016, 377, 66–74 CrossRef CAS.
- M. Yeh, C. Yao, C. Hsieh, H. Yang and C.-P. Wu, Eur. Polym. J., 2008, 44, 2777–2783 CrossRef.
- S. Zhang, Z. Chen, M. Guo, J. Zhao and X. Liu, RSC Adv., 2014, 4, 30938 RSC.
- X. Z. Kong, D. Zou and X. Zhu, J. Polym. Res., 2014, 21, 8537 CrossRef.
- F. Yu, X. Xu, N. Lin and X. Y. Liu, RSC Adv., 2015, 5, 72544–72552 RSC.
- Z. Wu, H. Wang, X. Tian, P. Cui, X. Ding and X. Ye, Phys. Chem. Chem. Phys., 2014, 16, 6787–6794 RSC.
|
This journal is © The Royal Society of Chemistry 2019 |
Click here to see how this site uses Cookies. View our privacy policy here.