DOI:
10.1039/C8QI00939B
(Review Article)
Inorg. Chem. Front., 2019,
6, 14-31
Ultrafast synthesis of zeolites: breakthrough, progress and perspective
Received
4th September 2018
, Accepted 9th October 2018
First published on 10th October 2018
Abstract
Zeolites maintain the momentum of their existing applications and continue to find new applications in the fields of catalysis and separation. Such application prospects call for an efficient synthesis of high-quality zeolites. Nevertheless, the conventional hydrothermal synthesis, which is typically carried out under batch operation, usually takes several days or even several weeks to yield a zeolite with the desired structure and properties. Improving the synthesis efficiency is of high significance to boost the applications of zeolites in diverse fields. Recently, our group has established an ultrafast route for synthesizing a series of industrially important zeolites. The synthesis periods for these zeolites were shortened to tens of or several minutes, which are in stark contrast to the long synthesis periods that are required in the conventional approach. The continuous flow synthesis of zeolites was also realized thanks to the ultrashort synthesis period. In this review, we present our recent progress on the ultrafast synthesis of zeolites, with a focus on discussing how the remarkably enhanced crystallization rate could be achieved. We also offer our perspective on the potential consequences that the ultrafast synthesis could initiate to the mechanism study as well as the mass production of zeolites.
 Zhendong Liu | Zhendong Liu received his PhD degree in chemical engineering (supervised by Professor Tatsuya Okubo) from The University of Tokyo in September 2015 and carried out postdoctoral research in the same institute until July 2016. He then moved to University of Minnesota at Twin Cities for another postdoctoral research with Professors Michael Tsapatsis and Andreas Stein. Since October 2017, he has been a project assistant professor at The University of Tokyo. His current research focuses on the efficient synthesis of zeolitic materials and nanostructures towards applications in energy and environment. |
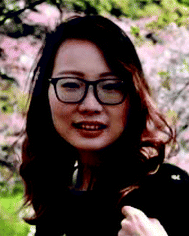 Jie Zhu | Jie Zhu received her bachelor's degree from East China University of Science and Technology in 2015 and master's degree from The University of Tokyo in 2017. She is currently a PhD candidate supervised by Professor Tatsuya Okubo in The University of Tokyo. Her current research is on the rational synthesis and catalytic study of noble/transition metal containing zeolites. |
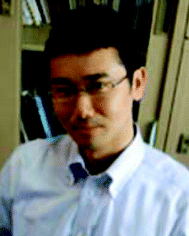 Toru Wakihara | Toru Wakihara is an associate professor at the Department of Chemical System Engineering of The University of Tokyo. He received his PhD degree from UTokyo in 2004, and started his academic career at Yokohama National University where he was promoted as assistant professor and associate professor in 2007 and 2012, respectively. He moved back to UTokyo and started to hold his current position in 2013. His research interests include powder technology, synthesis and application of nanosized zeolites, and synthesis of zeolites under extreme conditions. |
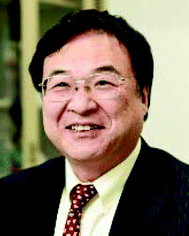 Tatsuya Okubo | Tatsuya Okubo is a professor at the Department of Chemical System Engineering, The University of Tokyo. He received his PhD degree from UTokyo and started his academic career at Kyushu University as a research associate in 1988. He moved to UTokyo in 1991, where he was promoted as a lecturer, an associate professor and a full professor in 1994, 1997 and 2006, respectively. He spent one year at California Institute of Technology (USA) as a visiting associate in 1993–1994. His research interests include the synthesis and application of zeolites. |
Introduction
The past few decades have witnessed tremendous progress in the synthesis and application of zeolites, which have greatly benefited modern chemical and petrochemical industries as catalysts, adsorbents and ion-exchangers.1–3 This prospect is mainly due to the fact that zeolites, featuring a highly ordered three-dimensional framework composed of nanometer-sized channels and cages, bring about excellent (hydrothermal) stability, high adsorption capacity and tunable active sites. Recently, driven by the rapid development of nanotechnology and biotechnology, applications of zeolites have been extended to new fields as sensors, optical devices and hosts for nano- and bio-related materials.4–6 These established and emerging applications call for new concepts in the design, engineering and production of zeolites.
The terminology of zeolites in this review preferentially refers to aluminosilicates (zeolites), aluminophosphates (AlPOs) and other zeotype metallosilicates that are built upon tetrahedral chemistry. The basic structural unit of these materials consists of a metal atom (typically Si, Al and P) tetrahedrally coordinated to four oxygen atoms. Other substituting elements (Ti, Ge, B, Sn and Zr) can also be incorporated into the framework, offering opportunities to broaden the applications as well as to discover new structures.7–9 To date, 239 structures have been authorized by the Structure Commission of the International Zeolite Association.10
Systematic studies into the synthesis of zeolites date back to the 1940s, when Richard Barrer began to investigate the synthesis with water as the solvent, a process today generally called hydrothermal synthesis.11,12 Since then, it has dominated the production of synthetic zeolites. Initially proposed to mimic the geological formation conditions of natural zeolites, the hydrothermal synthesis is effective in converting the amorphous reactants to crystalline phases in an aqueous environment. Nevertheless, this process takes long synthesis periods (usually several hours to several days, and in some cases even several weeks) to obtain the desired products, which renders the synthesis of zeolites less efficient in terms of time, energy and cost.13,14 Considering the ever emerging applications and increasing consumption of zeolites, the development of a fast synthesis route is highly desirable.
The complexity behind the hydrothermal synthesis of zeolites, however, makes ultrafast synthesis a challenging task to accomplish. For one thing, the formation of zeolites, in particular the nucleation step (including the induction period), is generally viewed as a kinetically slow process, which determines that a long synthesis time is required to obtain a crystalline product.15 Meanwhile, a crystalline microporous material is not the thermodynamically most stable phase but only a metastable one, and the formation of different types of zeolites is at almost the same level in view of free energy.16–18 This thermodynamic aspect further complicates the realization of an ultrafast synthesis, as any single effort toward accelerating the crystallization rate may only result in the formation of undesired frameworks or even dense phases.19
Herein, we review the breakthrough and the recent progress on the ultrafast synthesis of zeolites demonstrated by our group. To begin with, we briefly discuss the features of the hydrothermal synthesis and the crystallization mechanism of zeolites, followed by a short introduction of several methods that have been developed to accelerate the crystallization rate. Our purpose is not to a give a comprehensive review of the hydrothermal synthesis as well as the crystallization mechanism but to provide some important features of the crystallization of zeolites to better explain the challenges for a fast synthesis. The history of the hydrothermal synthesis and the mechanism of zeolite crystallization have been thoroughly examined in the previous reviews.20–28 Despite the complicated nature of crystallization, efforts have never ceased to shorten the synthesis period of zeolites. We then present the breakthrough as well as an overview of the ultrafast synthesis of zeolites in a tubular reactor, brief the factors that contribute to the enhancement of crystallization rates and rationalize how these factors work synergistically to lead to the ultrafast synthesis on the order of minutes. The ultrafast synthesis lays a solid foundation to realize a switch from the batch-wise synthesis conducted in conventional autoclaves to the continuous synthesis in flow reactors. Considerations on the establishment of a continuous flow synthesis of zeolites as well as several successful demonstrations are therefore discussed.
Hydrothermal synthesis of zeolites and the crystallization mechanism
A typical hydrothermal synthesis can be schematically illustrated as shown in Fig. 1a. The amorphous reactants containing a silica source, an aluminium source, an inorganic cation, an organic structure-directing agent (OSDA) and water are mixed to form an aqueous precursor. This precursor undergoes an aging process conducted either at room temperature or an elevated temperature to ensure adequate mixing and tuning of the precursor, and then this aged precursor is fed into a sealed autoclave and heated to the reaction temperature. After a certain synthesis period, the autoclave is cooled down and the crystalline product is recovered by separation, washing and drying.
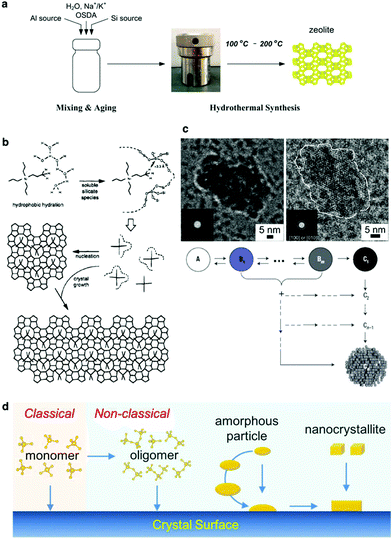 |
| Fig. 1 Features of the hydrothermal synthesis and the crystallization mechanism. (a) A scheme of the hydrothermal synthesis of zeolites. (b) Proposed mechanism of structure direction in the TPA-mediated synthesis of silicalite-1 (reprinted with permission from ref. 47. Copyright 1995 American Chemical Society). (c) TEM images of samples revealing the amorphous-to-crystal transformation (adapted with permission from ref. 35. Copyright 2008 American Chemical Society), and the proposed model for aggregative growth (adapted with permission from ref. 49. Copyright 2006 Macmillan Publishers Ltd: Nature Materials). (d) Possible crystallization pathways that may occur in the addition of a solute to a crystal surface. (Adapted with permission from ref. 50. Copyright 2016 American Chemical Society.) | |
Fig. 1a depicts that the hydrothermal synthesis involves multiple steps, which are performed at different temperatures. Mixing of the raw materials and the subsequent aging step are carried out at low temperatures (typically below 100 °C). Adequate aging is necessary because a fresh mixture of the starting ingredients may not be homogeneously mixed. More importantly, the events taking place during the aging process are beyond physical mixing. Substantial chemical reactions, for example hydrolysis and condensation of silicates, formation of the aluminosilicate hydrogel and reorganization of the hydrogels, have already started at this stage.29,30 Characterization techniques like nuclear magnetic resonance spectroscopy (NMR),31,32 high resolution transmission electron microscopy (high resolution TEM),33–35 X-ray/neutron scattering with pair distribution function analysis (PDF analysis),36,37 and Raman spectroscopy38 have been intensively employed to study the aging. The results have demonstrated that the species formed in the aging step can essentially influence the subsequent crystallization proceeding at high temperatures and consequently alter the properties of the products obtained. For instance, careful investigations showed that secondary building units like four- and six-membered rings were formed in the aging step, which played an important role in phase determination.39,40 The events occurring in the high temperature synthesis include: (1) further organization of the building units formed during the aging, (2) nucleation, and (3) crystal growth until the consumption of nutrient species. A suitable temperature is chosen for a certain hydrothermal synthesis because the rates of dissociation and reorganization of the (alumino)silicate species can be balanced and a delicate equilibrium achieved under such a temperature so as to prompt the formation of the nuclei and sustain the crystal growth for crystallizing the targeted phase.
Understanding the crystallization mechanism, especially at the molecular level, is crucial to improve the synthesis efficiency as well as to tune the property of the product. However, such a thorough understanding is still elusive. The difficulty mainly lies in the nucleation stage. Based on experimental observations, the nucleation of zeolites seems not to be well described by the classical nucleation theory, as among the species involved in the complex assembly of the precursors it is difficult to define a critical size upon which the energetic barrier is overcome.41 It is likely that nucleation may follow a complex mechanism, in which the assembly of the precursors provides a cluster of primary particles or a sol–gel like bulk aggregate which lowers the energetic barrier and initiates the heterogeneous nucleation.42–46 It is reasonable to believe that the amorphous-to-crystalline transformation, either via the cluster of primary particles or via the sol–gel like bulk aggregate, governs the phases to be formed, and consequently the overall crystallization rates. A clear picture of this amorphous-to-crystalline transformation at the molecular level is yet to come as the assembly of the precursors is too complex and the heterogeneous nucleation too fast. Based on the widely studied pure silica MFI zeolite (silicalite-1), Burkett and Davis proposed a mechanism of structure direction in zeolite synthesis, which considers that the formation of the inorganic–organic composite structure is driven by the overlap of hydrophobic hydration spheres composed of inorganic and organic components, and consequently ordered water is released to establish a favorable intermolecular van der Waals interaction (Fig. 1b).47,48 The Burkett–Davis model provides a plausible explanation to the driving force dictating the structure direction of the OSDA, which plays an essential role in the crystallization. Davis et al. performed a series of room temperature experiments to study the nanoparticle and crystal evolution in aqueous suspensions prepared from tetraethylorthosilicate and tetrapropylammonium hydroxide, and the characterization results obtained collectively from small-angle X-ray scattering (SAXS), high resolution TEM, in situ atomic force microscopy (AFM) and cryogenic TEM suggested an oriented-aggregation mechanism where the precursor nanoparticles evolve into zeolite crystals through several intermediate states that can contribute to aggregative growth (Fig. 1c).49
It is reasonable to speculate that the crystallization of zeolites involves different pathways depending on the growth units that are available for crystallization. Fig. 1d provides a comparison between classical and non-classical pathways. While the classical pathway via the addition of monomers could take place under certain circumstances, the non-classical pathways are considered to be dominant because oligomeric structures and amorphous particles of aluminosilicates can be easily formed during the crystallization of zeolites.50 Although questions remain regarding the exact nature of the growth units, experimental evidence suggests that both inorganic and organic materials could grow non-classically. Recently, Rimer et al. have demonstrated that the non-classical pathways offer the possibility to tailor the morphology of the zeolites through crystal modifiers.51–53
From the energetics point of view, zeolites are only metastable compared with their counterparts with denser frameworks. Calorimetry studies by Navrotsky and co-workers showed that the enthalpies of formation for pure silica zeolites follow a linear relationship with respect to the framework molar volume.16–18,54 Nevertheless, the enthalpy difference for different framework types is very small. The similarity in energetics further complicates the control of crystallization, as polymorphs or a mixture of different phases can easily be generated in the synthesis. Such phase transformation can be described by the Ostwald step rule, which states that the first generated phase could convert to a more thermodynamically stable phase and then the next until the most stable phase is formed.55–57 Because of the similarity in energetics and also the existence of other kinetic barriers, however, it is not easy in reality to screen the phases by the difference in energetics. Many other factors including the silica to aluminium ratio, alkalinity, extra-framework cations and type of the OSDA can exert influences on the phase determination as well as the crystallization rate, indicating that the crystallization of zeolites is kinetically governed.58–61
It is therefore understandable that the kinetic aspects and thermodynamic aspects of the crystallization are largely intertwined and cannot be considered independently. For example, changing the inorganic cations can lead to the formation of an undesired phase with a different crystallization rate.62,63 The role of the OSDA is more complex, as it dominates the interaction among various species involved in the amorphous-to-crystalline transformation, and thus influences the stabilization of the intermediates formed and thereof the crystallization rate.64,65
Previous efforts in speeding up the crystallization of zeolites
Remarkable efforts have been made to speed up the crystallization of zeolites. However, a basis for such claims is lacking. In most cases, the synthesis parameters are so optimized as to achieve the shortest crystallization time under a given range of synthesis conditions. In general, a method is effective only when one or a combination of the following consequences can take place: (1) shortening the induction period, (2) moving a non-ideal synthesis towards its optimum, or (3) altering the balance between nucleation and growth.14 Several methods leading to an accelerated crystallization of zeolites are introduced below.
Microwave-assisted synthesis of zeolites (Fig. 2a) has been extensively studied, which can change the crystallization rate in favorable ways.66,67 The features of microwave include fast heating, which helps to avoid the thermal lag, and selective heating, which may generate a heterogeneous environment containing components with different dielectric properties. Non-thermal effects of microwave irradiation have been claimed, although it was found that the energy of a microwave photon is insufficient to break chemical bonds and that the electric field strength is not enough to shift the chemical equilibrium nor to induce organization.68 Therefore, the enhancement of the crystallization rate by microwave heating may be attributed to either the thermal effect or the non-thermal effect, or a combination of both.69 For example, Cundy et al. performed the microwave-assisted synthesis of ZSM-5 in seeded systems with and without an OSDA.70 They found that microwave heating greatly enhanced the crystallization rate of ZSM-5, in particular, under the conditions in the presence of nanocrystalline seeds. They posited that the hydroxylated surface of the seed crystals and the associated water molecules in the boundary layers could be easily polarized under microwave heating, which resulted in a rapid activation of the seed crystals and consequently a much accelerated crystallization rate.
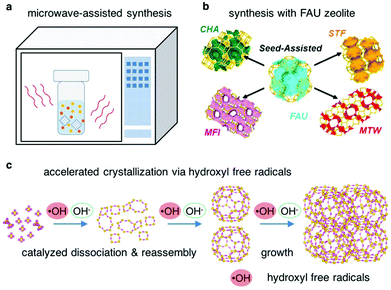 |
| Fig. 2 Methods aimed at speeding up the synthesis. (a) Microwave-assisted synthesis. (b) Synthesis using FAU zeolite as a starting material. (Adapted with permission from ref. 72. Copyright 2015 American Chemical Society.) (c) Accelerated crystallization via hydroxyl free radicals. | |
A number of zeolites (such as CHA, *BEA and MFI) have been successfully synthesized through a route which employs FAU type zeolite as a starting material (Fig. 2b).71–74 The crystallization rates for such syntheses were found to be faster compared with those for syntheses with normal starting materials. For example, Honda et al. successfully synthesized *BEA zeolite in only 2 h at 125 °C with FAU zeolite as the starting material.75 While it was supposed that the generation of locally ordered aluminosilicate species through the decomposition/dissolution of the starting FAU zeolite could facilitate the assembly and evolution of another zeolite, further efforts are needed to clarify the role of the FAU zeolite in accelerating the crystallization rate of the targeted zeolite.
Recently, Feng et al. have reported the enhancement of zeolite crystallization via hydroxyl free radicals (Fig. 2c).76 Usually the zeolites crystalize under basic conditions which favor breaking and reforming the oxide bridges between the aluminum and silicon atoms, while they discovered that hydroxyl free radicals, generated either by a physical method (UV irradiation) or a chemical method (Fenton reagent), could accelerate the crystallization rates of zeolites by about a factor of 2. Experimental results coupled with theoretical calculations indicate that the hydroxyl free radicals shorten the nucleation time by accelerating the rates of the dissolution and the re-assembly of the Si–O–Si bonds. This method was found to be applicable to other porous materials such as mesoporous silica.77
A couple of synthesis strategies have been developed in recent years, which enriched the toolbox for an economical and green synthesis of zeolites although the purposes were not to make the crystallization faster. For example, various methods have been developed to deal with the high cost of the OSDAs. Xie et al. reported the synthesis of zeolite beta without the use of OSDA but with the addition of beta seeds,78 and the OSDA-free route was thereafter broadened for the synthesis of a series of zeolites, such as MTW,79 MAZ,80 MWW,81 VET-type zincosilicate zeolite,82etc., which greatly reduces the high cost associated with the employment of OSDAs as well as their removal through thermal calcination.83–85 In the cases where the use of an OSDA is indispensable, attempts have been made to reduce the consumption of the OSDA or utilize an OSDA with a lower cost to replace the expensive one. For instance, the typical synthesis of SSZ-13 requires the use of the trimethyladamantammonium (TMAda+) cation, which is an expensive OSDA, while N. Martín et al. developed a recipe to synthesize SSZ-13 with the inexpensive tetraethylammonium (TEA+) cation as an OSDA.86 A similar strategy was also applied on the synthesis of MSE zeolite with a high yield.87 Meanwhile, the synthesis of zeolites with tailored properties, such as hierarchical zeolites,88–90 two-dimensional zeolites91–93 and chiral zeolites,94,95 is booming for diverse potential applications. In addition, continual endeavors have been made to control the distribution of Al atoms (or other heteroatoms such as Ti) in the zeolite framework because the siting of such atoms is an important factor for the catalytic performance of the zeolite.96–100
Ultrafast synthesis in the tubular reactor
Hydrothermal synthesis of zeolites is typically performed in the autoclave, which provides a relatively facile and safe platform to stand against the long-time synthesis under harsh conditions. The features of the autoclave sometimes exert important influence on the synthesis of zeolites. In view of the realization of ultrafast synthesis, however, the conventional autoclave is less incapable because it lacks the proper time resolution to accommodate an ultrafast synthesis, that is, long time is needed for the autoclave for mixing and heating/cooling, making it even impossible to accurately investigate the changes taking place in small time intervals. To increase the time resolution, a “mini autoclave” made from a standard ¼′′ stainless steel tube (denoted as “tubular reactor”) was designed and introduced to the synthesis of zeolites.101–109 The length of the tubular reactor is ca. 13.5 cm, and its two ends are sealed with standard Swagelok® caps. Thanks to its small size and high surface-to-volume ratio, this “mini autoclave” can enable faster heating and cooling, and thus provide a higher time resolution compared with its conventional counterpart. Fig. 3 shows a comparison of the heating curves obtained in the tubular reactor and that in a typical autoclave (Teflon-lined autoclave, #4749, Parr Instrument Company). It takes at least one hour for the autoclave to complete the temperature raise. In stark contrast, the tubular reactor can give a much faster heating rate. In particular, only one minute is required to complete the temperature raise if the tubular reactor is heated in a preheated oil bath, which enables the tubular reactor to be capable of probing any change taking place within very short time intervals.
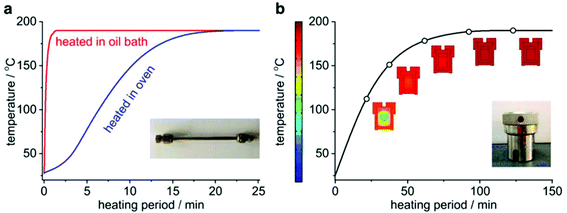 |
| Fig. 3 Comparison of temperature profiles during heating-up for the tubular reactor and the conventional autoclave. (a) Temperature profiles obtained in the tubular reactor heated in a preheated oil bath and a preset air-circulating oven. (b) Simulated temperature profile in the conventional autoclave heated in the preset air-circulating oven. (Reprinted from ref. 101. Copyright 2014 Royal Society of Chemistry.) | |
This feature of the tubular reactor, together with the rational design of synthesis precursors as well as the employment of seeding, allowed us to develop an ultrafast synthesis on the order of minutes. Fig. 4 gives an overview of the typical zeolites that have been synthesized via the ultrafast synthesis route. Typically, the synthesis periods were shortened to tens of and even several minutes.101 As a comparison, several hours or several days are the common synthesis periods reported in the previous studies. The results in Fig. 4 cover various frameworks and compositions, and the range is still expanding. Several representative cases of the ultrafast synthesis are featured below.
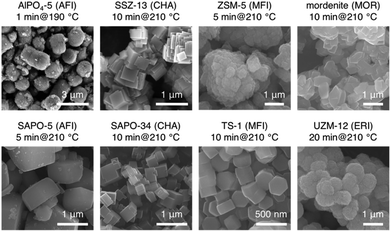 |
| Fig. 4 Representative zeolites and zeotype materials that have been synthesized via the ultrafast synthesis route. (Sources of the SEM images are indicated as follows: AlPO4-5 – reprinted from ref. 101. Copyright 2014 Royal Society of Chemistry. SSZ-13 – reprinted with permission from ref. 102. Copyright 2015 Wiley-VCH. Mordenite – reprinted from ref. 106. Copyright 2017 Royal Society of Chemistry. SAPO-5 and SAPO-34 – reprinted with permission from ref. 105. Copyright 2016 American Chemical Society. UZM-12 – reprinted from ref. 107. Copyright 2017 Royal Society of Chemistry.) | |
AlPO4-5
The first success of the ultrafast synthesis was demonstrated on AlPO4-5, an aluminophosphate with an AFI structure. Different approaches including microwave-assisted hydrothermal synthesis, dry gel conversion and microemulsion-based synthesis have been attempted to synthesize AlPO4-5, but in general it takes several hours or days to obtain fully crystalline AlPO4-5.110–112 By combining fast heating in the tubular reactor with the addition of a seed, the one-minute synthesis of AlPO4-5 was realized.101 Both fast heating and seeding were found to be crucial to the ultrafast synthesis. In the case of synthesis in the conventional autoclave, a by-product of VPI-5 was formed before the appearance of AlPO4-5 even though the same amount of the seed was added.
SSZ-13
The aluminosilicate zeolites are a class of materials of higher importance than the aluminophosphates due to their practical applications. In this sense, the establishment of the ultrafast synthesis of SSZ-13 represents a milestone, as the SSZ-13 case was the first success in terms of aluminosilicates. The synergistic effect of the addition of the seed, choice of the proper aluminum source and employment of high temperature was found to be effective in easing the bottlenecks in the overall process of the crystallization of SSZ-13, resulting in the ultrafast synthesis in 10 min. This synthesis period is remarkably shorter than the synthesis time reported in the previous reports (typically, greater than 5 days).113,114 Selection of the aluminum source was of particular importance to the ultrafast synthesis of SSZ-13. The ten-minute synthesis of SSZ-13 was realized when aluminum hydroxide with the gibbsite structure was used. In stark contrast, it took a much longer time (several hours) if non-crystalline aluminum hydroxide was used under otherwise similar conditions. These results indicate that the crystallization pathways may vary with aluminum sources, leading to different crystallization rates.
SAPO-34 and SAPO-5
The ultrafast synthesis can also be extended to silicoaluminophosphates, which are considered to be a result of incorporating Si atoms into the framework of aluminophosphates yet possess unique properties different from aluminophosphates and aluminosilicate zeolites.115–117 The minute-order synthesis of two representative silicoaluminophosphates (SAPO-34 and SAPO-5) was demonstrated, resulting in a much accelerated synthesis in the tubular reactor (10 min and 5 min for SAPO-34 and SAPO-5, respectively). Because of similarities in chemical compositions and formation conditions, SAPO-34 and SAPO-5 usually appear as a pair of competing phases in the conventional synthesis, no matter whether SAPO-34 is the targeted phase or SAPO-5.118,119 Owing to the feature of fast heating, the tubular reactor proved to be a facile and precise platform to control the phase selection between SAPO-34 and SAPO-5 by tuning the parameters of the ultrafast synthesis (e.g., the synthesis temperature and the method of pretreating the starting materials).
High-silica ERI zeolite
The ultrafast synthesis of high-silica erionite (ERI) zeolite is challenging as it was typically synthesized by the so-called charge density mismatch (CDM) approach.120 The CDM approach has proved to be a feasible way to discover new zeolites or synthesize the high-silica form of an existing zeolite.121–123 In that method, a charge density mismatch barrier (CDM barrier) is intentionally created by mixing an aluminosilicate solution with high charge density and one or several structure-directing agent(s) with low charge density, which obstructs the crystallization of any zeolites. This CDM barrier is then overcome by adding a sufficient amount of another SDA with higher charge density so as to make the crystallization possible and to proceed through the subsequent hydrothermal synthesis. Although the CDM barrier holds potential for new discoveries, it is not favorable for the ultrafast synthesis. In the case of the high-silica ERI zeolite with the CDM approach, the crystallization rate could hardly be improved by common techniques such as seeding, high temperature synthesis and even the combination of both. We therefore proposed that the ultrafast synthesis could be possible only if the CDM barrier is removed by skipping the CDM method. Inspired by this idea, we carefully designed the synthesis conditions and successfully realized the ultrafast synthesis of the high-silica ERI zeolite in 20 min (Fig. 5).
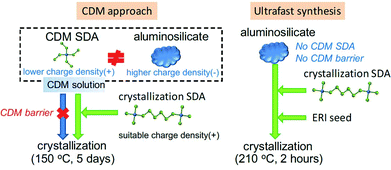 |
| Fig. 5 Ultrafast synthesis of high-silica ERI zeolite. The ultrafast synthesis (right scheme) was established by skipping the employment of CDM SDA and thereof the CDM barrier of the CDM approach (left scheme). (Adapted from ref. 107. Copyright 2017 Royal Society of Chemistry.) | |
Quality of the fast-synthesized zeolites
Because of the huge difference in crystallization rates, concerns might be raised as to whether the fast-synthesized zeolites possess the same property and exhibit the same performance as their conventionally, long-time synthesized counterparts. The characterization results demonstrated that the fast-synthesized products possessed quite similar properties, including silica-to-aluminium ratio and micropore volume, if compared with the seeds synthesized in the autoclaves.102,103 More convincing comparison comes from the application aspect (Fig. 6). Take SSZ-13 for example. SSZ-13 is a high-silica zeolite with a CHA structure that has been proven to be a superior candidate for use as a catalyst for the ammonium selective reduction (NH3-SCR) of NOx.124–126 We compared the NH3-SCR activities of SSZ-13 synthesized in 10 min and SSZ-13 synthesized in the autoclave for 5 days, which was used as the seed for the ultrafast synthesis.102 The results in Fig. 6 suggest that the fast-synthesized SSZ-13 performed similarly to the conventional SSZ-13 in terms of both fresh catalysts and hydrothermally aged catalysts. The comparable performance of the fast-synthesized product in catalytic reactions was also observed by Yu and co-workers, who realized the ultrafast synthesis of nanosized SAPO-34 and demonstrated its outstanding performance in the methanol-to-olefin (MTO) reaction.127
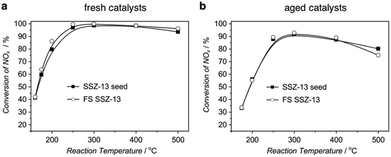 |
| Fig. 6 Comparison of the fast-synthesized SSZ-13 and SSZ-13 seed in a NH3-SCR activity test. (a) Conversion of NOx for the fresh catalysts. (b) Conversion of NOx for the catalysts hydrothermally aged at 900 °C for 1 h. (Reprinted with permission from ref. 102. Copyright 2015 Wiley-VCH.) | |
In some cases, the particle size of the fast-synthesized zeolite was observed to be larger than that of the seed, which is probably due to the fact that the newly generated crystals started to form on the external surface of the seed. Reducing the crystal size of zeolites to the nanometer scale is therefore required so as to enhance the accessibility to the micropores of the fast-synthesized zeolites. Recently, Wakihara et al. have developed a top-down approach to tune the particle size of zeolites, which combines an efficient post-synthesis milling using small beads with a subsequent recrystallization.128,129 We further demonstrated that it was possible to apply the fast synthesis technique to the recrystallization, that is, to combine the post-synthesis milling with the ultrafast recrystallization in the tubular reactor as a strategy to prepare nanosized zeolites (Fig. 7).104
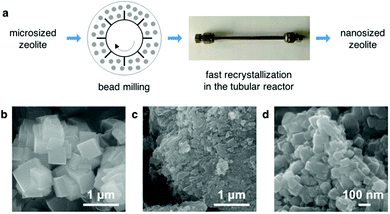 |
| Fig. 7 A top-down method combining post-synthesis milling with fast recrystallization in the tubular reactor to prepare nanosized zeolites. (a) A scheme of the fast recrystallization method. (b to d) SEM image of the fast-synthesized SSZ-13, the milled SSZ-13 and the recrystallized SSZ-13, respectively (the recrystallization was performed in the tubular reactor for 10 min at 210 °C). (Reprinted from ref. 104. Copyright 2015 Royal Society of Chemistry.) | |
Factors contributing to the ultrafast synthesis and a generalized scheme
Aging
It has long been realized that there exist aging effects that can benefit the synthesis. From the early stage of the hydrothermal synthesis, researchers started to perform an aging step prior to the synthesis in order to prompt the formation of the desired phase whilst suppressing the unwanted ones.130,131 Aging is also found to be effective in controlling the crystal size of the product.132,133 As the freshly prepared synthesis mixture may not be well mixed and has a high degree of heterogeneity, at least some certain amount of aging is required to enhance the homogeneity. Furthermore, various characterization results demonstrated that essential reactions have started to occur during aging and that the aging effect is far beyond an extension of physical mixing.134–138 A strong link between the aging behavior and the crystallization rate has been confirmed in the previous studies.13
In terms of ultrafast synthesis, the importance of aging is several-fold. First, it provides the homogeneity and the nutrient species that can support immediate crystal growth. Second, the interaction between inorganic and organic species has been started, which can protect the organic cations against decomposition when subjected to high temperature treatment. Third, the seed can be well mixed and starts its partial dissolution to create a better environment for seeded growth. Lastly, a sufficient nucleus may also be generated through adequate aging, which can eliminate the necessity of adding the seed.
Seeding
Nucleation is generally viewed as the major kinetic barrier in the synthesis. The addition of the seed is a useful practice to shorten the synthesis period, as it can help avoid the heterogeneous nucleation.139–143 Seeding is also expected to provide other merits like serving as a directing agent towards a desired phase and controlling the particle size distribution of the resultant crystals. Recently, OSDA-free synthesis of a series of zeolites by the seeding method has been realized.83–85,144 Effective seeding is viewed to be essential to a successful OSDA-free synthesis.
The addition of seed is one of the key contributing factors to ultrafast synthesis, as the crystallization rate can be greatly enhanced with proper seeding. In addition, the crystal size of the seed matters. A seed with a smaller crystal size is more effective, as smaller crystals can provide a larger external surface area which can absorb most of the available flux of the nutrient species to prompt crystal growth. Therefore, a nanosized seed was found to be more effective for the ultrafast synthesis.105,109 This result is consistent with the common practice for seeded growth (e.g., in the fabrication of the zeolite membrane) where a nanocrystalline seed is preferrable.145–147
High temperature
Compared with nucleation, the crystal growth is kinetically faster. To realize an ultrafast synthesis, however, the crystal growth rate should be improved further. Among the parameters influencing the crystal growth, temperature is considered to be the most sensitive, as many pieces of evidence have indicated that the crystal growth rate is strongly temperature dependent.13,148,149 Increasing the temperature is a straightforward method to accelerate the crystal growth rate, and therefore it was used to achieve ultrafast synthesis in the tubular reactor. As a result, much higher crystal growth rates were observed at high temperatures. For example, silicalite-1 exhibits a linear crystal growth rate, which was calculated to be on the order of tens of nm h−1 for syntheses at moderate temperatures. In a stark contrast, we observed an extraordinarily high crystal growth rate for silicalite-1 (ca. 103 nm h−1 to 104 nm h−1, depending on the silica sources used) when the synthesis was performed at 210 °C.103 Recently, a high-temperature synthesis, carried out under solvent-free conditions, has also demonstrated to be effective in a fast crystallization as well as a high space–time yield.150
Nevertheless, the employment of high temperature has its limit, that is, the synthesis temperature should be within an acceptable range that can ensure the formation of the desired phase rather than undesired ones. It is a common observation in the synthesis of zeolites that the desired phase can only be formed in a proper temperature range, beyond which undesired phases such as dense phases may appear or even dominate in the final product. This phenomenon is primarily because each phase may have its own optimal temperature at which it is the most kinetically preferred. If the OSDA is used, considerations should also be made to avoid the overly fast decomposition of OSDA at high temperatures.
Fast heating
Fast heating of the tubular reactor can offer other benefits that cannot be expected in the conventional autoclaves. For one thing, the tubular reactor can help address the negative effects associated with the thermal lag that exist in the conventional autoclaves. During the temperature increasing step, many reactions may take place, including the ones that can exert adverse effects on the synthesis, such as the decomposition of OSDA and the dissolution of the seed. For example, it was reported that the quaternary ammonium cations can decompose through Hoffman degradation.151–153 Meanwhile, the decomposition of the isolated quaternary ammonium cations is more pronounced compared with those that are trapped inside aluminosilicates.154 These results indicate that the decomposition of the OSDA at the temperature increasing stage cannot be neglected, especially when the heating is performed in a slow manner. The tubular reactor can to some extent minimize the negative effect of the OSDA decomposition, because it allows fast heating and avoids thermal lag. Consequently, fast crystallization at high temperatures can consume the OSDA before the onset of its considerable decomposition. In a similar manner, fast heating can also help avoid the undesired dissolution of the seed which may occur in a slow heating environment.
A generalized scheme of the ultrafast synthesis
Based on the above discussion, a generalized scheme of the ultrafast synthesis was proposed, which takes into consideration the events taking place consequently under different temperatures and at different time scales (Fig. 8).
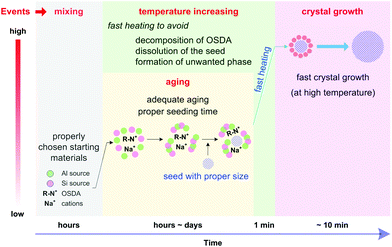 |
| Fig. 8 A generalized scheme for the ultrafast synthesis, which is proposed by taking into consideration the events taking place at different stages under different temperatures and at different time scales. | |
First of all, a synthesis precursor should be prepared with proper starting materials and be well tuned through aging. This precursor contains necessary species, either in the form of aluminosilicate monomers or in other forms like dimers, trimers and oligomers, which can lead to immediate crystal growth once it is subjected to high temperature treatment. To this end, aging at moderate temperatures (higher than room temperature but lower than 100 °C) may be helpful. Because aging and choice of the starting materials are largely dependent, optimization of the aging conditions and screening of the starting materials are always needed.155–159
Secondly, the addition of the seed can help avoid heterogeneous nucleation, a major bottleneck hindering the fast synthesis. It is worth noting that the size of the seed crystal matters. The seed with a smaller size is more effective than the one with a larger size because the smaller seed can provide sufficient external surface area to support seeded growth. Meanwhile, the timing for seeding should be tuned to optimize the seeding effect. The timing is particularly important in the case where aging is carried out at a relatively higher temperature, because dissolution of the seed may occur and be prompted at elevated temperatures.
Through the above tuning, a precursor ready for crystal growth has been created. Crystal growth may have already started at this moment, but at a less noticeable rate. Superficially, this precursor would lead to the formation of the desired phase at a relatively faster rate once it is subjected to hydrothermal treatment at high temperatures. However, that is not taken for granted. When the synthesis is carried out in an autoclave, nucleation of a competing phase may occur, leading to the formation of a by-product. This situation is primarily due to the fact that the slow heating in the autoclave creates an environment where the formation of a comparably metastable phase may be favored. To prevent any undesired phase from being formed, the tubular reactor which is to be heated in a preheated oil bath is a better alternative. Due to the feature of fast heating, the tubular reactor can help avoid the negative effects associated with thermal lag and thereof the generation of the undesired phases.
Finally, high temperatures are preferred to achieve an ultrafast crystal growth. Theoretically, the higher the synthesis temperature, the faster the crystallization rate. However, the maximum temperature is restrained by several aspects, which include but may not be limited to the following points: (1) the possibility of forming a denser phase, (2) the decomposition of OSDA (if any), (3) the limitation from the heating tool and medium, and (4) safety considerations.
Continuous flow synthesis of zeolites
Zeolites are typically synthesized in the reactors operated in batches. The batch process suffers from drawbacks like frequent start-up and shut-down operation and low energy efficiency. Alternatively, continuous flow reactors have shown effectiveness and efficiency in a wide range of fields such as organic synthesis, polymerization and preparation of nanoparticles.160–165 Remarkable improvements in continuous flow processes over batch processes have been demonstrated in emerging publications, including improved yield, high energy efficiency, low consumption of expensive chemicals, precise temperature management, moderate operating conditions and ease of scale-up.166–168
Generally, a continuous flow design may be easily applied to a reaction which has a fast reaction rate or to a reaction in which no solid reagents and/or products are involved.168 For example, several metal–organic framework (MOF) materials have been synthesized in continuous flow reactors, largely because the target crystalline materials could be obtained within a short period of synthesis time, i.e., a short residence time.169–171 Specific to zeolites, however, two features of the synthesis – the long synthesis period and the formation of a solid product – render the continuous flow synthesis difficult to perform.
A comprehensive strategy is therefore needed to address this challenge. The first prerequisite is to improve the overall crystallization rate of zeolites so as to shorten the residence time. Efforts aimed at modifying the hydrodynamic conditions should also be made to overcome possible flow failures. In addition, the synthesis conditions need careful tuning to avoid the generation of any undesired phases. Though the ultrafast synthesis lays a solid basis, other factors should be considered to realize a continuous-flow synthesis. The key to achieve continuous-flow preparation of high-silica zeolites is to match the kinetics, thermodynamics and hydrodynamics (Fig. 9a).102 Mismatch among these three factors may cause practical difficulties or even make continuous-flow synthesis impossible.
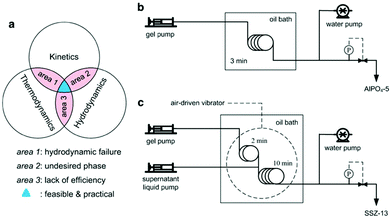 |
| Fig. 9 Continuous flow synthesis of zeolites. (a) General guideline for developing a continuous flow synthesis. (b) One-stage, continuous flow synthesis of AlPO4-5. (c) Two-stage, continuous flow synthesis of SSZ-13. (Adapted with permission from ref. 102. Copyright 2015 Wiley-VCH.) | |
The one-minute synthesis of AlPO4-5 in the tubular reactor was successfully reproduced in a continuous flow reactor where the synergistic effect between the seed-assisted method and fast heating could be achieved.172 The product synthesized in the continuous flow reactor was shown to possess the same properties as the one obtained in the tubular reactor. Meanwhile, the reuse of the product synthesized in the continuous flow reactor as a seed was also demonstrated, which can avoid the production of seed materials using the conventional method. The continuous flow synthesis of AlPO4-5 represents a simple, one-stage design (Fig. 9b), and can be applied to other cases (for example, SAPO-5 and SAPO-34)105 where the fluidity of the synthesis mixture can be well maintained throughout the synthesis.
In some cases, particular considerations should be taken into account to address the issues that lead to hydrodynamic failure. Taking the synthesis of SSZ-13 for example, it was found that the viscosity of the synthesis mixture increased sharply upon heating, causing the fluidity to decrease drastically. Thus it would be impossible to keep a noodle-like aluminosilicate gel flowing smoothly throughout the continuous flow reactor, even though the residence time was as short as 10 min. To solve this problem, a two-stage continuous flow synthesis in which the synthesis mixture was diluted with a supernatant liquid in the middle was developed (Fig. 9c). The introduction of the supernatant liquid significantly improved the fluidity of the synthesis mixture. Meanwhile, the use of the dilution did not alter the crystallization rate too much, largely because the supernatant liquid provided a solution nearly in equilibrium with the final SSZ-13 crystals, as similarly discussed in the previous studies.102,129
Another effective way to avoid the precipitation related problems in the continuous flow process is to utilize a segmented flow, which refers to a multiphase system consisting of an alternating succession of immiscible fluid segments.173–175 Emulsion is a typical segmented system, where an immiscible liquid is dispersed in another liquid to form discrete droplets in a continuous phase through the addition of surfactants.176,177 Very recently, we have demonstrated that the emulsion system offers a unique opportunity to address the sharp viscosity increase taking place in zeolite formation and thus enables a smooth continuous flow synthesis. The continuous flow synthesis of three important zeolites – ERI, *BEA and CHA – was achieved without any blockage issue, demonstrating the emulsion-based, continuous flow synthesis to be a general approach.178
One step further: continuous flow synthesis of ZSM-5 on the order of seconds
As discussed above, due to fast heating and thereof high time resolution, the tubular reactor has opened the possibility to synthesize zeolites on the order of minutes. But it does not mean that the limit of the crystallization rate has been reached. In fact, a higher crystallization rate could not be expected in the tubular reactor because it still takes around 1 min for heat transfer from the external heating medium to the reactant inside. Meanwhile, higher temperature could not be employed due to the restrictions from the heating medium. A new synthesis platform is thus required to explore the limit of crystallization further.
Recently, we have demonstrated a synthetic process for ZSM-5 on the order of seconds in a continuous flow reactor using pressurized hot water as a heating medium (Fig. 10).179 Owing to specific physical and chemical properties, the pressurized hot water with extremely high temperatures can be advantageous to the hydrothermal processing.180,181 By directly mixing a well-tuned synthesis precursor at 90 °C with a flow of the pressurized hot water preheated to 370 °C in the continuous flow reactor, immediate heating to high temperatures (240 to 300 °C, depending on the synthesis precursor to pressurized hot water ratio) could be achieved, which prompted the crystallization of ZSM-5 to completion within several seconds. This result is the first observation indicating the crystallization of zeolites on the order of seconds.
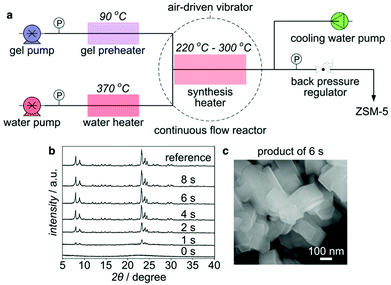 |
| Fig. 10 Continuous flow synthesis of ZSM-5 on the order of seconds. (a) Flow chart of the continuous flow synthesis. (b) XRD patterns of ZSM-5 products synthesized at 260 °C over different periods of time. (c) SEM image of the ZSM-5 product synthesized for 6 s at 260 °C. (Adapted with permission from ref. 179.) | |
The instantaneous heating to high temperature is one of the key factors for the synthesis on the order of seconds. Obvious crystal growth was observed even after a residence time as short as 1 s, indicating a time resolution of one second. This instantaneous heating could further minimize the thermal lag effect, which is very crucial, because the crystal growth can be induced immediately and completed before the total decomposition of the OSDA under strongly basic, high-temperature conditions. In a tubular reactor heated in an aluminium block, it took almost 5 min to complete the crystallization as opposed to 6 s in the continuous flow reactor, even though both syntheses were performed at the same temperature.
Proper tuning of the precursor is another key contributing factor. Aging at 90 °C for several hours was performed in an attempt to tune the precursor, and the synthesis time was found to be dependent on the aging time. An ultrafast synthesis within 16 s could also be achieved even when the synthesis precursor was aged for as short as 2 h. Characterization results indicated that the aging prompted the interactions between the inorganic and organic species and created a precursor with short-range order that could result in immediate crystal growth once it was subjected to high temperatures. It is worth noting that no ZSM-5 seed was added in this case, as proper aging could provide sufficient nuclei to support an immediate crystal growth.
Summary and outlook
The complexity of the formation of zeolites determines that the ultrafast synthesis is not an easy task. Establishment of the ultrafast synthesis should be based on a comprehensive strategy considering both engineering and chemistry perspectives. In the review, both the kinetic and thermodynamic barriers behind the crystallization and the factors that contribute to the ultrafast synthesis were discussed. The factors contributing to the ultrafast synthesis were individually analyzed. The results showed that a comprehensive strategy is needed to overcome the particular thresholds at each certain stage of crystallization. In general, this strategy aims to skip the steps that are actually unnecessary or could be conducted at a low temperature environment prior to the high temperature synthesis, which finally leads to successful synthesis in a very short period of time. These efforts would definitely be helpful to direct the ultrafast synthesis of other zeolites in the future. Based on the ultrafast synthesis, the continuous flow synthesis of zeolites was successfully demonstrated. Furthermore, continuous flow synthesis of ZSM-5 on the order of seconds was also achieved, which was the first observation showing that crystallization of zeolites could be completed within a period of time as short as several seconds, indicating a far-reaching consequence of the ultrafast synthesis.
The potential of the ultrafast synthesis has just been revealed. There might still be room to explore even further increases in the crystallization rate of zeolites. To this end, new reaction systems as well as new ideas for easing the synthesis bottlenecks should be conceived. It is worth noting that the entire synthesis includes not only the crystallization of zeolites taking place in the hydrothermal synthesis but also the pre-synthesis operation such as mixing and aging as well as the post-synthesis treatment such as washing and drying. Therefore, endeavors should be made to enhance the efficiency in these steps. In particular, the long period of aging should be carefully studied in order to shorten the overall preparation period. Such efforts towards the realization of a much faster synthesis, in return, would further benefit the understanding of the nature of crystallization of microporous materials. Recently, we have demonstrated the ultrafast synthesis of *BEA zeolite in 10 min, in which case aging was not involved but the optimization of the composition of the synthesis precursor was found to be crucial.182 This result could help us better understand and design the ultrafast synthesis of zeolites.
From another point of view, the ultrafast synthesis has opened a window for the mechanistic study of crystallization. Since the complexity of crystallization of zeolites is far from being fully understood, there are many fields where new perspectives are expected from new synthesis techniques/tools. The following are the fields where the ultrafast synthesis and the associate reactors can show advantages: (1) precise control over the properties, for example, morphology and the distribution of T-atoms, (2) preparation of zeolites for which competitive phases always exist, (3) fast incorporation of heteroatoms into zeolites, and (4) combination with post-treatment techniques to explore the properties of zeolites.
Conflicts of interest
There are no conflicts to declare.
Acknowledgements
We thank the coauthors of the papers that the Okubo group has published on the ultrafast synthesis and the continuous flow synthesis of zeolites and Mitsubishi Chemical Cooperation for partially funding those investigations. We also thank the New Energy and Industrial Technology Development Organization for partially funding those investigations.
References
- M. E. Davis, Ordered Porous Materials for Emerging Applications, Nature, 2002, 417, 813–821 CrossRef CAS PubMed.
- T. Wakihara and T. Okubo, Hydrothermal Synthesis and Characterization of Zeolites, Chem. Lett., 2005, 34, 276–281 CrossRef CAS.
- A. Primo and H. Garcia, Zeolites as catalysts in oil refining, Chem. Soc. Rev., 2014, 43, 7548–7561 RSC.
- M. Tsapatsis, Molecular Sieves in The Nanotechnology Era, AIChE J., 2002, 48, 654–660 CrossRef CAS.
- Z. Li, M. C. Johnson, M. Sun, E. T. Ryan, D. J. Earl, W. Maichen, J. I. Martin, S. Li, C. M. Lew, J. Wang, M. W. Deem, M. E. Davis and Y. Yan, Mechanical and Dielectric Properties of Pure-Silica-Zeolite Low-k Materials, Angew. Chem., Int. Ed., 2006, 45, 6329–6332 CrossRef CAS PubMed.
- G. W. Huber and A. Corma, Synergies between Bio- and Oil Refineries for the Production of Fuels from Biomass, Angew. Chem., Int. Ed., 2007, 46, 7184–7201 CrossRef CAS PubMed.
- M. Hartmann and L. Kevan, Transition-metal Ions in Aluminophosphate and Silicoaluminophosphate Molecular Sieves: Location, Interaction with Adsorbates and Catalytic Properties, Chem. Rev., 1999, 99, 635–664 CrossRef CAS.
- J. Li, A. Corma and J. Yu, Synthesis of new zeolite structures, Chem. Soc. Rev., 2015, 44, 7112–7127 RSC.
- J. A. van Bokhovena and C. Lamberti, Structure of aluminum, iron, and other heteroatoms in zeolites by X-ray absorption spectroscopy, Coord. Chem. Rev., 2014, 277, 275–290 CrossRef.
-
http://www.iza-structure.org/database
.
- R. M. Barrer, Synthesis of a zeolitic mineral with chabazite-like sorptive properties, J. Chem. Soc., 1948, 127–132 RSC.
- R. M. Barrer, L. Hinds and E. A. White, The hydrothermal chemistry of silicates. Part III. Reactions of analcite and leucite, J. Chem. Soc., 1953, 1466–1475 RSC.
- C. S. Cundy and P. A. Cox, The Hydrothermal Synthesis of Zeolites: History and Development from the Earliest Days to the Present Time, Chem. Rev., 2003, 103, 663–701 CrossRef CAS.
- C. S. Cundy and P. A. Cox, The hydrothermal synthesis of zeolites: Precursors, intermediates and reaction mechanism, Microporous Mesoporous Mater., 2005, 82, 1–78 CrossRef CAS.
- M. E. Davis and A. Corma, Issues in the Synthesis of Crystalline Molecular Sieves: Towards the Crystallization of Low Framework-Density Structures, ChemPhysChem, 2004, 53, 304–313 Search PubMed.
- A. Navrotsky, O. Trofymluk and A. A. Levchenko, Thermochemistry of Microporous and Mesoporous Materials, Chem. Rev., 2009, 109, 3885–3902 CrossRef CAS.
- A. Navrotsky, Energetics at the nanoscale: Impacts for geochemistry, the environment, and materials, MRS Bull., 2016, 41, 139–145 CrossRef CAS.
- D. Wu, S. Hwang, S. I. Zones and A. Navrotsky, Guest–host interactions of a rigid organic molecule inporous silica frameworks, Proc. Natl. Acad. Sci. U. S. A., 2014, 111, 1720–1725 CrossRef CAS.
- A. W. Burton, S. I. Zones and S. Elomari, The chemistry of phase selectivity in the synthesis of high-silica zeolites, Curr. Opin. Colloid Interface Sci., 2005, 10, 211–219 CrossRef CAS.
- M. E. Davis, Zeolites from a Materials Chemistry Perspective, Chem. Mater., 2014, 26, 239–245 CrossRef CAS.
- M. E. Davis and R. F. Lobo, Zeolite and molecular sieve synthesis, Chem. Mater., 1992, 4, 756–768 CrossRef CAS.
- M. Moliner and A. Avelino Corma, Advances in the synthesis of titanosilicates: From the medium pore TS-1zeolite to highly-accessible ordered materials, Microporous Mesoporous Mater., 2014, 189, 31–40 CrossRef CAS.
- J. Jiang, J. Yu and A. Corma, Extra-large-pore zeolites: bridging the gap between micro and mesoporous structures, Angew. Chem., Int. Ed., 2010, 49, 3120–3145 CrossRef CAS.
- M. E. Davis and S. I. Zones, Zeolite materials: recent discoveries and future prospects, Curr.
Opin. Colloid Interface Sci., 1996, 1, 107–117 CrossRef.
- X. Meng and F. Xiao, Green Routes for Synthesis of Zeolites, Chem. Rev., 2014, 114, 1521–1543 CrossRef CAS.
- M. Moliner, F. Fernando Rey and A. Corma, Towards the rational design of efficient organic structure-directing agents for zeolite synthesis, Angew. Chem., Int. Ed., 2013, 52, 13880–13889 CrossRef CAS PubMed.
- W. J. Roth, P. Nachtigall, R. E. Morris and J. Čejka, Two-Dimensional Zeolites: Current Status and Perspectives, Chem. Rev., 2014, 114, 4807–4837 CrossRef CAS.
- P. Eliášová, M. Opanasenko, P. S. Wheatley, M. Shamzhy, M. Mazur, P. Nachtigall, W. J. Roth, R. E. Morris and J. Čejka, The ADOR mechanism for the synthesis of new zeolites, Chem. Soc. Rev., 2015, 44, 7177–7206 RSC.
- Y. Wu, X. Ren and J. Wang, Effect of microwave-assisted aging on the static hydrothermal synthesis of zeolite MCM-22, Microporous Mesoporous Mater., 2008, 116, 386–393 CrossRef CAS.
- R. van Grieken, J. L. Sotelo, J. M. Menéndez and J. A. Melero, Anomalous crystallization mechanism in the synthesis of nanocrystalline ZSM-5, Microporous Mesoporous Mater., 2000, 39, 135–147 CrossRef CAS.
- J. Shi, M. W. Anderson and S. W. Carr, Direct Observation of Zeolite A Synthesis by in Situ Solid-State NMR, Chem. Mater., 1996, 8, 369–375 CrossRef CAS.
- J. Dougherty, L. E. Iton and J. W. White, Room temperature aging of a ZSM-5 preparation detected by small angle X-ray and neutron scattering and n.m.r. spectroscopy, Zeolites, 1995, 15, 640–649 CrossRef CAS.
- S. Mintova and V. Valtchev, Synthesis of nanosized FAU-type zeolite, Stand. Surf. Sci. Catal., 1999, 125, 141–148 CAS.
- V. Valtchev and K. Bozhilov, Transmission Electron Microscopy Study of the Formation of FAU-Type Zeolite at Room Temperature, J. Phys. Chem. B, 2004, 108, 15587–15598 CrossRef CAS.
- S. Kumar, Z. Wang, R. L Penn and M. Tsapatsis, A Structural Resolution Cryo-TEM Study of the Early Stage of MFI Growthm, J. Am. Chem. Soc., 2008, 130, 17284–17286 CrossRef CAS.
- T. Wakihara, S. Kohara, G. Sankar, S. Saito, M. Sanchez-Sanchez, A. R. Overweg, W. Fan, M. Ogura and T. Okubo, A new approach to the determination of atomic-architecture of amorphous zeolite precursors by high-energy x-ray diffraction technique, Phys. Chem. Chem. Phys., 2006, 8, 224–227 RSC.
- T. Umeda, H. Yamada, K. Ohara, K. Yoshida, Y. Sasaki, M. Takano, S. Inagaki, Y. Kubota, T. Takewaki, T. Okubo and T. Wakihara, Comparative study on the different interaction pathways between amorphous aluminosilicate species and organic structure-directing agents yielding different zeolite Phases, J. Phys. Chem. C, 2017, 121, 24324–24334 CrossRef CAS.
- Q. Li, B. ; Mihailov, D. Creaser and J. Sterte, Aging effects on the nucleation and crystallization kinetics of colloidal TPA-silicalite-1, Microporous Mesoporous Mater., 2001, 43, 51–59 CrossRef CAS.
- M. Ogura, Y. Kawazu, H. Takahashi and T. Okubo, Aluminosilicate Species in The Hydrogel Phase Formed during The Aging Process for The Crystallization of FAU Zeolite, Chem. Mater., 2003, 15, 2661–2667 CrossRef CAS.
- S. Inagaki, K. Thomas, V. Ruaux, G. Clet, T. Wakihara, S. Shinoda, S. Okamura, Y. Kubota and V. Valtchev, Crystal Growth Kinetics as a Tool for Controlling the Catalytic Performance of a FAU-Type Basic Catalyst, ACS Catal., 2014, 4, 2333–2341 CrossRef CAS.
- J. D. Rimer and M. Tsapatsis, Nucleation of Open Framework Materials: Navigating the Voids, MRS Bull., 2016, 41, 393–398 CrossRef CAS.
- J. D. Rimer, D. G. Vlachos and R. F. Lobo, Evolution of Self-Assembled Silica-Tetrapropylammonium Nanoparticles at Elevated Temperatures, J. Phys. Chem. B, 2005, 109(26), 12762–12771 CrossRef CAS.
- P. de Moor, T. P. M. Beelen and R. A. van Santen, In situ Observation of Nucleation and Crystal Growth in Zeolite Synthesis. A Small-Angle X-ray Scattering Investigation on Si-TPA-MFI, J. Phys. Chem. B, 1999, 103, 1639–1650 CrossRef CAS.
- N. D. Hould and R. F. Lobo, Nanoparticle Precursors and Phase Selectivity in Hydrothermal Synthesis of Zeolite β, Chem. Mater., 2008, 20, 5807–5815 CrossRef CAS.
- N. Ren, B. Subotic, J. Bronic, Y. Tang, M. D. Sikiric, T. Misic, V. Svetlicic, S. Bosnar and T. A. Jelic, Unusual Pathway of Crystallization of Zeolite ZSM-5 in a Heterogeneous System: Phenomenology and Starting Considerations, Chem. Mater., 2012, 24, 1726–1737 CrossRef CAS.
- V. Nikolakis, E. Kokkoli, M. Tirrell, M. Tsapatsis and D. Vlachos, Chem. Mater., 2000, 12, 845–853 CrossRef CAS.
- S. L. Burkett and M. E. Davis, Mechanisms of Structure Direction in the Synthesis of Pure-Silica Zeolites. 1. Synthesis of TPA/Si-ZSM-5, Chem. Mater., 1995, 7, 920–928 CrossRef CAS.
- S. L. Burkett and M. E. Davis, Mechanism of Structure Direction in the Synthesis of Pure-Silica Zeolites. 2. Hydrophobic Hydration and Structural Specificity, Chem. Mater., 1995, 7, 1453–1463 CrossRef CAS.
- T. M. Davis, T. O. Drews, H. Ramanan, C. He, J. S. Dong, H. Schnablegger, M. A. Katsoulakis, E. Kokkoli, A. V. McCormick and R. L. Penn,
et al. Mechanistic principles of nanoparticle evolution to zeolite crystals, Nat. Mater., 2006, 5, 400–408 CrossRef CAS PubMed.
- K. N. Olafson, R. Li, B. G. Alamani and J. D. Rimer, Engineering Crystal Modifiers: Bridging Classical and Nonclassical Crystallization, Chem. Mater., 2016, 28, 8453–8465 CrossRef CAS.
- J. D. Rimer, M. Kumar, R. Li, A. I. Lupulescu and M. D. Oleksiak, Tailoring the physicochemical properties of zeolite catalysts, Catal. Sci. Technol., 2014, 4, 3762–3771 RSC.
- M. Kumar, R. Li and J. D. Rimer, Assembly and Evolution of Amorphous Precursors in Zeolite L Crystallization, Chem. Mater., 2016, 28, 1714–1727 CrossRef CAS.
- M. Kumar, H. Luo, Y. Roman-Leshkov and J. D. Rimer, SSZ-13 Crystallization by Particle Attachment and Deterministic Pathways to Crystal Size Control, J. Am. Chem. Soc., 2015, 137, 13007–13017 CrossRef CAS PubMed.
- I. Petrovic, A. Navrotsky, M. E. Davis and S. I. Zones, Thermochemical study of the stability of frameworks in high silica zeolites, Chem. Mater., 1993, 5, 1805–1813 CrossRef CAS.
- R. A. van Santen, The Ostwald Step Rule, J. Phys. Chem., 1984, 88, 5768–5769 CrossRef CAS.
- M. Do, T. Wang, D. Cheng, F. Chen, X. Zhan and J. Gong, Zeolite Growth by Synergy Between Solution-Mediated and Solid-Phase Transformations, J. Mater. Chem. A, 2014, 2, 14360–14370 RSC.
- M. Maldonado, M. D. Oleksiak, S. Chinta and J. D. Rimer, Controlling Crystal Polymorphism in Organic-Free Synthesis of Na-Zeolites, J. Am. Chem. Soc., 2013, 135, 2641–2652 CrossRef CAS PubMed.
- T. Antonic and B. Subotic, Influence of gel properties on the crystallization of zeolites: Part 1: Influence of alkalinity during gel preparation on the kinetics of nucleation of zeolite A, Zeolites, 1997, 18, 291–300 CrossRef CAS.
- P. A. Barrett, M. A. Camblor, A. Corma, R. H. Jones and L. A. Villaescusa, Synthesis and Structure of As-Prepared ITQ-4, A Large Pore Pure Silica Zeolite: The Role and Location of Fluoride Anions and Organic Cations, J. Phys. Chem. B, 1998, 102, 4147–4155 CrossRef CAS.
- B. M. Lok, T. R. Cannan and C. A. Messina, The role of organic molecules in molecular sieve synthesis, Zeolites, 1983, 3, 282–291 CrossRef CAS.
- C. Shao, H. Kim, X. Li, S. Park and D. Lee, Synthesis of high-silica-content mordenite with different SiO2/Al2O3 ratios by using benzene-1,2-diol as additives, Mater. Lett., 2002, 56, 24–29 CrossRef CAS.
- G. Giannetto and F. Dos Santos, Effect of aluminum and gallium concentration on the crystallization rate of TPA/MFI zeolites synthesized with MeNH2 in the absence of inorganic cations, Zeolites, 1995, 15, 719–724 CrossRef CAS.
- Y. Wu, X. Ren, Y. Lu and J. Wang, Crystallization and morphology of zeolite MCM-22 influenced by various conditions in the static hydrothermal synthesis, Microporous Mesoporous Mater., 2008, 112, 138–146 CrossRef CAS.
- P. Wang, A. Lv, J. Hu, J. Xu and G. Lu, The synthesis of SAPO-34 with mixed template and its catalytic performance for methanol to olefins reaction, Microporous Mesoporous Mater., 2012, 152, 178–184 CrossRef CAS.
- T. Álvaro-Muñoz, C. Márquez-Álvarez and E. Sastre, Use of different templates on SAPO-34 synthesis: Effect on the acidity and catalytic activity in the MTO reaction, Catal. Today, 2012, 179, 27–34 CrossRef.
- G. Tompsett, W. C. Conner and K. S. Yngvesson, Microwave synthesis of nanoporous materials, ChemPhysChem, 2006, 7, 296–319 CrossRef CAS.
- M. Gharibeh, G. Tompsett and K. S. Yngvesson, Conner, W. C. Microwave synthesis of zeolites: Effect of power delivery, J. Phys. Chem. B, 2009, 26, 8930–8940 CrossRef.
- D. A. C. Stuerga and P. Gaillard, Microwave athermal effects in chemistry: A myth's autopsy: Part I: Historical background and fundamentals of wave-matter interaction, J. Microwave Power Electromagn. Energy, 1996, 31, 87–100 Search PubMed.
- W. C. Conner and G. A. Tompsett, How could and do microwaves influence chemistry at interfaces, J. Phys. Chem. B, 2008, 7, 2110–2118 CrossRef PubMed.
- C. S. Cundy, R. J. Plaisted and J. P. Zhao, Remarkable synergy between microwave heating and the addition of seed crystals in zeolite synthesis – a suggestion verified, Chem. Commun., 1998, 1465–1466 RSC.
- T. Sano, M. Itakura and M. Sadakane, High potential of interzeolite conversion method for zeolite synthesis, J. Jpn. Pet. Inst., 2013, 4, 183–197 CrossRef.
- S. Goel, S. I. Zones and E. Iglesia, Synthesis of zeolites via interzeolite transformations without organic structure-directing agents, Chem. Mater., 2015, 27, 2056–2066 CrossRef CAS.
- N. Martin, C. R. Boruntea, M. Moliner and A. Corma, Efficient synthesis of the Cu-SSZ-39 catalyst for DeNOx applications, Chem. Commun., 2015, 51, 11030–11033 RSC.
- Y. Kunitake, T. Takata, Y. Yamasaki, N. Yamanaka, N. Tsunoji, Y. Takamitsu, M. Sdakane and T. Sano, Synthesis of titanated chabazite with enhanced thermal stability by hydrothermal conversion of titanated faujasite, Microporous Mesoporous Mater., 2015, 215, 58–66 CrossRef CAS.
- K. Honda, A. Yashiki, M. Itakura, Y. Ide, M. Sadakane and T. Sano, Influence of seeding on FAU-*BEA interzeolite conversion, Microporous Mesoporous Mater., 2011, 142, 161–167 CrossRef CAS.
- G. Feng, P. Cheng, W. Yan, M. Boronat, X. Li, J. Su, J. Wang, Y. Li, A. Corma, R. Xu and J. Yu, Accelerated crystallization of zeolites via hydroxyl free radicals, Science, 2016, 6278, 1188–1191 CrossRef.
- G. Feng, J. Wang, M. Boronat, Y. Li, J. Su, H. Ju, Y. Ma and J. Yu, Radical-facilitated green synthesis of highly ordered mesoporous silica materials, J. Am. Chem. Soc., 2018, 140, 4770–4773 CrossRef CAS PubMed.
- B. Xie, J. Song, L. Ren, Y. Ji, J. Li and F. Xiao, Organotemplate-Free and Fast Route for Synthesizing Beta Zeolite, Chem. Mater., 2008, 20, 4533–4535 CrossRef CAS.
- K. Iyoki, Y. Kamimura, K. Itabashi, A. Shimojima and T. Okubo, Synthesis of MTW-type zeolites in the absence of organic structure-directing agent, Chem. Lett., 2010, 39, 730–731 CrossRef CAS.
- A. Ogawa, K. Iyoki, Y. Kamimura, S. P. Elangovan, K. Itabashi and T. Okubo, Seed-directed, rapid synthesis of MAZ-type zeolites without using organic structure-directing agent, Microporous Mesoporous Mater., 2014, 186, 21–28 CrossRef CAS.
- Y. Kamimura, K. Itabashi, Y. Kon, A. Endo and T. Okubo, Seed-assisted synthesis of MWW-type zeolite with organic structure-directing agent-free Na-aluminosilicate gel system, Chem. – Asian J., 2017, 12, 530–542 CrossRef CAS.
- K. Iyoki, K. Itabashi, W. Chaikittisilp, S. P. Elangovan, T. Wakihara, S. Kohara and T. Okubo, Broadening the application scope of seed-directed, organic structure-directing agent-free synthesis of zeolite to zincosilicate components: A case of VET-type zincosilicate zeolites, Chem. Mater., 2014, 26, 1957–1966 CrossRef CAS.
- K. Itabashi, Y. Kamimura, K. Iyoki, A. Shimojima and T. Okubo, A Working Hypothesis for Broadening Framework Types of Zeolites in Seed-Assisted Synthesis without Organic Structure Directing Agent, J. Am. Chem. Soc., 2012, 134, 11542–11549 CrossRef CAS PubMed.
- K. Iyoki, K. Itabashi and T. Okubo, Progress in seed-assisted synthesis of zeolites without using organic structure-directing agents, Microporous Mesoporous Mater., 2014, 189, 22–30 CrossRef CAS.
- Y. Kubota, K. Itabashi, S. Inagaki, Y. Nishita, R. Komatsu, Y. Tsuboi, S. Shinoda and T. Okubo, Effective Fabrication of Catalysts from Large-Pore, Multidimensional Zeolites Synthesized without Using Organic Structure-Directing Agents, Chem. Mater., 2014, 26, 1250–1259 CrossRef CAS.
- N. Martín, M. Moliner and A. Corma, High yield synthesis of high-silica chabazite by combining the role of zeolite precursors and tetraethylammonium: SCR of NOx, Chem. Commun., 2015, 51, 9965–9968 RSC.
- S. Sogukkanli, K. Iyoki, S. P. Elangovan, K. Itabashi, M. Takano, Z. Liu, S. Inagaki, T. Wakihara, Y. Kubota and T. Okubo, Rational seed-directed synthesis of MSE-type zeolites using a simple organic structure-directing agent by extending the composite building unit hypothesis, Microporous Mesoporous Mater., 2017, 245, 1–7 CrossRef CAS.
- L. Ren, Q. Guo, P. Kumar, M. Orazov, D. Xu, S. M. Alhassan, K. A. Mkhoyan, M. E. Davis and M. Tsapatsis, Self-pillared, single-unit-cell Sn-MFI zeolite nanosheets and their use for glucose and lactose isomerization, Angew. Chem., Int. Ed., 2015, 37, 10848–10851 CrossRef PubMed.
- D. Xu, G. R. Swindlehurst, H. Wu, D. H. Olson, X. Zhang and M. Tsapatsis, On the synthesis and adsorption properties of single-unit-cell hierarchical zeolites made by rotational intergrowths, Adv. Funct. Mater., 2014, 24, 201–208 CrossRef CAS.
- X. Shen, W. Mao, Y. Ma, D. Xu, P. Wu, O. Terasaki, L. Han and S. Che, A hierarchical MFI zeolite with a two-dimensional square mesostructure, Angew. Chem., Int. Ed., 2018, 57, 724–728 CrossRef CAS PubMed.
- M. Y. Jeon, D. Kim, P. Kumar, P. S. Lee, N. Rangnekar, P. Bai, M. Shete, B. Elyassi, H. S. Lee, K. Narasimharao, S. N. Basahel, S. Al-Thabaiti, W. Xu, H. J. Cho, E. O. Fetisov, R. Thyagarajan, R. F. DeJaco, W. Fan, K. A. Mkhoyan, J. I. Siepmann and M. Tsapatsis, Ultra-selective high-flux membranes from directly synthesized zeolite nanosheets, Nature, 2017, 543, 690–694 CrossRef CAS PubMed.
- D. Kim, M. Shete and M. Tsapatsis, Large-Grain, Oriented, and Thin Zeolite MFI Films from Directly Synthesized Nanosheet Coatings, Chem. Mater., 2018, 10, 3545–3551 CrossRef.
- L. Xu and J. Sun, Recent advances in the synthesis and application of two-dimensional zeolites, Adv. Energy Mater., 2016, 17, 1600441 CrossRef.
- S. K. Brand, J. E. Schmidt, M. W. Deem, F. Daeyaert, Y. Ma, O. Terasaki, M. Orazov and M. E. Davis, Enantiomerically Enriched, Polycrystalline Molecular Sieves, Proc. Natl. Acad. Sci. U. S. A., 2017, 114, 5101–5106 CrossRef CAS PubMed.
- M. E. Davis, A thirty-year journey to the creation of the first enantiomerically enriched molecular sieve, ACS Catal., 2018, 8, 10082–10088 CrossRef CAS.
- T. Yokoi, H. Mochizuki, S. Namba, J. N. Kondo and T. Tatsumi, Control of the Al distribution in the framework of ZSM-5 zeolite and its evaluation by solid-state NMR technique and catalytic properties, J. Phys. Chem. C, 2015, 119, 15303–15315 CrossRef CAS.
- M. Liu, T. Yokoi, M. Yoshioka, H. Imai, J. N. Kondo and T. Tatsumi, Differences in Al Distribution and Acidic Properties between RTH-type Zeolites Synthesized with OSDAs and without OSDAs, Phys. Chem. Chem. Phys., 2014, 16, 4155–4164 RSC.
- A. Vjunov, J. L. Fulton, T. Huthwelker, S. Pin, D. Mei, G. K. Schenter, N. Govind, D. M. Camaioni, J. Z. Hu and J. A. Lercher, Quantitatively Probing the Al Distribution in Zeolites, J. Am. Chem. Soc., 2014, 136, 8296–8306 CrossRef CAS PubMed.
- A. B. Pinar, R. Verel, J. Perez-Pariente and J. A. van Bokhoven, Direct Evidence of the Effect of Synthesis Conditions on Aluminum Siting in Zeolite Ferrierite: A 27Al MQ MAS NMR study, Microporous Mesoporous Mater., 2014, 193, 111–114 CrossRef CAS.
- J. Dedecek, Z. Sobalík and B. Wichterlova, Siting and Distribution of Framework Aluminium Atoms in Silicon-Rich Zeolites and Impact on Catalysis, Catal. Rev.: Sci. Eng., 2012, 54, 135–223 CrossRef CAS.
- Z. Liu, T. Wakihara, D. Nishioka, K. Oshima, T. Takewaki and T. Okubo, One-Minute Synthesis of Crystalline Microporous Aluminophosphate (AlPO4-5) by Combining Fast Heating with A Seed-Assisted Method, Chem. Commun., 2014, 50, 2526–2528 RSC.
- Z. Liu, T. Wakihara, K. Oshima, D. Nishioka, Y. Hotta, S. P. Elangovan, Y. Yanaba, T. Yoshikawa, W. Chaikittisilp, T. Matsuo, T. Takewaki and T. Okubo, Widening Synthesis Bottlenecks: Realization of Ultrafast and Continuous-Flow Synthesis of High-Silica Zeolite SSZ-13 for NOx Removal, Angew. Chem., 2015, 127, 5775–5779 CrossRef.
- Z. Liu, T. Wakihara, C. Anand, S. H. Keoh, D. Nishioka, Y. Hotta, T. Matsuo, T. Takewaki and T. Okubo, Ultrafast Synthesis of Silicalite-1 Using A Tubular Reactor with A Feature of Rapid Heating, Microporous Mesoporous Mater., 2016, 223, 140–144 CrossRef CAS.
- Z. Liu, N. Nomura, D. Nishioka, Y. Hotta, T. Matsuo, K. Oshima, Y. Yanaba, T. Yoshikawa, K. Ohara, S. Kohara, T. Takewaki, T. Okubo and T. Wakihara, A Top-Down Methodology for Ultrafast Tuning of Nanosized Zeolites, Chem. Commun., 2015, 51, 12567–12570 RSC.
- Z. Liu, T. Wakihara, N. Nomura, T. Matsuo, C. Anand, S. P. Elangovan, Y. Yanaba, T. Yoshikawa and T. Okubo, Ultrafast and Continuous Flow Synthesis of Silicoaluminophosphates, Chem. Mater., 2016, 28, 4840–4847 CrossRef CAS.
- J. Zhu, Z. Liu, A. Endo, Y. Yanaba, T. Yoshikawa, T. Wakihara and T. Okubo, Ultrafast, OSDA-free synthesis of mordenite zeolite, CrystEngComm, 2017, 4, 632–640 RSC.
- J. Zhu, Z. Liu, K. Iyoki, C. Anand, K. Yoshida, Y. Sasaki, S. Sukenaga, M. Ando, H. Shibata, T. Okubo and T. Wakihara, Ultrafast synthesis of high-silica erionite zeolites with improved hydrothermal stability, Chem. Commun., 2017, 50, 6796–6799 RSC.
- J. Zhu, Z. Liu, S. Sukenaga, M. Ando, H. Shibata, T. Okubo and T. Wakihara, Ultrafast synthesis of *BEA zeolite without the aid of aging pretreatment, Microporous Mesoporous Mater., 2018, 268, 1–8 CrossRef CAS.
- C. Peng, Z. Liu, T. Okubo and T. Wakihara, Fast synthesis of SSZ-24: A pure silica zeolite with AFI framework, Chem. Lett., 2018, 5, 654–656 CrossRef.
- Y. P. Xu, Z. J. Tian, S. J. Wang, Y. Hu, L. Wang, B. C. Wang, Y. C. Ma, L. Hou, J. Y. Yu and L. W. Lin, Microwave-enhanced ionothermal synthesis of aluminophosphates molecular sieves, Angew. Chem., Int. Ed., 2006, 45, 3965–3970 CrossRef CAS PubMed.
- B. Chen, C. W. Kirby and Y. Huang, Investigation of crystallization of molecular sieve AlPO4-5 by the dry gel conversion method, J. Phys. Chem. C, 2009, 113, 15868–15876 CrossRef CAS.
- M. Z. Yates, K. C. Ott, E. R. Birnbaum and T. M. McCleskey, Hydrothermal synthesis of molecular sieve fibers: using microemulsions to control crystal morphology, Angew. Chem., Int. Ed., 2002, 41, 494–496 CrossRef.
- F. Gao, N. M. Washton, Y. Wang, M. Kollar, J. Szanyi and C. H. F. Peden, Effects of Si/Al ratio on Cu/SSZ-13 NH3-SCR catalysts: Implications for the active Cu species and the roles of Brønsted acidity, J. Catal., 2015, 331, 25–38 CrossRef CAS.
- J. Luo, K. Kamasamudram, N. Currier and C. H. F. Peden, New insights into Cu/SSZ-13 SCR catalyst acidity. Part I: Nature of acidic sites probed by NH3 titration, J. Catal., 2017, 348, 291–299 CrossRef CAS.
- S. T. Wilson, B. M. Lok, C. A. Messina, T. R. Cannan and E. M. Flanigen, Aluminophosphate Molecular Sieves - A New Class of Microporous Crystalline Inorganic Solids, J. Am. Chem. Soc., 1982, 104, 1146–1147 CrossRef CAS.
- B. M. Lok, C. A. Messina, R. L. Patton, R. T. Gajek, T. R. Cannan and E. M. Flanigen, Silicoaluminophosphate Molecular Sieves - Another New Class of Microporous Crystalline Inorganic Solids, J. Am. Chem. Soc., 1984, 106, 6092–6093 CrossRef CAS.
- M. Hartmann and L. Kevan, Transition-metal Ions in Aluminophosphate and Silicoaluminophosphate Molecular Sieves: Location, Interaction with Adsorbates and Catalytic Properties, Chem. Rev., 1999, 99, 635–664 CrossRef CAS PubMed.
- G. Sastre, D. W. Lewis and C. R. A. Catlow, Modeling of Silicon Substitution in SAPO-5 and SAPO-34 Molecular Sieves, J. Phys. Chem. B, 1997, 101, 5249–5262 CrossRef CAS.
- D. Young and M. E. Davis, Studies on SAPO-5 - Synthesis with Higher Silicon Contents, Zeolites, 1991, 11, 277–281 CrossRef CAS.
- M. A. Miller, G. J. Lewis, J. G. Moscoso, S. Koster, F. Modica, M. G. Gatter and L. T. Nemeth, Synthesis and catalytic activity of UZM-12, Stud. Surf. Sci. Catal., 2007, 170, 487–492 CrossRef.
- J. H. Lee, M. B. Park, J. K. Lee, H. K. Min, M. K. Song and S. B. Hong, Synthesis and characterization of ERI-type UZM-12 zeolites and their methanol-to-olefin performance, J. Am. Chem. Soc., 2010, 132, 12971–12982 CrossRef CAS PubMed.
- C. S. Blackwell, R. W. Broach, M. G. Gatter, J. S. Holmgren, D. Y. Jan, G. J. Lewis, B. J. Mezza, T. M. Mezza, M. A. Miller, J. G. Moscoso, R. L. Patton, L. M. Rohde, M. W. Schoonover, W. Sinkler, B. A. Wilson and S. T. Wilson, Open-framework materials synthesized in the TMA+/TEA+ mixed-template system: The new low Si/Al ratio zeolites UZM-4 and UZM-5, Angew. Chem., Int. Ed., 2003, 42, 1737–1740 CrossRef CAS PubMed.
- G. J. Lewis, M. A. Miller, J. G. Moscoso, L. M. Knight and S. T. Wilson, Experimental charge density matching approach to zeolite synthesis, Stud. Surf. Sci. Catal., 2004, 154, 364–372 CrossRef.
- F. Göltl, R. E. Bulo, J. Hafner and P. Sautet, What Makes Copper-Exchanged SSZ-13 Zeolite Efficient at Cleaning Car Exhaust Gases?, J. Phys. Chem. Lett., 2013, 4, 2244–2249 CrossRef.
- U. Deka, I. Lezcano-Gonzalez, B. M. Weckhuysen and A. M. Beale, Local Environment and Nature of Cu Active Sites in Zeolite-Based Catalysts for the Selective Catalytic Reduction of NOx, ACS Catal., 2013, 3, 413–427 CrossRef CAS.
- D. W. Fickel and R. F. Lobo, Copper Coordination in Cu-SSZ-13 and Cu-SSZ-16 Investigated by Variable-Temperature XRD, J. Phys. Chem. C, 2010, 114, 1633–1640 CrossRef CAS.
- Q. Sun, N. Wang, G. Guo and J. Yu, Ultrafast synthesis of nano-sized zeolite SAPO-34 with excellent MTO catalytic performance, Chem. Commun., 2015, 51, 16397–16400 RSC.
- T. Wakihara, K. Sato, S. Inagaki, J. Tatami, K. Komeya, T. Meguro and Y. Kubota, Fabrication of Fine Zeolite with Improved Catalytic Properties by Bead Milling and Alkali Treatment, ACS Appl. Mater. Interfaces, 2010, 2, 2715–2718 CrossRef CAS.
- T. Wakihara, R. Ichikawa, J. Tatami, A. Endo, K. Yoshida, Y. Sasaki, K. Komeya and T. Meguro, Bead-Milling and Postmilling Recrystallization: An Organic Template-Free Methodology for The Production of Nano-Zeolites, Cryst. Growth Des., 2011, 11, 955–958 CrossRef CAS.
- E. F. Freund, Mechanism of the crystallization of zeolite X, J. Cryst. Growth, 1976, 34, 11–23 CrossRef CAS.
- P. K. Dutta, D. C. Shieh and M. Puri, Raman Spectroscopic Study of the Synthesis of Zeolite Y, J. Phys. Chem., 1987, 91, 2332–2336 CrossRef CAS.
- S. Alfaro, C. Rodríguez, M. A. Valenzuela and P. Bosch, Aging time effect on the synthesis of small crystal LTA zeolites in the absence of organic template, Mater. Lett., 2007, 61, 4655–4658 CrossRef CAS.
- E. P. Ng, J. M. Goupil, A. Vicente, C. Fernandez, R. Retoux, V. Valtchev and S. Mintova, Nucleation and Crystal Growth Features of EMT-Type Zeolite Synthesized from an Organic-Template-Free System, Chem. Mater., 2012, 24, 4758–4765 CrossRef CAS.
- S. Kumar, Z. Wang, R. L. Penn and T. Tsapatsis, A Structural Resolution Cryo-TEM Study of the Early Stages of MFI Growth, J. Am. Chem. Soc., 2008, 130, 17284–17286 CrossRef CAS PubMed.
- N. D. Hould, S. Kumar, M. Tsapatsis, V. Nikolakis and R. F. Lobo, Structure and Collodal Stability of Nanosized Zeolite Beta Precursors, Langmuir, 2010, 26, 1260–1270 CrossRef CAS PubMed.
- S. Mintova, N. H. Olson and T. Bein, Electron microscopy reveals the nucleation mechanism of zeolite Y from precursor colloids, Angew. Chem., Int. Ed., 1999, 38, 3201–3204 CrossRef CAS PubMed.
- S. Mintova, N. H. Olson, J. Senker and T. Bein, Mechanism of the Transformation
of Silica Precursor Solutions into Si-MFI Zeolite, Angew. Chem., Int. Ed., 2002, 41, 2558–2561 CrossRef CAS PubMed.
- C. H. Cheng and D. F. Shantz, 29Si NMR Studies of Zeolite Precursor Solutions, J. Phys. Chem. B, 2006, 110, 313–318 CrossRef CAS PubMed.
- R. W. Thompson and A. Dyer, Nucleation of zeolite NaA crystals in hydrothermal systems, Zeolites, 1985, 5, 302–308 CrossRef CAS.
- J. Warzywoda and R. W. Thompson, Synthesis of zeolite A in the Na/K system and the effect of seeding, Zeolites, 1991, 11, 577–582 CrossRef CAS.
- R. D. Edelman, D. V. Kudalkar, T. Ong, J. Warzywoda and R. W. Thompson, Crystallization phenomena in seeded zeolite syntheses, Zeolites, 1989, 9, 496–502 CrossRef CAS.
- U. Díaz, V. Fornés and A. Corma, On the mechanism of zeolite growing: Crystallization by seeding with delayered zeolites, Microporous Mesoporous Mater., 2006, 90, 73–80 CrossRef.
- M. Shibata, J. Gérard and Z. Gabelica, Rapid synthesis of MFI titanosilicates using in situ seeding method, Microporous Mater., 1997, 12, 141–148 CrossRef CAS.
- Y. Kamimura, S. Tanahashi, K. Itabashi, A. Sugawara, T. Wakihara, A. Shimojima and T. Okubo, Crystallization Behavior of Zeolite Beta in OSDA-Free, Seed-Assisted Synthesis, J. Phys. Chem. C, 2011, 115, 744–750 CrossRef CAS.
- M. C. Lovallo and M. Tsapatsis, Preferentially oriented submicron silicalite membranes, AIChE J., 1996, 11, 3020–3029 CrossRef.
- Z. Lai, M. Tsapatsis and J. P. Nicolich, Siliceous ZSM-5 membranes by secondary growth of b-oriented seed layers, Adv. Funct. Mater., 2004, 7, 716–729 CrossRef.
- M. A. Snyder and M. Tsapatsis, Hierarchical Nanomanufacturing: From Shaped Zeolite Nanoparticles to High-Performance Separation Membranes, Angew. Chem., Int. Ed., 2007, 40, 7560–7573 CrossRef PubMed.
- M. Dargahi, H. Kazemian, M. Soltanieh, S. Rohani and M. Hosseinpour, Rapid high-temperature synthesis of SAPO-34 nanoparticles, Particuology, 2011, 9, 452–457 CrossRef CAS.
- E. Aghaei and M. Haghighi, High temperature synthesis of nanostructured Ce-SAPO-34 catalyst used in conversion of methanol to light olefins: effect of temperature on physicochemical properties and catalytic performance, J. Porous Mater., 2015, 22, 187–200 CrossRef CAS.
- C. Bian, C. Zhang, S. Pan, F. Chen, W. Zhang, X. Meng, S. Maurer, D. Dai, A. Parvulescu, U. Muller and F. Xiao, Generalized High-Temperature Synthesis of Zeolite Catalysts with Unpredictably High Space-Time Yields (STYs), J. Mater. Chem. A, 2017, 2, 2613 RSC.
- X. Gao, C. Y. Yeh and P. Angevine, Mechanistic study of organic template removal from ZSM-5 precursors, Microporous Mesoporous Mater., 2004, 70, 27–35 CrossRef CAS.
- D. S. Belén-Cordero, S. Méndez-González and A. J. Hernández-Maldonado, SBE type cobalt aluminophosphate nanoporous materials: Degradation of the structure-directing agent, Microporous Mesoporous Mater., 2008, 109, 287–297 CrossRef.
- J. de la Zerda, R. Neumann and Y. Sasson, Hofmann decomposition of quaternary ammonium salts under phase-transfer catalytic conditions, J. Chem. Soc., Perkin Trans. 2, 1986, 823–826 RSC.
- L. M. Parker, D. M. Bibby and J. E. Patterson, Thermal decomposition of ZSM-5 and silicalite precursors, Zeolites, 1984, 4, 168–174 CrossRef CAS.
- K. E. Hamilton, E. N. Coker, A. Sacco, A. G. Dixon and R. W. Thompson, The effects of the silica source on the crystallization of zeolite NaX, Zeolites, 1993, 13, 645–653 CrossRef CAS.
- R. M. Mohamed, H. M. Aly, M. F. El-Shahat and I. A. Ibrahim, Effect of the silica sources on the crystallinity of nanosized ZSM-5 zeolite, Microporous Mesoporous Mater., 2005, 79, 7–12 CrossRef CAS.
- Z. Gabelica, N. Blom and E. G. Derouane, Synthesis and characterization of ZSM-5 type zeolites: III. A critical evaluation of the role of alkali and ammonium cations, Appl. Catal., 1983, 5, 227–248 CrossRef CAS.
- M. Isobe, T. Moteki, S. Tanahashi, R. Kimura, Y. Kamimura, K. Itabashi and T. Okubo, Plate-like precursors formed in crystallization process of ferrierite from (Na, K)-aluminosilicate system, Microporous Mesoporous Mater., 2012, 158, 204–208 CrossRef CAS.
- C. S. Cundy, B. M. Lowe and D. M. Sinclair, Direct measurements of the crystal growth rate and nucleation behaviour of silicalite, a zeolitic silica polymorph, J. Cryst. Growth, 1990, 100, 189–202 CrossRef CAS.
- A. Aimable, H. Muhr, C. Gentric, F. Bernard, F. Le Cras and D. Aymes, Continuous hydrothermal synthesis of inorganic nanopowders in supercritical water: towards a better control of the process, Powder Technol., 2009, 190, 99–106 CrossRef CAS.
- C. Tonhauser, A. Natalello, H. Löwe and H. Frey, Microflow Technology in Polymer Synthesis, Macromolecules, 2012, 45, 9551–9570 CrossRef CAS.
- Z. D. Liu, Y. C. Lu, B. D. Yang and G. S. Luo, Controllable preparation of poly (butyl acrylate) by suspension polymerization in a coaxial capillary microreactor, Ind. Eng. Chem. Res., 2011, 50, 11853–11862 CrossRef CAS.
- A. Adamo, R. L. Beingessner, M. Behnam, J. Chen, T. F. Jamison, K. F. Jensen, J.-C. M. Monbaliu, A. S. Myerson, E. M. Revalor, D. R. Snead, T. Stelzer, N. Weeranoppanant, S. Y. Wong and P. Zhang, On-demand continuous-flow production of pharmaceuticals in a compact, reconfigurable system, Science, 2016, 352, 61–66 CrossRef CAS PubMed.
- Z. Liu, Y. Lu, M. Zhang, W. Wan and G. Luo, Controllable preparation of uniform polystyrene nanospheres with premix membrane emulsification, J. Appl. Polym. Sci., 2013, 3, 1202–1211 CrossRef.
- Z. Liu, Y. Lu, B. Yang and G. Luo, Free radical polymerization of butyl acrylate in monodispersed droplets: Comparison between two heating strategies, J. Appl. Polym. Sci., 2013, 1, 628–635 Search PubMed.
- A. Günther and K. F. Jensen, Multiphase microfluidics: from flow characteristics to chemical and materials synthesis, Lab Chip, 2006, 6, 1487–1503 RSC.
- H. Pennemann, P. Watts, S. J. Haswell, V. Hessel and H. Löwe, Benchmarking of Microreactor Applications, Org. Process Res. Dev., 2004, 8, 422–439 CrossRef CAS.
- G. S. Calabrese and S. Pissavini, From batch to continuous flow processing in chemicals manufacturing, AIChE J., 2011, 57, 828–834 CrossRef CAS.
- M. P. Batten, M. Rubio-Martinez, T. Hadley, K.-C. Carey, K. Lim, A. Polyzos and M. R. Hill, Continuous flow production of metal-organic frameworks, Curr. Opin. Chem. Eng., 2015, 8, 55–59 CrossRef.
- R. M. Myers, D. E. Fitzpatrick, R. M. Turner and S. V. Ley, Flow Chemistry Meets Advanced Functional Materials, Chem. – Eur. J., 2014, 20, 12348–12366 CrossRef CAS PubMed.
- M. Faustini, J. Kim, G. Y. Jeong, J. Y. Kim, H. R. Moon, W. S. Ahn and D. P. Kim, Microfluidic Approach toward Continuous and Ultrafast Synthesis of Metal-Organic Framework Crystals and Hetero Structures in Confined Microdroplets, J. Am. Chem. Soc., 2013, 135, 14619–14626 CrossRef CAS PubMed.
- Z. Liu, T. Wakihara, D. Nishioka, K. Oshima, T. Takewaki and T. Okubo, Ultrafast Continuous-Flow Synthesis of Crystalline Microporous Aluminophosphate AlPO4-5, Chem. Mater., 2014, 26, 2327–2331 CrossRef CAS.
- S. A. Khan, A. Günther, M. A. Schmidt and K. F. Jensen, Microfluidic Synthesis of Colloidal Silica, Langmuir, 2004, 20, 8604–8611 CrossRef CAS PubMed.
- K. Robertson, Using flow technologies to direct the synthesis and assembly of materials in solution, Chem. Cent. J., 2017, 11, 4 CrossRef CAS PubMed.
- V. S. Cabeza, S. Kuhn, A. A. Kulkarni and K. F. Jensen, Size-Controlled flow synthesis of gold nanoparticles using a segmented flow microfluidic platform, Langmuir, 2012, 28, 7007–7013 CrossRef PubMed.
- H. T. Davis, Factors determining emulsion type: Hydrophile-lipophile balance and beyond, Colloids Surf., A, 1994, 91, 9–24 CrossRef CAS.
- K. Iwakai, T. Tago, H. Konno, Y. Nakasaka and T. Masuda, Preparation of nano-crystalline MFI zeolite via hydrothermal synthesis in water/surfactant/organic solvent using fumed silica as the Si source, Microporous Mesoporous Mater., 2011, 141, 167–174 CrossRef CAS.
- J. Zhu, Z. Liu, Y. Yonezawa, K. Honda, S. Okada, S. Deguchi, T. Okubo and T. Wakihara, Addressing the viscosity challenge: Ultrafast, stable-flow synthesis of zeolites with an emulsion method, React. Chem. Eng., 2018 10.1039/C8RE00139A.
- Z. Liu, K. Okabe, K. Anand, Y. Yonezawa, J. Zhu, H. Yamada, A. Endo, Y. Yanaba, T. Yoshikawa, K. Ohara, T. Okubo and T. Wakihara, Continuous Flow Synthesis of ZSM-5 Zeolite on the Order of Seconds, Proc. Natl. Acad. Sci. U. S. A., 2016, 50, 14267–14271 CrossRef PubMed.
- A. A. Peterson, F. Vogel, R. P. Lachance, M. Fröling, M. J. Antal and J. W. Tester, Thermochemical biofuel production in hydrothermal media: A review of sub- and supercritical water technologies, Energy Environ. Sci., 2008, 1, 32–65 RSC.
- K. Byrappa, S. Ohara and T. Adschiri, Nanoparticles synthesis using supercritical fluid technology – towards biomedical applications, Adv. Drug Delivery Rev., 2008, 3, 299–327 CrossRef PubMed.
- J. Zhu, Z. Liu, S. Sukenaga, M. Ando, H. Shibata, T. Okubo and T. Wakihara, Ultrafast synthesis of* BEA zeolite without the aid of aging pretreatment, Microporous Mesoporous Mater., 2018, 268, 1–8 CrossRef CAS.
|
This journal is © the Partner Organisations 2019 |
Click here to see how this site uses Cookies. View our privacy policy here.