DOI:
10.1039/C8NA00095F
(Paper)
Nanoscale Adv., 2019,
1, 342-346
Performing a catalysis reaction on filter paper: development of a metal palladium nanoparticle-based catalyst†
Received
21st July 2018
, Accepted 9th September 2018
First published on 10th September 2018
Abstract
We report the polyethylenimine (PEI)-mediated immobilization of palladium nanoparticles (Pd NPs) onto filter paper for catalytic applications. In this work, filter paper was first assembled with PEI via electrostatic interaction, and the PEI-assembled filter paper was then complexed with PdCl42− ions, followed by sodium borohydride reduction to generate Pd NP-immobilized filter paper. Transmission electron microscopy reveals that Pd NPs have a diameter of 3 nm and are capable of being immobilized onto the filter paper. The Pd NP-immobilized filter paper exhibits remarkable catalytic activity and is reusable in the reductive transformation of Cr(VI) to Cr(III) and 4-nitrophenol to 4-aminophenol. The strategy used to develop Pd NP-immobilized filter paper could be adopted to generate other metal NP-immobilized filter papers for other applications such as sensing materials, energy, environmental remediation, and biomedical sciences.
Introduction
Tremendous scientific and technological interest has been raised by metallic nanoparticles (NPs) for catalytic applications1–3 because of their huge surface area and distinctive surface electronic properties.4,5 Palladium NPs (Pd NPs), as one of the representatives, have been paid increasing attention owing to their intriguing properties and high catalytic activity.6,7 Colloidal Pd NPs have been widely used as catalysts,8–12 such as for the reduction of Cr(VI) to Cr(III), and 4-nitrophenol (4-NP) to 4-aminophenol (4-AP). Cr(VI) is a common heavy metal contaminant due to its carcinogenic and mutagenic nature. In addition, it leads to liver damage, pulmonary congestion and causes skin irritation. Because Cr(III) plays an important role in sugar and fat metabolism, the reduction of Cr(VI) to Cr(III) is usually chosen as an effective method for the remediation of Cr(VI)-contaminated water.13,14 4-NP generated from industrial effluent has been considered as the most toxic and refractory pollutant. It has been cited by the U.S. Environmental Protection Agency on the “Priority Pollutant List” due to the potential environmental and public health risks.15 The reduction of 4-NP to 4-AP has been intensively investigated because of the fact that the produced 4-AP is an important intermediate for the manufacture of chemicals and drugs.16 However, the practical catalytic applications of Pd NPs in solutions are limited owing to their colloidal stability issues and recyclability. The general approach to overcome such shortcomings is to immobilize metallic NPs onto different types of solid matrices such as fibers,17–19 clays,20 membranes,21 porous solids,22,23 graphenes24–28 and functionalized nanobeads.29
Commercial filter paper possesses many unique features such as high porosity, good flexibility, robust mechanical durability, and chemical stability.30 Furthermore, filter paper with cellulose as a major component can be easily modified due to the fact that cellulose is an oxygen-rich natural polymer,31 and the porous structure and microfibrils of the filter paper are amenable for metal NPs to be anchored.32 Hence, filter paper has been ideally used to immobilize Au,33,34 Ag,35 Fe,36 Ni,37,38 Cu39 and Pd NPs.40,41 For catalytic applications, Xu et al.42 immobilized Pd NPs onto cellulose fibers, but the process required long impregnation time (72 h) and high reaction temperature (60 °C) to obtain high loading efficiency. Zheng et al.40 fabricated Pd NP-loaded filter paper with a high catalytic efficiency and recyclability by a dip-coating process. However, the method employed to create Pd NPs was rather complicated and one has to use toxic organic solvents under high temperatures.
Previously, we have shown that Au,43,44 Au/Ag,18 Fe,45–48 Fe/Ni,49 and Fe/Pd NPs50 could be synthesized in situ and immobilized onto or within polymer nanofibers formed via electrospinning. We also demonstrated that Pd NPs can be in situ synthesized and embedded within electrospun polyethylenimine (PEI)/polyvinyl alcohol (PVA) nanofibers.51 In addition, branched PEI was adopted as either a template or stabilizer to prepare metal NPs.52–54 These earlier investigations associated with electrospun nanofibers immobilized with metal NPs prompted us to hypothesize that Pd NPs could also be immobilized onto filter paper through the assembly of PEI and the PEI-mediated in situ synthesis method.
In this paper, we present an in situ method to immobilize Pd NPs onto filter paper for subsequent applications as a catalyst. A piece of filter paper was first soaked into a PEI aqueous solution, followed by rinsing with water. Then, the PEI-assembled filter paper was dipped into a K2PdCl4 aqueous solution, rinsed with water, and the PdCl42− adsorbed onto the PEI-modified filter paper was reduced to Pd NPs by sodium borohydride (NaBH4). The generated filter paper containing Pd NPs was characterized via different technologies. We then tested the catalytic performance and reusability of the formed Pd NP-immobilized filter paper through reactions transforming Cr(VI) to Cr(III) (Scheme 1) and converting 4-NP to 4-AP. According to a thorough literature exploration, currently there are no similar studies using PEI to form Pd NP-immobilized filter paper for catalytic applications.
 |
| Scheme 1 Schematic illustration of the immobilization of Pd NPs onto filter paper for catalytic applications. | |
Experimental
Preparation of the Pd NP-immobilized filter paper
The process shown in Scheme 1 is the process of fabricating the Pd NP-containing filter paper. First, a piece of filter paper (1 × 2 cm2, 18 mg and pore size: 15–20 μm) was dipped into a PEI solution (20 mgmL−1 and 5 mL in water) for 5 min and rinsed with water 3 times to eliminate excess PEI. Then the PEI-modified filter paper was dipped into a K2PdCl4 solution (13 mgmL−1, 5 mL in water) for 5 min and was thoroughly rinsed. The filter paper was then immersed into a NaBH4 solution (8 mgmL−1, 5 mL in water) for 10 min to reduce the complexed PdCl42+ ions. Finally, the formed filter paper containing Pd NPs was washed with copious water, vacuum dried at room temperature, and stored in a desiccator.
Catalysis experiments
We performed the transformation of Cr(VI) to Cr(III)38,42 and 4-NP to 4-AP44 to assess the efficiency and reusability of the Pd NP-immobilized filter paper as a catalyst.51,55 The details are described in the ESI.†
Results and discussion
Preparation and characterization of the filter paper containing the immobilized Pd NPs
In this study, we immobilized Pd NPs onto the surface of the filter paper via the PEI-mediated in situ reduction of PdCl42− ions. First, PEI was adsorbed onto the filter paper through electrostatic interaction, and then PdCl42− was adsorbed onto PEI by coordination interaction. Finally, PdCl42− was reduced to form Pd NPs using NaBH4. The filter paper became quite brown after the formation of Pd NPs (Fig. S1, ESI†), verifying the success of the formation of Pd NPs.
The morphology of the Pd NP-loaded filter paper was then visualized by SEM (Fig. 1). As opposed to the Pd-free filter paper, the Pd NP-loaded filter paper shows some particles on the surface of cellulose fibers, indicating the success of the immobilization of Pd NPs onto the filter paper. Further, it seemed that the Pd NPs were well dispersed onto the cellulose fiber surface. The immobilization of the Pd NPs onto the filter paper was also confirmed by EDS (Fig. S2, ESI†), where the signal of Pd is apparent.
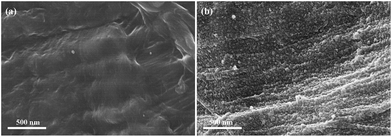 |
| Fig. 1 SEM images of the filter paper without (a) and with (b) the immobilized Pd NPs. | |
TEM was employed to observe the distribution of Pd NPs on the filter paper. From the cross-sectional TEM image (Fig. 2a), it can be observed that the Pd NPs are dispersed along the cellulose fiber surface of the filter paper. The Pd NPs exhibit an elliptical shape with a quite narrow size distribution (Fig. 2b). The average diameter of the Pd NPs was measured to be 3.0 ± 0.9 nm (Fig. 2c), which is smaller than that of Pd NPs (6.2 ± 1.5 nm) formed by in situ reduction.56 This suggests that PEI assembled onto the filter paper is capable of limiting the growth of Pd NPs.
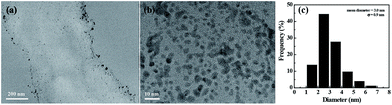 |
| Fig. 2 Cross-sectional TEM image (a) and high-resolution TEM image (b) of the Pd NP-loaded filter paper. (c) Diameter distribution histogram of the formed Pd NPs. | |
TGA was adopted to quantify the percentage of Pd NPs loaded onto the filter paper (Fig. S3, ESI†). The slight initial loss of weight for the filter paper without and with Pd NPs is likely to be attributed to the moisture loss in the samples, while the weight loss of the Pd NP-loaded filter paper is associated with the decomposition of the filter paper and PEI in the region of 300–800 °C. Compared with the filter paper without the loaded Pd NPs (Fig. S3, ESI,†curve a), the percentage of Pd NPs loaded onto the filter paper was estimated to be 1.1% (Fig. S3, ESI,†curve b). To further quantify the Pd loading percentage onto the filter paper, ICP-OES analysis was performed. The Pd concentration tested by ICP-OES was 12.5052 ppm, and the Pd loading percentage was calculated to be 1.0%, corroborating the TGA results.
Catalytic transformation of Cr(VI) to Cr(III)
The catalytic activity of the Pd NP-immobilized filter paper was estimated by converting Cr(VI) to Cr(III). The catalytic mechanism of Pd NPs can be explained as follows: (1) formic acid is first adsorbed onto the surface of Pd NPs, and then decomposed to form H2 and CO2; (2) Cr(VI) is reduced to Cr(III) by the formed H2 adsorbed onto the surface of Pd NPs.57 The amine groups on the surface of Pd NPs favor the decomposition of the O–H bond in formic acid dehydrogenation due to the amine group-rendered basic environment.58,59 We confirmed the catalytic activity of the filter paper immobilized with Pd NPs first by the gradual color change of the reaction solution. The color fading from yellow to colorless within 28 min showcased the effective transformation of Cr(VI) to Cr(III) (Fig. S4b, ESI†). In contrast, the Pd-free filter paper treated with K2Cr2O7 solution did not display any apparent color change (Fig. S4a, ESI†). In addition, a decrease in the characteristic absorbance of Cr2O72− at 350 nm with time (Fig. 3b) also validated the process of the reduction reaction. The catalytic activity of the Pd NP-immobilized filter paper was calculated to be 98% at 28 min. In comparison, the catalytic efficiency of Pd-activated carbon was 91.6% at 12 min and 94.2% at 28 min (Fig. 4). This means that Pd-activated carbon could catalyze the conversion of Cr(VI) to Cr(III) quickly, but the catalytic efficiency at 28 min was slightly lower than that of the Pd-immobilized filter paper. In addition, the biggest drawback of Pd-activated carbon is that it is difficult to recover it for the next round of catalytic reactions. In contrast, the Pd NP-immobilized filter paper can be easily recovered and used for at least 3 times (see below).
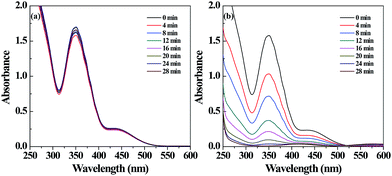 |
| Fig. 3 UV-vis spectra of the Cr(VI) solution treated with filter paper without (a) and with (b) Pd NPs loaded at different time intervals. | |
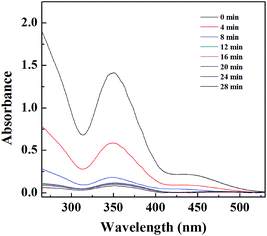 |
| Fig. 4 UV-vis spectra of the Cr(VI) solution treated with Pd-activated carbon at different time intervals. | |
To further prove the existence of Cr(III) in the final reaction solution, we added excess sodium hydroxide solution to the reaction mixture. The colorless solution quickly changed to green, implying the generation of hexahydroxochromate(III).55,60 In the control experiment, the Pd-free filter paper was used to catalyze the transformation of Cr(VI) to Cr(III). The absorption of Cr(VI) at 350 nm showed just a little change over 28 min (Fig. 3a). These data further supported that the powerful catalytic activity was associated with the Pd NPs immobilized onto the filter paper. The catalytic activity of the Pd NP-loaded filter paper may not be comparable to that of the Pd NPs loaded within the electrospun PAA/PVA nanofibrous mats51 due to the loading capacity and fiber structure of the materials. However, the adopted materials of filter paper and the PEI polymer are sustainable and quite cost-effective, and the immobilization procedure is quite simple. Therefore, the prepared Pd NP-loaded filter paper may be rather adaptable to industrial use.
The reusability of a catalyst is crucial for practical applications, especially for noble metals. To test the reusability of the Pd NP-immobilized filter paper, the filter paper was rinsed with water and dried for the next round of reaction. By plotting the remaining fraction of Cr(VI) versus reaction time, we compared the catalytic activity of the filter paper containing Pd NPs. Clearly, more than 98% of Cr(VI) can be converted to Cr(III) within 28 min for three reaction cycles (Fig. 5), validating the remarkable reusability of the Pd NP-immobilized filter paper. It is worth mentioning that the Pd NPs loaded onto the filter paper were stable and were not released during the reaction. This was proven by ICP-OES analysis, showing that no Pd content was detectable in the reaction mixture even after 3 cycles of catalytic reaction.
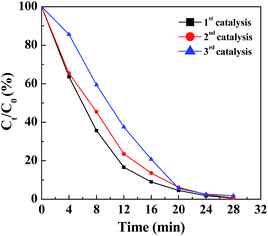 |
| Fig. 5 Remaining fraction of Cr(VI) as a function of time in the presence of the Pd NP-loaded filter paper for the first, second and third cycle of catalytic reaction. | |
Catalytic conversion of 4-NP to 4-AP
The catalytic property of the filter paper containing Pd NPs was also tested by a model reaction converting 4-NP to 4-AP. By immersing ordinary Pd-free filter paper into the reaction mixture, we did not see the color change of 4-NP solution (Fig. S5a, ESI†), and the absorption peak of 4-NP at 400 nm just slightly decreased within 36 min (Fig. 6a). This is likely attributed to the intrinsic physical adsorption of 4-NP onto the filter paper. It demonstrates that the Pd-free filter paper has no catalytic activity. In contrast, when the Pd NP-loaded filter paper was used, gradual color fading of the 4-NP solution occurred (Fig. S5b, ESI†). This can also be reflected by the gradual decrease of the absorbance of 4-NP at 400 nm and gradual emergence of a new peak at 300 nm, suggesting the formation of 4-AP (Fig. 6b). Around 95% of 4-NP can be converted to 4-AP within 10 min, implying that the Pd NP-loaded filter paper can efficiently catalyze the reduction reaction.
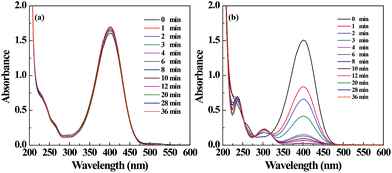 |
| Fig. 6 UV-vis spectra of the 4-NP solution treated with the filter paper without (a) and with (b) Pd NPs loaded at different time intervals. | |
Although colloidal Pd NPs have a high catalytic ability to catalyze the conversion of 4-NP to 4-AP, the colloidal Pd NPs suffer from recycling difficulty for further use. We also tested the reusability of the Pd NP-loaded filter paper. We can see that more than 98% of 4-NP is transformed to 4-AP within 36 min even at the fourth cycle of the catalytic reaction, demonstrating the reusability of the Pd NP paper (Fig. S6, ESI†). The slightly decreased catalytic activity of the Pd NP paper is likely owing to the swelling of the cellulose fibers during the reaction, thereby slightly affecting the access of 4-NP to the Pd NPs loaded inside the pores of the cellulose fibrils. This can also be applied to explain the slight decrease of the catalytic activity in the conversion of Cr(VI) to Cr(III) during reuses. In addition, the Pd NPs loaded onto the filter paper showed no appreciable release into the reaction solution, which can be further confirmed by ICP-OES analysis, where no Pd content could be detected even after 4 cycles of reaction.
Conclusions
We present a convenient, time-saving, cost-effective, and sustainable approach to immobilizing Pd NPs onto filter paper via PEI-mediated in situ reduction of PdCl42−. The porous filter paper can be immobilized with Pd NPs with a Pd core size of 3.0 nm and Pd loading percentage of 1.1%. The Pd NP-loaded filter paper can be adopted to catalyze the conversion of Cr(VI) to Cr(III) with an efficiency of 98% within 28 min and 4-NP to 4-AP with an efficiency of 98% within 36 min with an excellent reusability. Such a strategy to immobilize Pd NPs onto filter paper may be applicable to immobilize other metal or metal oxide NPs onto filter paper for a range of applications.
Conflicts of interest
There are no conflicts to declare.
Acknowledgements
Financial support from the Fundamental Research Funds for the Central Universities (M. Shen and X. Shi), “111 Project” (B07024), and the Science and Technology Commission of Shanghai Municipality (15520711400 and 17540712000) are greatly acknowledged. Y. Zhao thanks the Foundation of Zhejiang Educational Committee (No. Y201636691) and the Science Foundation of Zhejiang Sci-Tech University (ZSTU) under Grant No. 16012089-Y. Daniel Shi is a student from the International Division of No. 2 High School of East China Normal University working during the summer.
Notes and references
- P. Herves, M. Perez-Lorenzo, L. M. Liz-Marzan, J. Dzubiella, Y. Lu and M. Ballauff, Chem. Soc. Rev., 2012, 41, 5577–5587 RSC.
- K. An and G. A. Somorjai, Catal. Lett., 2015, 145, 233–248 CrossRef CAS.
- W. H. Eisa, A. M. Abdelgawad and O. J. Rojas, ACS Sustainable Chem. Eng., 2018, 6, 3974–3983 CrossRef CAS.
- M. Pelton, J. Aizpurua and G. Bryant, Laser Photonics Rev., 2008, 2, 136–159 CrossRef CAS.
- H. J. Yin, S. L. Zhao, K. Zhao, A. Muqsit, H. J. Tang, L. Chang, H. J. Zhao, Y. Gao and Z. Y. Tang, Nat. Commun., 2015, 6, 6430 CrossRef CAS PubMed.
- F. Wang, C. H. Li, L. D. Sun, C. H. Xu, J. F. Wang, J. C. Yu and C. H. Yan, Angew. Chem., Int. Ed., 2012, 51, 4872–4876 CrossRef CAS PubMed.
- M. T. Zhao, K. Deng, L. C. He, Y. Liu, G. D. Li, H. J. Zhao and Z. Y. Tang, J. Am. Chem. Soc., 2014, 136, 1738–1741 CrossRef CAS PubMed.
- A. Balanta, C. Godard and C. Claver, Chem. Soc. Rev., 2011, 40, 4973–4985 RSC.
- W. X. Tu, K. J. Li, X. H. Shu and W. W. Yu, J. Nanopart. Res., 2013, 15, 1593–1602 CrossRef.
- J. Gu, C. S. Hu, W. W. Zhang and A. Dichiara, Appl. Catal., B, 2018, 237, 482–490 CrossRef CAS.
- M. Rezayat, R. K. Blundell, J. E. Camp, D. A. Walsh and W. Thielemans, ACS Sustainable Chem. Eng., 2014, 2, 1241–1250 CrossRef CAS.
- X. D. Wu, C. H. Lu, W. Zhang, G. P. Yuan, R. Xiong and X. X. Zhang, J. Mater. Chem. A, 2013, 1, 8645–8652 RSC.
- P. Miretzky and A. F. Cirelli, J. Hazard. Mater., 2010, 180, 1–19 CrossRef CAS PubMed.
- W. Liu, J. Ni and X. Yin, Water Res., 2014, 53, 12–25 CrossRef CAS PubMed.
- K. B. Narayanan and N. Sakthivel, J. Hazard. Mater., 2011, 189, 519–525 CrossRef CAS PubMed.
- J. Li, C. Y. Liu and Y. Liu, J. Mater. Chem., 2012, 22, 8426–8430 RSC.
- H. C. Mu, C. P. Li, J. Bai and W. Y. Sun, J. Mol. Struct., 2018, 1165, 90–100 CrossRef CAS.
- D. M. Hu, Y. C. Xiao, H. Liu, H. Wang, J. C. Li, B. Q. Zhou, P. C. Liu, M. W. Shen and X. Y. Shi, Colloids Surf., A, 2018, 552, 9–15 CrossRef CAS.
- Z. Y. Xiang, Y. Chen, Q. G. Liu and F. C. Lu, Green Chem., 2018, 20, 1085–1094 RSC.
- Y. Ma and G. K. Zhang, Chem. Eng. J., 2016, 288, 70–78 CrossRef CAS.
- E. Hariprasad and T. P. Radhakrishnan, ACS Catal., 2012, 2, 1179–1186 CrossRef CAS.
- S. Y. Oh, J. Kim and Y. Kim, Mater. Lett., 2015, 154, 60–63 CrossRef CAS.
- E. Petala, K. Dimos, A. Douvalis, T. Bakas, J. Tucek, R. Zboril and M. A. Karakassides, J. Hazard. Mater., 2013, 261, 295–306 CrossRef CAS PubMed.
- W. H. Dong, S. S. Cheng, C. Feng, N. Z. Shang, S. T. Gao and C. Wang, Catal. Commun., 2017, 90, 70–74 CrossRef CAS.
- S. Navalon, A. Dhakshinamoorthy, M. Alvaro and H. Garcia, Coord. Chem. Rev., 2016, 312, 99–148 CrossRef CAS.
- L. Shang, T. Bian, B. Zhang, D. Zhang, L. Z. Wu, C. H. Tung, Y. Yin and T. Zhang, Angew. Chem., 2014, 53, 250–254 CrossRef CAS PubMed.
- H. J. Yin, H. J. Tang, D. Wang, Y. Gao and Z. Y. Tang, ACS Nano, 2012, 6, 8288–8297 CrossRef CAS PubMed.
- H. J. Yin, S. L. Zhao, J. W. Wan, H. J. Tang, L. Chang, L. C. He, H. J. Zhao, Y. Gao and Z. Y. Tang, Adv. Mater., 2013, 25, 6270–6276 CrossRef CAS PubMed.
- R. Linhardt, Q. M. Kainz, R. N. Grass, W. J. Stark and O. Reiser, RSC Adv., 2014, 4, 8541–8549 RSC.
- E. W. Nery and L. T. Kubota, Anal. Bioanal. Chem., 2013, 405, 7573–7595 CrossRef CAS PubMed.
- Y. Habibi, L. A. Lucia and O. J. Rojas, Chem. Rev., 2010, 110, 3479–3500 CrossRef CAS PubMed.
- L. Polavarapu and L. M. Liz-Marzan, Phys. Chem. Chem. Phys., 2013, 15, 5288–5300 RSC.
- T. Niu, J. B. Xu, W. Xiao and J. G. Huang, RSC Adv., 2014, 4, 4901–4904 RSC.
- G. C. Zheng, L. Polavarapu, L. M. Liz-Marzan, I. Pastoriza-Santos and J. Perez-Juste, Chem. Commun., 2015, 51, 4572–4575 RSC.
- S. Ashraf, R. Saifur, F. Sher, Z. M. Khalid, M. Mehmood and I. Hussain, Cellulose, 2014, 21, 395–405 CrossRef CAS.
- K. K. R. Datta, E. Petala, K. J. Datta, J. A. Perman, J. Tucek, P. Bartak, M. Otyepka, G. Zoppellaro and R. Zboril, Chem. Commun., 2014, 50, 15673–15676 RSC.
- T. Kamal, S. B. Khan and A. M. Asiri, Environ. Pollut., 2016, 218, 625–633 CrossRef CAS PubMed.
- G. Bodelon, S. Mourdikoudis, L. Yate, I. Pastoriza-Santos, J. Perez-Juste and L. M. Liz-Marzan, ACS Nano, 2014, 8, 6221–6231 CrossRef CAS PubMed.
- T. Kamal, S. B. Khan and A. M. Asiri, Cellulose, 2016, 23, 1911–1923 CrossRef CAS.
- G. C. Zheng, K. Kaefer, S. Mourdikoudis, L. Polavarapu, B. Vaz, S. E. Cartmell, A. Bouleghlimat, N. J. Buurma, L. Yate, A. R. de Lera, L. M. Liz-Marzan, I. Pastoriza-Santos and J. Perez-Juste, J. Phys. Chem. Lett., 2014, 6, 230–238 CrossRef PubMed.
- T. Nishikata, H. Tsutsumi, L. Gao, K. Kojima, K. Chikama and H. Nagashima, Adv. Synth. Catal., 2014, 356, 951–960 CrossRef CAS.
- Y. Xu, L. Zhang and Y. C. Cui, J. Appl. Polym. Sci., 2008, 110, 2996–3000 CrossRef CAS.
- X. fang, H. Ma, S. L. Xiao, M. W. Shen, R. Guo, X. Y. Cao and X. Y. Shi, J. Mater. Chem., 2011, 21, 4493–4501 RSC.
- D. M. Hu, Y. P. Huang, H. Liu, H. Wang, S. G. Wang, M. W. Shen, M. F. Zhu and X. Y. Shi, J. Mater. Chem. A, 2014, 2, 2323–2332 RSC.
- S. L. Xiao, M. W. Shen, R. Guo, Q. G. Huang, S. Y. Wang and X. Y. Shi, J. Mater. Chem., 2010, 20, 5700–5708 RSC.
- S. L. Xiao, H. Ma, M. W. Shen, S. Y. Wang, Q. G. Huang and X. Y. Shi, Colloids Surf., A, 2011, 381, 48–54 CrossRef CAS.
- S. L. Xiao, M. W. Shen, R. Guo, S. Y. Wang and X. Y. Shi, J. Phys. Chem. C, 2009, 113, 18062–18068 CrossRef CAS.
- S. L. Xiao, S. Q. Wu, M. W. Shen, R. Guo, Q. G. Huang, S. Y. Wang and X. Y. Shi, ACS Appl. Mater. Interfaces, 2009, 1, 2848–2855 CrossRef CAS PubMed.
- H. Ma, Y. P. Huang, M. W. Shen, D. M. Hu, H. Yang, M. F. Zhu, S. P. Yang and X. Y. Shi, RSC Adv., 2013, 3, 6455–6465 RSC.
- H. Ma, Y. P. Huang, M. W. Shen, R. Guo, X. Y. Cao and X. Y. Shi, J. Hazard. Mater., 2012, 211–212, 349–356 CrossRef CAS PubMed.
- Y. P. Huang, H. Ma, S. G. Wang, M. W. Shen, R. Guo, X. Y. Cao, M. F. Zhu and X. Y. Shi, ACS Appl. Mater. Inter., 2012, 4, 3054–3061 CrossRef CAS PubMed.
- B. Q. Zhou, M. W. Shen, I. Bányai and X. Y. Shi, Analyst, 2016, 141, 5390–5397 RSC.
- B. Q. Zhou, J. Yang, C. Peng, J. Z. Zhu, Y. Q. Tang, X. Y. Zhu, M. W. Shen, G. X. Zhang and X. Y. Shi, Colloids Surf., B, 2016, 140, 489–496 CrossRef CAS PubMed.
- B. Q. Zhou, L. F. Zheng, C. Peng, D. Li, J. C. Li, S. H. Wen, M. W. Shen, G. X. Zhang and X. Y. Shi, ACS Appl. Mater. Interfaces, 2014, 6, 17190–17199 CrossRef CAS PubMed.
- M. A. Omole, I. O. K'Owino and O. A. Sadik, Appl. Catal., B, 2007, 76, 158–167 CrossRef CAS.
- J. H. He, T. Kunitake and A. Nakao, Chem. Mater., 2003, 15, 4401–4406 CrossRef CAS.
- G. T. Fu, X. Jiang, R. Wu, S. H. Wei, D. M. Sun, Y. W. Tang, T. H. Lu and Y. Chen, ACS Appl. Mater. Interfaces, 2014, 6, 22790–22795 CrossRef CAS PubMed.
- M. Yadav, T. Akita, N. Tsumori and Q. Xu, J. Mater. Chem., 2012, 22, 12582–12586 RSC.
- K. Mori, M. Dojo and H. Yamashita, ACS Catal., 2013, 3, 1114–1119 CrossRef CAS.
- A. Dandapat, D. Jana and G. De, Appl. Catal., A, 2011, 396, 34–39 CrossRef CAS.
Footnote |
† Electronic supplementary information (ESI) available. See DOI: 10.1039/c8na00095f |
|
This journal is © The Royal Society of Chemistry 2019 |
Click here to see how this site uses Cookies. View our privacy policy here.