DOI:
10.1039/C8GC03304H
(Communication)
Green Chem., 2019,
21, 785-791
Isolation of phenolic monomers from kraft lignin using a magnetically recyclable TEMPO nanocatalyst†
Received
26th October 2018
, Accepted 10th January 2019
First published on 4th February 2019
Abstract
Three kraft lignins were subjected to oxidative depolymerization using a magnetically separable and reusable nitroxyl radical catalyst under greener conditions without the use of an alkali. Phenolic monomers and residual polymeric lignin were characterized to identify their potential end use. Vanillin was selectively isolated from one of the kraft lignins in high yield extending an opportunity of sustainably producing an aromatic platform chemical from lignin.
Introduction
A future bioeconomy will utilize platform chemicals sourced from biomass to create functional products and this action mirrors one central tenet of green chemistry.1,2 This alternative paradigm to a petroleum society will help to decarbonize lifestyles through adoption of renewable carbon in a variety of products rather than just fuels, with the lofty aim to help mitigate climate change. For example, vanillin has been suggested as a platform chemical that can be transformed into materials such as polyethylene terephthalate analogs useful in plastic containers to carpets and other textiles.3,4 While much research has been performed for second generation biorefineries producing cellulosic ethanol, a potential cornerstone of a bioeconomy, cellulosic ethanol targets have not been met to date.5 In part, biofuels have a poor valorization factor compared to platform chemicals such as vanillin and the environmental benefits have not been realized due to difficulties associated with scaling the technologies. Moreover, it is not clear whether there can be a return on investment of cellulosic ethanol biorefineries, prior to mass electrification of vehicle fleets occurring within the next decade. This issue ushers the existing pulp and paper industry to lead the crucial transformation towards the production of renewable feedstocks for a global bioeconomy. However, mills have faced economic hurdles and many of them have closed down in the last decade. In part, like second generation biorefineries, pulp and paper companies struggle to deal with a quarter to a third of the biomass which is composed of lignin.6 The majority of chemical pulps are produced from the kraft process, which uses sodium sulfate to delignify wood chips, breaking native C–O ether linkages in lignin and subsequently leaching its fragments into the alkaline pulping liquor. In this process, lignin gets modified with elemental sulphur and further gets repolymerized into a complicated macromolecule with considerable heterogeneity.7 This heterogeneity limits usage of lignin to its fuel value during chemical recovery and recycling of caustics. Moreover, this aromatic polymeric material plays an important role in the production of platform chemicals in bioeconomy, yet there are limited economic compelling reasons to work with lignin.8–10
In North America, three different kraft lignins are available in semi-commercial quantities from three mills that all use gymnosperm species, which contain more than 90% guaiacyl lignin derived from the dehydrogenative polymerization of coniferyl alcohol.11,12 There are oxidative routes to isolate phenolic aldehydes from this material.13–15 However, the technologies employed require consumption of a large amount of alkali and high temperature reactions with the pathway of vanillin cleavage.16,17 Deriving vanillin from biomass has low yields with large inputs of energy and material.18,19 Hence, novel catalytic oxidative depolymerization techniques play a crucial role in developing greener biobased feedstock processes.20–24 2,2,6,6-Tetramethylpiperidine-1-oxyl (TEMPO) has been used as a regioselective catalyst for oxidation of primary alcohol groups in cellulose pulp fibres and even thermomechanical pulp.25,26 However, using it in soluble form for deriving phenolic monomers from lignin through oxidative chemistry is cumbersome due to the undue usage of solvents and inability to reuse the catalyst.27,28 We had previously anchored 0.3 mmol g−1 TEMPO on magnetic nanoparticles and used it successfully to oxidize pulp fibres.29 In this work, we report the use of the same catalyst designated as Fe@MagTEMPO for the oxidative depolymerization of lignin to obtain a higher yield of vanillin with a lower calculated E factor than previously reported in the literature (Scheme 1 and Table S1†). Overall, the isolation of phenolics utilizing oxidative methods has been recently reviewed;15,30,31 it is worth noting germane studies listed in Table S1.† Recently, 17.3% vanillin was isolated directly from pine sawdust using a novel LaMn0.8Cu0.2O3 catalyst, while the upper vanillin isolation level from softwood kraft lignin was reported to be 12.4% by mass. In contrast, industrial production of softwood lignosulfonates was reported to be near 5.9%.
 |
| Scheme 1 Oxidative depolymerization of kraft lignin using the Fe@MagTEMPO catalyst. | |
The Fe@MagTEMPO catalyst has free amine groups (ca. 0.12 mmol g−1) attached to magnetic nanoparticles that were observed to provide a local alkaline environment to abstract protons from phenolic hydroxyl in lignin, eliminating the use of an alkali during oxidative depolymerization (Fig. S1†). This aspect reduces the waste generation by over 98% compared to the traditional methods of isolating vanillin from kraft liquor that were infamous for generating 160 kg alkali waste per kilogram of vanillin.32–34 The presence of amine groups on the Fe@MagTEMPO catalyst was confirmed by measuring the change in the zeta potential with respect to pH and comparing the variation in the zeta potential and isoelectric point with previous reports on similar nanoparticles (Fig. S2†).35–37 TEMPO has an acute aquatic toxicity and being a free radical molecule, can build up in an environment if allowed into waste water streams after oxidation. Having anchored TEMPO makes this catalyst reusable and eliminates the toxicity and accumulation issues. The inherent greener chemistry of deriving phenolic monomers from lignin using a reusable catalyst was complemented with greener reaction conditions of room temperature, atmospheric pressure, use of water as the solvent and neutral pH. Sodium hypochlorite in combination with sodium bromide, to increase reaction rates, was used as the primary oxidant, and when TEMPO is recycled, it creates a greener oxidation system that produces only benign sodium chloride as the residue.38–40
Results and discussion
Oxidative depolymerization of kraft lignin
Three kraft lignins with different processing history were primarily investigated to produce phenolic monomers. Indulin AT from West Rock, BioChoice from the Lignoboost process of Domtar and Lignoforce lignin from West Fraser showed a significant variation in the phenolic monomer yield and selectivity towards vanillin when subjected to oxidative depolymerization under the same processing conditions. Indulin AT yielded 22.5% phenolic monomers, however, Lignoboost and Lignoforce resulted in 8.5% and 2.5% yield of monomers respectively (Fig. 1a). This result is suggested to arise from a more condensed structure of the latter two-kraft lignins and to the fact that black liquor is subjected to oxidation in the Lignoforce process. Clearly, both pulping conditions and recovery options play a critical role in the ability to valorize lignin.41 Lignoboost interestingly yielded more 5-chlorovanillin than vanillin as a result of the oxidation process (Fig. S3†). Since Indulin AT showed the best oxidative depolymerisation performance, it was used for studying the effect of catalyst type, time, temperature, oxidant loading and catalyst reusability on oxidative depolymerization. Its fractionated versions viz. acetone soluble Indulin AT (ASKL), acetone insoluble Indulin AT (AIKL) and acid washed Indulin AT were also studied. ASKL showed superior depolymerization performance with 28.5% yield of phenolic monomers and 78% vanillin selectivity based on GCMS analysis. Vanillin concentration in a monomer mixture was also measured using FID providing 21% yield for this particular lignin (Fig. S4†). ASKL is reported to have a higher phenolic content and a highly modified structure that may have led to the increase in yield and vanillin selectivity.11,42 Further, AIKL that has a relatively greater amount of β-O-4 linkages showed limited production of vanillin relative to ASKL. Along similar lines, milled wood lignin from pine, subjected to significantly less processing than kraft lignin, was also depolymerized under the same conditions with Fe@MagTEMPO. The “native-like” lignin yielded chlorinated aliphatic compounds and chlorinated phenolic compounds indicating that β-O-4 linkages are detrimental to the selectivity of unsubstituted vanillin through this oxidative depolymerization pathway resulting in chlorinated derivatives (Fig. S3†). These observations demonstrated that the lignin structure after processing and recovery greatly influenced the production of high value monomers. Hence, not all softwood kraft lignins will depolymerize into the same monomers and industrial lignin recovery methodologies must be tailored to target specific monomers. A non-catalytic “control” reaction was conducted in the presence of alkali at pH 10 with 5 mmol g−1lignin loading of sodium hypochlorite as the primary oxidant that yielded 3.5% monomers with 51% vanillin selectivity indicating the significance of the Fe@MagTEMPO catalyst in oxidative depolymerization. Further, a solid nanocatalyst with TEMPO anchored on magnetic nanoparticles is commercially available from Sigma Aldrich and is marketed as TurboBeads.43 It was able to generate vanillin with similar selectivity to Fe@MagTEMPO but with a lower overall phenolic monomer yield of 6.5%. This can be attributed to the larger size of cobalt nanoparticles (∼50 nm), no free amine groups anchored to nanoparticles and a lower loading of 0.1 mmol g−1 TEMPO on TurboBeads. A control experiment with homogeneous TEMPO and NaClO at neutral pH only yielded 6.5% phenolic monomers, which was similar to the Turbobeads. Further, magnetic nanoparticles with only amine groups (0.42–0.46 mmol g−1) anchored on them were used as the catalyst designated as Fe@MagBasic. This approach with the addition of sodium hypochlorite yielded 10% phenolic monomers with 70% vanillin selectivity (Fig. 1b). After this encouraging result, we tried to conduct oxidative depolymerization using the Fe@MagTEMPO catalyst without a primary oxidant at neutral pH. However, when no progress in the reaction was observed, the pH was increased to 10 using 0.5 M sodium hydroxide and a yield of 9.5% phenolic monomers with 47% vanillin selectivity was observed after 4 h (Table S2†). Surprisingly, the use of 2.5 mmol g−1 sodium hypochlorite as the oxidant at neutral pH resulted in similar yield and selectivity values to the experiment at pH 10 without an oxidant. The result from these experiments and from the use of the Fe@MagBasic catalyst suggested that amine groups on Fe@MagTEMPO create a local alkaline environment to abstract protons from oxidized lignin thereby eliminating the use of an alkali. Reaction time had a significant effect on both the yield of monomers and selectivity towards vanillin. A maximum yield of phenolic monomers was observed at 4 h beyond which the yield and vanillin selectivity dropped due to the potential for further oxidation or substitution of vanillin and free radical repolymerization of other phenolic products. Though the drop in yield after 12 h was less than half, the drop in vanillin selectivity was significant (Fig. 1c). Temperature too seemed to have an optimum point as did the reaction time to obtain the highest yield of phenolic monomers and selectivity for vanillin as observed in previous studies.44,45 The oxidative depolymerization was possible even at a low temperature of 5 °C. However, the yield and selectivity increased significantly at 25 °C. Beyond this temperature, it appeared that the extra activation energy helped repolymerization of monomers and therefore decreased both the monomer yield and vanillin selectivity (Fig. 1d). Increasing the sodium hypochlorite loading to 5 mmol g−1 yielded 22.5% phenolic monomers with 63.5% vanillin selectivity (Fig. 1e). The increase in catalyst loading increased the phenolic monomer yield up to the loading of 0.175 mg cm−3. However, there was no significant effect even when the catalyst loading was doubled beyond that value indicating a diffusion controlled reaction (Fig. S5†). The catalyst reuse was studied over five cycles (Fig. 1f). The catalyst was recovered using a magnet at the end of each reaction and reused without any regeneration or makeup for the next reaction cycle. There was a slight decrease in monomer yield and selectivity values as a small amount of the catalyst was lost during recovery over the five cycles. The weight of the catalyst at the start of the first cycle was 35 mg and the weight of the recovered catalyst at the end of the fifth reuse was 27 mg. The loss in catalyst mass is suggested to occur over the recovery methods. Hence, the activity (Fig. 1f) and the structural fidelity of the catalyst were retained suggesting that no leaching of active TEMPO or silica coating occurred from the nanoparticle surface (Fig. S6†). The Fe@MagTEMPO catalyst has been found to be stable even at 65 °C in a previous study.29 Further, the reaction mixture (4 h, 25 °C, 5 mmol g−1 NaClO), the reaction mixture without the Fe@MagTEMPO catalyst (same conditions), and the reaction mixture with homogeneous TEMPO (same conditions) were analyzed with ICP analysis; no statistical differences were detected for the concentration of Fe and Si in the mixtures amongst the three samples (Table S3†).
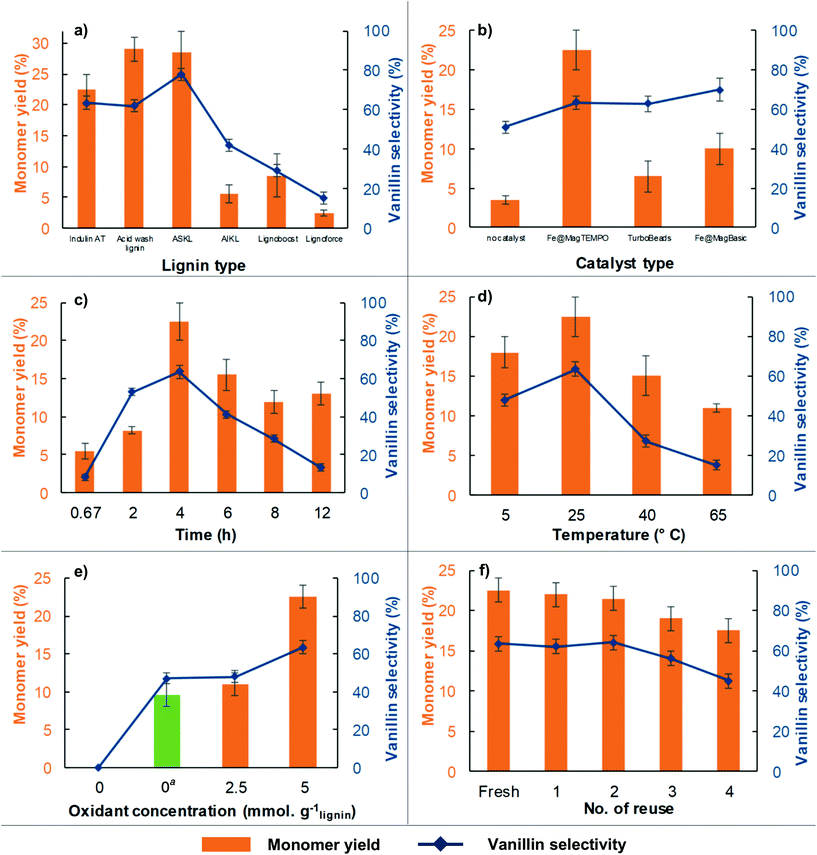 |
| Fig. 1 Effect of different parameters on vanillin selectivity and phenolic monomer yield during the oxidative depolymerization of kraft lignin using the Fe@MagTEMPO catalyst. Typical reaction conditions: 1% (w/w) Indulin AT, 200 cm3 water as the solvent, 0.175 mg cm−3 Fe@MagTEMPO, 0.2 mmol NaBr (fixed for all experiments), 5 mmol g−1 NaClO, 25 °C. The phenolic monomer yield was calculated based on the mass of the solid residue left after oxidation. a 0.5 M NaOH was used to perform the reaction in an alkaline environment at pH 10 in the absence of a primary oxidant. | |
GPC and NMR studies of kraft lignin
The reported catalytic oxidation of lignin to yield vanillin begins with the formation of a phenoxyl radical and ends with the retroaldol cleavage of substituted coniferaldehyde.46 In our endeavor to ascertain further structural changes to the lignin after oxidative depolymerization using the Fe@MagTEMPO catalyst, we carried out 31P and 2D HSQC NMR analysis along with GPC analysis on an acid soluble lignin fraction post-treatment. Non-oxidized and oxidized versions of ASKL (4 h 25 °C, 5 mmol g−1 NaClO) were used for this purpose owing to the homogeneity and smaller size of ASKL. Functional groups for aliphatic OH, aromatic OH, and carboxylic acid groups were retained in the spectrum after oxidative depolymerization (Table 1 and Fig. S7†). However, the total number of hydroxyl groups was slightly reduced. Available terminal phenolics were preferably removed in this reaction pathway. Further, no new linkages were formed in oxidized lignin as evident from 2D NMR (Fig. 2 and Table S4†). In this data, the overall β-O-4 linkages remained nearly the same and this may be attributed to the normalized intensity of signals from the aromatic ring; as the total phenolic content decreases, this can increase the relative value of linkages if they remain unchanged. Further, there was slight condensation in oxidized lignin as visible from the elution pattern of GPC, although the bulk of the lignin showed a similar response (Fig. S8 and Table S5†). These observations suggest that the system has some limited repolymerization and mainly is driven by isolating the phenolics from the chain ends of the lignin. This may be one reason why the depolymerization reaction is so effective with high selectivity towards vanillin.
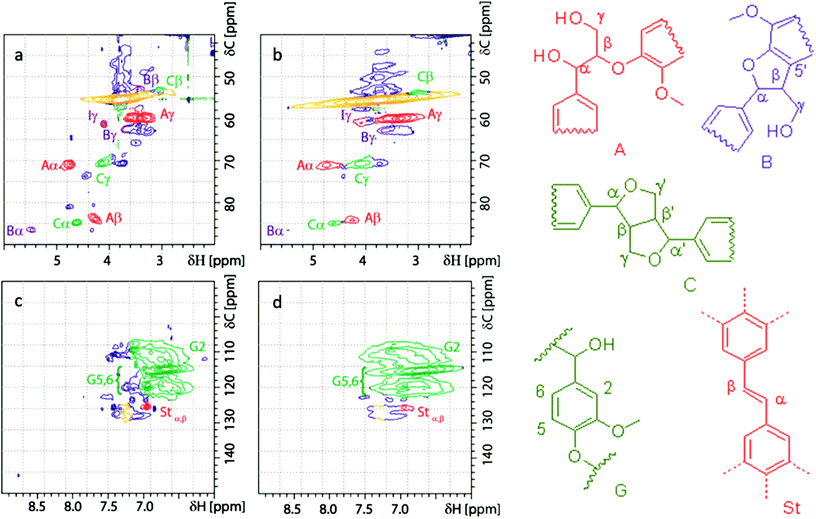 |
| Fig. 2 2D HSQC spectrum of ASKL before and after oxidative depolymerization using the Fe@MagTEMPO catalyst. The aliphatic region for (a) ASKL and (b) oxidized ASKL and the aromatic region for (c) ASKL and (d) oxidized ASKL. | |
Table 1 Quantitative 31P NMR analysis of ASKL before and after oxidative depolymerization (4 h, 25 °C, 5 mmol g−1 NaClO) using the Fe@MagTEMPO catalyst
Lignin |
Aliphatic OH (mmol g−1) |
5-Condensed (mmol g−1) |
Guaiacyl OH (mmol g−1) |
p-Hydroxyphenyl (mmol g−1) |
Aromatic OH (mmol g−1) |
COOH (mmol g−1) |
Total OH (mmol g−1) |
ASKL |
2.01 |
1.58 |
2.34 |
0.29 |
4.21 |
0.02 |
6.22 |
Oxidized ASKL |
1.60 |
1.63 |
2.06 |
0.18 |
3.88 |
0.43 |
5.48 |
Conclusion
We were able to selectively depolymerize softwood kraft lignin to vanillin with 20% yield of phenolic monomers using greener reaction conditions providing a possible pathway towards the valorization of technical lignin. The Fe@MagTEMPO catalyst enabled easy isolation of phenolic monomers, at room temperature, prevented the release of TEMPO and was reused without any loss of activity. The amine groups anchored along with TEMPO on magnetic nanoparticles were hypothesized to abstract protons from oxidized lignin enabling the reaction to occur at neutral pH. This oxidative depolymerization methodology is therefore a significant advancement in the development of greener biomass valorization processes. In future, to address the next challenges we plan for less energy intensive vanillin recovery methods. Also, a more benign primary oxidant must be explored as the use of sodium hypochlorite can lead to the formation of chlorinated phenolics during oxidative depolymerization.
Experimental
The Fe@MagTEMPO catalyst was synthesized through four stages of precipitation–condensation–silanization and reductive amination. The detailed catalyst synthesis methodology has been reported earlier.29 The oxidative depolymerization experiments were carried out in a 1 L round bottom flask. Temperature was controlled using a heating mantle equipped with a PID controller (±2 °C). An overhead stirrer was used to disperse the catalyst in the reaction mixture. pH was monitored using a Fischer Scientific AR 15 meter. A typical oxidation test involved using kraft lignin dispersed in distilled water such that the concentration of lignin was 1% (w/w). Required quantities of sodium bromide and Fe@MagTEMPO were then added to the dispersion of kraft lignin. Oxidation was started by dropwise addition of sodium hypochlorite. Addition of sodium hypochlorite increases the pH. However, the pH drops as the oxidant is consumed. The pH was maintained between 7 and 7.5. The mixing was stopped after a desired amount of time and the catalyst was immediately separated from the reaction mixture and collected using an external magnet for reuse.
Abbreviation
GCMS | Gas chromatography with mass spectroscopy |
FID | Flame ionization detector |
NMR | Nuclear magnetic resonance |
GPC | Gel permeation chromatography |
ASKL | Acetone soluble Indulin AT |
AIKL | Acetone insoluble Indulin AT |
TEMPO | 2,2,6,6-Tetramethylpipredinyl-1-oxyl |
Fe@MagTEMPO | Heterogeneous catalyst with TEMPO anchored on magnetic nanoparticles |
Fe@MagBasic | Heterogeneous catalyst with amine groups anchored on magnetic nanoparticles |
TurboBeads | Commercial catalyst with TEMPO anchored on cobalt nanoparticles |
ICP-MS | Inductively coupled plasma mass spectroscopy |
Conflicts of interest
UBC uses Flintbox to provide researchers the ability to purchase the Fe@MagTEMPO catalyst that allows for the oxidation of biomass with separation and reuse of the catalyst.
Acknowledgements
SC Patankar and Scott Renneckar would like to thank support from The Paul and Edwina Heller Memorial Fund and the MRPF. In addition, SR acknowledges the Canada Research Chairs program for the Advanced Renewable Materials funding program. SCP acknowledges assistance from Dimitrios Avramidis in performing oxidative depolymerization experiments.
References
- R. A. Sheldon, Green Chem., 2014, 16, 950–963 RSC
.
- P. Gallezot, Chem. Soc. Rev., 2012, 41, 1538–1558 RSC
.
- M. Fache, B. Boutevin and S. Caillol, ACS Sustainable Chem. Eng., 2016, 4, 35–46 CrossRef CAS
.
- M. Fache, B. Boutevin and S. Caillol, Eur. Polym. J., 2015, 68, 488–502 CrossRef CAS
.
- T. R. Brown, Biofuels, Bioprod. Biorefin., 2018, 12, 485–496 CrossRef CAS
.
-
C. Houtman, in Lignin Valorization Emerg. Approaches, ed. G. T. Beckham, The Royal Scociety Of Chemistry, Croydon, UK, 2018, pp. 62–73 Search PubMed
.
- J. Hu, Q. Zhang and D. J. Lee, Bioresour. Technol., 2018, 247, 1181–1183 CrossRef CAS PubMed
.
- P. C. A. Bruijnincx and B. M. Weckhuysen, Nat. Chem., 2014, 6, 1035–1036 CrossRef CAS PubMed
.
- E. A. B. da Silva, M. Zabkova, J. D. Araújo, C. A. Cateto, M. F. Barreiro, M. N. Belgacem and A. E. Rodrigues, Chem. Eng. Res. Des., 2009, 87, 1276–1292 CrossRef
.
- R. Rinaldi, R. Jastrzebski, M. T. Clough, J. Ralph, M. Kennema, P. C. A. Bruijnincx and B. M. Weckhuysen, Angew. Chem., Int. Ed., 2016, 55, 8164–8215 CrossRef CAS PubMed
.
- C. Crestini, H. Lange, M. Sette and D. S. Argyropoulos, Green Chem., 2017, 19, 4104–4121 RSC
.
- Z. Hu, X. Du, J. Liu, H. M. Chang and H. Jameel, J. Wood Chem. Technol., 2016, 36, 432–446 CrossRef CAS
.
- R. Ma, M. Guo and X. Zhang, Catal. Today, 2018, 128–158 Search PubMed
.
-
P. C. R. Pinto, E. A. B. da Silva and A. E. Rodrigues, in Biomass Conversion, ed. C. Baskar DR. and S. Baskar, Springer, Berlin, Heidelberg, 2012, pp. 381–420 Search PubMed
.
- W. Schutyser, T. Renders, S. Van Den Bosch, S. F. Koelewijn, G. T. Beckham and B. F. Sels, Chem. Soc. Rev., 2018, 47, 852–908 RSC
.
- V. E. Tarabanko and N. Tarabanko, Int. J. Mol. Sci., 2017, 18(11), 2421 CrossRef PubMed
.
- C. Xu, R. A. D. Arancon, J. Labidi and R. Luque, Chem. Soc. Rev., 2014, 43, 7485–7500 RSC
.
-
C. C. Bryan, US Pat, 2692291, 1954 Search PubMed
.
- J. D. P. Araújo, C. A. Grande and A. E. Rodrigues, Chem. Eng. Res. Des., 2010, 88, 1024–1032 CrossRef
.
- R. Ma, Y. Xu and X. Zhang, ChemSusChem, 2015, 8, 24–51 CrossRef CAS PubMed
.
- J. Dai, A. F. Patti and K. Saito, Tetrahedron Lett., 2016, 57, 4945–4951 CrossRef CAS
.
- G. F. De Gregoria, R. Prado, C. Vriamont, X. Erdocia, J. Labidi, J. P. Hallett and T. Welton, ACS Sustainable Chem. Eng., 2016, 4, 6031–6036 CrossRef
.
-
J. J. Bozell, in Selective Catalysis for Renewable Feedstocks and Chemicals, ed. K. M. Nicholas, Springer-Verlag, Berlin, 2014, pp. 229–256 Search PubMed
.
- R. Behling, S. Valange and G. Chatel, Green Chem., 2016, 18, 1839–1854 RSC
.
- A. Isogai, T. Saito and H. Fukuzumi, Nanoscale, 2011, 3, 71–85 RSC
.
- P. Ma, S. Fu, H. Zhai, K. Law and C. Daneault, Bioresour. Technol., 2012, 118, 607–610 CrossRef CAS PubMed
.
- A. Rahimi, A. Azarpira, H. Kim, J. Ralph and S. S. Stahl, J. Am. Chem. Soc., 2013, 135, 6415–6418 CrossRef CAS PubMed
.
- T. Vangeel, W. Schutyser, T. Renders and B. F. Sels, Top. Curr. Chem., 2018, 376, 30 CrossRef PubMed
.
- S. C. Patankar and S. Renneckar, Green Chem., 2017, 19, 4792–4797 RSC
.
- C. Li, X. Zhao, A. Wang, G. W. Huber and T. Zhang, Chem. Rev., 2015, 115(21), 11559–11624 CrossRef CAS PubMed
.
- Z. Sun, B. Fridrich, A. de Santi, E. Elanovan and K. Barta, Chem. Rev., 2018, 118(2), 614–628 CrossRef CAS PubMed
.
- M. B. Hocking, J. Chem. Educ., 1997, 74(9), 1055–1059 CrossRef CAS
.
-
R. Blair, US Pat, 20160009621A1, 2014 Search PubMed
.
-
N. Borthakur, US Pat, 7399889B2, 2008 Search PubMed
.
- Z. Xu, Q. Liu and J. A. Finch, Appl. Surf. Sci., 1997, 120, 269–278 CrossRef CAS
.
- S. Čampelj, D. Makovec and M. Drofenik, J. Magn. Magn. Mater., 2009, 321, 1346–1350 CrossRef
.
- R. A. Bini, R. F. C. Marques, F. J. Santos, J. A. Chaker and M. Jafelicci, J. Magn. Magn. Mater., 2012, 324, 534–539 CrossRef CAS
.
-
C. Sutton, E. Serum and M. Sibi, presented in part at 22nd Annual Green Chemistry and Engineering conference, Portland, June, 2018, p. GC&E 32
.
- R. A. Sheldon, I. W. Arends, G. J. Ten Brink and A. Dijksman, Acc. Chem. Res., 2002, 35, 774–781 CrossRef CAS PubMed
.
- B. Karimi and E. Farhangi, Chem. – Eur. J., 2011, 17, 6056–6060 CrossRef CAS PubMed
.
-
P. Fatehi and J. Chen, in Production of Biofuels and Chemicals from Lignin, ed. Z. Fang and R. L. Smith, Springer Science+Business Media, Singapore, 2016, pp. 35–54 Search PubMed
.
- L. Liu, M. Cho, N. Sathitsksanoh, S. Chowdhury and S. Renneckar, ACS Sustainable Chem. Eng., 2018, 6, 12251–12260 CrossRef CAS
.
- Sigma Aldrich, “TurboBeads TEMPO”, can be found under https://www.sigmaaldrich.com/catalog/DataSheetPage.do?brandKey=ALDRICH&symbol=742945 (accessed Oct 12, 2018).
- C. Fargues, Á. Mathias and A. Rodrigues, Ind. Eng. Chem. Res., 1996, 35, 28–36 CrossRef CAS
.
- A. E. Rodrigues, Holzforschung, 1995, 49, 273–278 CrossRef
.
- V. E. Tarabanko, D. V. Petukhov and G. E. Selyutin, Kinet. Catal., 2004, 45, 569–577 CrossRef CAS
.
Footnote |
† Electronic supplementary information (ESI) available. See DOI: 10.1039/c8gc03304h |
|
This journal is © The Royal Society of Chemistry 2019 |
Click here to see how this site uses Cookies. View our privacy policy here.