DOI:
10.1039/D2CS00606E
(Tutorial Review)
Chem. Soc. Rev., 2023,
52, 2553-2572
Less is more: a perspective on thinning lithium metal towards high-energy-density rechargeable lithium batteries†
Received
26th October 2022
First published on 15th March 2023
Abstract
Lithium (Li) metal, owing to its high specific capacity and low redox potential as a Li+ ion source in rechargeable lithium batteries, shows impressive prospects for electrochemical energy storage. However, engineering Li metal into thin foils has historically remained difficult, owing to its stickiness and fragility upon mechanical rolling. Consequently, using thick Li in battery systems betrays the original target for achieving higher energy density, results in material waste, and creates illusions on evaluating modification strategies for taming the highly reactive Li metal anode. Being apprehensive of this, in the tutorial review, we illustrate the argument of applying thin Li (<50 μm, preferably ≤30 μm) to achieve more realistic and advanced battery systems. A brief overview of Li is sketched first to help understand its role in batteries. Then, the reasons for pursuing thin Li are critically analyzed. Next, seminal technologies enabling the fabrication of thin Li are summarized and compared, which calls for the participation of experts from mechanical engineering, metallurgy, electrochemistry, and other fields. Subsequently, the possible applications of thin Li in batteries are presented. With the deployment of thin Li, there are new challenges and opportunities to encounter and an outlook is afforded thereof. Holy-grail Li metal anodes, combined with the subtraction operation in thickness and compatible modification strategies, would bring about a truly great leap forward in electrochemical energy storage.
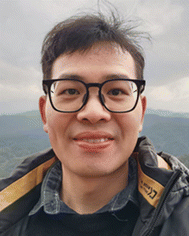
Wangyan Wu
| Wangyan Wu received his BE degree in Materials Science and Engineering at Tongji University in 2019. He is currently a PhD candidate in the School of Materials Science and Engineering at Tongji University, under the supervision of Prof. Wei Luo. His research interests focus on building LIBs with high energy density and liquid metals. |
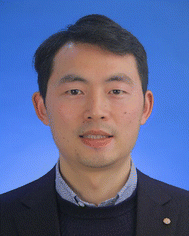
Wei Luo
| Wei Luo is currently a Professor in the School of Materials Science and Engineering at Tongji University. He received his BE and ME from Northwestern Polytechnical University, and PhD from Huazhong University of Science and Technology. Prior to his current position, Wei worked as a postdoctoral researcher at Oregon State University and the University of Maryland (UMD) until being promoted to Assistant Research Professor at UMD. His research interests include solid-state batteries, liquid metals, and high-entropy materials. |
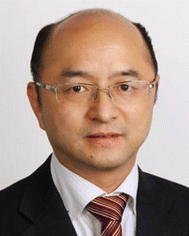
Yunhui Huang
| Yunhui Huang received his BS, MS, and PhD from Peking University. He worked with Prof. John B. Goodenough at the University of Texas at Austin from 2004 to 2007. In 2008, he became a Chair Professor of Materials Science at Huazhong University of Science and Technology. In 2017, he built up the Institute of New Energy for Vehicles at Tongji University. His research group mainly works on rechargeable batteries. |
Key learning points
1. Featured properties of lithium.
2. The reasons for pursuing thin Li in a lithium battery system.
3. Fabrication of thin Li.
4. Applications of thin Li in batteries.
5. New challenges and opportunities for thin Li.
|
1. Introduction
Rechargeable Li-ion batteries (LIBs), benefiting from their high energy/power density and long lifespan, outperform a myriad of other rechargeable batteries in consumer electronics (e.g., lead-acid batteries, nickel–metal hydride batteries, nickel–cadmium batteries), leading to their successful commercialization and permeation in daily life.1 Currently, there is a worldwide strong appetite for decarbonization and building a clean-energy economy, ushering in an era based on LIBs. We have witnessed that LIBs dominated the market of portable electronics, extended the market share of electric vehicles (EVs),2 and infiltrated the fields of grid-scale energy storage,3 containership,4 and aviation.5 What makes LIBs more popular are the roadmaps and policies formulated by the major countries and regions, such as “National Blueprint for Lithium Batteries 2021–2030” released by the United States,6 “Strategic Action Plan on Batteries” by the EU,7 and “Made in China 2025” plan by China.8 With emerging electric appliances as critical drivers of the demand for LIBs, LIBs based on intercalation chemistry (applying layer-structured electrode materials, such as graphite anode and LiCoO2 cathode, where Li ions can reversibly intercalate/de-intercalate from their layers) with a limited energy density ceiling cannot satisfy the insatiable needs for higher energy density, resulting in “low battery anxiety”, namely the fear of losing power or being without fully charged devices.
To alleviate this concern, a goal of energy density up to 500 W h kg−1 was set in the field of EVs.9 To achieve this target, systematic work on battery design is worthwhile, which includes not only material components, but also technological parameters (e.g., active material mass ratio, electrode thickness and porosity, anode/cathode capacity (N/P) ratio, electrolyte amount, testing protocol).10–12 Simultaneously, key performance metrics (e.g., energy and power densities, safety, Coulombic efficiency (CE), battery-production cost and lifespan)13–15 have to be comprehensively optimized and balanced. Thus, a number of strategies have been developed to fabricate thick cathodes to realize concomitant high energy and power capability,16 such as magnetic alignment method17,18 and gradient electrode design.19 Similarly, reports on the delicate control of electrode drying process,20 regulation of electrode porosity,21 the integration of thin film solid-state electrolytes22 or lean electrolytes23 were also observed. Among various strategies to further push the specific energy limit, Li metal anodes (LMAs) emerge as a focal point. Li metal is dubbed the “holy grail” of anode materials because it possesses the most negative redox potential at the standard state (−3.04 V vs. S.H.E.) and high specific capacity (3860 mA h g−1). Nevertheless, learning from the lessons of safety accidents that occurred with Li//MoS2 batteries of Moli Energy,24 introducing LMAs into rechargeable batteries needs to proceed with more caution. Owing to its extremely high reactivity and great volume change-induced SEI breaking and reforming, the low CE hampers the deployment of LMAs.25 Based on this hindsight, plenty of ingenious strategies were conceived to tame the highly reactive LMAs.26–30 However, most research studies have focused on addressing Li dendrite and low CE issues. Less attention is paid to the thickness of the applied LMAs, such that a great Li excess has become almost routine (Fig. 1). A large excess of Li not only brings about an energy density far below expectations,31 but also wastes materials and results in illusions of the validity of proposed strategies for prolonging the cycle life and improving CE.32 Recently, the thin LMA initiative was started.1,33,34 The Liu group investigated pouch cells applying LMAs with different thicknesses.35 They discovered thickness-related degradation mechanisms and fading modes, where a 20 μm thin Li with a modified ether-based localized high-concentration electrolyte brought unexpectedly promising results (over 600 long stable cycles of a 350 W h kg−1 Li metal pouch cell without a sudden cell death). Furthermore, Zhang and colleagues revealed the detailed failure mechanism of ultrathin LMAs applied in practical conditions.36 These reports underlie the necessity and possibility of thin Li in rechargeable Li batteries. Unfortunately, it was overwhelmed by the difficulties in obtaining cost-effective thin Li.
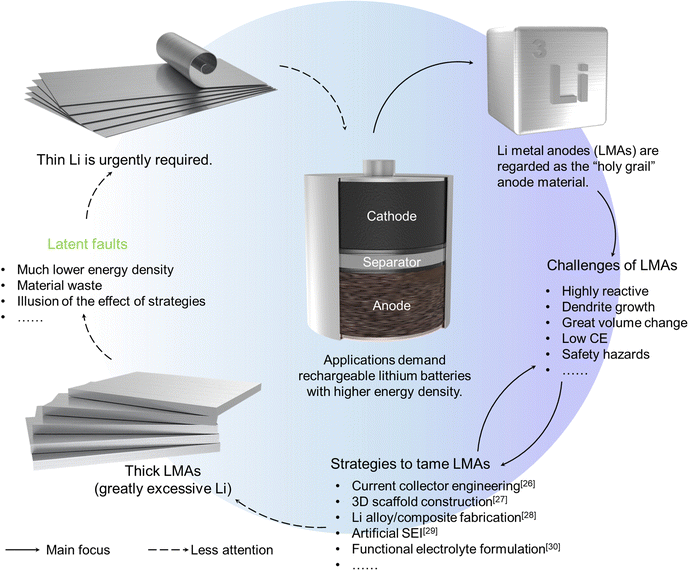 |
| Fig. 1 The promise, challenges, and solutions of Li metal anodes and the intuitive logic of thinning Li metal for battery applications. | |
Within the last few years, the academic and industrial communities have made exceptional progress in fabricating thin Li (generally refers to <50 μm, preferably ≤30 μm) or ultrathin Li foil (≤20 μm) (the definition of thin Li in published articles is referenced in Table S1, ESI†).35,37,38 Since there are few studies on the thickness of LMA in batteries, the aim of this review is to promote more fundamental research studies and practices in this leading edge. In this tutorial review, we first provide a brief overview of Li referring to its resources, extraction, and featured properties to help understand the role that Li plays in batteries. Then, the fundamental reasons for pursuing thin Li in a battery system from the perspectives of the electrochemical performance, material cost and safety are critically analyzed. Next, focusing on the fabrication of thin Li, the technologies and conceptualized ideas, categorized into solid, liquid and gaseous phase processes, respectively, are summarized and compared. Subsequently, the possible applications of thin Li in battery systems are presented. Finally, an outlook is offered concerning the challenges and opportunities accompanied with the deployment and fabrication of thin Li. The subtraction operation in thickness is a path that must be taken for Li metal to act as anodes in practical batteries. With thin Li, the merits of higher energy density, more realistic conditions, less materials, newer applications, and concurrently more stringent challenges are coming, and therefore more efforts are needed.
2. A brief overview of lithium
2.1 The resources, extraction and applications of lithium
The discovery of lithium dates back to 1817 by the Swedish scientist Johan August Arfwedson in a mineral ore called Petalite.39 Thus, it is named after the Greek word ‘‘lithos’’ meaning ‘‘stone’’. After years of exploration, Li was found to exist not only in a variety of rocks, such as Spodumene, Lepidolite, and Eucryptite, but also in brines and sea water. Unfortunately, Li possesses only an average abundance of 20 ppm in the continental crust, making it a geochemically scarce metal.40 According to the United States Geological Survey (USGS), the globally identified Li resources were about 89 million tons in 2021.41 Even worse, the global distribution of Li resources is prominently uneven, with more than 56% located in the so-called “Lithium Triangle”, a geographic area at the borders of Chile, Bolivia, and Argentina, followed by the USA, Australia and China (Fig. 2).
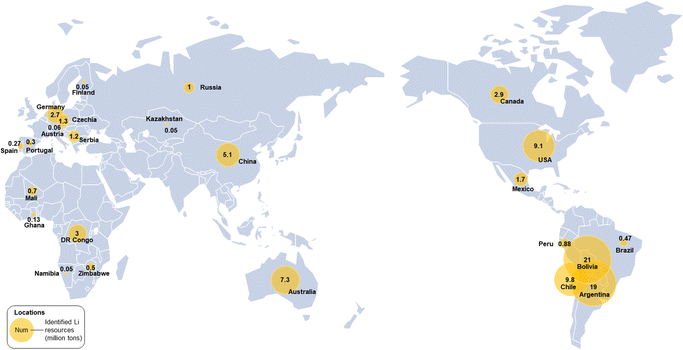 |
| Fig. 2 The world map of identified Li resources distribution according to the data of the latest USGS Li Statistics and Information.41 The amounts in each location are proportional to the areas of yellow circles. | |
Although lithium was discovered long ago, its exploitation was inconspicuous before 1950s. The United States acted as the principal producer of Li minerals from 1950s to 1980s. Thereafter, due to the ever-growing demand of global industry, the emergence of rock and brine operations in the main resource-holder countries, Australia and Chile, respectively, made them the largest producers.42 For mineral ores, they experience decrepitation, leaching, precipitation and purification processes to first get lithium carbonate.43 For brine precursors, they go through a long-term (12–24 months) lime-soda evaporation process to concentrate and purify Li salts to give the desired Li compounds, which is a time-consuming process.44 Recently, a new concept of electrochemical lithium extraction was demonstrated.45 Currently, brine sources support more than 2/3rd of the global demand for Li.46 Li compounds offer diversified applications, such as participating in the ceramics and glass industry to decrease the melting temperature and melt viscosity, assisting polymer synthesis as an initiator, and acting as a thickening agent in grease.47 Among them, ceramics, glass, and primary aluminum production consumed >60% of Li before 2005.48 Thereafter, with the thriving development of portable electronics and ever-growing interests in EVs, the share taken up by the Li battery industry presents a step-by-step increase. According to USGS, about 74% of the globally produced Li flowed into the Li battery sector in 2021 (Fig. 3).41
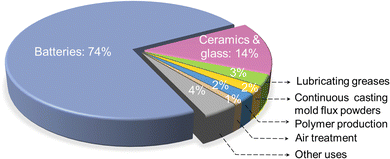 |
| Fig. 3 Global end-use markets of Li-containing chemicals and corresponding shares (2021).41 | |
2.2 Featured properties of metallic Li
Li is one of the alkali metals, and is located in Group IA and Period 2 in the periodic table, with an atomic number of 3, an electronic configuration of 1s22s1, and an atomic mass of 6.941 g mol−1. At standard temperature and pressure (293.15 K and 101.325 kPa, respectively, the National Institute of Standards and Technology), Li metal possesses a body-centered cubic crystal structure and is the lightest metal (0.534 g cm−3). With regard to the metallurgy of Li metal, it generally undergoes molten salt electrolysis of LiCl in a cell taking graphite as the anode, mild steel as the cathode, and LiCl-KCl eutectic as the electrolyte.49
Among a variety of metals, the melting point of Li ranks ninth from the lowest (Fig. 4a), and is as low as 180.5 °C. In recent years, with the emergence and rapid development of liquid metals that generally refer to metals with melting points near or below room temperature (e.g., Hg, Cs, Ga), the community considers metals that melt under 330 °C within the “extended family” of liquid metals, including metallic Li.50 A low melting point of Li enables liquid Li (molten state) to be readily accessible and adapted to a series of liquid engineering methods. Correlated with the low melting point and attributes of liquid metal, Li metal is soft and ductile, with a remarkably low Young's modulus of 5 GPa (Fig. 4b), which is 1/9th that of Mg, 1/14th that of Al, and 1/42nd that of Fe.49 A series of experiments demonstrated that the yield strength of Li is between 0.5 to 1.1 MPa, depending on the strain rates.51–53 The low yield strength enables Li metal to be shaped from bulk to sheet by a simple extrusion process. On the other hand, due to the sticky and soft characteristics, further pressing the Li sheet into a thin foil will be much more difficult without external assistance. Moreover, the easier plastic deformation would give rise to Li crystallographic reorientation or redistribution, even shape change, which introduces risks of dendrite growth in Li metal batteries (LMBs).54,55
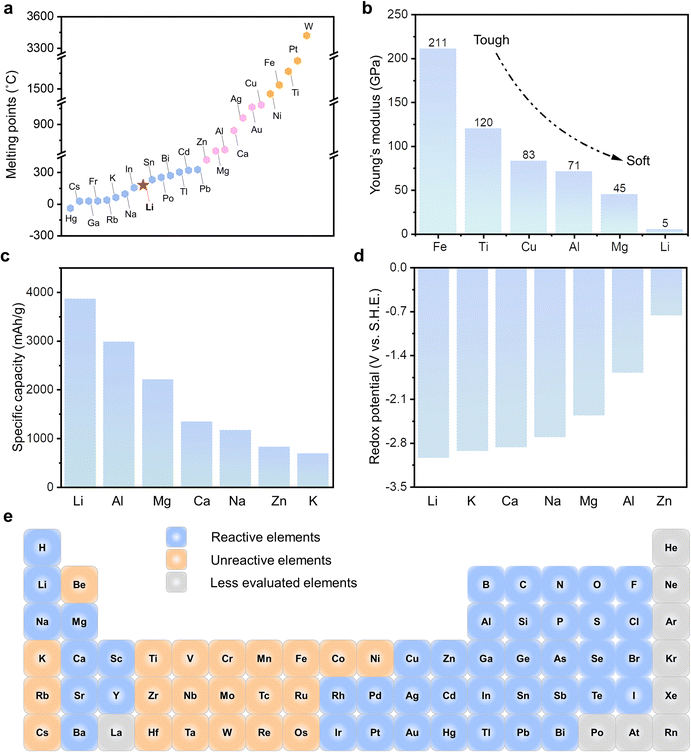 |
| Fig. 4 General properties of metallic Li. (a) The melting points of a series of metals.50 (b) Young's modulus of several metals.49 (c) The theoretical gravimetric capacity and (d) redox potential (vs. S.H.E.) of a series of metallic anodes, among which Li metal possesses the high specific capacity (3860 mA h g−1) and lowest average potential (−3.04 V). (e) Various elements in the first 6 periods that are reactive and unreactive with the molten Li.59–62 | |
According to the formula of nF/Mw, where n is the transferred electron number, F is the Faraday's constant (96
485 C mol−1 or 26,801.39 mA h mol−1), Mw is the molecular weight, the theoretical gravimetric capacity of a series of metallic anodes (Mn++ ne− ↔ M, where M represents a metal anode) can be calculated, among which Li possesses a high value of 3860 mA h g−1, as shown in Fig. 4c. Simultaneously, due to the lowest redox potential (Fig. 4d) and low electronegativity value of 0.98, Li metal is prone to donate one electron, and Li+ with a small ionic radius of 0.76 Å is easy to shuttle in the electrolytes.56 Thus, metallic Li is an excellent anode candidate. Before we go into the details of LMAs, the reactivity of metallic Li should be understood. Firstly, Li metal reacts readily with atmospheric gases and protic liquid due to its low work function of 2.9 eV.57 Thus, the storage of Li metal should be conducted in inert gases or selected non-polar solvents, such as cyclohexane, heptane, hexane, and similar solvents.58 Moreover, Li metal, especially in its molten state, can react with almost 42 out of 65 elements in the first 6 Periods (excluding lanthanides and noble gases), and a great number of oxides, nitrides and halides under ambient pressure (Fig. 4e).59–62 In addition, the wettability of molten Li with various substrates can be tuned by varying the temperature, surface chemistry and tomography.63 Benefiting from this, Li metal can reliably wet and adhere to a myriad of substrates, which significantly promotes its versatile applications.64,65
3. Why does thin Li matter?
In retrospect, although connected with electrochemistry since its birth by applying voltaic piles to fuse Li2CO3 or Li2O to isolate elemental Li,39 metallic Li's first positive participation in the electrochemical realm was in 1913 when Gilbert Lewis and his colleague determined the lowest potential of Li electrode.66 After another 50–60 years, Li metal began to act as anodes in primary and rechargeable batteries, respectively.67 Attractive for their high energy density, rechargeable LMBs were commercialized in the 1980s, although this quickly came to a premature end due to severe safety risks.24 After several decades, the surge of developing EVs has brought LMAs back into view. Most of the current research investigations aimed at taming the highly reactive LMAs, but were based on excessive Li. The electrode thickness significantly influences the battery performance from many key aspects, such as energy density, capacity fading rate, heat generation and distribution.68,69 Moreover, results based on an unrealistically thick LMA would provide some superficial information, and may even mislead the fundamental understanding. Towards more practical battery applications, it is worthwhile to analyze the critical reasons for thinning LMAs.
3.1 Electrochemical performance
From the perspective of the theoretical gravimetric capacity of LMAs, an ultrahigh value of 3860 mA h g−1 is generally quoted. It is worth noting that such an ideal value can only be achieved when all of the Li is electrochemically active in the stripping/plating process, namely zero excess of Li. Nevertheless, the reality is that an LMA with a thickness of up to several hundred microns (every 5 μm translates to an areal capacity of ∼1 mA h cm−2, see Note S1, ESI† for the correspondence) is commonly applied, but only a small fraction of it engages in the charge/discharge process. Consequently, the “true” specific capacity of LMA is calculated as 3860/(1 + X), where X is the times of Li excess. As illustrated in Fig. 5a, the LMA approaches the theoretical value only when its thickness matches the amount that is stripped/plated per cycle. Otherwise, a large excess of Li results in an intolerably low specific capacity that is even inferior to that of graphite anode (372 mA h g−1), as indicated by the dashed lines.
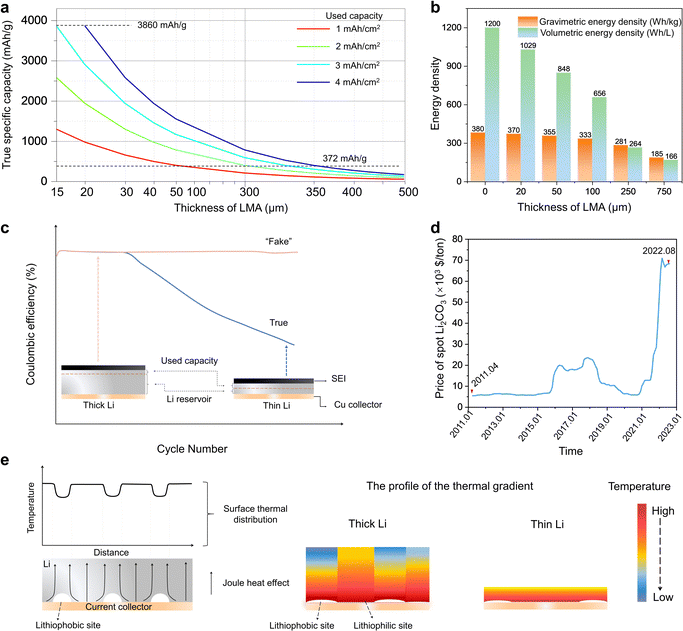 |
| Fig. 5 The reasons for thinning Li metal towards practical Li batteries. (a) The true specific capacity of an LMA considering the used capacity in the charge/discharge process and the overall thickness of an LMA. (b) The calculated energy density of a battery system pairing the LiCoO2 cathode with LMAs (different thicknesses) according to the reference data,37 where thin Li (<50 μm) enables an elevated energy density higher than 350 W h kg−1. The total mass and volume of the battery components are included in the calculation of gravimetric and volumetric energy density, respectively. It is worth noting that the LMB with the LMA thickness of 0 μm that provides energy densities is the anode-free configuration with a Cu collector on the anode side. (c) The illusion of CE created by applying thick Li. Compared with thick Li, thin Li has less Li reservoir to compensate for the lost Li consumed in SEI. Thus, thin Li reflects a more realistic CE. (d) The greatly increased price of battery-grade Li2CO3 from April, 2011 to August, 2022.79 (e) The inhomogeneous surface thermal distribution and cross-sectional thermal gradient caused by the imperfect interface structure between Li and the Cu current collector, where a thinner Li would minimize the inhomogeneity and lower the safety risks of the Li dendrite induced by hot spots. | |
Moving to the cell level, a sophisticated choice of materials and a thorough balance of technological parameters (e.g., active material mass ratio, electrode thickness, etc.) must be executed to maximize the deliverable energy of a battery with limited weight or volume. With metallic Li as the anode, ample room is set aside for cathode candidates. If a fully lithiated cathode is chosen, especially high-nickel–content LiNixM1−xO2 (M = Mn, Co and x ≥ 0.6) and Li- and Mn-rich oxides, the most ideal configuration to pursue high energy density is anode-free. Such an ingenious conception simplifies the production process, reduces the costs for materials, and prominently enhances the energy density.70,71 However, Li ions from the cathode would be consumed inevitably and quickly due to the formation of the solid electrolyte interphase (SEI) or dead Li.72 On the other hand, if a Li-free material (e.g., S8, O2) is appointed as the cathode, a thick LMA can be applied theoretically as the Li+ ion source. Nevertheless, a matched thick cathode is difficult to fabricate or operate functionally.16 Thus, the obstacle exists in the difficulty to balance the anode and cathode capacity (i.e., N/P ratio), which is of great significance to energy density.73,74 As exemplified in Fig. 5b, a thick LMA would immensely lower the theoretical energy densities.37 Therefore, introducing thin Li would be an excellent option. Occupying a very small volume or weight portion, thin Li can act as a compensation agent for Li loss of lithiated cathodes or a pure anode for unlithiated cathodes to realize the truly high energy density.
Still from the cell level, it would be a formidable challenge to simultaneously achieve high energy density and a long lifespan. Although a myriad of publications alleged superior performance, they are based on unpractical conditions, such as flood electrolytes and excess Li. In this case, abundant Li+ ion sources coming from the extra amounts of electrolytes and Li metal replenish the Li loss of the cathode. As a result, the cell exhibits a deceptively long cycling life and high CE (Fig. 5c).75–77 This implies that a seemingly high CE does not necessarily correlate with excellent cyclability. A thorough comprehension of the measured CE and cycling stability is important.32 There are two cell failure modes in practical conditions.78 The first one originates from electrolyte depletion when lean electrolyte is used. Under such a circumstance, refilling electrolyte would refresh the cell to function normally. The other one is attributed to the depletion of Li metal. In the case of the anode-free configuration with no excessive Li to artificially inflate the cyclability, the CE, albeit unsatisfactory most of the time, is true and correlates with the lifespan. To achieve this advantage of anode-free LMBs, thin Li would be a good choice. It enables a more accurate evaluation of the efficiency of lithium stripping and plating, the effectiveness of conceived strategies proposed to help prolong the cycling life and stabilize the cycling of LMAs (e.g., electrolyte formulation, artificial SEI), and earlier recognition of the failure and challenges (e.g., soft short).33 It is worth noting that thin Li can already bring the long cycling life to more than 600 cycles with 76% capacity retention without a sudden cell death by charging at 0.1 C and discharging at 0.3 C (where 1 C equals 4.0 mA cm−2 or corresponds to 2.3 A) when pairing with a high-loading NMC622 cathode (4 mA h cm−2, N/P ratio is 1
:
1) and lean electrolytes. In sharp contrast, under the same condition, anode-free LMBs show capacity decay from the beginning and maintain only 80% of its capacity after 100 cycles.35
3.2 Materials cost
The production of rechargeable lithium batteries needs the input of materials, labor, energy, and others. On the premise of delivering desirable electrochemical performances, lowering the materials cost is indispensable. As mentioned in Section 2, there are relatively abundant Li resources on the earth (89 million tons). Therefore, there should be no shortage of Li in the short term and its price should have been moderate out of intuition. Nevertheless, contrary to anticipation, the price of spot battery-grade Li2CO3 experienced skyrocketing rises in recent years, reaching $68,429/ton in August 2022 (Fig. 5d).79 The reason behind this is the thriving development of EVs and a concern about supply risks. Since the Li resources are distributed unevenly, the supply market can be regarded as an oligopoly, with Albemarle, SQM, FMC, Tianqi, and Ganfeng as the main players.80 On the other hand, there is significant latency between supply and demand, taking into consideration that merely the Li extraction step requires 12–24 months from brines. It is predicted that the high price of Li2CO3 will at least last until 2025.81 Moreover, the production of Li is an energy-intensive process.82 Thus, as a refined product derived from Li2CO3 or LiCl, metallic Li undoubtedly has high value. On account of the above analysis, thinning LMA is of great importance. However, there are possible arguments that the price of commercial thin Li is intolerably high. Indeed, that is why great endeavors have been devoted to realizing facile and cost-effective thin Li fabrication, which will be discussed in Section 4.
3.3 Safety
Accompanied with the target of high energy density, long lifespan and low cost, safety is another prerequisite that a consumer-grade rechargeable lithium battery needs to possess. With the intrinsically high reactivity, the Li metal contained in the battery runs as a barrel of gunpowder. Excess Li would instigate vigorous burning or explosion, especially when an accident happens. Based on this point, anode-free LMBs that eliminate free Li alleviate many safety hazards. Zooming into the microscale, the danger of applying LMAs usually derives from the runaway growth of Li dendrite and induced shorting. Among diversified factors affecting Li dendrite growth, temperature plays a significant role.83 A heterogeneous temperature distribution, such as hot spots, will initiate and accelerate dendrite growth due to the increased Li-ion diffusion coefficient and a locally enhanced surface exchange current density.84,85 On the contrary, an isothermal but high-temperature battery system can realize dendrite suppression or self-healing (the formed dendrites start to disappear when they are heated up under certain conditions).86,87 Typically, metallic Li is mechanically attached or plated on a Cu current collector. Due to the different lithiophilicity of sites on a current collector in practical conditions, gaps tend to appear on the interface between LMA and lithiophobic sites, which would inevitably affect heat conduction and lead to the formation of hot spots.88 Taking into consideration an unbalanced heat generation and cooling, an inhomogeneous thermal gradient is inevitable throughout the electrode (Fig. 5e). In the circumstances, a thinner Li foil promises a homogeneous thermal gradient in the thickness direction, which lowers the risks of dendrites.
4. How to fabricate thin Li?
To obtain thin Li foils for high-energy-density battery systems, researchers in academia and industry have worked to conceive concepts and develop technologies to enable their realization. It is worth noting that, different from the definition in surface engineering where the term ‘thin film’ refers to a thickness range below ∼1 μm,89 the thin Li foil/film in the electrochemical field generally refers to a thickness upper limit to ∼50 μm (∼10 mA h cm−2) and it is ultrathin Li when <20 μm (∼4 mA h cm−2). Based on such an understanding, a variety of fabrication strategies are roughly categorized into 3 types: solid phase processes, fusion and solution state processes, and gaseous phase processes. In this section, the detailed strategies for fabricating thin Li are summarized from the abovementioned three directions, and a comparison between them is given.
4.1 Solid phase processes
With a melting point of 180.5 °C the commonly available metallic Li exhibits a solid phase at room temperature. As a member of alkali metals, Li metal possesses some featured properties that facilitate its processing, such as softness, ductility and reactivity with proper polar solvents.
4.1.1 Mechanical rolling.
The most common Li metal products with a thickness of several hundred microns or above, regardless of the form (sheet, disk, strip, etc.), are obtained from hydraulic extrusion of Li ingots. Currently, the most widespread method for thinning Li metal is mechanical rolling, as also adopted by other metals. Generally, calendaring presses bulk Li down to a thickness of ∼100 μm with ease. Further reducing the thickness demands multiple calendaring steps, simultaneously with delicate control of the calendaring pressure and speed. This greatly increases the cost (up to one or more orders of magnitude), but has a limited effect,38 rendering a thickness above 50 μm. Due to the poor mechanical strength and the stickiness of metallic Li, it is extremely challenging or even impossible to fabricate ultrathin Li via simple mechanical rolling without any extra treatments since Li metal would crack in thickness reduction and easily be torn when detaching from the rollers. Given this, some modifications targeting different components of the rolling systems were designed.
As pointed out in Fig. 6a, the first scheme of modification is towards the roller, which is generally made of stainless steel. Since pure Li reacts with Cr2O3, an oxide derived from the alloy element Cr in stainless steel, it would be difficult to peel off thin Li from rollers. Considering the softness of Li, the stainless-steel roller can be replaced by a polymer-based one with acceptable mechanical strength. The polymer does not react with Li and simultaneously possesses a smooth surface and low surface energy to reduce asperity and stickiness.90 In such a case, Li metal can be rolled to a thickness of ∼40 μm. Instead of using polymer rollers, coating the stainless-steel one with specific polymers is also a feasible choice. Taking advantage of the excellent thermal conductivity of the metallic roller, inertness of the polymer coating layer, and easier mechanical strength transition of Li metal with temperature, cooling the stainless steel core can harden metallic Li, which facilitates the thinning process.91,92 Likewise, heating the stainless-steel core would also help thin Li by shifting the solid to semi-solid.93 However, this strategy needs auxiliary components, such as a base layer, to bear the non-free-standing semi-solid film.
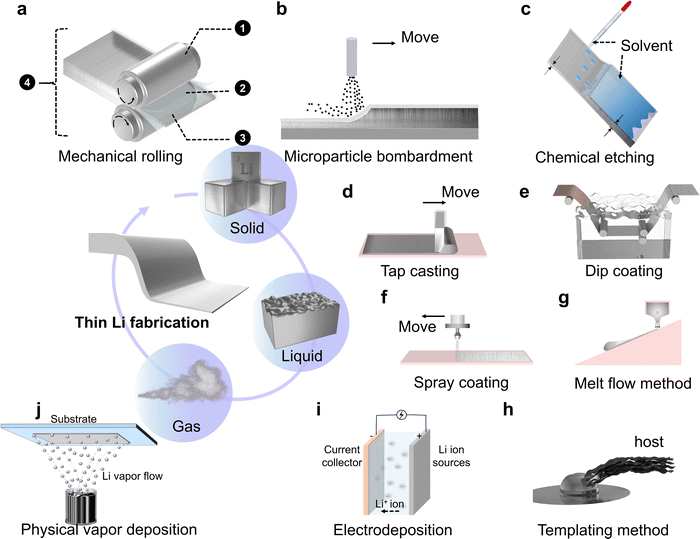 |
| Fig. 6 Concepts and strategies for thin Li fabrication. These strategies can be categorized into 3 types: (a–c) solid phase processes, (d–i) liquid phase processes, and (j) gaseous phase processes. (a) Mechanical rolling. A thick Li sheet is calendared by working rollers to narrow down the thickness. The marked numbers represent different schemes of modification towards the rolling system: (1) rollers, (2) the interlayer between rollers and metallic Li, (3) the component of metallic Li, and (4) the operation parameters of the whole mechanical rolling system. (b) Microparticle bombardment. A relatively thick Li sheet is sandwiched between an inert bottom hard substrate and a top protective polymer layer, and is bombarded by countless microparticles. (c) Chemical etching. The thick Li is treated by specific solvents to dissolve the Li to realize the thinning target. (d) Tape casting. (e) Dip coating. (f) Spray coating. (g) Melt flow method. (h) Templating method. (i) Electrodeposition. (j) Physical vapor deposition. | |
This introduces the second scheme of modification, an interlayer between the roller and Li metal. Firstly, since a thin Li foil, especially the ultrathin one, is too soft to be free-standing, substrates are introduced to aid Li metal thinning.94 Secondly, enlightened by the thin layer forming process of hard metals (e.g., Fe, Ni, Cu) where greases are called for help, a similar strategy is put forward to ameliorate Li metal sticking to the roller. The difference exists in a much higher reactivity of the alkali metal than traditional metals. Thus, a series of selected hydrocarbon compounds that are inert to Li metal were initially proposed as lubricating agents.95,96 Nevertheless, these compounds add an extra burden due to their insulating and insoluble characteristics. Specific post-treatment is needed to remove the lubricant before thin Li foils are laminated with other battery components to eliminate adverse effects, which increases manufacturing cost and risks of contaminating newly exposed Li. In view of this, organic solvents for Li batteries,97 specially designed lubricating additives,98,99 a volatile methyl siloxane lubricant,100 and polymers with specific formulations101 are demonstrated as feasible lubricants to promote detachment of thin Li. Accompanying with a single lubricant, a polymer film is applied to avoid Li sticking to the roller.102 As a separating layer, Sb2O3 powders are also demonstrated to enable ultrathin Li (15.5 μm) fabrication.103 From a different perspective, if there is a support layer whose adhesive force with Li is stronger than that between the roller and Li, the thinning process can also go on wheels. Such is the case that China Energy Lithium Co., Ltd. disclosed a functionalized surface layer on the substrate, which can react with metallic Li to form an SEI substance to motivate the subtraction operation to 5 μm.104
A brief retrospect of the abovementioned engineering examples indicates that all of them used pure extruded Li sheets as the feedstock. The intrinsic properties of Li cause difficulties in the thin layer forming process. Moreover, there are slip lines on the surface of Li metal due to deformation and recrystallization, which would act as defects in electrochemical stripping/plating.105,106 Instead of passively eliminating the adhesion by incorporating extra interlayers, the third scheme of mechanical rolling modification focuses on positively changing the constituent of Li metal. Alloys or composites are known to amplify merits and shrink demerits of a single component. Thus, a series of Li alloys (e.g., Li–Mg, Li–Al, Li–Zn) were fabricated as ingots and then went through the mechanical rolling procedure to reduce their thickness. With the involvement of alloy elements, the mechanical strength increases and the adhesive probability decreases.107,108 Compositing Li with carbon fibers is also demonstrated to realize 5–20 μm ultrathin Li.109 Instead of taking the bulk Li or its derivatives as the precursor, the feedstock can also shift to the stabilized Li metal powders (SLMPs). SLMPs generally refer to a kind of tens micrometer-sized Li metal particles that are fabricated via melting dispersion and droplet emulsion technique and have a nanometer-scale protective layer (e.g. Li2CO3) to stabilize them in dry air.110–114 With such building blocks, a simple compacting procedure gets the thickness further decreased for the LMAs, which present improved electrochemical performance compared to the Li foil counterpart due to reduced current density and enhanced ion conductivity of SEI layers on the compacted SLMPs.115–117 However, a concern arises for SLMPs since particles are easy to scatter in spraying before calendaring, which would result in unevenness. To ameliorate such a dilemma, SLMPs are mixed with compatible solvents and binders to formulate a slurry for tape casting or printing, followed by solvent evaporation and rolling, which enables facile and controllable thin Li fabrication.118–120
After modifying the single component of a mechanical rolling system, the last scheme is towards the tuning of operation parameters, which involves the collaboration of multiple components. By applying two or more pairs of working rollers whose surfaces are coated with lubricants or polymers, high-purity metallic Li precursors go through the gaps in between. In this process, the compression ratio, rate and temperature of each pair of rollers, the number of roller pairs, and the parameter variation between adjacent rollers are all delicately controlled.121–124 The combination of different parameters gives birth to more advanced rolling systems, which would increase the efficiency and scalability of thin Li manufacturing. Heretofore, mechanical rolling is relatively the most mature and widespread method for thin Li fabrication.
4.1.2 Microparticle bombardment.
Similar to the mechanism of mechanical rolling by applying stress to force the soft Li metal thinning, a noncontact microparticle bombardment technique was proposed.125 As schematically sketched in Fig. 6b, a relatively thick Li sheet sandwiched between an inert bottom hard substrate and a top protective polymer layer is bombarded by countless microparticles carried by a fluid. The high-speed microparticles strike the protective polymer layer and the impact force is conducted to the Li sheet, which compresses it to reduce thickness. As choices, the microparticles can be volatile dry ice, nonvolatile Al2O3, Si3N4, MgO and glasses, and others. The protective polymer layer does not react with metallic Li and has enough strength to resist the bombardment of fluid flow containing specific microparticles. For example, the protective polymer can be polyethylene (PE), polypropylene (PP), polyethylene terephthalate (PET), or polyimide (PI). By tuning the bombardment times, a thickness ranging from 1 to 50 μm can be easily achieved.
4.1.3 Chemical etching.
Before the electrochemical process, extremely reactive Li is generally treated with specific care to avoid possible corrosion by controlling the working atmosphere to be inert or with ultralow humidity, applying protective layers, and others. By reviewing metal processing technologies, a method that harnesses the corrosive reaction between metal samples and suitable chemicals gets our attention. As exemplified in the fabrication of printed circuit boards, desirable patterns are created by Cu etching,126 which is no doubt a promising subtractive manufacturing direction. Informed by this, we noticed there already have been similar trials for Li metal. For example, researchers have tried to use a variety of organic solvents to prepare metallographic specimens of Li metal single crystals.105 It was discovered that neither inert nor violently reactive solvents, but organic liquids with a moderate and steady surface reaction with the alkali metals were feasible, such as ketones. In addition, considering the possible natively formed impurities on the surface of commercially available Li products which would significantly affect electrochemical performance, Zheng and coworkers proposed to shortly react the Li product with naphthalene solution in tetrahydrofuran.127 Such a treatment removed surface films, and exposed a fresh and flat lithium surface. The one common feature for these trials is that all of them operated for a short time, and therefore the reaction zone is limited to the surface layer. In this regard, the process can be termed chemical polishing. As a truly chemical thinning strategy, Hu et al. introduced a method based on Lewis acid-base reaction between thick Li and naphthalene.128 By prolonging the reaction time, increasing the concentration of the etching solvent, and controlling the temperature and stirring condition, thin Li down to ∼10 μm can be efficiently obtained (Fig. 6c). Moreover, the etching solvent after thinning Li metal possesses a strong reductive ability, and thus can be further utilized as a multifunctional reagent. Finally, the free Li+ ions in the waste solution can be reextracted as a new Li source for the synthesis of a variety of key battery materials. The whole process shows superior lithium atom economy.
4.2 Fusion and solution state processes
4.2.1 Fusion processes.
Owing to the low melting point of 180.5 °C, molten Li is readily accessible. In this state, Li melt with a flowable feature and smooth surface, together with stronger maneuverability to its properties (e.g., surface tension, viscosity, wettability), can adapt to a series of liquid engineering methods for thin Li fabrication.
Like spreading an electrode slurry via a doctor blade, molten Li can spread on suitable support layers by a shear force to form thickness-controllable foils (Fig. 6d). There are several feasible practices for this process. Molten Li can be taken up from a bottom bath by brush rollers129,130 or extruded from a top storage tank131,132 to a moving substrate (metal foils or screens that are heat-resistant and inert to molten Li or its alloys, including nickel, copper, iron, molybdenum or their specific alloys, the same below). In the subsequent steps, auxiliary scrapers or rollers are applied to further even and thin the melt layer, simultaneously strengthen the bonding strength between Li and substrates. What is worth noting in this operation is that the viscosity of molten Li needs delicate control, and the movement of a substrate has to match the velocity of applying Li. Taking pure molten Li as the precursor, its spread can be conducted in a more positive way. Considering that metallic Li reacts with a plethora of elemental metals, oxides and nitrides as mentioned in Section 2, constructing a lithiophilic interphase on the supporting layer would greatly prompt the spreading of molten Li by reducing the Gibbs free energy or forming new chemical bonds.59,133 Different from the first practice where Li is relatively still but the substrate moves, here the poured Li positively spreads on the fixed substrate. Moreover, we recently proposed to magnetically actuate molten Li to move forward and form patterns on a series of substrates, which can also realize thin Li fabrication.134 In this research direction, a balance of the volume of poured Li and the area of supporting layers is significant for obtaining thin Li. Moreover, modifying the components of Li, whether formulating Li alloys or composites, can also facilitate tape casting by tuning the surface tension. With the new recipe, technologies such as ink-writing135 or stamping136 were introduced. With the involvement of dopants, newly developed thin Li exhibits lower polarization and more uniform nucleation and growth in the following electrochemical process.133,136
Rather than applying Li melt on the surface, another strategy is carried out by firstly immersing the substrate into and then removing it from a tank of molten Li, followed by cooling the coated pieces.137 This technology is named dip coating or hot dipping, as illustrated in Fig. 6e. In this process, the interfacial contact between molten Li and the substrate becomes significant. For Li, on the premise of having acceptable flowability, its heating temperature is not suggested to be high so as to increase the adhesive force with the support layer. On the substrate side, degreasing and/or roughing treatment is very common.138,139 On this basis, depositing lithiophilic interlayers (e.g., Cu2O) would protect the activated substrate and enhance its wettability.140 Changing the components of a substrate to alloy elements or composites is also a choice.141,142 After the components are determined, the thickness of the coated Li layer is affected by the temperature of molten Li, the withdrawal rate and angle, the time before solidification, and possible subsequent treatment procedures (e.g., rolling). With this hot dipping technology, the thickness lower limit of thin Li is declared to be 0.1 μm.142
Starting from a bottom-up strategy, the technology termed spray coating involves melting Li metal, breaking Li melts into fine droplets, and then depositing the droplet flow to a pre-heated surface. On the heating and advancing surface, countless Li microdroplets fuse together and form a thin film (Fig. 6f).143 Another method was proposed that takes advantage of the equilibrium of forces (gravity, adhesive force) of Li melts on an inclined, heated, but advancing substrate. With the melt flowing downward the substrate, a thin Li film is left on the substrate (Fig. 6g).144 In addition, one of the common strategies in the investigation of LMAs is constructing a 3D host. By designing the structure, surface functional groups, or coating the accessible surface with lithiophilic materials, molten Li can be readily infused into the host so that the great volume change and dendrite growth are greatly alleviated.145,146 However, most of the hosts are thick and therefore carry excessive Li. Moreover, the metal hosts are generally heavy. In light of this, Chen et al. declared the successful fabrication of ultrathin (0.5 to 20 μm) free-standing and mechanically robust Li metal foils with the aid of a thickness controllable graphene oxide host (Fig. 6h).38 By infusing molten Li into expanded graphene layers, the host protects the alkali metal and endows thin Li with enhanced mechanical strength. This templating method introduces a brand-new research direction.
4.2.2 Solution state processes.
Considering the generally liquid electrolyte working environment, electrodeposition is also categorized as liquid engineering technology. In the electrochemical deposition process, theoretically controlling the current density and time would enable the synthesis of thin Li on a conductive layer (Fig. 6i).82 However, due to the extremely high reactivity of metallic Li and the sensitivity of nucleation and growth, plating a flat, compact, and dendrite-free Li layer in nonaqueous electrolytes is a formidable challenge.147 From the thermodynamic perspective, the Nernst equation determines the practical redox potential and therefore the priority of cation reduction. Any impurities in the electrolytes can possibly affect the deposition of Li. Moreover, heterogeneous nucleation and growth are more prone to occur due to adventitious adsorbates or intrinsic defects on the substrate. From the kinetic perspective, sluggish ion transfer and resulting concentration gradient tend to induce dendrite growth. Thus, electrolyte formulations,148 supporting substrate materials,149,150 and operation parameters151 are carefully studied. For example, by controlling the reduction potential of the selected cations to be lower than Li+/Li to repel the approaching Li+ toward protrusions, an electrostatic shielding strategy was proposed to mitigate Li dendrite growth.152 Selecting appropriate substrates, such as those alloying (Au, Ag, Al, etc.) or possessing compatible lattice structure (Cu(100)) with Li, the nucleation overpotential is significantly reduced.153,154 Likewise, increasing the concentration of electrolytes,155 or constructing an interfacial layer to help homogenize Li+ flux are also proposed.156,157 Based on these precautions, a slow deposition process with well-controlled conditions enables a flat and thin Li.
4.3 Gaseous phase processes
Together with mechanical rolling and electrodeposition, physical vapor deposition (PVD) is another frequently applied technique to obtain thin Li. This process includes three basic steps, which are the creation of vapor-phase Li, transportation of the vapor from the source to a substrate, and finally the film growth on a substrate, as schematically illustrated in Fig. 6j. With this technique, different substrates can be applied.158–160 Moreover, the deposited Li exhibits higher purity and surface reactivity compared with mechanical rolling and electrodeposition.161 More importantly, the thickness lower limit of PVD-fabricated Li can reach the nanometer scale, albeit an excessively thin Li is not suitable for large capacity delivery. In practices, PVD is usually carried out to fabricate anodes for thin film batteries.162,163
4.4 A comparison of different strategies
To obtain a more comprehensive understanding of different fabrication strategies, we first summarize the details, such as the lowest achievable thickness of Li, the form of the input and output materials (i.e., pure Li sheet, Li/Cu sheet, etc.), the effect on Li purity/microstructure of various thin Li fabrication strategies, as presented in Table S2, ESI.† Then, independent and overall comparisons are conducted. In the comparison, seven parameters, namely simplicity, safety, scalability, cost-effectiveness, thickness limit, production speed, and related post-treatment of various strategies, are considered. Most of these parameters are just as their names implied, among which simplicity means if a special temperature, pressure, or apparatus is needed, and post-treatment means if extra treatment is needed after obtaining thin Li. The more up-scalable, cost-effective, efficient, simple, and safer a technique is, simultaneously thinner the produced Li and less necessary for post-treatment, more promising a method is. However, it is worth noting that since thin Li fabrication is an emerging topic, most research articles and patents are only at the stage of proposing new ideas, but not deeply discussing all these parameters. Based on these mentioned specifications and our understanding of the working conditions, independent comparisons of detailed technologies are sketched in Fig. 7a-c, which can refer to the abovementioned content in Sections 4.1 to 4.3, while an overall comparison is presented in Fig. 7d.
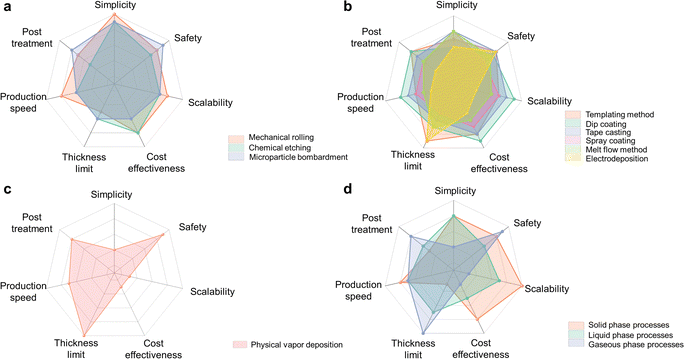 |
| Fig. 7 The comparison of different concepts and technologies for thin Li fabrication. (a) The solid phase processes. (b) The liquid phase processes. (c) The gaseous phase processes. (d) An overall comparison between three classes of technologies. | |
Solid engineering technologies are generally carried out at room temperature. Therefore, they possess the merits of being simple, safe, and up-scalable. As the representative of solid phase processes, mechanical rolling, however, may not easily reach an ultrathin Li due to the poor mechanical property and stickiness of pure Li. When applying lubricants, extra washing steps are necessary and may cause avoidable contaminations. Moreover, slip lines on the surface of the produced thin Li due to deformation and recrystallization would act as defects in electrochemical stripping/plating.105,106 If taking the SLMPs as the precursor, although a further decrease in thickness by mechanical rolling is realized, the fabrication of SLMPs introduces more challenges. It has been discovered that the rolled thin Li has a large number of impurities composed of C, O, and N on the surface compared to thermally evaporated samples.161 When it comes to the fusion processes, a relatively equilibrated performance can be achieved but it needs special care for the significantly enhanced reactivity of molten Li. The solution state electrodeposition is a time-consuming process, and highly dependent on the complex collaboration of electrolyte formulation, substrate, and operation parameters, which limits it to be more suitable for academic study. The PVD technology needs a massive investment to realize the vacuum sealing of the working chambers. In addition, the created vapor will coat on the wall of the vacuum chamber, leading to a waste of materials. In summary, there is no well-rounded technique heretofore and more future endeavors are still urgently needed. Whereas, according to the disclosure of studies, most of the fabricated thin Li foils (including pure Li, Li alloys or composites) present a similar or better electrochemical performance compared to commonly commercialized Li foils.59,119,120,133,136,140 Thus, the as-fabricated thin Li can deliver excellent performance without being affected by, or even benefiting from the different microstructures.164
Reviewing the thin Li fabrication technologies mentioned above, most of them are physical methods and a few correlate with chemistry or electrochemistry. It is envisioned that mechanical engineers, metallurgists, electrochemists, experts in thin film processing, and other fields, can all participate in this field and create new possibilities. However, for those who would shift to this profession in the future, it is worthwhile to emphasize the safety of Li metal engineering in particular. Metallic Li is more reactive than common metals, such as iron, copper, aluminum, etc., even at room temperature. For example, a spark reaction would happen when graphene oxide (GO) films contact with molten Li.27 Thus, an inert gas environment or at least a low-humidity atmosphere (e.g., in a dry room) should be provided to avoid safety risks and guarantee the surface purity of Li. Moreover, although a processing technology seems safe in small scales, the process of making thin high surface area Li inherently introduces significant risk. If this is scaled up to large volumes, the danger increases significantly. Furthermore, while the general process may not be especially dangerous, cleaning systems used to process Li can be extremely dangerous. All these should be taken into consideration in practical operations.
5. What are the application scenarios of thin Li in batteries?
Prompted by the above fabrication technologies, thin Li is easier to access and the likelihood of its application expands. With the involvement of thin Li, the promise of the Li battery will scale new heights by not only allowing the further improvement of widely commercialized LIBs, but also facilitating the development of more advanced electrochemical systems in a practical direction.
5.1 Prelithiation
As presented in Fig. 8a, a typical Li-free anode, such as graphite, pairs with a Li-contained cathode, such as LiCoO2, to give the commercialized LIBs. On this basis, an N/P ratio slightly larger than 1.0 is designed to avoid the deposition of Li metal on the anode side and problems arising therefrom, making the capacity of LIBs controlled by the limited Li from cathodes. However, Li ions are unavoidably consumed, especially in the first few cycles, to form SEI on the anode side. The initial CE thus is apparently lower than 100%, even resulting in a Li loss of up to 40% of the total capacity when some alloy-type anodes are applied,165 which significantly lowers energy density. Therefore, preloading a precise amount of Li (prelithiation) to compensate for the expected Li loss would greatly enhance the electrochemical performance. To date, among a variety of proposed prelithiation strategies,166,167 the two most promising are applying SLMPs or Li foils no matter by mechanical mixing or self-discharging with active anode materials. SLMPs were once more prevalent than Li foils since the commercially available Li foils were too thick to meet the small but precise needs, although the powders are more dangerous and difficult to distribute homogeneously. At present, with more ingenious strategies for thin Li fabrication, the precise Li compensation would be simpler by just attaching the ultrathin Li onto an anode (Fig. 8b), followed by common battery assembling steps. Here, due to the determination of the irreversible capacity of the corresponding anode materials ahead of schedule, researchers can calculate precisely the required lithium mass or volume for prelithiation. Thus, the degree of prelithiation is adjusted with high accuracy and the ultrathin Li foils are completely consumed, namely without residues in the anode. Therefore, no post treatment is needed after prelithiation. As a demonstration, heretofore graphite, silicon,38 hard carbon,168 alloy anodes169 have been successfully prelithiated by ultrathin Li foils and exhibit an initial CE approaching 100%. In addition, it is discovered that ultrathin Li foils are more efficient for prelithiation, especially when there are holes drilled on them.122,170 The introduced holes facilitate the permeation of organic electrolytes, but also enable the release of possible gases.
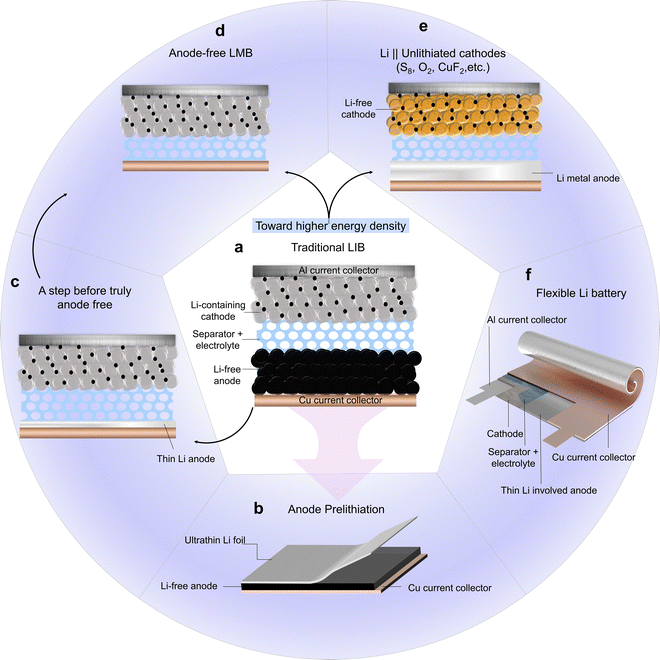 |
| Fig. 8 (a) The components and configuration of a traditional LIB. The promising applications of thin Li in a battery system: (b) prelithiation of traditional Li-free anodes; (c) compensation for Li loss in an LMB with Li-containing cathodes as a step before absolutely (d) anode-free LMBs; (e) anodes of a battery consisting of Li-free cathodes; and (f) flexible Li batteries. | |
5.2 A step before truly anode free
To achieve higher energy density, an anode-free cell configuration by pairing the Li-containing cathode with a bare Cu current collector on the anode side (Fig. 8d) would become one of the ultimate choices.171 However, the challenge is the limited cycle life due to the seriously irreversible consumption of Li in such a configuration. Faced with this, great efforts have been made to prolong the lifespan.172 Since the earliest investigation on “Li-free” solid-state thin-film batteries,173 the best developed anode-free high-energy-density battery can realize a 90% and 80% capacity retention after 300 cycles in the coin cell and pouch cell configuration, respectively, up to now, which is a huge improvement.72 Given this, applying an ultrathin LMA that occupies a very small volume of the cell as a source for Li compensation (Fig. 8c) would further improve the cycle life, but not deteriorate the energy density much. This is verified in Fig. 5b,where the difference between the energy density of the battery systems composed of LiCoO2 and LMA with a thickness of 0 (anode-free configuration with a Cu collector on the anode side) and 20 μm is only 10 W h kg−1. It was witnessed that the Battery500 consortium has taken this measure to achieve the proposed goal of energy density, and phase I (the first 5 year research stage) has achieved 350 W h kg−1 in practical conditions.35 Similarly, an MIT spinout demonstrated an “anode-free” LMB with ultrathin Li and safe electrolyte.174 Clearly, the combination of thin Li and Li-containing cathodes is a possible step before achieving a truly anode-free configuration.
5.3 Anode for unlithiated cathodes
If the application of thin Li in prelithiation and in “anode-free” configuration can merely be regarded as playing a supporting role, taking thin Li as the Li+ ion source in a battery system would further illustrate its significance. As another choice for achieving higher energy density, it can shift to applying Li-free cathodes (Fig. 8e), which possess much higher specific capacity (e.g., S8, O2, CuF2)175 than Li-containing cathode materials (e.g., LiCoO2, LiFePO4). In this case, the Li source coming from LMAs is the ultimate choice. With the combination of a thin but high-specific-capacity anode and cathode, the energy density of a single cell increases, which enables multilayer electrodes to stack in tandem without losing a flexible feature simultaneously.
5.4 Flexible batteries
Nowadays, the emergence of compact and wearable electronics urges the coming of matched energy storage units with shape amenability. To meet the satisfaction of new demands, great efforts have been made, such as the design of cable or wire-shaped cells.176,177 In such a configuration, a pure Li wire or a yarn composed of Li deposited on other fiber substrates is usually incorporated with a flexible cathode.178–180 Afterwards, multiple cable or wire-shaped cells are knitted into a larger battery module if necessary. However, it is worth noting that the present single-wire-like cell with a cable structure is commonly thick in the radial direction to at least several hundred microns and it is inevitable many intervals exist between single wire batteries when weaving into battery modules. Under such a circumstance, the obtained flexible features are at the expense of the energy density. At present, with the emergence of high specific capacity thin Li foils, a high-energy-density flexible battery would be more promising by pairing a properly designed cathode with the thin Li substituted traditional chunky anode.136 The new-generation fully flexible battery containing thin Li foils can be realized by designing specific structures, which is shown in Fig. 6d of the reference for inspiration.150Fig. 8f is a zoomed-in schematic diagram of part of the flexible batteries containing thin Li foils. It would meet the ever-increasing demand from wearable electronics for display, health monitoring, and other applications.
6. An outlook on thin Li
6.1 New challenges and countermeasures
Bearing in mind firstly that thin Li is still a highly reactive metal, the intrinsic challenges of LMA such as the tendency of dendrite growth and extremely high thermodynamic reactivity to organic electrolytes remain stringent, which are not further elaborated here but referred to elsewhere.181 More importantly, new obstacles emerge due to the narrowing of the LMA thickness. In the case of thin Li anodes, the irreversible Li loss would result in fast capacity fade since there is less Li reservoir for the compensation of irreversible Li loss. As illustrated in Fig. 9a, the disparity in dissolution rate of different sites on a thin Li anode initially induces pits, which in the subsequent cycles quickly evolve into cracks. These cracks run through the thickness and separate the entirety into several scattered (and thus electrochemically inactive) parts when there is no current collector. In comparison to the occurrence of dendrite penetration-induced shorting or depletion of Li sources, this failure comes earlier and proceeds as a brand-new mode for thin Li without a current collector. Due to the different redox potentials, thin LMA easily forms a galvanic couple with Cu when taking it as the current collector, resulting from possible flaws of thin Li that expose Cu to the electrolyte working environment. In this case, Li corrosion goes on via a charge transfer from Cu to the electrolyte, as illustrated in Fig. 9b,182,183 which causes extra Li loss. In addition, the galvanic corrosion further complicates the understanding of CE. As mentioned in Section 3, there is not much Li to compensate for Li+ loss in thin Li cases, which reflects a more realistic CE, albeit one that is not satisfactory. It is known that the average CE (CEavg) for Li plating/stripping processes on the anode side of an electrochemical system determines the cycle life. Fig. 9c illustrates the correlation between the cycle life and the thickness of LMA and corresponding CEavg of a battery consisting of a cathode with a capacity of 4 mA h cm−2. It is only when the CEavg is larger than 80% that an anode-free battery can run one cycle and a battery with 50 μm LMA run 13.5 cycles (see Note S2, ESI† for more details). For all the cells to possess a cycle life up to hundred times, a CEavg of about 99.9% is necessary, which is a great challenge. In a word, more challenging the development of practical LMBs would be by introducing thin Li, albeit it is necessary.
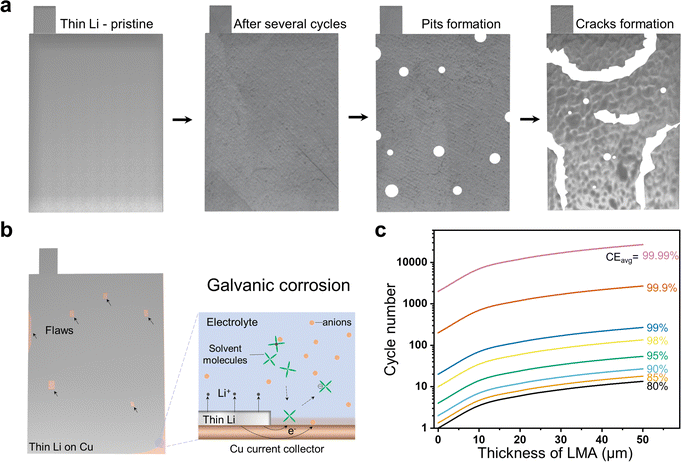 |
| Fig. 9 (a) The quick failure of thin Li anodes when there is no current collector due to the formation of cracks that run through the thickness and separate the entirety into several scattered pieces. (b) The galvanic corrosion of a thin Li loaded on a Cu current collector resulting from possible flaws of thin Li that expose Cu to the electrolyte working environment. (c) The correlation between the cycle life and the thickness of LMA, and the corresponding CEavg of a battery consisting of a cathode with a capacity of 4 mA h cm−2. It assumes that a 100% state of charge is realized and the possible Li losses only occur on the LMA side. A more detailed calculation is available in Note S2, ESI† or ref. 37. | |
To solve these problems, countermeasures to enable the function of thin Li are indispensable. From the anode current collector to the electrolyte zones, a series of strategies for stable thin Li performance have been demonstrated. Considering that the thin Li prepared by mechanically rolling SLMPs on Cu current collector is possible to peel off, a submicron-level carbon interlayer was introduced between them, which enhances the adhesion of both components and also helps the homogeneous deposition and nucleation of Li ions.184 To ensure the integrity of thin Li during repeated cycling, ultrathin mechanically robust and conductive hosts are incorporated.38 To protect the reactive thin Li, gas treating steps185–188 or other protective layer construction189–192 are included before assembling. A common feature of these strategies is that the introduced extra layers are all proportional to the thickness of the Li foil. Thus, they are also ultrathin and should not add too much weight or volume to the battery system. Additives are also introduced to formulate functional electrolytes.193,194 Moreover, the cooperation of thin Li and solid-state electrolytes is promising.195 With the collaboration of several strategies, the application of thin Li would become more feasible.
6.2 Possible fabrication methods
The essence of developing thin Li technology is to inherit the ideal merits of LMAs, such as the high specific capacity, but not be affected by the cumbersomely extra Li. Based on this start point and learning from the existing processing technologies, reveries on more possible thin Li fabrication methods are presented here. A thick metal foil after repeated folding and calendaring was transformed into 2D metal nanosheets.196 Similarly, interpenetrated Li-MXene or Li–Li alloy structures have been demonstrated.28,197 If the interpenetrated structure can be separated layer by layer, thin Li would be obtained easily. Reduced graphene oxide or MXene, which is ultralight and tunable in thickness, has been applied for the fabrication of thin Li.38,150 If researchers can further identify hosts with similar features, thin Li is also more accessible. Moreover, inspired by SLMPs, microparticles of Li–carbon matrix composites have been successfully fabricated by the Chen group, which can also be further processed into thin Li products.198–202 Nano-scaled Li metal powders are also a feasible choice.203 From the point of liquid phase engineering, there appears the concept of non-Newtonian semisolid or semiliquid LMAs204,205 and alkali metal-based organic liquid metal solution206,207 by suspending or dissolving Li into specific solvent systems. Combining the features of fluid, these Li counterparts are promising for thin Li fabrication by printing or brushing. More perspective technologies would be unfolded with interdisciplinary collaborations.
7. Conclusion
To develop practical LMBs, each element in this battery system needs a comprehensive understanding and investigation. Due to the difficulties in engineering Li metal into thin foil anode in the past and the chemical and electrochemical properties of Li metal, the thickness of LMAs has historically received less attention. Being aware of this, the tutorial review highlights the importance of applying thin Li (<50 μm, preferred to ≤30 μm) instead of thick Li for practical rechargeable Li batteries (Fig. 10). On the premise of normal operation, it is less Li that releases the full potential of an LMA, promises higher energy density of a cell, reflects a realistic CE and cycle life of batteries, instead of being hallucinated by results brought about by excessive Li. Meanwhile, thin Li saves the cost of raw materials. In a word, less Li in a usable extent means more than excessive Li towards the realization of high-energy-density LMBs in an economical way. Attracted by the charm of thin Li, a number of solid, fusion, solution and vapor state processes are developed to realize thin Li manufacturing. The encouraging results of emerging technologies for thin Li fabrication would greatly cut the spending when purchasing thin Li. Nevertheless, there is no well-rounded process heretofore that can simultaneously satisfy the requirement of various parameters, such as simplicity, safety, scalability, cost-effectiveness, thickness limit, production speed, and post-treatment. Thus, more ingenious and pragmatic approaches are still urgently needed. In this regard, researchers in different communities, such as mechanical engineering, metallurgy, electrochemistry, thin film processing, and other areas, can and are encouraged to participate in this subject and create new possibilities. With the assistance of the currently attainable thin Li, more efficient prelithiation, improved battery performance of commercialized LIBs, and more advanced battery systems are enabled. Due to the extreme reactivity of alkali metal Li, it is predictable what accompanies thin Li in applications is more challenges due to the narrowing down of Li foil thickness. To achieve anode metallic Li, much more efforts are necessary.
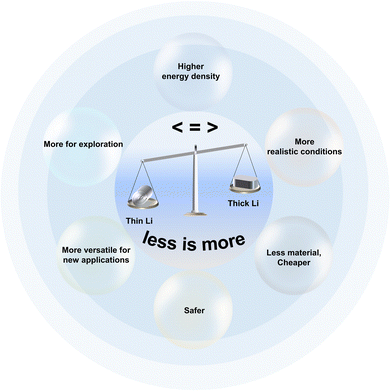 |
| Fig. 10 More opportunities and challenges accompany thin Li than thick Li. | |
Conflicts of interest
There are no conflicts to declare.
Acknowledgements
This work is supported by the National Natural Science Foundation of China (92163120, 5202780089) and the Fundamental Research Funds for the Central Universities.
References
- R. Schmuch, R. Wagner, G. Hörpel, T. Placke and M. Winter, Nat. Energy, 2018, 3, 267–278 CrossRef CAS.
- X. Zeng, M. Li, D. Abd El-Hady, W. Alshitari, A. S. Al-Bogami, J. Lu and K. Amine, Adv. Energy Mater., 2019, 9, 1900161 CrossRef.
- K. Wang, K. Jiang, B. Chung, T. Ouchi, P. J. Burke, D. A. Boysen, D. J. Bradwell, H. Kim, U. Muecke and D. R. Sadoway, Nature, 2014, 514, 348–350 CrossRef CAS PubMed.
- J. Kersey, N. D. Popovich and A. A. Phadke, Nat. Energy, 2022, 7, 664–674 CrossRef.
- A. Bills, S. Sripad, W. L. Fredericks, M. Singh and V. Viswanathan, ACS Energy Lett., 2020, 5, 663–668 CrossRef CAS.
- Federal Consortium for Advanced Batteries, National Blueprint for Lithium Batteries 2021-2030, https://www.energy.gov/eere/vehicles/articles/national-blueprint-lithium-batteries, (accessed July 23, 2022).
- European Economic and Social Committee, Strategic Action Plan on Batteries (report), https://www.eesc.europa.eu/en/our-work/opinions-information-reports/opinions/strategic-action-plan-batteries-report, (accessed July 30, 2022).
- The State Council of the People's Republic of China, 'Made in China 2025' plan issued, https://english.www.gov.cn/policies/latest_releases/2015/05/19/content_281475110703534.htm, (accessed July 23, 2022).
- Pacific Northwest National Laboratory, The Innovation Center for Battery500 Consortium, https://www.pnnl.gov/projects/battery500-consortium, (accessed July 23, 2022).
- Y. Cao, M. Li, J. Lu, J. Liu and K. Amine, Nat. Nanotechnol., 2019, 14, 200–207 CrossRef CAS PubMed.
- S. Chen, C. Niu, H. Lee, Q. Li, L. Yu, W. Xu, J.-G. Zhang, E. J. Dufek, M. S. Whittingham, S. Meng, J. Xiao and J. Liu, Joule, 2019, 3, 1094–1105 CrossRef CAS.
- M. Ue, K. Sakaushi and K. Uosaki, Mater. Horiz., 2020, 7, 1937–1954 RSC.
- Z. Lin, T. Liu, X. Ai and C. Liang, Nat. Commun., 2018, 9, 5262 CrossRef CAS PubMed.
- J. Betz, G. Bieker, P. Meister, T. Placke, M. Winter and R. Schmuch, Adv. Energy Mater., 2019, 9, 1803170 CrossRef.
- H. Li, Joule, 2019, 3, 911–914 CrossRef CAS.
- Y. Kuang, C. Chen, D. Kirsch and L. Hu, Adv. Energy Mater., 2019, 9, 1901457 CrossRef.
- J. S. Sander, R. M. Erb, L. Li, A. Gurijala and Y. M. Chiang, Nat. Energy, 2016, 1, 16099 CrossRef CAS.
- Z. Ju, S. T. King, X. Xu, X. Zhang, K. U. Raigama, K. J. Takeuchi, A. C. Marschilok, L. Wang, E. S. Takeuchi and G. Yu, Proc. Natl. Acad. Sci. U. S. A., 2022, 119, e2212777119 CrossRef CAS PubMed.
- X. Zhang, Z. Hui, S. T. King, J. Wu, Z. Ju, K. J. Takeuchi, A. C. Marschilok, A. C. West, E. S. Takeuchi, L. Wang and G. Yu, Nano Lett., 2022, 22, 2521–2528 CrossRef CAS PubMed.
- Y. S. Zhang, N. E. Courtier, Z. Zhang, K. Liu, J. J. Bailey, A. M. Boyce, G. Richardson, P. R. Shearing, E. Kendrick and D. J. L. Brett, Adv. Energy Mater., 2022, 12, 2102233 CrossRef CAS.
- N. Kang, Y. Lin, L. Yang, D. Lu, J. Xiao, Y. Qi and M. Cai, Nat. Commun., 2019, 10, 4597 CrossRef PubMed.
- X. Yang, K. R. Adair, X. Gao and X. Sun, Energy Environ. Sci., 2021, 14, 643–671 RSC.
- M. Zhao, B.-Q. Li, H.-J. Peng, H. Yuan, J.-Y. Wei and J.-Q. Huang, Angew. Chem., Int. Ed., 2020, 59, 12636–12652 CrossRef CAS PubMed.
-
E. Jarratt, New lessons from the epic story of Moli Energy,the Canadian pioneer of rechargeable lithiumbattery technology, https://electricautonomy.ca/2020/09/18/moli-energy-lithium-battery-technology/, (accessed August 10, 2022).
- C. Fang, X. Wang and Y. S. Meng, Trends Chem., 2019, 1, 152–158 CrossRef CAS.
- A. Fu, C. Wang, J. Peng, M. Su, F. Pei, J. Cui, X. Fang, J.-F. Li and N. Zheng, Adv. Funct. Mater., 2021, 31, 2009805 CrossRef CAS.
- D. Lin, Y. Liu, Z. Liang, H.-W. Lee, J. Sun, H. Wang, K. Yan, J. Xie and Y. Cui, Nat. Nanotechnol., 2016, 11, 626–632 CrossRef CAS PubMed.
- M. Wan, S. Kang, L. Wang, H.-W. Lee, G. W. Zheng, Y. Cui and Y. Sun, Nat. Commun., 2020, 11, 829 CrossRef CAS PubMed.
- J. Wu, Z. Rao, X. Liu, Y. Shen, C. Fang, L. Yuan, Z. Li, W. Zhang, X. Xie and Y. Huang, Adv. Mater., 2021, 33, 2007428 CrossRef CAS PubMed.
- Q. Zhou, S. Dong, Z. Lv, G. Xu, L. Huang, Q. Wang, Z. Cui and G. Cui, Adv. Energy Mater., 2020, 10, 1903441 CrossRef CAS.
- M. Genovese, A. J. Louli, R. Weber, S. Hames and J. R. Dahn, J. Electrochem. Soc., 2018, 165, A3321–A3325 CrossRef CAS.
- J. Xiao, Q. Li, Y. Bi, M. Cai, B. Dunn, T. Glossmann, J. Liu, T. Osaka, R. Sugiura, B. Wu, J. Yang, J.-G. Zhang and M. S. Whittingham, Nat. Energy, 2020, 5, 561–568 CrossRef CAS.
- P. Albertus, S. Babinec, S. Litzelman and A. Newman, Nat. Energy, 2018, 3, 16–21 CrossRef CAS.
- J. Liu, Z. Bao, Y. Cui, E. J. Dufek, J. B. Goodenough, P. Khalifah, Q. Li, B. Y. Liaw, P. Liu, A. Manthiram, Y. S. Meng, V. R. Subramanian, M. F. Toney, V. V. Viswanathan, M. S. Whittingham, J. Xiao, W. Xu, J. Yang, X.-Q. Yang and J.-G. Zhang, Nat. Energy, 2019, 4, 180–186 CrossRef CAS.
- C. Niu, D. Liu, J. A. Lochala, C. S. Anderson, X. Cao, M. E. Gross, W. Xu, J.-G. Zhang, M. S. Whittingham, J. Xiao and J. Liu, Nat. Energy, 2021, 6, 723–732 CrossRef CAS.
- P. Shi, X.-B. Cheng, T. Li, R. Zhang, H. Liu, C. Yan, X.-Q. Zhang, J.-Q. Huang and Q. Zhang, Adv. Mater., 2019, 31, 1902785 CrossRef PubMed.
- Y. Zhu, V. Pande, L. Li, B. Wen, M. S. Pan, D. Wang, Z.-F. Ma, V. Viswanathan and Y.-M. Chiang, Proc. Natl. Acad. Sci. U. S. A., 2020, 117, 27195–27203 CrossRef CAS PubMed.
- H. Chen, Y. Yang, D. T. Boyle, Y. K. Jeong, R. Xu, L. S. de Vasconcelos, Z. Huang, H. Wang, H. Wang, W. Huang, H. Li, J. Wang, H. Gu, R. Matsumoto, K. Motohashi, Y. Nakayama, K. Zhao and Y. Cui, Nat. Energy, 2021, 6, 790–798 CrossRef CAS.
- M. Winter, B. Barnett and K. Xu, Chem. Rev., 2018, 118, 11433–11456 CrossRef CAS PubMed.
- K. Hans Wedepohl, Geochim. Cosmochim. Acta, 1995, 59, 1217–1232 CrossRef.
- National Minerals Information Center, Lithium Statistics and Information, https://pubs.usgs.gov/periodicals/mcs2022/mcs2022-lithium.pdf, (accessed August 2, 2022).
- S. H. Mohr, G. M. Mudd and D. Giurco, Minerals, 2012, 2, 65–84 CrossRef.
- B. Swain, Sep. Purif. Technol., 2017, 172, 388–403 CrossRef CAS.
-
T. Tran and V. T. Luong, in Lithium Process Chemistry, ed. A. Chagnes and J. Światowska, Elsevier, Amsterdam, 2015, pp. 81–124 DOI:10.1016/B978-0-12-801417-2.00003-7.
- A. Battistel, M. S. Palagonia, D. Brogioli, F. La Mantia and R. Trócoli, Adv. Mater., 2020, 32, 1905440 CrossRef CAS PubMed.
- V. Flexer, C. F. Baspineiro and C. I. Galli, Sci. Total Environ, 2018, 639, 1188–1204 CrossRef CAS PubMed.
-
P. Christmann, E. Gloaguen, J.-F. Labbé, J. Melleton and P. Piantone, in Lithium Process Chemistry, ed. A. Chagnes and J. Światowska, Elsevier, Amsterdam, 2015, pp. 1–40 DOI:10.1016/B978-0-12-801417-2.00001-3.
- National Minerals Information Center, Lithium Statistics and Information, https://d9-wret.s3.us-west-2.amazonaws.com/assets/palladium/production/mineral-pubs/lithium/lithimcs05.pdf, (accessed August 2, 2022).
- D. R. Sadoway, JOM, 1998, 50, 24–26 CrossRef.
- K. Kalantar-Zadeh, J. Tang, T. Daeneke, A. P. O’Mullane, L. A. Stewart, J. Liu, C. Majidi, R. S. Ruoff, P. S. Weiss and M. D. Dickey, ACS Nano, 2019, 13, 7388–7395 CrossRef CAS PubMed.
-
R. P. Schultz, Lithium: Measurement of Young's Modulus and Yield Strength, B. Fermi National Accelerator Lab. (FNAL), IL (United States), United States, 2002 Search PubMed.
-
S. Tariq, K. Ammigan, P. Hurh, R. Schultz, P. Liu and J. Shang, Proceedings of the 2003 Particle Accelerator Conference, IEEE, Portland, OR, USA, 2003.
- A. Masias, N. Felten, R. Garcia-Mendez, J. Wolfenstine and J. Sakamoto, J. Mater. Sci., 2019, 54, 2585–2600 CrossRef CAS.
- L. L. Dienemann, A. Saigal and M. A. Zimmerman, J. Electrochem. Energy Convers. Storage, 2021, 18, 040908 CrossRef CAS.
- T. Sedlatschek, J. Lian, W. Li, M. Jiang, T. Wierzbicki, M. Z. Bazant and J. Zhu, Acta Mater., 2021, 208, 116730 CrossRef CAS.
- R. Usiskin, Y. Lu, J. Popovic, M. Law, P. Balaya, Y.-S. Hu and J. Maier, Nat. Rev. Mater., 2021, 6, 1020–1035 CrossRef CAS.
- H. B. Michaelson, J. Appl. Phys., 1977, 48, 4729–4733 CrossRef CAS.
- B. B. Fitch, M. Yakovleva, Y. Li, I. Plitz, A. Skrzypczak, F. Badway, G. G. Amatucci and Y. Gao, ECS Trans., 2007, 3, 15–22 CrossRef.
- S.-H. Wang, J. Yue, W. Dong, T.-T. Zuo, J.-Y. Li, X. Liu, X.-D. Zhang, L. Liu, J.-L. Shi, Y.-X. Yin and Y.-G. Guo, Nat. Commun., 2019, 10, 4930 CrossRef PubMed.
- J.-l Ma, F.-l Meng, Y. Yu, D.-P. Liu, J.-M. Yan, Y. Zhang, X.-B. Zhang and Q. Jiang, Nat. Chem., 2019, 11, 64–70 CrossRef CAS PubMed.
- W. Jia, Y. Liu, Z. Wang, F. Qing, J. Li, Y. Wang, R. Xiao, A. Zhou, G. Li, X. Yu, Y.-S. Hu, H. Li, Z. Wang, X. Huang and L. Chen, Sci. Bull., 2020, 65, 1907–1915 CrossRef CAS PubMed.
- H.-F. Huang, Y.-N. Gui, F. Sun, Z.-J. Liu, H.-L. Ning, C. Wu and L.-B. Chen, Rare Met., 2021, 40, 3494–3500 CrossRef CAS.
- J. Wang, H. Wang, J. Xie, A. Yang, A. Pei, C.-L. Wu, F. Shi, Y. Liu, D. Lin, Y. Gong and Y. Cui, Energy Storage Mater., 2018, 14, 345–350 CrossRef.
- D. N. Ruzic, W. Xu, D. Andruczyk and M. A. Jaworski, Nucl. Fusion, 2011, 51, 102002 CrossRef.
- Y. Fan, T. Tao, Y. Gao, C. Deng, B. Yu, Y. Chen, S. Lu and S. Huang, Adv. Mater., 2020, 32, 2004798 CrossRef CAS PubMed.
- G. N. Lewis and F. G. Keyes, J. Am. Chem. Soc., 1913, 35, 340–344 CrossRef CAS.
- M. V. Reddy, A. Mauger, C. M. Julien, A. Paolella and K. Zaghib, Materials, 2020, 13, 1884 CrossRef CAS PubMed.
- H. Zheng, J. Li, X. Song, G. Liu and V. S. Battaglia, Electrochim. Acta, 2012, 71, 258–265 CrossRef CAS.
- R. Zhao, J. Liu and J. Gu, Appl. Energy, 2015, 139, 220–229 CrossRef CAS.
- R. Weber, M. Genovese, A. J. Louli, S. Hames, C. Martin, I. G. Hill and J. R. Dahn, Nat. Energy, 2019, 4, 683–689 CrossRef CAS.
- O. Lohrberg, S. Maletti, C. Heubner, M. Schneider and A. Michaelis, J. Electrochem. Soc., 2022, 169, 030543 CrossRef.
- Y. Qiao, H. Yang, Z. Chang, H. Deng, X. Li and H. Zhou, Nat. Energy, 2021, 6, 653–662 CrossRef CAS.
- B. Son, M.-H. Ryou, J. Choi, S.-H. Kim, J. M. Ko and Y. M. Lee, J. Power Sources, 2013, 243, 641–647 CrossRef CAS.
- C.-S. Kim, K. M. Jeong, K. Kim and C.-W. Yi, Electrochim. Acta, 2015, 155, 431–436 CrossRef CAS.
- S. Jiao, J. Zheng, Q. Li, X. Li, M. H. Engelhard, R. Cao, J.-G. Zhang and W. Xu, Joule, 2018, 2, 110–124 CrossRef CAS.
- C. Niu, H. Lee, S. Chen, Q. Li, J. Du, W. Xu, J.-G. Zhang, M. S. Whittingham, J. Xiao and J. Liu, Nat. Energy, 2019, 4, 551–559 CrossRef CAS.
- W.-J. Chen, C.-X. Zhao, B.-Q. Li, Q. Jin, X.-Q. Zhang, T.-Q. Yuan, X. Zhang, Z. Jin, S. Kaskel and Q. Zhang, Energy Environ. Mater., 2020, 3, 160–165 CrossRef CAS.
- Y. Zhang, Y. Zhong, Q. Shi, S. Liang and H. Wang, J. Phys. Chem. C, 2018, 122, 21462–21467 CrossRef CAS.
- Xi'an Ytel Network Technology Co. LTD, Li2CO3 spot price, https://www.yte1.com/datas/tansuanli-pri?end=2022, (accessed August 8, 2022).
-
E. Ö. Jónsson and F. Larsson, Master of Science Thesis in the Supply Chain Management Programme, Chalmers University of Technology, 2016 Search PubMed.
- X. Sun, M. Ouyang and H. Hao, Joule, 2022, 6, 1738–1742 CrossRef.
- O. Mashtalir, M. Nguyen, E. Bodoin, L. Swonger and S. P. O’Brien, ACS Omega, 2018, 3, 181–187 CrossRef CAS PubMed.
- B. S. Vishnugopi, F. Hao, A. Verma and P. P. Mukherjee, ACS Appl. Mater. Interfaces, 2020, 12, 23931–23938 CrossRef CAS PubMed.
- Y. Zhu, J. Xie, A. Pei, B. Liu, Y. Wu, D. Lin, J. Li, H. Wang, H. Chen, J. Xu, A. Yang, C.-L. Wu, H. Wang, W. Chen and Y. Cui, Nat. Commun., 2019, 10, 2067 CrossRef PubMed.
- H. Wang, Y. Zhu, S. C. Kim, A. Pei, Y. Li, D. T. Boyle, H. Wang, Z. Zhang, Y. Ye, W. Huang, Y. Liu, J. Xu, J. Li, F. Liu and Y. Cui, Proc. Natl. Acad. Sci. U. S. A., 2020, 117, 29453–29461 CrossRef CAS PubMed.
- A. Aryanfar, D. J. Brooks, A. J. Colussi, B. V. Merinov, W. A. Goddard Iii and M. R. Hoffmann, Phys. Chem. Chem. Phys., 2015, 17, 8000–8005 RSC.
- K. Yan, J. Wang, S. Zhao, D. Zhou, B. Sun, Y. Cui and G. Wang, Angew. Chem., Int. Ed., 2019, 58, 11364–11368 CrossRef CAS PubMed.
- D. Wang, Y. Liu, G. Li, C. Qin, L. Huang and Y. Wu, Adv. Funct. Mater., 2021, 31, 2106740 CrossRef CAS.
- A. Olayinka Oluwatosin, A. Esther Titilayo, O. Oluseyi Philip, A. Stephen and U. Albert Uchenna, AIMS Mater. Sci., 2019, 6, 174–199 Search PubMed.
- E. I. Du Pont de Nemours & Co., US Pat., 3721113, 1973 Search PubMed.
- Pechiney Recherche, US Pat., 5102475, 1992.
- Fuji Photo Film Co., Ltd., JP Pat., 1997330707, 1997.
- Beijing Weilion New Energy, Technology Co., Ltd., CN Pat., 112563444 A, 2021.
- Polaroid Corporation, US Pat., 4502903, 1985.
- Hydro-Quebec, US Pat., 5528920, 1996.
- Fuji Photo Film Co., Ltd., Honjo Metal Co., Ltd., JP Pat., 1998058007, 1998.
- Honjo Metal Co., Ltd., JP Pat., 1998058008, 1998.
- Hydro-Quebec, US Pat., 5837401, 1998.
- Hydro-Quebec, US Pat., 6517590 B1, 2003.
- Bathium Canada Inc, US Pat., 9605229 B2, 2017.
-
Hydro-Quebec, US Pat., 0179491 A1, 2017.
- Gotion High-tech Power Energy Co., Ltd, CN Pat., 108787747 A, 2018.
- Z. Tang, S. Li, Y. Li, H. Xu, Y. Yu, Y. Huang and J. Li, Nano Energy, 2020, 69, 104399 CrossRef CAS.
-
China Energy Lithium Co., Ltd., CN Pat., 113363456 A, 2021.
- M. Krystian and W. Pichl, Mater. Charact., 2001, 46, 1–9 CrossRef CAS.
- T. Li, P. Shi, R. Zhang, H. Liu, X.-B. Cheng and Q. Zhang, Nano Res., 2019, 12, 2224–2229 CrossRef CAS.
- Pechiney Recherche, US Pat., 5102475, 1992.
-
Tongji University, CN Pat., 111883739 A, 2020.
- Advanced Electronic Technology Ltd. Company, CN Pat., 104466095 A, 2015.
-
FMC Corporation, US Pat., 5567474, 1996.
-
FMC Corporation, US Pat., 5776369, 1998.
-
FMC Corporation, US Pat., 5976403, 1999.
- S.-T. Hong, J.-S. Kim, S.-J. Lim and W. Y. Yoon, Electrochim. Acta, 2004, 50, 535–539 CrossRef CAS.
- B. Xiang, L. Wang, G. Liu and A. M. Minor, J. Electrochem. Soc., 2013, 160, A415–A419 CrossRef CAS.
-
Honjo Metal Co., Ltd., JP Pat., 1996250113, 1996.
- J. Heine, S. Krüger, C. Hartnig, U. Wietelmann, M. Winter and P. Bieker, Adv. Energy Mater., 2014, 4, 1300815 CrossRef.
- J. H. Lee, C. W. Lim, J. K. Lee, S. M. Cho, B. K. Kim and W. Y. Yoon, Electrochim. Acta, 2014, 131, 202–206 CrossRef CAS.
- Y. Li and B. Fitch, Electrochem. Commun., 2011, 13, 664–667 CrossRef CAS.
- D. Jin, J. Oh, A. Friesen, K. Kim, T. Jo, Y. M. Lee and M.-H. Ryou, ACS Appl. Mater. Interfaces, 2018, 10, 16521–16530 CrossRef CAS PubMed.
- J. Xia, B. Fitch, A. Watson, J. Cabaniss, R. Black and M. Yakovleva, ECS Meeting Abstr., 2021, MA2021-02, 362 CrossRef.
-
China Energy Lithium Co., Ltd., CN Pat., 111725496 A, 2020.
-
China Enerty Lithium Co., Ltd., CN Pat., 112151758 A, 2020.
-
Tianqi Lithium Corporation, CN Pat., 111299321 A, 2020.
- Tianqi Lithium Corporation, CN Pat., 213223755 U, 2021.
- Matsushita Electric Industrial Co., Ltd., JP Pat., 2007305548 A, 2007.
- VSE Engineering Team, The PCB Etching Process and its Role in Circuit Board Manufacturing, https://www.vse.com/blog/2021/07/27/the-pcb-etching-process-and-its-role-in-circuit-board-manufacturing/, (accessed January 7, 2023).
- W. Tang, X. Yin, Z. Chen, W. Fu, K. P. Loh and G. W. Zheng, Energy Storage Mater., 2018, 14, 289–296 CrossRef.
- M. Hu, Z. Tong, C. Cui, T. Zhai and H. Li, Nano Lett., 2022, 22, 3047–3053 CrossRef CAS PubMed.
- Hydro-Quebec, US Pat., 4824746, 1989.
-
MHB Joint Venture, US Pat., 5080932, 1992.
-
EVE Energy Co., Ltd., CN Pat., 104332586 A, 2015.
- Qingdao Institute of Bioenergy and Bioprocess Technology, Chinese Academy of Sciences, CN Pat., 107425175 A, 2017.
- J. Du, W. Wang, M. Wan, X. Wang, G. Li, Y. Tan, C. Li, S. Tu and Y. Sun, Adv. Energy Mater., 2021, 11, 2102259 CrossRef CAS.
- W. Wu, Z. Song, Y. Dai, X. Zheng, G. Chai, J. Yang and W. Luo, Adv. Energy Mater., 2022, 12, 2200999 CrossRef CAS.
- W. Wu, J. Duan, J. Wen, Y. Chen, X. Liu, L. Huang, Z. Wang, S. Deng, Y. Huang and W. Luo, Sci. China: Chem., 2020, 63, 1483–1489 CrossRef CAS.
- J. Gao, C. Chen, Q. Dong, J. Dai, Y. Yao, T. Li, A. Rundlett, R. Wang, C. Wang and L. Hu, Adv. Mater., 2021, 33, 2005305 CrossRef CAS PubMed.
-
E. I. Du Pont de Nemours & Co., US Pat., 3928681, 1975 Search PubMed.
- Wuxi Yongxing Metal Hose Co., Ltd., CN Pat., 107641782 A, 2018.
- Tianqi Lithium Corporation, CN Pat., 109161831 A, 2019.
- K. Schönherr, B. Schumm, F. Hippauf, R. Lissy, H. Althues, C. Leyens and S. Kaskel, Chem. Eng. J. Adv., 2022, 9, 100218 CrossRef.
- University of Electronic Science and Technology of China, CN Pat., 109378448 A, 2019.
-
China Energy Lithium Co., Ltd., CN Pat., 113206217 A, 2021.
- Hope Industries Inc., US Pat., 4888206, 1989.
-
Yangtze Delta Region Institute of University of Electronic Science and Technology of China, Huzhou, CN Pat., 114147192 A, 2022.
- C. Niu, H. Pan, W. Xu, J. Xiao, J.-G. Zhang, L. Luo, C. Wang, D. Mei, J. Meng, X. Wang, Z. Liu, L. Mai and J. Liu, Nat. Nanotechnol., 2019, 14, 594–601 CrossRef CAS PubMed.
- Z. Li, Q. He, C. Zhou, Y. Li, Z. Liu, X. Hong, X. Xu, Y. Zhao and L. Mai, Energy Storage Mater., 2021, 37, 40–46 CrossRef.
- X. Sun, X. Zhang, Q. Ma, X. Guan, W. Wang and J. Luo, Angew. Chem., Int. Ed., 2020, 59, 6665–6674 CrossRef CAS PubMed.
- K. Fukami, A. Sakurai, T. Tsujimoto, M. Yamagami, A. Kitada, K. Morimoto, K. Nishioka, S. Nakanishi, Y. Yoshikane, T. Nagao, J.-I. Katayama and K. Murase, Electrochem. Commun., 2022, 136, 107238 CrossRef CAS.
- X.-Q. Zhang, X. Chen, R. Xu, X.-B. Cheng, H.-J. Peng, R. Zhang, J.-Q. Huang and Q. Zhang, Angew. Chem., Int. Ed., 2017, 56, 14207–14211 CrossRef CAS PubMed.
- C.-Y. Wang, Z.-J. Zheng, Y.-Q. Feng, H. Ye, F.-F. Cao and Z.-P. Guo, Nano Energy, 2020, 74, 104817 CrossRef CAS.
- N. M. Schneider, J. H. Park, J. M. Grogan, D. A. Steingart, H. H. Bau and F. M. Ross, Nat. Commun., 2017, 8, 2174 CrossRef PubMed.
- F. Ding, W. Xu, G. L. Graff, J. Zhang, M. L. Sushko, X. Chen, Y. Shao, M. H. Engelhard, Z. Nie, J. Xiao, X. Liu, P. V. Sushko, J. Liu and J.-G. Zhang, J. Am. Chem. Soc., 2013, 135, 4450–4456 CrossRef CAS PubMed.
- K. Yan, Z. Lu, H.-W. Lee, F. Xiong, P.-C. Hsu, Y. Li, J. Zhao, S. Chu and Y. Cui, Nat. Energy, 2016, 1, 16010 CrossRef CAS.
- Y. Gu, H.-Y. Xu, X.-G. Zhang, W.-W. Wang, J.-W. He, S. Tang, J.-W. Yan, D.-Y. Wu, M.-S. Zheng, Q.-F. Dong and B.-W. Mao, Angew. Chem., Int. Ed., 2019, 58, 3092–3096 CrossRef CAS PubMed.
- J. Qian, W. A. Henderson, W. Xu, P. Bhattacharya, M. Engelhard, O. Borodin and J.-G. Zhang, Nat. Commun., 2015, 6, 6362 CrossRef CAS PubMed.
- Q. Meng, B. Deng, H. Zhang, B. Wang, W. Zhang, Y. Wen, H. Ming, X. Zhu, Y. Guan, Y. Xiang, M. Li, G. Cao, Y. Yang, H. Peng, H. Zhang and Y. Huang, Energy Storage Mater., 2019, 16, 419–425 CrossRef.
- C. Wei, H. Fei, Y. An, Y. Tao, J. Feng and Y. Qian, J. Mater. Chem. A, 2019, 7, 18861–18870 RSC.
-
R. J. Brodd, US Pat., 5522955, 1996 Search PubMed.
- Sumitomo Electric Industries Ltd., US Pat., 6713216, B2, 2004 Search PubMed.
-
Harbin Institute of Technology, CN Pat., 105489845 A, 2016.
- A. S. Ho, A. S. Westover, K. Browning, J. A. Maslyn, D. Y. Parkinson, R. Sahore, N. Dudney and N. P. Balsara, ACS Energy Lett., 2022, 7, 1120–1124 CrossRef CAS.
- J. B. Bates, N. J. Dudney, B. Neudecker, A. Ueda and C. D. Evans, Solid State Ion., 2000, 135, 33–45 CrossRef CAS.
- J. Li, C. Ma, M. Chi, C. Liang and N. J. Dudney, Adv. Energy Mater., 2015, 5, 1401408 CrossRef.
- D. K. Singh, T. Fuchs, C. Krempaszky, B. Mogwitz, S. Burkhardt, F. H. Richter and J. Janek, Adv. Funct. Mater., 2023, 33, 2211067 CrossRef CAS.
- Y. Hamon, T. Brousse, F. Jousse, P. Topart, P. Buvat and D. M. Schleich, J. Power Sources, 2001, 97–98, 185–187 CrossRef CAS.
- F. Holtstiege, P. Bärmann, R. Nölle, M. Winter and T. Placke, Batteries, 2018, 4, 4 CrossRef.
- R. Zhan, X. Wang, Z. Chen, Z. W. Seh, L. Wang and Y. Sun, Adv. Energy Mater., 2021, 11, 2101565 CrossRef CAS.
- W. J. Cao, J. F. Luo, J. Yan, X. J. Chen, W. Brandt, M. Warfield, D. Lewis, S. R. Yturriaga, D. G. Moye and J. P. Zheng, J. Electrochem. Soc., 2016, 164, A93–A98 CrossRef.
- H. Xu, S. Li, C. Zhang, X. Chen, W. Liu, Y. Zheng, Y. Xie, Y. Huang and J. Li, Energy Environ. Sci., 2019, 12, 2991–3000 RSC.
- J. Yan, W. J. Cao and J. P. Zheng, J. Electrochem. Soc., 2017, 164, A2164–A2170 CrossRef CAS.
- R. V. Salvatierra, W. Chen and J. M. Tour, Adv. Energy Sustainability Res., 2021, 2, 2000110 CrossRef CAS.
- S. Nanda, A. Gupta and A. Manthiram, Adv. Energy Mater., 2021, 11, 2000804 CrossRef CAS.
- B. J. Neudecker, N. J. Dudney and J. B. Bates, J. Electrochem. Soc., 2000, 147, 517 CrossRef CAS.
-
R. Matheson, Doubling battery power of consumer electronics, https://news.mit.edu/2016/lithium-metal-batteries-double-power-consumer-electronics-0817, (accessed August 15, 2022).
- L. Wang, Z. Wu, J. Zou, P. Gao, X. Niu, H. Li and L. Chen, Joule, 2019, 3, 2086–2102 CrossRef CAS.
- Y. H. Kwon, S.-W. Woo, H.-R. Jung, H. K. Yu, K. Kim, B. H. Oh, S. Ahn, S.-Y. Lee, S.-W. Song, J. Cho, H.-C. Shin and J. Y. Kim, Adv. Mater., 2012, 24, 5192–5197 CrossRef CAS PubMed.
- J. Ren, L. Li, C. Chen, X. Chen, Z. Cai, L. Qiu, Y. Wang, X. Zhu and H. Peng, Adv. Mater., 2013, 25, 1155–1159 CrossRef CAS PubMed.
- X. Fang, W. Weng, J. Ren and H. Peng, Adv. Mater., 2016, 28, 491–496 CrossRef CAS PubMed.
- J. Chang, J. Shang, Y. Sun, L. K. Ono, D. Wang, Z. Ma, Q. Huang, D. Chen, G. Liu, Y. Cui, Y. Qi and Z. Zheng, Nat. Commun., 2018, 9, 4480 CrossRef PubMed.
- Y. Gao, H. Hu, J. Chang, Q. Huang, Q. Zhuang, P. Li and Z. Zheng, Adv. Energy Mater., 2021, 11, 2101809 CrossRef CAS.
- X.-B. Cheng, R. Zhang, C.-Z. Zhao and Q. Zhang, Chem. Rev., 2017, 117, 10403–10473 CrossRef CAS PubMed.
- D. Lin, Y. Liu, Y. Li, Y. Li, A. Pei, J. Xie, W. Huang and Y. Cui, Nat. Chem., 2019, 11, 382–389 CrossRef CAS PubMed.
- A. Kolesnikov, M. Kolek, J. F. Dohmann, F. Horsthemke, M. Börner, P. Bieker, M. Winter and M. C. Stan, Adv. Energy Mater., 2020, 10, 2000017 CrossRef CAS.
- D. Jin, Y. Roh, T. Jo, D. O. Shin, J. Song, J. Y. Kim, Y.-G. Lee, H. Lee, M.-H. Ryou and Y. M. Lee, Chem. Eng. J., 2021, 406, 126834 CrossRef CAS.
- M. Wu, Z. Wen, Y. Liu, X. Wang and L. Huang, J. Power Sources, 2011, 196, 8091–8097 CrossRef CAS.
- S. L. Koch, B. J. Morgan, S. Passerini and G. Teobaldi, J. Power Sources, 2015, 296, 150–161 CrossRef CAS.
- J. Zhao, L. Liao, F. Shi, T. Lei, G. Chen, A. Pei, J. Sun, K. Yan, G. Zhou, J. Xie, C. Liu, Y. Li, Z. Liang, Z. Bao and Y. Cui, J. Am. Chem. Soc., 2017, 139, 11550–11558 CrossRef CAS PubMed.
- P. B. Samarasingha, M.-T. Lee and M. Valvo, Electrochim. Acta, 2021, 397, 139270 CrossRef CAS.
- M. S. Kim, J.-H. Ryu, Deepika, Y. R. Lim, I. W. Nah, K.-R. Lee, L. A. Archer and W. Il Cho, Nat. Energy, 2018, 3, 889–898 CrossRef CAS.
- X. Shen, Y. Li, T. Qian, J. Liu, J. Zhou, C. Yan and J. B. Goodenough, Nat. Commun., 2019, 10, 900 CrossRef PubMed.
- X. Chen, M. Shang and J. Niu, Nano Lett., 2020, 20, 2639–2646 CrossRef CAS PubMed.
- Y. Deng, M. Wang, C. Fan, C. Luo, Y. Gao, C. Zhou and J. Gao, Nano Lett., 2021, 21, 1896–1901 CrossRef CAS PubMed.
- J.-Y. Hwang, S.-J. Park, C. S. Yoon and Y.-K. Sun, Energy Environ. Sci., 2019, 12, 2174–2184 RSC.
- D. Jin, Y. Roh, T. Jo, M.-H. Ryou, H. Lee and Y. M. Lee, Adv. Energy Mater., 2021, 11, 2003769 CrossRef CAS.
- S. Chen, J. Zhang, L. Nie, X. Hu, Y. Huang, Y. Yu and W. Liu, Adv. Mater., 2021, 33, 2002325 CrossRef CAS PubMed.
- H. Liu, H. Tang, M. Fang, W. Si, Q. Zhang, Z. Huang, L. Gu, W. Pan, J. Yao, C. Nan and H. Wu, Adv. Mater., 2016, 28, 8170–8176 CrossRef CAS PubMed.
- B. Li, D. Zhang, Y. Liu, Y. Yu, S. Li and S. Yang, Nano Energy, 2017, 39, 654–661 CrossRef CAS.
- Y. Wang, Y. Shen, Z. Du, X. Zhang, K. Wang, H. Zhang, T. Kang, F. Guo, C. Liu, X. Wu, W. Lu and L. Chen, J. Mater. Chem. A, 2017, 5, 23434–23439 RSC.
- F. Guo, Y. Wang, T. Kang, C. Liu, Y. Shen, W. Lu, X. Wu and L. Chen, Energy Storage Mater., 2018, 15, 116–123 CrossRef.
- F. Guo, T. Kang, Z. Liu, B. Tong, L. Guo, Y. Wang, C. Liu, X. Chen, Y. Zhao, Y. Shen, W. Lu, L. Chen and Z. Peng, Nano Lett., 2019, 19, 6377–6384 CrossRef CAS PubMed.
- T. Kang, Y. Wang, F. Guo, C. Liu, J. Zhao, J. Yang, H. Lin, Y. Qiu, Y. Shen, W. Lu and L. Chen, ACS Cent. Sci., 2019, 5, 468–476 CrossRef CAS PubMed.
- L. Zheng, F. Guo, T. Kang, J. Yang, Y. Liu, W. Gu, Y. Zhao, H. Lin, Y. Shen, W. Lu and L. Chen, Nano Res., 2020, 13, 1324–1331 CrossRef CAS.
- K. Pu, X. Qu, X. Zhang, J. Hu, C. Gu, Y. Wu, M. Gao, H. Pan and Y. Liu, Adv. Sci., 2019, 6, 1901776 CrossRef CAS PubMed.
- S. Li, H. Wang, J. Cuthbert, T. Liu, J. F. Whitacre and K. Matyjaszewski, Joule, 2019, 3, 1637–1646 CrossRef CAS.
- Y. Zhang, Z. Han, Z. Huang, C. Zhang, C. Luo, G. Zhou, W. Lv and Q.-H. Yang, ACS Energy Lett., 2021, 6, 3761–3768 CrossRef CAS.
- H. Deng, Z. Chang, F. Qiu, Y. Qiao, H. Yang, P. He and H. Zhou, Adv. Energy Mater., 2020, 10, 1903953 CrossRef CAS.
- J. Peng, D. Wu, F. Song, S. Wang, Q. Niu, J. Xu, P. Lu, H. Li, L. Chen and F. Wu, Adv. Funct. Mater., 2022, 32, 2105776 CrossRef CAS.
|
This journal is © The Royal Society of Chemistry 2023 |
Click here to see how this site uses Cookies. View our privacy policy here.