DOI:
10.1039/C8TA00612A
(Review Article)
J. Mater. Chem. A, 2018,
6, 6754-6771
Metal–organic framework derived hollow materials for electrochemical energy storage
Received
19th January 2018
, Accepted 15th March 2018
First published on 16th March 2018
Abstract
Metal–organic frameworks (MOFs), a novel class of porous crystalline materials, have drawn enormous attention. Due to the inherent porosity and presence of both metal and organic moieties, MOF-based materials are naturally suitable as versatile precursors and sacrificial templates for a wide variety of metal/carbon-based nanostructured materials, such as metal oxides, metal carbides, metal sulfides and their composites. Recent developments in MOF-derived hollow nanostructures with well-defined interior voids and low density have revealed their extensive capabilities and thus give enhanced performance for energy storage and conversion. In this review, we summarize the recent progress in the fabrication of MOF-derived hollow materials and their applications for energy storage, particularly for lithium-ion batteries, sodium-ion batteries, lithium–Se batteries, lithium–sulfur batteries and supercapacitors. The superiorities of MOF-derived hollow materials are highlighted, and major challenges or opportunities for future research on them for electrochemical energy storage are also discussed, with prospective solutions in the light of current progress in MOF-derived hollow nanostructures.
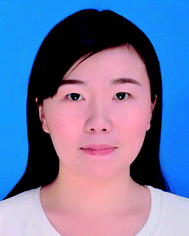 Xing-Chen Xie | Xing-chen Xie is a MS candidate majoring in chemistry and chemical engineering from Xinyang Normal University, China. Her research is focused on energy storage devices based on metal–organic framework derived materials. |
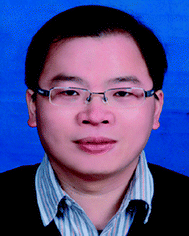 Ke-Jing Huang | Ke-Jing Huang received his PhD in 2006 from Wuhan University. Presently, he is a professor at Xinyang Normal University. His research interests include 2D nanomaterial preparation, supercapacitor electrode materials and electrochemical biosensors. |
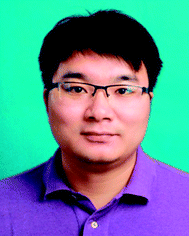 Xu Wu | Xu Wu received his PhD degree from Central China Normal University in 2016. He studied at the University of California, Los Angeles as a visiting PhD candidate from 2013 to 2015. Currently he is a lecturer at Xinyang Normal University. His research focuses on nanomaterials for electrochemical energy storage, including rechargeable batteries and supercapacitors. |
1. Introduction
With the dramatic increases of fossil fuel consumption and the associated environmental pollution, the development of renewable, safe, clean, efficient and sustainable energy sources as well as the related energy storage technologies thus has become a worldwide problem.1–6 Electrochemical energy storage technologies with numerous advantages, such as environmental-friendliness, high efficiency and high application flexibility, have attracted huge attention.7–10 Supercapacitors (SCs) and batteries are the two major electrochemical energy storage devices. Energy storage devices of different types have their own characteristics. SCs show high power density and long cycle life, with a competitive price, but always show low energy density.11–14 Lithium-ion batteries (LIBs) are the most widely used and promising power resources for portable electronic devices and electric vehicles, because of their high energy density and high energy efficiency, but relatively low power density, high price and safety hazards limit their further development.15–17 As a new star, sodium-ion batteries (SIBs) show many advantages regarding price and safety issues, and even with relatively low energy densities, they have attracted increasing attention in recent years, especially for large-scale energy storage applications. But till now, an energy storage device that can meet all application demands has not been reported.18–20 For energy storage devices, their performance highly depends on electrode materials. Developing advanced electrode materials is a key scientific issue to promote the development of energy storage devices.
MOFs are a kind of porous material firstly defined in the late 1990s by Yaghi and coworkers. They are formed by linking metal sites and organic ligands via strong coordination bonds.21–23 The metal sites can be ions of transition metals (e.g. Zn, Cu, Fe, Co, and Ni), p-block elements (e.g. Ga and In), alkaline earth metals (e.g. Sr and Ba), actinides (e.g. U and Th), and lanthanides, while the organic ligands can be divalent or polyvalent organic carboxylates. When organic ligands are linked to metal containing units (e.g. Zn2+, Cu2+, Co2+, Mg2+, and Ni2+) through interactions such as H-bonding, π–π stacking and van der Waals forces, architecturally three-dimensional (3D) structures with well-defined pore size distributions can be yielded.24–31 Till now, more than 20
000 MOFs with diverse compositions, crystal structures and morphologies have been discovered and this number is still growing.32 One of the most distinctive advantages of MOF materials is that the frameworks are designable via a modular self-assembly process, and various functional species of metal ions/clusters and organic linkers can be incorporated. This makes MOFs ideal precursors to prepare desired nano-species which have great application potential for energy storage electrode materials.33–36 But normally, MOFs themselves cannot be directly used on electrode materials because of their low electrical conductivity and stability, so simple and efficient ways are needed to convert MOFs into energy storage favorable materials. One of the most direct and effective ways is the thermal decomposition of MOFs under a certain atmosphere (e.g. argon, nitrogen, and air) at an elevated temperature (e.g. 500–900 °C) to prepare carbon species or carbon/oxide (chalcogenide) composites. During the decomposition process, organic ligands turn into carbon species via an in situ carbonization process. Some organic ligands contain nitrogen (e.g. methyl imidazole), and nitrogen doped carbon nanomaterials can be generated after thermolysis, resulting in the enhancement of the electrochemical activity of the resulting materials.37–42 Besides, metal sites can be converted to corresponding metal or oxides, which can act as catalysts to facilitate the formation of carbon species, or evaporate at high temperature to leave pores.22,43–45 In addition, MOFs can also be designed to combine with functional materials to construct complex nanostructures.46–48 Thus, nanomaterials with desired components and structures can be designed from MOFs, providing highly promising solutions to deal with the key problems exist in electrochemical energy storage.
As one type of attractive architecture, hollow nanostructures with well-defined interior voids, low density, large surface area, abundant active sites and ability to accommodate volume change without being pulverized compared with those of their solid counterparts of the same size have been studied for electrochemical energy storage for a long time.49–52 Precise control of the size, morphology, composition, crystallinity and building blocks of these hollow architectures can tune their fascinating physico-chemical properties as desired effectively.42,51,53 MOFs are good precursors to create hollow nanostructures. Approaches such as thermal treatments, ion exchange reactions, self-template-directed growth, galvanic replacement and chemical etching are extensively used to prepared hollow structures MOFs.31,54–61 These MOF-derived hollow materials are playing progressive roles in realizing optimal performance in energy storage and conversion. So, it is essential to summarize the recent research studies on these MOF-derived hollow materials, finding the underlying aspects for their performance enhancement, and give valuable prospects on their further development, to promote their efficient application for advanced electrochemical energy storage technologies.
Herein, in this review, we provide a broad overview of the latest developments in MOF derived hollow nanostructures (metal oxides/sulfides or their composition with carbon) for energy storage applications, practically for LIBs, lithium–sulfur (Li–S) batteries, lithium–selenium (Li–Se) batteries, SIBs, and SCs. The possible fundamentals and strategies to improve their energy storage performances are discussed. Finally, we end this review with a discussion on urgent challenges and further research directions of MOF-derived hollow nanostructures for electrochemical energy storage.
2. MOF-derived hollow materials for lithium-ion batteries
LIBs usually consist of a cathode, anode, separator and electrolyte. They store energy by intercalation and deintercalation of lithium ions between the two electrodes. They are the widely used batteries for portable electronic devices owing to their relatively high energy density and efficiency.62–65 Yet, they still cannot satisfy the high energy storage capability required for next-generation power sources, including electric vehicles (EVs), hybrid electric vehicles (HEVs) and electrical energy storage (EES).66,67 Electrode materials are one of the key factors that determine the overall performance of LIBs. It is urgent and significant to develop high-performance electrode materials with high energy/power density, superior cycling, reliable stability, and good rate capability.
Hollow nanomaterials with low mass density, higher porosity, and large surface area are quite suitable for energy storage applications.68–71 The unique hollow structures can not only shorten the diffusion distance of Li+ and increase the electrode–electrolyte interface, but also provide additional voids to buffer the commonly occurring volume changes during charge and discharge processes.72,73 MOFs can provide multiple possibilities to prepare hollow structured materials. Because of the inherent tunable pore structures and geometries made up of metal centers coordinated with organic complexes, controlled heating of MOFs in various environments can produce various unique hollow structures.53,74,75 During the thermal treatment, metal centers are converted to highly active metal oxide electrode materials. If the process is carried out under a protective atmosphere, the organic linkers would be carbonized to carbon shells coated outside the metal oxides, which can maintain the inherent porous framework of MOFs, thereby improving the structural integrity and increasing the electronic conductivity of electrode materials.76,77 As such, MOF-derived hollow materials offer tremendous opportunities to derive various forms of metal oxides, metal sulfides, metal sulfides/carbons and metal oxide/carbon composites with higher lithium storage performances.
2.1 MOF-derived hollow metal oxides for lithium batteries
Transition metal oxides are regarded as promising electrode materials for lithium batteries because of their high theoretical capacities and convenient synthetic routes.78–80 A series of MOF-derived metal oxide hollow structures have been prepared and applied for lithium batteries with high performance.
Co3O4, as an attractive electrode material for lithium batteries, has a high theoretical capacity with high electrical conductivity. However, its cycling performance is seriously hindered by the drastic volume changes during lithiation/delithiation processes.81,82 In order to solve this problem, various Co3O4 hollow structures are constructed from MOFs to release the volume changes, and these materials show enhanced electrochemical performance. For example, hollow Co3O4 dodecahedrons are synthesized via a facile one-step calcination of a cobalt-based metal–organic framework (ZIF-67), as shown in Fig. 1a–d. The hollow Co3O4 dodecahedrons exhibited a high capacity of 1550 mA h g−1 at 100 mA g−1 and an excellent cycling stability of 1335 mA h g−1 after 100 cycles.83 Hollow Co3O4 parallelepipeds are also prepared through the direct pyrolysis of the prepared Co–MOF (Fig. 1e and f) and the sample exhibits a capacity of 1115 mA h g−1 at 100 mA g−1 with improved cycling stability (Fig. 1g and h).84 In another study, porous hollow Co3O4 microfibers with 500 nm diameter and 60 nm wall thickness are obtained through a facile and scalable chemical precipitation method. The capacity of the hollow Co3O4 microfibers reaches 1177.4 mA h g−1 at 100 mA g−1, with high initial coulombic efficiency (82.9%) and cycling stability (76.6% capacity retention for 200 cycles). This enhancement could be ascribed to the unique nanostructure, which not only facilitates the electrolyte diffusion and intercalation of Li ions into the active phases, but also buffers the volume change of anodes during repeated Li-ion insertion/extraction.85 A composite of Co3O4/TiO2 hollow polyhedrons is also fabricated through a cation-exchange approach in a metal–organic framework (Fig. 1i). The obtained integrated Co3O4/TiO2 hollow composite exhibits a reversible capacity of 642 mA h g−1 at 500 mA g−1 after 200 cycles, accounting for 96.9% of the initial capacity, as shown in Fig. 1j, demonstrating its high potential as advanced electrode material for future LIBs.86
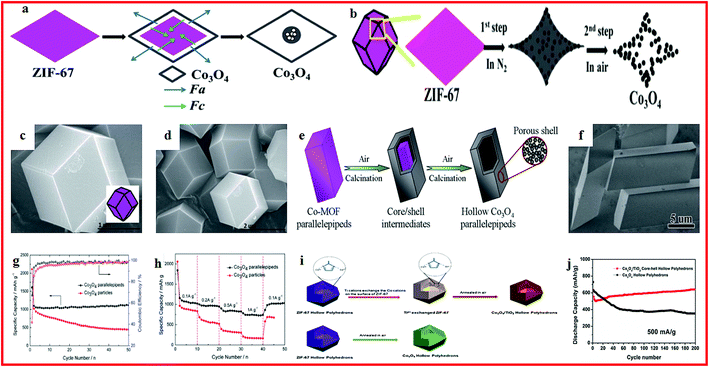 |
| Fig. 1 (a) Schematic illustration of the formation of ball-in-dodecahedron Co3O4; (b) schematic illustration of the formation of Co3O4 dodecahedrons with concave surfaces; (c and d) SEM images of ZIF-67 rhombic dodecahedrons. Reproduced with permission.83 Copyright 2014, Royal Society of Chemistry. (e) Schematic illustration of the formation of the hollow Co3O4 parallelepipeds; (f) SEM image of the Co–MOF precursor. (g) Cycling performance and (h) rate capability of the Co3O4 parallelepipeds and Co3O4 particles. Reproduced with permission.84 Copyright 2015, Royal Society of Chemistry. (i) The ZIF-67 sample possesses a hollow polyhedron structure; (j) cycling performance at 500 mA g−1. Reproduced with permission.86 Copyright 2016, Elsevier Ltd. | |
CuO is another promising metal oxide anode candidate for lithium batteries due to its abundant resources, affordable price, non-toxicity, chemical stability, and easy preparation in diverse shapes of nanosized dimensions.87–89 However, traditional CuO nanostructures show poor rate performance, which is mainly due to their inherent low electrical conductivity and unstable structure at high current density.90 Recently, many studies have reported the use of Cu-based MOFs as precursors or templates to construct CuO hollow architectures with excellent electrochemical performance in advanced Li-ion batteries. Porous CuO hollow architectures with a perfect octahedral morphology were obtained by annealing Cu-based MOF templates at 300 °C, exhibiting a high and stable capacity with excellent cycling stability.91 Novel CuO/Cu2O hollow polyhedrons with porous shells have been synthesized via a thermal decomposition of coordination compound polyhedrons at 350 °C, as displayed in Fig. 2a. The CuO/Cu2O hollow polyhedrons exhibited a reversible lithium storage capacity as high as 740 mA h g−1 at 100 mA g−1 with a long lifespan.92 These hollow structures exhibit enhanced lithium storage capacity and rate capability with increased cycling stability and good rate capability due to their unique architecture.
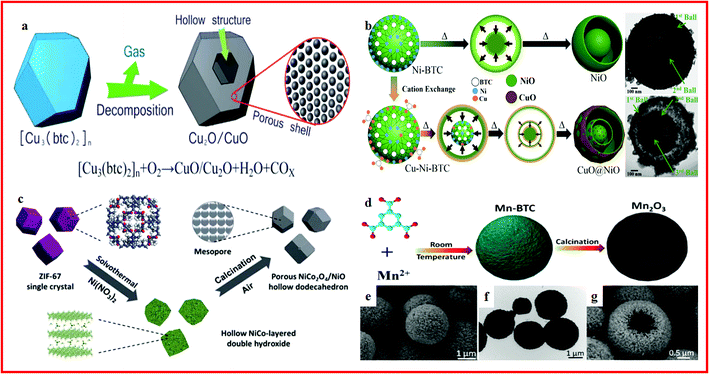 |
| Fig. 2 (a) Schematic illustration of the formation of CuO/Cu2O hollow polyhedrons with a porous shell. Reproduced with permission.92 Copyright 2013, Royal Society of Chemistry. (b) Schematic illustration showing the cationic exchange process of the MOF and its conversion to a multi-layer hollow structure. Reproduced with permission.95 Copyright 2015, American Chemical Society. (c) Schematic illustration of the preparation process of the porous NiCo2O4/NiO hollow dodecahedron (HD). Reproduced with permission.98 Copyright 2015, Royal Society of Chemistry. (d) Schematic illustration of the formation of Mn2O3 hollow microspheres; (e) FESEM images of Mn-BTC precursors prepared; (f) TEM images of Mn-BTC precursors prepared; (g) FESEM image of Mn2O3-10R. Reproduced with permission.99 Copyright 2016, Royal Society of Chemistry. | |
NiO is an alternative electrode material for lithium ion batteries, and it has been widely studied due to its high theoretical capacity, low cost and nontoxicity.93,94 The main problem of NiO electrodes is the poor cycling performance caused by the drastic volume change during a repeated lithiation/delithiation process.95 In order to overcome these drawbacks, porous NiO hollow quasi-nanospheres prepared from a Ni–MOF are reported. The MOF-derived NiO electrode exhibits a high capacity of 760 mA h g−1 at 200 mA g−1 with good stability and rate performance. This superior lithium ion storage performance is mainly attributed to the unique hollow and porous nanostructure of the as-synthesized NiO, which offers enough space to accommodate the volume change during cycling lithiation/delithiation processes.96 In addition, several novel strategies have also been developed for the fabrication of anisotropic NiO based hollow structures. For example, a CuO@NiO microsphere with a three-layer hollow ball-in-ball nanostructure is synthesized from Cu–Ni bimetallic organic frameworks, as shown in Fig. 2b. LIBs using the CuO@NiO microsphere as the anode show a large higher-than-theoretical capacity of 1061 mA h g−1. Excellent electrochemical properties are reported ascribed to the step-by-step lithium insertion reactions induced by the matched CuO@NiO composition from the shell to the core. Meanwhile, the lithium/electron diffusion can be facilitated, and the volume changes in the porous bimetallic oxide microsphere can also be accommodated with the multiple-layer yolk–shell nanostructure.97 In another study, a porous NiCo2O4/NiO hollow dodecahedron is prepared from ZIF-67 (Fig. 2c). The capacity of the porous NiCo2O4/NiO hollow dodecahedron reached 1535 mA h g−1 at 200 mA g−1 and remained at 97.2% after 100 cycles. The superior electrochemical performance is attributed to the unique hierarchical hollow nanoarchitecture, high mechanical tolerance, large surface area, and high conductivity.98
Manganese oxides are also promising anode materials for lithium ion batteries. Mn2O3 hollow microspheres prepared through the direct pyrolysis of Mn-based metal–organic frameworks (Fig. 2d–g.) demonstrate an extremely high reversible capacity of 582 mA h g−1 at a current density of 100 mA g−1 with good cycling stability. The unique hollow nanocage structures shorten the length of Li-ion diffusion and help to buffer the volumetric variation.99
Hollow ternary transition metal oxides (TMOs), with a spinel structure (AB2O4), are promising electrode materials for energy storage devices.100–102 In particular, hollow micro-/nanostructured ternary TMOs with controllable size, shape, and interior architectures and a variety of frameworks and compositions are highly desired, owing to their rich variety of crystallographic arrangements, low density, high porosity, high surface area and shell permeability.103 Among them, Fe-based ternary oxides are known for their natural abundance, non-toxicity and cost efficiency. In recent years, different strategies have been explored to fabricate various MOF derived hollow structured Fe-based ternary oxides with optimized structures and physical/chemical properties for lithium ion batteries.104,105 For example, a series of porous hollow spinel AFe2O4 nano-architectures of NiFe2O4, ZnFe2O4 and CoFe2O4 are synthesized by using MOFs as self-sacrificial templates. When used as an anode for lithium-ion batteries, ultrahigh rate capability and long-term cycling stability can be achieved by all three metal oxides. In particular, high specific capacities of 636, 449 and 380 mA h g−1 at 8.0 A g−1 with high cycling stability are achieved by NiFe2O4, ZnFe2O4, and CoFe2O4, respectively.106 Hollow porous CoFe2O4 nanocubes were also synthesized from MOFs as an anode material (Fig. 3a and b). A specific capacity of up to 1115 mA h g−1 could be retained over 200 cycles with an excellent rate performance (Fig. 3c).107 Similarly, a hollow hybrid NiFe2O4 nanomaterial is presented by using a MOF as the precursor (Fig. 3d and 2e). When used as an anode material, a stable capacity of 1017 mA h g−1 can be retained after 200 cycles (Fig. 3f).108 These outstanding electrochemical performances and facile synthesis routes provide a prospective insight into practical application of hollow ternary AB2O4 structured TMOs for future LIBs.
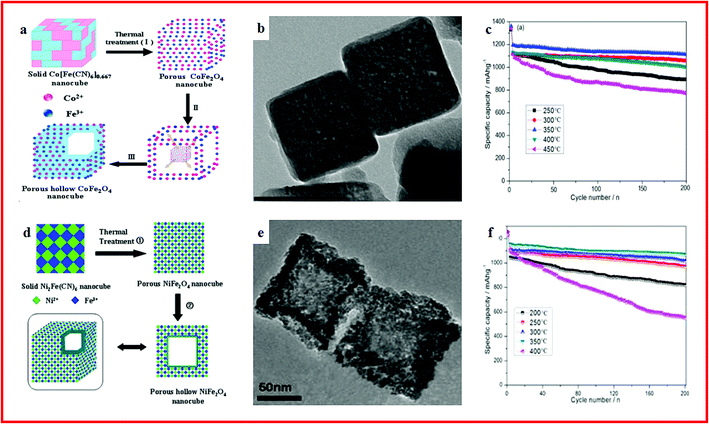 |
| Fig. 3 (a) Representative illustration of the formation of hollow CoFe2O4 nanocubes from NMOFs; (b) TEM images of porous CoFe2O4 nanocubes; (c) cycling performance of CoFe2O4 materials. Reproduced with permission.107 Copyright 2014, Royal Society of Chemistry. (d) Representative illustration of the formation of hollow NiFe2O4 nanocages for MOFs; (e) TEM images of porous NiFe2O4 nanocages; (f) cycling performance of NiFe2O4 materials. Reproduced with permission.108 Copyright 2014, Nature. | |
Due to the unique component and structural advantages, these MOF-derived metal oxide hollow materials show greatly enhanced performance, especially specific capacity and cycling stability, when evaluated as anode materials for LIBs. Meanwhile, the preparation methods of these MOF-derived metal oxide hollow structures are low-cost and convenient, which further increase their application potential for next generation energy storage and conversion.
2.2 MOF-derived hollow metal oxides/carbons for lithium batteries
MOF-derived hollow metal oxides/carbons can also be readily used as electrodes for high-performance electrochemical energy storage. For instance, Yin et al. proposed a simple and cost-effective method to synthesize hollow porous CuO/C composite microcubes from Cu–MOF templates (Fig. 4a–c). Benefiting from a high specific surface area, hollow porous structure and the enhanced conductivity of residual carbon, the hollow porous CuO/C composite microcubes exhibited a high and stable capacity of 510.5 mA h g−1 over 200 cycles at 300 mA g−1.109 Ramaraju et al. synthesized a CuOx–rGO composite by the use of MOFs as precursors along with a metal oxide and graphene oxide as backbones through a facile two-step annealing process. The CuOx–rGO composite exhibited a high-rate capability and long-term cycling stability for LIBs, which can be seen in Fig. 4d and e.110 Zou et al. used MOFs as the precursor and the self-sacrificing template to prepare porous ZnO/ZnFe2O4/C hollow octahedra, as shown in Fig. 4f and g. At a much higher current density of 2000 mA g−1, ZnO/ZnFe2O4/C could maintain a specific capacity of up to 988 mA h g−1 over 100 cycles.111 Zhao et al. reported Fe3O4/VOx hollow microboxes, which were synthesized by template-engaged reaction between Prussian blue cubes and Na3VO4 and subsequent calcination, as displayed in Fig. 4h–j. The obtained Fe3O4/VOx@C showed a high reversible specific capacity of 742 mA h g−1 after 400 cycles at a current density of 500 mA g−1 and coulombic efficiency was up to 100%. Even at a current of 2000 mA g−1, Fe3O4/VOx@C exhibited a remarkable reversible capacity of 556 mA h g−1.112 Sun et al. reported hollow silica–copper–carbon nanocomposites which were firstly synthesized using copper metal–organic frameworks as skeletons to form Cu–MOF@SiO2 with subsequent thermal treatment. The hollow silica–copper–carbon nanocomposites exhibited a high and stable capacity of 495 mA h g−1 over 400 cycles at 500 mA g−1. The good electrochemical performance can be attributed to their hollow structure and the decomposition of the MOF skeleton.113 Kang et al. reported a porous hollow Co3O4/N–C polyhedron composite, which was synthesized using Co–MOFs as a sacrificial template, as shown in Fig. 4k. The specific capacities are maintained at stable values of ∼620 mA h g−1 within 2000 cycles at 1000 mA g−1.114 Zou et al. reported NiO/Ni/graphene with a hollow ball-in-ball nanostructure, which was synthesized from Ni–MOFs. The NiO/Ni/graphene showed a high reversible capacity of 1144 mA h g−1, an excellent rate performance of 805 mA h g−1 at 15
000 mA g−1 and excellent cyclability (nearly no capacity loss after 1000 cycles). The unique hierarchical hollow ball-in-ball structure of NiO/Ni/graphene could accommodate the volume change of active materials during repeated cycles. Moreover, the highly conductive graphene not only facilitated the fast electron transfer, but also promoted the formation of a stable solid electrolyte interface film. Therefore, the development of a facile method for synthesizing hollow carbon-based metal–oxide structures derived from MOFs for high-performance rechargeable batteries is highly desired.115 In addition to the MOF-derived hollow material mentioned above, NiSb-embedded carbon hollow spheres (NiSb ⊂ CHSs) were reported by adopting Ni–MOFs as a Ni source and template through a simple annealing and galvanic replacement reaction method. The as-prepared NiSb ⊂ CHSs exhibited an excellent lithium-ion battery performance, which was attributed to the unique structure in which NiSb nanoparticles were coated by the formed carbon particles. This could effectively solve the problem of vigorous volume changes during the Li+ insertion/extraction process. Moreover, the porous hollow and network structure could extremely reduce the pathway for fast Li+/electron transport and provided extra free space for alleviating the structural strain.116
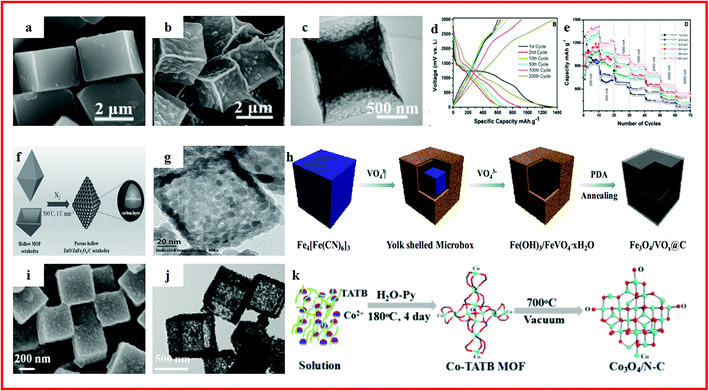 |
| Fig. 4 (a) High-magnification FESEM images of [Cu3(btc)2]n; (b) high-magnification porous cube FESEM images obtained by annealing [Cu3(btc)2]n; (c) TEM images of the CuO hollow cube. Reproduced with permission.109 Copyright 2017, Elsevier B.V. (d) Discharge–charge curves of the CuOx–rGO composite; (e) cycle performance of the CuOx–rGO composite. Reproduced with permission.110 Copyright 2016, Royal Society of Chemistry. (f) Schematic illustration of the preparation process of porous hollow ZnO/ZnFe2O4/C octahedra; (g) TEM image of the ZnO/ZnFe2O4 nanocomposite. Reproduced with permission.111 Copyright 2014, WILEY-VCH. (h) Schematic illustration of the fabrication of Fe3O4/VOx@C microboxes starting from Prussian blue cubes; (i) SEM images of PB microcubes; (j) TEM images of Fe(OH)3/FeVO4·xH2O. Reproduced with permission.112 Copyright 2017, American Chemical Society. (k) Schematic diagram of the preparation of the Co3O4/N–C composite. Reproduced with permission.114 Copyright 2017, American Chemical Society. | |
2.3 MOF-derived hollow metal sulfides/carbons for lithium batteries
Metal sulfides have received growing attention as advanced electrode materials owing to their high theoretical capacity arising from their rich stoichiometric compositions and good electrical conductivity.117–119 However, their practical applications are hampered by pronounced volume expansion and contraction during repetitive charging/discharging processes and sluggish ion/electron-transport kinetics, which result in a poor cycle life and unsatisfactory rate performance.120–122 One interesting way to overcome these problems is to synthesize hollow sulfide composites such as hollow sulfide/carbon materials. The hollow structure can help to shorten the lithium-ion diffusion length and mitigate volume change stress. Wrapping metal sulfides with a carbon layer is also an effective approach to enhance the electrical conductivity and maintain the structural integrity of the composite. What's more, it can help to suppress the dissolution of polysulfides.123–125 For example, Zhang et al. reported a rational design and synthesis of CoS2 ultrafine nanoparticles embedded in N-doped carbon nanotube hollow frameworks via the direct calcination of metal–organic frameworks and a subsequent sulfidation treatment. CoS2/NCNTF could maintain a specific capacity of up to 937 mA h g−1 at a current density of 1000 mA g−1 with a cycle life longer than 160 cycles. The good electrochemical performance can be attributed to its prominent structural and compositional advantages, which can help the material exhibit not only enhanced lithium storage properties but also an excellent cycling stability as an electrode material for lithium-ion batteries.126 Liu et al. reported a top-down route applying a room-temperature method to synthesize hollow cobalt sulfide nanoparticles embedded in graphitic carbon nanocages (HCSP ⊂ GCC) with Co-based ZIF-67 as the template. HCSP ⊂ GCC showed a high energy density of 707 W h kg−1, excellent rate performance with high capacities of 536, 489, 438, 393, 345, and 278 mA h g−1 at different current densities of 0.2, 0.5, 1, 2, 5, and 10C, respectively, and distinguished cycling stability (≈26% capacity loss after 150 cycles at 1C with a capacity retention of 365 mA h g−1). Even at 0.01–3.0 V, a higher stable capacity of 1600 mA h g−1 at a current density of 100 mA g−1 can be achieved. The outstanding electrochemical performance and novel and facile synthesis of HCSP ⊂ GCC provided a prospective insight into its practical application in future LIBs.127Table 1 gives a brief summary and comparison of hollow materials derived from MOFs for application in LIBs.
Table 1 Comparison of hollow materials derived from MOFs for application in LIBs
Original MOFs |
Sample |
Morphology |
Capacitance |
Cycling stability |
Ref. |
Co–MOF |
Co3O4 |
Dodecahedron |
1550 mA h g−1 at 100 mA g−1 |
1335 mA h g−1 after 100 cycles |
83
|
Co–MOF |
Co3O4 |
Parallelepipeds |
1115 mA h g−1 at 100 mA g−1 |
No capacity fading over the first 50 cycles |
84
|
Co–MOF |
Co3O4 |
Microfibers |
1177.4 mA h g−1 at 100 mA g−1 |
76.6% capacity retention at 100 mA g−1 in the 200th cycle |
85
|
Co–MOF |
Co3O4 |
Polyhedrons |
642 mA h g−1 at 500 mA g−1 |
96.9% capacity retention at 500 mA g−1 in the 200th cycle |
86
|
Cu–MOF |
CuO |
Octahedra |
1208 mA h g−1 at 100 mA g−1 |
470 mA h g−1 after 100 cycles |
91
|
Cu–MOF |
CuO/Cu2O |
Polyhedrons |
740 mA h g−1 at 100 mA g−1 |
Null |
92
|
Ni–MOF |
NiO |
Quasi-nanospheres |
392 mA h g−1 at 3200 mA g−1 |
760 mA h g−1 at 200 mA g−1 after 100 cycles |
96
|
Cu–Ni–MOF |
CuO@NiO |
Microsphere |
1218 mA h g−1 at 100 mA g−1 |
Reversible capacity can be retained at 1061 mA h g−1 after 200 cycles |
97
|
Co–MOF |
NiCo2O4/NiO |
Dodecahedron |
1535 mA h g−1 at 200 mA g−1 |
97.2% retention after 100 cycles |
98
|
Mn–MOF |
Mn2O3 |
Microspheres |
611 mA h g−1 at 100 mA g−1 |
582 mA h g−1 after 60 cycles |
99
|
MOF |
NiFe2O4 |
Cubes |
636 mA h g−1 at 8000 mA g−1 |
447 mA h g−1 at 5 A g−1 after 100 cycles |
106
|
MOF |
ZnFe2O4 |
Cubes |
449 mA h g−1 at 8000 mA g−1 |
390 mA h g−1 at 5 A g−1 after 100 cycles |
106
|
MOF |
CoFe2O4 |
Cubes |
380 mA h g−1 at 8000 mA g−1 |
290 mA h g−1 at 5 A g−1 after 100 cycles |
106
|
NMOFs |
CoFe2O4 |
Nanocubes |
1043 mA h g−1 at 1C |
Null |
107
|
NMOFs |
NiFe2O4 |
Nanocage |
975 mA h g−1 at 1C |
652 mA h g−1 at 10C after 200 cycles |
108
|
Cu–MOF |
CuO/C |
Microcubes |
1150.9 mA h g−1 at 100 mA g−1 |
510 mA h g−1 at 100 mA g−1 after 200 cycles |
109
|
Cu–MOF |
CuOx–rGO |
Polyhedron |
1490 mA h g−1 at 220 mA g−1 |
1100 mA g−1 after 600 cycles |
110
|
FeIII–MOF-5 |
ZnO/ZnFe2O4/C |
Octahedra |
1390 mA h g−1 at 500 mA g−1 |
988 mA h g−1 at 2000 mA g−1 after 100 cycles |
111
|
MOF |
Fe3O4/VOx |
Microboxes |
556 mA h g−1 at 2000 mA g−1 |
742 mA h g−1 after 400 cycles |
112
|
Cu–MOF |
H-SCC |
Nanocomposite |
492 mA h g−1 at 500 mA g−1 |
99.5% capacity retention at 500 mA g−1 from the 4th to the 400th cycle |
113
|
Co–MOF |
Co3O4/N–C |
Polyhedrons |
620 mA h g−1 at 1000 mA g−1 |
86.4% capacity retention after 2000 cycles |
114
|
Ni–MOF |
NiO/Ni/graphene |
Ball-in-ball |
805 mA h g−1 at 15 000 mA g−1 |
Nearly no capacity loss after 1000 cycles |
115
|
Ni–MOF |
NiSb ⊂ CHSs |
Spheres |
497.3 mA h g−1 at 100 mA g−1 |
309 mA h g−1 after 1000 cycles |
116
|
Co–MOF |
CoS2/NCNTF |
Nanoparticles |
1187 mA h g−1 at 1000 mA g−1 |
937 mA h g−1 at 1.0 A g−1 after 160 cycles |
126
|
Co–MOF |
HCSP ⊂ GCC |
Nanoparticles |
540 mA h g−1 at 0.25C |
74% capacity retention at 1C in the 150th cycle |
127
|
2.4 MOF-derived hollow materials for Li–S batteries
Li–S batteries have attracted considerable attention due to their low competitive cost, minimum environmental impact, outstanding theoretical capacity of 1675 mA h g−1 and high specific energy density of 2500 W h kg−1.128–130 Consequently, Li–S batteries are considered to be one of the most promising energy storage devices for next-generation high energy density rechargeable batteries. Meanwhile, the utilization of sulfur as a cathode material has additional advantages as sulfur is a promising low cost, naturally abundant and environmentally benign material.131–134 However, apart from these desirable advantages, lithium–sulfur batteries suffer from several inherent drawbacks.128,135 Firstly, sulfur shows poor electronic conductivity (5.0 × 10−30 S cm−1 at 25 °C). Secondly, the high solubility of long-chain polysulfides (Li2Sn, 4 ≤ n ≤ 8) and intermediate reaction species formed during the charge/discharge processes leads to loss of active materials and poor cycle life. Particularly, the dissolved polysulfide ions shuttle between the S cathode and Li anode during cycling, thus causing the precipitation of insoluble and insulating Li2S2/Li2S on the surface of the electrodes. Finally, the large volumetric expansion/shrinkage of sulfur during lithiation/delithiation gradually decreases the mechanical integrity and stability of the cathode.136 To address the above issues, one effective solution is to design novel porous sulfide composites such as porous hollow sulfide/carbon materials. Sulfur/carbon composites as cathode materials can optimize sulfur utilization and improve cycle stability as well.
Lately, Chen and his group reported a self-templated synthesis method and a simple sulfidation process to synthesize hollow nanopolyhedra with carbon shells and inlaid polar Co9S8 nanocrystals, which can be seen in Fig. 5a–d. The Co9S8/C–S composite showed a high specific capacity, long-term cycling stability (Fig. 5e–g), and remarkable cycle stability even with a high areal mass loading of sulfur, which was attributed to the hollow nanopolyhedra with large inner space that could accommodate high sulfur loading by spatial confinement and buffer the volume variation, and the embedded nanocrystals are highly polar and quasi-metallic and could strongly bind with polysulfides and restrict their outward diffusion.137
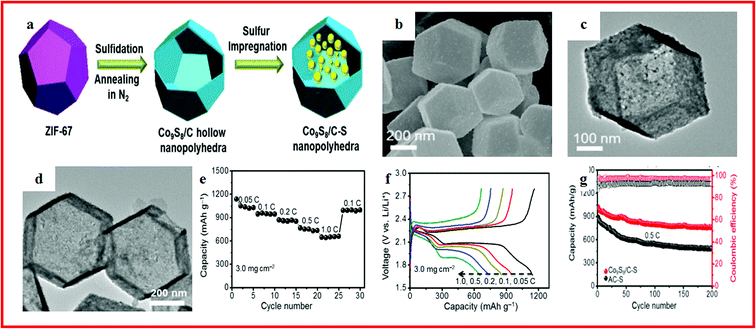 |
| Fig. 5 (a) Schematic illustration of the synthesis process of Co9S8/C–S nanopolyhedra; (b, c) SEM and TEM images of Co9S8/C hollow nanopolyhedra; (d) TEM images of Co9S8/C hollow nanopolyhedra; (e) discharge capacity of Co9S8/C–S; (f) voltage profiles of Co9S8/C–S; (g) cycling performance of the Co9S8/C–S cathode for 1000 cycles. Reproduced with permission.137 Copyright 2017, Elsevier. | |
2.5 MOF-derived hollow materials for Li–Se batteries
Selenium (Se) has attracted considerable attention as one of the most competitive cathode materials for lithium–selenium (Li–Se) batteries.138,139 Compared with sulfur, Se has a similar lithiation mechanism, following the reaction of 2Li+ + Se + 2e− ↔ Li2Se. During this reaction, two electrons are being converted. Se has a superior electrical conductivity of 1 × 10−5 S cm−1 at 25 °C which is much higher than that of sulfur (5 × 10−30 S cm−1). Moreover, Se provides a theoretical volumetric capacity density of 3253 mA h cm−3 based on 4.82 g cm−3 which is higher than that of sulfur (3467 mA h cm−3 based on 2.07 g cm−3), which ensures higher active material utilization as well as better rate capability at some level.140 However, its theoretical gravimetric capacity is 675 mA h g−1, which is considerably lower than that of sulfur. Se cathodes also have to face the low theoretical gravimetric capacity and large volume changes generated during delithiation–lithiation processes, which restrict their coulombic efficiency and cycling performance.135,141
One efficient way to solve these problems is to combine Se with conductive hollow porous carbon materials. The hollow porous structure can serve as a buffer layer to alleviate volume changes during the lithiation/delithiation process and improve the contact area between the electrode material and electrolyte for rapid ion diffusion. The carbon materials can provide an unhindered pathway for electrons.142 Liu et al. proposed a facile hydrothermal method followed by carbonization treatment to prepare a kind of novel hollow hierarchical porous carbon sphere using MOF precursors. Such MOF-derived hollow hierarchical porous carbon spheres (MHPCSs) were composed of masses of hollow carbon bubbles with sizes of 10–20 nm interconnected with each other. This kind of unique structure could not only make Se firmly confined in the micro–mesopores of MHPCSs by a vapor-melting diffusion route but also provide additional buffer space to adjust the volume change of Se during the charge/discharge process. When used as a Li–Se cathode material, the MHPCS/Se composite showed superior comprehensive battery properties including high rate capacity, long-term cycling stability and excellent coulombic efficiency.143
3. MOF-derived hollow materials for sodium-ion batteries
As lithium resources continue to decline worldwide, the next generation of portable electronics will most likely be powered by something other than LIBs.144–146 Recently, SIBs have attracted intense attention as a potential alternative to LIBs in the field of future large-scale energy storage due to the high abundance of sodium, the low cost of sodium sources, higher system safety, extensive distribution, and its similar storage mechanism and components to lithium.147–150 Unfortunately, the fact that the sodium ion radius (1.02 Å) is larger than that of the lithium ion (0.69 Å) makes rapid Na+ intercalation/extraction in active materials more difficult. Besides the kinetic issue, the larger Na+ radius is also relevant for the large volume change during sodium insertion and extraction.151–156 Up to now, researchers have tried countless kinds of active materials in order to obtain excellent electrochemical performance. The most frequently reported materials for SIBs are carbon materials and metal oxide materials.
3.1 MOF-derived hollow metal oxides for sodium-ion batteries
Recently, many studies have reported the use of Cu-based MOFs as precursors or templates to synthesize CuO nanostructures. Besides, CuO derived from MOFs was also used in sodium-ion batteries (SIBs) and exhibited excellent electrochemical performance.157–159 For example, Zhang et al. proposed a facile annealing method to prepare porous hollow CuO using MOF precursors (HKUST-1) in air. The porous hollow CuO exhibited a high initial reversible capacity of 612 mA h g−1 and a good capacity retention of 83% after 50 cycles with superior rate capability for SIBs.160 Zhang et al. presented a cost-effective method to synthesize porous CuO/Cu2O hollow octahedrons from Cu–MOF precursors by direct annealing. They showed a high reversible capacity of 415 mA h g−1 over 50 cycles at a current density of 50 mA g−1 with good cycling stability and an excellent rate performance. The superior electrochemical performance was attributed to their porous hollow structure and synergistic effect between CuO and Cu2O. In addition, Cu-based MOFs have received widespread attention as anode materials for SIBs due to their low cost, high theoretical capacity and rich redox reaction.161 Huang's group prepared MOF-derived Prussian blue microcubes and used them as self-sacrificial templates to fabricate hollow MgFe2O4 microboxes via the process of hydrolysis, ion exchange and subsequent calcination. The material exhibited a high capacity of 406 mA h g−1 at 300 mA g−1 and a reversible capacity of 135 mA h g−1 after 150 cycles, as shown in Fig. 5n–p.162 These results suggest that MOF-derived hollow materials should be suitable for the next generation of electrode materials for SIBs with superior electrochemical performance.
3.2 MOF-derived hollow metal oxides/carbons for sodium-ion batteries
With similar strategies to LIBs, metal oxide engineering and carbon modifications are typical treatments to improve the conversion reaction kinetics, increase the electronic conductivity, and accommodate the volume change.163,164 Kang et al. proposed a porous hollow Co3O4 with N-doped carbon coating (Co3O4/N–C) polyhedron composite using Co–MOFs as a sacrificial template. Co3O4/N–C polyhedrons showed a high specific capacity of 229 mA h g−1 after 150 cycles at a current density of 1000 mA g−1. Furthermore, MOFs are promising precursors and templates to synthesize binary oxides and graphene-based composites.165 Ramaraju et al. reported a two-step annealing method to synthesize a CuOx–rGO composite (CuO/Cu2O hollow polyhedrons on rGO) with Cu–MOFs as precursors and graphene oxide as the backbone. The CuOx–rGO composite showed a high specific capacity and good cycling stability. The superior electrochemical performance was attributed to good structural scaffolds as they stabilize the physical structure during charge-induced volume expansion, which further improved the conductivity of metal oxides. Besides, rGO can overcome the poor electrical conductivity of the MOF.166
Hierarchical hollow materials can effectively mitigate the volume expansion and promote the structural stability of electrode materials, leading to a long cycle life.167–169 Zou et al. reported NiO/Ni/Graphene composites with a hierarchical hollow ball-in-ball structure, which were synthesized by annealing Ni–MOFs, as displayed in Fig. 6a–c. The NiO/Ni/Graphene showed an excellent rate performance (207 mA h g−1 at 2 A g−1) and long-term cycling stability (0.2% specific capacity fading per cycle). The unique hierarchical hollow ball-in-ball structure of NiO/Ni/graphene could accommodate the volume change of active materials during repeated cycles. Moreover, the highly conductive graphene not only facilitated the fast electron transfer, but also promoted the formation of a stable solid electrolyte interface (SEI) film.115 Li et al. reported a hierarchical hollow hybrid Fe2O3@MIL-101(Fe)/C composite, which was obtained by a facile template-free procedure combined with a solvothermal synthesis reaction and subsequent calcination. The Fe2O3@MIL-101(Fe)/C exhibited a high capacity of 710 mA h g−1 which can be retained at 662 mA h g−1 after 200 cycles. The good electrochemical performance can be attributed to its intrinsic hollow nanostructure and nanoscale building blocks.170 Liu et al. reported a simple solvothermal reaction to synthesize a Ni3S2/Co9S8/N-doped carbon composite with a hollow spherical structure by utilizing a binary MOF as the precursor. After a controlled carbonization and sulfurization process, the structure of the MOF could be maintained, which could be seen in Fig. 6d and e. A capacity of 419.9 mA h g−1 at a current density of 100 mA g−1 was achieved after 100 cycles. Even at a higher discharge/charge current of 1000 mA g−1, the capacity retention was 92% after 300 cycles, as shown in Fig. 6f. This exceptional performance can be attributed to the unique nano-architecture.32
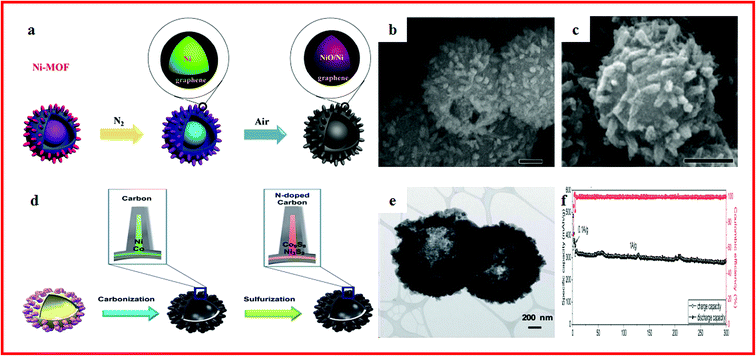 |
| Fig. 6 (a) Schematic illustration of the formation of NiO/Ni/Graphene composites; (b) SEM images of Ni–MOFs; (c) SEM images of the NiO/Ni/Graphene composite. Reproduced with permission.115 Copyright 2015, American Chemical Society. (d) Schematic illustration of the synthetic strategy for obtaining the Ni3S2/Co9S8/N-doped carbon composite; (e) TEM images of Ni3S2/Co9S8/N-doped carbon; (f) long-term cycling performance of Ni3S2/Co9S8/N-doped carbon. Reproduced with permission.32 Copyright 2017, Royal Society of Chemistry. | |
These studies demonstrate that novel electrode materials have enhanced sodium storage kinetics, improved volume expansion mitigation capability, and high electrical conductivity to enable high rate performance. On the one hand, the unique structure can effectively mitigate the volume expansion during the sodiation process.
In addition to the battery types above, MOF-derived hollow materials can also be used for other batteries, such as potassium-ion batteries (KIBs). Potassium-ion batteries have attracted significant attention due to their low cost and long term technological sustainability, but suitable cathode/anode materials still need to be developed.171,172 MOF-derived hollow structures can be good candidates; for example, Xiong et al. synthesized nitrogen-doped carbon nanotubes (NCNTs) by pyrolyzing cobalt-containing MOFs as a KIB anode. The NCNT anode showed an improved rate performance (102 mA h g−1 at a high current density of 2000 mA g−1) and stable cycling life without obvious capacity loss after 500 cycles at 2000 mA g−1.173 The edge-open layer-alignment hollow structure enables a facile and fast intercalation of K ions, effectively improving the rate capability of graphite anodes for KIBs.
4. MOF-derived hollow materials for supercapacitors
Electrochemical capacitors, also called supercapacitors (SCs) or ultracapacitors with high power density, fast charge rate, long cycle life and no harm to the environment, have attracted great attention.174–180 They can be classified into two categories: one is pseudo-capacitors, in which reversible redox reactions mainly occur on the electrode material surface. This type of SC usually employs active materials with increased energy density, such as transition metal oxides, conductive polymers and sulfides. The other one is electrochemical double-layer capacitors, which usually use carbon materials with a high surface area and porosity.181–185 To achieve excellent performance in terms of power density and energy storage capability, high conductivity and large electrolyte-accessible surface areas are two major prerequisites for the active materials used in SCs.186,187 MOF-derived hollow materials, which have a high surface area and tailored pore size, are attractive as high-performance supercapacitor electrodes.
4.1 MOF-derived hollow metal oxides for supercapacitors
Transition metal oxides exhibit potential application in energy conversion and storage because of their reversible surface redox reactions. Particularly, the first-row transition metal (Co, Fe, Ni, and Mn) oxides possessing mutable valence states have been considered as promising electrode materials for supercapacitors.188–191 MOF-derived hollow transition metal oxides with large accessible internal surface areas can facilitate the diffusion of ions through the highly porous substructures, which are critical for the electrochemical activity of the electrodes.192,193 Among them, Co3O4 is considered as a promising candidate electrochemical material because of its low cost, environmental benignity, and high catalytic activity. Zhang et al. reported porous hollow Co3O4 with rhombic dodecahedral structures, which was synthesized by the calcination of ZIF-67 ([Co(mim)2; mim = 2-methylimidazolate]) rhombic dodecahedral microcrystals. Benefiting from its excellent crystal and lattice integrity, the material exhibited a high specific capacitance of 1100 F g−1 and an outstanding capacity retention of 95.1% after 6000 cycles.194 Hu and Liu developed a stepwise strategy to produce novel starfish-shaped porous Co3O4/ZnFe2O4 hollow nanocomposites using Co3[Co(CN)6]2·nH2O and partial Fe(III)-substituted MOF-5 (FeIII–MOF-5) as precursors and sacrificial templates, which can be seen in Fig. 7a. The starfish-shaped porous Co3O4/ZnFe2O4 composites exhibited a specific capacitance as high as 326 F g−1 at 1 A g−1 and a high energy density of 82.5 W h kg−1 at a power density of 675 W kg−1, which may be attributed to the unique morphology of Co3O4/ZnFe2O4, as well as surface and interface exchange coupling effects.195 Guan et al. depicted a new approach to produce hollow and porous NiCo2O4 nanowall arrays on a flexible carbon cloth current collector using 2D Co–MOF solid nanowall arrays as precursors and templates, through an ion-exchange and etching process with an additional annealing treatment, as displayed in Fig. 7b. The hollow NiCo2O4 nanostructure arrays showed good capacitive performances because it could provide rich reaction sites and a short ion diffusion path.196 Li et al. reported a facile one-pot, template-free solvothermal method to synthesize nanorod-composed yolk–shell Ni/Zn–MOF microspheres. Subsequently, a new type of hierarchical double-shelled NiO/ZnO hollow sphere was obtained by thermal treatment of the yolk–shell Ni/Zn–MOF, as shown in Fig. 7c. The obtained flexible supercapacitor based on the hierarchical double-shelled NiO/ZnO hollow sphere showed a high energy density and a superior capacitance of 497 F g−1 at 1.3 A g−1 and the specific capacitance increased from 408 F g−1 to 478 F g−1 after 2000 cycles of charge–discharge at a current density of 5.2 A g−1.193 Lv and co-workers demonstrated the application of a nickel–cobalt layered double hydroxide (Ni–Co LDH) in supercapacitors. The Ni–Co LDH hollow structure was synthesized by using ZIF-67 nanocrystals as templates and etching in a nitrate solution, as displayed in Fig. 7d. The composite showed a specific capacitance of 790C g−1 at a current density of 2 A g−1 and a capacity retention of 82.9% after 1000 charge/discharge cycles.197 Similarly, Zhang et al. reported a hollow Ni–Co layered double hydroxide (LDH) which was synthesized with rhombic dodecahedral ZIF-67 as the self-sacrificial template and cobalt precursor. Electrochemical tests revealed that the material displayed a specific capacity of 1530 F g−1 at 1.0 A g−1.198
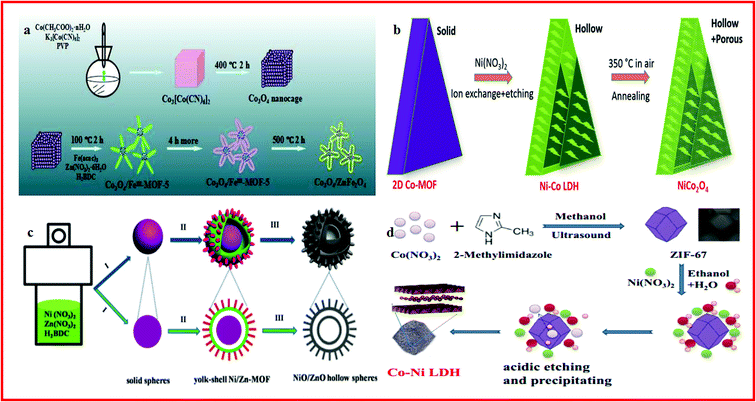 |
| Fig. 7 (a) Schematic illustrating the synthesis procedure of the starfish-shaped porous Co3O4/ZnFe2O4 hollow nanocomposite. Reproduced with permission.195 Copyright 2015, American Chemical Society. (b) Schematic illustration of the formation of the hollow NiCo2O4 nanostructure from 2D Co–MOF solid nanowalls. Reproduced with permission.196 Copyright 2017, WILEY-VCH. (c) Schematic of the formation process of the yolk–shell Ni/Zn–MOF microspheres and double-shelled NiO/ZnO hollow spheres. Reproduced with permission.193 Copyright 2016, Royal Society of Chemistry. (d) Schematic illustration of the synthesis procedure of Ni–Co LDH. Reproduced with permission.198 Copyright 2017, Springer Science + Business Media New York. | |
4.2 MOF-derived hollow metal sulfides for supercapacitors
Metal sulfides have drawn considerable attention because of their high theoretical capacitance, low cost and natural abundance.199–203 However, metal sulfides usually suffer from poor structural stability and low electronic conductivity, which can restrict their practical specific capacity and cycling performance during the charge/discharge process.204–208 One highly effective way to overcome these problems is to prepare nano/submicro-scale materials to shorten the diffusion distance of ions and electrons and provide more contact area between the electrolyte and electrode. Another common approach is constructing hollow structures which can relieve the volume change and increase the active reaction sites, resulting in the enhanced specific capacitance and cycling performance of the electrode materials.
Nickel, cobalt and nickel cobalt sulfides are promising supercapacitor electrode materials. Various cobalt and nickel cobalt sulfides with hollow structures have been well investigated, which always show enhanced specific capacitance and cycling stability.209–212 For instance, Ma et al. reported a simple and cost-effective method to synthesize NiS hierarchical hollow cubic structures by an anion exchange reaction of a low-cost Ni formate framework precursor with S2−, as shown in Fig. 8a and b. The NiS hierarchical hollow cubic structures showed a high specific capacity of 874.5 F g−1 at 1 A g−1, stability for 3000 cycles with a nearly 90.2% capacity retention at 4 A g−1. The asymmetric supercapacitor had an enhanced energy density of 34.9 W h kg−1 at a power density of 387.5 W kg−1.213 Jiang et al. developed an effective strategy to synthesize amorphous CoS hollow polyhedra with ZIF-67 nanocrystals as templates, as displayed in Fig. 8c–e. The amorphous CoS hollow polyhedra showed excellent electrochemical properties.214 Li and co-workers demonstrated the application of NiS2/ZnS hollow spherical nanocomposites in supercapacitors. The NiS2/ZnS hollow spherical nanocomposite was synthesized with a bimetallic Ni/Zn–BDC (BDC¼ 1,4-benzenedicarboxylate) MOF as both the precursor and the self-sacrificing template and thioacetamide as the sulfur source (Fig. 8f–h). It exhibited an outstanding capacitance of 1198 F g−1 at a current density of 1 A g−1. Moreover, an energy density of 28.0 W h kg−1 at a power density of 478.9 kW kg−1 was achieved for the assembled asymmetric supercapacitor.215
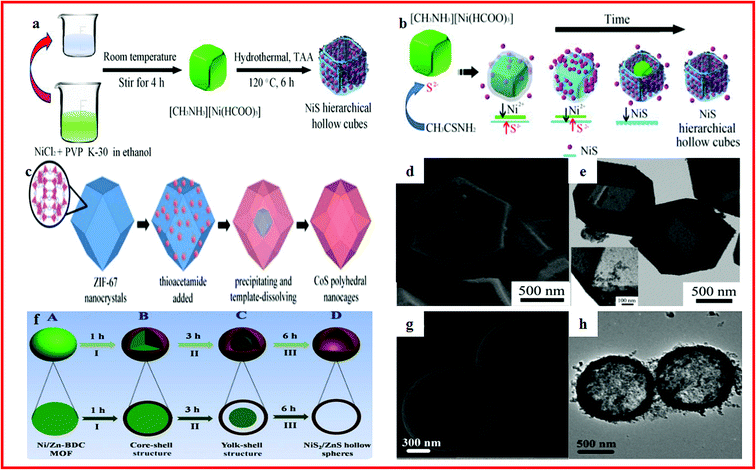 |
| Fig. 8 (a) Schematic illustration of the fabrication processes of NiS hierarchical hollow cubes; (b) schematic illustration of the formation process of NiS hierarchical hollow cubes. Reproduced with permission.213 Copyright 2017, Elsevier B.V. (c) The illustration of the formation of CoS polyhedral nanocages; (d, e) SEM and TEM images of the nanocages. Reproduced with permission.214 Copyright 2014, Royal Society of Chemistry. (f) Schematic illustration of the formation process of the NiS2/ZnS hollow nanospheres; (g) SEM images of the Ni/Zn-BDC MOF spheres; (h) TEM images of Ni/Zn-BDC. Reproduced with permission.215 Copyright 2016, Royal Society of Chemistry. | |
4.3 MOF-derived hollow carbon materials for supercapacitors
Porous carbons are the most widely used electrode materials for SCs, especially those with hollow nanostructures, due to their remarkable advantages such as an extremely high surface area, excellent chemical stability, relatively low cost, controlled pore structure and desirable electrical conductivity.216–218 When using MOFs to synthesize porous carbon materials, in addition to composites with template compounds to construct hollow structures, MOFs themselves can also work as precursors to obtain high quality porous carbons, and this can contribute to unique hierarchical porous carbon structures.219,220 For example, by carbonizing the prepared Zn–metal–organic frameworks (ZIF-8) and lotus pollen derived hollow carbon sphere composite precursor, a hierarchical interpenetrating 3D hollow carbon material can be formed, as displayed in Fig. 9a. The obtained sample inherits the large specific surface area of the MOF and the hollow structure of the lotus pollen derived carbon sphere, and shows a high specific capacitance of 280 F g−1 in a 6 M KOH electrolyte at a current density of 1 A g−1 and a superb cycle stability (89.0% capacitance retention after 10
000 cycles) at 0.5 A g−1 (Fig. 9b and c).221
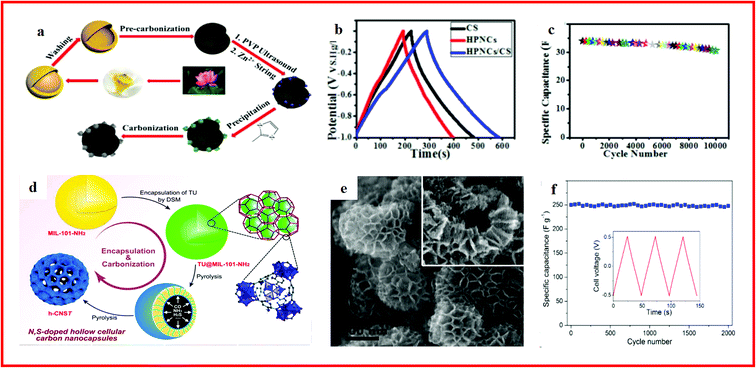 |
| Fig. 9 (a) Schematic illustration of the fabrication approach of the hierarchical interpenetrating 3D hollow HPNCs/CS composite; (b) various GC curves obtained at a current density of 1 A g−1; (c) long-term cycling performance of the HPNCs/CS composite. Reproduced with permission.221 Copyright 2017, Royal Society of Chemistry. (d) Schematic representation of the encapsulation of TU into MIL-101-NH2 by DSM and subsequent formation of N/S co-doped hollow cellular carbon nanocapsules (h-CNST); (e) SEM image of the h-CNS900 hollow cellular nanocapsules; (f) cycling stability of hCNS900 at 5 A g−1 over 2000 cycles. Reproduced with permission.222 Copyright 2017, Elsevier. | |
Moreover, nitrogen and sulfur doping can effectively increase the wettability and electrical conductivity of carbon materials, and doped hollow carbon materials can be prepared by using MOF composites as precursors. For example, Zhu and co-workers reported the synthesis of N/S co-doped hollow cellular carbon nanocapsules through the pyrolysis of a thiourea (TU) encapsulated MOF composite (Fig. 9d), which showed a unique hierarchical structure (Fig. 9e) with superior supercapacitor performance (Fig. 9f). The superior electrochemical performance was attributed to the hollow macroporous cavities and the mesopores of the shells, which can act as ion-buffering reservoirs and minimize the diffusion distance for the electrolyte ions, resulting in the outstanding performance.222
5. Conclusions and outlook
Due to the current urgent demand for high-performance energy storage and conversion systems, the development of novel electrode materials is of vital importance. Recent research progress mentioned above has demonstrated that MOFs have been widely used as sacrificial templates to generate highly oriented hollow nanostructures, including carbon, metal oxides, metal carbides, metal sulfides and their composites. MOF-derived hollow nanomaterials usually possess a high surface area, high porosity, adjustable pore size, and controllable structure. These advantages can highly meet the required features of high performance electrode materials, which makes MOF-derived hollow nanomaterials an exciting interdisciplinary research area for obtaining MOF-derived hollow structured electrode materials with superior performance for electrochemical energy storage.
The construction of various functional hollow nanostructures from MOFs is mainly controlled by the manipulation of precursors and/or the conversion process. Despite the substantial advances, it can be found that most investigated MOF-based precursors are confined to a few well-studied MOFs, such as PBAs and ZIFs. Besides, the obtained hollow materials are always metal oxides, sulfides, carbon, or their composite, and most of the morphologies are particles with highly isotropic shapes. Thus, exploring new MOFs, synthetizing metal carbides, pnictides, and chalcogenides, or their composites with carbon species, and constructing hollow structures with high complexity or hierarchical/3D self-supported architectures are still highly desirable for functional hollow nanostructures. Meanwhile, although the self-templating feature of many MOF-derived processes simplifies the synthetic procedures, universal and general synthetic conversion approaches with better controllability and scalability are still needed, because most studies are based on individual systems, and the ultimate goal of these research studies is real application. On the other hand, a fundamental understanding of the formation process of MOF-derived hollow structures and the relationships between the composition/structure and their electrochemical properties is still lacking, so theoretical calculation and modeling, besides experimental studies, would play dominating roles in future studies.
Overall, the recent progress of MOF-derived hollow materials used in batteries and supercapacitors is summarized. Although MOF-derived hollow materials have shown attractive performance in previous studies, there is still a long way to go in industrializing and commercializing these materials. We hope that this review can open up a new avenue for exploiting the great potential of hollow materials derived from MOFs in energy conversion and storage.
Conflicts of interest
There are no conflicts to declare.
Acknowledgements
This work was supported by the National Natural Science Foundation of China (21475115), Program for University Innovative Research Team of Henan (15IRTSTHN001), Henan Provincial Science and Technology innovation team (C20150026), Nanhu Scholars Program of XYNU, Nanhu Scholars Program for Young Scholars of XYNU, Natural Science Foundation of Henan Province (162300410230) and Henan Science and Technology Cooperation Project (172106000064).
References
- S. Li, J. Niu, Y. C. Zhao, K. P. So, C. Wang, C. A. Wang and J. Li, Nat. Commun., 2015, 6, 7872 CrossRef CAS PubMed.
- J. Deng, M. M. Li and Y. Wang, Green Chem., 2016, 18, 4824 RSC.
- D. B. Yu, B. Wu, L. Ge, L. Wu, H. T. Wang and T. W. Xu, J. Mater. Chem. A, 2016, 4, 10878 CAS.
- N. N. Guo, M. Li, X. K. Sun, F. Wang and R. Yang, Green Chem., 2017, 19, 2595 RSC.
- T. Ouyang, K. Cheng, Y. Y. Gao, S. Y. Kong, K. Ye, G. L. Wang and D. X. Cao, J. Mater. Chem. A, 2016, 4, 9832 CAS.
- S. S. Zheng, X. R. Li, B. Y. Yan, Q. Hu, Y. X. Xu, X. Xiao, H. G. Xue and H. Pang, Adv. Energy Mater., 2017, 18, 201602733 Search PubMed.
- B. Y. Guan, L. Yu, X. Wang, S. Y. Song and X. W. Lou, Adv. Mater., 2017, 29, 1605051 CrossRef PubMed.
- W. Xia, A. Mahmood, R. Q. Zou and Q. Xu, Energy Environ. Sci., 2015, 8, 1837 CAS.
- L. Wang, Y. Z. Han, X. Feng, J. W. Zhou, P. F. Qi and B. Wang, Coord. Chem. Rev., 2016, 307, 361 CrossRef CAS.
- W. Z. Bao, A. K. Mondal, J. Xu, C. Y. Wang, D. W. Su and G. X. Wang, J. Power Sources, 2016, 325, 286 CrossRef CAS.
- L. F. Chen, Y. Lu, L. Yu and X. W. D. Lou, Energy Environ. Sci., 2017, 10, 1777 CAS.
- Z. F. Wang, Y. S. Liu, C. W. Gao, H. Jiang and J. M. Zhang, J. Mater. Chem. A, 2015, 3, 20658 CAS.
- L. Wang, T. Wei, L. Z. Sheng, L. L. Jiang, X. L. Wu, Q. H. Zhou, B. Yuan, J. M. Yue, Z. Liu and Z. J. Fan, Nano Energy, 2016, 30, 84 CrossRef CAS.
- M. Shaibani, S. J. D. Smith, P. C. Banerjee, K. Konstas, A. Zafari, D. E. Lobo, M. Nazari, A. F. Hollenkamp, M. R. Hill and M. Majumder, J. Mater. Chem. A, 2017, 5, 2519 CAS.
- J. W. Choi and D. Aurbach, Nat. Rev. Mater., 2016, 1, 16013 CrossRef CAS.
- Y. Tang, Y. Zhang, W. Li, B. Ma and X. Chen, Chem. Soc. Rev., 2015, 44, 5926 RSC.
- H. W. Song, L. S. Shen, J. Wang and C. X. Wang, Nano Energy, 2017, 34, 47 CrossRef CAS.
- Z. M. Liu, X. Y. Yu, X. W. D. Lou and U. Paik, Energy Environ. Sci., 2016, 9, 2314 CAS.
- D. Kundu, E. Talaie, V. Duffort and L. F. Nazar, Angew. Chem., Int. Ed., 2015, 54, 3431 CrossRef CAS PubMed.
- L. Yu, J. F. Yang and X. W. D. Lou, Angew. Chem., Int. Ed., 2016, 55, 13422 CrossRef CAS PubMed.
- Y. Bai, Y. B. Dou, L. H. Xie, W. Rutledge, J. R. Li and H. C. Zhou, Chem. Soc. Rev., 2016, 45, 2327 RSC.
- J. K. Sun and Q. Xu, Energy Environ. Sci., 2014, 7, 2071 CAS.
- W. Liu, Y. Y. Mi, Z. Weng, Y. R. Zhong, Z. S. Wu and H. L. Wang, Chem. Sci., 2017, 8, 4285 RSC.
- J. T. Zhang, H. Hu, Z. Li and X. W. D. Lou, Angew. Chem., Int. Ed., 2016, 55, 3982 CrossRef CAS PubMed.
- B. Y. Xia, Y. Yan, N. Li, H. B. Wu, X. W. D. Lou and X. Wang, Nat. Energy, 2016, 1, 15006 CrossRef CAS.
- W. X. Liu, J. J. Huang, Q. Yang, S. J. Wang, X. M. Sun, W. N. Zhang, J. F. Liu and F. W. Huo, Angew. Chem., 2017, 129, 5604 CrossRef.
- A. Carné-Sánchez, I. Imaz, M. Cano-Sarabia and D. Maspoch, Nat. Chem., 2013, 5, 203 CrossRef PubMed.
- D. P. Cai, B. Liu, D. D. Wang, L. L. Wang, Y. Liu, B. H. Qu, X. C. Duan, Q. H. Li and T. H. Wang, J. Mater. Chem. A, 2016, 4, 183 CAS.
- Y. M. Chen, L. Yu and X. W. D. Lou, Angew. Chem., 2016, 128, 6094 CrossRef.
- H. B. Wu and X. W. D. Lou, Sci. Adv., 2017, 3, eaap9252 CrossRef PubMed.
- P. Wen, P. W. Gong, J. F. Sun, J. Q. Wang and S. R. Yang, J. Mater. Chem. A, 2015, 3, 13874 CAS.
- X. Y. Liu, F. Zou, K. W. Liu, Z. Qiang, C. J. Taubert, P. Ustriyana, B. D. Vogtb and Y. Zhu, J. Mater. Chem. A, 2017, 5, 11781 CAS.
- H. Li, M. Liang, W. Sun and Y. Wang, Adv. Funct. Mater., 2016, 26, 1098 CrossRef CAS.
- X. W. Liu, T. J. Sun, J. L. Huab and S. D. Wang, J. Mater. Chem. A, 2016, 4, 3584 CAS.
- J. Liang, Z. Liang, R. Zou and Y. Zhao, Adv. Mater., 2017, 29, 1701139 CrossRef PubMed.
- H. Zhang, J. Nai, L. Yu and X. W. D. Lou, Joule, 2017, 1, 77 CrossRef.
- L. Y. Chen, L. Zhang, Z. J. Chen, H. L. Liu, R. Luque and Y. W. Li, Chem. Sci., 2016, 7, 6015 RSC.
- M. Y. Tong, S. W. Liu, X. Zhang, T. X. Wu, H. M. Zhang, G. Z. Wang, Y. X. Zhang, X. G. Zhua and H. J. Zhao, J. Mater. Chem. A, 2017, 5, 9873 CAS.
- S. N. Liu, J. Zhou, Z. Y. Cai, G. Z. Fang, Y. S. Cai, A. Q. Pan and S. Q. Liang, J. Mater. Chem. A, 2016, 4, 17838 CAS.
- Y. Liang, J. Wei, Y. X. Hu, X. F. Chen, J. Zhang, X. Y. Zhang, S. P. Jiang, S. W. Tao and H. T. Wang, Nanoscale, 2017, 9, 5323 RSC.
- R. B. Wu, D. P. Wang, J. Y. Han, H. Liu, K. Zhou, Y. Z. Huang, R. Xu, J. Wei, X. D. Chen and Z. Chen, Nanoscale, 2015, 7, 965 RSC.
- X. Li, Q. Sun, J. Liu, B. W. Xiao, R. Y. Li and X. L. Sun, J. Power Sources, 2016, 302, 174 CrossRef CAS.
- C. Li, T. Q. Chen, W. J. Xu, X. B. Lou, L. K. Pan, Q. Chen and B. W. Hu, J. Mater. Chem. A, 2015, 3, 5585 CAS.
- G. L. Xia, D. Liu, F. C. Zheng, Y. Yang, J. W. Sua and Q. W. Chen, J. Mater. Chem. A, 2016, 4, 12434 CAS.
- D. Ji, H. Zhou, J. Zhang, Y. Y. Dan, H. X. Yang and A. H. Yuan, J. Mater. Chem. A, 2016, 4, 8283 CAS.
- J. Shao, T. Gao, Q. T. Qu, Q. Shi, Z. C. Zuo and H. H. Zheng, J. Power Sources, 2016, 324, 1 CrossRef CAS.
- W. Zeng, L. Wang, H. M. Shi, G. H. Zhang, K. Zhang, H. Zhang, F. L. Gong, T. H. Wang and H. G. Duan, J. Mater. Chem. A, 2016, 4, 8233 CAS.
- G. Huang, L. L. Zhang, F. F. Zhang and L. M. Wang, Nanoscale, 2014, 6, 5509 RSC.
- L. Yu, H. Hu, H. B. Wu and X. W. D. Lou, Adv. Mater., 2017, 29, 1604563 CrossRef PubMed.
- L. Zhang, H. B. Wu, S. Madhavi, H. H. Hng and X. W. D Lou, J. Am. Chem. Soc., 2012, 134, 17388 CrossRef CAS PubMed.
- X. J. Wang, J. Feng, Y. C. Bai, Q. Zhang and Y. D. Yin, Chem. Rev., 2016, 116, 10983 CrossRef CAS PubMed.
- X. Y. Yu, L. Yu and X. W. D. Lou, Adv. Energy Mater., 2016, 6, 1501333 CrossRef.
- L. Yu, H. B. Wu and X. W. D. Lou, Acc. Chem. Res., 2017, 50, 293 CrossRef CAS PubMed.
- D. B. Yu, B. Wu, J. Ran, L. Ge, L. Wu, H. T. Wang and T. W. Xu, J. Mater. Chem. A, 2016, 4, 16953 CAS.
- J. Qi, X. Y. Lai, J. Y. Wang, H. J. Tang, H. Ren, Y. Yang, Q. Jin, L. J. Zhang, R. B. Yu, G. H. Ma, Z. G. Su, H. J. Zhao and D. Wang, Chem. Soc. Rev., 2015, 44, 6749 RSC.
- R. R. Salunkhe, J. Tang, Y. Kamachi, T. Nakato, J. H. Kim and Y. Yamauchi, ACS Nano, 2015, 9, 6288 CrossRef CAS PubMed.
- J. Zhang, Z. Lyu, F. Zhang, L. Wang, P. Xiao, K. Yuan, M. Lai and W. Chen, J. Mater. Chem. A, 2016, 4, 6350 CAS.
- Z. H. Liu, L. Zhang, G. C. Xu, L. Zhang, D. Z. Jia and C. Y. Zhang, RSC Adv., 2017, 7, 11129 RSC.
- Y. Z. Wu, J. S. Meng, Q. Li, C. J. Niu, X. P. Wang, W. Yang, W. Li and L. Q. Mai, Nano Res., 2017, 10, 2364 CrossRef CAS.
- L. Zhang, H. B. Wu and X. W. D. Lou, J. Am. Chem. Soc., 2013, 135, 10664 CrossRef CAS PubMed.
- Z. X. Sun, F. X. Xin, C. Cao, C. C. Zhao, C. Shen and W. Q. Han, Nanoscale, 2015, 7, 20426 RSC.
- H. Jiang, D. Ren, H. Wang, Y. Hu, S. Guo, H. Yuan, P. Hu, L. Zhang and C. Li, Adv. Mater., 2015, 27, 3687 CrossRef CAS PubMed.
- J. F. Wu, Y. H. Song, R. H. Zhou, S. H. Chen, L. Zuo, H. Q. Hou and L. Wang, J. Mater. Chem. A, 2015, 3, 7793 CAS.
- H. Geng, Q. Zhou, Y. Pan, H. Gu and J. Zheng, Nanoscale, 2014, 6, 3889 RSC.
- Y. C. Yang, X. B. Ji, M. J. Jing, H. S. Hou, Y. R. Zhu, L. B. Fang, X. M. Yang, Q. Y. Chen and C. E. Banks, J. Mater. Chem. A, 2015, 3, 5648 CAS.
- Y. Zhong, X. Xia, F. Shi, J. Zhan, J. Tu and H. J. Fan, Adv. Sci., 2016, 3, 1500286 CrossRef PubMed.
- T. Liu, M. Jia, Y. Zhang, J. Han, Y. Li, S. J. Bao, D. Y. Liu, J. Jiang and M. W. Xu, J. Power Sources, 2017, 341, 53 CrossRef CAS.
- J. Qi, X. Lai, J. Wang, H. Tang, H. Ren, Y. Yang, Q. Jin, L. Zhang, R. Yu, G. Ma, Z. Su, H. Zhao and D. Wang, Chem. Soc. Rev., 2015, 44, 6749 RSC.
- Z. C. Zhang, Y. F. Chen, X. B. Xu, J. C. Zhang, G. L. Xiang, W. He and X. Wang, Angew. Chem., Int. Ed., 2014, 53, 429 CrossRef CAS PubMed.
- L. Shen, L. Yu, X. Y. Yu, X. Zhang and X. W. D. Lou, Angew. Chem., Int. Ed., 2015, 54, 1868 CrossRef CAS PubMed.
- L. L. Xing, G. G. Zhao, K. J. Huang and X. Wu, Dalton Trans., 2018, 47, 2256 RSC.
- Y. Feng, X. Li, Z. Shao and H. Wang, J. Mater. Chem. A, 2015, 3, 15274 CAS.
- W. Xiao, J. Zhou, L. Yu, D. H. Wang and X. W. D. Lou, Angew. Chem., Int. Ed., 2016, 55, 7427 CrossRef CAS PubMed.
- Y. C. Tan and H. C. Zeng, Chem. Commun., 2016, 52, 11591 RSC.
- A. Carné-Sánchez, I. Imaz, M. Cano-Sarabia and D. Maspoch, Nat. Chem., 2013, 5, 203 CrossRef PubMed.
- G. L. Xia, D. Liu, F. C. Zheng, Y. Yang, J. W. Sua and Q. W. Chen, J. Mater. Chem. A, 2016, 4, 12434 CAS.
- Y. Liang, J. Wei, Y. X. Hu, X. F. Chen, J. Zhang, X. Y. Zhang, S. P. Jiang, S. W. Tao and H. T. Wang, Nanoscale, 2017, 9, 5323 RSC.
- J. J. Ma, H. J. Wang, X. Yang, Y. Q. Chai and R. Yuan, J. Mater. Chem. A, 2015, 3, 12038 CAS.
- Q. Hao, J. P. Wang and C. X. Xu, J. Mater. Chem. A, 2014, 2, 87 CAS.
- G. Huang, F. F. Zhang, L. L. Zhang, X. C. Du, J. W. Wang and L. M. Wang, J. Mater. Chem. A, 2014, 2, 8048 CAS.
- Y. Z. Wu, J. S. Meng, Q. Li, C. J. Niu, X. P. Wang, W. Yang, W. Li and L. Q. Mai, Nano Res., 2017, 10, 2364 CrossRef CAS.
- J. Shao, Z. M. Wan, H. M. Liu, H. Y. Zheng, T. Gao, M. Shen, Q. T. Qu and H. H. Zheng, J. Mater. Chem. A, 2014, 2, 12194 CAS.
- J. Shao, Z. M. Wan, H. M. Liu, H. Y. Zheng, T. Gao, M. Shen, Q. T. Qu and H. H. Zheng, J. Mater. Chem. A, 2014, 2, 12194 CAS.
- Y. Han, M. L. Zhao, L. Dong, J. M. Feng, Y. J. Wang, D. J. Li and X. F. Li, J. Mater. Chem. A, 2015, 3, 22542 CAS.
- Y. Y. Chen, Y. Wang, H. X. Yang, H. Gan, X. W. Cai, X. M. Guo, B. Xu, M. F. Lü and A. H. Yuan, Ceram. Int., 2017, 43, 9945 CrossRef CAS.
- W. W. Xu, X. D. Cui, Z. Q. Xie, G. Dietrich and Y. Wang, Electrochim. Acta, 2016, 222, 1021 CrossRef CAS.
- D. Ji, H. Zhou, Y. Tong, J. P. Wang, M. Z. Zhu, T. H. Chen and A. H. Yuan, Chem. Eng. J., 2017, 313, 1623 CrossRef CAS.
- O. Waser, M. Hess, A. Güntner, P. Novók and S. E. Pratsinis, J. Power Sources, 2013, 241, 415 CrossRef CAS.
- S. Y. Zhang, H. Liu, P. F. Liu, Z. H. Yang, X. Feng, F. W. Huo and X. H. Lu, Nanoscale, 2015, 7, 9411 RSC.
- J. J. Zhang and A. S. Yu, Sci. Bull., 2015, 60, 823 CrossRef CAS.
- R. B. Wu, X. K. Qian, F. Yu, H. Liu, K. Zhou, J. Wei and Y. Z. Huang, J. Mater. Chem. A, 2013, 1, 11126 CAS.
- L. Hu, Y. M. Huang, F. P. Zhang and Q. W. Chen, Nanoscale, 2013, 5, 4186 RSC.
- S. F. Kong, R. L. Dai, H. Li, W. W. Sun and Y. Wang, ACS Sustainable Chem. Eng., 2015, 3, 1830 CrossRef CAS.
- Y. Q. Zhu, H. Z. Guo, Y. Wu, C. B. Cao, S. Tao and Z. Y. Wu, J. Mater. Chem. A, 2014, 2, 7904 CAS.
- Z. C. Bai, Z. C. Ju, C. L. Guo, Y. T. Qian, B. Tang and S. L. Xiong, Nanoscale, 2014, 6, 3268 RSC.
- J. M. Xu, H. B. Tang, T. T. Xu, D. Wu, Z. F. Shi, Y. T. Tian and X. J. Li, Ionics, 2017, 23, 3273 CrossRef CAS.
- W. X. Guo, W. W. Sun and Y. Wang, ACS Nano, 2015, 9, 11462 CrossRef CAS PubMed.
- C. C. Sun, J. Yang, X. H. Rui, W. N. Zhang, Q. Y. Yan, P. Chen, F. W. Huo, W. Huang and X. C. Dong, J. Mater. Chem. A, 2015, 3, 8483 CAS.
- F. C. Zheng, S. H. Xu, Z. C. Yin, Y. G. Zhang and L. Lu, RSC Adv., 2016, 6, 93532 RSC.
- H. H. You, L. Zhang, Y. Z. Jiang, T. Y. Shao, M. Li and J. L. Gong, J. Mater. Chem. A, 2017, 6, 5265 Search PubMed.
- C. Guan, X. L. Li, H. Yu, L. Mao, L. H. Wong, Q. Y. Yan and J. Wang, Nanoscale, 2014, 6, 13824 RSC.
- H. Yu, C. Guan, X. H. Rui, B. Ouyang, B. L. Yadian, Y. Z. Huang, H. Zhang, H. E. Hoster, H. J. Fan and Q. Y. Yan, Nanoscale, 2014, 6, 10556 RSC.
- M. Fu, Q. Jiao, Y. Zhao and H. Li, J. Mater. Chem. A, 2014, 2, 735 CAS.
- X. W. Hu, S. Liu, B. T. Qu and X. Z. You, ACS Appl. Mater. Interfaces, 2015, 7, 9972 CAS.
- S. Li, A. Li, R. Zhang, Y. He, Y. Zhai and L. Xu, Nano Res., 2014, 7, 1116 CrossRef CAS.
- H. Yu, H. S. Fan, B. L. Yadian, H. T. Tan, W. L. Liu, H. H. Hng, Y. Z. Huang and Q. Y. Yan, ACS Appl. Mater. Interfaces, 2015, 7, 26751 CAS.
- H. Guo, T. T. Li, W. W. Chen, L. X. Liu, X. J. Yang, Y. P. Wang and Y. C. Guo, Nanoscale, 2014, 6, 15168 RSC.
- H. Guo, T. T. Li, W. W. Chen, L. X. Liu, J. L. Qiao and J. J. Zhang, Sci. Rep., 2015, 5, 13310 CrossRef PubMed.
- H. Yin, X. X. Yu, Q. W. Li, M. L. Cao, W. Zhang, H. Zhao and M. Q. Zhu, J. Alloys Compd., 2017, 706, 97 CrossRef CAS.
- B. d. Ramaraju, C. H. Li, S. Prakash and C. C. Chen, Chem. Commun., 2016, 52, 946 RSC.
- F. Zou, X. L Hu, Z. Li, L. Qie, C. C. Hu, R. Zeng, Y. Jiang and Y. H. Huang, Adv. Mater., 2014, 26, 6622 CrossRef CAS PubMed.
- Z. W. Zhao, T. Wen, K. Liang, Y. F. Jiang, X. Zhou, C. C. Shen and A. W. Xu, ACS Appl. Mater. Interfaces, 2017, 9, 3757 CAS.
- Z. X. Sun, F. X. Xin, C. Cao, C. C. Zhao, C. Shen and W. Q. Han, Nanoscale, 2015, 7, 20426 RSC.
- W. P. Kang, Y. Zhang, L. L. Fan, L. L. Zhang, F. N. Dai, R. M. Wang and D. F. Sun, ACS Appl. Mater. Interfaces, 2017, 9, 10602 CAS.
- F. Zou, Y. M. Chen, K. W. Liu, Z. T. Yu, W. F. Liang, S. Bhaway, M. Gao and Y. Zhu, ACS Nano, 2015, 10, 377 CrossRef PubMed.
- L. T. Yu, J. Liu, X. J. Xu, L. G. Zhang, R. Z. Hu, J. W. Liu, L. C. Yang and M. Zhu, ACS Appl. Mater. Interfaces, 2017, 9, 2516 CAS.
- W. J. Zhang and K. J. Huang, Inorg. Chem. Front., 2017, 4, 1602 RSC.
- X. Y. Yu, H. Hu, Y. W. Wang, H. Y. Chen and X. W. D. Lou, Angew. Chem., Int. Ed., 2015, 54, 7395 CrossRef CAS PubMed.
- L. F. Shen, L. Yu, H. B. Wu, X. Y. Yu, X. G. Zhang and X. W. D. Lou, Nat. Commun., 2015, 6, 6694 CrossRef CAS PubMed.
- X. H. Rui, H. T. Tan and Q. Y. Yan, Nanoscale, 2014, 6, 9889 RSC.
- X. Xu, W. Liu, Y. Kim and J. Cho, Nano Today, 2014, 9, 604 CrossRef CAS.
- J. Wang, J. L. Liu, D. L. Chao, J. X. Yan, J. Y. Lin and Z. X. Shen, Adv. Mater., 2014, 26, 7162 CrossRef CAS PubMed.
- L. Yu, J. F. Yang and X. W. D. Lou, Angew. Chem., Int. Ed., 2016, 55, 13422 CrossRef CAS PubMed.
- Y. L. Zhou, D. Yan, H. Y. Xu, J. K. Feng, X. L. Jiang, J. Yue, J. Yang and Y. T. Qian, Nano Energy, 2015, 12, 528 CrossRef CAS.
- S. J. Deng, Y. Zhong, Y. X. Zeng, Y. D. Wang, Z. J. Yao, F. Yang, S. W. Lin, X. L. Wang, X. H. Lu, X. H. Xia and J. P. Tu, Adv. Mater., 2017, 29, 1700748 CrossRef PubMed.
- J. T. Zhang, L. Yu and X. W. D. Lou, Nano Res., 2017, 10, 4298 CrossRef CAS.
- J. Liu, C. Wu, D. D. Xiao, P. Kopold, L. Gu, P. A. van Aken, J. Maier and Y. Yu, Small, 2016, 12, 2354 CrossRef CAS PubMed.
- A. Manthiram, Y. Z. Fu, S. H. Chung, C. X. Zu and Y. S. Su, Chem. Rev., 2014, 114, 11751 CrossRef CAS PubMed.
- Y. Yang, G. Zheng and Y. Cui, Chem. Soc. Rev., 2013, 42, 3018 RSC.
- A. Manthiram, S. H. Chung and C. X. Zu, Adv. Mater., 2015, 27, 1980 CrossRef CAS PubMed.
- Z. Liang, G. Zheng, W. Li, Z. W. Seh, H. Yao, K. Yan, D. Kong and Y. Cui, ACS Nano, 2014, 8, 5249 CrossRef CAS PubMed.
- L. Ma, K. E. Hendrickson, S. Wei and L. A. Archer, Nano Today, 2015, 10, 315 CrossRef CAS.
- H. Liao, H. Ding, B. Li, X. Ai and C. Wang, J. Mater. Chem. A, 2014, 2, 8854 CAS.
- J. W. Zhou, X. S. Yu, X. X. Fan, X. J. Wang, H. W. Li, Y. Y. Zhang, W. Li, J. Zheng, B. Wang and X. G. Li, J. Mater. Chem. A, 2015, 3, 8272 CAS.
- C. P. Yang, Y. X. Yin and Y. G. Guo, J. Phys. Chem. Lett., 2015, 6, 256 CrossRef CAS PubMed.
- Y. V. Mikhaylik and J. R. Akridge, J. Electrochem. Soc., 2004, 151(11), A1969 CrossRef CAS.
- T. Chen, L. B. Ma, B. R. Cheng, R. P. Chen, Y. Hu, G. Y. Zhu, Y. R. Wang, J. Liang, Z. X. Tie, J. Liu and Z. Jin, Nano Energy, 2017, 38, 239 CrossRef CAS.
- C. Yang, S. Xin, Y. Yin, H. Ye, J. Zhang and Y. Guo, Angew. Chem., Int. Ed., 2013, 52, 8363 CrossRef CAS PubMed.
- Y. Cui, A. Abouimrane, J. Lu, T. Bolin, Y. Ren, W. Weng, C. Sun, V. A. Maroni, S. M. Heald and K. Amine, J. Am. Chem. Soc., 2013, 135, 8047 CrossRef CAS PubMed.
- A. Abouimrane, D. Dambournet, K. W. Chapman, P. J. Chupas, W. Weng and K. Amine, J. Am. Chem. Soc., 2012, 134, 4505 CrossRef CAS PubMed.
- K. Han, Z. Liu, H. Q. Ye and F. Dai, J. Power Sources, 2014, 263, 85 CrossRef CAS.
- Z. Li, J. T. Zhang, B. Y. Guan and X. W. D. Lou, Angew. Chem., 2017, 129, 16219 CrossRef.
- T. Liu, C. L. Dai, M. Jia, D. Y. Liu, S. J. Bao, J. Jiang, M. W. Xu and C. M. Li, ACS Appl. Mater. Interfaces, 2016, 8, 16063 CAS.
- C. Zhang, X. Wang, Q. Liang, X. Liu, Q. Weng, J. Liu, Y. Yang, Z. Dai, K. Ding, Y. Bando, J. Tang and D. Golberg, Nano Lett., 2016, 16, 2054 CrossRef CAS PubMed.
- L. Wu, D. Buchholz, C. Vaalma, G. A. Giffin and S. Passerini, ChemElectroChem, 2016, 3, 292 CrossRef CAS.
- S. W. Zhang, W. Lv, C. Luo, C. H. You, J. Zhang, Z. Z. Pan, F. Y. Kang and Q. H. Yang, Energy Storage Maters, 2016, 3, 18 CrossRef.
- C. Nithya and S. Gopukumar, Wiley Interdiscip. Rev.: Energy Environ., 2015, 4, 253 CrossRef CAS.
- H. Hou, X. Qiu, W. Wei, Y. Zhang and X. Ji, Adv. Energy Mater., 2017, 7, 1602898 CrossRef.
- W. H. Li, S. H. Hu, X. Y. Luo, Z. L. Li, X. Z. Sun, M. S. Li and Y. Yu, Adv. Mater., 2017, 29, 1605820 CrossRef PubMed.
- H. S. Hou, C. E. Banks, M. J. Jing, Y. Zhang and X. B. Ji, Adv. Mater., 2015, 27, 7861 CrossRef CAS PubMed.
- S. L. Liu, J. Y. Huang, J. Liu, M. Lei, J. Min, S. T. Li and G. Liu, Mater. Lett., 2016, 172, 56 CrossRef CAS.
- Y. Liu, N. Zhang, L. Jiao and J. Chen, Adv. Mater., 2015, 27, 6702 CrossRef CAS PubMed.
- Y. Zhang, Y. C. Yang, H. S. Hou, X. M. Yang, J. Chen, M. J. Jing, X. N. Jia and X. B. Ji, J. Mater. Chem. A, 2015, 3, 18944 CAS.
- X. Wang, K. Cao, Y. Wang and L. Jiao, Small, 2017, 13, 170087 Search PubMed.
- Z. Zhang, J. Zhang, X. Zhao and F. Yang, Carbon, 2015, 95, 552 CrossRef CAS.
- Y. Zhang, C. W. Foster, C. E. Banks, L. D. Shao, H. S. Hou, G. Q. Zou, J. Chen, Z. D. Huang and X. B. Ji, Adv. Mater., 2016, 28, 9391 CrossRef CAS PubMed.
- H. Kang, K. H. Park and H. K. Lee, Bull. Korean Chem. Soc., 2016, 37, 123 CrossRef CAS.
- Y. Wang, Y. Lü, W. Zhan, Z. Xie, Q. Kuang and L. Zheng, J. Mater. Chem. A, 2015, 3, 12796 CAS.
- X. Zhang, W. Shi, J. Zhu, D. J. Kharistal, W. Zhao, B. S. Lalia, H. H. Hng and Q. Yan, ACS Nano, 2011, 5, 2013 CrossRef CAS PubMed.
- S. N. Guo, Y. Zhu, Y. Y. Yan, Y. L. Min, J. C. Fan, Q. J. Xu and H. Yun, J. Power Sources, 2016, 316, 176 CrossRef CAS.
- X. J. Zhang, W. Qin, D. S. Li, D. Yan, B. W. Hu, Z. Sun and L. K. Pan, Chem. Commun., 2015, 51, 16413 RSC.
- Y. Guo, Y. Y. Zhu, C. Yuan and C. Y. Wang, Mater. Lett., 2017, 199, 101 CrossRef CAS.
- L. L. Xing, K. J. Huang and L. X. Fang, Dalton Trans., 2016, 45, 17439 RSC.
- J. Xu, Y. Y. Li, L. Wang, Q. F. Cai, Q. W. Li, B. Gao, X. M. Zhang, K. F. Huo and P. K. Chu, Nanoscale, 2016, 8, 16761 RSC.
- W. P. Kang, Y. Zhang, L. L. Fan, L. L. Zhang, F. N. Dai, R. M. Wang and D. F. Sun, ACS Appl. Mater. Interfaces, 2017, 9, 10602 CAS.
- B. D. Ramaraju, C. H. Li, S. Prakash and C. C. Chen, Chem. Commun., 2016, 52, 946 RSC.
- H. N. Ma, J. He, D. B. Xiong, J. S. Wu, Q. Q. Li, V. David and Y. F. Zhao, ACS Appl. Mater. Interfaces, 2016, 8, 1992 CAS.
- K. J. Huang, J. Z. Zhang, G. W. Shi and Y. M. Liu, Mater. Lett., 2014, 131, 45 CrossRef CAS.
- Y. M. Chen, L. Yu and X. W. David Lou, Angew. Chem., Int. Ed., 2016, 55, 5990 CrossRef CAS PubMed.
- C. P. Li, Q. Hu, Y. Li, H. Zhou, Z. L. Lv, X. J. Yang, L. X. Liu and H. Guo, Sci. Rep., 2016, 6, 25556 CrossRef CAS PubMed.
- S. Komaba, T. Hasegawa, M. Dahbi and K. Kubot, Electrochem. Commun., 2015, 60, 172 CrossRef CAS.
- A. Eftekhari, Z. Jian and X. Ji, ACS Appl. Mater. Interfaces, 2016, 9, 4404 Search PubMed.
- P. X. Xiong, X. X. Zhao and Y. H. Xu, ChemSusChem, 2018, 11, 202 CrossRef CAS PubMed.
- H. Yi, H. W. Wang, Y. T. Jing, T. Q. Peng and X. F. Wang, J. Power Sources, 2015, 285, 281 CrossRef CAS.
- L. L. Xing, K. J. Huang, S. X. Cao and H. Pang, Chem. Eng. J., 2018, 332, 253 CrossRef CAS.
- P. Huang, C. Lethien, S. Pinaud, K. Brousse, R. Laloo, V. Turq, M. Respaud, A. Demortiere, B. Daffos, P. L. Taberna, B. Chaudret, Y. Gogotsi and P. Simon, Science, 2016, 351, 691 CrossRef CAS PubMed.
- L. F. Chen, Y. Lu, L. Yu and X. W. D. Lou, Energy Environ. Sci., 2017, 10, 1777 CAS.
- J. F. Chen, Y. L. Han, X. H. Kong, X. Z. Deng, H. J. Park, Y. L. Guo, S. Jin, Z. K. Qi, Z. Lee, Z. H. Qiao, R. S. Ruoff and H. X. Ji, Angew. Chem., Int. Ed., 2016, 55, 13822 CrossRef CAS PubMed.
- X. H. Xia, D. L Chao, Z. X. Fan, C. Guan, X. H. Cao, H. Zhang and H. J. Fan, Nano Lett., 2014, 14, 1651 CrossRef CAS PubMed.
- Y. D. Zhang, B. P. Lin, J. C. Wang, P. Han, T. Xu, Y. Sun, X. Q. Zhang and H. Yang, Electrochim. Acta, 2016, 191, 795 CrossRef CAS.
- C. Zhang, J. Xiao, X. L. Lv, L. H. Qian, S. L. Yuan, S. Wang and P. X. Lei, J. Mater. Chem. A, 2016, 4, 16516 CAS.
- A. Borenstein, O. Hanna, R. Attias, S. Luski, T. Brousse and D. Aurbach, J. Mater. Chem. A, 2017, 5, 12653 CAS.
- S. J. Peng, L. L. Li, H. B. Wu, S. Madhavi and X. W. Lou, Adv. Energy Mater., 2015, 5, 1401172 CrossRef.
- J. F. Chen, Y. L. Han, X. H. Kong, X. Z. Deng, H. J. Park, Y. L. Guo, S. Jin, Z. K. Qi, Z. Lee, Z. H. Qiao, R. S. Ruoff and H. X. Ji, Angew. Chem., Int. Ed., 2016, 55, 13822 CrossRef CAS PubMed.
- Y. Cao, B. P. Lin, Y. Sun, H. Yang and X. Q. Zhang, Electrochim. Acta, 2015, 174, 41 CrossRef CAS.
- M. Y. Tong, S. W. Liu, X. Zhang, T. X. Wu, H. M. Zhang, G. Z. Wang, Y. X. Zhang, X. G. Zhua and H. J. Zhao, J. Mater. Chem. A, 2017, 5, 9873 CAS.
- Y. Jiao, J. Pei, C. S. Yan, D. H. Chen, Y. Y. Hu and G. Chen, J. Mater. Chem. A, 2016, 4, 13344 CAS.
- C. Yuan, H. B. Wu, Y. Xie and X. W. D. Lou, Angew. Chem., Int. Ed., 2014, 53, 1488 CrossRef CAS PubMed.
- J. L. Yang, F. X. Wei, Y. W. Sui, J. Q. Qi, Y. Z. He, Q. K. Meng and S. Zhang, RSC Adv., 2016, 6, 61803 RSC.
- Z. H. Liu, L. Zhang, G. C. Xu, L. Zhang, D. Z. Jia and C. Y. Zhang, RSC Adv., 2017, 7, 11129 RSC.
- Y. D. Zhang, B. P. Lin, Y. Sun, P. Han, J. C. Wang, X. J. Ding, X. Q. Zhang and H. Yang, Electrochim. Acta, 2016, 188, 490 CrossRef CAS.
- A. Jayakumar, R. P. Antony, R. H. Wang and J. M. Lee, Small, 2017, 13, 1603102 CrossRef PubMed.
- G. C. Li, P. F. Liu, R. Liu, M. M. Liu, K. Tao, S. R. Zhu, M. K. Wu, F. Y. Yia and L. Han, Dalton Trans., 2016, 45, 13311 RSC.
- Y. Z. Zhang, Y. Wang, Y. L. Xie, T. Cheng, W. Y. Lai, H. Pang and W. Huang, Nanoscale, 2014, 6, 14354 RSC.
- X. W. Hu, S. Liu, B. T. Qu and X. Z. You, ACS Appl. Mater. Interfaces, 2015, 7, 9972 CAS.
- C. Guan, X. M. Liu, W. N. Ren, X. Li, C. W. Cheng and J. Wang, Adv. Energy Mater., 2017, 1602391 CrossRef.
- Z. J. Lv, Q. Zhong and Y. F. Bu, Electrochim. Acta, 2016, 215, 500 CrossRef CAS.
- P. Y. Wang, Y. N. Li, S. D. Li, X. Q. Liao and S. M. Sun, J. Electron. Mater., 2017, 28, 9221 CrossRef CAS.
- X. H. Rui, H. T. Tan and Q. Y. Yan, Nanoscale, 2014, 6, 9889 RSC.
- X. Geng, W. Sun, W. Wu, B. Chen, A. Al-Hilo, M. Benamara, H. Zhu, F. Watanabe, J. Cui and T. P. Chen, Nat. Commun., 2016, 7, 10672 CrossRef CAS PubMed.
- T. Wang, P. Hu, C. Zhang, H. Du, Z. Zhang, X. Wang, S. Chen, J. Xiong and G. Cui, ACS Appl. Mater. Interfaces, 2016, 8, 7811 CAS.
- W. Yang, H. Wang, T. Liu and L. Gao, Mater. Lett., 2016, 167, 102 CrossRef CAS.
- Y. Zhao and A. Manthiram, Chem. Commun., 2015, 51, 13205 RSC.
- W. J. Li, C. Han, S. L. Chou, J. Z. Wang, Z. Li, Y. M. Kang, H. K. Liu and S. X. Dou, Chem.–Eur. J., 2016, 22, 590 CrossRef CAS PubMed.
- W. Sun, X. Rui, D. Zhang, Y. Jiang, Z. Sun, H. Liu and S. Dou, J. Power Sources, 2016, 309, 135 CrossRef CAS.
- W. Yang, H. Wang, T. Liu and L. Gao, Mater. Lett., 2016, 167, 102 CrossRef CAS.
- Y. Zhu, P. Nie, L. Shen, S. Dong, Q. Sheng, H. Li, H. Luo and X. Zhang, Nanoscale, 2015, 7, 3309 RSC.
- J. H. Choi, C. W. Ha, H. Y. Choi, H. C. Shin, C. M. Park, Y. N. Jo and S. M. Lee, Electrochim. Acta, 2016, 210, 588 CrossRef CAS.
- H. N. Ma, J. He, D. B. Xiong, J. S. Wu, Q. Q. Li, V. David and Y. F. Zhao, ACS Appl. Mater. Interfaces, 2016, 8, 1992 CAS.
- Y. F. Tang, S. J. Chen, S. C. Mu, T. Chen, Y. Q. Qiao, S. X. Yu and F. M. Gao, ACS Appl. Mater. Interfaces, 2016, 8, 9721 CAS.
- Z. F. Huang, J. J. Song, K. Li, M. Tahir, Y. T. Wang, L. Pan, L. Wang, X. W. Zhang and J. J. Zou, J. Am. Chem. Soc., 2016, 138, 1359 CrossRef CAS PubMed.
- P. L. He, X. Y. Yu and X. W. D. Lou, Angew. Chem., 2017, 129, 3955 CrossRef.
- X. Ma, L. Zhang, G. C. Xu, C. Y. Zhang, H. J. Song, Y. T. He, C. Zhang and D. Z. Jia, Chem. Eng. J., 2017, 320, 22 CrossRef CAS.
- Z. Jiang, W. J. Lu, Z. P. Li, K. H. Ho, X. Li, X. L. Jiao and D. Chen, J. Mater. Chem. A, 2014, 2, 8603 CAS.
- G. C. Li, M. M. Liu, M. K. Wu, P. F. Liu, Z. W. Zhou, S. R. Zhu, R. Liu and L. Han, RSC Adv., 2016, 6, 103517 RSC.
- Y. Q. Chen, B. P. Lin, X. Q. Zhang, J. C. Wang, C. W. Lai, Y. Sun, Y. R. Liu and H. Yang, J. Mater. Chem. A, 2014, 2, 14118 CAS.
- M. Klose, R. Reinhold, K. Pinkert, M. Uhlemann, F. Wolke, J. Balach, T. Jaumann, U. Stoeck and J. E. L. Giebeler, Carbon, 2016, 106, 306 CrossRef CAS.
- R. R. Salunkhe, Y. Kamachi, N. L. Torad, S. M. Hwang, Z. Q. Sun, S. X. Dou, J. H. Kimc and Y. Yamauchi, J. Mater. Chem. A, 2014, 2, 19848 CAS.
- Y. D. Zhang, B. P. Lin, J. C. Wang, J. H. Tian, Y. Sun, X. Q. Zhang and H. Yang, J. Mater. Chem. A, 2016, 4, 10282 CAS.
- P. Zhang, F. Sun, Z. G. Shen and D. P. Cao, J. Mater. Chem. A, 2014, 2, 12873 CAS.
- L. J. Xin, R. R. Chen, Q. Liu, J. Y. Liu, Z. S. Li, R. M. Lia and J. Wang, New J. Chem., 2017, 41, 12835 RSC.
- Q. L. Zhu, P. Pachfule, P. Strubel, Z. P. Li, R. Q. Zou, Z. Liu, S. Kaskel and Q. Xu, Energy Storage Maters, 2018, 13, 72 CrossRef.
|
This journal is © The Royal Society of Chemistry 2018 |
Click here to see how this site uses Cookies. View our privacy policy here.