Inexpensive, operationally simple flow reactor for rapid, chromatography free synthesis of siloxane based liquid crystals†
Received
20th February 2018
, Accepted 30th April 2018
First published on 30th May 2018
Abstract
We report on the hydrosilylation of terminal alkenes in flow using a “Karstedt-like” platinum-on-silica catalyst. A solution of alkene and siloxane in toluene was passed through the catalyst bed using a low pressure pump; the use of a high catalyst loading delivers quantitative β-addition of the siloxane to the alkene, hence the only purification required is removal of volatiles (toluene and siloxane). Following optimisation we synthesise a family of liquid crystalline siloxane terminated cyanobiphenyls, finding their properties to compare favourably to literature examples. The system and catalyst described is inexpensive, reusable, and chromatography free and thus prominently sustainable.
Introduction
The two most common ways of forming carbon–silicon bonds are the reaction of a nucleophile with a silyl halide, or the addition of a silyl hydride across an olefin using transition metal catalysis (typically platinum, e.g. Karstedt's catalyst).1–4 The incorporation of siloxanes into liquid crystals is often performed as a means to attain lower melting points,5 suppress nematic liquid crystal phase formation6 as well as to control smectic mesophase layer spacing7 and induce De Vries behaviour.8–12 One of the difficulties in preparing liquid-crystalline siloxanes is the need for chromatographic separation of unreacted olefin and silyl hydride from the desired product;13 the similar retention factors of the product and starting material make this time consuming. Siloxane/silane terminated materials are often not solid at room temperature, complicating recrystalisation. Given that the liquid-crystalline state is extremely sensitive to chemical purity,14 careful chromatographic purification of these materials is therefore often unavoidable. In addition to their cost and inherent lack of reusability, homogenous catalysts such as Karstedt's catalyst may also contaminate the resulting material with platinum colloids which, in addition to having catalytic activity of their own,15 can be difficult to remove and may affect properties of the resulting materials. The addition of a silyl hydride across an olefin is exothermic;16 with increased reaction temperature there is the possibility for increased formation of the (usually undesired) Markovnikov addition product. Lastly, the low catalyst loading used for hydrosilylation necessitates that even trace quantities of catalytic poisons – sulphurous in the case of platinum catalysts – are excluded. Flow chemistry techniques are increasingly being adopted in the synthesis of complex molecules,17–21 however the potential use of these techniques has not yet been applied to the synthesis of liquid crystalline media.22 In this article an inexpensive (cost of hardware ≈ $400) flow reactor utilising a platinum(0) catalyst on silica gel (cost ≈ $3 per g) is described for the hydrosilylation of terminal olefins. Following removal of volatiles (solvent and silyl hydride, both can be recovered if required) the desired products were obtained in high yield (>95%) and high purity (>99%) without chromatography or recrystalisation.
Experimental
Toluene was washed with >95% sulphuric acid to remove trace thiophene before distilling over CaH. The synthesis of the alkene-terminated cyanobiphenyls is described in a previous publication,23 use of high purity alkenes (>99.5% by HPLC assay) is essential as this dictates the purity of the target siloxanes. pentamethyldisiloxane was purchased from Fluorochem and purified by short path distillation. Triethoxysilane and silica gel were purchased from Sigma Aldrich, hexachloroplatinic acid hydrate was purchased from Alfa Aesar. The synthesis of Pt@SiO2 was performed as reported by Miao et al. on a scale of 20 g.24
The flow reactor (Fig. 1) was constructed from an Omnifit glass column (L × I.D. 150 × 10 mm, volume 9.5 ml, mfr. no. 6112) with an adjustable endpiece (mfr. no. 6165, allowing the volume of the packed bed to be varied) and PTFE frits (mfr. no. 6146). The column was loaded with 2.8 g of Pt@SiO2 which was packed by sonication. Fluorinated ethylene propylene (FEP) tubing was purchased from Saint Gobain Performance Plastics. The catalyst Pt@SiO2 is ≈1.9 wt% Pt; 2.8 g therefore corresponds to ≈0.24 mmol of Pt. The column was assembled and flushed with 10 ml of low sulphur toluene at 0.5 ml min−1 before use. Liquids were delivered via a syringe pump at the indicated flow rates. Instrumental details are given in the ESI† to this article.
 |
| Fig. 1 (A) Scheme 1, showing the synthesis of the catalyst Pt@SiO2 used in this work. (Bz) Top, diagram of the flow reactor. Bottom, photograph of the assembled reactor: the flow direction is from left to right through 0.89 mm I.D. fluorinated ethylene propylene (FEP) tubing, the Omnifit column (and therefore catalyst bed) is cylindrical, having a radius of 5 mm, a length of ≈50 mm and therefore a volume of ≈4 cm3. | |
Results and discussion
We chose the hydrosilylation of 4-(pent-4-eneyloxy)-4′-cyanobiphenyl with pentamethyldisiloxane (to give 2Si5OCB, Scheme 1 and Table 1) as the reaction to optimise the flow hydrosilylation. Our aim was to obtain quantitative conversion of the alkene to the β-addition product with the maximum possible throughput (i.e. flow rate) as shown in Table 1. A stock solution of alkene (20 mmol) and siloxane (22 mmol, 1.1 mol eq.) in toluene (100 ml) was prepared and 10 ml used for each reaction. The reactor output was collected and volatiles (toluene + siloxane) removed in vacuo at 60 °C and <5 mBar – no further purification was performed – to give both spectroscopically (1H, 13C{1H}, 13C{1H} DEPT135 and 29Si{1H}) and chromatographically (HPLC) homogenous material in effectively a quantitative yield. Following the completion of a given substrate the reactor bed was washed with ethyl acetate (∼10 ml, 0.5 ml min−1) to remove traces of starting materials and avoid contaminating subsequent runs. We did not observe any darkening of the reaction product nor did we observe a drop in conversion with successive runs, either of which would indicate leeching of platinum. However, as we are working at complete conversion conditions we must note that any decrease in catalyst activity with subsequent runs could be masked. As a control, 2 ml of the stock solution was concentrated in vacuo and studied by NMR (1H/13C{1H}/29Si{1H}) which confirmed no conversion takes place in the absence of a catalyst.
 |
| Scheme 1 | |
Table 1 Conversion – determined by 1H NMR – as a function of flow rate when using a 0.2 M solution of 4-allyloxy-4′-cyanobiphenyl (2 mmol) and pentamethyldisiloxane (1.1 mol eq.) in low sulphur toluene (10 ml). Conversions were determined by 1H NMR integration of the alkene peaks; where no alkene peaks remained conversion is given at >99%
Flow rate (ml min−1) |
Conversion (1H NMR) |
Assay (HPLC) |
0.1 |
>99% |
>99.5 |
0.2 |
>99% |
>99.5 |
0.3 |
>99% |
>99.5 |
0.4 |
>99% |
>99.5 |
0.5 |
>99% |
>99.5 |
0.6 |
<94% |
— |
We observed at flow rates of 0.6 ml min−1 we found 6% residual alkene in the product by 1H NMR integration; while this would be possible to separate via chromatography or crystallisation we considered a purification free synthetic transformation to be more desirable than higher throughput. Decreasing the flow rate increases the residence time of the reaction solution in the catalyst bed and lead to quantitative conversion at 0.5 ml min−1 and lower, as judged by 1H NMR and HPLC. The high conversion is probably due to the high catalyst loading; the reactor bed (4 ml volume) contains approximately 0.24 mmol of platinum, whereas the same volume of reaction solution contains 0.8 mmol of alkene; this equates to a catalyst loading of 30 mol% which is over two orders of magnitude above a typical catalyst loading used by us for homogenous hydrosilylation with Karstedt's catalyst.7 The ratio of α
:
β products was studied by 13C{1H} DEPT135 NMR (see Fig. 2); the secondary CH3–
H2–(Si…)–CH2– present in the undesired alpha product will give a resonance in positive phase, whereas the desired beta product will have negative phase due to the primary –
H2–Si. We observe only a negative phase resonance for the carbon adjacent to the siloxane (including 13C–19Si satellites), indicating quantitative formation of the β-addition product. The NMR resonance of the secondary CH3–
H2–(Si…)–CH2– would also be expected to be upfield of the resonance corresponding to the primary –
H2–(Si…). We subjected samples of 2Si5OCB prepared at differing flow rates to study by HPLC to assay purity; we used a gradient solvent (100% hexane to 100% DCM over 30 minutes) with a normal phase silica column. The material obtained at 0.6 ml min−1 was known to contain residual alkene as evidenced by 1H NMR and so HPLC assay was not performed; the remaining five samples all gave a single peak by HPLC assay which indicates a purity of above 99.5%.
 |
| Fig. 2
13C{1H} DEPT135 NMR spectra (100.5 MHz) of 2Si5OCB synthesised at a flow rate of 0.5 ml min−1, with an expansion showing the main resonance (and satellites from 13C–29Si coupling) for the CH2 adjacent to the siloxane. | |
With a catalyst bed volume of ∼4 cm3 and a concentration of 0.2 M, a flow rate of 0.5 ml min−1 is optimal and this gives a theoretical maximum throughput of 6 mmol an hour, e.g. 2.5 g of 2Si5OCB. A larger catalyst bed volume should allow higher conversion at a given flow rate; however the limited backpressures available through a syringe pump restricts us to the present catalyst bed volume (≈4 cm3). High pressure pumps and back pressure regulation would allow larger catalyst beds (therefore higher throughput) at the cost of increased cost and system complexity, negating the simple and inexpensive setup described.
With an optimum flow rate identified we undertook the hydrosilylation of the ω-alkeneyloxy-4′-cyanobiphenyl series of materials with pentamethyldisiloxane (Scheme 2). We combined the alkene (2 mmol) with pentamethyldisiloxane (1.1 mmol) and low sulphur toluene (10 ml) in a 14 ml vial, sonicating until a homogenous solution was obtained (typically <2 min). This solution was passed through the Pt@SiO2 reactor bed at 0.5 ml min−1, followed by 10 ml of ethyl acetate at 0.5 ml min−1. The toluene and excess pentamethyldisiloxane were removed in vacuo (70 °C < 5 mBar) to give the 2SinOCB materials, which were analysed without further purification. Purities were determined by HPLC and are given along with transition temperatures (°C, from the average of two DSC cycles) for the 2SinOCB materials in Table 2.
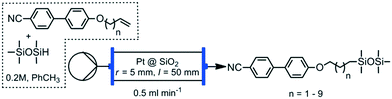 |
| Scheme 2 | |
Table 2 Transition temperatures (°C) were determined via DSC at a heat/cool rate of 10 °C min−1 and are the average of two runs. Phase identification was made by microscopy and assisted by SAXS studies. 2Si10OCB (n = 8) exhibits a crystal-to-crystal transition at 43.0 °C with an associated enthalpy of 0.38 kJ mol−1. Purity was assayed by HPLC as described in the text, retention times are given in the ESI
No. |
n = |
Transition temperatures |
Assay (HPLC) |
MP |
T
g
|
SmAd-Iso |
2Si3OCB |
1 |
74.2 |
−29.4 |
33.6 |
>99.5% |
2Si4OCB |
2 |
39.7 |
−30.6 |
29.1 |
99.3% |
2Si5OCB |
3 |
33.1 |
−30.8 |
52.4 |
>99.5% |
2Si6OCB |
4 |
39.6 |
−31.0 |
53.8 |
>99.5% |
2Si7OCB |
5 |
24.3 |
— |
63.2 |
>99.5% |
2Si8OCB |
6 |
42.3 |
— |
64.2 |
>99.5% |
2Si9OCB |
7 |
28.1 |
— |
71.2 |
> 99.5% |
2Si10OCB |
8 |
38.2 |
— |
70.9 |
> 99.5% |
2Si11OCB |
9 |
33.9 |
— |
74.4 |
> 99.5% |
For each material the yield was quantitative (>95%), confirming that the desired product is not retained by the catalyst bed. In the all cases we observe only one peak in HPLC analysis, indicating a purity of >99.5%, with the exception of 2Si4OCB which was obtained in only 99.3% purity. Most of the compounds presented in Table 2 have been reported previously, and we note that the transition temperatures (in particular melting points) reported by us are identical to or higher than previously reported examples.5,6,25 This is further evidence for the high purity of our materials and the advantage conferred by in-flow versus homogenous hydrosilylation. We note that if higher purity was desired the materials could still be subjected to distillation, crystallisation or chromatographic purification techniques. We used small angle X-ray scattering to measure the layer spacing in the smectic A phase of 2Si11OCB. We observe the smectic layer spacing of 2Si11OCB to be temperature dependent and to reach a maximum value of 49.5 Å in both samples, corresponding to a maximum d/l ratio of 1.74 when using the molecular length of 28.3 obtained from DFT(B3LYP/6-31G(d)) calculations. The smectic phase exhibited by 2Si11OCB is probably best described as being an interdigitated smectic A phase (SmAd), however the maximum value of the layer spacing is only fractionally smaller than that of a bilayer smectic phase (SmA2, d/l ≈ 1.8–2.0 (ref. 26)). The layer spacing (and therefore d/l ratio) of 2Si11OC increased approximately linearly with decreasing temperature as shown in Fig. 3. Comparison with an identical sample prepared in a batch reaction demonstrates the two materials have essentially identical behaviour.
 |
| Fig. 3 Plot of the smectic A layer spacing (d) of expressed as a d/l ratio (l = 28.3 Å) as a function of reduced temperature (TSmA-Iso/T, arb.) for 2Si11OCB prepared in batch (blue circles) and in flow (red squares). | |
As a demonstration we prepared a single pixel smectic A scattering device from a portion of 9 prepared in flow. The neat material was first doped with 0.05 wt% hexadecyltrimethylammonium perchlorate. The doped mixture of 9 was filled into a standard 5 μm thick cell with ITO electrodes over a surface area of 10 × 10 mm. A transparent state was induced by application of a high voltage, low frequency (200 VRMS, 1 Hz) electric field (Fig. 4a); this could be transformed into a scattering state with a high voltage, high frequency (200 VRMS, 1 kHz) electric field (Fig. 4b). Although the device is clearly suboptimal (low contrast due to thickness for example) the ability to rapidly synthesise materials could enable higher throughput screening of materials for use in display devices, to provide one example of this technology.
 |
| Fig. 4 A single pixel ion doped SmA scattering device prepared from a sample of 9 prepared in flow. The active area scatters light in its ‘on’ state (b) and is transparent in its off state (a). | |
Conclusions
Siloxanes in liquid-crystals are a popular terminal group to confer lower melting points and alter bulk material properties, however batch hydrosilylation reactions can give variable yields, poor selectivity and require extensive chromatography to afford pure materials. We demonstrate an inexpensive and operationally simple flow reactor for the hydrosilylation of terminal alkenes, and apply this to the synthesis of a family of liquid-crystalline materials. The reaction affords only the desired beta-addition product (1H/13C{1H}/DEPT135/29Si{1H} NMR) and complete conversion of the alkene to the siloxane was achieved with a throughput of 6 mmol h−1; increased throughput may be possible with modifications (higher pressure, larger catalyst bed and backpressure regulation), however this quantity is sufficient for the synthesis and evaluation of LC materials. The target siloxanes were obtained in sufficiently high purity (>99.5% by HPLC) that column chromatography was not required for any materials prepared in this work, although we note that the materials could be purified further if desired, with the only ‘purification’ being removal of volatiles. We prepared a family of liquid-crystalline siloxanes and compared their behaviour to previous reports, where available. The transition temperatures and smectic layer spacings we observe are generally superior to literature values. Lastly we construct a single pixel prototype ion doped SmA display device, demonstrating the application potential of flow derived LC materials. This technique has been shown to be useful in producing high purity materials for LCD technologies, and it is possible that it might have other applications to dendrimers,27 oligomers,28 polymers etc.
Conflicts of interest
There are no conflicts to declare.
Acknowledgements
The authors thank the EPSRC for funding the Bruker D8 SAXS equipment via grant EP/K039660/1 and ongoing work on smectic A materials via EP/M020584/1. We thank Frank Simpson of the University of York for preparing a bulk quantity of the alkene used to prepare 2Si5OCB. Raw data pertinent to this work are available upon request from the University of York data catalogue.
Notes and references
- J. Stein, L. N. Lewis, Y. Gao and R. A. Scott, J. Am. Chem. Soc., 1999, 121, 3693–3703 CrossRef.
- Y. Nakajima and S. Shimada, RSC Adv., 2015, 5, 20603–20616 RSC.
- T. K. Meister, K. Riener, P. Gigler, J. Stohrer, W. A. Herrmann and F. E. Kuhn, ACS Catal., 2016, 6, 1274–1284 CrossRef.
- D. Troegel and J. Stohrer, Coord. Chem. Rev., 2011, 255, 1440–1459 CrossRef.
- D. J. Gardiner and H. J. Coles, J. Phys. D: Appl. Phys., 2006, 39, 4948–4955 CrossRef.
- D. J. Gardiner and H. J. Coles, J. Appl. Phys., 2006, 100, 124903 CrossRef.
- R. J. Mandle, E. J. Davis, C. C. A. Voll, D. J. Lewis, S. J. Cowling and J. W. Goodby, J. Mater. Chem. C, 2015, 3, 2380–2388 RSC.
- J. C. Roberts, N. Kapernaum, F. Giesselmann and R. P. Lemieux, J. Am. Chem. Soc., 2008, 130, 13842–13843 CrossRef PubMed.
- G. Galli, M. Reihmann, A. Crudeli, E. Chiellini, Y. Panarin, J. Vij, C. Blanc, V. Lorman and N. Olsson, Mol. Cryst. Liq. Cryst., 2005, 439, 2111–2123 Search PubMed.
- L. Li, C. D. Jones, J. Magolan and R. P. Lemieux, J. Mater. Chem., 2007, 17, 2313–2318 RSC.
- F. Goc, C. Blanc, V. Lorman, M. Nobili, S. Samaritani, G. Galli and W. Kuczynski, Ferroelectrics, 2006, 343, 101–110 CrossRef.
- Q. X. Song, D. Nonnenmacher, F. Giesselmann and R. P. Lemieux, J. Mater. Chem. C, 2013, 1, 343–350 RSC.
- G. Nestor, M. S. White, G. W. Gray, D. Lacey and K. J. Toyne, Makromol. Chem., 1987, 188, 2759–2767 CrossRef.
- N. Vaupotic and M. Cepic, Phys. Rev. E: Stat., Nonlinear, Soft Matter Phys., 2005, 71, 041701 CrossRef PubMed.
- L. N. Lewis and N. Lewis, J. Am. Chem. Soc., 1986, 108, 7228–7231 CrossRef.
-
B. Marciniec, in Hydrosilylation: A Comprehensive Review on Recent Advances, ed. B. Marciniec, Springer Netherlands, Dordrecht, 2009, pp. 3–51, DOI:10.1007/978-1-4020-8172-9_1.
- B. J. Reizman and K. F. Jensen, Acc. Chem. Res., 2016, 49, 1786–1796 CrossRef PubMed.
- A. Adamo, R. L. Beingessner, M. Behnam, J. Chen, T. F. Jamison, K. F. Jensen, J. C. M. Monbaliu, A. S. Myerson, E. M. Revalor, D. R. Snead, T. Stelzer, N. Weeranoppanant, S. Y. Wong and P. Zhang, Science, 2016, 352, 61–67 CrossRef PubMed.
- H. P. L. Gemoets, Y. H. Su, M. J. Shang, V. Hessel, R. Luque and T. Noel, Chem. Soc. Rev., 2016, 45, 83–117 RSC.
- I. M. Mandity, S. B. Otvos and F. Fulop, ChemistryOpen, 2015, 4, 212–223 CrossRef PubMed.
- I. M. Mandity, S. B. Otvos, G. Szolosi and F. Fulop, Chem. Rec., 2016, 16, 1018–1033 CrossRef PubMed.
- J. Y. Li, C. B. Niu, J. J. Peng, Y. Deng, G. D. Zhang, Y. Bai, C. Ma, W. J. Xiao and G. Q. Lai, Appl. Organomet. Chem., 2014, 28, 454–460 CrossRef.
- R. J. Mandle and J. W. Goodby, Liq. Cryst., 2017, 44, 656–665 CrossRef.
- Q. J. Miao, Z. P. Fang and G. P. Cai, Catal. Commun., 2003, 4, 637–639 CrossRef.
- J. Newton, H. Coles, P. Hodge and J. Hannington, J. Mater. Chem., 1994, 4, 869–874 RSC.
- R. Shashidhar, K. A. Suresh, B. R. Ratna, S. K. Prasad, C. Bahr, A. Oestreicher and G. Heppke, Mol. Cryst. Liq. Cryst., Lett. Sect., 1985, 1, 89–93 Search PubMed.
- I. M. Saez, J. W. Goodby and R. M. Richardson, Chem. – Eur. J., 2001, 7, 2758–2764 CrossRef.
- A. Al-Janabi, R. J. Mandle and J. W. Goodby, RSC Adv., 2017, 7, 47235–47242 RSC.
Footnote |
† Electronic supplementary information (ESI) available. See DOI: 10.1039/c8re00027a |
|
This journal is © The Royal Society of Chemistry 2018 |
Click here to see how this site uses Cookies. View our privacy policy here.