DOI:
10.1039/C8RA05480K
(Paper)
RSC Adv., 2018,
8, 26251-26254
Zr–Cu alloy filler metal for brazing SiC ceramic
Received
26th June 2018
, Accepted 12th July 2018
First published on 23rd July 2018
Abstract
The Zr–Cu filler metal is mainly used for the joining of SiC ceramic as a nuclear fuel cladding material. The physical and chemical properties of the alloy, the interfacial reaction between the Zr–Cu filler metal and SiC ceramic, the residual stress of the SiC joint and the thermal neutron absorption cross section of the filler metal are considered during the design of the Zr–Cu filler metal. 80Zr–20Cu (wt%) is used as the filler metal in these experiments, showing good wettability and brazing properties with SiC ceramic.
1 Introduction
SiC ceramic has excellent mechanical properties, high temperature oxidation resistance, small thermal expansion coefficient and thermal stability.1–3 As a nuclear fuel cladding material, SiC ceramic has sufficient strength, tightness and corrosion resistance, and can prevent the overflow of fission products effectively.4,5 At the same time, the SiC ceramic material can reduce the risk of hydrogen production by thousands of times, and provide protection similar to zirconium alloys for nuclear fuel.5,6 However, SiC ceramic has characteristics of poor toughness and machinability due to the strong covalent bonding; it is very difficult to prepare large and complex parts with SiC ceramic materials. So joining technology is the key to expand the application of SiC ceramic materials.7–9 The active brazing10 is the most effective method to joining SiC ceramic because of low cost and mass production. The composition and properties of the filler metal have an important influence on the brazing joint. There are several brazing filler metals used for SiC brazing, such as Ag-based,11,12 Cu-based,11–13 Ti-based,11,12,14 Ni-based14,15 and Co-based filler metals.15 Among of them, brazed joints of the Ag-based and Cu-based filler metals have poor properties at high temperature, Ti-based, Ni-based and Co-based filler metals with high thermal neutron absorption cross sections cause nuclear fuel waste and other undesirable effects.16 Therefore, it is necessary to develop a new filler metal for brazing of SiC ceramic as nuclear fuel cladding material in order to obtain excellent joints with high temperature performance and low neutron absorption. In this paper, the design and brazing of a new type of Zr–Cu alloy filler metal are mainly investigated.
2 Design of Zr–Cu alloy filler metal
A new filler metal is designed for active brazing of SiC ceramic as nuclear fuel cladding material. In view of the contribution of Zr alloy as a cladding material for nuclear fuel, Zr-based filler metal is investigated. Zr element is a high-melting (1852 °C), which needs to be added to the alloy with low-melting, while the filler metal has good high-temperature properties and the melting temperature in the range of 950–1200 °C. Therefore, the Cu element is selected as the melting element. At the same time, the intermetallic alloys and compounds of the filler metal should be avoided as much as possible according to the phase diagram of Zr–Cu alloy, so Zr–Cu filler metal is put forward creatively. Moreover, the following factors should be taken into consideration in the design of Zr–Cu alloy filler metal:
(1) Interfacial reaction between SiC ceramic and Zr–Cu filler metal. The Cu element of the filler metal hardly reacts with SiC ceramics. However, Zr element, as an active element, has a complex chemical reaction with the interface of SiC ceramic during brazing. Interfacial reaction products have an important influence on the properties of the SiC joint. The possible interfacial reactions between active elements Zr and SiC ceramic are shown in Fig. 1. From thermodynamic analysis, the reaction of this chemical reaction (9): SiC + 3Zr = ZrC + Zr2Si has the lowest Gibbs free energy, and the ΔG are from −328.5 kJ mol−1 to −325.6 kJ mol−1 in the temperature range of 1100–1300 °C.17 Therefore, it is deduced that the products of interfacial reaction are mainly ZrC and Zr2Si. In addition, reaction products of the ZrC and Zr2Si are also often used as nuclear fuel element materials, and have good nuclear performance and nuclear compatibility.18,19 For this reason, the performance of SiC joint can be effectively improved by forming a certain thickness of the interface reaction layer by chemical metallurgy.
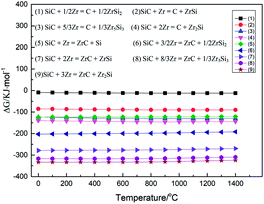 |
| Fig. 1 ΔG of interfacial reactions between active element Zr and SiC at different temperature. | |
(2) Residual stress of SiC ceramic joint. The residual stress of SiC ceramic brazed joints is inevitable, mainly due to the large difference of thermal expansion coefficient between filler metal and SiC ceramic. Therefore, the thermal expansion coefficient of raw materials is chosen as close as possible to SiC ceramic material. Thermal expansion coefficients of SiC ceramic and some materials are listed in Table 1. The thermal expansion coefficient of Zr is 6.9 × 10−6 K−1. Among the active elements, the thermal expansion coefficient of the Zr element is the closest to that of the SiC ceramic. Of course, the thermal expansion coefficient of Cu is larger, so the Cu content is reduced as much as possible so that the thermal expansion coefficient of filler metal is close to that of SiC ceramic. At the same time, the thermal expansion coefficients of the reaction products ZrC and Zr2Si are also close to that of SiC ceramic.
Table 1 Thermal expansion coefficients of SiC ceramic and some materials
Materials |
Coefficient of thermal expansion (×10−6 K−1) |
Materials |
Coefficient of thermal expansion (×10−6 K−1) |
SiC |
4.8 (20–500 °C) |
Cu |
17.2 (0–200 °C) |
Zr |
6.9 (20–600 °C) |
Mo |
5.7 (20–600 °C) |
Nb |
7.2 (18–900 °C) |
Ni |
11.0 (20–600 °C) |
Ti |
9.7 (20–600 °C) |
ZrC |
6.6 (20–600 °C) |
Si |
2.5 (20–600 °C) |
Zr2Si |
7.0 (20–600 °C) |
(3) Thermal neutron absorption cross section. Brazing joint of SiC ceramic is a part of nuclear fuel cladding material, so filler metal should take into account the thermal neutron absorption cross section of the selecting element. Low thermal neutron absorption area will increase the utilization of nuclear fuel. Thermal neutron absorption cross section of zirconium and some materials are listed in Table 2.16 From the table, it can be seen that the absorption cross section of Zr element is 0.18 × 10−28 m2. At the same time, the thermal neutron absorption cross section of the Cu element is 3.59 × 10−28m2, so Zr–Cu alloy filler metal has smaller thermal neutron absorption cross section.
Table 2 Thermal neutron absorption cross sections of zirconium and some materials
Materials |
Thermal neutron absorption cross section (×10−28 m2) |
Materials |
Thermal neutron absorption cross section (×10−28 m2) |
SiC |
0.12 |
Cu |
3.59 |
Zr |
0.18 |
Mo |
2.5 |
Nb |
1.1 |
Ni |
4.5 |
Ti |
5.6 |
Si |
0.13 |
3 Study on wettability of Zr–Cu alloy
Based on the design and phase diagram of Zr–Cu alloy, the filler metal has good high-temperature performance and intermetallic alloys and compounds as much as possible, 80Zr–20Cu (wt%) filler metal is designed for brazing SiC ceramic. The low thermal neutron absorption cross section about 1.07 × 10−28 m2 of 80Zr–20Cu (wt%) is obtained by calculation. The solidus and liquidus temperature of the filler metal are 1023 °C and 1056 °C by DSC analysis, respectively. The microstructure of the filler metal (Fig. 2) is mainly composed of eutectic alloy, Zr and CuZr2. The wettability of 80Zr–20Cu (wt%) on SiC ceramic substrate is shown in Fig. 3. Fig. 3(a) is obtained by high temperature wetting test, it is found that the 80Zr–20Cu (wt%) alloy can well wettability on SiC ceramic, and the wetting angle is about 34° at 1200 °C. A good interface is formed between the filler metal and SiC ceramic during the process of high temperature wetting and spreading.
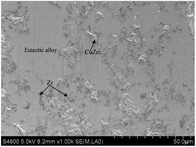 |
| Fig. 2 The microstructure of the filler metal. | |
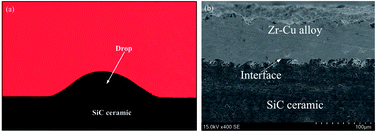 |
| Fig. 3 Wettability of the 80Zr–20Cu (wt%) on SiC ceramic substrate at 1200 °C: (a) wetting angle; (b) interface microstructure. | |
4 Brazing results
Brazing experiments were carried out with 80Zr–20Cu (wt%) alloy as filler metal and RBSiC ceramic as base material. A sandwich-style structure between the Zr–Cu alloy and two SiC ceramic was heated in the vacuum of 3 × 10−3 Pa at different brazing temperatures with the heating rate of 4 °C min−1, held for 20 min, and then at the same rate of the cooled to room temperature. The shear strength of the brazed joint at different temperatures is shown in Fig. 4. It can be seen that the shear strength of the joint increases with the increase of the brazing temperature, and the shear strength of SiC joint that achieves the maximum at 1200 °C is 57 MPa, and then decreases with the increase of brazing temperature. Therefore, the microstructure of SiC brazed joints at 1200 °C is mainly discussed. Fig. 5 shows that microstructure and relevant EDS analysis of SiC ceramic joint brazed at 1200 °C, it can be seen that filler metal can effectively fill the gap between SiC ceramic, and there are no pores and cracks in the brazed joint. Meanwhile, a good interface between Zr–Cu alloy and SiC ceramic is bonded. The phases of the joint are confirmed by the XRD patterns of Fig. 6. The possible phases of the brazing layer are mainly eutectic alloy, CuZr2 and Zr, and the main substances of the interfacial reaction layer are ZrC and Zr2Si. Therefore, the structures of the center of the brazing seam to the parent material are Zr–Cu/Zr2Si/Zr2Si + ZrC/ZrC/SiC, successively (Table 3).
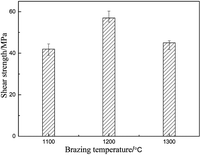 |
| Fig. 4 Shear strength of SiC ceramic brazing joint at different temperatures. | |
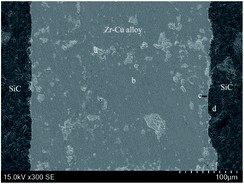 |
| Fig. 5 Microstructure of SiC ceramic joints brazed at 1200 °C. | |
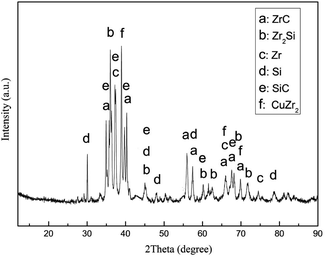 |
| Fig. 6 XRD patterns of the interface of the Zr–Cu alloy/SiC ceramic. | |
Table 3 EDS analysis of the brazed joint at 1200 °C (at%)
Phase region |
Zr |
Cu |
Si |
C |
Possible phase |
a |
75.59 |
24.08 |
0.13 |
0.20 |
CuZr2 + Zr |
b |
70.48 |
27.94 |
0.50 |
1.08 |
Eutectic alloy |
c |
63.58 |
9.80 |
19.39 |
7.23 |
Zr2Si |
d |
58.90 |
1.45 |
23.24 |
16.41 |
ZrC + Zr2Si |
SiC ceramic is a stable compound that is difficult to decompose at 1200 °C. However, the SiC ceramic interface will become thermodynamically unstable and decompose when the SiC ceramic interface contacts with strong reactive elements such as Zr, Ti and Nb.20 For this reason, the interface of SiC ceramics is first decomposed into Si and C atoms (SiC = Si + C) at joining temperature. The atomic radius Si and C are 0.146 nm and 0.091 nm respectively, which compared to the Zr atomic radius (0.216 nm) is very small, thus the small size Si atoms and C atoms can diffuse into Zr matrix to form a diffusion layer of solid solution. The Si and C atoms precipitate from the Zr matrix when they reach the supersaturated state in Zr atom. From thermodynamic analysis, the reaction of this chemical reaction (SiC + 3Zr = ZrC + Zr2Si) has the lowest Gibbs free energy, it is inferred that the stability of the carbides and silicides by the reaction of SiC and Zr is higher than that of the single carbon and silicon. Therefore, the precipitated C and Si atoms are more inclined to combine with Zr element to form ZrC and Zr2Si phases. The enthalpies of formation of Zr2Si (ΔHθ1473 k = −221.6 kJ mol−1) and ZrC (ΔHθ1473 k = −198.2 kJ mol−1) at brazing temperature are negative, which provides a thermal drive for the interface reaction between SiC and Zr-based filler metal. In summary, the interfacial reactions between SiC ceramics and Zr-based filler metals are described as follows ([Si]: solid solution Si atoms, [C]: solid solution C atoms):
In general, the thermal expansion coefficient between SiC ceramic and brazing alloy is quite different, which leads to the larger residual stress of the brazed joint. The thermal expansion coefficient of the filler metal measured by the hot expand coefficient measure instrument is 7.4 × 10−6 K−1. The thermal expansion coefficients of the Zr2Si and ZrC are 7.0 × 10−6 K−1and 6.6 × 10−6 K−1 respectively,21–23 and the thermal expansion coefficient of SiC ceramic is 4.80 × 10−6 K−1. Therefore, the gradient transition of the thermal expansion coefficients of Zr–Cu/Zr2Si/ZrC/SiC are formed, which can effectively relieve and release the residual stress of the welding process and improve the performance of the SiC ceramic joint.
5 Conclusions
The design of Zr–Cu alloy filler metal was applied to active brazing of SiC ceramic as a nuclear fuel cladding material. The safety, interface reaction, residual stress, thermal neutron absorption cross section of the SiC ceramic joint should be considered in the design of the filler metal. 80Zr–20Cu (wt%) alloy filler metal has good wettability and brazing property for SiC ceramic at 1200 °C. The active element Zr plays an important role in the interfacial reaction of SiC ceramic, and the interface compounds are mainly ZrC and Zr2Si. An essentially layered structure Zr–Cu/Zr2Si/ZrC/SiC are from the center of brazing seam to parent material, forming a gradient transition of the thermal expansion coefficients can effectively relieve and release the residual stress of brazed joints.
Conflicts of interest
There are no conflicts to declare.
Notes and references
- Y. Yu, H. Y. Dong, B. Ma, Q. Ren and W. Ma, J. Alloys Compd., 2017, 708, 373–379 CrossRef.
- Z. J. Ma, W. B. Chen, Z. L. Hu, X. Z. Pan, G. P. Dong, S. F. Zhou, M. Y. Peng, Y. Li, C. X. Liao, Q. L. Xiao and J. R. Qiu, RSC Adv., 2013, 3, 20132–20137 RSC.
- T. Dinh, H. P. Phan, T. Kozeki, A. Qamar, T. Namazu, N. T. Nguyena and D. V. Dao, RSC Adv., 2015, 5, 106083–106086 RSC.
- Y. Katoh, L. L. Snead, C. H. Henager, T. Nozawa, T. Hinoki and A. Ivekovic, J. Nucl. Mater., 2014, 55, 387–397 CrossRef.
- S. J. Zinkle, K. A. Terrani, J. C. Gehin, L. J. Ott and L. L. Snead, J. Nucl. Mater., 2014, 448, 374–379 CrossRef.
- T. Koyanagia, Y. Katoh, J. O. Kiggans, T. Hinoki, H. E. Khalifa and C. P. Deck, J. Nucl. Mater., 2017, 488, 150–159 CrossRef.
- Y. C. Yoo, J. H. Kim and K. Park, Mater. Lett., 2000, 42, 362–366 CrossRef.
- P. K. Gianchandania, V. Casalegnoa, M. Salvoa, G. Bianchib, A. Ortonab and M. Ferrarisa, Mater. Lett., 2018, 221, 240–243 CrossRef.
- P. Fitriani, A. Septiadi, J. D. Hyuk and D. H. Yoon, J. Eur. Ceram. Soc., 2018, 10, 3433–3440 CrossRef.
- G. Ceccone, M. G. Nicholas, S. D. Peteves, A. A. Kodentsov, J. K. Kivilahti and F. J. J. VanLoo, J. Eur. Ceram. Soc., 1995, 15, 563–572 CrossRef.
- Y. Jung, J. H. Park, H. G. Kim, D. J. Park, J. Y. Park and W. J. Kim, Nucl. Eng. Technol., 2016, 4, 1009–1014 CrossRef.
- X. Y. Dai, J. Cao, Z. Chen, X. G. Song and J. C. Feng, Ceram. Int., 2016, 42, 6319–6328 CrossRef.
- H. P. Xiong, B. Chen, Y. Pan, H. S. Zhao and L. Ye, J. Eur. Ceram. Soc., 2014, 34, 1481–1486 CrossRef.
- S. Morozumi, M. Endo, M. Kikuchi and K. Hamajima, J. Mater. Sci., 1985, 20, 3976–3982 CrossRef.
- W. W. Li, B. Chen, H. P. Xiong, W. J. Zou and H. S. Ren, J. Eur. Ceram. Soc., 2017, 13, 3849–3859 CrossRef.
- B. B. Gerasimov and A. C. Monakhov, Nuclear engineering materials, Atomic Energy Press, Beijing, 1982 Search PubMed.
- D. L. Ye and J. H. Hu, Handbook of thermodynamics data for inorganic compounds, Metallurgical Industry Press, Beijing, 2002 Search PubMed.
- L. Xu, C. Z. Huang, H. I. Liu, B. Zou, H. T. Zhu and G. L. Zhao, Int. J. Refract. Met. Hard Mater., 2014, 42, 116–119 CrossRef.
- H. Yeom, C. Lockhart, R. Mariani, P. Xu, M. Corradini and I. Sridharan, J. Nucl. Mater., 2018, 499, 256–267 CrossRef.
- J. S. Park, K. Landry and J. H. Perepezko, Mat. Sci. Eng. A, 1999, 259, 279–286 CrossRef.
- J. K. Li, L. Liu, Y. T. Wu, W. L. Zhang and W. B. Hu, Mater. Lett., 2008, 62, 3135–3138 CrossRef.
- G. Schneidner, Solid state physics, Academic Press, New York, 1965 Search PubMed.
- N. Leonard and L. N. Grossman, J. Eur. Ceram. Soc., 1995, 48, 236–242 Search PubMed.
|
This journal is © The Royal Society of Chemistry 2018 |
Click here to see how this site uses Cookies. View our privacy policy here.