DOI:
10.1039/C8RA04205E
(Review Article)
RSC Adv., 2018,
8, 28048-28085
A review of the interfacial characteristics of polymer nanocomposites containing carbon nanotubes
Received
17th May 2018
, Accepted 26th July 2018
First published on 6th August 2018
Abstract
This paper provides an overview of recent advances in research on the interfacial characteristics of carbon nanotube–polymer nanocomposites. The state of knowledge about the chemical functionalization of carbon nanotubes as well as the interaction at the interface between the carbon nanotube and the polymer matrix is presented. The primary focus of this paper is on identifying the fundamental relationship between nanocomposite properties and interfacial characteristics. The progress, remaining challenges, and future directions of research are discussed. The latest developments of both microscopy and scattering techniques are reviewed, and their respective strengths and limitations are briefly discussed. The main methods available for the chemical functionalization of carbon nanotubes are summarized, and particular interest is given to evaluation of their advantages and disadvantages. The critical issues related to the interaction at the interface are discussed, and the important techniques for improving the properties of carbon nanotube–polymer nanocomposites are introduced. Additionally, the mechanism responsible for the interfacial interaction at the molecular level is briefly described. Furthermore, the mechanical, electrical, and thermal properties of the nanocomposites are discussed separately, and their influencing factors are briefly introduced. Finally, the current challenges and opportunities for efficiently translating the remarkable properties of carbon nanotubes to polymer matrices are summarized in the hopes of facilitating the development of this emerging area. Potential topics of oncoming focus are highlighted, and several suggestions concerning future research needs are also presented.
1. Introduction
Carbon nanotubes were first observed by Iijima1,2 nearly three decades ago, and since then, they have been the focus of considerable research.3,4 Carbon nanotubes can be categorized as single-walled and multi-walled carbon nanotubes,1,2 and a multi-walled carbon nanotube consists of multiple rolled layers of graphene, as shown in Fig. 1. Carbon nanotubes have generated tremendous scientific and technical interest over the past decade due to their unique properties at the nanoscale. Extraordinary physical and mechanical properties have been reported for this form of carbon with a cylindrical nanostructure.3,4 As a consequence, carbon nanotubes offer unique opportunities for the development of fundamentally new nanomaterials.
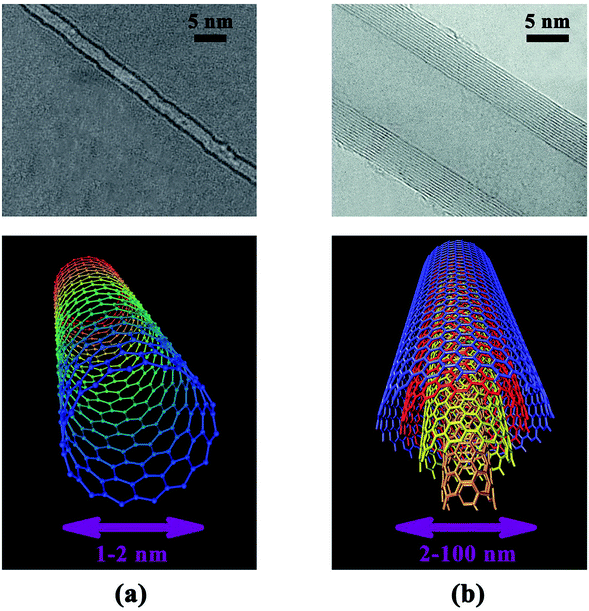 |
| Fig. 1 Transmission electron microscopy images and schematic diagrams of carbon nanotubes, showing typical diameters of (a) a single-walled carbon nanotube and (b) a multi-walled carbon nanotube. The microscopy image of the single-walled carbon nanotube is adapted with permission from ref. 5. Copyright 2012, Springer Nature Limited. The microscopy image of the multi-walled carbon nanotube is adapted from the “Endo Laboratory” website.6 | |
Due to the unique properties of carbon nanotubes, there has been an increasing interest in the development of nanocomposite materials.7–10 In particular, the outstanding mechanical properties are expected to have many advantages to develop the nanocomposite materials reinforced with carbon nanotubes.11,12 As a result, there has been a large focus on the research and development of carbon nanotube-based polymer composite materials.13,14 The first polymer nanocomposite material reinforced with carbon nanotubes was reported by Ajayan et al.15 in 1994. Since the realization of the remarkable properties of carbon nanotubes, various advanced carbon nanotube–polymer composite materials have been prepared by using a variety of fabrication techniques.16,17 A broad range of potential applications can be envisioned for the use of carbon nanotube–polymer composite materials, and some examples of their application are shown in Fig. 2.
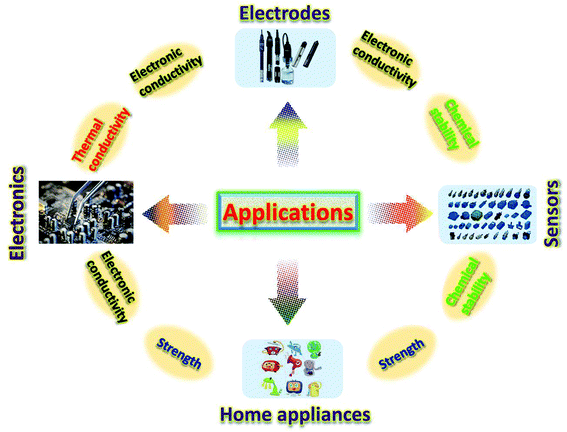 |
| Fig. 2 Examples of the potential application of carbon nanotube–polymer composite materials. | |
There has been considerable research in attempting to utilize carbon nanotubes as reinforcements for polymer composite materials, and significant progress has been made.7–10 However, after nearly three decades of research, the potential of carbon nanotubes as reinforcement in polymer composite materials has not been fully realized.11 To harness the unique attributes of carbon nanotubes exhibited at the nanoscale, it is necessary to resolve the issues related to the basic principle of the nanoscale mechanical reinforcement of polymer matrices with carbon nanotubes,11 as well as the characteristics of the interface between the carbon nanotube and the surrounding polymer matrix.18 To achieve the optimal reinforcement with carbon nanotubes, it is of great importance to understand the relationship between nanocomposite properties and interfacial characteristics.11,13
Great achievements have been made in the field of carbon nanotube–polymer composites during the past few years.11–17 However, poor dispersion and weak interfacial bonding remain obstacles for effectively incorporating carbon nanotubes into polymer matrices. There are still significant challenges encountered while exploring carbon nanotubes as filler materials to be overcome. It is often difficult to achieve a uniform dispersion of carbon nanotubes in the polymer matrix,11 as well as to enable a strong interaction at the interface between the carbon nanotube and the polymer matrix.18 Various attempts have been made to effectively reinforce a polymer matrix with carbon nanotubes.19–22
The issue related to the uniform dispersion of carbon nanotubes is critical to efficient reinforcement in polymer nanocomposite materials.23 Much effort has been devoted to improve the dispersion of carbon nanotubes, such as the use of physical treatment,13 surfactants,21 and chemical functionalization of the surface of carbon nanotubes.22,23 Additionally, strong interfacial bonding is critical to take full advantage of the exceptional properties of carbon nanotubes. Functionalization has been suggested to be an effective approach to acquire high-performance nanocomposite materials because of the ability to significantly improve the dispersion of carbon nanotubes and to greatly enhance the bonding at the interface.23
Much attention has been focused on the characteristics of the interface. To improve the properties of the polymer nanocomposites reinforced with carbon nanotubes, it is necessary to have a better understanding of the characteristics of the interface at the nanometric level.24,25 The interface plays a significant role in the stress transfer between the carbon nanotube and the polymer matrix, and the consequent improvement in nanocomposite properties. The characteristics of the interaction at the interface have been widely studied,24,25 and great achievements have been made in this field, as reviewed by Rahmat and Hubert.18 Unfortunately, it remains unclear how to optimize the interface for mechanical reinforcement. Furthermore, there is still a lack of understanding of the interaction at the interface. To unlock the potential of carbon nanotubes, it is important to fully understand the underlying mechanism responsible for the interfacial interaction at the molecular level to further optimize the interface in polymer nanocomposite materials.26
There is a large number of literatures about the topic discussed here, but a limited number of relevant previous review articles13,18,22–34 are available. Fig. 3 shows how the number of English language refereed journal articles in carbon nanotube–polymer composite materials has steadily increased since 2010. In recent years, the number of publications dealing with various aspects of the polymer nanocomposite materials containing carbon nanotubes has increased markedly. As a consequence, an overview article is required, and the objective of this paper is to address this need. Most of the relevant journal articles have been published since 2010, so that is the focus of this review.
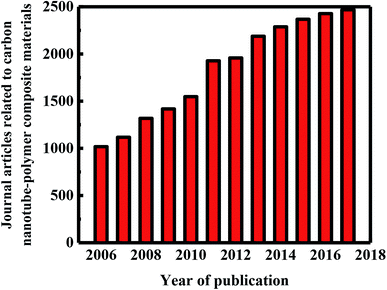 |
| Fig. 3 Recent English language refereed journal publications related to carbon nanotube–polymer composite materials. The data are collected from the Engineering Village© web-based information service. The number of publications dealing with various aspects of the polymer composite materials has increased markedly in recent years. | |
While significant insights have been achieved in this field, there are still many critical issues that need to be addressed to harness the maximum benefits from the remarkable properties of carbon nanotubes. In this paper, the recent advances in the development of carbon nanotube–polymer composites are reviewed, and the progress, remaining challenges, and future directions of research are discussed. Special emphasis is placed on the characteristics of the interaction at the interface.
2. Dispersion and characterization techniques
2.1. Dispersion of carbon nanotubes
The advantages of carbon nanotube–polymer composites include improved stiffness, strength, and fracture toughness. Unfortunately, the expected improvement in the properties of these polymer composites has not been fully realized. Their properties have been found to be critically dependent upon the degree of the dispersion of carbon nanotubes, the interfacial adhesion between the carbon nanotube and the polymer matrix, and the alignment along the principal axis of applied force.18,23 To employ carbon nanotubes as effective reinforcement in polymer composite materials, it is important to achieve uniform dispersion of carbon nanotubes within the polymer matrix. The synthetic methods of the polymer nanocomposite materials have overwhelmingly focused on improving the degree of the dispersion of carbon nanotubes, given the fact that uniform dispersion can significantly improve the properties of these nanocomposite materials.23
Much effort has been devoted to the fabrication of the composite materials. There are a number of effective methods for fabricating polymer nanocomposites with high mechanical or physical properties.23,26 The potential of carbon nanotubes as reinforcements has not been fully realized due partly to the difficulties associated with the dispersion of carbon nanotubes. Considerable progress has been made in the development of the techniques targeting good dispersion.35–38 Hence, the principles and features of these dispersion techniques are briefly summarized here.
Various methods have been proposed to improve the dispersion of carbon nanotubes in a polymer matrix. The most common method used to disperse carbon nanotubes is the ultrasonication technique. High-power ultrasonication is an effective method to disperse carbon nanotubes in a polymer matrix, but is only suitable for dispersing carbon nanotubes in small batches. The characteristics of the various mechanical techniques used for dispersing carbon nanotubes in a polymer matrix are summarized in Table 1, which can serve as a guideline for selecting an appropriate dispersion technique to synthesize carbon nanotube–reinforced polymer composite materials. Nevertheless, the techniques used for dispersing carbon nanotubes in a polymer matrix are not limited to those listed in Table 1. In practical operation, a combination of these techniques are often adopted.39–41 Overall, dispersion of carbon nanotubes in polymer matrices is problematic, and it still remains an active area of research at present.
Table 1 Comparison of various mechanical techniques used for dispersing carbon nanotubes in a polymer matrix
Technique |
Factor |
Damage to nanotubes |
Suitable polymer matrix |
Availability |
Governing factors |
Ultrasonication |
Yes |
Soluble polymer, low viscous polymer or oligomer, monomer |
Commonly used in lab, easy operation and cleaning after use |
Power and mode of sonicator, sonication time |
Calendering |
No |
Liquid polymer or oligomer, monomer |
Operation training is necessary, hard to clean after use |
Rotation speed, distance between adjacent rolls |
Ball milling |
Yes |
Powder (polymer or monomer) |
Easy operation, need to clean after use |
Milling time, rotation speed, size of balls, balls to nanotube ratio |
Shear mixing |
No |
Soluble polymer, low viscous polymer or oligomer, monomer |
Commonly used in lab, easy operation and cleaning after use |
Size and shape of the propeller, mixing speed and time |
Extrusion |
No |
Thermoplastics |
Large-scale production, operation training is necessary, hard to clean after use |
Temperature, configuration and rotation speed of the screw |
2.2. Characterization techniques
To better understand the macroscopic properties of polymer nanocomposite materials, a detailed characterization of several important microstructural features such as the dispersion state and the alignment of carbon nanotubes in polymer matrices is required. The main methods intended to characterize the microstructures of polymer nanocomposite materials can be categorized as microscopy and scattering techniques. Masenelli-Varlot et al.42 have reviewed the recent advances in the microscopy techniques for a better understanding of the mechanical and physical properties of carbon nanotube–reinforced polymer composite materials. Several imaging techniques such as scanning electron microscopy, transmission electron microscopy, near-field microscopies, and focused ion beam microscopy have been introduced, and their principles have also been briefly discussed.42 Microscopy and scattering techniques can provide a quantitative description of the morphology of polymer nanocomposite materials, and they are complementary for structural characterization.43–46
Transmission electron microscopy and scanning electron microscopy techniques can be used to characterize the microstructural features of nanocomposite materials, such as the dispersion state of carbon nanotubes in polymer matrices and the magnitude of the interfacial adhesion between them.47 Other important factors such as the alignment of carbon nanotubes in the polymer matrix, as well as other common analyses involving distribution and quantification of the dimension of carbon nanotubes can also be explored by using these electron microscopy methods. Solá48 have reviewed these electron microscopy techniques, and have also discussed their strengths and limitations, respectively. There is need for improving different aspects of the electron microscopy techniques, particularly the image contrast of carbon nanotubes within the polymer matrix.48
It is critical to determine the size distribution of suspended carbon nanotube objects. Given the variability in dimensions, characterization the size of carbon nanotubes is best accomplished with an imaging method, specifically atomic force microscopy.49–51 Atomic force microscopy has become an important technique in the field of composite materials due to its unique ability to image and characterize structures in liquid, ambient, and vacuum environments.52–54 Recently, light, neutron, and small-angle X-ray scattering techniques have also been used to quantitatively analyze the structure of carbon nanotubes in suspensions. Electron microscopy techniques are in principle more powerful than scattering techniques for elucidating the morphologies of polymer nanocomposite materials.45 Although transmission electron microscopy is typically used to “visually” characterize the dispersion state of carbon nanotubes, it is not an accurate means to determine this important quantity. In contrast, scattering techniques are the most appropriate means to characterize dispersion.46
The dispersion state of carbon nanotube in a polymer matrix should be evaluated over a broad range of scales and can be accomplished by using the following imaging techniques: transmission electron microscopy, scanning electron microscopy, scanning probe microscopy, polarized Raman spectroscopy,55–57 optical microscopy, and confocal microscopy. In recent years, confocal laser scanning microscopy has been successfully applied to evaluate the dispersion state of carbon nanotubes in polymer matrices.58,59 Scattering techniques, such as wide-angle X-ray scattering, small-angle X-ray scattering, and polarized Raman spectroscopy, are very useful for analyzing the alignment of carbon nanotubes in polymer matrices. Standard Raman spectroscopy has been used to monitor deformation of carbon nanotubes in a polymer matrix. Polarized Raman spectroscopy has been widely used to examine the alignment of different carbon nanotube assemblages.60–64 However, these scattering techniques seem difficult to interpret the dispersion state of carbon nanotubes in polymer matrices. This is because the contrast ratio is significantly lower, as well as the presence of rigid rod behavior is not equivalent to the uniform dispersion of carbon nanotubes at all length scales. At a local length scale, ultraviolet-visible-near infrared absorption spectroscopy can be used to determine the dispersion state of single-walled carbon nanotubes in solutions and nanocomposite materials qualitatively.65–69 This is because only individual or small bundles of single-walled carbon nanotubes exhibit sharp absorbance peaks,65 which can be termed as van Hove singularities. In contrast, large bundles, associates with the poor dispersion of carbon nanotubes, exhibit only monotonically decreasing absorbance with increasing wavelength.65,70
All common conventional microscopy techniques have their specific disadvantages about the image of the dispersion of carbon nanotubes within a polymer matrix. Optical microscopy is useful to assess the large-scale agglomerates of carbon nanotubes, but this technique becomes incapable to accurately determine the dispersion state at the sub-micron scale.71,72 Scanning probe microscopy, more specifically atomic force microscopy, and scanning electron microscopy can provide sufficient information about the surface features of polymer nanocomposite materials. However, these imaging techniques in general only yield a characteristic three-dimensional appearance of the surface of carbon nanotubes within a polymer matrix.73,74 While the spatial resolution achieved with transmission electron microscopy can offer sufficient information about the microstructure of carbon nanotubes, there are intrinsic challenges and imaging artifacts that need special attention to properly characterize the bulk characteristics of polymer nanocomposite materials.75,76
3. Functionalization of carbon nanotubes with polymers
Chemical modification or functionalization can effectively improve the dispersion state of carbon nanotubes. Given that mechanical properties of the composite materials depend critically upon the efficiency of load transfer at the interface,18,25 chemical functionalization is an effective approach to increase the strength of the interface. Functionalization of the surface of carbon nanotubes has received a significant amount of attention recently due to its potential applications in many fields. Chemical functionalization provides a convenient way to improve the dispersion state of carbon nanotubes as well as to modify the characteristics of the interface, which in turn may improve the properties of the polymer nanocomposite materials. Therefore, the nature of chemical functionalization may play an important role in determining the properties of the polymer nanocomposite materials reinforced with carbon nanotubes. This modification method will become more prevalent, since significant progress has been made recently in the field of chemical functionalization.
3.1. Functionalization method
The performance of the composite materials depends strongly upon the dispersion state of carbon nanotubes and the interaction at the interface.18,23 It has been realized that the main obstacle in the translation of the remarkable physical and mechanical properties of carbon nanotubes into useful polymer composite materials is the nonreactive nature of the carbon nanotubes, which ultimately results in a weak interfacial interaction with the polymer matrix that leads to inefficient load transfer and phase separation.23 Therefore, much effort has been devoted to develop various approaches to modify properties of the surface of carbon nanotubes.77–79 Functionalized carbon nanotubes have been playing an increasingly important role in the research, development, and application of the composite materials. Considerable advances related to the science and technology of chemical functionalization have been made.4,77,80,81 The principles of modification methods along with the benefits and disadvantages associated with these methods have been reviewed by Ma et al.23
It is necessary to improve the dispersion state of carbon nanotubes and the efficiency of load transfer at the interface in order to achieve optimum performance of the composite materials.13 Unless the interface is carefully designed, interfacial slippage may be appeared due to poor load transfer at the interface.82 Chemical functionalization of carbon nanotubes is of great importance to significantly improve the dispersion state of carbon nanotubes as well as to effectively enhance the load transfer efficiency in the composite materials.13,83 Various methods of the chemical functionalization of carbon nanotubes have been developed.4,84 The grafting of macromolecules onto the surfaces of carbon nanotubes has also been paid much attention during the past few years. It is expected that the addition of a whole polymer chain affects the properties of the carbon nanotubes and their affinity to polymer matrices more greatly than that of low molecular weight functionalities.
To improve the properties of the composite materials, low-cost and industrially feasible approaches to modification of the surface of carbon nanotubes have been much pursued vigorously in recent years. These approaches for the functionalization of carbon nanotubes by polymers can be simply divided into two categories, involving either non-covalent or covalent bonding between the carbon nanotube and the polymer matrix.85–87 Non-covalent functionalization of carbon nanotubes includes non-covalent coating with surfactants, surface wrapping with long polymer chains, and non-covalent adsorption of non-charged polymer chains. Non-covalent modifications utilize π–π interactions and van der Waals forces by adsorption of polymers, biomolecules, polynuclear aromatic compounds, or surfactants. Non-covalent functionalization helps to separate the carbon nanotube aggregates and improve the dispersion state of carbon nanotubes, while the structural integrity of carbon nanotubes is preserved and thus their properties are not disrupted.78
The interaction between carbon nanotubes and polymers, surfactants, or low-molecular-weight molecules has been widely studied.23,39,77–80 Conjugated polymers have been found recently to strongly interact with the surface of carbon nanotubes through π-stacking, in addition to small molecules with extended conjugation. This strong interaction allows the backbone of the conjugated polymers to wrap carbon nanotubes efficiently,78 as shown in Fig. 4. Unfortunately, the agents that can be used for this method are very limited, their dispersion is not very stable, and most importantly, it is difficult to further modify carbon nanotubes with different functionalities.
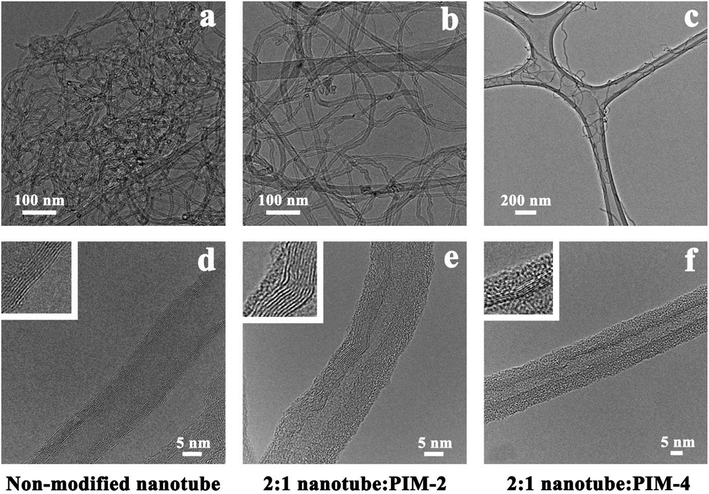 |
| Fig. 4 Transmission electron microscopy images for (panel (a)) pristine multi-walled carbon nanotubes, (panel (b)) PIM-2-modified multi-walled carbon nanotubes, and (panel (c)) PIM-4-modified multi-walled carbon nanotubes. Panel (d) high-resolution transmission electron microscopy for pristine multi-walled carbon nanotubes; the magnified area in the box shows the smooth surface of the walls of the carbon nanotube. Panel (e) high-resolution transmission electron microscopy for the PIM-2-modified multi-walled carbon nanotubes; the magnified area in the box shows the walls of the carbon nanotube with a thin layer of the coating polymer on the surface. Panel (f) high-resolution transmission electron microscopy for the PIM-4-modified multi-walled carbon nanotubes; similar to panel (e), the magnified area in the box shows the walls of the carbon nanotube with a thin layer of the coating polymer on the surface. The information about the chemical structures of conjugated polyelectrolytes PIM-2 and PIM-4 is described in ref. 78. The figure is adapted with permission from ref. 78. Copyright 2015, American Chemical Society. | |
The second method of carbon nanotube functionalization is covalent modifications. Covalent modifications attach a functional group onto ends or side wall of carbon nanotubes. Covalent modifications may alter the intrinsic properties of carbon nanotubes, but can greatly improve the solubility and compatibility of carbon nanotubes, which highlights the importance of this functionalization method. There are two overarching methods, “grafting to” and “grafting from”, to prepare the polymer nanocomposites containing carbon nanotubes.88–90
3.2. “Grafting to” method
According to the “grafting to” method, end-functionalized polymer molecules react with complementary functional groups located on the surface of either pristine or pre-functionalized carbon nanotubes to form tethered chains.91–95 The “grafting to” method mainly exploits carbon nanotube bound carboxylic acid groups in esterification or amidation reactions with hydroxyl or amine containing polymer or organic molecules.96–99 Unfortunately, there is limitation in the availability of acid groups generated through oxidation procedure on the surface and tips of carbon nanotubes.27 Furthermore, carbon nanotubes are usually digested in acid over a long period of time in order to introduce a large concentration of acid groups on their surfaces, which can damage the sp2 network severely and may greatly shorten the length of carbon nanotubes.27
The problems associated with wrapping and adsorption have also arisen during covalent grafting of macromolecules onto the surface of carbon nanotubes.100,101 The level of grafting is inversely proportional to the molecular weight of polymer, and grafting high molecular weight polymers is inefficient when the “grafting to” method is used. The “grafting to” method is preferred to attach small molecules on the surface of carbon nanotubes, although it has been widely used.27
3.3. “Grafting from” method
The “grafting from” method utilizes the polymerization initiated from the surface of carbon nanotubes by attached initiating groups.102–107 Appropriate initiator is covalently attached to the surface of carbon nanotubes, depending upon the polymerization mechanism selected for grafting. In recent years, atom transfer radical polymerization, reversible addition-fragmentation chain transfer polymerization, ring-opening metathesis polymerization, and in situ free radical polymerization have been successfully used to synthesize carbon nanotube–reinforced polymer composite materials.27 Grafting high molecular weight polymers could be efficient when the “grafting from” method is used.100,101 Furthermore, a quite high grafting density can be achieved by using this method. In recent years, there has been an increasing interest in the use of living anionic polymerization for the preparation of carbon nanotube–reinforced polymer composite materials. Even at a very low concentration of initiator, high-molecular-weight polymer nanocomposites can be synthesized in a controlled manner by using this polymerization mechanism.108,109
3.4. Mixed mechanism
Hyperbranched poly(amidoamine) grafted multi-walled carbon nanotubes have been prepared by using a “grafting from” method.110 Single-walled carbon nanotubes functionalized with polyamidoamine dendrimers have also been prepared,111 as shown in Fig. 5. The synthesized polymer nanocomposite material was a second-generation polyamidoamine dendrimers. Firstly, single-walled carbon nanotubes were functionalized by a 1,3-dipolar cycloaddition reaction, followed by the formation of a pyrrolidine ring functionalized with a N-tert-butoxycarbonyl-protected amine group. Secondly, the amino groups interacted with ethylenediamine and methyl acrylate to synthesize the carbon nanotubes grafted with the first-generation polyamidoamine. The same reaction sequence resulted in the second-generation dendrimer. Thermogravimetric analysis was performed, and the results indicated a loss of weight of approximately 33%.
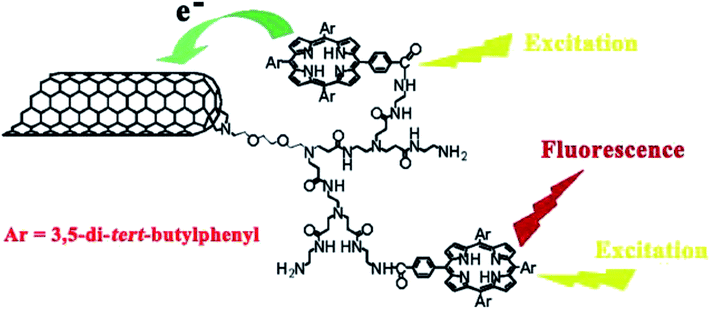 |
| Fig. 5 Reaction scheme for the synthesis and characterization of a series of single-walled carbon nanotubes functionalized with polyamidoamine dendrimers. The figure is adapted with permission from ref. 111. Copyright 2006, American Chemical Society. | |
Xu et al.112 reported single-step in situ synthesis of polystyrene-grafted multi-walled carbon nanotubes by cobalt-60 γ-ray irradiation. Chemical functionalization of carbon nanotubes was accomplished through γ-ray irradiation. The functionalized carbon nanotubes were characterized by thermal gravimetric analysis, and the polymer content could be up to 15 wt%, depending on the duration of irradiation. They suggested that chemical functionalization of carbon nanotubes accomplished through γ-ray irradiation involves both “grafting to” and “grafting from” mechanisms.
Liu and Chen113 prepared bromine-terminated poly(styrene) by using an atom transfer radical polymerization method, which was then grafted to multi-walled carbon nanotubes. The bromine atom is transferred from poly(styrene) to the surface of carbon nanotubes during the grafting process, and served as the initiator. In a subsequent step, a surface-initiated atom transfer radical polymerization of poly(N-isopropylacrylamide) from the carbon nanotube–poly(styrene) surfaces was carried out. Through the method combining “grafting to” and “grafting from”, the surface of carbon nanotubes were bounded by the a polymer brush consisted of two arms, i.e., poly(styrene) and poly(N-isopropylacrylamide), as shown in Fig. 6.
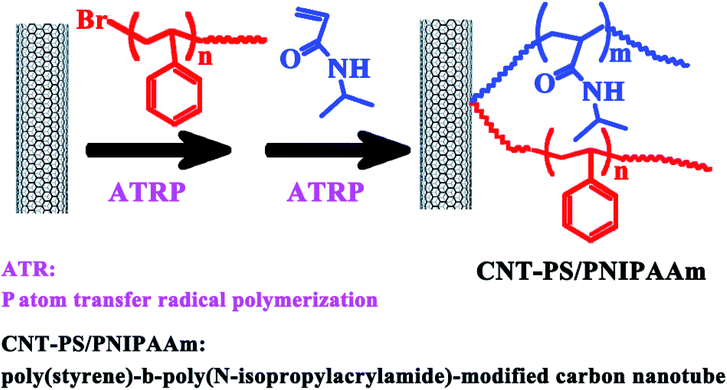 |
| Fig. 6 Incorporation of amphiphilic v-shaped poly(styrene)-b-poly(N-isopropylacrylamide) polymers onto the surface of multi-walled carbon nanotubes through sequential “grafting-to” and “grafting-from” techniques. The figure is adapted with permission from ref. 113. Copyright 2007, American Chemical Society. | |
3.5. Endohedral filling
There is an increasing interest in trapping polymer macromolecules into carbon nanotube channels. The first successful experiments on filling carbon nanotubes with polymers were reported by Liu et al.,114 who used supercritical carbon dioxide, an excellent solvent, to encapsulate polystyrene into hollow multi-walled carbon nanotubes with a length of approximately 2–3 μm and an outer diameter of approximately 40–50 nm. In this approach, the initiator of benzoyl peroxide and the monomer of styrene were carried into the cavities of carbon nanotubes by means of supercritical carbon dioxide. Both of the two components remained in the hollow cores of carbon nanotubes after removing the carbon dioxide, followed by polymerizing the monomers. Liu et al.114 prepared a carbon nanotube–polystyrene composite by using this technique. Furthermore, the concentration of fillers in the composite can be controlled by the release rate of supercritical carbon dioxide during the soaking process. On the other hand, preliminary experiments on the synthesis of carbon nanotube–polyacetylene composites have been carried out using a similar procedure.115 Steinmetz et al.116 reported the results of carbon nanotubes filled with the conducting polymer, polypyrrole, and the photo-conducting polymer, poly(N-vinyl carbazole), using supercritical fluid impregnation.
Previous studies have shown that polymer encapsulation in carbon nanotube channels is feasible using a two-step process.114–116 Firstly, supercritical carbon dioxide carries the monomer (initiator) components into the carbon nanotube cavities. Secondly, after the removal of carbon dioxide, the monomers are polymerized at a certain temperature. The supercritical fluid method, in principle, can be used to prepare other polymer nanocomposites containing carbon nanotubes. Consequently, Bazilevsky et al.117 devised a method to selectively intercalate relatively low-molecular-weight polymers into open-end, as-grown, wettable carbon nanotubes at room temperature in open air. Relatively low-molecular-weight polymers, such as poly(caprolactone) and poly(ethylene oxide), were encapsulated in multi-walled carbon nanotubes with diameters of 50–100 nm, as confirmed by transmission electron microscopy shown in Fig. 7. This revealed the morphological characterization of mixtures in nanoconfinements affected by intermolecular forces. This method can be explained by a novel self-sustained diffusion mechanism, as discussed in the literature.117 Larger macromolecules remained outside of the carbon nanotubes, whereas relatively small, flexible polymer molecules were allowed to enter. A theoretical model was also presented to describe the physical transport mechanism believed to be responsible for the selective filling of carbon nanotubes with different polymers.
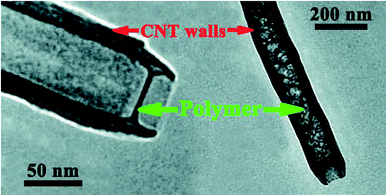 |
| Fig. 7 Transmission electron micrographs of poly(caprolactone) deposited inside multi-walled carbon nanotubes. They were obtained by dispensing poly(caprolactone) in methylene chloride over open-end, as-grown, wettable carbon nanotubes. The figure is adapted with permission from ref. 117. Copyright 2007, American Chemical Society. | |
4. Carbon nanotube–polymer interfaces
Mechanical properties of the polymer composites reinforced by carbon nanotubes have been widely studied.118–121 The ultimate goal is to achieve the polymer nanocomposites which are optimally reinforced. Recently, the carbon nanotube–polymer interface have attracted increasing attention.122–125 The interface is of fundamental importance, because it governs the load transfer efficiency and plays an important role in determining the mechanical properties of the polymer nanocomposites.126–131 As a consequence, the properties of these nanocomposites are highly dependent upon the nature of the interface, i.e., control of properties at the interface is critical. The nature of the interface is further complicated because the dimension of carbon nanotubes is of the same order of magnitude as that of polymer chains.
In addition to good dispersion and orientation of the carbon nanotubes, the interface needs to be carefully engineered to achieve a combination of adequate stress transfer at low strains and frictional energy dissipation at higher strains.132–135 Otherwise, poor load transfer at the interface may result in interfacial slippage and reduced performance of the polymer nanocomposites.14 Current efforts are focused on optimization of the interface to provide better interfacial load transfer, which demands a better understanding of the interfacial characteristics.136–139 It has been found that the interfacial characteristics can significantly influence the efficiency of carbon nanotube reinforcements in improving properties of the polymer nanocomposites.140–143
To ensure efficient load transfer, various approaches have been proposed for the optimization of the interface. One effective way to improve the interfacial bonding is chemical functionalization of the surface of carbon nanotubes. The ultimate interface is realized by constructing chemical bonds between the carbon nanotube and the polymer matrix. Chemical functionalization can provide a means for tailoring the interface to achieve optimal performance of the polymer nanocomposite materials. Consequently, the utilization of chemically functionalized carbon nanotubes offers tremendous scope for tailoring the interface and the development of advanced nanocomposite materials.
The efficiency of interfacial stress transfer has been widely studied,18 since the interaction at the interface is essential to understand the factors influencing the mechanical behavior of carbon nanotube–polymer composites. In particular, the stress-transfer mechanism is an important issue to be addressed, using both experiments and analysis.37 Experimental results showed that the strength of carbon nanotube–polymer composites is lower than that predicted by theory.144,145 This phenomenon may be attributed to poor interfacial bonding.11 Therefore, special attention should be paid to the interaction at the interface.
Some interesting results have described progress on addressing the above issue.146 The strength at the interface has been measured using nano-pull-out tests.147–156 These experiments are very difficult to perform and the scatters in the data are significantly high. Interfacial shear strength can be measured from the bulk composite by load transfer experiments, at higher load there is slippage between the carbon nanotube and the polymer matrix. Barber et al.147 have reported the force required to separate individual carbon nanotubes from polymer matrices, measured by reproducible nano-pull-out experiments using atomic force microscopy. Since the radius of gyration of polymers is of the same order of magnitude as the outer diameter of carbon nanotubes, the polymer chains close to the interface behaved differently than the bulk.147 Experimental and theoretical results obtained for the shear strength of the interface are listed in Table 2.
Table 2 Experimental and theoretical results obtained for the shear strength of the interface between the carbon nanotube and the polymer matrix
Observed strength |
System |
Author |
Reference |
47 MPa |
Pull-out measurement of multi-walled carbon nanotubes from polyethylene-butene |
Barber et al. |
147 |
17–88 MPa |
Pull-out tests of multi-walled carbon nanotubes from a polyethylene-butene matrix for various diameter nanotubes |
Barber et al. |
148 |
22–138 MPa |
Pull-out measurement of chemically modified multi-walled carbon nanotubes from epoxy matrix |
Barber et al. |
149 |
170 MPa |
Pull-out measurement for a carbon nanofiber–reinforced epoxy composite |
Manoharan et al. |
151 |
Larger than 160 MPa |
Collagen wrapped single-walled carbon nanotube in polyvinyl alcohol matrix |
Roy et al. |
152 |
3.5–14 MPa |
Pull-out tests of an individual multi-walled carbon nanotube from poly-ether-ether-ketone |
Tsuda et al. |
153 |
6.24 ± 3.6 MPa |
Pull-out measurement for an individual multi-walled carbon nanotube from an epoxy matrix |
Ganesan et al. |
154 |
36–51 MPa |
Pull-out tests of multi-walled carbon nanotubes from poly(methyl methacrylate) |
Xu et al. |
155 |
10.3–24.1 MPa |
Multi-walled carbon nanotubes and epoxy using shear-lag analysis |
Yashiro et al. |
156 |
Recent studies have demonstrated that there exists significant interaction at the interface.78,118,123,139,143,157 Dassios and Galiotis139 reported the manufacturing of millimeter-high, vertically aligned multi-walled carbon nanotube–poly(vinyl alcohol) composite mats. Direct evidence of significant interfacial interaction was gave by means of thermogravimetric analysis, as well as scanning electron microscope and transmission electron microscopy images, as shown in Fig. 8. It was found that extensive polymer sheathing occurred homogeneously over the carbon nanotubes in the mats without affecting their alignment, morphology, or physical characteristics. The procedure did not evolve any chemical modification or oxidation of the carbon nanotube surfaces.
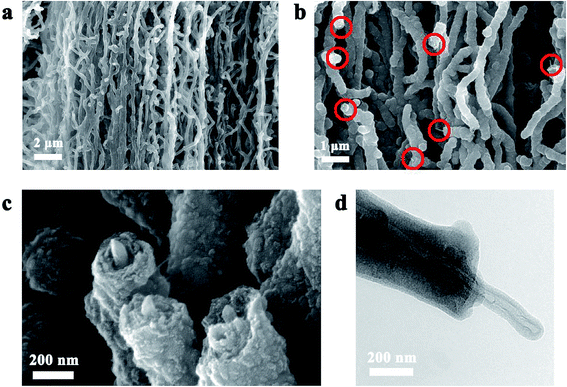 |
| Fig. 8 Poly(vinyl alcohol)-coated multi-walled carbon nanotubes in the composite. Panel (a) vertical alignment of multi-walled carbon nanotubes was retained in the composite mat. Panel (b) morphology at low-magnification. Open circles demonstrated carbon nanotube core tips exposed through the surrounding polymer. Panel (c) close-up of tips showing layers of poly(vinyl alcohol) absorbed around the carbon nanotubes. Panel (d) transmission electron microscopy image of poly(vinyl alcohol) absorption around a carbon nanotube. The figure is adapted with permission from ref. 139. Copyright 2012, Elsevier Ltd. | |
Recent studies have suggested that the chemical nature of the interface may play an important role in determining the mechanical properties of the final composite.79,158 Direct and indirect measurements have been performed for shear strength of the interface, and the results indicated that there exists strong bonding at the interface, which conflicts with other results that poor interfacial bonding and clean pull-out of carbon nanotubes have been reported.144,159 The magnitude of the strength of carbon nanotubes may preclude embedded carbon nanotube tensile failure in large numbers resulting in the dominant failure mode to be carbon nanotube pull-out. In order to obtain the best performance from the nanocomposite materials, it is necessary to achieve an increase in the shear strength of the interface by one order of magnitude or more. It remains unclear how to optimize the interface for mechanical reinforcement at the nanoscale. However, the evidence available suggests that chemical functionalization is an effective approach to increase the strength of the interface.
In addition to experimental measurements, theoretical treatments of carbon nanotube pull-out have attracted significant attention over the past decade.159–165 While experimental science has generated tremendous insights into the nature of the interface, mathematical and computational approaches can complement experimental studies by providing easy manipulation, analysis, and insights at the molecular level.166–171 Due to the inability of conducting experimental measurements at the nanoscale, computational approaches are invaluable in elucidating the mechanism underlying the improvement of the interfacial strength between the carbon nanotube and the polymer matrix. While the first-principles method, based on density-functional theory and pseudopotentials, may provide valuable information about the energetics and structure of polymer nanocomposite systems, this method is limited to smaller molecular systems and shorter times due to its high computational cost. In contrast, molecular dynamics and Monte Carlo simulations can significantly reduce the computational cost, and thus are applicable to larger molecular systems for longer times. As described by Haghighatpanah and Bolton,163 the macroscopic properties of polymer nanocomposites, such as the interfacial shear strength and Young's modulus, can be obtained through molecular dynamics simulations. It can also provide a unique insight into the mechanical performance of these composites at the nanoscale. Frankland and Harik159 modeled a carbon nanotube pulled-out from a polymer matrix to predict the force required.
To further optimize the performance of the interface, it is necessary to understand the mechanism of interfacial adhesion at the molecular level. Liao and Li172 have modeled the characteristics of the interface between carbon nanotubes and a polystyrene matrix by using molecular dynamics simulations and continuum elastic theory. They found that in the absence of atomic bonding of the carbon nanotube surface with the matrix, the interfacial adhesion comes from the interaction between electrostatic and van der Waals forces, deformation induced by these forces, and stress-deformation arising from the mismatch in the coefficients of thermal expansion between the reinforcement and the matrix material. Several other mechanisms have been proposed to describe these interfaces. To understand the factors influencing interfacial adhesion, Lordi and Yao173 investigated the sliding frictional stresses and binding energies between pristine carbon nanotubes and different polymer matrices. They suggested that in comparison with frictional forces and binding energies, a helical conformation of the polymer around the carbon nanotube can significantly improve the strength of the interface. However, further research is still needed to better understand how to optimize the performance of the interface.
5. Strongly coupled carbon nanotube–polymer systems
The degree of interfacial adhesion is important in understanding the nature of the interface, since it plays an important role in determining the properties of carbon nanotube–polymer composites.148 To enhance the load transfer efficiency in these nanocomposite materials, strong interfacial bonding is critical.120 Great efforts have been made to improve the efficiency of interfacial stress transfer.11,22 Unfortunately, there is still lack of understanding of the interfacial bonding between the carbon nanotube and the polymer matrix. Efforts to improve the performance of the interface include: wrapping of polymer matrix molecules around the carbon nanotube,174 as illustrated in Fig. 9, and introducing covalent bonding at the interface.175 In particular, a helical conformation of the polymer around the carbon nanotube can form a strong bond at the interface.173
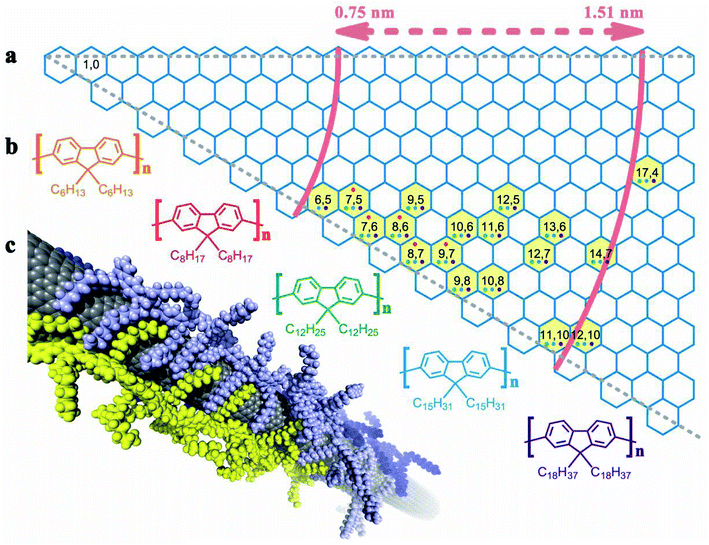 |
| Fig. 9 Panel (a) chirality map of single-walled carbon nanotubes selected by polymer wrapping. In yellow the single-walled carbon nanotubes selected are underlined; the color of the dots inside the hexagons indicates which of the polyfluorene derivatives (color code used for the chemical structures) is able to select the carbon nanotubes. Panel (b) chemical structure of the polyfluorene derivatives used: poly(9,9-di-n-hexylfluorene-2,7-diyl), poly(9,9-di-n-octylfluorene-2,7-diyl), poly(9,9-di-n-dodecylfluorene-2,7-diyl), poly(9,9-di-n-pentadecylfluorene-2,7-diyl), and poly(9,9-di-n-octadecylfluorene-2,7-diyl). Panel (c) structure as obtained by molecular dynamics simulations of three poly(9,9-di-n-dodecylfluorene-2,7-diyl) chains wrapped around a (12,10) carbon nanotube after 10 nanoseconds at constant-pressure in toluene solution. The figure is adapted with permission from ref. 174. Copyright 2013, John Wiley & Sons, Inc. | |
While the load transfer at the interface is certainly less than ideal, strong interfacial bonding is possible in conducting polymer nanocomposite materials.174,176 From mechanics point of view, available literatures to date also offered evidence of strong carbon nanotube–polymer interactions at the interface. Intrinsically conducting polymers or, more popularly, conducting polymers are a sub-class of conjugated polymers. Conducting polymers are a conjugated π-electron system, extending over a large number of recurring monomer units. The conduction mechanism is related to the motion of charged defects within the conjugated framework, and is highly dependent upon the level of doping.177 Typical examples are polyacetylene,177 polyphenylenevinylene,178 and polyaniline.14,179 Great efforts have been made to optimize the physical properties of conducting polymers.177
Multi-walled carbon nanotubes can serve as a conducting filler in a conjugated luminescent polymer, poly(m-phenylenevinylene-co-2,5-dioctyloxy-p-phenylenevinylene),180–182 and polyaniline.14,179,183 It has been demonstrated that the electronic structure of poly(m-phenylenevinylene-co-2,3-dioctoxy-p-phenylenevinylene)184 and other types of conducting polymers is modified by the presence of carbon nanotubes,185,186 suggesting that there is strong coupling between the conjugated π-electron system and the multi-walled carbon nanotube. In a different poly(2,6-pyridinylenevinylene-co-2,5-dioctyloxy-p-phenylenevinylene)-wrapped system,186 it has been suggested that the protonation of the polymer is promoted by the presence of single-walled carbon nanotubes, and the electrical property of the polymer nanocomposite material is also significantly improved. The polymer nanocomposite material containing carbon nanotubes and conjugated polymers is a strongly associating, tightly bound system. The molecular geometry of the polymer nanocomposite material is single or multi helical wrapping of single-walled carbon nanotubes by the polymer.186 On the other hand, wrapping of polymers around carbon nanotubes may be utilized to synthesize polymer nanocomposite materials, since the physical and mechanical properties of polymers can be greatly improved.187–189
Wrapping of polymers around carbon nanotubes, as well as strong bonding at the interface, was reported for a different type of macromolecules, i.e. biopolymers such as peptides and deoxyribonucleic acid (DNA). The interaction at the interface between carbon nanotubes and a specific type of DNA has been exploited for various applications such as drug delivery, gene therapy, sensing, and nanotechnology.190 They also affected the properties of the final composite,191 especially mechanical properties. Uniform dispersion of carbon nanotubes within a DNA matrix can be achieved,192 and their complexes have been found to enable separation of carbon nanotubes190,193 as well as preparation of composites and fibers194–196 and nanometer-scale electronic (nanoelectronic) devices.197,198 An in-depth review of the science and technology of carbon nanotube–DNA composite materials and related applications is available in the literature.190
Dieckmann et al.199 described an amphiphilic peptide specifically designed to disperse single-walled carbon nanotubes and to control the assembly of the amphiphilic peptide-coated carbon nanotubes into a macromolecular structure. It was found that single-walled carbon nanotubes can induce the preferential folding of amphiphilic peptide into a specific configuration, and the peptide–peptide interaction between adjacent peptide-wrapped carbon nanotubes can be utilized to control the self-assembly of the fibers. The concept is demonstrated in Fig. 10. Scanning electron microscopy and transmission electron microscopy images were acquired, and Raman spectroscopy was used to examine the structure of the fibers. The results indicated that the amphiphilic peptide-coated carbon nanotubes were aligned along the axis of the fibers.
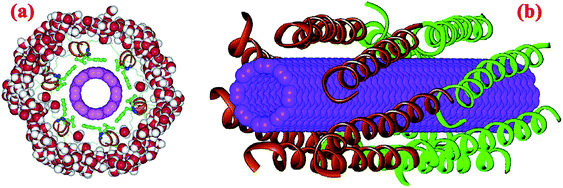 |
| Fig. 10 Model illustrating potential interactions between a synthetic, hydrophilic polypeptide and an individual single-walled carbon nanotube. Panel (a) cross-section view of a carbon nanotube (pink cylinder) wrapped by six peptide helices (one heptad of each shown). The backbone of each peptide is denoted by an orange ribbon, and the Val and Phe side chains packed against the carbon nanotube surface are rendered in green. The 5 Å thick water shell used in the energy refinement of the model is rendered as creatine phosphokinase spheres (red: oxygen, white: hydrogen, green: carbon, blue: nitrogen). Panel (b) view of peptide-wrapped carbon nanotube illustrating the 12 peptide helices used in the model. The head-to-tail alignment of helices in two adjacent layers (orange and green layers) is maintained throughout the molecular dynamics simulation. The unwinding observed at the C-terminus of each helix was manually introduced at the beginning of the molecular dynamics simulation to mimic the distortion observed in the crystal structure of coil-VaLd. The figure is adapted with permission from ref. 199. Copyright 2003, American Chemical Society. | |
To improve the degree of the dispersion of carbon nanotubes, wrapping of polymers around carbon nanotubes was also suggested in additional systems.200,201 Wrapping of water-soluble polymers may lead to screening of the hydrophobic interaction at the interface between the carbon nanotubes and water. A variety of linear water-soluble polymers has been examined, and this approach has been found to be robust and general. The thermodynamic driving force for the wrapping of polymers around carbon nanotubes in an aqueous environment has also been identified.200,201
6. Interfacial interaction improvement techniques
While significant insights into the nature of carbon nanotube–polymer interactions at the interface have been achieved, there are still a number of issues that need to be addressed.202,203 The physical and mechanical properties of the nanocomposites reinforced with carbon tubes is strongly influenced by the characteristics of the interface.140–143 To realize their potential as reinforcement for polymers, it is necessary to optimize the interface.18 Unfortunately, there is a lack of understanding of the characteristics of the interaction at the interface. Further investigations into the relationship between composite properties and interfacial optimization are needed to achieve optimal reinforcement of polymer matrices with carbon nanotubes.
While some important factors influencing properties of the polymer nanocomposites have been identified, there exist reports containing contradictory findings with regard to the effect of carbon nanotubes on a particular property.12 The contradictory findings could be partly due to technical reasons, such as differences in processing conditions and material characteristics. On the other hand, the role of several important factors such as the carbon nanotube curvature204,205 needs to be further determined. These factors may be critical to achieving optimal properties of the composites. However, regardless of the effect of carbon nanotube on the properties of the composites, there is still a gap between experimental results and theoretical predictions due to imperfect dispersion and especially poor load transfer at the interface.204,206 In the case of low carbon nanotube loadings, the experimental data are usually far behind the idealized results predicted by a rule-of-mixtures approach. In the case of high carbon nanotube loadings, the degree of improvement in mechanical properties is somewhat limited by relatively high viscosities of the polymer nanocomposites as well as the resulting void defects.22 The characteristics of the interaction at the interface play an important role in determining the properties of the polymer nanocomposites.18 Moreover, the issue of carbon nanotube dispersion is critical to efficient reinforcement, and lies partly in the interfacial interaction characteristics of the composite. Furthermore, the interfacial interaction properties should be tailored for the desired performance, when designing a carbon nanotube–polymer composite. Finally, to better understand the physical and mechanical behavior of the polymer nanocomposites, it is necessary to explore the characteristics of the interaction at the interface. There has been considerable research in attempting to improve the interfacial interaction. The interfacial interaction can be categorized into two types: non-covalent and covalent interaction.18 The recent advances in the interfacial interaction at the nanometric level is briefly discussed here.
6.1. Non-covalent interaction
It is an effective way to improve the load transfer at the interface through strengthening non-covalent bonding between the carbon nanotube and the polymer matrix by introducing specific interactions such as a CH–π interaction and especially a π–π interaction. Non-covalent interactions can be classified into different types such as van der Waals forces or π–π stacking. There have been a variety of techniques developed for enhancing the non-covalent interaction in carbon nanotube–polymer composites, such as bridging, specific interfacial area, wrapping. These techniques are of particular interest, because they enables one to tailor composite properties while still preserving nearly all of the carbon nanotube's intrinsic properties.
The bridging technique can be utilized to allow a polymer chain interacted with two or more reinforcements simultaneously. The bridging phenomenon is determined by the ratio of the average interface-to-interface distance between the nearest reinforcements to the radius of gyration of long polymer chains.207 As a result, the possibility of bridging phenomenon increases by using higher molecular weight polymers or with increasing the carbon nanotube content. An important issue for load transfer is the interfacial area between filler and polymer, as reported by Cadek et al.208 The specific interfacial area is the interfacial area per unit volume of a carbon nanotube–polymer composite, depending on diameter and loading of the reinforcement as well as the polymer to reinforcement density ratio.207 It has been found that there is a linear dependence of tensile modulus on the interfacial area per unit volume in carbon nanotube–polymer composites.208 Furthermore, as the specific interfacial area increases, the properties of polymer nanocomposite materials will become increasingly dominated by the nature of the interface.32
The non-covalent “wrapping” of polymer chains around a carbon nanotube is an interesting phenomenon that affects the properties of the composites. This wrapping behavior can be utilized to solubilize carbon nanotubes, tune the dispersity of carbon nanotubes, drive assembly mechanisms, and alter the functionalization of the carbon nanotubes.209–212 Consequently, the wrapping mechanism not only helps to improve the dispersion efficiency of carbon nanotubes in polymers, but also results in a stronger interfacial interaction. Wrapping is a general phenomenon occurring at the interface between the carbon nanotube and the polymer matrix, although the physicochemical states of such interfacial interactions are still poorly understood. The driving forces for wrapping are likely to be a combination of interactions due to electrostatics and aromaticity hydrophobic forces, and van der Waals forces.
Experimental evidence for polymer wrapping of carbon nanotubes has been reported.174,209,210 However, it is yet to be understood how non-covalent wrapping of polymers around the surface of carbon nanotubes contributes to the physical and mechanical of the composites. This molecular phenomenon is likely to be governed by the flexibility and affinity of the polymer species for the carbon nanotube. The polymer with a semi-flexible or stiff backbone tends to wrap around a carbon nanotube with a more distinct, helical conformation than that with a flexible backbone.213,214 In contrast, the polymer a flexible backbone with bulky and aromatic side groups prefers intrachain coiling rather than wrapping around a carbon nanotube.215 Fig. 11 shows examples of flexible and stiff backbone polymers interacting with single-walled carbon nanotubes. The chemical composition of a polymer can influence the wrapping mechanism of its chains around a carbon nanotube. For example, aromatic groups along the backbone of the polymer chain prefer to optimize the π–π stacking interaction at the interface and, consequently, dictate the distinct conformation for adsorption. In addition, the presence of aliphatic side groups can weaken the interaction occurred at the interface. Furthermore, the geometric parameters of carbon nanotubes and polymers can significantly affect the wrapping mechanism.207 When the diameter of carbon nanotubes is much smaller than the radius of gyration of polymers, there exists a strong interaction at the interface, thus improving interfacial load transfer and increasing the elastic moduli of the nanocomposite material. Consequently, nanocomposite materials with small diameter carbon nanotubes and high molecular weight polymers may lead to tight wrapping of polymers around a carbon nanotube.
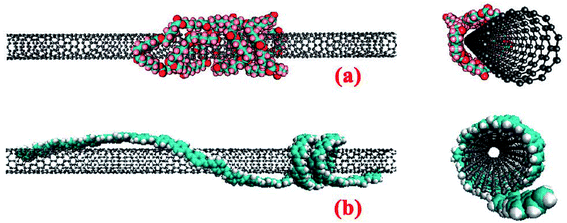 |
| Fig. 11 Molecular dynamics snapshots of polymer chains introduced into a single-walled carbon nanotube. Panel (a) shows flexible backbone poly(caprolactone) interacting with the carbon nanotube at 3200 ps.215 The colors used for the polymer represent the following atoms: carbon is aqua, hydrogen is pink, and oxygen is red. Panel (b) shows stiff backbone poly(para phenylene vinylene) interacting with the carbon nanotube at 2400 ps.213 The colors used for the polymer represent the following atoms: carbon is aqua, and hydrogen is white. The figure is adapted with permission from ref. 213 and 215. Copyright 2010, American Chemical Society. | |
A facile and efficient method was developed by Wang et al.216 to enrich a large quantity of semiconducting single-walled carbon nanotubes through the use of a series of polymers. Molecular dynamics simulations were also performed to understand how to improve the yield and quality of the final composite material. They found that polymer side chains play an important role in determining the selectivity to the final composite. Representative snapshots of the molecular dynamics simulations are shown in Fig. 12. The selectivity toward the desired product slightly increases with increasing the ratio of thiophene to dithiafulvalene units in the polymer backbone. Furthermore, they also fabricated solution-processed thin film transistors with a high on to off ratio.
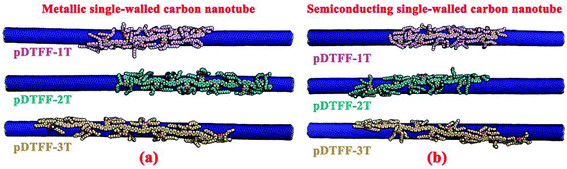 |
| Fig. 12 Representative snapshots of the molecular dynamics simulations performed for (panel (a)) a metallic single-walled carbon nanotube and (panel (b)) a semiconducting single-walled carbon nanotube with pDTFF-1T, pDTFF-2T, and pDTFF-3T polymers. The pDTFF-mT polymer represents poly(dithiafulvalene-fluorene-co-m-thiophene). The figure is adapted with permission from ref. 216. Copyright 2013, American Chemical Society. | |
The non-covalent interaction method is closely related to the physical adsorption and wrapping of polymers around a carbon nanotube. This method will be particularly advantageous for taking advantage of the inherent properties of carbon nanotubes, since the structural integrity of carbon nanotubes is preserved and thus their unique properties are not disrupted. Recent studies have demonstrated that polymer crystallization can improve the non-covalent interaction, which shows great promise for preparing high-performance polymer nanocomposite materials.217,218 A facile, highly effective technique is non-covalent grafting of carbon nanotubes with end-functionalized polymers.219,220 There is a strong non-covalent interaction at the interface by using this technique. This technique is expected to have a number of advantages for the synthesis of high-performance polymer nanocomposite materials. For example, physical and mechanical properties of the final composite can be significantly improved by using this technique, and the dispersibility of carbon nanotubes into a polymer matrix can also be highly increased.
6.2. Covalent interaction
The covalent interaction method involves the attachment of chemical bonds to either the ends or sidewalls of carbon nanotubes. In this context, strong interfacial bonding is established during the creation of covalent chemical bonds between the carbon nanotubes and the polymer matrix. This method can effectively enhance the interaction at the interface, and can easily give rise to higher interfacial shear strength, thus improving the mechanical properties of a polymer nanocomposite material.32 Covalent functionalization also provides an effective way to tailor the interface to achieve optimal performance of the composite materials.221,222 The interfacial adhesion can be greatly improved by using the covalent interaction method, and the load transfer efficiency can also be significantly enhanced. This method can be achieved by using the covalent chemical functionalization of the open-ends or sidewalls of carbon nanotubes. Hirsch,77 Meng et al.,80 and Balasubramanian and Burghard81 reviewed the recent advances in the development of reliable techniques for the covalent chemical functionalization of the open-ends or sidewalls of carbon nanotubes. The techniques discussed in these review articles can further expand the application range of carbon nanotubes. In particular, it is possible to chemically tailor the properties of the surface of carbon nanotubes in order to enable the design of polymer nanocomposite materials for engineering applications.
The covalent interaction method is an effective way to increase the strength of the interface between the carbon nanotube and the polymer matrix by introducing specific functional groups to the surface of carbon nanotubes. The functional groups on the surface of carbon nanotubes should be carefully designed in order to improve the compatibility with the polymer matrix.79,223,224 In situ polymerization is an effective method to improve the compatibility, and to improve the formation of covalent bonds between the functionalized carbon nanotubes and the polymer matrix.225,226 Covalent chemical functionalization of carbon nanotubes has been successfully applied to reactive polymers. Chemical functionalization of the chains of stable and non-reactive polymers such as commercially-available engineering plastics has also been reported by Chang and Liu227 through an ozone-mediated process. Polymer-functionalized carbon nanotubes were prepared to improve the compatibility with the polymer matrix.227 Ozonization of non-reactive polymer chains, instead of carbon nanotubes, was used. The experiments demonstrated the capability of carbon nanotubes functionalized by a matrix polymer as effective fillers in polymer nanocomposite materials. On the other hand, covalent functionalization of carbon nanotubes can also be accomplished through microwave irradiation224,228,229 and plasma enhanced chemical vapor deposition.230
To improve the properties of polymer nanocomposite materials, uniform dispersion of carbon nanotubes within the polymer matrix is a critical issue. Covalent functionalization of carbon nanotubes can improve the dispersion state of carbon nanotubes, and modify the properties at the interface, which eventually leads to the improved performance of polymer nanocomposite materials.231–233 With respect to mechanical properties of the composites, the load transfer efficiency can be significantly enhanced through covalent functionalization, since it is an effective method for tuning the properties at the interface.234 The covalent functionalization of carbon nanotubes leads to a change of carbon hybridization from sp2 to sp3, resulting in a possible partial loss of conjugation, with consequences for electron-acceptor and electron-transport properties. Polarized Raman spectroscopy is a powerful tool used to characterize the degree of the functionalization of carbon nanotubes through an increase in the intensity ratio of D Raman band to G Raman band as well as in the intensity of D′ Raman band.227 The latter is known to be directly influenced by the disorder in carbon nanotubes. Furthermore, thermal gravimetric analysis showed that pristine carbon nanotubes do not show significant weight loss until 850 °C, whereas there is a loss of the mass of functionalized carbon nanotubes prior to this temperature.227 Scanning electron microscope images of the fractured surface of functionalized carbon nanotube–polymer composites give further evidence of strong bonding at the interface.226,232 The representative field emission scanning electron microscope images of the cross-sectional fracture of multi-walled carbon nanotube–nylon 6 composites with the achieved dispersion of carbon nanotubes in the polymer matrix are shown in Fig. 13. Furthermore, transmission electron microscopy images suggested that the outer bundles of multi-walled carbon nanotubes are covered by amorphous polymer layers.224,227 Finally, the covalent interaction between the carbon nanotube and the polymer matrix can significantly affect the properties of polymer nanocomposite materials.235
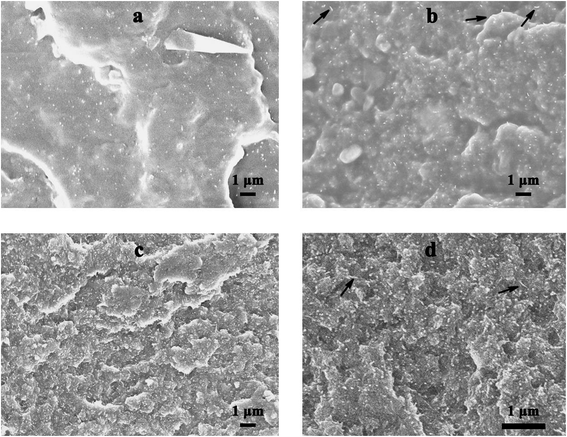 |
| Fig. 13 Field emission scanning electron microscope images of the cross-sectional fracture of multi-walled carbon nanotube–nylon 6 composites: panel (a) PRC10-II, panel (b) PRC10-I, panel (c) PRCS10 and panel (d) PAC10. For more detailed information about the definitions of these composites, the reader is referred to the relevant literature.226 It was clearly observed from panel (b) that the carbon nanotubes were broken, as indicated by arrow, which is of great importance to research and develop methods for the preparation of multi-walled carbon nanotube–reinforced polymer composites. It is interesting to note that a belt like carbon nanotube was observed which interconnected polymer lumps, as indicated by arrow in panel (d). This typical phenomenon also indicated that there was a strong interfacial adhesion between the carbon nanotube and the polymer matrix, and a sufficient load transfer from the polymer matrix to the carbon nanotubes. The figure is adapted with permission from ref. 226. Copyright 2009, Elsevier B.V. | |
Covalent functionalization provides a means for tailoring the interface to achieve optimal performance of the composite materials.236–238 Covalent functionalization can greatly improve the dispersion and interfacial bonding of the carbon nanotubes in a polymer matrix, and thus the route to the composite materials with excellent performance can be realized. The dispersion state of carbon nanotubes can be significantly improved and the bonding at the interface can also be substantially enhanced through covalent functionalization, thus providing a potential method to take full advantage of the remarkable physical and mechanical properties of carbon nanotubes. However, an obvious drawback of this method is the disruption of the bonding of the graphene sheet, which may eventually lead to the degradation of the performance of the composite materials. Covalent functionalization may cause a loss of mechanical and physical properties of the composite materials, since most of these properties are extended π-conjugation-dependent. Since each covalent functionalization site scatters electrons, this method has a profound influence on the electrical properties of the composite materials.
The purification process and other preparation steps should be strictly controlled during covalent functionalization to prevent the introduction of a large amount of defects into carbon nanotubes that may result in the deterioration of the performance of the composite materials.226 The creation of covalent chemical bonds at the interface can enhance the interaction between the functionalized carbon nanotubes and the polymer matrix, and higher interfacial shear strength can be achieved.232 Furthermore, the efficiency of interfacial stress transfer can be significantly improved, especially when covalent and non-covalent functionalization are used simultaneously.239
7. Property improvements
The outstanding properties of carbon nanotubes open up new perspectives for carbon nanotube–reinforced composite materials. The remarkable physical and mechanical properties of carbon nanotubes have attracted intensive attention in recent years, with the development of polymer nanocomposite materials for both functional and structural applications.240–246 The physical and mechanical properties of carbon nanotube–polymer composite materials have been extensively studied. From processing and application points of view, the improvement in mechanical properties is of special interest. The significantly improved electrical conductivity of these composite materials with the addition of a very small amount of carbon nanotubes is very important in many practical applications.247–251 Unfortunately, it is difficult to simultaneously achieve the improvement of several properties of polymer nanocomposite materials, since their properties are dependent upon a multitude of factors.22 Nevertheless, it is possible to simultaneously improve the mechanical and electrical properties of polymer nanocomposite materials, which is the focus of this section.
While great achievements have been made in the field of polymer nanocomposite materials, the ability to efficient translate the exceptional properties of carbon nanotubes into the polymer matrix is handicapped by the lack of the precise knowledge of the properties of polymer nanocomposite materials.29,32 Significant improvement in the properties of these nanocomposite materials through the incorporation of carbon nanotubes has been achieved. Consequently, it is highly desirable to summarize some important properties of carbon nanotube–polymer composite materials in comparison with the same properties of polymer matrices. A brief summary of the several important, physical and mechanical properties presented here serves to exemplify such improvement. The brief summary gives a generalization of the recent results of the physical and mechanical properties of carbon nanotube–polymer composite materials, as well as illustrates the improvement of these properties obtained from both experimental measurements and theoretical predictions.
7.1. Influence factors
The properties of these nanocomposite materials depend upon several factors such as type and amount of impurities in the carbon nanotubes, carbon nanotube purification process, synthetic process used to produce carbon nanotubes, carbon nanotube orientation in the polymer matrix, length, diameter, and aspect ratio of the carbon nanotube objects in the composite. These variations in carbon nanotubes account for the apparent inconsistent results reported in the literature. The given information only about the matrix polymer and the concentration of carbon nanotubes is insufficient. While it is impossible to quantify all of the factors listed above, it is very necessary to provide more accurate and complete information in order to reduce discrepancies between the published results obtained for similar composite materials. It has been suggested that the entire research should be carried out by using the same batch of purified carbon nanotubes in order to clarify the factors influencing the properties of carbon nanotube–polymer composite materials.22
It is important to understand the mechanism underlying the interaction at the interface at the molecular level to improve the properties of carbon nanotube–polymer composite materials. The interaction at the interface can significantly influence the dispersion state of carbon nanotubes, but its effect on the performance of polymer nanocomposite materials is potentially quite complex, depending on the target properties.252,253 It is important to note that the optimal microstructure for one physical property of polymer nanocomposite materials might not be the best microstructure of another physical property. In addition, the importance of the relationship between network structure and physical properties has been highlighted by the research group of Uttandaraman Sundararaj,254–256 and the effect of the geometry of fillers has been also clearly clarified.
Recently, the importance of the synthesis method of carbon nanotubes has also been highlighted by the research group of Uttandaraman Sundararaj.257–260 The electrical conductivity of polymer nanocomposite materials can be controlled by adjusting the nitrogen doping level of carbon nanotubes.257,259 Polyaniline is a conductive polymer, thus enabling a strong interaction with carbon nanotubes. The presence of polyaniline can enhance the capacity of adsorption of carbon nanotubes on the surface of a polymer matrix as well as the degree of their dispersion, thus improving the properties of final nanocomposite materials.257,259 In addition, the catalyst and temperature used for the synthesis of carbon nanotubes may be significant, because they can significantly affect the physical properties of polymer nanocomposite materials.258,260 Consequently, these operating parameters must be carefully designed to improve the performance of final nanocomposite materials.
On the other hand, there is an increasing interest in the development of the polymer blend nanocomposite materials containing carbon nanotubes in order to further improve the physical properties for practical applications.261,262 The addition of a small amount of carbon nanotubes is an effective way to manipulate the morphological characteristics of immiscible polymer blends, thus improving the properties of final nanocomposite materials.263 Although considerable progress has been made in this field,263 there is still a lack of understanding of the mechanism underlying the carbon nanotube induced morphological changes. To improve the properties of final nanocomposite materials, it is necessary to manipulate the microstructure of immiscible polymer blends. Morphology refinement is probably the most common consequence. This effect can be attributed to various factors such as the interfacial localization of carbon nanotubes. Recently, molecular simulations have been performed by the research group of Uttandaraman Sundararaj264 to gain insight into the interaction at the interface between carbon nanotubes and different polymer chains. They have found that the migration of carbon nanotubes between different phases plays an important role in determining the morphological changes of polymer blend nanocomposite materials.264 This finding is of particular importance, as it holds great promise for improving the properties of final nanocomposite materials.
The physical properties of carbon nanotube–polymer composites arise from the respective characteristics of the two components, and from the microstructures produced while fabricating and processing these nanocomposite materials. Therefore, much more efforts should be made to improve the control of the morphology of these polymer nanocomposite materials by using a combination of creativity and practicality. The development of the robust correlation between physical properties and interfacial characteristics will further advance the design of these polymer nanocomposite materials.
7.2. Mechanical properties
The extraordinary mechanical properties, fiber-like structure, high aspect ratio, and low density of carbon nanotubes provide unique opportunities for the development of polymer nanocomposite materials.22 The outstanding potential of carbon nanotubes as reinforcement for polymers has been realized.265–270 The mechanical properties of polymer composite materials can be significantly improved by using carbon nanotubes as a filler. Carbon nanotubes have been widely utilized as a filler to reinforce both thermoset polymers271–274 and thermoplastic polymers.275–280
The thermal properties of polymer composite materials can be moderately improved by using carbon nanotubes as a filler. The improvements in the mechanical and thermal properties of the various carbon nanotube–polymer composite materials reported in the literature are summarized in Table 3, with additional information about the methods used to collect the data. The amount of improvement can serve as a criterion for judging the quality of the interaction at the interface. The tensile strength and the tensile modulus of carbon nanotube–polymer composites are highly dependent upon the loading of carbon nanotubes, the degree of the dispersion of carbon nanotubes, and the orientation and degree of alignment of carbon nanotubes in the polymer matrix. The improvements in tensile strength and tensile modulus can be achieved simultaneously even in the case of a very low loading of carbon nanotubes. The information about the interaction at the interface is also given in Table 3. Spectroscopy techniques are widely used to characterize the interaction. In addition to experimental measurements, molecular simulation methods can also be used to estimate the properties of carbon nanotube–polymer composites. For each of the composite materials listed in Table 3, the details on the degree of the improvement in mechanical and thermal properties are also provided. The mechanical and thermal properties can be improved up to 40 times than those of the polymer matrix. Although there are significant improvements in both tensile strength and tensile modulus as shown in Table 3, there is a decrease in the breaking strength, toughness, and flexibility of carbon nanotube–polymer composites.
Table 3 Improvements in the mechanical and thermal properties of various carbon nanotube–polymer composite materialsa
Reinforcement |
Matrix |
Interaction |
Experiments (modeling) |
Improvements |
Ref. |
Type |
Content (%) |
Type |
Measuring technology |
Approach |
Loading |
Properties |
Pct. |
Pct. (percentage), Ref. (reference), SWCNTs (single-walled carbon nanotubes), Non-cov. (non-covalent functionalization), Cov. func. (covalent functionalization), TEM (transmission electron microscopy), FTIR (Fourier-transform infrared spectroscopy), MD (molecular dynamics), PMMA (poly(methyl methacrylate)), CNTs (carbon nanotubes), WAXD (wide-angle X-ray diffraction), MWCNTs (multi-walled carbon nanotubes), MM (molecular mechanics), PAN (poly(acrylonitrile)), PECVD (plasma enhanced chemical vapor deposition), PmPV (poly(m-phenylenevinylene-co-2,5-dioctyloxy-p-phenylenevinylene)), FESEM (field emission scanning electron microscope), ESEM (environmental scanning electron microscope), ABS (acrylonitrile butadiene styrene), TGA (thermal gravimetric analysis), DFT (discrete Fourier transform), VACNTs (vertically aligned carbon nanotubes), PDMS (polydimethylsiloxane), and AIBN (azobisisobutyronitrile). |
SWCNTs |
— |
Polyethylene |
Cov. func. |
— |
MD |
Pull-out |
Shear strength |
3829 |
175 |
SWCNTs |
28.1–39.1 wt |
Epon 862 epoxy |
Non-cov. |
— |
Mech., Ther. |
Tension |
Storage modulus |
492 |
206 |
SWCNTs |
1 and 2 wt |
PMMA |
Non-cov. wrapping |
Raman |
Mech. |
Tension |
Tensile modulus |
53 |
207 |
CNTs |
30 and 70 wt |
Polyethylene |
Non-cov. in situ polymer |
WAXD |
Mech. |
Tension |
Young's modulus |
300 |
217 |
MWCNTs |
0.2–10 wt |
Polystyrene |
Non-cov. grafting |
Raman |
Mech., Elec. |
Nanoindentation |
Young's modulus |
160 |
219 |
SWCNTs |
0.1–2.6 wt |
Polyurethane |
Cov. func. |
Raman |
Mech., Elec, Ther. |
Tension |
Tensile strength |
50 |
221 |
SWCNTs |
4.1 vol |
PMMA and polyethylene |
Cov. func. |
— |
MD and MM |
Pull-out |
Shear strength |
1000 |
222 |
SWCNTs and graphene |
1 wt |
PMMA and PAN |
Cov. func. |
X-ray diffraction |
Mech., Ther. |
Tension |
Young's modulus |
80 |
223 |
MWCNTs |
0.08–0.32 wt |
Polystyrene |
Cov. (irradiation) |
TEM |
Mech. |
Impact |
Impact strength |
250 |
224 |
MWCNTs |
1 and 1.5 wt |
PMMA |
Cov. func. and in situ polymer |
Raman and FTIR |
Mech., Ther. |
Tension |
Young's modulus |
82 |
225 |
MWCNTs |
10 wt |
Nylon 6 |
Cov. func. |
Raman and FTIR |
Mech., Ther. |
Tension |
Tensile strength |
126 |
226 |
MWCNTs |
1 wt |
PVDF |
Cov. func. |
Raman and FTIR |
Mech., Elec. |
Tension |
Tensile strength |
89 |
227 |
MWCNTs |
1–5 wt |
PMMA |
Cov. (PECVD) |
FTIR |
Mech. |
Tension |
Toughness |
29 |
230 |
MWCNTs |
0.1–3.6 wt |
Polypropylene |
Cov. func. |
Raman and FTIR |
Mech., Elec. |
Tension |
Young's modulus |
66 |
232 |
MWCNTs |
0.34 wt |
Diglycidyl ether bisphenol-A epoxy |
Cov. func. |
— |
Mech. |
Fracture |
Fracture toughness |
84 |
234 |
SWCNTs |
1 wt |
Epoxy |
Cov. func. and non-cov. (wrapping) |
Raman |
Ther. |
Temperature |
Coefficient of thermal expansion |
−52 |
235 |
SWCNTs |
— |
PmPV |
Hybrid (cov. and non-cov.) |
— |
MD |
Pull-out |
Shear strength |
453 |
239 |
MWCNTs |
0.55 wt |
Epoxy |
Non-cov. |
FESEM |
Mech. |
Tension |
Tensile strength |
29.7 |
281 |
SWCNTs |
0.1 and 0.4 wt |
Polypropylene |
Cov. (irradiation) |
ESEM |
Mech., Elec. |
Tension |
Tensile strength |
180 |
282 |
MWCNTs |
0.5–3.0 wt |
Polycarbonate |
Non-cov. grafting |
Raman |
Mech., Elec. |
Tension |
Young's modulus |
30 |
283 |
SWCNTs |
— |
Chitosan |
Non-cov. |
FTIR |
Mech. |
Tension |
Storage modulus |
444 |
284 |
MWCNTs |
1 wt |
Epoxy |
Cov. func. |
FTIR |
Mech., Ther. |
Tension |
Tensile strength |
20 |
285 |
MWCNTs |
10 wt |
ABS |
Cov. func. |
ESEM and TGA |
Mech. |
Tension |
Young's modulus |
107 |
286 |
MWCNTs |
1 wt |
Flax fiber |
Cov. func. |
FTIR |
Mech. |
Pull-out |
Fracture toughness |
31 |
287 |
MWCNTs |
0.1–2 wt |
Nylon 6 |
Non-cov. |
Raman, DFT |
Ther. |
Temperature |
Therm. Conductivity |
78 |
288 |
VACNTs |
10 wt |
PDMS |
Non-cov. |
Raman |
Mech. |
Tension |
Storage modulus |
91 |
289 |
MWCNTs |
1 wt |
AIBN |
Cov. func. |
SEM |
Mech. |
Tension |
Compressive modulus |
1042 |
290 |
MWCNTs |
47 vol |
Polypropylene and polyethylene |
Cov. func. |
Raman and FESEM |
Ther. |
Temperature |
Thermal conductivity |
150.1 |
291 |
SWCNTs |
0.5 wt |
PEI |
Cov. func. |
Raman |
Mech. |
Tension |
Tensile strength |
2700 |
292 |
MWCNTs |
0.5 wt |
PEI |
Cov. func. |
TEM |
Mech. |
Tension |
Young's modulus |
1500 |
293 |
MWCNTs |
1 wt |
Water-borne epoxy |
Non-cov. |
TEM and SEM |
Mech. |
Tension |
Tensile strength |
34 |
294 |
Table 3 provides some meaningful insights into the property improvements for various carbon nanotube–polymer composites. The great potential of carbon nanotubes as reinforcement for polymers has attracted much attention in recent years. However, their potential has not been fully realized, and further research is needed. The mechanical properties of carbon nanotube–polymer composite materials have fallen short of the theoretical predictions from the rule of mixtures. The concentration required for the carbon nanotubes acted as a filler in the polymer matrix is often low in order to take advantage of the inherent properties associated with polymers, e.g., flexibility and transparency. The mechanical reinforcement is highly dependent upon the loading of carbon nanotubes, but the degree of this reinforcement may be limited at high loadings by the high viscosity of the polymer matrix and the resulting void defects.231 Theoretical predictions tend to overestimate the benefits associated with the improvements in physical and mechanical properties. Based on experimental results, the improvements in mechanical and thermal properties are often bounded by a twofold increase and rarely exceed this threshold. Consequently, the full potential of these composite materials has yet to be realized. The gap between the experimental results and predictions arises from the insufficient dispersion of carbon nanotubes and the low load transfer efficiency at the interface.
From the data listed in Table 3, the polyelectrolyte composite films consisting of the carbon nanotube multilayers formed by using the layer-by-layer assembly technique show great promise as lightweight, high strength nanocomposite materials.292,293 Lightweight nanocomposite materials have attracted special attention in recent years. The most impressive mechanical properties of the polyelectrolyte nanocomposite materials containing 50 wt% single-walled carbon nanotubes are their tensile strength and tensile modulus with measured values up to 325 MPa and 11 GPa,292,293 respectively, which are about one order of magnitude higher than those of the polymer matrix. Furthermore, the cross-linking technique can significantly improve the structural integrity of the polyelectrolyte composite films.293 Similarly, the storage modulus of buckypaper–reinforced nanocomposite materials can be greatly enhanced after impregnation with an epoxy matrix.206 Carbon nanotubes as reinforcement for ductile polymer matrices are much more effective. In contrast, as a filler used for brittle polymer matrices, carbon nanotubes do not have ability to significantly improve the mechanical properties of these polymers.
The tensile strength and modulus of polymer nanocomposite materials can be significantly improved by using carbon nanotubes as a filler. However, there is often a reduction in strain at break, indicating a decrease in the flexibility and toughness of the polymer matrix.295 This is a common phenomenon even in commercial nanocomposite materials but might be particularly problematic while trying to modify elastomers for applications such as O-rings, seals, belts, and tires. The result reported by Dyke and Tour296 holds great promise for the fabrication of poly(dimethylsiloxane) nanocomposite materials with functionalized single-walled carbon nanotubes. Both the tensile modulus and strength can be considerably increased in these nanocomposite materials, but the strain at break remains largely unchanged. The functional groups on the sidewalls of carbon nanotube can be designed to improve the compatibility with the polymer matrix. Their fabrication method can be readily extended to a wide range of network-forming polymers and elastomers.
7.3. Electrical properties
The use of carbon nanotubes to modify the electrical properties of polymers has attracted a considerable amount of research interest. Polymer composite materials with highly electrically conductivities have been successfully prepared by using carbon nanotubes as a conducting filler.27,30,202 The presence of a very small amount of carbon nanotubes can significantly improve the electrical conductivity of polymer nanocomposite materials.
Polymer nanocomposite materials containing carbon nanotubes become electrically conductive when the content of the filler is higher than a critical value, known as the “percolation threshold”.297–299 Bauhofer and Kovacs30 reviewed the recent advances in the electrical percolation in carbon nanotube–polymer nanocomposite materials. The percolation threshold is characterized by a sharp jump in electrical conductivity by several orders of magnitude, as shown in Fig. 14. This is due to the formation of a three-dimensional conductive network within the polymer matrix.248
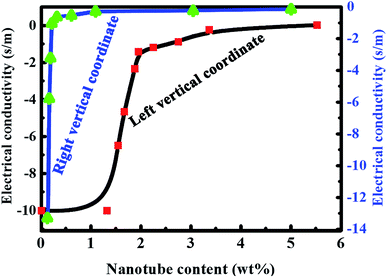 |
| Fig. 14 Electrical conductivity of multi-walled carbon nanotube–polystyrene composites as a function of the loading of carbon nanotubes, showing a typical percolation behavior. The blue line (left vertical coordinate) represents the carbon nanotube prepared by latex technology,336 and the black line (right vertical coordinate) represents the carbon nanotube prepared by tumble mixing and subsequent compression molding at elevated temperatures.327 The figure is adapted with permission from ref. 327 and 336. Copyright 2014, John Wiley & Sons, Inc.; Copyright 2007, Elsevier Ltd. | |
The electrical properties of carbon nanotube–polymer nanocomposites have been widely investigated in order to improve the conductive performance of these materials with a low concentration of the filler. Very low percolation thresholds can be achieved in these nanocomposite materials due to the nanoscale dimension and the large aspect ratio of carbon nanotubes. For single-walled carbon nanotube–polymer nanocomposite materials, the percolation thresholds reported in the literature vary from 0.005 wt% to several wt%. Ultra-low percolation thresholds as low as 0.0025 wt% were reported by Sandler et al.248 for a carbon nanotube–epoxy nanocomposite material. The percolation threshold of carbon nanotube–polymer nanocomposite materials is usually very low due primarily to the large aspect ratio of the filler. Very high electrical conductivities of these nanocomposite materials can be achieved due to the electrical conduction pathways provided by the carbon nanotube network within the polymer matrix.22
The percolation threshold for the electrical conductivity in these composites is closely related to the dispersion state of carbon nanotubes,248,300–303 alignment,304,305 dimensions (e.g., length and diameter) of carbon nanotubes,300,303,306–310 degree of modification of the surface of carbon nanotubes,310–312 type of polymers,313 and composite processing method.300,314–316 The percolation threshold is strongly dependent upon the degree of the dispersion of carbon nanotubes. Additionally, alignment of carbon nanotubes plays an important role in determining the electrical conductivity of the nanocomposite and its percolation threshold. When the uniform alignment is achieved, there is a decrease in the electrical conductivity but an increase in the percolation threshold due to fewer contacts between the carbon nanotubes. Furthermore, the aspect ratio of carbon nanotubes can significantly affect the percolation threshold. Since processing usually reduce the length of carbon nanotubes, it is necessary to develop a process that can preserve the high aspect ratio of carbon nanotubes, thus ensuring the desired electrical conductivity.
The electrical conductivity and the percolation threshold of various carbon nanotube–polymer nanocomposite materials are given in Table 4, with additional information about the carbon nanotube concentration used. The electrical conductivity of these nanocomposite materials can be improved with a very low concentration of carbon nanotubes by several orders of magnitude, which is valuable for their practical applications. A broad range of potential applications are being pursued using these conductive nanocomposite materials, such as electromagnetic interference shielding, electrostatic painting, printable circuit wiring, electrostatic dissipation, and transparent conductive coating.20,27 The data listed in Table 4 suggest that the electrical properties of these nanocomposite materials is highly dependent upon a variety of factors such as the loading of carbon nanotubes. The effect of carbon nanotube loading on the electrical properties of carbon nanotube–polymer nanocomposite materials has been widely studied,327,336 and some examples are provided in Fig. 14.
Table 4 Percolation threshold and electrical conductivity of various carbon nanotube–polymer composites
Polymer type |
Nanotube type |
Percolation threshold (wt%) |
Nanotube content (wt%) |
Maximum conductivity (S m−1) |
Reference |
Epoxy |
Multi-walled nanotubes |
0.0025 |
≤1 |
2 (1 wt%) |
248 |
Poly(vinyl alcohol) |
Multi-walled nanotubes |
10.5 |
≤25 |
9.17 (25 wt%) |
299 |
Polycarbonate |
Functionalized single-walled nanotubes |
0.11 |
≤10 |
4.81 × 102 (7 wt%) |
313 |
Polystyrene |
Functionalized single-walled nanotubes |
0.045 |
≤10 |
20 (10 wt%) |
314 |
Polystyrene |
Multi-walled nanotubes |
0.15–0.2 |
≤2.6 |
103 (2.6 wt%) |
317 |
Acetonitrile |
Multi-walled nanotubes |
0.04–0.05 |
≤1 |
4 × 102 (1 wt%) |
318 |
Cyclohexane |
Multi-walled nanotubes |
0.04–0.05 |
≤1 |
3 × 103 (1 wt%) |
318 |
Poly(methyl methacrylate) |
Multi-walled nanotubes |
0.3 |
≤40 |
3 × 103 (40 wt%) |
319 |
Poly(methyl methacrylate) |
Single-walled nanotubes |
0.17 |
≤10 |
1.7 × 103 (10 wt%) |
320 |
Poly(methyl methacrylate) |
Thionyl chloride-doped single-walled nanotubes |
0.17 |
≤13.5 |
104 (13.5 wt%) |
320 |
Poly(vinyl acetate) |
Single-walled nanotubes |
0.04 |
≤4 |
20 (4 wt%) |
321 |
Polystyrene |
Single-walled nanotubes |
0.27 |
≤2 |
10−3 (1 wt%) |
322 |
Syndiotactic polystyrene |
Modified multi-walled nanotubes |
2–3 |
≤14 |
10−3 (13 wt%) |
323 |
Syndiotactic polystyrene |
Multi-walled nanotubes |
2.5 |
≤10 |
0.135 (3 wt%) |
324 |
Polystyrene |
Single-walled nanotubes |
0.045 |
≤1 |
0.2 (1 wt%) |
325 |
Polystyrene |
Multi-walled nanotubes |
4 |
≤5 |
10−3 (4 wt%) |
326 |
Polystyrene |
Multi-walled nanotubes |
0.05 |
≤5 |
9.9 × 10−2 (0.1 wt%) |
327 |
Polystyrene |
Multi-walled nanotubes |
1.8 |
≤20 |
4 × 10−5 (19 wt%) |
328 |
Polystyrene |
Multi-walled nanotubes |
— |
≤10 |
1.46 × 10−6 (1 wt%) |
329 |
Polystyrene |
Multi-walled nanotubes |
— |
≤20 |
1 (20 wt%) |
330 |
Polystyrene |
Multi-walled nanotubes |
0.08 |
≤1 |
0.148 (0.26 wt%) |
331 |
Polystyrene |
TiO2-nanorod decorated nanotubes |
— |
≤17.2 (vol%) |
2.8 × 10−7 (17.2 vol%) |
332 |
Polystyrene |
Multi-walled nanotubes |
0.54 |
≤1 |
1.5 × 10−3 (0.6 wt%) |
333 |
Polystyrene |
Multi-walled nanotubes |
— |
≤15 |
0.05 (15 wt%) |
334 |
Polystyrene |
Ozone-treated multi-walled nanotubes |
0.8 |
≤3.5 |
10−5 (1.5 wt%) |
335 |
Polystyrene |
Multi-walled nanotubes |
1.5 |
≤5.5 |
1 (5.5 wt%) |
336 |
Polypropylene |
Multi-walled nanotubes |
0.5 |
≤2.5 |
4 × 10−4 (2.5 wt%) |
337 |
Poly(ε-caprolactone) |
Multi-walled nanotubes |
0.3 |
≤1.5 |
3 × 10−3 (1.5 wt%) |
338 |
Polyethylene |
Multi-walled nanotubes |
0.04 |
≤10 |
0.8 (10 wt%) |
339 |
Polycarbonate |
Multi-walled nanotubes |
0.5 |
≤1.5 |
10−4 (1.5 wt%) |
340 |
Epoxy |
Multi-walled nanotubes |
0.05 (vol%) |
≤0.8 (vol%) |
0.02 (0.8 vol%) |
341 |
High density polyethylene |
Multi-walled nanotubes |
0.4 (vol%) |
≤10 (vol%) |
0.02 (10 vol%) |
341 |
Epoxy |
Single-walled nanotubes |
0.3 |
≤0.6 |
0.2 (0.6 wt%) |
342 |
Polymer nanocomposites containing conducting fillers have been extensively investigated for various applications such as electromagnetic interference shielding.343–346 Electromagnetic interference shielding is a rapidly growing application of carbon nanotube–polymer nanocomposite materials.347–350 Polymer nanocomposite materials containing carbon nanotubes are attractive for shielding due to their processability and low density.351 However, currently used nanocomposite materials require a relatively high ratio of filler to polymer loading, which deteriorates the overall mechanical properties caused by the deterioration of intrinsic morphology of the matrix. A possible way to address the above problems, through using a relatively low concentration of carbon nanotubes, incorporates the filler in polymer nanocomposite materials.352–354 A concomitant high aspect ratio and a tunable electrical conductivity may enable the electrical percolation of polymer nanocomposite materials to be achieved at a very low concentration of carbon nanotubes, with a high efficiency of electromagnetic interference shielding being obtained.355,356 Recently, the underlying mechanism responsible for the electromagnetic interference shielding by using carbon nanotube–polymer nanocomposite materials has been illustrated by the research group of Uttandaraman Sundararaj.357,358 Additionally, the effect of nitrogen doping on the efficiency of electromagnetic interference shielding has also been evaluated in detail.359,360 However, the economic costs of carbon nanotubes as well as their clustering within the polymer matrix are critical issues that need to be addressed prior to large scale application.
Fig. 15 shows the electrical conductivity of carbon nanotube–polystyrene nanocomposite materials fabricated under various conditions such as the type of carbon nanotubes, carbon nanotube loading, and preparation method. The overall trend between the electrical conductivity and the carbon nanotube loading is extremely clear. When the carbon nanotube loading increases from low values, the electrical conductivity first increases quickly, up to approximately 0.1 S m−1 with the addition of 5 wt% carbon nanotubes, and then levels off in the range of high loadings. Overall, the excellent electrical properties of carbon nanotubes offer tremendous opportunities for the development of carbon nanotube–reinforced nanocomposite materials.361,362
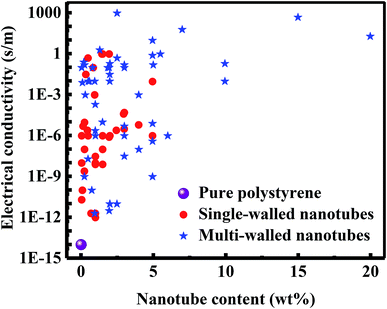 |
| Fig. 15 Electrical conductivities of pure polystyrene, single-walled carbon nanotube–polystyrene, and multi-walled carbon nanotube–polystyrene composites fabricated under different conditions with respect to the content of carbon nanotubes. | |
Chemical functionalization may disrupt the extended π-conjugation of carbon nanotubes, thus decreasing their electrical conductivities. However, it has also been reported that chemical functionalization of carbon nanotubes can improve the electrical properties of polymer nanocomposite materials.363,364 Valentini et al.363 have found that the amine-functionalized carbon nanotubes in an epoxy matrix allows for the migration of intrinsic charges, thus providing a contribution to the overall electrical conductivity. Tamburri et al.364 have found that the extensive functionalization of carbon nanotubes can significantly enhance the current in a conducting polymer matrix. In contrast, the pristine carbon nanotubes have shown only modest improvement in the electrical conductivity of a polymer nanocomposite material. This is because that the disadvantage of the chemical functionalization with respect to the electrical conductivity of carbon nanotubes is far outweighed by the improved dispersion in a polymer matrix enabled by this modification method.
7.4. Thermal properties
Very high thermal conductivities are inherent to carbon nanotubes, exhibiting a physical property known as “ballistic conduction”. Single-walled carbon nanotubes exhibit large phonon mean free path lengths, leading to an extremely high thermal conductivity. Their theoretical value can be up to approximately 6600 W m−1 K−1.365 Recent experiments have demonstrated that the thermal conductivity of an individual single-walled carbon nanotube along its axis is approximately 3500 W m−1 K−1 at room temperature.366 Recently, there is an increasing interest in the thermal properties of nanocomposite materials.367–370 Nanocomposite materials with high thermal conductivities offer great potential for applications in heat sinks, connectors, batteries, light-emitting diode devices, automotive electronic control units, printed circuit boards, electronic assembly and packaging, and other high-performance thermal management systems.371–374 In contrast, nanocomposite materials with high thermal conductivities can be used as thermal insulation. A general, facile, and eco-friendly way has been developed by the research group of Chul B. Park354,375 for the large-scale production of carbon nanotube–polymer nanocomposite materials by using foaming technology for both high-performance thermal insulation and electromagnetic interference shielding applications.
In comparison with the order of magnitude enhancement in electrical conductivity with a very low loading of carbon nanotubes, the polymer nanocomposite materials has found only moderate improvement in thermal conductivity.376,377 The thermal conductivity of these nanocomposite materials is dominated by phonon vibrations. Phonons entering a carbon nanotube–polymer composite are much more likely to travel through the matrix than electrons. This is because the ratio of thermal conductivity between carbon nanotube and polymer is about 104, whereas the ratio of electrical conductivity between the two components is in the range from 1019 to 1015. In addition to the lack of thermal conductivity contrast, the design of polymer nanocomposite materials with high thermal conductivities must also address the very high thermal resistance at the interface between carbon nanotubes, i.e., exceptionally small thermal conductance across the interface. This interfacial thermal resistance arises from the constraints that the energy contained in high-frequency phonon modes within the carbon nanotubes must first be transferred to low-frequency modes through phonon–phonon coupling in order to be exchanged with the surrounding medium.378 For polymer nanocomposite materials with high thermal conductivities, the thermal conductance across the interface between the carbon nanotube and the surrounding polymer matrix is of particular interest. To take full advantage of the intrinsic thermal properties of carbon nanotubes in polymer nanocomposite materials, it is a serious challenge to reduce the thermal resistance at the interface. Gojny et al.379 have suggested that multi-walled carbon nanotubes offer the greatest potential to improve the thermal properties of polymer nanocomposite materials due to their relatively small area of the interface and the existence of shielded internal layers which promote the conduction of phonons as well as minimize the loss of polymer matrix coupling. One promising approach to reduce the very high thermal resistance at the interface is the introduction of covalent bonds between the carbon nanotube and the matrix polymer.380
Nanocomposite materials with high thermal conductivities may be favorable to avoid localized overheating or the formation of hot spots. To improve the thermal properties of polymer nanocomposite materials containing carbon nanotubes, it is important to have a better understanding of the mechanism responsible for the phonon scattering at the interface.381,382 One common challenge is how to effectively improve the thermal conductivity of polymer nanocomposite materials with a low loading of carbon nanotubes. The thermal conductivity of these nanocomposite materials is also highly dependent upon the attributes discussed previously, such the loading, dispersion, alignment, and aspect ratio of carbon nanotubes.383–387 Defects in the structure of carbon nanotubes will lead inevitably to phonon scattering, i.e., a decrease in the thermal conductivity of polymer nanocomposite materials. In fact, any change in the regularity or linearity of the morphological aspect of carbon nanotubes may cause a decrease in their intrinsic thermal conductivity.
The optimization of the interface is another effective way to improve the thermal properties of polymer nanocomposite materials containing carbon nanotubes.388–390 The interface between the carbon nanotube and the surrounding polymer matrix can cause a large thermal resistance, and this is the primary factor of affecting the heat flow in polymer nanocomposite materials.391–394 To achieve excellent thermal properties of these polymer nanocomposite materials, it is crucial to improve the rate of heat transfer across the interface by modulating the interaction between the two components. Recent experiments have demonstrated that the chemical functionalization of carbon nanotubes has both positive and negative effects on the thermal conductivity of polymer nanocomposite materials, i.e., there is an increase in the thermal conductance across the interface and a decrease in the intrinsic thermal conductivity of the filler.395,396 Consequently, it has become a major issue how to benefit from the optimization of the interface through the chemical functionalization of carbon nanotubes without any noticeable loss of the intrinsic thermal properties of the filler. While great achievements have been made in this field,397,398 how to maximize the benefits derived from the intrinsic thermal properties of carbon nanotubes for polymer nanocomposite materials is still a major challenge.
8. Concluding remarks
Remarkable advances have been made in the preparation of carbon nanotube–polymer composites with exceptional mechanical and physical properties. Before these exceptional properties can be fully realized in a macroscopic nanocomposite material by designing the structure at the nanometric level, there is still a large amount of basic research that is needed in this field. To take full advantage of the inherent properties of carbon nanotubes, it is important to understand the characteristics of the interface between the carbon nanotube and the surrounding polymer matrix.
In response to a significant increase in the research activity in the polymer nanocomposites reinforced with carbon nanotubes in the last few years, this paper is an attempt to discuss the topic which is most relevant to the interfacial characteristics of these polymer nanocomposites, as well as review representative journal publications which are closely related to this topic. Special emphasis is placed on the journal articles published since 2010. Knowledge of the characteristics of the interaction at the interface is required to have a thorough understanding of the mechanical and physical behavior of carbon nanotube–polymer composites. The state of research on carbon nanotube–polymer composites for improving mechanical and physical properties has been critically reviewed. The primary focus of this review is on the characteristics of the interface between the carbon nanotube and the polymer matrix, since the performance of these polymer nanocomposites depends critically on the interfacial characteristics. Particular interest is also given to the factors influencing the properties of the polymer nanocomposites reinforced with carbon nanotubes.
Functionalization of carbon nanotubes provides a convenient way to improve the dispersion state of carbon nanotubes as well as to modify the characteristics of the interface, which in turn may improve the properties of the polymer nanocomposite materials, especially mechanical properties. This method for modifying carbon nanotubes will become more prevalent, since significant progress has been made recently in the field of chemical functionalization.
The characteristics of the interface play a crucial role in determining the properties of carbon nanotube–polymer nanocomposite materials. It is important to understand the mechanism responsible for the interfacial interaction at the molecular level to further optimize the design of the interface. Further investigations into the mechanism of the interaction are necessary to provide in-depth understanding of the characteristics of the interface and to evaluate the benefits and disadvantages associated with different functionalization methods.
The properties of carbon nanotube–polymer composites are dependent upon a variety of factors such as the type, dimension, purity, chirality, defect density, and loading of carbon nanotubes, the dispersion state and alignment of carbon nanotubes in the polymer matrix, the degree of modification of the surface of carbon nanotubes, the type of polymer, processing method, and the interfacial adhesion. These factors should be taken into account simultaneously when reporting, comparing, and interpreting the results obtained from experimental measurements and theoretical predictions.
While carbon nanotube–polymer composites offer great potential, they also pose significant challenges. The polymer nanocomposites containing carbon nanotubes have developed as a vibrant area of research for years to come. The application of these nanocomposite materials and the improvement of their properties will be heavily dependent upon how to effectively design and optimize the interface. The substantial progress in the understanding of the interfacial characteristics of polymer nanocomposites containing carbon nanotubes in recent years points toward a bright future.
Conflicts of interest
There are no conflicts to declare.
Acknowledgements
This work was supported by the National Natural Science Foundation of China (No. 51506048) and the Fundamental Research Funds for the Universities of Henan Province (No. NSFRF140119).
References
- S. Iijima, Helical microtubules of graphitic carbon, Nature, 1991, 354(6348), 56–58 CrossRef.
- S. Iijima and T. Ichihashi, Single-shell carbon nanotubes of 1 nm diameter, Nature, 1993, 363(6430), 603–605 CrossRef.
- M. F. L. De Volder, S. H. Tawfick, R. H. Baughman and A. J. Hart, Carbon nanotubes: present and future commercial applications, Science, 2013, 339(6119), 535–539 CrossRef PubMed.
- D. Tasis, N. Tagmatarchis, A. Bianco and M. Prato, Chemistry of carbon nanotubes, Chem. Rev., 2006, 106(3), 1105–1136 CrossRef PubMed.
- F. Hao, P. Dong, J. Zhang, Y. Zhang, P. E. Loya, R. H. Hauge, J. Li, J. Lou and H. Lin, High electrocatalytic activity of vertically aligned single-walled carbon nanotubes towards sulfide redox shuttles, Sci. Rep., 2012, 2(4), 368 CrossRef PubMed.
- Endo Laboratory, Application to the composite material of carbon fiber, https://endomoribu.shinshu-u.ac.jp/research/cnt/composit.html, 2005, accessed July 25, 2018.
- A. Munir, Microwave radar absorbing properties of multiwalled carbon nanotubes polymer composites: a review, Adv. Polym. Technol., 2017, 36(3), 362–370 CrossRef.
- T. Ji, Y. Feng, M. Qin and W. Feng, Thermal conducting properties of aligned carbon nanotubes and their polymer composites, Composites, Part A, 2016, 91(1), 351–369 CrossRef.
- C. Pramanik, D. Nepal, M. Nathanson, J. R. Gissinger, A. Garley, R. J. Berry, A. Davijani, S. Kumar and H. Heinz, Molecular engineering of interphases in polymer/carbon nanotube composites to reach the limits of mechanical performance, Compos. Sci. Technol., 2018 DOI:10.1016/j.compscitech.2018.04.013.
- G. Pal and S. Kumar, Modeling of carbon nanotubes and carbon nanotube-polymer composites, Prog. Aeronaut. Sci., 2016, 80, 33–58 CrossRef.
- R. Andrews and M. C. Weisenberger, Carbon nanotube polymer composites, Curr. Opin. Solid State Mater. Sci., 2004, 8(1), 31–37 CrossRef.
- R. F. Gibson, A review of recent research on mechanics of multifunctional composite materials and structures, Compos. Struct., 2010, 92(12), 2793–2810 CrossRef.
- M. T. Byrne and Y. K. Gun'ko, Recent advances in research on carbon nanotube-polymer composites, Adv. Mater., 2010, 22(15), 1672–1688 CrossRef PubMed.
- S. Bose, R. A. Khare and P. Moldenaers, Assessing the strengths and weaknesses of various types of pre-treatments of carbon nanotubes on the properties of polymer/carbon nanotubes composites: a critical review, Polymer, 2010, 51(5), 975–993 CrossRef.
- P. M. Ajayan, O. Stephan, C. Colliex and D. Trauth, Aligned carbon nanotube arrays formed by cutting a polymer resin-nanotube composite, Science, 1994, 265(5176), 1212–1214 CrossRef PubMed.
- B. P. Grady, Carbon Nanotube-Polymer Composites: Manufacture, Properties, and Applications, John Wiley & Sons, Inc., Hoboken, New Jersey, 2011 Search PubMed.
- D. Tasis, Carbon Nanotube-Polymer Composites, Royal Society of Chemistry, London, 2013 Search PubMed.
- M. Rahmat and P. Hubert, Carbon nanotube-polymer interactions in nanocomposites: a review, Compos. Sci. Technol., 2011, 72(1), 72–84 CrossRef.
- U. A. Joshi, S. C. Sharma and S. P. Harsha, Effect of carbon nanotube orientation on the mechanical properties of nanocomposites, Composites, Part B, 2012, 43(4), 2063–2071 CrossRef.
- M. Kaseem, K. Hamad and Y. G. Ko, Fabrication and materials properties of polystyrene/carbon nanotube (PS/CNT) composites: a review, Eur. Polym. J., 2016, 79, 36–62 CrossRef.
- R. M. F. Fernandes, B. Abreu, B. Claro, M. Buzaglo, O. Regev, I. Furó and E. F. Marques, Dispersing carbon nanotubes with ionic surfactants under controlled conditions: comparisons and insight, Langmuir, 2015, 31(40), 10955–10965 CrossRef PubMed.
- M. Moniruzzaman and K. I. Winey, Polymer nanocomposites containing carbon nanotubes, Macromolecules, 2006, 39(16), 5194–5205 CrossRef.
- P.-C. Ma, N. A. Siddiqui, G. Marom and J.-K. Kim, Dispersion and functionalization of carbon nanotubes for polymer-based nanocomposites: a review, Composites, Part A, 2010, 41(10), 1345–1367 CrossRef.
- B. Mensah, H. G. Kim, J.-H. Lee, S. Arepalli and C. Nah, Carbon nanotube-reinforced elastomeric nanocomposites: a review, Int. J. Smart Nano Mater., 2015, 6(4), 211–238 CrossRef.
- C. Velasco-Santos, A. L. Martinez-Hernandez and V. M. Castano, Carbon nanotube-polymer nanocomposites: the role of interfaces, Compos. Interfaces, 2005, 11(8–9), 567–586 CrossRef.
- A. Kausar, I. Rafique and B. Muhammad, Review of applications of polymer/carbon nanotubes and epoxy/CNT composites, Polym.-Plast. Technol. Eng., 2016, 55(11), 1167–1191 CrossRef.
- Z. Spitalsky, D. Tasis, K. Papagelis and C. Galiotis, Carbon nanotube-polymer composites: chemistry, processing, mechanical and electrical properties, Prog. Polym. Sci., 2010, 35(3), 357–401 CrossRef.
- S. V. Ahir, Y. Y. Huang and E. M. Terentjev, Polymers with aligned carbon nanotubes: active composite materials, Polymer, 2008, 49(18), 3841–3854 CrossRef.
- E. T. Thostenson, Z. Ren and T.-W. Chou, Advances in the science and technology of carbon nanotubes and their composites: a review, Compos. Sci. Technol., 2001, 61(13), 1899–1912 CrossRef.
- W. Bauhofer and J. Z. Kovacs, A review and analysis of electrical percolation in carbon nanotube polymer composites, Compos. Sci. Technol., 2009, 69(10), 1486–1498 CrossRef.
- J. N. Coleman, U. Khan, W. J. Blau and Y. K. Gun'ko, Small but strong: a review of the mechanical properties of carbon nanotube-polymer composites, Carbon, 2006, 44(9), 1624–1652 CrossRef.
- E. T. Thostenson, C. Li and T.-W. Chou, Nanocomposites in context, Compos. Sci. Technol., 2005, 65(3–4), 491–516 CrossRef.
- J. N. Coleman, U. Khan and Y. K. Gun'ko, Mechanical reinforcement of polymers using carbon nanotubes, Adv. Mater., 2006, 18(6), 689–706 CrossRef.
- R. K. Prusty, D. K. Rathore and B. C. Ray, CNT/polymer interface in polymeric composites and its sensitivity study at different environments, Adv. Colloid Interface Sci., 2017, 240, 77–106 CrossRef PubMed.
- Y. Liu and S. Kumar, Polymer/carbon nanotube nano composite fibers – a review, ACS Appl. Mater. Interfaces, 2014, 6(9), 6069–6087 CrossRef PubMed.
- G. Mittal, V. Dhand, K. Y. Rhee, S.-J. Park and W. R. Lee, A review on carbon nanotubes and graphene as fillers in reinforced polymer nanocomposites, J. Ind. Eng. Chem., 2015, 21, 11–25 CrossRef.
- O. Breuer and U. Sundararaj, Big returns from small fibers: a review of polymer/carbon nanotube composites, Polym. Compos., 2004, 25(6), 630–645 CrossRef.
- D. Fong and A. Adronov, Recent developments in the selective dispersion of single-walled carbon nanotubes using conjugated polymers, Chem. Sci., 2017, 8(11), 7292–7305 RSC.
- Y. J. V. Ruban, S. G. Mon and D. V. Roy, Processing and thermal/mechanical studies of unsaturated polyester toughened epoxy composites filled with amine functionalized carbon nanotubes, Int. J. Plast. Technol., 2011, 15(2), 133–149 CrossRef.
- M. Moniruzzaman, F. M. Du, N. Romero and K. I. Winey, Increased flexural modulus and strength in SWNT/epoxy composites by a new fabrication method, Polymer, 2006, 47(1), 293–298 CrossRef.
- A. I. Isayev, R. Kumar and T. M. Lewis, Ultrasound assisted twin screw extrusion of polymer-nanocomposites containing carbon nanotubes, Polymer, 2009, 50(1), 250–260 CrossRef.
- K. Masenelli-Varlot, C. Gauthier, L. Chazeau, F. Dalmas, T. Epicier and J. Y. Cavaillé, Advanced microscopy techniques for a better understanding of the polymer/nanotube composite properties, in Polymer Nanotube Nanocomposites: Synthesis, Properties, and Applications, ed. V. Mittal, John Wiley & Sons, Inc., Hoboken, New Jersey, 2nd edn, 2014 Search PubMed.
- B. Natarajan, N. D. Orloff, R. Ashkar, S. Doshi, K. Twedt, A. Krishnamurthy, C. Davis, A. M. Forster, E. Thostenson, J. Obrzut, R. Sharma and J. A. Liddle, Multiscale metrologies for process optimization of carbon nanotube polymer composites, Carbon, 2016, 108, 381–393 CrossRef.
- M. Tehrani, T. N. B. Etampawala, M. Dadmun and M. A. Hossain, Resolving hierarchical structures in carbon nanotube networks using small- and ultrasmall-angle neutron scattering, J. Phys. Chem. C, 2017, 121(40), 22442–22451 CrossRef.
- D. W. Schaefer and R. S. Justice, How nano are nanocomposites?, Macromolecules, 2007, 40(24), 8501–8517 CrossRef.
- S. K. Kumar, B. C. Benicewicz, R. A. Vaia and K. I. Winey, 50th anniversary perspective: are polymer nanocomposites practical for applications?, Macromolecules, 2017, 50(3), 714–731 CrossRef.
- S. Pegel, T. Villmow and P. Pötschke, Quantification of dispersion and distribution of carbon nanotubes in polymer composites using microscopy techniques, in Polymer-Carbon Nanotube Composites: Preparation, Properties and Applications, ed. T. McNally and P. Pötschke, Woodhead Publishing Limited, Cambridge, UK, 2011 Search PubMed.
- F. Solá, SEM and TEM characterization of polymer CNT nanocomposites, in Polymer Nanotube Nanocomposites: Synthesis, Properties, and Applications, ed. V. Mittal, John Wiley & Sons, Inc., Hoboken, New Jersey, 2nd edn, 2014 Search PubMed.
- A. Kalinin, V. Atepalikhin, O. Pakhomov, A. L. Kholkin and A. Tselev, An atomic force microscopy mode for nondestructive electromechanical studies and its application to diphenylalanine peptide nanotubes, Ultramicroscopy, 2018, 185, 49–54 CrossRef PubMed.
- A. Rafati and P. Gill, Ultrastructural characterizations of DNA nanotubes using scanning tunneling and atomic force microscopes, J. Microsc. Ultrastruct., 2016, 4(1), 1–5 CrossRef PubMed.
- T. Hayashida and K. Umemura, Atomic force microscopy of DNA-wrapped single-walled carbon nanotubes in aqueous solution, Colloids Surf., B, 2016, 143, 526–531 CrossRef PubMed.
- M. Freeley, H. L. Worthy, R. Ahmed, B. Bowen, D. Watkins, J. E. Macdonald, M. Zheng, D. D. Jones and M. Palma, Site-specific one-to-one click coupling of single proteins to individual carbon nanotubes: a single-molecule approach, J. Am. Chem. Soc., 2017, 139(49), 17834–17840 CrossRef PubMed.
- H. Zhang, J. Huang, Y. Wang, R. Liu, X. Huai, J. Jiang and C. Anfuso, Atomic force microscopy for two-dimensional materials: a tutorial review, Opt. Commun., 2018, 406, 3–17 CrossRef.
- S. B. Jagtap, V. D. Patil, K. Suresh, F. Ram, M. S. Mohan, S. S. Rajput, S. Patil, P. G. Shukla and K. Shanmuganathan, Functionalized carbon nanotube reinforced polymer nanocomposite microcapsules with enhanced stiffness, Colloids Surf., A, 2018, 550, 82–89 CrossRef.
- S. Versavaud, G. Régnier, G. Gouadec and M. Vincent, Influence of injection molding on the electrical properties of polyamide 12 filled with multi-walled carbon nanotubes, Polymer, 2014, 55(26), 6811–6818 CrossRef.
- T. H. Nam, K. Goto, Y. Yamaguchi, E. V. A. Premalal, Y. Shimamura, Y. Inoue, K. Naito and S. Ogihara, Effects of CNT diameter on mechanical properties of aligned CNT sheets and composites, Composites, Part A, 2015, 76, 289–298 CrossRef.
- S. Gbordzoe, S. Yarmolenko, Y.-Y. Hsieh, P. K. Adusei, N. T. Alvarez, S. Fialkova and V. Shanov, Three-dimensional texture analysis of aligned carbon nanotube structures, Carbon, 2017, 121, 591–601 CrossRef.
- S. Bellayer, J. W. Gilman, N. Eidelman, S. Bourbigot, X. Flambard, D. M. Fox, H. C. DeLong and P. C. Trulove, Preparation of homogeneously dispersed multiwalled carbon nanotube/polystyrene nanocomposites via melt extrusion using trialkyl imidazolium compatibilizer, Adv. Funct. Mater., 2005, 15(6), 910–916 CrossRef.
- M. Ilčíková, M. Danko, M. Doroshenko, A. Best, M. Mrlík, K. Csomorová, M. Šlouf, D. Chorvát, K. Koynov and J. Mosnáček, Visualization of carbon nanotubes dispersion in composite by using confocal laser scanning microscopy, Eur. Polym. J., 2016, 79, 187–197 CrossRef.
- J. Cheng and H. Pu, Influences of matrix viscosity on alignment of multi-walled carbon nanotubes in one-dimensional confined space, Eur. Polym. J., 2017, 89, 431–439 CrossRef.
- A. Y. Glamazda, A. M. Plokhotnichenko, V. S. Leontiev and V. A. Karachevtsev, DNA-wrapped carbon nanotubes aligned in stretched gelatin films: polarized resonance Raman and absorption spectroscopy study, Phys. E, 2017, 93, 92–96 CrossRef.
- W. A. Chapkin, J. K. Wenderott, P. F. Green and A. I. Taub, Length dependence of electrostatically induced carbon nanotube alignment, Carbon, 2018, 131, 275–282 CrossRef.
- W. A. Chapkin, D. Q. McNerny, M. F. Aldridge, Y. He, W. Wang, J. Kieffer and A. I. Taub, Real-time assessment of carbon nanotube alignment in a polymer matrix under an applied electric field via polarized Raman spectroscopy, Polym. Test., 2016, 56, 29–35 CrossRef.
- J. Cheng, H. Pu and J. Du, A processing method with high efficiency for low density polyethylene nanofibers reinforced by aligned carbon nanotubes via nanolayer coextrusion, Polymer, 2017, 111, 222–228 CrossRef.
- T. Chatterjee, K. Yurekli, V. G. Hadjiev and R. Krishnamoorti, Single-walled carbon nanotube dispersions in poly(ethylene oxide), Adv. Funct. Mater., 2005, 15(11), 1832–1838 CrossRef.
- A. G. Ryabenko, T. V. Dorofeeva and G. I. Zvereva, UV-VIS-NIR spectroscopy study of sensitivity of single-wall carbon nanotubes to chemical processing and van-der-Waals SWNT/SWNT interaction. Verification of the SWNT content measurements by absorption spectroscopy, Carbon, 2004, 42(8–9), 1523–1535 CrossRef.
- A. Casey, G. F. Farrell, M. McNamara, H. J. Byrne and G. Chambers, Interaction of carbon nanotubes with sugar complexes, Synth. Met., 2005, 153(1–3), 357–360 CrossRef.
- N. S. Komarova, A. G. Krivenko, A. G. Ryabenko, A. V. Naumkin, E. V. Stenina and L. N. Sviridova, Spectroscopic characterization of the electrochemical functionalization of single-walled carbon nanotubes in aqueous and organic media, Carbon, 2012, 50(3), 922–931 CrossRef.
- S. N. Kourkouli, A. Siokou, A. A. Stefopoulos, F. Ravani, T. Plocke, M. Müller, J. Maultzsch, C. Thomsen, K. Papagelis and J. K. Kallitsis, Electronic properties of semiconducting polymer-functionalized single wall carbon nanotubes, Macromolecules, 2013, 46(7), 2590–2598 CrossRef.
- R. Saito, G. Dresslhaus and M. S. Dresselhaus, Physical Properties of Carbon Nanotubes, Imperial College Press, London, 1998 Search PubMed.
- J. Loos, A. Alexeev, N. Grossiord, C. E. Koning and O. Regev, Visualization of single-wall carbon nanotube (SWNT) networks in conductive polystyrene nanocomposites by charge contrast imaging, Ultramicroscopy, 2005, 104(2), 160–167 CrossRef PubMed.
- H. J. Barraza, F. Pompeo, E. A. O'Rea and D. E. Resasco, SWNT-filled thermoplastic and elastomeric composites prepared by miniemulsion polymerization, Nano Lett., 2002, 2(8), 797–802 CrossRef.
- M. Rahmat, K. Das and P. Hubert, Interaction stresses in carbon nanotube-polymer nanocomposites, ACS Appl. Mater. Interfaces, 2011, 3(9), 3425–3431 CrossRef PubMed.
- Y. Oh and M. F. Islam, Preformed nanoporous carbon nanotube scaffold-based multifunctional polymer composites, ACS Nano, 2015, 9(4), 4103–4110 CrossRef PubMed.
- T. Vad, J. Wulfhorst, T.-T. Pan, W. Steinmann, S. Dabringhaus, M. Beckers, G. Seide, T. Gries, W. F. C. Sager, M. Heidelmann and T. E. Weirich, Orientation of well-dispersed multiwalled carbon nanotubes in melt-spun polymer fibers and its impact on the formation of the semicrystalline polymer structure: a combined wide-angle X-ray scattering and electron tomography study, Macromolecules, 2013, 46(14), 5604–5613 CrossRef.
- J. Fan, Z. Shi, M. Tian, J. Wang and J. Yin, Unzipped multiwalled carbon nanotube oxide/multiwalled carbon nanotube hybrids for polymer reinforcement, ACS Appl. Mater. Interfaces, 2012, 4(11), 5956–5965 CrossRef PubMed.
- A. Hirsch, Functionalization of single-walled carbon nanotubes, Angew. Chem., Int. Ed., 2002, 41(11), 1853–1859 CrossRef PubMed.
- A. Ezzeddine, Z. Chen, K. S. Schanze and N. M. Khashab, Surface modification of multiwalled carbon nanotubes with cationic conjugated polyelectrolytes: fundamental interactions and intercalation into conductive poly(methyl methacrylate) composites, ACS Appl. Mater. Interfaces, 2015, 7(23), 12903–12913 CrossRef PubMed.
- A. Eitan, K. Jiang, D. Dukes, R. Andrews and L. S. Schadler, Surface modification of multiwalled carbon nanotubes: toward the tailoring of the interface in polymer composites, Chem. Mater., 2003, 15(16), 3198–3201 CrossRef.
- L. Meng, C. Fu and Q. Lu, Advanced technology for functionalization of carbon nanotubes, Prog. Nat. Sci., 2009, 19(7), 801–810 CrossRef.
- K. Balasubramanian and M. Burghard, Chemically functionalized carbon nanotubes, Small, 2005, 1(2), 180–192 CrossRef PubMed.
- X. Peng and S. A. Meguid, Molecular simulations of the influence of defects and functionalization on the shear strength of carbon nanotube-epoxy polymer interfaces, Comput. Mater. Sci., 2017, 126, 204–216 CrossRef.
- J. N. Coleman, M. Cadek, R. Blake, V. Nicolosi, K. P. Ryan, C. Belton, A. Fonseca, J. B. Nagy, Y. K. Gun'ko and W. J. Blau, High performance nanotube-reinforced plastics: Understanding the mechanism of strength increase, Adv. Funct. Mater., 2004, 14(8), 791–798 CrossRef.
- N. Karousis, N. Tagmatarchis and D. Tasis, Current progress on the chemical modification of carbon nanotubes, Chem. Rev., 2010, 110(9), 5366–5397 CrossRef PubMed.
- T. Lorne, M. Jiménez-Ruiz, S. Rols, J.-M. Escudier, J. Rubio-Zuazo, M. Zbiri, A.-M. Galibert, B. Soula and E. Flahaut, Competition between covalent and non-covalent grafting of fluorescein isothiocyanate on double-walled carbon nanotubes: a quantitative approach, Carbon, 2017, 123, 735–743 CrossRef.
- V. Georgakilas, M. Otyepka, A. B. Bourlinos, V. Chandra, N. Kim, K. C. Kemp, P. Hobza, R. Zboril and K. S. Kim, Functionalization of graphene: covalent and non-covalent approaches, derivatives and applications, Chem. Rev., 2012, 112(11), 6156–6214 CrossRef PubMed.
- W. Yuan and M. B. Chan-Park, Covalent cum noncovalent functionalizations of carbon nanotubes for effective reinforcement of a solution cast composite film, ACS Appl. Mater. Interfaces, 2012, 4(4), 2065–2073 CrossRef PubMed.
- H. Mahmoodian, O. Moradi and B. Shariatzadeh, Grafting
chitosan and polyHEMA on carbon nanotubes surfaces: “grafting to” and “grafting from” methods, Int. J. Biol. Macromol., 2014, 63, 92–97 CrossRef PubMed.
- Y.-S. Ye, Y.-N. Chen, J.-S. Wang, J. Rick, Y.-J. Huang, F.-C. Chang and B.-J. Hwang, Versatile grafting approaches to functionalizing individually dispersed graphene nanosheets using RAFT polymerization and click chemistry, Chem. Mater., 2012, 24(15), 2987–2997 CrossRef.
- N. Rubio, H. Au, H. S. Leese, S. Hu, A. J. Clancy and M. S. P. Shaffer, Grafting from versus grafting to approaches for the functionalization of graphene nanoplatelets with poly(methyl methacrylate), Macromolecules, 2017, 50(18), 7070–7079 CrossRef.
- J. J. Ge, D. Zhang, Q. Li, H. Hou, M. J. Graham, L. Dai, F. W. Harris and S. Z. D. Cheng, Multiwalled carbon nanotubes with chemically grafted polyetherimides, J. Am. Chem. Soc., 2005, 127(28), 9984–9985 CrossRef PubMed.
- J. Chattopadhyay, F. de Jesus Cortez, S. Chakraborty, N. K. H. Slater and W. E. Billups, Synthesis of water-soluble pegylated single-walled carbon nanotubes, Chem. Mater., 2006, 18(25), 5864–5868 CrossRef.
- A. J. Clancy, J. M. Serginson, J. L. Greenfield and M. S. P. Shaffer, Systematic comparison of single-walled carbon nanotube/poly(vinyl acetate) graft-to reactions, Polymer, 2017, 133, 263–271 CrossRef.
- B. Zhao, H. Hu, A. Yu, D. Perea and R. C. Haddon, Synthesis and characterization of water soluble single-walled carbon nanotube graft copolymers, J. Am. Chem. Soc., 2005, 127(22), 8197–8203 CrossRef PubMed.
- M. Peng, Z. Liao, Z. Zhu and H. Guo, A simple polymerizable polysoap greatly enhances the grafting efficiency of the “grafting-to” functionalization of multiwalled carbon nanotubes, Macromolecules, 2010, 43(23), 9635–9644 CrossRef.
- H.-S. Kim, B. H. Park, J.-S. Yoon and H.-J. Jin, Nylon 610/functionalized multiwalled carbon nanotubes composites by in situ interfacial polymerization, Mater. Lett., 2007, 61(11–12), 2251–2254 CrossRef.
- H. Kitano, K. Tachimoto and Y. Anraku, Functionalization of single-walled carbon nanotube by the covalent modification with polymer chains, J. Colloid Interface Sci., 2007, 306(1), 28–33 CrossRef PubMed.
- L. Qu, Y. Lin, D. E. Hill, B. Zhou, W. Wang, X. Sun, A. Kitaygorodskiy, M. Suarez, J. W. Connell, L. F. Allard and Y.-P. Sun, Polyimide-functionalized carbon nanotubes: synthesis and dispersion in nanocomposite films, Macromolecules, 2004, 37(16), 6055–6060 CrossRef.
- W. Wang, Y. Lin and Y.-P. Sun, Poly(N-vinyl carbazole)-functionalized single-walled carbon nanotubes: synthesis, characterization, and nanocomposite thin films, Polymer, 2005, 46(20), 8634–8640 CrossRef.
- C. M. Homenick, U. Sivasubramaniam and A. Adronov, Effect of polymer chain length on the solubility of polystyrene grafted single-walled carbon nanotubes in tetrahydrofuran, Polym. Int., 2008, 57(8), 1007–1011 CrossRef.
- R. C. Chadwick, U. Khan, J. N. Coleman and A. Adronov, Polymer grafting to single-walled carbon nanotubes: effect of chain length on solubility, graft density and mechanical properties of macroscopic structures, Small, 2013, 9(4), 552–560 CrossRef PubMed.
- Z. Yao, N. Braidy, G. A. Botton and A. Adronov, Polymerization from the surface of single-walled carbon nanotubes – preparation and characterization of nanocomposites, J. Am. Chem. Soc., 2003, 125(51), 16015–16024 CrossRef PubMed.
- D. Baskaran, J. W. Mays and M. S. Bratcher, Polymer-grafted multiwalled carbon nanotubes through surface-initiated polymerization, Angew. Chem., Int. Ed., 2004, 43(16), 2138–2142 CrossRef PubMed.
- T. Sun, H. Liu, W. Song, X. Wang, L. Jiang, L. Li and D. Zhu, Responsive aligned carbon nanotubes, Angew. Chem., Int. Ed., 2004, 43(35), 4663–4666 CrossRef PubMed.
- S. Qin, D. Qin, W. T. Ford, D. E. Resasco and J. E. Herrera, Polymer brushes on single-walled carbon nanotubes by atom transfer radical polymerization of n-butyl methacrylate, J. Am. Chem. Soc., 2004, 126(1), 170–176 CrossRef PubMed.
- H. Roghani-Mamaqani, V. Haddadi-Asl, M. Ghaderi-Ghahfarrokhi and Z. Sobhkhiz, Reverse atom transfer radical polymerization of methyl methacrylate in the presence of azo-functionalized carbon nanotubes: a grafting from approach, Colloid Polym. Sci., 2014, 292(11), 2971–2981 CrossRef.
- H.-L. Zeng, C. Gao and D.-Y. Yan, Poly(ε-caprolactone)-functionalized carbon nanotubes and their biodegradation properties, Adv. Funct. Mater., 2006, 16(6), 812–818 CrossRef.
- C. M. Homenick, G. Lawson and A. Adronov, Polymer grafting of carbon nanotubes using living free – radical polymerization, Polym. Rev., 2007, 47(2), 265–290 CrossRef.
- G. Pandey and E. T. Thostenson, Carbon nanotube-based multifunctional polymer nanocomposites, Polym. Rev., 2012, 52(3), 355–416 CrossRef.
- L. Cao, W. Yang, J. Yang, C. Wang and S. Fu, Hyperbranched poly(amidoamine)-modified multi-walled carbon nanotubes via grafting-from method, Chem. Lett., 2004, 33(5), 490–491 CrossRef.
- S. Campidelli, C. Sooambar, E. L. Diz, C. Ehli, D. M. Guldi and M. Prato, Dendrimer-functionalized single-wall carbon nanotubes: synthesis, characterization, and photoinduced electron transfer, J. Am. Chem. Soc., 2006, 128(38), 12544–12552 CrossRef PubMed.
- H. Xu, X. Wang, Y. Zhang and S. Liu, Single-step in situ preparation of polymer-grafted multi-walled carbon nanotube composites under 60Co γ-ray irradiation, Chem. Mater., 2006, 18(13), 2929–2934 CrossRef.
- Y.-L. Liu and W.-H. Chen, Modification of multiwall carbon nanotubes with initiators and macroinitiators of atom transfer radical polymerization, Macromolecules, 2007, 40(25), 8881–8886 CrossRef.
- Z. Liu, X. Dai, J. Xu, B. Han, J. Zhang, Y. Wang, Y. Huang and G. Yang, Encapsulation of polystyrene within carbon nanotubes with the aid of supercritical CO2, Carbon, 2004, 42(2), 458–460 CrossRef.
- J. Steinmetz, H.-J. Lee, S. Kwon, D.-S. Lee, C. Goze-Bac, E. Abou-Hamad, H. Kim and Y.-W. Park, Routes to the synthesis of carbon nanotube-polyacetylene composites by Ziegler-Natta polymerization of acetylene inside carbon nanotubes, Curr. Appl. Phys., 2007, 7(1), 39–41 CrossRef.
- J. Steinmetz, S. Kwon, H.-J. Lee, E. Abou-Hamad, R. Almairac, C. Goze-Bac, H. Kim and Y.-W. Park, Polymerization of conducting polymers inside carbon nanotubes, Chem. Phys. Lett., 2006, 431(1–3), 139–144 CrossRef.
- A. V. Bazilevsky, K. Sun, A. L. Yarin and C. M. Megaridis, Selective intercalation of polymers in carbon nanotubes, Langmuir, 2007, 23(14), 7451–7455 CrossRef PubMed.
- K. S. Khare, F. Khabaz and R. Khare, Effect of carbon nanotube functionalization on mechanical and thermal properties of cross-linked epoxy-carbon nanotube nanocomposites: role of strengthening the interfacial interactions, ACS Appl. Mater. Interfaces, 2014, 6(9), 6098–6110 CrossRef PubMed.
- S. B. Kadambi, K. Pramoda, U. Ramamurty and C. N. R. Rao, Carbon-nanohorn-reinforced polymer matrix composites: synergetic benefits in mechanical properties, ACS Appl. Mater. Interfaces, 2015, 7(31), 17016–17022 CrossRef PubMed.
- E. Roumeli, D. G. Papageorgiou, V. Tsanaktsis, Z. Terzopoulou, K. Chrissafis, A. Avgeropoulos and D. N. Bikiaris, Amino-functionalized multiwalled carbon nanotubes lead to successful ring-opening polymerization of poly(ε-caprolactone): enhanced interfacial bonding and optimized mechanical properties, ACS Appl. Mater. Interfaces, 2015, 7(21), 11683–11694 CrossRef PubMed.
- G. Keledi, J. Hári and B. Pukánszky, Polymer nanocomposites: structure, interaction, and functionality, Nanoscale, 2012, 4(6), 1919–1938 RSC.
- M. Wong, M. Paramsothy, X. J. Xu, Y. Ren, S. Li and K. Liao, Physical interactions at carbon nanotube-polymer interface, Polymer, 2003, 44(25), 7757–7764 CrossRef.
- J. Chen, X. Cui, Y. Zhu, W. Jiang and K. Sui, Design of superior conductive polymer composite with precisely controlling carbon nanotubes at the interface of a co-continuous polymer blend via a balance of π-π interactions and dipole-dipole interactions, Carbon, 2017, 114, 441–448 CrossRef.
- Q. L. Xiong and S. A. Meguid, Atomistic investigation of the interfacial mechanical characteristics of carbon nanotube reinforced epoxy composite, Eur. Polym. J., 2015, 69, 1–15 CrossRef.
- T. Tsafack, J. M. Alred, K. E. Wise, B. Jensen, E. Siochi and B. I. Yakobson, Exploring the interface between single-walled carbon nanotubes and epoxy resin, Carbon, 2016, 105, 600–606 CrossRef.
- J. M. Wernik, B. J. Cornwell-Mott and S. A. Meguid, Determination of the interfacial properties of carbon nanotube reinforced polymer composites using atomistic-based continuum model, Int. J. Solids Struct., 2012, 49(13), 1852–1863 CrossRef.
- S. Chopra, K. A. Deshmukh and D. Peshwe, Theoretical prediction of interfacial properties of PBT/CNT nanocomposites and its experimental evaluation, Mech. Mater., 2017, 109, 11–17 CrossRef.
- M. Nie, D. M. Kalyon, K. Pochiraju and F. T. Fisher, A controllable way to measure the interfacial strength between carbon nanotube and polymer using a nanobridge structure, Carbon, 2017, 116, 510–517 CrossRef.
- M. Naraghi, G. H. Bratzel, T. Filleter, Z. An, X. Wei, S. T. Nguyen, M. J. Buehler and H. D. Espinosa, Atomistic Investigation of load transfer between DWNT bundles “crosslinked” by PMMA oligomers, Adv. Funct. Mater., 2013, 23(15), 1883–1892 CrossRef.
- M. Q. Tran, J. T. Cabral, M. S. P. Shaffer and A. Bismarck, Direct measurement of the wetting behavior of individual carbon nanotubes by polymer melts: the key to carbon nanotube-polymer composites, Nano Lett., 2008, 8(9), 2744–2750 CrossRef PubMed.
- L. Liu, A. H. Barber, S. Nuriel and H. D. Wagner, Mechanical properties of functionalized single-walled carbon-nanotube/poly(vinyl alcohol) nanocomposites, Adv. Funct. Mater., 2005, 15(6), 975–980 CrossRef.
- M. Nie, D. M. Kalyon and F. T. Fisher, Interfacial load transfer in polymer/carbon nanotube nanocomposites with a nanohybrid shish kebab modification, ACS Appl. Mater. Interfaces, 2014, 6(17), 14886–14893 CrossRef PubMed.
- M. Wang, K. P. Pramoda and S. H. Goh, Enhancement of interfacial adhesion and dynamic mechanical properties of poly(methyl methacrylate)/multiwalled carbon nanotube composites with amine-terminated poly(ethylene oxide), Carbon, 2006, 44(4), 613–617 CrossRef.
- E. Y. Choi, L. W. Choi and C. K. Kim, Noncovalent functionalization of multi-walled carbon nanotubes with hydroxyl group-containing pyrene derivatives for their composites with polycarbonate, Carbon, 2015, 95, 91–99 CrossRef.
- L. Cao, Y. Wang, P. Dong, S. Vinod, J. T. Tijerina, P. M. Ajayan, Z. Xu and J. Lou, Interphase induced dynamic self-stiffening in graphene-based polydimethylsiloxane nanocomposites, Small, 2016, 12(27), 3723–3731 CrossRef PubMed.
- X. Chen, L. Zhang, M. Zheng, C. Park, X. Wang and C. Ke, Quantitative
nanomechanical characterization of the van der Waals interfaces between carbon nanotubes and epoxy, Carbon, 2015, 82, 214–228 CrossRef.
- F. Liu, N. Hu, H. Ning, S. Atobe, C. Yan, Y. Liu, L. Wu, X. Liu, S. Fu, C. Xu, Y. Li, J. Zhang, Y. Wang and W. Li, Investigation on the interfacial mechanical properties of hybrid graphene-carbon nanotube/polymer nanocomposites, Carbon, 2017, 115, 694–700 CrossRef.
- B. A. Newcomb, H. G. Chae, L. Thomson, J. Luo, J.-B. Baek and S. Kumar, Reinforcement efficiency of carbon nanotubes and their effect on crystal-crystal slip in poly(ether ketone)/carbon nanotube composite fibers, Compos. Sci. Technol., 2017, 147, 116–125 CrossRef.
- K. G. Dassios and C. Galiotis, Polymer-nanotube interaction in MWCNT/poly(vinyl alcohol) composite mats, Carbon, 2012, 50(11), 4291–4294 CrossRef.
- M. Chen and Z. Lu, A comparative study of the load transfer mechanisms of the carbon nanotube reinforced polymer composites with interfacial crystallization, Composites, Part B, 2015, 79, 114–123 CrossRef.
- F. Yazdandoost, R. Mirzaeifar, Z. Qin and M. J. Buehler, Multiscale mechanics of the lateral pressure effect on enhancing the load transfer between polymer coated CNTs, Nanoscale, 2017, 9(17), 5565–5576 RSC.
- S. Yang, J. Choi and M. Cho, Intrinsic defect-induced tailoring of interfacial shear strength in CNT/polymer nanocomposites, Compos. Struct., 2015, 127, 108–119 CrossRef.
- N. Ning, D. Cheng, J. Yang, L. Liu, M. Tian, Y. Wu, W. Wang, L. Zhang and Y. Lu, New insight on the interfacial interaction between multiwalled carbon nanotubes and elastomers, Compos. Sci. Technol., 2017, 142, 214–220 CrossRef.
- J. B. Bai, Evidence of the reinforcement role of chemical vapour deposition multi-walled carbon nanotubes in a polymer matrix, Carbon, 2003, 41(6), 1325–1328 CrossRef.
- J. Cha, G. H. Jun, J. K. Park, J. C. Kim, H. J. Ryu and S. H. Hong, Improvement of modulus, strength and fracture toughness of CNT/Epoxy nanocomposites through the functionalization of carbon nanotubes, Composites, Part B, 2017, 129, 169–179 CrossRef.
- A. K.-T. Lau and D. Hui, The revolutionary creation of new advanced materials-carbon nanotube composites, Composites, Part B, 2002, 33(4), 263–277 CrossRef.
- A. H. Barber, S. R. Cohen and H. D. Wagner, Measurement of carbon nanotube-polymer interfacial strength, Appl. Phys. Lett., 2003, 82(23), 4140–4142 CrossRef.
- A. H. Barber, S. R. Cohen, S. Kenig and H. D. Wagner, Interfacial fracture energy measurements for multi-walled carbon nanotubes pulled from a polymer matrix, Compos. Sci. Technol., 2004, 64(15), 2283–2289 CrossRef.
- A. H. Barber, S. R. Cohen, A. Eitan, L. S. Schadler and H. D. Wagner, Fracture transitions at a carbon-nanotube/polymer interface, Adv. Mater., 2006, 18(1), 83–87 CrossRef.
- W. Ding, L. Calabri, K. M. Kohlhaas, X. Chen, D. A. Dikin and R. S. Ruoff, Modulus, fracture strength, and brittle vs. plastic response of the outer shell of arc-grown multi-walled carbon nanotubes, Exp. Mech., 2007, 47(1), 25–36 CrossRef.
- M. P. Manoharan, A. Sharma, A. V. Desai, M. A. Haque, C. E. Bakis and K. W. Wang, The interfacial strength of carbon nanofiber epoxy composite using single fiber pullout experiments, Nanotechnology, 2009, 20(29), 295701 CrossRef PubMed.
- D. Roy, S. Bhattacharyya, A. Rachamim, A. Plati and M.-L. Saboungi, Measurement of interfacial shear strength in single wall carbon nanotubes reinforced composite using Raman spectroscopy, J. Appl. Phys., 2010, 107(4), 043501 CrossRef.
- T. Tsuda, T. Ogasawara, F. Deng and N. Takeda, Direct measurements of interfacial shear strength of multi-walled carbon nanotube/PEEK composite using a nano-pullout method, Compos. Sci. Technol., 2011, 71(10), 1295–1300 CrossRef.
- Y. Ganesan, C. Peng, Y. Lu, P. E. Loya, P. Moloney, E. Barrera, B. I. Yakobson, J. M. Tour, R. Ballarini and J. Lou, Interface toughness of carbon nanotube reinforced epoxy composites, ACS Appl. Mater. Interfaces, 2011, 3(2), 129–134 CrossRef PubMed.
- Q. Xu, Y. Yao, Z. Ma and Z. Xia, Measurement of interfacial energy and friction between carbon nanotubes and polymer matrix by a micro-pullout test, Sci. Adv. Mater., 2012, 4(8), 888–892 CrossRef.
- S. Yashiro, Y. Sakaida, Y. Shimamura and Y. Inoue, Evaluation of interfacial shear stress between multi-walled carbon nanotubes and epoxy based on strain distribution measurement using Raman spectroscopy, Composites, Part A, 2016, 85, 192–198 CrossRef.
- W. Ding, A. Eitan, F. T. Fisher, X. Chen, D. A. Dikin, R. Andrews, L. C. Brinson, L. S. Schadler and R. S. Ruoff, Direct observation of polymer sheathing in carbon nanotube-polycarbonate composites, Nano Lett., 2003, 3(11), 1593–1597 CrossRef.
- J. Bae, J. Jang and S.-H. Yoon, Cure behavior of the liquid-crystalline epoxy/carbon nanotube system and the effect of surface treatment of carbon fillers on cure reaction, Macromol. Chem. Phys., 2002, 203(15), 2196–2204 CrossRef.
- S. J. V. Frankland and V. M. Harik, Analysis of carbon nanotube pull-out from a polymer matrix, Surf. Sci., 2003, 525(1–3), L103–L108 CrossRef.
- J. Gou, B. Minaie, B. Wang, Z. Liang and C. Zhang, Computational and experimental study of interfacial bonding of single-walled nanotube reinforced composites, Comput. Mater. Sci., 2004, 31(3–4), 225–236 CrossRef.
- S. C. Chowdhury and T. Okabe, Computer simulation of carbon nanotube pull-out from polymer by the molecular dynamics method, Composites, Part A, 2007, 38(3), 747–754 CrossRef.
- Y. Li, Y. Liu, X. Peng, C. Yan, S. Liu and N. Hu, Pull-out simulations on interfacial properties of carbon nanotube-reinforced polymer nanocomposites, Comput. Mater. Sci., 2011, 50(6), 1854–1860 CrossRef.
- S. Haghighatpanah and K. Bolton, Molecular-level computational studies of single wall carbon nanotube-polyethylene composites, Comput. Mater. Sci., 2013, 69, 443–454 CrossRef.
- B. Coto, I. Antia, J. Barriga, M. Blanco and J.-R. Sarasua, Influence of the geometrical properties of the carbon nanotubes on the interfacial behavior of epoxy/CNT composites: a molecular modelling approach, Comput. Mater. Sci., 2013, 79, 99–104 CrossRef.
- R. Rafiee and M. Mahdavi, Characterizing nanotube-polymer interaction using molecular dynamics simulation, Comput. Mater. Sci., 2016, 112(Part A), 356–363 CrossRef.
- Y. Hu and J. L. Ding, Effects of morphologies of carbon nanofillers on the interfacial and deformation behavior of polymer nanocomposites – a molecular dynamics study, Carbon, 2016, 107, 510–524 CrossRef.
- R. Chawla and S. Sharma, Molecular dynamics simulation of carbon nanotube pull-out from polyethylene matrix, Compos. Sci. Technol., 2017, 144, 169–177 CrossRef.
- A. R. Aliana and S. A. Meguid, Molecular dynamics simulations of the effect of waviness and agglomeration of CNTs on interface strength of thermoset nanocomposites, Phys. Chem. Chem. Phys., 2017, 19(6), 4426–4434 RSC.
- H.-L. Ma, K.-T. Lau, D. Hui, S.-Q. Shi and C.-K. Poon, Theoretical analysis on the pullout behavior of carbon nanotube at cryogenic environment with the consideration of thermal residual stress, Composites, Part B, 2017, 128, 67–75 CrossRef.
- Y. Chandra, F. Scarpa, S. Adhikari, J. Zhang, E. I. S. Flores and H.-X. Peng, Pullout strength of graphene and carbon nanotube/epoxy composites, Composites, Part B, 2016, 102, 1–8 CrossRef.
- K. Sharma, K. S. Kaushalyayan and M. Shukla, Pull-out simulations of interfacial properties of amine functionalized multi-walled carbon nanotube epoxy composites, Comput. Mater. Sci., 2015, 99, 232–241 CrossRef.
- K. Liao and S. Li, Interfacial characteristics of a carbon nanotube-polystyrene composite system, Appl. Phys. Lett., 2001, 79(25), 4225–4227 CrossRef.
- V. Lordi and N. Yao, Molecular mechanics of binding in carbon-nanotube-polymer composites, J. Mater. Res., 2000, 15(12), 2770–2779 CrossRef.
- W. Gomulya, G. D. Costanzo, E. J. F. de Carvalho, S. Z. Bisri, V. Derenskyi, M. Fritsch, N. Fröhlich, S. Allard, P. Gordiichuk, A. Herrmann, S. J. Marrink, M. C. dos Santos, U. Scherf and M. A. Loi, Semiconducting single-walled carbon nanotubes on demand by polymer wrapping, Adv. Mater., 2013, 25(21), 2948–2956 CrossRef PubMed.
- C. J. An, Y. C. Lee, Y. H. Kang and S. Y. Cho, Improved interaction between semiconducting polymer and carbon nanotubes in thermoelectric composites through covalent grafting, Carbon, 2017, 124, 662–668 CrossRef.
- I. Szleifer and R. Yerushalmi-Rozen, Polymers and carbon nanotubes-dimensionality, interactions and nanotechnology, Polymer, 2005, 46(19), 7803–7818 CrossRef.
- J. Z. Sun, A. Qin and B. Z. Tang, Functional polyacetylenes: hybrids with carbon nanotubes, Polym. Chem., 2013, 4(2), 211–223 RSC.
- J. H. Burroughes, D. D. C. Bradley, A. R. Brown, R. N. Marks, K. Mackay, R. H. Friend, P. L. Burns and A. B. Holmes, Light-emitting diodes based on conjugated polymers, Nature, 1990, 347(6293), 539–541 CrossRef.
- T. Farrell, K. Wang, C.-W. Lin and R. B. Kaner, Organic dispersion of polyaniline and single-walled carbon nanotubes and polyblends with poly(methyl methacrylate), Polymer, 2017, 129, 1–4 CrossRef.
- W. Yi, A. Malkovskiy, Q. Chu, A. P. Sokolov, M. L. Colon, M. Meador and Y. Pang, Wrapping of single-walled carbon nanotubes by a π-conjugated polymer: the role of polymer conformation-controlled size selectivity, J. Phys. Chem. B, 2008, 112(39), 12263–12269 CrossRef PubMed.
- A. Frikha, S. Zghal and F. Dammak, Finite rotation three and four nodes shell elements for functionally graded carbon nanotubes-reinforced thin composite shells analysis, Comput. Methods Appl. Mech. Eng., 2018, 329, 289–311 CrossRef.
- S. Zghal, A. Frikha and F. Dammak, Static analysis of functionally graded carbon nanotube-reinforced plate and shell structures, Compos. Struct., 2017, 176, 1107–1123 CrossRef.
- W. Zhao, Y. Li, S. Wu, D. Wang, X. Zhao, F. Xu, M. Zou, H. Zhang, X. He and A. Cao, Highly stable carbon nanotube/polyaniline porous network for multifunctional applications, ACS Appl. Mater. Interfaces, 2016, 8(49), 34027–34033 CrossRef PubMed.
- A. B. Dalton, W. J. Blau, G. Chambers, J. N. Coleman, K. Henderson, S. Lefrant, B. McCarthy, C. Stephan and H. J. Byrne, A functional conjugated polymer to process, purify and selectively interact with single wall carbon nanotubes, Synth. Met., 2001, 121(1–3), 1217–1218 CrossRef.
- S. Meer, A. Kausar and T. Iqbal, Trends in conducting polymer and hybrids of conducting polymer/carbon nanotube: a review, Polym.-Plast. Technol. Eng., 2016, 55(13), 1416–1440 CrossRef.
- D. W. Steuerman, A. Star, R. Narizzano, H. Choi, R. S. Ries, C. Nicolini, J. F. Stoddart and J. R. Heath, Interactions between conjugated polymers and single-walled carbon nanotubes, J. Phys. Chem. B, 2002, 106(12), 3124–3130 CrossRef.
- J. H. Rouse, Polymer-assisted dispersion of single-walled carbon nanotubes in alcohols and applicability toward carbon nanotube sol-gel composite formation, Langmuir, 2005, 21(3), 1055–1061 CrossRef PubMed.
- K. Rajalakshmi and S. A. John, Functionalized multiwalled carbon nanotubes-nanostructured conducting polymer composite modified electrode for the sensitive determination of uricase inhibitor, Electrochim. Acta, 2015, 173, 506–514 CrossRef.
- C.-E. Zhao, J. Wu, S. Kjelleberg, J. S. C. Loo and Q. Zhang, Employing a flexible and low-cost polypyrrole nanotube membrane as an anode to enhance current generation in microbial fuel cells, Small, 2015, 11(28), 3440–3443 CrossRef PubMed.
- H. Sun, J. Ren and X. Qu, Carbon nanomaterials and DNA: From molecular recognition to applications, Acc. Chem. Res., 2016, 49(3), 461–470 CrossRef PubMed.
- J. McMorrow, M. Freeley and M. Palma, DNA-wrapped single-walled carbon nanotube assemblies, Chem. Phys. Lett., 2017, 56(18), 5302–5308 Search PubMed.
- D. Pramanik and P. K. Maiti, DNA-assisted dispersion of carbon nanotubes and comparison with other dispersing agents, ACS Appl. Mater. Interfaces, 2017, 9(40), 35287–35296 CrossRef PubMed.
- G. Ao, J. K. Streit, J. A. Fagan and M. Zheng, Differentiating left- and right-handed carbon nanotubes by DNA, J. Am. Chem. Soc., 2016, 138(51), 16677–16685 CrossRef PubMed.
- H. Joshi, A. Kaushik, N. C. Seeman and P. K. Maiti, Nanoscale structure and elasticity of pillared DNA nanotubes, ACS Nano, 2016, 10(8), 7780–7791 CrossRef PubMed.
- T. D. Jorgenson, A. M. Mohammed, D. K. Agrawal and R. Schulman, Self-assembly of hierarchical DNA nanotube architectures with well-defined geometries, ACS Nano, 2017, 11(2), 1927–1936 CrossRef PubMed.
- A. M. Mohammed, L. Velazquez, A. Chisenhall, D. Schiffels, D. K. Fygenson and R. Schulman, Self-assembly of precisely defined DNA nanotube superstructures using DNA origami seeds, Nanoscale, 2017, 9(2), 522–526 RSC.
- R. Rastogi, N. Dhindsa, C. R. Suri, B. D. Pant, S. K. Tripathi, I. Kaur and L. M. Bharadwaj, Interfacing of DNA with carbon nanotubes for nanodevice applications, Mater. Chem. Phys., 2012, 135(2–3), 268–276 CrossRef.
- Y. Chen, K. Qu, C. Zhao, L. Wu, J. Ren, J. Wang and X. Qu, Insights into the biomedical effects of carboxylated single-wall carbon nanotubes on telomerase and telomeres, Nat. Commun., 2012, 3(3), 1074 CrossRef PubMed.
- G. R. Dieckmann, A. B. Dalton, P. A. Johnson, J. Razal, J. Chen, G. M. Giordano, E. Muñoz, I. H. Musselman, R. H. Baughman and R. K. Draper, Controlled assembly of carbon nanotubes by designed amphiphilic peptide helices, J. Am. Chem. Soc., 2003, 125(7), 1770–1777 CrossRef PubMed.
- M. J. O'Connell, P. Boul, L. M. Ericson, C. Huffman, Y. Wang, E. Haroz, C. Kuper, J. Tour, K. D. Ausman and R. E. Smalley, Reversible water-solubilization of single-walled carbon nanotubes by polymer wrapping, Chem. Phys. Lett., 2001, 342(3–4), 265–271 CrossRef.
- A. Star, D. W. Steuerman, J. R. Heath and J. F. Stoddart, Starched carbon nanotubes, Angew. Chem., Int. Ed., 2002, 41(14), 2508–2512 CrossRef PubMed.
- N. G. Sahoo, S. Rana, J. W. Cho, L. Li and S. H. Chan, Polymer nanocomposites based on functionalized carbon nanotubes, Prog. Polym. Sci., 2010, 35(7), 837–867 CrossRef.
- S. I. Yengejeh, S. A. Kazemi and A. Öchsner, Carbon nanotubes as reinforcement in composites: a review of the analytical, numerical and experimental approaches, Comput. Mater. Sci., 2017, 136, 85–101 CrossRef.
- F. T. Fisher, R. D. Bradshaw and L. C. Brinson, Fiber waviness in nanotube-reinforced polymer composites – I: modulus predictions using effective nanotube properties, Compos. Sci. Technol., 2003, 63(11), 1689–1703 CrossRef.
- R. D. Bradshaw, F. T. Fisher and L. C. Brinson, Fiber waviness in nanotube-reinforced polymer composites – II: modeling via numerical approximation of the dilute strain concentration tensor, Compos. Sci. Technol., 2003, 63(11), 1705–1722 CrossRef.
- Z. Wang, Z. Liang, B. Wang, C. Zhang and L. Kramer, Processing and property investigation of single-walled carbon nanotube (SWNT) buckypaper/epoxy resin matrix nanocomposites, Composites, Part A, 2004, 35(10), 1225–1232 CrossRef.
- M. Mu and K. I. Winey, Improved load transfer in nanotube-polymer composites with increased polymer molecular weight, J. Phys. Chem. C, 2007, 111(48), 17923–17927 CrossRef.
- M. Cadek, J. N. Coleman, K. P. Ryan, V. Nicolosi, G. Bister, A. Fonseca, J. B. Nagy, K. Szostak, F. Béguin and W. J. Blau, Reinforcement of polymers with carbon nanotubes: the role of nanotube surface area, Nano Lett., 2004, 4(2), 353–356 CrossRef.
- J. Gao, M. A. Loi, E. J. F. de Carvalho and M. C. dos Santos, Selective wrapping and supramolecular structures of polyfluorene-carbon nanotube hybrids, ACS Nano, 2011, 5(5), 3993–3999 CrossRef PubMed.
- W. Yi, A. Malkovskiy, Y. Xu, X.-Q. Wang, A. P. Sokolov, M. Lebron-Colon, M. A. Meador and Y. Pang, Polymer conformation-assisted wrapping of single-walled carbon nanotube: the impact of cis-vinylene linkage, Polymer, 2010, 51(2), 475–481 CrossRef.
- S. K. Samanta, M. Fritsch, U. Scherf, W. Gomulya, S. Z. Bisri and M. A. Loi, Conjugated polymer-assisted dispersion of single-wall carbon nanotubes: the power of polymer wrapping, Acc. Chem. Res., 2014, 47(8), 2446–2456 CrossRef PubMed.
- T. Lei, I. Pochorovski and Z. Bao, Separation of semiconducting carbon nanotubes for flexible and stretchable electronics using polymer removable method, Acc. Chem. Res., 2017, 50(4), 1096–1104 CrossRef PubMed.
- S. S. Tallury and M. A. Pasquinelli, Molecular dynamics simulations of polymers with stiff backbones interacting with single-walled carbon nanotubes, J. Phys. Chem. B, 2010, 114(29), 9349–9355 CrossRef PubMed.
- I. Kusner and S. Srebnik, Conformational behavior of semi-flexible polymers confined to a cylindrical surface, Chem. Phys. Lett., 2006, 430(1–3), 84–88 CrossRef.
- S. S. Tallury and M. A. Pasquinelli, Molecular dynamics simulations of flexible polymer chains wrapping single-walled carbon nanotubes, J. Phys. Chem. B, 2010, 114(12), 4122–4129 CrossRef PubMed.
- H. Wang, J. Mei, P. Liu, K. Schmidt, G. Jiménez-Osés, S. Osuna, L. Fang, C. J. Tassone, A. P. Zoombelt, A. N. Sokolov, K. N. Houk, M. F. Toney and Z. Bao, Scalable and selective dispersion of semiconducting arc-discharged carbon nanotubes by dithiafulvalene-thiophene copolymers for thin film transistors, ACS Nano, 2013, 7(3), 2659–2668 CrossRef PubMed.
- S. Zhang, W. Lin, C.-P. Wong, D. G. Bucknall and S. Kumar, Nanocomposites of carbon nanotube fibers prepared by polymer crystallization, ACS Appl. Mater. Interfaces, 2010, 2(6), 1642–1647 CrossRef PubMed.
- V. V. Didenko, V. C. Moore, D. S. Baskin and R. E. Smalley, Visualization of individual single-walled carbon nanotubes by fluorescent polymer wrapping, Nano Lett., 2005, 5(8), 1563–1567 CrossRef PubMed.
- S. H. Lee, J. S. Park, B. K. Lim and S. O. Kim, Polymer/carbon nanotube nanocomposites via noncovalent grafting with end-functionalized polymers, J. Appl. Polym. Sci., 2008, 110(4), 2345–2351 CrossRef.
- E.-Y. Choi, T. H. Han, J. Hong, J. E. Kim, S. H. Lee, H. W. Kim and S. O. Kim, Noncovalent functionalization of graphene with end-functional polymers, J. Mater. Chem., 2010, 20(10), 1907–1912 RSC.
- F. Buffa, G. A. Abraham, B. P. Grady and D. Resasco, Effect of nanotube functionalization on the properties of single-walled carbon nanotube-polyurethane composites, J. Polym. Sci., Part B: Polym. Phys., 2007, 45(4), 490–501 CrossRef.
- Q. Zheng, Q. Xue, K. Yan, X. Gao, Q. Li and L. Hao, Effect of chemisorption on the interfacial bonding characteristics of carbon nanotube-polymer composites, Polymer, 2008, 49(3), 800–808 CrossRef.
- T. Ramanathan, A. A. Abdala, S. Stankovich, D. A. Dikin, M. Herrera-Alonso, R. D. Piner, D. H. Adamson, H. C. Schniepp, X. Chen and R. S. Ruoff, Functionalized graphene sheets for polymer nanocomposites, Nat. Nanotechnol., 2008, 3(6), 327–331 CrossRef PubMed.
- J.-M. Yuan, Z.-F. Fan, X.-H. Chen, X.-H. Chen, Z.-J. Wu and L.-P. He, Preparation of polystyrene-multiwalled carbon nanotube composites with individual-dispersed nanotubes and strong interfacial adhesion, Polymer, 2009, 50(14), 3285–3291 CrossRef.
- C. Velasco-Santos, A. L. Martínez-Hernández, F. T. Fisher, R. Ruoff and V. M. Castaño, Improvement of thermal and mechanical properties of carbon nanotube composites through chemical functionalization, Chem. Mater., 2003, 15(23), 4470–4475 CrossRef.
- N. G. Sahoo, H. K. F. Cheng, J. Cai, L. Li, S. H. Chan, J. Zhao and S. Yu, Improvement of mechanical and thermal properties of carbon nanotube composites through nanotube functionalization and processing methods, Mater. Chem. Phys., 2009, 117(1), 313–320 CrossRef.
- C.-M. Chang and Y.-L. Liu, Functionalization of multi-walled carbon nanotubes with non-reactive polymers through an ozone-mediated process for the preparation of a wide range of high performance polymer/carbon nanotube composites, Carbon, 2010, 48(4), 1289–1297 CrossRef.
- S. Mallakpour and A. Zadehnazari, A facile, efficient, and rapid covalent functionalization of multi-walled carbon nanotubes with natural amino acids under microwave irradiation, Prog. Org. Coat., 2014, 77(3), 679–684 CrossRef.
- E. Rezvanpanah, S. R. G. Anbaran and E. Di Maio, Carbon nanotubes in microwave foaming of thermoplastics, Carbon, 2017, 125, 32–38 CrossRef.
- R. E. Gorga, K. K. S. Lau, K. K. Gleason and R. E. Cohen, The importance of interfacial design at the carbon nanotube/polymer composite interface, J. Appl. Polym. Sci., 2006, 102(2), 1413–1418 CrossRef.
- J. Zhu, H. Peng, F. Rodriguez-Macias, J. L. Margrave, V. N. Khabashesku, A. M. Imam, K. Lozano and E. V. Barrera, Reinforcing epoxy polymer composites through covalent integration of functionalized nanotubes, Adv. Funct. Mater., 2004, 14(7), 643–648 CrossRef.
- A. A. Koval'chuk, V. G. Shevchenko, A. N. Shchegolikhin, P. M. Nedorezova, A. N. Klyamkina and A. M. Aladyshev, Effect of carbon nanotube functionalization on the structural and mechanical properties of polypropylene/MWCNT composites, Macromolecules, 2008, 41(20), 7536–7542 CrossRef.
- J. Liu, Y. Ye, Y. Xue, X. Xie and Y.-W. Mai, Recent advances in covalent functionalization
of carbon nanomaterials with polymers: Strategies and perspectives, J. Polym. Sci., Part A: Polym. Chem., 2017, 55(4), 622–631 CrossRef.
- N. Lachman and H. D. Wagner, Correlation between interfacial molecular structure and mechanics in CNT-epoxy nano-composites, Composites, Part A, 2010, 41(9), 1093–1098 CrossRef.
- S. Wang, Z. Liang, P. Gonnet, Y.-H. Liao, B. Wang and C. Zhang, Effect of nanotube functionalization on the coefficient of thermal expansion of nanocomposites, Adv. Funct. Mater., 2007, 17(1), 87–92 CrossRef.
- J. Goclon, M. Kozlowska and P. Rodziewicz, Covalent functionalization of single-walled carbon nanotubes through attachment of aromatic diisocyanate molecules from first principles, Chem. Phys. Lett., 2015, 619, 103–108 CrossRef.
- M. Eguílaz, A. Gutiérrez, F. Gutierrez, J. M. González-Domínguez, A. Ansón-Casaos, J. Hernández-Ferrer, N. F. Ferreyra, M. T. Martínez and G. Rivas, Covalent functionalization of single-walled carbon nanotubes with polytyrosine: characterization and analytical applications for the sensitive quantification of polyphenols, Anal. Chim. Acta, 2016, 909, 51–59 CrossRef PubMed.
- C. Baudot and C. M. Tan, Covalent functionalization of carbon nanotubes and their use in dielectric epoxy composites to improve heat dissipation, Carbon, 2011, 49(7), 2362–2369 CrossRef.
- J. Q. Liu, T. Xiao, K. Liao and P. Wu, Interfacial design of carbon nanotube polymer composites: a hybrid system of noncovalent and covalent functionalizations, Nanotechnology, 2007, 18(16), 165701 CrossRef.
- Y.-Z. Long, M.-M. Li, C. Gu, M. Wan, J.-L. Duvail, Z. Liu and Z. Fan, Recent advances in synthesis, physical properties and applications of conducting polymer nanotubes and nanofibers, Prog. Polym. Sci., 2011, 36(10), 1415–1442 CrossRef.
- C. Oueiny, S. Berlioz and F.-X. Perrin, Carbon nanotube-polyaniline composites, Prog. Polym. Sci., 2014, 39(4), 707–748 CrossRef.
- E. M. Jackson, P. E. Laibinis, W. E. Collins, A. Ueda, C. D. Wingard and B. Penn, Development and thermal properties of carbon nanotube-polymer composites, Composites, Part B, 2016, 89, 362–373 CrossRef.
- V. D. Punetha, S. Rana, H. J. Yoo, A. Chaurasia, J. T. McLeskey, M. S. Ramasamy, N. G. Sahoo and J. W. Cho, Functionalization of carbon nanomaterials for advanced polymer nanocomposites: a comparison study between CNT and graphene, Prog. Polym. Sci., 2017, 67, 1–47 CrossRef.
- Z. Jia, H.-L. Ma, L.-K. Cheng, K.-T. Lau, D. Hui and G. Yuan, Stress transfer properties of carbon nanotube reinforced polymer composites at low temperature environments, Composites, Part B, 2016, 106, 356–365 CrossRef.
- A. Patti, P. Russo, D. Acierno and S. Acierno, The effect of filler functionalization on dispersion and thermal conductivity of polypropylene/multi wall carbon nanotubes composites, Composites, Part B, 2016, 94, 350–359 CrossRef.
- Q. Jiang, X. Wang, Y. Zhu, D. Hui and Y. Qiu, Mechanical, electrical and thermal properties of aligned carbon nanotube/polyimide composites, Composites, Part B, 2014, 56, 408–412 CrossRef.
- S. Gong, Z. H. Zhu and S. A. Meguid, Anisotropic electrical conductivity of polymer composites with aligned carbon nanotubes, Polymer, 2015, 56, 498–506 CrossRef.
- J. K. W. Sandler, J. E. Kirk, I. A. Kinloch, M. S. P. Shaffer and A. H. Windle, Ultra-low electrical percolation threshold in carbon-nanotube-epoxy composites, Polymer, 2003, 44(19), 5893–5899 CrossRef.
- R. Taherian, Experimental and analytical model for the electrical conductivity of polymer-based nanocomposites, Compos. Sci. Technol., 2016, 123, 17–31 CrossRef.
- Y. Zare and K. Y. Rhee, Development of a conventional model to predict the electrical conductivity of polymer/carbon nanotubes nanocomposites by interphase, waviness and contact effects, Composites, Part A, 2017, 100, 305–312 CrossRef.
- G. Fei, Q. Gong, D. Li, M. Lavorgna and H. Xia, Relationship between electrical conductivity and spatial arrangements of carbon nanotubes in polystyrene nanocomposites: the effect of thermal annealing and plasticization on electrical conductivity, Compos. Sci. Technol., 2017, 146, 99–109 CrossRef.
- A. H. A. Hoseini, M. Arjmand, U. Sundararaj and M. Trifkovic, Significance of interfacial interaction and agglomerates on electrical properties of polymer-carbon nanotube nanocomposites, Mater. Des., 2017, 125, 126–134 CrossRef.
- M. Li, I.-H. Kim and Y. G. Jeong, Cellulose acetate/multiwalled carbon nanotube nanocomposites with improved mechanical, thermal, and electrical properties, J. Appl. Polym. Sci., 2010, 118(4), 2475–2481 Search PubMed.
- S. Sadeghi, A. Z. Yazdi and U. Sundararaj, Controlling short-range interactions by tuning surface chemistry in HDPE/graphene nanoribbon nanocomposites, J. Phys. Chem. B, 2015, 119(35), 11867–11878 CrossRef PubMed.
- M. Arjmand, S. Sadeghi, M. Khajehpour and U. Sundararaj, Carbon nanotube/graphene nanoribbon/polyvinylidene fluoride hybrid nanocomposites: rheological and dielectric properties, J. Phys. Chem. C, 2017, 121(1), 169–181 CrossRef.
- S. Sadeghi, M. Arjmand, I. O. Navas, A. Z. Yazdi and U. Sundararaj, Effect of nanofiller geometry on network formation in polymeric nanocomposites: comparison of rheological and electrical properties of multiwalled carbon nanotube and graphene nanoribbon, Macromolecules, 2017, 50(10), 3954–3967 CrossRef.
- J. P. F. Santos, M. Arjmand, G. H. F. Melo, K. Chizari, R. E. S. Bretas and U. Sundararaj, Electrical conductivity of electrospun nanofiber mats of polyamide 6/polyaniline coated with nitrogen-doped carbon nanotubes, Mater. Des., 2018, 141, 333–341 CrossRef.
- A. Sarvi and U. Sundararaj, Rheological percolation in polystyrene composites filled with polyaniline-coated multiwall carbon nanotubes, Synth. Met., 2014, 194, 109–117 CrossRef.
- A. Ameli, M. Arjmand, P. Pötschke, B. Krause and U. Sundararaj, Effects of synthesis catalyst and temperature on broadband dielectric properties of nitrogen-doped carbon nanotube/polyvinylidene fluoride nanocomposites, Carbon, 2016, 106, 260–278 CrossRef.
- S. A. Mirkhani, M. Arjmand, S. Sadeghi, B. Krause, P. Pötschke and U. Sundararaj, Impact of synthesis temperature on morphology, rheology and electromagnetic interference shielding of CVD-grown carbon nanotube/polyvinylidene fluoride nanocomposites, Synth. Met., 2017, 230, 39–50 CrossRef.
- I. Otero-Navas, M. Arjmand and U. Sundararaj, Carbon nanotube induced double percolation in polymer blends: morphology, rheology and broadband dielectric properties, Polymer, 2017, 114, 122–134 CrossRef.
- A. H. A. Hoseini, M. Arjmand, U. Sundararaj and M. Trifkovic, Tunable electrical conductivity of polystyrene/polyamide-6/carbon nanotube blend nanocomposites via control of morphology and nanofiller localization, Eur. Polym. J., 2017, 95, 418–429 CrossRef.
- M. S. de Luna and G. Filippone, Effects of nanoparticles on the morphology of immiscible polymer blends – challenges and opportunities, Eur. Polym. J., 2016, 79, 198–218 CrossRef.
- I. O. Navas, M. Arjmand and U. Sundararaj, Effect of carbon nanotubes on morphology evolution of polypropylene/polystyrene blends: understanding molecular interactions and carbon nanotube migration mechanisms, RSC Adv., 2017, 7(85), 54222–54234 RSC.
- Y. Li, S. Wang, Q. Wang and M. Xing, A comparison study on mechanical properties of polymer composites reinforced by carbon nanotubes and graphene sheet, Composites, Part B, 2018, 133, 35–41 CrossRef.
- M. Tarfaoui, K. Lafdi and A. E. Moumen, Mechanical properties of carbon nanotubes based polymer composites, Composites, Part B, 2016, 103, 113–121 CrossRef.
- J. Sethi, E. Sarlin, S. S. Meysami, R. Suihkonen, A. R. S. S. Kumar, M. Honkanen, P. Keinänen, N. Grobert and J. Vuorinen, The effect of multi-wall carbon nanotube morphology on electrical and mechanical properties of polyurethane nanocomposites, Composites, Part A, 2017, 102, 305–313 CrossRef.
- Z. Li, M. Tang, J. Dai, T. Wang and R. Bai, Effect of multiwalled carbon nanotube-grafted polymer brushes on the mechanical and swelling properties of polyacrylamide composite hydrogels, Polymer, 2016, 85, 67–76 CrossRef.
- A. K. Gupta and S. P. Harsha, Analysis of mechanical properties of carbon nanotube reinforced polymer composites using multi-scale finite element modeling approach, Composites, Part B, 2016, 95, 172–178 CrossRef.
- Y. Martinez-Rubi, B. Ashrafi, M. B. Jakubinek, S. Zou, K. Laqua, M. Barnes and B. Simard, Fabrication of high content carbon nanotube-polyurethane sheets with tailorable properties, ACS Appl. Mater. Interfaces, 2017, 9(36), 30840–30849 CrossRef PubMed.
- L. Guadagno, B. De Vivo, A. Di Bartolomeo, P. Lamberti, A. Sorrentino, V. Tucci, L. Vertuccio and V. Vittoria, Effect of functionalization on the thermo-mechanical and electrical behavior of multi-wall carbon nanotube/epoxy composites, Carbon, 2011, 49(6), 1919–1930 CrossRef.
- C. Ma, H.-Y. Liu, X. Du, L. Mach, F. Xu and Y.-W. Mai, Fracture resistance, thermal and electrical properties of epoxy composites containing aligned carbon nanotubes by low magnetic field, Compos. Sci. Technol., 2015, 114, 126–135 CrossRef.
- E. Moaseri, M. Karimi, M. Baniadam and M. Maghrebi, Improvements in mechanical properties of multi-walled carbon nanotube-reinforced epoxy composites through novel magnetic-assisted method for alignment of carbon nanotubes, Composites, Part A, 2014, 64, 228–233 CrossRef.
- A. Martone, C. Formicola, M. Giordano and M. Zarrelli, Reinforcement efficiency of multi-walled carbon nanotube/epoxy nano composites, Compos. Sci. Technol., 2010, 70(7), 1154–1160 CrossRef.
- K. T. Kim and W. H. Jo, Non-destructive functionalization of multi-walled carbon nanotubes with naphthalene-containing polymer for high performance nylon66/multi-walled carbon nanotube composites, Carbon, 2011, 49(3), 819–826 CrossRef.
- E. Y. Choi, S. C. Roh and C. K. Kim, Noncovalent functionalization of multi-walled carbon nanotubes with pyrene-linked nylon66 for high performance nylon66/multi-walled carbon nanotube composites, Carbon, 2014, 72, 160–168 CrossRef.
- E. Y. Choi, J. Y. Kim and C. K. Kim, Fabrication and properties of polycarbonate composites with polycarbonate grafted multi-walled carbon nanotubes by reactive extrusion, Polymer, 2015, 60, 18–25 CrossRef.
- R. M. Kumar, S. K. Sharma, B. V. M. Kumar and D. Lahiri, Effects of carbon nanotube aspect ratio on strengthening and tribological behavior of ultra high molecular weight polyethylene composite, Composites, Part A, 2015, 76, 62–72 CrossRef.
- X. Zhang, X. Yan, Q. He, H. Wei, J. Long, J. Guo, H. Gu, J. Yu, J. Liu, D. Ding, L. Sun, S. Wei and Z. Guo, Electrically conductive polypropylene nanocomposites with negative permittivity at low carbon nanotube loading levels, ACS Appl. Mater. Interfaces, 2015, 7(11), 6125–6138 CrossRef PubMed.
- H. Yazdani, B. E. Smith and K. Hatami, Multi-walled carbon nanotube-filled polyvinyl chloride composites: Influence of processing method on dispersion quality, electrical conductivity and mechanical properties, Composites, Part A, 2016, 82, 65–77 CrossRef.
- K. A. Zarasvand and H. Golestanian, Determination of nonlinear behavior of multi-walled carbon nanotube reinforced polymer: experimental, numerical, and micromechanical, Mater. Des., 2016, 109, 314–323 CrossRef.
- M. H. Al-Saleh, Electrically conductive carbon nanotube/polypropylene nanocomposite with improved mechanical properties, Mater. Des., 2015, 85, 76–81 CrossRef.
- W. S. Choi and S. H. Ryu, Improvement of
interfacial interaction via ATRP in polycarbonate/carbon nanotube nanocomposites, Colloids Surf., A, 2011, 375(1–3), 55–60 CrossRef.
- G. Venugopal, J. C. Veetil, N. Raghavan, V. Singh, A. Kumar and A. Mukkannan, Nano-dynamic mechanical and thermal responses of single-walled carbon nanotubes reinforced polymer nanocomposite thinfilms, J. Alloys Compd., 2016, 688(Part B), 454–459 CrossRef.
- A. Hameed, M. C. Islam, I. ahmad, N. Mahmood, S. Saeed and H. Javed, Thermal and mechanical properties of carbon nanotube/epoxy nanocomposites reinforced with pristine and functionalized multiwalled carbon nanotubes, Polym. Compos., 2015, 36(10), 1891–1898 CrossRef.
- M. H. Al-Saleh, B. A. Al-Saidi and R. M. Al-Zoubi, Experimental and theoretical analysis of the mechanical and thermal properties of carbon nanotube/acrylonitrile-styrene-butadiene nanocomposites, Polymer, 2016, 89, 12–17 CrossRef.
- Y. Li, C. Chen, J. Xu, Z. Zhang, B. Yuan and X. Huang, Improved mechanical properties of carbon nanotubes-coated flax fiber reinforced composites, J. Mater. Sci., 2015, 50(3), 1117–1128 CrossRef.
- C.-C. Li, C.-L. Lu, Y.-T. Lin, B.-Y. Wei and W.-K. Hsu, Creation of interfacial phonons by carbon nanotube-polymer coupling, Phys. Chem. Chem. Phys., 2009, 11(29), 6034–6037 RSC.
- D. Ürk, E. Demir, O. Bulut, D. Çakıroğlu, F. Ç. Cebeci, M. L. Öveçoğlu and H. Cebeci, Understanding the polymer type and CNT orientation effect on the dynamic mechanical properties of high volume fraction CNT polymer nanocomposites, Compos. Struct., 2016, 155, 255–262 CrossRef.
- T. Yamamoto and K. Kawaguchi, Synthesis of composite polymer particles with carbon nanotubes and evaluation of their mechanical properties, Colloids Surf., A, 2017, 529, 765–770 CrossRef.
- H. J. Park, A. Badakhsh, I. T. Im, M.-S. Kim and C. W. Park, Experimental study on the thermal and mechanical properties of MWCNT/polymer and Cu/polymer composites, Appl. Therm. Eng., 2016, 107, 907–917 CrossRef.
- A. A. Mamedov, N. A. Kotov, M. Prato, D. M. Guldi, J. P. Wicksted and A. Hirsch, Molecular design of strong single-wall carbon nanotube/polyelectrolyte multilayer composites, Nat. Mater., 2002, 1(3), 190–194 CrossRef PubMed.
- M. Olek, J. Ostrander, S. Jurga, H. Möhwald, N. Kotov, K. Kempa and M. Giersig, Layer-by-layer assembled composites from multiwall carbon nanotubes with different morphologies, Nano Lett., 2004, 4(10), 1889–1895 CrossRef.
- Y. Dong, H. Xia, Y. Zhu, Q.-Q. Ni and Y. Fu, Effect of epoxy-graft-polyoxyethylene octyl phenyl ether on preparation, mechanical properties and triple-shape memory effect of carbon nanotube/water-borne epoxy nanocomposites, Compos. Sci. Technol., 2015, 120, 17–25 CrossRef.
- J. Gao, M. E. Itkis, A. Yu, E. Bekyarova, B. Zhao and R. C. Haddon, Continuous spinning of a single-walled carbon nanotube-nylon composite fiber, J. Am. Chem. Soc., 2005, 127(11), 3847–3854 CrossRef PubMed.
- C. A. Dyke and J. M. Tour, Covalent functionalization of single-walled carbon nanotubes for materials applications, J. Phys. Chem. A, 2004, 108(51), 11151–11159 CrossRef.
- B. Krause, P. Pötschke, E. Ilin and M. Predtechenskiy, Melt mixed SWCNT-polypropylene composites with very low electrical percolation, Polymer, 2016, 98, 45–50 CrossRef.
- A. A. Vasileiou, M. Kontopoulou, H. Gui and A. Docoslis, Correlation between the length reduction of carbon nanotubes and the electrical percolation threshold of melt compounded polyolefin composites, ACS Appl. Mater. Interfaces, 2015, 7(3), 1624–1631 CrossRef PubMed.
- H.-C. Li, S.-Y. Lu, S.-H. Syue, W.-K. Hsu and S.-C. Chang, Conductivity enhancement of carbon nanotube composites by electrolyte addition, Appl. Phys. Lett., 2008, 93(3), 033104 CrossRef.
- J. Li, P. C. Ma, W. S. Chow, C. K. To, B. Z. Tang and J.-K. Kim, Correlations between percolation threshold, dispersion state, and aspect ratio of carbon nanotubes, Adv. Funct. Mater., 2007, 17(16), 3207–3215 CrossRef.
- W. Yuan, J. Che and M. B. Chan-Park, A novel polyimide dispersing matrix for highly electrically conductive solution-cast carbon nanotube-based composite, Chem. Mater., 2011, 23(18), 4149–4157 CrossRef.
- A. A. Moud, A. Javadi, H. Nazockdast, A. Fathi and V. Altstaedt, Effect of dispersion and selective localization of carbon nanotubes on rheology and electrical conductivity of polyamide 6 (PA6), Polypropylene (PP), and PA6/PP nanocomposites, J. Polym. Sci., Part B: Polym. Phys., 2015, 53(5), 368–378 CrossRef.
- M. Liebscher, J. Domurath, B. Krause, M. Saphiannikova, G. Heinrich and P. Pötschke, Electrical and melt rheological characterization of PC and co-continuous PC/SAN blends filled with CNTs: relationship between melt-mixing parameters, filler dispersion, and filler aspect ratio, J. Polym. Sci., Part B: Polym. Phys., 2018, 56(1), 79–88 CrossRef.
- T. Souier, C. Maragliano, M. Stefancich and M. Chiesa, How to achieve high electrical conductivity in aligned carbon nanotube polymer composites, Carbon, 2013, 64, 150–157 CrossRef.
- S. U. Khan, J. R. Pothnis and J.-K. Kim, Effects of carbon nanotube alignment on electrical and mechanical properties of epoxy nanocomposites, Composites, Part A, 2013, 49, 26–34 CrossRef.
- C. Gao, B. Han, S. Zhang, J. Pang, G. Wang and Z. Jiang, Enhanced electrical properties by tuning the phase morphology of multiwalled carbon nanotube-filled poly(ether ether ketone)/polyimide composites, Polym. Int., 2015, 64(6), 828–832 CrossRef.
- H.-D. Bao, Y. Sun, Z.-Y. Xiong, Z.-X. Guo and J. Yu, Effects of the dispersion state and aspect ratio of carbon nanotubes on their electrical percolation threshold in a polymer, J. Appl. Polym. Sci., 2013, 128(1), 735–740 CrossRef.
- J. B. Bai and A. Allaoui, Effect of the length and the aggregate size of MWNTs on the improvement efficiency of the mechanical and electrical properties of nanocomposites-experimental investigation, Composites, Part A, 2003, 34(8), 689–694 CrossRef.
- M. B. Bryning, M. F. Islam, J. M. Kikkawa and A. G. Yodh, Very low conductivity threshold in bulk isotropic single-walled carbon nanotube-epoxy composites, Adv. Mater., 2005, 17(9), 1186–1191 CrossRef.
- J. Guo, N. Briggs, S. Crossley and B. P. Grady, Morphology of polystyrene/poly(methyl methacrylate) blends: effects of carbon nanotubes aspect ratio and surface modification, AIChE J., 2015, 61(10), 3500–3510 CrossRef.
- L. Cao, W. Zhang, X. Zhang, L. Yuan, G. Liang and A. Gu, Low-cost preparation of high-k expanded graphite/carbon nanotube/cyanate ester composites with low dielectric loss and low percolation threshold, Ind. Eng. Chem. Res., 2014,(7), 2661–2672 CrossRef.
- R. Kotsilkova, E. Ivanov, D. Bychanok, A. Paddubskaya, M. Demidenko, J. Macutkevic, S. Maksimenko and P. Kuzhir, Effects of sonochemical modification of carbon nanotubes on electrical and electromagnetic shielding properties of epoxy composites, Compos. Sci. Technol., 2015, 106, 85–92 CrossRef.
- R. Ramasubramaniam, J. Chen and H. Liu, Homogeneous carbon nanotube/polymer composites for electrical applications, Appl. Phys. Lett., 2003, 83(14), 2928–2930 CrossRef.
- S. M. S. Ghezghapan and A. Javadi, Effect of processing methods on electrical percolation and electromagnetic shielding of PC/MWCNTs nanocomposites, Polym. Compos., 2017, 38(S1), E269–E276 CrossRef.
- A. Kasgoz, M. Korkmaz, M. B. Alanalp and A. Durmus, Effect of processing method on
microstructure, electrical conductivity and electromagnetic wave interference (EMI) shielding performance of carbon nanofiber filled thermoplastic polyurethane composites, J. Polym. Res., 2017, 24(9), 148 CrossRef.
- S. H. Lee, J. Y. Kim, C. M. Koo and W. N. Kim, Effects of processing methods on the electrical conductivity, electromagnetic parameters, and EMI shielding effectiveness of polypropylene/nickel-coated carbon fiber composites, Macromol. Res., 2017, 25(9), 936–943 CrossRef.
- N. Grossiord, J. Loos, L. van Laake, M. Maugey, C. Zakri, C. E. Koning and A. J. Hart, High-conductivity polymer nanocomposites obtained by tailoring the characteristics of carbon nanotube fillers, Adv. Funct. Mater., 2008,(20), 3226–3234 CrossRef.
- B. Krause, R. Boldt, L. Häußler and P. Pötschke, Ultralow percolation threshold in polyamide 6.6/MWCNT composites, Compos. Sci. Technol., 2015, 114, 119–125 CrossRef.
- H. M. Kim, K. Kim, C. Y. Lee, J. Joo, S. J. Cho, H. S. Yoon, D. A. Pejaković, J. W. Yoo and A. J. Epstein, Electrical conductivity and electromagnetic interference shielding of multiwalled carbon nanotube composites containing Fe catalyst, Appl. Phys. Lett., 2003, 84(4), 589–591 CrossRef.
- V. Skákalová, U. Dettlaff-Weglikowska and S. Roth, Electrical and mechanical properties of nanocomposites of single wall carbon nanotubes with PMMA, Synth. Met., 2005, 152(1–3), 349–352 CrossRef.
- J. C. Grunlan, A. R. Mehrabi, M. V. Bannon and J. L. Bahr, Water-based single-walled-nanotube-filled polymer composite with an exceptionally low percolation threshold, Adv. Mater., 2004, 16(2), 150–153 CrossRef.
- T.-E. Chang, A. Kisliuk, S. M. Rhodes, W. J. Brittain and A. P. Sokolov, Conductivity and mechanical properties of well-dispersed single-wall carbon nanotube/polystyrene composite, Polymer, 2006, 47(22), 7740–7746 CrossRef.
- X. Wang and S. C. Jana, Syndiotactic polystyrene aerogels containing multi-walled carbon nanotubes, Polymer, 2013, 54(2), 750–759 CrossRef.
- G. Sun, G. Chen, Z. Liu and M. Chen, Preparation, crystallization, electrical conductivity and thermal stability of syndiotactic polystyrene/carbon nanotube composites, Carbon, 2010, 48(5), 1434–1440 CrossRef.
- D. O. O. Ayewah, D. C. Davis, R. Krishnamoorti, D. C. Lagoudas, H.-J. Sue and M. Willson, A surfactant dispersed SWCNT-polystyrene composite characterized for electrical and mechanical properties, Composites, Part A, 2010, 41(7), 842–849 CrossRef.
- S. Mazinani, A. Ajji and C. Dubois, Morphology, structure and properties of conductive PS/CNT nanocomposite electrospun mat, Polymer, 2009, 50(14), 3329–3342 CrossRef.
- V. K. Sachdev, S. Bhattacharya, K. Patel, S. K. Sharma, N. C. Mehra and R. P. Tandon, Electrical and EMI shielding characterization of multiwalled carbon nanotube/polystyrene composites, J. Appl. Polym. Sci., 2014, 131(24), 205–212 CrossRef.
- S. Kara, E. Arda, F. Dolastir and Ö. Pekcan, Electrical and optical percolations of polystyrene latex-multiwalled carbon nanotube composites, J. Colloid Interface Sci., 2010, 344(2), 395–401 CrossRef PubMed.
- A. H. Shah and T. Z. Rizvi, Improvement in electrical and thermal behavior of polystyrene/multiwalled carbon nanotubes nanocomposites, Measurement, 2013, 46(4), 1541–1550 CrossRef.
- M. Arjmand, T. Apperley, M. Okoniewski and U. Sundararaj, Comparative study of electromagnetic interference shielding properties of injection molded versus compression molded multi-walled carbon nanotube/polystyrene composites, Carbon, 2012, 50(14), 5126–5134 CrossRef.
- N. K. Shrivastava and B. B. Khatua, Development of electrical conductivity with minimum possible percolation threshold in multi-wall carbon nanotube/polystyrene composites, Carbon, 2011, 49(13), 4571–4579 CrossRef.
- C. Wu, X. Huang, X. Wu, J. Yu, L. Xie and P. Jiang, TiO2-nanorod decorated carbon nanotubes for high-permittivity and low-dielectric-loss polystyrene composites, Compos. Sci. Technol., 2012, 72(4), 521–527 CrossRef.
- N. K. Shrivastava, S. Maiti, S. Suin and B. B. Khatua, Influence of selective dispersion of MWCNT on electrical percolation of in situ polymerized high-impact polystyrene/MWCNT nanocomposites, eXPRESS Polym. Lett., 2014, 8(1), 15–29 CrossRef.
- R. Bhatia, J. Galibert and R. Menon, Magnetic field induced delocalization in multi-wall carbon nanotube-polystyrene composite at high fields, Carbon, 2014, 69, 372–378 CrossRef.
- A. Ayesh, S. Ibrahim and A. Aljaafari, Electrical, optical, and rheological properties of ozone-treated multiwalled carbon nanotubes-polystyrene nanocomposites, J. Reinf. Plast. Compos., 2013, 32(6), 359–370 CrossRef.
- J. Yu, K. Lu, E. Sourty, N. Grossiord, C. E. Koning and J. Loos, Characterization of conductive multiwall carbon nanotube/polystyrene composites prepared by latex technology, Carbon, 2007, 45(15), 2897–2903 CrossRef.
- M. H. Al-Saleh, Clay/carbon nanotube hybrid mixture to reduce the electrical percolation threshold of polymer nanocomposites, Compos. Sci. Technol., 2017, 149, 34–40 CrossRef.
- A.-K. Du, K.-L. Yang, T.-H. Zhao, M. Wang and J.-B. Zeng, Poly(sodium 4-styrenesulfonate) wrapped carbon nanotube with low percolation threshold in poly(ε-caprolactone) nanocomposites, Polym. Test., 2016, 51, 40–48 CrossRef.
- T. Deplancke, O. Lame, S. Barrau, K. Ravi and F. Dalmas, Impact of carbon nanotube prelocalization on the ultra-low electrical percolation threshold and on the mechanical behavior of sintered UHMWPE-based nanocomposites, Polymer, 2017, 111, 204–213 CrossRef.
- J. R. Bautista-Quijano, P. Pötschke, H. Brünig and G. Heinrich, Strain sensing, electrical and mechanical properties of polycarbonate/multiwall carbon nanotube monofilament fibers fabricated by melt spinning, Polymer, 2016, 82, 181–189 CrossRef.
- M. Jouni, J. Faure-Vincent, P. Fedorko, D. Djurado, G. Boiteux and V. Massardier, Charge carrier transport and low electrical percolation threshold in multiwalled carbon nanotube polymer nanocomposites, Carbon, 2014, 76, 10–18 CrossRef.
- C. Leopold, T. Augustin, T. Schwebler, J. Lehmann, W. V. Liebig and B. Fiedler, Influence of carbon nanoparticle modification on the mechanical and electrical properties of epoxy in small volumes, J. Colloid Interface Sci., 2017, 506, 620–632 CrossRef PubMed.
- S. Gong, Z. H. Zhu, M. Arjmand, U. Sundararaj, J. T. W. Yeow and W. Zheng, Effect of carbon nanotubes on electromagnetic interference shielding of carbon fiber reinforced polymer composites, Polym. Compos., 2018, 39(S2), E655–E663 CrossRef.
- M. Mahmoodi, M. Arjmand, U. Sundararaj and S. Park, The electrical conductivity and electromagnetic interference shielding of injection molded multi-walled carbon nanotube/polystyrene composites, Carbon, 2012, 50(4), 1455–1464 CrossRef.
- B. Zhao, C. Zhao, R. Li, S. M. Hamidinejad and C. B. Park, Flexible, Ultrathin, and high-efficiency electromagnetic shielding properties of poly(vinylidene fluoride)/carbon composite films, ACS Appl. Mater. Interfaces, 2017, 9(24), 20873–20884 CrossRef PubMed.
- S. H. Park, P. Thielemann, P. Asbeck and P. R. Bandaru, Enhanced dielectric constants and shielding effectiveness of, uniformly dispersed, functionalized carbon nanotube composites, Appl. Phys. Lett., 2009, 94(24), 243111 CrossRef.
- K. Chizari, M. Arjmand, Z. Liu, U. Sundararaj and D. Therriault, Three-dimensional printing of highly conductive polymer nanocomposites for EMI shielding applications, Mater. Today Commun., 2017, 11, 112–118 CrossRef.
- A. K. Singh, A. Shishkin, T. Koppel and N. Gupta, A review of porous lightweight composite materials for electromagnetic interference shielding, Composites, Part B, 2018, 149, 188–197 CrossRef.
- Y. Zamani Keteklahijani, M. Arjmand and U. Sundararaj, Cobalt catalyst grown carbon nanotube/poly(vinylidene fluoride) nanocomposites: effect of synthesis temperature on morphology, electrical conductivity and electromagnetic interference shielding, ChemistrySelect, 2017, 2(31), 10271–10284 CrossRef.
- M. Arjmand, M. Mahmoodi, G. A. Gelves, S. Park and U. Sundararaj, Electrical and electromagnetic interference shielding properties of flow-induced oriented carbon nanotubes in polycarbonate, Carbon, 2011, 49(11), 3430–3440 CrossRef.
- D. D. L. Chung, Electromagnetic interference shielding effectiveness of carbon materials, Carbon, 2001, 39(2), 279–285 CrossRef.
- N. Li, Y. Huang, F. Du, X. He, X. Lin, H. Gao, Y. Ma, F. Li, Y. Chen and P. C. Eklund, Electromagnetic interference (EMI) shielding of single-walled carbon nanotube epoxy composites, Nano Lett., 2006, 6(6), 1141–1145 CrossRef PubMed.
- M. A. Poothanari, J. Abraham, N. Kalarikkal and S. Thomas, Excellent electromagnetic interference shielding and high electrical conductivity of compatibilized polycarbonate/polypropylene carbon nanotube blend nanocomposites, Ind. Eng. Chem. Res., 2018, 57(12), 4287–4297 CrossRef.
- G. Wang, L. Wang, L. H. Mark, V. Shaayegan, G. Wang, H. Li, G. Zhao and C. B. Park, Ultralow-threshold and lightweight biodegradable porous PLA/MWCNT with segregated conductive networks for high-performance thermal insulation and electromagnetic interference shielding applications, ACS Appl. Mater. Interfaces, 2018, 10(1), 1195–1203 CrossRef PubMed.
- H. Xu, S. M. Anlage, L. Hu and G. Gruner, Microwave shielding of transparent and conducting single-walled carbon nanotube films, Appl. Phys. Lett., 2007, 90(18), 183119 CrossRef.
- Z. Liu, G. Bai, Y. Huang, Y. Ma, F. Du, F. Li, T. Guo and Y. Chen, Reflection and absorption contributions to the electromagnetic interference shielding of single-walled carbon nanotube/polyurethane composites, Carbon, 2007, 45(4), 821–827 CrossRef.
- M. H. Al-Saleh and U. Sundararaj, Electromagnetic interference shielding mechanisms of CNT/polymer composites, Carbon, 2009, 47(7), 1738–1746 CrossRef.
- M. H. Al-Saleh, W. H. Saadeh and U. Sundararaj, EMI shielding effectiveness of carbon based nanostructured polymeric materials: a comparative study, Carbon, 2013, 60, 146–156 CrossRef.
- M. Arjmand and U. Sundararaj, Electromagnetic interference shielding of Nitrogen-doped and Undoped carbon nanotube/polyvinylidene fluoride nanocomposites: a comparative study, Compos. Sci. Technol., 2015, 118, 257–263 CrossRef.
- M. Arjmand, K. Chizari, B. Krause, P. Pötschke and U. Sundararaj, Effect of synthesis catalyst on structure of nitrogen-doped carbon nanotubes and electrical conductivity and electromagnetic interference shielding of their polymeric nanocomposites, Carbon, 2016, 98, 358–372 CrossRef.
- Z. Yang, J. Ren, Z. Zhang, X. Chen, G. Guan, L. Qiu, Y. Zhang and H. Peng, Recent advancement of nanostructured carbon for energy applications, Chem. Rev., 2015, 115(11), 5159–5223 CrossRef PubMed.
- H. J. Salavagione, S. Quiles-Díaz, P. Enrique-Jimenez, G. Martínez, F. Ania, A. Flores and M. A. Gómez-Fatou, Development of advanced elastomeric conductive nanocomposites by selective chemical affinity of modified graphene, Macromolecules, 2016, 49(13), 4948–4956 CrossRef.
- L. Valentini, I. Armentano, D. Puglia, J. M.Kenny and S. Santucci, Dynamics of amine functionalised nanotubes/epoxy composites by dielectric relaxation spectroscopy, Carbon, 2004, 42(2), 323–329 CrossRef.
- E. Tamburri, S. Orlanducci, M. L. Terranova, F. Valentini, G. Palleschi, A. Curulli, F. Brunetti, D. Passeri, A. Alippi and M. Rossi, Modulation of electrical properties in single-walled carbon nanotube/conducting polymer composites, Carbon, 2005, 43(6), 1213–1221 CrossRef.
- S. Berber, Y.-K. Kwon and D. Tománek, Unusually high thermal conductivity of carbon nanotubes, Phys. Rev. Lett., 2000, 84(20), 4613–4616 CrossRef PubMed.
- E. Pop, D. Mann, Q. Wang, K. Goodson and H. Dai, Thermal conductance of an individual single-wall carbon nanotube above room temperature, Nano Lett., 2006, 6(1), 96–100 CrossRef PubMed.
- M. Zhang and U. Sundararaj, Thermal, rheological, and mechanical behaviors of LLDPE/PEMA/clay nanocomposites: effect of interaction between polymer, compatibilizer, and nanofiller, Macromol. Mater. Eng., 2006, 291(6), 697–706 CrossRef.
- M. Zhang, B. Lin and U. Sundararaj, Effects of processing sequence on clay dispersion, phase morphology, and thermal and rheological behaviors of PA6-HDPE-clay nanocomposites, J. Appl. Polym. Sci., 2012, 125(S1), E714–E724 CrossRef.
- Y. Gao and F. Müller-Plathe, Molecular dynamics study on the thermal conductivity of the end-grafted carbon nanotubes filled polyamide-6.6 nanocomposites, J. Phys. Chem. C, 2018, 122(2), 1412–1421 CrossRef.
- M. K. Hassanzadeh-Aghdam, M. J. Mahmoodi and J. Jamali, Effect of CNT coating on the overall thermal conductivity of unidirectional polymer hybrid nanocomposites, Int. J. Heat Mass Transfer, 2018, 124, 190–200 CrossRef.
- Z. Han and A. Fina, Thermal conductivity of carbon nanotubes and their polymer nanocomposites: a review, Prog. Polym. Sci., 2011, 36(7), 914–944 CrossRef.
- I.-L. Ngo, S. Jeon and C. Byon, Thermal conductivity of transparent and flexible polymers containing fillers: a literature review, Int. J. Heat Mass Transfer, 2016, 98, 219–226 CrossRef.
- H. Chen, V. V. Ginzburg, J. Yang, Y. Yang, W. Liu, Y. Huang, L. Du and B. Chen, Thermal conductivity of polymer-based composites: fundamentals and applications, Prog. Polym. Sci., 2016, 59, 41–85 CrossRef.
- N. Burger, A. Laachachi, M. Ferriol, M. Lutz, V. Toniazzo and D. Ruch, Review of thermal conductivity in composites: mechanisms, parameters and theory, Prog. Polym. Sci., 2016, 61, 1–28 CrossRef.
- P. Gong, G. Wang, M.-P. Tran, P. Buahom, S. Zhai, G. Li and C. B. Park, Advanced bimodal polystyrene/multi-walled carbon nanotube nanocomposite foams for thermal insulation, Carbon, 2017, 120, 1–10 CrossRef.
- S. N. Leung, Thermally conductive polymer composites and nanocomposites: processing-structure-property relationships, Composites, Part B, 2018, 150, 78–92 CrossRef.
- S. Song, M. Cao, H. Shan, C. Du and B. Li, Polyhedral oligomeric silsesquioxane functionalized carbon nanotubes for high thermal conductive poly(vinylidene fluoride) composite membrane, Mater. Des., 2018, 156, 242–251 CrossRef.
- S. T. Huxtable, D. G. Cahill, S. Shenogin, L. Xue, R. Ozisik, P. Barone, M. Usrey, M. S. Strano, G. Siddons, M. Shim and P. Keblinski, Interfacial heat flow in carbon nanotube suspensions, Nat. Mater., 2003, 2(11), 731–734 CrossRef PubMed.
- F. H. Gojny, M. H. G. Wichmann, B. Fiedler, I. A. Kinloch, W. Bauhofer, A. H. Windle and K. Schulte, Evaluation and identification of electrical and thermal conduction mechanisms in carbon nanotube/epoxy composites, Polymer, 2006, 47(6), 2036–2045 CrossRef.
- S. Shenogin, A. Bodapati, L. Xue, R. Ozisik and P. Keblinski, Effect of chemical functionalization on thermal transport of carbon nanotube composites, Appl. Phys. Lett., 2004, 85(12), 2229–2231 CrossRef.
- R. Kochetov, A. V. Korobko, T. Andritsch, P. H. F. Morshuis, S. J. Picken and J. J. Smit, Modelling of the thermal conductivity in polymer nanocomposites and the impact of the interface between filler and matrix, J. Phys. D: Appl. Phys., 2011, 44(39), 395401 CrossRef.
- S. Pal and I. K. Puri, Thermal rectification in a polymer-functionalized single-wall carbon nanotube, Nanotechnology, 2014, 25(34), 345401 CrossRef PubMed.
- M. Jouni, D. Djurado, V. Massardier and G. Boiteux, A representative and comprehensive review of the electrical and thermal properties of polymer composites with carbon nanotube and other nanoparticle fillers, Polym. Int., 2017, 66(9), 1237–1251 CrossRef.
- V. Kostopoulos, A. Masouras, A. Baltopoulos, A. Vavouliotis, G. Sotiriadis and L. Pambaguian, A critical review of nanotechnologies for composite aerospace structures, CEAS Space Journal, 2017, 9(1), 35–57 CrossRef.
- S. Jabeen, A. Kausar, B. Muhammad, S. Gul and M. Farooq, A review on polymeric nanocomposites of nanodiamond, carbon nanotube, and nanobifiller: structure, preparation and properties, Polym.-Plast. Technol. Eng., 2015, 54(13), 1379–1409 CrossRef.
- H. S. Kim, J. Jang, J. Yu and S. Y. Kim, Thermal conductivity of polymer composites based on the length of multi-walled carbon nanotubes, Composites, Part B, 2015, 79, 505–512 CrossRef.
- C. Huang, X. Qian and R. Yang, Thermal conductivity of polymers and polymer nanocomposites, Mater. Sci. Eng., R, 2018, 132, 1–22 CrossRef.
- Y. Ni, H. Han, S. Volz and T. Dumitricǎ, Nanoscale azide polymer functionalization: a robust solution for suppressing the carbon nanotube-polymer matrix thermal interface resistance, J. Phys. Chem. C, 2015, 119(22), 12193–12198 CrossRef.
- V. Varshney, A. K. Roy and J. W. Baur, Modeling the role of bulk and surface characteristics of carbon fiber on thermal conductance across the carbon-fiber/matrix interface, ACS Appl. Mater. Interfaces, 2015, 7(48), 26674–26683 CrossRef PubMed.
- M. R. Gharib-Zahedi, M. Tafazzoli, M. C. Böhm and M. Alaghemandi, Interfacial thermal transport and structural preferences in carbon nanotube-polyamide-6,6 nanocomposites: how important are chemical functionalization effects?, Phys. Chem. Chem. Phys., 2015, 17(22), 14502–14512 RSC.
- S. Shenogin, L. Xue, R. Ozisik and P. Keblinski, Role of thermal boundary resistance on the heat flow in carbon-nanotube composites, J. Appl. Phys., 2004, 95(12), 8136–8144 CrossRef.
- X. Wei, T. Zhang and T. Luo, Thermal energy transport across hard-soft interfaces, ACS Energy Letters, 2017, 2(10), 2283–2292 CrossRef.
- X. Xu, J. Chen, J. Zhou and B. Li, Thermal conductivity of polymers and their nanocomposites, Adv. Mater., 2018, 30(17), 1705544 CrossRef PubMed.
- N. Mehra, L. Mu, T. Ji, X. Yang, J. Kong, J. Gu and J. Zhu, Thermal transport in polymeric materials and across composite interfaces, Appl. Mater. Today, 2018, 12, 92–130 CrossRef.
- C. H. Liu and S. S. Fan, Effects of chemical modifications on the thermal conductivity of carbon nanotube composites, Appl. Phys. Lett., 2005, 86(12), 123106 CrossRef.
- R. Gulotty, M. Castellino, P. Jagdale, A. Tagliaferro and A. A. Balandin, Effects of functionalization on thermal properties of single-wall and multi-wall carbon nanotube-polymer nanocomposites, ACS Nano, 2013, 7(6), 5114–5121 CrossRef PubMed.
- N. Roy, R. Sengupta and A. K. Bhowmick, Modifications of carbon for polymer composites and nanocomposites, Prog. Polym. Sci., 2012, 37(6), 781–819 CrossRef.
- M. Namasivayam and J. Shapter, Factors affecting carbon nanotube fillers towards enhancement of thermal conductivity in polymer nanocomposites: a review, J. Compos. Mater., 2017, 51(26), 3657–3668 CrossRef.
|
This journal is © The Royal Society of Chemistry 2018 |
Click here to see how this site uses Cookies. View our privacy policy here.