DOI:
10.1039/C8RA04151B
(Paper)
RSC Adv., 2018,
8, 28386-28394
Development of reprocessable novel sulfur-containing epoxy based on thermal treatment
Received
16th May 2018
, Accepted 25th July 2018
First published on 8th August 2018
Abstract
Inspired by the Diels–Alder reaction (DA reaction), the product of the reaction of 2-thiophenecarboxaldehyde (TCD) with epichlorohydrin (ECH) was combined with 1,4-anthraquinone to form a DA structure (a sulfur-containing self-healing epoxy resin (EP-DA) containing a large amount of π-electrons) was synthesized. The chemical structure, thermal properties, thermo-reversibility and tribological properties of EP-DA were studied by FTIR, DSC, gel–sol conversion and MRH-3G, respectively. The results indicated that the as-prepared epoxy composite network, which contains the thermally reversible D–A bond, enabled the epoxy resin to undergo self-repair. Moreover, the waste epoxy resin can be recycled and reused. The friction and wear of the epoxy during actual use were simulated. Macroscopic qualitative observation and quantitative measurement of shearing and peeling recovery were combined to examine the repair behavior and reprocessing ability of EP-DA, confirming that this material has good performance of self-repair and reprocessability, with the highest repair efficiency of up to 83.4%. Moreover, the introduced sulfur-containing diene body greatly improved the lubricating performance of the material, and the treatment time of waste reprocessing had a great influence on the content of the sulfur-containing epoxy monomer in the final EP-DA film. It was often possible to determine the degree of recovery of frictional properties. Inspired by the D–A reaction, a self-assembled large molecule that shares a large number of π-electrons is constructed.
1 Introduction
Epoxy resins, owing to their excellent mechanical properties, chemical stability, good adhesion, and low shrinkage, have long been considered as one of the most extensively applied thermosetting polymers in a wide range of fields, such as transportation, machinery and construction1–5 However, when epoxy resins are used as structural materials, they are likely to initiate minor defects during service. The formed defects may gradually propagate into large damage within a short time and cause a failure of the entire system. Epoxy resins have a self-repair function, so that generated cracks can be healed. This not only can prolong the service life of epoxy resins, but also further broaden the application field of epoxy-based composite materials.6 The introduction of Diels–Alder bond (D–A bond),7 hydrazide bond,8 disulfide bond,9 N–O bond10 and other reversible chemical bonds into the molecule through reversible chemical reactions to heal cracks and other damage is one of the research hotspots for self-healing materials. Among them, the DA reaction, which is a cycloaddition reaction between a diene body and a dienophile, has broad application prospects due to its mild reaction conditions, no catalyst requirement, and great thermal reversibility. This type of intrinsic self-healing has received great attention in recent years.11–15 Cai et al.16 synthesized a high-performance cross-linked epoxy resin (ER)/graphite, which exhibits good performance in terms of rapidly self-healing ability and recyclability, and simultaneously incorporated thermally reversible D–A covalent bonds and multiple-responsive graphene into the ER matrix. Coope et al.17 studied the mechanical properties and self-healing performance of furan-functionalized epoxy resins containing varying amounts (10, 20, 30, or 40 phr) of bismaleimides. The newly studied D–A material exhibited favorable processing characteristics for fiber reinforced polymer (FRP) composites. Li et al.18 proved that amino-functionalized multi-walled carbon nanotube rings based on the dynamic covalent D–A network (NH2-MWCNTs/DA-epoxy) were recoverable and self-healing. Iacono et al.19 added the D–A adduct (2Ph2Epo) to diglycidyl ether of bisphenol A (DGEBA); the resulting hybrid epoxy resin was able to recover from damage. Li et al.20 prepared a series of novolac epoxy resins modified with pendant furan groups by phenol novolac epoxy resins and furfuryl alcohol, followed by cross-linking of bifunctional maleimides by D–A reaction to obtain thermally reversible and self-repairing phenolic epoxy resin. Kuang et al.21 demonstrated a reversible cross-linked epoxy resin with efficient reprocessing and intrinsic self-healing prepared from the diamine D–A adduct and commercial epoxy oligomers. Turkenburg et al.22 successfully synthesized oligomers from furfuryl amine and DGEBA in bulk to achieve full self-healing of a severely cracked and delaminated test specimen. The above studies mainly focused on the synthesis of epoxy resins containing D–A bonds and discussed its self-repair behavior in detail. However, the intrinsic relationship between the time of the D–A reaction and the D–A reverse reaction (r-DA reaction) and the recovery of the mechanical properties was not studied. In addition, epoxy resin is difficult to be recycled as a thermosetting material, thus resulting in a waste of resources. Therefore, it is necessary to explore the reprocessability of self-repairing epoxy resin, but related research has not discussed the reprocessing behavior of this type of self-healing resin. Only by exploring these issues clearly can the self-repairing performance and multiple-repairing ability of such materials be brought into full light and eventually, the waste thermosetting resin can be recycled and reused.
In this study, we achieved a good recovery of the sample after reprocessing the waste to the original sample level, demonstrating that this new type of reusable DA network epoxy material is self-healing and recyclable. When the coating is applied to mechanical parts, its excellent mechanical properties and thermal reversibility can further reduce production costs and material losses and ensures the protection of the environment and the economic utilization of resources. The intrinsic self-repairing epoxy resin containing a thermo-reversible D–A bond was synthesized by reacting a synthetic sulfur-containing mono-epoxy monomer with 1,4-anthraquinone. In the case of mechanical damage caused by wear, peeling, and extrusion, the effect of heat treatment on the healing effect of cracks, furrows, and pits formed by abrasion and peeling was investigated. The combination of macroscopic qualitative observation, recovery of peeling, shearing strength and coefficient of friction (COF) diagrams were combined to quantitatively determine and investigate the self-repair behavior of EP-DA. The intrinsic relationship between time of the D–A reaction as well as r-DA reaction and mechanical as well as lubricating performance recovery effects were discussed in depth. The results confirm that this material has higher repair efficiency and it can exhibit multiple self-repairs. In addition, for the epoxy resin as a wear-resistant consumable, its life, surface cracks and furrows have a greater relationship; hence, the surface lubrication often determines the life span of epoxy composite materials. Therefore, when the self-healing coating on the basis of sulphur-containing EP, designed in this study, is subjected to friction, the presence of the sulphur element promotes the formation of the lubrication transfer film more efficiently and reduces the COF value. When the coating surface is cracked and the furrows are severe, the epoxy coating can be self-repaired and smoothed with precise thermal conductivity through the thermal field effect. These conclusions have important reference value for the further development of epoxy self-repairing wear-resistant consumables.
2 Experimental section
2.1 The main reagent
ECH (AR) was purchased from Tianjin Guangfu Fine Chemical Research Institute. TCD (AR) was obtained from Aladdin Reagent (Shanghai) Co., Ltd. 1,4-Anthraquinone (CP) was procured from Shisihewei Chemical Technology (Shanghai) Co., Ltd. N,N′-Dimethylformamide (DMF) and anhydrous ethyl ether (AR) were obtained from Rion Long Bohua (Tianjin) Pharmaceutical Chemistry Co., Ltd. Tetraethylenepentamine (TEPA) was purchased from Shanghai Titanchem Co., Ltd.
2.2 Synthesis of thermo-reversible self-repairing EP and sample preparation
Initially, 0.1 g sodium borohydride (NaBH4) was uniformly dispersed in 5 mL diethyl ether, and the dispersed NaBH4/diethyl ether solution was added to a four-necked flask, in which 2 g of TCD was dissolved in 40 g of diethyl ether. Then, an additional 13 mL of 5% hydrochloric acid solution was added. At a temperature below 25 °C, 45 mL of ECH was slowly added to the system through a constant pressure funnel under nitrogen atmosphere. After reacting for 4 hours at room temperature, 50 mL of 15% NaOH solution was added and the reaction was continued at room temperature for 2 hours. The resulting product was extracted with diethyl ether; the upper liquid phase was removed and the ether was completely volatilized. Then, the remaining liquid was washed three times to remove the lower oil phase. Residual moisture was removed by distillation under reduced pressure to obtain an epoxy resin monomer TEE containing a thiophene ring. The epoxy value of the resulting product was determined using the hydrochloric acid–acetone method to determine the amount of TEE in the product and consequently determine the amount of 1,4-anthraquinone used in the D–A reaction and the amount of curing agent TEPA.
TEE and 1,4-anthraquinone were mixed in a molar ratio of 2
:
1. The temperature of the system was slowly raised to 55 °C with slow stirring until the solution was clear. Then, 13 phr of TEPA was added dropwise slowly in an ice water bath. After stirring slowly, the mixture was poured into a mold and reacted at 68 °C for 36 hours. EP-DA was obtained after demoulding. The synthesis scheme is shown in Fig. 1.
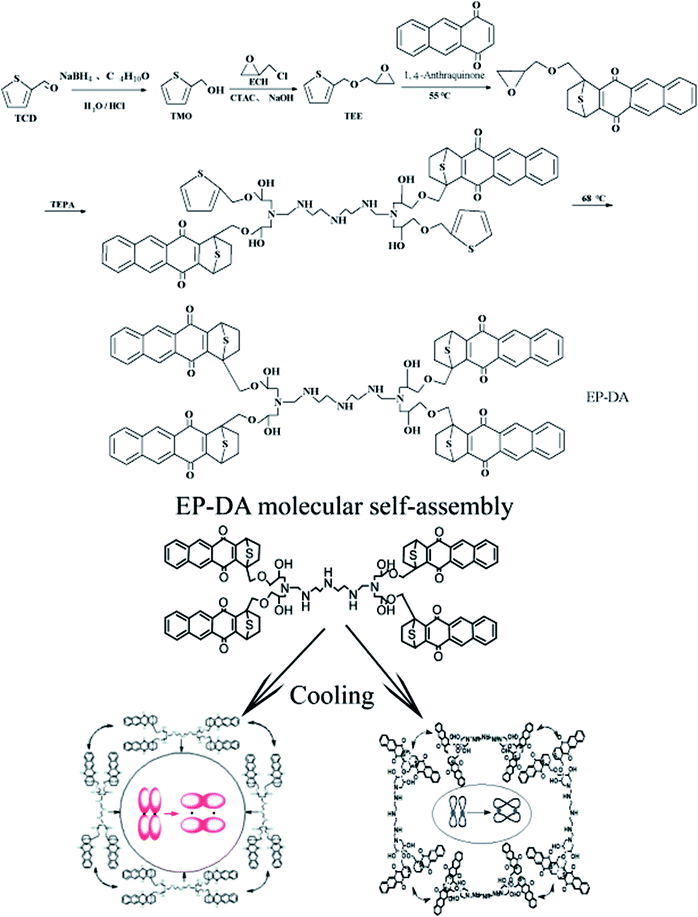 |
| Fig. 1 Synthesis process of EP-DA. | |
2.3 Test and characterization
The material structures were investigated by the 8400 FT-IR spectrometer in the range of 500–4000 cm−1. The surface morphologies of the EP-DA composite were investigated by scanning electron microscopy (SEM, SUV-1500). Differential scanning calorimetry was performed using TA-Q20 Differential Scanning Calorimeter (manufactured by Tvos, USA). Heat-weight analysis was performed using ZCT-A (Beijing Jingji Hi-Tech Instrument Co., Ltd.) type differential thermal weight loss analyzer. The temperature range was 25–800 °C and heating rate was 10 °C min−1; the analysis was performed under nitrogen atmosphere. The friction and wear properties were investigated by the ring block device (GB3960-83), whose accuracy rate, steel ring dimensions, outer diameter, roughness, steel block dimensions and HRC were ±5%, ∅49.22 mm × 13.06 mm, 40 mm, 0.7–0.9 μm, 19.05 mm × 12.32 mm × 12.32 mm and 60, respectively. The coating was tested for shearing strength according to ISO-9653-2000.
3 Results and discussion
3.1 Chemical structure of EP-DA
Fig. 2 shows the infrared spectra of EP-DA, TEE and 1,4-anthraquinone. In the infrared spectrum of EP-DA, there is a distinct absorption peak of D–A adduct at 1720 cm−1. In addition, the other characteristic absorption peaks of TEE and 1,4-anthraquinone are present, indicating that the D–A bond was successfully introduced into the epoxy resin and the epoxy resin EP-DA containing the D–A bond was successfully synthesized. In the infrared spectrum of TEE, the peak at 1728 cm−1 represents the vibration of C
C stretching on the thiophene ring. The peaks at 1010 cm−1 and 870 cm−1 are attributed to C–O–C stretching on the epoxy ring. The peak at 680 cm−1 is the absorption peak of the C–S bond on the thiophene ring. In the infrared spectrum of 1,4-anthraquinone, the peak at 1730 cm−1 represents the stretching vibration of C
O affected by the conjugated phenyl ring. The peak at 1515 cm−1 is ascribed to a series of C
C stretching vibrations on the phenyl ring.
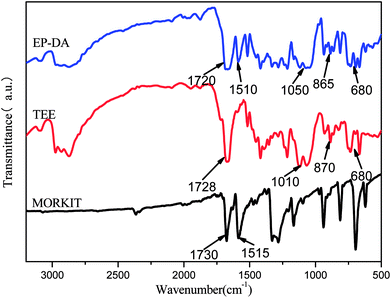 |
| Fig. 2 FTIR spectra of EP-DA, TEE and 1,4-anthraquinone. | |
3.2 Thermal properties and thermal reversibility and reusability of EP-DA
Fig. 3 shows the DSC curves of EP-DA samples for different treatment times at 65 °C. It can be seen that there is an exothermic peak at 55–75 °C, which was due to the equilibrium of the system energy after the D–A reaction. The optimum temperature (peak temperature) of the D–A reaction was 65 °C. When the treatment time was 36 h, the exothermic peak of D–A reaction is the strongest, indicating that the D–A reaction reached an overall equilibrium state at 36 h. A pronounced exothermic peak appears at 120–140 °C. This peak was attributed to the gradual release of accumulated energy during the reaction, which caused the system to equilibrate again, indicating that the r-DA reaction occurred. The best r-DA reaction temperature was 125 °C, and the peak temperature increased with the processing time. Simultaneously, with the increase in processing time, it can be found that the exothermic peak at 150–160 °C is still present, and when the heat treatment time are 36 h and 48 h, the exothermic peaks were more obvious. This can occur because the increase in processing time had a promoting effect on the formation of D–A networks and improved the heat capacity and material durability of the entire system.
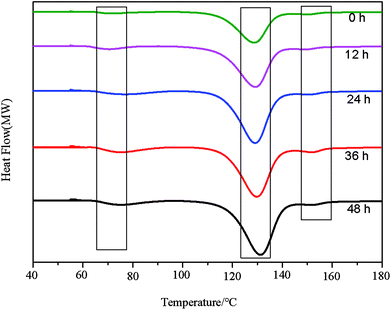 |
| Fig. 3 DSC curves of EP-DA after heat-treated at 65 °C for different times. | |
The phase changes of the as-synthesized EP-DA at different heat treatment temperatures were investigated by gel–sol method to observe the thermo-reversible behavior of EP-DA more intuitively. The results were shown in Fig. 4. When EP-DA with DMF were heated at 125 °C for 15 min, the EP-DA became a viscous liquid that can flow easily, indicating that the D–A bond in the molecule underwent an r-DA reaction, resulting in a long molecular chain. When the molecular weight decreased, the viscosity decreased. Furthermore, when EP-DA was treated at 65 °C, the broken D–A bond recombined to form a long molecular chain. With the progress of the D–A reaction, the molecular weight of the system gradually increased, which promoted the viscosity of the sample. After 2 h, the sample lost its fluidity and became solid. This phase change process can be repeated several times, indicating that EP-DA had good thermal reversibility.
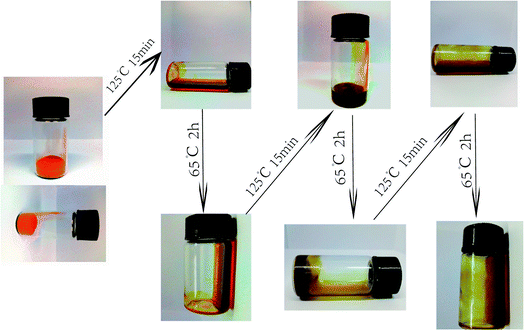 |
| Fig. 4 Phase transformation behavior of EP-DA treated with different temperature/time for three cycles. | |
Based on the good thermal reversibility of EP-DA, it can be inferred that EP-DA should have a certain recovery and processing performance. Fig. 5 shows the EP-DA reprocessing process. First, the EP-DA crushed pieces were molded at 125 °C for 2 h, and then treated at 65 °C for 10 h; it was observed that a complete EP-DA template can be obtained by demoulding. This was due to the fact that under the effect of pressure, the distance between the sample pieces gradually decreased; at the same time, the samples were heat-treated at 125 °C. In the D–A bond in the r-DA reaction broke into a relatively small molecule. Hence, heat movement was more likely to occur, so that the gap between the fragments was further reduced to finally disappear. When treated at 65 °C, broken molecules were again combined with D–A bonds as macromolecules to fuse the specimens into a whole; in macroscopic terms, the broken specimens became a complete template. This shows that EP-DA had good reprocessing properties and can be recycled and reused. Also, studies have shown that this destruction-reprocessing process can be repeated many times, thus enabling multiple recycling of the epoxy resin.
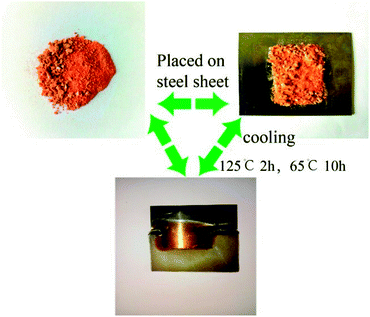 |
| Fig. 5 Reprocessing of EP-DA. | |
3.3 Self-healing performance of EP-DA
Because EP-DA existed in the hot field, there were positive and negative directions in its reaction. Based on this finding, we can realize the recycling and reprocessing of the produced epoxy composite material waste. Therefore, the reusability of the EP-DA was designed in this study. Fig. 6 shows the reprocessed wear debris generated after the friction test of the collected sample. The samples were processed at different temperatures for different times and the microscopic changes were observed by SEM. It can be seen that as the temperature increased, the grinding debris gradually melted into a smooth and dense coating and the furrows and pits on the surface were gradually smoothed out. After heat treatment at 105 °C, the wear debris gradually adhered to form a flat surface. After treatment at 125 °C for 5 min, the furrows and pits formed on the surface were significantly reduced. A more flat coating was seen at 10 minutes. With the increase in the heat treatment temperature, the healing speed of cracks was further accelerated. When heated at 125 °C for 15 minutes, a smooth and regular coating was obtained.
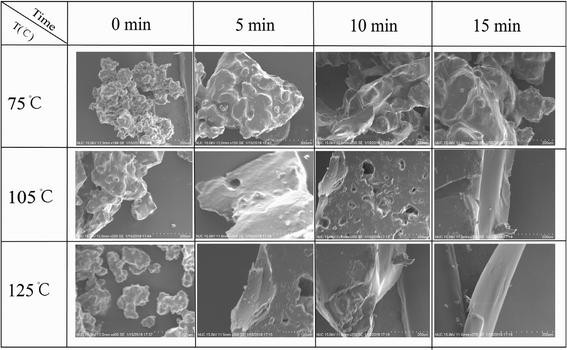 |
| Fig. 6 Visual inspection of crack evolution in EP-DA. | |
In order to make up for the limitations of the macroscopic observation self-repair process, the mechanical properties of the samples treated at 125 °C for different times and at 65 °C for 36 hours were tested and compared. In addition, the relationship between shearing, peeling strength and heat treatment temperature as well as reaction time after reprocessing of the scraps were discussed.
Quantitative analysis. As shown in Fig. 7, the shearing and peeling strength of the recycled EP-DA specimens were measured. The shearing and peeling strength of the original epoxy composite were 42.7 MPa and 6.5 kN m−1, respectively. With the prolongation of the heat treatment time at 125 °C, the maximum strength of EP-DA increased gradually, indicating that as the recovery degree of the recovered waste material gradually increased, the strength of the sample increased. This was due to the r-DA reaction of macromolecules bonded with D–A bonds at 125 °C in the waste sample, which broke into short-chain molecules with a terminal diene and small molecules with a dienophile. The thermal movement of short-chain molecules and small molecules caused the damaged part to be gradually filled with molecular chains, and the D–A bonds were recombined again at 65 °C, so that the broken parts gradually recover. When the heat treatment time was increased to 100 minutes, the sample strength can increase up to 83.4% of the maximum load of the original sample (Table 1). When the high-temperature treatment time was extended to 120 minutes or more, the maximum strength of the sample decreased in reverse because long-term high-temperature heating caused self-aggregation of the sulfur-containing epoxy monomer molecules and 1,4-anthraquinone containing dienophiles. As a result, the amount of D–A bonds formed decreased, leading to poor repairing ability and poor mechanical properties. Hence, the optimum time for the r-DA reaction was determined to be 100 min at 125 °C.
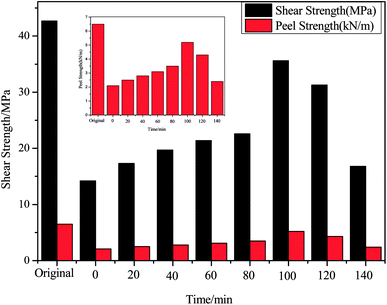 |
| Fig. 7 Effect of heat treatment time at 125 °C on shearing and peeling of EP-DA. | |
Table 1 Average data and healing efficiency of EP-DA from shearing and peeling test
Sample |
Shearing strength (MPa) |
Peeling strength (kN m−1) |
Healing efficiency (%) |
EP-DA0 |
42.7 |
6.5 |
— |
EP-DA1 |
35.6 |
5.2 |
83.4 |
EP-DA2 |
30.1 |
3.9 |
70.5 |
EP-DA3 |
27.2 |
3.0 |
63.7 |
In the macroscopic observation of the repair process and recovery of the mechanical properties of the specimen for different processing times at 125 °C, it can be inferred that the self-repair mechanism of EP-DA was as follows: after the sample was destroyed, the DA bond of the sample began to function when the sample was processed at 125 °C for a period of time. The combined macromolecules underwent r-DA reactions and fragmented into short-chain molecules and small molecules. These short-chain molecules and small molecules were prone to thermal movement and migration, so that the pits were gradually filled with molecular chains. The broken sample was treated at 65 °C. As shown in Fig. 8, the bonds recombined to form macromolecules, such that the damaged portion was filled and repaired by macromolecular chains. Thermal field accumulation was a key part of the initiation of the D–A and r-DA reactions. When there was no thermal field effect, the sulfur-containing epoxy composites had distinct boundaries. When the composite material was in a broken state, the coating was placed under a high-temperature thermal field. Furthermore, due to the accumulation of heat, its thermal reversibility was established, the grid boundary was in a continuous state, and the system was opened and allowed to flow, thus allowing breakage healing and recovery.
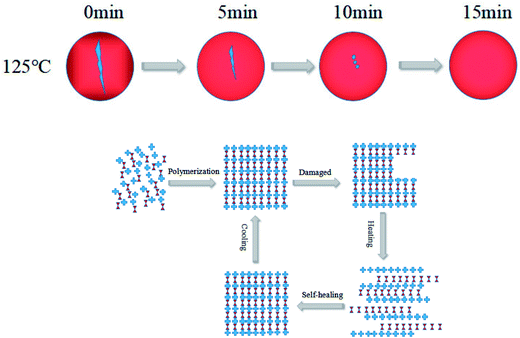 |
| Fig. 8 Schematic of the crack healing process. | |
Inspired by the D–A reaction, a self-assembled supramolecule that shares a large number of π-electrons was constructed. Since the energy of the system tended to be stable and the electrons attracted each other due to the electrostatic force, it can be expected that the self-assembling may occur due to the following two reasons: first, the overlap between the electron clouds on the π-bond of the phenyl ring formed a larger conjugated region; second, the electrons in the diastolic condition approached and then overlapped. The schematic is shown in Fig. 9.
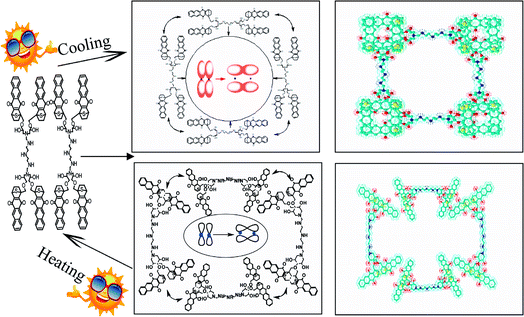 |
| Fig. 9 Schematic of the self-healing process of EP-DA. | |
3.4 Dynamic friction coefficient diagram of EP-DA material
Fig. 10 shows the dynamic friction coefficient graph obtained by reprocessing the epoxy consumable scraps for different repair times. It can be clearly seen in the diagram that the result is the same as that of the shear peeling test. When the repair time was 100 minutes, the COF value of the reprocessed coating obtained was similar to that of the original coating. In addition, it can be seen in the figure that the repair time had a decisive influence on the COF value of the coating. The reasons for the analysis were as follows: when the repair time was 20 minutes, although its COF value recovered slightly, its peeling strength was weak and the coating peeled off. Therefore, during the subsequent occlusal phase, the COF value was severely worn and fluctuated violently. When the repair time was 60 minutes, the film formation of the coating tended to be complete. However, because the surface was not completely repaired, there were a large number of holes, furrows and debris. Hence, the COF value is present in the high-frequency oscillation range, and the entire coating was unstable. When the repair time was 100 minutes, the film formation performance was the best and the degree of D–A reaction of the sulfur-containing epoxy monomer and the diene-containing compound was the highest. Many DA bonds were formed. In the EP-DA grid, most of the sulphur elements can be transferred by friction and the formed surface was the most complete. Therefore, the COF value of EP-DA was close to the COF value of the original material. However, when repair time was further extended to 140 minutes, the film integrity was destroyed due to long-term high-temperature heating causing self-agglomeration of the diene-containing fluorene and sulfur-containing epoxy monomer molecules; therefore, its COF value showed a downward trend.
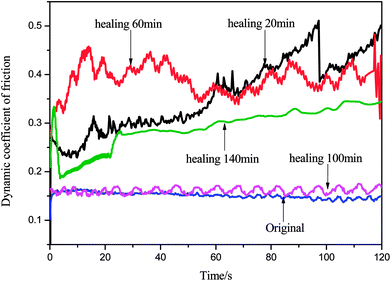 |
| Fig. 10 Dynamic friction coefficient diagram of different repair time for EP-DA materials. | |
We selected the sample after the scrap was processed for 100 minutes as a comparison with the original sample. By comparing the relationship between its dynamic friction coefficient in the friction test and the surface force induced by its frictional environment, it can be seen in the isopotential diagram in Fig. 11 that the fluctuation of the dynamic friction coefficient produced by the sample after healing was considered as the inherent property of the material. This was very similar to that of the original sample, and it can be proved that the reusability was higher and the plasticity was stronger. However, comparing the dynamic surface force changes of the original and the reprocessed sample, it can be observed that the latter was much larger than that of the original sample when subjected to the same loading environment. Therefore, we believe that the aim of our next optimization is to treat the surface conditions of reprocessed waste samples to further improve the performance of this new type of self-repairable and reprocessable epoxy materials, thus further reducing costs, material losses, etc.
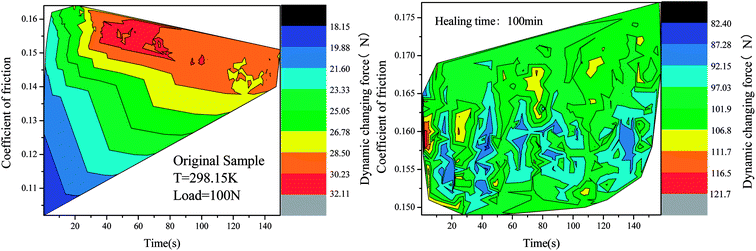 |
| Fig. 11 Within the conditions of dynamic friction working environment, an isopotential plot between the coefficient of friction and the varying surface force is shown. | |
4 Conclusion
The epoxy monomer TEE containing thiophene ring at the end group was synthesized, and the thermally reversible self-healing sulfur-containing epoxy resin material was prepared by the D–A reaction. The molecular structure of epoxy monomer and self-healing epoxy resin was characterized by FTIR. The optimal temperature and time of D–A reaction and r-DA reaction were determined by the DSC test. The gel–sol transition test showed that the as-prepared epoxy resin had good thermal reversibility. Based on this type of thermal reversibility, the sample showed good reusability and self-healing properties, and the repair efficiency was 83.4%. Using the MRH-3G to simulate friction conditions, it was found that the sulfur-containing epoxy composite had a lower COF value. Moreover, the sample scraps were reused and showed excellent film formation and lubricating properties. The COF value of the sample prepared from the scrap can be close to that of the original material, indicating that the recycling and processing efficiency was higher.
As an important biomimetic smart material, self-healing polymer materials have potential applications in many fields, such as high-rise buildings, marine equipment, and underground pipelines. In the next study, the further improvement of repair efficiency and extension of the number of cycles is a key part of broadening its application prospects.
Conflicts of interest
The authors declare that they have no conflict of interest.
Acknowledgements
This research was financially supported by the National Natural Science Foundation of China (No. 51272239), Research Project Supported by Shanxi Scholarship Council of China (2014-6), North University of China Science and Technology Project (20171449), North University of China Science and Technology Project (20171447).
References
- D. Min, W. Zhou and Y. Qing, J. Mater. Sci., 2017, 52(4), 2373–2383 CrossRef.
- A. Romo-Uribe, K. Santiago-Santiago and A. Reyes-Mayer, Eur. Polym. J., 2017, 89, 101–118 CrossRef.
- Y. Wang, S. K. R. Pillai and J. Che, ACS Appl. Mater. Interfaces, 2017, 9(10), 8960–8966 CrossRef PubMed.
- M. Raimondo, L. Guadagno and C. Naddeo, J. Mol. Struct., 2017, 1130, 400–407 CrossRef.
- G. Han, Z. Yang and X. X. Yang, Chin. J. Polym. Sci., 2016, 34(9), 1103–1116 CrossRef.
- N. Bai, G. Simon and K. Saito, RSC Adv., 2013, 3(43), 20699–20707 RSC.
- G. Postiglione, S. Turri and M. Levi, Prog. Org. Coat., 2014, 78, 526–531 CrossRef.
- G. Deng, C. Tang, F. Li, H. Jiang and Y. Chen, Macromolecules, 2010, 43(3), 1191–1194 CrossRef.
- V. R. Sastri and G. C. Tesoro, J. Appl. Polym. Sci., 1990, 39(7), 1439–1457 CrossRef.
- C. E. Yuan, M. Z. Rong, M. Q. Zhang, Z. P. Zhang and Y. C. Yuan, J. Mater. Chem., 2011, 23, 5076–5081 CrossRef.
- Y. Zhengyang, F. Libang and C. Changsheng, Acta Polym. Sin., 2016,(11), 1579–1586 Search PubMed.
- Z. Mingqiu and R. Minzhi, Acta Polym. Sin., 2012,(11), 1183–1199 CrossRef.
- P. Mineo, V. Barbera and G. Romeo, J. Appl. Polym. Sci., 2015, 132(30), 42314 CrossRef.
- V. Froidevaux, M. Borne and E. Laborbe, RSC Adv., 2015, 5(47), 37742–37754 RSC.
- X. Kuang, G. Liu and X. Dong, Polym. J., 2016, 84, 1–9 Search PubMed.
- C. Cai, Y. Zhang and X. Zou, et al., RSC Adv., 2017, 7, 46336 RSC.
- T. S. Coope, D. H. Turkenburg and H. R. Fischer, et al., Smart Mater. Struct., 2016, 25, 084010 CrossRef.
- Q.-T. Li, M.-J. Jiang and G. Wu, et al., ACS Appl. Mater. Interfaces, 2017, 9, 20797–20807 CrossRef PubMed.
- S. Dello Iacono, A. Martone and G. Filippone, et al., AIP Conf. Proc., 2016, 1736(1), 020075 CrossRef.
- J. Li, G. Zhang and L. Deng, et al., J. Appl. Polym. Sci., 2015, 132(26), 12467 Search PubMed.
- X. Kuang, G. Liu and X. Dong, et al., J. Polym. Sci., Part A: Polym. Chem., 2015, 53, 2094–2103 CrossRef.
- D. H. Turkenburg and H. R. Fischer, Polym. J., 2015, 79, 187–194 Search PubMed.
|
This journal is © The Royal Society of Chemistry 2018 |
Click here to see how this site uses Cookies. View our privacy policy here.