DOI:
10.1039/C8RA03296C
(Review Article)
RSC Adv., 2018,
8, 22710-22728
Recent advances in hydrophilic modification and performance of polyethersulfone (PES) membrane via additive blending
Received
17th April 2018
, Accepted 25th May 2018
First published on 20th June 2018
Abstract
The blending of additives in the polyethersulfone (PES) matrix is an important approach in the membrane industry to reduce membrane hydrophobicity and improve the performance (flux, solute rejection, and reduction of fouling). Several (hydrophilic) modifications of the PES membrane have been developed. Given the importance of the hydrophilic modification methods for PES membranes and their applications, we decided to dedicate this review solely to this topic. The types of additives embedded into the PES matrix can be divided into two main categories: (i) polymers and (ii) inorganic nanoparticles (NPs). The introduced polymers include polyvinylpyrrolidone, chitosan, polyamide, polyethylene oxide, and polyethylene glycol. The introduced nanoparticles discussed include titanium, iron, aluminum, silver, zirconium, silica, magnesium based NPs, carbon, and halloysite nanotubes. In addition, the applications of hydrophilic PES membranes are also reviewed. Reviewing the research progress in the hydrophilic modification of PES membranes is necessary and imperative to provide more insights for their future development and perhaps to open the door to extend their applications to other more challenging areas.
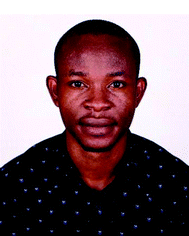 Tunmise Ayode Otitoju | Tunmise Ayode Otitoju received his B. Tech. in Industrial Design (Ceramics) from the Federal University of Technology, Akure, Nigeria, in 2011. He then obtained his M. Sc. in Environmental Management (Waste and Wastewater treatment) from the Universiti Malaysia Sarawak in 2015. He joined as a PhD student in Chemical Engineering (Membrane Technology) under the supervision of Professor Dr Abdul Latif Ahmad at the Universiti Sains Malaysia. His research areas of interest includes composite membrane (ceramic, polymeric, and inorganic membrane) for fouling mitigation, water and wastewater treatment, wastewater engineering. |
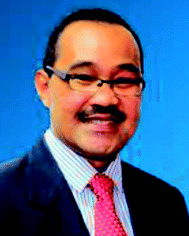 Abdul Latif Ahmad | Abdul Latif Ahmad is presently a professor in the School of Chemical Engineering at the Universiti Sains Malaysia. He obtained his B. Eng. in Chemical Engineering from the University of Wales, Swansea, UK, in 1990, He obtained his M.Sc. in Chemical Engineering from the University of Wales, Swansea, UK, in 1991. He thereafter received his PhD in Chemical Engineering from the University of Wales, Swansea, UK in 1995. He was the Dean of School of Chemical Engineering, USM, from 2005–2010 and Research Dean, Science Fundamental Platform from 2010–2012. His research areas includes membrane technology, wastewater engineering, separation process, adsorption technology. |
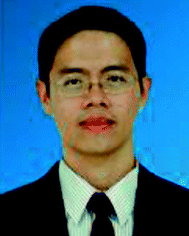 Boon Seng Ooi | Boon Seng Ooi is presently an associate professor in the School of Chemical Engineering at the Universiti Sains Malaysia. He did his B. Eng. in Chemical Engineering (Bioprocess Engineering) from Universiti Sains Malaysia in 1999. He then obtained his PhD in Chemical Engineering (Membrane Technology) from the Universiti Sains Malaysia in 2005. His current research areas includes functional polymeric membranes, composite membranes for fouling mitigation, product recovery from waste using membrane technology, and integrated and energy efficient membrane technology for water reclamation. |
Introduction
Polyethersulfone (PES) is a recognized polymeric material, which is widely employed in the fabrication of membranes for various applications. Due to its high glass transition temperature (225 °C), and amorphous and transparent properties, PES possesses a high mechanical and hydrolytic stability, thermal and chemical resistance, and outstanding oxidative characteristics,1 making it ideal for the preparation of asymmetric membranes with different surfaces and pore sizes.1–3 Asymmetric PES membranes are generally prepared via a phase-separation method. The final membrane properties and performance are influenced by the composition (additives, concentration, and solvent), temperature of the doping solution, the non-solvent or the mixture of non-solvents, and the coagulation bath or the environment.4 The risk of the fouling effect due to the high hydrophobicity of PES, especially in protein-contacting applications and aqueous filtrations, limits their wide applications.2,3 Numerous research studies have reported efforts to enhance the hydrophilicity of the PES membrane surface.1,5
Basically, the water contact angle (WCA) formed between the membrane–liquid boundary and liquid–gas tangent is generally employed to evaluate the hydrophilic properties of the membrane.6 Commercial PES membranes are hydrophobic in nature with high mechanical, chemical, and thermal stability.7 Usually, these membranes possesses high WCA values and are prone to solute adsorption from various feed streams. It has been well documented that membranes with hydrophilic surfaces are less prone to the fouling effect with microorganisms and organic substances due to: (i) a decreased interaction between the membrane surface and foulant, and (ii) no interaction of hydrogen bonds in the boundary layer between water and the membrane interface.8–10 The repulsion of water molecules away from the surface of the hydrophobic PES membrane is a spontaneous process with increasing entropy, and therefore foulant molecules have a tendency to dominate the boundary layer and adsorb onto the PES membrane surface. However, a modified PES membrane with a hydrophilic chain and high surface tension can enhance the formation of hydrogen bonds with the surrounding water molecules. This hydrogen bonding can reduce or prevent the adhesion of foulants on the surface of the PES membrane.11,12 The membrane WCA is related to the zeta potential, surface roughness, and functional groups.13,14 Ref. 15 and 16 demonstrated that an improved membrane hydrophilicity can be favored by increasing the density of the surface hydrophilic-group, including –NH2 and –OH.
Numerous studies on PES membranes have been carried out with the aim to enhance the hydrophilicity and performance, including through an improvement in their preparation process (blending) and by surface modification of the nascent membranes. In surface modification, a hydrophilic layer is formed on the existing PES membrane surface, which can then aid the prevention of contact between the solute and membrane surface, thus reducing the membrane fouling effect. The surface modification can be classified based on two categories, namely chemical or physical modification. In chemical modification, the PES membrane surface is modified through covalent bonding interactions. In this procedure, PES chains are first activated by chemical reaction, followed by the grafting with hydrophilic additives. The use of surface modification may render the hydrophilicity permanent, but may, however, lead to degradation of the PES chains on the membrane surface.17 In practice, these methods usually require caustic chemicals, which limits their wide use and long-term stability in membrane applications. Physical modification signifies that the hydrophilic modifiers exist on the PES membrane surface via physical interaction. Here, the blending approach is a versatile and convenient procedure under mild conditions to enhance the hydrophilicity and performance of PES membranes.18,19 Blending is a process in which two (or more) inorganic and/or organic materials are physically mixed to obtain the required properties on the membrane. This introduction can be achieved by adding polymer material and inorganic nanofillers into the casting solution. Table 1 presents the advantages and disadvantages of both approaches. Since most of these additives are hydrophilic in nature, they are able to increase the hydrophilicity of the resulting membranes and thus can reduce the fouling effects. Other advantages of blending with hydrophilic additives include an increase in the water flux (WF) due to the enlarged effective membrane surface area and the introduction of additional functional groups.20
Table 1 Advantages and disadvantages of incorporating polymer and inorganic additives in the PES membrane matrix
Membrane synthesis approach |
Advantages |
Disadvantages |
Blending with a polymer |
(a) Miscibility in common solvents |
(a) Tendency toward physical and/or chemical aging |
(b) Flexible to incorporate |
(b) Leaching during the preparation and operation process, which may reduce the efficiency |
|
(c) Poor compatibility in the polymer matrix |
Blending with an inorganic material |
(a) High chemical resistance |
(a) More expensive than equivalent polymeric ones |
(b) Improve thermal stability |
(b) Defect-free commercial-scale inorganic PES membranes are difficult to manufacture |
(c) The resultant membrane combines the advantages of the organic and inorganic parts |
(c) Stability of the doped form is a big issue due to its nano-size |
(d) Can be easily incorporated |
(d) Very expensive formulations |
(e) Provides an enhanced surface that allows multiple functional groups to be added on the membrane surface |
(e) Non-uniform dispersion of NPs in the polymer matrix |
|
(f) Aggregation phenomenon |
|
(g) Weak interaction with the polymer matrix |
|
(h) Leaching of NPs during the operation process |
|
(i) Uncontrollable pore size |
|
(j) Poor dissolution in various organic solvents |
Embedding polymer materials
In this approach, hydrophilic organic polymers are dissolved in PES solution. The materials most commonly used include polyvinyl pyrrolidone (PVP), chitosan (CS), polyamide, polyethylene oxide (PEO), and polyethylene glycol (PEG) derivatives due to their reasonable price and high compatibility with PES.21 Table 2 shows the progress reported in recent studies on polymeric addition in PES membranes.
Table 2 Progress of recent studies for the fabrication of hydrophilic PES–polymer blend membranes
Additive |
Additive loadings (wt%) |
Hydrophilic change (°) |
Ref. |
PEG |
2 |
∼70 to ∼57 |
22 |
PEG/PVP |
— |
85 to 59 |
23 |
PVP 40K |
4 |
71 to 47 |
24 |
PVP |
5 |
∼63 to ∼56 |
25 |
P31R1 |
5 |
∼63 to 44 |
25 |
PVP |
2 |
∼76 to ∼71 |
26 |
T904 |
5 |
∼63 to ∼52 |
25 |
PVP |
2 |
∼76 to ∼71 |
27 |
PA-6 |
2 |
∼76 to 68 |
26 |
PVP |
10 |
70 to 51 |
28 |
NPhthCs |
0.9 |
61 to 56 |
29 |
One general issue of blending with a polymer is the elution of this polymer and poor compatibility with the PES matrix.17 To address this issue, some researchers have looked into the use of amphiphilic copolymers as well as amphiphilic copolymers containing PES chains with hydrophobic parts as modifiers. Amphiphilic modifiers contain hydrophilic and hydrophobic properties, which means they are able to interact with the hydrophobic PES polymer, which is totally insoluble in water, and are also able to interact with hydrophobic PES polymers. The hydrophobic chains guarantees the compatibility with the host PES polymer, while the hydrophilic chains are enriched onto the membrane pore during phase inversion due to a segregation effect, thus, providing a high coverage of hydrated side chains anchored by a hydrophobic backbone entangled with the PES bulk that is water insoluble.30,31 Moreover, by controlling the ratio of hydrophobicity and enhancing the hydrophilicity during the membrane casting, desirable membrane performance properties can be achieved, such as a higher solute rejection, fouling resistance, and permeability.32 Table 3 show a summary of hydrophilic PES-amphiphilic copolymer blend membranes.
Table 3 Progress in recent studies in the fabrication of hydrophilic PES-amphiphilic copolymer blend membranes
Additive |
Synthesis of the additive |
Additive loadings (wt%) |
Hydrophilic change (°) |
Ref. |
Unit in grams |
PDMAEMA |
RAFT |
20 |
∼84 to 56 |
33 |
PNIPAAm |
RAFT |
20 |
∼84 to ∼71 |
33 |
F127-b-PDMAEMA |
ATRP |
15 |
72 to 53 |
34 |
PSf-g-POEM |
ATRP |
5 |
85 to 52 |
35 |
PS-b-PAA |
Free radical polymerization |
— |
∼70 to ∼50 |
36 |
MF-g-PEG6k |
Etherification |
0.36 |
— |
37 |
PMAAn–F127–PMAA |
Free radical |
1.92a |
∼56 to 39 |
38 |
PSA-PVP |
Condensation reaction of 5, 5′-thiobis (4-(3-nitrophenyl) thiazol-2- amine) in the presence of terephthalic acid |
1 |
∼76 to 68 |
27 |
PVP-b-PMMA-b-PVP |
RAFT |
5 |
73 to 60 |
39 |
PES-g-PSBMA |
RAFT and quaternization |
15 |
90 to 60 |
40 |
Generally, it has been well documented that these copolymers have better compatibility with the PES bulk, and could be used as modifiers to enhance the hydrophilicity, antifouling properties, and performance of PES membranes.41–44
Embedding inorganic materials
Apart from introducing polymers and copolymers, inorganic NPs are another promising modifier. The addition of inorganic NPs with the PES matrix has become an attractive approach for the fabrication of polymeric membranes and has captured much attention in recent times.45–50 Much of the bulk of the research has been carried out on the preparation of composite PES–inorganic membranes by the addition of inorganic NPs. For instance, the presence of dispersed inorganic NPs in the membrane matrix has been reported to improve the membrane performance and properties, particularly by: (a) increasing the permeability due to the larger effective membrane surface area of NPs; (b) inducing a membrane with the functional properties of the nanomaterials;20 (c) enhancing the mass transfer in the membrane pre-evaporation process;51 (d) improving a membrane's hydrophilicity as well as fouling resistance properties;46,52 (e) improving the thermal and mechanical properties.53–58 To date, many types of inorganic materials have been incorporated as additives in the PES matrix, including titanium dioxide, silicon dioxide, carbon nanotubes, halloysite nanotubes, manganese oxide, cellulose nanocrystals, graphene oxide, silver NPs, zirconia, zinc oxide, alumina, and metal–organic frameworks. However, there are two ways to introduce these NPs into the PES membrane during the preparation process: blending them in a coagulation bath or in the polymer solution. Compared to the blending of nanofillers in a coagulation bath, blending the nanoparticles in the polymer solution has been the dominant method. The discussion below introduces the incorporation of inorganic additives in the PES matrix.
Embedding titanium dioxide NPs
Titanium dioxide (TiO2) has been the major focus of quite a significant number of studies in recent and past years, due to its photocatalytic effects, which aid in killing bacteria and decomposing organic chemicals, relative cheapness, chemical stability, optical property, and non-toxicity.49,59–65 As one of the most investigated NPs, when TiO2 NPs are dispersed in the PES matrix, the membrane hydrophilicity and antifouling ability can be enhanced. On this basis, lots of effort has been devoted to investigating the effect of TiO2 NPs to improve the PES membrane hydrophilicity. For instance, ref. 66 introduced TiO2 to produce PES–TiO2 membranes and found that modification with 0.2 wt% led to an improved hydrophilicity as WCA decreased from 75.2° to 66.4°. Another study by ref. 67 showed a decrease in WCA from 72.2° to 57.4° when the content of TiO2 was 1 wt% in the PES matrix. The result by ref. 68 showed an improved hydrophilicity of 54.2° when the content of NPs was 0.1 wt% as compared to an unmodified membrane (65.5°). Ref. 69 observed a significant reduction in WCA from 71.9° to 59.6° when the content of TiO2 NPs was 2 wt%. Ref. 70 also reported a PES/TiO2 composite membrane that resulted in an enhanced hydrophilicity of 44.1° upon the introduction of 0.4 wt% TiO2 as compared to the neat membrane of 52.3°. Ref. 71 introduced a mechanically modified TiO2 into the PES matrix and observed a reduction in WCA from 64° to 56° when the concentration of the modified NPs was increased to 2 wt%. Furthermore, the hydrophilicity was improved to 50° when mechanically and chemically modified TiO2 was introduced. This result was similar to that reported in the study by ref. 69, who observed an improved hydrophilicity from 71.9° to 62.3° when the content of a mechanically and chemically modified TiO2 was 2 wt%.
Embedding silica (SiO2) NPs
The addition of SiO2 NPs has been investigated intensively and proven ideal as an additive for PES membranes due to their many useful properties, such as fine suspendability in aqueous solution, relatively environmentally inert, being thermally and chemically stable with a large surface area (SA), and highly miscible.72 A significant number of works have been reported on their addition into the PES matrix and they have been found to be a promising additive for enhanced hydrophilic PES membranes. For example, ref. 73 introduced a SiO2/PES membrane, which showed a significant reduction in WCA from 78.6° to 58.1° when the SiO2 content was 2 wt% in the matrix. Ref. 74 prepared a PES nano-SiO2 membrane by introducing monodisperse silica spheres in the PES matrix, which led to an improvement in hydrophilicity with WCA decreasing from 52.4° to 45.7° when the content of NPs was 0.3 wt%. Ref. 75 synthesized a series of amine-functionalized mesostructured silica (SBA-15) particles and then incorporated these in the PES matrix. The synthesis of the different organically functionalized SBA-15 particles was similar to that for the conventional SBA-15 except for the addition of a certain amount of selected organosilanes 1 h after adding tetraethyl orthosilicate (TEOS). In the case of the amino-functionalized silica materials, [3-(2-aminoethylamino) propyl] trimethoxysilane (AEAPTMS) and (3-aminopropyl) trimethoxysilane (APTMS) were used as an organosilane with an organosilane/TEOS molar ratio of 15%. In the case of the carboxylic-functionalized silica materials, carboxyethylsilanetriol sodium salt (CES) was used as a carboxylic group source with organosilane/TEOS molar ratios of 15% and 30%. The WCA of the neat membrane and the PES/mesostructured SBA-15 were 70.3° and 64.7°, respectively. However, upon the introduction of 0.6 wt% SBA-15/CES-15, SBA-15/AEAPTMS-15, and SBA-15-APTMS-15, the WCA decreases to 63°, 61.7°, 58.1°, and 55°, respectively. Ref. 76 prepared a hydrophilic hollow mesoporous silica sphere (HMSS) prepared via a surfactant-assembly sol–gel route, which was then blended into PES membranes to fabricate a mixed matrix membrane. The WCA of the pure PES membrane was 76.8°, indicating a strong intrinsic hydrophobicity of the pure PES membrane. However, with the increase in HMSS loading (up to 1.5%), the WCA of the PES composite membrane decreased to 63.8°. Ref. 77 embedded a N-halamine-modified SiO2 in the PES matrix to prepare SiO2@N-Halamine/PES MMM. Modified SiO2 NPs grafted with N-halamine were obtained via a three-step reaction process (Fig. 1). Their result showed an improved hydrophilicity with a WCA of 70.6° using 5 wt% of modified NPs, which was lower than the neat membrane WCA of 90.7°.
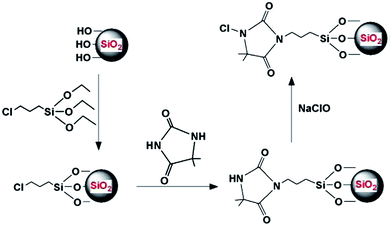 |
| Fig. 1 Basic principles of the reactions with modified SiO2.77 | |
Embedding zinc oxide NPs
Zinc oxide (ZnO) is another compound that has excellent electrical, optical, chemical, and mechanical properties, including antimicrobial activity.78–80 With its low cost and increased surface-to-volume ratio, ZnO is a potential NP that could meet the demand for the fabrication of a lower-cost and efficient membrane. For example, ref. 81 prepared a PES ZnO HF membrane by introducing ZnO NPs in the PES matrix, which led to an improvement in the hydrophilicity, with WCA decreasing from 70° to 58° when the content of NPs was 3.62 wt%. Ref. 82 observed a significant reduction in WCA from 79.92° to 62.92° when the content of ZnO NPs was 0.3 wt%. Ref. 83 also observed a significant reduction in WCA from 71.4° to 57.7° when the content of ZnO NPs was 10 wt%. Ref. 84 prepared and compared two nano-ZnO (ZnO NPs and ZnO nanorod) and then introduced them in the PES matrix. The ZnO nanoparticles were synthesized by co-precipitation technique, while ZnO nanorods were synthesized by the sol–gel method. In their study, the hydrophilicity of the ZnO-blended membranes rose to 60° at 0.1 wt% and reached 54° when the ZnO NPs were replaced with ZnO nanorods as compared to the neat membrane of 77.9°. Ref. 85 synthesized a chitosan (CS)-modified ZnO NPs using chemical precipitation prior to doping in the PES matrix to prepare a PES/CS-ZnO NPs membrane, which resulted to an improved hydrophilicity with the WCA declining from 60.73° for the neat membrane to 40.33° when the content of CS-ZnO was 15 wt%. Ref. 86 presented PES ultrafiltration membranes blended with different contents of the CuO/ZnO nanocomposite (CZN). In their study, CZN was prepared through a facile one-step homogeneous co-precipitation method at a low temperature (Fig. 2). Their results showed an improve hydrophilicity of 65.5° against 70.2° for the neat membrane at an optimal content of CZN (0.2 wt%).
 |
| Fig. 2 Schematic illustration of the formation process of CZN.87 | |
Embedding zirconium dioxide NPs
Zirconium dioxide (ZrO2), or zirconia, is a white crystalline oxide of zirconium with excellent chemical stability, melting point, good mechanical properties, and strong anti-corrosion. Zirconia membranes are known to be chemically more stable than alumina and titania PES membranes, and are more suitable for liquid phase applications under harsh conditions.88 For instance, ref. 70 presented ZrO2-entrapped membranes, which showed a slight reduction in WCA from 52.23° to 48.86° when the content of NPs was 0.4 wt%. In a study by ref. 89, hydrous ZrO2 sol was synthesized by the addition of an anion-exchange resin in N,N-dimethylformamide solvent containing zirconyl chloride and then doped in the PES matrix to prepare a ZrO2/PES composite membrane, which significantly led to a significant reduction in WCA from 73.6° to 52.3° at an optimal content of 1 wt%.
Embedding aluminum oxide NPs
Similar to other metal oxide NPs, aluminum oxide (Al2O3) NPs have attracted great attention in membrane technology for the development of nanocomposite (NC) PES membranes with enhanced properties. Ref. 90 introduced Al2O3 to produce PES/Al2O3 membranes and found that modification with 0.1 wt% led to an improved hydrophilicity as the WCA decreased from 74.1° to 64.3°. Another study by ref. 70 showed a decrease in WCA from 52.3° to 37.8° when the content of Al2O3 was 0.4 wt% in the PES matrix.
Embedding iron oxide-based nanoparticles
The unique features of iron oxide-based nanoparticles (Fe-NPs), mainly magnetite (Fe3O4), have encouraged many researchers to investigate these engineered magnetic NPs in the synthesis of PES composite membranes. The addition of Fe-NPs has been extensively introduced in the PES matrix to produce composite membranes. For instance, ref. 91 prepared a PES/Fe-NP HF membrane by introducing magnetite NPs in the PES matrix, which led to an improvement in hydrophilicity with the WCA decreasing from 62.22° to 49.27° when the content of NPs was 2 wt%. Ref. 92 also presented four sets of PES/NC membranes, such as trisodium citrate-treated Fe3O4, Fe3O4/SiO2, Fe3O4/SiO2-amine, and Fe3O4/SiO2-metformine (Met). Fe3O4/SiO2 was prepared by the Stober method, while the surface functionalization of Fe3O4/SiO2 NP was achieved by using APTES as a silylation agent (Fig. 3). The WCA of the neat membrane was 78°. However, upon the introduction of 0.1 wt% Fe3O4/SiO2-amine, 0.1 wt% trisodium citrate-treated Fe3O4, 0.1 wt% Fe3O4/SiO2-Met, or 0.1 wt% Fe3O4/SiO2, the WCA decreased to 75°, 72°, 69°, or 67°, respectively.
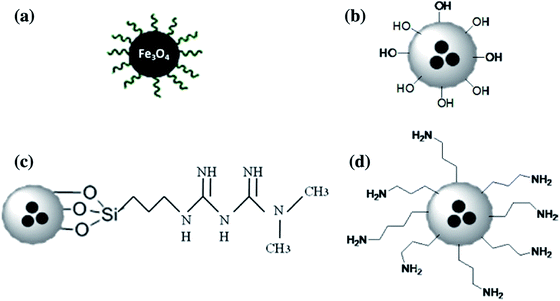 |
| Fig. 3 Schematic of (a) Fe3O4 treated with trisodium citrate, (b) Fe3O4/SiO2, (c) Fe3O4/SiO2-Met, and (d) Fe3O4/SiO2-amine NPs.92 | |
Ref. 93 reported six sets of PES/NC membranes, such as magnetic-treated Fe3O4 (m-Fe3O4), magnetic-treated polyaniline-coated Fe3O4 (m-PANI/Fe3O4), magnetic-treated Fe3O4-coated multi-walled carbon nanotubes (m-MWCNT/Fe3O4), untreated Fe3O4, PANI-coated Fe3O4 (PANI/Fe3O4), and Fe3O4-coated MWCNT (MWCNT/Fe3O4) membranes. For magnetic field induced casting, the casting was carried out under a magnetic field (0.1 Tesla) at a distance of 4 cm (Fig. 4). The WCA of the neat membrane was 71.45°. However, upon the introduction of 0.1 wt% MWCNT/Fe3O4, 0.1 wt% m-MWCNT/Fe3O4, 0.1 wt% untreated Fe3O4, 0.1 wt% m-Fe3O4, 0.1 wt% PANI/Fe3O4, or 0.1 wt% m-PANI/Fe3O4, the WCA decreased to 67.06°, 60.24°, 56.16°, 53.38°, 51.53°, or 51.12°, respectively.
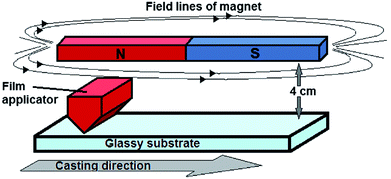 |
| Fig. 4 Scheme of casting under a magnetic field.93 | |
Embedding silver nanoparticles
Within the wide range of commercially available nanoscale materials, silver nanoparticles (AgNPs) have also received a great deal of attention. AgNPs have unique properties (such as extremely large surface-to-volume ratio, antimicrobial, optical, and electrical properties), making the NP able to serve as a sustained local supply of Ag+ ions in membranes, and so it can prevent bacterial and solute adhesion onto the membrane surface.94–96 Several preparation techniques have been reported for the synthesis of silver NPs; notable examples include photochemical methods, gamma irradiation, laser ablation, microwave processing, electron irradiation, biological synthetic methods, and chemical reduction.95 The effects of AgNPs on the final membrane hydrophilicity have been investigated in many studies. A study by ref. 97 showed a decrease in WCA from 71° to 41° when the content of AgNP was 0.03 wt% in the PES matrix. Ref. 98 fabricated antibacterial PES/Ag nanocomposite membranes and reported an improvement in surface hydrophilicity from 59.85° to 40.29° when the AgNP concentration was 0.5 wt%. In another study by ref. 99, n-Ag NPs were prepared by a bacteria-mediated biosynthesis method (Fig. 5) and then introduced to produce the resulting composite membrane. The resulting PES membrane showed an improved hydrophilicity of 65° upon doping with 1.5 wt% NPs as compared to the neat membrane showing a value of 88°. This was associated as being due to the higher affinity or intrinsic nature of n-Ag with the water molecules.
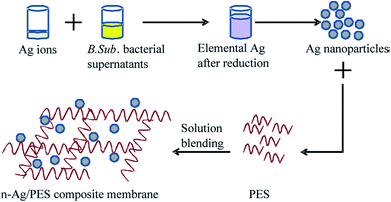 |
| Fig. 5 Schematic representation of the preparation of PES/n-Ag composite membranes.99 | |
Embedding graphene oxide NPs
Graphene oxide (GO), a two-dimensional carbon material, has received tremendous attention due to the presence of abundant O2-containing functional groups (such as carboxyl, epoxy, hydroxyl, and carbonyl groups), fantastic chemical stability, high strength, superior electron transport, low thickness, high flexibility and a negatively charged surface, innocuity, high surface area, and good miscibility with polymers.100–113 The existence of these groups makes GO possess good hydrophilicity, is easy to be modified, and has the capability of dispersion in water to yield a prolonged, stable suspension.114 All these factors make it more appropriate for the hydrophilic modification of PES membranes.115,116 On this basis, a large amount of work has been devoted to developing GO/PES NC membranes and their summaries are shown in Table 4.
Table 4 Progress in recent studies in the fabrication of hydrophilic PES/GO nanocomposite membranes
Additive |
Filler loadings (wt%) |
Hydrophilic change (°) |
Ref. |
GO |
0.3 |
72 to ∼55 |
117 |
GO/T904 |
0.3 |
72 to 54 |
117 |
GO NS |
0.5 |
65 to 53 |
118 |
GO/PAA |
1 |
∼71 to 58 |
119 |
UiO-66@GO |
3.0 |
∼86 to 60 |
120 |
GO |
3.0 |
∼86 to 72 |
120 |
Partially rGO/TiO2 |
0.1 |
∼66 to 56 |
68 |
GO |
0.1 |
∼66 to ∼59 |
68 |
GO–ZnO |
0.1 |
∼78 to ∼54 |
121 |
HPEI–GO |
5 |
∼86 to 63 |
114 |
Embedding CNTs
Carbon nanotubes (CNTs) are a member of the fullerene structural family and consist of six-membered carbon rings in the honeycomb lattice relative to the axis of the nanotubes (NT).122 The pioneer discovery of CNTs by Lijima123 has opened up new directions for many applications. CNTs have the ability to interact and alter the physico-chemical properties of the membrane.124 This property coupled with their high specific surface area with low density, exceptional mechanical properties, nanoscale dimensions and highly precise diameters, high thermal stability, very low frictional coefficients on their internal surface, high strength-to weight ratio, formation of highly porous structures, and chemical stability makes CNTs a promising candidate for complementing or substituting conventional NPs in the fabrication of new generation nanocomposite membranes.125–138 The excellent mechanical properties of CNTs arise from the presence of C–C bonds in the graphite layer, which are most probably the strongest chemical bonds known in nature. CNTs can be synthesized either as a series of shells of different diameters spaced around a common axis, called multi-walled carbon nanotubes, MWCNTs (consisting of up to 10–100 carbon shells), or as singular tubes, called single-walled carbon nanotubes (SWCNTs).139 The former are of particular interest over the latter due to their availability in larger quantities and relatively low cost as a result of their more advanced stage in commercial production.
The most crucial problem when using CNTS is the poor dissolution and dispersion of synthesized CNTs in various organic solvents and different polymers as well as their weak interaction with the polymer matrix.140–143 Moreover during CNTs preparation, the presence of metal catalytic particles and amorphous carbon, as impurities, could add an additional burden to the intended application.144 These factors are important in the utilization of additives in polymer composites as well as CNTs.145,146 Therefore, the purification and functionalization of CNTs could be established to negate the hydrophobic nature of CNTs and to broaden their promising scope. For this reason, different linking groups, e.g., –NH2, –SO3H, –COOH, –OH, or –CONH2 could be introduced to the CNTs surface to facilitate linking different metal clusters to the nanotubes surface via polymer wrapping, covalent attachment (grafting), and non-covalent attachment (adsorbing).122,146–159 The amine (NH2) group has a wealth of chemistry and high reactivity with many chemicals, such as polymers.160–162 After modification, they become soluble in different solvents, as well as contain functional groups, which turn them into a multidisciplinary materials in other applications. The functionalization by chemical oxidation of CNTs is the most commonly used method, which breaks the sp2 hybrid carbon bonds on the sidewalls, and attaches carboxyl/hydroxyl groups to the CNTs.163 Functionalized CNTs can enhance the properties of PES membranes by increasing the hydrophilicity and surface charge of the membrane top layer,147–151,164,165 which will influence the permeability and reduce fouling.147–151,164–169 An increase in the surface charge will raise the Donnan exclusion effect and electrostatic interactions, which will result in an improved rejection of salt and an increase in hydrophilicity, which will provide better fouling resistance.170,171 To date, several authors have shown the successful preparation of CNT-blended PES membranes. The summary of their results are presented in Table 5.
Table 5 Progress in recent studies in the fabrication of hydrophilic PES/CNTs nanocomposite membranes
Additive |
Treatment |
Filler loadings (wt%) |
Hydrophilic change (°) |
Ref. |
CNTs (20 nm) |
— |
0.1 |
∼63 to ∼55 |
172 |
CNTs (40 nm) |
— |
0.1 |
∼63 to 56 |
172 |
Carboxyl-functionalized SWCNT |
— |
0.025 |
∼70 to ∼62 |
173 |
PCA-functionalized MWCNT |
In situ polymerization reaction |
0.1 |
75 to 49 |
174 |
PAA-functionalized MWCNT |
In situ polymerization reaction |
0.1 |
75 to ∼58 |
174 |
SiO2 |
— |
3 |
67 to ∼55 |
175 |
Polyacrylamide-functionalized MWCNT |
In situ polymerization reaction |
0.1 |
75 to ∼63 |
174 |
MWCNT |
— |
0.1 |
75 to 65 |
174 |
NH2-MWCNTs |
Covalent-functionalization |
0.045 |
∼65 to ∼56 |
176 |
PCL modified MWCNTs |
With Sn(Oct)2 |
3 |
∼67 to 57 |
177 |
Amine-functionalized MWCNTs |
Strong acids (H2SO4/HNO3) and 1,3-phenylenediamine |
1 |
69 to ∼52 |
1 |
MWCNT-OH |
— |
0.8 |
∼77 to ∼74 |
178 |
MWCNT-COOH |
— |
0.8 |
∼77 to 59 |
178 |
Acid-oxidized MWCNTs |
HNO3/H2SO4 |
0.04 |
66 to 63 |
179 |
MWCNTs |
HNO3/H2SO4 |
2 |
∼71 to ∼60 |
168 |
MWCNTs |
— |
2 |
∼65 to ∼47 |
180 |
Acid-functionalized MWCNT |
PVP |
0.1 |
∼88 to 52 |
181 |
Functionalized MWCNT |
Non-covalent modification with SLS |
2 |
∼79 to 51 |
182 |
Acid-oxidized MWCNTs coated by anatase TiO2 |
Precipitation of TiCl4 precursor |
0.1 |
66 to ∼63 |
183 |
ZnO coated MWCNTs |
Coating |
0.5 |
68 to 57 |
184 |
PAA grafted MWCNTs |
In situ polymerization of AA in aqueous solution in the presence of KPS as initiator and EG as cross-linker |
0.1 |
∼73 to ∼57 |
185 |
Ag-coated MWCNTs |
Ag |
0.9 |
64 to 51 |
186 |
MWCNTs-PANI |
In situ polymerization in the presence of aniline and APS |
2 |
73 to ∼53 |
187 |
Fe–Ag/functionalized MWCNT |
Acid and then Fe and Ag NPs |
1 |
75 to ∼44 |
188 |
TETA-MWCNTs |
— |
0.4 |
∼68 to 60 |
189 |
Acid-functionalized MWCNTs |
HNO3 and H2SO4 |
0.5 |
∼70 to ∼57 |
190 |
Embedding halloysite nanotubes
Halloysite nanotubes (HNTs) are a kind of naturally occurring aluminosilicate (Al2Si2O5(OH)4·2H2O) with a hollow nano-tubular structure,191,192 regular open-ending pores, as well as a great deal of hydroxyls on their surface.193 HNTs can easily be dispersed in a polymer matrix, even at high loading due to their tubular shape, low density of hydroxyl functional groups, and well-crystallized structure.194–197 In contrast with other NPs, HNTs can be obtained easily and are much cheaper.198,199 HNTs own a low charge density, which means they cannot affect the membrane potential when they are embedded into the polymer matrix.193 Recently, HNTs have been used as a new type of filler for PES to improve the properties and performance of the composites. For instance, ref. 200 synthesized a HNTs loaded with copper ions (Cu2+-HNTs) by the chemical modification of HNTs, which were then incorporated in the PES matrix to produce Cu2+-HNTs/PES MMM, which significantly resulted in an improvement of membrane hydrophilicity, with WCA decreasing from 84.9° to 69.8° for 3 wt% of Cu2+-HNTs. Ref. 193 presented a sulfonated halloysite nanotubes (HNTs-SO3H)/PES membrane. To prepare highly cross-linked HNTs-SO3H, styrene was grafted onto HNTs surface via distillation–precipitation polymerization and then sulfonated with concentrated sulfuric acid. Fig. 6 shows a schematic illustration of the overall preparation process of HNTs-SO3H. The control PES membrane presented the highest contact angle of 83.5°, which was decreased to 58.3° when 3 wt% HNTs-SO3H was introduced.
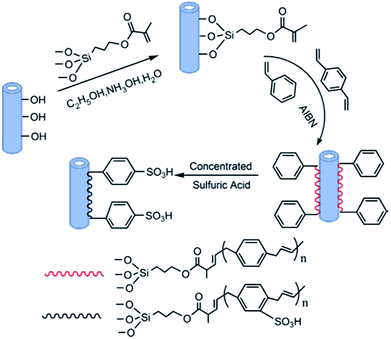 |
| Fig. 6 Schematic illustration of the overall preparation process of HNTs-SO3H.193 | |
In another study by ref. 201, sodium 4-styrene sulfonate was grafted onto HNTs surfaces via surface-initiated atom transfer radical polymerization, as shown in Fig. 7, which was then introduced in the PES matrix to prepared negatively charged nanofiltration membranes. WCA was observed to decrease from 83.5° to 56.6° at 3 wt%.
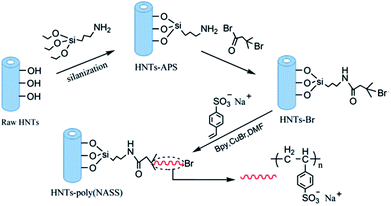 |
| Fig. 7 Preparation process of sodium 4-styrene sulfonate grafted onto HNTs surface.201 | |
Ref. 202 reported a PES hybrid membrane containing HNTs grafted with 2-methacryloyloxyethyl phosphorylcholine (MPC). Fig. 8 presents the preparation process of HNTs-MPC via reverse atom transfer radical polymerization. The contact angle of the membrane decreased with the addition of HNTs-MPC. The WCA value was reduced from 88.4° to 66.1° at 3 wt%.
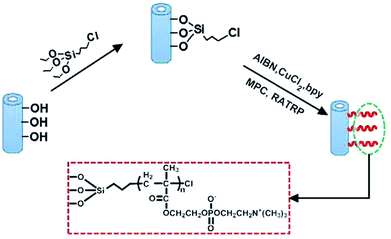 |
| Fig. 8 Preparation process of HNTs-MPC via reverse atom transfer radical polymerization.202 | |
Ref. 203 introduced HNTs-chitosan-Ag nanoparticles (HNTs-CS@Ag) into the PES matrix. Prior to blending, the HNTs-CS@Ag were synthesized by chemically modifying HNTs with chitosan, and then mixing with silver nitrate for complexing the silver ions, and finally the silver NPs were formed using sodium tetrahydroborate as a reducing agent. Fig. 9 presents the reaction principle for preparing the HNTs-CS@Ag NPs. The hybrid membranes were shown to be more hydrophilic, with the optimum membrane displaying the lowest contact angle of 55° when the content of HNTs-CS@Ag amounted to 3 wt%.
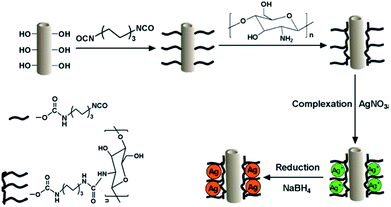 |
| Fig. 9 Reaction principle for preparing HNTs-CS@Ag NPs.203 | |
Ref. 204 presented polyethersulfone (PES) ultrafiltration membrane by incorporating dextran grafted HNTs (HNTs-dextran). Fig. 10 presents the basic reactions of the modified HNTs. The results indicated that the surface hydrophilicity of the membranes was significantly improved after adding HNTs-dextran. The WCA of the pristine PES membrane amounted to 90.8°, while the WCA of the hybrid membrane with the modified HNTs-dextran content of 3% was 58.3°.
 |
| Fig. 10 Basic principles of the reactions of the modified HNTs.204 | |
Embedding metal–organic frameworks
Metal–organic frameworks (MOFs) are organic–inorganic hybrid solids with infinite, uniform framework structures built from inorganic metal (or metal-containing cluster) nodes and organic linkers.205–208 MOFs are zeolite-like structures but they do not have the limitations of zeolites in terms of the material's chemistry. MOFs are recently attracting a lot of attention as potential additive materials for MMMs, owing to their extraordinary porosity (as high as 50% of the crystal volume), high surface area (ranging from 1000 to 10
000 m2 g−1), affinity for certain molecules, capability for functionalization, low density (0.2–1 g cm−3), tunable chemical composition, and flexible structure.209–212 MOFs have regular and highly harmonic pore structures and they play a very vital role in increasing the hydrophilic property of the membrane.213–223
To date, different types of MOFs, including zeolitic imidazolate framework (ZIF), ZIF-8, [Zn(oba)(4-bpdh)0.5]·(DMF)1.5 (TMU-5), UiO-66, matériauxs de l'Institut Lavoisier, have been developed and introduced in the PES matrix to prepare a MMM. Their potentials have been well recognized both experimentally and computationally.120,224–230 The emerging zirconium MOFs (Zr-MOFs) has exhibited exceptionally high chemical and thermal stability.231 Ref. 224 reported a novel hydrophilic PES/TMU-5 UF membrane synthesized by blending with TMU-5. The growth of TMU-5 upon silk fiber was achieved by sequential dipping in alternating baths of aqueous Zn(NO3)2·6H2O and DMF solution of 4-bpdh and (H2oba) under an ultrasound bath. They found that upon the addition of 0.1 wt% NPs, the hydrophilicity was enhanced, with WCA declining from 67.2° to 57.5°. In another study by ref. 225, a two-dimensional zeolitic imidazolate framework with a leaf-shaped morphology (ZIF-L) was synthesized in zinc salt and 2-methylimidazole aqueous solution and then doped in the PES matrix to prepare the MMM. Upon the introduction of 0.5 wt% loading of NPs, the WCA declined slightly to 62.72° as compared to the neat membrane of 67.72°.
Other inorganic materials
Ref. 232 synthesized hydrous manganese oxide (HMO) from the oxidation of manganous ions by permanganate and then impregnated them in the PES matrix which yielded a WCA of 27.2° at 1.5 wt% of HMO as compared to the nascent membrane of 69.5°. Ref. 233 embedded mesoporous carbon nanoparticles (MCNs) to prepare a hydrophilic PES membrane, which resulted in a decreased WCA from 75° to 36° when the content of MCM was increased to 0.2 wt%. In a study by ref. 20, cellulose nanocrystals (CNCs) were incorporated into PES membranes, which resulted in an improved hydrophilicity from 66.2° to 51.3° at 1 wt% of CNC. In another study by ref. 234, chitosan nanobiopolymers (CS-NPs) were synthesized using tripoly phosphate and introduced in the PES matrix to prepare a nanobiopolymer composite membrane. The addition of 0.2 wt% nanopolymer caused a reduction of WCA from 73° to 65°. Ref. 235 incorporated aragonite precipitated calcium carbonate (A-PCC) from magnesium rich carbonate rock into the PES matrix to prepare a PES composite membrane. They observed a reduction in WCA from 72.3° to 62.5° when the content of the A-PCC was 3 wt%.
Applications of the hydrophilic PES membrane
With the increasing demand for functional hydrophilic membrane materials, a great deal of attention has been focused on the development of hydrophilic PES membranes. Due to their interaction with water, the use of a hydrophilic PES membrane has found use in various applications, such as desalination, water treatment, wastewater treatment, textile applications, and protein purifications. In fact, hydrophilic PES membrane modification via blending is a simple approach to overcoming the performance trade-off and minimizing membrane fouling. A significant number of works have shown that enhancing the hydrophilicity of the PES membrane will result in a reduction of membrane fouling as well as leading to performance improvement. Tables 6 and 7 show summaries of the applications of hydrophilic PES membranes.
Table 6 Summaries of the applications of hydrophilic PES-organic membranes
Additive |
Application (operating pressure) |
Performance of neat membrane {MR (m−1); PWF (L m−2 h−1); PF (L m−2 h−1); HP (L m−2 h−1); R (%); FRR (%); RFR (%)} |
Performance of composite membrane {MR (m−1); PWF (L m−2 h−1); PF (L m−2 h−1); HP (L m−2 h−1); R (%); FRR (%); RFR (%)} |
Ref. |
PSA-PVP |
Protein purification (4 bar) |
PWF: 12.3; PF: 9.5; FRR: 76; BSA R: 95.9 |
PWF: 244.2; PF: 57; FRR: 60.2; BSA R: 97.8 |
27 |
PA-6 |
Protein purification (4 bar) |
PWF: 7.1; BSA R: 92.4; FRR: N/A |
PWF: 80.7; BSA R: 98.5; FRR: 64.2 |
26 |
PEG |
Water treatment (1 bar) |
HP: 4.998; MR: 8.060 × 10−11 |
HP: 9.422; MR: 4.275 × 10−11 |
22 |
PVP |
Protein purification (4 bar) |
PWF: 7.1; BSA R: 92.4; FRR: (N/A) |
PWF: 166.5; BSA R: 95.6; FRR: 57 |
26 |
PVP |
Protein purification (4 bar) |
PWF: 12.3; PF: 9.5; FRR: 76; BSA R: 95.9 |
PWF: 277.4; PF: 63.6; FRR: 54.6; BSA R: 97.6 |
27 |
PEG-PVP |
Water treatment (2 bar) |
PWF: 2201.8 |
PWF: 18 899.1 |
23 |
PES-g-PDMAEMA |
Protein purification (2 bar) |
PWF: 18.76; R: 99 |
PWF: 126.7; R: 96.4 |
33 |
PEG |
Protein purification (1 bar) |
PWF: N/A; BSA R: N/A |
PWF: 76.7; BSA R: 99 |
236 |
PVP-b-PMMA-b-PVP |
Protein purification (0.05 bar) |
FRR: 50.6; PA: 19.3 |
FRR: 96.6; PA: 10 |
39 |
PVP |
Water treatment (1 bar) |
PWF: 64.34; R: 96.03 |
PWF: 108.09; R: 88.07 |
24 |
PES-g-PNIPAAm |
Protein purification (2 bar) |
PWF: 18.76; R: 99 |
PWF: 110; R: 97.5 |
33 |
PVP |
Wastewater treatment (1 bar) |
PWF: 2.2; BSA R: 88.9 |
PWF: 15.8; BSA R: 65 |
25 |
PES-b-PSBMA |
Protein purification (1 bar) |
PWF: 45.6; FRR: 49.3; BSA R: 76 |
PWF: 115; FRR: 84.2; BSA R: 80.7 |
40 |
P31R1 |
Wastewater treatment (1 bar) |
PWF: 2.2; BSA R: 88.9 |
PWF: 116.5; BSA R: 62.4 |
25 |
F127-b-PDMAEMA |
Protein purification (2 bar) |
PA: 13.2 |
PA: 34.3 |
34 |
T904 |
Wastewater treatment (1 bar) |
PWF: 2.2; BSA R: 88.9 |
PWF: 62; BSA R: 69.2 |
25 |
PVP |
Protein purification (2.5 bar) |
PWF: 67.6; PEG35k R: 99.2; PEG20k R: 98.1; PEG10k R: 97.9; PEG4k R: 93.5 |
PWF: 134.8; PEG35k R: 97.9; PEG20k R: 97.9; PEG10k R: 97.3; PEG4k R: 94.8 |
237 |
PSf-g-POEM |
Protein purification (1.5 bar) |
PA: 44.2; BSA R: 74; FRR: 51.7 |
PA: 22.3; BSA R: 0; FRR: 80.8 |
35 |
PVP |
Wastewater treatment (5 bar) |
PWF: 108.21; FRR: 38.8; COD R: 79.4; TDS R: 71.3 |
PWF: 59.2; FRR: 59; COD R: 84.4; TDS R: 78.5 |
28 |
PVP |
Water treatment (2 bar) |
PWF: N/A; PF: N/A; FRR: N/A; HA R: N/A |
PWF: 2439; PF: 266.5; FRR: 98.5; HA R: 89.4 |
238 |
MF-g-PEG6k |
Water treatment (1 bar) |
PWF: 60.7; FRR: 70.8 |
PWF: 164.7; FRR: 91.6 |
37 |
PVP |
Water treatment (0.2–0.3 bar) |
PWF: 128.26 |
PWF: 376.8 |
239 |
PMAAn–F127–PMAA |
Protein purification (1 bar) |
PWF: 180.8; BSA R: 96.75 |
PWF: 238.6; BSA R: 85.5 |
38 |
NPhthCs |
Water treatment (3–6 bar) |
BSA flux: 17.6; HP: 7.1; BSA R: 90 |
BSA flux: 55.2; HP: 26.8; BSA R: 86 |
29 |
Table 7 Summaries of the applications of hydrophilic PES–inorganic membranes
Additives |
Applications (operating pressure) |
Performance of neat membrane {PWF (L m−2 h−1); PF (L m−2 h−1); R (%); FRR (%); RFR (%)} |
Performance of composite membrane {PWF (L m−2 h−1); PF (L m−2 h−1); R (%); FRR (%); RFR (%)} |
Ref. |
CNTs |
Desalination (4 bar) |
PWF: 24.25; Na2SO4 R: 24.7 |
PWF: 52.86; Na2SO4 R: 71.71 |
172 |
Fe3O4 |
Water treatment (4 bar) |
Cu+ R: 19.5; PWF: 8.8 |
Cu+ R: 34.4; PWF: 16.8 |
92 |
CNTs |
Desalination (4 bar) |
PWF: 24.25; Na2SO4 R: 24.7 |
PWF: 38.91; Na2SO4 R: 87.25 |
172 |
TiO2 |
Water treatment (10 bar) |
PWF: 1.7 |
PWF: 8.2 |
66 |
Fe3O4–SiO2 |
Water treatment (4 bar) |
Cu+ R: 19.5; PWF: 8.8 |
Cu+ R: 40.7; PWF: 32.6 |
92 |
GO |
Protein purification (1 bar) |
PWF: 2; FRR: 26; BSA R: 88.6 |
PWF: 37; FRR: 58; BSA R: 95.3 |
117 |
TiO2 |
Wastewater treatment (6 bar) |
PWF: 21; DR23 R: 97 |
PWF: 33.4; DR23 R: 94.9 |
67 |
SWCNT |
Wastewater treatment (2 bar) |
FRR: 93.7; BPA R: 45.7; NPH R: 62.95; BPA flux: 30.5; NPH flux: 42 |
FRR: 96.8; BPA R: 45.2; NPH R: 59.2; BPA flux: 30.2; NPH flux: 39.5 |
173 |
PES/Fe3O4–SiO2-amine |
Water treatment (4 bar) |
Cu+ R: 19.5; PWF: 8.8 |
Cu+ R: 79.7; PWF: 14.3 |
92 |
TiO2 |
Wastewater treatment (5 bar) |
PWF: 23; FRR: 75.2; RG19 R: 92.9; RB21 R: 88.9; DY12 R: 61.4 |
PWF: 32.6; FRR: 87.4; RG19 R: 99; RB21 R: 73.2; DY12 R: 91.1 |
68 |
MWCNT |
Water treatment (4 bar) |
FRR: 44; PWF: 9 |
FRR: 95; PWF: 23 |
174 |
Fe3O4–SiO2-Met |
Water treatment (4 bar) |
Cu+ R: 19.5; PWF: 8.8 |
Cu+ R: 92.3; PWF: 27.8 |
92 |
Mechanically modified TiO2 |
Water treatment (1 bar) |
FRR: 83.33; PWF: 17.6 |
FRR: 51.85; PWF: 39.8 |
71 |
FeN |
Water treatment (1 bar) |
PWF: 6.1; Cu + R: 95; Zn2+ R: 95; Cu+ flux: 4.7; Zn2+ flux: 5.2 |
PWF: 24; Cu + R: 89.7; Zn2+ R: 87; Cu+ flux: 12.9; Zn2+ flux: 13.6 |
91 |
MWCNT |
Water treatment (4 bar) |
FRR: 44; PWF: 9 |
FRR: 67; PWF: 30.5 |
174 |
Mechanically and chemically modified TiO2 |
Water treatment (1 bar) |
FRR: 83.33; PWF: 17.6 |
FRR: 61.54; PWF: 54.9 |
71 |
GO-T904 |
Protein purification (1 bar) |
PWF: 2; FRR: 26; BSA R: 89.3 |
PWF: 245; FRR: 62; BSA R: 93.6 |
117 |
A-PCC |
Wastewater treatment (1.5 bar) |
PWF: 102; PF: 49.87; FRR: 61.8; oil R: 93.9 |
PWF: 180; PF: 102.15; FRR: 86.4; oil R: 99.8 |
235 |
Fe3O4 |
Water treatment (1–10 bar) |
PWF: 12.3; NaCl R: 15.3; MgSO4 R: 16.16 |
PWF: 86.2; NaCl R: 68; MgSO4 R: 82 |
83 |
Mechanically and chemically modified TiO2 |
Water treatment (1 bar) |
FRR: 60; PA: 33.5; PWF: 364.8 |
FRR: 84; PA: 22.6; PWF: 462.3 |
69 |
MWCNT |
Water treatment (4 bar) |
FRR: 44; PWF: 9 |
FRR: 76; PWF: 26 |
174 |
n-Ag |
Protein purification (1 bar) |
PWF: 25; FRR: 53.5; PF: 42.7; BSA R: 97.4 |
PWF: 64; FRR: 79.4; PF: 67.7; BSA R: 90.3 |
99 |
TiO2 |
Water treatment (1 bar) |
FRR: 60; PA: 33.5; PWF: 364.8 |
FRR: 57; PA: 37.5; PWF: 345.9 |
69 |
MWCNT |
Water treatment (4 bar) |
FRR: 44; PWF: 9 |
FRR: 53; PWF: 23 |
174 |
AgNP |
Water treatment (2–4 bar) |
PWF: 365 |
PWF: 327 |
97 |
SiO2@N-Halamine |
Water treatment (1 bar) |
PVA R: 96.2; PWF: 192.7; FRR: 87 |
PVA R: 94.8; PWF: 384.9; FRR: 96 |
77 |
Amine-functionalized MWCNT |
Desalination (4 bar) |
PWF: 13.6; Na2SO4 R: 52; FRR: 68.6; PA: 60.9 |
PWF: 23.7; Na2SO4 R: 65; FRR: 88.1; PA: 41 |
176 |
TMU-5 |
Water treatment (3 bar) |
PWF: 133.29; FRR: 24.47 |
PWF: 182.02; FRR: 98.74 |
224 |
Mesostructured SBA-15 |
Water treatment (3 bar) |
PWF: 181.4 |
PWF: 316.1 |
75 |
PCL modified CNT |
Desalination (8 bar) |
PWF: 28; Cd ions R: 8.7; FRR: 13.3; BSA flux: 4.3 |
PWF: 61; Cd ions R: 27; FRR: 11.1; BSA flux: 6.4 |
177 |
PES/mesostructured SBA-15/CES-15 |
Water treatment (3 bar) |
PWF: 181.4 |
PWF: 351.7 |
75 |
GO |
Wastewater treatment (4 bar) |
PWF: 8.2; FRR: 35; dye R: 90 |
PWF: 20.4; FRR: 90.5; dye R: 96 |
118 |
Mesostructured SBA-15-APTMS-15 |
Water treatment (3 bar) |
PWF: 181.4 |
PWF: 356.8 |
75 |
ZIF-L |
Water treatment (1 bar) |
PWF: 215; FRR: 72 |
PWF: 378; FRR: 82 |
225 |
F-MWCNTs |
Protein purification (3 bar) |
PWF: 124; PF: 14.5; BSA R: 86.5; FRR: 27 |
PWF: 184; PF: 33.2; BSA R: 81; FRR: 46 |
1 |
Mesostructured SBA-15/AEAPTMS-15 |
Water treatment (3 bar) |
PWF: 181.4 |
PWF: 595.8 |
75 |
Hydroxylated MWCNT |
Water treatment (1 bar) |
PWF: 587.1 |
PWF: 812.9 |
178 |
Mesostructured SBA-15/CES-30 |
Water treatment (3 bar) |
PWF: 181.4 |
PWF: 463.6 |
75 |
Carboxylated MWCNT |
Water treatment (1 bar) |
PWF: 587.1 |
PWF: 412.9 |
178 |
Nano-SiO2 |
Wastewater treatment (2–6 bar) |
FRR: 82.1; HA flux: 59.2; HA R: 94.1; MB flux: 81.1; MB R: 32.5 |
FRR: 86.2; HA flux: 77.4; HA R: 94.7; MB flux: 92.9; MB R: 42.2 |
74 |
GO-PAA |
Wastewater treatment (4 bar) |
PWF: 43; PF: 9.8; CR (SM): 44.1; CR (SWE): 39.7 |
PWF: 57; PF: 21.8; CR (SM): 53.5; CR (SWE): 48.8 |
119 |
SiO2 |
Water treatment (4 bar) |
PWF: 249.37; BSA R: 91.9; FRR: 80.6 |
PWF: 510.76; BSA R: 97.8; FRR: 98 |
73 |
Oxidized MWCNT |
Desalination (4 bar) |
PWF: 5; Na2SO4 R: 20; FRR: 29.7 |
PWF: 7.3; Na2SO4 R: 75; FRR: 87.7 |
179 |
ZnO |
Protein purification (1 bar) |
PWF: 32.8; BSA R: 99.2; RFR: 27.7 |
PWF: 116.6; BSA R: 98.8; RFR: 7.8 |
82 |
CNT |
Water treatment (4.1 bar) |
TOC R: 35.5; UVA254 R: 20.2 |
TOC R: 48.8; UVA254 R: 41.8 |
168 |
ZnO |
Water treatment (1.5 bar) |
FRR: 97.01; PWF: 30.42; HA flux: 24.84; RFR: 17.72 |
FRR: 91.1; PWF: 51.01; HA flux: 44.64; RFR: 12.27 |
81 |
CNT |
Water treatment (3.5 bar) |
BSA R: 95.8; OVA R: 95.2; BSA flux: 3.2; OVA flux: 2.1; FRR (OVA*): 31.7; FRR (BSA): 40.8; PWF: 12 |
BSA R: 98.2; OVA R: 98.1; BSA flux: 35.1; OVA flux: 26.1; FRR (OVA*): 70.83; FRR (BSA): 80; PWF: 70 |
180 |
ZnO |
Water treatment (4 bar) |
PWF: 31; FRR: 39.4 |
PWF: 48; FRR: 68.9 |
84 |
UiO-66@GO |
Water treatment (2.5 bar) |
PWF: 3.8; DR R: 93.1; MO R: 85; FRR: 42.9 |
PWF: 15.8; DR R: 98.4; MO R: 89.1; FRR: 88.6 |
120 |
ZnO nanorod |
Water treatment (4 bar) |
PWF: 31; FRR: 39.4 |
PWF: 50; FRR: 73.1 |
84 |
Nano-hybrid f-MWCNT/PVP90 |
Protein purification (2.75–3.25 bar) |
PWF: 7.6; PA: 16.9 |
PWF: 71.7; PA: 7 |
181 |
CS-ZnO HNPS |
Water treatment (N/A) |
PWF: 1215.8 |
PWF: 4135.8 |
85 |
SLS-CNT |
Protein purification (1 bar) |
PWF: 141; BSA R: 97.9; PA: 111.4; FRR: 61.4 |
PWF: 595.6; BSA R: 95.8; PA: 56.9; FRR: 94.4 |
182 |
CZN |
Protein purification (3 bar) |
BSA flux: 92.5; FRR: 44.6; PWF: 514.1 |
BSA flux: 117.7; FRR: 50.1; PWF: 678.5 |
86 |
TiO2 coated MWCNT |
Desalination (5 bar) |
PWF: 3.71; FRR: 53.1; Na2SO4 R: 69.5; NaCl R: 36.1 |
PWF: 4.35; FRR: 83; Na2SO4 R: 80.7; NaCl R: 41.4 |
183 |
ZrO2 |
Wastewater treatment (0.345–3.1 bar) |
PWF: 878.3 |
PWF: 1581 |
240 |
GO |
Water treatment (at 2.5 bar) |
PWF: 3.8; DR R: 93.1; MO R: 85; FRR: 42.9 |
PWF: 8.8; DR R: 87.9; MO R: 81.4; FRR: 84.3 |
120 |
ZrO2 |
Protein purification (1 bar) |
BSA R: 97.2; OVA R: 94.6; PWF: 8.2 |
BSA R: 92.7; OVA R: 91.2; PWF: 83.6 |
89 |
ZnO coated MWCNTs |
Wastewater treatment (4 bar) |
Dye R: 91; PWF: 8.2; PF: 7.5; FRR: 67.1 |
Dye R: 96.1; PWF: 16.7; PF: 16.1; FRR: 95.2 |
184 |
Al2O3 |
Water treatment (4.5 bar) |
PWF: 8.5; Cu R: 28 |
PWF: 25.3; Cu R: 55.9 |
90 |
PAA grafted MWCNTs |
Desalination (4 bar) |
Na2SO4 R: 48.4; NaCl R: 0.56; PWF: 8.9; FRR: 52 |
Na2SO4 R: 65.5; NaCl R: 19.1; PWF: 29.3; FRR: 69 |
185 |
Alumina |
Protein purification (2 bar) |
PWF: 182.2; BSA R: 98.8 |
PWF: 209; BSA R: 96.7 |
70 |
rGO-TiO2 |
Wastewater treatment (5 bar) |
PWF: 23; FRR: 75.2; RG19 R: 92.9; DY12 R: 88.9; RB21 R: 61.4 |
PWF: 43.3; FRR: 96.8; RG19 R: 99.2; DY12 R: 95.2; RB21 R: 81.4 |
68 |
ZrO2 |
Protein purification (2 bar) |
PWF: 182.2; BSA R: 98.8 |
PWF: 190.1; BSA R: 95.2 |
70 |
Ag coated MWCNTs |
Water treatment (4 bar) |
PWF: 554 |
PWF: 556 |
186 |
TiO2 |
Protein purification (2 bar) |
PWF: 182.2; BSA R: 98.8 |
PWF: 198.6; BSA R: 95.5 |
70 |
MWCNTs-PANI |
Water treatment (1 bar) |
HA R: 18.4; PWF: 265.4 |
HA R: 62.9; PWF: 1498.1 |
187 |
Al2O3 |
Water treatment (0.69–1.03 bar) |
PWF: 866.5 |
PWF: 1268 |
241,242 |
HMO(0.75)–TiO2 (0.25) |
Wastewater treatment (1 bar) |
PWF: 23.71; oil R: 98.16; FRR: 45.9 |
PWF: 28.48; oil R: 98.57; FRR: 91.5 |
243 |
GO |
Wastewater treatment (5 bar) |
PWF: 23; FRR: 75.2; RG19 R: 92.9; DY12 R: 88.9; RB21 R: 61.4 |
PWF: 35.9; FRR: 90.7; RG19 R: 98.7; DY12 R: 89.6; RB21 R: 69.4 |
68 |
Cu2+-HNTs |
Protein purification (1 bar) |
PF: 73.1; PEG10k R: 84.3; PEG20k R: 95.2 |
PF: 120; PEG10k R: 73.9; PEG20k R: 93 |
200 |
Magnetic-treated Fe3O4 |
Water treatment (4 bar) |
PWF: 36; FRR: 52 |
PWF: 65; FRR: 77.7 |
93 |
Fe–Ag/f-MWCNT |
Water treatment (4 bar) |
PWF: 26.5; Cr6+ ions R: 9.34; FRR: 64 |
PWF: 36.9; Cr6+ ions R: 94.8; FRR: 94.98 |
188 |
HMO(0.25)–TiO2 (0.75) |
Wastewater treatment (1 bar) |
PWF: 23.71; R: 98.16; FRR: 45.9 |
PWF: 27.33; R: 97.17; FRR: 63.6 |
243 |
HMO |
Protein purification (1.5 bar) |
PWF: 39.4; BSA R: 57; pepsin R: 50; trypsin R: 39; FRR: 53.7; BSA flux: 17.3 |
PWF: 499.2; BSA R: 85; pepsin R: 70; trypsin R: 66; FRR: 96.2; BSA flux: 158.4 |
232 |
SiO2 |
Wastewater treatment (1.5 bar) |
PWF: N/A; PF: N/A; oil R: N/A; FRR: N/A |
PWF: 117; PF: 76.67; oil R: 98.57; FRR: 81 |
244 |
Sulfonated HNT |
Desalination and wastewater treatment (4 bar) |
PWF: 29.3; NaCl R: 16.5; MgCl2 R: 22.8; Na2SO4 R: 17.2; MgSO4 R: 17.5; RR49 R: 93.6; RB5 R: 94.9 |
PWF: 40.3; NaCl R: 1.9; MgCl2 R: 7.4; Na2SO4 R: 16.4; MgSO4 R: 13.6; RR49 R: 90.4; RB5 R: 94 |
193 |
Magnetic-treated PANI/Fe3O4 |
Water treatment (4 bar) |
PWF: 36; FRR: 52 |
PWF: 52; FRR: 80 |
93 |
GO-ZnO |
Wastewater treatment (5 bar) |
PWF: 1.5; salt R: 17 |
PWF: 13.5; salt R: 28 |
121 |
Magnetic-treated MWCNT |
Water treatment (4 bar) |
PWF: 36; FRR: 52 |
PWF: 29; FRR: 64.6 |
93 |
TETA-MWCNT |
Desalination (10 bar) |
PWF: 36.27; NaCl R: 18.58; Na2SO4 R: 72.65; MgCl2 R: 47.23; MgSO4 R: 62.08; FRR: 72.9 |
PWF: 84.35; NaCl R: 27.02; Na2SO4 R: 32.56; MgCl2 R: 92.73; MgSO4 R: 55.36; FRR: 93.1 |
189 |
Chitosan nano-biopolymers |
Water treatment (4 bar) |
PWF: 13 |
PWF: 22 |
234 |
Fe3O4 |
Water treatment (4 bar) |
PWF: 36; FRR: 52 |
PWF: 33; FRR: 68 |
93 |
Hollow mesoporous SiO2 spheres |
Protein purification (1 bar) |
PWF: 38; BSA R: 93.2; FRR: 62.2 |
PWF: 195.7; BSA R: 92.6; FRR: 82.4 |
76 |
HPEI-GO |
Protein purification (1 bar) |
FRR: 86.6; PWF: 204.5; PA: 61.11 |
FRR: 92.1; PWF: 206.9; PA: 25.89 |
114 |
HNTs-poly(NASS) |
Desalination (4 bar) |
PWF: 29.4; RR49 R: 93.7; RB5 R: 95.2; NaCl R: 83.5; MgCl2 R: 77; Na2SO4 R: 82.8; MgSO4 R: 82.5 |
PWF: 97.5; RR49 R: 90.5; RB5 R: 91.7; NaCl R: 97.2; MgCl2 R: 96.5; Na2SO4 R: 90; MgSO4 R: 90.9 |
201 |
HNTs-CS@Ag |
Protein purification (1 bar) |
PEG20k R: 94; PWF: 112.11 |
PEG20k R: 72.8; PWF: 375.8 |
203 |
PANI/Fe3O4 |
Protein purification (4 bar) |
PWF: 36; FRR: 52 |
PWF: 33; FRR: 68 |
93 |
MCNs |
Protein purification (1 bar) |
PWF: 218.9; PF: 37.8; FRR: 64.9: PA: 40.3: BSA R: 99.9 |
PWF: 257.8; PF: 30.4; FRR: 60.9: PA: 7.8: BSA R: 99.9 |
233 |
HNTs-dextran |
Protein purification (1 bar) |
PWF: 80.3; FRR: 86; PEG20k R: 93.2; PVA30–70k R: 96.9 |
PWF: 224.5; FRR: 96; PEG20k R: 76.1; PVA30–70k R: 100 |
204 |
f-MWCNTs |
Wastewater treatment (4.1 bar) |
PWF: 24.28; PF: 4.4 |
PWF: 53.91; PF: 7.4 |
190 |
Fe3O4-MWCNT |
Water treatment (4 bar) |
PWF: 36; FRR: 52 |
PWF: 45; FRR: 76.6 |
93 |
HNTs-MPC |
Protein purification (1 bar) |
FRR: 85.2; PWF: 110.06; PEG20k R: 91.8; PA: 63.6 |
FRR: 93.1; PWF: 224.39; PEG20k R: 83.6; PA: 8.3 |
202 |
CNC |
Protein purification (2.7 bar) |
PWF: 93.4; BSA R: 93; FRR: 51 |
PWF: 195; BSA R: 96; FRR: 76.2 |
20 |
SiO2 |
Wastewater treatment (1.5 bar) |
PWF: 87.347; PF: 60.112; oil R: 95.77; FRR: 71.17; RFR: 31.18 |
PWF: 102.43; PF: 90.937; oil R: 99.98; FRR: 93.33; RFR: 11.22 |
175 |
Conclusions and future prospects
Seemingly the permanent hydrophilic modification of PES membranes can be achieved by blending with organic and/or inorganic materials. Furthermore, there is no denying the fact that the amount of data available today on the hydrophilic enhancement of PES membranes via blending is a stepping stone to upgrading PES membranes to new heights. Some of the conclusions drawn from this comprehensive review are listed as follows:
• To achieve an improved surface hydrophilicity and performance, many factors need to be considered in the overall process of composite membrane preparation, such as precise control over the functional groups, uniformity, and reproducibility. For instance, the functional groups on CNTs have the ability to be converted to membrane functional groups and can change the surface hydrophilicity and performance of the PES membrane. Therefore, more functional groups on CNTs are expected to reveal more significant changes in membrane hydrophilicity and performance. However, there is also a need for comprehensive investigation concerning the use and influence of multiple-modified SWCNTs and MWCNTs on PES NC membranes characteristics to verify the efficiency of PES modification of CNTs on the surface hydrophilization of PES membranes. Furthermore, the production costs of carbon nanotubes are quite high. Thus, further work should investigate and address the economic aspects so that their potentials for commercial scale can be realized.
• In the case of blending with inorganic materials, the interaction between PES and NPs is specific and the final membrane hydrophilicity and performance depends on such interaction. Therefore, the effectiveness of hydrophilicity will depend on the location of NPs in the membrane matrix because the location of NPs can change the diffusivity in the PES matrix. The surface energy and concentration are other important factors that can affect NPs dispersion and location, which could lead to NPs aggregation on the surface of the PES NC membrane. NPs aggregation will mean that the effectiveness of surface hydropilicity will be reduced during intended applications. To decrease the surface energy or improve the dispersion of NPs in the PES matrix, the surface modification of the NPs by grafting with a polymer can be an effective method.
• The use of a variety of functional and synthetic materials (i.e., lyotropic liquid crystals, aquaporins) will improve the hydrophilicity, enable the highest permeation rates, as well as keep the doors open for research and development in the field of multifunctional, high-performance, and antifouling PES membranes.
• Although, the combination of two or three additives can be more complex in terms of the environmental drawbacks and cost effectiveness, these could lead to multifunctional PES membranes that are of great interest for ‘future hydrophilic PES membranes’. Comparison with the existing ones to determine their adaptability and sustainability for commercial purposes will be the next step.
• With a hydrophilic PES membrane, it should be mentioned that solute adsorption is reduced at the produced hydrophilic surfaces, but is never completely prevented. Therefore, it is expected that membrane surface hydrophilicity can be tuned for specific applications through the discussed methods, although they still need to be developed further in such a way that they allow even more and better environmentally friendly control over other modification methods.
• Finally, but also very important, is the processing ability and economic cost. Generally, the cost is a major concern in the commercialization of membrane technology. Some hydrophilic PES membranes might produce a better quality of permeate and solute removal but the operating costs may be higher. Thus, the cost associated with the synthesis and incorporation of these additives needs to be addressed at the earliest for their development from the laboratory to a commercial-applicable scale.
Conflicts of interest
We declare that there is no conflict of interest in this work.
Symbols and abbreviations
AA | Acrylic acid |
AEAPTMS | [3-(2-Aminoethylamino)propyl] trimethoxysilane |
Ag | Silver |
Al2O3, AgNP | Silver nanoparticles |
Al2O3 | Aluminum oxide |
A-PCC | Aragonite precipitated calcium carbonate |
APS | Ammonium peroxidisulfate |
APTMS | (3-Aminopropyl) trimethoxysilane |
ATRP | Atom transfer radical polymerization |
4-bpdh | 2,5-Bis(4-pyridyl)-3,4-diaza-2,4-hexadiene |
BPA | Bisphenol A |
BSA | Bovine serum albumin |
CES | Carboxyethylsilanetriol sodium salt |
COD | Chemical oxygen demand |
COOH | Carboxyl |
CNC | Cellulose nanocrystals |
CNTs | Carbon nanotubes |
CR | Color rejection |
CS | Chitosan |
Cu2+ | Copper ions |
CZN | CuO/ZnO nanocomposite |
DIW | Deionized water |
DR | Direct red 80 |
DY12 | Direct yellow 12 |
EG | Ethylene glycol |
F127-b-PDMAEMA | F127-based amphiphilic block copolymers containing poly(N,N-dimethylamino-2-ethyl methacrylate) end blocks |
Fe-NPs | Iron oxide-based nanoparticles |
FeN | Iron nanoparticles |
FRR (%) | Flux recovery ratio |
GO | Graphene oxide |
H2oba | 4,4′-Oxybisbenzoic acid |
HA | Humic acid |
HMSS | Hollow mesoporous silica sphere |
HNTs | Halloysite nanotubes |
HNTs-SO3H | Sulfonated halloysite nanotubes |
HP (L m−2 h−1) | Hydraulic permeability |
HPEI | Hyperbranched polyethylenimine |
KPS | Potassium persulfate |
MB | Methylene blue |
Met | Metformine |
MF | Melamine formaldehyde |
MgO | Manganese oxide |
MO | Methyl orange |
MOFs | Metal–organic frameworks |
m-Fe3O4 | Magnetic-treated Fe3O4 |
m-PANI/Fe3O4 | Magnetic-treated polyaniline-coated Fe3O4 |
m-MWCNT/Fe3O4 | Magnetic-treated Fe3O4 coated multi-walled carbon nanotubes |
MMM | Mixed matrix membrane |
MPC | 2-Methacryloyloxyethyl phosphorylcholine |
MR (m−1) | Membrane resistance |
NC | Nanocomposite |
NPH | 4-Nonylphenol |
NPhthCs | N-Phthaloyl-chitosan |
NPs | Nanoparticles |
NT | Nanotubes |
OH | Hydroxyl |
OVA | Ovalbumin |
P31R1 | Linear pluronic 31R1 |
PA | Protein adsorption |
PA-6 | Polyamide |
PAA | Polyacrylic acid |
PANI/Fe3O4 | Polyaniline-coated Fe3O4 |
PCA | Polycitric acid |
PCL | Polycaprolactone |
PDMAEMA | Poly(N,N-dimethylamino-2-ethyl methacrylate) |
PEG | Polyethylene glycol |
PEO | Polyethylene oxide |
PES | Polyethersulfone |
PES-g-PSBMA | Polyethersulfone-block-poly(sulfobetaine methacrylate) |
PF (L m−2 h−1) | Permeate flux |
PMAA | Poly(methacrylic acid) |
PNIPAAm | Poly (N-isopropyl acrylamino) |
PS-b-PAA | Polystyrene-block-poly(acrylic acid) |
PSA | Polysulfide-amide |
PSf-g-POEM | polysulfone-graft-poly (ethylene glycol) methyl ether methacrylate |
PVP | Polyvinyl pyrrolidone |
PWF (L m−2 h−1) | Pure water flux |
R (%) | Rejection |
RAFT | Reversible addition-fragmentation polymerization |
RB5 | Reactive black 5 |
RB 21 | Reactive blue 21 |
RFR (%) | Reversible fouling ratio |
RG 19 | Reactive green 19 |
rGO | Partially reduced graphene oxide |
RR49 | Reactive red 49 |
SiO2 | Silicon dioxide |
SLS | Sodium lignosulfonate |
SM | Synthetic melanoidin |
SWCNTs | Single-walled carbon nanotubes |
SWE | Spent wash effluent |
T904Star-like tetronic | Star-like tetronic 904 |
TDS | Total dissolved solids |
TEOS | Tetraethyl orthosilicate |
TETA | Triethylenetetramine |
TiO2 | Titanium dioxide |
TMU-5 | [Zn(oba)(4-bpdh)0.5]·(DMF)1.5 |
WCA | Water contact angle |
WF (L m−2 h−1) | Water flux |
ZIF | Zeolitic imidazolate framework |
ZIF-L | Zeolitic imidazole framework with leaf-shaped morphology (ZIF-L) |
ZnO | Zinc oxide |
ZrO2 | Zirconium dioxide |
Acknowledgements
The authors acknowledge the financial support provided by Universiti Sains Malaysia under the USM fellowship scheme, Fundamental Research Grant Scheme (FRGS) Ministry of Higher Education (MOHE) Malaysia (Grant no: 203.PJKIMIA.6071334 and 203.PJKIMIA.6071355), and Universiti Sains Malaysia (USM) RU Membrane Science and Technology Cluster.
References
- A. Rahimpour, M. Jahanshahi, S. Khalili, A. Mollahosseini, A. Zirepour and B. Rajaeian, Desalination, 2012, 286, 99–107 CrossRef.
- Q. Shi, Y. Su, S. Zhu, C. Li, Y. Zhao and Z. Jiang, J. Membr. Sci., 2007, 303, 204–212 CrossRef.
- H. Wang, L. Yang, X. Zhao, T. Yu and Q. Du, Chin. J. Chem. Eng., 2009, 17, 324–329 CrossRef.
- C. Barth, M. C. Gonçalves, A. T. N. Pires, J. Roeder and B. A. Wolf, J. Membr. Sci., 2000, 169, 287–299 CrossRef.
- N. Bolong, A. F. Ismail, M. R. Salim, D. Rana and T. Matsuura, J. Membr. Sci., 2009, 331, 40–49 CrossRef.
- B. J. A. Tarboush, D. Rana, T. Matsuura, H. A. Arafat and R. M. Narbaitz, J. Membr. Sci., 2008, 325, 166–175 CrossRef.
- M. Ulbricht, Polymer, 2006, 47, 2217–2262 CrossRef.
- N. Hilal, O. O. Ogunbiyi, N. J. Miles and R. Nigmatullin, Sep. Sci. Technol., 2005, 40, 1957–2005 CrossRef.
- A. G. Fane and C. J. D. Fell, Desalination, 1987, 62, 117–136 CrossRef.
- A. Nabe, E. Staude and G. Belfort, J. Membr. Sci., 1997, 133, 57–72 CrossRef.
- J. Mulder, Basic principles of membrane technology, Springer Science & Business Media, 2012 Search PubMed.
- G. Kang and Y. Cao, Water Res., 2012, 46, 584–600 CrossRef PubMed.
- T. Humplik, J. Lee, S. C. O'Hern, B. A. Fellma, M. A. Baig, S. F. Hassan, M. A. Atieh, F. Rahman, T. Laoui, R. Karnik and E. N. Wang, Nanotechnology, 2011, 22, 292001 CrossRef PubMed.
- J. Gilron, S. Belfer, P. Väisänen and M. Nyström, Desalination, 2001, 140, 167–179 CrossRef.
- H. Zou, Y. Jin, J. Yang, H. Dai, X. Yu and J. Xu, Sep. Purif. Technol., 2010, 72, 256–262 CrossRef.
- V. Freger, J. Gilron and S. Belfer, J. Membr. Sci., 2002, 209, 283–292 CrossRef.
- G. dong Kang and Y. ming Cao, J. Membr. Sci., 2014, 463, 145–165 CrossRef.
- E. Yuliwati and A. F. Ismail, Desalination, 2011, 273, 226–234 CrossRef.
- C. Feng, B. Shi, G. Li and Y. Wu, J. Membr. Sci., 2004, 237, 15–24 CrossRef.
- D. Zhang, A. Karkooti, L. Liu, M. Sadrzadeh, T. Thundat, Y. Liu and R. Narain, J. Membr. Sci., 2018, 549, 350–356 CrossRef.
- D. Rana and T. Matsuura, Chem. Rev., 2010, 110, 2448–2471 CrossRef PubMed.
- J. Garcia-Ivars, M. I. Alcaina-Miranda, M. I. Iborra-Clar, J. A. Mendoza-Roca and L. Pastor-Alcañiz, Sep. Purif. Technol., 2014, 128, 45–57 CrossRef.
- T. Marino, E. Blasi, S. Tornaghi, E. Di Nicolò and A. Figoli, J. Membr. Sci., 2018, 549, 192–204 CrossRef.
- B. Vatsha, J. C. Ngila and R. M. Moutloali, Phys. Chem. Earth, 2014, 67–69, 125–131 CrossRef.
- A. Abdel-Karim, T. A. Gad-Allah, A. S. El-Kalliny, S. I. A. Ahmed, E. R. Souaya, M. I. Badawy and M. Ulbricht, Sep. Purif. Technol., 2017, 175, 36–46 CrossRef.
- A. Shockravi, V. Vatanpour, Z. Najjar, S. Bahadori and A. Javadi, Microporous Mesoporous Mater., 2017, 246, 24–36 CrossRef.
- A. Jalali, A. Shockravi, V. Vatanpour and M. Hajibeygi, Microporous Mesoporous Mater., 2016, 228, 1–13 CrossRef.
- A. Sumisha, G. Arthanareeswaran, Y. Lukka Thuyavan, A. F. Ismail and S. Chakraborty, Ecotoxicol. Environ. Saf., 2015, 121, 174–179 CrossRef PubMed.
- F. F. Ghiggi, L. D. Pollo, N. S. M. Cardozo and I. C. Tessaro, Eur. Polym. J., 2017, 92, 61–70 CrossRef.
- F. Liu, N. A. Hashim, Y. Liu, M. R. M. Abed and K. Li, J. Membr. Sci., 2011, 375, 1–27 CrossRef.
- A. Bushell, PhD thesis, University of Manchester, 2012.
- S. P. Nunes and A. Car, Ind. Eng. Chem. Res., 2013, 52, 993–1003 CrossRef.
- Z. Yi, L. Zhu, L. Cheng, B. Zhu and Y. Xu, Polymer, 2012, 53, 350–358 CrossRef.
- Z. Yi, L. P. Zhu, Y. Y. Xu, X. L. Li, J. Z. Yu and B. K. Zhu, J. Membr. Sci., 2010, 364, 34–42 CrossRef.
- Z. Yi, L. P. Zhu, Y. Y. Xu, Y. F. Zhao, X. T. Ma and B. K. Zhu, J. Membr. Sci., 2010, 365, 25–33 CrossRef.
- T. Luo, S. Lin, R. Xie, X. J. Ju, Z. Liu, W. Wang, C. L. Mou, C. Zhao, Q. Chen and L. Y. Chu, J. Membr. Sci., 2014, 450, 162–173 CrossRef.
- Y. Liu, Y. Su, X. Zhao, Y. Li, R. Zhang and Z. Jiang, J. Membr. Sci., 2015, 486, 195–206 CrossRef.
- Y. Su, Y. Liu, X. Zhao, Y. Li and Z. Jiang, Chin. J. Chem. Eng., 2015, 23, 1283–1290 CrossRef.
- F. Ran, S. Nie, W. Zhao, J. Li, B. Su, S. Sun and C. Zhao, Acta Biomater., 2011, 7, 3370–3381 CrossRef PubMed.
- Y. F. Zhao, P. Bin Zhang, J. Sun, C. J. Liu, L. P. Zhu and Y. Y. Xu, J. Membr. Sci., 2016, 510, 306–313 CrossRef.
- N. A. Hashim, F. Liu and K. Li, J. Membr. Sci., 2009, 345, 134–141 CrossRef.
- J. K. Koh, Y. W. Kim, S. H. Ahn, B. R. Min and J. H. Kim, J. Polym. Sci., Part B: Polym. Phys., 2010, 48, 183–189 CrossRef.
- J.-H. Li, M.-Z. Li, J. Miao, J.-B. Wang, X.-S. Shao and Q.-Q. Zhang, Appl. Surf. Sci., 2012, 258, 6398–6405 CrossRef.
- Y. Sui, X. Gao, Z. Wang and C. Gao, J. Membr. Sci., 2012, 394–395, 107–119 CrossRef.
- A. Bottino, Sep. Purif. Technol., 2001, 22–23, 269–275 CrossRef.
- X. Cao, J. Ma, X. Shi and Z. Ren, Appl. Surf. Sci., 2006, 253, 2003–2010 CrossRef.
- L. Yan, Y. S. Li and C. B. Xiang, Polymer, 2005, 46, 7701–7706 CrossRef.
- A. Bottino, G. Capannelli and A. Comite, Desalination, 2002, 146, 35–40 CrossRef.
- E. S. Džunuzović, J. V Džunuzović, A. D. Marinković, M. T. Marinović-Cincović, K. B. Jeremić and J. M. Nedeljković, Eur. Polym. J., 2012, 48, 1385–1393 CrossRef.
- E. Džunuzović, K. Jeremić and J. M. Nedeljković, Eur. Polym. J., 2007, 43, 3719–3726 CrossRef.
- W. Ji and S. K. Sikdar, Ind. Eng. Chem. Res., 1996, 35, 1124–1132 CrossRef.
- J.-H. Li, Y.-Y. Xu, L.-P. Zhu, J.-H. Wang and C.-H. Du, J. Membr. Sci., 2009, 326, 659–666 CrossRef.
- L.-H. Li, J.-C. Deng, H.-R. Deng, Z.-L. Liu and L. Xin, Carbohydr. Res., 2010, 345, 994–998 CrossRef PubMed.
- K. Ebert, D. Fritsch, J. Koll and C. Tjahjawiguna, J. Membr. Sci., 2004, 233, 71–78 CrossRef.
- A. Anžlovar, Z. Crnjak Orel and M. Žigon, Eur. Polym. J., 2010, 46, 1216–1224 CrossRef.
- C. Calebrese, L. Hui, L. S. Schadler and J. K. Nelson, IEEE Trans. Dielectr. Electr. Insul., 2011, 18, 938–945 Search PubMed.
- Y. Hu, R. C. Smith, J. K. Nelson and L. S. Schadler, Annu. Rep. - Conf. Electr. Insul. Dielectr. Phenomena, CEIDP, 2006, pp. 31–34 Search PubMed.
- R. C. Smith, C. Liang, M. Landry, J. K. Nelson and L. S. Schadler, IEEE Trans. Dielectr. Electr. Insul., 2008, 15, 187–196 Search PubMed.
- H. Tong, S. Ouyang, Y. Bi, N. Umezawa, M. Oshikiri and J. Ye, Adv. Mater., 2012, 24, 229–251 CrossRef PubMed.
- Y. Hou, L. Wu, X. Wang, Z. Ding, Z. Li and X. Fu, J. Catal., 2007, 250, 12–18 CrossRef.
- N. Lu, H. T. Yu, Y. Su and Y. Wu, Sep. Purif. Technol., 2012, 90, 196–203 CrossRef.
- L. Djafer, A. Ayral and A. Ouagued, Sep. Purif. Technol., 2010, 75, 198–203 CrossRef.
- X. Zhu, C. Yuan, Y. Bao, J. Yang and Y. Wu, J. Mol. Catal. A: Chem., 2005, 229, 95–105 CrossRef.
- A. Mills and S. Le Hunte, J. Photochem. Photobiol., A, 1997, 108, 1–35 CrossRef.
- S. Q. Wang, Q. L. Liu and A. M. Zhu, Eur. Polym. J., 2011, 47, 1168–1175 CrossRef.
- A. Sotto, A. Boromand, R. Zhang, P. Luis, J. M. Arsuaga, J. Kim and B. Van der Bruggen, J. Colloid Interface Sci., 2011, 363, 540–550 CrossRef PubMed.
- M. Tilahun, J. Wang, J. Zhu and S. Velizarov, J. Membr. Sci., 2018, 550, 462–469 CrossRef.
- M. Safarpour, V. Vatanpour and A. Khataee, Desalination, 2015, 393, 65–78 CrossRef.
- A. Razmjou, J. Mansouri and V. Chen, J. Membr. Sci., 2011, 378, 73–84 CrossRef.
- J. María Arsuaga, A. Sotto, G. del Rosario, A. Martínez, S. Molina, S. B. Teli and J. de Abajo, J. Membr. Sci., 2013, 428, 131–141 CrossRef.
- A. Razmjou, A. Resosudarmo, R. L. Holmes, H. Li, J. Mansouri and V. Chen, Desalination, 2012, 287, 271–280 CrossRef.
- D. Tang, R. Yuan and Y. Chai, Clin. Chem., 2007, 53, 1323–1329 CrossRef PubMed.
- J. nan Shen, H. min Ruan, L. guang Wu and C. jie Gao, Chem. Eng. J., 2011, 168, 1272–1278 CrossRef.
- J. Lin, W. Ye, K. Zhong, J. Shen, N. Jullok, A. Sotto and B. Van der Bruggen, Chem. Eng. Process., 2016, 107, 194–205 CrossRef.
- A. Martín, J. M. Arsuaga, N. Roldán, J. de Abajo, A. Martínez and A. Sotto, Desalination, 2015, 357, 16–25 CrossRef.
- Q. Li, S. Pan, X. Li, C. Liu, J. Li, X. Sun, J. Shen, W. Han and L. Wang, Colloids Surf., A, 2015, 487, 180–189 CrossRef.
- H. Yu, X. Zhang, Y. Zhang, J. Liu and H. Zhang, Desalination, 2013, 326, 69–76 CrossRef.
- A. Moezzi, A. M. McDonagh and M. B. Cortie, Chem. Eng. J., 2012, 185–186, 1–22 CrossRef.
- B. Li, T. Liu, Y. Wang and Z. Wang, J. Colloid Interface Sci., 2012, 377, 114–121 CrossRef PubMed.
- W. Hu, S. Chen, B. Zhou and H. Wang, Mater. Sci. Eng., B, 2010, 170, 88–92 CrossRef.
- A. L. Ahmad, A. A. Abdulkarim, Z. M. H. Mohd Shafie and B. S. Ooi, Desalination, 2017, 403, 53–63 CrossRef.
- L. Shen, X. Bian, X. Lu, L. Shi, Z. Liu, L. Chen, Z. Hou and K. Fan, Desalination, 2012, 293, 21–29 CrossRef.
- J. Alam, L. A. Dass, M. Ghasemi and M. Alhoshan, Polym. Compos., 2013, 34, 1870–1877 CrossRef.
- H. Rajabi, N. Ghaemi, S. S. Madaeni, P. Daraei, B. Astinchap, S. Zinadini and S. Hossein, Appl. Surf. Sci., 2015, 349, 66–77 CrossRef.
- I. Munnawar, S. S. Iqbal, M. N. Anwar, M. Batool, S. Tariq, N. Faitma, A. L. Khan, A. U. Khan, U. Nazar, T. Jamil and N. M. Ahmad, Carbohydr. Polym., 2017, 175, 661–670 CrossRef PubMed.
- N. Nasrollahi, V. Vatanpour, S. Aber and N. Mohammad, Sep. Purif. Technol., 2018, 192, 369–382 CrossRef.
- B. Li and Y. Wang, Superlattices Microstruct., 2010, 47, 615–623 CrossRef.
- J. F. Callejas, C. G. Read, C. W. Roske, N. S. Lewis and R. E. Schaak, Chem. Mater., 2016, 28, 6017–6044 CrossRef.
- R. Pang, X. Li, J. Li, Z. Lu, X. Sun and L. Wang, Desalination, 2014, 332, 60–66 CrossRef.
- N. Ghaemi, Appl. Surf. Sci., 2016, 364, 221–228 CrossRef.
- K. Rambabu and S. Velu, Recent Advances in Chemical Engineering, 2014, vol. 6, pp. 4468–4470 Search PubMed.
- N. Ghaemi, S. S. Madaeni, P. Daraei, H. Rajabi, S. Zinadini, A. Alizadeh, R. Heydari, M. Beygzadeh and S. Ghouzivand, Chem. Eng. J., 2015, 263, 101–112 CrossRef.
- P. Daraei, S. S. Madaeni, N. Ghaemi, M. A. Khadivi, B. Astinchap and R. Moradian, Sep. Purif. Technol., 2013, 109, 111–121 CrossRef.
- M. Ahamed, M. S. AlSalhi and M. K. J. Siddiqui, Clin. Chim. Acta, 2010, 411, 1841–1848 CrossRef PubMed.
- S. Iravani, H. Korbekandi, S. V Mirmohammadi and B. Zolfaghari, Res. Pharm. Sci., 2014, 9, 385–406 Search PubMed.
- X. Cao, M. Tang, F. Liu, Y. Nie and C. Zhao, Colloids Surf., B, 2010, 81, 555–562 CrossRef PubMed.
- M. Sile-yuksel, B. Tas, D. Y. Koseoglu-imer and I. Koyuncu, Desalination, 2014, 347, 120–130 CrossRef.
- H. Basri, A. F. Ismail and M. Aziz, Desalination, 2011, 273, 72–80 CrossRef.
- A. Ananth, G. Arthanareeswaran, A. F. Ismail, Y. S. Mok and T. Matsuura, Colloids Surf., A, 2014, 451, 151–160 CrossRef.
- C.-N. Yeh, K. Raidongia, J. Shao, Q.-H. Yang and J. Huang, Nat. Chem., 2015, 7, 166 CrossRef PubMed.
- H. Huang, Y. Mao, Y. Ying, Y. Liu, L. Sun and X. Peng, Chem. Commun., 2013, 49, 5963–5965 RSC.
- R. K. Joshi, P. Carbone, F. C. Wang, V. G. Kravets, Y. Su, I. V Grigorieva, H. A. Wu, A. K. Geim and R. R. Nair, Science, 2014, 343, 752–754 CrossRef PubMed.
- F. Perreault, A. Fonseca de Faria and M. Elimelech, Chem. Soc. Rev., 2015, 44, 5861–5896 RSC.
- L. L. Zhang, R. Zhou and X. S. Zhao, J. Mater. Chem., 2010, 20, 5983–5992 RSC.
- T. A. Otitoju, A. L. Ahmad and B. S. Ooi, Journal of Water Process Engineering, 2016, 14, 41–59 CrossRef.
- Y. Zhu, S. Murali, W. Cai, X. Li, J. W. Suk, J. R. Potts and R. S. Ruoff, Adv. Mater., 2010, 22, 3906–3924 CrossRef PubMed.
- D. Fu, G. Han, Y. Chang and J. Dong, Mater. Chem. Phys., 2012, 132, 673–681 CrossRef.
- M. Safarpour, A. Khataee and V. Vatanpour, Ind. Eng. Chem. Res., 2014, 53, 13370–13382 CrossRef.
- J. R. Werber, C. O. Osuji and M. Elimelech, Nat. Rev. Mater., 2016, 1, 16018 CrossRef.
- P. Sun, K. Wang and H. Zhu, Adv. Mater., 2016, 28, 2287–2310 CrossRef PubMed.
- P. Fernández-Ibáñez, M. I. Polo-López, S. Malato, S. Wadhwa, J. W. J. Hamilton, P. S. M. Dunlop, R. D'Sa, E. Magee, K. O'Shea, D. D. Dionysiou and J. A. Byrne, Chem. Eng. J., 2015, 261, 36–44 CrossRef.
- Y. Han, Y. Jiang and C. Gao, ACS Appl. Mater. Interfaces, 2015, 7, 8147–8155 CrossRef PubMed.
- Y. Zhang, S. Zhang and T.-S. Chung, Environ. Sci. Technol., 2015, 49, 10235–10242 CrossRef PubMed.
- L. Yu, Y. Zhang, B. Zhang, J. Liu, H. Zhang and C. Song, J. Membr. Sci., 2013, 447, 452–462 CrossRef.
- Z. Wang, H. Yu, J. Xia, F. Zhang, F. Li, Y. Xia and Y. Li, Desalination, 2012, 299, 50–54 CrossRef.
- C. Zhao, X. Xu, J. Chen and F. Yang, J. Environ. Chem. Eng., 2013, 1, 349–354 CrossRef.
- A. Abdel-Karim, S. Leaper, M. Alberto, A. Vijayaraghavan, X. Fan, S. M. Holmes, E. R. Souaya, M. I. Badawy and P. Gorgojo, Chem. Eng. J., 2018, 334, 789–799 CrossRef.
- S. Zinadini, A. A. Zinatizadeh, M. Rahimi, V. Vatanpour and H. Zangeneh, J. Membr. Sci., 2014, 453, 292–301 CrossRef.
- S. Aditya Kiran, Y. Lukka Thuyavan, G. Arthanareeswaran, T. Matsuura and A. F. Ismail, Chem. Eng. J., 2016, 286, 528–537 CrossRef.
- J. Ma, X. Guo, Y. Ying, D. Liu and C. Zhong, Chem. Eng. J., 2017, 313, 890–898 CrossRef.
- O. T. Mahlangu, R. Nackaerts, J. M. Thwala, B. B. Mamba and A. R. D. Verliefde, J. Membr. Sci., 2017, 524, 43–55 CrossRef.
- J. Liu, A. G. Rinzler, H. Dai, J. H. Hafner, R. K. Bradley, P. J. Boul, A. Lu, T. Iverson, K. Shelimov, C. B. Huffman, F. Rodriguez-Macias, Y.-S. Shon, T. R. Lee, D. T. Colbert and R. E. Smalley, Science, 1998, 280, 1253–1256 CrossRef PubMed.
- S. Iijima, Nature, 1991, 354, 56 CrossRef.
- B. Sakintuna and Y. Yürüm, Ind. Eng. Chem. Res., 2005, 44, 2893–2902 CrossRef.
- F. Peng, F. Pan, H. Sun, L. Lu and Z. Jiang, J. Membr. Sci., 2007, 300, 13–19 CrossRef.
- J. H. Sung, H. S. Kim, H.-J. Jin, H. J. Choi and I.-J. Chin, Macromolecules, 2004, 37, 9899–9902 CrossRef.
- Y. Lin, B. Zhou, K. A. Shiral Fernando, P. Liu, L. F. Allard and Y.-P. Sun, Macromolecules, 2003, 36, 7199–7204 CrossRef.
- W.-X. Chen, J. Y. Lee and Z. Liu, Mater. Lett., 2004, 58, 3166–3169 CrossRef.
- K. Kardimi, T. Tsoufis, A. Tomou, B. J. Kooi, M. I. Prodromidis and D. Gournis, Int. J. Hydrogen Energy, 2012, 37, 1243–1253 CrossRef.
- A. I. López-Lorente, B. M. Simonet and M. Valcárcel, Anal. Chem., 2010, 82, 5399–5407 CrossRef PubMed.
- M. A. Aroon, A. F. Ismail, M. M. Montazer-Rahmati and T. Matsuura, Sep. Sci. Technol., 2010, 45, 2287–2297 CrossRef.
- B. Van der Bruggen, ISRN Nanotechnol., 2012, 2012, 1–17 CrossRef.
- F. H. Gojny, M. H. G. Wichmann, U. Köpke, B. Fiedler and K. Schulte, Compos. Sci. Technol., 2004, 64, 2363–2371 CrossRef.
- J. Zhu, H. Peng, F. Rodriguez-Macias, J. L. Margrave, V. N. Khabashesku, A. M. Imam, K. Lozano and E. V Barrera, Adv. Funct. Mater., 2004, 14, 643–648 CrossRef.
- Q. Chen, R. Xu and D. Yu, Polymer, 2006, 47, 7711–7719 CrossRef.
- N. Robertson and C. A. McGowan, Chem. Soc. Rev., 2003, 32, 96–103 RSC.
- Y. Shirazi, M. A. Tofighy and T. Mohammadi, J. Membr. Sci., 2011, 378, 551–561 CrossRef.
- P. Calvert, Nature, 1999, 399, 210 CrossRef.
- A. F. Ismail, N. H. Rahim, A. Mustafa, T. Matsuura, B. C. Ng, S. Abdullah and S. A. Hashemifard, Sep. Purif. Technol., 2011, 80, 20–31 CrossRef.
- C. Oueiny, S. Berlioz and F. X. Perrin, Prog. Polym. Sci., 2014, 39, 707–748 CrossRef.
- J. Choi, J. Jegal and W. Kim, J. Membr. Sci., 2006, 284, 406–415 CrossRef.
- A. L. Ahmad, M. Sarif and S. Ismail, Desalination, 2005, 179, 257–263 CrossRef.
- L. Vast, Z. Mekhalif, A. Fonseca, J. B.Nagy and J. Delhalle, Compos. Sci. Technol., 2007, 67, 880–889 CrossRef.
- Y. Hu and C. Guo, IntechOpen, 2011 Search PubMed.
- H. T. Ham, C. M. Koo, S. O. Kim, Y. S. Choi and I. J. Chung, Macromol. Res., 2004, 12, 384–390 CrossRef.
- C. S. Chen, X. H. Chen, L. S. Xu, Z. Yang and W. H. Li, Carbon, 2005, 43, 1660–1666 CrossRef.
- H. Yu, X. Mo, J. Peng, M. Zhai, J. Li, G. Wei, X. Zhang and J. Qiao, Radiat. Phys. Chem., 2008, 77, 656–662 CrossRef.
- P. Liu, Eur. Polym. J., 2005, 41, 2693–2703 CrossRef.
- N. G. Sahoo, S. Rana, J. W. Cho, L. Li and S. H. Chan, Prog. Polym. Sci., 2010, 35, 837–867 CrossRef.
- C.-H. Jung, D.-K. Kim and J.-H. Choi, Curr. Appl. Phys., 2009, 9, S85–S87 CrossRef.
- P. Petrov, G. Georgiev, D. Momekova, G. Momekov and C. B. Tsvetanov, Polymer, 2010, 51, 2465–2471 CrossRef.
- A. Liu, I. Honma, M. Ichihara and H. Zhou, Nanotechnology, 2006, 17, 2845 CrossRef.
- L. Qu, Y. Lin, D. E. Hill, B. Zhou, W. Wang, X. Sun, A. Kitaygorodskiy, M. Suarez, J. W. Connell, L. F. Allard and Y.-P. Sun, Macromolecules, 2004, 37, 6055–6060 CrossRef.
- A. Eitan, K. Jiang, D. Dukes, R. Andrews and L. S. Schadler, Chem. Mater., 2003, 15, 3198–3201 CrossRef.
- K. Balasubramanian and M. Burghard, Small, 2005, 1, 180–192 CrossRef PubMed.
- J. Li, T. Tang, X. Zhang, S. Li and M. Li, Mater. Lett., 2007, 61, 4351–4353 CrossRef.
- K.-W. Lee, B.-K. Seo, S.-T. Nam and M.-J. Han, Desalination, 2003, 159, 289–296 CrossRef.
- A. G. Osorio, I. C. L. Silveira, V. L. Bueno and C. P. Bergmann, Appl. Surf. Sci., 2008, 255, 2485–2489 CrossRef.
- J.-H. Choi, J. Jegal and W.-N. Kim, J. Membr. Sci., 2006, 284, 406–415 CrossRef.
- G. Vuković, A. Marinković, M. Obradović, V. Radmilović, M. Čolić, R. Aleksić and P. S. Uskoković, Appl. Surf. Sci., 2009, 255, 8067–8075 CrossRef.
- J. Shen, W. Huang, L. Wu, Y. Hu and M. Ye, Mater. Sci. Eng., A, 2007, 464, 151–156 CrossRef.
- J. Kathi, K.-Y. Rhee and J. H. Lee, Composites, Part A, 2009, 40, 800–809 CrossRef.
- S. W. Kim, T. Kim, Y. S. Kim, H. S. Choi, H. J. Lim, S. J. Yang and C. R. Park, Carbon, 2012, 50, 3–33 CrossRef.
- C.-M. Chang and Y.-L. Liu, Carbon, 2010, 48, 1289–1297 CrossRef.
- K. T. Kim and W. H. Jo, Carbon, 2011, 49, 819–826 CrossRef.
- T. Knoell, J. Safarik, T. Cormack, R. Riley, S. W. Lin and H. Ridgway, J. Membr. Sci., 1999, 157, 117–138 CrossRef.
- H. L. Zhang, eXPRESS Polym. Lett., 2012, 6, 620–628 CrossRef.
- E. Celik, H. Park, H. Choi and H. Choi, Water Res., 2011, 45, 274–282 CrossRef PubMed.
- S. Qiu, L. Wu, X. Pan, L. Zhang, H. Chen and C. Gao, J. Membr. Sci., 2009, 342, 165–172 CrossRef.
- R. Levenstein, D. Hasson and R. Semiat, J. Membr. Sci., 1996, 116, 77–92 CrossRef.
- C. Van Chung, N. Q. Buu and N. H. Chau, Sci. Technol. Adv. Mater., 2005, 6, 246–250 CrossRef.
- L. Wang, X. Song, T. Wang, S. Wang, Z. Wang and C. Gao, Appl. Surf. Sci., 2015, 330, 118–125 CrossRef.
- G. Kaminska, J. Bohdziewicz, J. I. Calvo, P. Prádanos, L. Palacio and A. Hernández, J. Membr. Sci., 2015, 493, 66–79 CrossRef.
- P. Daraei, S. S. Madaeni, N. Ghaemi, M. A. Khadivi, B. Astinchap and R. Moradian, J. Membr. Sci., 2013, 444, 184–191 CrossRef.
- T. A. Otitoju, A. L. Ahmad and B. S. Ooi, J. Polym. Res., 2017, 24, 1–11 CrossRef.
- V. Vatanpour, M. Esmaeili and M. H. D. A. Farahani, J. Membr. Sci., 2014, 466, 70–81 CrossRef.
- Y. Mansourpanah, S. S. Madaeni, A. Rahimpour, M. Adeli, M. Y. Hashemi and M. R. Moradian, Desalination, 2011, 277, 171–177 CrossRef.
- R. Sengur, C. F. de Lannoy, T. Turken, M. Wiesner and I. Koyuncu, Desalination, 2015, 359, 123–140 CrossRef.
- V. Vatanpour, S. S. Madaeni, R. Moradian, S. Zinadini and B. Astinchap, J. Membr. Sci., 2011, 375, 284–294 CrossRef.
- E. Celik, L. Liu and H. Choi, Water Res., 2011, 45, 5287–5294 CrossRef PubMed.
- M. Irfan, A. Idris, N. M. Yusof, N. F. M. Khairuddin and H. Akhmal, J. Membr. Sci., 2014, 467, 73–84 CrossRef.
- W. Wang, L. Zhu, B. Shan, C. Xie, C. Liu, F. Cui and G. Li, J. Membr. Sci., 2018, 548, 459–469 CrossRef.
- V. Vatanpour, S. S. Madaeni, R. Moradian, S. Zinadini and B. Astinchap, Sep. Purif. Technol., 2012, 90, 69–82 CrossRef.
- S. Zinadini, S. Rostami, V. Vatanpour and E. Jalilian, J. Membr. Sci., 2017, 529, 133–141 CrossRef.
- P. Daraei, S. S. Madaeni, N. Ghaemi, H. Ahmadi Monfared and M. A. Khadivi, Sep. Purif. Technol., 2013, 104, 32–44 CrossRef.
- S. Al Aani, V. Gomez, C. J. Wright and N. Hilal, Chem. Eng. J., 2017, 326, 721–736 CrossRef.
- J. Lee, Y. Ye, A. J. Ward, C. Zhou, V. Chen, A. I. Minett, S. Lee, Z. Liu, S. R. Chae and J. Shi, Sep. Purif. Technol., 2016, 163, 109–119 CrossRef.
- M. L. Masheane, L. N. Nthunya, S. P. Malinga, E. N. Nxumalo, B. B. Mamba and S. D. Mhlanga, Sep. Purif. Technol., 2017, 184, 79–87 CrossRef.
- M. Peydayesh, T. Mohammadi and O. Bakhtiari, Sep. Purif. Technol., 2018, 194, 488–502 CrossRef.
- R. Saranya, G. Arthanareeswaran and D. D. Dionysiou, Chem. Eng. J., 2014, 236, 369–377 CrossRef.
- Y. Zhang, Y. Chen, H. Zhang, B. Zhang and J. Liu, J. Inorg. Biochem., 2013, 118, 59–64 CrossRef PubMed.
- R. Zhai, B. Zhang, Y. Wan, C. Li, J. Wang and J. Liu, Chem. Eng. J., 2013, 214, 304–309 CrossRef.
- Y. Wang, J. Zhu, G. Dong, Y. Zhang, N. Guo and J. Liu, Sep. Purif. Technol., 2015, 150, 243–251 CrossRef.
- S. R. Levis and P. B. Deasy, Int. J. Pharm., 2002, 243, 125–134 CrossRef PubMed.
- E. Joussein, S. Petit, J. Churchman, B. Theng, D. Righi and B. Delvaux, Clay Miner., 2005, 40, 383–426 CrossRef.
- M. Liu, B. Guo, M. Du and D. Jia, Appl. Phys. A, 2007, 88, 391–395 CrossRef.
- H. Ismail, P. Pasbakhsh, M. N. A. Fauzi and A. Abu Bakar, Polym. Test., 2008, 27, 841–850 CrossRef.
- P. Luo, Y. Zhao, B. Zhang, J. Liu, Y. Yang and J. Liu, Water Res., 2010, 44, 1489–1497 CrossRef PubMed.
- R. Zhai, B. Zhang, L. Liu, Y. Xie, H. Zhang and J. Liu, Catal. Commun., 2010, 12, 259–263 CrossRef.
- Y. Chen, Y. Zhang, J. Liu, H. Zhang and K. Wang, Chem. Eng. J., 2012, 210, 298–308 CrossRef.
- J. Zhu, N. Guo, Y. Zhang, L. Yu and J. Liu, J. Membr. Sci., 2014, 465, 91–99 CrossRef.
- Z. Wang, H. Wang, J. Liu and Y. Zhang, Desalination, 2014, 344, 313–320 CrossRef.
- Y. Chen, Y. Zhang, H. Zhang, J. Liu and C. Song, Chem. Eng. J., 2013, 228, 12–20 CrossRef.
- H. Yu, Y. Zhang, X. Sun, J. Liu and H. Zhang, Chem. Eng. J., 2014, 237, 322–328 CrossRef.
- S. L. James, Chem. Soc. Rev., 2003, 32, 276–288 RSC.
- J. L. C. Rowsell and O. M. Yaghi, Microporous Mesoporous Mater., 2004, 73, 3–14 CrossRef.
- G. Ferey, Chem. Soc. Rev., 2008, 37, 191–214 RSC.
- G. S. Papaefstathiou and L. R. MacGillivray, Coord. Chem. Rev., 2003, 246, 169–184 CrossRef.
- S. Sorribas, P. Gorgojo, C. Téllez, J. Coronas and A. G. Livingston, J. Am. Chem. Soc., 2013, 135, 15201–15208 CrossRef PubMed.
- D. Zacher, O. Shekhah, C. Woll and R. A. Fischer, Chem. Soc. Rev., 2009, 38, 1418–1429 RSC.
- H. Furukawa, K. E. Cordova, M. O'Keeffe and O. M. Yaghi, Science, 2013, 341, 6149 CrossRef PubMed.
- S. Keskin and S. Kızılel, Ind. Eng. Chem. Res., 2011, 50, 1799–1812 CrossRef.
- J. Ma, Y. Ying, Q. Yang, Y. Ban, H. Huang, X. Guo, Y. Xiao, D. Liu, Y. Li, W. Yang and C. Zhong, Chem. Commun., 2015, 51, 4249–4251 RSC.
- J. Ma, Y. Ying, X. Guo, H. Huang, D. Liu and C. Zhong, J. Mater. Chem. A, 2016, 4, 7281–7288 RSC.
- T. Rodenas, M. Van Dalen, E. García-Pérez, P. Serra-Crespo, B. Zornoza, F. Kapteijn and J. Gascon, Adv. Funct. Mater., 2014, 24, 249–256 CrossRef.
- Y. Peng, Y. Li, Y. Ban, H. Jin, W. Jiao, X. Liu and W. Yang, Science, 2014, 346, 1356–1359 CrossRef PubMed.
- A. Huang, W. Dou and J. Caro, J. Am. Chem. Soc., 2010, 132, 15562–15564 CrossRef PubMed.
- J. R. Li, J. Sculley and H. C. Zhou, Chem. Rev., 2012, 112, 869–932 CrossRef PubMed.
- Q. Zhang, Y. Liu, Y. Su, R. Zhang, L. Fan, Y. Liu, T. Ma and Z. Jiang, RSC Adv., 2016, 6, 35532–35538 RSC.
- M. S. Denny Jr., J. C. Moreton, L. Benz and S. M. Cohen, Nat. Rev. Mater., 2016, 1, 16078 CrossRef.
- O. K. Farha, A. Özgür Yazaydın, I. Eryazici, C. D. Malliakas, B. G. Hauser, M. G. Kanatzidis, S. T. Nguyen, R. Q. Snurr and J. T. Hupp, Nat. Chem., 2010, 2, 944 CrossRef PubMed.
- W. Xuan, C. Zhu, Y. Liu and Y. Cui, Chem. Soc. Rev., 2012, 41, 1677–1695 RSC.
- T. Loiseau, C. Serre, C. Huguenard, G. Fink, F. Taulelle, M. Henry, T. Bataille and G. Férey, Chem.–Eur. J., 2004, 10, 1373–1382 CrossRef PubMed.
- F. Gholami, S. Zinadini, A. A. Zinatizadeh and A. R. Abbasi, Sep. Purif. Technol., 2018, 194, 272–280 CrossRef.
- Z. X. Low, A. Razmjou, K. Wang, S. Gray, M. Duke and H. Wang, J. Membr. Sci., 2014, 460, 9–17 CrossRef.
- R. Ranjan and M. Tsapatsis, Chem. Mater., 2009, 21, 4920–4924 CrossRef.
- G. Lu and J. T. Hupp, J. Am. Chem. Soc., 2010, 132, 7832–7833 CrossRef PubMed.
- E. Biemmi, C. Scherb and T. Bein, J. Am. Chem. Soc., 2007, 129, 8054–8055 CrossRef PubMed.
- S. Hermes, F. Schröder, R. Chelmowski, C. Wöll and R. A. Fischer, J. Am. Chem. Soc., 2005, 127, 13744–13745 CrossRef PubMed.
- S. Keskin and D. S. Sholl, J. Phys. Chem. C, 2007, 111, 14055–14059 CrossRef.
- J. H. Cavka, S. Jakobsen, U. Olsbye, N. Guillou, C. Lamberti, S. Bordiga and K. P. Lillerud, J. Am. Chem. Soc., 2008, 130, 13850–13851 CrossRef PubMed.
- R. Jamshidi Gohari, E. Halakoo, N. A. M. Nazri, W. J. Lau, T. Matsuura and A. F. Ismail, Desalination, 2014, 335, 87–95 CrossRef.
- Y. Orooji, M. Faghih, A. Razmjou, J. Hou, P. Moazzam, N. Emami, M. Aghababaie, F. Nourisfa, V. Chen and W. Jin, Carbon, 2017, 111, 689–704 CrossRef.
- F. S. A. Negin Ghaemi and P. Daraei, Carbohydr. Polym., 2018, 2, 165–182 Search PubMed.
- O. A. Jimoh, P. U. Okoye, T. A. Otitoju and K. Shah Ariffin, J. Cleaner Prod., 2018, 195, 79–92 CrossRef.
- Q. F. Alsalhy, H. A. Salih, S. Simone, M. Zablouk, E. Drioli and A. Figoli, Desalination, 2014, 345, 21–35 CrossRef.
- Y. Kourde-hana, P. Loulergue, A. Szymczyk, B. Van Der Bruggen, M. Nachtnebel, M. Rabiller-baudry, J. Audic, P. Pölt and K. Baddari, J. Membr. Sci., 2017, 533, 261–269 CrossRef.
- M. Son, H. Kim, J. Jung, S. Jo and H. Choi, Chemosphere, 2017, 179, 194–201 CrossRef PubMed.
- S. A. Al Malek, M. N. Abu Seman, D. Johnson and N. Hilal, Desalination, 2012, 288, 31–39 CrossRef.
- N. Maximous, G. Nakhla, W. Wan and K. Wong, J. Membr. Sci., 2010, 352, 222–230 CrossRef.
- N. Maximous, G. Nakhla, W. Wan and K. Wong, J. Membr. Sci., 2009, 341, 67–75 CrossRef.
- N. Maximous, G. Nakhla, K. Wong and W. Wan, Sep. Purif. Technol., 2010, 73, 294–301 CrossRef.
- G. S. Lai, M. H. M. Yusob, W. J. Lau, R. Jamshidi Gohari, D. Emadzadeh, A. F. Ismail, P. S. Goh, A. M. Isloor and M. Rezaei-Dasht Arzhandi, Sep. Purif. Technol., 2017, 178, 113–121 CrossRef.
- T. A. Otitoju, A. L. Ahmad and B. S. Ooi, Korean J. Chem. Eng., 2017, 34, 1–7 CrossRef.
|
This journal is © The Royal Society of Chemistry 2018 |
Click here to see how this site uses Cookies. View our privacy policy here.