DOI:
10.1039/C8RA02739K
(Paper)
RSC Adv., 2018,
8, 16330-16335
Green approaches in the synthesis of furan-based diepoxy monomers†
Received
29th March 2018
, Accepted 26th April 2018
First published on 2nd May 2018
Abstract
Two eco-respectful, one-step synthetic routes for the preparation of a bio-based epoxy monomer derived from furan precursors are developed. The diglycidyl ester products are throughly characterized in terms of structure and thermal properties. Gathered results indicate that the two selected approaches allow the preparation of pure, furanic diglycidyl ester, which represents a viable bio-based alternative to its petrochemical aromatic counterpart.
Research on bio-based polymers has been rapidly increasing in past years, pushed by growing environmental and economic concerns, as well as by the uncertainty about future availability of finite petrochemical resources.1 Sustainability is a keyword in this process. In this frame, products that are respectful towards the environment, including eco-compatible building blocks and additives, are now researched to replace petroleum-based polymers with those derived from naturally occurring feedstocks.2–4 In the field of epoxy resins, this trend is related also to the necessity to find a good candidate to substitute the controversial building block bisphenol A (BPA), a molecule recognized as an endocrine disrupter and reprotoxic substance.5 Epoxy resins are very versatile thermosetting polymers, extremely resistant to corrosion, moisture and chemicals, with good adhesive strength toward most materials (wettability) and low shrinkage upon curing. Due to their high glass transition temperatures and excellent mechanical strength, epoxy resins are widely employed in a broad range of applications, such as electronics, structural adhesives, aerospace composites and protective coatings. In the latter application, the use of BPA results in hazard for customers of food and beverage products packed into containers treated with epoxy resins. The effects of human body contamination caused by BPA are diabetes, cardiovascular diseases, altered liver enzymes and reproductive apparatus damages.5 For these reasons, this molecule has been banned in many countries for the manufacturing of child products, and in France and Canada from all the materials in direct contact with food. Therefore, the necessity to find non-toxic and sustainable building blocks to replace BPA in the production of epoxy resins results mandatory. If one considers also the decreasing availability of oil-derived feedstock, the research of new molecules is logically focusing on bio-derived chemicals. Epoxidized vegetable oils have been widely studied for their use in epoxy resins preparation, thanks to their characteristics, availability and low cost.6–8 Mechanical properties of epoxy resins obtained using these long aliphatic molecules, alone or mixed to aromatic epoxy comonomers, are encouraging.9,10 In order to further improve chemical, thermal and mechanical properties of epoxy resins, the presence of significant content of aromatic moieties is required. In this frame, lignin derivatives appear to be the natural substitutes of BPA. However, time- and energy-consuming extraction processes make lignin-based epoxies expensive and barely available. On the other hand, furanic molecules combine aromatic structure and easily available feedstock, such as carbohydrate biomass. Among furanic molecules, furan-2,5-dicarboxylic acid (FDCA) has been labelled in 2004 as “top value added chemical from biomass” from U.S. Department of Energy, and it has been confirmed being a valuable chemical in 2010.11,12 FDCA is a commercially available compound obtained by dehydration of hexose polysaccharides and consequent oxidation of the 5-hydroxymethylfurfural (HMF) intermediate.13–18 As a matter of fact, FDCA already results to be an excellent substitute of terephthalic acid in the production of polyesters. Polyethylene furanoate (PEF), obtained from polycondensation of FDCA and ethylene glycol, showed up to be a perfect substitute of PET thanks also to the improved barrier properties.19–21 Some big companies, indeed nowadays commercialize bottles made of PEF.22 Nevertheless, the number of scientific papers reporting on FDCA-based epoxy resins is still limited and their applicability requires optimization. In a recent work, FDCA has been used as linker between two eugenol molecules, which were then epoxidized leading to materials with good heat resistance properties.23 Only Deng et al. used FDCA to obtain the corresponding diglycidyl ester, with a two-step procedure involving first allylation on the acidic groups with allyl bromide and consequent epoxidation with m-chloroperoxybenzoic acid (m-CPBA).24 The long reaction time, reagents and solvents used and the dangerous by-products, especially from an environmental point of view, make this process still complex and only moderately safe. Therefore, the obtainment of epoxy resins from FDCA monomers through simple, scalable and low environmental and human health impact protocols represents still a challenge. Some authors synthesized the diglycidyl ether of furan reacting the 2,5-bis(hydroxymethyl) furan with epichlorohydrin.25–27
In this paper, two new single-step synthetic routes are proposed for the obtainment of bis(oxiran-2-yl-methyl)furan-2,5-dicarboxylate (BOFD), starting from FDCA or from and its dimethyl ester (DM-FDCA), respectively.
In the first synthetic route the furan diepoxide is obtained through a one-step reaction starting from the furan dicarboxylic acid (FDCA) with epichlorohydrin. This protocol recalls the industrially optimized procedure for production of DGEBA, being performed through the condensation of FDCA with epichlorohydrin (ECH). This approach is remarkable, as bio-based epichlorohydrin prepared from glycerol is already commercially available.28 The second synthetic route proposed is based on the transesterification between DM-FDCA and glycidol. DM-FDCA, obtained by esterification of FDCA, is a commercial compound used for the production of PEF.19,29
The reaction between FDCA and ECH to form BOFD proceeds through a mechanism similar to that recently reported by other authors for the acid moieties of vanillic and gallic acids30–32 and represented in Scheme 1.
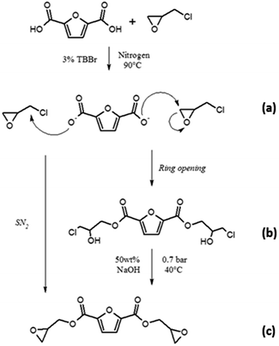 |
| Scheme 1 Reaction mechanism in the glycidylation of FDCA. | |
The reaction proceeds through the addition of the carboxylate group of FDCA to the epoxy ring of ECH. Experimental details are reported in “Synthesis procedures” Section in ESI.† As a first step of this procedure, FDCA is mixed with ECH in inert atmosphere in presence of the phase transfer catalyst tetrabutylammonium bromide (TBBr). The catalyst allows the furan-2,5-dicarboxylate oxyanion to coexist with ECH, used also as solvent (Scheme 1a). The reaction proceeds directly with an SN2 mechanism or with a mechanism involving the opening of the epoxy ring that binds to the ion, resulting in the formation of the chlorohydrin intermediate represented in Scheme 1b.33 Subsequently, cyclization of the chlorohydrin yields the glycidyl product (Scheme 1c). A preliminary TLC (hexane/ethyl acetate 1
:
1) performed on the yellow viscous product showed the presence of at least six different compounds. Among them, oligomers and unreacted halohydrins could be detected by NMR analysis of the fractions obtained upon purification through column chromatography that resulted mandatory. In particular, several yellow and highly viscous fractions were obtained, except for BOFD, which was a white crystalline solid. To prove the occurrence of the condensation reaction between glycidyl group and FDCA, first FTIR-ATR and mono- and multi-dimensional 1H and 13C-NMR analyses were carried out. FTIR-ATR spectra of FDCA and the purified BOFD are shown in Fig. 1.
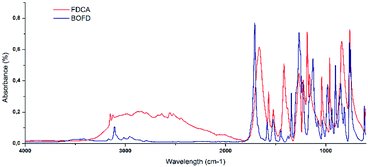 |
| Fig. 1 FTIR spectra of FDCA and BOFD. | |
The disappearance of the broad adsorption band due to –OH from carboxylic groups between 3200 and 2300 cm−1 correlated with the appearance of the strong ester band at 1709 cm−1 confirmed the conversion of carboxylic acids into ester moieties. The formation of the glycidyl group was confirmed by the appearance of the characteristic epoxy C–O–C absorption band at 902 cm−1 as well as of a peak at 1342 cm−1 related to the glycidyl methylene.
In Tables 1 and 2 are listed the characteristic FTIR bands of FDCA and BOFD, respectively.
Table 1 Peak assignments in FTIR spectrum of FDCA
Wavenumber (cm−1) |
Assignment |
3151–2520 |
Stretching O–H carboxylic acid |
1665 |
Stretching C O carbonyls |
1570–1416 |
Stretching C C aromatics (furan) |
1267–1039 |
Stretching C–O carboxylic acid |
960 |
Stretching C O, C–C–C bending 2,5 sub-furan ring |
840–760 |
Bending C–H alkene (furan) |
Table 2 Peak assignment in FTIR spectrum of BOFD obtained by FDCA glycidylation
Wavenumber (cm−1) |
Assignment |
3165–2955 |
Stretching C–H aromatics (furan) |
1708 |
Stretching C O ester |
1585 to 1448 |
Stretching C C aromatics (furan) |
1375–1343 |
Bending C–H, CH2 of glycidyl |
1267–1235 |
Stretching C–O ester and epoxy ring |
1127–1077 |
Stretching C–O aromatic (furan) |
1034–902 |
Stretching C–O epoxy ring |
862–815 |
Stretching C–C epoxy ring |
764–753 |
Rocking C–H glycidyl |
To get a further insight on the structure of BOFD, NMR analysis was also performed through monodimensional 1H and 13C NMR spectroscopy to check the presence of the predicted structure and its purity. Fig. 2 displays the 1H-NMR spectrum of BOFD. The characteristic peaks of furanic proton at 7.27 ppm, overlapped with the signal of CDCl3, is visible in the figure inset; two double doublets at 4.65 and 4.20, due to protons of methylene linked to the ester group, a sextet at 3.34 ppm from methyne proton of oxirane ring, a triplet at 2.93–2.86 and a double doublet 2.73 due to protons of methylene on oxirane ring are also visible. These signals are in agreement with those reported in literature for the BOFD molecule obtained with a two-step procedure involving first the allylation of FDCA and the subsequent epoxidation of the double bond.24
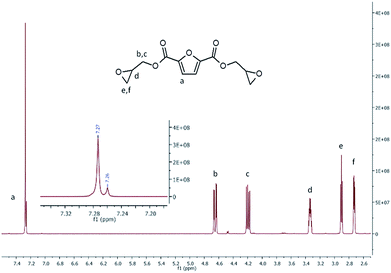 |
| Fig. 2 1H-NMR spectra of BOFD obtained by FDCA glycidylation. | |
13C-NMR spectrum of BOFD (Fig. 3) shows the peak at 157.73 ppm corresponding to the ester carbon, the quaternary furanic carbon peak at 146.65 ppm, the CH furanic peak of 119.16 ppm, the glycidyl CH2 carbon peak at 66.16 ppm, and the peaks related to the CH and CH2 carbons of oxirane ring at 49.23 and 44.95 ppm, respectively. This spectrum is in agreement with that reported by Deng et al.24 The multiplicity of carbons to get the exact hydrogen–hydrogen and carbon–hydrogen correlations, was determined by DEPT 90 and DEPT 135 analysis reported in ESI.† Moreover, multidimensional NMR analysis was also carried out through homonuclear correlation spectroscopy (COSY), heteronuclear single-quantum correlation spectroscopy (HSQC) and heteronuclear multiple-bond correlation spectroscopy (HMBC), as reported in the ESI (Fig. 3S–6S†).
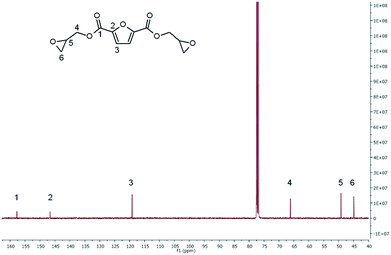 |
| Fig. 3 13C-NMR spectra of BOFD obtained by glycidylation. | |
Epoxy Equivalent Weight (EEW) was evaluated according to an alternative method proposed in literature, which relates the ratio between the peak intensity of epoxy and furanic ring protons in the 1H-NMR spectra, with the polymerization degree n.34,35 In the specific case of BOFD, according to equation reported in “Methods” Section in ESI† the calculated was EEW = 152.41, corresponding to a degree of polymerization n = 0.17.
Transesterification of DM-FDCA with diols is part of an industrially optimized two-step procedure for the production of furanic/furanoate polyesters (followed by a polycondensation).19,36 This procedure requires high temperature (190–200 °C) and the use of potentially toxic catalysts.37–39 In this paper, the synthesis is carried out at relatively low temperature (60 °C) (“Synthesis procedures” Section in ESI†). This is the maximum temperature that can be reached due to the high reactivity of glycidol, as it easily polymerizes, already at room temperature. An excess of glycidol was used in order to avoid as much as possible the formation of oligomers and a slight vacuum was used in order to allow stripping of methanol produced during the reaction, yet hindering the volatile solvent evaporation. An improvement introduced by the proposed procedure is the use of a cheap, non-toxic catalyst, potassium cyanate (KOCN). The transesterification proceeded in a single-step reaction sketched in Scheme 2.
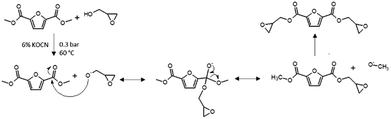 |
| Scheme 2 Mechanism of transesterification of DM-FDCA with glycidol. | |
At room temperature, DM-FDCA and the catalyst were insoluble in the reaction mixture. However, heating resulted in a clear and transparent solution. The successful progress of the reaction was confirmed by the appearance of the mixture cooled down after 6 hours of reaction, which was viscous and transparent, with no evidence of precipitates. The so-obtained reaction mixture was extracted with a mixture of ethyl acetate and distilled water; in this way, the undesired by-products were dissolved in the aqueous phase, while the diglycidyl ester product was recovered in the organic. A further chromatographic purification was then performed to remove the residual unreacted DM-FDCA in the product.25,26,30,31,40
The conversion of DM-FDCA into BOFD was confirmed by FTIR-ATR and mono- and multi-dimensional 1H and 13C-NMR analyses. Both FTIR-ATR and NMR spectra of BOFD obtained by transesterification present the same peaks as those of BOFD obtained by glycidylation. The spectrum of DM-FDCA and the table with peaks assignments are reported in the ESI.† As for the EEW calculation, in the case of BOFD obtained by transesterification, the degree of polymerization n, was 0.011, providing also in this case a pure, low-molecular weight diepoxy compound, with EEW = 135, 30.
Once we proved the obtainment of the monomeric diglycidyl ester of furan, an accurate thermal characterization was carried out by thermogravimetric analysis (TGA) and differential scanning calorimetry (DSC), to determine the thermal stability, as well as melting and crystallization temperatures of the compounds. As can be noticed in TGA thermogram (Fig. 4a), BOFD resulted thermally stable up to 185 °C, when it lost 5% of the initial weight. At the end of this degradation step a total weight loss of 95% was measured. A further slight degradation step is visible at temperatures above 300 °C, after which the residue at 650 °C was 1%. DSC analysis (Fig. 4b) showed a sharp endothermic peak associated to the melting process of BOFD at 88 °C (ΔH = 112 J g−1). During the cooling scan the occurrence of crystallization was evidenced by the presence of an exothermic peak having a maximum at 47 °C (91 J g−1). The second heating scan overlapped the first scan. The sharpness of the endothermic peak was a further evidence of the compound purity.
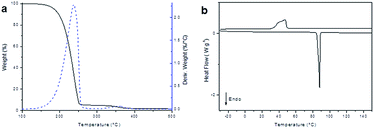 |
| Fig. 4 (a) TGA analysis (10 °C min−1, under nitrogen), and (b) dynamic DSC analysis (heating–cooling cycle) of BOFD obtained by transesterification. | |
Conclusions
In the present work, two new single-step synthetic routes are reported for the production of BOFD. Both approaches aim to limit the use of toxic reagents and propose low temperatures and short reaction times, with the easiness of the procedures based on fast, single-step procedures. FTIR-ATR, mono- and multi-dimensional analysis confirmed the structure expected for BOFD and evidenced a highly pure compound. Thermal properties of BOFD were determined through TGA and DSC analyses, which indirectly confirmed the purity of the compounds. In the present work, a proof of concept demonstrating the feasibility of simple and scalable routes to the synthesis of BOFD is provided. Further optimization of the presented synthesis protocols is needed to get higher reaction yields and consider these new procedures of great potential in actual applications.
Conflicts of interest
There are no conflicts to declare.
Acknowledgements
Alice Mija thanks RUDN University Program 5–100 for the financially support offered by the Ministry of Education and Science of The Russian Federation, agreement number 02.a03.0008.
References
- S. Lambert and M. Wagner, Environmental performance of bio-based and biodegradable plastics: the road ahead, Chem. Soc. Rev., 2017, 46, 6855–6871 RSC.
- A. Gandini, The irruption of polymers from renewable resources on the scene of macromolecular science and technology, Green Chem., 2011, 13, 1061–1083 RSC.
- A. K. Mohanty, M. Misra and L. T. Drzal, Sustainable Bio-Composites from renewable resources: Opportunities and challenges in the green materials world, J. Polym. Environ., 2002, 10, 19–26 CrossRef CAS.
- R. Auvergne, S. Caillol, G. David, B. Boutevin and J. P. Pascault, Biobased thermosetting epoxy: Present and future, Chem. Rev., 2014, 114, 1082–1115 CrossRef CAS PubMed.
- B. S. Rubin, Bisphenol A: An endocrine disruptor with widespread exposure and multiple effects, J. Steroid Biochem. Mol. Biol., 2011, 127, 27–34 CrossRef CAS PubMed.
- S. G. Tan and W. S. Chow, Biobased Epoxidized Vegetable Oils and Its Greener Epoxy Blends: A Review, Polym.-Plast. Technol. Eng., 2010, 49, 1581–1590 CrossRef CAS.
- C. Zhang, T. F. Garrison, S. A. Madbouly and M. R. Kessler, Recent advances in vegetable oil-based polymers and their composites, Prog. Polym. Sci., 2017, 71, 91–143 CrossRef CAS.
- M. Pawar, A. Kadam, O. Yemul, V. Thamke and K. Kodam, Biodegradable bioepoxy resins based on epoxidized natural oil (cottonseed & algae) cured with citric and tartaric acids through solution polymerization: A renewable approach, Ind. Crops Prod., 2016, 89, 434–447 CrossRef CAS.
- J.-M. Pin, N. Sbirrazzuoli and A. Mija, From epoxidized linseed oil to bioresin: An overall approach of epoxy/anhydride cross-linking, ChemSusChem, 2015, 8, 1232–1243 CrossRef CAS PubMed.
- J.-M. Pin, N. Guigo, L. Vincent, N. Sbirrazzuoli and A. Mija, Copolymerization as a Strategy to Combine Epoxidized Linseed Oil and Furfuryl Alcohol: The Design of a Fully Bio-Based Thermoset, ChemSusChem, 2015, 8, 4149–4161 CrossRef CAS PubMed.
- T. Werpy and G. Petersen, Top Value Added Chemicals from Biomass. Volume I -Results of Screening for Potential Candidates from Sugars and Synthesis Gas, U. S. D. of Energy, 2004, DOI:10.2172/926125.
- J. J. Bozell and G. R. Petersen, Technology development for the production of biobased products from biorefinery carbohydrates—the US Department of Energy's ‘Top 10’ revisited, Green Chem., 2010, 12, 539–554 RSC.
- C. Yang and C. Huang, Biotransformation of 5-hydroxy-methylfurfural into 2,5-furan-dicarboxylic acid by bacterial isolate using thermal acid algal hydrolysate, Bioresour. Technol., 2016, 214, 311–318 CrossRef CAS PubMed.
- A. Boisen, T. B. Christensen, W. Fu, Y. Y. Gorbanev, T. S. Hansen, J. S. Jensen, S. K. Klitgaard, S. Pedersen, A. Riisager, T. Ståhlberg and J. M. Woodley, Process integration for the conversion of glucose to 2,5-furandicarboxylic acid, Chem. Eng. Res. Des., 2009, 87, 1318–1327 CrossRef CAS.
- X. Han, L. Geng, Y. Guo, R. Jia and X. Liu, Base-free aerobic oxidation of 5-hydroxymethylfurfural to 2,5-furandicarboxylic acid over a Pt/C–O–Mg catalyst, Green Chem., 2016, 18, 1597–1604 RSC.
- N. Jiang, B. You, R. Boonstra, I. M. Terrero Rodriguez and Y. Sun, Integrating Electrocatalytic 5-Hydroxymethylfurfural Oxidation and Hydrogen Production via Co–P-Derived Electrocatalysts, ACS Energy Lett., 2016, 1, 386–390 CrossRef CAS.
- F. Koopman, N. Wierckx, J. H. de Winde and H. J. Ruijssenaars, Efficient whole-cell biotransformation of 5-(hydroxymethyl) furfural into FDCA, 2,5-furandicarboxylic acid, Bioresour. Technol., 2010, 101, 6291–6296 CrossRef CAS PubMed.
- G. Yi, S. P. Teong and Y. Zhang, Base-free conversion of 5-hydroxymethylfurfural to 2,5-furandicarboxylic acid over a Ru/C catalyst, Green Chem., 2016, 18, 979–983 RSC.
- G. Z. Papageorgiou, V. Tsanaktsis and D. N. Bikiaris, Synthesis of poly(ethylene furandicarboxylate) polyester using monomers derived from renewable resources: thermal behavior comparison with PET and PEN, Phys. Chem. Chem. Phys., 2014, 16, 7946–7958 RSC.
- S. K. Burgess, J. E. Leisen, B. E. Kraftschik, C. R. Mubarak, R. M. Kriegel and W. J. Koros, Chain Mobility, Thermal, and Mechanical Properties of Poly(ethylene furanoate) Compared to Poly(ethylene terephthalate), Macromolecules, 2014, 47, 1383–1391 CrossRef CAS.
- M. Vannini, P. Marchese, A. Celli and C. Lorenzetti, Fully biobased poly(propylene 2,5-furandicarboxylate) for packaging applications: excellent barrier properties as a function of crystallinity, Green Chem., 2015, 17, 4162–4166 RSC.
- Avantium, https://www.avantium.com/press-releases/alpla-joins-coca-cola-company-danone-avantiums-pef-bottle-development/.
- J. T. Miao, L. Yuan, Q. Guan, G. Liang and A. Gu, Biobased Heat Resistant Epoxy Resin with Extremely High Biomass Content from 2,5-Furandicarboxylic Acid and Eugenol, ACS Sustain. Chem. Eng., 2017, 5(8), 7003–7011 CrossRef CAS.
- J. Deng, X. Liu, C. Li, Y. Jiang and J. Zhu, Synthesis and properties of a bio-based epoxy resin from 2,5-furandicarboxylic acid (FDCA), RSC Adv., 2015, 5, 15930–15939 RSC.
- J. K. Cho, J. Lee, J. Jeong and B. Kim, Synthesis of carbohydrate biomass- based furanic compounds bearing epoxide end group (s) and evaluation of their feasibility as adhesives, J. Adhes. Sci. Technol., 2013, 27, 2127–2138 CrossRef CAS.
- F. Hu, J. J. La Scala, J. M. Sadler and G. R. Palmese, Synthesis and characterization of thermosetting furan-based epoxy systems, Macromolecules, 2014, 47, 3332–3342 CrossRef CAS.
- X. Shen, X. Liu, J. Wang, J. Dai and J. Zhu, Synthesis of an Epoxy Monomer from Bio-Based 2,5-Furandimethanol and Its Toughening via Diels-Alder Reaction, Ind. Eng. Chem. Res., 2017, 56, 8508–8516 CrossRef CAS.
- G. M. Lari, G. Pastore, C. Mondelli and J. Pérez-Ramírez, Towards sustainable manufacture of epichlorohydrin from glycerol using hydrotalcite-derived basic oxides, Green Chem., 2018, 20, 148–159 RSC.
- G. Z. Papageorgiou, D. G. Papageorgiou, Z. Terzopoulou and D. N. Bikiaris, Production of bio-based 2,5-furan dicarboxylate polyesters: Recent progress and critical aspects in their synthesis and thermal properties, Eur. Polym. J., 2016, 83, 202–229 CrossRef CAS.
- M. Fache, R. Auvergne, B. Boutevin and S. Caillol, New vanillin-derived diepoxy monomers for the synthesis of biobased thermosets, Eur. Polym. J., 2015, 67, 527–538 CrossRef CAS.
- C. Aouf, S. Benyahya, A. Esnouf, S. Caillol, B. Boutevin and H. Fulcrand, Tara tannins as phenolic precursors of thermosetting epoxy resins, Eur. Polym. J., 2014, 55, 186–198 CrossRef CAS.
- C. Aouf, C. Le Guernevé, S. Caillol and H. Fulcrand, Study of the O-glycidylation of natural phenolic compounds. The relationship between the phenolic structure and the reaction mechanism, Tetrahedron, 2013, 69, 1345–1353 CrossRef CAS.
- M. Fache, E. Darroman, V. Besse, R. Auvergne, S. Caillol and B. Boutevin, Vanillin, a promising biobased building-block for monomer synthesis, Green Chem., 2014, 16, 1987–1998 RSC.
- S. A. Garea, A. C. Corbu, C. Deleanu and H. Iovu, Determination of the epoxide equivalent weight (EEW) of epoxy resins with different chemical structure and functionality using GPC and 1H-NMR, Polym. Test., 2006, 25, 107–113 CrossRef CAS.
- F. G. Garcia and B. G. Soares, Determination of the epoxide equivalent weight of epoxy resins based on diglycidyl ether of bisphenol A (DGEBA) by proton nuclear magnetic resonance, Polym. Test., 2003, 22, 51–56 CrossRef.
- G. Z. Papageorgiou, V. Tsanaktsis, D. G. Papageorgiou, S. Exarhopoulos, M. Papageorgiou and D. N. Bikiaris, Evaluation of polyesters from renewable resources as alternatives to the current fossil-based polymers. Phase transitions of poly(butylene 2,5-furan-dicarboxylate), Polymer, 2014, 55, 3846–3858 CrossRef CAS.
- J. Carlos Morales-Huerta, A. Martínez De Ilarduya and S. Muñoz-Guerra, Poly(alkylene 2,5-furandicarboxylate)s (PEF and PBF) by ring opening polymerization, Polymer, 2016, 87, 148–158 CrossRef CAS.
- J. Wang, X. Liu, Y. Zhang, F. Liu and J. Zhu, Modification of poly(ethylene 2,5-furandicarboxylate) with 1,4-cyclohexanedimethylene: Influence of composition on mechanical and barrier properties, Polymer, 2016, 103, 1–8 CrossRef CAS.
- L. G. Voskressensky, O. A. Storozhenko, A. A. Festa, R. A. Novikov and A. V. Varlamov, Synthesis of Chromenoimidazoles, Annulated with an Azaindole Moiety, through a Base-Promoted Domino Reaction of Cyanomethyl Quaternary Salts, Synthesis, 2017, 49, 2753–2760 CrossRef CAS.
- Z. Rapi, B. Szolnoki, P. Bakó, P. Niedermann, A. Toldy, B. Bodzay, G. Keglevich and G. Marosi, Synthesis and characterization of biobased epoxy monomers derived from d-glucose, Eur. Polym. J., 2015, 67, 375–382 CrossRef CAS.
Footnote |
† Electronic supplementary information (ESI) available. See DOI: 10.1039/c8ra02739k |
|
This journal is © The Royal Society of Chemistry 2018 |
Click here to see how this site uses Cookies. View our privacy policy here.