DOI:
10.1039/C8RA02161A
(Paper)
RSC Adv., 2018,
8, 19426-19431
Preparation and performance of electrically conductive Nb-doped TiO2/polyaniline bilayer coating for 316L stainless steel bipolar plates of proton-exchange membrane fuel cells
Received
12th March 2018
, Accepted 30th April 2018
First published on 25th May 2018
Abstract
A bilayer coating composed of an inner layer of Nb-doped TiO2 obtained by the sol–gel method and an external polyaniline layer with small SO42− groups obtained by galvanostatic deposition was prepared to protect 316L stainless steel bipolar plates of proton-exchange membrane fuel cells. The corrosion resistances of bare 316L and 316L with single polyaniline coating and Nb-doped TiO2/polyaniline bilayer coating were investigated. The experimental results indicated that both single and bilayer coatings increased the corrosion potential and decreased the corrosion current density compared with bare 316L stainless steel. A thirty-day exposure experiment indicated that the Nb-doped TiO2/polyaniline bilayer showed high stability, and it protected 316L more effectively from the penetration of the corrosive ions.
1. Introduction
A bipolar plate is one of the important components in a proton-exchange membrane fuel cell (PEMFC), accounting for about 80% of the total weight and 45% of the stack manufacturing cost.1 Among all the materials used as the bipolar plates, metallic bipolar plates have aroused increasing interest due to their higher strength, better processability and lower cost, which can greatly improve the power and energy density of PEMFC. However, the metallic bipolar plates exhibit dissolution and passivation in the acidic PEMFC environments.2,3 The poor conductivity of the passivation film causes an increase in the contact resistance between the bipolar plate and the diffusion layer, thus decreasing the performance of the cell. The application of a conductive coating has been shown to be a simple and effective way to improve the corrosion resistance and the conductivity of the bipolar plates.
The conductive polymer coatings have received considerable attention as a kind of protective coating on the metallic bipolar plates because of their good conductivity, high thermal stability, simple synthetic process, smaller density and good corrosion resistance.4–6 Since DeBerry7 found that the polyaniline coatings on the stainless steel possess good corrosion resistance in the H2SO4 aqueous solution, the corrosion resistance and mechanism of the conductive polymer coatings on the metallic substrates have been attracting significant attention. Up to now, conductive polymer coatings have been successfully used on metal bipolar plates.8–13 Herrasti8 found that the polypyrrole coating increased the corrosion potential and reduced the oxidation current density compared to bare stainless steel. Zhang9 investigated the corrosion behavior of polypyrrole (Ppy) in HCl aqueous solution for fifty days. They reported that the Ppy coating not only increased the corrosion potential of the steel, but also significantly increased the pitting corrosion potential. Ren researched the corrosion resistance of polyaniline10 and polyaniline/polypyrrole11 coatings, and the results indicated that single polyaniline coating could decrease the corrosion rate by about two orders of magnitude, and a bilayer coating showed better corrosion resistance. The conductivity of the polymer coating is related to the doping ions. However, in an anodic PEMFC environment, the polymer coating is in a reductive state, which facilitates the de-doping reaction. This can result in the passivation of the substrate and the release of the doping ions from the polymer coating,14 which limits the applications of the polymer coating in PEMFCs.
In the present study, an Nb-doped TiO2 coating is prepared as the interlayer between 316L stainless steel and the polyaniline coating. The corrosion behaviors of the uncoated and coated 316L in H2SO4 solution were investigated.
2. Experimental procedures
A type of 316L stainless steel was used as the substrate alloy in the present study. The bulk materials were cut into specimens with a size of 10 mm × 15 mm × 2 mm by an electric spark cutter, followed by grinding with 1000# grit emery paper, cleaning with distilled water and acetone, and then drying with an electric hair drier. The Ti0.94Nb0.06O2 film was prepared by the sol–gel method. Tetrabutyl titanate and niobium(V) ethoxide were used as the raw materials for the sol. Acetyl acetone was used as a chelating agent, and ethanol was used as the solvent. The sol was aged for 12 h before spin-coating it on the 316L substrate. After the spin-coating process, the gel films were annealed at 500 °C at a heating rate of 4 °C min−1 for 2 h in air to obtain a stable Ti0.94Nb0.06O2 film. Then, the bare 316L and Ti0.94Nb0.06O2-coated-316L film specimens were embedded in an epoxy resin. For the preparation of the Ti0.94Nb0.06O2/Pani bilayer coatings, a Pani layer doped with SO42− was galvanostatically deposited on the 316L/Ti0.94Nb0.06O2 specimens at a current density of 3 mA cm−2 in a 0.5 M polyaniline + 1 M H2SO4 solution at 5 °C. For comparison, single Pani layer doped with SO42− was electrodeposited on the bare 316L stainless steel in a solution of 0.5 M polyaniline and 1 M H2SO4 at 5 °C. Then, scanning electron microscopy (SEM), X-ray diffraction (XRD) and Fourier transform infrared spectroscopy (FTIR) were used to characterize the coatings.
For the electrochemical measurements, a three-electrode system was used; a Pt electrode was used as the counter electrode, and Ag/AgCl (saturated KCl) was used as the reference electrode. An accelerated corrosion test was performed in 0.1 M H2SO4 solution at 80 °C to rapidly evaluate the protection provided by the coatings to 316L. All electrochemical experiments including potentiodynamic polarization, open circuit potential and electrochemical impedance measurements were conducted with the Princeton Applied Research Versa STAT 4 potentiostat/galvanostat system. Potentiodynamic polarization was performed at a scan rate of 20 mV min−1 after 1 h immersion in the solution. Electrochemical impedance measurements were obtained at an open circuit potential between 0.01 Hz and 100 kHz, with the amplitude of input sine wave voltage of 10 mV.
3. Results and discussion
3.1. 1Characterization of the coatings
Fig. 1a shows the XRD pattern of the Ti0.94Nb0.06O2 thin film coated onto 316L at an annealing temperature of 500 °C. The pattern reveals that the Ti0.94Nb0.06O2 film consists of the anatase phase. Fig. 1b gives the cross-sectional morphology of Ti0.94Nb0.06O2-coated 316L. It can be seen that the thickness of the Ti0.94Nb0.06O2 film is about 0.64 μm. Furthermore, the adherence between the film and the substrate is good. Fig. 2 presents the potential-time dependence for the galvanostatic electrodeposition of Pani coatings on bare 316L and Ti0.94Nb0.06O2-coated 316L specimens. Both the curves show the same changes and the presence of a potential peak, which may be related with the nucleated over-potential.10 The potential is then stabilized at different constant values, which may be related to the growth of the Pani coatings on different surfaces. The thickness (d) of Pani is correlated with the electric quantity (Q), as shown in the following equation:
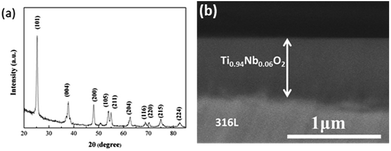 |
| Fig. 1 XRD pattern (a) and the cross-sectional morphology (b) of the Ti0.94Nb0.06O2 thin film at an annealing temperature of 500 °C. | |
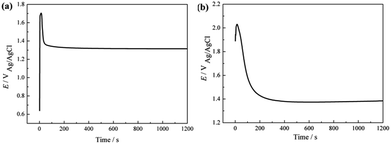 |
| Fig. 2 Potential-time dependence for the galvanostatic electrodeposition of Pani coating on bare 316L (a) and Ti0.94Nb0.06O2-coated 316L (b) specimens. | |
Therefore, the thickness of Pani in our experiment is about 18 μm.
The Pani coatings doped with sulfate ions deposited on 316L stainless steel and Ti0.94Nb0.06O2 film were characterized by FTIR, as shown in Fig. 3. The FTIR spectra of Pani coated on the 316L stainless steel and the Ti0.94Nb0.06O2 film showed the same characteristics. The peak at 790 cm−1 represented the out-of-plane bending vibration of a C–H bond on the benzene ring. The peak at 1225 cm−1 represented the bending vibration of a C
C bond on the quinone ring. The peak at 1295 cm−1 represented the stretching vibration of a secondary amine (C–N) connected to the benzene ring. The peaks at 1473 and 1560 cm−1 represented the characteristics of the quinoid ring and the benzene ring in the polyaniline, respectively. The peak at 1115 cm−1 represented the antisymmetric stretching vibration of SO42−, indicating the successful doping of protonic acid. These typical peaks were in accordance with the main peaks of Pani reported previously.15
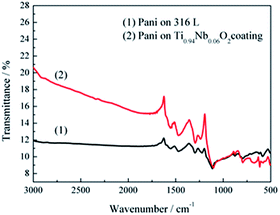 |
| Fig. 3 FTIR spectra of the Pani coating doped with sulfate ions deposited on 316L stainless steel and the Ti0.94Nb0.06O2 film. | |
The XRD pattern of Pani deposited on 316L is shown in Fig. 4. Some peaks appeared due to the local crystallinity of Pani, which may be caused by the periodicity perpendicular to the polymer chain.16 The SEM images of 316L with the single polyaniline coating and Ti0.94Nb0.06O2/polyaniline bilayer coating are presented in Fig. 5, and they showed that both Pani coatings were porous. The Pani coating deposited on 316L was slightly smoother than that deposited on the Ti0.94Nb0.06O2 film.
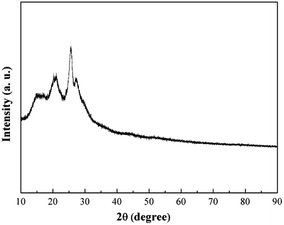 |
| Fig. 4 XRD pattern of the polyaniline coating on 316L. | |
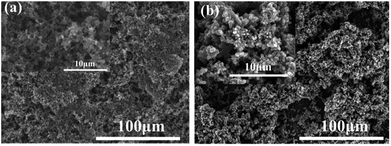 |
| Fig. 5 The SEM images of 316L with single polyaniline coating and Nb-doped TiO2/polyaniline bilayer coating. | |
3.2 Free corrosion potential
Fig. 6 presents the free corrosion potentials for bare 316L and 316L with Pani and Ti0.94Nb0.06O2/Pani coatings in 0.1 M H2SO4 solution bubbled with air at 80 °C for 720 h. For bare 316L, Ecorr increases with time in the initial 25 h and then decreases slowly after immersion for 240 h. Ecorr for the single Pani coating increases slowly to around 220 mVAg/AgCl at the initial stage, which may be related to the passivation of the 316L substrate.10 However, Ecorr decreases slowly after immersion for 240 h, reaching a value of about 155 mVAg/AgCl, which is still higher than that for the bare 316L; the same trend can be seen for the Pani-coated type 304 steel, as reported by Ren.10 This can be related to the inward penetration of the solution into the coating. Unlike the observations for the single Pani coating, Ecorr for the Ti0.94Nb0.06O2/Pani coating is almost constant at around 400 mVAg/AgCl during the 720 h immersion in 0.1 M H2SO4 solution. Both the Pani coating and the Ti0.94Nb0.06O2/Pani coating can improve the corrosion potential of the bare 316L, thus providing anodic protection for 316L, which is similar to the result reported in.17 It can be indicated that the bilayer coating is more protective than the single Pani coating.
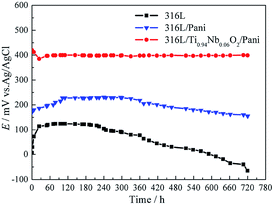 |
| Fig. 6 Free corrosion potentials for bare 316L and 316L with Pani and Ti0.94Nb0.06O2/Pani coatings in 0.1 M H2SO4 solution bubbled with air at 80 °C for 720 h. | |
3.3 Potentiodynamic polarization measurements
Fig. 7 gives the potentiodynamic polarization curves of 316L and 316L with Pani and Ti0.94Nb0.06O2/Pani coatings after immersion in 0.1 M H2SO4 solution bubbled with air at 80 °C for 1 h. The corrosion potential and corrosion current density for bare 316L are around 46 mVAg/AgCl and 24 μA cm−2, respectively, which are obtained by the cathodic Tafel extrapolation, whereas those for 316L with Pani coating are approximately 184 mVAg/AgCl and 20 μA cm−2, and those for 316L with Ti0.94Nb0.06O2/Pani bilayer coating are about 400 mVAg/AgCl and 13.8 μA cm−2. Thus, the Ti0.94Nb0.06O2/Pani bilayer coating causes a positive shift of more than 210 mVAg/AgCl in the corrosion potential relative to the Pani coating. The corrosion current density for the bilayer coating is lower than that for the single Pani coating. Additionally, 316L suffers from transpassive dissolution at potentials higher than around 0.9 V, whereas the Pani- and Ti0.94Nb0.06O2/Pani-coated steels exhibit wider passive regions. These results suggest that the coatings can effectively protect the bare 316L steel from the corrosion of the H2SO4 solution.
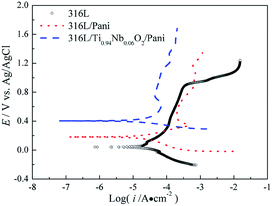 |
| Fig. 7 Potentiodynamic polarization curves of 316L and 316L with Pani and Ti0.94Nb0.06O2/Pani coatings after immersion in 0.1 M H2SO4 solution bubbled with air at 80 °C for 1 h. | |
3.4 Electrochemical impedance spectra at the cathode potential
Fig. 8–10 show the Nyquist and Bode plots for the corrosions of 316L and 316L with Pani and Ti0.94Nb0.06O2/Pani coatings potentiostatically polarized at +600 mVAg/AgCl in 0.1 M H2SO4 solution bubbled with air at 80 °C for various lengths of time. The Nyquist plots for the bare 316L consist of two depressed capacitive loops (Fig. 8a). Although the two capacitive loops cannot be distinguished well, the plots of the phase angle clearly show two time constants (Fig. 8b). The capacitive loops at low frequencies expand with the increasing immersion time, which corresponds to the passivation of the 316L substrate. The plots at the high frequency section represent the behavior of the film, and those in the low frequency section indicate the response to the electrochemical reaction at the interface between the film and the substrate. Unlike the observations for 316L, the Nyquist plots for the corrosion of the coated steels show a small capacitive loop at high frequencies and a line at low frequencies instead of two depressed capacitive loops (Fig. 9 and 10). The line is almost perpendicular to the real axis, probably suggesting an effective barrier behavior. The impedance spectra of 316L can be fitted by the equivalent circuit shown in Fig. 11a, and those of 316L with Pani and Ti0.94Nb0.06O2/Pani coatings can all be fitted by the equivalent circuit shown in Fig. 11b. In Fig. 11, Rs represents the solution resistance, Cdl and Rt represent the double-layer capacitance and charge transfer resistance, Cf and Rf represent the capacitance and resistance of the porous corrosion product layer or coatings, respectively, and Zd represents the diffusion impedance of the barrier layer. The impedance, Zd, is expressed as follows: |
Zd = T(jw)−1/2 Coth[t(jw)1/2]
| (2) |
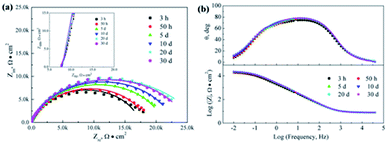 |
| Fig. 8 Nyquist and Bode plots for the corrosion of 316L potentiostatically polarized at +600 mVAg/AgCl in 0.1 M H2SO4 solution bubbled with air at 80 °C for various time durations. Symbol: experimental data; line: simulation data. | |
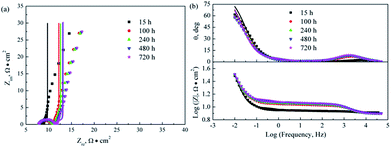 |
| Fig. 9 Nyquist and Bode plots for the corrosion of 316L with Pani coating potentiostatically polarized at +600 mVAg/AgCl in 0.1 M H2SO4 solution bubbled with air at 80 °C for various lengths of time. Symbol: experimental data; line: simulation data. | |
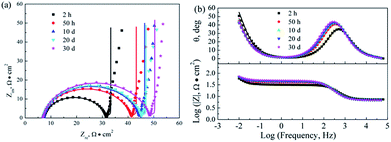 |
| Fig. 10 Nyquist and Bode plots for the corrosion of 316L with Ti0.94Nb0.06O2/Pani coating potentiostatically polarized at +600 mVAg/AgCl in 0.1 M H2SO4 solution bubbled with air at 80 °C for various lengths of time. Symbol: experimental data; line: simulation data. | |
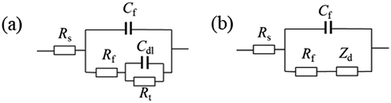 |
| Fig. 11 Equivalent circuit for fitting the impedance spectra of the bare 316L (a) and 316L with Pani and Ti0.94Nb0.06O2/Pani coatings (b). | |
In the fitting procedure, a constant phase angle element (CPE) Qdl is used to replace the element Cdl. The impedance of CPE is expressed as follows:
According to the equivalent circuit shown in Fig. 11, the impedance spectra for the corrosion of the samples have been fitted, and some electrochemical parameters are listed in Tables 1–3.
Table 1 Fitting results of impedance spectra for the corrosion of 316L in 0.1 M H2SO4 solution at 80 °C
Time (h) |
Rs (Ω cm2) |
Yf (Ω−1 cm−2 S−n) |
nf |
Rf (Ω cm2) |
Ydl (Ω−1 cm−2 S−n) |
ndl |
Rt (Ω cm2) |
1 |
7.84 |
9.38 × 10−5 |
0.88 |
0.67 × 104 |
4.08 × 10−5 |
0.89 |
1.07 × 104 |
3 |
7.87 |
7.68 × 10−5 |
0.90 |
0.69 × 104 |
6.25 × 10−5 |
0.78 |
1.20 × 104 |
15 |
7.90 |
7.56 × 10−5 |
0.90 |
0.77 × 104 |
6.99 × 10−5 |
0.84 |
1.06 × 104 |
50 |
7.93 |
7.39 × 10−5 |
0.90 |
0.87 × 104 |
6.40 × 10−5 |
0.82 |
1.13 × 104 |
100 |
7.93 |
7.39 × 10−5 |
0.90 |
0.87 × 104 |
7.07 × 10−5 |
0.84 |
1.06 × 104 |
150 |
7.90 |
7.26 × 10−5 |
0.90 |
0.89 × 104 |
6.57 × 10−5 |
0.77 |
1.21 × 104 |
240 |
7.95 |
7.12 × 10−5 |
0.90 |
0.95 × 104 |
6.16 × 10−5 |
0.76 |
1.30 × 104 |
360 |
7.94 |
6.96 × 10−5 |
0.90 |
1.02 × 104 |
5.99 × 10−5 |
0.67 |
1.52 × 104 |
480 |
7.93 |
6.95 × 10−5 |
0.90 |
1.03 × 104 |
6.55 × 10−5 |
0.70 |
1.40 × 104 |
720 |
7.90 |
6.97 × 10−5 |
0.90 |
1.16 × 104 |
8.03 × 10−5 |
0.90 |
1.01 × 104 |
Table 2 Fitting results of impedance spectra for the corrosion of 316L with Pani coating in 0.1 M H2SO4 solution at 80 °C
Time (h) |
R (Ω cm2) |
Yf (Ω−1 cm−2 sn) |
nf |
Rf (Ω cm2) |
T (Ω−1 cm−2 s0.5) |
t (s0.5) |
3 |
7.447 |
4.88 × 10−4 |
0.7179 |
0.735 |
0.2735 |
1.577 |
15 |
7.719 |
2.03 × 10−4 |
0.8147 |
1.014 |
0.2735 |
1.577 |
50 |
7.331 |
2.38 × 10−4 |
0.8205 |
1.687 |
0.3344 |
1.59 |
100 |
7.721 |
8.06 × 10−5 |
0.9029 |
2.092 |
0.4036 |
1.28 |
150 |
7.845 |
8.31 × 10−5 |
0.8983 |
2.549 |
0.4015 |
1.264 |
240 |
7.845 |
8.41 × 10−5 |
0.896 |
2.81 |
0.3934 |
1.284 |
360 |
7.775 |
7.04 × 10−5 |
0.915 |
3.023 |
0.3167 |
1.69 |
480 |
7.942 |
7.01 × 10−5 |
0.9138 |
3.355 |
0.3025 |
1.738 |
720 |
7.815 |
7.30 × 10−5 |
0.9102 |
3.413 |
0.3013 |
1.75 |
Table 3 Fitting results of impedance spectra for the corrosion of 316L with Ti0.94Nb0.06O2/Pani coating in 0.1 M H2SO4 solution at 80 °C
Time (h) |
R (Ω cm2) |
Yf (Ω−1 cm−2 sn) |
nf |
Rf (Ω cm2) |
T (Ω−1 cm−2 s0.5) |
t (s0.5) |
2 |
7.36 |
4.19 × 10−5 |
0.94 |
23.55 |
0.2171 |
1.544 |
15 |
7.06 |
4.83 × 10−5 |
0.94 |
30.59 |
0.2102 |
1.552 |
50 |
7.10 |
4.96 × 10−5 |
0.94 |
33.55 |
0.2074 |
1.602 |
100 |
7.04 |
5.10 × 10−5 |
0.94 |
34.83 |
0.2111 |
1.524 |
150 |
7.09 |
5.19 × 10−5 |
0.94 |
36.68 |
0.1984 |
1.610 |
240 |
6.98 |
5.34 × 10−5 |
0.94 |
37.12 |
0.1976 |
1.637 |
360 |
6.97 |
5.44 × 10−5 |
0.94 |
37.54 |
0.2105 |
1.554 |
480 |
6.99 |
5.76 × 10−5 |
0.93 |
40.28 |
0.196 |
1.637 |
720 |
6.96 |
5.89 × 10−5 |
0.93 |
40.76 |
0.1955 |
1.580 |
Table 1 indicates that Rt for the corrosion of 316L is around 104 Ω cm2 and hardly changes with the increase in the exposure time, indicating that 316L is in a steady corrosion state. Rf increases gradually with the immersion time from 0.67 × 104 to 1.16 × 104 Ω cm2, corresponding to the formation of a passive film on the substrate during the immersion. Tables 2 and 3 indicate that the value of Rf for the corrosion of the Ti0.94Nb0.06O2/Pani bilayer coating is approximately one order of magnitude larger than that of the single Pani coating, indicating better corrosion resistance. However, Rf for the bilayer coating is slightly larger than that for the single coating. The SO42− ion doping reaction can occur easily at +600 mVAg/AgCl. In this system, the corrosion of the single Pani coating exhibits an effective barrier behavior. The corrosion potential for the bilayer is much higher than that for the single Pani layer; the whole corrosion process of the bilayer is controlled by the diffusion of corrosive ions between the Pani and Ti0.94Nb0.06O2 coatings. The presence of the inner Ti0.94Nb0.06O2 coating increases the diffusion distance of the corrosive ions. All the results indicate that the Ti0.94Nb0.06O2/Pani bilayer coating can more effectively protect 316L than the single Pani coating.
4. Conclusions
Bilayer coatings consisting of an inner Ti0.94Nb0.06O2 layer and an outer Pani layer are prepared on a 316L substrate for use as bipolar plates in proton-exchange membrane fuel cells. The bilayer coating increases the corrosion potential by more than 350 mVAg/AgCl. Moreover, the bilayer coating decreases the corrosion current density of bare 316L from 24 to 13.8 μA cm−2. Potentiostatic polarization at +600 mVAg/AgCl in 0.1 M H2SO4 solution at 80 °C for 720 h occurs at around 400 mVAg/AgCl, confirming the high stability and good corrosion resistance of the bilayer coating. The electrochemical impedance spectra of the bilayer consist of a small capacitive loop at high frequencies and a line at low frequencies, suggesting an effective barrier behavior.
Conflicts of interest
There are no conflicts to declare.
Acknowledgements
This project is supported by the China Postdoctoral Science Foundation (Grant No. 2018M631050), Guangxi Natural Science Foundation for Young Scholars, the Bagui scholars program of Guangxi autonomous region in 2016, Guangxi Key Laboratory of Processing for Nonferrous Metallic and Featured Materials, Scientific Research Project of Guangxi Educational Committee, the Academician Workstation Building Project of Guangxi Zhuang Autonomous Region Scientific and Technological Department [Grant No. [2014] 91].
Notes and references
- B. Cunningham and D. G. Baird, J. Mater. Chem., 2006, 16, 4385 RSC.
- I. S. Lee, J. S. Kim, S. T. Kim, J. H. Kim and Y. Y. Lee, Corros. Sci., 2013, 70, 93 CrossRef.
- H. Tawfik, Y. Hung and D. Mahajan, J. Power Sources, 2007, 163, 755 CrossRef.
- S. Biallozor and A. Kupniewska, Synth. Met., 2005, 155, 443 CrossRef.
- H. Hammache, L. Makhloufi and B. Saidani, Corros. Sci., 2003, 45, 2031 CrossRef.
- A. T. Ozyilmaz, M. Erbil and B. Yazici, Thin Solid Films, 2006, 496, 431 CrossRef.
- D. W. DeBerry, J. Electrochem. Soc., 1985, 132, 1022 CrossRef.
- P. Herrasti and P. Ocon, Appl. Surf. Sci., 2001, 172, 276 CrossRef.
- T. Zhang and C. L. Zeng, Electrochim. Acta, 2005, 50, 4721 CrossRef.
- Y. J. Ren, J. Chen and C. L. Zeng, J. Power Sources, 2010, 195, 1914 CrossRef.
- Y. J. Ren and C. L. Zeng, J. Power Sources, 2008, 182, 524 CrossRef.
- S. Joseph, J. C. McClure, R. Chianeli, P. Pich, P. Pich and P. J. Sebastian, Int. J. Hydrogen Energy, 2005, 30, 1339 CrossRef.
- M. A. Lucio Garcia and M. A. Smit, J. Power Sources, 2006, 158, 397 CrossRef.
- S. Sathiyanarayanan, V. Karpakam, K. Kamaraj, S. Muthukrishnan and G. Venkatachari, Surf. Coat. Technol., 2010, 204, 1426 CrossRef.
- J. F. Pagotto, F. J. Recio, A. J. Motheo and P. Herrasti, Surf. Coat. Technol., 2016, 289, 23 CrossRef.
- T. Abdirgrim, Z.-X. gang and R. Jamal, Mater. Chem. Phys., 2005, 90, 367 CrossRef.
- P. J. Kinlen, D. C. Silverman and C. R. Jeffreys, Synth. Met., 1997, 85, 1327 CrossRef.
|
This journal is © The Royal Society of Chemistry 2018 |
Click here to see how this site uses Cookies. View our privacy policy here.