DOI:
10.1039/C7QM00548B
(Review Article)
Mater. Chem. Front., 2018,
2, 456-467
Ultrathin two-dimensional metallic nanomaterials
Received
30th November 2017
, Accepted 13th January 2018
First published on 16th January 2018
Abstract
Two dimensional (2D) nanomaterials, such as graphene, black phosphorus, covalent–organic frameworks, hexagonal boron nitride, layered double hydroxides, metals, metal oxide, metal–organic frameworks, MXenes, and transition metal dichalcogenides, have attracted increasing attention during recent years. Compared with other 2D nanomaterials, the 2D metallic nanomaterials have their own specialties as well as corresponding applications. In this review, different synthesis methods for 2D metallic nanomaterials are systematically presented, aiming to supply possible fabrication routes and assist the study in this domain. The main applications of the 2D metallic nanomaterials are also discussed.
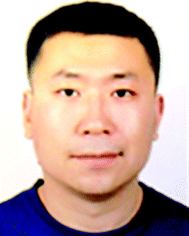
Yang Ma
| Dr Yang Ma is a postdoctoral researcher at the College of Beihang University. He received his PhD from Université Paris-Saclay in 2016 under the supervision of Prof. Jinbo Bai, and continues his research at the School of Materials Science and Engineering at Beihang University. His research focuses on the design and preparation of two-dimensional materials by chemical vapor deposition. |
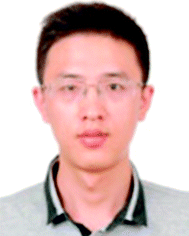
Bin Li
| Dr Bin Li is an Assistant Professor at the School of Materials Science and Engineering at Beihang University. He received his B.S. degree and PhD in Material Science from Beihang University in 2009 and 2016, respectively. His research interests are focused on electrochemical energy storage technology, including metallic lithium anode design and fabrication, sulfur cathode design and fabrication, and energy storage electrochemistry. |
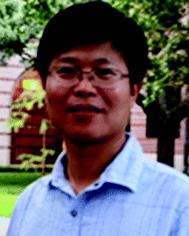
Shubin Yang
| Dr Shubin Yang is a Professor at the School of Materials Science and Engineering, Beihang University. He received his PhD from Beijing University of Chemical Technology in 2008 after carrying out studies on high-performance lithium ion batteries under the guidance of Prof. Huaihe Song. He then pursued postdoctoral studies with Prof. K. Muellen and P. M. Ajayan at Max Planck Institute for Polymer Research and Rice University, respectively. His current research interests involve graphene, MXenes and other two-dimensional materials for energy storage and conversions. |
Introduction
Since the very convenient mechanical cleavage method for graphene exfoliation was discovered in 2004,1 nanomaterials with two-dimensional (2D) structures have attracted tremendous interest. Being only a few atoms of thick but having a much larger lateral area, 2D nanomaterials show their unconventional structure-related properties in physical, chemical, electronic as well as optical aspects, compared to their 3D counterparts. For example, at room temperature, graphene has a thermal conductivity that exceeds 5 × 103 W m−1 K−1, while its charge carrier mobility is up to ∼10
000 cm2 V−1 s−1,2,3 and a guaranteed high modulus of elasticity of ∼1 TPa.4 Graphene also has many other characteristics that indicate the possibilities for its use in electronic and optical devices.5–7 All these advantages have led to the search for other 2D nanomaterials that are superior to the traditional bulk materials, and encouraged the full exploration of their potential applications.
Nowadays, 2D nanomaterials are a part of a really big family that includes many more members than graphene. New members like black phosphorus, covalent–organic frameworks, hexagonal boron nitride, layered double hydroxides, metals, metal oxide, metal–organic frameworks, MXenes, transition metal dichalcogenides, etc. have been synthesized and studied for their structures and properties.8–10 The various synthesis methods that have been developed can usually be classified as either top-down or bottom up strategies. The former includes exfoliation methods like mechanical cleavage,11,12 liquid exfoliation,13,14 exfoliation assisted by chemical reactions15–17 and their derived techniques, aiming to acquire 2D structures from bulk structures. The bottom up strategies are usually achieved by chemical vapor deposition (CVD)18,19 and wet chemical synthesis,20 in which the 2D nanomaterials are formed from other raw materials. It is worth mentioning that like exfoliation methods that include many derived branches, for CVD and wet chemical synthesis, various subdivisions also exist. Apart from the mentioned synthesis routes, there is a new quasi top-down method called repeated size reduction, which is typically applied for 2D metallic nanomaterial fabrication.21 Instead of conducting exfoliation like other top-down methods, this repeated size reduction uses a repeat folding-rolling process to achieve 2D sheets. With all these methods, more and more 2D nanomaterials are being fabricated and a host of studies are being carried out for their further exploration.
Compared to other members in the 2D nanomaterials family, the 2D metallic materials are special because they may have either non-layered crystal structures, like some pure metals & alloys, or layered crystal structures for the metalenes such as silicene, antimonene, germanene, and stanene. The layered/non-layered differences are based on whether the materials have crystal structures with chemical bonding in three dimensions or merely two dimensions.10 However, as far as we know, these two kinds are discussed separately, and their studies still need to be deepened. A brief overview focusing on the 2D metallic nanomaterials is given in this article, where the corresponding synthesis methods for the different layered/non-layered structures are paid significant attention, with the aim of finding the characteristics and potential of each synthesis route. 2D nanomaterial structures made by diverse fabrication methods are respectively discussed by using some typical examples, and their related current/potential applications based on their unique properties are introduced after the presentation of synthesis methods.
Synthesis and structures of 2D metallic nanomaterials
Various synthesis methods are the key point of this review; in this section, after a separation based on the layered/non-layered differences, various synthesis methods are discussed, and the 2D metallic materials that share the same synthesis technique are presented together. One 2D metallic material can be fabricated by different methods, but there are always different features that may influence the demand for specific attributes like thickness, planar surface, crystalline phase, free-standing, etc.
Non-layered crystals
2D metallic materials with the non-layered structure are mainly pure metals and their alloys. For these materials, both chemical and mechanical synthesis methods are included. The chemical methods generally comprise space-confined synthesis, template-directed synthesis, surfactant/ligand assisted energy controlled synthesis, hydrothermal/solvothermal synthesis, seeded growth synthesis as well as some other synthesis routes, and the mechanical methods include different compression approaches (Table 1).
Table 1 Summary of the reported 2D metallic non-layered structure; fcc means face-centered cubic, and hcp means hexagonal close-packed
Synthesis method |
Element |
Dimensions |
Information about structure & morphology |
Thickness |
Lateral dimensions |
Space-confined growth |
Au25 |
3.6 ± 0.5 nm |
Surface > 100 μm2 |
Single-crystalline nanosheets |
Au26 |
Several to tens of nm |
Surface > 100 μm2 |
Single-crystalline nanosheets along the (111) lattice plane, fcc |
Pt27 |
4–10 nm |
up to 500 nm or above |
Nanohole-structured single crystalline nanosheets |
PtCu23 |
0.88–1.32 nm |
from 10 to 50 nm |
fcc nanosheets |
PtCu24 |
0.22 nm |
∼10 nm |
Core–shell with Pt |
|
Template-directed synthesis |
Au28 |
2.4 nm |
200–500 nm |
hcp square sheets, fcc phase induced by electron beam |
Fe29 |
0.26 nm |
1–2 nm |
(100) and (110) Fe edges with the zigzag and armchair edges from graphene respectively |
Ag31 |
∼5 nm |
∼940 nm |
fcc triangular nanosheets |
|
Surfactant/ligand assisted energy controlled synthesis |
Au30 |
2–6 nm |
>10 μm |
Hexagonal(4H) nanoribbons |
Rh32 |
<0.4 nm |
500–600 nm |
hcp nanosheets |
Rh33 |
1.3 ± 0.2 nm |
∼10 nm |
fcc nanosheets |
Pd34 |
<1.8 nm |
20–160 nm |
Growth along the 〈111〉 directions, fcc hexagonal nanosheets |
Pd35 |
>0.26 nm |
Micrometers scale |
fcc, hcp, hexagonal nanosheets |
Pd36 |
1.8 nm |
∼23 nm |
Upper and lower surfaces of the Pd nanosheets are Pd(111) facets while their side walls are Pd(100), fcc, hexagonal nanosheets |
Pd37 |
12–14 nm |
∼1 μm |
Exposed top and bottom surfaces to {111} plane |
Pd38 |
∼2 nm |
70–80 nm |
Ultrathin hexagonal nanosheets |
Co39 |
0.84 nm |
>400 nm |
Slab along the [001] direction |
Co40 |
2–4 nm |
4–90 nm |
hcp nanodisks |
Co41 |
∼4 nm |
less than 75 nm |
hcp nanosheets |
|
Hydrothermal/solvothermal synthesis |
Rh42 |
1.0 ± 0.3 nm |
5–20 nm |
(111) planes, fcc |
Ru43 |
1.3–3.6 nm |
13–27 nm |
A large portion of (0001) facets exposed, triangular &irregular nanosheets |
|
Seeded growth |
Ag44 |
<10 nm |
∼4 μm |
Triangular nanosheets with {111} facets exposed |
Au45 |
∼7.5 nm |
∼59 nm |
Triangular nanoprisms |
Pd@Ag48 |
3.5–19.8 nm |
∼83 nm |
Ag epitaxially grown on the Pd, core–shell hexagonal nanosheets |
Pd@Ag46 |
2.9–6.0 nm |
∼50 nm |
{111} planes, fcc Ag confined on the Pd surface, core–shell structure |
Pd@Au47 |
∼4 nm |
∼30 nm |
{111} planes Au on Pd, core shell hexagonal nanosheets |
Pd@Ru49 |
1.9 nm |
∼4 nm |
fcc, sub-monolayered Ru decorated-Ultrathin Pd nanosheets |
Au@Ag51 |
2.8 ± 0.5 nm |
100–200 nm |
hcp/fcc square sheets |
Au@Pt50 |
3.5 ± 0.7 nm |
>40 nm |
fcc (101) rhombic nanosheets |
Au@Pd50 |
3.4 ± 0.8 nm |
>50 nm |
fcc (101) rhombic nanosheets |
Ag52 |
9.8 ± 1.0 nm |
Bimodal, 70 ± 12 nm, 150 ± 16 nm |
Triangular nanoprisms |
Au@Ag53 |
More than 7 nm |
43–87 nm |
Core–shell nanoprisms |
|
Other chemical methods |
Cu55 |
1.3 nm |
Micrometers scale |
Nanoribbons |
Pd@Pt57 |
4.7 ± 0.1 nm |
∼200 nm |
Core–shell hexagonal nanosheets |
|
Large thermocompression |
Bi60 |
∼2 nm |
More than several μm |
Irregular nanosheets |
|
Repeated size reduction |
Ag, Au, Fe21 |
0.9–3.4 nm |
3–5 μm |
fcc structure nanosheets |
Al61 |
∼3 nm |
>1 μm |
Irregular nanosheets |
Space-confined synthesis
For space-confined synthesis, before the actual synthesis process begins, the “bricks” that build up a 2D space are needed. This confined lamellar interspace, generally having a periodically ordered structure, can effectively slow down the diffusion of the reactive precursor ions, thus limiting the growth of the materials within the confined structure. In the studies that use this synthesis strategy, various polymers are usually used as raw materials for the bricks;22–24 however, there exist polymer-free routes in which some surfactants like dodecylglyceryl itaconate (DGI) and its derivative hexadecyl-glyceryl maleate (HGM) have been applied.25,26 It must be mentioned that there also exists the special case where the space is not strictly lamellar. As was reported in 2009, a surfactant hexagonal lyotropic liquid crystal (LLCs) structure was used for 2D metallic nanosheet synthesis; the structure disappeared during the reduction process, leaving behind the nanohole-structured single-crystalline platinum nanosheets.27 The 2D metallic materials made by this method, for example the PtCu nanosheet, can be as small as a single atom thick,24 which is much thinner than the gold nanoplates synthesized by the same method in 2004, with a thickness of ∼100 nm.22 The products made by this method can have a relatively large area, while keeping the thickness at several nanometers, e.g., the gold membranes (with area surface >100 μm2 and 3.6 ± 0.5 nm thickness) fabricated by Jian Niu and co-workers.25 Pure metallic 2D structures made by this method have a large probability to be single crystalline, due to the template influence of the highly ordered bricks.25,26Fig. 2a shows a typical space-confined synthesis process, and it could be concluded from Fig. 2b and c that the 2D nanomaterials Au membranes made by this method have good crystallization properties as well as a high surface/thickness ratio.
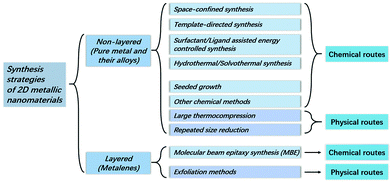 |
| Fig. 1 Classification of the synthesis strategies of 2D metallic nanomaterials. | |
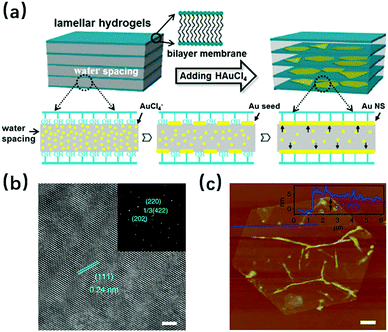 |
| Fig. 2 (a) Schematic illustration of the confined strategy for the synthesis of Au NSs (Reproduced with permission.26 Copyright 2013, American Chemical Society). (b) High-resolution transmission electron microscopy images (scale bar, 2 nm) and (inset) selected-area electron diffraction pattern of a typical Au membrane showing a single crystal. (c) Atomic force microscopy image (scale bar, 1 μm) with the corresponding height profile (inset) of a typical Au membrane (reproduced with permission.25 Copyright 2014, Nat. Commun.). | |
Template-directed synthesis.
Even in the space-confined synthesis the formed surfactant bricks can be regarded as soft- templates, the template-directed synthesis still has its difference with the former. As in this case, the space is not limited as a lamellar form, and it is the pre-prepared non-metallic substrate that plays the role of growth template, over which the 2D metallic materials are synthesized directly. For example, Au and Fe nanosheets have been reported, which were synthesized on graphene oxide (GO) and graphene pores, respectively.28,29 Although both examples can be classified in the same synthesis method, their growth mechanisms, or more precisely the template influenced modalities still differ. In the case of the Au nanosheets, it is the polarity induced by the oxygenated functional groups on the GO surface, cooperating with the hexane/ethanol solution that contributes to a sheet-like tendency for the nanosheet formation.30 For the Fe nanosheets, the free-standing single-atom-thick iron membranes are mainly influenced by the interaction between Fe and C atoms at the pore edges of the graphene. It was found that the interfaces between Fe(110) and the armchair graphene edge are the most stable, and the graphene pore size limits the planar size of the Fe membrane to a diameter of only 1–2 nm. The electron beam was involved in both experiments; it was used to carry out the Au nanosheet hcp–fcc structure transformation and was an energy source for Fe membrane formation. It has been proved by the work of A. Courty and co-workers, that the template contributes to good product quality since the silver particles recrystallize more easily on highly oriented pyrolitic graphite (HOPG) than on amorphous graphite, which resulted in nine times larger triangular single crystals on the former substrate than on the latter.31Fig. 3a shows the formation process for the mentioned Au square sheet, while Fig. 3b and c provide the structural information for the Fe sheet in the graphene pore.
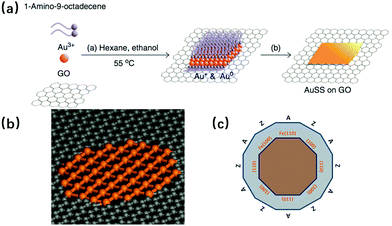 |
| Fig. 3 (a) Schematic illustration of the formation process of the Au square sheet by the template-directed synthesis method (reproduced with permission.28 Copyright 2011, Nat. Commun.). (b) Atomic structure of a suspended mono/atomic Fe layer in a graphene pore. (c) Schematic diagram showing the relationship between the (100) and (110) Fe edges and the zigzag (Z) and armchair (A) edges from graphene (reproduced with permission.29 Copyright 2014, Science). | |
Surfactant/ligand assisted energy controlled synthesis.
Surfactant/ligand assisted energy controlled synthesis is a commonly used method for the fabrication of 2D metallic nanomaterials such as Au,30 Rh,32,33 Pd,34–38 Co,39–41etc.; this production process has resulted in the 2D form for many different metals. Various surfactants or ligands are highly required in this method, including polymers,32 active gases,35 amines33,39etc. Since the surface energy is effectively influenced after the addition of these materials to the original system, the growth in some specific direction is favored/inhibited, which facilitates the formation of the anisotropic planar structure. For example, during the synthesis of Pd nanosheets made by Xi Yin and co-workers,35 CO gas was bubbled into the Pd(acac)2/glacial acetic acid solution, which led to the preferred adsorption of the formed Pd4(CO)4(OAc)4 onto the Pd(110) surface, resulting in the anisotropic growth of Pd nanosheets. For the Co nanosheet made by Shan Gao and co-workers,39 as shown in Fig. 4, n-butylamine was used and adsorbed on the hydrolysis product of Co(acac)3, thus reducing the surface energy and avoiding the aggregation. Compared with the space-confined synthesis and template-directed synthesis where the confined space or template are already prepared before the beginning of the real synthesis process, surfactants/ligands are generally added to the reaction system simultaneously with the metal source in this method, which takes effect mainly through their surface energy influence. The thickness of the 2D metallic nanosheet made by this method can be as little as one atom thick, while the single crystals can be guaranteed due to the surfactant/ligand contribution.32
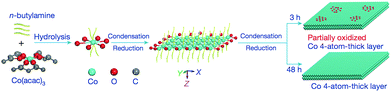 |
| Fig. 4 Schematic formation process for the partially oxidized and pure-Co 4-atomic-layer via the surfactant/ligand assisted energy controlled synthesis method (reproduced with permission.39 Copyright 2016, Nature). | |
Hydrothermal/solvothermal synthesis.
Contrary to the surfactant/ligand assisted energy controlled synthesis where the surfactants/ligands are added to the reaction system with the metal sources, there is also hydrothermal/solvothermal synthesis, which includes two steps to fabricate 2D metallic nanosheets. In the first step, the materials having surfactant/ligand function are released by their precursors during the hydrothermal process, thus it could be regarded as a quasi-surfactant/ligand-free process to some extent; in the second step, rather than surfactant/ligand influences, it is the metal's own tendency to lower the surface energy that has the crucial impact in determining the product morphology. For example, in the work by Changping Hou and co-workers,42 it is the combined effect of CO and H2 that leads to the formation of ultrathin Rh 2D nanosheets. These two materials are not directly provided at the beginning of the reaction, but originate from the formaldehyde solvothermal decomposition during the synthesis process. According to the study by An-Xiang Yin and co-workers,43 rather than the polymer poly(vinylpyrrolidone) (PVP) and formaldehyde decomposition product influence, it is due to the much lower surface energy of Ru(0001) that intrinsic growth of Ru nanocrystals occurs. It has to be pointed out that even in other synthesis methods, the hydrothermal/solvothermal process may also exist; in this synthesis method, this process sometimes has an important role, which contributes to the decomposition of the mentioned surfactant/ligand precursors. Even though there is no direct surfactant/ligand, the synthesized 2D structures are still crystallized with the thickness limited to several nanometers, and their surface diameters are no more than 30 nm.
Seeded growth synthesis.
Seeded growth synthesis usually involves two steps. The first step is the fabrication of so-called “seeds”, which are usually metallic (rather than the non-metallic ones in the template-directed synthesis), while in the following step these seeds are used for the growth of the final nanosheet structure. Even though the seeds and the final products may have the same elementary composition, new elements are likely to be added and bimetallic structures are constructed. The work of Qiao Zhang and co-workers shows a seeded growth synthesis process where the seeds and final synthesized nanosheet are both Ag, in which the Ag seeds were firstly formed under the influence of PVP and citrate ion, then the Ag nanosheets were anisotropically synthesized due to the block of citrate ligands on {111} facets after the removal of PVP polymer (as shown in Fig. 5a).44 Erik Martinsson and co-workers have synthesized anisotropic gold nanoprisms from gold seeds, followed by oxygen plasma treatment to improve the sensing performance and catalytic properties of the products.45 Bimetallic nanosheets like Pd@Ag, Pd@Au Pd@Ru have been reported where Pd plates were synthesized by surface energy control as seeds firstly, then the Ag, Au and Ru were respectively deposited on the seeds to form the final core–shell structures.46–49 According to the work of Zhanxi Fan from the Hua Zhang group,50,51 ultrathin face-centered-cubic Au@Ag, Au@Pt and Au@Pd have been synthesized, using just the Au nanosheets, via template-directed synthesis. It is worth mentioning that possessing a core–shell structure has no inherent interrelation to the thickness of these bimetallic nanosheets. For example, for the Pd@Ag made by Zheng and co-workers, the thinnest nanosheets were only 2.9 nm; moreover, the diagnostic results showed that the Ag deposited on Pd had well-defined lattice fringes corresponding to the {111} planes of the face-centered-cubic (fcc) structure. The corresponding reaction mechanism for this work is shown in Fig. 5b, in which Ag+ is reduced to Ag(0) by hydrogen atoms and then deposited directly on Pd.46 This example of thinness as well as good crystallinity proves that the product thickness and quality can be guaranteed by using the seeded growth synthesis method. In this synthesis process, plasmon is sometimes used. By changing the wavelength of the incident light and the exposure time, the photo- induced conversion from nanoparticles to nanosheets, as well as the control of the final product properties can be achieved.52,53 This photo induced method is not limited to only the seeded growth synthesis of 2D nanosheets, it can also be used for nanoparticle formation via other synthesis methods.54 In fact, this seeded growth synthesis, especially for the core–shell structure cases, could be more or less regarded as template-directed synthesis to a certain extent. However, for the 2D nanosheets synthesized by the template-directed method, since their growth usually occurs over the non-metallic substrates, additional procedures are often needed to separate the as-grown products from the substrates. For the core–shell ones, since their “templates” are already metal nanosheets, the products and the templates could be regarded as an entirety for the follow-up studies and utilizations.
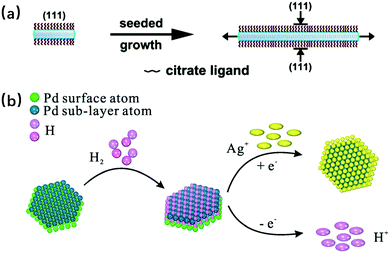 |
| Fig. 5 (a) Schematic illustration of the anisotropic seeded growth of Ag nanosheets where the citrate ions selectively protect the {111} basal facets of Ag nanoplates and only allow lateral overgrowth (reproduced with permission.44 Copyright 2010, Nano. Lett.). (b) Proposed reaction mechanism for the synthesis of Pd@Ag core–shell nanocrystals in the presence of H2 (reproduced with permission.46 Copyright 2014, Nanoscale). | |
Other chemical synthesis routes.
Apart from all the synthesis methods mentioned above, there are also other chemical fabrication routes that are not typical, which are hard to classify, such as the Cu nanosheets made by Zhennan Wu and coworkers.55 In their experiments, firstly copper(II) acetylacetonate (CuAc2) was reduced by 1-dodecanethiol (DT) in a solvent, then under the influence of capping ligand, DT, as well as mutual dipolar attraction effects, the reduction product Cu12DT8Ac4 nanoclusters were generated to form nanowires, and after an annealing process of these nanowires, the 2D “Cu” ribbons were obtained, for which the thickness was only 1.3 nm. The corresponding synthesis process is shown in Fig. 6; both the surface energy controlled method and annealing treatment were involved in this process. In addition, the final so-called “Cu” ribbons are in fact “Cu8DT8”, according to their mass spectrometry diagnostic results. Underpotential deposition may also be considered as a possible synthesis process, and there are still many studies that have been conducted in this domain.56–59 In these studies, thin layer metals are electro-deposited on the pre-prepared foreign metal substrates at a potential less negative than their equilibrium (Nernst) potential for the reduction. Among the synthesis products, some have surface roughness less than 0.5 nm and the layer can be atomically thin,59 which strongly suggests that this synthesis route can be used in the case of 2D metallic nanosheets fabrication. However, the separation of the thin metal film from the substrates has not yet been widely studied, and further studies are needed to obtain free-standing metallic nanosheets. As has been previously discussed, for the core shell structures there is sometimes no need to separate the products and substrates, and it is suggested that the underpotential deposition can be applied to the as-prepared 2D nanosheets to achieve a core–shell structure. Wenxin Wang and co-workers have realized this idea in their work and 2D ultrathin core–shell Pd@Pt nanosheets have been synthesized through underpotential deposition, which have outstanding catalytic activity and stability for the oxygen reduction reaction (ORR) application.57
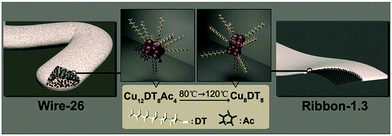 |
| Fig. 6 Evolution of Cu nanocluster self-assembly architectures from Wire-26 to Ribbon-1.3, where Wire-26 represents the nanowire whose average diameter is 26 nm, and Ribbon-1.3 represents the 1.3 nm thick nanoribbon (reproduced with permission.55 Copyright 2014, Angew. Chem., Int. Ed.). | |
Compression synthesis.
Besides the wet chemical synthesis discussed above, there are also synthesis methods that proceed in a more mechanical way, such as compression. Methods like large thermocompression and repeated size reduction belong to this category. According to the report by Naveed Hussain and co-workers, using the large thermocompression method, the Bi nanoparticles were compressed under certain temperature/pressure parameters, so that free-standing ultrathin Bi nanosheets were synthesized with thickness is as low as 2 nm, while the surface diameter was more than several micrometers (the synthesis process is shown in Fig. 7).60 Compared with this large thermocompression method where the nanosheets are obtained by the compression process only once, the nanosheets acquired by repeated size reduction need to experience the compression several times, where the metals are repeatedly folded and rolled. Hanwen Liu and co-workers have synthesized Ag, Au and Fe nanosheets by this repeated size reduction method.21 It is worth mentioning that the manipulation of the repeated size reduction process occurs at room temperature, and the product thickness can reach under 1 nm, with their lateral sizes being ∼3–5 μm; moreover, diagnostic results suggest that these produced nanosheets are more like defect-free crystals with good crystallinity. Recently, the electrochemically active Al 2D nanosheets with ∼3 nm thickness and large aspect ratio were fabricated in our group,61 for which the size reduction method was also applied. Besides the original synthesis process, where the Al and Sn were pressed simultaneously and then the Sn composition was removed by chemical etching, the new composition graphene was added to the as-prepared Al layers in the last step, so that Al layers-graphene films were obtained by vacuum filtration. This adjusted size reduction method involves the addition of new materials, and thus serves to achieve new properties and benefit the expansion of potential applications. Both repeated size reduction procedures mentioned above are shown in Fig. 8a and b respectively.
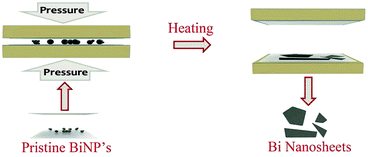 |
| Fig. 7 Schematic diagram illustrating the fabrication process for Bi nanosheets using pristine Bi nanoparticles (BiNP's) via the thermocompression method (reproduced with permission.60 Copyright 2017, Small). | |
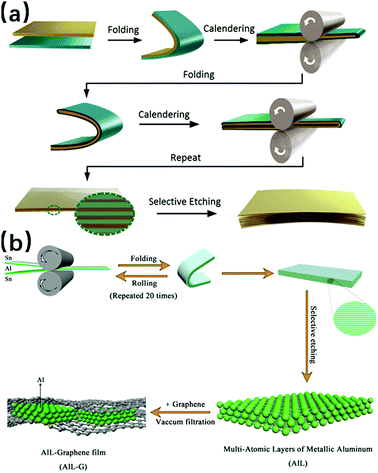 |
| Fig. 8 (a) Schematic of the fabrication of metal nanosheets by the repeated size reduction method (reproduced with permission.21 Copyright 2016, Adv. Mater.). (b) Schematic of the synthesis process of Al layers-Graphene films (reproduced with permission.61 Copyright 2017, Adv. Funct. Mater.). | |
Layered crystals
Compared with the non-layered 2D metallic materials, the layered materials are mainly metalenes, and their synthesis methods are not as rich as the methods applied for non-layered structures. Major synthesis methods applied on layered crystals concentrate on methods of molecular beam epitaxy (MBE) and types of exfoliation. Besides these two methods, it should be mentioned that other methods exist where the metalenes are fabricated in a non-pure form. For example, according to the work of Eiichi Noguchi and coworkers, using a mixture of Si and Ca as the starting material, CaSi2 was synthesized through temperature-controlled heating under an argon atmosphere, in which the hexagonal Si bilayer (silicene) and trigonal Ca monolayer were stacked alternately.62 However, these kinds of synthesis methods will not be discussed in detail in this review, but the following separation techniques are presented, by which the synthesized metalenes can be isolated without any damage. As a complementary tool to analyze the atomic and electronic structures of the fabricated metalenes, density functional theory (DFT) calculations are often conducted along with the diagnostic methods like scanning tunneling microscopy (STM), low energy electron diffraction (LEED), angle-resolved photoemission spectroscopy (ARPES), etc. Some DFT results will be shown, aiming to assist the comparisons and explanations (Fig. 1).
Molecular beam epitaxy synthesis.
In a typical synthesis by molecular beam epitaxy (MBE), firstly a clean substrate needs to be made with argon ion sputtering and annealing under ultrahigh vacuum (UHV) until the requisite crystal structure is obtained on the surface; then, still under UHV conditions, the metal source is heated followed by the evaporated content being deposited on the prepared substrate. In the end, with another annealing process of the substrate, the desired metalene is acquired. So far, various metalenes have been fabricated through this method, including silicene,63–66 germanene,67–69 antimonene,70 stanene,71 bismuthene,72 hafnene,73etc., and different substrates have been studied as well. Among all these studies, even for the same metalene, sometimes there are multiple choices for the substrates, which eventually influence the metalene structure. Taking germanene as an example, with respect to varied Au(111), Al(111) and Pt(111) substrates, its superstructure is identified as (√7 × √7), (3 × 3) and (√19 × √19), respectively, and the corresponding illustrations are shown in Fig. 9.67–69 This change makes it more complicated to determine a universal structure for a certain metalene; thus, the substrate influence always needs to be considered for even the metalenes formed by the same element.
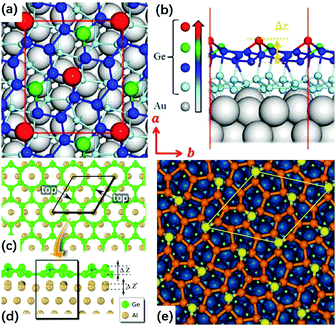 |
| Fig. 9 Top (a) and side (b) views of the atomic structure of the germanene on Au(111) substrate. The red rectangle represents the unit cell of germanene. The vectors a and b represent lattice directions. Δz is the buckling height of germanene. (Reproduced with permission.67 Copyright 2017, ACS Nano.). Top (c) and side (d) views of the relaxed atomic model of the germanene on Al(111) surface. The rhombus indicates the unit mesh of germanene. The protruding Ge atoms are labeled as the top. For clarity, only the first Al plane is displayed in (c). (Reproduced with permission.68 Copyright 2015, Nano Lett.). (e) Top view of the relaxed atomic model of the germanene on Pt(111) substrate. The blue, yellow, and orange spheres represent Pt, protruding Ge, and other Ge atoms, respectively; a unit cell is outlined in yellow (reproduced with permission.69 Copyright 2014, Adv. Mater.). | |
Exfoliation synthesis.
The exfoliation method is usually used to get 2D layered structures for the metalenes, which have a natural stable allotropic form within the bulk. Due to their special rhombohedral layered structures as shown in Fig. 10a, antimonene and bismuthene are good candidates for this exfoliation manipulation, and the ways to exfoliate them are relatively mechanical, like the repetitive peeling-pressing transformation using adhesive tape,74 sonication of the crystals in various solvents,75,76 as well as realizing the separation by shear force in aqueous dispersion with surfactants.77 However, besides its outstanding performance to obtain large and stable metalenes in the situations above, the exfoliation method has another task, which is to separate the synthesized metalenes from substrates, usually acting as an effective complement to the MBE synthesis. In this case, the exfoliation process is no longer that mechanical because chemical reactions play an important role instead. For example, according to the simulation results obtained by T. P. Kaloni and U. Schwingenschlögl, it has been found that the hydrogenation can effectively reduce the interaction between the germanene and the substrate GaAs(0001); thus the germanene can be exfoliated to be free standing.78 For silicene, using the DFT simulation, L. Tsetseris and D. Kaltsas suggested that hydrogenation as well as calcium intercalation also work well for silicene/Ag(111) substrate exfoliation.79 The thesis work of Elisabeth Bianco proves experimentally the hydrogenation contribution for exfoliation in an indirect way, in which a topotactic deintercalation route for hydrogen-terminated germanene was proposed.80 With hydrogen atoms in the vertical direction of the surface, the layers of this special germanene are held together mainly via van der Waals forces, and can be exfoliated by scotch tape and polydimethylsiloxane. The synthesis process of this work is shown in Fig. 10b.
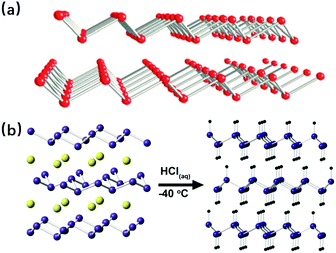 |
| Fig. 10 (a) Structures of rhombohedral layered antimonene (above) and bismuthene (below) (reproduced with permission.77 Copyright 2017, Angew. Chem., Int. Ed.). (b) Schematic illustration of the topotactic deintercalation of CaGe2 to hydrogen-terminated germanene (reproduced with permission.80 Copyright 2013, ACS Nano). | |
Applications of the 2D metallic materials
Thanks to various synthesis methods, a wide range of 2D metallic materials have been fabricated. Their diverse properties have been studied in depth, aiming to make full use of potential abilities in different domains. In order to focus on the unique properties such as dominantly exposed active metallic sites, fast kinetics for energy storage (rapid diffusion of electron and ions) and surface plasmon resonance (SPR), the applications like catalysis, electronic/battery devices, as well as various applications related to surface plasmon resonance, etc., have been developed. In this section, the three mentioned applications will be presented, but there are other applications such as hydrogen sensing,37 laser protection,76 magnetic memory devices,81etc.
Catalysis
It is well known that there are metals that have good catalytic performance even in bulk form, like Fe, Co, Ni and some noble metals; in a 2D planar structure, their catalytic behaviours are enforced due to more exposed active metallic sites. This suggests therefore that the 2D metallic materials can be good candidates for the study of catalytic activities. These functions reflect two aspects: oxidation and reduction. For the former, it mainly involves the oxidation of carbon monoxide,42 ethanol23 and formic acid.24,34,35,82 Compared with the traditional nanoparticles, the nanosheets can significantly lower the reaction energy barriers in some cases. For example, in the work of Changping Hou and co-workers,42 once the Rh nanoparticles were replaced by Rh nanosheets, the necessary temperature for 100% CO conversion was reduced by 10 K, while the starting conversion temperature decreased by 50 K. The use of metallic nanosheets not only influences the reaction energy barriers, but also enhances the catalytic properties; there is an example where during the formic acid oxidation process, the free-standing palladium nanosheets exhibited electrocatalytic activity that was 2.5 times greater, compared with the commercial palladium black catalyst.34 Apart from their influences on oxidation, the 2D metallic materials are also studied for their performance as reduction catalysts, thus the applications like the oxygen reduction reaction,27,55,82 hydrogen evolution reaction,77,83 hydrogenation and hydroformylation reaction,32,43 as well as CO2 electroreduction39 are under research. In the study of these applications, some results have been really surprising. For example, during the study of atomic cobalt layers, it has been found that only partial oxidation can even make this material experience a total change from nearly non-catalytic to very active for CO2 reduction.39 By comparing the results shown in Fig. 11, the advantages of nanosheets over nanoparticles have also been proved in the field of reduction catalysis. These discoveries are so inspiring that they encourage deeper exploration of the potential of the 2D metallic materials.
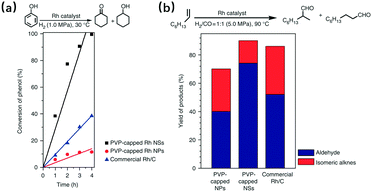 |
| Fig. 11 Comparison of the catalytic ability of PVP-capped Rh nanosheets (NSs), PVP-capped Rh nanoparticles (NPs), and commercial Rh/C. (a) Hydrogenation of phenol and (b) hydroformylation of 1-octene (reproduced with permission.32 Copyright 2014, Nat. Commun.). | |
Electronic/battery devices
Using 2D nanomaterials to make electronic/battery devices has been a hot issue in recent years, and many studies have been made in this field using graphene, transition metal dichalcogenides, black phosphorus, etc., aiming to make full use of their unique features like good flexibility, relatively high carrier mobility and tuneable band structure.84–86 Therefore, it is reasonable to look into 2D metallic nanosheets to see what they can do, and to date, there have already been some achievements. For example, in the work of Jian Niu and co-workers,25 they successfully synthesized single crystalline Au membranes via space-confined synthesis, with resistivity of 4.0 × 10−8 Ω m. This value is 1–2 orders of magnitude lower than the traditional thermally evaporated Au film conductivity,87 for which both transfer and evaporation processes bring undesired damages and defects on the film. Apart from this Au membrane, there are other 2D metallic materials being studied that have the potential for application in electronic devices, due to their properties like high transmittance, superior plasmonic performance, etc.26,46,71,74 In addition, using 2D metallic materials as battery units is also being researched, in which silicene has displayed its advantages as a promising anode for lithium-ion batteries.63 It has better performance than the bulk Si, due to its high aspect ratio and ultrathin nature, which are favorable for the fast diffusion of lithium ions and electrons. Moreover, the multilayer silicene anode has enough space to prevent itself from being pulverized under volume change caused by repeated charge/discharge courses, and its high chemical resistance to oxygen allows it to withstand more than 150 h of exposure, even to the ambient environment. If extending the pure 2D metallic nanomaterials to those with metal containing layers, there can be even more candidates for anodes. In our group, we have used Ti3C2, graphene and BN as skeletons; they successfully isolated the Li metal during the size reduction process, and thus the sandwich structures were formed, in which the 2D Li metal was achieved between the Ti3C2, graphene and BN layers.88 This structure not only benefits the Li ion and electron transfer, but also buffers the volume change during the charge/discharge process, leading to a high cycling stability (more than 400 h) as well as an outstanding rate performance (at 5 mA cm−2). The illustration of this structure and the detailed comparison of cycle performances are shown in Fig. 12, where G signifies graphene. With more and more new 2D metallic materials being fabricated, there is a greater chance that new applications will be developed in this aspect.
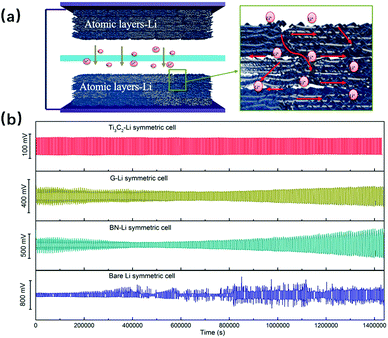 |
| Fig. 12 (a) Schematic illustration of the symmetric cell with numerous transfer channels for lithium ions and (b) the symmetric cell cycle performances of Ti3C2–Li, G–Li, BN–Li and bare Li at a constant current density of 1.0 mA cm−2 (reproduced with permission.88 Copyright 2017, Nano Energy). | |
Applications related to surface plasmon resonance
For the metal nanostructures, one of their typical characteristics is the surface plasmon resonance (SPR), which is fundamental to many applications like optical sensing,89 catalytic reactions probes,90 semiconductor optical absorption enhancement,91etc. Since anisotropic structures can contribute to good SPR tunability over a wide spectral region,48 studying the SPR performance of the 2D metallic materials has attracted constant attention. To date, many achievements have been made, in which the photothermal therapy is the most eye-catching, where the 2D metallic materials are used as light-activated nano heaters for curing cancer. Since the nanosheets are needed to work in the human body, different nanosheets have been synthesized and investigated, such as Ag,44 Pd,34 Pd@Ag48 as well as Pd@Au,47etc., aiming to achieve the best properties to serve the medical treatment goal. In particular, for the mentioned Pd@Au case, not only have SPR peaks changing from 600 nm to 1300 nm been achieved by nanosheet size adjustment, but the other aspects like photothermal efficiency, nanosheets blood circulation as well as toxicity effects have been experimentally studied through operations on mice, and it turns out that this operation is quite effective for tumor treatment (as shown in Fig. 13). This work provides further evidence to promote advances in SPR applications.
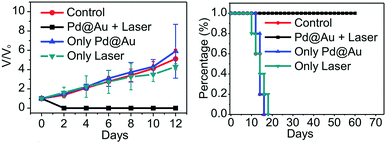 |
| Fig. 13 (a) Relative tumor volume and (b) survival rate curves of different groups of mice. Relative tumor volumes were normalized to their initial sizes (reproduced with permission.47 Copyright 2014, Adv. Mater.). | |
Conclusions and perspectives
In summary, focusing on the characteristics and differences, we have briefly introduced various synthesis methods for the ultrathin two-dimensional metallic nanomaterials, including a series of top-down and bottom-up strategies. It can be seen that for different kinds of metallic nanosheets, e.g., non-layered crystal nanosheets and layered crystal nanosheets, their corresponding synthesis methods differ. Even for same elements, their nanosheets may have some different structures and properties along with the varied synthesis routes, as these factors have their roots in distinct growth mechanisms; regardless of the synthesis process, it is always important to have good control over the thickness and size. As previously mentioned, there are several methods where the products could be under 1 nm thick, while there are synthesis processes by which the product's lateral dimensions are in the micrometer scale. However, even in the same synthesis strategy, these values change along with different metals and varied experimental procedures. To obtain 2D metallic materials with desired structures and properties that can serve accurate demands, deep consideration of the choice of materials/synthesis methods is highly recommended. For the synthesized 2D metallic nanomaterials, they have shown their potential applications in many aspects, such as catalysis, electronic/battery devices, applications related to surface plasmon resonance, etc. As these applications are based on the 2D metallic properties, the modifications and updates for the existing methods can effectively lead to new improvements as well as expand the applications range.
For the further study of 2D metallic nanomaterials, there are some challenges that need to be overcome. The study of the 2D metals is still mainly limited to the domain of Fe, Co, Cu, Al, the noble metals as well as several metalenes; thus, for other metals, their new properties along with their corresponding applications need to be explored. Moreover, the combination of 2D metallic nanomaterials with other kinds of materials may also lead to unexpected performances and so the research in this domain is in high demand. High yield production of desired 2D metallic materials is another challenge to overcome, which calls for deeper understanding of the synthesis mechanisms. Nowadays, there are various characterization methods that have been used for the study of 2D metallic materials, including atomic force microscopy (AFM),92 optical microscopy,76 Raman spectra,77 scanning tunneling microscopy (STM),67 transmission electron microscopy (TEM),30 X-ray photoelectron spectroscopy (XPS),49 X-ray diffraction (XRD),93etc., and the DFT calculation also contributes significantly to a better understanding of the structures, properties as well as growth mechanisms. However, there is still the need for in situ characterization techniques that can contribute to observations and diagnostics during the synthesis. New detection methods are needed in order to better understand how the 2D metallic nanomaterials can be applied to make more appropriate use of their unique features. New techniques are therefore required to achieve the transfer from ex situ to in situ for the existing diagnostic methods. Considering the new developments in synthesis methods and applications in recent years, it is worth looking forward to the future performance of the 2D metallic nanomaterials.
Conflicts of interest
There are no conflicts to declare.
Acknowledgements
This work was financially supported by National Natural Science Foundation of China (No. 51572007 and 51622203), “Recruitment Program of Global Experts”
Notes and references
- K. S. Novoselov, A. K. Geim, S. V. Morozov, D. Jiang, Y. Zhang, S. V. Dubonos, I. V. Grigorieva and A. A. Firsov, Science, 2004, 306, 666–669 CrossRef CAS PubMed.
- A. A. Balandin, S. Ghosh, W. Bao, I. Calizo, D. Teweldebrhan, F. Miao and C. N. Lau, Nano Lett., 2008, 8, 902–907 CrossRef CAS PubMed.
- A. K. Geim and K. S. Novoselov, Nat. Mater., 2007, 6, 183–191 CrossRef CAS PubMed.
- C. Lee, X. Wei, J. W. Kysar and J. Hone, Science, 2008, 321, 385–388 CrossRef CAS PubMed.
- Y. Zhang, Y. W. Tan, H. L. Stormer and P. Kim, Nature, 2005, 438, 201 CrossRef CAS PubMed.
- M. D. Stoller, S. Park, Y. Zhu, J. An and R. S. Ruoff, Nano Lett., 2008, 8, 3498–3502 CrossRef CAS PubMed.
- R. R. Nair, P. Blake, A. N. Grigorenko, K. S. Novoselov, T. J. Booth, T. Stauber, N. M. Peres and A. K. Geim, Science, 2008, 320, 1308 CrossRef CAS PubMed.
- H. Zhang, ACS Nano, 2015, 9, 9451–9469 CrossRef CAS PubMed.
- C. Tan, X. Cao, X.-J. Wu, Q. He, J. Yang, X. Zhang, J. Chen, W. Zhao, S. Han and G.-H. Nam, Chem. Rev., 2017, 117, 6225–6331 CrossRef CAS PubMed.
- F. Wang, Z. Wang, T. A. Shifa, Y. Wen, F. Wang, X. Zhan, Q. Wang, K. Xu, Y. Huang and L. Yin, Adv. Funct. Mater., 2017, 27, 1603254 CrossRef.
- M. Yi and Z. Shen, J. Mater. Chem. A, 2015, 3, 11700–11715 CAS.
- H. Li, J. Wu, Z. Yin and H. Zhang, Acc. Chem. Res., 2014, 47, 1067–1075 CrossRef CAS PubMed.
- V. Nicolosi, M. Chhowalla, M. G. Kanatzidis, M. S. Strano and J. N. Coleman, Science, 2013, 340, 1226419 CrossRef.
- K. R. Paton, E. Varrla, C. Backes, R. J. Smith, U. Khan, A. O’Neill, C. Boland, M. Lotya, O. M. Istrate and P. King, Nat. Mater., 2014, 13, 624–630 CrossRef CAS PubMed.
- Z. Zeng, C. Tan, X. Huang, S. Bao and H. Zhang, Energy Environ. Sci., 2014, 7, 797–803 CAS.
- K. Parvez, Z.-S. Wu, R. Li, X. Liu, R. Graf, X. Feng and K. Müllen, J. Am. Chem. Soc., 2014, 136, 6083–6091 CrossRef CAS PubMed.
- Y. Zhu, S. Murali, W. Cai, X. Li, J. W. Suk, J. R. Potts and R. S. Ruoff, Adv. Mater., 2010, 22, 3906–3924 CrossRef CAS PubMed.
- Y. Zhang, L. Zhang and C. Zhou, Acc. Chem. Res., 2013, 46, 2329–2339 CrossRef CAS PubMed.
- J. Yu, J. Li, W. Zhang and H. Chang, Chem. Sci., 2015, 6, 6705–6716 RSC.
- C. Tan and H. Zhang, Nat. Commun., 2015, 6, 7873 CrossRef CAS PubMed.
- H. Liu, H. Tang, M. Fang, W. Si, Q. Zhang, Z. Huang, L. Gu, W. Pan, J. Yao and C. Nan, Adv. Mater., 2016, 28, 8170–8176 CrossRef CAS PubMed.
- J. U. Kim, S. H. Cha, K. Shin, J. Jho and J. C. Lee, Adv. Mater., 2004, 16, 459–464 CrossRef CAS.
- F. Saleem, Z. Zhang, B. Xu, X. Xu, P. He and X. Wang, J. Am. Chem. Soc., 2013, 135, 18304–18307 CrossRef CAS PubMed.
- F. Saleem, B. Xu, B. Ni, H. Liu, F. Nosheen, H. Li and X. Wang, Adv. Mater., 2015, 27, 2013–2018 CrossRef CAS PubMed.
- J. Niu, D. Wang, H. Qin, X. Xiong, P. Tan, Y. Li, R. Liu, X. Lu, J. Wu, T. Zhang, W. Ni and J. Jin, Nat. Commun., 2014, 5, 3313 Search PubMed.
- H. L. Qin, D. Wang, Z. L. Huang, D. M. Wu, Z. C. Zeng, B. Ren, K. Xu and J. Jin, J. Am. Chem. Soc., 2013, 135, 12544–12547 CrossRef CAS PubMed.
- T. Kijima, Y. Nagatomo, H. Takemoto, M. Uota, D. Fujikawa, Y. Sekiya, T. Kishishita, M. Shimoda, T. Yoshimura, H. Kawasaki and G. Sakai, Adv. Funct. Mater., 2009, 19, 545–553 CrossRef CAS.
- X. Huang, S. Li, Y. Huang, S. Wu, X. Zhou, S. Li, C. L. Gan, F. Boey, C. A. Mirkin and H. Zhang, Nat. Commun., 2011, 2, 292 CrossRef PubMed.
- J. Zhao, Q. Deng, A. Bachmatiuk, G. Sandeep, A. Popov, J. Eckert and M. H. Rümmeli, Science, 2014, 343, 1228–1232 CrossRef CAS PubMed.
- Z. Fan, X. Huang, Y. Chen, W. Huang and H. Zhang, Nat. Protoc., 2017, 12, 2367–2378 CrossRef CAS PubMed.
- A. Courty, A.-I. Henry, N. Goubet and M.-P. Pileni, Nat. Mater., 2007, 6, 900–907 CrossRef CAS PubMed.
- H. Duan, N. Yan, R. Yu, C.-R. Chang, G. Zhou, H.-S. Hu, H. Rong, Z. Niu, J. Mao and H. Asakura, Nat. Commun., 2014, 5, 3093 Search PubMed.
- K. Jang, H. J. Kim and S. U. Son, Chem. Mater., 2010, 22, 1273–1275 CrossRef CAS.
- X. Huang, S. Tang, X. Mu, Y. Dai, G. Chen, Z. Zhou, F. Ruan, Z. Yang and N. Zheng, Nat. Nanotechnol., 2011, 6, 28–32 CrossRef CAS PubMed.
- X. Yin, X. Liu, Y.-T. Pan, K. A. Walsh and H. Yang, Nano Lett., 2014, 14, 7188–7194 CrossRef CAS PubMed.
- H. Li, G. Chen, H. Yang, X. Wang, J. Liang, P. Liu, M. Chen and N. Zheng, Angew. Chem., Int. Ed. Engl., 2013, 52, 8368–8372 CrossRef CAS PubMed.
- Y. T. Pan, X. Yin, K. S. Kwok and H. Yang, Nano Lett., 2014, 14, 5953–5959 CrossRef CAS PubMed.
- P. F. Siril, L. Ramos, P. Beaunier, P. Archirel, A. Etcheberry and H. Remita, Chem. Mater., 2009, 21, 5170–5175 CrossRef CAS.
- S. Gao, Y. Lin, X. Jiao, Y. Sun, Q. Luo, W. Zhang, D. Li, J. Yang and Y. Xie, Nature, 2016, 529, 68 CrossRef CAS PubMed.
- V. F. Puntes, D. Zanchet, C. K. Erdonmez and A. P. Alivisatos, J. Am. Chem. Soc., 2002, 124, 12874–12880 CrossRef CAS PubMed.
- V. F. Puntes, K. M. Krishnan and A. P. Alivisatos, Science, 2001, 291, 2115–2117 CrossRef CAS PubMed.
- C. Hou, J. Zhu, C. Liu, X. Wang, Q. Kuang and L. Zheng, CrystEngComm, 2013, 15, 6127–6130 RSC.
- A.-X. Yin, W.-C. Liu, J. Ke, W. Zhu, J. Gu, Y.-W. Zhang and C.-H. Yan, J. Am. Chem. Soc., 2012, 134, 20479–20489 CrossRef CAS PubMed.
- Q. Zhang, Y. Hu, S. Guo, J. Goebl and Y. Yin, Nano Lett., 2010, 10, 5037–5042 CrossRef CAS PubMed.
- E. Martinsson, M. M. Shahjamali, N. Large, N. Zaraee, Y. Zhou, G. C. Schatz, C. A. Mirkin and D. Aili, Small, 2016, 12, 330–342 CrossRef CAS PubMed.
- X. Wang, B. Wu, G. Chen, Y. Zhao, P. Liu, Y. Dai and N. Zheng, Nanoscale, 2014, 6, 6798–6804 RSC.
- M. Chen, S. Tang, Z. Guo, X. Wang, S. Mo, X. Huang, G. Liu and N. Zheng, Adv. Mater., 2014, 26, 8210–8216 CrossRef CAS PubMed.
- X. Huang, S. Tang, B. Liu, B. Ren and N. Zheng, Adv. Mater., 2011, 23, 3420–3425 CrossRef CAS PubMed.
- Z. Zhang, Y. Liu, B. Chen, Y. Gong, L. Gu, Z. Fan, N. Yang, Z. Lai, Y. Chen, J. Wang, Y. Huang, M. Sindoro, W. Niu, B. Li, Y. Zong, Y. Yang, X. Huang, F. Huo, W. Huang and H. Zhang, Adv. Mater., 2016, 28, 10282–10286 CrossRef CAS PubMed.
- Z. Fan, Y. Zhu, X. Huang, Y. Han, Q. Wang, Q. Liu, Y. Huang, C. L. Gan and H. Zhang, Angew. Chem., 2015, 54, 5672–5676 CrossRef CAS PubMed.
- Z. Fan, X. Huang, Y. Han, M. Bosman, Q. Wang, Y. Zhu, Q. Liu, B. Li, Z. Zeng, J. Wu, W. Shi, S. Li, C. L. Gan and H. Zhang, Nat. Commun., 2015, 6, 6571 CrossRef CAS PubMed.
- R. Jin, Y. C. Cao, E. Hao, G. S. Métraux, G. C. Schatz and C. A. Mirkin, Nature, 2003, 425, 487–490 CrossRef CAS PubMed.
- C. Xue, J. E. Millstone, S. Li and C. A. Mirkin, Angew. Chem., 2007, 119, 8588–8591 CrossRef.
- S. Tsukuda, K. Okamoto, H. Yamamoto, T. Kozawa and T. Omata, Jpn. J. Appl. Phys., 2017, 56, 06GG06 CrossRef.
- Z. Wu, Y. Li, J. Liu, Z. Lu, H. Zhang and B. Yang, Angew. Chem., Int. Ed., 2014, 53, 12196–12200 CrossRef CAS PubMed.
- I. Cebula, H. Lu, M. Zharnikov and M. Buck, Chem. Sci., 2013, 4, 4455–4464 RSC.
- W. Wang, Y. Zhao and Y. Ding, Nanoscale, 2015, 7, 11934–11939 RSC.
- H. Aitchison, N. Meyerbröker, T.-L. Lee, J. Zegenhagen, T. Potter, H. Früchtl, I. Cebula and M. Buck, Phys. Chem. Chem. Phys., 2017, 19, 24146–24153 RSC.
- J. H. Zhong, X. Jin, L. Meng, X. Wang, H. S. Su, Z. L. Yang, C. T. Williams and B. Ren, Nat. Nanotechnol., 2017, 12, 132–136 CrossRef CAS PubMed.
- N. Hussain, T. Liang, Q. Zhang, T. Anwar, Y. Huang, J. Lang, K. Huang and H. Wu, Small, 2017, 13, 1701349 CrossRef PubMed.
- J. Gu, B. Li, Z. Du, C. Zhang, D. Zhang and S. Yang, Adv. Funct. Mater., 2017, 1700840 CrossRef.
- E. Noguchi, K. Sugawara, R. Yaokawa, T. Hitosugi, H. Nakano and T. Takahashi, Adv. Mater., 2015, 27, 856–860 CrossRef CAS PubMed.
- J. Zhuang, X. Xu, G. Peleckis, W. Hao, S. X. Dou and Y. Du, Adv. Mater., 2017, 29, 1606716 CrossRef PubMed.
- L. Meng, Y. Wang, L. Zhang, S. Du, R. Wu, L. Li, Y. Zhang, G. Li, H. Zhou, W. A. Hofer and H. J. Gao, Nano Lett., 2013, 13, 685–690 CrossRef CAS PubMed.
- C. L. Lin, R. Arafune, K. Kawahara, M. Kanno, N. Tsukahara, E. Minamitani, Y. Kim, M. Kawi and N. Takagi, Phys. Rev. Lett., 2013, 110, 076801 CrossRef PubMed.
- P. Vogt, P. De Padova, C. Quaresima, J. Avila, E. Frantzeskakis, M. C. Asensio, A. Resta, B. Ealet and G. Le Lay, Phys. Rev. Lett., 2012, 108, 155501 CrossRef PubMed.
- J. Zhuang, N. Gao, Z. Li, X. Xu, J. Wang, J. Zhao, S. X. Dou and Y. Du, ACS Nano, 2017, 11, 3553–3559 CrossRef CAS PubMed.
- M. Derivaz, D. Dentel, R. Stephan, M.-C. Hanf, A. Mehdaoui, P. Sonnet and C. Pirri, Nano Lett., 2015, 15, 2510–2516 CrossRef CAS PubMed.
- L. Li, S. Z. Lu, J. Pan, Z. Qin, Y. Q. Wang, Y. Wang, G. Y. Cao, S. Du and H. J. Gao, Adv. Mater., 2014, 26, 4820–4824 CrossRef CAS PubMed.
- X. Wu, Y. Shao, H. Liu, Z. Feng, Y. L. Wang, J. T. Sun, C. Liu, J. O. Wang, Z. L. Liu, S. Y. Zhu, Y. Q. Wang, S. X. Du, Y. G. Shi, K. Ibrahim and H. J. Gao, Adv. Mater., 2017, 29, 1605407 CrossRef PubMed.
- F.-f. Zhu, W.-j. Chen, Y. Xu, C.-l. Gao, D.-d. Guan, C.-h. Liu, D. Qian, S.-C. Zhang and J.-f. Jia, Nat. Mater., 2015, 14, 1020–1025 CrossRef CAS PubMed.
- F. Reis, G. Li, L. Dudy, M. Bauernfeind, S. Glass, W. Hanke, R. Thomale, J. Schäfer and R. Claessen, Science, 2017, 357, 287–290 CrossRef CAS PubMed.
- L. Li, Y. Wang, S. Xie, X. B. Li, Y. Q. Wang, R. Wu, H. Sun, S. Zhang and H. J. Gao, Nano Lett., 2013, 13, 4671–4674 CrossRef CAS PubMed.
- P. Ares, F. Aguilar-Galindo, D. Rodríguez-San-Miguel, D. A. Aldave, S. Díaz-Tendero, M. Alcamí, F. Martín, J. Gómez-Herrero and F. Zamora, Adv. Mater., 2016, 28, 6332–6336 CrossRef CAS PubMed.
- C. Gibaja, D. Rodriguez-San-Miguel, P. Ares, J. Gomez-Herrero, M. Varela, R. Gillen, J. Maultzsch, F. Hauke, A. Hirsch, G. Abellan and F. Zamora, Angew. Chem., Int. Ed. Engl., 2016, 55, 14345–14349 CrossRef CAS PubMed.
- C. Huo, X. Sun, Z. Yan, X. Song, S. Zhang, Z. Xie, J. Liu, J. Ji, L. Jiang, S. Zhou and H. Zeng, J. Am. Chem. Soc., 2017, 139, 3568 CrossRef CAS.
- R. Gusmão, Z. Sofer, D. Bouša and M. Pumera, Angew. Chem., Int. Ed., 2017, 56, 14417–14422 CrossRef PubMed.
- T. P. Kaloni and U. Schwingenschlögl, J. Appl. Phys., 2013, 114, 184307 CrossRef.
- L. Tsetseris and D. Kaltsas, Phys. Chem. Chem. Phys., 2014, 16, 5183–5187 RSC.
- E. Bianco, S. Butler, S. Jiang, O. D. Restrepo, W. Windl and J. E. Goldberger, ACS Nano, 2013, 7, 4414–4421 CrossRef CAS PubMed.
- T. Ling, J. J. Wang, H. Zhang, S. T. Song, Y. Z. Zhou, J. Zhao and X. W. Du, Adv. Mater., 2015, 27, 5396–5402 CrossRef CAS PubMed.
- Z. Fan and H. Zhang, Chem. Soc. Rev., 2016, 45, 63–82 RSC.
- Z. Fan and H. Zhang, Acc. Chem. Res., 2016, 49, 2841–2850 CrossRef CAS PubMed.
- S. Yang, X. Feng, S. Ivanovici and K. Mullen, Angew. Chem., 2010, 49, 8408–8411 CrossRef CAS PubMed.
- C. Tan and H. Zhang, Chem. Soc. Rev., 2015, 44, 2713–2731 RSC.
- Y. Deng, Z. Luo, N. J. Conrad, H. Liu, Y. Gong, S. Najmaei, P. M. Ajayan, J. Lou, X. Xu and P. D. Ye, ACS Nano, 2014, 8, 8292–8299 CrossRef CAS PubMed.
- G. D. Moon, G. Lim, J. H. Song, M. Shin, T. Yu, B. Lim and U. Jeong, Adv. Mater., 2013, 25, 2707–2712 CrossRef CAS PubMed.
- B. Li, D. Zhang, Y. Liu, Y. Yu, S. Li and S. Yang, Nano Energy, 2017, 39, 654–661 CrossRef CAS.
- R. Gordon, D. Sinton, K. L. Kavanagh and A. G. Brolo, Acc. Chem. Res., 2008, 41, 1049–1057 CrossRef CAS PubMed.
- E. M. Larsson, C. Langhammer, I. Zorić and B. Kasemo, Science, 2009, 326, 1091–1094 CrossRef CAS PubMed.
- D. Schaadt, B. Feng and E. Yu, Appl. Phys. Lett., 2005, 86, 063106 CrossRef.
- N. Yang, Z. Zhang, B. Chen, Y. Huang, J. Chen, Z. Lai, Y. Chen, M. Sindoro, A. L. Wang, H. Cheng, Z. Fan, X. Liu, B. Li, Y. Zong, L. Gu and H. Zhang, Adv. Mater., 2017, 29, 1700769 CrossRef PubMed.
- X. Huang, H. Li, S. Li, S. Wu, F. Y. C. Boey, J. Ma and H. Zhang, Angew. Chem., 2011, 50, 12245–12248 CrossRef CAS PubMed.
|
This journal is © the Partner Organisations 2018 |
Click here to see how this site uses Cookies. View our privacy policy here.