DOI:
10.1039/C7NJ03285D
(Paper)
New J. Chem., 2018,
42, 67-75
Heterogenization of a homogenous catalyst: synthesis and characterization of imidazolium ionene/OH−@SiO2 as an efficient basic catalyst for biodiesel production†
Received
30th August 2017
, Accepted 12th November 2017
First published on 13th November 2017
Abstract
To develop green and recyclable catalysts for biodiesel production, herein, a reusable, eco-friendly catalyst was designed by immobilizing an oligomeric ionic liquid inside a SiO2 mesoporous matrix. Then, it was used in transesterification of several natural oils with methanol to produce biodiesel. In this study, the effect of an ionic liquid on the reaction rate has been demonstrated and compared with that of KOH as a routine catalyst for this reaction. The catalyst was characterized by FTIR, XRD, BET, FESEM, TEM, and TGA techniques. The effect of different parameters, such as temperature, molar ratio of methanol/oil, and amount of catalyst, was investigated to optimize the reaction conditions. The results showed that after 8 h of reaction at 60 °C with a methanol/oil molar ratio of 8
:
1 and 50 mg of the catalyst, the yield of methyl ester reached 96%. The reaction was also conducted in an autoclave at 200 °C, and the conversion after 1 h was over 97%. More importantly, due the SiO2 coating, the catalyst could be successfully recovered, and the catalyst could be used repeatedly for at least 5 cycles without any significant loss of activity. In particular, we were able to heterogenize a water soluble basic catalyst that was not soluble in methanol and separate it from the reaction mixture very easily.
1. Introduction
Currently, the world is confronted with environmental crises because of increased consumption of fossil fuels. Extraction and non-selective consumption of fossil fuels by big economies and developing countries have led to reduction of fossil fuel resources. In this context, meeting the energy demands for transport has been a major concern, which has led to search for alternative fuels in compliance with sustainable development. Biomass resources have gained extensive attention. Biodiesel is an alternative fuel that can be produced by transesterification of natural oils.1–4
Usually, sodium or potassium hydroxide is used as a homogeneous basic catalyst because this catalyst can complete the reaction under mild conditions.5 It should be mentioned that the operational use of these catalysts creates many problems such as soap formation and corrosion in the lines. Moreover, a large amount of water is needed to eliminate the residual catalyst from the product; this increases the cost of the process.6–14 In this regard, heterogeneous catalysts are more cost-effective and more efficient for the production of biodiesel.10,13,14 There are many studies on biodiesel production using heterogeneous basic catalysts such as CaO-La2O3,15 KOH-clay,16 Li4SiO4,17 LiAlO2,18 KNO3-NaX,19 CaO-NaY,20 KF/CaO-MgO,21etc.
In the last few decades, the use of ionic liquids for the production of biodiesel has been introduced as a new eco-benign strategy towards modern chemistry; ionic liquids are used in a variety of reactions such as synthesis, catalysis, and gas absorption.22–24 Ionic liquids with properties, such as non-volatility, adjustable hydrophilicity/hydrophobicity, and non-corrosiveness, can provide higher conversion and selectivity in reactions; this makes them reliable alternatives as homogeneous or even heterogeneous catalysts.25–27 As is known, esterification of fatty acids, such as oleic acid, and transesterification of oils can be catalyzed by functionalized ionic liquids.28–31 However, drawbacks, such as solubility of ionic liquid in the aqueous phase, difficult separation procedures, and consumption of a large amount of catalyst, inhibit their extensive usage. Moreover, recovery of the catalyst is very important to reduce the cost of operation. Therefore, heterogenization of an ionic liquid is a necessary step, especially, if we want to use an ionic liquid as a reusable catalyst. In this respect, we could exemplify the work of Dyson's research team32–34 which made an ionic liquid as part of a polymer, and studied transformation of lignocelluloses biomass into 5-hydroxymethyfurfural.
Considering that ionic liquids are environmentally benign media for catalytic processes and many reactions can be catalyzed with ionic liquids, in this study, we prepared an oligomeric, water-soluble ionic liquid and heterogenized it by encapsulation in a mesoporous silica matrix; the heterogenized IL is denoted as IL 4/OH−@SiO2 and has been used for biodiesel production. The aim of this study was to encapsulate an ionic liquid, exchange its anion with hydroxide ion (HO−), and observe its catalytic effect in a green reaction such as synthesis of biodiesel. To ascertain this idea, a significantly large ionic liquid should be designed such that it can be trapped in a mesoporous matrix such as SiO2; practically, we should admit that complexity of its synthesis is a drawback! Finally, after synthesis of the designed ionic liquid, the anions of the oligomeric ionic liquid were exchanged by hydroxide anion and then trapped in a dense mesoporous silica layer. This silica matrix acts as a support, which prevents diffusion of the ionic liquid through its pores. The catalyst was thoroughly characterized and applied as a heterogeneous basic catalyst for transesterification of different fatty oils, which resulted in a clean biodiesel product. This study was mainly focused on the heterogenization technique applied for a soluble catalyst. The study also highlights the activity and stability of a catalyst and determinant parameters for the production of biodiesel. Control experiments have been conducted, and the results of conventional catalysts, such as KOH, have been provided.
2. Experimental
2.1. Chemicals and instruments
The chemicals 1,2-dibromoethane, benzyl chloride, imidazole, and Dowex 1 × 4 resin were purchased from Sigma-Aldrich and Fluka and used without further purification. All solvents used in this study were of analytical grade.
FTIR spectra were obtained by an FTIR spectrophotometer (Jasco 680-plus) using KBr pellets. Nuclear magnetic resonance spectra were obtained using a Bruker avance 400 MHz spectrometer in D2O or DMSO-d6 as a solvent. The products of each experiment were analyzed using Chrompack GC Model CP9001 equipped with a Varian capillary column (50 m, 0.25 mm, and 0.25 lm) and an FID detector. The biodiesel yield, defined as the amount of fatty acid methyl esters obtained during transesterification, was calculated using n-decane as the internal standard. X-Ray diffraction analyses were performed using a diffractometer with a Cu anode (Philips X′pert, Netherland). The TGA curve of the catalyst was obtained under a nitrogen atmosphere at a sample heating rate of 10 °C min−1 using BAHR-STA/TGA-503. The adsorption–desorption isotherms of nitrogen at 77.3 K were obtained using NOVA Win 2, version 2.2 (Quantachrome instruments), and the surface area was measured by the BET equation. FESEM and transmission electron microscopy (TEM) were performed using Mira 3-XMU FESEM (Germany) equipped with an EDX spectrometer and Philips CM120 transmission electron microscope with an accelerator voltage of 100 kV (Germany), respectively.
2.2. Preparation of the catalyst
2.2.1. Synthesis of 1,2-di(1H-imidazol-1-yl)ethane (1).
Sodium hydride (60% in oil, 400 mg, 10 mmol) was added to imidazole (680 mg, 10 mmol) dissolved in 30 mL acetonitrile at 0 °C; then, 0.43 mL (5 mmol) 1,2-dibromoethane was added to the mixture, and the mixture was then refluxed for 8 h. The reaction was monitored by TLC, and upon completion of the reaction, the solid was separated by filtration. By removing the solvent under a reduced pressure, the oily product was purified by column chromatography (solvent: cyclohexane–EtOAc). 1H NMR (400 MHz, DMSO-d6): δ 4.17–4.31 (m, 4H, CH2), 6.85 (m, 2H, CH), 7.01 (m, 2H, CH), 7.37 (m, 2H, CH) (Fig. S1, ESI†).
2.2.2. Synthesis of 3,3′-(ethane-1,2-diyl)bis(2-bromoethyl-1H-imidazol-3-ium)bromide (IL 1).
Herein, 2.58 mL (30 mmol) 1,2-dibromoethane was added to an acetonitrile solution of 1,2-di(1H-imidazol-1-yl)ethane (810 mg, 5 mmol). The resulting solution was stirred at 80 °C for 6 h under reflux. After completion of the reaction, the solvent was evaporated under reduced pressure, and then, after the addition of 20 mL H2O, the mixture was extracted with CCl4. The IL-1 was extracted from the aqueous solution by ethylacetate (2 × 25 mL) and purified by column chromatography on silica gel (solvent: cyclohexane–EtOAc) (Scheme 1). 1H NMR (400 MHz, DMSO-d6): δ 4.66–4.79 (m, 12H, CH2), 7.42 (m, 2H, CH), 7.50 (m, 2H, CH), 7.72 (m, 2H, CH) (Fig. S2, ESI†).
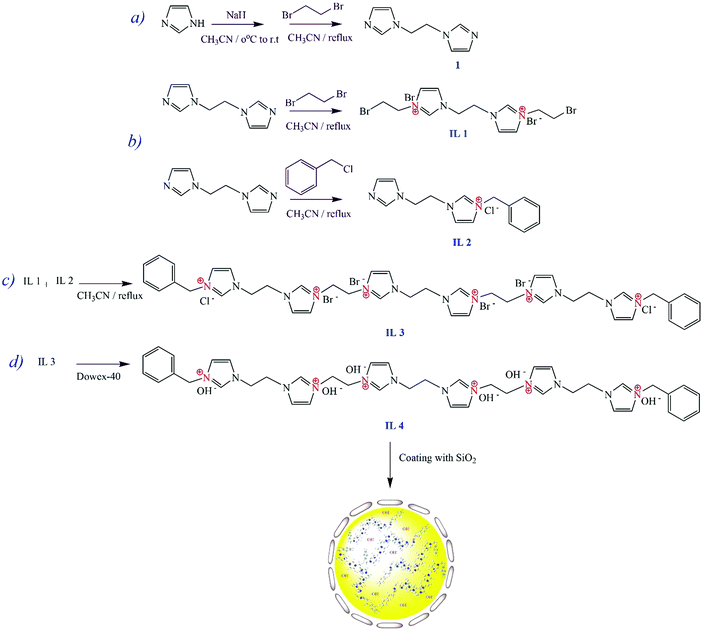 |
| Scheme 1 Preparation process for the synthesis of the IL-4/OH−@SiO2 catalyst. | |
2.2.3. Synthesis of 1-(2(1H-imidazol-1-yl)ethyl)-3-(benzyl-1H-imidazol-3-ium)chloride (IL 2).
Herein, 0.57 mL (5 mmol) benzyl chloride was added to a solution of acetonitrile containing 810 mg (5 mmol) of 1,2-di(1H-imidazol-1-yl)ethane; then, the mixture was stirred under reflux for 8 h. After completion of the reaction, 50 mL water was added to the reaction mixture, and after extraction with CCl4 (2 × 25 mL), the aqueous solution was extracted with EtOAc (2 × 25 mL) to separate the crude IL-2, which was purified by column chromatography (cyclohexane–EtOAc). 1H NMR (400 MHz, DMSO-d6): δ 5.20 (m, 4H, CH2), 5.48 (m, 2H, CH2),6.88 (s, 1H, CH), 7.02 (m, 3H, CH), 7.23–7.44 (s, 5H, CH), 7.69 (s, 1H, CH), 7.77 (s, 1H, CH) (Fig. S3, ESI†).
2.2.4. Synthesis of 1,1′-(ethane-1,2-diyl)bis(3-(2-(1-(2-(3-benzyl-1H-imidazol-3-ium-1-yl)ethyl)-1H-imidazol-3-ium-3-yl)ethyl)-1H-imidazol-3-ium) tetrabromide dichloride (IL 3).
For the preparation of the ionic liquid IL-3, in a 100 mL round-bottom flask, 534 mg (1 mmol) of IL-1 and 579 mg (2 mmol) of IL-2 and 30 mL dry DMF were added, and the mixture was refluxed for 24 h. The progress of the reaction was monitored by TLC, and upon completion of the reaction, the solvent was evaporated under vacuum at 100 °C. The IL-3 ionic liquid was precipitated by adding ethanol to the aqueous solution of crude IL-3 and then characterized by 1H NMR spectroscopy. 1H NMR (400 MHz, DMSO-d6): δ 4.55–4.59 (m, 6H, CH2), 4.61–4.62 (m, 4H, CH2), 4.82–4.85 (m, 14H, CH2), 6.89 (m, 4H, CH), 7.22 (m, 4H, CH), 7.83–7.88 (m, 16H, CH), 8.13 (s, 2H, CH) (Fig. S4, ESI†). Anal. calcd for C42H52N12Cl2Br4: C 45.20, H 4.66, N 15.07%. Found: C 45.38, H 4.73, N 14.89%.
2.2.5. Synthesis of 1,1′-(ethane-1,2-diyl)bis(3-(2-(1-(2-(3-benzyl-1H-imidazol-3-ium-1-yl)ethyl)-1H-imidazol-3-ium-3-yl)ethyl)-1H-imidazol-3-ium) hydroxide (IL 4/OH−).
In a 100 mL beaker, 1 g Dowex 1 × 4 (Cl− as the counter ion) was added to 20 mL of NaOH solution (1 M) and left overnight to exchange the chloride anion with hydroxide ion. Then, the resin was separated from the solution and washed with deionized water until neutralization of the filtrate. The anion exchanged resin was dried in an oven. Then, 1 g of the IL-3 was dissolved in deionized water and passed through a column of the solid anion exchanged resin. Upon decreasing the volume of the aqueous solution, the IL-4/OH− was separated as a crystalline solid.
2.2.6. Preparation of the IL 4/OH−@SiO2 catalyst.
In the first step, 250 mg of the IL-4 was ground well and then added to 10 mL of dry n-hexane under vigorous stirring at room temperature for its complete dispersion. The mixture was sonicated (2 × 15 min), and then, a calculated amount of tetraethylorthosilicate (868 mg) dissolved in 5 mL n-hexane was added dropwise to the suspension. After 4 h, for hydrolysis of tetraethylorthosilicate, a calculated amount of deionized water was added to the suspension. The mixture was left for 24 h, and then, the solid was separated using a centrifuge, washed with water, and dried. The obtained solid was used as a new basic catalyst and named the IL-4/OH−@SiO2 catalyst.
2.2.7. General procedure for biodiesel synthesis.
A 50 mL round-bottom flask was charged with an appropriate amount of oil (sesame oil), methanol, and the catalyst, and it was fitted with a reflux condenser. The transesterification reaction was typically conducted under vigorous stirring at a defined temperature. After completion of the reaction, the extra methanol was distilled under reduced pressure, and then, upon centrifugation of the residue, three phases appeared: the solid catalyst, glycerol, and the biodiesel containing phase. The catalyst was washed thoroughly by chloroform and dried under vacuum at 50 °C to be used for the next run. The products were analyzed quantitatively by GC using an internal standard (n-decane). The yield of the reaction was defined as the ratio of the weight of fatty acid methyl esters (determined by GC) to the weight of fatty acid methyl esters calculated theoretically (Fig. S5, ESI†). All experiments were conducted in triplicate, and the results were averaged.
3. Result and discussion
3.1. Characterization of the catalyst
The oligoionene IL-3 contains quaternary nitrogen atoms in its chain. These types of ionenes were synthesized for the first time in 1933 by Gibbs and his co-workers.35 A variety of these polyionic compounds can be prepared due to availability of a wide range of di-tertiary amines and dihalides. As a general statement, synthesis of these polyionic compounds is tedious and time-consuming. However, the reason for synthesizing the ionenes like IL-3 was to check their potential applications in heterogeneous catalysis and also to check the idea of heterogenization of a very soluble polyionic liquid using different inorganic mesoporous materials such as SiO2, TiO2, etc. Moreover, we expected that by trapping this big ionic liquid in a matrix of inorganic mesoporous material and exchanging anions present in the ionic liquid with hydroxide ions and because of low electrostatic interaction between the imidazolium cationic part and the hydroxide anion, the catalyst would demonstrate an appropriate catalytic activity. Clearly, extensive hydrogen bonding between hydroxide anions of the IL-4 molecules and also hydrogen bonding of the polar hydrogen in the imidazolium ring with the hydroxyl groups of the mesoporous silica are the main reasons for the stability of the composite. If it is true that IL-3 cannot escape from the matrix around it, we should also be able to regenerate or refresh the catalyst by immersing it in a sodium hydroxide solution.
The FTIR spectra of IL-1, IL-2, IL-3, IL-4, and IL-4/OH−@SiO2 are shown in Fig. 1. In the spectrum of IL-1, the aromatic C–H stretching vibration in imidazolium rings appears in the range of 3143–3050 cm−1, the aliphatic C–H stretching vibration appears in the range of 2987–2850 cm−1, the aromatic ring deformations appear in the range of 1620–1465 cm−1, and the C–Br stretching vibration can be seen at 634 cm−1. The peaks at 1635 cm−1 and the broad band at 3435 cm−1 were assigned to the bending and stretching vibrations of absorbed water and the O–H groups, respectively. The ionic liquids IL-2, IL-3, and IL-4 showed the same vibrations in the final stage when the ionic liquid IL-4 was covered by a mesoporous SiO2 to prepare the IL4/OH−@SiO2. In Fig. 1e, the Si–O–Si stretching vibration appears as a strong peak in the range of 1200–1000 cm−1. The band at 459 cm−1 can be assigned to the bending mode of the vibration of Si–O bonds.36–39
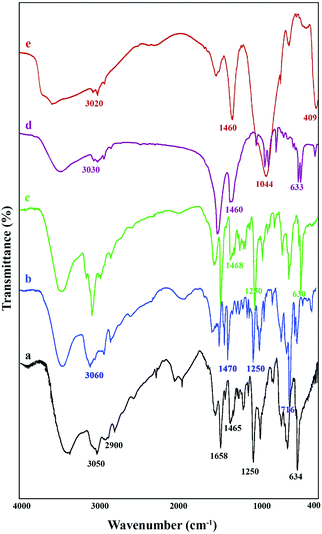 |
| Fig. 1 FTIR spectra of (a) IL-1, (b) IL-2, (c) IL-3, (d) IL-4, and (e) IL-4/OH−@SiO2. | |
The XRD patterns of IL-3, IL-4, and IL-4/OH−@SiO2 are shown in Fig. 2. The characteristic peaks at 26°, 31°, 32°, and 43° in Fig. 2a illustrate that IL-3 should have a crystalline structure. By exchanging its counter-ion (Br−) with hydroxide ion, the new ionic liquid (IL-4) demonstrates new diffraction peaks at 30° and 68°. By coating the IL-4 with an amorphous SiO2 layer, the ionic liquid chains probably tolerate conformational changes, which end up in new crystallinity with the characteristic diffraction pattern.
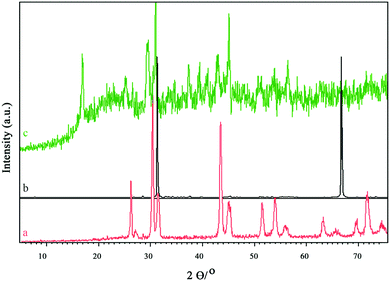 |
| Fig. 2 XRD patterns of (a) IL-3, (b) IL-4, and (c) IL-4/OH−@SiO2. | |
The N2 adsorption–desorption isotherm and pore size diameter of the IL-4/OH−@SiO2 composite are shown in Fig. 3. The composite has a specific surface area of 63 m2 g−1, pore volume of 0.14 cm3 g−1, and an average pore diameter of 7.9 nm, which shows a type II adsorption–desorption isotherm and an H3 hysteresis loop. According to the IUPAC definitions,40,41 the composite IL-4/OH−@SiO2 should be categorized as a mesoporous solid.42 On the basis of back-titration, the total hydroxide anion of the IL-4/OH−@SiO2 catalyst was measured to be 5.48 mmol OH− g−1 (calculated: 7.2 mmol g−1). Therefore, the catalyst has a high density of basic sites, which are surrounded by silica. The textural properties of the catalyst allow the triglyceride and methanol to reach the basic sites where the transesterification reaction occurs.
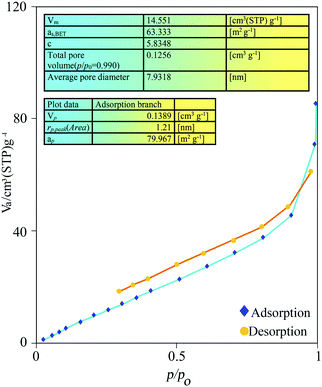 |
| Fig. 3 Nitrogen adsorption–desorption isotherm of the IL-4/OH−@SiO2 catalyst. | |
The FE-SEM images of the IL-4/OH−@SiO2 composite are shown in Fig. 4. The images show that almost spherical particles are trapped in a dense matrix of silica. The EDX data and EDX mapping (Fig. 5) of the composite show the dispersion of the ionic liquid and SiO2 in the whole sample.
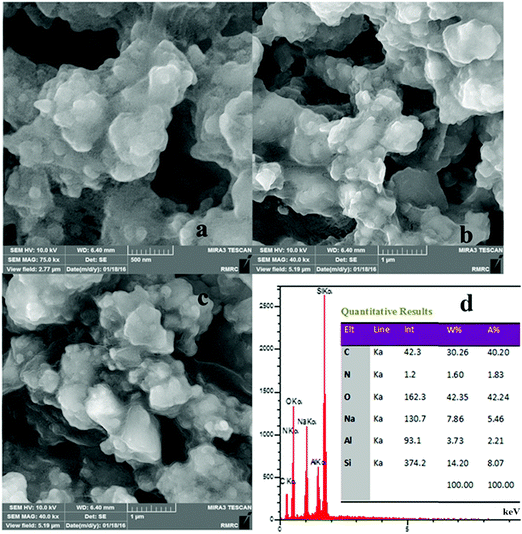 |
| Fig. 4 FE-SEM images (a–c) and EDX data of the IL-4/OH−@SiO2 catalyst (d). | |
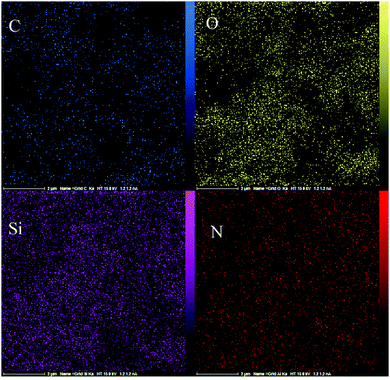 |
| Fig. 5 Mapping images of the elements in the IL-4/OH−@SiO2 catalyst. | |
The TEM images (Fig. 6) are in compliance with our prediction based on the FE-SEM images. The images show the distribution of spherical particles in the range of 100–200 nm in the matrix of mesoporous and amorphous silica.
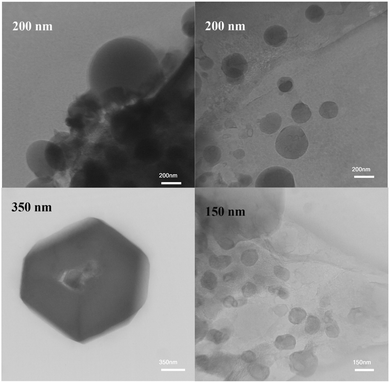 |
| Fig. 6 TEM images of the IL-4/OH−@SiO2 catalyst at different magnifications. | |
The thermal stability of the IL-4/OH−@SiO2 composite was studied by analyzing the TGA thermogram (Fig. 7). The TGA curve shows that the composite has lost about 80% of its mass between 100 °C and 1200 °C; this can be related to the degradation of the ionic liquid by different kind of reactions such as elimination, radical reactions, and finally shrinkage of amorphous SiO2 through water loss. The initial weight loss of 12% up to about 200 °C can be attributed mainly to the loss of water bound or trapped in the composite. On the basis of the weight lost in the range of 200–550 °C, which is related to the decomposition of the ionic liquid, the quantity of the ionic liquid in the composite has been calculated to be around 18%. After 600 °C, amorphous silica starts losing water by condensation until a stable composition, around 70 wt% for silica as estimated via the thermogram, is achieved.
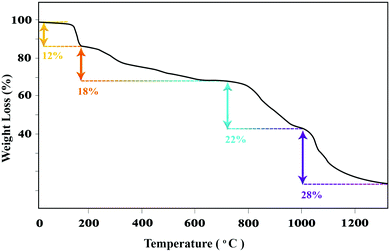 |
| Fig. 7 TGA analysis of the IL-4/OH−@SiO2 catalyst. | |
3.2. Catalytic performance
IL-4/OH−@SiO2 as a new heterogeneous basic catalyst was employed for the transesterification reaction of different oils with methanol to produce biodiesel. Different parameters, such as temperature, amount of catalyst, methanol to oil ratio, and reaction time, affecting the reaction were investigated.
3.2.1. Effect of temperature and amount of catalyst.
The reaction of sesame oil with methanol was investigated at room temperature; after 6 h, the yield of biodiesel was less than 5%, whereas it reached a maximum value (96%) at refluxing temperature (60 °C). We examined the reaction at other temperatures (20–50 °C), but the yields were not satisfactory. Therefore, the desired temperature for the transesterification of sesame oil with methanol for the production of biodiesel was chosen as 60 °C.
The effect of the catalyst amount on the yield of biodiesel in the transesterification of sesame oil with methanol (CH3OH
:
oil ratio = 8) was investigated (Table 1). As shown in the table, by increasing the amount of catalyst from 20 to 100 mg, the yield of reaction was increased; however, with an increase in the amount of catalyst from 50 mg to 100 mg, no considerable impact on the yield was observed. Therefore, the desired amount of catalyst was set to be 50 mg. More importantly, we have investigated the reaction with KOH as the catalyst; as seen in Table 1, upon using 6 mg of KOH, which has more than twice the amount of hydroxide ion in 50 mg of the catalyst, after 8 h, the yield is just 10%; on the other hand, upon using 40 mg KOH, the yield reaches an acceptable value. We also tried to compare the Dowex 1 × 4-OH− activities with the those of the IL-4/OH−@SiO2 catalyst, and as shown in Table 1 (entry 11), the reaction efficiency of the IL-4/OH−@SiO2 catalyst was much higher than that of Dowex1-OH−. As expected, the IL-4/OH−@SiO2 catalyst is more hydrophobic at the active site than Dowex 1 × 4-OH, and the oil has a greater tendency to reach the active site of the IL-4/OH−@SiO2 catalyst.
Table 1 Effect of the amount of catalyst on the transesterification reaction of sesame oil with methanol
Entry |
Amount of the catalyst (mg) |
Time (h) |
Yielda (%) |
Reaction conditions: MeOH : oil (molar ratio) = 8, reaction temperature = 60 °C. Determined by GC. Reaction in autoclave at 150 °C. KOH as the catalyst. Dowex 1 × 4-chloride anion exchanged with hydroxide ion. |
1 |
Blank |
12 |
No reaction |
2 |
20 |
8 |
90 |
3 |
50 |
8 |
96 |
4 |
100 |
8 |
97 |
5b |
50 |
1 |
96 |
6c |
6 |
8 |
10 |
7c |
15 |
8 |
71 |
8c |
20 |
8 |
80 |
9c |
30 |
8 |
85 |
10c |
40 |
8 |
85 |
11d |
50 |
1 |
45 |
3.2.2. Effect of the reaction time.
The yield of biodiesel was steadily improved as the time of reaction increased from 3 h to 8 h and thereafter remained constant at 96% (Table 2). Therefore, the suitable time for transesterification reaction was set at 8 h under optimized conditions. We also carried out the reaction in an autoclave at 200 °C. The time of the reaction for completion, or in better words, for reaching equilibrium, was 1 h.
Table 2 Effect of reaction time on the transesterification reaction of sesame oil with methanol
Entry |
Time (h) |
Yielda (%) |
Reaction conditions: MeOH : oil (molar ratio) = 8, reaction temperature = 60 °C, amount of catalyst = 50 mg. Determined by GC. |
1 |
3 |
60 |
2 |
6 |
85 |
3 |
8 |
96 |
4 |
10 |
96 |
3.2.3. Effect of the molar ratio of methanol to oil.
The stoichiometric molar ratio of methanol to sesame oil is 3, and to force the equilibrium toward the completion, excess methanol needs to applied in the transesterification reaction. Therefore, the range from 3
:
1 to 10
:
1 molar ratio of MeOH to oil was examined (Table 3). The reaction was carried out with 50 mg of the IL-4/OH−@SiO2 catalyst for 8 h at 60 °C. The yield of biodiesel was enhanced considerably by increasing the ratio of methanol to sesame oil; an increase in the molar ratio to above 10
:
1 had little effect on the yield of the reaction.
Table 3 Effect of the MeOH
:
oil molar ratio on the transesterification reaction of sesame oil with methanol
Entry |
MeOH : oil molar ratio |
Yielda (%) |
Reaction conditions: reaction time = 8 h, reaction temperature = 60 °C. Amount of catalyst = 50 mg. Determined by GC. |
1 |
3 : 1 |
52 |
2 |
4 : 1 |
65 |
3 |
5 : 1 |
90 |
4 |
8 : 1 |
96 |
5 |
10 : 1 |
92 |
3.3. Reusability of the catalyst
It was of utmost importance to show the stability of the catalyst under the reaction conditions. Therefore, the catalytic stability of the IL-4/OH−@SiO2 catalyst was demonstrated by performing the reaction under optimized conditions (60 °C, CH3OH
:
oil = 8
:
1, and 8 h). After each run, the catalyst was separated, washed with methanol and chloroform, and then dried under vacuum. The reusability results for the IL-4/OH−@SiO2 catalyst are shown in Fig. 8. The yield decreased only a few percent after 5 runs; this is a good indication of catalyst stability. This demonstrates efficiency of the proposed heterogenization method for a soluble catalyst via creation of a mesoporous shell around it. Moreover, after 5 runs, the catalyst was washed thoroughly with chloroform, then stirred in a solution of 0.1 N KOH overnight, and again washed with water until the filtrate became neutral. The catalyst was dried and used in another run (6th run), and surprisingly, the yield increased to 96%.
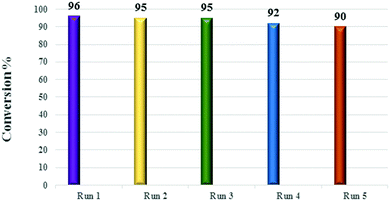 |
| Fig. 8 Reusability of the IL-4/OH−@SiO2 catalyst. | |
Different catalytic systems such as KOH-modified ZnO,43 NaOH,44 MgO–SrO45 and H3PW12O40/SiO246 are some examples of the catalysts that have been reported for biodiesel formation. Table 4 shows a comparison of the activity of the IL–OH@SiO2 catalyst with that of other catalysts that have been reported in the literature. Of course, if the problems related with the synthesis of the catalyst are overlooked, this composite can be defended as a green catalyst for the synthesis of biodiesel.
Table 4 Comparison of the catalytic performance of IL–OH−@SiO2 with that of some previously reported catalysts in biodiesel production
Entry |
Catalyst |
TON |
Ref. |
1 |
KOH-modified ZnO |
32.58 |
43
|
2 |
NaOH |
4.21 |
44
|
3 |
KOH |
4.07 |
44
|
4 |
MgO–SrO |
3.27 |
45
|
5 |
H3PW12O40/SiO2 |
6 |
46
|
6 |
IL–OH@SiO2 |
39.13 |
This work |
3.4. Effect of different oils
To determine whether the size of the molecule has any effect on the yield of the reaction, several vegetable oils with different degrees of unsaturation were tested. The catalytic activity of the IL-4/OH−@SiO2 catalyst with mesoporous silica under optimum conditions is shown in Table 5. Clearly, upon increasing the degree of unsaturation in the oil molecule, a less packed conformation may be expected; therefore, the rate at which the active site of the catalyst is approached by the reactants should decrease. As can be seen, the difference in yield for these reactions can be in the range of uncertainty; therefore, we conclude that the mesoporous shell has not played any barrier role for the reactants to reach the active site of the catalyst.
Table 5 Transesterification of different oils
Entry |
Vegetable oil |
Yielda (%) |
Reaction conditions: reaction time = 8 h, reaction temperature = 60 °C, amount of catalyst = 50 mg, MeOH : oil molar ratio = 8 : 1. Determined by GC. |
1 |
Canola |
93 |
2 |
Grape seed |
93 |
3 |
Corn |
96 |
4 |
Olive |
96 |
4. Conclusion
The methodology reported in this study is a new way of immobilization of a homogeneous catalyst. The catalyst was characterized by various techniques and tested for transesterification of different vegetable oils with methanol for the production of biodiesel. A yield of more than 90% in all the reactions under optimum conditions was obtained. The catalyst was active and fully recyclable with a yield higher than 90% for five runs, and even after refreshing the catalyst by stirring in a 0.1 N KOH, the yield obtained was significantly acceptable.
Conflicts of interest
The authors declare no competing financial interest.
Acknowledgements
We would like to thank the Research Council of Isfahan University of Technology for supporting this work and Dr Payam Ghiaci for his helpful comments.
References
- Y. Zhu, J. Patel, S. Mujcinovic, W. Jacson and A. Robinson, Preparation of terminal oxygenates from renewable natural oils by a one-pot metathesis–isomerisation–methoxycarbonylation–transesterification reaction sequence, Green Chem., 2006, 8, 746–749 RSC.
- S. Shahla, N. G. Cheng and R. Yusoff, An overview on transesterification of natural oils and fats, Biotechnol. Bioprocess Eng., 2010, 15, 891–904 CrossRef CAS.
- L. Damas, G. Costa, J. Ruas, R. Carrilho, R. Abreu, G. Aquino, M. Calvete, M. Pineiro and M. Pereira, Microwave assisted reactions of natural oils: transesterification and hydroformylation/isomerization as tools for high value compounds, Curr. Microwave Chem., 2015, 2, 53–60 CrossRef CAS.
- D. D. Pukale, G. L. Maddikeri, P. R. Gogate, A. B. Pandit and A. P. Pratap, Ultrasound assisted transesterification of waste cooking oil using heterogeneous solid catalyst, Ultrason. Sonochem., 2015, 22, 278–286 CrossRef CAS PubMed.
- H. Fukuda, A. Kondo and H. Noda, Biodiesel fuel production by transesterification of oils, J. Biosci. Bioeng., 2001, 92, 405–416 CrossRef CAS PubMed.
- W. Xie, H. Peng and L. Cheng, Biodiesel Production from Simaroubaglauca Oil using CaO and KOH Catalysts: A Comparative Study, Appl. Catal., A, 2006, 300, 67–74 CrossRef CAS.
- Y. C. Sharma, B. Singh and J. Korstad, Latest developments on application of heterogenous basic catalysts for an efficient and eco friendly synthesis of biodiesel: a review, Fuel, 2011, 90, 1309–1324 CrossRef CAS.
- S. Semwal, A. K. Arora, R. P. Badoni and D. K. Tuli, Biodiesel production using heterogeneous catalysts, Bioresour. Technol., 2011, 102, 2151–2161 CrossRef CAS PubMed.
- M. E. Borges and L. Díaz, Recent developments on heterogeneous catalysts for biodiesel production by oil esterification and transesterification reactions: A review, Renewable Sustainable Energy Rev., 2012, 16, 2839–2849 CrossRef CAS.
- X. Liang, S. Gao, H. Wu and J. Yang, Highly efficient procedure for the synthesis of biodiesel from soybean oil, Fuel Process. Technol., 2009, 90, 701–704 CrossRef CAS.
- O. Ilgen and A. N. Akin, Transesterification of Canola Oil to Biodiesel Using MgO Loaded with KOH as a Heterogeneous Catalyst, Energy Fuels, 2009, 23, 1786–1789 CrossRef CAS.
- M. Di Serio, R. T. Esser, L. Pengmei and E. Santacesaria, Heterogeneous Catalysts for Biodiesel Production, Energy Fuels, 2008, 22, 207–217 CrossRef CAS.
- Z. Helwani, M. R. Othman, N. Aziz, J. Kim and W. J. N. Fernando, Solid heterogeneous catalysts for transesterification of triglycerides with methanol: A review, Appl. Catal., A, 2009, 363, 1–10 CrossRef CAS.
- A. Islam, Y. H. Taufiq-Yap, C. M. Chu and E. S. Chan, Studies on design of heterogeneous catalysts for biodiesel production, Process Saf. Environ. Prot., 2013, 91, 131–144 CrossRef CAS.
- S. E. Mahesh and A. Ramanathan, Begum KMMS, Narayanan A. Biodiesel productionfrom waste cooking oil using KBr impregnated CaO as catalyst, Energy Convers. Manage., 2015, 91, 442–450 CrossRef CAS.
- F. E. Soetaredjo, A. Ayucitra, S. Ismadji and A. L. Maukar, KOH/bentonite catalysts for transesterification of palm oil to biodiesel, Appl. Clay Sci., 2011, 53, 341–346 CrossRef CAS.
- Y. M. Dai, K. T. Chen and C. C. Chen, Study of the microwave lipid extraction from microalgae for biodiesel production, Chem. Eng. J., 2014, 250, 267–273 CrossRef CAS.
- Y. M. Dai, J. S. Wu, C. C. Chen and K. T. Chen, Evaluating the optimum operating parameters on transesterification reaction for biodiesel production over a LiAlO2 catalyst, Chem. Eng. J., 2015, 280, 370–376 CrossRef CAS.
- R. Peña, R. Romero, S. L. Martínez, R. Natividad and A. Ramírez, Characterization of KNO3/NaX catalyst for sunflower oil transesterification, Fuel, 2013, 110, 63–69 CrossRef.
- H. Wu, J. Zhang, Q. Wei, J. Zheng and J. Zhang, Transesterification of soybean oil to biodiesel using zeolite supported CaO as strong base catalysts, Fuel Process. Technol., 2013, 109, 13–18 CrossRef CAS.
- Y. Wang, S. Y. Hu, Y. P. Guan, L. B. Wen and H. Y. Han, Preparation of Mesoporous Nanosized KF/CaO–MgO Catalyst and its Application for Biodiesel Production by Transesterification, Catal. Lett., 2009, 131, 574–578 CrossRef CAS.
- M. A. P. Martins, C. P. Frizzo, D. N. Moreira, N. Zanatta and H. G. Bonacorso, Ionic Liquids in Heterocyclic Synthesis, Chem. Rev., 2008, 108, 2015–2050 CrossRef CAS PubMed.
- J. S. Ghomi and S. Zahedi, Novel ionic liquid supported on Fe3O4 nanoparticles and its application as a catalyst in Mannich reaction under ultrasonic irradiation, Ultrason. Sonochem., 2017, 34, 916–923 CrossRef PubMed.
- G. R. M. Dowson, D. G. Reed, J. M. Bellas, C. Charalambous and P. Styring, Fast and selective separation of carbon dioxide from dilute streams by pressure swing adsorption using solid ionic liquids, Faraday Discuss., 2016, 192, 511–527 RSC.
- M. Grilc, B. Likozar and J. Levec, Kinetic model of homogeneous lignocellulosic biomass solvolysis in glycerol and imidazolium-based ionic liquids with subsequent heterogeneous hydro-deoxygenation over NiMo/Al2O3 catalyst, Catal. Today, 2015, 256, 302–314 CrossRef CAS.
- W. Zhang, Q. Wang, H. Wu, P. Wu and M. A. He, highly ordered mesoporous polymer supported imidazolium-based ionic liquid: an efficient catalyst for cycloaddition of CO2 with epoxides to produce cyclic carbonates, Green Chem., 2014, 16, 4767–4774 RSC.
- Q. C. Tran, V. D. Dao, H. Y. Kim, K. D. Jung and H. S. Choi, Pt-based alloy/carbon black nanohybrid covered with ionic liquid supramolecules as an efficient catalyst for oxygen reduction reactions, Appl. Catal., B, 2017, 204, 365–373 CrossRef CAS.
- T. Qiu, X. Guo, J. Yang, L. Zhou, L. Li, H. Wang and Y. Niu, The synthesis of biodiesel from coconut oil using novel Brønsted acidic ionic liquid as green catalyst, Chem. Eng. J., 2016, 296, 71–78 CrossRef CAS.
- P. Fan, S. Xing, J. Wang, J. Fu, L. Yang, G. Yang, C. Miao and P. Lv, Sulfonated imidazolium ionic liquid-catalyzed transesterification for biodiesel synthesis, Fuel, 2017, 188, 483–488 CrossRef CAS.
- E. Rafiee and F. Mirnezami, Temperature regulated Brønsted acidic ionic liquid-catalyze esterification of oleic acid for biodiesel application, J. Mol. Struct., 2017, 1130, 296–302 CrossRef CAS.
- M. Olkiewicz, N. V. Plechkova, M. J. Earle, A. Fabregat, F. Stüber, A. Fortuny, J. Font and C. Bengoa, Biodiesel production from sewage sludge lipids catalysed by Brønsted acidic ionic liquids, Appl. Catal., B, 2016, 181, 738–746 CrossRef CAS.
- S. Siankevich, S. Mozzettini, F. Bobbink, S. Ding, Z. Fei, N. Yan and P. J. Dyson, Influence of the anion on the oxidation of 5-hydroxymethylfurfural using platinum nanoparticle-ionic polymer supported catalysts, ChemPlusChem, 2017, 82, 1–6 CrossRef.
- S. Siankevich, Z. Fei, N. Yan and P. J. Dyson, Application of Ionic Liquids in the Downstream Processing of Lignocellulosic Biomass, Chimia, 2015, 69, 592–595 CrossRef CAS PubMed.
- S. Siankevich, G. Savoglidis, Z. Fei, G. Laurenczy, D. T. L. Alexander, N. Yan and P. J. Dyson, A novel platinum nanocatalyst for the oxidation of 5-Hydroxymethylfurfural into 2,5-Furandicarboxylicacid under mild conditions, J. Catal., 2014, 315, 67–74 CrossRef CAS.
- C. F. Gibbs and E. R. Littmann, Marvel CS. Quaternary Ammonium Salts from Halogenated
Alkyl Dimethylamines II. The Polymerization of Gamma-Halogenopropyldimethylamines, J. Am. Chem. Soc., 1933, 55, 753–757 CrossRef CAS.
- C. C. Perry, X. Li and D. N. Waters, Structural studies of gel phases—IV, An infrared reflectance and Fourier transform Raman study of silica and silica/titania gel glasses, Spectrochim. Acta, Part A, 1991, 47, 1484–1494 CrossRef.
- I. Waclawska, Glass transition effect of amorphous borates, Thermochim. Acta, 1995, 269, 457–464 CrossRef.
-
C. Gautam, A. K. Yadav and A. K. Singh, A Review on Infrared Spectroscopy of Borate Glasses with Effects of Different Additives, International Scholarly Research Network, 2012 Search PubMed.
- X. Rios, P. Moriones, J. C. Echeverría, A. Luquín, M. Laguna and J. J. Garrido, Characterisation of hybrid xerogels synthesised in acid media using methyltriethoxysilane (MTEOS) and tetraethoxysilane (TEOS) as precursors, Adsorption, 2011, 17, 583–593 CrossRef CAS.
- I. Langmuir, Adsorption of Gases on Plane Surfaces of Glass, Mica and Platinum, J. Am. Chem. Soc., 1918, 40, 1361–1403 CrossRef CAS.
-
S. J. Gregg and K. S. W. Sing, Adsorption, surface area and porosity, Academic Press, New York, 2nd edn, 1982 Search PubMed.
- L. B. Sun, W. H. Tian and W. Q. Liu, Magnesia-Incorporated Mesoporous Alumina with Crystalline Frameworks: A Solid Strong Base Derived from Direct Synthesis, J. Phys. Chem. C, 2009, 113, 19172–19178 CAS.
-
A. Y. Yacob, A. M. Bello, A. Ruskam and K. S. Kabo Catalytic Performance by Kinetics Evaluation of Novel KOH Modified Zinc Oxide in the Heterogeneous Transesterification of Rice Bran Oil to Biodiese, 6th International Conference on Environmental Science and Technology 2015, 84, 101-107.
- A. N. Phan, A. P. Harvey and V. Eze, Rapid production of biodiesel in mesoscale oscillatory baffled reactors, Chem. Eng. Technol., 2012, 35, 1214–1220 CrossRef CAS.
- B. Yoosuk, P. Krasae, B. Puttasawat, P. Udomsap, N. Viriya-empikul and K. Faungnawakij, Magnesia modified with strontium as a solid base catalyst for transesterification of palm olein, Chem. Eng. J., 2010, 162, 58–66 CrossRef CAS.
- B. Hamad, R. O. Lopes de Souza, G. Sapaly, M. G. Rocha, P. G. Pries de Oliveira, W. A. Gonzalez, E. A. Andrade Sales and N. Essayema, Transesterification of rapeseed oil with ethanol over heterogeneous heteropolyacids, Catal. Commun., 2008, 10, 92–97 CrossRef CAS.
Footnote |
† Electronic supplementary information (ESI) available. See DOI: 10.1039/c7nj03285d |
|
This journal is © The Royal Society of Chemistry and the Centre National de la Recherche Scientifique 2018 |
Click here to see how this site uses Cookies. View our privacy policy here.