DOI:
10.1039/C8GC02195C
(Critical Review)
Green Chem., 2018,
20, 5245-5260
Vertically aligned carbon nanotubes: production and applications for environmental sustainability
Received
15th July 2018
, Accepted 12th September 2018
First published on 5th October 2018
Abstract
Carbon nanomaterials play an essential role in resolving the increasingly urgent energy and environmental crises. A unique type of carbon nanotubes (CNTs), vertically aligned CNTs (VACNTs) possess the intrinsic, extraordinary nanoscale properties (mechanical, electrical, and thermal) of individual CNTs, but present them in a hierarchical and anisotropic morphology, which holds promise to transform a diverse set of practical environmental application processes from water filtration to energy storage. Nevertheless, the potential environmental impacts beholden to their synthetic methodology might reduce the net sustainability benefits of this advanced material, where environmental impacts of the synthesis may be reduced or offset by the lifetime benefits of the proposed technologies. Aiming to provide a holistic view of the robust development of VACNT-enabled environmental technologies, this critical review assesses recent advances in their production routes and applications, both with a focus on environmental objective optimization. In particular, sustainable production of VACNTs, VACNT-based functional composite materials, and their environmental engineering applications based on different functional mechanisms (i.e., sorption, catalysis, and separation) are thoroughly featured. Finally, we illustrate VACNTs as an example to explore strategies to co-optimize their environmental benefits and costs, which could potentially impact the way all other emerging materials are designed for environmental sustainability purposes.
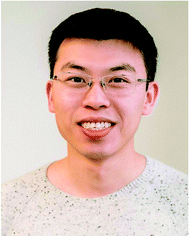 Wenbo Shi | Wenbo Shi is a Postdoctoral Associate in the Department of Civil and Environmental Engineering at MIT. Before joining MIT, he received a B.E. in Environmental Engineering from Tsinghua University (Beijing, China), a M.S. in Civil and Environmental Engineering from Duke University, and a Ph.D. in Chemical and Environmental Engineering from Yale University. He is interested in the sustainable production of advanced nanomaterials and is dedicated to promoting their application in energy and environment-related fields. |
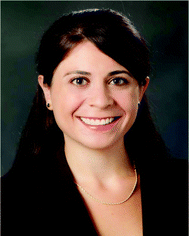 Desiree L. Plata | Desiree Plata's research seeks to maximize technology's benefits to society while minimizing environmental impacts of industrially important practices through the use of geochemical tools and chemical mechanistic insights. Plata earned her doctoral degree in Chemical Oceanography and Environmental Chemistry from the MIT/Woods Hole Oceanographic Institution's Joint Program in Oceanography and her bachelor's degree in Chemistry from Union College in Schenectady, NY. Plata is a National Academy of Engineers Frontiers of Engineering Fellow, a two-time National Academy of Sciences Kavli Frontiers of Science Fellow, and an NSF CAREER Awardee. Plata is currently Gilbert W. Winslow Career Development Assistant Professor of Civil and Environmental Engineering at the Massachusetts Institute of Technology. |
1. Introduction
Their intrinsic chemical and mechanical properties, such as exceptional thermal and electrical conductivities, have inspired widespread research efforts on carbon nanotubes (CNTs).1 Along with a boom in CNT-related publications and patents, CNT production has become a large-scale industrial chemical process, with annual production reaching a level of thousands of tons in the year 2011.2 The favored method for CNT mass production is catalytic chemical vapor deposition (CVD),3 which is a heterogeneous catalytic conversion process where carbon-containing gas species are converted to nano-tubular graphitic structures with the assistance of nanoparticles under thermal treatment (note that CNTs can also be synthesized by arc discharge and laser ablation). Generally, as-grown CNTs display three different morphologies achieved via variable growth techniques: (1) agglomerated “powdered” CNTs, (2) horizontally aligned CNTs, and (3) vertically aligned CNTs (Fig. 1).
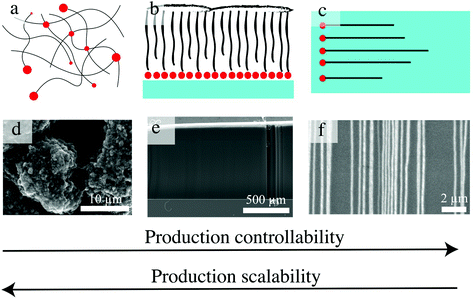 |
| Fig. 1 Illustration of three as-grown CNT morphologies: (a) agglomerated CNTs, (b) vertically aligned CNTs, and (c) horizontally aligned CNTs through CVD and their corresponding SEM images (d–f). (d–f are reproduced from ref. 4 with permission from Elsevier, ref. 5 with permission from the Royal Society of Chemistry, and ref. 6 with permission from Copyright 2014 American Chemistry Society, respectively.) | |
Agglomerated CNT powders are grown from fluidized bed reactors to take advantage of the uniform gas diffusion and heat transfer to metal catalyst nanoparticles in the CVD process. This production method is the easiest to scale, but inevitably causes mixing with impurities (amorphous carbon and catalyst), resulting in the need for post-synthesis treatment to yield pure CNTs. Impurities are removed by acid treatment/thermal annealing, which can introduce other structural impurities, degrade nanotube length and perfection, and inevitably add production cost and indirect costs associated with environmental damages. This form of CNTs is the most widely produced CNT today, dominating the annual production, whereas the contribution of aligned forms is trivial, and the powered CNTs have already been incorporated into commercial applications (e.g., in bulk composite materials and thin films). In addition, high single-chirality abundance SWCNT powders are available after tedious post-synthesis selection processes or, for 6,5 (n,m) tubes, by careful catalyst selection used in a few commercial products.7,8 However, these unorganized CNT architectures usually fail to meet expected material properties, likely due to poor alignment, loss of anisotropy, or loss of nano-dependent features through the formation of an agglomerated structure. For example, others have shown that whereas isolated CNTs were highly thermally conductive, their unorganized assemblies behaved more like thermal insulators due to the contact resistance of CNT overlaps or junctions.9 The production and applications of agglomerated CNTs have been reviewed previously.10–16
In contrast to powdered, agglomerated products, horizontally aligned CNTs and VACNTs provide flat and/or substrate-bounded growth, which directs them into organized morphologies. Horizontally aligned CNTs have the highest crystallinities, but suffer extremely low yields (areal density usually less than 200 CNTs μm−1 (ref. 17)). In addition, they have narrow and confining, although potentially transformative, application fields, specifically for nanoscale electronic devices. However, a lack of chirality control, low number density, and precise placement are current challenges faced by the scaled development of this CNT form. The advances in the controlled synthesis of horizontally aligned carbon nanotubes and their applications were reviewed recently.18–24 Here, we note that a “trick” to achieve horizontally aligned tubes requires a relatively low areal density of deposited catalyst (i.e., catalyst deposited in a 1D line that gives rise to orthogonal tube growth) and strong tube–substrate adhesion. In contrast, a high areal density of the catalyst provided with an appropriate C feeding rate (high enough to sustain the nucleation and elongation of high density tubes simultaneously) can promote the formation of vertically aligned, substrate-bound CNTs. This anisotropic and 3D macroporous morphology renders the unique properties of a fully accessible surface area, little-to-no amorphous carbon, minimal residual catalyst, 1D ballistic mass transport through tube pores,25 high electrical conductivity, and mechanical, chemical, and electrochemical stability, which lead to their broad proposed application in supercapacitors,26,27 electronic interconnects,28 emitters,29 dry adhesives,30 mechanical materials,31,32 separation membranes,33,34 advanced yarns and fabrics,35 black-body absorption,36 high-resolution printing stamps,37 optical rectennas,38 chemically driven thermopower wave guides,39 and ultrasensitive virus detection.40 Among these applications, the environment- and energy-related ones are in urgent need of development (i.e., for implementation to tackle the environmental and energy crises). Due to the critical role of advanced materials in solving environmental and energy problems, these applications were reviewed recently for other emerging hierarchical nanomaterials (e.g., graphene-based nanomaterials,41–45 transition-metal dichalcogenide nanomaterials,46,47 and metal–organic frameworks48), but VACNTs, although exceptional among CNT forms, have not been summarized or forecast. This review aims to provide a holistic analysis of the robust development of environmental optimization objectives for related VACNT production, architecture fabrication, and potential applications. Specifically, this review lays out routes to sustainable synthesis of VACNTs with minimized energy and emission burdens, and goes on to describe how these VACNT hierarchies might transform environmental materials applications. The ultimate goal is to employ advanced materials to achieve environmental and economic sustainability by working at the interface of material and environmental engineering.
2. Environmentally optimized synthesis
Incorporating environmentally-motivated perspectives into chemistry, engineering, and process design is essential to maximize benefits and minimize the risks of novel material and technology design.49 Engineered nanomaterial (ENM) synthesis enables potentially transformative nanotechnologies, which allow humans to access previously unattained material properties. Nevertheless, the chemical process associated with ENM production might exert adverse impacts on the environment and human health. Regarding CNTs, and particularly those with controlled 3D morphologies, the intensive energy and resource consumption of current synthetic routes raises environmental concerns for future industrialization.50–52 That is, early synthetic interests focus on controllability to achieve the desired device performances with little focus on environmental impacts, and because early design choices often propagate to the scaled processes, early omissions of impact prevention can lead to catastrophic damages for industry (e.g., asbestos,53 bisphenol A,54 or methyl-tert-butyl ether55).
Similar to other industrial processes, environmental impact investigations of CNT production are delayed by roughly 20 years from the onset of the invention.5 In 2008, Healy et al.50 conducted the first life cycle assessment (LCA) on CNT manufacturing via arc ablation, CVD, and high-pressure carbon monoxide, and they highlighted that the life cycle impacts were dominated by energy consumption. Indeed, CNTs were found to be among the short list of the most energy-intensive materials syntheses, of the order of up to 100 times more than aluminum.51 In addition to the specific energy requirements, toxic byproduct emissions from CNT production might exert potential human health impacts,56 where environmental impacts from emissions can exceed direct exposure impacts.57 Aware of the potential environmental concerns of CNT production, more studies on environmental optimization of CNT manufacturing were inspired by these pioneering works, and several milestones have been achieved (Fig. 2).
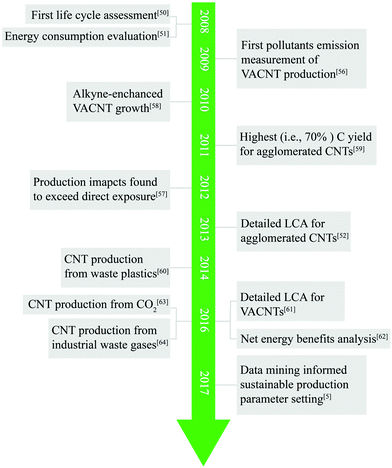 |
| Fig. 2 Timeline of milestones of CNT production studies pertaining to environmental optimization objectives. These efforts include the following discoveries: the first life cycle assessment (LCA) of CNT production,50 energy consumption evaluation,51 the first pollutant emission measurement for VACNTs,56 alkyne-enhanced VACNT growth,58 the highest reported carbon conversion efficiency for agglomerated CNTs,59 production impacts found to exceed direct exposure impacts for CNTs,57 detailed LCA for agglomerated CNTs,52 CNT production from waste plastics,60 detailed LCA for VACNTs,61 net energy benefit analysis for CNT applications,62 CNT production from CO2,63 CNT production from industrial waste gases,64 and the first data mining for CNT growth recipes and improved efficiency strategies.5 | |
Atomic carbon conversion efficiency and thermodynamic limitations are the fundamental chemical drivers that directly control byproduct generation and minimum energy cost, respectively. The atomic carbon conversion efficiency for agglomerated, bulk powdered CNTs is almost universally higher than that for vertically aligned CNTs due to the contact between the reactant gas and more available catalytic sites (i.e., large amounts of catalyst are loaded and mixed in contact with the reactant C source). For example, Kim et al.59 developed a semi-continuous fluidized-bed with augmented catalyst dispersing on ceramic beads, reaching a remarkable atom efficiency of over 70%; in contrast, the VACNT grown from substrate-affixed catalysts and C2H4-fed chemistry exhibited only 0.05%5 C conversion. Note that the residual input gaseous materials are all exhausted as environmental pollutants (i.e., volatile organic compounds (VOCs) and polycyclic aromatic hydrocarbons (PAHs)), and thus low yields necessarily correspond to high emissions rates (unless recycling is used, which is rare65–68). Low carbon conversion efficiency is influenced by reactant imbalances and poor contact, but could be exacerbated by some thermodynamic limitations. Thermodynamic insights are popular to explain the resulting CNT controllability; for example, SWCNT selectivity commonly relies on minimized formation energy to determine the geometrical association between CNT structure and one specific crystal lattice of the catalyst during active carbon species arrangement.21 However, from the overall energy consumption perspective, the conversion from the starting carbon materials to the active carbon species tends to correlate with the minimum operational temperature requirements, which are related to energy costs.5 In fact, most previous successful approaches for lower temperature CNT synthesis reflected the elimination of this carbon precursor conversion process, including plasma enhancement,69,70 preheater implementation,71 and more active gas precursor choice.72
To achieve better yield, the CNT growth via CVD has been modified through advancing reactor design and altering chemical processes. Simultaneously, these approaches happen to benefit the environmental sustainability of CNT manufacturing. Two successful representative reactor design modifications include controlling the gas flow direction (i.e., employing a gas shower system to deliver gas from the top of the forest instead of from the side)73 and manufacturing CNTs in a continuous manner,74 both of which serve to maximize the contact between the gaseous reactants and catalyst and enhance the yield performance. While reactor setup modification is a promising strategy, it is often less accessible once significant capital costs have been invested, and manipulating the chemical reaction process is a more common strategy to enhance the carbon yield, including investing in heteroatom growth enhancers (e.g., H2O,75–80 O2,78,81–84 H2,59,85 alcohol,86,87 CO2,72,88,89 and acetone90) or/and altering the hydrocarbon source.58 In addition, new branches of research aimed at using waste streams for CNT production have gained attention recently, including CNTs from waste plastics,60 converting CO2 to CNTs,63,91 and utilizing industrial gas effluents as CNT feedstock material,64,92 which hold promise to enhance the environmental sustainability due to reaction source accessibility and low cost.
Based on the CVD process of CNT synthesis, a strategic modification route (Fig. 3) to promote sustainable production of CNTs is proposed. From changing the starting materials to increasing the catalyst efficiency, to reusing effluent gases, each modification (either through chemistry or reactor design) would advance the economic and environmental sustainability of this energy and material-intensive process. The synthetic strategy not only determines the overall sustainability of the production–application circuit, but also is critical to tune as-grown CNT properties for desired applications (e.g., alignment for shorted charge or thermal transport path and diameter for filtration).
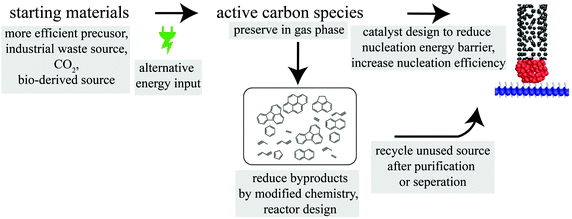 |
| Fig. 3 Flow chart of CNT synthesis steps and modification suggestions (grey boxes) for future environmentally sustainable CNT production. | |
3. Integration in VACNT-composite functional materials
In addition to the manipulation of VACNT growth, chemical and structural modifications are commonly employed to preserve the structural stiffness or to introduce new functionalities into the hierarchical porous platform of VACNTs. VACNT–polymer composites,93 VACNT–inorganic hybrids,94 and heteroatom doped VACNTs95 are important derivatives to serve as functional materials for environmental and energy beneficial purposes (Fig. 4). Since VACNTs will experience surface-tension driven aggregation and densification following liquid infiltration and evaporation,96 the traditional treatment methods (e.g., mechanical-reinforced solution dispersion or strong acid oxidation) used with powdered CNTs can not be used with VACNTs in order to form these VACNT-composites if one seeks to preserve their 3D structure. With this constraint, a wide array of unique fabrication methods have been developed to achieve VACNT-composite functional materials, which confer VACNTs new properties (i.e., catalysis) or augment the properties of individual components for superior overall performance.
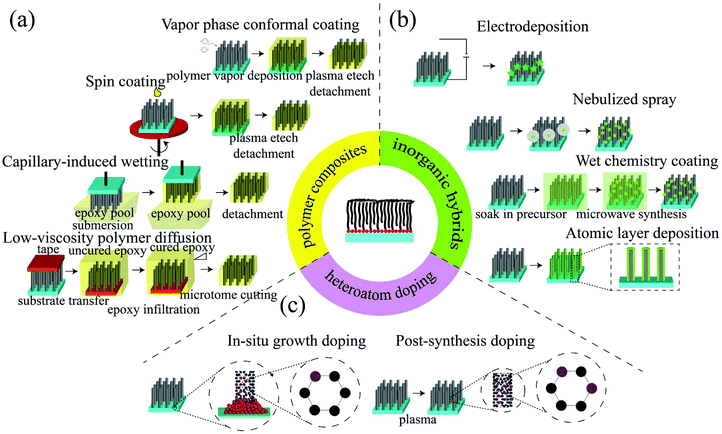 |
| Fig. 4 Schematic illustration of VACNT-enabled functional materials and their corresponding fabrication methodologies. (a) VACNT–polymer composites, (b) VACNT–inorganic hybrids, and (c) heteroatom-doping VACNTs. Note that the heteroatom (purple) in c is merely a schematic illustration of the concept and the newly-formed structure doesn't necessarily still retain a hexagonal structure after heteroatom doping. | |
For demanding applications requiring optimized permeability and selectivity, such as wastewater treatment membranes, open and aligned nanochannels of VACNTs are the unique characteristic needed to achieve fast mass transport through these superhydrophobic nanochannels.25,33 Polymer infiltration would maintain the integrity of the VACNTs under their functioning environment (e.g., pressurized or aqueous conditions) and guarantee that the targeted molecule(s) travel through the defined nanopores only. Such VACNT–polymer composites have been efficiently fabricated through vapor phase conformal coating polymers,34,97 spin coating polymers,33,98 capillary-induced wetting polymer infiltration,31 and direct polymer diffusion through immersing VACNTs in a polymer solution99,100 (Fig. 4a). Spin coating, capillary-induced wetting polymer infiltration, and direct polymer diffusion are easy to operate and are sufficient to accomplish the target of blocking the interstitial space between tubes in the VACNT forest. In contrast to these solution-based polymerization techniques, vapor phase polymer coating methods utilize the polymerization of delivered vapor-phase monomers on the surface of the substrate, which could result in more controllability.101 The tunable, conformal coating not only is capable of forming a VACNT membrane, but also might enable additive functionalities (e.g., superhydrophobicity102) onto VACNTs.
In the VACNT–inorganic hybrids, VACNTs work as a support in most cases to maximize the performance of active inorganic components, usually by functionally increasing their exposed surface area, such as for catalysis and/or adsorption. Compared with other large surface area supporting materials, the unique advantages of VACNT are their synergistic characteristics of high conductivity and well-ordered hierarchical structures. The metal oxides or metals can be deposited through electrodeposition,103 nebulized spray,104 wet chemistry coating,105,106 and atomic layer deposition107,108 (Fig. 4b). Electrodeposition and wet chemistry methods are solution-based coating approaches. Due to the capillary-driven aggregation of the CNT forest upon liquid infiltration and evaporation,96 these two techniques usually result in large coating particle size or non-uniform coating. Atomic layer deposition utilized a sequential self-terminating reaction between the gas phase molecules and the solid surface to ensure the extreme coating controllability (less than one nanometer),109 but this process needs to operate in a special apparatus. To avoid liquid contact and overcome the difficulty of limited device accessibility, an interesting nebulized spray method was developed in 2014 and was found to work universally for different metal oxides.104 Besides the VACNT–metal oxides, VACNT–graphene hybrid materials110,111 have emerged as a promising composite for energy storage devices due to the efficient covalent bonding between these two types of materials when forming 3D architectures, and they are usually made by CVD to deposit graphene and VACNTs on the substrate consecutively.
In contrast to coating metal oxides on the outer surface of VACNTs to serve as the catalytic active sites, replacing carbon atoms in the VACNT structures with heteroatoms (e.g., N, S, B, and P) could directly introduce active sites inside VACNTs, rendering them highly efficient, metal-free catalysts.112 These dopants can change the physical and chemical properties of VACNTs through inducing CNT graphitic structure charge redistribution and lattice structure distortion, leading the VACNTs to convey catalytic activity.113 The heteroatom doping can be realized through in situ doping during VACNT synthesis114–116 or doping during post-treatment117 (Fig. 4c). In situ doping processes are conducted via co-delivering the C-containing precursor and the heteroatom-containing precursor for the catalytic thermal CVD process, whereas post-treatment doping relies on incorporating heteroatoms into the existing vacancies in the graphitic lattice. This results in the traditional post-synthesis thermal annealing that is not compatible with well-crystalline SWCNTs (i.e., nearly no N- or S-doping is available)118 and the highest N doping level (5.0 at%, defined as mol heteroatom/mol C × at%) was achieved through in situ synthesis.119 Considering plasma etching has been used to open VACNT caps as well as functionalize them, that technique, simultaneously generating graphitic vacancies and incorporating heteroatoms into these sites, might emerge as an alternative post-synthesis treatment approach to doping VACNTs under a N2 or NH3 gas environment.120–122
4. Environmental applications of VACNTs
While there are a large number of environmental applications proposed for CNTs, three categories have garnered the most attention, leading to the most notable demonstrations. These are in the areas of sorption, catalysis, and separations (via size sieving) (Fig. 5).
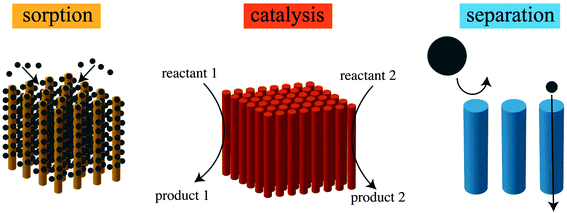 |
| Fig. 5 Schematic illustration of the environmental applications of CNTs, including sorption, catalysis, and separation. | |
4.1 Adsorption
Adsorption processes are a traditional technique in point-of-use devices to selectively remove viruses, inorganic and organic pollutants to produce clean and safe water or gas.123 Due to their high surface area, well-defined pore structures, inherent hydrophobicity, and tunable nanoscale properties, CNTs have been considered as remarkable adsorption materials in the past few decades. Although most studies utilized randomly oriented CNTs, previous efforts have identified four possible adsorption sites in CNT bundles:11,124 (1) the hollow interior of individual nanotubes, (2) the interstitial channels between individual nanotubes inside nanotube bundles, (3) the external groove site where two outermost adjacent parallel tubes meet, and (4) the curved surface of the outermost, “exposed” nanotubes at the edges of the nanotube bundles (Fig. 6a). Note that functional groups and defects in the CNT structure may change the accessibility and affinity of CNT surfaces for sorbates, dramatically altering the adsorption behavior.125 Interestingly, alignment has emerged as a critical factor to control adsorption capacity, ultimately allowing free-standing VACNT films to fulfill their promise to outperform randomly oriented CNTs. For example, using N2 adsorption as the study model, the self-oriented CNT vertical arrays were found to deliver increased adsorption uptake compared to the disarranged counterparts following ultrasonication treatment, due to the enhanced interstitial spaces between the individual nanotubes inside the VACNTs, along with better alignment.126 The potential adsorption applications of VACNTs for environmental remediation and energy engineering are categorized in the following discussion into (1) gas phase adsorption, (2) liquid phase adsorption, and (3) ion adsorption from liquid systems (Fig. 6).
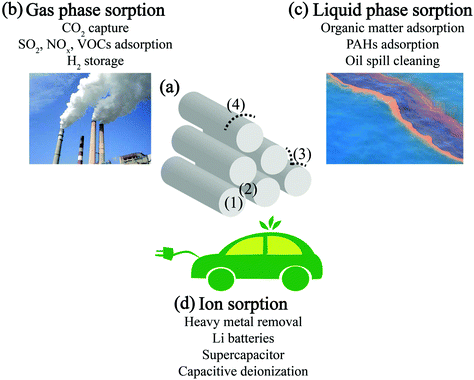 |
| Fig. 6 (a) CNT bundles’ possible adsorption sites and (b–d) CNTs’ adsorption functional mechanisms for environmental and energy engineering purposes at different media–CNT interfaces. | |
4.1.1 Gas phase adsorption.
Adsorption technologies have played a vital role in gaseous pollutant management due to their fast reaction kinetics, simple design and operation, and sometimes low cost. CNTs have been investigated as adsorbents for removing key pollutants (e.g., NOx,127 SO2,128 VOCs,129–131 and CO2132–134) that either are toxic to human health, hazardous to environmental ecosystems, or contribute to climate change from waste gas streams. However, available examples using VACNTs as gaseous pollutant adsorbents are extremely limited. Babu et al.135 studied double-walled VACNT forests with varied average diameters and discovered that decreasing the CNT diameter could increase the adsorption capacity of CO2 at high pressure regimes (ranging from 5 to 60 bar). To potentially enhance the adsorption performance at low pressure (less than 15 bar), the authors found that oxygen plasma could functionalize the VACNTs with C–O functional groups in situ without impacting the well-ordered 3D structure, and the product exhibited better adsorption characteristics. Here, we note that most VACNT adsorption studies still remain in the theoretical prediction stage,136–141 but all indicate the superiority of this unique morphology as effective adsorbents, merely due to their well-defined open-end pore arrangement and tunable inter-tube space when compared to their powdered CNT counterparts.
In addition to the gas pollutant remediation-oriented gas phase adsorption, the signature adsorption characteristic enables CNTs to store H2
142,143 for energy generation, providing a critical solution to “renewable” energy storage and transformation. When using VACNTs, Cao et al.144 demonstrated that controlling the inter-nanotube space between adjacent parallel tubes could contribute more H2 storage capacity enhancement space as the supplement to the generally suggested hollow interior storing space of individual nanotubes. However, over the evolution of this technique, there has been substantial controversy regarding the reported H2 uptake capability of CNTs,145 and this hinders advancement of this technology. Poignantly, this highlights the importance of reproducibility while developing applications for advanced materials and the threshold for rigor that should be applied for robust proof-of-concept demonstrations.
4.1.2 Liquid phase adsorption.
Many hydrophobic sorbents are used to enhance partitioning of dissolved organic chemicals (i.e., the sorbates) from the aqueous phase to the solid sorbent, and while VACNTs are effective in this mechanism of uptake, their unique geometry can offer wicking and sponge behaviors that enhance chemical partitioning via physical uptake. Accordingly, a representative proposed application of 3D CNT structures in liquid phase adsorption is oil spill cleaning. Using a similar growth methodology to produce VACNTs (i.e., CVD) but with a different carbon source (i.e., ferrocene dissolved in 1,2-dichlorobenzene as a catalyst precursor and a carbon source, respectively, fed by a syringe pump), a CNT sponge with a porous, interconnected, and 3D framework was fabricated and it exhibited an exceptional (i.e., up to 180 times its own weight, about 100 times higher than activated carbon) oil adsorption capacity.146 In addition to those physical drivers for sorption, chemical modification was shown to improve sorption capacity; for example, boron substitution doping created covalent bonding between the 3D, interconnected CNT skeleton, which enhanced the oil adsorption performance and enabled sorbent reuse.147 In addition to oil uptake, aromatic compounds (e.g., dioxin,130 benzene,125,148 phenol,149 and PAHs150), humic acid,151 and dye molecules152 can also be adsorbed by CNTs. However, similar to gas phase adsorption studies, these explorations are limited to randomly-oriented and aqueous-solution-dispersed CNTs derived from powdered CNTs.125 Nevertheless, the sorptive properties of these powdered CNTs are as good or better on both a mass and surface-area normalized basis than granular activated carbon sorbents.153,154 Compared to powdered CNTs and activated carbons, where most of the carbon mass is internal and inaccessible to large sorbates, VACNTs have theoretically maximized surface areas, tunable functional groups, great accessibility to the adsorbates, intrinsic chemical stability, and, most importantly, their bulk structure integrity could result in orders of magnitude adsorption enhancement and reuse properties that are beneficial for real world applications.
4.1.3 Ion sorption.
Ion sorption is the fundamental property that enables heavy metal removal, electrochemical desalination, supercapacitors, and batteries; that is, most of the energy storage applications rely on this property of CNTs. The nanoporous structure, enormous number of available adsorption sites, and high conductivity enable CNTs to act as the active component in devices for both water treatment and energy storage, potentially tackling the water scarcity and energy crises (and some have proposed that this could be done simultaneously155,156). The available heavy metal ion adsorption investigations are mostly confined to randomly oriented and solution-dispersed CNTs, and several studies have claimed that surface functional group density is the key control factor to enhance heavy metal adsorption capacity.157–162 In contrast, for energy storage applications, better control of ion and electron flow is required, and thus, VACNTs have been intensively explored for supercapacitors26,27,163 and Li-ion batteries.164,165 The 3D, well-ordered framework of these materials creates a more accessible surface area (i.e., confers mesoporosity166) and well-directed electron transport paths for electrochemical ion adsorption. While maintaining a vertically aligned shape, densification26,163 and nanotube cap opening27 were found to enhance their capacitance as an electrical double layer capacitor, due to increased volumetric specific electrode surface area and accessibility of the inner cavity, respectively. Moreover, the VACNT surface could serve as a platform for metal oxide deposition, providing novel routes to CNT/metal oxides103–106,167–170 materials that may perform as a hybrid capacitor/battery, which store charge relying on the electrochemical double layer (i.e., electrostatically) and also via the fast surface redox reactions of metal oxides (i.e., electrochemically). This additive electrochemical pseudocapacitance could augment overall total capacitance and contribute to the overall performance of the energy storage materials.
4.2 Catalysis
A perfect CNT structure does not exhibit outstanding catalytic capability. The catalytic activity relies on functional groups, defects, dopants, and decorated catalytic active species, where the catalytic activity can be enhanced by the presence of the CNTs. CNT-based catalysts provide high activity and durability because of their high surface area, high crystallinity, controllable homogeneity, chemically uniform active sites and stable geometric structure.113,171,172 However, the majority of CNT-based catalysts have been explored for electrochemical fields, whereas non-electrochemical catalysis targeting industrially important transformation technologies (e.g., environmental remediation) are still under development. Similar to the benefits of morphology (enhanced surface area) in adsorption, VACNTs have also shown improved catalytic performance with their corresponding functional composites (Table 1).
Table 1 Summary of VACNT-based catalysts and their catalytic processes for environmental and energy applications
Catalysis type |
Functional materials |
Catalytic reaction |
Environmental and energy implications |
Ref. |
Photocatalysis |
VACNT/TiO2 |
E. coli bacteria inactivation |
Water disinfection with solar energy |
Akhavan et al.173 |
VACNT/TiO2 |
2H2O → O2 + 4H+ + 4e− |
Solar energy conversion |
Yang et al.174 |
CdS–CNT sponge |
Rhodamine B dye degradation |
Water purification |
Li et al.175 |
N-Doped CNT/TiO2 core/shell nanowires |
Methylene blue and p-nitrophenol dye degradation |
Water purification |
Lee et al.176 |
TiO2/CNT/Pt nanoarrays |
Dye degradation: 2H2O → O2 + 4H+ + 4e− |
Water purification and solar energy conversion |
Park et al.177 |
Biocatalysis |
VACNTs |
Organic matter consumption by microorganism |
Wastewater remediation and power generation |
Mink et al.178 |
Electrocatalysis |
Pt–VACNT–carbon fibers |
O2 + 4H+ + 4e− → 2H2O |
Environmental sensor |
Xiang et al.179 |
VA–N-doped CNTs |
O2 + 4H+ + 4e− → 2H2O |
Fuel cells; renewable and clean energy technology |
Gong et al.114 |
Electrocatalysis |
VA–N-doped CNTs |
CO2 + 2H+ + 2e− → CO + H2O |
CO2 reduction, climate change mitigation |
Sharma et al.116 |
VA–boron–carbon–nitrogen NTs |
O2 + 4H+ + 4e− → 2H2O |
Fuel cells; renewable and clean energy technology |
Wang et al.180 |
VACNT/metal oxides |
O2 + 4H+ + 4e− → 2H2O |
Fuel cells; renewable and clean energy technology |
Yang et al.104 |
MoSx-VANCNTs |
2H+ + 2e− → H2 |
H2 production, renewable energy |
Li et al.181 |
Pt-VACNT |
CH3OH + H2O → 6H+ + 6e− + CO2 |
Methanol oxidation, fuel cells, renewable and clean energy |
Su et al.182 |
4.2.1 Catalysis in the liquid phase.
Catalytic technology for liquid waste treatment includes catalytic ozonation, photocatalysis, electrocatalysis, and electron-Fenton systems, which could efficiently remove organic compounds (e.g., pesticides, pharmaceuticals, and personal care products), nitrates, and other aqueous pollutants.183 Even though CNTs were reported to benefit these processes,184,185 they have been rarely used in a 3D form, except during photocatalysis. A good example of VACNTs’ photocatalytic applications is to support and tune the properties of titanium dioxide, which is a widely used photocatalyst, but one that suffers from a low surface area and a large band gap energy.174,176,177 In addition to pollutant remediation and water splitting, a composite CNT-TiO2 3D photocatalyst was found to photoinactivate bacteria under visible light irradiation (differing from the UV light irradiation of TiO2 itself).173 To achieve the same purpose of water disinfection, replacing TiO2 with Ag in the VACNT arrays has been demonstrated to show strong antibacterial activity in the dark (no light required).186
4.2.2 Catalysis in the gas phase.
Environmental catalysis also plays an essential role in gaseous pollutant control from both stationary and mobile sources with applications ranging from selective catalytic reduction of NOx with NH3, CO oxidation, Hg0 oxidation, to VOC catalytic combustion.187 The mode of participation in these reactions for CNTs is usually as the support or confinement for the active compounds.188–193 Taking manganese oxide as an example (a highly efficient heterogeneous catalyst for gaseous pollutant removal194), employing CNTs as the support efficiently enlarges its surface area and thus enhances the catalytic performance.195 Following the rising attention on the importance of the hierarchical geometric structure of the metal oxide catalysts,196 VACNTs with well-defined nanoscale and macroscale structures could provide an outstanding platform to support and sufficiently disperse the active catalyst, paving the way for improved catalytic performance.
4.2.3 Electrochemical catalysis.
A large portion of catalysis work using VACNTs is in the field of electrochemical catalysis, which is critical for renewable and clean energy technologies. These catalytic reactions include oxygen reduction,104,114,180 hydrogen evolution reaction,181,197 and CO2 reduction.116 VACNTs have demonstrated success when doped by heteroatoms (e.g., nitrogen or boron) or decorated with metal/metal oxides, where CNT electronic properties were tuned (e.g., by locally charging due to the difference in electronegativity of C and the substitutional elements or extra catalytic active sites due to the introduced metal cation incorporating in the graphitized carbon structure or embedding on the carbon plane) but their geometric features were maintained (i.e., shorter electron transport path and better electrolyte or reactant diffusion). In addition to these traditional electrochemical systems, VACNTs have also been used as anodes in a bio-electrochemical system (i.e., microbial fuel cells178,198), which is a technique that has been suggested to integrate organic waste remediation and electricity generation in one system via the bio-catalytic activity of microorganisms for waste water treatment.
4.3 Separation
CNTs have been proposed as nanochannels for fundamental nanofluidic studies and membrane-based separation applications,199,200 due to their tunable nanoscale properties, uniform hollow geometry, molecularly smooth inner surface, and exciting fluid transport rate (Table 2). The fast size exclusion selectivity feature of CNT-based membranes enables promising applications ranging from water purification,201,202 water desalination,203 gas purification and separation,204 and drug delivery,205 to breathable and protective textiles.206 Since the permeate selectivity heavily relies on the homogeneity of nanopore size, the application of CNT-enabled separation devices requires strict requirements on the synthetic controllability of CNT manufacturing.
Table 2 VACNT-based nanofluid devices and their performed permeation tests
Interstitial filler |
CNT diameter |
CNT forest height (μm) |
Area size (cm2) |
Fluid test |
Ref. |
Silicon nitride |
20–50 nm |
5–10 |
0.196 |
Water permeability |
Holt et al.224 |
Silicon nitride |
Average diameter 1.6 nm |
2–3 |
4 |
2 nm gold particle and Ru2+ (bipy)3 permeability; gas selectivity |
Holt et al.25 |
Silicon nitride |
Average diameter 1.6 nm |
|
0.00175 |
Ion rejection of salt solution (K3FeCN6, KCl, pyrenetetrasulfonic acid tetrasodium (Na4PTS), K2SO4, CaSO4, CaCl2, Ru(bipy)3Cl2) |
Fornasiero et al.210 |
Polystyrene |
30 ± 10 nm outer diameter, 4.3 ± 2.3 nm inner-core diameter |
5–10 |
3.1 |
N2 and Ru(NH3)63+ ionic species permeability |
Hinds et al.33 |
Polystyrene |
6.3 nm MWCNT diameter |
10 |
3.1 |
Gas (He, H2, and N2) permeability |
Mi et al.98 |
Polystyrene |
7 nm pore diameter |
126 |
0.3 |
Gas, liquid permeability, ions transport |
Majumder et al.225 |
Urethane monomer |
4.1 nm average pore size |
1000 |
0.067 |
Polyethylene oxide rejection, water permeability |
Lee et al.226 |
Parylene–N |
3.3 nm average diameter |
20–30 |
1.8 |
Charged dyes, 5 nm Au nanoparticle, 40–60 nm Dengue virus rejection; water vapor transport |
Bui et al.34 |
Polysulfone |
1.2 nm average pore diameter |
0.6 |
13.8 |
Single gas permeability and mixed gas selectivity |
Kim et al.221 |
Polystyrene–polybutadiene (PS–PB) copolymer |
Average 3.3 nm diameter |
20–50 |
cm2 scale |
5 nm gold nanoparticle, K3Fe(CN)6 and Direct Blue 71 permeability; gas permeability |
Kim et al.97 |
Epoxy resin |
8 nm average diameter |
1000 |
1 |
None |
Wardle et al.31 |
Epoxy resin |
7–14 nm diameter |
7000 |
4 |
Various liquid (water, ethanol, hexane, decane, N,N-dimethylformamide (DMF), dodecane, and 2-propanol) permeability |
Du et al.99 |
Epoxy resin |
4.8 nm diameter |
200 |
0.1 |
Liquid permeability |
Baek et al.227 |
None |
2.8 nm inner tube |
750 |
0.25 |
Gas permeability and selectivity; 3.2 nm gold nanoparticle permeability |
Yu et al.228 |
None |
6.7 inner diameter, 10 nm outer diameter |
4000 |
0.25 |
Gas permeability and their selectivity vs. H2O |
Yoon et al.214 |
None |
After densification, 7 nm outer wall pore |
1300 |
1 |
Water permeability, dextran rejection |
Lee et al.100 |
4.3.1 Ion exclusion.
Ion exclusion is the primary principle for VACNTs to serve as filters for water purification.203 The atomically smooth and hydrophobic inner core of CNTs provides a high speed tunnel for water molecule transport (4–5 orders of magnitude flux enhancement),207 while the diameter of the hollow cylinder serves as the gate keeper to exclude the undesirable permeates. Moreover, the functional chemistry on the tip of CNTs may enhance or tune the ionic selectivity, ultimately mimicking the rapid and selective ion transport in biological membranes.208 Majumder et al.209 first demonstrated the effects of CNT tip functionalization on the flux and selectivity of permeates, where grafting long chain functional molecules would decrease the pore size and adding anionically charge dye molecule onto the CNT core entrance would enhance the flux of cationic permeates (i.e., methyl viologen MV2+ and ruthenium bipyridine Ru-(bipy)32+). Furthermore, Fornasiero et al.210 proposed that the electrostatic interactions between the CNT membranes and mobile ions drove the ion rejection phenomenon, rather than steric or hydrodynamic effects when the narrow tubular confinement channel (CNT inner diameter) was larger than the diameter of hydrated ions. In addition, the capability of being able to independently functionalize each side of the VACNT membrane entrance211 and the potential utilization of electrophoresis212,213 could further stimulate membrane science with a viable route towards overcoming the tradeoff between permeability and selectivity.
4.3.2 Gas separation.
Besides ion exclusion in liquid interfaces, VACNT membranes also function in gas interfaces. VACNT membranes for gas molecular separation could be used for natural gas dehydration,214 H2 production,215,216 CO2 removal,217 air separation,218 and membrane-distilled water desalination.219 The transport of gases in CNTs was predicted to be over one order of magnitude faster than similar sized zeolites, which are commonly employed for selective gas separation at the expense of low flux.220 The theoretical predictions have been verified by Hinds et al.33 with multi-walled CNT (MWCNT) membranes (4.3 nm inner diameters) and Holt et al.25 with double-walled CNT (DWCNT) membranes (sub-2 nm diameters) independently. CNT gas permeability selectivity has been demonstrated for hydrocarbon/He,25 CO2/CH4,221 H2/CH4,216,222 H2/CO2
216 mixtures, all of which have practical gas separation implications. It is noteworthy that the fast water vapor transport in carbon nanotubes has far-reaching implications, which could enable membranes for gas separations applications including, but not limited to breathable and protective fabrics, moisture control, and desalination via distillation.206 Combining this ultrafast water transport property and VACNTs’ strong optical absorption behavior enabled VACNTs to perform well in the solar–thermal–steam generation system (evaporation rate 10 times higher than bare water with a 90% solar thermal conversion efficiency),223 providing a low cost, renewable energy-based desalination technique.
5. Conclusion and outlook
VACNT arrays with a hierarchical and anisotropic morphology effectively extend the intrinsic yet extraordinary nanoscale properties (mechanical, electrical, and thermal) of individual nanotubes to the macroscale, which hold promise to transform a diverse set of practical environmental application processes (sorption, catalysis, and separation) that will ultimately enable enhanced sustainability. The route towards realizing these goals requires sufficient integration of controllable, scalable, reproducible, and sustainable VACNT production, and effective functional composite fabrication (i.e., tailored for targeting applications and functioning environments), and there have been some primary challenges limiting the broad adoption of these nano-enabled materials.
The challenges in controllability must be addressed through further efforts: the narrowest diameters produced so far (sub-1.5 nm (ref. 229)) in VACNT still do not meet the requirement for desalination (0.8 nm (ref. 230)), a further increase of the areal number density is necessary to enhance ion storage performance,231 and bulk property homogeneity requires alignment control.232 In addition to controllability challenges, production sustainability has emerged as an overlooked factor for future large-scale manufacturing, where proactive efforts are urgently needed. The relatively poor environmental performance associated with VACNT manufacturing is largely attributed to the limited fundamental understanding of the CNT growth process. Unveiling this is critical to eliminating unnecessary heating steps for reactive intermediate generation, which could reduce energy and resource costs.58,233 In addition, the scaled-up manufacture of VACNTs is still rare, which gives rise to the gap between their bench scale application tests and practical industrial scale processes. Taking the VACNT-membrane as an example, most reported devices are in the cm2 size range, whereas wafer-scale or m2 scale membranes are necessary for real-world applications. Nevertheless, progress has been made in this area and routes toward such scaled synthesis are readily traceable.74,234
While essential concepts and methods for VACNT-enabled advanced materials have been proposed and demonstrated (e.g., VACNT–inorganic hybrids, VACNT–polymer composites, and heteroatom-doped VACNTs), challenges such as lacking facile substrate transfer methods235 and the undesirable structural deformation in functioning environments (e.g., elastocapillary densification in aquatic environments236) are persistent challenges that remain in order to accomplish the goals of ultimately incorporating VACNTs into device configurations. The stable, robust, and safe device (i.e., integrated system) design is closely related with not only the functional performance durability, but also the prevention of potential nanomaterial release during device operation.
Another aspect of robustly developing VACNT-enabled environmental technologies is to integrate proactive environmental and economic analyses into the device design, use, and disposal for guiding their environmental and economic optimizations. LCA studies have been deployed for engineered nanomaterials and even CNT-based applications.62,237–239 However, few of them have differentiated CNTs from their morphologically distinct counterparts; thus, studies focused on VACNTs and their enabled innovative technologies are limited.
Finally, this review aims to inspire the methodologies to holistically incorporate environment-driven perspectives into VACNTs: not only discussing their innovative application opportunities in environmental and energy engineering, but also featuring efforts to promote their production in a sustainable manner. This critical thinking and panoramic view based insight of co-optimizing environmental benefits and environmental costs should be expanded to the development of other emerging nanomaterials and could ultimately promote green nanotechnology to maximize the benefits for future environmental and economic sustainability.
Conflicts of interest
The authors declare no competing financial interests.
Acknowledgements
This work was supported by NSF Award Number 1552993, EPA grant number RD83558001, and Yale University graduate fellowships.
References
- H. J. Dai, Acc. Chem. Res., 2002, 35, 1035–1044 CrossRef CAS PubMed.
- M. F. L. De Volder, S. H. Tawfick, R. H. Baughman and A. J. Hart, Science, 2013, 339, 535–539 CrossRef CAS PubMed.
- G. D. Nessim, Nanoscale, 2010, 2, 1306–1323 RSC.
- F. Wei, Q. Zhang, W. Z. Qian, H. Yu, Y. Wang, G. H. Luo, G. H. Xu and D. Z. Wang, Powder Technol., 2008, 183, 10–20 CrossRef CAS.
- W. B. Shi, K. Xue, E. R. Meshot and D. L. Plata, Green Chem., 2017, 19, 3787–3800 RSC.
- J. H. Li, K. H. Liu, S. B. Liang, W. W. Zhou, M. Pierce, F. Wang, L. M. Peng and J. Liu, ACS Nano, 2014, 8, 554–562 CrossRef CAS PubMed.
- M. Zheng, A. Jagota, M. S. Strano, A. P. Santos, P. Barone, S. G. Chou, B. A. Diner, M. S. Dresselhaus, R. S. McLean, G. B. Onoa, G. G. Samsonidze, E. D. Semke, M. Usrey and D. J. Walls, Science, 2003, 302, 1545–1548 CrossRef CAS PubMed.
- M. S. Arnold, A. A. Green, J. F. Hulvat, S. I. Stupp and M. C. Hersam, Nat. Nanotechnol., 2006, 1, 60–65 CrossRef CAS PubMed.
- R. S. Prasher, X. J. Hu, Y. Chalopin, N. Mingo, K. Lofgreen, S. Volz, F. Cleri and P. Keblinski, Phys. Rev. Lett., 2009, 102 CrossRef CAS PubMed , 105901.
- M. S. Mauter and M. Elimelech, Environ. Sci. Technol., 2008, 42, 5843–5859 CrossRef CAS PubMed.
- X. M. Ren, C. L. Chen, M. Nagatsu and X. K. Wang, Chem. Eng. J., 2011, 170, 395–410 CrossRef CAS.
- S. C. Smith and D. F. Rodrigues, Carbon, 2015, 91, 122–143 CrossRef CAS.
- C. W. Tan, K. H. Tan, Y. T. Ong, A. R. Mohamed, S. H. S. Zein and S. H. Tan, Environ. Chem. Lett., 2012, 10, 265–273 CrossRef CAS.
- V. K. K. Upadhyayula, S. G. Deng, M. C. Mitchell and G. B. Smith, Sci. Total Environ., 2009, 408, 1–13 CrossRef CAS PubMed.
- Q. Zhang, J. Q. Huang, W. Z. Qian, Y. Y. Zhang and F. Wei, Small, 2013, 9, 1237–1265 CrossRef CAS PubMed.
- Q. Zhang, J. Q. Huang, M. Q. Zhao, W. Z. Qian and F. Wei, ChemSusChem, 2011, 4, 864–889 CrossRef CAS PubMed.
- Y. Hu, L. X. Kang, Q. C. Zhao, H. Zhong, S. C. Zhang, L. W. Yang, Z. Q. Wang, J. J. Lin, Q. W. Li, Z. Y. Zhang, L. M. Peng, Z. F. Liu and J. Zhang, Nat. Commun., 2015, 6 Search PubMed , 6099.
- B. L. Liu, C. Wang, J. Liu, Y. C. Che and C. W. Zhou, Nanoscale, 2013, 5, 9483–9502 RSC.
- I. Ibrahim, T. Gemming, W. M. Weber, T. Mikolajick, Z. F. Liu and M. H. Rummeli, ACS Nano, 2016, 10, 7248–7266 CrossRef CAS PubMed.
- C. Liu and H. M. Cheng, J. Am. Chem. Soc., 2016, 138, 6690–6698 CrossRef CAS PubMed.
- F. Yang, X. Wang, M. H. Li, X. Y. Liu, X. L. Zhao, D. Q. Zhang, Y. Zhang, J. Yang and Y. Li, Acc. Chem. Res., 2016, 49, 606–615 CrossRef CAS PubMed.
- B. L. Liu, F. Q. Wu, H. Gui, M. Zheng and C. W. Zhou, ACS Nano, 2017, 11, 31–53 CrossRef CAS PubMed.
- R. F. Zhang, Y. Y. Zhang and F. Wei, Chem. Soc. Rev., 2017, 46, 3661–3715 RSC.
- R. F. Zhang, Y. Y. Zhang and F. Wei, Acc. Chem. Res., 2017, 50, 179–189 CrossRef CAS PubMed.
- J. K. Holt, H. G. Park, Y. M. Wang, M. Stadermann, A. B. Artyukhin, C. P. Grigoropoulos, A. Noy and O. Bakajin, Science, 2006, 312, 1034–1037 CrossRef CAS PubMed.
- D. N. Futaba, K. Hata, T. Yamada, T. Hiraoka, Y. Hayamizu, Y. Kakudate, O. Tanaike, H. Hatori, M. Yumura and S. Iijima, Nat. Mater., 2006, 5, 987–994 CrossRef CAS PubMed.
- W. Lu, L. T. Qu, K. Henry and L. M. Dai, J. Power Sources, 2009, 189, 1270–1277 CrossRef CAS.
- S. Esconjauregui, M. Fouquet, B. C. Bayer, C. Ducati, R. Smajda, S. Hofmann and J. Robertson, ACS Nano, 2010, 4, 7431–7436 CrossRef CAS PubMed.
- N. Perea-Lopez, B. Rebollo-Plata, J. A. Briones-Leon, A. Morelos-Gomez, D. Hernandez-Cruz, G. A. Hirata, V. Meunier, A. R. Botello-Mendez, J. C. Charlier, B. Maruyama, E. Munoz-Sandoval, F. Lopez-Urias, M. Terrones and H. Terrones, ACS Nano, 2011, 5, 5072–5077 CrossRef CAS PubMed.
- L. T. Qu, L. M. Dai, M. Stone, Z. H. Xia and Z. L. Wang, Science, 2008, 322, 238–242 CrossRef CAS PubMed.
- B. L. Wardle, D. S. Saito, E. J. Garcia, A. J. Hart, R. G. de Villoria and E. A. Verploegen, Adv. Mater., 2008, 20, 2707–2714 CrossRef CAS PubMed.
- A. Brieland-Shoultz, S. Tawfick, S. J. Park, M. Bedewy, M. R. Maschmann, J. W. Baur and A. J. Hart, Adv. Funct. Mater., 2014, 24, 5728–5735 CrossRef CAS.
- B. J. Hinds, N. Chopra, T. Rantell, R. Andrews, V. Gavalas and L. G. Bachas, Science, 2004, 303, 62–65 CrossRef CAS PubMed.
- N. Bui, E. R. Meshot, S. Kim, J. Pena, P. W. Gibson, K. J. Wu and F. Fornasiero, Adv. Mater., 2016, 28, 5871–5877 CrossRef CAS PubMed.
- K. L. Jiang, J. P. Wang, Q. Q. Li, L. A. Liu, C. H. Liu and S. S. Fan, Adv. Mater., 2011, 23, 1154–1161 CrossRef CAS PubMed.
- K. Mizuno, J. Ishii, H. Kishida, Y. Hayamizu, S. Yasuda, D. N. Futaba, M. Yumura and K. Hata, Proc. Natl. Acad. Sci. U. S. A., 2009, 106, 6044–6047 CrossRef CAS PubMed.
- S. Kim, H. Sojoudi, H. Zhao, D. Mariappan, G. H. McKinley, K. K. Gleason and A. J. Hart, Sci. Adv., 2016, 2 CAS , e1601660.
- A. Sharma, V. Singh, T. L. Bougher and B. A. Cola, Nat. Nanotechnol., 2015, 10, 1027–1032 CrossRef CAS PubMed.
- W. Choi, S. Hong, J. T. Abrahamson, J. H. Han, C. Song, N. Nair, S. Baik and M. S. Strano, Nat. Mater., 2010, 9, 423–429 CrossRef CAS PubMed.
- Y. T. Yeh, Y. Tang, A. Sebastian, A. Dasgupta, N. Perea-Lopez, I. Albert, H. G. Lu, M. Terrones and S. Y. Zheng, Sci. Adv., 2016, 2 CAS , e1601026.
- H. X. Chang and H. K. Wu, Energy Environ. Sci., 2013, 6, 3483–3507 RSC.
- K. C. Kemp, H. Seema, M. Saleh, N. H. Le, K. Mahesh, V. Chandra and K. S. Kim, Nanoscale, 2013, 5, 3149–3171 RSC.
- S. Nardecchia, D. Carriazo, M. L. Ferrer, M. C. Gutierrez and F. del Monte, Chem. Soc. Rev., 2013, 42, 794–830 RSC.
- F. Perreault, A. F. de Faria and M. Elimelech, Chem. Soc. Rev., 2015, 44, 5861–5896 RSC.
- Y. Shen, Q. L. Fang and B. L. Chen, Environ. Sci. Technol., 2015, 49, 67–84 CrossRef CAS PubMed.
- Z. Y. Wang and B. X. Mi, Environ. Sci. Technol., 2017, 51, 8229–8244 CrossRef CAS PubMed.
- Q. B. Yun, Q. P. Lu, X. Zhang, C. L. Tan and H. Zhang, Angew. Chem., Int. Ed., 2018, 57, 626–646 CrossRef CAS PubMed.
- H. Zhang, J. Nai, L. Yu and X. W. Lou, Joule, 2017, 1, 77–107 CrossRef CAS.
- L. M. Gilbertson, J. B. Zimmerman, D. L. Plata, J. E. Hutchison and P. T. Anastas, Chem. Soc. Rev., 2015, 44, 5758–5777 RSC.
- M. L. Healy, L. J. Dahlben and J. A. Isaacs, J. Ind. Ecol., 2008, 12, 376–393 CrossRef CAS.
- D. Kushnir and B. A. Sanden, J. Ind. Ecol., 2008, 12, 360–375 CrossRef CAS.
- O. G. Griffiths, J. P. O'Byrne, L. Torrente-Murciano, M. D. Jones, D. Mattia and M. C. McManus, J. Cleaner Prod., 2013, 42, 180–189 CrossRef CAS.
- B. Mossman, W. Light and E. Wei, Annu. Rev. Pharmacol., 1983, 23, 595–615 CrossRef CAS PubMed.
- L. N. Vandenberg, R. Hauser, M. Marcus, N. Olea and W. V. Welshons, Reprod. Toxicol., 2007, 24, 139–177 CrossRef CAS PubMed.
- P. J. Squillace, J. S. Zogorski, W. G. Wilber and C. V. Price, Environ. Sci. Technol., 1996, 30, 1721–1730 CrossRef CAS.
- D. L. Plata, A. J. Hart, C. M. Reddy and P. M. Gschwend, Environ. Sci. Technol., 2009, 43, 8367–8373 CrossRef CAS PubMed.
- M. J. Eckelman, M. S. Mauter, J. A. Isaacs and M. Elimelech, Environ. Sci. Technol., 2012, 46, 2902–2910 CrossRef CAS PubMed.
- D. L. Plata, E. R. Meshot, C. M. Reddy, A. J. Hart and P. M. Gschwend, ACS Nano, 2010, 4, 7185–7192 CrossRef CAS PubMed.
- D. Y. Kim, H. Sugime, K. Hasegawa, T. Osawa and S. Noda, Carbon, 2011, 49, 1972–1979 CrossRef CAS.
- C. F. Wu, M. A. Nahil, N. Miskolczi, J. Huang and P. T. Williams, Environ. Sci. Technol., 2014, 48, 819–826 CrossRef CAS PubMed.
- A. F. Trompeta, M. A. Koklioti, D. K. Perivoliotis, I. Lynch and C. A. Charitidis, J. Cleaner Prod., 2016, 129, 384–394 CrossRef CAS.
- P. Zhai, J. A. Isaacs and M. J. Eckelman, Appl. Energy, 2016, 173, 624–634 CrossRef CAS.
- S. Licht, A. Douglas, J. W. Ren, R. Carter, M. Lefler and C. L. Pint, ACS Cent. Sci., 2016, 2, 162–168 CrossRef CAS PubMed.
- H. Almkhelfe, J. Carpena-Nunez, T. C. Back and P. B. Amama, Nanoscale, 2016, 8, 13476–13487 RSC.
- I. A. Martorell, W. D. Partlow, R. M. Young, J. J. Schreurs and H. E. Saunders, Diamond Relat. Mater., 1999, 8, 29–36 CrossRef CAS.
- M. J. Bronikowski, P. A. Willis, D. T. Colbert, K. A. Smith and R. E. Smalley, J. Vac. Sci. Technol., A, 2001, 19, 1800–1805 CrossRef CAS.
- A. E. Agboola, R. W. Pike, T. A. Hertwig and H. H. Lou, Clean Technol. Environ., 2007, 9, 289–311 CrossRef CAS.
- S. S. Meysami, L. C. Snoek and N. Grobert, Anal. Chem., 2014, 86, 8850–8856 CrossRef CAS PubMed.
- M. Cantoro, S. Hofmann, S. Pisana, V. Scardaci, A. Parvez, C. Ducati, A. C. Ferrari, A. M. Blackburn, K. Y. Wang and J. Robertson, Nano Lett., 2006, 6, 1107–1112 CrossRef CAS PubMed.
- S. Hofmann, C. Ducati, J. Robertson and B. Kleinsorge, Appl. Phys. Lett., 2003, 83, 135–137 CrossRef CAS.
- G. D. Nessim, M. Seita, K. P. O'Brien, A. J. Hart, R. K. Bonaparte, R. R. Mitchell and C. V. Thompson, Nano Lett., 2009, 9, 3398–3405 CrossRef CAS PubMed.
- A. Magrez, J. W. Seo, R. Smajda, B. Korbely, J. C. Andresen, M. Mionic, S. Casimirius and L. Forro, ACS Nano, 2010, 4, 3702–3708 CrossRef CAS PubMed.
- S. Yasuda, D. N. Futaba, T. Yamada, J. Satou, A. Shibuya, H. Takai, K. Arakawa, M. Yumura and K. Hata, ACS Nano, 2009, 3, 4164–4170 CrossRef CAS PubMed.
- R. G. de Villoria, A. J. Hart and B. L. Wardle, ACS Nano, 2011, 5, 4850–4857 CrossRef PubMed.
- K. Hata, D. N. Futaba, K. Mizuno, T. Namai, M. Yumura and S. Iijima, Science, 2004, 306, 1362–1364 CrossRef CAS PubMed.
- D. N. Futaba, K. Hata, T. Yamada, K. Mizuno, M. Yumura and S. Iijima, Phys. Rev. Lett., 2005, 95 CrossRef CAS PubMed , 056104.
- M. Bystrzejewski, R. Schonfelder, G. Cuniberti, H. Lange, A. Huczko, T. Gemming, T. Pichler, B. Buchner and M. Rummeli, Chem. Mater., 2008, 20, 6586–6588 CrossRef CAS.
- C. L. Pint, S. T. Pheasant, A. N. G. Parra-Vasquez, C. Horton, Y. Q. Xu and R. H. Hauge, J. Phys. Chem. C, 2009, 113, 4125–4133 CrossRef CAS.
- K. Hasegawa and S. Noda, ACS Nano, 2011, 5, 975–984 CrossRef CAS PubMed.
- R. M. Wyss, J. E. Klare, H. G. Park, A. Noy, O. Bakajin and V. Lulevich, ACS Appl. Mater. Interfaces, 2014, 6, 21019–21025 CrossRef CAS PubMed.
- G. Y. Zhang, D. Mann, L. Zhang, A. Javey, Y. M. Li, E. Yenilmez, Q. Wang, J. P. McVittie, Y. Nishi, J. Gibbons and H. J. Dai, Proc. Natl. Acad. Sci. U. S. A., 2005, 102, 16141–16145 CrossRef CAS PubMed.
- G. D. Nessim, A. Al-Obeidi, H. Grisaru, E. S. Polsen, C. R. Oliver, T. Zimrin, A. J. Hart, D. Aurbach and C. V. Thompson, Carbon, 2012, 50, 4002–4009 CrossRef CAS.
- Z. J. Ruan, W. H. Rong, Q. Q. Li and Z. Li, Carbon, 2015, 87, 338–346 CrossRef CAS.
- W. B. Shi, J. J. Li, E. S. Polsen, C. R. Oliver, Y. K. Zhao, E. R. Meshot, M. Barclay, D. H. Fairbrother, A. J. Hart and D. L. Plata, Nanoscale, 2017, 9, 5222–5233 RSC.
- I. V. Anoshkin, A. G. Nasibulin, Y. Tian, B. Liu, H. Jiang and E. I. Kauppinen, Carbon, 2014, 78, 130–136 CrossRef CAS.
- R. Xiang, E. Einarsson, J. Okawa, Y. Miyauchi and S. Maruyama, J. Phys. Chem. C, 2009, 113, 7511–7515 CrossRef CAS.
- Y. Y. Zhang, J. M. Gregoire, R. B. van Dover and A. J. Hart, J. Phys. Chem. C, 2010, 114, 6389–6395 CrossRef CAS.
- Q. Wen, W. Z. Qian, F. Wei, Y. Liu, G. Q. Ning and Q. Zhang, Chem. Mater., 2007, 19, 1226–1230 CrossRef CAS.
- Z. R. Li, Y. Xu, X. D. Ma, E. Dervishi, V. Saini, A. R. Biris, D. Lupu and A. S. Biris, Chem. Commun., 2008, 3260–3262, 10.1039/b803465f.
- D. N. Futaba, J. Goto, S. Yasuda, T. Yamada, M. Yumura and K. Hata, Adv. Mater., 2009, 21, 4811–4815 CrossRef CAS PubMed.
- A. Douglas, R. Carter, N. Muralidharan, L. Oakes and C. L. Pint, Carbon, 2017, 116, 572–578 CrossRef CAS.
- H. Almkhelfe, X. Li, R. Rao and P. B. Amama, Carbon, 2017, 116, 181–190 CrossRef CAS.
- Z. Spitalsky, D. Tasis, K. Papagelis and C. Galiotis, Prog. Polym. Sci., 2010, 35, 357–401 CrossRef CAS.
- D. Eder, Chem. Rev., 2010, 110, 1348–1385 CrossRef CAS PubMed.
- J. C. Li, P. X. Hou and C. Liu, Small, 2017, 13 Search PubMed , 1702002.
- M. De Volder, S. H. Tawfick, S. J. Park, D. Copic, Z. Z. Zhao, W. Lu and A. J. Hart, Adv. Mater., 2010, 22, 4384–4389 CrossRef CAS PubMed.
- S. Kim, F. Fornasiero, H. G. Park, J. Bin In, E. Meshot, G. Giraldo, M. Stadermann, M. Fireman, J. Shan, C. P. Grigoropoulos and O. Bakajin, J. Membr. Sci., 2014, 460, 91–98 CrossRef CAS.
- W. L. Mi, Y. S. Lin and Y. D. Li, J. Membr. Sci., 2007, 304, 1–7 CrossRef CAS.
- F. Du, L. T. Qu, Z. H. Xia, L. F. Feng and L. M. Dai, Langmuir, 2011, 27, 8437–8443 CrossRef CAS PubMed.
- B. Lee, Y. Baek, M. Lee, D. H. Jeong, H. H. Lee, J. Yoon and Y. H. Kim, Nat. Commun., 2015, 6 CAS , 7109.
- M. E. Alf, A. Asatekin, M. C. Barr, S. H. Baxamusa, H. Chelawat, G. Ozaydin-Ince, C. D. Petruczok, R. Sreenivasan, W. E. Tenhaeff, N. J. Trujillo, S. Vaddiraju, J. J. Xu and K. K. Gleason, Adv. Mater., 2010, 22, 1993–2027 CrossRef CAS PubMed.
- K. K. S. Lau, J. Bico, K. B. K. Teo, M. Chhowalla, G. A. J. Amaratunga, W. I. Milne, G. H. McKinley and K. K. Gleason, Nano Lett., 2003, 3, 1701–1705 CrossRef CAS.
- H. Zhang, G. P. Cao, Z. Y. Wang, Y. S. Yang, Z. J. Shi and Z. N. Gu, Nano Lett., 2008, 8, 2664–2668 CrossRef CAS PubMed.
- Z. Yang, X. M. Zhou, Z. P. Jin, Z. Liu, H. G. Nie, X. A. Chen and S. M. Huang, Adv. Mater., 2014, 26, 3156–3161 CrossRef CAS PubMed.
- J. Y. Cheng, B. Zhao, W. K. Zhang, F. Shi, G. P. Zheng, D. Q. Zhang and J. H. Yang, Adv. Funct. Mater., 2015, 25, 7381–7391 CrossRef CAS.
- W. K. Zhang, B. Zhao, Y. L. Yin, T. Yin, J. Y. Cheng, K. Zhan, Y. Yan, J. H. Yang and J. Q. Li, J. Mater. Chem. A, 2016, 4, 19026–19036 RSC.
- H. B. Zhao, C. Jacob, H. A. Stone and A. J. Hart, Langmuir, 2016, 32, 12686–12692 CrossRef CAS PubMed.
- L. Acauan, A. C. Dias, M. B. Pereira, F. Horowitz and C. P. Bergmann, ACS Appl. Mater. Interfaces, 2016, 8, 16444–16450 CrossRef CAS PubMed.
- S. M. George, Chem. Rev., 2010, 110, 111–131 CrossRef CAS PubMed.
- F. Du, D. S. Yu, L. M. Dai, S. Ganguli, V. Varshney and A. K. Roy, Chem. Mater., 2011, 23, 4810–4816 CrossRef CAS.
- R. V. Salvatierra, D. Zakhidov, J. W. Sha, N. D. Kim, S. K. Lee, A. R. O. Raji, N. Q. Zhao and J. M. Tour, ACS Nano, 2017, 11, 2724–2733 CrossRef CAS PubMed.
- C. G. Hu and L. M. Dai, Angew. Chem., Int. Ed., 2016, 55, 11736–11758 CrossRef CAS PubMed.
- X. Liu and L. M. Dai, Nat. Rev. Mater., 2016, 1 Search PubMed , 16064.
- K. P. Gong, F. Du, Z. H. Xia, M. Durstock and L. M. Dai, Science, 2009, 323, 760–764 CrossRef CAS PubMed.
- W. Xiong, F. Du, Y. Liu, A. Perez, M. Supp, T. S. Ramakrishnan, L. M. Dai and L. Jiang, J. Am. Chem. Soc., 2010, 132, 15839–15841 CrossRef CAS PubMed.
- P. P. Sharma, J. J. Wu, R. M. Yadav, M. J. Liu, C. J. Wright, C. S. Tiwary, B. I. Yakobson, J. Lou, P. M. Ajayan and X. D. Zhou, Angew. Chem., Int. Ed., 2015, 54, 13701–13705 CrossRef CAS PubMed.
- X. Q. Wang, J. S. Lee, Q. Zhu, J. Liu, Y. Wang and S. Dai, Chem. Mater., 2010, 22, 2178–2180 CrossRef CAS.
- Y. Liu, Y. T. Shen, L. T. Sun, J. C. Li, C. Liu, W. C. Ren, F. Li, L. B. Gao, J. Chen, F. C. Liu, Y. Y. Sun, N. J. Tang, H. M. Cheng and Y. W. Du, Nat. Commun., 2016, 7 Search PubMed , 10921.
- D. S. Yu, Q. Zhang and L. M. Dai, J. Am. Chem. Soc., 2010, 132, 15127–15129 CrossRef CAS PubMed.
- Y. Wang, Y. Y. Shao, D. W. Matson, J. H. Li and Y. H. Lin, ACS Nano, 2010, 4, 1790–1798 CrossRef CAS PubMed.
- H. M. Jeong, J. W. Lee, W. H. Shin, Y. J. Choi, H. J. Shin, J. K. Kang and J. W. Choi, Nano Lett., 2011, 11, 2472–2477 CrossRef CAS PubMed.
- G. Singh, D. S. Sutar, V. D. Botcha, P. K. Narayanam, S. S. Talwar, R. S. Srinivasa and S. S. Major, Nanotechnology, 2013, 24 Search PubMed , 355704.
- K. R. Zodrow, Q. L. Li, R. M. Buono, W. Chen, G. Daigger, L. Duenas-Osorio, M. Elimelech, X. Huang, G. B. Jiang, J. H. Kim, B. E. Logan, D. L. Sedlak, P. Westerhoff and P. J. J. Alvarez, Environ. Sci. Technol., 2017, 51, 10274–10281 CrossRef CAS PubMed.
- S. Agnihotri, J. P. B. Mota, M. Rostam-Abadi and M. J. Rood, J. Phys. Chem. B, 2006, 110, 7640–7647 CrossRef CAS PubMed.
- B. Pan and B. S. Xing, Environ. Sci. Technol., 2008, 42, 9005–9013 CrossRef CAS PubMed.
- D. Zilli, P. R. Bonelli and A. L. Cukierman, Nanotechnology, 2006, 17, 5136–5141 CrossRef.
- R. Q. Long and R. T. Yang, Ind. Eng. Chem. Res., 2001, 40, 4288–4291 CrossRef CAS.
- F. Sun, J. H. Gao, Y. W. Zhu, G. Q. Chen, S. H. Wu and Y. K. Qin, Adsorption, 2013, 19, 959–966 CrossRef CAS.
- S. Agnihotri, M. J. Rood and M. Rostam-Abadi, Carbon, 2005, 43, 2379–2388 CrossRef CAS.
- R. Q. Long and R. T. Yang, J. Am. Chem. Soc., 2001, 123, 2058–2059 CrossRef CAS PubMed.
- P. Kondratyuk, Y. Wang, J. K. Johnson and J. T. Yates, J. Phys. Chem. B, 2005, 109, 20999–21005 CrossRef CAS PubMed.
- F. S. Su, C. S. Lu, W. F. Cnen, H. L. Bai and J. F. Hwang, Sci. Total Environ., 2009, 407, 3017–3023 CrossRef CAS PubMed.
- A. E. Creamer and B. Gao, Environ. Sci. Technol., 2016, 50, 7276–7289 CrossRef CAS PubMed.
- M. Cinke, J. Li, C. W. Bauschlicher, A. Ricca and M. Meyyappan, Chem. Phys. Lett., 2003, 376, 761–766 CrossRef CAS.
- D. J. Babu, M. Lange, G. Cherkashinin, A. Issanin, R. Staudt and J. J. Schneider, Carbon, 2013, 61, 616–623 CrossRef CAS.
- D. P. Cao, X. R. Zhang, J. F. Chen, W. C. Wang and J. Yun, J. Phys. Chem. B, 2003, 107, 13286–13292 CrossRef CAS.
- W. J. Wang, X. Peng and D. P. Cao, Environ. Sci. Technol., 2011, 45, 4832–4838 CrossRef CAS PubMed.
- M. Rahimi, J. K. Singh, D. J. Babu, J. J. Schneider and F. Muller-Plathe, J. Phys. Chem. C, 2013, 117, 13492–13501 CrossRef CAS.
- M. Rahimi, D. J. Babu, J. K. Singh, Y. B. Yang, J. J. Schneider and F. Muller-Plathe, J. Chem. Phys., 2015, 143 Search PubMed , 124701.
- M. Rahimi, J. K. Singh and F. Muller-Plathe, Phys. Chem. Chem. Phys., 2016, 18, 4112–4120 RSC.
- Y. B. Yang, M. Rahimi, J. K. Singh, M. C. Bohm and F. Muller-Plathe, J. Phys. Chem. C, 2016, 120, 7510–7521 CrossRef CAS.
- A. C. Dillon, K. M. Jones, T. A. Bekkedahl, C. H. Kiang, D. S. Bethune and M. J. Heben, Nature, 1997, 386, 377–379 CrossRef CAS.
- C. Liu, Y. Y. Fan, M. Liu, H. T. Cong, H. M. Cheng and M. S. Dresselhaus, Science, 1999, 286, 1127–1129 CrossRef CAS PubMed.
- A. Y. Cao, H. W. Zhu, X. F. Zhang, X. S. Li, D. B. Ruan, C. L. Xu, B. Q. Wei, J. Liang and D. H. Wu, Chem. Phys. Lett., 2001, 342, 510–514 CrossRef CAS.
- C. Liu, Y. Chen, C. Z. Wu, S. T. Xu and H. M. Cheng, Carbon, 2010, 48, 452–455 CrossRef CAS.
- X. C. Gui, J. Q. Wei, K. L. Wang, A. Y. Cao, H. W. Zhu, Y. Jia, Q. K. Shu and D. H. Wu, Adv. Mater., 2010, 22, 617–621 CrossRef CAS PubMed.
- D. P. Hashim, N. T. Narayanan, J. M. Romo-Herrera, D. A. Cullen, M. G. Hahm, P. Lezzi, J. R. Suttle, D. Kelkhoff, E. Munoz-Sandoval, S. Ganguli, A. K. Roy, D. J. Smith, R. Vajtai, B. G. Sumpter, V. Meunier, H. Terrones, M. Terrones and P. M. Ajayan, Sci. Rep., 2012, 2 CAS , 363.
- W. Chen, L. Duan and D. Q. Zhu, Environ. Sci. Technol., 2007, 41, 8295–8300 CrossRef CAS PubMed.
- K. Yang, W. Wu, Q. Jing and L. Zhu, Environ. Sci. Technol., 2008, 42, 7931–7936 CrossRef CAS PubMed.
- S. Gotovac, H. Honda, Y. Hattori, K. Takahashi, H. Kanoh and K. Kaneko, Nano Lett., 2007, 7, 583–587 CrossRef CAS PubMed.
- X. L. Wang, S. Tao and B. S. Xing, Environ. Sci. Technol., 2009, 43, 6214–6219 CrossRef CAS PubMed.
- H. B. Li, X. C. Gui, L. H. Zhang, S. S. Wang, C. Y. Ji, J. Q. Wei, K. L. Wang, H. W. Zhu, D. H. Wu and A. Y. Cao, Chem. Commun., 2010, 46, 7966–7968 RSC.
- F. S. Su and C. S. Lu, J. Environ. Sci. Health, Part A: Toxic/Hazard. Subst. Environ. Eng., 2007, 42, 1543–1552 CrossRef CAS PubMed.
- X. J. Zhou, X. D. Li, S. X. Xu, X. Y. Zhao, M. J. Ni and K. F. Cen, Environ. Sci. Pollut. Res., 2015, 22, 10463–10470 CrossRef CAS PubMed.
- D. Desai, E. S. Beh, S. Sahu, V. Vedharathinam, Q. van Overmeere, C. F. de Lannoy, A. P. Jose, A. R. Völkel and J. B. Rivest, ACS Energy Lett., 2017, 375–379, DOI:10.1021/acsenergylett.7b01220.
- B. Shapira, I. Cohen, T. R. Penki, E. Avraham and D. Aurbach, J. Power Sources, 2018, 378, 146–152 CrossRef CAS.
- Y. H. Li, S. G. Wang, J. Q. Wei, X. F. Zhang, C. L. Xu, Z. K. Luan, D. H. Wu and B. Q. Wei, Chem. Phys. Lett., 2002, 357, 263–266 CrossRef CAS.
- Y. H. Li, S. G. Wang, Z. K. Luan, J. Ding, C. L. Xu and D. H. Wu, Carbon, 2003, 41, 1057–1062 CrossRef CAS.
- Y. H. Li, Z. C. Di, J. Ding, D. H. Wu, Z. K. Luan and Y. Q. Zhu, Water Res., 2005, 39, 605–609 CrossRef CAS PubMed.
- G. P. Rao, C. Lu and F. Su, Sep. Purif. Technol., 2007, 58, 224–231 CrossRef CAS.
- Z. M. Gao, T. J. Bandosz, Z. B. Zhao, M. Han and J. S. Qiu, J. Hazard. Mater., 2009, 167, 357–365 CrossRef CAS PubMed.
- X. Y. Yu, T. Luo, Y. X. Zhang, Y. Jia, B. J. Zhu, X. C. Fu, J. H. Liu and X. J. Huang, ACS Appl. Mater. Interfaces, 2011, 3, 2585–2593 CrossRef CAS PubMed.
- Y. Zhou, M. Ghaffari, M. Lin, E. M. Parsons, Y. Liu, B. L. Wardle and Q. M. Zhang, Electrochim. Acta, 2013, 111, 608–613 CrossRef CAS.
- J. Chen, Y. Liu, A. I. Minett, C. Lynam, J. Z. Wang and G. G. Wallace, Chem. Mater., 2007, 19, 3595–3597 CrossRef CAS.
- A. L. M. Reddy, M. M. Shaijumon, S. R. Gowda and P. M. Ajayan, Nano Lett., 2009, 9, 1002–1006 CrossRef CAS PubMed.
- E. Frackowiak and F. Beguin, Carbon, 2002, 40, 1775–1787 CrossRef CAS.
- J. W. Liu, J. Essner and J. Li, Chem. Mater., 2010, 22, 5022–5030 CrossRef CAS.
- X. W. Cui, F. P. Hu, W. F. Wei and W. X. Chen, Carbon, 2011, 49, 1225–1234 CrossRef CAS.
- Y. Q. Jiang, P. B. Wang, X. N. Zang, Y. Yang, A. Kozinda and L. W. Lin, Nano Lett., 2013, 13, 3524–3530 CrossRef CAS PubMed.
- C. Y. Jung, T. S. Zhao, L. Zeng and P. Tan, J. Power Sources, 2016, 331, 82–90 CrossRef CAS.
- Y. B. Yan, J. W. Miao, Z. H. Yang, F. X. Xiao, H. B. Yang, B. Liu and Y. H. Yang, Chem. Soc. Rev., 2015, 44, 3295–3346 RSC.
- G. Wu, A. Santandreu, W. Kellogg, S. Gupta, O. Ogoke, H. G. Zhang, H. L. Wang and L. M. Dai, Nano Energy, 2016, 29, 83–110 CrossRef CAS.
- O. Akhavan, M. Abdolahad, Y. Abdi and S. Mohajerzadeh, Carbon, 2009, 47, 3280–3287 CrossRef CAS.
- Y. D. Yang, L. T. Qu, L. M. Dai, T. S. Kang and M. Durstock, Adv. Mater., 2007, 19, 1239–1243 CrossRef CAS.
- H. Li, X. Gui, C. Ji, P. Li, Z. Li, L. Zhang, E. Shi, K. Zhu, J. Wei, K. Wang, H. Zhu, D. Wu and A. Cao, Nano Res., 2012, 5, 265–271 CrossRef CAS.
- W. J. Lee, J. M. Lee, S. T. Kochuveedu, T. H. Han, H. Y. Jeong, M. Park, J. M. Yun, J. Kwon, K. No, D. H. Kim and S. O. Kim, ACS Nano, 2012, 6, 935–943 CrossRef CAS PubMed.
- H. A. Park, S. Y. Liu, Y. Oh, P. A. Salvador, G. S. Rohrer and M. F. Islam, ACS Nano, 2017, 11, 2150–2159 CrossRef CAS PubMed.
- J. E. Mink, J. P. Rojas, B. E. Logan and M. M. Hussain, Nano Lett., 2012, 12, 791–795 CrossRef CAS PubMed.
- L. Xiang, P. Yu, M. N. Zhang, J. Hao, Y. X. Wang, L. Zhu, L. M. Dai and L. Q. Mao, Anal. Chem., 2014, 86, 5017–5023 CrossRef CAS PubMed.
- S. Y. Wang, E. Iyyamperumal, A. Roy, Y. H. Xue, D. S. Yu and L. M. Dai, Angew. Chem., Int. Ed., 2011, 50, 11756–11760 CrossRef CAS PubMed.
- D. J. Li, U. N. Maiti, J. Lim, D. S. Choi, W. J. Lee, Y. Oh, G. Y. Lee and S. O. Kim, Nano Lett., 2014, 14, 1228–1233 CrossRef CAS PubMed.
- X. Su, J. Wu and B. J. Hinds, Carbon, 2011, 49, 1145–1150 CrossRef CAS PubMed.
- D. P. Li and J. H. Qu, J. Environ. Sci., 2009, 21, 713–719 CrossRef CAS.
- T. Tsubota, A. Ono, N. Murakami and T. Ohno, Appl. Catal., B, 2009, 91, 533–538 CrossRef CAS.
- Z. Q. Liu, J. Ma, Y. H. Cui, L. Zhao and B. P. Zhang, Appl. Catal., B, 2010, 101, 74–80 CrossRef CAS.
- O. Akhavan, M. Abdolahad, Y. Abdi and S. Mohajerzadeh, J. Mater. Chem., 2011, 21, 387–393 RSC.
- G. Centi, P. Ciambelli, S. Perathoner and P. Russo, Catal. Today, 2002, 75, 3–15 CrossRef CAS.
- L. S. Wang, B. C. Huang, Y. X. Su, G. Y. Zhou, K. L. Wang, H. C. Luo and D. Q. Ye, Chem. Eng. J., 2012, 192, 232–241 CrossRef CAS.
- H. J. Joung, J. H. Kim, J. S. Oh, D. W. You, H. O. Park and K. W. Jung, Appl. Surf. Sci., 2014, 290, 267–273 CrossRef CAS.
- C. H. Kuo, W. K. Li, W. Q. Song, Z. Luo, A. S. Poyraz, Y. Guo, A. W. K. Ma, S. L. Suib and J. He, ACS Appl. Mater. Interfaces, 2014, 6, 11311–11317 CrossRef CAS PubMed.
- J. Han, D. S. Zhang, P. Maitarad, L. Y. Shi, S. X. Cai, H. R. Li, L. Huang and J. P. Zhang, Catal. Sci. Technol., 2015, 5, 438–446 RSC.
- Z. P. Qu, L. Miao, H. Wang and Q. Fu, Chem. Commun., 2015, 51, 956–958 RSC.
- B. Zhao, X. W. Liu, Z. J. Zhou, H. Z. Shao and M. H. Xu, Chem. Eng. J., 2016, 284, 1233–1241 CrossRef CAS.
- H. M. Xu, N. Q. Yan, Z. Qu, W. Liu, J. Mei, W. J. Huang and S. J. Zhao, Environ. Sci. Technol., 2017, 51, 8879–8892 CrossRef CAS PubMed.
- C. Fang, D. S. Zhang, S. X. Cai, L. Zhang, L. Huang, H. R. Li, P. Maitarad, L. Y. Shi, R. H. Gao and J. P. Zhang, Nanoscale, 2013, 5, 9199–9207 RSC.
- B. Y. Bai, J. H. Li and J. M. Hao, Appl. Catal., B, 2015, 164, 241–250 CrossRef CAS.
- X. J. Fan, H. Q. Zhou and X. Guo, ACS Nano, 2015, 9, 5125–5134 CrossRef CAS PubMed.
- R. Amade, M. Vila-Costa, S. Hussain, E. O. Casamayor and E. Bertran, J. Mater. Sci., 2015, 50, 1214–1220 CrossRef CAS.
- H. G. Park and Y. Jung, Chem. Soc. Rev., 2014, 43, 565–576 RSC.
- S. R. Guo, E. R. Meshot, T. Kuykendall, S. Cabrini and F. Fornasiero, Adv. Mater., 2015, 27, 5726–5737 CrossRef CAS PubMed.
- H. Y. Yang, Z. J. Han, S. F. Yu, K. L. Pey, K. Ostrikov and R. Karnik, Nat. Commun., 2013, 4 Search PubMed , 2220.
- R. H. Tunuguntla, R. Y. Henley, Y. C. Yao, T. A. Pham, M. Wanunu and A. Noy, Science, 2017, 357, 792–796 CrossRef CAS PubMed.
- R. Das, M. E. Ali, S. B. Abd Hamid, S. Ramakrishna and Z. Z. Chowdhury, Desalination, 2014, 336, 97–109 CrossRef CAS.
- M. N. Nejad, M. Asghari and M. Afsari, ChemBioEng Rev., 2016, 3, 276–298 CrossRef CAS.
- J. Wu, K. S. Paudel, C. Strasinger, D. Hammell, A. L. Stinchcomb and B. J. Hinds, Proc. Natl. Acad. Sci. U. S. A., 2010, 107, 11698–11702 CrossRef CAS PubMed.
- F. Fornasiero, Curr. Opin. Chem. Eng., 2017, 16, 1–8 CrossRef.
- G. Hummer, J. C. Rasaiah and J. P. Noworyta, Nature, 2001, 414, 188–190 CrossRef CAS PubMed.
- B. Corry, Energy Environ. Sci., 2011, 4, 751–759 RSC.
- M. Majumder, N. Chopra and B. J. Hinds, J. Am. Chem. Soc., 2005, 127, 9062–9070 CrossRef CAS PubMed.
- F. Fornasiero, H. G. Park, J. K. Holt, M. Stadermann, C. P. Grigoropoulos, A. Noy and O. Bakajin, Proc. Natl. Acad. Sci. U. S. A., 2008, 105, 17250–17255 CrossRef CAS PubMed.
- M. Majumder, A. Stinchcomb and B. J. Hinds, Life Sci., 2010, 86, 563–568 CrossRef CAS PubMed.
- J. Wu, K. Gerstandt, H. B. Zhang, J. Liu and B. J. Hinds, Nat. Nanotechnol., 2012, 7, 133–139 CrossRef CAS PubMed.
- X. H. Sun, X. Su, J. Wu and B. J. Hinds, Langmuir, 2011, 27, 3150–3156 CrossRef CAS PubMed.
- D. Yoon, C. Lee, J. Yun, W. Jeon, B. J. Cha and S. Baik, ACS Nano, 2012, 6, 5980–5987 CrossRef CAS PubMed.
- H. B. Chen and D. S. Sholl, J. Membr. Sci., 2006, 269, 152–160 CrossRef CAS.
- L. Ge, L. Wang, A. J. Du, M. Hou, V. Rudolph and Z. H. Zhu, RSC Adv., 2012, 2, 5329–5336 RSC.
- S. Ban and C. Huang, J. Membr. Sci., 2012, 417, 113–118 CrossRef.
- G. Arora and S. I. Sandler, J. Chem. Phys., 2005, 123 CrossRef CAS PubMed , 044705.
- K. Gethard, O. Sae-Khow and S. Mitra, ACS Appl. Mater. Interfaces, 2011, 3, 110–114 CrossRef CAS PubMed.
- A. I. Skoulidas, D. M. Ackerman, J. K. Johnson and D. S. Sholl, Phys. Rev. Lett., 2002, 89 CrossRef CAS PubMed , 185901.
- S. Kim, J. R. Jinschek, H. Chen, D. S. Sholl and E. Marand, Nano Lett., 2007, 7, 2806–2811 CrossRef CAS PubMed.
- H. B. Chen and D. S. Sholl, J. Am. Chem. Soc., 2004, 126, 7778–7779 CrossRef CAS PubMed.
- Z. Yin, H. Wang, M. Jian, Y. Li, K. Xia, M. Zhang, C. Wang, Q. Wang, M. Ma, Q.-S. Zheng and Y. Zhang, ACS Appl. Mater. Interfaces, 2017, 9, 28596–28603 CrossRef CAS PubMed.
- J. K. Holt, A. Noy, T. Huser, D. Eaglesham and O. Bakajin, Nano Lett., 2004, 4, 2245–2250 CrossRef CAS.
- M. Majumder, N. Chopra and B. J. Hinds, ACS Nano, 2011, 5, 3867–3877 CrossRef CAS PubMed.
- K. J. Lee and H. D. Park, J. Membr. Sci., 2016, 501, 144–151 CrossRef CAS.
- Y. Baek, C. Kim, D. K. Seo, T. Kim, J. S. Lee, Y. H. Kim, K. H. Ahn, S. S. Bae, S. C. Lee, J. Lim, K. Lee and J. Yoon, J. Membr. Sci., 2014, 460, 171–177 CrossRef CAS.
- M. Yu, H. H. Funke, J. L. Falconer and R. D. Noble, Nano Lett., 2009, 9, 225–229 CrossRef CAS PubMed.
- N. Yang, M. Li, J. Patscheider, S. K. Youn and H. G. Park, Sci. Rep., 2017, 7 Search PubMed , 46725.
- B. Corry, J. Phys. Chem. B, 2008, 112, 1427–1434 CrossRef CAS PubMed.
- H. K. Mutha, Y. Lu, I. Y. Stein, H. J. Cho, M. E. Suss, T. Laoui, C. V. Thompson, B. L. Wardle and E. N. Wang, Nanotechnology, 2017, 28 CrossRef CAS PubMed , 05LT01.
- E. R. Meshot, D. W. Zwissler, N. Bui, T. R. Kuykendall, C. Wang, A. Hexerner, K. J. J. Wu and F. Fornasiero, ACS Nano, 2017, 11, 5405–5416 CrossRef CAS PubMed.
- E. R. Meshot, D. L. Plata, S. Tawfick, Y. Y. Zhang, E. A. Verploegen and A. J. Hart, ACS Nano, 2009, 3, 2477–2486 CrossRef CAS PubMed.
- E. S. Polsen, M. Bedewy and A. J. Hart, Small, 2013, 9, 2564–2575 CrossRef CAS PubMed.
- M. Wang, T. T. Li, Y. G. Yao, H. F. Lu, Q. Li, M. H. Chen and Q. W. Li, J. Am. Chem. Soc., 2014, 136, 18156–18162 CrossRef CAS PubMed.
- H. Sojoudi, S. Kim, H. Zhao, R. K. Annavarapu, D. Mariappan, A. J. Hart, G. H. McKinley and K. K. Gleason, ACS Appl. Mater. Interfaces, 2017, 9, 43287–43299 CrossRef CAS PubMed.
- V. K. K. Upadhyayula, D. E. Meyer, M. A. Curran and M. A. Gonzalez, J. Cleaner Prod., 2012, 26, 37–47 CrossRef CAS.
- L. J. Dahlben, M. J. Eckelman, A. Hakimian, S. Somu and J. A. Isaacs, Environ. Sci. Technol., 2013, 47, 8471–8478 CrossRef CAS PubMed.
- L. M. Gilbertson, A. A. Busnaina, J. A. Isaacs, J. B. Zimmerman and M. J. Eckelman, Environ. Sci. Technol., 2014, 48, 11360–11368 CrossRef CAS PubMed.
|
This journal is © The Royal Society of Chemistry 2018 |
Click here to see how this site uses Cookies. View our privacy policy here.