DOI:
10.1039/C8CC01144C
(Communication)
Chem. Commun., 2018,
54, 4657-4660
Modulating the physical properties of solid forms of urea using co-crystallization technology†
Received
9th February 2018
, Accepted 12th March 2018
First published on 22nd March 2018
Abstract
The solid-form landscape of urea was explored using full interaction maps (FIMs) and data from the CSD to develop optimum protocols for synthesizing co-crystals of urea. As a result, 49 of the 60 attempted reactions produced new co-crystals, and the crystal structures of four of these are presented. Moreover, the goal of reducing the solubility and lowering the hygroscopicity of the parent compound was achieved, which in turn offers new opportunities for application as a slow-release fertilizer with limited hygroscopicity, thereby reducing many current problems of transport, handling, and storage of urea.
Urea holds a unique place in the history of organic chemistry, and almost 200 years after it was first synthesized it remains a hugely important chemical, notably in the agrochemical and polymer industries. Urea has the highest nitrogen content among commonly used solid fertilizers, but its high solubility in water (ca. 110–170 g/100 ml, in the 20–40 °C range)1 and rapid moisture uptake after application make it particularly susceptible to mobility and runoff. As a result, excessive amounts of urea are frequently used to ensure that sufficient quantities are available to plants and crops. This is not cost-effective, and excess nitrogen in the environment can negatively impact air and water quality, biodiversity and human health.2 In addition, the high moisture content of urea at relative humidity of 40–50% causes stickiness, leading to substantial storage and stability issues. To remedy some of these issues, slow-release fertilizer technologies have been developed,3–13 but disadvantages related to manufacturing costs and irregular nutrient release remain. However, a possible alternative may be found through co-crystal technologies,14–18 wherein the crystalline environment of a compound is altered without changing its molecular structure, which in principle makes it possible to “dial-in” desirable physical properties.19 Co-crystals have been used to develop new anticancer,20 antifungal,21 antiviral,22 anticonvulsant,23,24 and antidepressant25 drugs with enhanced aqueous solubility. The same type of technology has also been explored for improving energetic materials26 and for stabilizing volatile chemicals.27 So far, there has been relatively limited interest in applications in the agrochemical industry,28–30 although combinations of inorganic salts and urea have recently been employed to improve nitrogen management.31 The goal of our study is to explore whether co-crystals can provide new solid forms of urea with substantially reduced aqueous solubility and lowered hygroscopicity, which may limit negative environmental impact and ease storage and handling of a chemical that is used globally on a multi-ton scale each year. In addition, we want to establish an effective protocol for a priori identifying the most likely co-formers in order to reduce the number of screens and costly experiments that need to be performed before a suitable candidate is found. The aim of the synthetic strategy is to incorporate co-formers within a series of crystalline solids that are characterized by considerable structural consistency. By controlling the main structural features within a new crystalline material, we hope to alter its properties in a modular manner. This can be accomplished by making appropriate changes to the molecular structure of the co-former whilst leaving most of the molecular recognition events that drive the supramolecular assembly intact. In this study, we present the results from a systemic co-crystallization study comprising 60 experiments between urea and selected co-formers that are relatively inexpensive and readily available. The co-formers were selected using a structural-informatics approach that allowed us to target functionalities capable of forming complementary hydrogen bonds with the recognition sites that urea presents to its surroundings, Scheme 1.
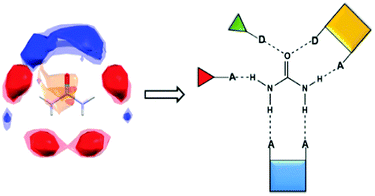 |
| Scheme 1 FIM indicating the four potential avenues for intermolecular ‘intervention’ on urea (A and D = hydrogen-bond acceptor and donor, respectively). | |
The structural landscape occupied by urea was mapped out using full interaction maps (FIMs).32 As expected, a large number of short-contacts were found in close proximity of (i) both lone pairs on the carbonyl oxygen atom and (ii) the four N–H protons, leading to four avenues for targeting co-crystals of urea, Scheme 1.
The FIM provides an overview of short contacts to urea in the solid state, but to add more granularity to the map, an analysis of relevant data from the Cambridge Structural Database (CSD)33–35 was also conducted. The type of interaction that urea tends to engage in can be divided into five different synthons, Scheme 2.
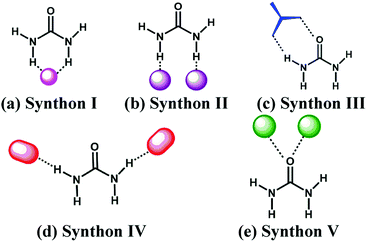 |
| Scheme 2 Five synthons in co-crystals of urea. | |
A hydrogen-bond acceptor can act as an effective co-former by interacting with the two N–H groups of urea via a bifurcated hydrogen-bond (Synthon I)36–39 or via two single-point interactions (Synthon II).12,40 Synthon III has a ditopic donor–acceptor moiety that can form a R22(8) heterosynthon that complements the N–H/O
C pocket.12,41–45 In synthon IV, a suitable hydrogen-bond acceptor forms A⋯H–N interactions which frequently results in infinite 1-D or 2-D architectures.46,47 Finally, in synthon V, one or both lone-pairs of the carbonyl group of urea bind to an appropriate hydrogen-bond donor via single point or two-point interactions.48,49
The FIM of urea, combined with the CSD analysis, guided the choice of sixty co-formers all with an opportunity to drive co-crystal formation via one or more of the synthons identified in the structure-based analysis, Table 1. The screen was performed using solvent-assisted grinding, SAG (with methanol), and the outcome of each attempted experiment was analysed using IR spectroscopy in order to determine if a co-crystal had formed.
Table 1 Urea co-crystal screen
Co-formers |
# of co-formers studied |
SAG success rate |
Synthons expected |
Aliphatic acids |
13 |
13/13 |
Synthon III, V |
Aromatic acids |
14 |
10/14 |
Synthon II, III, V |
Nitro-substituted aromatics |
9 |
8/9 |
Synthon I, III |
Amino acids |
6 |
4/6 |
Synthon III, V |
Nicotinamides |
4 |
2/4 |
Synthon II, III |
N-Oxides |
5 |
5/5 |
Synthon I |
Various |
9 |
7/9 |
Synthon I–V |
Overall |
60 |
49/60 |
|
In 49 of the 60 experiments (82%), the IR analysis showed prominent new features or significant changes to the spectra of one or both reactants, indicating the formation of a co-crystal, Table 1. Four of the co-crystals yielded crystals suitable for single-crystal X-ray diffraction. The crystal structures of urea:tetra-methyl(N-oxide)pyrazine, U:TmPy_NO, and urea:tetra-methyl bis(N,N-oxide)pyrazine, U:TmPy_NNO, both contain Synthon I, a five-membered ring constructed from a bifurcated N–O⋯(H–N)2 interaction, Fig. 1a and b.
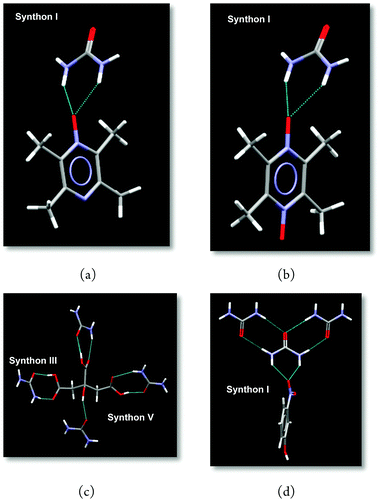 |
| Fig. 1 Synthons in crystal structures of U:TmPy_NO (a), U:TmPy_NNO (b), U2:CA (c), and U:3NP (d), respectively. | |
The crystal structure of urea:citric acid, U2:CA, contains both Synthon III, an R22(8) ring constructed from O–H(acid)⋯C
O(urea) and N–H(urea)⋯C
O(acid) hydrogen bonds, and Synthon V, C
O(urea)⋯H–O(acid), Fig. 1c. Finally, the synthesis of urea:3-nitrophenol, U:3NP, is also driven by Synthon I, based on a bifurcated five-membered ring, Fig. 1d.
Two co-crystals identified in a subsequent solubility screen test were selected for quantitative solubility and qualitative hygroscopicity studies; urea:pimelic acid,50 (U2:PA) and urea:4-nitrophenol51–53 (U:4NP). Large scale syntheses of these were achieved using solvo-thermal methods and the structural homogeneity was established using powder X-ray diffraction (see ESI†). The aqueous solubility of U2:PA and U:4NP was measured using gravimetric methods and compared with that of urea, Fig. 2.
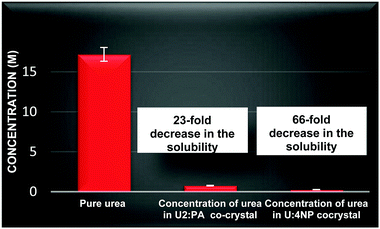 |
| Fig. 2 Aqueous solubility of urea, U2:PA and U:4NP after 1 month. | |
The solubility of urea in water is approx. 17.18 (±0.30) M in the 20–40 °C range.54 The solubility of urea in U2:PA is 0.76 (±0.10) M and in U:4NP it decreased to 0.27 (±0.07) M (as measured after 1 month). This represents a more than 20-fold decrease in the aqueous solubility of urea in U2:PA and a more than 60-fold decrease in U:4NP.
Another major concern with urea is its sensitivity to moisture, therefore we examined if these new solid formulations of urea, U2:PA and U:4NP, are better equipped to tolerate humidity. Our results demonstrate that even though urea becomes a transparent liquid in less than 24 hours at 85% humidity, both U2:PA and U:4NP remain crystalline solids for over one month, Fig. 3.
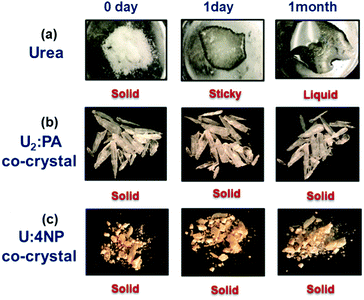 |
| Fig. 3 Response to 85% humidity of (a) urea, (b) U2:PA, and (c) U:4NP. | |
Additional thermal analyses (DSC and TGA) of U2:PA and U:4NP after exposure to 85% humidity for a month found no thermodynamic events prior to their respective melting points in either case (see ESI†), indicating that the two co-crystals are very tolerant to prolonged exposure to highly humid conditions.
In conclusion, FIMs combined with CSD analysis guided the choice of sixty co-formers for co-crystallization, resulting in 49 out of 60 positive results. Furthermore, solubility and hygroscopicity studies of U2:PA and U:4NP indicate that the two co-crystals were able to reduce the solubility of urea by more than 20 times in U2:PA and by more than 60 times in U:4NP, as well as making the new solid forms of urea more tolerant towards excess humidity. These results indicate that considerable changes to solid forms of urea can be readily made by systematic co-crystallization with suitable co-formers identified using a variety of structural-informatic tools. This has allowed us to deliver drastically improved physicochemical properties of urea, such as decreased aqueous solubility and much improved stability with respect to humidity. These changes can, in turn, optimise the performance and benefits of urea as a plant nutrient. Co-crystal technologies can also be used to overcome solubility problems associated with agrochemicals such as herbicides, pesticides and insecticides, and hence, positively impact efficiency and limit many environmental concerns.
We are grateful for invaluable financial support from ICL.
Conflicts of interest
There are no conflicts to declare.
References
- F. M. Lee and L. E. Lahti, J. Chem. Eng. Data, 1972, 17, 304–306 CrossRef CAS.
- K. Goulding, S. Jarvis and A. Whitmore, Philos. Trans. R. Soc., B, 2008, 363, 667–680 CrossRef CAS PubMed.
-
M. Ruark, Advantages and disadvantages of controlled release fertilizers, Department of Soil Science, University of Wisconsin-Madison, WI FFVC, 2012, pp. 1–33 Search PubMed.
- J. Shi, J. Li, W. Zhou and D. Zhang, Front. Forest. China, 2007, 2, 104 CrossRef.
- B. Benzian, S. C. R. Freeman and J. D. D. Mitchell, Plant Soil, 1971, 35, 517–532 CrossRef CAS.
- P. H. Peng, W. R. Ernst, G. L. Bridger and E. M. Hartley, Ind. Eng. Chem. Process Des. Dev., 1979, 18, 453–458 CAS.
- T. R. Shattock, K. K. Arora, P. Vishweshwar and M. J. Zaworotko, Cryst. Growth Des., 2008, 8, 4533–4545 CAS.
-
T. D. Landis and R. K. Dumroese, Using polymer-coated controlled-release fertilizers in the nursery and after outplanting, Forest Nursery Notes, 2009, pp. 5–12 Search PubMed.
- N. Kottegoda, C. Sandaruwan, G. Priyadarshana, A. Siriwardhana, U. A. Rathnayake, D. M. Berugoda Arachchige, A. R. Kumarasinghe, D. Dahanayake, V. Karunaratne and G. A. J. Amaratunga, ACS Nano, 2017, 11, 1214–1221 CrossRef CAS PubMed.
- M. Zaman, S. Saggar, J. D. Blennerhassett and J. Singh, Soil Biol. Biochem., 2009, 41, 1270–1280 CrossRef CAS.
- J.-M. Lehn, Science, 2002, 295, 2400–2403 CrossRef CAS PubMed.
- G. Smith, K. E. Baldry, K. A. Byriel and C. H. L. Kennard, Aust. J. Chem., 1997, 50, 727–736 CrossRef CAS.
-
A. D. Blaylock, J. Kaufmann and R. D. Dowbenko, Nitrogen fertilizer technologies, Proceedings of the Western Nutrient Management Conference, Salt Lake City, Utah, USA, 2005, vol. 6 Search PubMed.
- S. Basavoju, D. Boström and S. P. Velaga, Pharm. Res., 2008, 25, 530–541 CrossRef CAS PubMed.
- D. Braga, E. Dichiarante, G. Palladino, F. Grepioni, M. R. Chierotti, R. Gobetto and L. Pellegrino, CrystEngComm, 2010, 12, 3534–3536 RSC.
- R. Liantonio, P. Metrangolo, T. Pilati, G. Resnati and A. Stevenazzi, Cryst. Growth Des., 2003, 3, 799–803 CAS.
- L. Orola, M. V. Veidis, I. Mutikainen and I. Sarcevica, Cryst. Growth Des., 2011, 11, 4009–4016 CAS.
- B. Olenik, R. Boese and R. Sustmann, Cryst. Growth Des., 2003, 3, 175–181 CAS.
-
C. B. Aakeröy and P. D. Chopade, Supramolecular Chemistry, John Wiley & Sons, Ltd, 2012 DOI:10.1002/9780470661345.smc113.
- Y. N. Zhang, H.-M. Yin, Y. Zhang, D.-J. Zhang, X. Su and H.-X. Kuang, J. Mol. Struct., 2017, 1130, 199–207 CrossRef CAS.
- A. Shevchenko, I. Miroshnyk, L.-O. Pietilä, J. Haarala, J. Salmia, K. Sinervo, S. Mirza, B. van Veen, E. Kolehmainen and J. Yliruusi, Cryst. Growth Des., 2013, 13, 4877–4884 CAS.
- S. Jung, J. Lee and I. W. Kim, J. Cryst. Grow., 2013, 373, 59–63 CrossRef CAS.
- L. S. Reddy, S. J. Bethune, J. W. Kampf and N. Rodríguez-Hornedo, Cryst. Growth Des., 2009, 9, 378–385 CAS.
- N. Takata, K. Shiraki, R. Takano, Y. Hayashi and K. Terada, Cryst. Growth Des., 2008, 8, 3032–3037 CAS.
- A. Sarkar and S. Rohani, J. Pharm. Biomed. Anal., 2015, 110, 93–99 CrossRef CAS PubMed.
- K. B. Landenberger, O. Bolton and A. J. Matzger, J. Am. Chem. Soc., 2015, 137, 5074–5079 CrossRef CAS PubMed.
- C. B. Aakeröy, T. K. Wijethunga, J. Benton and J. Desper, Chem. Commun., 2015, 51, 2425–2428 RSC.
- E. Nauha, E. Kolehmainen and M. Nissinen, CrystEngComm, 2011, 13, 6531–6537 RSC.
- E. Nauha and M. Nissinen, J. Mol. Struct., 2011, 1006, 566–569 CrossRef CAS.
-
N. George, J. O. Forrest, R. C. Burton and C. B. Aakeröy, US Pat., US2013/0203792A1, 2013 Search PubMed.
- K. Honer, E. Kalfaoglu, C. Pico, J. McCann and J. Baltrusaitis, ACS Sustainable Chem. Eng., 2017, 5, 8546–8550 CrossRef CAS.
- P. A. Wood, T. S. G. Olsson, J. C. Cole, S. J. Cottrell, N. Feeder, P. T. A. Galek, C. R. Groom and E. Pidcock, CrystEngComm, 2013, 15, 65–72 RSC.
- I. J. Bruno, J. C. Cole, P. R. Edgington, M. Kessler, C. F. Macrae, P. McCabe, J. Pearson and R. Taylor, Acta Crystallogr., Sect. B: Struct. Sci., 2002, 58, 389–397 CrossRef.
- C. F. Macrae, I. J. Bruno, J. A. Chisholm, P. R. Edgington, P. McCabe, E. Pidcock, L. Rodriguez-Monge, R. Taylor, J. van de Streek and P. A. Wood, J. Appl. Crystallogr., 2008, 41, 466–470 CrossRef CAS.
- C. F. Macrae, P. R. Edgington, P. McCabe, E. Pidcock, G. P. Shields, R. Taylor, M. Towler and J. van de Streek, J. Appl. Crystallogr., 2006, 39, 453–457 CrossRef CAS.
- J. Marti-Rujas, B. M. Kariuki, C. E. Hughes, A. Morte-Rodenas, F. Guo, Z. Glavcheva-Laleva, K. Tastemur, L.-L. Ooi, L. Yeo and K. D. M. Harris, New J. Chem., 2011, 35, 1515–1521 RSC.
- C. Taouss and P. G. Jones, CrystEngComm, 2014, 16, 5695–5704 RSC.
- R. Thaimattam, D. Shekhar Reddy, F. Xue, T. C. W. Mak, A. Nangia and G. R. Desiraju, J. Chem. Soc., Perkin Trans. 2, 1998, 1783–1790, 10.1039/A802452I.
- V. Videnova-Adrabinska and E. Janeczko, Chem. Commun., 1999, 1527–1528, 10.1039/A903602D.
- S. K. Seth, N. K. Das, K. Aich, D. Sen, H. K. Fun and S. Goswami, J. Mol. Struct., 2013, 1048, 157–165 CrossRef CAS.
- A. Alhalaweh, S. George, D. Boström and S. P. Velaga, Cryst. Growth Des., 2010, 10, 4847–4855 CAS.
- J. Emsley, L. Y. Y. Ma, M. B. Hursthouse, S. A. Karaulov and M. Motevalli, J. Chem. Soc., Perkin Trans. 2, 1990, 1077–1080, 10.1039/P29900001077.
- A. O. F. Jones, C. K. Leech, G. J. McIntyre, C. C. Wilson and L. H. Thomas, CrystEngComm, 2014, 16, 8177–8184 RSC.
- A. Krawczuk, M. Gryl, M. B. Pitak and K. Stadnicka, Cryst. Growth Des., 2015, 15, 5578–5592 CAS.
- J. X. Song, Y. Yan, J. Yao, J. M. Chen and T. B. Lu, Cryst. Growth Des., 2014, 14, 3069–3077 CAS.
- C. Taouss, L. Thomas and P. G. Jones, CrystEngComm, 2013, 15, 6829–6836 RSC.
- S. Tothadi, CrystEngComm, 2014, 16, 7587–7597 RSC.
- B. Chetia and P. K. Iyer, Tetrahedron Lett., 2006, 47, 8115–8117 CrossRef CAS.
- M. D. Hollingsworth, M. E. Brown, M. Dudley, H. Chung, M. L. Peterson and A. C. Hillier, Angew. Chem., Int. Ed., 2002, 41, 965–969 CrossRef CAS PubMed.
- W. Xu, W. Huang and H. Chen, Acta Crystallogr., Sect. E: Struct. Rep. Online, 2011, 67, o1795 CAS.
- J. Zhao and X. H. Li, Acta Crystallogr., Sect. E: Struct. Rep. Online, 2005, 61, 3366 Search PubMed.
- S. Selvakumar and A. Leo Rajesh, J. Mater. Sci.: Mater. Electron., 2016, 27, 7509–7517 CrossRef CAS.
- A. Rathika and R. Ganapathi Raman, Optik, 2014, 125, 2978–2982 CrossRef CAS.
- L. Shnidman and A. A. Sunier, J. Phys. Chem., 1931, 36, 1232–1240 CrossRef.
Footnote |
† Electronic supplementary information (ESI) available: Experimental procedures, details of the crystallographic work, melting data, IR spectra, and powder patterns. CCDC 1822958–1822961. For ESI and crystallographic data in CIF or other electronic format see DOI: 10.1039/c8cc01144c |
|
This journal is © The Royal Society of Chemistry 2018 |
Click here to see how this site uses Cookies. View our privacy policy here.