Energy efficiency: a critically important but neglected factor in battery research
Received
21st July 2017
, Accepted 22nd October 2017
First published on 23rd October 2017
Abstract
In fundamental studies of electrode materials for lithium-ion batteries (LIBs) and similar energy storage systems, the main focus is on the capacity, rate capability, and cyclability. The efficiency is usually judged by the coulombic efficiency indicating the electrochemical reversibility. As practical measures, power and energy densities are calculated for discharging, but less attention (if any) is paid to the energy efficiency. Although in the past the energy efficiency was almost close to unity for all electrode materials of LIBs, this factor is critically important for new high-density materials (e.g., based on conversion mechanism) since the energy density can be way below the requirements for the practical development. In fact, a low energy density is due to high overpotentials and is an essential part of the basic research for the material design because it cannot be improved during commercialisation. In large-scale energy storage devices such as batteries in electric vehicles (EVs) or household energy storage systems, the cost of energy consumed to charge the battery is a significant factor and is directly translated into the cost of the energy supplied by the storage device. The present paper clarifies how neglecting the energy efficiency has caused a fraction of research on LIBs to go astray in developing new electrode materials, which are not of practical interest because of huge overpotentials. Particular attention is given to conversion-based electrode materials, which are the common candidates for anode materials of lithium-ion batteries and cathode materials of lithium–sulphur (Li–S) and similar batteries. Furthermore, the impact of nanostructures is considered.
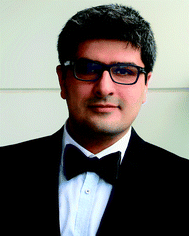 Ali Eftekhari | Ali Eftekhari is a professor of chemistry temporarily with the University of Ulster and Queen's University Belfast. He has worked on energy storage systems for 20 years. In addition to the fundamental understanding of the underlying electrochemical systems, he has attempted to close the gap between the materials research and the battery industry. He is a fellow of the Royal Society of Chemistry (RSC) and the Institute of Materials, Minerals and Mining (IMMM). He is the principal author of over 100 papers published in leading scholarly journals and has supervised over 110 postdoctoral researchers and graduate students. Following to his outstanding contribution to the academic excellence, he was elected as a principal fellow of the Higher Education Academy. |
Introduction
Energy density in battery research reveals the overall capability of the battery (or the half cell under consideration) for storing energy. Since it is calculated based on the discharging process, the value of energy density is the amount of energy the battery can supply. Ideally, the energy density for charging should be the same, but in practice a part of the energy is wasted. Therefore, the ratio of discharge energy density to charge energy density is smaller than 1. For example, to store 10 W h energy in a portable electronic device, we have to pay 11 W h for the electricity supplied by the grid. Since the commercialisation of lithium-ion batteries (LIBs), the focus was on the battery performance in terms of higher capacity, better rate capability, and longer cyclability. The importance of these factors has overshadowed the disadvantage of the cost of 1 W h wasted energy. However, in large-scale LIBs such as in electric vehicles (EVs) or household energy storage systems, the cost of this wasted energy is significant. For instance, the overall cost of electricity for driving an electric vehicle (EV) is now comparable with that of petrol/diesel. If the energy density is low (as will be discussed here), EVs are no longer competitive in the market. In the case of storing solar energy, the amount of energy supplied by the solar panels is limited, and this is the reason that the main focus is to improve the efficiency of solar energy conversion.
It is, therefore, evident that considering the energy efficiency in battery research is of vital importance. The problem is that in fundamental studies of electrode materials, comparison of the charging and discharging processes is usually made by calculating the coulombic efficiency, which only represents the charge stored without accounting for the actual energy. The present paper attempts to clarify that estimating the energy density is essentially required for the investigation of an electrode material to prove its suitability for the practical development. Although the present discussion applies to all energy storage systems from a methodological perspective, the focus is on LIBs and supercapacitors. Owing to the rapidly growing market demand for these electrochemical power sources, numerous research projects have been devoted to the investigation of new electroactive materials.1 As will be quoted, some of these materials meet the common requirements for energy storage, but the energy efficiency is at the level of 50% only. The present paper does not aim to criticise any report in the literature. Instead, it is attempted to clarify that no electrode material can be of practical interest without a considerably high energy efficiency even if other factors are excellent.
Electrochemical reversibility and energy efficiency
Fig. 1 displays a typical charge/discharge profile of a LiCoO2 cathode in the full cell utilising a Li anode. The charge/discharge efficiency can be calculated by the following factors:
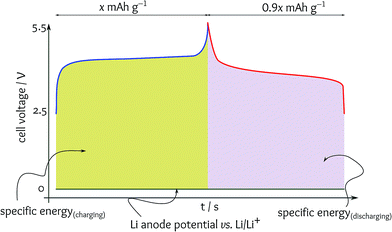 |
| Fig. 1 A typical model of the charge/discharge profile of a Li/LiCoO2 full cell. | |
In the charge/discharge profiles, the amount of charge during charging or discharging is simply equivalent to the length of the x-axis given in mA h g−1. Note that the units are not important as a ratio is calculated. The specific capacity recorded represents the total number of Li atoms supplied by the cathode during charging and accommodated during discharging. In the typical model presented in Fig. 1, x number of Li atoms were extracted from the LiCoO2 cathode to reach the fully charged status of Li0.5CoO2, but only 0.9x number of Li atoms could be re-accommodated during discharging to reach the composition of Li0.95CoO2. Here, the coulombic efficiency is 90% as we have lost 10% of the capacity. Although it is an important measure, the Li atoms (or the electrons on the other side) are treated regardless of the fact that each Li atom might have a different energy level when participating in the redox reaction. For instance, some Li atoms need 2 V energy to be extracted and some need 4 V during charging. If their intercalations release 1 V and 3 V of energy, then huge amounts of overpotentials have been consumed during charging, which cannot be restored. Hence, the total amount of energy spent for extracting all Li atoms and the total amount of energy released by the intercalation of all Li atoms should be calculated to estimate the energy efficiency of the cathode energy storage capability.
These values, known as energy density (with respect to the unit of volume) or specific energy (with respect to the unit of mass), can be estimated from the area under the charge/discharge profiles when the anode is a metallic Li with a constant potential of 0 vs. Li/Li+. Otherwise, the specific energy is the area between the anode and cathode curves. When converting the x-axis into the number of Li atoms, each point represents the energy consumed or released for the extraction or intercalation of each Li atom, respectively. This clearly indicates that the height of the profile is as important as its length when estimating the battery efficiency.
Another important factor contributing to the energy inefficiency is the iR drop in the system. When the cell resistance is higher, part of the energy is consumed against the electrical resistance. This justifies the importance of the electrical conductivity of electroactive materials and the necessity of utilising conductive agents.
Cathode materials with low energy efficiencies
The concepts introduced in the previous section may seem simple and known to all researchers, but in practice were ignored in numerous reports in the literature. Fig. 2a shows an ideal charge/discharge profile with 100% energy efficiency. The charge/discharge symmetry guarantees that the Li atoms are accompanied at the same level of energy as they have been extracted. However, in practice, charging and discharging do not occur exactly at the redox standard potential. This overpotential can be observed as peak-to-peak separation in cyclic voltammetry where electrons with a higher level of energy are consumed during the oxidation scan, and the reverse peak is deferred. The same behaviour can be seen in the charge/discharge plateaus at distinguishably different potentials (Fig. 2b). Here, the energy efficiency is slightly lower than 100%, but it is of practical interest to be maximised. However, there are numerous reports on new electrode materials with surprisingly low energy efficiencies at the level of 50% (Fig. 2c), but since this factor is neglected in battery research, this failure is not realisable. Note that the coulombic efficiencies for all cases illustrated in Fig. 2 are 100%.
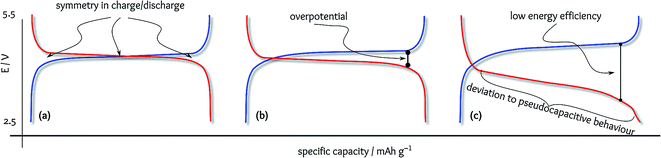 |
| Fig. 2 Various types of charge/discharge profiles in terms of energy efficiency: (a) idea with 100% energy efficiency, (b) practical with 90% energy efficiency, and (c) impractical with 50% energy efficiency. The coulombic efficiency is the same in all cases. | |
Regardless of other factors in the battery performance, cathode materials with low energy efficiencies are not of practical interest. The problem is that there are too many reports of this type of cathode material in the literature. Table 1 represents typical examples for the sake of clarity. The concept of overpotential is more considered in the realm of electrocatalysis, and thus, reducing the difference between the charge and discharge plateaus is a known target in Li–O2 batteries.2 However, in the absence of flat plateaus (which is the case for most of the available materials), this potential difference does not represent the battery performance as accurate as energy efficiency.
Table 1 Some typical low energy efficiencies of electrode materials reported in the literature during the last six months (first half of 2017). The values mentioned in parentheses for the anode materials have been calculated based on an imaginary 4.1 V cathode. Disclaimer: these values have been estimated from the charge/discharge profiles illustrated in the corresponding reference and heavily rounded for the sake of comparison. All the data were normalized to reach a coulombic efficiency of 100% to solely highlight the importance of the energy efficiency. When considering the actual coulombic efficiency, the energy efficiencies listed here would be even lower. For the anode materials, the value in parentheses is the energy efficiency calculated with respect to a Li anode
System |
Electrode |
Material |
Energy efficiency |
Ref. |
LIB |
Cathode |
Li1.2Ni0.2Mn0.6O2 |
70 |
12
|
LIB |
Cathode |
Li1.24Ni0.12Co0.12Mn0.56O2 |
80 |
13
|
LIB |
Cathode |
Li1.2Mn0.54Ni0.13Co0.13O2 |
80 |
14
|
LIB |
Cathode |
Li1.2Mn0.54Ni0.13Co0.13O2 |
80 |
15
|
LIB |
Cathode |
Layered-spinel Li–Co–Mn–O |
80 |
16
|
LIB |
Cathode |
Li1.2Mn0.56Co0.12Ni0.12O2 |
70 |
17
|
LIB |
Cathode |
AlF3 |
30 |
18
|
LIB |
Anode |
Co3O4 |
40 (55) |
19
|
LIB |
Anode |
SnO2 |
30 (70) |
20
|
LIB |
Anode |
NiO |
40 (60) |
21
|
LIB |
Anode |
ZnO |
40 (70) |
22
|
LIB |
Anode |
Li2ZnTi3O8 |
50 |
23
|
LIB |
Anode |
MoS2 |
40 (70) |
24
|
LIB |
Anode |
MoS2 |
40 (60) |
25
|
Li–S |
Cathode |
S |
80 |
26
|
Li–S |
Cathode |
VN |
70 |
27
|
Li–S |
Cathode |
Mesoporous carbon |
70 |
28
|
Li–O2 |
Cathode |
Pd |
60 |
29
|
Li–O2 |
Cathode |
Pd3Co |
70 |
30
|
Li–O2 |
Cathode |
PtRu |
70 |
31
|
Li–O2 |
Cathode |
TiN |
60 |
32
|
Li–O2 |
Cathode |
B4C |
60 |
33
|
Li–O2 |
Cathode |
Co/CoO |
70 |
34
|
Li–O2 |
Cathode |
LaNi0.9Cu0.1O3 |
60 |
35
|
Li–O2 |
Cathode |
Carbon nanofibers |
50 |
36
|
Li–O2 |
Cathode |
Graphene |
70 |
37
|
Supercapacitor |
|
Graphene/carbon |
30 |
38
|
Supercapacitor |
|
Carbon/graphene |
|
39
|
Supercapacitor |
|
Graphene/polyaniline |
30 |
40
|
Supercapacitor |
|
CuO |
30 |
41
|
Supercapacitor |
|
MnO2 |
50 |
42
|
Supercapacitor |
|
MnO2/polyaniline |
60 |
43
|
Supercapacitor |
|
NiCo2O4@rGO |
50 |
44
|
Supercapacitor |
|
MoS2 |
30 |
45
|
Supercapacitor |
|
Ag |
40 |
46
|
Anode materials and pseudocapacitive behaviour
The situation is much worse in the studies of anode materials because of a literal mistake in the terminology.3 In a full cell, charging and discharging of the anode are the opposite of those of the cathode; the anode is lithiated while the cathode is delithiated during charging and vice versa. In fundamental studies of anode materials, the full cell is made of Li metal as the counter and the reference electrode. Thus, the anode material is tested as a cathode in the cell. As a result, many papers reported the potential of lithiation for anode materials, which is indeed the energy consumed to charge the full cell rather than the capacity for supplying energy during discharging.
In a half cell, the anode material acts as a cathode with respect to the metallic Li anode (Fig. 3a). In this case, the energy efficiency is calculated as a ratio of the specific capacity for delithiation (equivalent to the anode process in a full cell discharging) to the specific capacity for lithiation (i.e., equivalent to the anode process in a full cell charging). In many anode materials, a high cell voltage is applied to reduce the anode potential close to that of Li/Li+ during charging, but the anode voltage delivered during discharging is much higher resulting in a significantly lower cell voltage. When considering a relatively ideal cathode delivering a constant voltage, the specific energies can be estimated from the area between the anode and cathode profiles (i.e., the cell voltage) (Fig. 3b). It is evident that the voltage supplied for charging is significantly higher than the cell voltage during the battery usage, and obviously, the energy efficiency is poor.
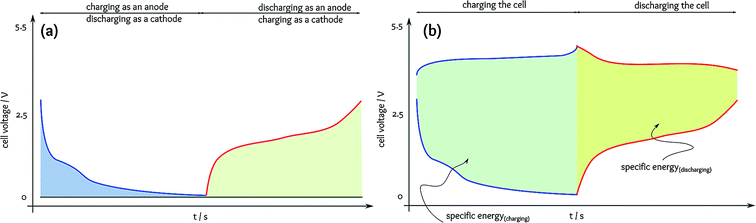 |
| Fig. 3 A schematic of the charge/discharge of a full cell consisting of an ideal cathode and an inefficient anode. The first part (presented in blue) corresponds to the cell charging (i.e., charging the cathode by delithiation and charging the anode by lithiation), and the second part (presented in red) corresponds to the cell discharging (i.e., discharging the cathode by lithiation and charging the anode by delithiation). | |
Note that calculating the energy efficiency in the way presented in Fig. 3a, when the anode material is treated as a cathode, is misleading because the target cell voltage is not against Li/Li+. For instance, the Si anode can be lithiated with an average potential of 0.15 V vs. Li/Li+ and delithiated with an average potential of 0.35 V vs. Li/Li+.4 When calculating the energy efficiency with respect to a metallic Li anode, a terrible value of 43% is obtained. However, in a full cell utilising a LiCoO2 cathode, this anode can work with an energy efficiency of 95%. Anode materials delivering the capacity in the potential range of 2–3 V vs. Li/Li+ have recently become common (see ref. 3 for a comprehensive review). Having a significantly higher specific capacity by sacrificing the cell voltage is practical as the overall energy density remains the same, but if the anode can be lithiated at the range of 2–3 V vs. Li/Li+. Most of these anode materials can be lithiated at low potentials close to that of Li/Li+, and thus, the energy efficiency drops to the level of 50% making the material impractical for commercialisation.
Although charging and discharging in supercapacitors occur over a broad range of potentials, the average potentials are equal during charging and discharging, and thus, the energy efficiency might be 100%. Nonetheless, when a battery material deviates from the flat plateau exhibiting a pseudocapacitive behaviour, this phenomenon is usually asymmetrical, i.e., happening on one side only, during either charging or discharging. This is very common for conversion-based materials, which are among the most promising candidates for the anode materials.3 On the other hand, nanomaterials have a tendency to show a degree of pseudocapacitive behaviour instead of ideal battery performance characterised by a flat plateau. Hence, battery materials with pseudocapacitance show high specific capacity close to ideal coulombic efficiency, but the energy efficiency is poor due to the declining cell voltage (Fig. 3 and 4). Wu and Yushin stressed that a key challenge of conversion-based electrode materials is high voltage hysteresis resulting in low energy efficiency.5
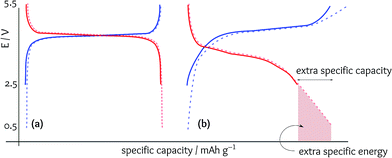 |
| Fig. 4 Charge/discharge profiles of (a) an ideal cathode material and (b) an inefficient cathode material with pseudocapacitance between the 2.5–5.5 V cutoffs (solid lines) and 0.5–5.5 V (dashed lines) potential cutoffs. | |
Intercalation and conversion mechanism
In intercalation materials with high crystallinity, the ordered architecture of the lattice can guarantee a low redox overpotential resulting in high energy efficiency. This is the reason that energy efficiency was not a critical issue in the classic LIBs, and thus, neglected in time. If the diffusion channels within the lattice are spacious and straightforward, the intercalating ion can reach the redox sites with a negligible energy barrier. Therefore, the energy spent for extracting the redox ion will be supplied upon intercalation. Most of the intercalation cathode materials such as LiFePO4, LiCoO2, etc. exhibit well-defined cyclic voltammetric behaviour with a small peak-to-peak separation. However, the thermodynamics of the intercalation of multivalent cations are not straightforward (e.g., because of the complicated interactions during the solid-state diffusion) resulting in high overpotentials (i.e., low energy efficiency), which is indeed one of the key challenges of multivalent charge carriers such as aluminium batteries.6
The situation is substantially different in conversion mechanism where the redox sites are not fixed. Instead, the material undergoes a massive structural change, which is associated with the huge volume change (i.e., the key disadvantage of conversion-based electrode materials). Because of this structural change, the redox potential is not constant, and the flat plateau of an ideal battery material transforms to pseudocapacitive materials, as mentioned in the previous section. However, this is not limited to anode materials, but fewer cathode materials are considered as promising candidates. Instead, cathode materials of Li–S7 and Li–Se8 and similar energy storage systems are based on conversion mechanism because chalcogens do not have a firm and spacious lattice to accommodate intercalating Li-ions. Instead, the cathode works by a direct reaction associated with the formation of a new phase. Note that this is different from the geometrical phase transformation of intercalation materials.
Most of the conversion-based electrode materials exhibit a massive capacity fading during the first cycle. This phenomenon is normally attributed to an essential structural change in the electrode material, which can be somehow considered as part of the material preparation. However, the energy efficiency can be fairly calculated for all cycles. Therefore, when starting to calculate the energy efficiency from the first cycle, an increase can be observed during the first cycle(s). Similar behaviour is known for the initial increase in the coulombic efficiency as a structural rearrangement in both intercalation and conversion materials. In fact, plotting the energy efficiency as a function of cycle number can reveal the range of practical cyclability of the electrode. Furthermore, the value of the energy efficiency in the first cycle can provide a useful comparative factor to understand the initial structural change of the electrode materials.
From bulk to nanoparticles
In the case of intercalation materials, reducing the particle size generally increases the charge/discharge overpotentials. In the bulk form, the lattice architecture guarantees a smooth solid-state diffusion. Although this process is slow, the intercalating ions do not require excess energy to reach the redox sites. When reducing the particle size, more redox sites are exposed through a larger surface area. However, the interfacial resistance might cause an excess overpotential. The interface at the electroactive material/electrolyte is quite complicated and depends on both sides. This is the reason that the formation of a suitable solid electrolyte interphase (SEI) is of utmost importance in the cyclability of LIBs.
Notwithstanding, another possibility is the formation of highly active sites at the surface. A good example is the dangling carbon atoms at the graphene edges.9 These active sites can break the interfacial barrier to assist the intercalation process. For instance, it is reasonable to assume that the intercalation of Li-ions into graphite anode is initiated by the electrochemical reaction at the graphene edges followed by the solid-state diffusion within the graphite interlayers. As it has been discussed for supercapacitors, there is a higher probability for the surface sites to have quite different energies as compared with the identical redox sites within the lattice architecture.10 As a result, reducing the particle size usually tends to strengthen the pseudocapacitive behaviour. It should be taken into account that having a set of different redox potentials does not necessarily reduce the energy efficiency.
In general, preparing nanostructured materials for energy storage devices is not straightforward. In most cases, the well-defined electrochemical behaviour of the conventional electroactive material is sacrificed by nanostructuring. Although increasing the active surface area favours the system kinetics and usually results in faster charging/discharging, the thermodynamics benefit from the ordered lattice in the bulk material. Therefore, energy storage materials should be subtly tailored to gain an electrochemically active interface, which is the key part of the nanomaterials.
Potential cutoffs
In an ideal case, the specific capacity should be independent of the potential cutoffs, as the redox system should be completed at the redox potential (Fig. 4a). In fact, widening the potential window is to make sure that the redox capacity has been fully achieved. However, in the electrode materials displaying pseudocapacitive behaviour, extending the potential cutoff can increase the total specific capacity achieved, but the energy efficiency is dramatically dropped. Since the latter factor is not normally reported in the literature, the importance of the potential cutoffs is not realised. In other words, when appropriately adjusting the potential cutoffs based on the energy efficiencies, a majority of these works cannot report a considerable specific capacity (because the high specific capacities reported are at the cost of sacrificing the energy efficiency, which is vitally important for the practical performance).
In Fig. 4b, the achieved extra specific capacity is significantly considerable (e.g., 20%) but the added specific energy is not very high (e.g., less than 10%). The reason is that extending the potential window provided an opportunity for the intercalation of Li+ into low-energy redox sites. On the other hand, during charging, Li+ is extracted from high-energy redox sites. In other words, enormous overpotentials are applied to extract the excess Li+ while their intercalation during discharging releases much lower energy, and thus, the energy efficiency has become worse by expanding the potential cutoffs. Moreover, in the practical performance of a LIB, the cell voltage should not go below ca. 3 V, and it is meaningless to reach a cell voltage of ca. 1 V for a LIB (Fig. 4b). Although the voltage is regulated by the battery electronic circuit, going to low cell voltages means that the cell should be discharged at higher rates (higher currents) to deliver a constant energy.
Concluding remarks
Energy efficiency is the most important factor in battery research, at least for the large-scale LIBs, because it directly translates into the final cost of the energy supplied. In the past, there was no need to calculate the energy efficiency in the fundamental research for two reasons: the target of novel energy storage systems such as LIBs was portable electronic devices such as mobile phone and laptops where the cost of charging was negligible for the consumers, and almost all classical intercalation materials could fairly show an energy efficiency of close to unity. However, many new electrode materials are impractical because of high overpotentials in the corresponding redox systems. Estimating the energy efficiency is not difficult and can be done based on the experimental data currently being reported in the literature. Simply reporting the value of energy efficiency can give a better picture on how a novel material or electrode design might have a practical potential.
Conversion-based materials can surely provide new opportunities for the future generation of energy storage devices because of a high specific energy.1,3 The present paper aims to emphasise that the energy efficiency of these materials should be considered along with the attractive specific energy. Otherwise, these materials cannot economically justify a possible commercialisation. In other words, neglecting the critical role of energy efficiency in the production of commercial batteries will leave numerous research efforts in vain. In fact, many of the available materials could be eliminated because of poor energy efficiency, and the research investments on them have already gone astray.
Furthermore, energy efficiency can represent the role of overpotentials, which should be minimised for practical developments. This factor can modify the strategy of research for the future development of LIBs, supercapacitors, and similar energy storage systems. It is not only a matter of cost-effectiveness of the energy storage devices, but low energy efficiency also indicates that something is not right in the electrochemical system. This can help us to better design the electrode materials at both lattice and nanoscales. Rate capability is among the most common tests for electrode materials monitoring the capacity fading at higher charge/discharge rates.11 However, the impact of the charge/discharge rate on energy efficiency is more significant due to the role of a lower specific capacity along with higher overpotentials. In other words, rate capability should be inspected in terms of the decay in energy efficiency. In conclusion, developing new electrode materials without considering the energy efficiency is lame because it does not tell us how much is precisely the cost of the energy supplied.
Conflicts of interest
There are no conflicts to declare.
References
- N. Nitta, F. Wu, J. T. Lee and G. Yushin, Li-Ion Battery Materials: Present And Future, Mater. Today, 2015, 18, 252–264, DOI:10.1016/j.mattod.2014.10.040.
- A. Eftekhari and B. Ramanujam, In Pursuit Of Catalytic Cathodes For Lithium–Oxygen Batteries, J. Mater. Chem. A, 2017, 5, 7710–7731, 10.1039/c7ta01124e.
- A. Eftekhari, Low Voltage Anode Materials For Lithium-Ion Batteries, Energy Storage Materials, 2017, 7, 157–180, DOI:10.1016/j.ensm.2017.01.009.
- D. Liu, Y. Zhao, R. Tan, L. Tian, Y. Liu, H. Chen and F. Pan, Novel Conductive Binder For High-Performance Silicon Anodes In Lithium Ion Batteries, Nano Energy, 2017, 36, 206–212, DOI:10.1016/j.nanoen.2017.04.043.
- F. Wu and G. Yushin, Conversion Cathodes For Rechargeable Lithium And Lithium-Ion Batteries, Energy Environ. Sci., 2016, 10, 435–459, 10.1039/c6ee02326f.
- A. Eftekhari and P. Corrochano, Electrochemical Energy Storage By Aluminum As A Lightweight And Cheap Anode/Charge Carrier, Sustainable Energy Fuels, 2017, 1, 1246–1264, 10.1039/c7se00050b.
- A. Eftekhari and D. Kim, Cathode Materials For Lithium–Sulfur Batteries: A Practical Perspective, J. Mater. Chem. A, 2017, 5, 17734–17776, 10.1039/c7ta00799j.
- A. Eftekhari, The Rise Of Lithium–Selenium Batteries, Sustainable Energy Fuels, 2017, 1, 14–29, 10.1039/c6se00094k.
- A. Eftekhari and H. García, The Necessity Of Structural Irregularities For The Chemical Applications Of Graphene, Mater. Today Chem., 2017, 4, 1–16, DOI:10.1016/j.mtchem.2017.02.003.
- A. Eftekhari and M. Mohamedi, Tailoring Pseudocapactive Materials From A Mechanistic Perspective, Materials Today Energy, 2017, 6, 211–229, DOI:10.1016/j.mtener.2017.10.009.
- A. Eftekhari, Lithium-Ion Batteries With High Rate Capabilities, ACS Sustainable Chem. Eng., 2017, 5, 2799–2816, DOI:10.1021/acssuschemeng.7b00046.
- Y. Xiang, Z. Sun, J. Li, X. Wu, Z. Liu, L. Xiong, Z. He, B. Long, C. Yang and Z. Yin, Improved Electrochemical Performance Of Li1.2Ni0.2Mn0.6O2 Cathode Material For Lithium Ion Batteries Synthesized By The Polyvinyl Alcohol Assisted Sol-Gel Method, Ceram. Int., 2017, 43, 2320–2324, DOI:10.1016/j.ceramint.2016.11.016.
- J. Ding, Z. Lu, M. Wu, C. Liu, H. Ji and G. Yang, Preparation And Performance Characterization Of AlF3 As Interface Stabilizer Coated Li1.24Ni0.12Co0.12Mn0.56O2 Cathode For Lithium-Ion Batteries, Appl. Surf. Sci., 2017, 406, 21–29, DOI:10.1016/j.apsusc.2017.02.115.
- M. Lou, H. Zhong, H. Yu, S. Fan, Y. Xie and T. Yi, Li1.2Mn0.54Ni0.13Co0.13O2 Hollow Hierarchical Microspheres With Enhanced Electrochemical Performances As Cathode Material For Lithium-Ion Battery Application, Electrochim. Acta, 2017, 237, 217–226, DOI:10.1016/j.electacta.2017.03.201.
- L. He, J. Xu, T. Han, H. Han, Y. Wang, J. Yang, J. Wang, W. Zhu, C. Zhang and Y. Zhang, SmPO4-Coated Li1.2Mn0.54Ni0.13Co0.13O2 As A Cathode Material With Enhanced Cycling Stability For Lithium Ion Batteries, Ceram. Int., 2017, 43, 5267–5273, DOI:10.1016/j.ceramint.2017.01.052.
- D. Li, H. Zhang, C. Wang, D. Song, X. Shi and L. Zhang, New Structurally Integrated Layered-Spinel Lithium-Cobalt-Manganese-Oxide Composite Cathode Materials For Lithium-Ion Batteries, J. Alloys Compd., 2017, 696, 276–289, DOI:10.1016/j.jallcom.2016.11.246.
- F. Fu, Y. Yao, H. Wang, G. Xu, K. Amine, S. Sun and M. Shao, Structure Dependent Electrochemical
Performance Of Li-Rich Layered Oxides In Lithium-Ion Batteries, Nano Energy, 2017, 35, 370–378, DOI:10.1016/j.nanoen.2017.04.005.
- N. Owen and Q. Zhang, Investigations Of Aluminum Fluoride As A New Cathode Material For Lithium-Ion Batteries, J. Appl. Electrochem., 2017, 47, 417–431, DOI:10.1007/s10800-017-1049-2.
- R. Hu, H. Zhang, Y. Bu, H. Zhang, B. Zhao and C. Yang, Porous Co3O4 Nanofibers Surface-Modified By Reduced Graphene Oxide As A Durable, High-Rate Anode For Lithium Ion Battery, Electrochim. Acta, 2017, 228, 241–250, DOI:10.1016/j.electacta.2017.01.067.
- X. Hu, G. Zeng, J. Chen, C. Lu and Z. Wen, 3D Graphene Network Encapsulating SnO2 Hollow Spheres As A High-Performance Anode Material For Lithium-Ion Batteries, J. Mater. Chem. A, 2017, 5, 4535–4542, 10.1039/c6ta10301d.
- X. Wang, L. Sun, X. Sun, X. Li and D. He, Size-Controllable Porous NiO Electrodes For High-Performance Lithium Ion Battery Anodes, Mater. Res. Bull., 2017, 96, 533–537, DOI:10.1016/j.materresbull.2017.04.046.
- H. Fan, H. Yu, Y. Zhang, J. Guo, Z. Wang, H. Wang, X. Hao, N. Zhao, H. Geng, Z. Dai, Q. Yan and J. Xu, From Zinc-Cyanide Hybrid Coordination Polymers To Hierarchical Yolk-Shell Structures For High-Performance And Ultra-Stable Lithium-Ion Batteries, Nano Energy, 2017, 33, 168–176, DOI:10.1016/j.nanoen.2017.01.043.
- C. Chen, C. Ai, Y. He, S. Yang and Y. Wu, High Performance Li2ZnTi3O8 Coated With N-Doped Carbon As An Anode Material For Lithium-Ion Batteries, J. Alloys Compd., 2017, 705, 438–444, DOI:10.1016/j.jallcom.2017.02.143.
- Q. Pang, Y. Zhao, X. Bian, Y. Ju, X. Wang, Y. Wei, B. Liu, F. Du, C. Wang and G. Chen, Hybrid Graphene@MoS2@TiO2 Microspheres For Use As A High Performance Negative Electrode Material For Lithium Ion Batteries, J. Mater. Chem. A, 2017, 5, 3667–3674, 10.1039/c6ta10216f.
- J. Liu, A. Fu, Y. Wang, P. Guo, H. Feng, H. Li and X. S. Zhao, Spraying Coagulation-Assisted Hydrothermal Synthesis Of MoS2/Carbon/Graphene Composite Microspheres For Lithium-Ion Battery Applications, ChemElectroChem, 2017, 4, 2027–2036, DOI:10.1002/celc.201600769.
- L. Ma, M. S. Kim and L. A. Archer, Stable Artificial Solid Electrolyte Interphases For Lithium Batteries, Chem. Mater., 2017, 29, 4181–4189, DOI:10.1021/acs.chemmater.6b03687.
- N. Mosavati, S. O. Salley and K. S. Ng, Characterization And Electrochemical Activities Of Nanostructured Transition Metal Nitrides As Cathode Materials For Lithium Sulfur Batteries, J. Power Sources, 2017, 340, 210–216, DOI:10.1016/j.jpowsour.2016.11.033.
- C. Luo, H. Zhu, W. Luo, F. Shen, X. Fan, J. Dai, Y. Liang, C. Wang and L. Hu, Atomic-Layer-Deposition Functionalized Carbonized Mesoporous Wood Fiber For High Sulfur Loading Lithium Sulfur Batteries, ACS Appl. Mater. Interfaces, 2017, 9, 14801–14807, DOI:10.1021/acsami.7b01205.
- X. Ren, B. Liao, Y. Li, P. Zhang, L. Deng and Y. Gao, Facile Synthesis Of PdSnCo/nitrogen-Doped Reduced Graphene As A Highly Active Catalyst For Lithium-Air Batteries, Electrochim. Acta, 2017, 228, 36–44, DOI:10.1016/j.electacta.2017.01.032.
- S. M. Cho, J. H. Yom, S. W. Hwang, I. W. Seong, J. Kim, S. H. Cho and W. Y. Yoon, Morphology Control Of Lithium Peroxide Using Pd3Co As An Additive In Aprotic Li–O2 Batteries, J. Power Sources, 2017, 342, 427–434, DOI:10.1016/j.jpowsour.2016.12.076.
- Y. Yui, S. Sakamoto, M. Nohara, M. Hayashi, J. Nakamura and T. Komatsu, Electrochemical Properties Of Lithium Air Batteries With Pt100−xRux (0 ≤ x ≤ 100) Electrocatalysts For Air Electrodes, J. Power Sources, 2017, 340, 121–125, DOI:10.1016/j.jpowsour.2016.11.063.
- B. G. Kim, C. Jo, J. Shin, Y. Mun, J. Lee and J. W. Choi, Ordered Mesoporous Titanium Nitride As A Promising Carbon-Free Cathode For Aprotic Lithium-Oxygen Batteries, ACS Nano, 2017, 11, 1736–1746, DOI:10.1021/acsnano.6b07635.
- S. Song, W. Xu, R. Cao, L. Luo, M. H. Engelhard, M. E. Bowden, B. Liu, L. Estevez, C. Wang and J. Zhang, B4C As A Stable Non-Carbon-Based Oxygen Electrode Material For Lithium-Oxygen Batteries, Nano Energy, 2017, 33, 195–204, DOI:10.1016/j.nanoen.2017.01.042.
- S. Hyun and S. Shanmugam, Mesoporous Co-CoO/N-CNR Nanostructures As High-Performance Air Cathode For Lithium-Oxygen Batteries, J. Power Sources, 2017, 354, 48–56, DOI:10.1016/j.jpowsour.2017.04.029.
- T. V. Pham, H. P. Guo, W. B. Luo, S. L. Chou, J. Z. Wang and H. K. Liu, Carbon- And Binder-Free 3D Porous Perovskite Oxide Air Electrode For Rechargeable Lithium–oxygen Batteries, J. Mater. Chem. A, 2017, 5, 5283–5289, 10.1039/c6ta10751f.
- S. Martinez Crespiera, D. Amantia, E. Knipping, C. Aucher, L. Aubouy, J. Amici, J. Zeng, U. Zubair, C. Francia and S. Bodoardo, Cobalt-Doped Mesoporous Carbon Nanofibres As Free-Standing Cathodes For Lithium–oxygen Batteries, J. Appl. Electrochem., 2017, 47, 497–506, DOI:10.1007/s10800-016-1035-0.
- Y. Lin, B. Moitoso, C. Martinez-Martinez, E. D. Walsh, S. D. Lacey, J. Kim, L. Dai, L. Hu and J. W. Connell, Ultrahigh-Capacity Lithium–Oxygen Batteries Enabled By Dry-Pressed Holey Graphene Air Cathodes, Nano Lett., 2017, 17, 3252–3260, DOI:10.1021/acs.nanolett.7b00872.
- H. A. A. Bashid, H. N. Lim, S. Kamaruzaman, S. A. Rashid, R. Yunus, N. M. Huang, C. Y. Yin, M. M. Rahman, M. Altarawneh, Z. T. Jiang and P. Alagarsamy, Electrodeposition Of Polypyrrole And Reduced Graphene Oxide Onto Carbon Bundle Fibre As Electrode For Supercapacitor, Nanoscale Res. Lett., 2017, 12, 246, DOI:10.1186/s11671-017-2010-3.
- A. Gopalakrishnan, P. Sahatiya and S. Badhulika, Low Temperature, One-Pot Green Synthesis Of Tailored Carbon Nanostructures/reduced Graphene Oxide Composites And Its Investigation For Supercapacitor Application, Mater. Lett., 2017, 198, 46–49, DOI:10.1016/j.matlet.2017.03.182.
- M. G. Hosseini and E. Shahryari, A Novel High-Performance Supercapacitor Based On Chitosan/GO-MWCNT/PANI, J. Colloid Interface Sci., 2017, 496, 371–381, DOI:10.1016/j.jcis.2017.02.027.
- S. C. Bhise, D. V. Awale, M. M. Vadiyar, S. K. Patil, B. N. Kokare and S. S. Kolekar, Facile Synthesis Of CuO Nanosheets As Electrode For Supercapacitor With Long Cyclic Stability In Novel Methyl Imidazole-Based Ionic Liquid Electrolyte, J. Solid State Electrochem., 2017, 21, 1–7, DOI:10.1007/s10008-016-3490-2.
- J. Noh, C. Yoon, Y. K. Kim and J. Jang, High Performance Asymmetric Supercapacitor Twisted From Carbon Fiber/MnO2 And Carbon Fiber/MoO3, Carbon, 2017, 116, 470–478, DOI:10.1016/j.carbon.2017.02.033.
- K. Ghosh, C. Y. Yue, M. M. Sk and R. K. Jena, Development Of 3D Urchin-Shaped Coaxial Manganese Dioxide@Polyaniline (MnO2@PANI) Composite And Self-Assembled 3D Pillared Graphene Foam For Asymmetric All-Solid-State Flexible Supercapacitor Application, ACS Appl. Mater. Interfaces, 2017, 9, 15350–15363, DOI:10.1021/acsami.6b16406.
- C. Zhang, X. Geng, S. Tang, M. Deng and Y. Du, NiCo2O4@rGO Hybrid Nanostructures On
Ni Foam As High-Performance Supercapacitor Electrodes, J. Mater. Chem. A, 2017, 5, 5912–5919, 10.1039/c7ta00571g.
- R. Pujari, A. Lokhande, A. Shelke, J. Kim and C. Lokhande, Chemically Deposited Nano Grain Composed MoS2 Thin Films For Supercapacitor Application, J. Colloid Interface Sci., 2017, 496, 1–7, DOI:10.1016/j.jcis.2016.11.026.
- J. Lee, J. Lee, J. Kwon, H. Lee, H. Eom, Y. Yoon, I. Ha, M. Yang and S. H. Ko, Highly Controlled Nanoporous Ag Electrode By Vaporization Control Of 2-Ethoxyethanol For A Flexible Supercapacitor Application, Langmuir, 2017, 33, 1854–1860, DOI:10.1021/acs.langmuir.6b04625.
|
This journal is © The Royal Society of Chemistry 2017 |
Click here to see how this site uses Cookies. View our privacy policy here.