DOI:
10.1039/C7SE00050B
(Review Article)
Sustainable Energy Fuels, 2017,
1, 1246-1264
Electrochemical energy storage by aluminum as a lightweight and cheap anode/charge carrier
Received
24th January 2017
, Accepted 13th April 2017
First published on 20th April 2017
Abstract
Various lightweight metals such as Li, Na, Mg, etc. are the basis of promising rechargeable batteries, but aluminium has some unique advantages: (i) the most abundant metal in the Earth's crust, (ii) trivalent charge carrier storing three times more charge with each ion transfer in comparison with Li, (iii) the volumetric capacity of the Al anode is four times higher than that of Li while their gravimetric capacities are comparable, (iv) employing a metallic Al anode does not have a major safety risk as is the case for alkali metals. However, there are serious obstacles to the practical development of Al batteries such as the complicated nature of trivalent Al3+ intercalation into the cathode of Al-ion batteries and corrosion of the metallic Al anode in aqueous electrolytes. Owing to the highly charged nature of small Al3+ ions, the diffusing species are indeed the Al complexed ions, which might be the intercalating ions in the solid-state too. The present manuscript reviews the current status of various aluminum batteries to narrate their unique potentials while highlighting the issues that should be addressed at this stage. Although Al–air batteries have a long history going back to the 1960s, the focus of this manuscript is on Al-ion batteries including Al–sulfur batteries, but other possibilities for electrochemical energy storage by Al charge carriers such as Al redox batteries, Al supercapacitors, etc. will be reviewed too. In the latter case, it seems the pseudocapacitance is more practical than intercalation for the case of Al3+ ions. Furthermore, the application of Al anodes in lithium-ion batteries is briefly described as the anode performance is similar to their application in Al batteries.
1 Introduction
Due to the growing market for portable energy storage systems, the demand for lithium-ion batteries (LIBs) is dramatically increasing day by day, but the natural scarcity of lithium is a serious obstacle in this direction, particularly for large-scale batteries for electric vehicles or household storage. Therefore, alternative batteries such as sodium,1–7 potassium,8,9 magnesium,10–15 and calcium16–19 are being considered as efficient and cheap replacements for LIBs. All these batteries work with the same principle in which the oxidative redox system of the metal at the cathode provides a positive potential, and the metal/cation redox system at the anode side creates the cell voltage. Alkali metals provide low anode potentials, and thus, a high cell voltage can be achieved. This is, indeed, the first motivation for the development of LIBs. On the cathode side also, novel conversion-based cathodes are being considered such as lithium–sulfur20 and lithium–selenium.21 Owing to the novelty of these systems, their electrochemistry is not entirely understood, as will be discussed for aluminum batteries in the present manuscript.
Another important problem observed in these batteries is the inherent chemical reactivity of the metallic anode, and thus, new anode materials should be developed for the practical applications causing an extra burden for the cell performance. Magnesium is a less reactive metal, which can be easily employed as the metallic anode while gaining a divalent charge carrier of Mg2+. These characteristic advantages promoted the study of magnesium batteries as potential energy storage systems for decades.
The volumetric capacity of the Al anode is 8.0 A h cm−3, which is four times higher than that of the Li anode (i.e., 2.0 A h cm−3). The gravimetric capacity is also comparable (2.0 A h g−1 for Al vs. 3.9 A h g−1 for Li). In a sense, aluminum batteries could be the best of rechargeable batteries because of unique advantages.22,23 This is the only practical battery based on a trivalent charge carrier, which means each ion transfer is accompanied by three times more charge storage as compared with LIBs. On the other hand, a metallic anode is not an issue due to the appropriate chemical reactivity of aluminum (not too much, even in comparison with magnesium). Aluminum is lightweight and much cheaper than its counterparts, and the cell design would be facile and inexpensive. However, the applicability of aluminum batteries is limited by severe problems, which will be reviewed here.
2 Aluminum-ion batteries
2.1 Cathode materials
The main obstacle of the aluminum-ion batteries (AIBs) is the cathode material, as the intercalation mechanism of trivalent Al3+ ion is much more complex than that of simple ions such as Li+. The charge density of Al3+ ions is quite high, though the size of the Al3+ cation (67.5 pm) is smaller than that of Li+ (90 pm). The Al3+ ions are very small with a high valence state. The high charge density of Al3+ results in numerous interactions within the host lattice. However, this is not an ultimate obstacle, as the scarcity of potential cathode materials is probably due to the lack of knowledge since Al3+ has never been among the common counterions in the realms of electrochemistry. On the other hand, an extremely high current density of 0.8 A cm−2 can be obtained on the Al anode side,24 and thus, the rate-determining step is the cathodic process.
Furthermore, the highly charged small ion of Al3+ is too active for a non-interactive diffusion. This is the major impediment towards Al3+ diffusion. As will be discussed later, the diffusion of Al3+ is not a process as straightforward as that found for monovalent cations such as Li+ and K+. Instead, co-ions such as Cl− can participate in the intercalation process,25 or in a more strict way, the intercalating anion is indeed the product of the complexation reaction with the Al3+ ions, i.e., AlCl4− ions.26 The extension of these complexation reactions, of course, depends on the electrolyte media.
An important issue in studies of the cathode materials is the potential cutoffs in the galvanostatic experiments. It has been recently discussed for the case of LIBs that inappropriate choice of the potential cutoffs causes recording of unrealistic specific capacities.27 Classically, the potential cutoffs were not important for the common electroactive materials displaying a flat plateau in their battery performances since the majority of the specific capacity was delivered in a narrow range of potential regardless of the final cutoff (as characterized by a sudden drop of the voltage at the end of charging). However, novel electroactive materials may have a pseudocapacitive nature, and thus, the recorded capacity monotonically increases by widening the potential cutoffs. In the case of Al batteries, many cathode materials have been tested with a potential cutoff of 0, but in practice, it is meaningless to discharge a full battery up to the voltage of 0. However, the case is different from supercapacitors, and this is the importance of differentiating batteries from supercapacitors.28
2.1.1 Titanium oxide.
Liu et al. reported that Al3+ ions could be intercalated into TiO2 nanotubes from an AlCl3 electrolyte.29 The interesting point is that while Al3+ can be easily intercalated into TiO2, Li+ or Mg2+ cannot. They reported a specific capacity of 75 mA h g−1 at a discharge rate of 4 mA g−1. The intercalation process of the Al3+ ions is not straightforward and highly dependent on the anion, which accompanies the Al3+ ions, e.g., Al3+ ions cannot intercalate into the same TiO2 electrode from an Al2(SO4)3 electrolyte.30 Following another report emphasizing the importance of Cl− anions in an ionic liquid (IL) electrolyte for the Al3+ intercalation into V2O5, Liu et al. investigated the influence of the Cl− counter anion on the battery performance of TiO2 nanotubes.30 They found that the electrochemical redox system of the Al3+ intercalation/deintercalation in an Al2(SO4)3 aqueous electrolyte appears by adding NaCl to the solution. As a result, the AIB could achieve the same specific capacity obtained in an AlCl3 electrolyte as well as in an Al2(SO4)3 electrolyte too if the Cl− anion is introduced into the electrolyte solution. Similar results have been reported by Sang et al., for easier intercalation of Al3+ along with Cl− as compared with Al2(SO4)3 in aqueous solutions.30
Following the excellent electrochemical performance of black anatase TiO2 in LIBs due to the presence of the electro-conducting Ti3+ species,31 He et al. employed this cathode material in AIBs.32 While a commercial white anatase TiO2 cathode could only deliver a specific capacity of 75 mA h g−1, the cathode made of black anatase TiO2 nanoleaves delivered a specific capacity of over 275 mA h g−1. Despite the significant difference in the specific capacity, both cathodes showed the same pattern of discharging via three stages suggesting that the intercalation mechanisms are quite similar.
2.1.2 Vanadium pentoxide.
V2O5 is a promising candidate in LIBs due to its high capacity and easy intercalation of Li ions.33,34 It has also shown promising potential for the intercalation of other cations such as Na1+,35 and Mg2+.10,36 Both experimental36–38 and computational39 studies suggested that V2O5 can accommodate Al3+ ions. However, this mechanism of Al3+ intercalation is very complicated and subject to controversies. Reed and Menke suggested that V2O5 is electrochemically inactive for the Al3+ intercalation, and the capacity obtained is due to a redox reaction between the Al3+ and the stainless steel current collector.40 On the other hand, Wu et al. investigated the intercalation of Al3+ ions into V2O5 nanowires by eliminating the role of the stainless steel current collector and showed that the V2O5 lattice could accommodate the Al3+ ions reversibly. However, this process is not straightforward and accompanied by an essential phase transition.
Fig. 1 shows the process of Al3+ intercalation into V2O5. The reaction of Al3+ ions at the V2O5 surface is not exactly an intercalation process. Instead, an amorphous layer is formed. Then, the intercalation occurs at a sub-surface which is accompanied by a phase transition. Recent studies have suggested that only this amorphous layer is electrochemically active to host the Al3+ ions.41 The theoretical capacity of V2O5 is 442 mA h g−1, but only a fraction of this capacity is practically achieved. The reason is that the electrochemically active amorphous layer is laterally formed on the electroactive material, and the majority of the V2O5 bulk does not participate in the intercalation mechanism. Similar results have also been reported for the orthorhombic V2O5 obtained from xerogel delivering a specific capacity of 120 mA h g−1 as a result of amorphization in the course of Al intercalation/deintercalation.42 This is probably due to the difficulty of three-valent Al ions to diffuse within the lattice structure because of strong interactions. Overall, these results suggest that the intercalation of Al3+ ions needs more spacious channels for the diffusion, which can be provided by an amorphous architecture or large lattice structures.
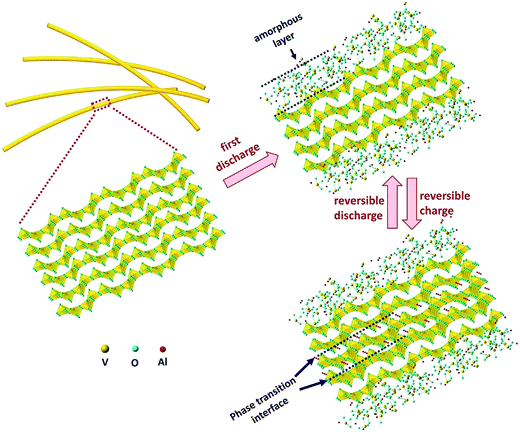 |
| Fig. 1 A schematic diagram of Al3+ electrochemical insertion/extraction in crystallized V2O5 nanowires. Reproduced with permission.41 Copyright 2017, Elsevier. | |
Considering the complexity of the Al intercalation, one may conclude that the presence of a binder adds to this complexity. Amine and his coworkers synthesized V2O5 directly onto a Ni foam current collector to fabricate a binder-free cathode.43 The initial specific capacity was 239 mA h g−1, which was higher than that of the common V2O5 nanowire cathodes employing conventional binders.
In addition to the intercalation complexity, the diffusion of Al electroactive species is not as simple as common monovalent charge carriers, as it is accompanied by a series of reactions resulting in the regular formation of various intermediates. The nature of these intermediates may vary depending on the electrolyte media, but similar mechanisms are involved in the current electrolytes. Fig. 2 illustrates the mechanism of charge carrier transport by the Al electroactive species in an IL electrolyte toward a V2O5 cathode.
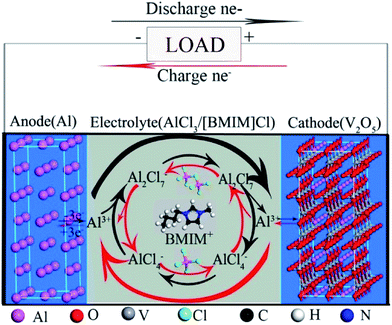 |
| Fig. 2 A schematic illustrating the Al electroactive species formed within an IL electrolyte before reaching the surface of a V2O5 cathode. Reproduced with permission.43 Copyright 2015, American Chemical Society. | |
2.1.3 Transition metal hexacyanoferrates.
Prussian blue (PB) is the flagship of the family of transition metal hexacyanoferrates, which are well known because of their well-defined electrochemical behaviors. The excellent electrochemical performance of PB for the intercalation/deintercalation of K ions caused the birth of potassium-ion batteries.9 Since then, various transition metal hexacyanoferrates have been successfully employed as cathode materials in various rechargeable batteries such as lithium,44–46 sodium,47–49 calcium50,51 and also aluminum.52,53
Transition metal hexacyanoferrates have a cage-like lattice structure with appropriate empty channels for the diffusion of the counterions. Therefore, the electrochemical performance is highly reversible accompanied by an excellent cyclability.9 However, this excellent performance has only been obtained for potassium, as the size of K+ ions well matches with the open channels of PB and its analogs, but still, the cyclability should be satisfactory as compared with other intercalation materials. The key issue of PB for potassium-ion batteries is that the PB lattice is too large in comparison with common metal oxide cathode materials, and thus, the specific capacity is significantly lower than those of available LIB cathode materials. This is not the case in AIBs, as the specific capacity is still higher than other candidates.
Fig. 3 displays the electrochemical performance of copper hexacyanoferrate in an Al2(SO4)3 electrolyte. The redox system is not straightforward as the sharp redox peaks in a potassium electrolyte have been transformed to broad peaks. As a result, a flat plateau during the galvanostatic charging/discharging is not expected. However, the battery performance is still acceptable with a good rate capability. Li et al. investigated the Al intercalation in PB and concluded that the electrochemical performance is of a pseudocapacitive nature rather than a battery performance.54 They employed this system for fabricating an Al supercapacitor, as will be described later.
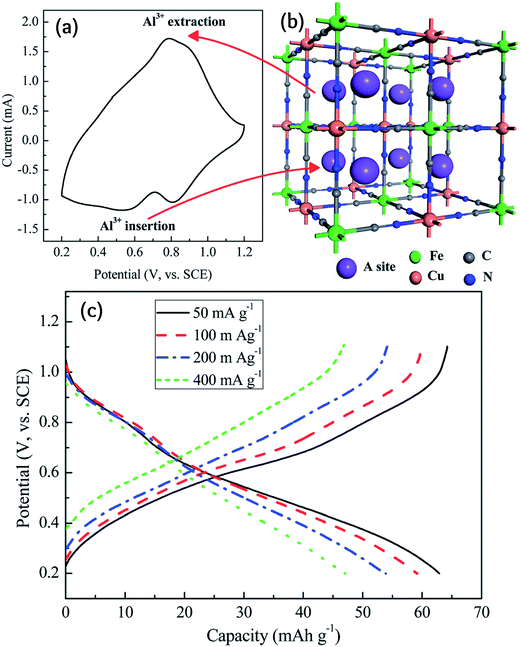 |
| Fig. 3 (a) Typical CV curve of a copper hexacyanoferrate (CuHCF) electrode in aqueous Al2(SO4)3 and (b) the schematic positions of Al3+ in the CuHCF framework. (c) Charge/discharge curves at different current densities of the CuHCF electrode in 0.5 M Al2(SO4)3 aqueous solution. Reproduced with permission.52 Copyright 2015, Royal Society of Chemistry. | |
Cui and his coworkers conducted a comparative study of the intercalation of a wide range of multivalent cations (including transition metals, which are somehow considered exotic ions as the intercalating counterions) into copper hexacyanoferrate.55 The electrochemical behaviors of the divalent cations (Pb2+, Ni2+, Zn2+, Co2+, and Cu2+) were significantly different, while surprisingly, the intercalation of Pb2+ exhibited the best battery performance. Among the trivalent cations (Al3+, Y3+, La3+, Ce3+, Nd3+, Sm3+), Y3+ showed the most well-defined performance. Overall, the electrochemical performances of trivalent cations were better than those of divalent cations, suggesting the potential of trivalent charge carriers for future energy storage. Quite interestingly, the specific capacities and rate capabilities of the trivalent cations were as good as those of potassium intercalation/deintercalation.
2.1.4 Conductive polymers.
Anion intercalation plays a substantial role in the battery performance of various cathode materials. In this regard, conductive polymers can be an excellent choice, as the electrochemical activities of conductive polymers are normally associated with anion doping/de-doping, which is highly reversible. Hudak investigated the battery performance of polypyrrole and polythiophene in an AIB and achieved specific capacities in the range of 30–100 mA h g−1.56 It was proposed that the intercalating ions are indeed AlCl4− and Al2Cl7−.
2.1.5 Metal sulfides.
Another possibility for the Al positive electrode is to replace the intercalation redox with a reactive redox in which the Al3+ ions react with the cathode material. While the former accommodates the counterion within the lattice structure, the latter is based on a reaction resulting in the formation of a new lattice. Metal sulfides seem to be a good candidate for this purpose, as the Al–S bond is strong enough to handle the electrochemical redox and weak enough to be suitable for the reverse process.
FeS2 was first employed as a cathode metal in AIBs about four decades ago in molten media and ILs.57 The applicability of the FeS2 cathode in AIBs has been recently revisited by Mori et al., as they shed light on the mechanism involved in the charge/discharge process.58 The proposed reaction is as follows:
| FeS2 + 2/3Al3+ + 2e− = FeS + 1/3Al2S3 | (1) |
and thus, the theoretical capacity is 447 mA h g
−1.
Fig. 4 displays the structural change of the FeS
2 to form an amorphous Al
2S
3. Since the reaction mainly occurs at the FeS
2 surface, it is reasonable to consider that the specific capacity is dependent on the specific surface area of the electroactive material. This is indeed what was experimentally observed as the specific capacity increased exponentially by reducing the particle size.
58
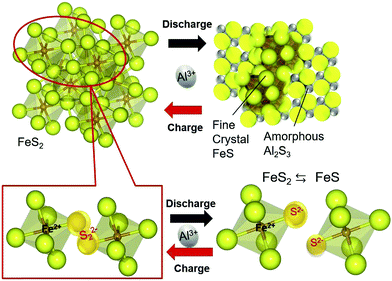 |
| Fig. 4 Charge–discharge reaction model of FeS2 with aluminum ions in an AlCl3–EMIC ionic liquid at 55 °C. Reproduced with permission.58 Copyright 2016, Elsevier. | |
By comparing Fig. 1 and 4, one may conclude that the mechanisms are somehow similar. This suggests that there is no pure intercalation mechanism for the Al3+ redox at the cathode side. Wang et al. employed a Ni3S2/graphene cathode for the intercalation of Al3+ ions and achieved a specific capacity of 350 mA h g−1 at a current density of 0.1 A g−1.59 Although the cyclability was poor resulting in 80% capacity fading over 100 cycles, the coulombic efficiency was quite good in the course of cycling.
Geng et al. proposed Mo6S8 as a potential intercalation material for AIBs due to the charge redistribution in the sulfide anionic frameworks60 following the successful application of Mo6S8 in magnesium-ion batteries.61 The Mo6S8 cathode showed two plateaus for the Al intercalation/deintercalation. Although the first discharge capacity was almost 150 mA h g−1, the capacity dropped by half during the first cycle, the cell could maintain its capacity afterward. Crystallographic studies revealed the two different sites of Al intercalation in Mo6S8, but none of them was directly responsible for the initial capacity fading, as the capacity was equally decreased in both plateaus.
2.1.6 Graphite.
Intercalation of Al into graphite is conducted by the Al complex anion. Although the intercalation process is not straightforward (at least in comparison with the intercalation of other cations), the electrochemical performance is well-defined as characterized by a sharp redox couple. As a result, the battery delivers a constant voltage between 1.8 and 1.4 V.62Fig. 5 shows the electrochemical behavior of a carbon-based cathode. The battery performance is of practical interest with a good cyclability. The cathode is restructured during the first cycles to facilitate the subsequent intercalation. This increases both the specific capacity and the cell voltage. However, the rate capability is still poor due to the rate-determining nature of the intercalation process.
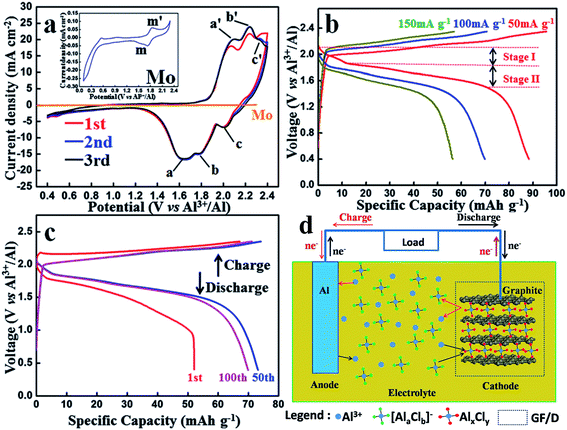 |
| Fig. 5 (a) Cyclic voltammograms of an Al-ion full battery and that of Mo. The inset is the CV curve of Mo without carbon paper. (b) Charge and discharge curves under different current densities. (c) 1st, 50th and 100th charge–discharge curves at 100 mA g−1. (d) Cycling performances of an Al-ion full battery under different current densities over 50 cycles. Schematic representation of an aluminium-based full-battery system during the charge and discharge process. Reproduced with permission.62 Copyright 2015, Royal Society of Chemistry. | |
Jung et al. inspected the influence of the number of graphene layers on the diffusivity of the counterions within graphitic foams composed of few layers of graphene in the graphite stacking.26 While proposing that the intercalating ion is indeed AlCl4−, they experimentally showed that the diffusivity is dramatically increased by reducing the number of graphene layers, as reducing the number of graphene layers from five to four, three, and two will enhance the diffusivity by 45, 153, and 225 times, respectively. This suggests that the diffusion of the counterions is not limited to the interlayer spacing provided by the graphite architecture, and the diffusing ions tend to push the layers to open up more space, which is easier when a lower number of graphene layers are in the graphite stacking.
In fact, an appropriate architecture of graphite can provide a facile diffusion for the Al counterions. Wu et al. synthesized a somehow indigenous 3D graphitic foam by the intercalation of chloroaluminate anion and thermal expansion, and the resulting cathode material could deliver a specific capacity of 60 mA h g−1 after 4000 cycles at an extremely high current density of 12 A g−1.63 Lin et al. have also reported an ultrafast Al-ion battery, which could be charged within one minute with a current density of 4 A g−1 and retain its capacity fully after 7500 cycles.64
Owing to the good rate capability of AIBs, an important question is how AlCl4 clusters can diffuse within the graphite structure so fast? Computational studies suggested that the AlCl4 clusters intercalated within the graphite structure are in the form of a planar quadrangle rather than tetrahedral.65 With an expanded d spacing of over 6 Å, the diffusion is facile along the 2D structure of graphite.
One of the first examples of Al batteries was Al/Cl2 employing a graphite cathode for the intercalation/deintercalation of chlorine in an IL electrolyte.25 This battery, which is indeed an analog to the Al–oxygen battery, exhibited excellent performance in terms of cell voltage, cyclability, and capacity, but chlorine evolution was a serious obstacle to the practical development. The performance of this battery was due to the capability of graphite for accommodating a wide range of electroactive species in an electrochemical cell. This causes uncertainty about the exact mechanism of Al intercalation into the graphite cathode in AIBs.
2.2 Anode process
Like similar battery systems, the anode process of an AIB is based on the electrodissolution of Al3+ ions from the anode transferring toward the cathode during the discharge process. Conversely, the Al3+ ions return from the cathode in the course of charging towards the anode to form Al0. Despite the chemical stability of aluminum in an ambient atmosphere, an AIB cannot generally perform in an aqueous solution, because the Al/Al3+ redox potential is below that of the hydrogen evolution reaction (HER). Therefore, hydrogen bubbles are formed before the reduction of Al3+. On the other hand, the electrochemical dissolution/deposition of Al in a conventional organic electrolyte is sluggish. Thus, the anode performance is a major issue.66–68 In general, the anode performance is mainly controlled by the type of the electrolyte.
2.3 Electrolytes
Finding an appropriate electrolyte for the AIBs is now an active area of research. A practical option is the emerging ILs, which are common media for the electrodeposition of active metals. As a matter of fact, chloroaluminates are among the first ILs reported in the literature. Al can be electrochemically stripped/deposited from IL electrolytes with an efficiency of over 98%.69–72
In aqueous solutions, the H+ counterion competes with the Al3+ counterion in the intercalation process. Sang et al. proposed that H+ does not intercalate within the TiO2 lattice, as the tendency is to hydroxylate the surface sites, while the Al3+ cation intercalates into the lattice along with the Cl− anion.30 Overall, the electrochemical performance is highly dependent on the electrolyte pH. For example, while TiO2 shows a well-defined strong electrochemical behavior in an aqueous electrolyte of Al2(SO4)3 with pH 1.0, the electrochemical activity disappears for the same electrolyte with pH 2.0. The sensitivity of both the anodic and cathodic processes to the electrolyte pH and other factors makes the comparison of different reports very difficult.
Angell et al. prepared a cheap electrolyte by mixing AlCl3 and urea in a molar ratio of 1.3
:
1, as an alternative to expensive organic salt-based ILs.73 The corresponding battery delivered a specific capacity of 73 mA h g−1 at 1.4C (i.e., 0.1 A g−1). The spectroscopic studies revealed the presence of AlCl4−, Al2Cl7− anions and (AlCl2·(urea)n)+ cations in the electrolyte, which were involved in both anodic and cathode processes in one way or another.
The performance of the Al anode is similar in all types of Al batteries, as will be reviewed for other cases too. The key processes are the reversible electrochemical dissolution and deposition of Al in the course of discharging and charging, respectively. The reversibility of this system is dependent on the nature of the films formed on the Al anode and the electrode/electrolyte interface. Therefore, the type of the electrolyte crucially controls the anode performance. In a different context, electrodeposition of Al from ILs has been extensively investigated to find better electrolytes.74–78
Reed et al. computationally and experimentally investigated the electrochemical behavior of a typical Al-based IL electrolyte and reported that this IL electrolyte displays a straightforward behavior with ion pairing at very low concentrations.79 The electrochemical stability was significantly dependent on the salt concentration. This performance can be ascribed to the capability of Al3+ ions in complexing with the IL organic ions. Another computational study suggested that the formation of low stability ion–solvent complexes in an IL electrolyte paves the path for rapid Al-ion solvation/desolvation, which is of utmost importance at the electrode/electrolyte interface.80 Molecular dynamics simulations showed that Al3+ ions mainly interact with the carbonyl and ether-oxygen groups in the conventional non-aqueous solvents such as organic carbonates while the Cl− ions are indeed the counter anions in ILs.
Polymer gel electrolytes have recently attracted considerable attention because they are solid-like but still flexible. The polymer matrix can be impregnated by ILs to provide facile ionic transport across the polymer matrix while preserving the polymer structure. A common practical problem of ILs is high cost, but in the polymer gel electrolyte, a lesser amount of gel is required in the cell design in comparison with liquid electrolytes. Sun et al. prepared a chloroaluminate-based IL by complexing 1-ethyl-3-methylimidazolium chloride (EMImCl) and AlCl3.81 They were able to successfully conduct the Al electrodeposition with this gel electrolyte and showed that the electrochemical performance of an Al anode with this gel electrolyte is satisfactory for battery applications.
Since the battery performance is dependent on the IL complex formed, the influence of concentration is not simple and straightforward. Fig. 6 depicts the battery performance in different ratios of the AlCl3/BMIm electrolyte. As can be seen, the battery performance vanishes where the AlCl3 concentration is lower than 1.1
:
1, while the 1.1
:
1 ratio is the optimum value. This ratio changes the Lewis acidity of the electrolyte.
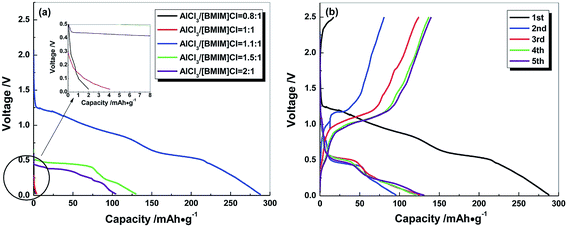 |
| Fig. 6 Initial discharge profiles of rechargeable aluminum batteries using AlCl3/[BMIM]Cl ionic liquids with different mole ratios. Reproduced with permission.179 Copyright 2015, Royal Society of Chemistry. | |
In contrast to the basic impression, finding the appropriate IL is not an easy task, as the common AlCl3-containing imidazole-based ILs are moisture sensitive and corrosive. Although having a wide stable electrochemical window is a characteristic feature of ILs, it is not always sufficient for the high operating voltage of batteries. Wang et al. introduced a new IL-based electrolyte made of 1-butyl-3-methylimidazolium trifluoromethanesulfonate (BMIM–OTF) and an aluminum salt (Al(OTF)3) with a high oxidation voltage of 3.25 V vs. Al/Al3+.82 The electrolyte was also water-stable and non-corrosive while having a high ionic conductivity.
As depicted in Fig. 2, the Al diffusion is not simple even in an IL electrolyte, and a series of intermediates are formed before the ultimate intercalation/deintercalation into/from the cathode. The nature of the intercalating species might be different depending on the electrolytic intermediates formed, but our knowledge is very limited to fully understand this process at the electrode/electrolyte interface. In general, Al-ion batteries based on IL electrolytes can be considered as a new generation of Al batteries, as the electrochemistry is quite different from that of conventional Al batteries (mostly Al–air) performing in aqueous media. Although it has been explained that ILs are not practical choices to replace the current problematic electrolytes of lithium-ion batteries,83 there is a rapidly growing interest in designing the AIBs based on IL electrolytes.59,82,84 As a matter of fact, ILs are introducing new opportunities in the realm of Al batteries.
3 Aluminum–sulfur batteries
Metal–sulfur batteries have recently attracted considerable attention due to their high specific capacity and the low cost of sulfur. The flagship of this class of rechargeable batteries is as usual lithium–sulfur batteries due to the negative potential of the Li anode. The prototype of aluminum–sulfur (Al–S) batteries dates back to 1993 when Peramunage and Licht fabricated a battery with the overall reaction | 2Al + 3S + 3OH− + 3H2O → 2Al(OH)3 + 3HS− | (2) |
delivering a cell voltage of 1.3 V and a specific energy of 910 W h kg−1.85
Xia et al. reported an Al–S battery based on the common cathode of Li–S batteries, which was sulfur embedded within a carbon matrix.86 An advantage of the Al–S batteries in comparison with the Al–air batteries is that the system is thermodynamically closed. There is also a noticeable privilege over the AIBs, as the cathode material is not based on an intercalation redox. Therefore, the interactive diffusion of trivalent Al3+ ions is no longer an issue. However, the idea of Al–S batteries is at its preliminary stage, and its obstacles and issues have not been visualized yet.
Cohn et al. investigated the performance of an Al–S battery in a series of IL-based electrolytes.87 The molar ratio of EMICl
:
AlCl3 had a substantial impact on the cell performance. The best battery performance was achieved at the ratio of 1
:
1.5 where a specific capacity of over 1400 mA h g−1 was achieved via a perfectly flat plateau at 1.2 V. The lithium–selenium battery has been recently introduced as an alternative because of the considerable advantages of selenium in comparison with sulfur, such as high electrical conductivity, low solubility of the polyselenides (vs. polysulfides) causing the harmful shuttle phenomenon, low chemical reactivity of selenium, etc.21 Designing an Al–Se battery should be challenging due to the similar metallicity of the anode and cathode, but it might provide new opportunities.
4 Aluminum–air batteries
Aluminum–air (Al–air) batteries are among the oldest examples of metal–air batteries introduced in the 1960s and have been considered for various applications such as electric vehicles.88 The theoretical cell voltage and specific capacity of the Al–air battery are 2.75 V and 2978 mA h g−1, respectively. Its mechanism is somehow similar to those of other metal–air batteries, except for the tendency of Al for the formation of complexes in the electrolyte solution. The history of Al–air batteries prior to 2013 has been extensively reviewed by Egan et al.,24 and thus will be excluded here. The anode side is the conventional supplier of the charge carrier cation, and the cathode involves a catalytic reaction associated with the oxygen evolution reaction (OER) or oxygen reduction reaction (ORR) resulting in the decomposition or formation of the corresponding metal oxide.
The performance of an Al–air battery is based on the following anodic and cathodic reactions:
| Al + 4OH− → Al(OH)4− + 3e−, E0 = −2.35 V | (3) |
| O2 + 2H2O + 4e− → 4OH−, E0 = +0.40 V | (4) |
Therefore, the overall reaction of the battery can be written as
| 4Al + 3O2 + 6H2O + 4OH− → 4Al(OH)4−, E0 = 2.75 V | (5) |
A side reaction which can cause capacity fading is
| 2Al + 6H2O + 2OH− → 2Al(OH)4− + 3H2 | (6) |
However, the practical cell voltage is much lower than this theoretical value. A recent computational study suggested that the maximum open-circuit voltage of an Al anode is less than −1.9 V vs. SHE rather than the classical value of −2.35 V vs. SHE.89 As a result, the low cell voltage of the current Al–air batteries should not be attributed to an experimental failure but the system complexity in the theoretical considerations.
Similar to other metal–air batteries, there is a tendency to replace the conventional noble metal catalysts for ORR due to the cost. Metal oxides are among the promising candidates, but still, their overpotentials are high for the ORR electrocatalysis.90 However, the electrocatalysis mechanism is somehow different due to the different nature of the Al intermediates. The current focus is on high surface area carbon nanomaterials providing a large number of electrochemically accessible electrocatalytic sites.91 However, the current studies on the cathode of Al–air batteries are mainly limited to the common ORR electrocatalysts based on a high surface area carbon and a metallic catalyst. In this direction, the carbon architecture and chemical structure are adjusted to facilitate the ORR mechanism, while cheaper catalysts such as Ag are also investigated.92 N-doping is a common approach for facilitating the adsorption and surface diffusion across the carbon matrix, and most of the Al–air battery cathodes have employed N-doped carbon.92–94 The key point is that the Al anode can provide fast and facile kinetics in comparison with the cathode, and the cathodic process is indeed the rate-determining step.
Metal oxides have been widely employed for the ORR electrolysis. Liu et al. employed LiMn2O4, which is indeed a common cathode material in lithium-ion batteries, to fabricate a cheap cathode for Al–air batteries.94 A nanocomposite of conducting polymers and metal oxides can be a promising candidate as a low-cost ORR electrocatalyst. For example, MnO2/poly-(3,4-ethylenedioxythiophene) (PEDOT) has been successfully employed for this purpose. Kuo et al. utilized ORR electrocatalysts for the cathode performance of an Al–air battery.95 The corresponding computational study attributed the excellent performance to the clear charge transfer between PEDOT and MnO2.
Xu et al. designed an Al–air battery with a fiber architecture.96Fig. 7 shows a schematic of the fiber-shaped Al–air battery. This possibility is because of the capability of aluminum for flexible casting. As can be seen, the Al anode is coated by a hydrogel electrolyte. The cathode is an Ag-coated CNT sheet, which is the lateral layer. In this design, the cathode is largely exposed to air. This all-solid-state Al battery delivered a specific capacity of 935 mA h g−1 and an energy density of 1168 W h kg−1. Sun et al. exploited the synergetic effect among Ag nanoparticles placed on MnO2 to significantly improve the ORR electrocatalytic activity as compared with the single metal catalysts for Al–air batteries.97
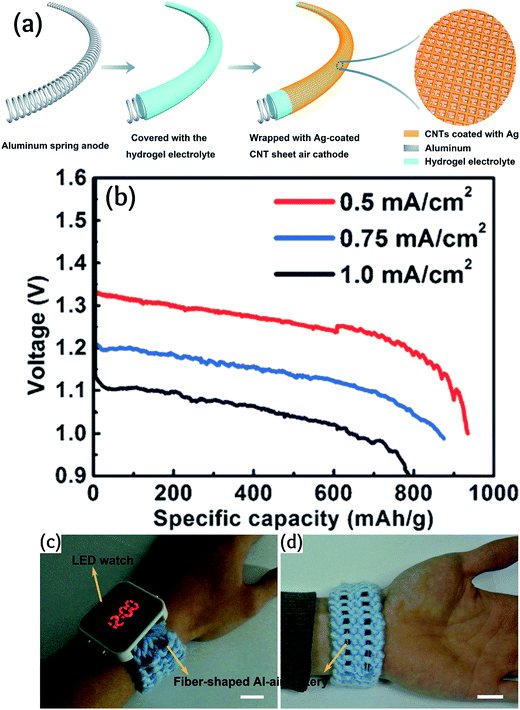 |
| Fig. 7 Fabrication of the fiber-shaped Al–air battery. Discharge curves of fiber-shaped Al–air batteries at current densities of 0.5, 0.75, and 1.0 mA cm−2. Photographs of a commercial LED watch powered by two fiber-shaped Al–air batteries woven into a fabric and connected in series. Scale bars: 2 cm. Reproduced with permission.96 Copyright 2016, Wiley-VCH. | |
The main obstacle for the practical development of Al–air batteries is self-corrosion of aluminum in the common electrolyte media. Two common approaches for overcoming this problem are improving the aluminum corrosion resistance by alloying it with appropriate metals98–100 or reducing the corrosive nature of the electrolyte.101–103 Another approach is to coat the anode with a protective material which somehow serves as an ion conductive membrane.104 Mori employed two protective layers of activated carbon to avoid the irreversible deposition of the harmful by-products on the anode or cathode.105
4.1 Electrolytes
Two common electrolytes for the Al–air batteries are alkaline and saline electrolytes, in which the redox potentials are theoretically −1.66 and −2.35 V, respectively.24 In practice, neither of these potentials can be achieved due to the formation of aluminum oxide/hydroxide layers. Wang et al. made a comparative study of the kinetic reaction of Al–air batteries in various aqueous electrolytes.106
The most common electrolyte of the Al–air batteries is alkaline media because of the high cell voltage and excellent performance.107 However, Al corrosion in an alkaline electrolyte is a major issue.24 The Al corrosion can be reduced by choosing the appropriate electrolyte. A common approach is to employ corrosion inhibitors within the electrolyte. For instance, when the electrolyte contains ZnO, a protective layer of Zn deposits is formed on the Al electrode as a result of the formation of Zn(OH)42−.108,109
In addition to the common electrolytic corrosion inhibitors, soluble polymers have also shown promising potential. While the polymer can thicken the solution (which also reduces the risk of leakage due to a higher viscosity), it can provide a synergetic effect in combination with another electrolytic inhibitor. For instance, Liu et al. employed carboxymethyl cellulose (CMC) along with ZnO to reduce the Al corrosion in an Al–air cell.110 They concluded that the Zn protective layer formed on the Al surface is porous because of the amphoteric nature of Zn, and then, CMC fills the porosity to further inhibit the corrosion. This is indeed a known approach to employ an inorganic salt in combination with an organic compound as the electrolyte corrosion inhibitors, as they simultaneously adsorb on the electrode surface and protect the Al surface from corrosion.111
From a practical perspective, it is beneficial to employ environmentally friendly corrosion inhibitors to achieve low toxicity and biodegradability. Grishina et al. fabricated an Al–air battery with a 5 M KOH electrolyte and used 3 vol% flax straw extract as a corrosion inhibitor.112 While the cell voltage remained almost intact (only 0.1 V lower), the corrosion rate was reduced about three times in the initial run.
Neutral electrolytes are another choice with a better long-term stability due to the weaker corrosion of Al, but the cell voltage is much lower.113–115 On the other hand, the notorious shuttle effect is more severe due to the partial solubility of the Al(OH)3 product, which subsequently results in the formation of a gel-like layer on the Al anode.116 Kühnel et al. investigated the correction of Al current collectors in highly concentrated aqueous electrolytes and concluded that Al corrosion is significantly suppressed in such electrolytes making it suitable for the high-voltage performance of batteries over the conventional thermodynamic stability of water.117
Mori protected both the anode and cathode by an ion conductive membrane of Al2(WO4)3, but the Al2O3 and Al(OH)3 films were also deposited on the membrane blocking the battery performance.118 This is due to the strong tendency for the formation of Al(OH)3 in alkaline media. To overcome this issue, the battery was also investigated with a neutral electrolyte.104 Although the battery was stable over a month, the cell voltage was low similar to other Al–air batteries in neutral electrolytes. A protective layer composed of Al2O3 can also be employed by assuming that the electrochemical reactivity of the chemically synthesized Al2O3 is less than that electrochemically formed on the electrode surface.119
Gelman et al. employed an IL electrolyte to eliminate the harmful side-processes in aqueous media.120 They used an EMIm(HF)2.3F electrolyte because of its prior successful application in Si–air batteries owing to its low viscosity and chemical stability in interaction with oxygen and water.121,122 The battery performance at low discharge rates was quite good by delivering an almost constant potential of 1.7 V. The interesting feature was that the cathode product was Al2O3. The cell reported had a gravimetric energy density of 2300 W h kg−1 and a volumetric energy density of 6200 W h l−1, which are over four times higher than a similar Al–air battery in aqueous media.120 Nakayama et al. introduced the possibility of using sulfone-based electrolytes as a non-corrosive media for Al batteries.123
Even in ILs, the electrodissolution of Al is not straightforward and somewhat hindered by a native oxide layer formed on the anode surface. Shvartsev et al. proposed that utilizing EMIm(HF)2.3F IL electrolyte can facilitate the formation of an Al–O–F layer in lieu of the native oxide layer.124 The latter dramatically reduced the Al corrosion, and thus improved the battery performance.
In general, leakage of liquid electrolytes is a serious safety issue, since the metal–air batteries cannot be sealed. As mentioned earlier, gel electrolytes have noticeable advantages for the fabrication of modern batteries. Impregnation of gel electrolytes with alkaline solutions has also been applied for designing Al–air batteries.125–127 Even in a cell with a gel electrolyte, the battery performance and Al corrosion are highly dependent on the alloy composition.127 Therefore, matching the anode alloy and the electrolyte is a major task in designing the Al batteries, while there is no vivid insight for this purpose.
All-solid-state Al–air batteries can be fabricated by utilizing an appropriate ion conducting separator serving as the solid electrolyte. Hibino et al. employed an anhydrous hydroxide ion conductor (Sn0.92Sb0.08P2O7) having an ionic conductivity of 10 mS cm−1.128 By separating an Al plate anode and a Pt/C cathode with this separator, they could achieve a specific capacity of 800 mA h g−1.
4.2 Anode
Since pure aluminum is not a suitable anode in alkaline media, there are numerous attempts to design new Al anodes which are resistive against alkaline corrosion to gain the advantages of alkaline media for future Al–air batteries.129 The simplest approach is alloying Al with other metals as this can control the passive layer formed on the electrode and push the corrosion potential to more negative regions.98,113,130–138 For this purpose, it is more convenient to utilize metals having high overpotentials for HER to avoid the unfavorable hydrogen evolution.114,139 Since some impurities such as iron and silicon dramatically strengthen the Al corrosion, the starting material is usually pure aluminum.140 As a matter of fact, some components in the alloys are merely responsible for deactivating the influence of such impurities. For instance, magnesium is usually used in Al alloys to form Mg2Si on interaction with possible Si impurities to avoid its harmful effect.140
The crucial impact of the aluminum purity on the battery performance has been reported.141 This indicates that even small amounts of impurities can affect the battery performance, and this factor should be taken into account, particularly in comparative studies.
The role of the electrolytic corrosion inhibitors is to form a protective layer on the Al anode. It is also feasible to coat the Al anode by a protective permeable layer. For instance, a thin layer of aluminum oxide or aluminum tungsten oxide can avoid direct contact and the Al anode between the corrosive species while allowing the transport of the charge carriers.142 Depending on the electrochemical properties of these protective layers, their performance might be dependent on the type of the electrolyte (e.g., a significant difference between the performance in NaOH and KOH142). Therefore, careful attention should be paid to matching the protective layer and the electrolyte. To avoid the direct interactions of the Al(OH)3 dissolved within the electrolyte with the Al metallic anode, Pino et al. coated the Al anode with a carbon protective layer.143
The Al anode performance is very complicated and highly dependent on its chemical composition due to the involvement of a series of side-reactions.144Fig. 8 compares the performance of similar anodes made of commercial aluminum samples. It is evident that small changes in the Al alloy composition can result in substantial changes in the battery performance.
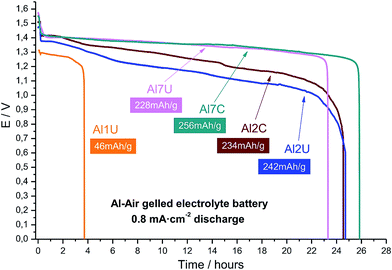 |
| Fig. 8 Discharge plot of all studied alloys at a constant current density of 0.8 mA cm−2. Reproduced with permission.127 Copyright 2015, Elsevier. | |
In addition to the chemical composition, the Al crystal orientation also plays a crucial role in the battery performance of an Al anode. The cell voltages of single crystal Al anodes are usually higher than those of polycrystalline Al anodes.145 Among the single crystals, Al (001) showed the highest cell voltage while having the lowest corrosion rate.145
The key point is that the unfavorable side reaction is HER, and the electrocatalysis can be facilitated on the surface irregularities where the charge distribution is non-uniform.146 When preparing the Al anode from aluminum particles, finer grain size provides better battery performance, as the HER electrocatalysis is less active.147
Owing to the variety of commercial aluminum alloys available in the literature, it is an active area of research to find the best possible choice for the anode of Al–air batteries in terms of corrosion.148–151 This is not only limited to the chemical composition of the alloy but also its structure. Fan et al. showed that utilizing finer grains improves the performance of an Al anode in alkaline media, while it has no noticeable effect on the performance in neutral media.152
The morphology of the Al anode also plays a specific role in its battery performance. Li et al. synthesized Al nanorods via vapor deposition and made an anode with a composition of 65 wt% Al, 25 wt% carbon, and 10 wt% PTFE.153 In this case, the specific capacity was two times higher than that of the commercial Al powder.
5 Aluminum redox batteries
Similar to Al–air batteries, it is possible to design an Al battery by employing a redox system at the cathode. This redox system can be conducted within the electrolyte solution to keep the whole cell closed. A typical example of this class of batteries is Al–ferricyanide battery154 in which the anode is the conventional Al anode associated with the reaction (3), while the cathodic process is the well-defined ferricyanide/ferrocyanide redox systems as | Fe(CN)63− + e− → Fe(CN)64−, E0 = 0.46 | (7) |
Therefore, the overall battery reaction can be written as
| Al + 3OH− + 3Fe(CN)63− → Al(OH)3 + 3Fe(CN)64−, Ecell = 2.76 | (8) |
Another example of this family is based on a sulfur redox system within the electrolyte.155,156 This is similar to the Al–S batteries, but the redox is associated with the S42−/HS− system within the electrolyte rather than the redox system of a solid sulfur cathode.
This is indeed a class of batteries that were extensively investigated during the 1990s and referred to as superbatteries because of their high power density.154–158 However, less attention is currently paid to this class of batteries. In the emerging field of Al batteries, such studies might be the guiding stars to pave the path for the creation of the next generation of Al batteries.
6 Aluminum as the anode of LIBs
Aluminum is a common current collector in various electrochemical systems including LIBs, and thus its electrochemical activity has been extensively studied in the conventional environment of common batteries.159–161 Moreover, aluminum can be employed as an anode material owing to its capability of forming an alloy with Li. In this case, the Al electrode serves as both a current collector and anode.162 In fact, aluminum can be a multi-functional material in the design of LIBs.163
In some cases, the overall cell is referred to as an aluminum battery, though Al is not involved in the charge carrying process. For instance, Zhang et al. reported a dual-ion battery composed of an Al anode and a graphite cathode.164 The electrolyte was LiPF6 to provide Li+ ions for the formation of AlLi alloys on the anode side, and the anion intercalation of PF6− into/from the graphite cathode. This dual-ion battery is not a conventional LIB as the Li+ ions are not involved in the cathode process, but it cannot be simply considered as an aluminum battery because the Al anode can be replaced by another metal. On the other hand, the anode negative potential comes from the negative redox system of Li/Li+. In fact, it is confusing to claim that an aluminum battery can deliver a cell voltage over 4 V.
Some of the novel promising candidates for the anode materials of LIBs are based on conversion mechanisms forming lithium alloys.27 In the same family of anode materials, Al is a promising anode material with a theoretical capacity of 2234 mA h g−1 corresponding to Li9Al4.165,166 A low redox potential of 0.19–0.45 V vs. Li/Li+ is also expected,167 which is of utmost importance.27 However, only a fraction of this capacity has been practically achieved.168,169 Since the primary problem in the cyclability of Al anodes is capacity fading as a result of volume changes in the course of lithiation/delithiation, common approaches providing sufficient space within the anode architecture have been utilized to improve the battery performance of Al anodes. Li et al. synthesized a yolk–shell architecture by covering Al nanoparticles with a TiO2 shell, and the resulting anode exhibited a specific capacity of over 1000 mA h g−1 at 1C while retaining about 90% of the initial capacity after 500 cycles.170
Au et al. prepared a free-standing Al anode with a 3D structure by depositing aligned Al nanorods using glancing angle deposition.171 Owing to the high surface area and the empty spaces between the nanorods, which could compensate the volume expansion, the anode delivered a specific capacity of 1243 mA h g−1 at 0.5C. However, capacity fading was noticeable accompanied by severe structural changes upon cycling.
The performance of the Al anode is quite good in ILs, as the Al-based ions can complex with the IL electrolyte. Introducing an aluminum salt in the IL electrolyte (e.g., a mixture of EMImCl and AlCl3) can change the role of the Al anode as merely an alloying electroactive material. In this case, Al2Cl7− or similar aluminum-based anions are exchanged with the electrolyte.172 However, no exact mechanism has been proposed as to how these ions can change the anode performance.
During the performance of an Al anode in LIBs, an ultra thin layer of Al2O3 is formed on the electrode surface.173 As a result, the anode process does not occur at the surface but a sub-surface where the LiAl alloy is formed under the Al2O3 lateral layer. The main problem, which causes capacity fading in the course of cycling, is that the Li atoms can diffuse deep within the Al bulk to spread the LiAl alloy. When the upper layers of the LiAl alloys are subject to dealloying during the discharging process, the lower layer of the LiAl alloys is trapped by an Al layer. Therefore, part of the alloyed Li is no longer electrochemically accessible.
Even when using aluminum as a current collector for the cathode, Al corrosion is an important factor, which should be taken into account. Depending on the electrolyte salt, the Al current collector might not be stable at the cathode redox potential,174 and this causes a self-discharge of the cathode.175 Although this is indeed a different context, it clearly shows the importance of the electrochemistry of Al in the conventional electrolyte, which has yet to be understood.
7 Aluminum supercapacitors
It is known that depending on the redox system, a battery performance may transform into a pseudocapacitive behavior.176,177 Wang et al. inspected the pseudocapacitance of a polypyrrole-coated MoO3 anode for the redox system associated with Al3+.178 When coupling with an activated carbon (AC) cathode, the supercapacitor could deliver a specific capacitance of 693 F g−1, which was three times higher than the supercapacitor performance in a sodium electrolyte.
Li et al. showed that the electrochemical performance of a PB electrode for the intercalation/deintercalation of Al is pseudocapacitive resembling supercapacitors.54 The corresponding Al supercapacitor could deliver a specific capacity of 35 mA h g−1 at 1C discharge rate over a potential window of 0–1.0 V.
8 Summary and outlook
Owing to the excellent performance of the Al anode in ILs, it is believed that the anode and electrolyte for the practical development of AIBs are already available. Of course, pure ILs are too expensive for the fabrication of low-cost batteries, but the target electrolytes are indeed gel polymer electrolytes, which are composed of a small amount of ILs. On the other hand, these solid-like electrolytes provide excellent opportunities for the construction of safe and flexible batteries. In this direction, the key issue is still a suitable intercalation material for the cathode. Noticeable advancement has been made during the past few years, as there are some new candidates under consideration; however, the performance is way below the practical expectations. Not only the specific capacity is much lower than the cathodes of counterpart batteries, but also the cyclability is poor. Nevertheless, this is mainly due to the lack of appropriate research in this area, as a trivalent cation was not a case of study in the realm of solid-state electrochemistry where all the attention has been paid to more conventional electrolytes of Li, Na, K, etc. For most of the well-known electroactive materials, Al intercalation has not even been investigated. As reported for the case of TiO2, Al3+ can be intercalated while other cations such as Li+ and Mg2+ cannot. This indicates that the electroactive materials for the Al3+ intercalation might be different from the available intercalation materials.
From the limited experimental data reported in the literature, it is evident that not only is the intercalation of Al3+ ions much more complicated than that of monovalent ions such as Li+ and K+, but also the Al3+ diffusion within the electrolyte is accompanied by complicated processes. For the conventional intercalation systems, a crystalline lattice structure provides a straightforward opportunity for the diffusion of the counterions, but an amorphous structure is preferred for the intercalation of Al3+. Two reasons might be responsible for this peculiar phenomenon: (i) the lattice structure of common electroactive materials is too small for the diffusion of Al3+ ions (note that the space required is not based on the ion size but its interactions), and (ii) an amorphous architecture provides a less-interactive environment for the diffusing Al3+ ions. On the other hand, Al3+ ions released from the anode will be subject to various complexations within the electrode before the intercalation into the cathode or vice versa. In a similar fashion, it is believed that, at least in many cases, the intercalating ion is not Al3+ but its complex with the accompanying anion.
For Al–air batteries, the operating voltage provides an opportunity for performing in aqueous media. However, the acceptable voltage can only be achieved in alkaline electrolytes in which the aluminum corrosion is significant. Therefore, the research on Al–air batteries is mostly focused on the corrosion inhibition of Al anodes. These studies are also useful for improving the stability of Al current collectors in LIBs since non-aqueous electrolytes are becoming more popular for Al–air batteries too.
In conclusion, there are various opportunities for the development of energy storage systems based on Al charge carriers, as different systems have been examined so far. Although Al batteries are associated with some serious problems, the prototypes of ultrafast batteries with an excellent cyclability are indeed impressive. The present obstacles are severe but should not be considered when judging the prospect of this class of electrochemical energy storage, because most of these systems are less known from an electrochemistry standpoint. It is wrongly believed that there are not many appropriate materials for the Al intercalation, but the fact is that most of the available intercalation materials have been discovered based on the corresponding intercalation of simple monovalent cations. In fact, Al batteries are still in their infancy, despite a long history. The essential step towards the practical development of various Al batteries is to fundamentally understand their underlying mechanism, and then planning the quest for finding practical materials.
References
- S. Tepavcevic, H. Xiong, V. R. Stamenkovic, X. Zuo, M. Balasubramanian, V. B. Prakapenka, C. S. Johnson and T. Rajh, Nanostructured Bilayered Vanadium Oxide Electrodes for Rechargeable Sodium-Ion Batteries, ACS Nano, 2012, 6, 530–538, DOI:10.1021/nn203869a.
- H. Li, X. Yu, Y. Bai, F. Wu, C. Wu, L. Liu and X. Yang, Effects of Mg Doping on the Remarkably Enhanced Electrochemical Performance of Na3V2(PO4)3 Cathode Materials for Sodium Ion Batteries, J. Mater. Chem. A, 2015, 3, 9578–9586, 10.1039/c5ta00277j.
- M. H. Han, E. Gonzalo, G. Singh and T. Rojo, A Comprehensive Review of Sodium Layered Oxides: Powerful Cathodes for Na-Ion Batteries, Energy Environ. Sci., 2015, 8, 81–102, 10.1039/c4ee03192j.
- X. Wang, D. Chen, Z. Yang, X. Zhang, C. Wang, J. Chen, X. Zhang and M. Xue, Novel Metal Chalcogenide SnSSe As a High-Capacity Anode for Sodium-Ion Batteries, Adv. Mater., 2016, 28, 8645–8650, DOI:10.1002/adma.201603219.
- I. Hasa, S. Passerini and J. Hassoun, Characteristics of an Ionic Liquid Electrolyte for Sodium-Ion Batteries, J. Power Sources, 2016, 303, 203–207, DOI:10.1016/j.jpowsour.2015.10.100.
- C. Wu, P. Pan, Y. Cheng, C. Liu, C. Chang, M. Avdeev and S. Lin, The Mechanism of the Sodiation and Desodiation in Super P Carbon Electrode for Sodium-Ion Battery, J. Power Sources, 2017, 340, 14–21, DOI:10.1016/j.jpowsour.2016.11.048.
- H. Su, S. Jaffer and H. Yu, Transition Metal Oxides for Sodium-Ion Batteries, Energy Storage Mater., 2016, 5, 116–131, DOI:10.1016/j.ensm.2016.06.005.
- A. Eftekhari, Z. Jian and X. Ji, Potassium Secondary Batteries, ACS Appl. Mater. Interfaces, 2017, 9, 4404–4419, DOI:10.1021/acsami.6b07989.
- A. Eftekhari, Potassium Secondary Cell Based on Prussian Blue Cathode, J. Power Sources, 2004, 126, 221–228, DOI:10.1016/j.jpowsour.2003.08.007.
- S. Tepavcevic, Y. Liu, D. Zhou, B. Lai, J. Maser, X. Zuo, H. Chan, P. Král, C. S. Johnson, V. Stamenkovic, N. M. Markovic and T. Rajh, Nanostructured Layered Cathode for Rechargeable Mg-Ion Batteries, ACS Nano, 2015, 9, 8194–8205, DOI:10.1021/acsnano.5b02450.
- J. Muldoon, C. B. Bucur, A. G. Oliver, T. Sugimoto, M. Matsui, H. S. Kim, G. D. Allred, J. Zajicek and Y. Kotani, Electrolyte Roadblocks to a Magnesium Rechargeable Battery, Energy Environ. Sci., 2012, 5, 5941–5950, 10.1039/c2ee03029b.
- H. Zhang, K. Ye, X. Huang, X. Wang, K. Cheng, X. Xiao, G. Wang and D. Cao, Preparation of Mg1.1Mn6O12·4.5H2O with Nanobelt Structure and Its Application in Aqueous Magnesium-Ion Battery, J. Power Sources, 2017, 338, 136–144, DOI:10.1016/j.jpowsour.2016.10.078.
- F. Bertasi, F. Sepehr, G. Pagot, S. J. Paddison and V. Di Noto, Toward a Magnesium–Iodine Battery, Adv. Funct. Mater., 2016, 26, 4860–4865, DOI:10.1002/adfm.201601448.
- J. Muldoon, C. B. Bucur and T. Gregory, Quest for Nonaqueous Multivalent Secondary Batteries: Magnesium and Beyond, Chem. Rev., 2014, 114, 11683–11720, DOI:10.1021/cr500049y.
- P. Saha, M. K. Datta, O. I. Velikokhatnyi, A. Manivannan, D. Alman and P. N. Kumta, Rechargeable Magnesium Battery: Current
Status and Key Challenges for the Future, Prog. Mater. Sci., 2014, 66, 1–86, DOI:10.1016/j.pmatsci.2014.04.001.
- P. Reinsberg, C. J. Bondue and H. Baltruschat, Calcium–Oxygen Batteries As a Promising Alternative to Sodium–Oxygen Batteries, J. Phys. Chem. C, 2016, 120, 11219–11226, DOI:10.1021/acs.jpcc.6b06674.
- M. Cabello, F. Nacimiento, J. R. González, G. Ortiz, R. Alcántara, P. Lavela, C. Pérez-Vicente and J. L. Tirado, Advancing Towards a Veritable Calcium-Ion Battery: CaCo2O4 Positive Electrode Material, Electrochem. Commun., 2016, 67, 59–64, DOI:10.1016/j.elecom.2016.03.016.
- T. Tojo, Y. Sugiura, R. Inada and Y. Sakurai, Reversible Calcium Ion Batteries Using a Dehydrated Prussian Blue Analogue Cathode, Electrochim. Acta, 2016, 207, 22–27, DOI:10.1016/j.electacta.2016.04.159.
- A. Ponrouch, C. Frontera, F. Bardé and M. R. Palacin, Towards a Calcium-Based Rechargeable Battery, Nat. Mater., 2015, 15, 169–172, DOI:10.1038/nmat4462.
- Q. Pang, X. Liang, C. Y. Kwok and L. F. Nazar, Advances in Lithium–Sulfur Batteries Based on Multifunctional Cathodes and Electrolytes, Nat. Energy, 2016, 1, 16132, DOI:10.1038/nenergy.2016.132.
- A. Eftekhari, The Rise of Lithium–Selenium Batteries, Sustainable Energy Fuels, 2017, 1, 14–29 Search PubMed.
- G. A. Elia, K. Marquardt, K. Hoeppner, S. Fantini, R. Lin, E. Knipping, W. Peters, J. Drillet, S. Passerini and R. Hahn, An Overview and Future Perspectives of Aluminum Batteries, Adv. Mater., 2016, 28, 7564–7579, DOI:10.1002/adma.201601357.
- E. Shkolnikov, A. Zhuk and M. Vlaskin, Aluminum As Energy Carrier: Feasibility Analysis and Current Technologies Overview, Renewable Sustainable Energy Rev., 2011, 15, 4611–4623, DOI:10.1016/j.rser.2011.07.091.
- D. Egan, C. Ponce de León, R. Wood, R. Jones, K. Stokes and F. Walsh, Developments in Electrode Materials and Electrolytes for Aluminium–Air Batteries, J. Power Sources, 2013, 236, 293–310, DOI:10.1016/j.jpowsour.2013.01.141.
- P. R. Gifford, An Aluminum/Chlorine Rechargeable Cell Employing a Room Temperature Molten Salt Electrolyte, J. Electrochem. Soc., 1988, 135, 650–654, DOI:10.1149/1.2095685.
- S. C. Jung, Y. Kang, D. Yoo, J. W. Choi and Y. Han, Flexible Few-Layered Graphene for the Ultrafast Rechargeable Aluminum-Ion Battery, J. Phys. Chem. C, 2016, 120, 13384–13389, DOI:10.1021/acs.jpcc.6b03657.
- A. Eftekhari, Low Voltage Anode Materials for Lithium-Ion Batteries, Energy Storage Mater., 2017, 7, 157–180, DOI:10.1016/j.ensm.2017.01.009.
- A. Eftekhari, L. Li and Y. Yang, Polyaniline Supercapacitors, J. Power Sources, 2017, 347, 86–107, DOI:10.1016/j.jpowsour.2017.02.054.
- S. Liu, J. J. Hu, N. F. Yan, G. L. Pan, G. R. Li and X. P. Gao, Aluminum Storage Behavior of Anatase TiO2 Nanotube Arrays in Aqueous Solution for Aluminum Ion Batteries, Energy Environ. Sci., 2012, 5, 9743–9746, 10.1039/c2ee22987k.
- Y. Liu, S. Sang, Q. Wu, Z. Lu, K. Liu and H. Liu, The Electrochemical Behavior of Cl− Assisted Al3+ Insertion into Titanium Dioxide Nanotube Arrays in Aqueous Solution for Aluminum Ion Batteries, Electrochim. Acta, 2014, 143, 340–346, DOI:10.1016/j.electacta.2014.08.016.
- S. Myung, M. Kikuchi, C. S. Yoon, H. Yashiro, S. Kim, Y. Sun and B. Scrosati, Black Anatase Titania Enabling Ultra High Cycling Rates for Rechargeable Lithium Batteries, Energy Environ. Sci., 2013, 6, 2609–2614, 10.1039/c3ee41960f.
- Y. J. He, J. F. Peng, W. Chu, Y. Z. Li and D. G. Tong, Black Mesoporous Anatase TiO2 Nanoleaves: A High Capacity and High Rate Anode for Aqueous Al-Ion Batteries, J. Mater. Chem. A, 2014, 2, 1721–1731, 10.1039/c3ta13906a.
- E. Brown, J. Acharya, G. P. Pandey, J. Wu and J. Li, Highly Stable Three Lithium Insertion in Thin V2O5 Shells on Vertically Aligned Carbon Nanofiber Arrays for Ultrahigh-Capacity Lithium Ion Battery Cathodes, Adv. Mater. Interfaces, 2016, 3, 1600824, DOI:10.1002/admi.201600824.
- M. Chen, X. Xia, J. Yuan, J. Yin and Q. Chen, Free-Standing Three-Dimensional Continuous Multilayer V2O5 Hollow Sphere Arrays As High-Performance Cathode for Lithium Batteries, J. Power Sources, 2015, 288, 145–149, DOI:10.1016/j.jpowsour.2015.04.130.
- D. W. Su, S. X. Dou and G. X. Wang, Hierarchical Orthorhombic V2O5 Hollow Nanospheres As High Performance Cathode Materials for Sodium-Ion Batteries, J. Mater. Chem. A, 2014, 2, 11185–11194, 10.1039/c4ta01751j.
- D. B. Le, S. Passerini, F. Coustier, J. Guo, T. Soderstrom, B. B. Owens and W. H. Smyrl, Intercalation of Polyvalent Cations into V2O5 Aerogels, Chem. Mater., 1998, 10, 682–684, DOI:10.1021/cm9705101.
- N. Jayaprakash, S. K. Das and L. A. Archer, The Rechargeable Aluminum-Ion Battery, Chem. Commun., 2011, 47, 12610–12612, 10.1039/c1cc15779e.
- M. Chiku, H. Takeda, S. Matsumura, E. Higuchi and H. Inoue, Amorphous Vanadium Oxide/Carbon Composite Positive Electrode for Rechargeable Aluminum Battery, ACS Appl. Mater. Interfaces, 2015, 7, 24385–24389, DOI:10.1021/acsami.5b06420.
- W. Wang, B. Jiang, W. Xiong, H. Sun, Z. Lin, L. Hu, J. Tu, J. Hou, H. Zhu and S. Jiao, A New Cathode Material for Super-Valent Battery Based on Aluminium Ion Intercalation and Deintercalation, Sci. Rep., 2013, 3, 03383, DOI:10.1038/srep03383.
- L. D. Reed and E. Menke, The Roles of V2O5 and Stainless Steel in Rechargeable Al-Ion Batteries, J. Electrochem. Soc., 2013, 160, A915, DOI:10.1149/2.114306jes.
- S. Gu, H. Wang, C. Wu, Y. Bai, H. Li and F. Wu, Confirming Reversible Al3+ Storage Mechanism Through Intercalation of Al3+ into V2O5 Nanowires in a Rechargeable Aluminum Battery, Energy Storage Mater., 2017, 6, 9–17, DOI:10.1016/j.ensm.2016.09.001.
- J. R. Gonzalez, F. Nacimiento, M. Cabello, R. Alcántara, P. Lavela and J. L. Tirado, Reversible Intercalation of Aluminium into Vanadium Pentoxide Xerogel for Aqueous Rechargeable Batteries, RSC Adv., 2016, 6, 62157–62164, 10.1039/c6ra11030d.
- H. Wang, Y. Bai, S. Chen, X. Luo, C. Wu, F. Wu, J. Lu and K. Amine, Binder-Free V2O5 Cathode for Greener Rechargeable Aluminum Battery, ACS Appl. Mater. Interfaces, 2015, 7, 80–84, DOI:10.1021/am508001h.
- X. Sun, X. Ji, Y. Zhou, Y. Shao, Y. Zang, Z. Wen and C. Chen, A New Gridding Cyanoferrate Anode Material for Lithium and Sodium Ion Batteries: Ti0.75Fe0.25[Fe(CN)6]0.96·1.9H2O with Excellent Electrochemical Properties, J. Power Sources, 2016, 314, 35–38, DOI:10.1016/j.jpowsour.2016.03.011.
- M. Omarova, A. Koishybay, N. Yesibolati, A. Mentbayeva, N. Umirov, K. Ismailov, D. Adair, M. Babaa, I. Kurmanbayeva and Z. Bakenov, Nickel Hexacyanoferrate Nanoparticles As a Low Cost Cathode Material for Lithium-Ion Batteries, Electrochim. Acta, 2015, 184, 58–63, DOI:10.1016/j.electacta.2015.10.031.
- M. H. Wong, Z. Zhang, X. Yang, X. Chen and J. Y. Ying, One-Pot in situ Redox Synthesis of Hexacyanoferrate/Conductive Polymer Hybrids As Lithium-Ion Battery Cathodes, Chem. Commun., 2015, 51, 13674–13677, 10.1039/c5cc04694g.
- M. Xie, Y. Huang, M. Xu, R. Chen, X. Zhang, L. Li and F. Wu, Sodium Titanium Hexacyanoferrate As an Environmentally Friendly and Low-Cost Cathode Material for Sodium-Ion Batteries, J. Power Sources, 2016, 302, 7–12, DOI:10.1016/j.jpowsour.2015.10.042.
- S. Yu, Y. Li, Y. Lu, B. Xu, Q. Wang, M. Yan and Y. Jiang, A Promising Cathode Material of Sodium Iron–Nickel Hexacyanoferrate for Sodium Ion Batteries, J. Power Sources, 2015, 275, 45–49, DOI:10.1016/j.jpowsour.2014.10.196.
- M. Pasta, R. Y. Wang, R. Ruffo, R. Qiao, H. Lee, B. Shyam, M. Guo, Y. Wang, L. A. Wray, W. Yang, M. F. Toney and Y. Cui, Manganese–Cobalt Hexacyanoferrate Cathodes for Sodium-Ion Batteries, J. Mater. Chem. A, 2016, 4, 4211–4223, 10.1039/c5ta10571d.
- P. Padigi, G. Goncher, D. Evans and R. Solanki, Potassium Barium Hexacyanoferrate – a Potential Cathode Material for Rechargeable Calcium Ion Batteries, J. Power Sources, 2015, 273, 460–464, DOI:10.1016/j.jpowsour.2014.09.101.
- A. L. Lipson, B. Pan, S. H. Lapidus, C. Liao, J. T. Vaughey and B. J. Ingram, Rechargeable Ca-Ion Batteries: A New Energy Storage System, Chem. Mater., 2015, 27, 8442–8447, DOI:10.1021/acs.chemmater.5b04027.
- S. Liu, G. L. Pan, G. R. Li and X. P. Gao, Copper Hexacyanoferrate Nanoparticles As Cathode Material for Aqueous Al-Ion Batteries, J. Mater. Chem. A, 2015, 3, 959–962, 10.1039/c4ta04644g.
- L. D. Reed, S. N. Ortiz, M. Xiong and E. J. Menke, A Rechargeable Aluminum-Ion Battery Utilizing a Copper Hexacyanoferrate Cathode in an Organic Electrolyte, Chem. Commun., 2015, 51, 14397–14400, 10.1039/c5cc06053b.
- Z. Li, K. Xiang, W. Xing, W. C. Carter and Y. Chiang, Reversible Aluminum-Ion Intercalation in Prussian Blue Analogs and Demonstration of a High-Power Aluminum-Ion Asymmetric Capacitor, Adv. Energy Mater., 2015, 5, 1401410, DOI:10.1002/aenm.201401410.
- R. Y. Wang, B. Shyam, K. H. Stone, J. Nelson Weker, M. Pasta, H. Lee, M. F. Toney and Y. Cui, Reversible Multivalent (Monovalent, Divalent, Trivalent) Ion Insertion in Open Framework Materials, Adv. Energy Mater., 2015, 5, 1401869, DOI:10.1002/aenm.201401869.
- N. S. Hudak, Chloroaluminate-Doped Conducting Polymers As Positive Electrodes in Rechargeable Aluminum Batteries, J. Phys. Chem. C, 2014, 118, 5203–5215, DOI:10.1021/jp500593d.
- N. Koura, A Preliminary Investigation for an Al/AlCl3–NaCl/FeS2 Secondary Cell, J. Electrochem. Soc., 1980, 127, 1529–1531, DOI:10.1149/1.2129943.
- T. Mori, Y. Orikasa, K. Nakanishi, C. Kezheng, M. Hattori, T. Ohta and Y. Uchimoto, Discharge/Charge Reaction Mechanisms of FeS2 Cathode Material for Aluminum Rechargeable Batteries at 55 °C, J. Power Sources, 2016, 313, 9–14, DOI:10.1016/j.jpowsour.2016.02.062.
- S. Wang, Z. Yu, J. Tu, J. Wang, D. Tian, Y. Liu and S. Jiao, A Novel Aluminum-Ion Battery: Al/AlCl3–[EMIm]Cl/Ni3S2@Graphene, Adv. Energy Mater., 2016, 6, 1600137, DOI:10.1002/aenm.201600137.
- L. Geng, G. Lv, X. Xing and J. Guo, Reversible Electrochemical Intercalation of Aluminum in Mo6S8, Chem. Mater., 2015, 27, 4926–4929, DOI:10.1021/acs.chemmater.5b01918.
- D. Aurbach, Z. Lu, A. Schechter, Y. Gofer, H. Gizbar, R. Turgeman, Y. Cohen, M. Moshkovich and E. Levi, Prototype Systems for Rechargeable Magnesium Batteries, Nature, 2000, 407, 724–727, DOI:10.1038/35037553.
- H. Sun, W. Wang, Z. Yu, Y. Yuan, S. Wang and S. Jiao, A New Aluminium-Ion Battery with High Voltage, High Safety and Low Cost, Chem. Commun., 2015, 51, 11892–11895, 10.1039/c5cc00542f.
- Y. Wu, M. Gong, M. Lin, C. Yuan, M. Angell, L. Huang, D. Wang, X. Zhang, J. Yang, B. Hwang and H. Dai, 3D Graphitic Foams Derived from Chloroaluminate Anion Intercalation for Ultrafast Aluminum-Ion Battery, Adv. Mater., 2016, 28, 9218–9222, DOI:10.1002/adma.201602958.
- M. Lin, M. Gong, B. Lu, Y. Wu, D. Wang, M. Guan, M. Angell, C. Chen, J. Yang, B. Hwang and H. Dai, An Ultrafast Rechargeable Aluminium-Ion Battery, Nature, 2015, 520, 324–328, DOI:10.1038/nature14340.
- M. Wu, B. Xu, L. Chen and C. Ouyang, Geometry and Fast Diffusion of AlCl4 Cluster Intercalated in Graphite, Electrochim. Acta, 2016, 195, 158–165, DOI:10.1016/j.electacta.2016.02.144.
- S. Licht, The Organic Phase for Aluminum Batteries, Electrochem. Solid-State Lett., 1999, 2, 262–264, DOI:10.1149/1.1390805.
- Y. Matsuda, Y. ŌOuchi and H. Tamura, Anodic Polarization of Aluminium in Organic Electrolytes, J. Appl. Electrochem., 1974, 4, 53–56, DOI:10.1007/bf00615905.
- G. Levitin, C. Yarnitzky and S. Licht, Fluorinated Graphites As Energetic Cathodes for Nonaqueous Al Batteries, Electrochem. Solid-State Lett., 2002, 5, A160, DOI:10.1149/1.1481797.
- Y. Zhao and T. Vandernoot, Electrodeposition of Aluminium from Nonaqueous Organic Electrolytic Systems and Room Temperature Molten Salts, Electrochim. Acta, 1997, 42, 3–13, DOI:10.1016/0013-4686(96)00080-1.
- T. Jiang, M. Chollier Brym, G. Dubé, A. Lasia and G. Brisard, Electrodeposition of Aluminium from Ionic Liquids: Part I—Electrodeposition and Surface Morphology of Aluminium from Aluminium Chloride (AlCl3)–1-Ethyl-3-Methylimidazolium Chloride ([EMIm]Cl) Ionic Liquids, Surf. Coat. Technol., 2006, 201, 1–9, DOI:10.1016/j.surfcoat.2005.10.046.
- W. Simka, D. Puszczyk and G. Nawrat, Electrodeposition of Metals from Non-Aqueous Solutions, Electrochim. Acta, 2009, 54, 5307–5319, DOI:10.1016/j.electacta.2009.04.028.
- T. Jiang, M. Chollier Brym, G. Dubé, A. Lasia and G. Brisard, Electrodeposition of Aluminium from Ionic Liquids: Part II – Studies on the Electrodeposition of Aluminum from Aluminum Chloride (AICl3) – Trimethylphenylammonium Chloride (TMPAC) Ionic Liquids, Surf. Coat. Technol., 2006, 201, 10–18, DOI:10.1016/j.surfcoat.2005.12.024.
- M. Angell, C. Pan, Y. Rong, C. Yuan, M. Lin, B. Hwang and H. Dai, High Coulombic Efficiency Aluminum-Ion Battery Using an AlCl3–Urea Ionic Liquid Analog Electrolyte, Proc. Natl. Acad. Sci. U. S. A., 2017, 114, 834–839, DOI:10.1073/pnas.1619795114.
- F. Endres, Ionic Liquids: Solvents for the Electrodeposition of Metals and Semiconductors, ChemPhysChem, 2002, 3, 144–154, DOI:10.1002/1439-7641(20020215)3:2<144::AID-CPHC144>3.0.CO;2-#.
- S. Zein El Abedin and F. Endres, Electrodeposition of Metals and Semiconductors in Air- and Water-Stable Ionic Liquids, ChemPhysChem, 2006, 7, 58–61, DOI:10.1002/cphc.200500288.
- H. M. A. Abood, A. P. Abbott, A. D. Ballantyne and K. S. Ryder, Do All Ionic Liquids Need
Organic Cations? Characterisation of [AlCl2·nAmide]+AlCl4− and Comparison with Imidazolium Based Systems, Chem. Commun., 2011, 47, 3523–3525, 10.1039/c0cc04989a.
- Y. Fang, K. Yoshii, X. Jiang, X. Sun, T. Tsuda, N. Mehio and S. Dai, An AlCl3 Based Ionic Liquid with a Neutral Substituted Pyridine Ligand for Electrochemical Deposition of Aluminum, Electrochim. Acta, 2015, 160, 82–88, DOI:10.1016/j.electacta.2015.02.020.
- Y. Fang, X. Jiang, X. Sun and S. Dai, New Ionic Liquids Based on the Complexation of Dipropyl Sulfide and AlCl3 for Electrodeposition of Aluminum, Chem. Commun., 2015, 51, 13286–13289, 10.1039/c5cc05233e.
- L. D. Reed, A. Arteaga and E. J. Menke, A Combined Experimental and Computational Study of an Aluminum Triflate/Diglyme Electrolyte, J. Phys. Chem. B, 2015, 119, 12677–12681, DOI:10.1021/acs.jpcb.5b08501.
- G. Kamath, B. Narayanan and S. K. R. S. Sankaranarayanan, Atomistic Origin of Superior Performance of Ionic Liquid Electrolytes for Al-Ion Batteries, Phys. Chem. Chem. Phys., 2014, 16, 20387–20391, 10.1039/c4cp02840f.
- X. Sun, Y. Fang, X. Jiang, K. Yoshii, T. Tsuda and S. Dai, Polymer Gel Electrolytes for Application in Aluminum Deposition and Rechargeable Aluminum Ion Batteries, Chem. Commun., 2016, 52, 292–295, 10.1039/c5cc06643c.
- H. Wang, S. Gu, Y. Bai, S. Chen, F. Wu and C. Wu, High-Voltage and Noncorrosive Ionic Liquid Electrolyte Used in Rechargeable Aluminum Battery, ACS Appl. Mater. Interfaces, 2016, 8, 13384–13389, DOI:10.1021/acsami.6b10579.
- A. Eftekhari, Y. Liu and P. Chen, Different Roles of Ionic Liquids in Lithium Batteries, J. Power Sources, 2016, 334, 221–239, DOI:10.1016/j.jpowsour.2016.10.025.
- J. V. Rani, V. Kanakaiah, T. Dadmal, M. S. Rao and S. Bhavanarushi, Fluorinated Natural Graphite Cathode for Rechargeable Ionic Liquid Based Aluminum-Ion Battery, J. Electrochem. Soc., 2013, 160, A1781, DOI:10.1149/2.072310jes.
- D. Peramunage and S. Licht, A Solid Sulfur Cathode for Aqueous Batteries, Science, 1993, 261, 1029–1032, DOI:10.1126/science.261.5124.1029.
- S. Xia, X. Zhang, K. Huang, Y. Chen and Y. Wu, Ionic Liquid Electrolytes for Aluminium Secondary Battery: Influence of Organic Solvents, J. Electroanal. Chem., 2015, 757, 167–175, DOI:10.1016/j.jelechem.2015.09.022.
- G. Cohn, L. Ma and L. A. Archer, A Novel Non-Aqueous Aluminum Sulfur Battery, J. Power Sources, 2015, 283, 416–422, DOI:10.1016/j.jpowsour.2015.02.131.
- X. Zhang, S. H. Yang and H. Knickle, Novel Operation and Control of an Electric Vehicle Aluminum/Air Battery System, J. Power Sources, 2004, 128, 331–342, DOI:10.1016/j.jpowsour.2003.09.058.
- L. D. Chen, J. K. Nørskov and A. C. Luntz, Al–Air Batteries: Fundamental Thermodynamic Limitations from First-Principles Theory, J. Phys. Chem. Lett., 2015, 6, 175–179, DOI:10.1021/jz502422v.
- E. Davydova, I. Atamanyuk, A. Ilyukhin, E. Shkolnikov and A. Zhuk, Nitrogen-Doped Carbonaceous Catalysts for Gas-Diffusion Cathodes for Alkaline Aluminum–Air Batteries, J. Power Sources, 2016, 306, 329–336, DOI:10.1016/j.jpowsour.2015.11.112.
- G. Y. Yang, L. Chen, P. Jiang, Z. Y. Guo, W. Wang and Z. P. Liu, Fabrication of Tunable 3D Graphene Mesh Network with Enhanced Electrical and Thermal Properties for High-Rate Aluminum-Ion Battery Application, RSC Adv., 2016, 6, 47655–47660, 10.1039/c6ra06467a.
- S. Li, H. Miao, Q. Xu, Y. Xue, S. Sun, Q. Wang and Z. Liu, Silver Nanoparticles Supported on a Nitrogen-Doped Graphene Aerogel Composite Catalyst for an Oxygen Reduction Reaction in Aluminum Air Batteries, RSC Adv., 2016, 6, 99179–99183, 10.1039/c6ra23049k.
- M. Wang, Y. Lai, J. Fang, J. Li, F. Qin, K. Zhang and H. Lu, N-Doped Porous Carbon Derived from Biomass As an Advanced Electrocatalyst for Aqueous Aluminium/Air Battery, Int. J. Hydrogen Energy, 2015, 40, 16230–16237, DOI:10.1016/j.ijhydene.2015.09.054.
- Y. Liu, J. Li, W. Li, Y. Li, Q. Chen and Y. Liu, Spinel LiMn2O4 Nanoparticles Dispersed on Nitrogen-Doped Reduced Graphene Oxide Nanosheets As an Efficient Electrocatalyst for Aluminium–Air Battery, Int. J. Hydrogen Energy, 2015, 40, 9225–9234, DOI:10.1016/j.ijhydene.2015.05.153.
- Y. Kuo, C. Wu, W. Chang, C. Yang and H. Chou, Study of Poly(3,4-Ethylenedioxythiophene)/MnO2 As Composite Cathode Materials for Aluminum–Air Battery, Electrochim. Acta, 2015, 176, 1324–1331, DOI:10.1016/j.electacta.2015.07.151.
- Y. Xu, Y. Zhao, J. Ren, Y. Zhang and H. Peng, An All-Solid-State Fiber-Shaped Aluminum–Air Battery with Flexibility, Stretchability, and High Electrochemical Performance, Angew. Chem., Int. Ed., 2016, 55, 7979–7982, DOI:10.1002/anie.201601804.
- S. Sun, H. Miao, Y. Xue, Q. Wang, S. Li and Z. Liu, Oxygen Reduction Reaction Catalysts of Manganese Oxide Decorated by Silver Nanoparticles for Aluminum–Air Batteries, Electrochim. Acta, 2016, 214, 49–55, DOI:10.1016/j.electacta.2016.07.127.
- S. Zein El Abedin and A. Saleh, Characterization of Some Aluminium Alloys for Application As Anodes in Alkaline Batteries, J. Appl. Electrochem., 2004, 34, 331–335, DOI:10.1023/b:jach.0000015611.65219.64.
- M. Krishnan and N. Subramanyan, The Influence of Some Aldehydes on the Corrosion and Anodic Behaviour of Aluminium in Sodium Hydroxide Solution, Corros. Sci., 1977, 17, 893–900, DOI:10.1016/0010-938X(77)90095-6.
- M. Paramasivam and S. V. Iyer, Influence of Alloying Additives on Corrosion and Hydrogen Permeation Through Commercial Aluminium in Alkaline Solution, J. Appl. Electrochem., 2001, 31, 115–119, DOI:10.1023/a:1004194832336.
- D. D. Macdonald and C. English, Development of Anodes for Aluminium/Air Batteries? Solution Phase Inhibition of Corrosion, J. Appl. Electrochem., 1990, 20, 405–417, DOI:10.1007/bf01076049.
- Y. Ein-Eli, M. Auinat and D. Starosvetsky, Electrochemical and Surface Studies of Zinc in Alkaline Solutions Containing Organic Corrosion Inhibitors, J. Power Sources, 2003, 114, 330–337, DOI:10.1016/S0378-7753(02)00598-0.
- A. Maayta and N. Al-Rawashdeh, Inhibition of Acidic Corrosion of Pure Aluminum by Some Organic Compounds, Corros. Sci., 2004, 46, 1129–1140, DOI:10.1016/j.corsci.2003.09.009.
- R. Mori, A Novel Aluminium–air Secondary Battery with Long-Term Stability, RSC Adv., 2014, 4, 1982–1987, 10.1039/c3ra44659j.
- R. Mori, Capacity Recovery of Aluminium–Air Battery by Refilling Salty Water with Cell Structure Modification, J. Appl. Electrochem., 2015, 45, 821–829, DOI:10.1007/s10800-015-0834-z.
- C. Wang, K. Hsueh and C. Hsieh, The Kinetic Reaction of Aluminum–Air Battery in Different Aqueous Solution, ECS Trans., 2013, 50, 29–35, DOI:10.1149/05025.0029ecst.
- V. Kapali, S. V. Iyer, V. Balaramachandran, K. Sarangapani, M. Ganesan, M. A. Kulandainathan and A. S. Mideen, Studies on the Best Alkaline Electrolyte for Aluminium/Air Batteries, J. Power Sources, 1992, 39, 263–269, DOI:10.1016/0378-7753(92)80147-4.
- J. B. Wang, J. M. Wang, H. B. Shao, X. T. Chang, L. Wang, J. Q. Zhang and C. N. Cao, The Corrosion and Electrochemical Behavior of Pure Aluminum in Additive-Containing Alkaline Methanol–Water Mixed Solutions, Mater. Corros., 2009, 60, 269–273, DOI:10.1002/maco.200805074.
- D. Gelman, I. Lasman, S. Elfimchev, D. Starosvetsky and Y. Ein-Eli, Aluminum Corrosion Mitigation in Alkaline Electrolytes
Containing Hybrid Inorganic/Organic Inhibitor System for Power Sources Applications, J. Power Sources, 2015, 285, 100–108, DOI:10.1016/j.jpowsour.2015.03.048.
- J. Liu, D. Wang, D. Zhang, L. Gao and T. Lin, Synergistic Effects of Carboxymethyl Cellulose and ZnO As Alkaline Electrolyte Additives for Aluminium Anodes with a View Towards Al–Air Batteries, J. Power Sources, 2016, 335, 1–11, DOI:10.1016/j.jpowsour.2016.09.060.
- D. Wang, H. Li, J. Liu, D. Zhang, L. Gao and L. Tong, Evaluation of AA5052 Alloy Anode in Alkaline Electrolyte with Organic Rare-Earth Complex Additives for Aluminium–Air Batteries, J. Power Sources, 2015, 293, 484–491, DOI:10.1016/j.jpowsour.2015.05.104.
- E. Grishina, D. Gelman, S. Belopukhov, D. Starosvetsky, A. Groysman and Y. Ein-Eli, Improvement of Aluminum–Air Battery Performances by the Application of Flax Straw Extract, ChemSusChem, 2016, 9, 2103–2111, DOI:10.1002/cssc.201600298.
- J. Ma, J. Wen, J. Gao and Q. Li, Performance of Al–0.5 Mg–0.02 Ga–0.1 Sn–0.5 Mn As Anode for Al–Air Battery in NaCl Solutions, J. Power Sources, 2014, 253, 419–423, DOI:10.1016/j.jpowsour.2013.12.053.
- Y. Tang, L. Lu, H. W. Roesky, L. Wang and B. Huang, The Effect of Zinc on the Aluminum Anode of the Aluminum–Air Battery, J. Power Sources, 2004, 138, 313–318, DOI:10.1016/j.jpowsour.2004.06.043.
- I. Smoljko, S. Gudić, N. Kuzmanić and M. Kliškić, Electrochemical Properties of Aluminium Anodes for Al/Air Batteries with Aqueous Sodium Chloride Electrolyte, J. Appl. Electrochem., 2012, 42, 969–977, DOI:10.1007/s10800-012-0465-6.
- A. R. Despić, D. M. Dražić, M. M. Purenović and N. Ciković, Electrochemical Properties of Aluminium Alloys Containing Indium, Gallium and Thallium, J. Appl. Electrochem., 1976, 6, 527–542, DOI:10.1007/bf00614541.
- R. Kühnel, D. Reber, A. Remhof, R. Figi, D. Bleiner and C. Battaglia, “Water-In-Salt” Electrolytes Enable the Use of Cost-Effective Aluminum Current Collectors for Aqueous High-Voltage Batteries, Chem. Commun., 2016, 52, 10435–10438, 10.1039/c6cc03969c.
- R. Mori, A New Structured Aluminium–air Secondary Battery with a Ceramic Aluminium Ion Conductor, RSC Adv., 2013, 3, 11547–11551, 10.1039/c3ra42211a.
- R. Mori, A Novel Aluminium–Air Rechargeable Battery with Al2O3 As the Buffer to Suppress Byproduct Accumulation Directly Onto an Aluminium Anode and Air Cathode, RSC Adv., 2014, 4, 30346–30351, 10.1039/c4ra02165g.
- D. Gelman, B. Shvartsev and Y. Ein-Eli, Aluminum–Air Battery Based on an Ionic Liquid Electrolyte, J. Mater. Chem. A, 2014, 2, 20237–20242, 10.1039/c4ta04721d.
- G. Cohn, D. Starosvetsky, R. Hagiwara, D. D. Macdonald and Y. Ein-Eli, Silicon–Air Batteries, Electrochem. Commun., 2009, 11, 1916–1918, DOI:10.1016/j.elecom.2009.08.015.
- G. Cohn and Y. Ein-Eli, Study and Development of Non-Aqueous Silicon–Air Battery, J. Power Sources, 2010, 195, 4963–4970, DOI:10.1016/j.jpowsour.2010.02.070.
- Y. Nakayama, Y. Senda, H. Kawasaki, N. Koshitani, S. Hosoi, Y. Kudo, H. Morioka and M. Nagamine, Sulfone-Based Electrolytes for Aluminium Rechargeable Batteries, Phys. Chem. Chem. Phys., 2015, 17, 5758–5766, 10.1039/c4cp02183e.
- B. Shvartsev, D. Gelman, D. Amram and Y. Ein-Eli, Phenomenological Transition of an Aluminum Surface in an Ionic Liquid and Its Beneficial Implementation in Batteries, Langmuir, 2015, 31, 13860–13866, DOI:10.1021/acs.langmuir.5b03362.
- A. Mohamad, Electrochemical Properties of Aluminum Anodes in Gel Electrolyte-Based Aluminum–Air Batteries, Corros. Sci., 2008, 50, 3475–3479, DOI:10.1016/j.corsci.2008.09.001.
- Z. Zhang, C. Zuo, Z. Liu, Y. Yu, Y. Zuo and Y. Song, All-Solid-State Al–Air Batteries with Polymer Alkaline Gel Electrolyte, J. Power Sources, 2014, 251, 470–475, DOI:10.1016/j.jpowsour.2013.11.020.
- M. Pino, J. Chacon, E. Fatás and P. Ocón, Performance of Commercial Aluminium Alloys As Anodes in Gelled Electrolyte Aluminium–Air Batteries, J. Power Sources, 2015, 299, 195–201, DOI:10.1016/j.jpowsour.2015.08.088.
- T. Hibino, K. Kobayashi and M. Nagao, An All-Solid-State Rechargeable Aluminum–air Battery with a Hydroxide Ion-Conducting Sb(V)-Doped SnP2O7 Electrolyte, J. Mater. Chem. A, 2013, 1, 14844–14848, 10.1039/c3ta12707a.
- H. Moghanni-Bavil-Olyaei and J. Arjomandi, Enhanced Electrochemical Performance of Al–0.9Mg–1Zn–0.1Mn–0.05Bi–0.02In Fabricated from Commercially Pure Aluminum for Use As the Anode of Alkaline Batteries, RSC Adv., 2016, 6, 28055–28062, 10.1039/c6ra02113a.
- J. Ma, J. Wen, J. Gao and Q. Li, Performance of Al–1Mg–1Zn–0.1Ga–0.1Sn As Anode for Al–Air Battery, Electrochim. Acta, 2014, 129, 69–75, DOI:10.1016/j.electacta.2014.02.080.
- H. Moghanni-Bavil-Olyaei and J. Arjomandi, Performance of Al–1Mg–1Zn–0.1Bi–0.02In As Anode for the Al–AgO Battery, RSC Adv., 2015, 5, 91273–91279, 10.1039/c5ra15567c.
- M. Nestoridi, D. Pletcher, R. J. Wood, S. Wang, R. L. Jones, K. R. Stokes and I. Wilcock, The Study of Aluminium Anodes for High Power Density Al/Air Batteries with Brine Electrolytes, J. Power Sources, 2008, 178, 445–455, DOI:10.1016/j.jpowsour.2007.11.108.
- M. Mokhtar, M. Z. Meor Talib, E. H. Majlan, S. M. Tasirin, W. M. F. W. Ramli, W. R. W. Daud and J. Sahari, Recent Developments in Materials for Aluminum–Air Batteries: A Review, J. Ind. Eng. Chem., 2015, 32, 1–20, DOI:10.1016/j.jiec.2015.08.004.
- J. Ma, J. Wen, J. Gao and Q. Li, Performance of Al-0.5 Mg-0.02 Ga-0.1 Sn-0.5 Mn As Anode for Al–Air Battery, J. Electrochem. Soc., 2014, 161, A376, DOI:10.1149/2.074403jes.
- Z. Sun and H. Lu, Performance of Al-0.5In As Anode for Al–Air Battery in Inhibited Alkaline Solutions, J. Electrochem. Soc., 2015, 162, A1617, DOI:10.1149/2.0881508jes.
- Z. Sun, H. Lu, L. Fan, Q. Hong, J. Leng and C. Chen, Performance of Al–Air Batteries Based on Al–Ga, Al–In and Al–Sn Alloy Electrodes, J. Electrochem. Soc., 2015, 162, A2116, DOI:10.1149/2.0681510jes.
- L. Fan, H. Lu, J. Leng and Z. Sun, Performance of Al-0.6 Mg-0.05 Ga-0.1 Sn-0.1 in As Anode for Al–Air Battery in KOH Electrolytes, J. Electrochem. Soc., 2015, 162, A2623, DOI:10.1149/2.0871512jes.
- M. Jingling, W. Jiuba, Z. Hongxi and L. Quanan, Electrochemical Performances of Al–0.5Mg–0.1Sn–0.02In Alloy in Different Solutions for Al–Air Battery, J. Power Sources, 2015, 293, 592–598, DOI:10.1016/j.jpowsour.2015.05.113.
- A. S. Mideen, M. Ganesan, M. Anbukulandainathan, K. Sarangapani, V. Balaramachandran, V. Kapali and S. V. Iyer, Development of New Alloys of Commercial Aluminium (2S) with Zinc, Indium, Tin, and Bismuth As Anodes for Alkaline Batteries, J. Power Sources, 1989, 27, 235–244, DOI:10.1016/0378-7753(89)80038-2.
- J. Wen, J. He and X. Lu, Influence of Silicon on the Corrosion Behaviour of Al–Zn–In–Mg–Ti Sacrificial Anode, Corros. Sci., 2011, 53, 3861–3865, DOI:10.1016/j.corsci.2011.07.039.
- Y. Cho, I. Park, H. Lee and J. Kim, Aluminum Anode for Aluminum–Air Battery – Part I: Influence of Aluminum Purity, J. Power Sources, 2015, 277, 370–378, DOI:10.1016/j.jpowsour.2014.12.026.
- R. Mori, Addition of Ceramic Barriers
to Aluminum–Air Batteries to Suppress By-Product Formation on Electrodes, J. Electrochem. Soc., 2014, 162, A288, DOI:10.1149/2.0241503jes.
- M. Pino, D. Herranz, J. Chacon, E. Fatás and P. Ocón, Carbon Treated Commercial Aluminium Alloys As Anodes for Aluminium–Air Batteries in Sodium Chloride Electrolyte, J. Power Sources, 2016, 326, 296–302, DOI:10.1016/j.jpowsour.2016.06.118.
- A. Mukherjee and I. N. Basumallick, Complex Behaviour of Aluminium Dissolution in Alkaline Aqueous 2-Propanol Solution, J. Power Sources, 1996, 58, 183–187, DOI:10.1016/S0378-7753(96)02388-9.
- L. Fan, H. Lu, J. Leng, Z. Sun and C. Chen, The Effect of Crystal Orientation on the Aluminum Anodes of the Aluminum–Air Batteries in Alkaline Electrolytes, J. Power Sources, 2015, 299, 66–69, DOI:10.1016/j.jpowsour.2015.08.095.
- A. Eftekhari, Electrocatalysts for Hydrogen Evolution Reaction, Int. J. Hydrogen Energy, 2017, 42(16), 11053–11077 CrossRef CAS.
- L. Fan and H. Lu, The Effect of Grain Size on Aluminum Anodes for Al–Air Batteries in Alkaline Electrolytes, J. Power Sources, 2015, 284, 409–415, DOI:10.1016/j.jpowsour.2015.03.063.
- L. Fan, H. Lu, J. Leng, Z. Sun and C. Chen, The Study of Industrial Aluminum Alloy As Anodes for Aluminum–Air Batteries in Alkaline Electrolytes, J. Electrochem. Soc., 2016, 163, A8, DOI:10.1149/2.0021602jes.
- M. Pino, C. Cuadrado, J. Chacón, P. Rodríguez, E. Fatás and P. Ocón, The Electrochemical Characteristics of Commercial Aluminium Alloy Electrodes for Al/Air Batteries, J. Appl. Electrochem., 2014, 44, 1371–1380, DOI:10.1007/s10800-014-0751-6.
- D. Wang, D. Zhang, K. Lee and L. Gao, Performance of AA5052 Alloy Anode in Alkaline Ethylene Glycol Electrolyte with Dicarboxylic Acids Additives for Aluminium–Air Batteries, J. Power Sources, 2015, 297, 464–471, DOI:10.1016/j.jpowsour.2015.08.033.
- M. Doche, F. Novel-Cattin, R. Durand and J. Rameau, Characterization of Different Grades of Aluminum Anodes for Aluminum/Air Batteries, J. Power Sources, 1997, 65, 197–205, DOI:10.1016/S0378-7753(97)02473-7.
- L. Fan, H. Lu and J. Leng, Performance of Fine Structured Aluminum Anodes in Neutral and Alkaline Electrolytes for Al–Air Batteries, Electrochim. Acta, 2015, 165, 22–28, DOI:10.1016/j.electacta.2015.03.002.
- C. Li, W. Ji, J. Chen and Z. Tao, Metallic Aluminum Nanorods: Synthesis via Vapor-Deposition and Applications in Al/Air Batteries, Chem. Mater., 2007, 19, 5812–5814, DOI:10.1021/cm7018795.
- S. Licht, Novel Aluminum Batteries: A Step Towards Derivation of Superbatteries, Colloids Surf., A, 1998, 134, 241–248, DOI:10.1016/S0927-7757(97)00329-4.
- S. Licht, Novel Aqueous Aluminum/Sulfur Batteries, J. Electrochem. Soc., 1993, 140, L4, DOI:10.1149/1.2056120.
- D. Peramunage, R. Dillon and S. Licht, Investigation of a Novel Aqueous Aluminum/Sulfur Battery, J. Power Sources, 1993, 45, 311–323, DOI:10.1016/0378-7753(93)80020-P.
- S. Licht, A High Energy and Power Novel Aluminum/Nickel Battery, J. Electrochem. Soc., 1995, 142, L179, DOI:10.1149/1.2050036.
- F. M. Donahue, S. E. Mancini and L. Simonsen, Secondary Aluminium–Iron(III) Chloride Batteries with a Low Temperature Molten Salt Electrolyte, J. Appl. Electrochem., 1992, 22, 230–234, DOI:10.1007/bf01030182.
- C. Bonatti and D. Mohr, Anisotropic Viscoplasticity and Fracture of Fine Grained Metallic Aluminum Foil Used in Li-Ion Batteries, Mater. Sci. Eng., A, 2016, 654, 329–343, DOI:10.1016/j.msea.2015.11.048.
- A. Hofmann, L. Merklein, M. Schulz and T. Hanemann, Anodic Aluminum Dissolution of LiTFSA Containing Electrolytes for Li-Ion-Batteries, Electrochim. Acta, 2014, 116, 388–395, DOI:10.1016/j.electacta.2013.11.085.
- G. Oltean, M. Valvo, L. Nyholm and K. Edström, On the Electrophoretic and Sol–Gel Deposition of Active Materials on Aluminium Rod Current Collectors for Three-Dimensional Li-Ion Micro-Batteries, Thin Solid Films, 2014, 562, 63–69, DOI:10.1016/j.tsf.2014.03.069.
- F. Zhang, B. Ji, X. Tong, M. Sheng, X. Zhang, C. Lee and Y. Tang, A Dual-Ion Battery Constructed with Aluminum Foil Anode and Mesocarbon Microbead Cathode via an Alloying/Intercalation Process in an Ionic Liquid Electrolyte, Adv. Mater. Interfaces, 2016, 3, 1600605, DOI:10.1002/admi.201600605.
- A. Eftekhari, Aluminum Oxide As a Multi-Function Agent for Improving Battery Performance of LiMn2O4 Cathode, Solid State Ionics, 2004, 167, 237–242, DOI:10.1016/j.ssi.2004.01.016.
- X. Zhang, Y. Tang, F. Zhang and C. Lee, A Novel Aluminum–Graphite Dual-Ion Battery, Adv. Energy Mater., 2016, 6, 1502588, DOI:10.1002/aenm.201502588.
- E. C. Gay, Performance Characteristics of Solid Lithium–Aluminum Alloy Electrodes, J. Electrochem. Soc., 1976, 123, 1591, DOI:10.1149/1.2132652.
- C. J. Wen, Thermodynamic and Mass Transport Properties of “LiAl”, J. Electrochem. Soc., 1979, 126, 2258, DOI:10.1149/1.2128939.
- N. Nitta and G. Yushin, High-Capacity Anode Materials for Lithium-Ion Batteries: Choice of Elements and Structures for Active Particles, Part. Part. Syst. Charact., 2014, 31, 317–336, DOI:10.1002/ppsc.201300231.
- J. H. Park, C. Hudaya, A. Kim, D. K. Rhee, S. J. Yeo, W. Choi, P. J. Yoo and J. K. Lee, Al–C Hybrid Nanoclustered Anodes for Lithium Ion Batteries with High Electrical Capacity and Cyclic Stability, Chem. Commun., 2014, 50, 2837–2840, 10.1039/c3cc47900e.
- Y. Liu, N. S. Hudak, D. L. Huber, S. J. Limmer, J. P. Sullivan and J. Y. Huang,
In situ Transmission Electron Microscopy Observation of Pulverization of Aluminum Nanowires and Evolution of the Thin Surface Al2O3 Layers During Lithiation–Delithiation Cycles, Nano Lett., 2011, 11, 4188–4194, DOI:10.1021/nl202088h.
- S. Li, J. Niu, Y. C. Zhao, K. P. So, C. Wang, C. A. Wang and J. Li, High-Rate Aluminium Yolk-Shell Nanoparticle Anode for Li-Ion Battery with Long Cycle Life and Ultrahigh Capacity, Nat. Commun., 2015, 6, 7872, DOI:10.1038/ncomms8872.
- M. Au, S. McWhorter, H. Ajo, T. Adams, Y. Zhao and J. Gibbs, Free Standing Aluminum Nanostructures As Anodes for Li-Ion Rechargeable Batteries, J. Power Sources, 2010, 195, 3333–3337, DOI:10.1016/j.jpowsour.2009.11.102.
- X. Sun, Z. Bi, H. Liu, Y. Fang, C. A. Bridges, M. P. Paranthaman, S. Dai and G. M. Brown, A High Performance Hybrid Battery Based on Aluminum Anode and LiFePO4 Cathode, Chem. Commun., 2016, 52, 1713–1716, 10.1039/c5cc09019a.
- G. Oltean, C. Tai, K. Edström and L. Nyholm, On the Origin of the Capacity Fading for Aluminium Negative Electrodes in Li-Ion Batteries, J. Power Sources, 2014, 269, 266–273, DOI:10.1016/j.jpowsour.2014.06.118.
- S. Zhang and T. Jow, Aluminum Corrosion in Electrolyte of Li-Ion Battery, J. Power Sources, 2002, 109, 458–464, DOI:10.1016/S0378-7753(02)00110-6.
- S. Zhang, M. S. Ding and T. Jow, Self-Discharge of Li/LixMn2O4 Batteries in Relation to Corrosion of Aluminum Cathode Substrates, J. Power Sources, 2001, 102, 16–20, DOI:10.1016/S0378-7753(01)00781-9.
- A. Eftekhari and F. Molaei, Carbon Nanotube-Assisted Electrodeposition. Part I: Battery Performance of Manganese Oxide Films Electrodeposited at Low Current Densities, J. Power Sources, 2015, 274, 1306–1314, DOI:10.1016/j.jpowsour.2013.10.136.
- A. Eftekhari and F. Molaei, Carbon Nanotube-Assisted Electrodeposition. Part II: Superior Pseudo-Capacitive Behavior of Manganese Oxide Film Electrodeposited at High Current Densities, J. Power Sources, 2015, 274, 1315–1321, DOI:10.1016/j.jpowsour.2013.10.144.
- F. Wang, Z. Liu, X. Wang, X. Yuan, X. Wu, Y. Zhu, L. Fu and Y. Wu, A Conductive Polymer Coated MoO3 Anode Enables an Al-Ion Capacitor with High Performance, J. Mater. Chem. A, 2016, 4, 5115–5123, 10.1039/c6ta01398h.
- H. Wang, S. Gu, Y. Bai, S. Chen, N. Zhu, C. Wu and F. Wu, Anion-Effects on Electrochemical Properties of Ionic Liquid Electrolytes for Rechargeable Aluminum Batteries, J. Mater. Chem. A, 2015, 3, 22677–22686, 10.1039/c5ta06187c.
|
This journal is © The Royal Society of Chemistry 2017 |
Click here to see how this site uses Cookies. View our privacy policy here.