DOI:
10.1039/C7RA11031F
(Paper)
RSC Adv., 2017,
7, 55547-55554
Potential waste from palm empty fruit bunches and eggshells as a heterogeneous catalyst for biodiesel production
Received
7th October 2017
, Accepted 26th November 2017
First published on 7th December 2017
Abstract
Biodiesel is one of the potential alternative energies produced from a variety of vegetable oils. The utilization of a CaO/SiO2 catalyst generated from eggshell and palm empty fruit bunch (PEFB) waste for biodiesel production from waste cooking oil was investigated. The optimum silica yield extracted from PEFB was 68.2% using 10% NaOH (w/v) at 80 °C for 1 h. Methanol with a mol ratio of 14 to waste cooking oil was used. The presence of a silica support in the CaO catalyst increased the yield of biodiesel from 78% to 96%. Three runs of the catalyst led to only a 1% reduction in biodiesel yield. The utilization of activated PEFB as a support showed a potential result with a biodiesel yield of 83%. The prospective heterogeneous catalysts were also characterized by using XRD, SEM, BET and FT-IR. The developed CaO/SiO2 stands out as a promising catalyst for biodiesel production due to the utilization of abundant and cheap waste materials. Moreover, a significant yield of biodiesel was obtained using the catalyst; hence, it is feasible to be developed on a larger scale.
Introduction
An increased demand for energy has arisen due to increased industrial development, transportation, and human growth. The availability of conventional energy sources such as petroleum, coal and natural gas will eventually be exhausted. Fuel from renewable energy such as biodiesel is one of the solutions to replace the limited fossil fuels.1 On the other hand, the use of fossil fuels can lead to the greenhouse effect from gas emissions and other environmental pollution. Biodiesel is a renewable, sustainable and non-toxic fuel that can reduce the problems of fossil fuel utilization.2 The main raw material of biodiesel production is commonly vegetable oils such as palm oil, soy, corn, etc.3 However, the use of vegetable oils is less attractive due to its competitiveness with the fulfilment of food requirements.4 Currently, researchers are attempting to develop biodiesel production processes from various waste materials, like used cooking oil. Waste cooking oil is an abundant and low-cost material;5 however, the high levels of free fatty acids (FFAs) in the oil will be a challenge for researchers.
Biodiesel is generally produced by using homogeneous catalysts such as NaOH and KOH.6 However, the purification process required is expensive due to the difficulty in handling the separation of the catalyst from the product.1 Moreover, the catalyst cannot be recovered for reuse; as a result, it is simply disposed of as waste and causes environmental contamination.7 This issue can be resolved by using a heterogeneous catalyst. Nowadays, researchers are extensively developing biodiesel processes using heterogeneous catalysts.1,7,8 Recently, the use of cesium-impregnated sodium zirconate with soybean and jatropha oils has been observed.9 Kumar and Ali10 reported the transesterification of used cotton seed oil using a Li, Na and K catalytic process. The utilization of lithium in the transesterification of canola oil has been demonstrated by Alsharifi et al.11 High yields of biodiesel were obtained in these studies; but, unfortunately, the developed catalysts still used commercial materials. Heterogeneous catalysts based on commercial materials are still expensive; hence, the development of heterogeneous catalysts from waste materials should be considered.
Hindryawati and Maniam12 have demonstrated a prospective waste material as a catalyst, i.e. waste marine sponges, in the ultrasound-assisted transesterification of waste cooking oil. A high yield of biodiesel (98%) was obtained. However, the ultrasound method uses a large volume of solvent and requires a long reaction time.13 Li et al. have utilized a carbide slag waste material as a heterogeneous catalyst for biodiesel production.14 However, the yield obtained was about 91% and they used fresh oil, i.e., soybean oil. Therefore, the utilization of waste materials as a heterogeneous catalyst for biodiesel production is still being developed. CaO is one of the potential catalysts for biodiesel production.15 CaO catalysts can be formed from a calcination process of CaCO3. A plentiful waste material – eggshell – is a potential material, because it contains more than 94% CaCO3.16 Unfortunately, CaO catalysts have a low surface area of about 13 m2 g−1,17 and catalysts with a higher surface area lead to higher biodiesel yields.18 To conquer this weakness, the use of a catalyst support such as silica with CaO catalysts should be considered to increase the surface area of the catalyst. Silica has been widely used as a support for many applications of catalytic reactions.19,20
This research aims to produce efficient and low-cost heterogeneous catalysts, i.e., CaO/SiO2, prepared from eggshell and palm empty fruit bunch (PEFB) waste. Silica for the catalyst support was extracted from palm empty fruit bunches and eggshells were used as the source of CaO. The developed catalyst was used in a transesterification process to produce biodiesel. The characterization of the catalysts using XRD, SEM, BET and FTIR was also performed. The utilization of waste materials as a heterogeneous catalyst for biodiesel production in this work can hopefully reduce the cost of catalyst preparation as compared to the use of commercial catalysts. This is possible due to the abundant availability of palm empty fruit bunches. In addition, waste cooking oil was also used to solve the environmental problem and to promote friendly biodiesel production processes.
Method
Catalyst preparation
Eggshells were initially washed twice using distilled water to remove impurities. They were then dried at 90 °C overnight. The dried material was finely crushed and sieved with a 400-mesh sieve. This material was further named as the fine CaCO3 material. To obtain the CaO catalyst, the fine CaCO3 material was calcined at 900 °C for 2 h.
Support preparation
Palm empty fruit bunches were cleaned of impurities using distilled water and then dried at 100 °C overnight. The material was then ground into smaller pieces and sieved with a 20-mesh sieve. The material was further calcined at 700 °C for 4 h. Ten grams of the calcined material was further extracted using a solution of 60 mL of NaOH with various concentrations of 7.5% (w/v), 10% (w/v) and 12.5% (w/v) at 80 °C for 1 h. These concentrations led to sodium hydroxide molarities of 1.87, 2.5 and 3.125 N. Then, 1 N HCl was carefully dropped into the obtained filtrate to achieve a solution pH of 7; hence, a silica precipitate was obtained. The precipitate was filtered and heated at 90 °C overnight. This final material was further named as the SiO2 support.
Catalyst formation
The fine CaCO3 was impregnated with 4 grams of SiO2 support using 20 mL of distilled water for 2 h. The ratio of catalyst to support used was 10% (w/w) based on the weight of CaCO3 to SiO2, respectively. The solution was then heated at 90 °C overnight. The obtained solid material was calcined at 900 °C for 2 h. The final catalyst was further called CaO/SiO2. The same method was applied for the palm empty fruit bunch material without the extraction process used as a support. This final catalyst was named as CaO/PEFB. The performance of both catalysts, CaO/SiO2 and CaO/PEFB, was compared to a CaO catalyst without a support as a control.
Transesterification process and biodiesel separation
A 100 mL sample of waste cooking oil was placed in a three-necked glass flask. Methanol was carefully poured into the flask with a ratio of methanol to waste cooking oil of 14 molar. The heterogeneous catalyst was added into the flask at a concentration of 8% (w/w). The reaction was further carried out for 90 min at a temperature of 60 °C.
The solution after the reaction process was filtered to separate the solid catalyst from the solution. The catalyst was then washed using distilled water and dried in an oven at 90 °C for 5 h. The catalyst was reused for the next transesterification reaction. The filtrate was annealed in a funnel overnight to separate the mixture of biodiesel–methanol and glycerol. The biodiesel–methanol mixture was then evaporated to obtain the biodiesel. The biodiesel was identified by using GCMS (2010S Shimadzu, Tokyo, Japan) equipped with a HP-1 capillary column (ID = 0.25 mm, film = 0.25 μm, Hewlett-Packard, USA) and connected to a flame ionization detector. Helium was used as the carrier gas at a flow rate of 3 mL min−1; the split ratio was 49. The yield of biodiesel was evaluated after the separation process using the method reported elsewhere.21
Catalyst characterization
The CaO catalyst, silica as the catalyst support and the fresh and used CaO/SiO2 catalysts were characterized to compare their physical and chemical characteristics. The characterization techniques used for the catalysts included XRD, SEM, BET and FT-IR. XRD (PANalytical X'PERT QUANTIFY, Almelo, Netherlands) was used for phase identification, using copper K-alpha (Cu Kα) radiation with 2θ in the range from 10 to 80° at a scan rate of 2° min−1. The operation voltage and current were kept at 40 kV and 100 mA, respectively. SEM (Inspect S50, Hillsboro, USA) conducted under an electrical potential of 20 kV at 10
000 times magnification, was utilized for the morphological studies. BET (NOVA 1200E, Florida, USA), by applying nitrogen adsorption measurements, was used for observing the surface area. FT-IR (Thermo Scientific Nicolet iS10 FT-IR, Madison, USA), recorded over the range of 500–4000 cm−1, was utilized for structural studies of the bonded chemical compounds.
Results and discussion
Characterization results
Fig. 1 shows the results of XRD characterization for the CaO catalyst, SiO2 support, fresh CaO/SiO2 catalyst and used CaO/SiO2 catalyst. The silica used here was produced from the extraction of oil palm empty fruit bunches using 7.5% NaOH. The presence of CaO was shown at 2θ values of approximately 34° and 64°;22 meanwhile, SiO2 was found at around 27° and 48°.20 The existence of a CaCO3 peak at around 30° (ref. 22) was shown for the CaO catalyst, indicating that the CaCO3 was not completely decomposed into CaO. A high temperature of calcination up to 1000 °C led to complete decomposition of CaCO3 into CaO.22 On the other hand, fewer peaks were observed for the fresh CaO/SiO2 catalyst. This may be because the crystalline domains were small, and thus not detected by XRD.23 Another possibility is that a new phase, such as Ca–Si–O, was formed due to interactions between CaO and SiO2 on the surface of the catalyst during calcination; hence, their presence could not be detected by XRD.20,24,25 This occurrence probably also supported the observation of a lower intensity of the CaCO3 peaks in the CaO/SiO2 catalyst.
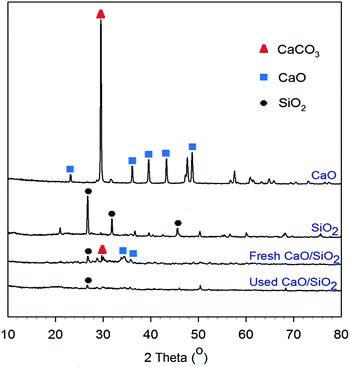 |
| Fig. 1 XRD characterization results for the CaO catalyst, SiO2 support, fresh CaO/SiO2 catalyst and used CaO/SiO2 catalyst. | |
Fig. 2a–d show SEM images for the CaO catalyst, SiO2 support, fresh CaO/SiO2 catalyst and used CaO/SiO2 catalyst, respectively. Fig. 2a shows the structure of the CaO catalyst without a support, which is like a beehive,26 with a catalyst texture wherein the particles are agglomerated.27 As shown in Fig. 2b, strong compact particles were observed for the structure of silica. Fig. 2c shows that CaO was uniformly distributed on the surface of the silica. This supported the previous XRD discussion, as the small crystalline domains of CaO were observed to spread on the surface of the silica as shown in Fig. 2c. On the other hand, the used CaO/SiO2 catalyst was likely covered by oil; hence, the peaks for CaO were reasonably undetected, as also found in the XRD result.
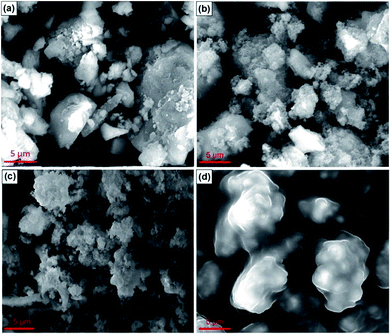 |
| Fig. 2 SEM characterization results of for: (a) CaO, (b) SiO2, (c) CaO/SiO2 (fresh), and (d) CaO/SiO2 (used). | |
Table 1 shows the surface area results for the CaO catalyst, SiO2 support, fresh CaO/SiO2 catalyst and used CaO/SiO2 catalyst. The pure CaO catalyst generated in this work had a low surface area, i.e., 2.8 m2 g−1; this value was close to the commercial one (3 m2 g−1). Silica showed great potential as a support as it provided a high surface area (39.7 m2 g−1). The silica surface area obtained here was comparable to those reported in other studies (12–67 m2 g−1).28,29 The various values of silica surface area depend on the preparation and process of formation.30 The CaO catalyst supported with silica demonstrated a very high surface area, i.e., 79.8 m2 g−1, as shown in Table 1. Catalysts possessing a high surface area lead to high catalytic activity in biodiesel production.31,32 The low surface area for the used CaO/SiO2 was due to the closure of the catalyst surface by oil, supported by the previous characterization results.
Table 1 BET characterization results of catalyst surface area
Catalyst |
Surface area (m2 g−1) |
Reference |
CaO |
2.8 |
This work |
Commercial CaO |
3.0 |
26 |
SiO2 |
39.7 |
This work |
SiO2 |
12 |
28 |
CaO/SiO2 (fresh) |
79.8 |
This work |
CaO/SiO2 (used) |
3.6 |
This work |
Fig. 3 shows the FT-IR characterization results for the CaO catalyst, SiO2 support, fresh CaO/SiO2 catalyst and used CaO/SiO2 catalyst. The band at 1414 cm−1 for the CaO catalyst can be attributed to the stretching vibration of surface CO32− groups,33 indicating the presence of CaCO3. This finding again supported the previous characterization results that the compound was not fully decomposed into CaO. The broad absorption in the range of 700–900 cm−1 can be assigned to Ca–O,34,35 and the broad absorption found here was at about 864 cm−1. The stretching mode region of Si–O is assigned to a wavenumber of about 1015 cm−1,36 and was clearly observed here for the SiO2 support. For both the fresh and used CaO/SiO2 catalysts, the two peaks at wavenumbers of 864 cm−1 and 1015 cm−1 assigned to Ca–O and Si–O, respectively, were observed to not separate, and even merged. For the used CaO/SiO2 catalyst, the bands at around 2933 cm−1 and 2844 cm−1 are attributed to the symmetric and asymmetric stretching vibration of aliphatic CH2 groups, respectively.33 The broad absorption at 1744 cm−1 is assigned to ester carbonyl functional groups of the triglycerides.37 These peaks observed for the used CaO/SiO2 catalyst were obviously due to the presence of oil covering the catalyst; thus, they again confirm the previous characterization results.
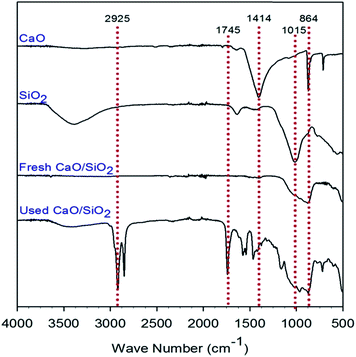 |
| Fig. 3 FT-IR characterization results for CaO/SiO2 (fresh), CaO/SiO2, SiO2 extracted and CaO calcined. | |
Extraction of silica
Fig. 4 shows the results of silica extraction from oil palm empty fruit bunches. The optimum yield of silica was obtained at the sodium hydroxide concentration of 10%. It was reported that a higher yield of silica extraction from rice hull was obtained by increasing the concentration of sodium hydroxide.38 The silica yield in their work was in the range of 35–89% using a concentration of 0.25–1 N of NaOH. There is no silica extracted using a concentration of less than 0.25 N and no improvement in the silica yield for concentrations higher than 1 N. The yields of extraction obtained here were 62.9%, 68.2% and 52.7% for the utilization of a sodium hydroxide concentration of 7.5%, 10% and 12.5% (w/v), respectively.
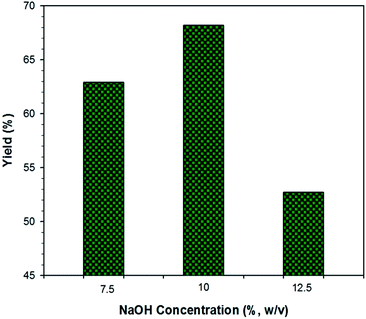 |
| Fig. 4 Yield of silica extraction from empty fruit bunches. | |
The lower yield of silica obtained and the higher sodium hydroxide concentration used in this work were attributed to the higher amount of minerals in palm empty fruit bunches compared to rice husk.39 The absence of these minerals is an important parameter in the extraction of silica.38 At higher concentrations of NaOH (12.5%), less silica was extracted, because the amount of solvent became saturated in the system. Hence, the silica became more difficult to extract.
Transesterification of waste cooking oil
Fig. 5 shows the result of the transesterification process from waste cooking oil using catalysts of CaO, fresh CaO/SiO2, CaO/PEFB and used CaO/SiO2 (after 3 cycles). The CaO catalyst prepared from eggshells was capable of producing biodiesel with a yield of 78%; this shows that eggshell waste is a prospective source of catalysts for biodiesel applications. On the addition of a support to the catalyst, the yield of biodiesel was increased to 96%. This increase in yield was related to the increase in the surface area of the catalyst.18 A higher surface area leads to the improvement of the catalyst activity,40 thus accelerating reactions on the surface of the catalyst.
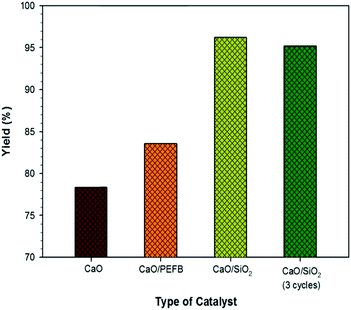 |
| Fig. 5 Transesterification of waste cooking oil for biodiesel production. | |
The reusability and stability are also important parameters for biodiesel production to be economically feasible when applied on an industrial scale.41 The CaO/SiO2 catalyst after three runs showed an insignificant change in performance with a decrease in yield of only 1%. In previous reports, the decrease in yield after three cycles was substantial for CaO catalysts at up to 5–20%.41–43 To eliminate the extraction process and the usage of chemicals and energy, the CaO was directly supported on palm empty fruit bunch powder via an impregnation method. As compared to the CaO catalyst, the performance of CaO/PEFB was slightly enhanced from 78% to 83%.
Fig. 6 shows a chromatogram of the biodiesel product produced using the CaO/SiO2 catalyst. The components of methyl palmitate (C17), methyl 11-cyclohexylundecanoate (C18), methyl linoleate (C19), methyl oleate (C19) and methyl stearate (C19) are present in the biodiesel with mole percentages of 22.55%, 4.44%, 10.90%, 53.41% and 5.69%, respectively (Table 2). The biodiesel generally produced through direct transesterification processes contains fatty acids in the range of C16–C20;44–46 the biodiesel obtained here was consistent with the previous literature in terms of fatty acid type. On the other hand, the composition of biodiesel is also associated with the source of natural oil used,47 because many factors such as soil characteristics, plant maturity, climate and genetics of the plant affect the fatty acid composition. It has also been reported that the fatty acid composition in biodiesel produced via direct trans-esterification from various vegetable oils is typically in the range of C15–C24.48–50
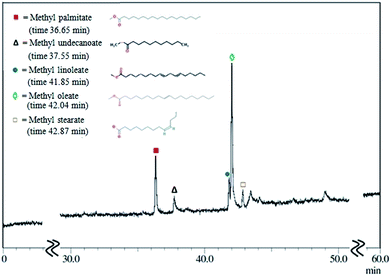 |
| Fig. 6 Chromatogram of GC-MS analysis for the biodiesel product. | |
Table 2 Fatty acid composition in the biodiesel product
Fatty acid type |
Chemical formula |
Retention time |
Mole conc. (%) |
Hexadecanoic acid methyl ester (methyl palmitate) |
C17H34O2 |
36.35 |
22.55 |
11-Cyclohexylundecanoate methyl ester (methyl undecanoate) |
C18H34O2 |
37.75 |
4.44 |
9,12-Octadecadienoic acid methyl ester (methyl linoleate) |
C19H34O2 |
41.85 |
10.90 |
9-Octadecenoic acid methyl ester (methyl oleate) |
C19H36O2 |
42.04 |
53.41 |
Octadecanoic acid methyl ester (methyl stearate) |
C19H38O2 |
42.87 |
5.69 |
Comparison of various catalyst types
Table 3 presents a comparison of several types of catalysts utilized for biodiesel production using waste cooking oil. As shown in work #1, biodiesel could be produced using a homogeneous catalyst; however, the yield is still below 90%. To reduce the formation of foam due to a high FFA (free fatty acid) content, and thus consequently increase the yield, a mixed process (work #2) of using homogeneous acid and heterogeneous base catalysts was used. An improvement in the yield (96%) was observed. Nevertheless, the process requires a costly separation process. Work numbers #3, #4 and #5 show transesterification processes using commercial material-based heterogeneous catalysts, with potential yields in the range of 79.7–98.9% being observed. The reactions were processed at high temperature and mol ratio of reactant. It has been reported that reaction processes using such mixed oxide catalysts require high temperatures and pressures during the process.60 Moreover, the commercial catalysts are not cheap. This will consequently increase the cost of biodiesel production and its sale, thus limiting biodiesel applications on a larger scale over other potential catalysts.61 Therefore, it is highly recommended to use waste materials as heterogeneous catalysts in biodiesel production. Potential waste materials including golden apple snails, mereterix venus, chicken bone and mereterix mereterix (clamshell) as heterogeneous catalysts utilized in biodiesel production were reported in work numbers #8, #9, #10 and #11. The obtained yields of biodiesel were still below 90%, and the values were comparable to those of our work (#12). It has been reported that only a few waste materials can be employed for biodiesel production from a waste cooking oil type of feedstock.62 This is because the high content of FFAs in WCO contributes to a reduction in biodiesel yield. As recently reported by Tshizanga et al.,63 a higher surface area catalyst could significantly mediate the transesterification of WCO containing a high FFA content. Therefore, here the presence of silica in the CaO catalyst resulted in a significant increase in the yield of biodiesel (#13), associated with the high surface area obtained. This reveals that such heterogeneous catalysts sourced from waste materials will always be of major interest in the development of biodiesel production processes.
Table 3 Comparison of various types of catalysts used in the transesterification of waste cooking oil as a feedstock
Work number |
Catalyst |
Processing conditions |
Yield (%) |
Reference |
Remarks |
Temperature (°C) |
Time (h) |
Molar ratioa |
Methanol: waste cooking oil (WCO). |
#1 |
KOH |
87 |
2 |
9 : 1 |
87 |
51 |
Homogeneous catalyst. Soap formation |
#2 |
Ferric sulphate followed by KOH |
100, 100 |
2, 2 |
9 : 1, 7.5 : 1 |
96 |
52 |
Mixture of homogeneous and heterogeneous |
#3 |
K3PO4 |
60 |
2 |
6 : 1 |
97.3 |
53 |
Commercial chemical |
#4 |
Zinc stearate |
200 |
10 |
18 : 1 |
98 |
|
Commercial chemical |
#5 |
Zr0.7H0.2PW12O40 |
65 |
8 |
20 : 1 |
98.9 |
54 |
Commercial chemical |
#6 |
MgO/TiO2 |
150 |
6 |
30 : 1 |
91.6 |
55 |
Commercial chemical |
#7 |
Sr/ZrO2 |
115 |
1.45 |
29 : 1 |
79.7 |
56 |
Commercial chemical |
#8 |
Golden apple snail |
60 |
1 |
18 : 1 |
83 |
57 |
Waste material |
#9 |
Mereterix venus |
60 |
1 |
18 : 1 |
78 |
57 |
Waste material |
#10 |
Chicken bone |
65 |
4 |
15 : 1 |
89.3 |
58 |
Waste material |
#11 |
Mereterix mereterix |
60 |
6 |
6 : 1 |
87.9 |
59 |
Waste material |
#12 |
Eggshell (CaO) |
60 |
1.5 |
14 : 1 |
78 |
This work |
Waste material |
#13 |
CaO/SiO2 based on eggshell/PEFB |
60 |
1.5 |
14 : 1 |
96 |
This work |
Waste material |
Future work
The developed catalyst obtained in this work showed a number of potential results in increasing the yield of biodiesel. Moreover, the palm empty fruit bunch and eggshell waste materials are abundantly available. The activated PEFB could also be directly used as the support of a CaO catalyst. Bearing in mind that biodiesel production was achieved without a chemical extraction process and the amount of CaO was only one-tenth the amount of PEFB, this catalyst is a prospective material to be applied on an industrial scale. For this, it is strongly recommended that a pilot plant and the economic feasibility of the catalysts be studied in future work. Because the raw materials for the developed catalysts and the used oils are waste materials, the policy of waste usage and its collection should also be supported by the government of each country. In addition, the biodiesel production process should be developed to not only reduce the cost of the process (by using a heterogeneous catalyst without chemical processes of separation) but also minimize the waste-related environmental issues.64
Conclusions
Silica as a support for a CaO catalyst could be extracted from palm empty fruit bunches (PEFBs). The presence of a silica support in the CaO catalyst significantly increased the surface area from 2.8 to 79.8 m2 g−1. This resulted in an improvement in the biodiesel yield from 78 to 96%. Three cycles of catalyst use led to only a 1% drop in the biodiesel yield. The CaO catalyst supported on activated PEFB resulted in an improvement in the biodiesel yield from 78 to 83%.
Conflicts of interest
There are no conflicts to declare.
Abbreviations
BET | Brunauer, Emmett and Teller |
CaCO3 | Calcium carbonate |
CaO | Calcium oxide |
FFA | Free fatty acid |
FT-IR | Fourier-transform infrared spectroscopy |
GCMS | Gas chromatography mass spectrometry |
K3PO4 | Potassium phosphate |
KOH | Potassium hydroxide |
MgO | Magnesium oxide |
NaOH | Sodium hydroxide |
PEFB | Palm empty fruit bunch |
SEM | Scanning electron microscope |
SiO2 | Silicon dioxide |
Sr | Strontium |
TiO2 | Titanium dioxide |
WCO | Waste cooking oil |
XRD | X-ray diffraction |
ZrO2 | Zirconium dioxide |
Acknowledgements
The authors extend their appreciation to the Faculty of Engineering, Lambung Mangkurat University, which provided a Research Grant under contract No. 440/UN8.1.31/KU/2016, for their generous support and funding of this study.
References
- S. Wang, C. Zhao, R. Shan, Y. Wang and H. Yuan, Energy Convers. Manage., 2017, 139, 89–96 CrossRef CAS.
- F. Ullah, L. Dong, A. Bano, Q. Peng and J. Huang, J. Energy Inst., 2016, 89, 282–292 CrossRef CAS.
- L. F. Chuah, J. J. Klemeš, S. Yusup, A. Bokhari and M. M. Akbar, J. Cleaner Prod., 2017, 146, 181–193 CrossRef CAS.
- R. L. Naylor and M. M. Higgins, Renewable Sustainable Energy Rev., 2017, 77, 695–705 CrossRef.
- M. A. Ahmad Farid, M. A. Hassan, Y. H. Taufiq-Yap, M. L. Ibrahim, M. R. Othman, A. A. M. Ali and Y. Shirai, Renewable Energy, 2017, 114, 638–643 CrossRef CAS.
- N. Sano, K. Yamada, S. Tsunauchi and H. Tamon, Chem. Eng. J., 2017, 307, 135–142 CrossRef CAS.
- G. Chen, R. Shan, J. Shi, C. Liu and B. Yan, Energy Convers. Manage., 2015, 98, 463–469 CrossRef CAS.
- I. F. Nata, M. D. Putra, C. Irawan and C.-K. Lee, J. Environ. Chem. Eng., 2017, 5, 2171–2175 CrossRef CAS.
- D. A. Torres-Rodríguez, I. C. Romero-Ibarra, I. A. Ibarra and H. Pfeiffer, Renewable Energy, 2016, 93, 323–331 CrossRef.
- D. Kumar and A. Ali, Energy Fuels, 2010, 24, 2091–2097 CrossRef CAS.
- M. Alsharifi, H. Znad, S. Hena and M. Ang, Renewable Energy, 2017, 114, 1077–1089 CrossRef CAS.
- N. Hindryawati and G. P. Maniam, Ultrason. Sonochem., 2015, 22, 454–462 CrossRef CAS PubMed.
- P. Cintas, S. Mantegna, E. C. Gaudino and G. Cravotto, Ultrason. Sonochem., 2010, 17, 985–989 CrossRef CAS PubMed.
- F.-J. Li, H.-Q. Li, L.-G. Wang and Y. Cao, Fuel Process. Technol., 2015, 131, 421–429 CrossRef CAS.
- N. Asikin-Mijan, H. V. Lee, J. C. Juan, A. R. Noorsaadah and Y. H. Taufiq-Yap, RSC Adv., 2017, 7, 46445–46460 RSC.
- M. J. Quina, M. A. R. Soares and R. Quinta-Ferreira, Resour., Conserv. Recycl., 2017, 123, 176–186 CrossRef.
- M. Kouzu, T. Kasuno, M. Tajika, Y. Sugimoto, S. Yamanaka and J. Hidaka, Fuel, 2008, 87, 2798–2806 CrossRef CAS.
- K. Jacobson, R. Gopinath, L. C. Meher and A. K. Dalai, Appl. Catal., B, 2008, 85, 86–91 CrossRef CAS.
- M. D. Putra, S. M. Al-Zahrani and A. E. Abasaeed, J. Ind. Eng. Chem., 2012, 18, 1153–1156 CrossRef CAS.
- M. D. Putra, M. K. Al-Mesfer, A. E. Abasaeed and S. M. Al-Zahrani, J. Chem. Eng. Jpn., 2013, 46, 389–395 CrossRef CAS.
- G. K. Ayetor, A. Sunnu and J. Parbey, Alexandria Eng. J., 2015, 54, 1285–1290 CrossRef.
- Z. Wei, C. Xu and B. Li, Bioresour. Technol., 2009, 100, 2883–2885 CrossRef CAS PubMed.
- E. V. Kondratenko and M. Baerns, Appl. Catal., A, 2001, 222, 133–143 CrossRef CAS.
- J.-y. Jing, S.-d. Wang, X.-w. Zhang, Q. Li and W.-y. Li, J. Fuel Chem. Technol., 2017, 45, 956–962 CrossRef CAS.
- M. D. Putra, S. M. Al-Zahrani and A. E. Abasaeed, J. Energy Chem., 2013, 22, 778–782 CrossRef CAS.
- S. Niju, K. M. Meera, S. Begum and N. Anantharaman, J. Saudi Chem. Soc., 2014, 18, 702–706 CrossRef.
- C. Chi, Y. Li, X. Ma and L. Duan, Chem. Eng. J., 2017, 326, 378–388 CrossRef CAS.
- S. Faramawy, A. Y. El-Naggar, A. M. El-Fadly, S. M. El-Sabagh and A. A. Ibrahim, Arabian J. Chem., 2016, 9, S765–S775 CrossRef CAS.
- S. Katoh, M. Imada, N. Takeda, T. Katsuda, H. Miyahara, M. Inoue and S. Nakamura, J. Chromatogr. A, 2007, 1161, 36–40 CrossRef CAS PubMed.
- A. Galarneau, N. Calin, J. Iapichella, M. Barrande, R. Denoyel, B. Coasne and F. Fajula, Chem. Mater., 2009, 21, 1884–1892 CrossRef CAS.
- X. Liu, X. Piao, Y. Wang, S. Zhu and H. He, Fuel, 2008, 87, 1076–1082 CrossRef CAS.
- M. P. Dorado, E. Ballesteros, M. Mittelbach and F. J. López, Energy Fuels, 2004, 18, 1457–1462 CrossRef CAS.
- S. Yan, M. Kim, S. O. Salley and K. Y. S. Ng, Appl. Catal., A, 2009, 360, 163–170 CrossRef CAS.
- A. K. Parchur and R. S. Ningthoujam, Dalton Trans., 2011, 40, 7590–7594 RSC.
- H. Zaitan, D. Bianchi, O. Achak and T. Chafik, J. Hazard. Mater., 2008, 153, 852–859 CrossRef CAS PubMed.
- P. C. Ricci, G. Gulleri, F. Fumagalli, C. M. Carbonaro and R. Corpino, Appl. Surf. Sci., 2013, 265, 470–474 CrossRef CAS.
- L. Yang, H. Dai, A. Yi, B. Lin and G. Li, J. Therm. Anal. Calorim., 2008, 93, 875–879 CrossRef CAS.
- U. Kalapathy, A. Proctor and J. Shultz, Bioresour. Technol., 2000, 73, 257–262 CrossRef CAS.
- N. A. Sari, C. F. Ishak and R. A. Bakar, Am. J. Agric. Biol. Sci., 2014, 9, 450–456 CrossRef.
- T.-H. Đặng, B.-H. Chen and D.-J. Lee, J. Taiwan Inst. Chem. Eng., 2017, 79, 14–22 CrossRef.
- P. R. Pandit and M. H. Fulekar, J. Environ. Manage., 2017, 198, 319–329 CrossRef CAS PubMed.
- L. M. Correia, J. A. Cecilia, E. Rodríguez-Castellón, C. L. Cavalcante Jr and R. S. Vieira, J. Chem., 2017, 2017, 5679512 Search PubMed.
- Y. H. Taufiq-Yap, H. V. Lee, M. Z. Hussein and R. Yunus, Biomass Bioenergy, 2011, 35, 827–834 CrossRef CAS.
- R. W. Jenkins, N. E. Stageman, C. M. Fortune and C. J. Chuck, Energy Fuels, 2014, 28, 1166–1174 CrossRef CAS.
- N. Kondamudi, S. K. Mohapatra and M. Misra, J. Agric. Food Chem., 2008, 56, 11757–11760 CrossRef CAS PubMed.
- Y. Liu, Q. Tu, G. Knothe and M. Lu, Fuel, 2017, 199, 157–161 CrossRef CAS.
- A. Abdullah, R. N. Rahmawati Sianipar, D. Ariyani and I. F. Nata, Sustainable Environ. Res., 2017, 27, 291–295 CrossRef.
- M. Farooq, A. Ramli and D. Subbarao, J. Cleaner Prod., 2013, 59, 131–140 CrossRef CAS.
- M. Yadav, V. Singh and Y. C. Sharma, Energy Convers. Manage., 2017, 148, 1438–1452 CrossRef CAS.
- S. S. Satputaley, D. B. Zodpe and N. V. Deshpande, J. Energy Inst., 2017, 90, 513–521 CrossRef CAS.
- A. Demirbas, Energy Convers. Manage., 2009, 50, 923–927 CrossRef CAS.
- P. Patil, S. Deng, J. Isaac Rhodes and P. J. Lammers, Fuel, 2010, 89, 360–364 CrossRef CAS.
- G. Guan, K. Kusakabe and S. Yamasaki, Fuel Process. Technol., 2009, 90, 520–524 CrossRef CAS.
- X. Zhang, J. Li, Y. Chen, J. Wang, L. Feng, X. Wang and F. Cao, Energy Fuels, 2009, 23, 4640–4646 CrossRef CAS.
- Z. Wen, X. Yu, S.-T. Tu, J. Yan and E. Dahlquist, Bioresour. Technol., 2010, 101, 9570–9576 CrossRef CAS PubMed.
- W. N. N. Wan Omar and N. A. Saidina Amin, Biomass Bioenergy, 2011, 35, 1329–1338 CrossRef.
- N. Viriya-empikul, P. Krasae, B. Puttasawat, B. Yoosuk, N. Chollacoop and K. Faungnawakij, Bioresour. Technol., 2010, 101, 3765–3767 CrossRef CAS PubMed.
- M. Farooq, A. Ramli and A. Naeem, Renewable Energy, 2015, 76, 362–368 CrossRef CAS.
- P. Nair, B. Singh, S. N. Upadhyay and Y. C. Sharma, J. Cleaner Prod., 2012, 29–30, 82–90 CrossRef CAS.
- Y. C. Sharma, B. Singh and J. Korstad, Fuel, 2011, 90, 1309–1324 CrossRef CAS.
- L. Bournay, D. Casanave, B. Delfort, G. Hillion and J. A. Chodorge, Catal. Today, 2005, 106, 190–192 CrossRef CAS.
- S. H. Y. S. Abdullah, N. H. M. Hanapi, A. Azid, R. Umar, H. Juahir, H. Khatoon and A. Endut, Renewable Sustainable Energy Rev., 2017, 70, 1040–1051 CrossRef CAS.
- N. Tshizanga, E. F. Aransiola and O. Oyekola, S. Afr. J. Chem. Eng., 2017, 23, 145–156 Search PubMed.
- K. Shahzad, A. S. Nizami, M. Sagir, M. Rehan, S. Maier, M. Z. Khan, O. K. M. Ouda, I. M. I. Ismail and A. O. BaFail, PLoS One, 2017, 12, e0171297 CAS.
|
This journal is © The Royal Society of Chemistry 2017 |
Click here to see how this site uses Cookies. View our privacy policy here.