DOI:
10.1039/C7RA10608D
(Paper)
RSC Adv., 2017,
7, 52151-52164
Electrochemical properties of lithium–titanium oxide, modified with Ag–Cu particles, as a negative electrode for lithium-ion batteries
Received
25th September 2017
, Accepted 5th November 2017
First published on 9th November 2017
Abstract
Composites of Li4Ti5O12 with Ag–Cu particles were successfully synthesized by solid-state reaction followed by thermal decomposition of the metal substrates. The presence of metallic particles was confirmed by X-ray diffraction, scanning transmission electron microscopy and X-ray photoelectron spectroscopy. Galvanostatic charge–discharge tests showed improved specific capacity and capacity retention of Li4Ti5O12/Ag–Cu composites at a 10C current rate, while cyclic voltammetry and electrochemical impedance spectroscopy revealed changes in Li+ ion chemical diffusion coefficient values and charge-transfer resistance with increasing amount of Ag–Cu in prepared powders. The synthesis and structural, morphological and electrochemical evaluation of Li4Ti5O12/Ag–Cu powders, carried out in this work, were also presented here for the first time.
1. Introduction
One of the candidates to replace graphite as an anode material in lithium-ion batteries is lithium–titanium oxide (Li4Ti5O12, LTO) of spinel structure. It shows excellent cyclability due to negligible volume change during intercalation/deintercalation reactions (so called “zero-strain” electrode material).1,2 A high operating potential of 1.55 V vs. Li+/Li0 is responsible for LTO's enhanced safety, due to hindering the formation of a Solid Electrolyte Interface (SEI) layer on the electrode's surface, although some research groups reported SEI creation as a result of spontaneous reactions with the electrolyte or migration of SEI components formed on counter electrodes.3,4 Li4Ti5O12 has an acceptable specific capacity of 175 mAh g−1 when charged/discharged in the potential range of 1.00–3.00 V (vs. Li+/Li0) when the following reaction occurs: |
Li4Ti5O12 + 3Li+ + 3e− ↔ Li7Ti5O12,
| (1) |
and 293 mAh g−1 while expanding the potential window to 0.01–3.00 V (vs. Li+/Li0). Increased capacity of lithium–titanium oxide when cycled to 0.01 V is related to full reduction of titanium ions from +4 to +3 oxidation state which involves additional two Li+ ions:5 |
Li7Ti5O12 + 2Li+ + 2e− ↔ Li9Ti5O12.
| (2) |
All mentioned properties make LTO a good material for next generations of Li-ion batteries. However, due to low electric conductivity of Li4Ti5O12, its widespread application is still limited.6–8
Many approaches were suggested to improve the electrochemical performance of electrode materials for lithium-ion batteries which included, among others, carbon coating,9 ion doping,10 surface modifying11,12 or even electrode design.13 In Li4Ti5O12 case, to enhance its electrochemical properties, many research groups tried various synthetic routes (such as solid-state,14–18 sol–gel,19–23 hydrothermal,24–28 combustion,29–31 microwave,32–34 spray pyrolysis,35,36 or atomic layer deposition37), cation (Mg2+,38,39 Ni2+,40 Al3+,41–43 Cr3+,44,45 Zr4+,46–48 V5+,49,50 Nb5+,51 Ta5+,52) and anion (Br−,53,54 F−,41,55,56) doping or surface modification with conductive materials (carbon coat,57–61 graphene/graphene oxide,62–65 carbon nanotubes,66–68 Ag,69–79 Cu,80–84 Au,85 TiN86–88).
In our previous studies, we synthesized and fully characterized Li4Ti5O12 modified with silver nanoparticles.78,79 The deposition of Ag nanoparticles highly enhanced electrochemical properties of lithium–titanium oxide, such as cyclability, high-rate performance and intercalation/deintercalation reaction kinetics. Due to the fact, that silver is considered as an “expensive” metal, in this work we focused on reducing the amount of Ag by incorporating a metal from the same periodic table's group into LTO powders, which is less costly and highly conductive, obtaining and fully characterizing a cheaper, silver–copper composite of Li4Ti5O12 with enhanced electrochemical properties in lithium-ion batteries.
2. Experimental
2.1 Synthesis of pristine Li4Ti5O12
The one-step solid-state synthesis was used to obtain single-phase lithium–titanium oxide powder of spinel structure. The synthesis was carried out under high-energy ball-milling (HEBM) process, using ethanol as a medium and zirconia balls, in a Planetary Mono Mill PULVERISETTE 6 (Fritsch, Germany). The starting reagents used were titanium dioxide (TiO2, 99%, Sigma-Aldrich) mixed with lithium carbonate (Li2CO3, synthesized in-house, at the Institute of Electronic Materials Technology) at the Ti
:
Li molar ratio of 5
:
4. The high-energy ball-milling process was carried out at a constant speed of 200 rpm and processing time of 12 h, respectively. Following the ball-milling process, the remaining alcohol medium was evaporated and the obtained powder was subsequently dried at 150 °C for a few hours in air atmosphere. Finally, the powder was ground in an agate mortar and heat-treated in air: a two-stage thermal treatment, consisting of 6 h annealing at 500 °C followed by 20 h annealing at 800 °C, was employed.18
2.2 Synthesis of Li4Ti5O12/Ag–Cu composites
To synthesize the Li4Ti5O12/Ag–Cu composites, AgNO3 (Avantor Performance Materials Poland S.A.) and Cu(NO3)2·3H2O (Chempur) were firstly dissolved in an ethanol solution, separately. The nitrate–ethanol solutions of Ag and Cu were mixed together. Then, the prepared nanocrystalline Li4Ti5O12 powder was added to the silver–copper nitrate solution to obtain a suspension. In subsequent processes the weight ratio of Ag
:
Cu (equal volume) and LTO was 0.005
:
0.005, 0.01
:
0.01, 0.015
:
0.015, 0.02
:
0.02 and 0.025
:
0.025, respectively. The mixture was magnetically stirred for a few hours to obtain a homogenously dispersed suspension and then was dried in air for a few hours at 150 °C. At the last step, the composites were ground in an agate mortar to obtain a fine powder.78,79
2.3 XRD, SEM, STEM, XPS
Phase identification of the prepared samples was carried out by X-ray diffraction (XRD) using an X-ray Powder Diffractometer Siemens D-500. X-ray profiles were measured between 10 and 60° (2θ angle) with a Cu Kα radiation source (λ = 1.542 Å).
Scanning electron microscopy (SEM) was used to study the microstructure of the surface modified LTO powders. Samples were prepared by dispersing a small portion of dry powders on a conductive carbon tape and were investigated on Hitachi S5500 (Hitachi High Technologies Corporation, Japan) scanning electron microscope using backscattered electron (BSE) detector. Scanning transmission electron microscope Hitachi-HD2700 (STEM), operated at 200 kV and equipped with energy dispersive X-ray spectrometer (EDS) was used for more detailed microstructural analysis. Bright Field STEM and High Angle Annular Dark Field STEM modes were used for imaging.
X-ray photoelectron spectroscopy (XPS) experiments have been performed using Kratos Axis Supra instrument with Al Kα monochromatic beam (1486.7 eV) as an X-ray source. The X-ray takeoff angle was set to standard 45°. Pass energy was set to 160 eV and 20 eV for low and high resolution spectra acquisition respectively, providing an energy resolution of ∼7.5 and ∼0.8 eV respectively. Data treatment was performed within the ESCA software. Curve fitting was achieved by using standard Shirley background subtraction and Gaussian/Lorentzian peak shapes. All spectra were calibrated by using C 1s adventitious carbon as a reference binding energy (284.8 eV).
2.4 Electrochemical measurements
For electrochemical measurements, the electrodes were made of Li4Ti5O12/Ag–Cu composite ground with Vulcan XC72R (Cabot) carbon in an agate mortar for 20 min. The obtained powder was added to 5% solution of polyvinylidene fluoride (Alfa Aesar) in N-methyl pyrrolidinone (Sigma-Aldrich) and the mixture was homogeneously stirred for 4 h. Such prepared slurry was uniformly coated onto copper foil using Elcometer® 3545 and dried in 55 °C for 1 h in air and 120 °C overnight in vacuum. Round electrodes were then cut from the foil and pressed in hydraulic press under 200 bar pressure for 1 min followed by vacuum drying at 120 °C for 16 h. The electrode composition was 8
:
1
:
1 wt ratio of Li4Ti5O12/Ag–Cu
:
PVdF
:
carbon. The cells were assembled in an argon-filled glove-box (MBraun Unilab MB-20-G).
The electrochemical tests were carried out in three-electrode Swagelok®-type cells with Li4Ti5O12/Ag–Cu working electrode, lithium metal foil (Sigma-Aldrich) as a reference and a counter electrodes, a porous polymer separator (Celgard® 2400) and liquid electrolyte mixture containing 1 M LiPF6 in ethylene and dimethyl carbonate (1
:
1 wt/wt) solvents (BASF). The chronopotentiometry (CP) experiments were performed using a multichannel battery tester Sollich ATLAS 1361. All examined cells were preliminarily discharged at current rate of 0.1C (C corresponds to current density of 175 mA g−1). Then, the cyclability and high-rate tests were performed. For cyclability tests, the cells were charged/discharged at constant current rate of 1C for 50 consequent cycles. For high-rate tests, the cells were charged at constant current rate of 1C and were discharged at current rates of 1, 2, 5 and 10C for 5 cycles each. All the cells were cycled in 1.00–3.00 V potential range (vs. Li+/Li0). After high-rate tests, the cells were examined by cyclic voltammetry (CV) and electrochemical impedance spectroscopy (EIS) using CHI760d electrochemical workstation. The CV measurements were performed in the potential range of 1.00–2.20 V (vs. Li+/Li0) at scan rates of 0.1, 0.2, 0.5, 1.0 and 2.0 mV s−1. The EIS experiments were performed at the potential of 1.00 V (after one hour of cell conditioning) with the amplitude of 10 mV in 10−2–105 Hz frequency range. The EIS spectra were analyzed using ZView2 software. For the lithium ion diffusion coefficient calculations, for both CV and EIS tests, the geometric surface area of the electrodes was used.
3. Results and discussion
3.1 XRD, SEM, STEM, XPS
Fig. 1 depicts the XRD patterns of the Ag–Cu modified Li4Ti5O12 powders. All the peaks from each sample associated with lithium–titanium oxide are in good agreement with the spinel phase Li4Ti5O12 pattern (ICDD-49-0207) confirming, that modifying the surface using Ag–Cu nanoparticles of pristine Li4Ti5O12 does not lead to any phase segregation. As presented in Fig. 1 all seven characteristic XRD peaks observed for Li4Ti5O12/Ag–Cu powders at the 2θ angles of: 18.35, 30.21, 35.60, 27.24, 43.28, 47.39 and 57.27° correspond to the (111), (220), (311), (222), (400), (331) and (333) crystal planes of the cubic structure of lithium–titanium oxide (ICDD-49-0207), respectively. The additional 2 peaks (signed as “+” in Fig. 1) at 38.11 and 44.28° correspond to the (111) and (200) planes of cubic structure of metallic silver (silver-3C, syn, cubic, Fm3m; ICDD-04-0783), respectively. The intensity of these two reflections increased with the increasing of Ag (and also Cu) content in all Li4Ti5O12/Ag–Cu powders. Also, it should be pointed out, that the characteristic reflection line of Cu metallic at 43.29° (intensity of 100%, at (111) plane) matched to reflection line of LTO (43.28°; ICDD-04-0836). A systematic appearance of, mentioned above, two characteristics diffraction lines for metallic silver indicated that metallic Ag nanoparticles were successfully deposited on the surface of Li4Ti5O12 (as we presented in our previous work).76 It should be noted, that the process of surface modification of LTO grains using both silver and copper, nanoparticles in equal volume was reported in this work for the first time.
 |
| Fig. 1 XRD patterns of Li4Ti5O12/Ag–Cu composites (* – Li4Ti5O12, + – Ag). | |
Lattice parameters of the lithium titanium oxide powders and their average crystallite sizes, calculated based on the XRD patterns shown in Fig. 1, are listed in Table 1. No significant change related to Ag–Cu presence was observed. In particular, for all samples, the average crystallites sizes of lithium–titanium oxide (as calculated from Scherrer formula, allowing for the instrumental line broadening) were in the range of 64 to 90 nm. The unit cell parameter of Li4Ti5O12 powders with silver–copper nanoparticles calculated from the XRD data is consistent with the standard value (a0 = 8.359 Å) of the ICDD PDF card.
Table 1 Crystallite sizes and lattice parameters for Li4Ti5O12/Ag–Cu composites obtained from XRD measurements
Ag–Cu content [%] |
Average crystallite sizes [nm] (±5 nm) |
Lattice parameter [Å] (±0.001 Å) |
1 |
81 |
8.358 |
2 |
90 |
8.359 |
3 |
85 |
8.357 |
4 |
81 |
8.357 |
5 |
64 |
8.354 |
The SEM images of Li4Ti5O12/Ag–Cu composite powders are presented in Fig. 2. The Ag–Cu particles are visible on BSE images as bright particles located on lithium–titanium oxide substrate. It can be seen, that the Ag–Cu nanoparticles are below 100 nm in diameter and they are distributed on LTO surface relatively homogeneous. The SEM analysis did not show significant difference in Ag–Cu nanoparticles size for lower concentration (1–3%) and slight growth of the nanoparticles size for higher concentration (4–5%). In this case Ag–Cu nanoparticles with diameter above 100 nm can be observed.
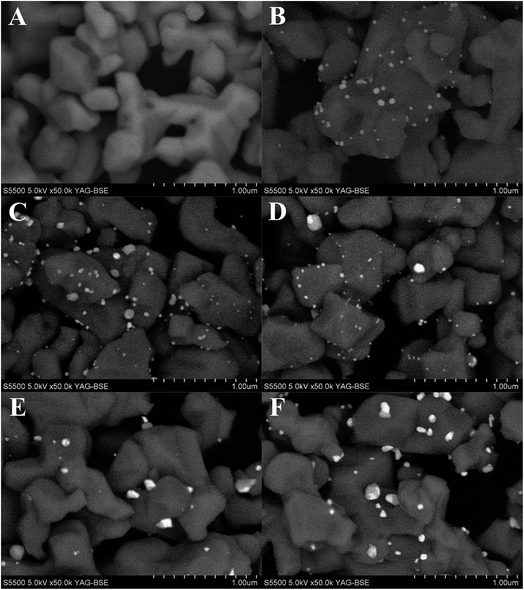 |
| Fig. 2 SEM images of Li4Ti5O12/Ag–Cu composites: (A) 0%, (B) 1%, (C) 2%, (D) 3%, (E) 4%, (F) 5% wt Ag–Cu. | |
STEM images confirms homogeneous distribution Ag–Cu particles on LTO surface (Fig. 3A and B). The differences in brightness intensity observed for different areas of Ag–Cu particles on HAADF-STEM images suggest elemental composition variability (Fig. 3B). It means that Ag–Cu particles composition is not homogenous. This observations were confirmed by EDS mapping results where silver content was found only in selected areas of Ag–Cu particles (Fig. 3C and D). The example of EDS spectrum taken from Ag–Cu particle area, indicated by the circle, is presented in Fig. 3E. The Cu-L and Ag-L lines, visible on the spectrum, confirm the presence of silver and copper elements in one particle. Due to small volume of analyzed material, the signal is relatively weak, however the peaks of Ag and Cu are clearly visible. Other observed peaks are related to oxygen from Li4Ti5O12 particle and sample contamination.
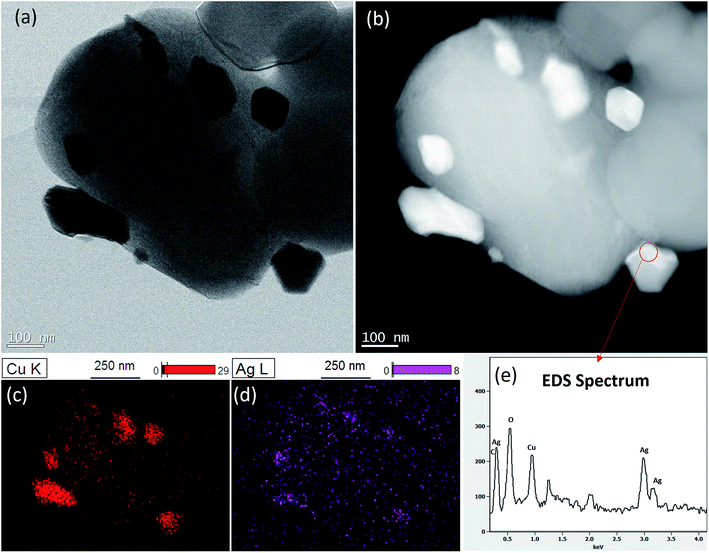 |
| Fig. 3 STEM analysis of Li4Ti5O12/5% Ag–Cu composite: (a) STEM, (b) HAADF-STEM, (c) Cu EDS mapping, (d) Ag EDS mapping, (e) EDS spectrum of the area circled in red. | |
Fig. 4 represents the XPS wide scan spectrum of Li4Ti5O12/5% Ag–Cu powder. It also includes wide scan of Li4Ti5O12/5% n-Ag sample prepared by the same method and taken as a reference material.78 The spectrum comprises several main peaks which correspond to titanium, oxygen and silver. Spectrum of Li4Ti5O12/5% Ag–Cu also reveals the presence of copper in the sample: Cu 2p3/2 and Cu 2p1/2 peaks at 932.6 eV and 952.0 eV binding energies respectively. It can be also seen that Li4Ti5O12/5% n-Ag powder is slightly contaminated by nitrogen (from AgNO3 precursor) as well as zirconium and silicon (from ceramic mortar). The relative surface concentrations of main species present in both samples are listed in Table 2. Lithium–titanium oxide modified with 5% wt of silver nanoparticles reveals a significant amount of Ag at the surface of grains (21% wt). In comparison, surface concentration of silver in LTO sample modified with 2.5% wt of silver and 2.5% wt of copper is much lower (6% wt). It might indicates that silver in Li4Ti5O12/5% Ag–Cu powder forms much larger grains of non-uniform distribution resulting in apparently lower concentration of Ag detected by XPS measurement. This statement is consisted with EDS mapping, which confirms high agglomeration of silver in Li4Ti5O12/5% Ag–Cu sample. One can also recognize that surface copper content is 33% lower than silver even though bulk concentration of these specie is equal. It suggest that Ag localizes on the surface of Cu. This observations are consistent with EDS mapping. The presence of the most intense peaks (Ag 3d located at ca. 370 eV) at the XPS spectra is a clear evidence of silver existence at the surface of examined material. It can be seen, that spectra of Li4Ti5O12/n-Ag sample consist of mainly Ag 3s, Ag 3p and Ag 3d photoelectron lines, although, due to decreasing of cross-section factor, the Ag 3s and Ag 3p peaks are of diminished intensity, in comparison with Ag 3d peak. In the case of Li4Ti5O12/Ag–Cu sample, the surface concentration of silver is much lower, thus the Ag 3s and Ag 3p peaks are barely detected.
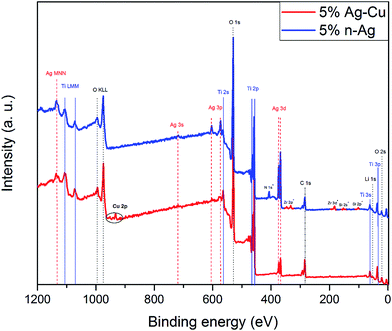 |
| Fig. 4 XPS spectra of Li4Ti5O12/5% Ag–Cu and Li4Ti5O12/5% n-Ag composites. | |
Table 2 Mass surface concentrations of titanium, oxygen, silver and copper elements in Li4Ti5O12/5% n-Ag and Li4Ti5O12/5% Ag–Cu composites
Element |
Mass surface concentration [%] |
5% n-Ag |
5% Ag–Cu |
Ti |
35 |
48 |
O |
44 |
44 |
Ag |
21 |
6 |
Cu |
— |
2 |
3.2 Electrochemistry
3.2.2 High-rate tests. Fig. 8 shows the initial discharge curves of Li4Ti5O12/Ag–Cu composites during high-rate tests. Similar to cyclability tests, the examined cells showed higher specific capacity than theoretical value for LTO, suggesting other, non-faradaic processes present during the initial discharge. The results of high-rate tests are presented on Fig. 9, 10 and in Table 4. Also in this case, the examined electrodes' specific capacity at 1C rate was in 160–162 mAh g−1 range and no relationship between specific capacity at 1C rate and the amount of Ag–Cu modification was found. However, after raising the current rate, Li4Ti5O12/Ag–Cu powders behavior began to differ from each other. At 10C rate, every modified sample reveals higher specific capacity than pristine one, reaching 101.1 ± 1.0 mAh g−1 for Li4Ti5O12/5% Ag–Cu composite and retaining 63.13 ± 0.01% of specific capacity at 1C rate. On the other hand, the pristine sample showed only 82.0 ± 0.7 mAh g−1 of specific capacity and retained 50.59 ± 0.01% of its 1C rate specific capacity while discharged at 10C current rate. From Fig. 10, one can also see, that every modified sample has higher operating potential than pristine powder. All the above suggest better reaction kinetics and lower electrodes polarization for Li4Ti5O12/Ag–Cu compounds. In order to get a better insight on the reasons behind enhanced electrochemical properties of Ag–Cu modified composite powders we conducted CV and EIS experiments.
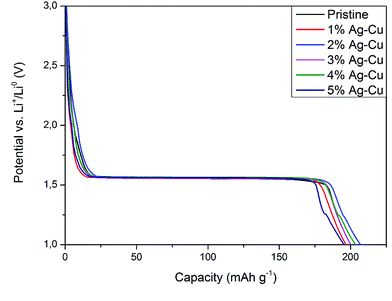 |
| Fig. 8 Initial discharge curves of Li4Ti5O12/Ag–Cu composites during high-rate tests. | |
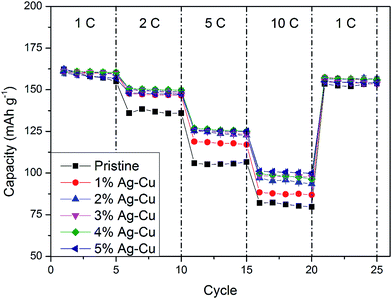 |
| Fig. 9 Rate capability of Li4Ti5O12/Ag–Cu composites. | |
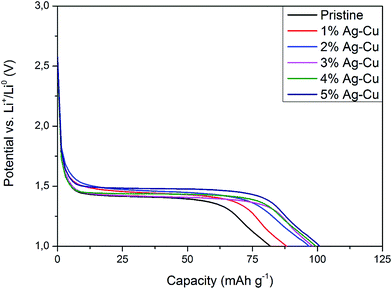 |
| Fig. 10 Discharge curves of Li4Ti5O12/Ag–Cu composites at 10C rate. | |
Table 4 Results of high-rate CP tests of Li4Ti5O12/Ag–Cu composites
Material |
Electrode loading [mg cm−2] (±0.02 mg cm−2) |
Initial discharge capacity [mAh g−1] |
1C discharge capacity [mAh g−1] |
2C discharge capacity [mAh g−1] |
5C discharge capacity [mAh g−1] |
10C discharge capacity [mAh g−1] |
Capacity retained at 10C [%] (±0.01%) |
Pristine |
2.16 |
200.3 ± 1.8 |
162.1 ± 1.5 |
136.0 ± 1.2 |
105.9 ± 1.0 |
82.0 ± 0.7 |
50.59 |
1% Ag–Cu |
2.27 |
196.8 ± 1.7 |
160.9 ± 1.4 |
147.8 ± 1.3 |
118.9 ± 1.0 |
88.4 ± 0.8 |
54.95 |
2% Ag–Cu |
1.99 |
206.9 ± 2.0 |
162.3 ± 1.6 |
150.3 ± 1.5 |
125.3 ± 1.2 |
97.0 ± 1.0 |
59.76 |
3% Ag–Cu |
2.28 |
200.2 ± 1.7 |
161.1 ± 1.4 |
150.1 ± 1.3 |
125.7 ± 1.1 |
98.4 ± 0.8 |
61.12 |
4% Ag–Cu |
2.15 |
203.6 ± 1.9 |
160.5 ± 1.5 |
150.8 ± 1.4 |
126.9 ± 1.2 |
99.7 ± 0.9 |
62.11 |
5% Ag–Cu |
1.98 |
195.4 ± 1.9 |
160.1 ± 1.6 |
148.0 ± 1.5 |
125.9 ± 1.2 |
101.1 ± 1.0 |
63.13 |
3.2.3 Cyclic voltammetry. Fig. 11 presents CV curves of pristine and Ag–Cu modified Li4Ti5O12. One can see, that the peaks originated only from oxidation and reduction reactions of Li4Ti5O12 and no other signals are visible. With increasing amount of Ag–Cu in analyzed composite powders, one can see slight changes in CV curves resulting in narrowed peak shape. This phenomenon is a result of better reaction kinetics and lower electrode's resistance after surface modification.91 Increasing the scan rate resulted in higher peak currents and increase in oxidation–reduction peak separation (caused mainly by electrode's polarization). The linear trend of relationship between current intensity and square root of scan rate had been present in all examined samples (Fig. 12), which suggests a diffusion-controlled mechanism of oxidation/reduction reactions. According to Randles–Sevcik equation for a reversible electrochemical process, Ip(v1/2) relationship can be described as:92,93 |
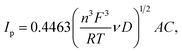 | (3) |
in which A is electrode's electrochemically active surface area (cm2), v is scan rate (V s−1), n is number of electrons involved during the electrochemical process, F is Faraday's constant (C mol−1), R is gas constant (J (mol K)−1), T is absolute temperature (K), C is molar concentration of lithium ions in Li4Ti5O12 crystal (mol cm−3) and D is chemical diffusion coefficient of lithium ions inside Li4Ti5O12 matrix (cm2 s−1), described as: |
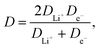 | (4) |
and dependent on both Li+ ion and electron diffusion in the host matrix.91 By using the eqn (3) and equations obtained from linear functions of Ip(v1/2), we calculated Li+ ion chemical diffusion coefficient values for oxidation and reduction reactions of Li4Ti5O12/Ag–Cu powders (Fig. 13) and listed them in Table 5. Because of the two-phase mechanism of LTO intercalation/deintercalation reaction and poor Li+ ionic conductivity of fully reduced compound (Li7Ti5O12 of rock-salt structure),94 Li+ ion transport across lithium–titanium oxide matrix is faster during oxidation reaction, which corresponds to higher Li+ chemical diffusion coefficient values for oxidation processes.
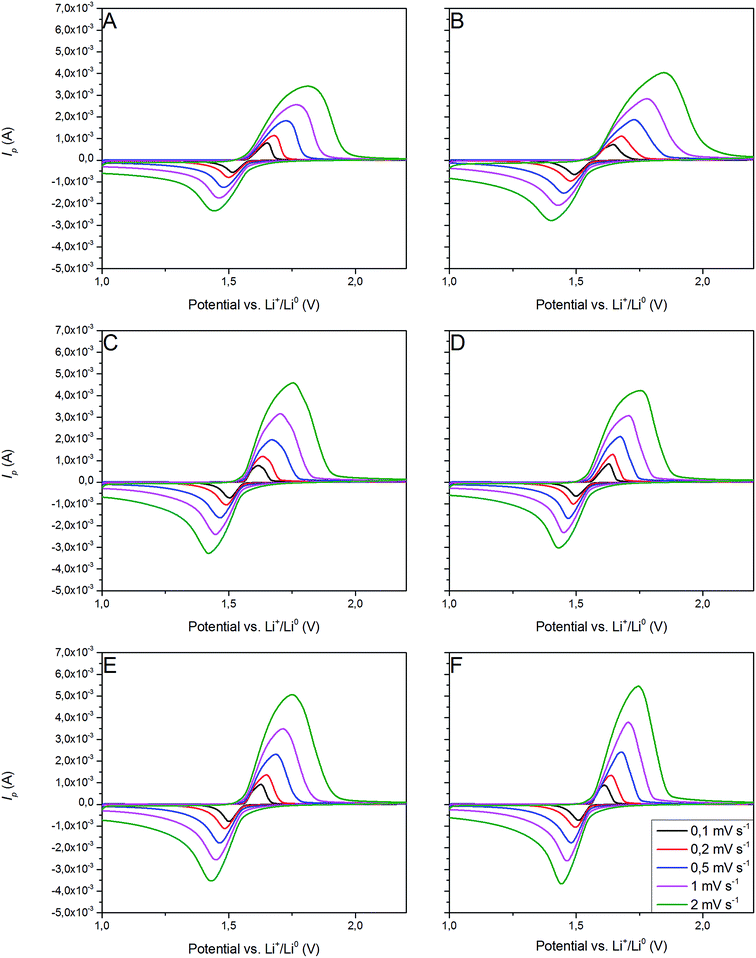 |
| Fig. 11 CV curves of Li4Ti5O12/Ag–Cu composites: (A) 0%, (B) 1%, (C) 2%, (D) 3%, (E) 4%, (F) 5% wt Ag–Cu. | |
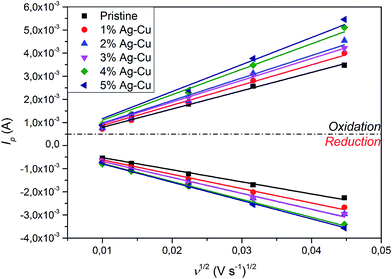 |
| Fig. 12 Ip(v−1/2) relationship acquired from CV curves of Li4Ti5O12/Ag–Cu composites. | |
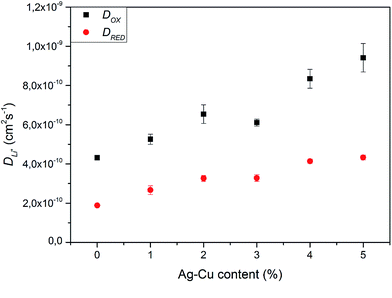 |
| Fig. 13 Li+ chemical diffusion coefficient values calculated from CV experiments of Li4Ti5O12/Ag–Cu composites. | |
Table 5 Li+ chemical diffusion coefficient values calculated from CV experiments of Li4Ti5O12/Ag–Cu composites
Material |
Electrode loading [mg cm−2] (±0.02 mg cm−2) |
DOX [cm2 s−1] |
DRED [cm2 s−1] |
Pristine |
2.13 |
(4.31 ± 0.11) × 10−10 |
(1.88 ± 0.08) × 10−10 |
1% Ag–Cu |
2.35 |
(5.26 ± 0.26) × 10−10 |
(2.66 ± 0.22) × 10−10 |
2% Ag–Cu |
2.08 |
(6.54 ± 0.48) × 10−10 |
(3.26 ± 0.15) × 10−10 |
3% Ag–Cu |
2.26 |
(6.11 ± 0.18) × 10−10 |
(3.28 ± 0.17) × 10−10 |
4% Ag–Cu |
2.19 |
(8.34 ± 0.48) × 10−10 |
(4.14 ± 0.10) × 10−10 |
5% Ag–Cu |
1.98 |
(9.41 ± 0.73) × 10−10 |
(4.33 ± 0.13) × 10−10 |
Modification of Li4Ti5O12 surface resulted in an increase in chemical diffusion coefficient values for every modified sample – from (4.31 ± 0.11) × 10−10 and (1.88 ± 0.08) × 10−10 cm2 s−1 for pristine LTO oxidation and reduction processes to (9.41 ± 0.73) × 10−10 and (4.33 ± 0.13) × 10−10 cm2 s−1 for Li4Ti5O12/5% Ag–Cu oxidation and reduction reactions. Furthermore, with every increase of Ag–Cu amount in examined powders the values of D increased. There is no saturation in chemical diffusion coefficients occurring while increasing the amount of Ag–Cu modification, which suggest that the lithium–titanium oxide's particles are not fully covered with silver and copper even at 5% wt of Ag–Cu. These findings are in good agreement with SEM, XPS, galvanostatic measurements and with our previous studies about Li4Ti5O12/n-Ag composites78,79 and can be explained by increase in electrode's active surface area and the amount of active centers capable of insertion/extraction reaction of Li+ ions into/out of Li4Ti5O12 framework79 but, as the LTO's surface is not covered completely by silver–copper particles, the electrochemical performance of Li4Ti5O12/Ag–Cu composites is not as good as in the case of Li4Ti5O12/n-Ag78 due to lower electrochemically active surface area of examined composites than in our previous studies.79
3.2.4 Electrochemical impedance spectroscopy. Fig. 14 presents the complex plane plots of pristine and Ag–Cu modified lithium–titanium oxide. The equivalent circuit used for data fitting is presented in the inset of Fig. 14. In the mentioned circuit, RS corresponds to ohmic resistance (intersection with Z′ axis at high frequency), RSEI is the resistance of passivation film on electrode's surface (depressed semicircle at high frequencies), RCT is the charge-transfer resistance through electrode|electrolyte interface (depressed semicircle at medium frequencies), CPE elements correspond to capacitance of Li+ transport through SEI layer and electrode's surface and WO is a Warburg resistance linked to a long-range diffusion of Li+ ions inside lithium–titanium oxide crystal (inclined line at low frequencies).4,54–56,75 The results obtained through data fitting are listed in Table 6. One can see, that Ag–Cu modification resulted in lower RCT values of Li4Ti5O12/Ag–Cu composites, suggesting faster reaction kinetics and increased conductivity of synthesized composite powders. After reaching 3% wt of Ag–Cu modification the charge-transfer resistance stabilizes in the range of 17–25 Ω, which is ca. 30 Ω lower than for pristine sample.
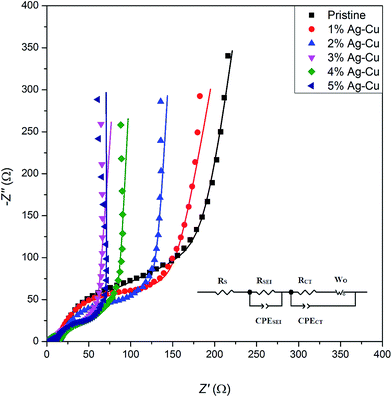 |
| Fig. 14 Complex plane plots of Li4Ti5O12/Ag–Cu composites. Inset shows the equivalent circuit used for data fitting. | |
Table 6 Data acquired after fitting and analysis of EIS spectra of Li4Ti5O12/Ag–Cu composites
Material |
Electrode loading [mg cm−2] (±0.02 mg cm−2) |
RS [Ω] |
RSEI [Ω] |
RCT [Ω] |
DEIS [cm2 s−1] |
Pristine |
2.13 |
2.82 ± 0.05 |
14.26 ± 0.19 |
58.78 ± 2.60 |
(6.20 ± 0.69) × 10−14 |
1% Ag–Cu |
2.25 |
3.47 ± 0.03 |
12.67 ± 0.19 |
62.81 ± 2.60 |
(1.12 ± 0.11) × 10−13 |
2% Ag–Cu |
2.08 |
3.08 ± 0.03 |
14.52 ± 0.18 |
50.57 ± 2.02 |
(1.31 ± 0.14) × 10−13 |
3% Ag–Cu |
2.23 |
2.36 ± 0.02 |
6.57 ± 0.14 |
24.48 ± 1.85 |
(1.64 ± 0.16) × 10−13 |
4% Ag–Cu |
2.19 |
2.34 ± 0.06 |
16.09 ± 0.21 |
17.27 ± 1.24 |
(1.98 ± 0.10) × 10−13 |
5% Ag–Cu |
1.91 |
3.13 ± 0.04 |
9.72 ± 0.13 |
22.03 ± 1.20 |
(2.53 ± 0.27) × 10−13 |
We calculated Li+ ion chemical diffusion coefficient from EIS data by using the equation:13,15,25,26,34,47
|
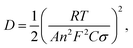 | (5) |
in which
σ is a Warburg coefficient (Ω s
−1), corresponding to a slope of
Z′(
ω−1/2) function, described by equation:
and fulfilled for the frequency range in which the EIS spectrum is inclined to
Z′ axis at 45° (
Fig. 15). The rest of the symbols have the same meaning as in
eqn (3). The acquired
D values are presented on
Fig. 16 and listed in
Table 6. The obtained lithium ion chemical diffusion coefficient values show similar trend with increasing Ag–Cu content in Li
4Ti
5O
12/Ag–Cu composite as in the case of CV experiments. One can see an increase in
D values with increasing amount of Ag–Cu modification – from (6.20 ± 0.69) × 10
−14 cm
2 s
−1 for pristine powder to (2.53 ± 0.27) × 10
−13 cm
2 s
−1 for Li
4Ti
5O
12/Ag–Cu composite. EIS results are also in good agreement with galvanostatic tests and with our previous studies about Li
4Ti
5O
12/n-Ag compounds
78,79 and can be explained by enhancing the surface conductivity of Li
4Ti
5O
12, enhancing its electrochemically active surface area and providing more active centers for intercalation/deintercalation reactions to take place.
79 Also in this case, the saturation of
D values is not present, which suggest not fully covered crystals of Li
4Ti
5O
12 by Ag–Cu modification, as seen on SEM and XPS results, and lower electrochemically active surface area than in our previous studies about Li
4Ti
5O
12/n-Ag compounds.
79
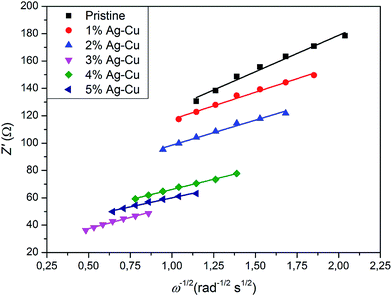 |
| Fig. 15 Z′(ω−1/2) relationship acquired from EIS experiments of Li4Ti5O12/Ag–Cu composites. | |
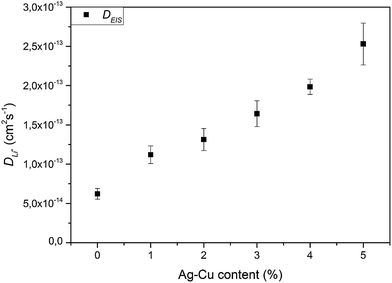 |
| Fig. 16 Li+ chemical diffusion coefficient values calculated from EIS spectra of Li4Ti5O12/Ag–Cu composites. | |
4. Conclusions
We successfully synthesized lithium–titanium oxide and modified its surface with Ag–Cu metals. The XRD and SEM experiments showed a presence of metallic nanoparticles, 100 nm in diameter, in examined powders. XPS experiments revealed lower surface concentration of Ag–Cu particles than in the case of Li4Ti5O12/5% n-Ag composite. Galvanostatic charge/discharge evaluation of studied materials showed enhanced electrochemical properties of Li4Ti5O12 powders after Ag–Cu modification, namely ca. 12.5% increase in specific capacity retention at 10C current rate and ca. 19 mAh g−1 increase in specific capacity at 10C current rate were observed. Furthermore, CV and EIS experiments showed an increase in Li+ chemical diffusion coefficient values with increasing amount of Ag–Cu present in Li4Ti5O12/Ag–Cu composites and decrease in examined powders impedance and charge-transfer resistance after Ag–Cu surface modification.
Enhanced electrochemical properties of Li4Ti5O12/Ag–Cu composites are an effect of Li4Ti5O12 surface activation through contact with conductive particles. That mechanism was more thoroughly explained in our previous work.79 This research is in very good agreement with our previous studies about Li4Ti5O12/n-Ag composites78,79 and gives insight on the influence of conductive particles morphology and surface coverage on electrochemistry of electrode materials. It also further confirms a positive effect of conductive nanoparticles deposition on electrode's material surface on its electrochemical properties for next generation of lithium-ion batteries. Additional studies are currently in progress, involving Li4Ti5O12 modified only with copper element and controlling the morphology of metal deposits by using reducing and complexing agents.
Conflicts of interest
There are no conflicts to declare.
Acknowledgements
This work was supported by The Polish National Centre of Research and Development through the research grant PBS1/A1/4/2012 and by The Polish National Centre of Science through the research grant UMO-2014/15/B/ST5/02118.
References
- S. Panero, P. Reale, F. Ronci, B. Scrosati, P. Perfetti and V. R. Albertini, Refined, in-situ EDXD structural analysis of the Li[Li1/3Ti5/3]O4 electrode under lithium insertion-extraction, Phys. Chem. Chem. Phys., 2001, 3, 845 RSC.
- T. Ohzuku, A. Ueda and N. Yamamoto, Zero-Strain Insertion Material of Li[Li1/3Ti5/3]O4 for Rechargeable Lithium Cells, J. Electrochem. Soc., 1995, 142, 1431 CrossRef CAS.
- T. Nordh, R. Younesi, D. Brandell and K. Edström, Depth profiling the solid electrolyte interface on lithium titanate (Li4Ti5O12) using synchrotron-based photoelectron spectroscopy, J. Power Sources, 2015, 294, 173 CrossRef CAS.
- R. Dedryvère, D. Foix, S. Franger, S. Patoux, L. Daniel and D. Gonbeau, Electrode/Electrolyte Interface Reactivity in High-Voltage Spinel LiMn1.6Ni0.4O4/Li4Ti5O12 Lithium-Ion Battery, J. Phys. Chem. C, 2010, 114, 10999 Search PubMed.
- H. Ge, N. Li, D. Li, C. Dai and D. Wang, Study on the Theoretical Capacity of Spinel Lithium Titanate Induced by Low-Potential Intercalation, J. Phys. Chem. C, 2009, 113, 6324 CAS.
- C. Y. Ouyang, Z. Y. Zhong and M. S. Lei, Ab initio studies of structural and electronic properties of Li4Ti5O12 spinel, Electrochem. Commun., 2007, 9, 1107 CrossRef CAS.
- T.-F. Yi, L.-J. Jiang, J. Shu, C.-B. Yue, R.-S. Zhu and H.-B. Qiao, Recent development and application of Li4Ti5O12 as anode material of lithium ion battery, J. Phys. Chem. Solids, 2010, 71, 1236 CrossRef CAS.
- T.-F. Yi, S.-Y. Yang and Y. Xie, Recent advances of Li4Ti5O12 as a promising next generation anode material for high power lithium-ion batteries, J. Mater. Chem. A, 2015, 3, 5750 CAS.
- W. Ojczyk, J. Marzec, K. Swierczek, W. Zajac, M. Molenda, R. Dziembaj and J. Molenda, Studies of selected synthesis procedures of the conducting LiFePO4-based composite cathode materials for Li-ion batteries, J. Power Sources, 2007, 173, 700 CrossRef CAS.
- G. Xu, Z. Liu, C. Zhang, G. Cui and L. Chen, Strategies for improving the cyclability and thermos-stability of LiMn2O4-based batteries at elevated temperatures, J. Mater. Chem. A, 2015, 3, 4092 CAS.
- D. Ziolkowska, K. Korona, B. Hamankiewicz, S.-H. Wu, M.-S. Chen, J. B. Jasinski, M. Kaminska and A. Czerwinski, The role of SnO2 surface coating on the electrochemical performance of LiFePO4 cathode materials, Electrochim. Acta, 2013, 108, 532 CrossRef CAS.
- M. Michalska, B. Hamankiewicz, D. Ziolkowska, M. Krajewski, L. Lipinska, M. Andrzejczuk and A. Czerwinski, Influence of LiMn2O4 modification with CeO2 on electrode performance, Electrochim. Acta, 2014, 136, 286 CrossRef CAS.
- B. Hamankiewicz, M. Michalska, M. Krajewski, D. Ziolkowska, L. Lipińska, K. Korona, M. Kaminska and A. Czerwinski, The effect of electrode thickness on electrochemical performance of LiMn2O4 cathode synthesized by modified sol-gel method, Solid State Ionics, 2014, 262, 9 CrossRef CAS.
- W. Liu, J. Zhang, Q. Wang, X. Xie, Y. Lou and B. Xia, The effects of Li2CO3 particle size on the properties of lithium titanate as anode material for lithium-ion batteries, Ionics, 2014, 20, 1553 CrossRef CAS.
- T.-F. Yi, S.-Y. Yang, M. Tao, Y. Xie, Y.-R. Zhu and R.-S. Zhu, Synthesis and application of a novel Li4Ti5O12 composite as anode material with enhanced fast charge-discharge performance for lithium-ion battery, Electrochim. Acta, 2014, 134, 377 CrossRef CAS.
- X. Li, H. Hu, S. Huang, G. Yu, L. Gao, H. Liu and Y. Yu, Nano-sized Li4Ti5O12 anode material with excellent performance prepared by solid state reaction: The effect of precursor size and morphology, Electrochim. Acta, 2013, 112, 356 CrossRef CAS.
- W. Liu, J. Zhang, Q. Wang, X. Xie, Y. Lou, X. Han and B. Xia, Microsized TiO2 activated by high-energy ball milling as starting material for the preparation of Li4Ti5O12 anode material, Powder Technol., 2013, 247, 204 CrossRef CAS.
- M. Michalska, M. Krajewski, D. Ziolkowska, B. Hamankiewicz, M. Andrzejczuk, L. Lipinska, K. P. Korona and A. Czerwinski, Influence of milling time in solid-state synthesis on structure, morphology and electrochemical properties of Li4Ti5O12 of spinel structure, Powder Technol., 2014, 266, 372 CrossRef CAS.
- G. Luo, J. He, X. Song, X. Huang, X. Yu, Y. Fang and D. Chen, Bamboo carbon assisted sol-gel synthesis of Li4Ti5O12 anode material with enhanced electrochemical activity for lithium ion battery, J. Alloys Compd., 2015, 621, 268 CrossRef CAS.
- Y.-J. Hao, Q.-Y. Lai, J.-Z. Lua, D.-Q. Liu and X.-Y. Ji, Influence of various complex agents on electrochemical property of Li4Ti5O12 anode material, J. Alloys Compd., 2007, 439, 330 CrossRef CAS.
- R. B. Khomane, A. S. Prakash, K. Ramesha and M. Sathiya, CTAB-assisted sol-gel synthesis of Li4Ti5O12 and its electrochemical performance as anode material for Li-ion batteries, Mater. Res. Bull., 2011, 46, 1139 CrossRef CAS.
- N. Zhang, Z. Liu, T. Yang, C. Liao, Z. Wang and K. Sun, Facile preparation of nanocrystalline Li4Ti5O12 and its high electrochemical performance as anode material for lithium-ion batteries, Electrochem. Commun., 2011, 13, 654 CrossRef CAS.
- C. Jiang, Y. Zhou, I. Honma, T. Kudo and H. Zhou, Preparation and rate capability of Li4Ti5O12 hollow-sphere anode material, J. Power Sources, 2007, 166, 514 CrossRef CAS.
- Q. Zhou, L. Liu, H. Guo, R. Xu, J. Tan, Z. Yan, Z. Huang, H. Shu, X. Yang and X. Wang, Synthesis of nanosheets-assembled lithium titanate hollow microspheres and their application to lithium ion battery anodes, Electrochim. Acta, 2015, 151, 502 CrossRef CAS.
- T.-F. Yi, S.-Y. Yang, Y.-R. Zhu, M.-F. Ye, Y. Xie and R.-S. Zhu, Enhanced rate performance of Li4Ti5O12 anode material by ethanol-assisted hydrothermal synthesis for lithium-ion battery, Ceram. Int., 2014, 40, 9853 CrossRef CAS.
- W. Liu, D. Shao, G. Luo, Q. Gao, G. Yan, J. He, D. Chen, X. Yu and Y. Fang, Mesoporous Spinel Li4Ti5O12 Nanoparticles for High Rate Lithium-ion Battery Anodes, Electrochim. Acta, 2014, 133, 578 CrossRef CAS.
- Y. Li, G. L. Pan, J. W. Liu and X. P. Gao, Preparation of Li4Ti5O12 Nanorods as Anode Materials for Lithium-Ion Batteries, J. Electrochem. Soc., 2009, 156, A495 CrossRef CAS.
- Y. Tang, L. Yang, S. Fang and Z. Qiu, Li4Ti5O12 hollow microspheres assembled by nanosheets as an anode material for high-rate lithium ion batteries, Electrochim. Acta, 2009, 54, 6244 CrossRef CAS.
- T. Yuan, R. Cai, K. Wang, R. Ran, S. Liu and Z. Shao, Combustion synthesis of high-performance Li4Ti5O12 for secondary Li-ion battery, Ceram. Int., 2009, 35, 1757 CrossRef CAS.
- J. Wang, H. Zhao, Y. Wen, J. Xie, Q. Xia, T. Zhang, Z. Zeng and X. Du, High performance Li4Ti5O12 material as anode for lithium-ion batteries, Electrochim. Acta, 2013, 113, 679 CrossRef CAS.
- A. S. Prakash, P. Manikandan, K. Ramesha, M. Sathiya, J.-M. Tarascon and A. K. Shukla, Solution-Combustion Synthesized Nanocrystalline Li4Ti5O12 As High-Rate Performance Li-Ion Battery Anode, Chem. Mater., 2010, 22, 2857 CrossRef CAS.
- J. Li, Y.-L. Jin, X.-G. Zhang and H. Yang, Microwave solid-state synthesis of spinel Li4Ti5O12 nanocrystallites as anode material for lithium-ion batteries, Solid State Ionics, 2007, 178, 1590 CrossRef CAS.
- L. H. Yang, C. Dong and J. Guo, Hybrid microwave synthesis and characterization of the compounds in the Li-Ti-O system, J. Power Sources, 2008, 175, 575 CrossRef CAS.
- S.-L. Chou, J.-Z. Wang, H.-K. Liu and S.-X. Dou, Rapid Synthesis of Li4Ti5O12 Microspheres as Anode Materials and Its Binder Effect for Lithium-Ion Battery, J. Phys. Chem. C, 2011, 115, 16220 CAS.
- S. H. Ju and Y. C. Kang, Effects of types of drying control chemical additives on the morphologies and electrochemical properties of Li4Ti5O12 anode powders prepared by spray pyrolysis, J. Alloys Compd., 2010, 506, 913 CrossRef CAS.
- X. Zhang, H. Xu, Y. Zhao, G. Zhu and A. Yu, A facile one-step spray pyrolysis method to synthesize spherical Li4Ti5O12 for lithium-ion battery, Mater. Lett., 2014, 129, 101 CrossRef CAS.
- V. Miikkulainen, O. Nilsen, M. Laitinen, T. Sajavaara and H. Fjellvåg, Atomic layer deposition of LixTiyOz thin films, RSC Adv., 2013, 3, 7537 RSC.
- S. Ji, J. Zhang, W. Wang, Y. Huang, Z. Feng, Z. Zhang and Z. Tang, Preparation and effects of Mg-doping on the electrochemical properties of spinel Li4Ti5O12 as anode material for lithium ion battery, Mater. Chem. Phys., 2010, 123, 510 CrossRef CAS.
- W. Wang, B. Jiang, W. Xiong, Z. Wang and S. Jiao, A nanoparticle Mg-doped Li4Ti5O12 for high rate lithium-ion batteries, Electrochim. Acta, 2013, 114, 198 CrossRef CAS.
- C. Lin, M. O. Lai, L. Lu, H. Zhou and Y. Xin, Structure and high rate performance of Ni2+ doped Li4Ti5O12 for lithium ion battery, J. Power Sources, 2013, 244, 272 CrossRef CAS.
- S. Huang, Z. Wen, Z. Gu and X. Zhu, Preparation and cycling performance of Al3+ and F− co-substituted compounds Li4AlxTi5-xFyO12-y, Electrochim. Acta, 2005, 50, 4057 CrossRef CAS.
- J. S. Park, S.-H. Baek, Y.-I. Jeong, B.-Y. Noh and J. H. Kim, Effects of a dopant on the electrochemical properties of Li4Ti5O12 as a lithium-ion battery anode material, J. Power Sources, 2013, 244, 527 CrossRef CAS.
- J.-Y. Lin, C.-C. Hsu, H.-P. Ho and S.-H. Wu, Sol-gel synthesis of aluminum doped lithium titanate anode material for lithium ion batteries, Electrochim. Acta, 2013, 87, 126 CrossRef CAS.
- H. Song, S.-W. Yun, H.-H. Chun, M.-G. Kim, K. Y. Chung, H. S. Kim, B.-W. Cho and Y.-T. Kim, Anomalous decrease in structural disorder due to charge redistribution in Cr-doped Li4Ti5O12 negative-electrode materials for high-rate Li-ion batteries, Energy Environ. Sci., 2012, 5, 9903 CAS.
- F. Wu, X. Li, Z. Wang and H. Guo, Synthesis of chromium-doped lithium titanate microspheres as high-performance anode material for lithium ion batteries, Ceram. Int., 2014, 40, 13195 CrossRef CAS.
- X. Li, M. Qu and Z. Yu, Structural and electrochemical performances of Li4Ti5-xZrxO12 as anode material for lithium-ion batteries, J. Alloys Compd., 2009, 487, L12 CrossRef CAS.
- T.-F. Yi, B. Chen, H.-Y. Shen, R.-S. Zhu, A.-N. Zhou and H.-B. Qiao, Spinel Li4Ti5-xZrxO12 (0 ≤ x ≤ 0.25) materials as high-performance anode materials for lithium-ion batteries, J. Alloys Compd., 2013, 558, 11 CrossRef CAS.
- Z. Wang, Z. Wang, W. Peng, H. Guo and X. Li, An improved solid-state reaction to synthesize Zr-doped Li4Ti5O12 anode material and its application in LiMn2O4/Li4Ti5O12 full-cell, Ceram. Int., 2014, 40, 10053 CrossRef CAS.
- T.-F. Yi, J. Shu, Y.-R. Zhu, X.-D. Zhu, C.-B. Yue, A.-N. Zhou and R.-S. Zhu, High-performance Li4Ti5-xVxO12 (0 ≤ x ≤ 0.3) as an anode material for secondary lithium-ion battery, Electrochim. Acta, 2009, 54, 7464 CrossRef CAS.
- C.-C. Yang, H.-C. Hu, S. J. Lin and W.-C. Chien, Electrochemical performance of V-doped spinel Li4Ti5O12/C composite anode in Li-half and Li4Ti5O12/LiFePO4-full cell, J. Power Sources, 2014, 258, 424 CrossRef CAS.
- L. Shi, X. Hu and Y. Huang, Fast microwave-assisted synthesis of Nb-doped Li4Ti5O12 for high-rate lithium-ion batteries, J. Nanopart. Res., 2014, 16, 2332 CrossRef.
- M. Guo, S. Wang, L.-X. Ding, C. Huang and H. Wang, Tantalum-doped lithium titanate with enhanced performance for lithium-ion batteries, J. Power Sources, 2015, 283, 372 CrossRef CAS.
- Y. Qi, Y. Huang, D. Jia, S.-J. Bao and Z. P. Guo, Preparation and characterization of novel spinel Li4Ti5O12-xBrx anode materials, Electrochim. Acta, 2009, 54, 4772 CrossRef CAS.
- J. Wang, Z. Yang, W. Li, X. Zhong, L. Gu and Y. Yu, Nitridation Br-doped Li4Ti5O12 anode for high rate lithium ion batteries, J. Power Sources, 2014, 266, 323 CrossRef CAS.
- Z. Zhao, Y. Xu, M. Ji and H. Zhang, Synthesis and electrochemical performance of F-doped Li4Ti5O12 for lithium-ion batteries, Electrochim. Acta, 2013, 109, 645 CrossRef CAS.
- X. Han, Z. Zhao, Y. Xu, D. Liu, H. Zhang and C. Zhao, Synthesis and characterization of F-doped nanocrystalline Li4Ti5O12/C compounds for lithium-ion batteries, RSC Adv., 2014, 4, 41968 RSC.
- X. Guo, H. F. Xiang, T. P. Zhou, X. K. Ju and Y. C. Wu, Morphologies and structures of carbon coated on Li4Ti5O12 and their effects on lithium storage performance, Electrochim. Acta, 2014, 130, 470 CrossRef CAS.
- J. Wang, X.-M. Liu, H. Yang and X.-D. Shen, Characterization and electrochemical properties of carbon-coated Li4Ti5O12 prepared by a citric acid sol-gel method, J. Alloys Compd., 2011, 509, 712 CrossRef CAS.
- Y. Ren, P. Lu, X. Huang, S. Zhou, Y. Chen, B. Liu, F. Chu and J. Ding, In-situ synthesis of nano-Li4Ti5O12/C composite as an anode material for Li-ion batteries, Solid State Ionics, 2015, 274, 83 CrossRef CAS.
- H.-G. Jung, J. Kim, B. Scrosati and Y.-K. Soon, Micron-sized, carbon-coated Li4Ti5O12 as high power anode for advanced lithium batteries, J. Power Sources, 2011, 196, 7763 CrossRef CAS.
- H. Liu, Y. Feng, K. Wang and J. Xie, Synthesis and electrochemical properties of Li4Ti5O12/C composite by the PVB rheological phase method, J. Phys. Chem. Solids, 2008, 69, 2037 CrossRef CAS.
- X. Li, P. Huang, Y. Zhou, H. Peng, W. Li, M. Qu and Z. Yu, A novel Li4Ti5O12/graphene/carbon nano-tubes hybrid material for high rate lithium ion batteries, Mater. Lett., 2014, 133, 289 CrossRef CAS.
- Y. Yang, B. Qiao, X. Yang, L. Fang, C. Pan, W. Song, H. Hou and X. Ji, Lithium Titanate Tailored by Cathodically Induced Graphene for an Ultrafast Lithium Ion Battery, Adv. Funct. Mater., 2014, 24, 4349 CrossRef CAS.
- J. Zhang, Y. Cai, J. Wu and J. Yao, Graphene oxide-confined synthesis of Li4Ti5O12 microspheres as high-performance anodes for lithium ion batteries, Electrochim. Acta, 2015, 165, 422 CrossRef CAS.
- Y. Ding, G. R. Li, C. W. Xiao and X. P. Gao, Insight into effects of graphene in Li4Ti5O12/carbon composite with high rate capability as anode materials for lithium ion batteries, Electrochim. Acta, 2013, 102, 282 CrossRef CAS.
- X. Li, M. Qu and Z. Yu, Preparation and electrochemical performance of Li4Ti5O12/graphitized carbon nanotubes composite, Solid State Ionics, 2010, 181, 635 CrossRef CAS.
- Z. Wang, Z. Wang, W. Peng, H. Guo and X. Li, Li4Ti5O12 co-modified with carbon nanotubes and pyrolytic carbon as an advanced anode material for lithium-ion batteries, Mater. Lett., 2014, 137, 413 CrossRef CAS.
- T. Liu, H. Ni, W.-L. Song and L.-Z. Fan, Enhanced electrochemical performance of Li4Ti5O12 as anode material for lithium-ion batteries with different carbons as support, J. Alloys Compd., 2015, 646, 189 CrossRef CAS.
- S. Huang, Z. Wen, X. Zhu and Z. Gu, Preparation and electrochemical performance of Ag doped Li4Ti5O12, Electrochem. Commun., 2004, 6, 1093 CrossRef CAS.
- S. Huang, Z. Wen, J. Zhang, Z. Gu and X. Xu, Li4Ti5O12/Ag composite as electrode materials for lithium-ion battery, Solid State Ionics, 2006, 177, 851 CrossRef CAS.
- S. Huang, Z. Wen, J. Zhang and X. Yang, Improving the electrochemical performance of Li4Ti5O12/Ag composite by an electroless deposition method, Electrochim. Acta, 2007, 52, 3704 CrossRef CAS.
- Y.-R. Zhu, T.-F. Yi, H.-T. Ma, Y.-Q. Ma, L.-J. Jiang and R.-S. Zhu, Improved electrochemical performance of Ag-modified Li4Ti5O12 anode material in a broad voltage window, J. Chem. Sci., 2014, 126, 17 CrossRef CAS.
- Z. Liu, N. Zhang, Z. Wang and K. Sun, Highly dispersed Ag nanoparticles (<10 nm) deposited on nanocrystalline Li4Ti5O12 demonstrating high-rate charge/discharge capability for lithium-ion battery, J. Power Sources, 2012, 205, 479 CrossRef CAS.
- H. Ge, L. Chen, S. Lin, X. Shi and X.-M. Song, Advanced electrochemical performances of Li4Ti5O12/Ag prepared by a facile synthesis route, Ionics, 2014, 20, 1189 CrossRef CAS.
- J.-G. Kim, D. Shi, M.-S. Park, G. Jeong, Y.-U. Heo, M. Seo, Y.-J. Kim, J. H. Kim and S. X. Dou, Controlled Ag-driven superior rate-capability of Li4Ti5O12 anodes for lithium rechargeable batteries, Nano Res., 2013, 6, 365 CrossRef CAS.
- G. B. Xu, W. Li, L. W. Yang, X. L. Wei, J. W. Ding, J. X. Zhong and P. K. Chu, Highly-crystalline ultrathin Li4Ti5O12 nanosheets decorated with silver nanocrystals as a high-performance anode material for lithium ion batteries, J. Power Sources, 2015, 276, 247 CrossRef CAS.
- A. Erdas, S. Ozcan, D. Nalci, M. O. Guler and H. Akbulut, Novel Ag/Li4Ti5O12 binary composite anode electrodes for high capacity Li-ion batteries, Surf. Coat. Technol., 2015, 271, 136 CrossRef CAS.
- M. Krajewski, M. Michalska, B. Hamankiewicz, D. Ziolkowska, K. P. Korona, J. B. Jasinski, M. Kaminska, L. Lipinska and A. Czerwinski, Li4Ti5O12 modified with Ag nanoparticles as an advanced anode material in lithium-ion batteries, J. Power Sources, 2014, 245, 764 CrossRef CAS.
- M. Krajewski, B. Hamankiewicz and A. Czerwinski, Voltammetric and impedance characterization of Li4Ti5O12/n-Ag composite for lithium-ion batteries, Electrochim. Acta, 2016, 219, 277 CrossRef CAS.
- S. Huang, Z. Wen, B. Lin, J. Han and X. Xu, The high-rate performance of the newly designed Li4Ti5O12/Cu composite anode for lithium ion batteries, J. Alloys Compd., 2008, 477, 400 CrossRef.
- C. Cheng, H. Liu, X. Xue, H. Cao and L. Shi, Highly dispersed copper nanoparticle modified nano Li4Ti5O12 with high rate performance for lithium ion battery, Electrochim. Acta, 2014, 120, 226 CrossRef CAS.
- N. Li, J. Liang, D. Wei, Y. Zhu and Y. Qian, Solvothermal synthesis of micro-/nanoscale Cu/Li4Ti5O12 composites for high rate Li-ion batteries, Electrochim. Acta, 2014, 123, 346 CrossRef CAS.
- Q. Wang, W. Liu, J. Zhang, X. Xie and B. Xia, Performance of electroless-plated lithium titanate/copper composites as anode materials in 18650-type lithium-ion batteries, J. Solid State Electrochem., 2015, 19, 1411 CrossRef CAS.
- A. Erdas, S. Ozcan, M. O. Guler and H. Akbulut, Sol-Gel Synthesis of Nanocomposite Cu-Li4Ti5O12 Structures for Ultrahigh Rate Li-Ion Batteries, Acta Phys. Pol., A, 2015, 127, 1026 CrossRef.
- W. Wang, Y. Guo, L. Liu, S. Wang, X. Yang and H. Guo, Gold coating for a high performance Li4Ti5O12 nanorod aggregates anode for lithium-ion batteries, J. Power Sources, 2014, 245, 624 CrossRef CAS.
- K.-S. Park, A. Benayad, D.-J. Kang and S.-G. Doo, Nitridation-Driven Conductive Li4Ti5O12 for Lithium Ion Batteries, J. Am. Chem. Soc., 2008, 130, 14930 CrossRef CAS PubMed.
- X. Zhao, Q. Zhou, H. Ming, J. Adkins, M. Liu, L. Su and J. Zheng, Surface nitridation induced high electrochemical performance of Li4Ti5O12 using urea as a nitrogen source, Ionics, 2013, 19, 1843 CrossRef CAS.
- H. Park, T. Song, H. Han and U. Paik, Electrospun Li4Ti5O12 nanofibers sheathed with conductive TiN/TiOxNy layer as an anode for high power Li-ion batteries, J. Power Sources, 2013, 244, 726 CrossRef CAS.
- J. Shu, M. Shui, F. Huang, D. Xu, Y. Ren, L. Hou, J. Cui and J. Xu, Comparative study on surface behaviors of copper current collector in electrolyte for lithium-ion batteries, Electrochim. Acta, 2011, 56, 3006 CrossRef CAS.
- S.-T. Myung, Y. Hitoshi and Y.-K. Sun, Electrochemical behavior and passivation of current collectors in lithium-ion batteries, J. Mater. Chem., 2011, 21, 9891 RSC.
- Y. Zhu and C. Wang, Novel CV for Phase Transformation Electrodes, J. Phys. Chem. C, 2011, 115, 823 CAS.
- D. Linden and T. B. Reddy, Handbook of Batteries, McGraw-Hill, New York, 2002 Search PubMed.
- A. J. Bard and L. R. Faulkner, Electrochemical methods: fundamentals and applications, John Willey & Sons, Inc., New York, 2001 Search PubMed.
- N. Takami, K. Hoshina and H. Inagaki, Lithium Diffusion in Li4/3Ti5/3O4 Particles during Insertion and Extraction, J. Electrochem. Soc., 2011, 158, A725 CrossRef CAS.
|
This journal is © The Royal Society of Chemistry 2017 |
Click here to see how this site uses Cookies. View our privacy policy here.