DOI:
10.1039/C7RA10063A
(Paper)
RSC Adv., 2017,
7, 50537-50545
Efficient hydrolysis and ethanol production from rice straw by pretreatment with organic acids and effluent of biogas plant
Received
9th September 2017
, Accepted 17th October 2017
First published on 30th October 2017
Abstract
The effluent of biogas production plant was used for the pretreatment of rice straw for the improvement of ethanol production. In addition, the organic active ingredients of the effluent, i.e., acetic, butyric, lactic and propionic acids (1–4%), as well as water were employed for the pretreatment at 100 and 140 °C. The results indicated that pretreatment at 100 °C had no significant effect on the performance of subsequent enzymatic hydrolysis and ethanol production by simultaneous saccharification and fermentation (SSF). Among different types of organic acids presented in the effluent, lactic acid showed a better performance. The highest concentration of glucose and ethanol were achieved after 72 h enzymatic hydrolysis and SSF from the straw pretreated at 140 °C with 4% lactic acid. Applying the effluent for the straw pretreatment at 140 °C resulted in an increase in glucose and ethanol concentrations by 42.4 and 47.5%, respectively, compared to those from untreated samples. SEM, FTIR, BET, BJH, and compositional analyses were used to characterize the changes in the structure and composition of rice straw by the pretreatment. Changes in the straw swelling, cellulose crystallinity, pore size distribution, and composition were responsible for the acquired improvements.
Introduction
The high energy demand and the negative environmental impact of fossil fuels have increased the global demand for the development of new energy sources.1 Biofuels are a promising alternative due to flexibility and availability in feedstock, reduction in greenhouse gas emissions, and potential for decreasing the production costs.2,3 Different types of energy crops (first generation) and lignocellulosic biomass (second generation) have been used as biofuel feedstocks. As first generation bioethanol is restricted due to fuel feed/food conflict, second generation bioethanol seems to be the more sustainable source of energy production.4–6 Rice is the third most important grain crop in the world, generating a huge amount of straw every year. The global production of rice straw is estimated to be 650–975 million tons annually, where a minor fraction is utilized as cattle feed and mainly treated as waste. The most common practice of rice straw managing is burning in the fields. On the other hand, the application of this agricultural waste for bioethanol production would provide viable energy in addition to environmental benefits.7–9 However, due to the highly stabile recalcitrant structure of the straw, like other lignocelluloses, enzymatic hydrolysis as the first step of bioethanol production cannot be effectively performed without introducing a suitable pretreatment step.10 Different types of pretreatment methods aiming at the reduction of biomass recalcitrance have been examined10–15
Dilute acid pretreatment is known to be one of the most promising methods due to low cost and for keeping the cellulose in the solid residue for the subsequent enzymatic hydrolysis.7 The hemicellulose fraction is removed, liberating dissolved sugars and disrupting lignin structure, leading to increased reaction rate in the subsequent cellulose hydrolysis. Besides availability, its low cost has made sulfuric acid as the most widely used acid for the pretreatment of lignocellulosic biomass.16,17 However, pretreatment with sulfuric acid leads to the degradation and loss of free sugars and formation of inhibitory compounds, affecting subsequent fermentation. Moreover, the need for neutralization after the pretreatment step will produce large amounts of gypsum, which cause environmental concern.18 All these drawbacks make it necessary to find a replacement for sulfuric acid in lignocellulosic biomass pretreatment processes.19,20 Organic acids might be suitable alternatives, because they are environmentally friendly and improve the quality of by-products such as the remaining solids left after the recovery of ethanol to be used as animal feed, soil fertilizer, and co-firing installations fuel.19 Kootstra et al.19 reported the effect of fumaric, maleic, and sulfuric acid pretreatment on wheat straw at different conditions and evaluated the possible improvement of enzymatic hydrolysis. They have found fumaric and maleic acids as suitable candidates to replace sulfuric acid in pretreatment. Scordia et al.21 showed that oxalic acid pretreatment can effectively remove hemicellulose from giant reed, improving the accessibility of the solid residue for enzymatic hydrolysis and simultaneous saccharification and fermentation. In another study, the effect of oxalic acid pretreatment was investigated after deacetylation of yellow poplar by NaOH. Without detoxifying the pretreated hydrolysate, 90.93% of theoretical ethanol yield was achieved by simultaneous saccharification and fermentation at the optimum conditions.22
A large amount of effluent is produced every year in anaerobic digestion plants. Handling of this waste is a serious concern of biogas plants worldwide. Typically, the outlet slurry of the plants is dewatered, e.g., by centrifugation, the sludge is recycled to the anaerobic digestion bioreactor, and the effluent is discharged to the environment. However, the effluent contains notable amounts of organic substances and other materials that accompanied with serious health risk and environmental problems when released without additional treatment. Diluting effluent with water is a conventional way to solve this problem. Increment in the wastewater volume and high processing costs are the main problems of this conventional method.23 Thus, other options such as incineration and landfilling as well as its utilization as fertilizer are considered. Discharging the digested effluent in farming areas cause nitrogen pollution. In addition, this method is not suitable for municipal area because of limited agricultural area and unpleasant smell of the effluent.24–26 Therefore, finding an appropriate procedure for dealing with this waste can help biogas technology.
The organic part of biogas plants effluent mainly composed of short chain organic acids, including acetic acid, butyric acid, lactic acid, and propionic acid. To our knowledge, applying this source for the pretreatment of lignocellulosic materials has not considered yet. Using this waste stream instead of water or other chemicals may reduce environmental problems in addition to decreasing the pretreatment processing cost.
The aim of this study was to evaluate the effects of biogas plant effluent and its organic ingredients, i.e., acetic acid, butyric acid, lactic acid, and propionic acid, for the pretreatment of rice straw. The pretreated rice straws were subjected to enzymatic hydrolysis as well as ethanol production. Furthermore, chemical and structural characterization of pretreated rice straw as well as untreated straw were carried by scanning electron microscopy (SEM), Fourier transformation infrared (FTIR), and Brunauer–Emmett–Teller (BET), and Barrett–Joyner–Halenda (BJH), to identify changes made by pretreatment.
Material and methods
Raw materials
Rice straw was obtained from a local farm near Lenjan, Isfahan, Iran. The straw was milled and screened by 20 and 80 meshes, to achieve the particle size of between 0.18–0.88 mm. The sieved rice straw was stored at room temperature until further use. The dry weight was determined after keeping the straw in an oven at 105 °C overnight. The effluent of a 7000 m3 biogas reactor (Isfahan Municipal Wastewater Treatment Plant, Isfahan, Iran) was used for the pretreatment. The effluent was anaerobically handled and centrifuged at 4000 rpm for 20 min and the liquid phase was used for the pretreatments.
Pretreatment
Acetic, butyric, lactic, and propionic acids with the concentrations of 1 and 4% v/v were used for the pretreatments. Besides, the supernatant obtained after centrifugation of biogas effluent as well as water was also applied for pretreating the straw. The straw (17 g) was mixed with pretreatment liquid (250 mL) in a 500 mL stainless steel reactor. Pressure and temperature of the reactor were monitored (using a thermostat and a pressure indicator) during the process. Using an oil bath, the reactor temperature was gradually increased to the desired temperature (i.e. 100 °C or 140 °C) at a rate of 5 °C min−1 and kept at these final values for 30 min. Then, the reactor was cooled down in a cold water bath to decrease the temperature and pressure. After opening the reactor, the solid phase was separated by centrifugation (6000 rpm for 5 min) and washed with pure water several times until pH 7. The neutralized solid then was dried at room temperature for 48 h and stored in plastic bags.
Enzymatic hydrolysis
Enzymatic hydrolysis of raw and treated rice straw was conducted in 118 mL glass bottles by suspending 25 g L−1 substrate in 50 mM sodium citrate buffer at pH of 4.8. After autoclaving the suspension at 121 °C for 20 min, the mixture was cooled down to room temperature. Then, 30 FPU cellulase (Cellic CTec2, Novozymes, Denmark) and 60 IU β-glucosidase (Cellic HTec2, Novozymes, Denmark) per gram of substrate were added. To prevent contamination and microbial growth, 0.5 g L−1 sodium azide was also added to mixtures. All enzymatic hydrolysis experiments were conducted at 45 °C and 125 rpm in a shaker incubator for 72 h. All of the experiments were performed in duplicates.
Simultaneous saccharification and fermentation (SSF)
The SSF experiments were performed in 118 mL glass bottles at 37 °C and 125 rpm for 72 h under anaerobic conditions. Cell growth nutrients (5 g L−1 yeast extract, 7.5 g L−1 (NH4)2SO4, 3.5 g L−1 K2HPO4, 0.75 g L−1 MgSO4·7H2O, and 1.0 g L−1 CaCl2·2H2O) were added to 50 mM sodium citrate buffer, and then the pH was adjusted to 5 using 2.5 M sodium hydroxide. Next, 50 g L−1 treated and untreated straw were added to the medium. The mixtures were then autoclaved for 20 min at 120 °C. After cooling down to room temperature, the mixtures were supplemented with 1 g L−1 Saccharomyces cerevisiae together with 20 FPU cellulase and 30 IU β-glucosidase per gram of substrate. The strain of S. cerevisiae CCUG53310 used in all ethanol fermentation was a fluctuation strain obtained from Culture Collection of University of Gothenburg, Sweden. The SSF process was performed in a shaker incubator under anaerobic conditions. All SSF experiments were conducted in duplicates.
Analyses
Total solids (TS) and volatile solids (VS) of treated and untreated rice straw were measured by drying at 105 °C until constant weight followed by heating at 575 °C until constant weight.27 The volatile fatty acid concentration of biogas effluent was measured with GC (SP 3420a, Beijing Beifen Ruili Analytical Instrument CO, China) after centrifuging and filtrating the supernatant. Nitrogen and hydrogen were used at the flow rate of 45 mL min−1 and 25 mL min−1, respectively, as carrier gas. Column temperature was increased to 125 °C and maintained at this temperature. Injector and detector temperatures were set at 115 and 200 °C, respectively.
According to NREL/TP-510-42618 method, a two-step acid hydrolysis was performed to determine carbohydrates and lignin contents of the samples.28
The crystallinity index and structural changes of the rice straw after pretreatment were investigated using FTIR spectroscopy (TENSOR 27 FT-IR, Bruker, Leipzig, Germany) equipped with a universal attenuated total reflection (ATR) accessory and a deuterated triglycine sulfate (DTGS) detector. The spectra were obtained with an average of 60 scans and resolution of 4 cm−1 from 600 to 4000 cm−1.
The effects of the pretreatment on the substrate surface morphology were studied by SEM. Treated and untreated straw samples were dried for 24 h in the freeze dryer, coated with gold (Emitech SC7640 Sputter Coater), and the pictures were captured with SEM (Zeiss, Jena, Germany) at 13 kV with 500 times magnification.
BET specific surface areas and BJH pore size distributions of the samples were determined by nitrogen adsorption/desorption at 77 K using BELSORP-miniII instrument. Nitrogen molecules are big enough to enter the pores with sufficient size during the analysis, so the BET surface area is a good estimate for enzyme accessible surface area.29 Before analysis, the samples were subjected to degasification at 60 °C for 2 h.
Results
Pretreatment
The biogas effluent used in this study contained 0.9 g L−1 acetic acid, 0.2 g L−1 butyric acid, 0.2 g L−1 lactic acid, and 0.1 g L−1 propionic acid.
Table 1 reports the TS and VS contents as well as the percentage of solid recovery after the treatment of rice straw at different conditions. As it is shown, the solid recovery yield has decreased for straw treated at higher temperatures.
Table 1 Total solids, volatile solids, and solid recovery of treated and untreated rice straw
Pretreatment conditions |
Total solid (%) |
Volatile solid (%) |
Recovery (%) |
Acetic acid (1%, 100 °C) |
95.2 |
87.5 |
85.7 |
Acetic acid (4%, 100 °C) |
96.1 |
88.1 |
82.9 |
Butyric acid (1%, 100 °C) |
93.9 |
86.3 |
86.0 |
Butyric acid (4%, 100 °C) |
96.5 |
88.1 |
82.4 |
Lactic acid (1%, 100 °C) |
97.4 |
90.3 |
79.5 |
Lactic acid (4%, 100 °C) |
97.2 |
88.5 |
83.7 |
Propionic acid (1%, 100 °C) |
96.2 |
86.6 |
79.1 |
Propionic acid (4%, 100 °C) |
97.7 |
86.9 |
83.3 |
Biogas effluent (100 °C) |
95.7 |
86.7 |
83.5 |
Water (100 °C) |
95.6 |
86.1 |
75.9 |
Acetic acid (1%, 140 °C) |
96.5 |
89.1 |
78.6 |
Acetic acid (4%, 140 °C) |
96.2 |
88.8 |
72.5 |
Butyric acid (1%, 140 °C) |
97.4 |
88.2 |
64.4 |
Butyric acid (4%, 140 °C) |
97.1 |
88.5 |
74.9 |
Lactic acid (1%, 140 °C) |
97.1 |
90.3 |
72.0 |
Lactic acid (4%, 140 °C) |
97.6 |
86.4 |
63.7 |
Propionic acid (1%, 140 °C) |
97.6 |
87.4 |
58.5 |
Propionic acid (4%, 140 °C) |
96.7 |
88.3 |
73.6 |
Biogas effluent (140 °C) |
97.6 |
89.0 |
70.2 |
Water (140 °C) |
97.0 |
87.6 |
77.9 |
Untreated |
96.8 |
85.8 |
100.0 |
Enzymatic hydrolysis of untreated and treated rice straw
The result of glucose production from untreated and treated straws after 24 h and 72 h enzymatic hydrolysis are shown in Fig. 1. The glucose concentration obtained after 72 h enzymatic hydrolysis of raw straw was 6.9 g L−1. This amount was increased to 14.6 g L−1 for straw treated with 4% lactic acid at 140 °C, which was the highest increment achieved among the treated samples. The amount of liberated glucose increased after all pretreatment, except for the pretreatment with water at 100 °C. Water at low temperature was not strong enough to break the lignocellulosic structure of straw. The results indicate that pretreatment temperature and acid concentration had important effects on the amount of sugar released during enzymatic hydrolysis process. As results shown, acetic acid, butyric acid, and propionic acid had the same effects; however, lactic acid acted in a different way. Inoculum supernatant was also found effective in increasing straw digestibility. Pretreatment at 140 °C with this challenging waste increased sugar concentration by 42% after 72 h hydrolysis.
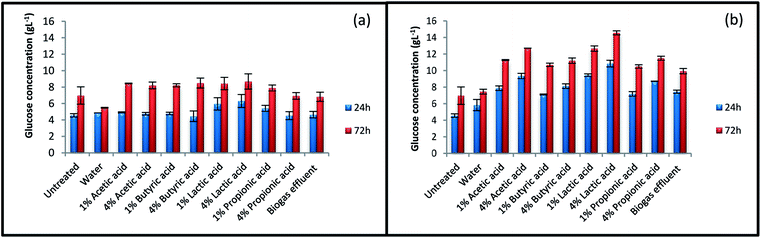 |
| Fig. 1 Glucose concentration of untreated and various treated straws. Treatments were performed at (a) 100 °C and (b) 140 °C. | |
Ethanol production
Fig. 2 summarizes ethanol concentration for untreated and treated rice straw after 24 and 72 h SSF process. No major enhancements were observed in ethanol concentration for the samples treated at 100 °C, even for some of the samples, the amount of ethanol has decreased after the treatment. The results for ethanol concentration indicate that more severe condition is needed for pretreatment to enhance ethanol concentration. Treatment at 140 °C showed positive effect on ethanol production. Ethanol concentration was improved from 5.2 g L−1 for untreated straw to 9.7 g L−1 for straw treated with 4% lactic acid at 140 °C. The highest amount of glucose concentration was also achieved at this condition during enzymatic hydrolysis process (Fig. 1). After pretreatment with 4% lactic acid, ethanol concentration at the end of 72 h SSF process for straw treated with 1% lactic acid, effluent, and 4% acetic acid at 140 °C was 7.9, 7.7, and 7.5 g L−1, respectively.
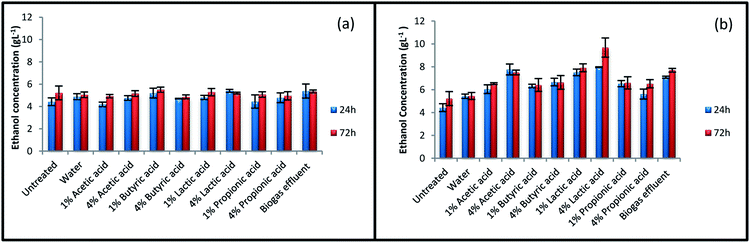 |
| Fig. 2 Ethanol concentration of treated and various untreated straws. Treatments were performed at (a) 100 °C and (b) 140 °C. | |
Effect of pretreatment on composition of rice straw
The chemical characterization results for untreated and treated rice straw are presented in Table 2. Cellulose was the main component in both treated and untreated straw. About half of the rice straw dry weight was glucan, which is providing a potential substrate for sugar and ethanol production. The pretreatments resulted in significant changes in the composition of rice straw, particularly after the treatment at high temperature. The highest increment was gained after treatment with 1% lactic acid at 140 °C, corresponding to 27% increase in glucan content as compared to that of untreated straw. Moreover, the treatment at 100 °C resulted in the liberation of xylose and other hemicellulosic sugars. Remarkable hemicellulose release was observed after treatment with 1% lactic acid and 4% acetic acid at 140 °C (Table 2). In agreement with previous studies, e.g., Hue et al. and Kumar et al., no significant lignin removal was obtained after the dilute acid treatments. For some of the samples, an increase in the lignin content was observed due to the reduction of hemicellulose from the solid fraction during the treatment.17,30 Rice straw contains a minor portion of lignin in comparison to other lignocellulosic biomass such as wheat straw and corn stover. Therefore, the hydrolytic degradation of rice straw was not strongly affected by the lignin content.17
Table 2 Constituent of untreated and pretreated solid residuesa
Pretreatment condition |
Temperature (°C) |
Glucanb (%) |
Xylan (%) |
Arabinan (%) |
Total lignin (%) |
Ash (%) |
The reported values are the averages of duplicate analyses. The range of variations was not more than 5%. The calculation is based on oven dry weight of samples. |
Untreated straw |
— |
44.8 |
28.4 |
0.7 |
11.2 |
5.8 |
Acetic acid (1%) |
100 |
50.6 |
19.7 |
1.0 |
12.2 |
6.6 |
Butyric acid (1%) |
100 |
50.6 |
19.9 |
0.8 |
10.9 |
6.8 |
Lactic acid (4%) |
100 |
48.7 |
23.1 |
0.3 |
10.3 |
6.7 |
Propionic acid (1%) |
100 |
45.1 |
27.8 |
0.6 |
11.1 |
6.4 |
Biogas effluent |
100 |
46.8 |
25.0 |
0.8 |
10.8 |
6.9 |
Water |
140 |
52.2 |
20.9 |
0.7 |
10.5 |
6.2 |
Acetic acid (4%) |
140 |
63.0 |
9.2 |
0.0 |
12.6 |
7.2 |
Butyric acid (1%) |
140 |
55.1 |
18.4 |
0.1 |
10.9 |
5.6 |
Lactic acid (1%) |
140 |
71.8 |
3.8 |
0 |
14.9 |
8.1 |
Propionic acid (1%) |
140 |
58.2 |
13.7 |
0.1 |
13.7 |
7.2 |
Biogas effluent |
140 |
50.7 |
20.0 |
0.8 |
10.3 |
7.4 |
Effect of pretreatment on rice straw morphology
Changes in the morphology of straw by pretreatments were investigated using SEM images (Fig. 3). Comparing SEM images of treated and untreated straw shows remarkable changes in the surface structure and porosity. As it is shown in Fig. 3a, untreated straw had a packed structure covered by a layer of silica. However, due to the treatment, the silica layer was opened up, resulting in the increased accessible surface area for the enzyme penetration (Fig. 3b–d). Samples treated with water and 4% v/v lactic acid at 140 °C had a demolished structure (Fig. 3b and c) and the sample treated with effluent supernatant had a swelled shape.
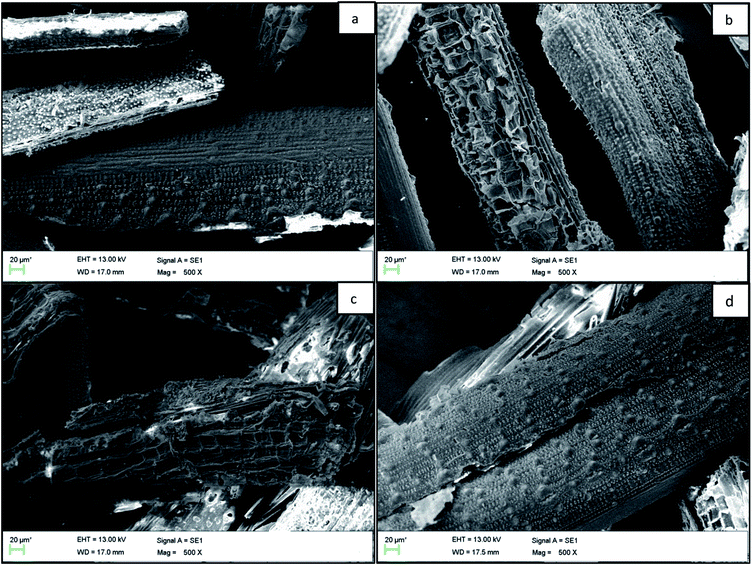 |
| Fig. 3 SEM image of (a) untreated rice straw and the straw pretreated at 140 °C with (b) water, (c) 4% lactic acid, (d) biogas effluent. | |
Effect of pretreatment on the rice straw crystallinity
TIR analysis was used to identify functional groups presented within the substrate and to determine the conversion of crystalline cellulose to amorphous cellulose as a result of the treatment.31 Cellulose is categorized according to hydrogen bonds as cellulose I (crystal domains) and cellulose II (amorphous domains). Cellulose I contain two intramolecular bonds (O(2)H⋯O(6) and O(3)H⋯O(5)) and also one intermolecular bond (O(6)H⋯O(3)). Cellulose II include three intramolecular bonding of (O(2)H⋯O(6), O(3)H⋯O(5), and O(2)H⋯O(2)), as well as two intermolecular bonding of (O(6)H⋯O(2) and O(6)H⋯O(3)). The absorption band at 1430 cm−1 indicate cellulose I which has high resistance to hydrolysis, and absorption band 896 cm−1 indicate cellulose II with easier digestibility. Crystallinity index (CI) is defined as ratio A1430/A869.32 The base lines of spectra were corrected first and then normalized at a band position of 1510 cm−1.33,34 FTIR results of selected samples are presented in Fig. 4 and in Table 3. According to the results, CI was decreased by pretreatments. CI reduction indicates the presence of more cellulose II and less cellulose I in the pretreated solids. The intensity reductions of broad bands at near 3200 cm−1 after treatment, indicate the disruption of cellulose hydrogen bonds. Furthermore, a decline in adsorption peaks at 1740 cm−1, which was responsible for ester linkage between hemicellulose and lignin, was also observed after the treatment. Diminishing this ester groups makes easier hydrolysis of hemicellulose. The increases in intensity in the region between 850–1200 cm−1 for the treated samples was attributed to more cellulose content.
 |
| Fig. 4 FTIR spectrum of untreated and pretreated straw. | |
Table 3 FTIR spectrum of untreated and pretreated straw
Wavenumber (cm−1) |
Functional group |
Band assignment |
Untreated straw |
Water treated straw (100 °C) |
4% lactic acid treated straw (140 °C) |
Biogas effluent treated straw (140 °C) |
3327 |
–OH stretching intramolecular hydrogen bonds |
Cellulose II |
4.42 |
4.082 |
4.086 |
3.808 |
2918 |
C–H stretching cellulose |
Cellulose |
1.88 |
1.72 |
1.47 |
1.47 |
1724 |
C O stretching of acetyl or carboxylic acid |
Hemicellulose & lignin |
1.25 |
1.13 |
0.8 |
0.74 |
1627 |
C C stretching of the aromatic ring |
Lignin |
2.47 |
1.93 |
1.7 |
1.9 |
1465 |
Asymmetric bending in C–H3 |
Lignin |
1.64 |
1.57 |
1.47 |
1.51 |
1430 |
C–H2 bending |
Cellulose |
1.69 |
1.57 |
1.45 |
1.56 |
1375 |
C–H bending |
Cellulose |
1.81 |
1.81 |
1.69 |
1.73 |
1315 |
C–H2 wagging |
Cellulose |
1.94 |
1.79 |
1.85 |
1.85 |
1245 |
C–O adsorption |
Cellulose |
2.02 |
2.15 |
1.98 |
1.97 |
1158 |
C–O–C asymmetric stretching |
Cellulose |
2.85 |
3.10 |
3.25 |
3.25 |
1056 |
C–O stretch |
|
4.61 |
4.69 |
5.15 |
5.33 |
896 |
Asym., out of phase ring stretching (cellulose) |
Cellulose |
0.50 |
0.64 |
0.67 |
0.64 |
CI 1430/896 |
|
|
3.32 |
2.62 |
2.15 |
2.44 |
Effect of pretreatment on surface area and pore diameter distribution
Adsorption of endoglucanases and cellobiohydrolases onto cellulose surface is the first step of hydrolysis; therefore, the accessible surface area is an important parameter in the hydrolysis process.35 Cellulase enzyme has access to the pores with diameter bigger than 5.4 nm; thus, pore size distribution as well as the accessible surface area plays an important role.36
The mean pore diameter of treated straw was considerably increased in comparison to that of untreated straw. Furthermore, treated straws had their maximum at larger pore areas according to the pore size distribution diagram, Fig. 5. Also, the specific surface area has decreased slightly for the treated samples, but as pore size distribution diagram shows, most of the surface area for untreated straw is attributed to small diameter pores. A notable enhance has occurred in the mean pore size diameter and maximum of pore size distribution after treatment (Table 4).
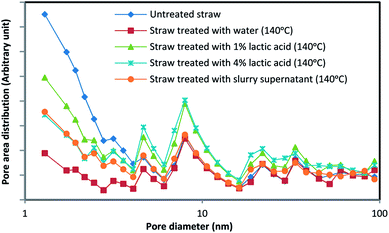 |
| Fig. 5 Pore size distribution of samples. | |
Table 4 BET results for 5 substrates
Substrate |
as, BET m2 g−1 |
Total pore volume, cm3 g−1 |
Mean pore diameter, nm |
Untreated straw |
3.36 |
0.022 |
26.17 |
Straw treated with water (140 °C) |
3.16 |
0.020 |
37.31 |
Straw treated with 1% lactic acid (140 °C) |
3.34 |
0.028 |
33.49 |
Straw treated with 4% lactic acid (140 °C) |
3.3 |
0.029 |
34.88 |
Straw treated with biogas effluent (140 °C) |
2.62 |
0.022 |
33.46 |
Overall mass balance
Fig. 6 shows the overall mass balance for the straw treated with 1% lactic acid at 140 °C through the pretreatment, enzymatic hydrolysis, and SSF process steps. Pretreatment at this condition and neutralizing with water caused in a loss of 64% of solids. The solid residue was then dried and used to produce ethanol.
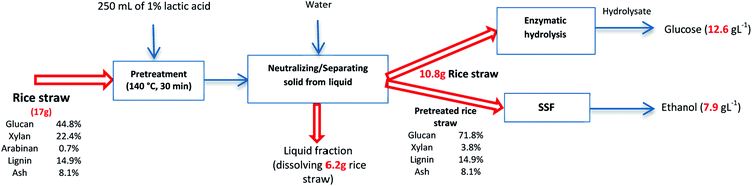 |
| Fig. 6 Overall mass balance of rice straw treated at 140 °C with 1% lactic acid for 30 min. | |
Discussion
Adequate composition and plentiful availability of rice straw have made this biomass as an attractive candidate for bioethanol production. On the other hand, the recalcitrant structure of straw should be diminished before enzymatic hydrolysis and subsequent ethanol production. Therefore, pretreatment is an essential stage before saccharification and fermentation of the straw.37–39 Dilute acid pretreatment was performed by different group of researchers. Most of the researches were focused on using mineral acids especially sulfuric acid for treatment.40–42 Despite less negative environmental impact of organic acids, a few researches have been done on pretreating lignocelluloses with organic acids.18,19,21 Furthermore, biogas effluent supernatant seems to be a source of weak organic acid and other useful material for the destruction of straw resistant structure. In this study, four organic acids, water, and supernatant of biogas plant effluent were evaluated to improve enzymatic hydrolysis and ethanol production by SSF. Dilute acid pretreatment was supposed to disintegrate hemicellulose structure and redistribute lignin presented in the lignocellulosic structure of rice straw.43,44 Temperature plays an important role in the pretreatment effectiveness. As results showed, pretreating at 100 °C caused a minor change in rice straw composition (Table 2). In agreement with composition analysis results, no remarkable enhancement was obtained in glucose and ethanol yields of treated straw at 100 °C after 72 h enzymatic hydrolysis and SSF (Fig. 1 and 2). By raising pretreatment temperature to 140 °C, the glucan content of pretreated solid residue was notably increased (Table 2). This increment could be as a result of hemicellulose dissolution in liquid portion. By omission of xylose as a glucan barrier, enzyme penetration has become easier and the glucose and ethanol concentration has increased. Previous studies also showed that pretreatment efficiency was increased at higher temperature.19,45,46 SEM, FTIR, and BET analyses also show the reduction in CI, changes in packed structure, and enhancement in mean pore size diameter after treatment (Fig. 3, Table 3, Fig. 4, 5, and Table 4). As a consequence of all these detected structural changes, higher glucose and ethanol concentration could be achieved from treated samples. Acetic acid, butyric acid, and propionic acid pretreatments led to the similar performance. These acids have similar chemical structure and have acted during pretreatment process in a similar way. Lactic acid has one more hydroxyl group in comparison to the other three acids. This led to the formation of more hydrogen bonds between lactic acid and the lignocellulosic structure, resulting in better performances. From straw pretreated with 4% lactic acid at 140 °C, the highest glucose yield achieved after 72 h enzymatic hydrolysis, and similarly, ethanol was produced with the highest concentration during the SSF process. The biogas plant effluent was a new and inexpensive source for efficient pretreatment. In methane fermentation plans, compounds with high molecular mass as well as organic materials are converted to volatile fatty acid, which transformed into biogas. As the yield usually is not 100%, relatively high VFA concentration is produced in biogas plant, as an effluent.18 Unreacted VFA and other effective compounds effectively have decreased rice straw recalcitrant structure. Improvement in product attained after enzymatic hydrolysis and SSF process for straw treated with this liquid at 140 °C, in comparison to untreated straw, specified its suitability for the pretreatment. Application of this waste as a liquid for pretreatment had different beneficial aspects. It acted better than water and even some of the diluted acids used in this study. As moderate conditions, i.e., low temperature and pressure, was used for pretreatment, the observed increase in ethanol production seems to be acceptable.
Conclusion
Treating at 100 °C with 1 and 4% v/v acetic acid, butyric acid, lactic acid, propionic acid as well as water and biogas plant effluent was not strong enough to open up rice straw structure and make cellulose more accessible to the hydrolytic enzymes. However, a considerable increase in enzymatic digestibility and ethanol production was achieved after rice straw pretreatment at 140 °C. Pretreatment with 4% lactic acid with two hydroxyl groups in its structure showed the best effect during pretreatment process for improving sugar and ethanol production. Biogas plant effluent acted better than water and some of the dilute acids investigated in this study. This waste is produced in a huge amount without specific application. Glucose and ethanol concentration of residue treated with biogas plant effluent increased by 42% and 47%, repetitively, in comparison to the untreated rice straw. Consuming this waste in treatment instead of water seems to be a good solution for its handling, preventing water loss and reducing pretreatment cost.
Moreover, changes in rice straw crystallinity, porosity, pore size distribution, and composition detected by SEM, FTIR, BET, compositional analyses were the main reasons for the increased sugar and ethanol production.
Conflicts of interest
There are no conflicts to declare.
Acknowledgements
The authors are grateful to the Research Institute of Biotechnology and Bioengineering, Isfahan University of Technology, Iran, as well as the Swedish Centre for Resource Recovery at University of Borås, Sweden for the financial supports.
References
- N. Lior, Energy, 2008, 33, 842–857 CrossRef CAS.
- J. Hill, E. Nelson, D. Tilman, S. Polasky and D. Tiffany, Proc. Natl. Acad. Sci. U. S. A., 2006, 103, 11206–11210 CrossRef CAS PubMed.
- P. Havlík, U. A. Schneider, E. Schmid, H. Böttcher, S. Fritz, R. Skalský, K. Aoki, S. D. Cara, G. Kindermann, F. Kraxner, S. Leduc, I. McCallum, A. Mosnier, T. Sauer and M. Obersteiner, Energy Policy, 2011, 39, 5690–5702 CrossRef.
- B. P. J. Andrée, V. Diogo and E. Koomen, Renewable Sustainable Energy Rev., 2017, 67, 848–862 CrossRef.
- K. T. Tan, K. T. Lee and A. R. Mohamed, Energy Policy, 2008, 36, 3360–3365 CrossRef.
- T. L. Bezerra and A. J. Ragauskas, Biofuels, Bioprod. Biorefin., 2016, 10, 634–647 CrossRef CAS.
- K. Karimi, G. Emtiazi and M. J. Taherzadeh, Enzyme Microb. Technol., 2006, 40, 138–144 CrossRef CAS.
- P. Binod, R. Sindhu, R. R. Singhania, S. Vikram, L. Devi, S. Nagalakshmi, N. Kurien, R. K. Sukumaran and A. Pandey, Bioresour. Technol., 2010, 101, 4767–4774 CrossRef CAS PubMed.
- M. Kapoor, S. Soam, R. Agrawal, R. P. Gupta, D. K. Tuli and R. Kumar, Bioresour. Technol., 2017, 224, 688–693 CrossRef CAS PubMed.
- M. J. Taherzadeh and K. Karimi, Int. J. Mol. Sci., 2008, 9, 1621–1651 CrossRef CAS PubMed.
- S. Mohapatra, S. J. Dandapat and H. Thatoi, J. Environ. Manage., 2017, 187, 537–549 CrossRef PubMed.
- S. S. Hashemi, K. Karimi, M. J. Nosratpour and I. Sárvári Horváth, Energy Fuels, 2016, 30, 10592–10601 CrossRef CAS.
- D. C. Martino, J. L. Colodette, R. Chandra and J. Saddler, Wood Sci. Technol., 2017, 51, 557–569 CrossRef CAS.
- Q. Li, Y.-C. He, M. Xian, G. Jun, X. Xu, J.-M. Yang and L.-Z. Li, Bioresour. Technol., 2009, 100, 3570–3575 CrossRef CAS PubMed.
- S. Kuhar, L. M. Nair and R. C. Kuhad, Can. J. Microbiol., 2008, 54, 305–313 CrossRef CAS PubMed.
- Ó. J. Sánchez and C. A. Cardona, Bioresour. Technol., 2008, 99, 5270–5295 CrossRef PubMed.
- T.-C. Hsu, G.-L. Guo, W.-H. Chen and W.-S. Hwang, Bioresour. Technol., 2010, 101, 4907–4913 CrossRef CAS PubMed.
- R. Zhao, Z. Zhang, R. Zhang, M. Li, Z. Lei, M. Utsumi and N. Sugiura, Bioresour. Technol., 2010, 101, 990–994 CrossRef CAS PubMed.
- A. M. J. Kootstra, H. H. Beeftink, E. L. Scott and J. P. M. Sanders, Biochem. Eng. J., 2009, 46, 126–131 CrossRef CAS.
- M. Shafiei, K. Karimi and M. J. Taherzadeh, Bioresour. Technol., 2010, 101, 4914–4918 CrossRef CAS PubMed.
- D. Scordia, S. L. Cosentino, J.-W. Lee and T. W. Jeffries, Biomass Bioenergy, 2011, 35, 3018–3024 CrossRef CAS.
- C. Kundu, H.-J. Lee and J.-W. Lee, Bioresour. Technol., 2015, 178, 28–35 CrossRef CAS PubMed.
- K. Sasaki, T. Tanaka, Y. Nishizawa and M. Hayashi, Appl. Microbiol. Biotechnol., 1990, 32, 727–731 CrossRef CAS.
- X. Lei, N. Sugiura, C. Feng and T. Maekawa, J. Hazard. Mater., 2007, 145, 391–397 CrossRef CAS PubMed.
- E. Salminen, J. Rintala, J. Härkönen, M. Kuitunen, H. Högmander and A. Oikari, Bioresour. Technol., 2001, 78, 81–88 CrossRef CAS PubMed.
- K. P. Woli, T. Nagumo, K. Kuramochi and R. Hatano, Sci. Total Environ., 2004, 329, 61–74 CrossRef CAS PubMed.
- A. Sluiter, B. Hames, R. Ruiz, C. Scarlata, J. Sluiter and D. Templeton, National Renewable Energy Laboratory, CO, NREL Technical Report No. NREL/TP-510-42622, 2005.
- A. Sluiter, B. Hames, R. Ruiz, C. Scarlata, J. Sluiter, D. Templeton and D. Crocker, National Renewable Energy Laboratory, CO, NREL Technical Report No. NREL/TP-510-42618, 2008.
- M. Wiman, D. Dienes, M. A. T. Hansen, T. van der Meulen, G. Zacchi and G. Lidén, Bioresour. Technol., 2012, 126, 208–215 CrossRef CAS PubMed.
- R. Kumar and C. E. Wyman, Biotechnol. Bioeng., 2009, 103, 252–267 CrossRef CAS PubMed.
- K. Karimi and M. J. Taherzadeh, Bioresour. Technol., 2016, 200, 1008–1018 CrossRef CAS PubMed.
- M. Salih, Fourier Transform Infrared Spectroscopy for Natural Fibres, 2012 Search PubMed.
- L. E. Gollapalli, B. E. Dale and D. M. Rivers, Appl. Biochem. Biotechnol., 2002, 98, 23–35 CrossRef PubMed.
- R. Kumar, G. Mago, V. Balan and C. E. Wyman, Bioresour. Technol., 2009, 100, 3948–3962 CrossRef CAS PubMed.
- C. Piccolo, M. Wiman, F. Bezzo and G. Lidén, Enzyme Microb. Technol., 2010, 46, 159–169 CrossRef CAS.
- H. E. Grethlein, Nat. Biotechnol., 1985, 3, 155–160 CrossRef CAS.
- W.-H. Chen, B.-L. Pen, C.-T. Yu and W.-S. Hwang, Bioresour. Technol., 2011, 102, 2916–2924 CrossRef CAS PubMed.
- K. Srilekha Yadav, S. Naseeruddin, G. Sai Prashanthi, L. Sateesh and L. Venkateswar Rao, Bioresour. Technol., 2011, 102, 6473–6478 CrossRef CAS PubMed.
- J. K. Ko, J. S. Bak, M. W. Jung, H. J. Lee, I.-G. Choi, T. H. Kim and K. H. Kim, Bioresour. Technol., 2009, 100, 4374–4380 CrossRef CAS PubMed.
- E. Hong, J. Kim, S. Rhie, S.-J. Ha, J. Kim and Y. Ryu, Biotechnol. Bioprocess Eng., 2016, 21, 612–619 CrossRef CAS.
- S. M. de Vasconcelos, A. M. P. Santos, G. J. M. Rocha and A. M. Souto-Maior, Bioresour. Technol., 2013, 135, 46–52 CrossRef CAS PubMed.
- B. C. Saha, L. B. Iten, M. A. Cotta and Y. V. Wu, Process Biochem., 2005, 40, 3693–3700 CrossRef CAS.
- P. Kumar, D. M. Barrett, M. J. Delwiche and P. Stroeve, Ind. Eng. Chem. Res., 2009, 48, 3713–3729 CrossRef CAS.
- M. J. Selig, S. Viamajala, S. R. Decker, M. P. Tucker, M. E. Himmel and T. B. Vinzant, Biotechnol. Prog., 2007, 23, 1333–1339 CrossRef CAS PubMed.
- G. Garrote, H. Domínguez and J. C. Parajó, Holz Roh- Werkst., 1999, 57, 191–202 CrossRef CAS.
- A. Safari, K. Karimi and M. Shafiei, RSC Adv., 2016, 6, 36441–36449 RSC.
|
This journal is © The Royal Society of Chemistry 2017 |
Click here to see how this site uses Cookies. View our privacy policy here.