DOI:
10.1039/C7RA09941J
(Paper)
RSC Adv., 2017,
7, 53970-53976
Preparation and characterization of novel naphthyl epoxy resin containing 4-fluorobenzoyl side chains for low-k dielectrics application†
Received
6th September 2017
, Accepted 15th November 2017
First published on 23rd November 2017
Abstract
A new type of epoxy monomer 1,5-bis(4-fluorobenzoyl)-2,6-diglycidyl ether naphthalene (DGENF) was obtained through a three-step procedure involving Friedel–Crafts acylation, demethylation, and followed by nucleophilic reaction. The chemical structures were confirmed by 1HNMR, 19FNMR and FT-IR. After curing with methylhexahydrophthalic anhydride (MeHHPA), the properties of DGENF epoxy resin were measured and compared with three other kinds of commercial epoxy resins. As a result, DGENF exhibited excellent thermal stability, hydrophobic and dielectric properties. For example, DGENF had a higher glass transition temperature of 170 °C than the other three commercial epoxy resins. DGENF showed a higher contact angle of 116°, which could satisfy the standard of hydrophobic materials. In addition, DGENF showed significantly lower dielectric constant (2.97 at 1 MHz) and dielectric loss (0.0188 at 1 MHz) than those of the other commercial epoxy resins because of the introduction of fluorine on the side chains, which improved the electronegativity of the epoxy resin and reduced the polarizability of molecules efficiently. Herein, we believe the novel naphthyl epoxy resin (DGENF) has demonstrated potential application in electronic industries.
1. Introduction
With the rapid development of micro-electronics industries and the continuing miniaturization in dimensions of electronic devices, there is a demand for electronic materials to possess more functions to satisfy the requirements for optimal performance and lifetime of electronic components. These functions mainly include electric insulation, mechanical support and overcoming the propagation delay caused by interconnection. Therefore, advanced electronic materials are required to possess better mechanical properties, good thermal stability, excellent chemical and corrosion resistance as well as lower dielectric properties.1–9
As one of the most important electrical materials, epoxy resins have been widely used in electrical coatings, electronic packaging, electrical substrates, adhesives of chips and encapsulation.10–19 However, conventional epoxy resins do not have adequate electrical performance to satisfy the requirements of advanced microelectronic materials, especially dielectric properties.20 Therefore, the development of novel epoxy resins possessing lower dielectric constants and loss (low-k) has attracted more and more attention of researchers around the world.
According to reports, there are various methods to achieve low dielectric constant materials, such as the incorporation of fluorinate groups and stiff non-polar structures, as well as the introduction of controlled porosity in polymer.21,22 Furthermore, the existence of fluorinate and stiff non-polar structure can also decrease moisture absorption and improve the thermal stability of materials.23 Sasaki24 reported that the bisphenol A type epoxy resin cured with fluorinated phthalic anhydride had the lowest dielectric constant (2.77) and dielectric loss factor (0.01) among all cured epoxy resins. Meanwhile, the water absorption of this fluorinated epoxy resins could be reduced by 75%. Tao and coworkers25 also reported fluorinated epoxy resins with reduced moisture absorption and dielectric constant. They had lower dielectric constant (3.3) and water uptake (0.38%) than diglycidyl ether of bisphenol A (DGEBA) cured with the same curing agent. Xu et al.26 synthesized a series of novel epoxy resins bearing naphthyl and limonene moieties, which showed a remarkably higher Tg (171 °C), lower coefficient (36 ppm °C−1) of thermal expansion, better moisture resistance (0.13%) and lower dielectric property (3.7). All of the properties were better than DGEBA cured with the same curing agent. Therefore, we believe that the introduction of fluorinate groups and stiff non-polar structure into polymer is a promising method for developing low dielectric materials with improved thermal stability and excellent moisture resistance.
In this work, we synthesized a novel naphthyl epoxy monomer, 1,5-bis(4-fluorobenzoyl)-2,6-diglycidyl ether naphthalene (DGENF) containing 4-fluorobenzoyl side chains and stiff non-polar naphthalene moieties simultaneously. After the addition of methylhexahydrophthalic anhydride (MeHHPA) as the curing agent and 2-methylimidazolate (2-MI) as the accelerator with a stoichiometric amount, the cured epoxy resins with low dielectric properties and improved thermal stabilities were obtained. Additionally, we prepared other three kinds of cured commercial epoxy resins in the same method and characterized their properties for comparison, including bisphenol A epoxy resin (BPA-EP), bisphenol F epoxy resin (BPF-EP) and 4,4′-diglycidyl(3,3′,5,5′-tetramethylbiphenyl) epoxy resin (TMBP).
2. Experimental
2.1 Materials
2,6-Dimethoxynaphthalene (99.0%), 4-fluorobenzoyl chloride (98.0%), boron tribromide (BBr3, 99.99%) and ferric chloride (FeCl3, 97.5%) were purchased from Sigma-Aldrich Chemical Co., Ltd. Epichlorohydrin (ECH, 98.0%), MeHHPA (98.0%), 2-MI (99.0%), NaOH, tetrabutylammonium bromide (purity 98.0%) were obtained from Sinopharm Chemical Reagent Co., Ltd. BPA-EP (KDS-8128 EEW = 172 g per eq.) was purchased by Kukdo Chemical (Kunshan) Co., Ltd and BPF-EP (NPEF-170 EEW = 170 g per eq.) were obtained by Nanya plastics (Taiwan) Co., Ltd. TMBP was prepared according to our method reported previously.27 All other solvents were obtained commercially and used without further purification.
2.2 Synthesis of 1,5-bis(4-fluorobenzoyl)-2,6-dimethoxy-naphthalene (DMNF)
The synthetic procedure of DMNF is described in Scheme 1. 2,6-Dimethoxynaphthalene (9.4 g, 0.05 mol) and 4-fluorobenzoyl chloride (17.4 g, 0.11 mol) were dissolved in chloroform (CHCl3). Then anhydrous ferric chloride (1.65 g, 0.01 mol) was added to the mixture under 5 °C and the reaction was then kept at ambient temperature for 24 h. The resulting mixture was poured into hydrochloric acid. The liquid phase was removed by decantation and the brown solid was precipitated in methanol. The crude product was then recrystallized from dimethylformamide (yield: 78%).
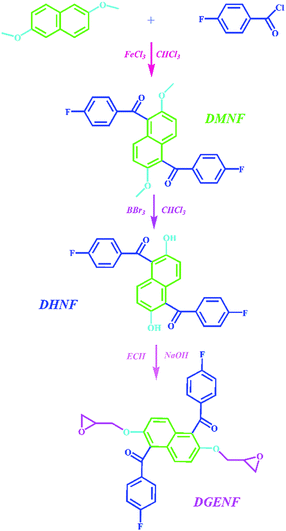 |
| Scheme 1 The synthesis routes of DMNF, DHNF and DGENF monomers. | |
2.3 Synthesis of 1,5-bis(4-fluorobenzoyl)-2,6-dihydroxynaphthalene (DHNF)
DMNF (12.975 g, 0.03 mol) obtained from above procedure was added into 300 mL CHCl3 and mixed under 5 °C (ice bath). Then 1 mol L−1 CHCl3 solution of BBr3 (300 mL) was added into the mixture dropwise during 2 h. The mixture was stirred at room temperature for 48 h before pouring into ice-water to absorb excess BBr3, and then washed with deionized water. The resulting yellow powder (DHNF) was dried under vacuum at 60 °C for 24 h (Scheme 1) (yield: 80%).
2.4 Synthesis of epoxy monomer 1,5-bis(4-fluorobenzoyl)-2,6-diglycidyl ether naphthalene (DGENF)
The synthesis route of the epoxy monomer DGENF is illustrated in Scheme 1. A mixture of DHNF (4.05 g, 0.01 mol), ECH (16 mL, 0.20 mol) and tetrabutylammonium bromide (0.096 g, 0.3 mmol) were stirred in a three-neck flask at 90 °C for 6 h. After cooling to room temperature, the excess ECH was removed at a reduced pressure. Subsequently, 30 mL toluene and 2.88 g NaOH (50 wt% aqueous solution) were added and the mixture was kept at 90 °C for another 3 h. Then the mixture was washed and distilled under reduced pressure. After drying in a vacuum oven at 60 °C for 12 h, the white crystalline product DGENF was finally obtained(yield: 88%).
2.5 Preparation of cured epoxy resin samples
As shown in Scheme 2, a stoichiometric amount of MeHHPA was added into DGENF, BPA-EP, BPF-EP and TMBP, respectively. The mixtures were stirred continuously for 1 h, and 2-MI was then added into the mixtures as the curing accelerator. After stirred for 30 min, the mixtures were put into the vacuum oven in order to remove the entrapped air. Finally, the mixtures were poured into a polish mould and cured at 120 °C for 2 h, 160 °C for 2 h and 200 °C for 2 h to obtain the epoxy resins.
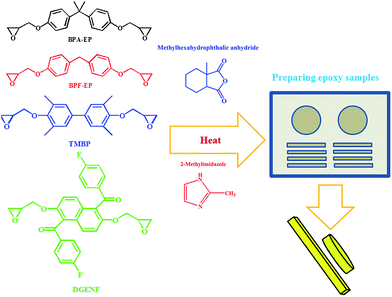 |
| Scheme 2 Procedure of preparing epoxy resins. | |
2.6 Characterization
1H-NMR spectra were measured on a 500 MHz Bruker Avance 510 spectrometer at 298 K with DMSO-d6 as the solvent and tetramethylsilane as the standard.
FT-IR spectra were obtained with a Nicolet Impact 410 Fourier transform spectrometer using KBr pellets.
Dynamic mechanical analysis (DMA) was performed on a DMA Q800 analyzer (TA Instruments, New Castle, DE, USA) using a single cantilever clamp over a temperature range of 40–200 °C at a heating rate of 3 °C min−1 with a constant frequency of 1 Hz.
Thermogravimetric analysis (TGA) was conducted on a Pyris 1 TGA analyzer (Perkin-Elmer, USA). The samples were heated from 100 °C to 700 °C at a rate of 10 °C min−1 under nitrogen atmosphere. Before the heating scan, all the samples were pre-dried under N2 at 100 °C for 10 min to remove the residual water and solvent thoroughly.
Dielectric constants of the samples were measured using a Hewlett-Packard 4294A apparatus at room temperature over a frequency range of 0–106 Hz.
Contact angle measurements were carried out on a JC2000C2 contact angle goniometer (Shanghai Zhongchen Powereach Company, China) by the sessile drop method with a micro syringe at room temperature.
3. Results and discussion
3.1 Synthesis and characterization of monomers
As depicted in Scheme 1, the epoxy monomer DGENF was synthesized via a three-step synthetic procedure. Firstly, the monomer DMNF was synthesized by a Friedel–Crafts acylation reaction between 2,6-dimethoxynaphthalene and 4-fluorobenzoyl chloride using anhydrous ferric chloride as the catalyst. Then, DMNF containing two methoxyl groups was demethylated to DHNF bearing hydroxyl groups by using BBr3 solution. Finally, DGENF containing epoxy groups was obtained by a nucleophilic reaction between DHNF and ECH under the catalyst of NaOH. The structure of DMNF and DHNF intermediates as well as the epoxy monomer DGENF was confirmed by their 1H NMR spectra in DMSO-d6. As displayed in Fig. 1, the proton peak at 3.7 ppm was assigned to the protons on –OCH3 groups of DMNF (Fig. 1a). After the demethylation reaction, the signal of –OCH3 at 3.7 ppm disappeared completely in the spectrum of DHNF (Fig. 1b). Instead, the characteristic peak for the proton of –OH can be observed at 10.0 ppm. This variation indicated that methoxyl groups in DMNF were completely converted into hydroxyl groups in DHNF.
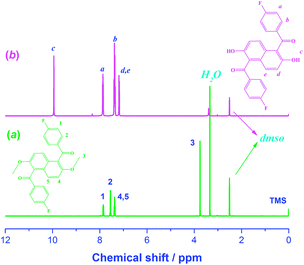 |
| Fig. 1 1H-NMR spectra of DMNF and DHNF monomers. | |
Fig. 2 shows the 1H-NMR spectrum of the epoxy monomer DGENF. Compared to DHNF, the proton peak of –OH at 10.0 ppm disappeared, while the proton peaks (He and Hg) for the methylene group (–CH2–) appeared at 4.30 ppm, 3.98 ppm, 2.62 ppm and 2.48 ppm due to the incorporation of epoxy groups. The results indicated that the hydroxyl groups were converted to epoxy groups thoroughly by reacting with ECH.
 |
| Fig. 2 1H-NMR spectra of epoxy monomer DGENF. | |
Fig. 3 shows the 19F NMR of DGENF. The only one peak at −105 ppm corresponds to the terminal fluorine atom on 4-fluorobenzoyl side chains. Therefore, we could confirm that 4-fluorobenzoyl side chains exist in the structure of our target DGENF product.
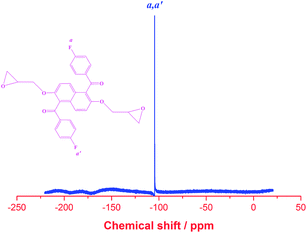 |
| Fig. 3 19F NMR of the epoxy monomer DGENF. | |
3.2 FT-IR spectra of cured epoxy resins
DGENF epoxy resin was prepared using MeHHPA as the curing agent and 2-MI as the accelerator. Another three kinds of cured commercial epoxy resins including BPA-EP, BPF-EP and TMBP were also prepared at the same condition for comparison. Fig. 4 shows the FT-IR spectra of the epoxy monomer DGENF and four kinds of cured epoxy resins. For the DGENF monomer, the absorption bands observed from 1500 cm−1 to 1650 cm−1 can be attributed to the skeleton vibration of naphthalene rings. A sharp and strong characteristic band at 1740 cm−1 was assigned to the C
O absorption on the side chains. The characteristic absorption peak of oxirane ring vibration was observed at 912 cm−1, which demonstrated that the epoxy group had been successfully introduced into DGENF monomer. In order to confirm that the curing reaction was completed, we also used FT-IR to characterize the cured epoxy samples. As shown in Fig. 4, the characteristic peak of epoxy group (912 cm−1) disappeared after curing with MeHHPA for all the samples. It is believed that the anhydride group of MeHHPA reacted with epoxy ring thoroughly to form ester groups in the presence of cured regent and accelerator at high temperature.
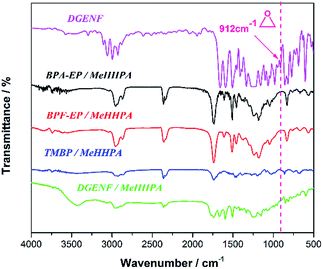 |
| Fig. 4 FT-IR spectra of epoxy monomer DGENF and cured epoxy resins. | |
3.3 Mechanical and thermal properties
The mechanical property is essential for epoxy materials for applications in electronic field. In this study, we used DMA to investigate the mechanical properties and glass transition temperature (Tg) of the cured epoxy resins. As shown in Fig. 5, TMBP had a highest storage modulus (2375 MPa) among all epoxy resin samples within the experimental temperature range due to the biphenyl structure in TMBP, which improved the stiffness of the molecule chains and enhanced the mechanical strength. Compared to BPA-EP and BPF-EP, DGENF possessed a higher storage modulus (1976 MPa) at 40 °C and showed a slower decreasing rate with the temperature increasing. This result was ascribed to the naphthyl group with sufficient stiffness in DGENF, which also provided good thermal stability for the cured epoxy resin. Although DGENF possessed rigid naphthyl group, the existence of 4-fluorobenzoyl side chains decreased the cross-linking density of the cured epoxy resin, thus resulting in a relatively lower storage modulus than TMBP.
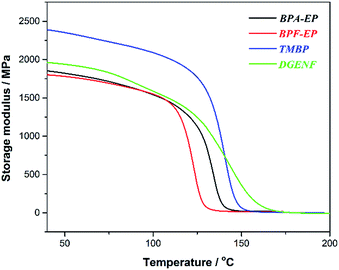 |
| Fig. 5 Storage modulus curves of cured epoxy resin samples. | |
As shown in Fig. 6, the Tg of DGENF resin samples derived from tan
δmax is 170 °C, which is much higher than those of other three kinds of epoxy resin materials (Table 1). The result can be explained by the existence of stiff naphthy group in DGENF, thus improving the rigid nature of polymer chains. Meanwhile, DGENF resin shows a relatively broad tan delta peak, which is indicative of the chain branching within the epoxy resin due to the introduction of 4-fluorobenzoyl side chains. DMA results indicated that this novel naphthyl epoxy material could satisfy the demand of thermal and mechanical stabilities to be used as the electronic materials.
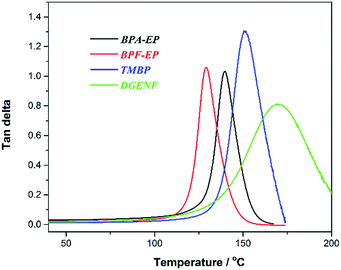 |
| Fig. 6 Tan delta curves of cured epoxy resin samples. | |
Table 1 TGA, DMA and dielectric properties of cured epoxy resins
Samples |
TGA (°C) |
Char yield [%] |
DMA |
Dielectric properties at 1 MHz |
T5% |
T10% |
T50% |
At 700 °C |
Storage modulus (MPa) |
Tg (°C) |
Dk |
Df |
BPA-EP |
334 |
384 |
453 |
14.5 |
1852 |
129 |
3.81 |
0.0219 |
BPF-EP |
334 |
381 |
446 |
26.8 |
1800 |
139 |
3.95 |
0.0205 |
TMBP |
313 |
340 |
450 |
7.7 |
2375 |
150 |
3.77 |
0.0244 |
DGENF |
288 |
313 |
532 |
34.5 |
1976 |
170 |
2.97 |
0.0188 |
Fig. 7 shows the TGA curves of the cured epoxy resin samples measured under N2 atmospheres. The relevant thermal decomposition data, including the decomposition temperature of 5% weight loss (T5%), 10% weight loss (T10%) and 50% weight loss (T50%), and the char residues at 700 °C are listed in Table 1. It was obviously found that DGENF exhibited a lower 5% weight loss temperatures (T5%) of 288 °C than those of other kinds of epoxy resin materials (BPA-EP 334 °C, BPF-EP 334 °C and TMBP 313 °C). This result was mainly caused by two reasons. Firstly, the existence of 4-fluorobenzoyl side chains decreased the cross-linking density of the cured resins. Secondly, the side chains group could be degraded prior to the rigid main chain. This is also demonstrated by its tan delta curve with a relatively broad peak due to the introduction of 4-fluorobenzoyl side chains. However, as the temperature increased, the degradation rate of DGENF became much slower than other three kinds of epoxy resin samples. For example, as the temperature reached up to 400 °C, DGENF displayed a slow decreasing tendency in the thermal degradation, while the other epoxy resins maintained the continuous process of thermal degradation. Consequently, T50% of DGENF (532 °C) became much higher than BPA-EP (453 °C), BPF-EP (446 °C) and TMBP (450 °C). Meanwhile, the char yield of the epoxy resin samples at 700 °C listed in Table 1 indicated DGENF showed more residual (34.5%) than other three kinds of epoxy resins. It can therefore be deduced that the introduced naphthyl group improves the thermal stability of cured epoxy resins at high temperatures efficiently and delays the degradation process of the material.
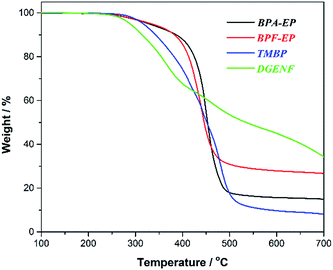 |
| Fig. 7 TGA curves of cured epoxy samples. | |
3.4 Contact angle and dielectric properties
Water absorption as one of the important property of materials not only greatly impair the mechanical and thermal properties of epoxy resins, but also increase relative dielectric constant even at small quantities, which widely limit the usage of epoxy resins as low-k materials. Therefore we measured contact angles of all epoxy samples to determine the relative wettability of the surface. Fig. 8 exhibits the photographs and the result of contact angles. Photos represented the contact angles of BPA-EP (ϑ = 78.2°), BPF-EP (ϑ = 80.2°), TMBP (ϑ = 83.2°) and DGENF (ϑ = 116°), respectively. All the contact angles were less than 90° except DGENF, which was consistent with the standard of hydrophobic materials. This result was attributed to the stiff naphthalene moieties as the skeleton of the molecular chains and the hydrophobic fluorine in the side chains, thus decreasing the surface wettability of the material.
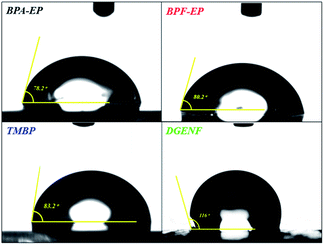 |
| Fig. 8 Contact angles of cured epoxy samples. | |
To the best of our knowledge, the signal propagation loss is related to the dielectric constant (Dk) and the dielectric loss factor (Df), which are the most important parameters for epoxy resins used for the electronic materials. Therefore, selecting lower Dk and Df material is beneficial for improving propagating speed and reducing the propagation loss. Fig. 9 and 10 showed the dielectric constant and dielectric loss of all these epoxy samples. It was clearly observed that DGENF had a remarkably lower dielectric constant (Dk = 2.97 at 1 MHz) than that of other kinds of conventional epoxy resins (BPA-EP, BPF-EP and TMBP). The result was owing to the existence of non-polar naphthalene moieties in the polymer main chains and 4-fluorobenzoyl groups in the side chain, which provided the small dipole of C–F bonds and thus making the molecule difficult to be polarized. As shown in Fig. 10, we could obviously observe that the dielectric loss of all of these epoxy materials showed an increasing tendency with the frequency increasing. Moreover, the Df of DGENF (0.0188 at 1 MHz) was slightly lower than other three kinds of epoxy resin materials (BPA-EP: 0.0219, BPF: 0.0205 and TMBP: 0.0244). It can therefore be deduced that the introduction of non-polar naphthalene group and C–F bond into the polymer could modify the dielectric properties significantly. Thus we believed that this novel naphthyl epoxy resin could satisfy the demand to be used as potential electronic materials.
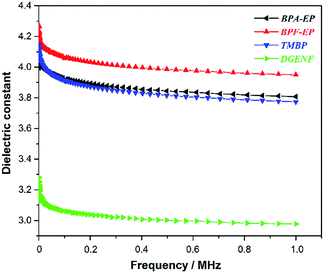 |
| Fig. 9 Dielectric constants of cured epoxy samples. | |
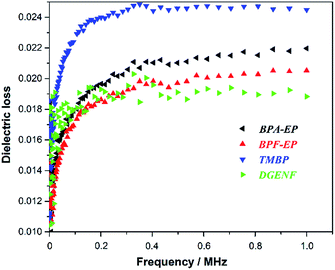 |
| Fig. 10 Dielectric loss of cured epoxy samples. | |
Conclusions
A novel type of 1,5-bis(4-fluorobenzoyl)-2,6-diglycidyl ether naphthalene (DGENF) was synthesized via a three-step procedure involving Friedel–Crafts acylation, demethylation, followed by nucleophilic reaction with ECH. Then a novel naphthyl epoxy resin containing 4-fluorobenzoyl side chains were prepared by curing with MeHHPA at high temperature. By comparing the properties of DGENF with other three kinds of conventional epoxy resins (BPA-EP, BPF-EP and TMBP), this novel naphthyl epoxy resin showed more hydrophobic and much lower dielectric properties. Therefore, DGENF is considered to be one of the most promising candidates to substitute future low-k dielectrics in microelectronic. These results could motivate the research on the design of lower dielectric constant materials and the investigation of the relationship between the structure and properties of epoxy resins to be used as thermoset materials.
Conflicts of interest
There are no conflicts to declare.
Acknowledgements
We acknowledge the financial support from the Natural Science Foundation of China (No. 21374034 and 21474036).
References
- J. Hao, Y. Wei and J. Mu, RSC Adv., 2016, 6, 90 Search PubMed.
- J. Mo, W. Ma and W. Zhang, et al., Mater. Des., 2017, 128, 56 CrossRef CAS.
- G. Maier, Prog. Polym. Sci., 2001, 26(1), 3 CrossRef CAS.
- Y. Huang, S. Zhang and H. Hu, et al., J. Polym. Sci., Part A: Polym. Chem., 2017, 55(11), 1920 CrossRef CAS.
- W. Volksen, R. D. Miller and G. Dubois, Chem. Rev., 2010, 110(1), 56 CrossRef CAS PubMed.
- X. Zeng, L. Ye and K. Guo, et al., Adv. Bioelectron. Mater., 2016, 2(5), 1500485 CrossRef.
- T. Fukumaru, T. Fujigaya and N. Nakashima, Polym. Chem., 2012, 3(2), 369 RSC.
- C. Yuan, J. Wang and K. Jin, et al., Macromolecules, 2014, 47(18), 6311 CrossRef CAS.
- Y. Wang, J. Yu and J. Zhu, et al., J. Polym. Sci., Part A: Polym. Chem., 2016, 54(11), 1623 CrossRef CAS.
- M. Dogan and S. Unlu, Polym. Degrad. Stab., 2014, 99, 12 CrossRef CAS.
- J. Wang, L. Qian, B. Xu, W. Xi and X. Liu, Polym. Degrad. Stab., 2015, 122, 8 CrossRef CAS.
- B. Kandola, B. Biswas, D. Price and A. Richard, Polym. Degrad. Stab., 2010, 95, 144 CrossRef CAS.
- S. Tang, J. Qian, X. Liu and Y. Dong, Polym. Degrad. Stab., 2016, 133, 350 CrossRef CAS.
- Z. Chen, J. Yang, Q. Ni, S. Fu and Y. Huang, Polymer, 2009, 50, 4753 CrossRef CAS.
- X. Wang, Y. Hu, L. Song, W. Xing, H. Lu, P. Lv and G. Jie, Polymer, 2010, 51, 2435 CrossRef CAS.
- A. Konuray, X. Fernández-Francos and X. Ramis, Polymer, 2017, 116, 191 CrossRef CAS.
- B. Yang, W. Wang and J. Huang, Polymer, 2015, 77, 129 CrossRef CAS.
- D. Carolan, A. Ivankovic, A. Kinloch, S. Sprenger and A. Taylor, Polymer, 2016, 97, 179 CrossRef CAS.
- S. Yang, Q. Zhang and Y. Hu, Polym. Degrad. Stab., 2016, 133, 358 CrossRef CAS.
- L. Luo, Y. Meng and T. Qiu, et al., Polym. Compos., 2013, 34(7), 1051 CrossRef CAS.
- L. Kong, Y. Cheng and Y. Jin, et al., J. Appl. Polym. Sci., 2016, 133(21), 43456 CrossRef.
- C. Yuan, K. Jin and K. Li, et al., Adv. Mater., 2013, 25(35), 4875 CrossRef CAS PubMed.
- Z. Liu, G. Zhang and Z. Liu, et al., Polym. Degrad. Stab., 2012, 97(5), 691 CrossRef CAS.
- S. Sasaki, J. Polym. Sci., Polym. Lett. Ed., 1986, 24(6), 249 CrossRef CAS.
- Z. Tao, S. Yang and Z. Ge, et al., Eur. Polym. J., 2007, 43(2), 550 CrossRef CAS.
- K. Xu, M. Chen and K. Zhang, et al., Polymer, 2004, 45(4), 1133 CrossRef CAS.
- Z. Liu, G. Zhang and K. Tu, et al., Polym. Int., 2011, 60(10), 1556 CrossRef CAS.
Footnote |
† Electronic supplementary information (ESI) available. See DOI: 10.1039/c7ra09941j |
|
This journal is © The Royal Society of Chemistry 2017 |
Click here to see how this site uses Cookies. View our privacy policy here.