DOI:
10.1039/C7RA07209K
(Paper)
RSC Adv., 2017,
7, 40881-40886
Solvent-free and melt aerobic oxidation of benzyl alcohols using Pd/Cu2(BDC)2DABCO–MOF prepared by one-step and through reduction by dimethylformamide†
Received
29th June 2017
, Accepted 10th August 2017
First published on 22nd August 2017
Abstract
In this paper we report an efficient method for the aerobic oxidation of benzyl alcohols to aldehydes by supported palladium nanoparticles in a nanoporous metal–organic framework Cu2(BDC)2(DABCO) (BDC = 1,4-benzenedicarboxylate, DABCO = 1,4-diazabicyclo[2.2.2]octane) under a temperature control program and through reduction by dimethylformamide. The Pd-NPs/Cu2(BDC)2(DABCO) offered higher catalytic activity and recyclability than reported in literature. The supported Pd nanoparticles (PdNPs/Cu2(BDC)2(DABCO)) were characterized by X-ray diffraction, BET analysis, field emission scanning electron microscopy, transmission electron microscopy, inductively coupled plasma atomic emission spectroscopy and X-ray photoelectron spectroscopy (XPS).
The oxidation of organic compounds, such as alcohols is a primary and essential transformation in organic synthesis and industrial chemistry.1 Among the alcohols, benzyl alcohol is one of the most studied substrates.2–8 Traditionally, various oxidants, such as peroxides,9,10 toxic metal oxides,11 halides,12 ozone,13 etc., were used for the oxidation of alcohols. Compared with those oxidants, undoubtedly, air is the most atom-economical and environmentally benign oxidant. Catalysis using metal nanoparticles (MNPs) has attracted great interest in recent years. Considering the current impetus of nanoscience, it is understandable that all aspects related to the preparation of small nanoparticles (NPs) with narrow size distribution, their stabilization and their unique properties compared to large particles.14–17 The liquid-phase oxidation of alcohols over supported metal catalysts has been extensively studied in the last decade.18–21 Crystalline microporous and mesoporous metal–organic frameworks (MOFs) are constructed by joining metal-containing units [secondary building units (SBUs)] with organic linkers such as dicarboxylate or other organic rings, using strong bonds (reticular synthesis) to create open crystalline frameworks with permanent porosity.22 During the past century, extensive work was done on crystalline extended structures in which metal ions are joined by organic linkers containing Lewis base-binding atoms such as nitriles and bipyridines.23 MOFs have low density, very high surface area with a large percentage of transition metals that can act as catalytic sites.24 Also MOFs have a wide range of potential uses including gas storage, separations, solar cells and catalysis.25 In particular, applications in energy technologies such as fuel cells, supercapacitors, and catalytic conversions have made them objects of extensive study, industrial-scale production, and application.26 Recently, metal–organic frameworks (MOFs), as a new class of organic inorganic hybrid porous materials, have attracted considerable attention for stabilization and supporting of metal nanoparticles as a novel class of functional materials due to their high surface areas, tunable pore sizes, and thermal stability.27–29 The employment of MOFs as the supports for PdNPs has attracted considerable interest.30–32 For catalytic applications, PdNPs have been successfully deposited at the outer surface of the MOF supports (Pd/MOFs)33–38 or loaded inside the cavities of the MOFs (Pd@MOFs) via various methods such as impregnation and chemical vapor deposition.39–43 Although great efforts have been made in this field, a general and facile method is needed that can easily introduce the palladium(0) precursor inside the cavities of MOFs in one-pot and without any reducing agent and control the formation of PdNPs with a small particle size, which is beneficial in the cases such as catalysis. Herein, we report the one-step and reducing-agent-free encapsulation of ultrafine PdNPs in to nanopores Cu2(BDC)2(DABCO) without Pd(0) NPs aggregation on the external surface of framework and application of this catalyst in aerobic oxidation of benzyl alcohols.
Cu2(BDC)2(DABCO) was synthesized and characterized by that are reported in our previous work.44 At the first we evaluated a simple and straightforward one-step protocol to encapsulate PdNPs inside MOFs through temperature programming control from 80 °C to 130 °C for 20 h. Cu2(BDC)2(DABCO) has been shown to act as a proper support for deposition of PdNPs. Using temperature controlling method after sonication, Pd(II) cations reduced to Pd(0) nanoparticles deposed on the surface of activated Cu2(BDC)2(DABCO) carriers. The actual loading of Pd(0) was characterized by ICP analysis and found to be 0.9%. To investigate the oxidation state information of palladium, XPS analysis of Pd 3d binding energies was performed. As a shown in Fig. 1 the peaks at 341.5 (Pd-3d3/2) and 336.2 (Pd-3d5/2) eV are due to the binding energy corresponds to the Pd(0), and the peaks at 342.7 (Pd-3d3/2) and 337.6 (Pd-3d5/2) eV are due to the binding energy corresponds to the Pd(II). Based on the peak areas of Pd-3d5/2 at 336.2 and 337.6 eV, the ratio of Pd(0) to Pd(II) in Pd/Cu2(BDC)2DABCO is calculated to be 1.5 (Fig. 1a). XPS analysis of recycling Pd/Cu2(BDC)2DABCO did not show any significant change in palladium oxidation state (Fig. 1b).
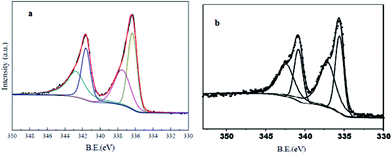 |
| Fig. 1 (a) XPS spectrum of synthesized Pd-NPs/Cu2(BDC)2DABCO and (b) recycled Pd-NPs/Cu2(BDC)2DABCO. | |
The XRD pattern of PdNPs/Cu2(BDC)2(DABCO) shows that the crystalline structure of Cu2(BDC)2(DABCO) is maintained after deposition of PdNPs. The absence of a Pd diffraction pattern relates to the low Pd contents in the materials (Fig. 2).
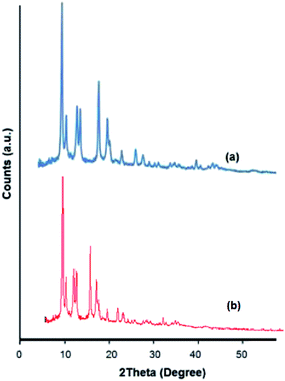 |
| Fig. 2 (a) XRD pattern of prepared Cu2(BDC)2(DABCO). (b) XRD pattern of prepared PdNPs@Cu2(BDC)2(DABCO). | |
There have theretofore been many processes reported for the encapsulation of Pd(0) NPs in MOFs but in most of the methods used a reducing agent for reduction of Pd(II) to Pd(0), while in this work we encapsulated and supported Pd(0) NPs in MOFs by temperature control program and without using any reducing agent through reduction by DMF.45–47 The DMF organic solvent is a powerful reducing agent to reduce different ions such as Ag+, Au3+ and etc.48–50 The possible reaction mechanism for the reduction of Pd2+ incorporated in MOF by DMF is as the following equation:
HCONMe2 + Pd2+ + H2O → Pdo + Me2NCOOH + 2H+ |
This mechanism is supported by a measured increase of conductivity as the reaction proceeds, which indicates that the larger Pd2+ ions are progressively exchanged for the more mobile H+ ions. Accordingly, a decrease of the solution pH was observed. Based on a literature report48–50 we also proposed that carbamic acid produced during the reduction was easily decomposed to dimethyl amine and gaseous CO2 in high temperature.
Specific surface areas of the samples were measured by N2 adsorption at 77 K, with results presented in Table 1. Nitrogen adsorption and surface areas of Pdo-in-Cu2(BDC)2(DABCO) samples were noticeably reduced compared to Cu2(BDC)2(DABCO), indicating that the cavities of Cu2(BDC)2(DABCO) may be occupied by highly dispersed Pd nanoparticles (Table 1).
Table 1 Textural properties of [Cu2(BDC)2(DABCO)] and PdNPs@[Cu2(BDC)2(DABCO)] from N2 adsorption–desorption experiments
Material |
BET surface area (m2 g−1) |
Pore volume (cm3 g−1) |
[Cu2(BDC)2(DABCO)] |
1496 |
0.48 |
PdNPs@[Cu2(BDC)2(DABCO)] |
873 |
0.475 |
TEM micrograph (Fig. 3), confirmed that a crystalline and nano-scaled material was produced. It is also to emphasize that Pd nanoparticle has resulted in producing uniformly distributed nano-scale. It is also to emphasize that Pd nanoparticle has resulted in producing uniformly distributed nano-scale and with a mean particle diameter of 2.9 ± 0.2 nm as estimated from particle size distribution.
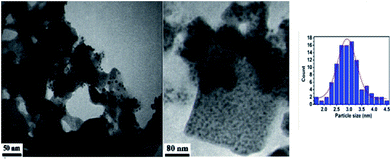 |
| Fig. 3 TEM micrograph of the PdNPs/Cu2(BDC)2DABCO. | |
The synthetic PdNPs/Cu2(BDC)2DABCO was employed as a catalyst in the aerobic oxidation of benzyl alcohols (Scheme 1).
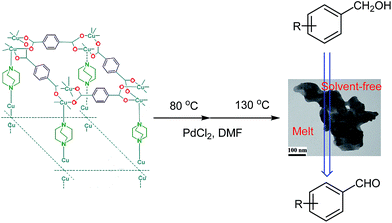 |
| Scheme 1 Schematic representation of PdNPs@Cu2(BDC)2DABCO catalyzed oxidation of benzyl alcohols. | |
Benzyl alcohol was chosen as a model substrate to study the catalytic activity of PdNPs/Cu2(BDC)2DABCO to identify suitable reaction conditions using atmospheric air as the terminal oxidant. The results are presented in Table 1. Initially, the oxidation of benzyl alcohol was tested in CH3CN at 80 °C with 20 mg of PdNPs/Cu2(BDC)2DABCO (0.9% Pd) and a stream of air produced by air pump was conducted into the reaction mixture, in this condition negligible yield of benzaldehyde was attained. When oxidation of benzyl alcohol was tested in toluene at 110 °C, conversion of benzyl alcohol to the benzaldehyde was increased. These tests shown that the nature of solvent and temperature greatly affect the efficiency of oxidation. So, in another attempts for confirmation of this hypothesis, reaction was performed in xylene at 135 °C. As expected, conversion of benzyl alcohol was increased. From the viewpoint of green chemistry and toxicity of above solvent, in another attempt, when oxidation of benzyl alcohols was performed in absences of solvent and under solvent-free condition at 120 °C, conversion increased significantly.
In another attempt to investigate the role of the base in the rate and yield of oxidation, a catalytic amount of mineral base (20 mol% Na2CO3 or K2CO3) was used. As was expected the rates and yields improved.
For the optimization of loading of the catalyst, different amount of catalyst was used. As shown in Table 2, with increasing the amount of catalyst, yield was improved (Table 2, entry 5–7). In another attempt, when the reaction was carried out in the absence of PdNPs/Cu2(BDC)2DABCO or Cu2(BDC)2DABCO, no product was formed after 24 hours at 120 °C. It has been observed that PdNPs/Cu2(BDC)2DABCO promotes the oxidation of benzyl alcohol under solvent-free condition with atmospheric air. So, as shown in Table 2 the best result observed in entry 5.
Table 2 Optimization of reaction conditions

|
Run |
Catalyst (mg) |
Solvent |
Base (20 mol%) |
Time (h) |
T (°C) |
Yielda (%) |
Isolated yield. |
1 |
15 |
CH3CN |
Na2CO3 |
24 |
80 |
5 |
2 |
15 |
Toluene |
Na2CO3 |
24 |
110 |
20 |
3 |
15 |
Xylene |
Na2CO3 |
24 |
135 |
40 |
4 |
15 |
— |
Na2CO3 |
24 |
120 |
89 |
5 |
20 |
— |
Na2CO3 |
24 |
120 |
99 |
6 |
25 |
— |
Na2CO3 |
24 |
120 |
90 |
7 |
30 |
— |
Na2CO3 |
24 |
120 |
95 |
8 |
— |
— |
Na2CO3 |
24 |
120 |
0 |
9 |
20 |
— |
— |
24 |
120 |
51 |
10 |
Cu–MOF (20 mg) |
— |
Na2CO3 |
24 |
120 |
15 |
For review of the catalytic performance of Cu2(BDC)2(DABCO) on the aerobic oxidation of benzyl alcohol an experiment was performed as a shown in Table 2 entry 10. As expected, little efficiency was achieved. It can be concluded that palladium is very effective in this study.
Encouraged by this success, we next investigated the scope of the oxidation of benzyl alcohols derivatives (Table 3). The aerobic oxidation reactions of the benzylic alcohols with different substituted groups under solvent-free were carried out in air (monitored by GC).
Table 3 Oxidation of different benzyl alcohols

|
Entry |
R |
Time (h) |
Yielda |
Isolated yield. |
1 |
H |
24 |
99 |
2 |
4-Me |
24 |
97 |
3 |
2-Me |
24 |
96 |
4 |
4-OMe |
24 |
93 |
5 |
4-Cl |
24 |
96 |
6 |
4-Br |
24 |
95 |
7 |
4-NO2 |
24 |
96 |
8 |
2-NO2 |
24 |
97 |
We found that all benzylic alcohols with both electron-withdrawing (–NO2) and electron-donating groups (–OMe, –Me) at either para- or ortho-position gave excellent conversions. To determine the degree of leaching of the palladium from the PdNPs/Cu2(BDC)2DABCO catalyst, after the filtration of catalyst the palladium content of the filtrate was determined by ICP. It was shown that less than 0.1% of the total amount of the original palladium species was lost into solution during the reaction. This leaching level was negligible which was also confirmed by the excellent reusability of this heterogeneous catalyst.
One of the important properties of the heterogeneous catalyst is the reusability, so to confirm this for our catalyst, we performed recycling experiment; so the oxidation of benzyl alcohol was chosen as a model reaction with recycled catalyst; the reaction was completed after 24 hour and the conversion and isolated yield of the reaction was 100 and 98%, respectively (experimental section). This reusability test was repeated for three times and the result summarized in Table 4.
Table 4 Reusability test of catalyst
Experiment no. |
Yield |
1 |
98 |
2 |
95 |
3 |
95 |
4 |
93 |
A comparison with other catalytic systems in the oxidation of benzyl alcohol demonstrated that our present Pd/MOF catalyst system exhibited a higher conversion and yield under milder conditions (Table 5). In the literature has been reported that the oxidative dehydrogenation of alcohols to the corresponding aldehydes happened on all exposed metallic palladium faces and the undesired products such as toluene, benzyl ether often produce on hollow sites of Pd particle faces.51 However, in our work, undesired products not were formed, so we proposed that the sites on face centered cubic Pd are the primary sites for the oxidation of benzyl alcohols.52 The proposed mechanism for this reaction is given below (Scheme 2).
Table 5 Comparison of activity for different catalytic systems in the oxidation of benzyl alcohols
Entry |
Catalyst |
Reaction condition |
Yield |
(Sel.%) |
Ref. no. |
1 |
Pd@C–GluA-550 |
Substrate 4 mL/air 1 atm/120 °C |
48.9 |
63 |
53 |
2 |
Pd@C–GluA-550 |
Solvent-free/O2 (1 MPa)/120 °C |
48.9 |
80 |
53 |
3 |
Pd/NaX zeolite |
Toluene/100 °C/O2 (3 mL min−1) |
66 |
97 |
54 |
4 |
Pd/Al2O3 |
Solvent free/120 °C/O2 (50 mL min−1) |
80 |
94 |
55 |
5 |
Pd cluster colloid |
Water/32 °C/air bubbling/(pH 3.5) |
86 |
100 |
56 |
6 |
MNP–Pd |
Toluene/K2CO3/85–90 °C/air |
89 |
93 |
57 |
7 |
Pd@Cu2(BDC)2DABCO |
Solvent free/Na2CO3 (20 mol%)/air |
99 |
100 |
Present work |
 |
| Scheme 2 Proposed mechanism for the oxidation of benzyl alcohols. | |
The structures of all products were elucidated from their melting point (for the solid product) and 1H-NMR spectra.
Materials and instruments
All reagents including organic linker H2BDC, metal salt Cu(OAc)2·H2O, 1,4-benzenedicarboxylate (BDC, 99%), 1,4-diazabicyclo[2.2.2]octane (DABCO), palladium(II) chloride (PdCl2), benzyl alcohols and solvent were obtained from commercially available sources such as Sigma-Aldrich and Merck without any purification. X-ray powder diffraction (XRD) measurements were performed using an X'pert MPD. Philips diffractometer with Cu radiation source (λ = 1.54050 Å) at 40 kV voltage and 40 mA current. BET (Brunauer–Emmett–Teller) surface area of the samples was determined from N2 adsorption–desorption isotherms using a micromeritics ASAP 2020 analyzer. The sample was characterized using a scanning electron microscope (SEM) with a ZEISS at 30 kV with gold coating. Transmission electron microscopy (TEM) was carried out using an EM10C-100 kV series microscope from the Zeiss Company, Germany. The actual loading of palladium was determined by Inductively Coupled Plasma (ICP) analysis on sequential plasma spectrometer, Shimadzu (ICPS-7000 ver. 2). X-ray photoelectron spectroscopy (XPS) measurements were conducted on a PHI Quantum 2000 XPS system equipped with an Al X-ray source (1486.6 eV). 1H-NMR spectra were measured (CDCl3) with a Bruker DRX-500 AVANCE spectrometer at 400.13. Melting points were measured on an Electrothermal 9100 apparatus and GC analysis of determination of conversions and selectivities was performed on an Agilent 6890N.
One-step supporting of palladium nanoparticle in Cu2(BDC)2(DABCO) (Pd/Cu2(BDC)2(DABCO))
[Cu2(BDC)2DABCO] was synthesized by that are reported in our previous work.40 A mixture of Cu(OAc)2·H2O (0.6 mmol), H2BDC (0.6 mmol) and DABCO (0.3 mmol) with molar ratio of 2
:
2
:
1 were ball-milled vigorously at 28 Hz at room temperature for 2 hours. The obtained green powder was washed with DMF (3 × 10 mL). Solvent exchange was carried out with methanol (3 × 10 mL) at room temperature. To remove the guest molecules of MOFs, obtained powder was treated by heating under vacuum at 130 °C for 12 hours, resulting in 1.6 g of pure product which corresponds to 94% isolated yield.
The synthesized Cu2(BDC)2(DABCO) (0.1 g) was dissolved in 2 mL of DMF and then 3 mg of PdCl2 with purity of 99.9% were added to the mixture. The solution was sonicated for 20 min, then stirred at 80 °C for 20 h and finally it was stirred at 130 °C with the purpose of reduction of Pd(II) to Pd(0) and encapsulation in cavities of MOF. Finally, the product PdNPs/Cu2(BDC)2(DABCO) was centrifuged, washed with DMF and methanol and dried in vacuum at 120 °C for 12 h.
Catalyst usage for the oxidation of benzyl alcohols
In a typical oxidation, 0.5 mL substrate (grams for the solid benzyl alcohols), catalysts and base used as described in the manuscript and were added into a 10 mL three-neck round-bottom flask, which was fitted with a magnetic stirrer and an air inlet tube. The reaction was performed at 120 °C in an oil bath with magnetic stirring. A stream of air produced by air pump was conducted into the reaction mixture and controlled by a flow meter at a constant flow rate (5 mL min−1). After completion of the reaction that monitored by TLC, ethyl acetate was added to the reaction mixture and catalyst was filtered. The filtrate was analysed by GC. The solvent was evaporated on a rotary evaporator to afford benzaldehyde (0.5 g, 98%) which in some cases were essentially pure cyanohydrin TMS ethers. All of the aldehydes characterized by melting point (for solids) and 1H-NMR spectroscopy and confirmed with what is reported in the literature.48–52
In the reusability test, oxidation of benzyl alcohol under above condition was chosen as a model reaction, the conversion and isolated yield was 100 and 91% respectively.
Conclusions
In summary, we have successfully developed a facile and effective strategy to prepare PdNPs supported on Cu2(BDC)2(DABCO) and on-site moderate reduction process to control the size and location of PdNPs within MOFs. This synthesis process could be achieved in one step through a simple temperature control program without adding any external reduction agent. The Pd/MOFs offered higher catalytic activity than common palladium salts for the quantitative and selective oxidation of benzyl alcohols. Further studies on encapsulation of other useful PdNPs in MOFs and development of its catalytic scope are in progress and would be presented in due course.
Conflicts of interest
There are no conflicts to declare.
Acknowledgements
The authors gratefully acknowledge from Science and Research Branch, Islamic Azad University for partial financial support of this work.
References
- R. A. Sheldon and J. K. Kochi, Metal-Catalyzed Oxidations of Organic Compounds, Academic Press, 1981 Search PubMed.
- M. Saiman, Angew. Chem., Int. Ed., 2012, 51, 5981–5985 CrossRef PubMed.
- X. Tong, J. Xu and H. Miao, Adv. Synth. Catal., 2005, 347, 1953–1957 CrossRef CAS.
- S. S. Shannon, Science, 2005, 309, 1824–1826 CrossRef PubMed.
- K. P. Peterson and R. C. Larock, J. Org. Chem., 1998, 63, 3185–3189 CrossRef CAS.
- M. J. Schultz, C. C. Park and M. S. Sigman, Chem. Commun., 2002, 3034–3035 RSC.
- T. Iwasawa, M. Tokunaga, Y. Obora and Y. Tsuji, J. Am. Chem. Soc., 2004, 126, 6554–6555 CrossRef CAS PubMed.
- S. S. Shannon, Angew. Chem., Int. Ed., 2004, 43, 3400–3420 CrossRef PubMed.
- Y. Wang, J. S. Zhang, X. C. Wang, M. Antonietti and H. R. Li, Angew. Chem., Int. Ed., 2010, 49, 3356–3359 CrossRef CAS PubMed.
- H. Zhou, Chem. Commun., 2012, 48, 6954–6956 RSC.
- J. Muzart, Chem. Rev., 1992, 92, 113–140 CrossRef CAS.
- X. Tong, J. Xu and H. Miao, Adv. Synth. Catal., 2005, 347, 1953–1957 CrossRef CAS.
- M. Waser, W. G. Jary, P. Pochlauer and H. Falk, J. Mol. Catal. A: Chem., 2005, 236, 187–193 CrossRef CAS.
- Y. Huang, Z. Zheng, T. Liu, J. Lu, Z. Lin, H. Li and R. Cao, Catal. Commun., 2011, 14, 27 CrossRef CAS.
- A. S. Roy, J. Mondal, B. Banerjee, P. Mondala and A. Bhaumik, Appl. Catal., A, 2014, 469, 320 CrossRef CAS.
- P. Puthiaraj and W. S. Ahn, Catal. Commun., 2015, 65, 91 CrossRef CAS.
- S. Gao, N. Zhao, M. Shu and S. Che, Appl. Catal., A, 2010, 338, 196 CrossRef.
- M. Besson and P. Gallezot, Catal. Today, 2000, 57, 127–141 CrossRef CAS.
- T. Mallat and A. Baiker, Chem. Rev., 2004, 104, 3037–3058 CrossRef CAS PubMed.
- N. Dimitratos, J. A. Lopez-Sanchez and G. J. Hutchings, Chem. Sci., 2012, 3, 20–44 RSC.
- S. E. Davis, M. S. Ide and R. J. Davis, Green Chem., 2013, 15, 17–45 RSC.
- O. M. Yaghi, Nature, 2003, 423, 705 CrossRef CAS PubMed.
-
(a) A. F. Wells, Structural Inorganic Chemistry, Oxford Univ. Press, New York, 1984 Search PubMed;
(b) Y. Kinoshita, I. Matsubara, T. Higuchi and Y. Saito, Bull. Chem. Soc. Jpn., 1959, 32, 1221 CrossRef CAS.
-
(a) D. J. Tranchemontagne, J. L. Mendoza-Cortés and M. O'Keeffe, Chem. Soc. Rev., 2009, 38, 1257 RSC;
(b) M. Ranocchiari and J. A. VanBokhoven, Phys. Chem. Chem. Phys., 2011, 13, 6388 RSC;
(c) U. Mueller, J. Mater. Chem., 2006, 16, 626 RSC.
-
(a) M. Jacoby, Chem. Eng. News, 2008, 86, 13 Search PubMed;
(b) S. H. Hsu, C. T. Li, H. T. Chien, R. R. Salunkhe, N. Suzuki, Y. Yamauchi, K. C. Ho and K. C. W. Wu, Sci. Rep., 2014, 4, 6983 CrossRef CAS PubMed;
(c) Y. C. Sue, J. W. Wu, S. E. Chung, C. H. Kang, K. Tung, K. C. Wu and F. K. Shieh, ACS Appl. Mater. Interfaces, 2014, 6, 5192–5198 CrossRef CAS PubMed;
(d) F. K. Shieh, S. C. Wang, C. Yen, C. Wu, S. Dutta, L. Y. Chou, J. V. Morabito, P. Hu, M. H. Hsu, K. C. W. Wu and C. K. Tsung, J. Am. Chem. Soc., 2015, 137, 4276–4279 CrossRef CAS PubMed.
- M. Meilikhov, K. Yusenko, D. Esken, S. Turner, G. Van Tendeloo and R. A. Fischer, Eur. J. Inorg. Chem., 2010, 3701–3714 CrossRef CAS.
- H. Kobayashi, Y. Mitsuka and H. Kitagawa, Inorg. Chem., 2016, 55, 7301–7310 CrossRef CAS PubMed.
- P. Falcaro, R. Ricco, A. Yazdi, I. Imaz, S. Furukawa, D. Maspoch, R. Ameloot, J. D. Evans and C. J. Doonan, Coord. Chem. Rev., 2016, 307, 237–254 CrossRef CAS.
- A. S. Roy, J. Mondal, B. Banerjee, P. Mondala and A. Bhaumik, Appl. Catal., A, 2014, 469, 320 CrossRef CAS.
- P. Puthiaraj and W. S. Ahn, Catal. Commun., 2015, 65, 91 CrossRef CAS.
- S. Gao, N. Zhao, M. Shu and S. Che, Appl. Catal., A, 2010, 388, 196 CrossRef CAS.
- B. Yuan, Y. Pan, Y. Li, B. Yin and H. Jiang, Angew Chem., Int. Ed., 2010, 49, 4054 CrossRef CAS PubMed.
- L. Zhang, Z. Su, F. Jiang, Y. Zhou, W. Xu and M. Hong, Tetrahedron, 2013, 69, 9237 CrossRef CAS.
- N. Shang, S. Gao, X. Zhou, C. Feng, Z. Wang and C. Wang, RSC Adv., 2014, 4, 54487 RSC.
- V. Pascanu, Q. Yao, A. Bermejo Gomez, M. Gustafsson, Y. Yun, W. Wan, L. Samain, X. Zou and B. Martin-Matute, Chem.–Eur. J., 2013, 19, 17483 CrossRef CAS PubMed.
- L. Shen, W. Wu, R. Liang, R. Lin and L. Wu, Nanoscale, 2013, 5, 9374 RSC.
- J. Juan-Alcaniz, J. Ferrando-Sori, I. Luz, P. Serra-Crespo, E. Skupien, V. P. Santos, E. Pardo, I. Llabres, F. X. Xamena, F. Kapteijn and J. Gascon, J. Catal., 2013, 307, 295 CrossRef CAS.
- V. Pascanu, P. R. Hansen, A. Bermejo Gomez, C. Ayats, A. E. Platero-Prats, M. J. Johansson, M. A. Pericas and B. Martin-Matute, ChemSusChem, 2015, 8, 123 CrossRef CAS PubMed.
- Y. Huang, S. Liu, Z. Lin, W. Li, X. Li and R. Cao, J. Catal., 2012, 292, 111 CrossRef CAS.
- M. Zhang, J. Guan, B. Zhang, D. Su, C. T. Williams and C. Liang, Catal. Lett., 2012, 142, 313 CrossRef CAS.
- N. T. S. Phan, T. T. Nguyen and L. Vu, ChemCatChem, 2013, 5, 3068 CrossRef CAS.
- M. Klimakow, P. Klobes, K. Rademann and F. Emmerling, Microporous Mesoporous Mater., 2012, 154, 113 CrossRef CAS.
- A. Pichon, A. Lazuen-Garay and S. L. James, CrystEngComm, 2006, 8, 211 RSC.
- L. Panahi, M. R. Naimi-Jamal, J. Mokhtari and A. Morsali, Microporous Mesoporous Mater., 2017, 244, 208 CrossRef CAS.
- L. Chen, X. Chen, H. Liu, C. Baia and Y. Li, J. Mater. Chem. A, 2015, 3, 15259 CAS.
- J. Y. Yu, S. Schreiner and L. Vaska, Inorg. Chim. Acta, 1990, 170, 145 CrossRef CAS.
-
(a) Z. A. Qiao, P. F. Zhang, S. H. Chai, M. F. Chi, G. M. Veith, N. C. Gallego, M. Kidder and S. Dai, J. Am. Chem. Soc., 2014, 136, 11260–11263 CrossRef CAS PubMed;
(b) S. Rana, S. Maddila and S. B. Jonnalagadda, Catal. Sci. Technol., 2015, 5, 3235–3241 RSC.
- I. P. Santos and L. M. L. Marzan, Nano Lett., 2002, 2, 903 CrossRef.
- I. P. Santos and L. M. L. Marzan, Adv. Funct. Mater., 2009, 19, 679 CrossRef.
- I. P. Santos and L. M. L. Marzan, Langmuir, 1999, 15, 948 CrossRef.
- Z. A. Qiao, P. F. Zhang, S. H. Chai, M. F. Chi, G. M. Veith, N. C. Gallego, M. Kidder and S. J. Dai, J. Am. Chem. Soc., 2014, 136, 11260–11263 CrossRef CAS PubMed.
- K. Mori, T. Hara, T. Mizugaki, K. Ebitani and K. Kaneda, J. Am. Chem. Soc., 2004, 126, 10657–10666 CrossRef CAS PubMed.
- P. Zhang, Y. Gong, H. Li, Z. Chen and Y. Wang, Nat. Commun., 2013, 4, 1593 CrossRef PubMed.
- F. Li, Q. H. Zhang and Y. Wang, Appl. Catal., A, 2008, 334, 217–226 CrossRef CAS.
- X. M. Wang, G. J. Wu, N. J. Guan and L. D. Li, Appl. Catal., B, 2012, 115, 7–15 CrossRef.
- R. R. Dun, X. G. Wang, M. W. Tan, Z. Huang, X. M. Huang, W. Z. Ding and X. G. Lu, ACS Catal., 2013, 3, 3063–3066 CrossRef CAS.
- D. Wang, C. Deraedt, L. Salmon, C. Labrugère, L. Etienne, J. Ruiz and D. Astruc, Chem.–Eur. J., 2015, 21, 6501–6510 CrossRef CAS PubMed.
Footnote |
† Electronic supplementary information (ESI) available. See DOI: 10.1039/c7ra07209k |
|
This journal is © The Royal Society of Chemistry 2017 |
Click here to see how this site uses Cookies. View our privacy policy here.