DOI:
10.1039/C7RA07147G
(Paper)
RSC Adv., 2017,
7, 41973-41979
Efficient utilization of potash alum as a green catalyst for production of furfural, 5-hydroxymethylfurfural and levulinic acid from mono-sugars†
Received
28th June 2017
, Accepted 19th August 2017
First published on 30th August 2017
Abstract
In present work, we have explored potash alum (PA) as an efficient and green catalyst for production of high value platform chemicals such as 5-hydroxymethylfurfural (HMF) furfural from bio-renewable feedstocks in a biphasic reaction medium. Maximum 64% and 49% HMF yields were obtained from the dehydration reactions of fructose and glucose, respectively, at 140 °C over a 6 h reaction time. Similarly, 55% furfural yield was obtained from xylose at 190 °C in 6 h period. Products obtained have been analyzed by 1H-NMR spectra and a detailed mechanistic understanding of the dehydration reactions has been developed. This is first report highlighting a strategy for the utilization of cost effective and non-hazardous potash alum as catalyst for the conversion of glucose, fructose, and xylose to respective furans.
Introduction
Forthcoming energy crisis due to expeditious depletion of conventional fossil fuel resources has been a major cause for recent socio-economic changes across the world.1 Excessive exploitation of conventional fuels have escalated the emission of toxic and greenhouse gases, thereby causing an irrevocable threat to the environment as well as to human health.2 Thus, attempts have been made to produce alternatives to conventional fossil fuels from renewable sources. In this regard, biomass has emerged as a likely bio-renewable source capable of producing fuel and value added chemicals in a closed carbon loop, thus eliminating greenhouse gas problems.3 Biomass derived high octane liquid fuels1,4,5–8 such as 2,5-dimethylfuran (DMF), 5-ethoxymethylfurfural (EMF), ethyl levulinate (EL),9 jet/diesel ranged alkanes and chemicals such as 2,5-bis-ethoxymethylfurfural (BEMF),10,11 2,5-furandicarboxylic acid (FDCA),12 2,5-diformylfuran (DFF), gamma-valerolactone (GVL), tetrahydrofuran (THF), 2-methyltetrahydrofuran (2MeTHF), levulinic acid (LA), 5-hydroxymethylfurfural (HMF) route13,14 are some of the contenders for being alternatives to fossil based products. Moreover, HMF itself is a promising platform chemical employed to produce an array of chemicals and fuel such as gasoline, diesel, polymers, solvents15 and other value added productss.16,17 Similarly, LA is one of the top ten biomass-derived platform chemicals that can be used to produce alternative of petroleum-derived chemicals and transportation fuels.18–20 In addition to HMF, LA, and furfural (FL) which are produced from cellulosic and hemi cellulosic component of the lignocellulosic biomass, have sought attention as a major precursor for the production of biofuel.17,19
In general, fructose is the preferred C6 carbohydrate substrate by choice for HMF and LA production due to simple dehydration step. On the contrary, glucose as a substrate is relatively cheaper and produced in bulk as compared to fructose. Moreover, fructose itself is produced from glucose via isomerization reaction, thus producing HMF and LA directly from glucose holds a better sustainability and industrial value.21 Since, HMF and LA are well known platform chemicals acting as precursor for an array of products including biodiesel, surfactants, solvents and lubricants, a more sustainable approach to produce these platform chemicals by using a readily available, abundant, cost-effective and green acid catalyst is required.
Recently, efforts have been made to produce HMF and LA via isomerization, dehydration and rehydration of glucose at elevated temperatures in the presence of homogeneous Lewis acidic salts and Brønsted acidic materials such as LaCl3,CrCl2, CrCl3, FeCl3, FeCl2, CuCl, CuCl2, VCl3, MoCl3, PdCl2, PtCl2, PtCl4, RuCl3, RhCl3, SnCl2, SnCl4,AlCl3, IrCl3 etc.,21,22 ionic liquids,23 solid acids14 and mineral acids.24 Interestingly, glucose conversion into HMF requires isomerization of glucose to fructose followed by dehydration reaction. The isomerization step essentially requires Lewis acidity whereas dehydration is favored in the presence of Brønsted acids. Thus, neither Lewis acid nor Brønsted acidity alone may be helpful in complete conversion of glucose into HMF and LA.20,25 Indeed, a combination of Lewis and Brønsted acid sites may be more favorable than individual acid sites. In this regard, An et al. explored metal sulfates such as (Al2(SO4)3·18H2O, Ti(SO4)2, Co(SO4)3, Fe2(SO4)3, CuSO4, CoSO4, MgSO4, ZnSO4 and K2SO4) as promising catalysts for the synthesis of n-butyl levulinate from carbohydrates.26 However, in case of homogeneous catalyzed reactions, the separation of metal salts and mineral acids from the product stream is a challenging task, whereas metal supported catalysts are relatively costlier which limits their application. On the contrary, potash-alum (PA) is an inexpensive and readily available material that has been used for a long time in water purification, due to its excellent internal pores.27 PA is reported to have mild Lewis acidity and relatively non-corrosive nature28 which makes it a promising catalyst for dehydration of C5 and C6 sugars into value added chemicals such as HMF and LA. Interestingly, reaction pathway for production of furfural from hemicellulose derived xylose and arabinose is analogous to reaction pathway followed in the production of HMF from glucose. Along these lines, catalysts which are effective for HMF production from glucose should also be effective in FL production from xylose. Moreover, application of PA as a potential catalyst is important because of its low cost and environment friendliness, which essentially allows it to qualify in the category of green catalysts. Therefore, here we envisaged the application of economical and commercially available PA as a green and novel catalyst for the production of HMF, LA and FL from bio-renewable carbohydrate substrates such as glucose and xylose, respectively. To the best of our knowledge, use of PA for the synthesis of HMF, LA and FL from glucose and xylose is reported for the first time.
Materials and methods
Materials
Glucose, fructose, xylose, and sucrose were purchased from Thomas-Baker Chemicals (India) and used as received. Methyl isobutyl ketone (MIBK) was purchased from Spectrochem Chemicals, India, sodium chloride and potash-alum (PA) were procured from local shop in Delhi. DMSO-d6 and CDCl3 were purchased from Sigma-Aldrich, India. All the chemicals used were of high purity (>99.9%).
Experimental. Effectiveness of PA as catalyst for production of HMF, LA and FL from bio-renewable feedstocks was tested in a biphasic system (water and MIBK) by adding desired amount of substrate, solvent and catalyst in a 100 mL hydrothermal reactor. In a typical experimental procedure, 10 mmol of sugar and 1.2 mmol of PA were dispensed into the reactor containing 10 mL of water + MIBK mixture (1
:
4 v/v). Prior to reaction, the solution was stirred for 5 minutes with 600 rpm at room temperature to completely dissolve the reactants into the solvent. The reactor was then placed inside a temperature controlled furnace pre-heated to desired temperature range of 140–190 °C. After completion of reaction, the reactor was cooled down to room temperature and the organic phase was separated by decantation. The aqueous phase was washed three times with MIBK to extract remaining organic products. Collected organic phase was evaporated under vacuum in a rotary evaporator for MIBK separation and crude product was weighed. The purity and yield of products were measured by 1H-NMR, using known amount of mesitylene as an internal standard.1H-NMR (CDCl3) HMF: δ 9.55 (s, CHO), 7.24 (d, J = 3.99 Hz, CH), 6.53(d, J = 3.68 Hz, CH), 4.75 (s, CH2–) ppm. 13C NMR (CDCl3): δ 177.68, 161.08, 123.23, 109.79, 57.073 ppm. LA: δ 2.712 (t, J = 12.43 Hz, CH2), 2.56 (t, J = 10.96 Hz, CH2), 2.13 (s, CH3) ppm. 13C NMR (CDCl3) LA: δ 207.04 (C
O) 177.59 (C
O, COOH), 37.8796 (CH2), 30.49 (CH2), and 29.77 (CH3) ppm.
1H-NMR of FL in CDCl3: δ 9.6447 (s, 1H), 7.68 (d, 1H), 7.24 (d, 1H), 6.59 (q, 1H).
Determination of total yield and individual yield. The qualitative and quantitative analysis of products were done by 1H NMR spectroscopic method. A known amount of mesitylene as internal standard was added into the crude product mixture in CDCl3. The yields of HMF, LA and FL were calculated from integrated values of –CHO and –CH2 protons of HMF, LA and three aromatic ring protons of mesitylene. The NMR yields were further validated by HPLC analysis for some experiments. Agilent HPLC equipped with a C-18 reverse phase and Hi-Plex H column, a refractive index (RI) detector and a photodiode array (PDA) detector, was used. The PDA detector was used for analysis of HMF, LA and FL using water–acetonitrile as a mobile phase. Post this, characteristic peaks of products were identified from their retention times. Each peak was integrated, and the actual concentrations of products were calculated from their respective pre-calibrated plots of peak areas vs. concentrations. All the experiments were performed in triplicate and averaged to ensure the repeatability of data. There was less than 5% error in overall yield of the products.
Determination of remaining sugar. Unreacted sugar in product mixture was calculated by phenol–sulphonic acid method. For typical measurement, 100 μL aqueous solution in 10 mL distilled water, mix. 1 mL this diluted solution in 5 mL measuring conical flask, added 0.5 mL, 5% phenol, stirred 30 min, then added 2.5 mL conc. H2SO4, mix and heated 5 min at 100 °C, cool and analyzed by UV, spectra shown in Fig. S5.†
Results and discussions
Preliminary experiments were carried out for dehydration of glucose/fructose using 1.2 mmol of PA as catalyst in a glucose to PA molar ratio of 8.3, which led to 61% and 40% total known products yield from fructose and glucose, respectively, in 6 h at 140 °C reaction temperature. HMF was the major product (58% and 40% yield) from both the reactants fructose and glucose (Table 1, entries 1 & 2) whereas levulinic acid was measured minor product. It is evident that PA as a catalyst is very active which can be attributed to the acidity arising from incompletely coordinated aluminum atoms (three rather than four or six). Moreover, it is well known that [Al(OH)2(aq)2] is an active species for the isomerization and dehydration of mono-sugar including glucose and xylose.29–31 Thus, PA (KAl2(SO4)3·12H2O) in aqueous medium may have undergone a transformation to yield [Al(OH)2(aq)2] and sulphate group causing significant activity in PA. Other possible reason may be the trapped water molecules inside the interlayer structure of potash alum which may have caused acidity.32 The results obtained are in line with earlier studies by various prominent research groups which suggests that PA contains acidic properties possibly due to presence of alumina which makes it an interesting and effective catalyst for one pot conversion of mono-sugar conversion as compared to mineral acids, metals salts and zeolites.33,34 In this regard, Yao-Bing Huang et al., have recently reported 100% conversion of LA and 99.4% methyl levulinate yield from Al2(SO4)3 at 110 °C under microwave-irradiation.35
Table 1 Dehydration of hexose sugar (glucose/fructose) and product distributiona
S. No. |
Substrate |
Catalyst |
Solvent |
t (h) |
Total yield (%) |
Yield (%) |
HMF |
LA |
W = water, M = MIBK, W* = water saturated with NaCl, T = THF. AlCl3 + KCl = 1.2 mmol. AlCl3 + KCl + Na2SO4 = 1.2 mmol, substrate =10 mmol, PA = 1.2 mmol, solvent = 10 mL (water + MIBK, 1 : 4). |
1 |
Fructose |
PA |
W + M |
6 |
61 |
58 |
3 |
2 |
Glucose |
PA |
W + M |
6 |
40 |
40 |
— |
3 |
Fructose |
PA |
W* + M |
6 |
66 |
64 |
2 |
4 |
Glucose |
PA |
W* + M |
6 |
49 |
49 |
— |
5 |
Glucose |
PA |
W* + M |
10 |
57 |
39 |
18 |
6 |
Glucose |
PA |
W + T |
6 |
22 |
22 |
— |
7 |
Glucose |
PA |
W* + T |
6 |
25 |
25 |
— |
8 |
Glucose |
PA |
W* + T |
15 |
63 |
21 |
42 |
9b |
Glucose |
Al3+ + K+ |
W + M |
6 |
34 |
34 |
— |
10b |
Glucose |
Al3+ + K+ |
W*+ M |
6 |
42 |
42 |
— |
11c |
Glucose |
Al3+ + K+ + SO42− |
W + M |
6 |
27 |
27 |
— |
12c |
Glucose |
Al3+ + K+ + SO42− |
W* + M |
6 |
37 |
37 |
— |
Similarly, experiments were performed in the presence of saturated solution of NaCl, (30 wt%) resulting an improvement yield of HMF (64% and 49%, from glucose and fructose respectively) (Table 1, entries 3 and 4). The HMF yield improved from 58% to 64% and 40–49% from fructose and glucose, respectively by loading the sodium chloride in aqueous phase (Table 1, entries 1, 3 and 2, 4). Enhancement in yield could be attributed to the “salting-out effect” of metal salts which causes improved partitioning of HMF into the extracting phase.36 Eventually, the result indicates that yield of HMF can be enhanced without using a high boiling solvent like DMSO.37 Moreover, total product yield obtained from glucose further improved from 49% to 57% when the reaction time was increased to 10 h (Table 1, entry 5). In contrast, a swift decline in HMF yield (from 49% to 39%) was measured on further increase in reaction time from 6 h to 10 h (Table 1, entry 5). It is possible that partial amount of HMF may have remained in the aqueous phase which underwent rehydration reaction to yield LA with passage of time. Interestingly, 18% LA yield measured in prolonged reaction time of 10 h further supports this hypothesis.
Similarly, HMF yield from glucose and fructose declined significantly when experiments were performed using THF instead of MIBK as solvent at 140 °C temperature for 6 h (Table 1, entries 6 & 7). THF and water are miscible and thereby formed a monophasic solution, which may be a possible cause for reduced total yield. Moreover, HMF cannot be concurrently extracted from the reactive phase, thereby leading to possibility of further reactions due to prolonged interaction between products and the catalyst. On the contrary, LA selectivity increased to 42% when experiments were performed in the presence of water + THF solvent at 140 °C temperature for 15 h (Table 1, entry 8). The system consisting of water + THF as solvent comparatively took longer time to desired yield (22% total yield in 6 h at 140 °C) as compared to system with water + MIBK media (40% total yield in 6 h at 140 °C). Again, formation of undesired and byproducts could be attributed to prolonged contact time between intermediates, reactants and the catalysts in water + THF phase. In contrast, use of MIBK leads to formation of a biphasic system which immediately extracts products when formed; thus, minimizes the possibility of further reaction or reverse mechanism. In addition, dehydration of glucose or fructose in water phase for prolonged time in the presence of an acid catalyst is non-selective due to the rehydration of HMF to LA and formic acid.36 The result obtained for a longer reaction time (15 h) was found to be in line with this hypothesis (Table 1, entry 8). A further detailed study on other possible reasons for LA formation is undergoing which may provide a detailed insight into it in future. Nevertheless, overall role of PA remained instrumental in determining the total yield.
Further experiments were performed under comparable reaction conditions using homogeneous mixture of AlCl3 + KCl and AlCl3 + KCl + Na2SO4 salts in order to develop insights into PA catalytic activity, consequently 34% total yield was measured in the presence of AlCl3 + KCl and 27% in the presence of AlCl3 + KCl + Na2SO4 (Table 1, entries 9 and 11). The difference in catalytic performances for the Al3+ salts with other salts (KCl, Na2SO4) may be due to different Brønsted acidities in the water. Moreover, when experiments were repeated with NaCl saturated water in the presence of other salts and sulphates, overall total yield remained low as compared to pure PA catalyst as shown in Table 1 (entries 9–12). Thus, PA offered higher catalytic activity based on HMF yield as compared to the activity of the individual components mixed separately. Similarly, a blank run (without PA) yielded only ∼2% of HMF at 140 °C for 6 h. Eventually, glucose converted to blackish mass (in blank reaction) in 6 h at 180 °C temperature, suggesting hydrothermal conversion of sugar to undesired carbonaceous material. Consequently, it is difficult to make a complete carbon balance of products due to limitations of NMR technique to identify all undesired products.
Effect of reaction time and temperature
Table 2 shows total yield, HMF and LA yields. The trend of the results reveals that formation of key products depends on the reaction time and temperature. Dehydration of glucose for 1 h (Table 2, entry 1) resulted in a merely 8% total yield with 100% HMF selectivity. The total yield improved from 8% to 19% when the reaction time was increased to 3 h (Table 2, entry 2). A further increase in reaction time to 6 h resulted in 49% total yield with 100% HMF selectivity. Further experiments for longer reaction time (10–15 h) showed a marginal difference in total yield (Table 2, entries 4 and 5). However, HMF selectivity decreased probably due to its rehydration to LA.
Table 2 Dehydration of glucose to HMF, ring opening and formation of LA at high temperaturea
S. No. |
T (°C) |
Time |
% Total yield |
% Yield |
HMF |
LA |
Other reaction condition: glucose = 10 mmol (1.8 g), PA = 1.2 mmol, solvent = 10 mL (water + MIBK, 1 : 4). |
1 |
140 |
1 h |
8 |
8 |
— |
2 |
140 |
3 h |
19 |
19 |
— |
3 |
140 |
6 h |
49 |
49 |
— |
4 |
140 |
10 h |
57 |
39 |
18 |
5 |
140 |
15 h |
63 |
21 |
42 |
6 |
160 |
6 |
62 |
28 |
34 |
7 |
180 |
6 |
53 |
15 |
38 |
Fig. 1 shows a stack plot of 1H-NMR spectra of the crude products obtained from reaction time variation experiments. It shows HMF rehydration to LA and formic acid (FA) starts after 6 h. Self-polymerization or cross-polymerization of HMF with glucose or fructose could be another possible reason for lower HMF yield. The signal intensity of the –COOH proton of formic acid (δ = 8.10 ppm) is very low as compared to the methylene protons of LA (2CH2, δ 2.7 and 2.5 ppm), although equimolar amounts of LA and formic acid are expected from HMF rehydration. This may be due to fact that the –COOH proton signal of formic acid did not resolve well in a reaction mixture or disappeared due to its consumption and appeared in undefined side products like humins. In comparison to LA, low intensity of FA peaks was also confirmed by the 1H-NMR spectroscopy NMR (Fig. S3†). NMR spectra clearly shows that FA in the presence of PA acts as formylating agent and formed 5-(formyloxymethyl)furfural (FMF).38 Moreover, to explore the effect of reaction temperature on total yield of the crude product and HMF yield, we performed dehydration reaction at 160 °C for 6 h. Where significant improvement in total yield was observed (62%). However; HMF yield decreased to 28% (Table 2, entry 6), possibly due to subsequent conversion of HMF into LA. Further increase in the reaction temperature to 180 °C resulted in a decrease in HMF yield (15%), but an enhanced yield of LA (38%) (Table 2, entry 7). One possible reason for the decrease in HMF yield is likely due to rehydration of HMF into LA. In addition, loss of HMF yield can also be attributed to formation of undesired products and humins at higher temperature. Thus, optimum condition for higher HMF production (49% yield) from glucose in the presence of PA catalysts is 6 h at 140 °C reaction temperature whereas optimum conditions for higher levulinic acid yield (42% yield) is 15 h at 140 °C reaction temperature.
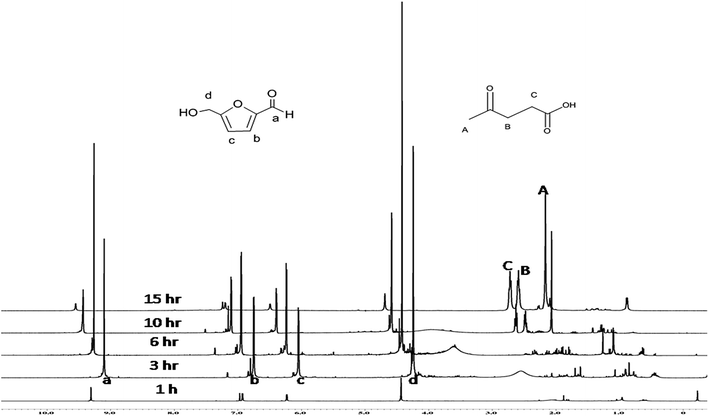 |
| Fig. 1 1H NMR in CDCl3, aqueous phase PA catalyzed glucose dehydration in a stirred, oil-bath reflection reaction at 140 °C. Other reaction condition: glucose = 10 mmol (1.8 g), PA = 0.6 g, solvent = 10 mL (1 : 4, water + MIBK). In this plot, X-axis of 3 h, move 0.2 ppm right, 10 h 0.2 ppm left, 15 h, 0.4 ppm left, with respect to 1 h as standard parameter, for clarity of peak 1H-NMR analysis. | |
The effect of PA loading. Fig. 2 represents effect of catalyst loading on overall yield of HMF and LA at 140 °C reaction temperature for 6 h. It was observed that catalyst concentration has played a key role in determining HMF and LA yield respectively. PA concentration played a key role in the conversion of glucose. At a PA/glucose weight ratio of 1
:
6, 28% HMF yield was obtained which further enhanced to 49% at PA to glucose weight ratio of 1
:
3. However, as the catalyst to glucose ratio increased (1
:
1), the HMF yield and selectivity decreased in the form LA. However, total combined yield (HMF, 40% + LA, 13%) increased to 63%. At high catalyst to substrate loading (1
:
1) at 140 °C for 6 h, rehydration of HMF occurred in the form of LA, results shown in Fig. 3. This behavior can be attributed that 1
:
3 catalyst to glucose ratio is sufficient for selective conversion of HMF at the lower temperature (140 °C) and time (6 h).
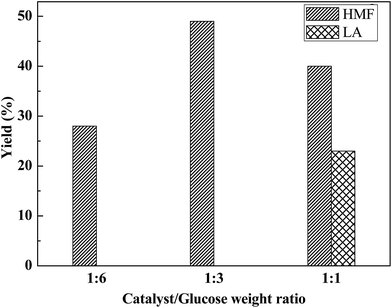 |
| Fig. 2 Effect of catalyst loading on the dehydration of glucose at 140 °C for 6 h. | |
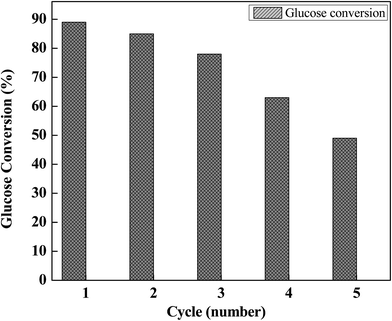 |
| Fig. 3 Reuse of PA catalyst, for the transformation of glucose to HMF, reaction condition: glucose = 10 mmol, PA = 1.2 mmol, solvent = 10 mL (1 : 4, water + MIBK), at 140 °C. | |
Catalyst reusability
In order to study the catalyst's reusability, experiments were performed at optimal reaction conditions (140 °C and 6 h). The result of the first cycle is discussed in earlier section and tabulated in Table 1, entry 4. Post this, spent aqueous phase was collected after separation of the organic phase from the 1st cycle. 2nd reaction cycle was started after addition of 10 mmol of glucose and 8 mL fresh MIBK, in the spent aqueous phase. Moreover, no fresh PA catalyst was added to compensate any loss of the catalyst in the first run. This process was repeated till five catalytic cycles to ensure long term sustainability of the process. The total conversion of glucose from each cycle is shown in Fig. 3. The results indicate that total conversions of glucose slightly decrease. This suggests that the catalyst activity decreases slowly over cycles due to an interaction of side products humins with active metal species Al3+. The color of the solution turned from colorless (in the 1st cycle) to sticky-brownish (in the 5th cycle) due to accumulation of humins in the aqueous phase.
Dehydration mechanism
The dehydration of glucose and fructose into HMF precedes either via cyclic or acyclic pathways.22 Overall, direct transformation of glucose into HMF involves two steps: (1) isomerization of glucose (glucopyranose) to fructose (fructofuranose), and (2) dehydration of fructofuranose (loss of 3 mol of water) to HMF. It is well known that Gibbs free energy of fructose interaction with DMSO causes release of first water molecule from β-D-fructofuranoses, whereas the interaction through H atom of -1OH and -4OH with DMSO causes release of second and third water molecules, respectively.39 In our earlier study, we have proposed that glucose conversion proceeds via 1,6-anhydro-β-D-glucopyranose (AGP), 1,6-anhydro-β-D-glucofuranose (AGF) and 1,6-anhydro-α-D-fructofuranose (AFF) intermediates in water (Scheme 1).20 However, due to the presence of Al3+ and Brønsted acidity in the investigated reaction, an aluminate-mediated rearrangement of glucose to fructose occurs through formation of a furanoid fructose–aluminate complex, where Al3+ catalyze the mutarotation of α-and β-glucopyranose isomers.40 A similar mechanism has been suggested by other prominent research groups working in the area of biomass conversion and related catalysis.41 Thus, we propose a similar mechanism for experiments performed in the presence of Al containing PA catalyst. Lewis acidity of PA is responsible for the isomerization of glucose to fructose, whereas Brønsted acidity facilitates for the dehydration isomerized intermediates to HMF followed by HMF rehydration into LA and FA at a prolonged reaction time.
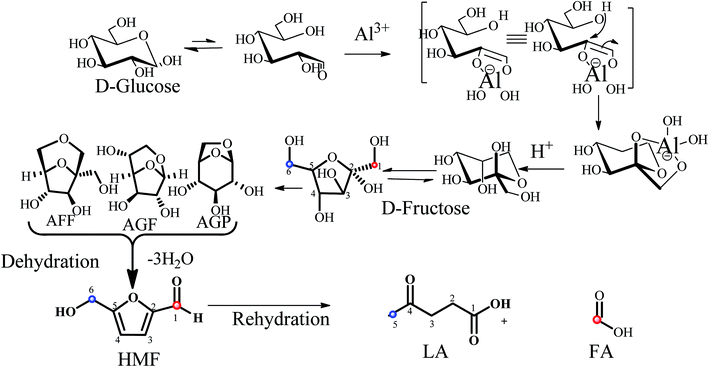 |
| Scheme 1 Reaction pathway for catalytic conversion of glucose into HMF & LA. | |
Dehydration of xylose to furfural (FL)
Since xylose to furfural (FL) conversion follows a similar reaction pathway to that of glucose to HMF, experiments were performed using PA for conversion of xylose into FL. The preliminary experiments for xylose conversion were performed in biphasic solvent (water + MIBK). 10 mmol of xylose in the presence of 3.1 mmol PA catalyst at 140 °C yielded 5% furfural in 6 h. On increasing the reaction temperature from 140 to 160 °C, a significant improvement in FL yield (27%) was observed (as shown in Fig. 4) in 6 h. The increase in FL yield at 180 °C and 190 °C resulting into 47% and 55% FL yield respectively, in 6 h reaction time. Increase in FL yield at higher temperatures can be attributed to the entropy effect.42 Furthermore, effect of reaction time on FL yield was investigated by performing the experiments at 180 °C for longer time (10 h), however, very less improvement in furfural yield (51%) was observed.
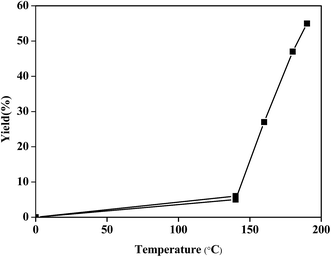 |
| Fig. 4 Influence of the reaction temperature in the dehydration of D-xylose in the presence of PA as catalyst in biphasic solvents. Other reaction condition: xylose = 10 mmol, PA as catalyst = 1.2 mmol, time = 6 h, solvent (water + MIBK) = 10 mL, 1 : 4, *yield = molar yield. | |
Techno-economic assessment of carbohydrate conversion to value added chemicals
Carbohydrate based chemicals synthesis and use have got significant attention in recent years due to its carbon neutral ability and environmental benefits. However, common implementation of carbohydrate based chemicals mainly depends on the cost competitiveness with fossil based chemicals and fuels and due to high cost of catalyst, carbohydrate based chemicals are not attractive choice for industry. PA has great potential to replace the high cost heterogeneous materials and best alternative of mineral acid based catalyst. PA alum is cheapest materials (>1$ per kg) can be utilized in the large scale production of furfural (5–9$ per kg), HMF (∼300 $ per kg) and LA (40–70$ per kg), and may be able to lower-down the price and competitive with fossil fuel based chemicals.
Conclusion
The use of potash alum as catalyst for the conversion of carbon dioxide neutral biomass fraction for the production of furfural and HMF is a vital alternative to hazardous mineral acid and costly nanoparticles solid acid. The use of potash alum is the most inexpensive and green catalyst for dehydration of carbohydrate fraction. The results showed that potash alum (PA) is a promising catalyst for catalytic conversion of carbohydrates and xylose into HMF and FL, respectively. Under optimum reaction conditions, glucose and fructose yielded 40% and 58% HMF, respectively, in 6 h at 140 °C temperature in the presence of 1.2 mmol PA. In biphasic solvent containing NaCl saturated water as a reactive phase, HMF yield improved to 49% and 64% from glucose and fructose, respectively, under identical reaction parameters. Similarly, conversion of xylose in the presence of 1.2 mmol PA in 6 h at 190 °C resulted in 55% FL. Overall, PA shows significant promises for catalytic conversion of carbohydrates and xylose. The basic strategy, thereby, to use cheap and inexpensive PA catalyst as a replacement for mineral acids, metal chlorides, ionic liquids, strong organic acids, strong Lewis and Brønsted acids which are comparatively expensive and pose hazardous effect to the environment.
Conflicts of interest
There are no conflicts to declare.
Acknowledgements
Dinesh Gupta is grateful to Science and Engineering Research Board (SERB), Government of India for National Post Doctoral Fellowship (PDF/2016/000458).
References
- F. W. Lichtenthaler, Acc. Chem. Res., 2002, 35, 728–737 CrossRef CAS PubMed.
- C. J. Campbell and J. H. Laherrare, Sci. Am., 1998, 278, 60–65 CrossRef.
- R. A. Sheldon, Green Chem., 2016, 18, 3180–3183 RSC.
- H. Olcay, A. V. Subrahmanyam, R. Xing, J. Lajoie, J. A. Dumesic and G. W. Huber, Energy Environ. Sci., 2013, 6, 205–216 CAS.
- M. J. Climent, A. Corma and S. Iborra, Green Chem., 2014, 16, 516–547 RSC.
- A. Corma, S. Iborra and A. Velty, Chem. Rev., 2007, 107, 2411–2502 CrossRef CAS PubMed.
- O. Casanova, S. Iborra and A. Corma, ChemSusChem, 2009, 2, 1138–1144 CrossRef CAS PubMed.
- M. Mascal and S. Dutta, Green Chem., 2011, 13, 40–41 RSC.
- E. Ahmad, M. I. Alam, K. K. Pant and M. A. Haider, Green Chem., 2016, 18, 4804–4823 RSC.
- S. Van de Vyver, J. Thomas, J. Geboers, S. Keyzer, M. Smet, W. Dehaen, P. A. Jacobs and B. F. Sels, Energy Environ. Sci., 2011, 4, 3601–3610 CAS.
- M. Balakrishnan, E. R. Sacia and A. T. Bell, Green Chem., 2012, 14, 1626–1634 RSC.
- B. Saha, D. Gupta, M. M. Abu-Omar, A. Modak and A. Bhaumik, J. Catal., 2013, 299, 316–320 CrossRef CAS.
- A. Dutta, D. Gupta, A. K. Patra, B. Saha and A. Bhaumik, ChemSusChem, 2014, 7, 925–933 CrossRef CAS PubMed.
- M. G. Mazzotta, D. Gupta, B. Saha, A. K. Patra, A. Bhaumik and M. M. Abu-Omar, ChemSusChem, 2014, 7, 2342–2350 CrossRef CAS PubMed.
- D. Gupta and B. Saha, Catal. Commun., 2017, 100, 206–209 CrossRef CAS.
- A. Bohre, B. Saha and M. M. Abu-Omar, ChemSusChem, 2015, 8, 4022–4029 CrossRef CAS PubMed.
- A. Bohre, S. Dutta, B. Saha and M. M. Abu-Omar, ACS Sustainable Chem. Eng., 2015, 3, 1263–1277 CrossRef CAS.
- J. P. Lange, E. van der Heide, J. van Buijtenen and R. Price, ChemSusChem, 2012, 5, 150–166 CrossRef CAS PubMed.
- G. M. G. l. Maldonado, R. S. Assary, J. A. Dumesic and L. A. Curtiss, Energy Environ. Sci., 2012, 5, 8990–8997 Search PubMed.
- D. Gupta, S. Kundu and B. Saha, RSC Adv., 2016, 6, 100417–100426 RSC.
- V. Choudhary, R. I. Burnett, D. G. Vlachos and S. I. Sandler, J. Phys. Chem. B, 2012, 116, 5116–5120 CAS.
- S. Dutta, S. De, M. I. Alam, M. M. Abu-Omar and B. Saha, J. Catal., 2012, 288, 8–15 CrossRef CAS.
- H. Zhao, J. E. Holladay, H. Brown and Z. C. Zhang, Science, 2007, 316, 1597–1600 CrossRef CAS PubMed.
- J. N. Chheda, Y. Roman-Leshkov and J. A. Dumesic, Green Chem., 2007, 9, 342–350 RSC.
- H. Yan, Y. Yang, D. Tong, X. Xiang and C. Hu, Catal. Commun., 2009, 10, 1558–1563 CrossRef CAS.
- R. An, G. Xu, C. Chang, J. Bai and S. Fang, J. Energy Chem., 2017, 26, 556–563 CrossRef.
- K.-N. Oo, K.-S. Aung, M. Thida, W.-W. Khine, M.-M. Soe and T. Aye, J. Diarrhoeal Dis. Res., 1993, 172–174 CAS.
- G. S. S. Kumar and S. Kumaresan, J. Chem. Sci., 2012, 124, 857–863 CrossRef.
- Y. Yang, C.-w. Hu and M. M. Abu-Omar, Green Chem., 2012, 14, 509–513 RSC.
- Y. Yang, C.-W. Hu and M. M. Abu-Omar, ChemSusChem, 2012, 5, 405–410 CrossRef CAS PubMed.
- Y. Yang, C. Hu and M. M. Abu-Omar, Bioresour. Technol., 2012, 116, 190–194 CrossRef CAS PubMed.
- H. Sachdeva, D. Dwivedi and R. Saroj, Sci. World J., 2013, 22, 4953–4963 CAS.
- J. Azizian, A. A. Mohammadi, A. R. Karimi and M. R. Mohammadizadeh, J. Org. Chem., 2005, 70, 350–352 CrossRef CAS PubMed.
- L. Zhou, H. Zou, J. Nan, L. Wu, X. Yang, Y. Su, T. Lu and J. Xu, Catal. Commun., 2014, 50, 13–16 CrossRef CAS.
- Y.-B. Huang, T. Yang, B. Cai, X. Chang and H. Pan, RSC Adv., 2016, 6, 2106–2111 RSC.
- B. Saha and M. M. Abu-Omar, Green Chem., 2014, 16, 24–38 RSC.
- Y. Román-Leshkov and J. A. Dumesic, Top. Catal., 2009, 52, 297–303 CrossRef.
- S. De, S. Dutta and B. Saha, ChemSusChem, 2012, 5, 1826–1833 CrossRef CAS PubMed.
- M.-F. He, H.-Q. Fu, B.-F. Su, H.-Q. Yang, J.-Q. Tang and C.-W. Hu, J. Phys. Chem. B, 2014, 118, 13890–13902 CrossRef CAS PubMed.
- J. Tang, L. Zhu, X. Fu, J. Dai, X. Guo and C. Hu, ACS Catal., 2016, 7, 256–266 CrossRef.
- J. Tang, X. Guo, L. Zhu and C. Hu, ACS Catal., 2015, 5, 5097–5103 CrossRef CAS.
- A. S. Dias, M. Pillinger and A. A. Valente, J. Catal., 2005, 229, 414–423 CrossRef CAS.
Footnote |
† Electronic supplementary information (ESI) available. See DOI: 10.1039/c7ra07147g |
|
This journal is © The Royal Society of Chemistry 2017 |
Click here to see how this site uses Cookies. View our privacy policy here.