DOI:
10.1039/C7RA06785B
(Paper)
RSC Adv., 2017,
7, 35795-35804
Performance of ZnMn2O4/SiO2 sorbent for high temperature H2S removal from hot coal gas
Received
19th June 2017
, Accepted 8th July 2017
First published on 19th July 2017
Abstract
A spinel ZnMn2O4 sorbent supported on SiO2 was fabricated using a wetness impregnation method for high temperature desulfurization. The operating parameters including operating temperature, ZnMn2O4 content, space velocity, gas composition, and multiple desulfurization/regeneration cycles were evaluated to understand the optimal condition. The ZnMn2O4/SiO2 sorbent exhibits better desulfurization performance when operating temperature is controlled above 600 °C and the suitable space velocity is between 5000–15
000 h−1. The relationship among CO, H2, and CO2 on sorbent utilization could be explained via the water shift reaction. The sorbent utilization of the ZnMn2O4/SiO2 sorbent was retained at approximately 70% after ten desulfurization/regeneration cycles. Elemental analyses demonstrated that the formation of the spinel structure of ZnMn2O4/SiO2 improved the Zn stability and no Zn vaporization or loss were observed after ten desulfurization/regeneration cycles. X-ray diffraction (XRD) and temperature programmed regeneration (TPR) were used to characterize the crystal phase and regeneration phenomena of the ZnMn2O4/SiO2 sorbent. XRD results demonstrated the presence of spinel structure of ZnMn2O4, and no Zn and Mn oxides were observed after multiple cycles, indicating that the ZnMn2O4/SiO2 sorbent is thermodynamically stable for high temperature desulfurization. Through the EDS and TPR analyses, the residual sulfur was found in the regenerated sorbent and this sulfur species is sulfate from incomplete regeneration. A regeneration temperature of 700 °C was the best choice to overcome the formation of metal sulfate.
1. Introduction
In past years, various metal oxides and modified metals have been widely used as sorbents for hot coal gas desulfurization at high temperatures.1–6 Among the investigated metal sorbents, studies have primarily focused on Zn oxide (ZnO) and related modified sorbents because they present numerous advantages, such as a favorable thermodynamic property with sulfur species, they are suitable for use at a wide range of operating temperatures, and can reduce the concentration of sulfur species to less than 10 ppm.7–9 However, the reduction of ZnO and subsequent vaporization of elemental Zn remain a severe problem when the temperature is increased to 650 °C.10,11 More recently, Mn oxides and Mn-based oxides have attracted considerable attention for high temperature desulfurization.12–14 The reactivity of Mn-based oxides is higher than that of ZnO, and Mn-based oxides cannot be easily reduced to elemental Mn during hot coal gas desulfurization. To overcome the vaporization of Zn, a series of metals were added with Zn to form alloy sorbents oxides for H2S removal from hot coal gas. Huang et al.15 prepared Zn–Fe–Mn/MCM-48 sorbent for H2S removal at 550 °C and the sorbent utilization of 66.1% was achieved. They also indicated that the significant decrease in sorbent utilization after regeneration. It was due to the migration of Zn onto the sorbent surface and Zn accumulated on the surface and vaporized to the exterior from the surface. Guo et al.16 evaluated the regeneration test of Zn–Mn sorbent supported on γ-Al2O3 at 400 °C and 600 °C. The results showed that the sulfur capacity decreased with regeneration cycles and over 50% sorbent utilization was loss after nine regeneration cycles for 400 °C and 600 °C due to the destruction of BET surface and pore structure. Furthermore, the previous study revealed that the addition of Mn significantly improves the vaporization of Zn, and it can be used for high-temperature desulfurization. In addition, some crucial operating parameters were obtained and established in the temperature range of 500–700 °C.17
It is recognized that supported sorbents have high dispersion of activated species. The mesoporous silica have received much attention because of high surface, large pore volume and uniformly pore size distribution in comparison to TiO2 and γ-Al2O3.18–21 To our knowledge the preparation and application of Zn–Mn supported on SiO2 for high temperature desulfurization has not been investigated in-depth and incompletely understood. Therefore, in this study, the ZnMn2O4/SiO2 sorbent was systematically fabricated using a wetness impregnation method to obtain thermal-stable structure that is widely dispersed on SiO2. In addition to multiple desulfurization/regeneration cycles, X-ray diffraction (XRD), N2 adsorption with Brunauer–Emmett–Teller (BET), temperature programmed regeneration (TPR), scanning electronic microscopy equipped with an energy dispersive spectroscopy (SEM/EDS), and elemental analysis were used to elucidate the surface and structure properties of fresh, reacted, and regenerated ZnMn2O4/SiO2 sorbent. The experimental results provide a new aspect for the development of new sorbents for high temperature desulfurization.
2. Materials and methods
2.1 Preparation of ZnMn2O4 sorbent
The ZnMn2O4 sorbents were prepared by using the wetness impregnation process with an aqueous solutions of Mn(NO3)2·4H2O and Zn(NO3)2·4H2O as the precursors to form the structure of ZnMn2O4. Support materials used for the sorbent preparation were pure commercial products SiO2, TiO2 and γ-Al2O3 which were purchased from Sinopharm Chemical Reagent Company. All the chemical reagents used in this study were analytical grade.
First of all, pure SiO2, TiO2 and γ-Al2O3 were shattered and sieved to the desired size (50–100 mesh) and dried for 24 h before mixing with metal aqueous solution. For the preparation of ZnMn2O4/SiO2 sorbent, 12.4 g of Mn(NO3)2·4H2O and 6.1 g of Zn(NO3)2·4H2O were added in a 80 mL distilled water. The mixed solution was drop-wise added to 50 g SiO2 and was dried for 2 h at room temperature followed by drying for one day at 25 °C in an oven. For the preparation of ZnMn2O4/TiO2 sorbent, 11.3 g of Mn(NO3)2·4H2O and 5.8 g of Zn(NO3)2·4H2O were added in a 80 mL distilled water. The mixed solution was drop-wise added to 50 g TiO2 and was dried for 2 h at room temperature followed by drying for one day at 25 °C in an oven. For the preparation of ZnMn2O4/γ-Al2O3 sorbent, 11.4 g of Mn(NO3)2·4H2O and 5.8 g of Zn(NO3)2·4H2O were added in a 80 mL distilled water. The mixed solution was drop-wise added to 50 g γ-Al2O3 and was dried for 2 h at room temperature followed by drying for one day at 25 °C in an oven. Finally, all the samples were calcined at 700 °C for 2 h in air flow conditions.
2.2 Desulfurization activity performance
Simulative coal-derived gases consisted of 1% H2S, 25% CO, 15% H2, and a balance of N2 from regulation cylinders, which are similar to the quenched exit gas of the popular Kellogg Rust Westinghousecoal gasifier. The gas flow rates were monitored through mass flow controllers. All mass flow controllers were monitored accurately by an infrared soap bubble meter and the concentration of all species were calculated at the condition of standard temperature and pressure. Prior to entering the reactor, the gases were conducted in a mixing pipe to confirm that the mixture gas exhibited turbulent flow. The reactor consisted of a quartz tube, 1.6 cm i.d., 2.0 cm o.d., and 150 cm length, located inside an electric furnace. Quartz fibres were placed in the reactor to support the samples. Two K-type thermocouples were exactly inserted into the reactor near the top and bottom of the samples to measure and control the inlet and outlet temperatures. Prior to the experiment, pure nitrogen gas (purity 99.99%) was fed into the reactor for 30 min at 500 °C to remove adsorbed water and impure materials coated on the surface of the samples. In addition, blank breakthrough experiments were also conducted under the same conditions and it was verified that no reaction occurred anywhere between H2S and the lines/reactor. The inlet and outlet concentration of H2S were analysed by an on-line gas chromatograph (HP, GC-5890) equipped with a flame photometry detector (FPD) and fitted with a GS-Q capillary column. A six-port sampling with a 0.5 mL sampling loop was used to sample the inlet and outlet H2S concentrations. The desulfurization experiment was terminated when the outlet H2S concentration from the reactor approached the inlet H2S concentration. After each desulfurization run, the reactor was purged with He gas for 15 min, and regeneration began at 650 °C with 5% O2. The regeneration experiment was terminated when the SO2 concentration in the effluent gas was lower than 10 ppm.
2.3 ZnMn2O4 sorbent characterization
Crystalline structures of the ZnMn2O4 sorbent before and after desulfurization/regeneration cycles were determined by X-ray powder diffraction (RIGAKU Model D/MAX III–V) with CuKα radiation. The applied current and voltage were 30 mA and 40 kV, respectively. The diffraction patterns were recorded in the angle range 2θ = 10–80° at a scan rate of 3° min−1. The surface area was measured with a Micromeritics ASAP 2010 instrument using adsorption of nitrogen at 77 K. Prior to adsorption measurements, the samples were degassed under vacuum conditions (5 μm Hg) at 100 °C for 2 h. The surface area was calculated by the BET equation. The ZnMn2O4 sorbents were digested with aqueous aqua regia in a microwave oven. After digestion, filtration, and dilution processes, the extracted solution was analyzed by inductively coupled plasma atomic emission spectrometry (ICP/AES, JY38P model, JOBIN YVON) for determining the Zn and Mn contents.
2.4 Temperature programmed regeneration (TPR) performance
Temperature programmed regeneration (TPR) was performed by a thermogravimetric analysis equipped with differential thermal analysis (TGA/DTA, Perkin Elmer Pyris Diamond model). TPR experiments were conducted in a mixture of 5% O2 and He. A quantity of 25 mg of the reacted ZnMn2O4 sorbent was heated from room temperature to 900 °C at a heating rate of 10 °C min−1. The sample was placed on a quartz-made reactor with a PID control electronic furnace. The gaseous sulfur compounds from the outlet in the TPR were measured and recorded with a gas chromatography (Shimadzu, GC-14B) equipped with a flame photometry detector.
2.5 Scanning electronic microscopy (SEM)/energy dispersive spectroscopy (EDS)
Surface distribution of elements in red soils was obtained by using an EDS technique which employs a Phillip XL-40FEG scanning electron microscope. All the test samples were mounted on the Cu holder and were coated with platinum prior to EDS analysis.
2.6 X-ray absorption spectroscopy (XAS)
Mn K-edge spectra were undertaken on the wiggler beam-line at the National Synchrotron Radiation Research Center (NSRRC) of Taiwan. The electron storage ring operated at the energy of 1.3 GeV and the beam current varied (current of 80–200 mA). A Si (111) double-crystal monochromator (DCM) was used for providing highly monochromatized photo beams with energies 1–9 keV.
2.7 Solid-state nuclear magnetic resonance (SSNMR)
The solid-state 29Si MAS (magic angle spinning) NMR spectra of samples were recorded under 9.4 tesla with operating frequency of 104.2 MHz on a Bruker Avance DSX400 spectrometer. Zirconia rotors were spun in air at 5 kHz. The deconvolution results and regression fitting of 29Si MAS NMR were performed with Gaussian model using Origin 6.0 version software.
2.8 Elemental analysis (EA)
Elementar vario EL III Heraeus CHNOS Rapid F002, equipped with a flash combustion furnace and thermal conductivity detector (TCD) was used for determination of sulfur content after the desulfurization experimental processes.
3. Results and discussion
3.1 Effect of supports
To facilitate the expression of removal efficiency for ZnMn2O4, the sorbent utilization is used in this study and is defined as the ratio of the experimental breakthrough time and theoretical breakthrough time. The experimental breakthrough time is defined as the time from the beginning of the desulfurization to the point outlet H2S concentration reached 50 ppm. The theoretical breakthrough time is defined as the time that ZnMn2O4 is completely reacted with H2S. The theoretical breakthrough time can be accurately determined based on the contents of ZnMn2O4 and the mass flow rate of H2S and the stoichiometric reaction is represented as follows: |
ZnMn2O4 + 3H2S + H2 → ZnS + 2MnS + 4H2O
| (1) |
To explore the effect of supports on the high temperature desulfurization, 10 wt% ZnMn2O4 loading on various supports including SiO2, TiO2 and γ-Al2O3 were used and the result was shown in Fig. 1. Prior to the experiments performing, the blank, SiO2, TiO2 and γ-Al2O3 supports were preliminarily tested for their influence on the removal of H2S and results indicated that no other reactions were observed between H2S and supports. The influence of removal efficiency for supports can therefore be neglected in this study. As shown in Fig. 1, the SiO2 is found to have the best sorbent utilization whereas γ-Al2O3 appeared to have the worst sorbent utilization. The optimal temperature for all samples was observed at 600 °C. The sorbent utilization slightly decreased when temperature was controlled at 700 °C. Surprisingly, the γ-Al2O3 support appeared to have low sorbent utilization. The γ-Al2O3 has the largest BET surface area among test supports. A reasonable reason for low sorbent utilization probably associated with the formation of the metal aluminium oxide, MeAl2O4.22,23 Although TiO2 has a moderate sorbent utilization, its thermal stability is a key factor to govern the overall efficiency because of transformation of anatase to rutile/brookite. Temperature exceeded 650 °C is a formation temperature for anatase into rutile form and results in a loss of surface area.24,25 SiO2 is a thermal stability material and has been widely used as a support in catalytic field. In this study, SiO2 has the best sorbent utilization and only a slight decrease in sorbent utilization when temperature is controlled at 700 °C. Therefore, SiO2 was chosen as a key role for the rest of the experiments.
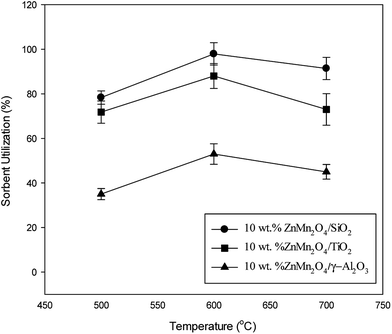 |
| Fig. 1 Sorbent utilization as a function of temperature for ZnMn2O4 on different supports. | |
3.2 Effect of operating temperature
Fig. 2 shows the effect of operating temperature on ZnMn2O4/SiO2 utilization under the experimental condition of T = 400–750 °C. Experimental results indicate that sorbent utilization increases with operating temperature. The sorbent utilization maintains a stable state when the operating temperature was controlled over 600 °C. No deactivation phenomenon is observed even the operating temperature exceed 750 °C, implying that the addition of Mn improves the vaporization of Zn at high temperature. To understand the contents of Zn and Mn, the fresh and used samples were analyzed with ICP to determine the contents of Zn and Mn. Table 1 shows the contents of Zn and Mn together with recoveries. Note that the recoveries of Zn for all samples are fairly good and no vaporization is found even at 750 °C. This study is motivated to evaluate the effectiveness of applying Mn as a promoter to improve the shortcoming of Zn-based sorbent for high temperature desulfurization. Indeed, ZnMn2O4/SiO2 sorbent shows good performance for H2S removal at high temperature. Although it is well known that high temperature enhances the desulfurization efficiency, the equilibrium concentration of H2S is a function of metal oxides and the inlet H2O content. For example, the equilibrium concentration of H2S for the reaction of MnO2 and H2S is 2.5 ppm and 216 ppm at 400 °C and 750 °C (gas composition involved CO: 42.5%, H2: 32.175%, H2O: 12.5%, CO2: 12.5%, H2S: 0.325%). When the operating temperature is controlled at 970 °C with the identical condition, the equilibrium concentration of H2S is 100 ppm.26 Recent studies have revealed that desulfurization system components become prohibitively expensive as the operating temperature increases and the optimum desulfurization temperature is controlled between 350–600 °C.27,28 Over such a range of temperatures, the efficiency of the process and its technical viability reduce the overall cost of the process.
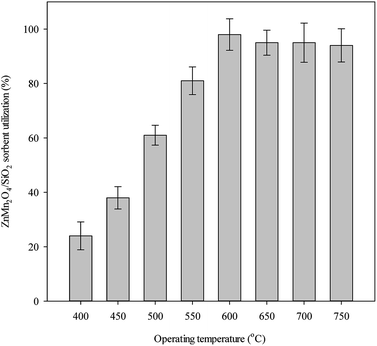 |
| Fig. 2 Effect of operating temperature on ZnMn2O4/SiO2 sorbent utilization. | |
Table 1 Contents of Zn and Mn together with the recovery for various sorbent statesa
Sorbent state |
Contents of Zn, Mn (g kgsorbent−1) and sulfur (%) |
Recovery (%) |
Preparation concentration of Zn: 27.2 g kgsorbent−1, preparation concentration of Mn: 46.1 g kgsorbent−1, sulfur content was detected by EA. |
Fresh sorbent |
Zn: 26.8 |
Zn: 98.5 |
Mn: 46.3 |
Mn: 100.4 |
Reacted sorbent at 600 °C |
Zn: 27.3 |
Zn: 100.4 |
Mn: 46.1 |
Mn: 101.3 |
S: 1.97 |
|
Reacted sorbent at 700 °C |
Zn: 26.8 |
Zn: 98.6 |
Mn: 44.7 |
Mn: 97.0 |
S: 1.91 |
|
Reacted sorbent at 750 °C |
Zn: 27.2 |
Zn: 100 |
Mn: 46.8 |
Mn: 101.6 |
S: 1.89 |
|
Regenerated sorbent |
Zn: 27.1 |
Zn: 99.6 |
Mn: 46.7 |
Mn: 101.3 |
S: 0.17 |
|
Regenerated sorbent after 3 cycles |
Zn: 27.3 |
Zn: 100.4 |
Mn: 45.7 |
Mn: 99.1 |
Regenerated sorbent after 5 cycles |
Zn: 27.7 |
Zn: 101.8 |
Mn: 46.5 |
Mn: 100.9 |
Regenerated sorbent after 10 cycles |
Zn: 27.5 |
Zn: 101.1 |
Mn: 45.8 |
Mn: 99.3 |
S: 0.17 |
|
3.3 Effect of ZnMn2O4 content
To investigate the effect of ZnMn2O4 content on the removal of H2S, various ZnMn2O4 contents ranging from 5.1–39.2 wt% were carried out in order to understand the optimal preparation content. Fig. 3 exhibits the sorbent utilization as a function of the ZnMn2O4 content. More than 95% sorbent utilization was obviously achieved when the ZnMn2O4 content was controlled less than 14.8 wt%. The sorbent utilization decreased with ZnMn2O4 content and only 60% sorbent utilization is observed for 39.2 wt% content. This implies that the higher sorbent utilization ranging from 5–15 wt% is attributed to a good dispersion of ZnMn2O4 on the SiO2 support. On the other hand, the higher content of ZnMn2O4 enhances the overall removal reaction from the kinetic consideration. The product, metal sulfides are dense materials, which increase the mass transfer resistance and further repress H2S diffusion into the sorbent core. The sorbent utilizations for 10.2 wt% and 14.8 wt% are close to 100%, however, the breakthrough curve of 14.8 wt% sorbent exhibits a more smooth feature than that of 10.2 wt% sorbent. This is due to the fact that diffusion resistance of H2S through thick sulfide layer increases and reduces the reaction rate of internal oxide. Therefore, 10.2 wt% ZnMn2O4/SiO2 sorbent is considered to be more available for a series of desulfurization reactions.
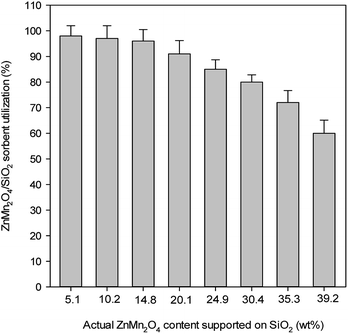 |
| Fig. 3 Effect of ZnMn2O4 contents on the on ZnMn2O4/SiO2 sorbent utilization. | |
3.4 Effect of space velocity
The effect of space velocity on ZnMn2O4/SiO2 utilization is shown in Fig. 4. The operating temperature is controlled at 600 °C and the inlet concentration of gases is fixed at 1% H2S, 25% CO, 15% H2, and a balance of N2. Results indicate that sorbent utilization reaches and maintains at the maximum value of 98% with the space velocity varying from 5000–15
000 h−1. The sorbent utilization is gradually decreased when the space velocity is increased to 20
000 h−1. With the space velocity of 35
000 h−1, the sorbent utilization is further reduced to 60%, which is about 60% of the maximum value. Reduction of sorbent utilization at high space velocity might result from the limitation of diffusion. No significant change in the sorbent utilization within the ranges of 5000–15
000 h−1, suggesting that the external mass transfer resistance can be ignored at this range. Space velocity can be further defined by the phase of the reactants at given conditions. Special values for this measurement exist for liquids and gases, and for systems that use solid catalysts. The effect of external mass transfer should be considered for the kinetic experiment when the space velocity is controlled more than 20
000 h−1. The design of space velocity depends on the scale of gas composition and the size of desulfurization reactor.
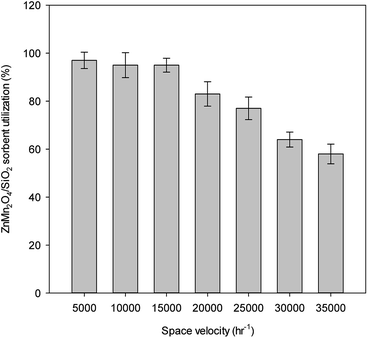 |
| Fig. 4 Effect of space velocity on ZnMn2O4/SiO2 sorbent utilization. | |
3.5 Effect of gas composition
In addition to H2S, other gases such as CO, H2 and CO2 are the main gaseous components that generated from syngas and their effects should be evaluated to understand the real condition. Fig. 5 shows the effect of different gas composition on sorbent utilization. Results indicate that the sorbent utilization can be significantly increased when CO2, H2 and CO are introduced to the gas stream individually. In the presence of CO2, H2 and CO, the sorbent utilization increases from 47 to 61, 95, and 98%. This may be explained by the water-shift reaction.
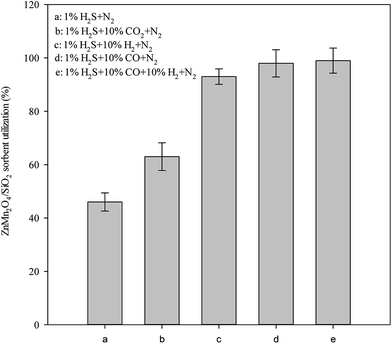 |
| Fig. 5 Effect of gas composition on ZnMn2O4/SiO2 sorbent utilization. | |
The water–gas shift reaction favors the right-hand side of the equation according to Le Chatelier's rule when CO concentration is increased. This also means that H2O is consumed in the water–gas shift reaction. Lower H2O content will favor reactions (2), which is in favor of the adsorption of H2S. Therefore, increasing the concentration of CO will enhance the adsorption reaction. On the other hand, increasing the concentration of H2 will favor the reaction toward left-hand side of the equation for the water–gas shift reaction results in formation of H2O. Similarly, the adsorption progress is inhibited due to excess H2O formation from the water–gas shift reaction.
3.6 Multiple cycles test for ZnMn2O4/SiO2 sorbent
The experimental results of the ten successive desulfurization/regeneration cycles are shown in Fig. 6. Nearly 100% of ZnMn2O4 sorbent utilization was achieved in the first cycle, indicating that all of the ZnMn2O4 sorbent reacted with H2S. The amount of ZnMn2O4/SiO2 sorbent utilization decreased gradually with an increase in the number of desulfurization/regeneration cycles, and approached a stable state. The ZnMn2O4/SiO2 sorbent utilizations for 2, 3, 4, 5 and 10 cycles were 85%, 78%, 70%, 68% and 68.5%, respectively. The ZnMn2O4/SiO2 sorbent utilization did not decrease further after multiple desulfurization/regeneration cycles. The reduction of approximately 30% of utilization was lost during the desulfurization/regeneration cycles. The reasons to cause the deactivation of sorbent probably attributed to (i) the vast loss of BET surface area, (ii) activated species loss, (iii) uncompleted regeneration. Regeneration is an intense exothermic reaction and the surface and bulk structures of the ZnMn2O4/SiO2 sorbent likely underwent a major change because of the exothermic condition. The N2 adsorption isotherm and pore size distribution for fresh, reacted and regenerated sorbents is shown in Fig. 7. It can be found that all the samples possessed the typical characteristic of type II isotherm according to the IUPAC classification. It indicated that all the sorbents exhibited a uniform ordered macro-pore structure. Furthermore, after desulfurization and regeneration processes the isotherm features have similar with the fresh sorbent, which means that the pore structures did not change too much before and after desulfurization and regeneration. BET surface areas were 86 m2 g−1, 80 m2 g−1 and 76 m2 g−1 for fresh, reacted, and regenerated sorbents. On the other hand, the sorbent after ten desulfurization/regeneration cycles retained 70 m2 g−1 of BET surface area. As shown in Fig. 7, the fresh sorbent exhibited the smaller pore diameter ranging 10–20 nm, while it ranged from 15–30 nm for the reacted sorbent. The probable reason was that few mesopores maybe collapsed during the high temperature desulfurization or resulted from the formation of metal sulfides because of larger radius of metal sulfides. After regeneration process, a broad feature of pore size distribution is obviously observed. The main pore diameter is in 20–80 nm, which indicated that the regeneration reaction is the major reason to change pore size distribution and is attributed to the exothermic reaction from regeneration. Although BET surface area was found to decrease after reaction and regeneration, it may be one of the reasons to cause sorbents' degeneration because approximately 18% BET surface area was lost after ten successive desulfurization/regeneration cycles. As mentioned, the primary problem of a Zn-based sorbent is the vaporization of elemental Zn at 550 °C. The Zn and Mn contents and the recovery (%) of various samples are listed in Table 1. As expected, the recoveries of Zn and Mn were satisfactory, and no vaporization or loss was observed. The sulfur content was measured by EA. The sulfur content were 1.97%, 1.91%, and 1.89% for 600 °C, 700 °C, and 750 °C, respectively which is corresponding to the result of Fig. 2. It is also observed the presence of sulfur after regeneration sorbent. Residual sulfur presence probably came from the incompleted regeneration reaction.
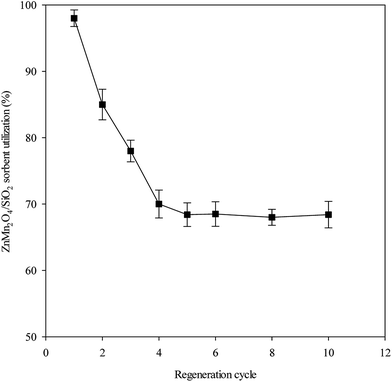 |
| Fig. 6 ZnMn2O4/SiO2 sorbent utilization as a function of multiple desulfurization/regeneration cycles. | |
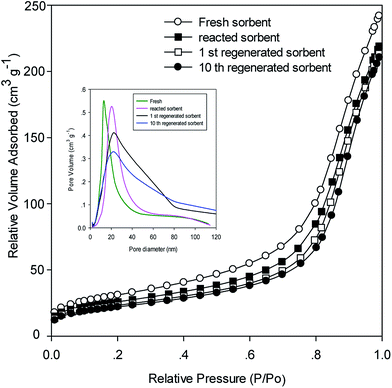 |
| Fig. 7 N2 adsorption isotherm of 10 wt% ZnMn2O4/SiO2 sorbent at different status. | |
3.7 XRD patterns
XRD was used to understand the changes in the crystal phase of the fresh, reacted and regenerated ZnMn2O4/SiO2 sorbents after multiple desulfurization/regeneration cycles. The XRD patterns of various states of sorbents were displayed in Fig. 8. As can be seen that the fresh sorbent has an amorphous structure in which a smooth peak located around at 2θ = 23° is assigned to the SiO2 support [PDF#39-1425]. On the other hand, the specific peaks at 2θ = 29.3°, 33°, 36.4°, and 60.8° were attributed to the reflection of ZnMn2O4 [PFD#05-0602], implying that all of Zn and Mn were completely reacted to form the spinel structure. No other Si–Zn–Mn oxides were detected, indicating that the interaction between SiO2 and Zn/Mn can be ignored during calcinations process. After reaction the major peaks were observed at 2θ = 34.2° and 49.2° are ascribed to the diffraction of MnS [PFD#65-0891], whereas 2θ = 26.9°, 28.5°, 30.5° and 47.5° are assigned to the reflection of ZnS [PFD#65-0891]. Note that no Zn/Mn oxides were observed after reaction, implying that the spinel structures of ZnMn2O4 sorbent were completely converted into ZnS and MnS. After regeneration the sorbent possessed the same diffraction pattern in comparison with fresh one. It is noteworthy that the intensity of MnS signals gradually decreased with reaction cycle and was not detected for the reacted sorbent after ten cycles. Previous study prepared Mn-based sorbents for high temperature desulfurization and a series of steam contents were carried out for desulfurization reaction. According to experimental results, the diffraction peaks of MnS weakened with incremental steam content, which showed that the desulfurization reaction was strongly influenced in the atmosphere.29 Another possible reasons is ascribed to the well dispersed as an amorphous phase or as nano-crystallites after multiple desulfurization/regeneration cycles.5,30 In addition to the MnS disappearance, an obvious reflection signal at 2θ = 21.9° was assigned to the diffraction of well-crystalline structure of SiO2 [PFD#46-1045]. The reaction between metal sulfides and O2 is highly exothermic and accompanying many times of desulfurization/regeneration cycles, an amorphous SiO2 may result in lattice transformation due to the high temperature rise. The well-crystalline structure of SiO2 was firstly observed in the regenerated sorbent after three cycles. Although the well-crystalline structure of SiO2 was formed during regeneration process, there is no change in the presence of ZnMn2O4 even after ten desulfurization/regeneration cycle. This result is consistence with the analysis of ICP (shown in Table 1), in which the recoveries of Zn and Mn maintained at least 99%. Ahmed et al.31 verified that spinel oxides were significantly decomposed and the single metal oxide appeared during the continuous desulfurization/regeneration cycles. From the present results obtained, the formation of ZnMn2O4 overcame the vaporization of Zn at high temperature.
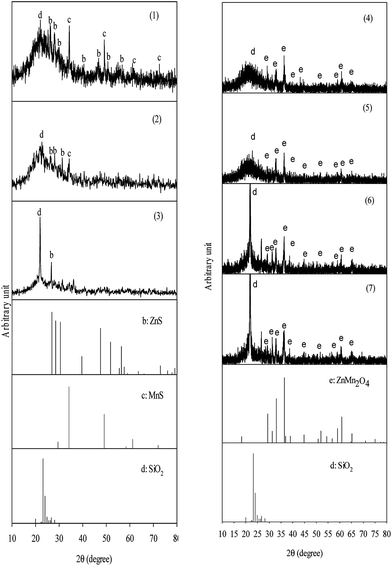 |
| Fig. 8 XRD patterns of the ZnMn2O4/SiO2 sorbent in various reactions, (1) reacted sorbent (2) reacted sorbent after three cycles (3) reacted sample after ten cycles (4) fresh sorbent (5) regenerated sorbent (6) regenerated sorbent after three cycles (7) regenerated sorbent after ten cycles. | |
3.8 XAS and SSNMR identification
The XRD patterns showed the disappearance of MnS and a significant peak of SiO2 were observed after multiple desulfurization/regeneration cycles. For better understand the fine structure of MnS after multiple desulfurization/regeneration cycles, the reacted, regenerated sorbents after ten cycles, and reference materials were evaluated by the X-ray synchrotron radiation. The extended X-ray absorption fine structure fitting results revealed that the Mn–S bond length was 2.582 Å for the reacted ZnMn2O4 sorbent. Mn–S bond length for the regenerated sorbent after ten cycles was 2.486 Å, which is longer than that of the reacted sorbent. In addition, we also evaluated the local atomic structure in Zn1−xMnxS. We found that the Mn–S bond length were 2.415, 2.418 and 2.421 Å for Zn0.88Zn0.12S, Zn0.8Mn0.2S and Zn0.67Mn0.33S, respectively. Based on our finding, it is speculated that the composition of Mn–S after ten desulfurization/regeneration cycles is a nonstoichiometric structure with zinc. The possible structure of can be expressed as Zn1−xMnxS, where x ranged from 0.33 to one and maybe present in amorphous phase. In order to understand the structural changes in SiO2 before and after regeneration in ZnMn2O4 sorbent, 29Si MAS NMR was measured and fitted by Origin software. Generally, four types of 29Si spectra are identified, namely Q1, Q2, Q3 and Q4 (Qn represents the SiO4 tetrahedron of the amorphous network which forms n bonds with neighboring tetrahedral). The analyses and deconvolution results is tabulated in Table 2. The 29Si spectrum of the fresh ZnMn2O4/SiO2 contain a main resonance at around −109.6 ppm corresponding to a trioctahedral structure with four oxygen neighbors and is assigned to the Q4 structure. The pronounced moderate peak located at −101.6 ppm corresponds to Q3, (SiO)3Si(OH) is attached to one hydroxyl group and three Si–O–Si bonds. The signal located at −92.1 ppm is assigned to the Q2 structure, (SiO)2Si(OH)2 is bound to two hydroxyl group and two Si–O–Si bonds. The fraction of Q2, Q3 and Q4 are 8.3%, 20.4% and 71.3%, respectively. This implies that the major Si structure in fresh sample is a bulk siloxane group connected with four Si–O–Si bonds. As shown in Table 2, no Q2 signal was detected and fractions of Q3 decreased for the regenerated and reacted sorbents after triple and ten cycles. The hydroxyl groups presented in Q2 and Q3 gradually disappeared from the crystal lattice of silica oxide because of the extremely heat released from the regeneration reaction at high temperature. The fraction of Q3 significantly decreased and a fraction of Q4 increased for regenerated and reacted sorbent after multiple cycles. In fact, the regeneration reaction is a highly exothermic reaction and it is believed that the highly exothermic reaction leads to the change in 29Si chemical shift. On the basis of XAS and SSMNR, it is summarily concluded that the disappearance of MnS in XRD is probably attributed to the nonstoichiometric structure of Zn1−xMnxS. On the other hand, the well-crystalline of SiO2 results from the transformation of spatial structure in lattice.
Table 2 29Si MAS NMR fitting results and deconvolution of Qn species for different status of ZnMn2O4/SiO2a
Sample status |
Q2 |
Q3 |
Q4 |
FWHM (ppm) |
δ (ppm) |
I (%) |
FWHM (ppm) |
δ (ppm) |
I (%) |
FWHM (ppm) |
δ (ppm) |
I (%) |
FWHM, δ and I represent the full width at half maximum, 29Si chemical shift, and relative intensity, respectively. Error value: FWHM ± 0.4 ppm, δ ± 1.5 ppm, I ± 3.6%. |
Fresh sorbent |
8.2 |
−92.1 |
8.3 |
6.4 |
−101.6 |
20.4 |
5.7 |
−109.6 |
71.3 |
Reacted sorbent |
9.1 |
−94.2 |
5.1 |
7.0 |
−101.8 |
17.5 |
6.3 |
−110.3 |
77.4 |
Regenerated sorbent (triple cycles) |
— |
— |
— |
7.4 |
−105.2 |
8.4 |
6.8 |
−111.5 |
92.6 |
Regenerated sorbent (ten cycles) |
— |
— |
— |
7.8 |
−106.4 |
4.8 |
6.9 |
−112.7 |
96.2 |
Reacted sorbent (ten cycles) |
— |
— |
— |
7.8 |
−106.3 |
5.1 |
6.6 |
−112.8 |
94.9 |
3.9 TPR analysis
Fig. 9 shows the TPR patterns of the reacted sorbent with a series of MnS, ZnS, ZnSO4, and MnSO4 standard samples. For MnS standard sample, two evident peaks were detected and the first peak located at 400 °C is assigned to the oxidation of MnS to Mn3O4. The second one located at 800 °C is due to the formation of MnSO4, which comes from the reaction of MnOx and SO2. For ZnS standard sample, two obvious peaks were measured at higher temperature, namely at 625 °C and 850 °C, respectively. They are assigned to the reactions of the oxidation of ZnS to ZnO, and the formation of ZnSO4, respectively. It is remarkable that the formation of metal sulfates during regeneration process. Metal sulfates were undesired by-products, which were inevitably formed due to thermodynamic favorable property with O2 and may inhibit the diffusion of O2, thereby restraining the regeneration of the interior region of the sorbent.32 Unlike metal sulfides, only one peak was obviously detected for both MnSO4 and ZnSO4 standard samples. The peak for MnSO4 and ZnSO4 standard sample is located at 775 °C and 825 °C, respectively. Therefore, it can be concluded that the MnSO4 and ZnSO4 may be decomposed at the temperature higher than of 775 °C and 825 °C. For the reacted sorbent, three major peaks appeared at 400 °C, 625 °C, and 825 °C were detected. This illustrated that the regeneration of the reacted sorbent had three stages. The signal at 400 °C was assigned to the conversion of MnS into Mn3O4 whereas the peak at 625 °C was assigned to the conversion of ZnS into ZnO. Note that a small peak appeared at 550 °C was found. The most likely explanation is that the decomposition and oxidation of ZnS that coated on the surface of reacted sorbent. Similar to the second peak, a shoulder peak was also observed at 775 °C and was attributed to the decomposition of MnSO4. There is no doubt that the final peak appeared at 825 °C was assigned to the decomposition of ZnSO4. The regeneration temperature in this study was controlled at 650 °C, which is relatively lower than the requirement of TPR result. In fact, the regeneration is a highly exothermic reaction and actual temperature should be higher than the regeneration temperature. To confirm this viewpoint, the internal temperature of reacted sorbent during regeneration process was experimentally monitored. As expected, although regeneration temperature was controlled at 650 °C, the internal temperature was measured about 780 °C. Unfortunately, the internal temperature of 780 °C appeared too low to complete the regeneration reaction according to the TPR observation and resulted in the presence of metal sulfates due to incomplete reaction.
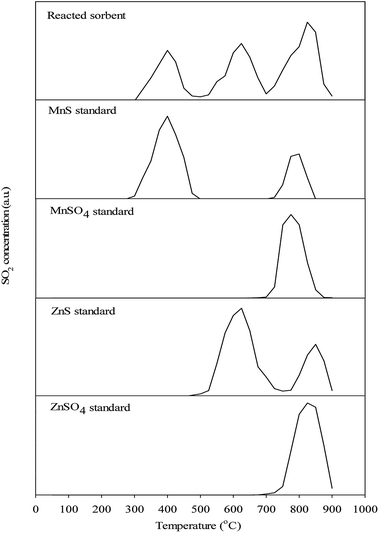 |
| Fig. 9 Temperature programmed regeneration (TPR) patterns of the reacted ZnMn2O4/SiO2 sorbent and reference compounds. | |
The TPR result showed that the temperature to complete regeneration reaction for ZnMn2O4/SiO2 sorbent should be set at 825 °C. Therefore, two sets of different regeneration temperature were conducted based on the identical condition at the regeneration temperature of 650 °C. Experimental results show that the regeneration temperature of 700 °C appears to have the better sorbent utilization than that of 750 °C (Fig. 10). After sixth desulfurization/regeneration cycles, the sorbent utilization maintain stable state. The stable sorbent utilization for 650 °C, 700 °C, and 750 °C are approximately at 70%, 85%, and 65%, respectively. In addition, the internal temperatures during regeneration process were 843 °C and 876 °C for the regeneration temperature of 700 °C and 750 °C. Note that the higher regeneration temperature (750 °C) cannot achieve the better sorbent utilization after multiple cycles. The internal temperature of 876 °C likely leads to the sintering phenomenon and further results in sorbent degradation due to the loss of surface area. ICP measurements demonstrated that the Zn recovery was 98.5%, which confirms no Zn vaporization during desulfurization/regeneration cycles at the regeneration temperature of 750 °C. However, the surface area decreased by 32 m2 g−1 and small pore structures was distinctly destructed. It is believed that the temperature of 700 °C is the optimal operating choice because of higher sorbent utilization after multiple cycles.
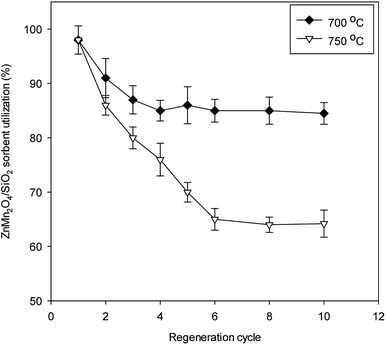 |
| Fig. 10 ZnMn2O4/SiO2 sorbent utilization as a function of multiple desulfurization/regeneration cycles at 700 °C and 750 °C. | |
The SEM and EDS images of different sorbents status are shown Fig. 11. The surface of the fresh sorbent was loose and porous. After desulfurization, compact and dense particles were observed on the surface of the reacted sorbent. The sulfur content in the reacted sorbent was estimated about 13.3%, indicating that the H2S were reacted with ZnMn2O4/SiO2 to form metal sulfides (MnS and ZnS). For the regenerated sorbent (after three desulfurization/regeneration cycles) the porous structure was partially restored, which reflected the slight decrease in BET surface. Compared with the fresh sorbent, it is clear observed that the well-crystalline structure appeared after regeneration. Furthermore, it can be found that the presence of sulfur in the regenerated sorbent and it may be attributed to the formation of metal sulfates due to incomplete regeneration reaction. According to the results of TPR the one of reasons for the loss of activity of ZnMn2O4 is the formation of metal sulfate, and an increase in the regeneration temperature is believed to overcome the problem of the formation of metal sulfate.
 |
| Fig. 11 SEM images and EDS patterns of the (a) fresh (b) reacted (c) regenerated ZnMn2O4/SiO2 sorbent. | |
4. Conclusions
A spinel structure of the ZnMn2O4 sorbent supported on SiO2 was fabricated for high temperature desulfurization. Multiple desulfurization/regeneration cycles were conducted to assess the ability of the ZnMn2O4/SiO2 sorbent. The ZnMn2O4/SiO2 sorbent utilization was retained at 70% and no Zn vaporization was observed after ten desulfurization/regeneration cycles. According to the XRD results, no major changes in the crystal phases occurred after multiple cycles. Through the EA, EDS and TPR analyses, the residual sulfur was found in the regenerated sorbent and this sulfur species is sulphate which resulted by incompleted regeneration. It is suggested that the regeneration temperature of 700 °C should be the best condition and maintains the sorbent utilization at 85% after multiple cycles.
Acknowledgements
This work was partially funded by Anxi College of Tea Science, Fujian Agriculture and Forestry University and Yung-Hsing Financial Workshop Cooperation Company.
Notes and references
- S. Cheah, D. L. Carpenter and K. A. Magrini-Bair, Energy Fuels, 2009, 23, 5291–5307 CrossRef CAS.
- N. R. Jeon, H. S. Song, M. G. Park, S. J. Kwon, H. J. Ryu and K. B. Yi, Clean technology, 2013, 19, 300–305 CrossRef.
- B. Guo, L. Chang and K. Xie, Ind. Eng. Chem. Res., 2014, 53, 8874–8880 CrossRef CAS.
- K. Svoboda, J. Leitner, J. Havlica, M. Hartman, M. Pohorely, J. Brynda, M. Syc, Y. P. Chyou and P. C. Chen, Fuel, 2017, 197, 277–289 CrossRef CAS.
- H. Xia and B. Liu, J. Hazard. Mater., 2017, 324, 281–290 CrossRef CAS PubMed.
- K. Y. Chang and E. S. Jae, Adv. Powder Technol., 2010, 21, 119–124 CrossRef.
- J. B. Gibson and D. P. Harrison, Ind. Eng. Chem. Process Des. Dev., 1980, 19, 231–237 CAS.
- M. Mureddu, I. Ferino, E. Rombi, M. G. Cutrufello, P. Deiana, A. Ardu, A. Musinu, G. Piccaluga and C. Cannas, Fuel, 2012, 102, 691–700 CrossRef CAS.
- V. Girard, D. Chiche, A. Baudot, D. Bazer-Bachi, I. Clemencon, F. Moreau and C. Geantet, Fuel, 2015, 140, 453–461 CrossRef CAS.
- R. E. Ayala and D. W. Marsh, Ind. Eng. Chem. Res., 1991, 30, 55–60 CrossRef CAS.
- T. H. Ko, Environ. Chem. Lett., 2011, 9, 77–82 CrossRef CAS.
- J. P. Wakker, A. W. Gerritsen and J. A. Moulijn, Ind. Eng. Chem. Res., 1993, 32, 139–149 CrossRef CAS.
- L. Alonso, J. M. Palacios, E. Garcia and R. Moliner, Fuel Process. Technol., 2000, 62, 31–44 CrossRef CAS.
- S. Cheah, J. L. Olstad, W. S. Jablonski and M. Bair, Energy Fuels, 2011, 25, 379–387 CrossRef CAS.
- Z. B. Huang, B. S. Liu, F. Wang and R. Amin, Appl. Surf. Sci., 2015, 353, 1–10 CrossRef CAS.
- L. F. Guo, K. L. Pan, H. M. Lee and M. B. Chang, Ind. Eng. Chem. Res., 2015, 54, 11040–11047 CrossRef CAS.
- T. H. Ko, H. Chu and Y. J. Liu, J. Hazard. Mater., 2007, 147, 334–341 CrossRef CAS PubMed.
- S. Lew, A. F. Sarofim and M. Flytzani-Stephanopoulos, Ind. Eng. Chem. Res., 1992, 31, 1890–1899 CrossRef CAS.
- J. C. Zhang, Y. H. Wang, R. Y. Ma and D. Y. Wu, Fuel Process. Technol., 2003, 84, 217–227 CrossRef CAS.
- J. C. Wang, B. Qiu, L. Han, G. Feng, Y. F. Hu, L. P. Chang and W. R. Bao, J. Hazard. Mater., 2012, 213–214, 184–192 CrossRef CAS PubMed.
- B. S. Liu, X. N. Wei, Y. P. Zhan, R. Z. Chang, F. Subhan and C. T. Au, Appl. Catal., B, 2011, 102, 27–36 CrossRef CAS.
- J. Zhang, Y. Wang and D. Wu, Energy Convers. Manage., 2003, 44, 357–367 CrossRef CAS.
- J. Wang, B. Liang and R. Parnas, Fuel, 2013, 107, 539–546 CrossRef CAS.
- R. S. Sonawance, S. G. Hegde and M. K. Dongare, Mater. Chem. Phys., 2000, 77, 744–750 CrossRef.
- C. S. Fang and Y. W. Chen, Mater. Chem. Phys., 2003, 78, 739–745 CrossRef CAS.
- W. F. Elseviers and H. Verelst, Fuel, 1999, 78, 601–612 CrossRef CAS.
- R. B. Slimane and J. Abbasian, Adv. Environ. Res., 2000, 4, 147–162 CrossRef.
- L. D. Galvin, A. T. Atimtay and R. P. Gupta, Ind. Eng. Chem. Res., 1998, 37, 4157–4166 CrossRef.
- Z. B. Huang, B. S. Liu, X. Y. Tang, X. H. Wang and R. Amin, Fuel, 2016, 177, 217–225 CrossRef CAS.
- K. Polychronopoulou, J. L. G. Fierro and A. M. Efstathiou, Appl. Catal., B, 2005, 57, 125–137 CrossRef CAS.
- M. A. Ahmed, L. Alonso, J. M. Palacios, C. Cilleruelo and J. C. Abanades, Solid State Ionics, 2000, 138, 51–62 CrossRef CAS.
- J. Wang, J. Guo, R. Parnas and B. Liang, Fuel, 2015, 154, 17–23 CrossRef CAS.
|
This journal is © The Royal Society of Chemistry 2017 |
Click here to see how this site uses Cookies. View our privacy policy here.