DOI:
10.1039/C7RA04627H
(Paper)
RSC Adv., 2017,
7, 39604-39610
The synthesis of poly(phenylene sulfide sulfone) in ionic liquids at atmospheric pressure†
Received
25th April 2017
, Accepted 12th July 2017
First published on 14th August 2017
Abstract
A novel chemical approach to prepare the high performance polymer poly(phenylene sulfide sulfone) under mild conditions was presented based on 4,4-difluorodiphenylsulfone and sodium sulfide (Na2S) in i-pmim PF6 (IL)/MImBS (ZI) at atmospheric pressure and compared with conventional methods. The highest molecular weight (2.5 × 104) and yield (>99%) polymers were synthesized in IL/ZI in the presence of sodium carbonate and sodium hydroxide at 200 °C for 4 h. ZI can significantly improve solubility of the basic inorganic salt Na2S. And using ILs as solvents made removing toluene by purging with nitrogen much easier and the time was shortened significantly from 5–8 min to 1–2 min. In addition, the ILs can be recycled easily and still possess excellent performance.
Introduction
Poly(arylene sulfide)s (PAS) are a kind of high performance polymers (HPP) containing sulfide with desirable properties such as excellent mechanical properties, high thermal stability, good resistance to chemical degradation and fire resistance under a wide range of conditions. As an important member of the PAS family, poly(phenylene sulfide sulfone) (PPSS) has received more and more attention in the past several decades (Fig. 1). PPSS is described as an amorphous polymer with a glass transition temperature (Tg = 215 °C) much higher than that of PPS (Tg = 93 °C), as well as a similar degradation temperature (Td = 490 °C).
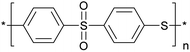 |
| Fig. 1 Structure of PPSS. | |
As thermoplastic materials, PPSS is well known for several inherently attractive characteristics such as rapid processibility, etc. The applications of PPSS span across automotive, aerospace, weaponry, nuke industry and membrane technologies, etc.1,2
PPSS can be prepared by three main synthetic pathways: self-condensation reaction of 4-(4-halophenylsulfonyl)benzenethiol (halogen = chlorine, preferably fluorine), solution polymerization of sulphur and 4,4′-dihalodiphenylsulfone, and solution polymerization of Na2S (or sodium hydrosulfide) and 4,4′-dihalodiphenyl-sulfone. Up to present, industrial PPSS was synthesized via nucleophilic aromatic substitution polycondensation (SNAR) between Na2S and 4,4′-dichlorophenylsulfone (DCDPS)/4,4′-difluorodiphenylsulfone (DFDPS). The reaction was performed in polar organic amine solvent at elevated reaction temperature (ca. 180–230 °C) and pressure in the presence of an alkali salt. Additionally, Na2S and DCDPS/DFDPS were utilized as the nucleophile and activated aromatic halide, respectively.
PPSS is generally synthesized in polar organic amine solvent and the most commonly used one is NMP.3–5 However, the high volatility of NMP limited its application of PPSS synthesis in high reaction temperature at atmospheric pressure, and the pressure reactor was needed, which made the synthetic process exhibit high energy consumption and demand special equipment.1 Therefore, novel solvent with high boiling point, high thermal stability and good solubility for the monomer and PPSS are strongly required.
Ionic liquids (ILs) are organic molten salts composing of organic cations and inorganic or organic anions. Owing to their distinctive physicochemical properties of high chemical and thermal stability, negligible volatility, ability to dissolve organic/inorganic solutes and gases, designability, low melting temperature, and low toxicity, ILs have been widely used as solvents, catalysis, monomer, additive, plasticizer, porogenic agent and so on.6,7 ILs, employed as a novel and environmentally benign solvents, instead of classical organic ones, have attracted much attentions in the fields of chemistry and industry, such as organic synthesis, polymer preparation, and composite membrane preparation and so on.8–10 So far, the traditional free radical polymerization, controlled radical polymerization, polycondensation and ionic polymerization have been carried out successfully in ILs.11–13
Polycondensation in ILs has been well investigated in the past decades. Polycondensation generally needs harsh conditions (e.g. high temperature, high vacuum, high pressure, etc.) in order to remove condensed small molecules from viscous reaction system and achieve high conversions and molecular weights. It seems to be reasonable to take ILs as reaction media in polycondensation since ILs as “green solvents” have inherently properties.
High molecular weights polyimides, polyamides, polyesters and polysulfones have been synthesized through polycondensation and aromatic nucleophilic substitution polymerization (SNAP) in conventional ILs by our and other research groups. In 2002, Vygodskii et al. firstly reported that imidazolyl-cationic ILs, which were used as solvents and catalysts, could been applied for the synthesis of high molecular weights aromatic polyimides and polyamides.14 Later, Ohno et al. reported that the polyimides (1.3 dL g−1) could been obtained by addition of zwitterionic type ILs (ZI) in 1-benzyl-3-methylimidazolium bis(trifluoromethanesulfonyl)-imide.15 Aliphatic polyesters with high molecular weights were synthesized in 1-alkyl-3-methylimidazolium ILs and the correlation between the miscibility of aliphatic polyester and ILs was also investigated.16 Poly(ethylene terephthalate) (PET) with high molecular weights was obtained at 190–240 °C in phenylalkylpyrrolidinium ILs and novel benzyl imidazolium ILs.17 High performance polymers polysulfone (PSF), poly(ether sulfone) (PES) and poly(aryl-ether-ketone) (PAEK) with high molecular weights and yields were presented by using IL/ZI as reaction media.18–20 Brønsted acidic ionic liquids (BAILs) as both solvents and catalysts and Tf2N-anionic ionic liquids as solvents were applied for polycondensation of L-lactic acid and ε-caprolactone.21
Herein we report a novel synthetic approach for PPSS with IL/ZI as reaction media by aromatic nucleophilic substitution polymerization. To the best of our knowledge, it is the first time that PPSS was prepared in ILs. Influences of various polymerization conditions, such as ILs, catalyst, reaction temperature and time was studied.
Experimental section
Materials
N-Methylimidazole (TCI, >99%) was distilled under reduced pressure. 1,4-Butanesultone (99%), n-butyl bromide (>99%), potassium hexafluorophosphate (99%), and nine hydrated sodium sulfide (Na2S·9H2O) (99%), benzyl bromide (>98%), isopropyl bromide (>99%) were purchased from Aladdin and utilized as received. N-(2-Hydroxyethyl)-2-pyrrolidone (Energy Chemical, 98%), phosphorus tribromide (Energy Chemical, 98%), N-isopropvlimdazole (Accela, >97%) were used without further purification. All alkali metal salts and ILs were dried under vacuum before used to eliminate the trace amount of water. 4,4-Difluorodiphenylsulfone (J&K, 99%), sodium hydroxide (NaOH) (AR, Tianjing 3rd chemical agent plant) and other solvents were used as received.
Characterization
The molecular weights analysis was performed using a gel permeation chromatograph (GPC) conducted on a system comprised of a Waters 515 HPLC pump, and a Waters 2414 RI detector equipped with two Agilent columns (PLgel 20 μm MIXED-A and PLgel 10 μm MIXED-B, PLgel 10 μm MIXED-B). DMF with 0.01 M LiBr was used as the eluent at a flow rate of 1.0 mL min−1 at 40 °C, and polystyrene standards were used for the calibration.
IR spectroscopic measurements were conducted on a NEXUS 670 SX FT-IR instrument at a resolution of 1 cm−1. The PPSS powder was dispersed on KBr disk and measured with the transmission FT-IR spectrum.
1H NMR spectra were recorded at ca. 20 °C on a Bruker Avance DRX-500 NMR spectrometer in DMSO-d6 solutions.
XPS analysis was performed on a Perkin-Elmer ESCSLAB 250 Xi spectrometer employing an AlKα (1361 eV) achromatic X-ray source operated at an energy resolution ≤0.5 eV, space resolution a sensitivity of the 3d5/2 photopeak intensity of silver at 2.5 Mcps. The surface area analyzed was about 3 mm2. The spectrometer was calibrated to the 1s photopeak of carbon at 284.4 eV.
Powder X-ray diffraction (XRD) patterns were recorded on a PANalytical B.V. XPERT-PROMPD diffractometer using Cu as anode Material.
Thermogravimetric Analysis (TGA) was carried out on a METTLER STRAE SW 9.30 thermogravimetric analyzer at a heating rate of 10 °C min−1 in flowing air or nitrogen. Thin film or powder samples of 3–6 mg were placed in a platinum pan connected to an electric microbalance, and weight loss of the samples was measured as a function of temperature.
Phase transition (mainly glass transitions and melting points) temperatures were recorded from the second heat of the differential scanning calorimetry (DSC) traces on a METTLER TOLEDO instrument with liquid dinitrogen cryostatic cooling (5–8 mg samples, 10 °C min−1 heating and cooling rates under a nitrogen atmosphere).
Preparation of ionic liquid
All ILs and zwitterionic type IL (ZI) used in this work were synthesized according to procedures from literature and the structures of the ILs were confirmed by 1H NMR.16
Synthesis of poly(phenylene sulfide sulfone) in mixed ionic liquids
A series of PPSSs were prepared by SNAP of DFDPS and Na2S in mixed ILs at elevated reaction temperature and atmospheric pressure. Polymerizations were conducted in a 100 mL three-necked round flask equipped with mechanical stirrer, nitrogen inlet, Dean–Stark trap and reflex condenser. A typical preparation of PPSS was described below. The flask was added 0.36 g (1.4 mmol) of DFDPS, 0.34 g (1.4 mmol) of nine hydrated sodium sulfide (Na2S·9H2O), 0.006 g (0.14 mmol) of sodium hydroxide (NaOH), 0.90 g of IL and 0.45 g of ZI. The flask was closed, purged by vacuum/nitrogen cycles using a Schlenk line. The mixture was heated to liquid state and stirred vigorously. After the solution was heated up to 140 °C, 0.16 g (1.5 mmol) of ground sodium carbonate (Na2CO3) was added. Then 5–8 mL of toluene was added and the reaction mixture was refluxed under a Dean–Stark system at 145–155 °C for 0.5 h. Inleting nitrogen to the flask removed toluene, and the reaction mixture was heated to 200 °C for 4 h. The obtained brown slurry was cooled to room temperature and mixed with a propanone–water mixture (1
:
1 w/w, 50 cm3), vigorously stirred. An insoluble material was washed with a propanone–water mixture (1
:
1 w/w, 2 × 250 cm3) and water (2 × 250 cm3), then collected by simple filtration. After drying in vacuum at 60 °C for 24 h, a gray solid product was received. The ILs fraction could be recovered by distillation of volatile solvents from the propanone–water extracts.
Results and discussion
In our work, PPSSs were synthesized by the reaction of DFDPS and Na2S via SNAP mechanism in the present of NaOH and Na2CO3 in IL/ZI. ZI, which is composed of cation and anion, has similar characteristics to general ILs except for high melting point. ZI used in this work was 1-methylimidazolium-3-butylsulfonate zwitterion (MImBS) (Scheme 1). Toluene, Na2CO3 and NaOH were used as azeotroping solvent, catalyst and additive, respectively.
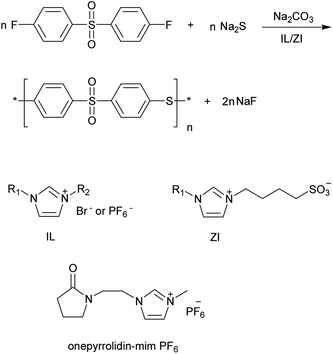 |
| Scheme 1 Synthetic route for PPSS in IL/ZI and structures of imidazolium-based IL and ZI (MImBS). | |
The identification of PPSS
In order to confirm PPSS was truly synthesized in IL/ZI system, the PPSS were identified by FT-IR, 1H NMR and XPS. The representative infrared spectra are shown in Fig. S1,† and the assignments of these absorption peaks are detailed in Table 1. As shown in Fig. S1,† the characteristic peaks at 1574, 1474 and 1392 cm−1 corresponded to stretch of ring C–C (phenyl). The absorption peaks at 3082, 817, 1074, 1321 and 1156 cm−1 ascribed to stretch of C–H (phenyl), out-of-plane bend of C–H (phenyl) at para disubstituted, C–S (phenyl), asymmetric and symmetric stretch of sulfonyl group, respectively. The band at 3414 cm−1, characteristics of water, attributed to moisture absorbed by PPSS.3 Compared with that of the monomer DFDPS, red shift of nearly all corresponding characteristic absorption peaks was observed, attributing to the formation of long conjugate π bonds. Moreover, the novel absorption peak at 1074 cm−1, belonging to phenyl–sulfide bond, indicated the formation of PPSS.
Table 1 Infrared absorption peaks and assignments of DFDPS and PPSS
Assignment |
Wavenumber (cm−1) |
DFDPS |
PPSS |
C–H stretch (phenyl) |
3104 |
3082 |
Ring C–C stretch (phenyl) |
1589 |
1574 |
1493 |
1474 |
1408 |
1392 |
C–H out-of-plane bend (phenyl)-para disubstituted |
835 |
817 |
Phenyl–sulfide bond |
— |
1074 |
Sulfonyl |
asym. |
1327 |
1321 |
sym. |
1156 |
1156 |
Fig. S2† shows the 1H NMR spectrum and its assignments of PPSS. The two main resonances at ca. 7.5 ppm (the hydrogen atoms of phenyl next to sulfide) and 7.9 ppm (the hydrogen atoms of phenyl close to sulfone) implied the symmetric disubstitution of phenyl ring. The integration of peak at ca. 7.9 ppm is more than that at ca. 7.5 ppm, which implied the sulfone moiety is more than that of sulfur in PPSS.
XPS was used to analyze the element composition of PPSS. As shown in Fig. S3,† the sulfur peak at 168.0 eV corresponded to the sulfone moiety in the polymer backbone, the other sulfur peak at 163.9 eV ascribed to the sulfide moiety.1 The shoulder of sulfone moiety is higher than the sulfur peak, which implied the sulfone moiety is more than that of sulfur, and the end groups mainly –F in PPSS. This phenomenon is consistent with that in the 1H NMR spectrum (Fig. S2†).
Accordingly, from above results, we can conclude that sulfide and sulfone of phenyl ring in PPSS was symmetric disubstituted and the end groups mainly –F.
In addition, the structure of PPSS can be further explored by XRD. X-ray pattern of PPSS is shown in Fig. S4.† The broad peak at the low scan angle of 19° shown in Fig. S4† could be ascribe to the amorphous polymer chains of PPSS.
Effect of polymerization conditions
NMP was most commonly used solvent in traditional preparation process of PPSS. When NMP was used as solvent, 5–8 min was needed to remove toluene by purging nitrogen, and there were some liquid droplets on the inner wall of Dean–Stark trap after purging nitrogen for 5 min. Besides, NMP was reduced because of its high volatility. Oppositely, in this study, little liquid droplets on the inner wall was observed by using ILs as solvent, and the time of removing toluene was shortened to 1–2 min. Simultaneously, the ILs remained unchanged owning to its negligible volatility. Therefore, removing toluene by purging nitrogen became much easier when ILs were used as solvent and the time was shortened significantly. The possible reason is that NMP is mutual solubility with toluene, but ILs are almost not (Table S1 and Fig. S5†).
1. Polymerization media. It was found from Table 2 that PPSS with high molecular weights and good yield was obtained in traditional ILs with addition of ZI (entry 1). The ILs used here were i-pmim PF6 and i-pmim Br. Due to the poor solubility of Na2S in pure i-pmim PF6, we introduced ZI into this system to improve the solubility of Na2S during the synthesis of PPSS. Consequently, good solubility of Na2S was gained when the mass ratio of IL to ZI was 2
:
1, thus no phase separation was observed in the mixture. However, with addition of overmuch ZI, melting temperature and viscosity of IL/ZI system would raise greatly, which were not desired to the synthesis of PPSS. Compared PPSS synthesized in i-pmim PF6/MImBS (Table 2, entry 1) with that prepared in i-pmim Br/MImBS (Table 2, entry 2), we can clearly know that i-pmim PF6 worked better than i-pmim Br. As indicated in entries 3 and 4, when PPSSs were synthesized in i-pmim PF6/i-pmim Br, yields were all higher than 90%, but Mw were equal or lower than 104. When PPSS was synthesized in pure i-pmim PF6, either yield (1.1%) or Mw (1 × 104) were all low (Table 2, entry 5). Yield was increased to 83.3% and Mw was 1 × 104 yet as i-pmim Br was used as solvent (Table 2, entry 6). And the highest molecular weight and good yield were achieved by synthesis of PPSS in i-pmim PF6/MImBS (Table 2, entry 1). In addition, pyrrolidine and 1,4-diazabicyclo[2.2.2]octane based ILs were also tested as solvent for the preparation of PPSS, but the molecular weights of PPSS were extremely low.
Table 2 Influence of ZI on the synthesis of PPSS
Entrya |
ILs and ZI (weight ratio) |
Mnb (104) |
Mwb (104) |
PDIb |
Yield (%) |
General polymerization conditions: equimolar of Na2S·9H2O and DFDPS, slightly excess of Na2CO3, 0.1 mole NaOH, 25.9 wt% monomer concentration, dehydrate at 145–155 °C for 0.5 h, and then polymerized at 200 °C for another 4 h. Polymers were washed by propanone–water mixture (1 : 1 w/w) and water, and then collected by simple filtration. Number-average molecular weight (Mn), weight-average molecular weight (Mw) and polydispersity index (PDI) were measured by GPC calibrated with polystyrene standards. |
1 |
i-pmim PF6/MImBS = 2/1 |
1.6 |
2.5 |
1.55 |
>99 |
2 |
i-pmim Br/MImBS = 2/1 |
0.8 |
1.1 |
1.27 |
91.9 |
3 |
i-pmim PF6/i-pmim Br = 2/1 |
0.8 |
1.0 |
1.31 |
91.3 |
4 |
i-pmim PF6/i-pmim Br = 1/2 |
0.7 |
0.9 |
1.26 |
91.2 |
5 |
i-pmim PF6 |
0.7 |
1.0 |
1.51 |
1.1 |
6 |
i-pmim Br |
0.8 |
1.0 |
1.28 |
83.3 |
Above results inferred us that imidazolium-based ILs showed some advantages during the synthesis of PPSS and ZI MImBS may play crucial dual roles of dissolvent and catalyst, leading to the high molecular weight PPSS.
To study the effect of ILs structure on the synthesis of PPSS, except for the ILs, other polymerization variables were kept constant in the whole study (Table 3). ILs, having various anions and different alkyl chain, symmetrical and asymmetrical imidazolium cations, were synthesized and studied (Scheme 1). As for the 1-isopropyl-3-methyl-imidazoliumcation, PF6− based ILs showed greater advantages over Br− based ILs according to the molecular weight of PPSS (Table 3, entries 1, 6). It is clear from Table 3, entries 1, 2 that asymmetrical imidazolium-based IL worked better than symmetric one. As the length of alkyl groups in imidazolium was increased from propyl to butyl, molecular weight and yield were all decreased (Table 3, entries 1, 3). It is speculated that this is related to the interaction of ILs and the monomer. The molecular weights were all lower than 104 when PPSS were prepared in benzyl imidazolium ILs or pyrrolidone imidazolium ILs (Table 3, entries 4, 5). The highest molecular weight (2.5 × 104) was gained in i-pmim PF6/ZI at yield as high as >99% (Table 3, entry 1). Accordingly, imidazolium-based ILs with short alkyl chain was more desired to synthesis of high molecular weight PPSS. i-pmim PF6 will be used during the following studies.
Table 3 Influence of ILs on the synthesis of PPSS
Entrya |
IL |
Mnb (104) |
Mwb (104) |
PDIb |
Yield (%) |
General polymerization conditions: equimolar of Na2S·9H2O and DFDPS, slightly excess of Na2CO3, 0.1 mole NaOH, 25.9 wt% monomer concentration, IL : ZI = 2 : 1 by weight, dehydrate at 145–155 °C for 0.5 h, and then polymerized at 200 °C for another 4 h. Polymers were washed by propanone–water mixture (1 : 1 w/w) and water, and then collected by simple filtration. Number-average molecular weight (Mn), weight-average molecular weight (Mw) and polydispersity index (PDI) were measured by GPC calibrated with polystyrene standards. |
1 |
i-pmim PF6 |
1.6 |
2.5 |
1.55 |
>99 |
2 |
d-ipmim PF6 |
1.0 |
1.3 |
1.27 |
30.1 |
3 |
bmim PF6 |
0.9 |
1.1 |
1.25 |
54.3 |
4 |
Onepyrrolidin-mim PF6 |
0.7 |
0.9 |
1.27 |
54.4 |
5 |
Benzyl-mim PF6 |
0.5 |
0.6 |
1.14 |
35.4 |
6 |
i-pmim Br |
0.8 |
1.1 |
1.27 |
91.9 |
2. Catalyst. It was reported that PPSSs with high molecular weights were obtained in the presence of alkali metal carboxylate.1 Herein we selected several carboxylates and carbonates as catalysts and investigated its influence on the synthesis of PPSS in i-pmim PF6/MImBS. The molecular weights and yield of PPSSs obtained using different catalysts are listed in Table 4. It is apparent from Table 4 that Na2CO3 worked best among all of the carboxylates and carbonates we chose, and both highest molecular weight and yield were obtained. Consequently, Na2CO3 was selected as catalyst in this study.
Table 4 Influence of catalyst on the synthesis of PPSS
Entrya |
Catalyst |
Mnb (104) |
Mwb (104) |
PDIb |
Yield (%) |
General polymerisation conditions: equimolar of Na2S·9H2O and DFDPS, slightly excess of catalyst, 0.1 mole NaOH, 25.9 wt% monomer concentration, IL : ZI = 2 : 1 by weight, dehydrate at 145–155 °C for 0.5 h, and then polymerized at 200 °C for another 4 h. Polymers were washed by propanone–water mixture (1 : 1 w/w) and water, and then collected by simple filtration. Number-average molecular weight (Mn), weight-average molecular weight (Mw) and polydispersity index (PDI) were measured by GPC calibrated with polystyrene standards. |
1 |
Na2CO3 |
1.6 |
2.5 |
1.55 |
>99 |
2 |
K2CO3 |
0.8 |
1.1 |
1.35 |
68.5 |
3 |
CH3COONa |
0.9 |
1.1 |
1.29 |
61.4 |
4 |
CH3COOK |
1.2 |
1.6 |
1.37 |
78.7 |
5 |
C6H5COOK |
1.2 |
1.6 |
1.38 |
93.2 |
3. Additive. We also investigated the effect of NaOH on the synthesis of PPSS. Table 5 shows that NaOH play a vital role for the high molecular weights PPSS. The maximum molecular weight was obtained when the molar ratio of NaOH/Na2S was 1/10 (Table 5, entry 1). In contrast, when excess NaOH was added, that is, molar ratio of NaOH/Na2S was increased to 2/10, PPSS with lower degree of polymerization was gained (Table 5, entry 3). This inferred that excess NaOH would interfere with the synthesis of PPSS. However, molecular weight was not high yet while no NaOH was used during the preparation of PPSS (Table 5, entry 2). The possible reasons are as follows. Because of the strong basic group and the weak acidic group of Na2S, it is unstable and decomposes very easily. When appropriate amount of NaOH was added, it could regulate acidity and alkalinity of the polymerization system, so that Na2S became more stable and could work as monomer to participate in the synthesis of PPSS. However, excess NaOH resulted in the degradation of PPSS attributing to the chemical attack of the sulfur–carbon bonds in the polymer chain by excessive OH− at elevated temperature.1 From Table 5, entry 4, one can see that molecular weights decreased to lower than 104 as only NaOH was added but no Na2CO3 was used.
Table 5 Influence of NaOH on the synthesis of PPSS
Entrya |
NaOH/Na2CO3/Na2S |
Mnb (104) |
Mwb (104) |
PDIb |
Yield (%) |
General polymerization conditions: equimolar of Na2S·9H2O and DFDPS, slightly excess of Na2CO3, 25.9 wt% monomer concentration, IL : ZI = 2 : 1 by weight, dehydrate at 145–155 °C for 0.5 h, and then polymerized at 200 °C for another 4 h. Polymers were washed by propanone–water mixture (1 : 1 w/w) and water, and then collected by simple filtration. Number-average molecular weight (Mn), weight-average molecular weight (Mw) and polydispersity index (PDI) were measured by GPC calibrated with polystyrene standards. |
1 |
1/10/10 |
1.6 |
2.5 |
1.55 |
>99 |
2 |
0/10/10 |
1.1 |
1.4 |
1.32 |
91.4 |
3 |
2/10/10 |
0.5 |
0.6 |
1.19 |
61.9 |
4 |
1/0/10 |
0.6 |
0.8 |
1.31 |
82.5 |
Above results shown in Tables 4 and 5 implied that both Na2CO3 contributing to the high molecular weights and NaOH contributing to the stability of Na2S were indispensable and irreplaceable during the preparation of PPSS.
4. Polymerization temperature. In order to search optimum polymerization conditions, the influence of polymerization temperature on the preparation of PPSS was examined in i-pmim PF6/MImBS. Except for polymerization temperature varied from 160 to 210 °C, other polymerization variables were kept constants in the whole study including the weight percentage of DFDPS of 25.9 wt%, molar ratio of Na2S·9H2O/DFDPS of 1/1, molar ratio of Na2S·9H2O/NaOH/Na2CO3 of 1/0.1/1, and polymerization time of 4 h at atmospheric pressure. Mn and Mw of PPSS are plotted in Fig. 2 as function of polymerization temperature. As shown in Fig. 2, with the increase of polymerization temperature from 160 °C to 200 °C, the molecular weights increase gradually and the color of PPSS became dark. The highest molecular weights was obtained at 200 °C. However, when we continued to raise the polymerization temperature, the molecular weights decrease. This may attribute to the degradation of PPSS under basic environment at high temperature.
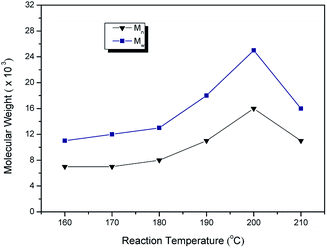 |
| Fig. 2 Variation of Mn and Mw of PPSS versus polymerization temperature in i-pmim PF6/MImBS (25.9 wt% of DFDPS, molar ratio of Na2S·9H2O/DFDPS of 1/1, molar ratio of Na2S·9H2O/NaOH/Na2CO3 of 1/0.1/1, reaction time of 4 h at atmospheric pressure). | |
5. Polymerization time. The influence of polymerization time on the preparation of PPSS was also examined by varying the polymerization time from 0.5 h to 6 h in i-pmim PF6/MImBS. The temporal evolution of molecular weights is shown in Fig. 3. As indicated in Fig. 3, with increasing polymerization time from 0.5 h to 4 h, the molecular weights of PPSS became larger and larger. And the highest molecular weight was acquired as the polymerization time was 4 h. Contrastly, when we continued to prolong the polymerization time, the molecular weights of PPSS no longer increased but decreased. It is speculated that overlong polymerization time may result in the decomposition of PPSS and side reactions so that the molecular weights decreased continuously from 4 h to 6 h.
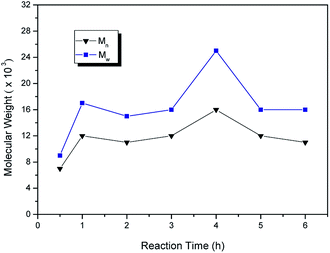 |
| Fig. 3 The temporal evolution of Mn and Mw of PPSS in i-pmim PF6/MimBS (25.9% weight percentage of DFDPS, molar ratio of Na2S·9H2O/DFDPS of 1/1, molar ratio of Na2S·9H2O/NaOH/Na2CO3 of 1/0.1/1, polymerization temperature of 200 °C at atmospheric pressure). | |
From above study, the optimum polymerization condition for synthesis of PPSS was achieved in i-pmim PF6/MImBS (25.9 wt% monomer concentration, ratio of i-pmim PF6/MImBS (weight), Na2S·9H2O/DFDPS (molar) and Na2S·9H2O/NaOH/Na2CO3 (molar) was 2
:
1, 1/1, and 1/0.1/1, respectively, polymerized at 200 °C and atmospheric pressure for 4 h).
Thermal properties of PPSS
TGA and DSC have proved to be suitable methods to investigate the thermal property of polymeric systems. The threshold decomposition temperature in TGA gives an indication of the highest processing temperature that can be used. Fig. 4 depicts TGA curves of PPSS in nitrogen and air, respectively. PPSS showed two-step weight loss progress in air: between 350 and 520 °C, and above 520 °C. The process at 350–520 °C is attributed to the degradation of sulfone moiety in the polymer backbone. The second degradation above 520 °C is ascribed to the decomposition of sulfide moiety. The temperature of 5% weight loss of PPSS was over 400 °C in nitrogen, and the char yield values at 700 °C was 8.1% in air and 48.4% in nitrogen, respectively. The glass transition temperature (Tg) of PPSS were measured by DSC and showed up to 206 °C, as illustrated in Fig. 5.22,23
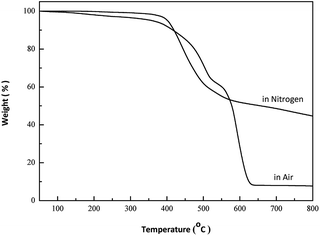 |
| Fig. 4 TGA of PPSS at the heating rate of 10 °C min−1. | |
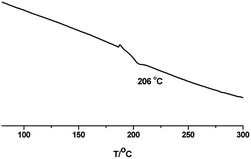 |
| Fig. 5 DSC trace of PPSS. | |
Recycle and reuse of ionic liquid
The main advantage of ILs over conventional organic solvents as solvent is facile to recycle and reuse after polymerization, which is absolutely very intriguing from the viewpoint of environmental conservation and economic benefits. In our study, the solid product was precipitated into propanone under mechanical stirrer, and the PPSS and IL i-pmim PF6 were separated by filtration. After that, the residual i-pmim PF6 in the filtrate and propanone were recycled by vacuum evaporation. And white solid was obtained ultimately and no oligomer residue was observed in them. FTIR spectra of i-pmim PF6 before and after use in polymerization were performed (Fig. S6†). The characteristic peak at 840 cm−1 was assigned to the P–F bond of PF6−. The absorption peaks at 3093 and 1322 cm−1 ascribed to stretch of C–H (phenyl) and asymmetric stretch of sulfonyl group of DFDPS. The absorption peak at 1062 cm−1 belonged to sulfide. These indicated that IL i-pmim PF6 underwent virtually no decomposition throughout the polymerization. The recycled i-pmim PF6 was also analyzed by 1H NMR (Fig. S7†). Fig. S6† indicated that no obvious change of the chemical shifts of i-pmim PF6 and little remaining monomer was observed after synthesis of PPSS. To confirm the validity of recycled ILs, SNRP between DFDPS and Na2S was performed in recycled ILs. Although the molecular weight of PPSS prepared in recycled IL was slightly lower (Mw = 15
000), it still illustrated that the recycled ILs could be applicable in new polymerization cycle, even after more several cycles.
Conclusions
In this work, a series of PPSSs were prepared successfully via SNAP based on Na2S and DFDPS in IL/ZI at atmospheric pressure, which was different from other studies conducted at high pressure. The highest molecular weight (2.5 × 104) and yield (>99%) PPSS were synthesized in i-pmim PF6 (IL)/MImBS (ZI) in the presence of Na2CO3 and NaOH at 200 °C for 4 h. The structure of PPSS was confirmed by FT-IR, 1H NMR, XPS and XRD.
The influence factors of the polymerization, such as catalyst, additive, polymerization media, polymerization temperature and polymerization time were all investigated. And it showed that optimum polymerization conditions for synthesis of PPSS was relatively mild in i-pmim PF6 and MImBS (weight ratio of IL to ZI was 2
:
1, monomer concentration was 25.9 wt%, the polymerization temperature was 200 °C and the polymerization time was 4 h). ZI can significantly improve the solubility of basic inorganic salt Na2S, thus PPSS with high molecular weights and good yield was obtained. Appropriate amount of NaOH contributed to synthesis of PPSS but excess interfered. Using ILs as solvent made remove toluene by purging nitrogen much easier and the time was shortened obviously from 5–8 min to 1–2 min. For ILs with different coupling of cation and anion, imidazolium-based ILs with short alkyl chain was favorable to synthesis of high molecular weights PPSS. ILs was facile to recycle and reuse after polymerization and it also had excellent recyclability in this polymerization system.
It is possible to improve the degrees of polymerization by further designing of the cation and anion of the ILs, and thus deserves further research.
Acknowledgements
This work was financially supported by the National Natural Science Foundation of China (No. 21274014), the Fundamental Research Funds for the Central Universities, Program for Changjiang Scholars and Innovative Research Team in University, and Measuring Fund of Large Apparatus of Beijing Normal University.
Notes and references
- Y. Liu, A. Bhatnagar, Q. Ji, J. S. Riffle, J. E. McGrath, J. F. Geibel and T. Kashiwagi, Polymer, 2000, 41, 5137–5146 CrossRef CAS
. - L. Liu, X. Wang, Y. Wang, L. Li, K. Pan, J. Yang and B. Cao, Mater. Lett., 2014, 132, 11–14 CrossRef CAS
. - J. Yang, H.-D. Wang, S.-X. Xu, G.-X. Li and Y.-J. Huang, J. Polym. Res., 2005, 12, 317–323 CrossRef CAS
. - R. W. Capbell, US Pat. 4, 016, 145, 1977
. - R. W. Capbell, US Pat. 4, 125, 525, 1978
. - C. C. Weber, A. F. Masters and T. Maschmeyer, Green Chem., 2013, 15, 2655–2679 RSC
. - J. Lu, F. Yan and J. Texter, Prog. Polym. Sci., 2009, 34, 431–448 CrossRef CAS
. - D. S. Lakshmi, T. Cundari, E. Furia, A. Tagarelli, G. Fiorani, M. Carraro and A. Figoli, Macromol. Symp., 2015, 357, 159–167 CrossRef CAS
. - Z. Yi, C.-J. Liu, L.-P. Zhu and Y.-Y. Xu, Langmuir, 2015, 31, 7970–7979 CrossRef CAS PubMed
. - E. Coletta, M. F. Toney and C. W. Frank, Polymer, 2014, 55, 6883–6895 CrossRef CAS
. - C. Zhang, L. Liao and S. Gong, Green Chem., 2007, 9, 303–314 RSC
. - J.-S. Wang and K. Matyjaszewski, J. Am. Chem. Soc., 1995, 117, 5614–5615 CrossRef CAS
. - T. Biedroń, M. Bednarek and P. Kubisa, Macromol. Rapid Commun., 2004, 25, 878–881 CrossRef
. - Y. S. Vygodskii, E. I. Lozinskaya and A. S. Shaplov, Macromol. Rapid Commun., 2002, 23, 676–680 CrossRef CAS
. - M. Tamada, T. Hayashi and H. Ohno, Tetrahedron Lett., 2007, 48, 1553–1557 CrossRef CAS
. - C. Fu and Z. Liu, Polymer, 2008, 49, 461–466 CrossRef CAS
. - J. Dou and Z. Liu, Green Chem., 2012, 14, 2305–2313 RSC
. - J. Wang and Z. Liu, Green Chem., 2012, 14, 3204–3210 RSC
. - J. Wang and Z. Liu, Chin. Sci. Bull., 2013, 58, 1262–1266 CrossRef CAS
. - J. Wang, Y. Wu and Z.-p. Liu, Chin. J. Polym. Sci., 2016, 34, 981–990 CrossRef CAS
. - Q. Peng, K. Mahmood, Y. Wu, L. Wang, Y. Liang, J. Shen and Z. Liu, Green Chem., 2014, 16, 2234–2241 RSC
. - H. Wang, J. Yang, S. Long, X. Wang, Z. Yang and G. Li, Polym. Degrad. Stab., 2004, 83, 229–235 CrossRef CAS
. - A. P. Gies, S. T. Ellison, J. F. Geibel and D. M. Hercules, Macromolecules, 2011, 44, 5093–5104 CrossRef CAS
.
Footnote |
† Electronic supplementary information (ESI) available. See DOI: 10.1039/c7ra04627h |
|
This journal is © The Royal Society of Chemistry 2017 |
Click here to see how this site uses Cookies. View our privacy policy here.