DOI:
10.1039/C7RA04454B
(Paper)
RSC Adv., 2017,
7, 29779-29785
Blocked isocyanate silane modified Al2O3/polyamide 6 thermally conductive and electrical insulation composites with outstanding mechanical properties
Received
20th April 2017
, Accepted 1st June 2017
First published on 7th June 2017
Abstract
The surface of alumina (Al2O3) particles was modified by a blocked isocyanate silane coupling agent, which was synthesized by using methylethyl ketoxime (MEKO) to block isocyanate-propyltriethoxy silane via nucleophilic reactions. For comparison, the surface of Al2O3 particles was also modified by propyltrimethoxy silane (KH-331). The thermally conductive and electrical insulating Al2O3/polyamide 6 composites were prepared by dispersing modified Al2O3 in polyamide 6 (PA6) using a twin-screw extruder. The X-ray photoelectron spectroscopy (XPS) results revealed that blocked isocyanate-propyltriethoxy silane and KH-331 were successfully attached to the surface of Al2O3 particles with chemical bonds. The blocked isocyanate silane modified Al2O3 were well dispersed in PA6 as revealed by scanning electron microscopy (SEM). When the Al2O3 content was 70 wt%, the tensile strength (85.2 MPa) and flexural strength (136.4 MPa) of blocked isocyanate silane modified Al2O3/PA6 composites were higher than those of KH-331 modified Al2O3/PA6 composites (52.5 MPa, 77.8 MPa), respectively. The thermal conductivity and impact strength of blocked isocyanate silane modified Al2O3/PA6 composites were also higher than that of KH-331 modified Al2O3/PA6 composites at the same content of Al2O3. The volume electrical resistivity of modified Al2O3/PA6 composites decreased with increasing Al2O3 content, but they still were good electrical insulating materials.
1. Introduction
The demands of materials, which are thermally conductive but electrically insulating, increase rapidly in electronic and electric products. Conventional polymers have the advantages of electrical insulation and easy processing, but have the drawback of being thermally insulating.1 Various high thermally conductive and electrically insulating fillers, such as Al2O3,2 BN,3 AlN,4 Si3N4 (ref. 5) and SiC,6 have been widely used to improve the thermal conductivity of polymer matrices.
To get polymer/filler composites with high thermal conductivity and electrical resistivity, especially with a thermal conductivity higher than 1.0 W (m−1 K−1), a large amount of fillers must be added to the polymer matrix.7 However, composites with such a high loading of fillers usually possess low mechanical properties, because the surface of most thermally conductive fillers possess many polar hydroxyl groups and a high surface energy, and the fillers tend to aggregate and have weak interfacial bonding with the polymer matrix. The surface modification of fillers can improve the dispersion of fillers in polymer matrices and enhance the interfacial interactions between the fillers and polymer. Konnola et al.8 grafted carboxyl terminated poly(acrylonitrile-co-butadiene) on to graphite oxide, and the modified graphite oxide excellently dispersed in epoxy matrix, resulting in an effective sheet/matrix interfacial bonding. Sandomierski et al.9 modified silica-based fillers with in situ generated 4-hydroxymethylbenzenediazonium salt, the surface-functionalized fillers could react with phenolic resins, and the flexural strength of diazonium-modified silica/phenolic resin composites was found to be up to 35% higher than that of the composites prepared without any diazonium salts. Gardebjer et al.10 chemically modified the surface of cellulose nanocrystals (CNC) with polylactic acid, and they found that grafted PLA chains on average comprised two lactic acid units attached to 48% of all available hydroxyl groups on the surface of the CNC. Compared to unmodified CNC, the modified CNC showed less aggregation in organic solvents and hydrophobic polymer materials. The increased interaction was observed between the polymer and fillers after surface modification.
PA6, which owns good mechanical properties, heat resistance and electrical insulation, and also easy processing performance, is suitable for using as thermally conductive composites matrix. Jia et al.11 found that graphite and Sn have a significant synergistic effect on the thermal conductivity improvement of PA6. Li et al.12 prepared PA6 composites by in situ thermal polycondensation of ε-caprolactam in the existing of 3D graphene foam, the thermal conductivity was improved by 300% to 0.847 W (m−1 K−1) of PA6 composites at 2.0 wt% graphene loading from 0.210 W (m−1 K−1) of pure PA6 matrix. The loading of graphite or graphene can improve the thermal conductivity but drastically decrease electrical insulation of PA6 composites. Sato et al.13 made 3-aminopropyltriethoxysilane treated alumina and water-dispersible polycarbodiimide grafted alumina, and they found the organic substance layer with ordered structure decreased scattering for phonon transfer between alumina fillers and PA6 matrices. The mechanical properties of composites were not mentioned. Li et al.14 used carbon and glass fibers to reinforce the mechanical properties of Mg(OH)2, Al2O3, and flake graphite-filled PA6 composites, the mechanical properties and thermal conductivity of carbon fibers reinforced composites were better than that of glass fibers reinforced composites, while carbon fibers decreased the electrical insulation of composites. Hu et al.15 melt blended 3-aminopropyltriethoxysilane modified tetrapod-shaped zinc oxide whisker (T-ZnOw) with nylon 11, they found the tensile strength increased with the initial loading of T-ZnOw, but decreased when the loading of T-ZnOw higher than 15 phr.
The purpose of this work is to prepare PA6 based composites which have not only good heat dissipation and electrical insulation but also excellent mechanical properties. First, thermal conductive but electrical insulation filler of Al2O3 particles were surface modified by a blocked isocyanate silane. Then, PA6 based composites were obtained by melt-blending of surface modified Al2O3 and PA6. During melt-blending process, the blocked isocyanate groups on Al2O3 surface deblocked to regenerate isocyanate groups, which could react in situ with the terminal amino groups and/or carboxyl groups of PA6 chain. The molecular weight of PA6 was increased and the interface compatibility of Al2O3 particles and PA6 matrix was enhanced. As a result, the mechanical property and thermal conductivity of composites were improved simultaneously.
2. Experimental
2.1 Materials
Commercially available PA6 (YH800) was supplied by Hunan YueHua Chemical Co., Ltd. (China). Al2O3 powders were obtained from Fsvictor Chemical Material Co., Ltd. (China) with average particle sizes of 4–6 μm. Isocyanate-propyltriethoxy silane, propyltrimethoxy silane (KH-331), methylethyl ketoxime (MEKO), toluene, ethanol were purchased from Aladdin Industrial Corporation (China). All reagents were laboratory grade chemicals and were used as received without any further purification except toluene must be purified by removing the moisture before using. In a 250 mL round-bottom flask, 160 mL toluene, 1 g sodium, and 0.1 g benzophenone were introduced. The mixture was refluxed at 120 °C until the solution color changed to dark blue. Then the solution was heated to 130 °C and the toluene in the flask was distilled, sealed and stored for using.
2.2 Synthesis of MEKO blocked isocyanate-propyltriethoxy silane
Isocyanate-propyltriethoxy silane was dissolved by anhydrous toluene in a 4-neck glass reactor equipped with a condenser, a constant pressure dropping funnel, a N2 inlet and a stirrer. The calculated amount of MEKO diluted with anhydrous toluene was added into the reactor dropwisely under stirring with the OH/NCO molar ratio of 1.2
:
1 in 0.5 h at room temperature. The reaction mixture was kept for an additional 0.5 h at ambient temperature, subsequently heated to 80 °C and stirred continuously for 4 h in an oil bath under nitrogen atmosphere. After the completion of the reaction, the reaction mixture was allowed to cool down to room temperature. The final liquid product was obtained after toluene and excess MEKO were removed by rotary evaporators at 70 °C under vacuum.
2.3 Surface modification of Al2O3 particles
The blocked isocyanate silane (0.5 wt% based on the weight of Al2O3 particles), water (the molar ratio of water/blocked isocyanate silane was 3
:
1), and ethanol (the weight is the same as blocked isocyanate silane) were added to a glass vessel, acetic acid (hydrolysis catalyst) was added to regulate the pH value to 3.5–5.5, then the mixture was maintained at 30 °C for 0.5 h in order to hydrolyze blocked isocyanate silane. On the other hand, the Al2O3 powders were added to a SHR-10C high-speed mixer (Jiangsu Zhangjiagang Beier Machinery Co., Ltd. China). When the temperature of Al2O3 powders arrived at 100 °C, the hydrolyzed blocked isocyanate silane solution was injected homogeneously to high-speed mixer and stirred for 15 min. The modified Al2O3 powders were dried in a vacuum oven at 80 °C for 8 h to eliminate the solvent. Similar process was employed to prepare KH-331 modified Al2O3 powders.
2.4 Preparation of modified Al2O3/PA6 composites
Before blending, PA6 was dried at 80 °C in vacuum oven for 5 h to remove the moisture. PA6 and modified Al2O3 powders were mixed in above high-speed mixer at 1550 rpm for 10 min. After mixing, modified Al2O3/PA6 composites were manufactured by a SJSH-30 twin-screw extruder (Nanjing Rubber & Plastic Machinery Plant Co., Ltd. China) at screw speed of 79 rpm, feeding speed of 17.9 rpm and melt temperature at 235–250 °C. The granule modified Al2O3/PA6 composites were dried at 80 °C for 5 h and injection molded to obtain specimens with standard shapes by a HTL90-F5B injection molding machine (Ningbo Haitai Machinery Manufacture Co., Ltd. China).
2.5 Characterization
Fourier transform infrared spectroscopy (FTIR). To characterize completion of the blocking reaction, isocyanate-propyltriethoxy silane and blocked isocyanate silane were coated on KBr chip and analyzed by FTIR (Nicolet 67, Thermo Nicolet, USA), respectively. The scans were performed in the frequency range from 400 to 4000 cm−1.
Differential scanning calorimetry analysis (DSC). The deblocking temperature of the blocked isocyanate silane was tested by DSC (Q2000, TA, USA). The samples was heated from room temperature to 250 °C at a heating rate of 5 °C min−1 under a nitrogen atmosphere. To test the crystallization and melt temperatures of PA6 and composites, sample (typically 8 mg) was heated at a rate of 50 °C min−1 to 270 °C and maintained isothermal conditions for 3 min to eliminate any residual crystals, then the resulting melt was cooled at 10 °C min−1 to room temperature and heated at 10 °C min−1 to 270 °C under a nitrogen atmosphere.
X-ray photoelectron spectroscopy (XPS). XPS (ESCALAB250, Thermo, USA) was employed to analyze the interaction between coupling agent and Al2O3 particles. Prior to test, modified Al2O3 powders samples were packed with filter paper, and extracted by Soxhlet extraction apparatus for 48 h with acetone as extraction solvent.
Scanning electron microscopy (SEM). SEM (JSM-6490LV, JEOL Ltd., Japan) was used to observe the dispersion of modified Al2O3 particles in the PA6 matrix. The cross-section of impact samples were coated with gold prior to fractographic examination.
Mechanical properties testing. Electronic universal testing machine (CMT4304, Shenzhen Sans, China) and pendulum impact testing machine (ZBC1400-1, Shenzhen Sans, China) were carried out to investigate the mechanical properties of modified Al2O3/PA6 composites. The tensile strength was measured according to ISO 527-2:1993 at a cross-head rate of 50 mm min−1. Bending testing were performed in accordance with ISO 178:2001 at a bending rate of 2 mm min−1 and the deflection of 7 mm. The impact strength was measured according to ISO 179-1:2000, the notch depth of samples was 2 mm and pendulum energy used was 2.75 J. The values reported were the averages from five specimens each.
Thermal conductivity testing. The thermal conductivity (in units of W m−1 K−1) of composites at room temperature were measured according to ISO 22007-2.2 using Thermal analyzer (TPS 2500S, Hot Disk, Sweden), which is based on the Transient Plane Source Method. The double helix probe of 4 mm diameter was placed between two lamellar samples of 2 mm thickness, flat on both sides.
Electrical resistivity measurements. The measurements were conducted on a digital high resistance test fixture PC68 (Shanghai Precision Instrument Manufacture, China) using an injection-molded plate with a diameter of 60.0 mm and a thickness of 1.0 mm.
3. Results and discussion
3.1 Blocking and deblocking of isocyanate-propyltriethoxy silane
The FT-IR spectra of isocyanate-propyltriethoxy silane and MEKO blocked isocyanate-propyltriethoxy silane were shown in Fig. 1. The absorption at around 2270 cm−1, which was attributed to the antisymmetric stretching vibration of the –N
C
O groups, was found in isocyanate-propyltriethoxy silane sample (Fig. 1(a)), but not appeared in MEKO blocked isocyanate-propyltriethoxy silane sample (Fig. 1(b)). This result indicated that the –N
C
O groups of isocyanate-propyltriethoxy silane were completely blocked by MEKO. Absorptions at 3350 cm−1 (N–H stretching vibration), 1510 cm−1 (N–H bending vibration) and 1730 cm−1 (the stretching vibration of the C
O group of urea combined with the N–H group)16 confirmed that the –N
C
O groups of isocyanate-propyltriethoxy silane and the hydroxyl groups of MEKO had reacted to generate –NHCO– groups. The band at 1080 cm−1 was corresponded to stretching vibrations of Si–O bonds.
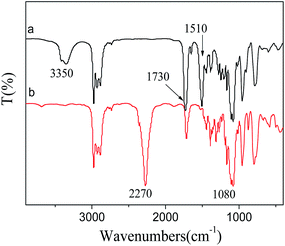 |
| Fig. 1 FT-IR spectra of the samples (a) isocyanate-propyltriethoxy silane, (b) MEKO blocked isocyanate-propyltriethoxy silane. | |
The blocking and deblocking reaction of MEKO and isocyanate-propyltriethoxy silane could be described as Scheme 1.
 |
| Scheme 1 Blocking and deblocking reaction of MEKO and isocyanate-propyltriethoxy silane. | |
The deblocking temperature of MEKO blocked isocyanate-propyltriethoxy silane was tested by DSC method, and the result was presented in Fig. 2. There was a sharp endothermic peak in the temperature from 177 to 200 °C, which corresponded to the deblocking temperature of blocked isocyanate silane.
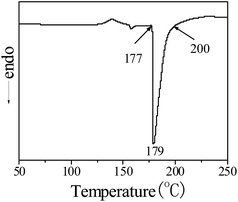 |
| Fig. 2 DSC curve of MEKO blocked isocyanate-propyltriethoxy silane. | |
3.2 The interaction of modified Al2O3 particles and PA6
The MEKO blocked isocyanate-propyltriethoxy silane and KH-331 (for comparing) modified Al2O3 particles were Soxhlet extracted for 48 h to remove free coupling agents and any physically bonded coupling. The modified Al2O3 particles were characterized by XPS analysis, and the results were shown in Fig. 3. Two strong peaks emerged at about 531.25 eV and 74.31 eV, which attributed to the binding energies of O 1s and Al 2p, respectively. Two additional peaks appeared at 285 eV and 101.68 eV which corresponded to the binding energies of C 1s and Si 2p, respectively. In Fig. 3(a), the binding energy of N 1s was appeared at 399 eV. All these results confirmed that MEKO blocked isocyanate-propyltriethoxy silane and KH-331 was successfully attached to the surface of Al2O3 particles with a chemical bond.
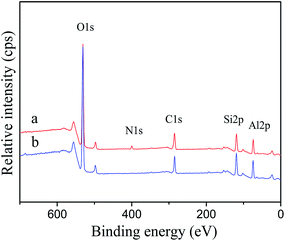 |
| Fig. 3 XPS spectra of modified Al2O3 (a) by MEKO blocked isocyanate-propyltriethoxy silane, (b) by KH-331. | |
The SEM images of MEKO blocked isocyanate-propyltriethoxy silane and KH-331 modified Al2O3/PA6 composites filled with 40 wt% Al2O3 were shown in Fig. 4(a) and (b), respectively. It could be seen that MEKO blocked isocyanate-propyltriethoxy silane modified Al2O3 particles dispersed well than that of KH-331 modified Al2O3. It was known from Fig. 2 that the deblocking temperature of MEKO blocked isocyanate-propyltriethoxy silane was in the temperature range from 177 to 200 °C. The isocyanate groups kept in blocked state in the process of the surface modification of Al2O3. However, at the melt extrusion temperature of Al2O3/PA6 composites (235–250 °C), the blocked isocyanate groups attached to the surface of Al2O3 particles deblocked to regenerate isocyanate groups, which could react in situ with the terminal amino groups and/or carboxyl groups of PA6 chain. As a result, interfacial adhesion between Al2O3 particles and PA6 matrix was improved and the PA6 chains were extended by MEKO blocked isocyanate-propyltriethoxy silane modified Al2O3 particles.
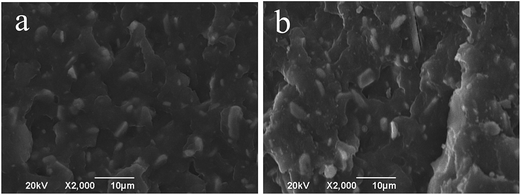 |
| Fig. 4 SEM images of modified Al2O3/PA6 composites (a) modified by MEKO blocked isocyanate-propyltriethoxy silane, (b) modified by KH-331. | |
3.3 DSC analysis
The crystallization and melt behavior of PA6 and composites were evaluated by DSC, and the results were shown in Fig. 5. The effect of pristine and modified Al2O3 on crystallization and melt temperature on PA6 matrix was almost the same (Fig. 5(b)–(d)). The crystallization temperature of Al2O3/PA6 composites (191–192 °C) was considerably higher than that of pure PA6 (173 °C) (Fig. 5 left), indicating that Al2O3 particles had nucleation effect on PA6 matrix. The melt behavior of Al2O3/PA6 composites was very different from that of pure PA6 (Fig. 5 right). The lower temperature endotherm (around 213 °C) of Al2O3/PA6 composites attributed to the γ-phase crystallites present in the samples,17 indicating that Al2O3 particles promoted part of PA6 formatting γ-phase crystallites.
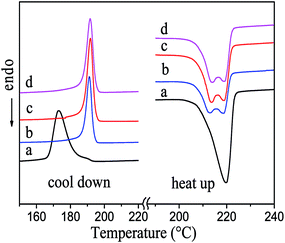 |
| Fig. 5 DSC curve of materials (a) PA6. Composites (40 wt% Al2O3): (b) pristine Al2O3, (c) Al2O3 modified by KH-331, (d) Al2O3 modified by MEKO blocked isocyanate-propyltriethoxy silane. | |
3.4 Mechanical properties
The tensile strength of modified Al2O3/PA6 composites with different content of Al2O3 was shown in Fig. 6. The tensile strength of KH-331 modified Al2O3/PA6 composites (Fig. 6(a)) increased first and then decreased with the increasing of Al2O3 content, while the tensile strength of MEKO blocked isocyanate-propyltriethoxy silane modified Al2O3/PA6 composites (Fig. 6(b)) increased steadily with the increasing of Al2O3 content. When the content of Al2O3 was higher than 50 wt%, the tensile strength of KH-331 modified Al2O3/PA6 composites decreased sharply, but the tensile strength of MEKO blocked isocyanate-propyltriethoxy silane modified Al2O3/PA6 composites increased rapidly. When the content of Al2O3 increased to 70 wt%, the tensile strength of MEKO blocked isocyanate-propyltriethoxy silane modified Al2O3/PA6 composites reached 85.2 MPa, which was considerably higher than that of neat PA6. The reasonable explain might be that MEKO blocked isocyanate-propyltriethoxy silane modified Al2O3 played a role of chain extender, so with the increasing of Al2O3 content, the active points participated in the extender chain reaction increased, which contributed to increase the molecular weight of PA6 and enhance the interface compatibility of Al2O3 particles and PA6 matrix. Meanwhile, the dispersion of Al2O3 particles in PA6 matrix was also improved.
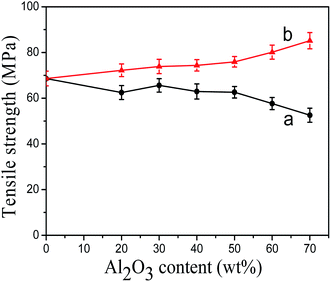 |
| Fig. 6 The tensile strength of modified Al2O3/PA6 composites (a) by KH-331, (b) by MEKO blocked isocyanate-propyltriethoxy silane. | |
Fig. 7 showed the flexural strength of modified Al2O3/PA6 composites filled with different content of Al2O3. The flexural strength of KH-331 modified Al2O3/PA6 composites (Fig. 7(a)) increased first and then decreased with the increasing of Al2O3 content. It was observed that the tendency of the flexural strength of MEKO blocked isocyanate-propyltriethoxy silane modified Al2O3/PA6 composites (Fig. 7(b)) was the same as that of tensile strength, which increased significantly with the increasing of Al2O3 content. When the content of Al2O3 was 70 wt%, the flexural strength of MEKO blocked isocyanate-propyltriethoxy silane modified Al2O3/PA6 composites reached 136.4 MPa.
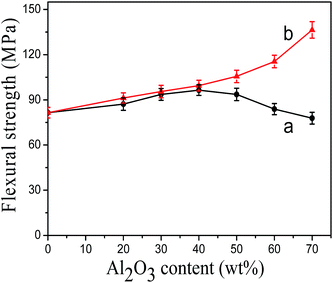 |
| Fig. 7 The flexural strength of modified Al2O3/PA6 composites (a) by KH-331, (b) by MEKO blocked isocyanate-propyltriethoxy silane. | |
The impact strength of modified Al2O3/PA6 composites was shown in Fig. 8. The impact strength of modified Al2O3/PA6 composites decreased monotonously with the increasing of Al2O3 content. At the same Al2O3 content, the impact strength of MEKO blocked isocyanate-propyltriethoxy silane modified Al2O3/PA6 composites was higher than that of KH-331 modified Al2O3/PA6 composites.
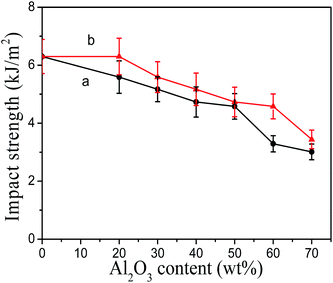 |
| Fig. 8 The impact strength of modified Al2O3/PA6 composites (a) by KH-331, (b) by MEKO blocked isocyanate-propyltriethoxy silane. | |
The reason, which flexural strength and impact strength of MEKO blocked isocyanate-propyltriethoxy silane modified Al2O3/PA6 composites were better than that of KH-331 modified Al2O3/PA6 composites, might be the same as the explain in tensile strength.
3.5 Thermal conductivity
Fig. 9 showed the thermal conductivity of modified Al2O3/PA6 composites with different content of Al2O3. The thermal conductivity of modified Al2O3/PA6 composites increased significantly with the increasing of weight fraction of modified Al2O3. Sato et al.13 reported similar conclusions. With the increasing of Al2O3 content, thermal conductivity particles could touch each other closely, the thickness between PA6 and Al2O3 particles reduced, which decreased the thermal resistance of Al2O3/PA6 composites, resulting in an increase in thermal conductivity of Al2O3/PA6 composites. Moreover, the thermal conductivity of modified Al2O3/PA6 composites increased rapidly when the Al2O3 content was higher than 60 wt%. Once the heat network is formed by the fillers, the composite exhibits a percolation behavior, the thermal conductivity enhanced steeply for instance.18 In addition, the MEKO blocked isocyanate-propyltriethoxy silane modified Al2O3/PA6 composites exhibited higher thermal conductivity as compared with the KH-331 modified Al2O3/PA6 composites at the same weight fraction of Al2O3 loading. The thermal conductivity of the filled composites is determined not only by the content of filler, but also by the synergetic effect of matrix and filler. In this paper, in situ reaction of deblocked isocyanate groups with the terminal amino groups and/or carboxyl groups of PA6 chain strengthened the interfacial interactions between PA6 and blocked isocyanate silane modified Al2O3 particles. Fig. 4 also showed that MEKO blocked isocyanate-propyltriethoxy silane modified Al2O3 particles were more uniformly dispersed in PA6, so the thermal conductive particles could touch each other more closely, which can form net-like or chain-like thermal conductive channel and heat could more easily be transferred. Many researchers19,20 also got the conclusion that composites with a better interfacial adhesion exhibited a higher thermal conductivity. When the content of Al2O3 was 70 wt%, the thermal conductivity of MEKO blocked isocyanate-propyltriethoxy silane modified Al2O3/PA6 composites reached 1.18 W (m−1 K−1), which was almost 6 times higher than that of neat PA6.
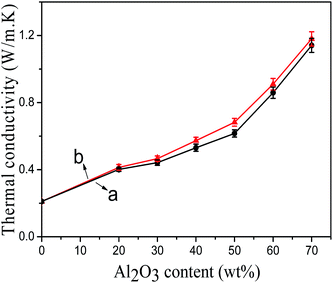 |
| Fig. 9 The thermal conductivity of modified Al2O3/PA6 composites (a) by KH-331, (b) by MEKO blocked isocyanate-propyltriethoxy silane. | |
3.6 Electrical insulation
The volume electrical resistivity of modified Al2O3/PA6 composites with different Al2O3 content was shown in Fig. 10. The decreased tendency of volume electrical resistivity of KH-331 and blocked isocyanate silane modified Al2O3/PA6 composites was almost the same. The results indicated that different surface modification of Al2O3 almost unaffected the electrical insulation of modified Al2O3/PA6 composites. When the content of modified Al2O3 was 70 wt%, the volume electrical resistivity of modified Al2O3/PA6 composite decreased by one order of magnitude. Wu et al.7 also found that the volume electrical resistivity of 57.4 vol% AlN/polyetherimide composite decreased by two orders of magnitude. The modified Al2O3/PA6 composites can be still regarded as good electrical insulating materials.
 |
| Fig. 10 The electrical insulation of modified Al2O3/PA6 composites (a) by KH-331, (b) by MEKO blocked isocyanate-propyltriethoxy silane. | |
4. Conclusions
The thermally conductive and electrical insulating PA6 composites containing blocked isocyanate silane modified Al2O3 particles as fillers were successfully fabricated by twin-screw extruder. The blocked isocyanate-propyltriethoxy silane attached to the surface of Al2O3 particles with chemical bond. The blocked isocyanate groups on the surface of Al2O3 deblocked to regenerate isocyanate groups, which could react in situ with the terminal amino groups and/or carboxyl groups of PA6 chain. As a result, blocked isocyanate silane modified Al2O3 particles were more homogeneous dispersed and had stronger interaction with PA6 matrix.
The tensile and flexural strength of blocked isocyanate silane modified Al2O3/PA6 composites increase steadily with increasing the content of Al2O3, while the tensile and flexural strength of KH-331 modified Al2O3/PA6 composites decreased when Al2O3 content was higher than 40 wt%. When the Al2O3 content increased to 70 wt%, the tensile strength and flexural strength of blocked isocyanate silane modified Al2O3/PA6 composites reached 85.2 MPa and 136.4 MPa, respectively, which was considerably higher than that of neat PA6. The thermal conductivity and impact strength of blocked isocyanate silane modified Al2O3/PA6 composites were also improved due to the enhanced interaction between Al2O3 particles and PA6 matrix. When the content of Al2O3 was 70 wt%, the thermal conductivity of blocked isocyanate silane modified Al2O3/PA6 composites reached 1.18 W (m−1 K−1). Though the volume electrical resistivity of modified Al2O3/PA6 composites decreased with increasing Al2O3 content, it is still higher than 3.0 × 1014 Ω cm.
Acknowledgements
The authors are grateful for the financial support from Anhui Science and Technology Department, China (no. 1501021071).
References
- N. Burger, A. Laachachi, M. Ferriol, M. Lutz, V. Toniazzo and D. Ruch, Prog. Polym. Sci., 2016, 61, 1–28 CrossRef CAS.
- Y. Hu, G. P. Du and N. Chen, Compos. Sci. Technol., 2016, 124, 36–43 CrossRef CAS.
- J. W. Gu, Z. Y. Lv, Y. L. Wu, Y. Q. Guo, L. D. Tian, H. Qiu, W. Z. Li and Q. Y. Zhang, Composites, Part A, 2017, 94, 209–216 CrossRef CAS.
- T. M. L. Dang, C. Y. Kim, Y. M. Zhang, J. F. Yang, T. Masaki and D. H. Yoon, Composites, Part B, 2017, 114, 237–246 CrossRef CAS.
- Z. X. Shi, R. L. Fu, S. Agathopoulos, X. G. Gu and W. W. Zhao, Mater. Des., 2012, 34, 820–824 CrossRef CAS.
- W. Dai, J. H. Yu, Z. D. Liu, Y. Wang, Y. Z. Song, J. L. Lyu, H. Bai, K. Nishimura and N. Jiang, Composites, Part A, 2015, 76, 73–81 CrossRef CAS.
- S. Y. Wu, Y. L. Huang, C. C. M. Ma, S. M. Yuen, C. C. Teng and S. Y. Yang, Composites, Part A, 2011, 42, 1573–1583 CrossRef.
- R. Konnola, J. Joji, J. Parameswaranpillai and K. Joseph, RSC Adv., 2015, 5, 61775–61786 RSC.
- M. Sandomierski, B. Strzemiecka, M. M. Chehimi and A. Voelkel, Langmuir, 2016, 32, 11646–11654 CrossRef CAS PubMed.
- S. Gardebjer, A. Bergstrand, A. Idstrom, C. Borstell, S. Naana, L. Nordstierna and A. Larsson, Compos. Sci. Technol., 2015, 107, 1–9 CrossRef.
- Y. C. Jia, H. He, P. Yu, J. Chen and X. L. Lai, eXPRESS Polym. Lett., 2016, 10, 679–692 CrossRef CAS.
- X. H. Li, L. B. Shao, N. Song, L. Y. Shi and P. Ding, Composites, Part A, 2016, 88, 305–314 CrossRef CAS.
- K. Sato, A. Ijuin and Y. Hotta, Ceram. Int., 2015, 41, 10314–10318 CrossRef CAS.
- M. H. Li, Y. Z. Wan, Z. F. Gao, G. Y. Xiong, X. M. Wang, C. B. Wan and H. L. Luo, Mater. Des., 2013, 51, 257–261 CrossRef CAS.
- G. S. Hu, Y. L. Ma and B. B. Wang, Mater. Sci. Eng., A, 2009, 504, 8–12 CrossRef.
- A. F. Li, G. D. Fan, H. Chen and Q. Zhao, Res. Chem. Intermed., 2013, 39, 3565–3577 CrossRef CAS.
- D. M. Lincoln, R. A. Vaia, Z. G. Wang, B. S. Hsiao and R. Krishnamoorti, Polymer, 2001, 42, 9975–9985 CrossRef CAS.
- H. L. Lee, O. H. Kwon, S. M. Ha, B. G. Kim, Y. S. Kim, J. C. Won, J. Kim, J. H. Choi and Y. Yoo, Phys. Chem. Chem. Phys., 2014, 16, 20041–20046 RSC.
- P. Ding, S. S. Su, N. Song, S. F. Tang, Y. M. Liu and L. Y. Shi, RSC Adv., 2014, 4, 18782–18791 RSC.
- T. G. Qu, N. Yang, J. Hou, G. H. Li, Y. M. Yao, Q. X. Zhang, L. Q. He, D. Z. Wu and X. W. Qu, RSC Adv., 2017, 7, 6140–6151 RSC.
|
This journal is © The Royal Society of Chemistry 2017 |
Click here to see how this site uses Cookies. View our privacy policy here.