DOI:
10.1039/C7RA02396K
(Paper)
RSC Adv., 2017,
7, 16901-16907
Synthesis of C15 and C10 fuel precursors with cyclopentanone and furfural derived from hemicellulose†
Received
26th February 2017
, Accepted 13th March 2017
First published on 16th March 2017
Abstract
Fuel precursors 2,5-bis(2-furylmethylidene)cyclopentanone (F2Cp) and 2-(2-furylmethylidene)cyclopentanone (FCp) were obtained through aldol condensation of cyclopentanone and furfural over solid acid catalysts under solvent-free conditions. Nafion exhibited the best performance among the investigated catalysts (Nafion, Amberlyst-15, Amberlyst-36, H-USY, ZSM-5, H-β, and SiO2/Al2O3). Under optimized conditions, yields of F2Cp and FCp were 37.48% and 23.77%, respectively. Selectivities of F2Cp and FCp were 50.74% and 32.18%, respectively. Nafion showed good stability and did not deactivate during 4 runs. Meanwhile, a certain amount of humin was also generated during the reaction. The reaction mechanism for the aldol condensation of cyclopentanone and furfural and the formation mechanism of humin were also proposed.
Introduction
Utilization of renewable biomass for the production of fuels and chemicals has drawn worldwide attention as concerns grow over diminishing petroleum sources, greenhouse effect, and environmental pollution.1–6 Diesel and jet fuels are two kinds of frequently used transportation fuels mainly obtained from petrochemical engineering. In recent years, biomass diesel and jet fuels have been used as important fungible fuels owing to their renewability, low toxicity, low sulfur content, high octane number, and biodegradability.7–10 Lignocellulose is the major component of agriculture wastes or forest residues. Following the pioneering work of Dumesic et al.11–13 and Huber et al.,14,15 the synthesis of renewable diesel and jet-fuel-range alkanes with lignocellulose-derived platform chemicals has attracted increasing attention. Furfural is an important raw material obtained on an industrial scale by the hydrolysis/dehydration of hemicellulose.16–18 In recent studies, C8 and C13 oxygenates were produced through aldol condensation of furfural and acetone.14,19–22 Oxygenated derivatives of furfural were obtained by aldol condensation with methyl isobutyl ketone, pentanone, hexanone, and other biomass feedstock or hydroxyalkylation/alkylation with methyl furan.23 These oxygenates can be converted to alkanes by low-temperature hydrogenation and hydrodeoxygenation (HDO).
Cyclopentanone can be obtained from a furfural and furfural alcohol selective hydrogenation and rearrangement reaction.24–31 Zhang and his group studied selective conversion of furfural to cyclopentanone with CuZnAl catalysts, where the yield obtained was 62%.24 Furfural and furfural alcohol selective hydrogenation and rearrangement reaction can be catalyzed with Ni, Pt, Pd, Pt–Ru, and Ru catalysts by using water as the solvent, with a yield of cyclopentanone up to 76.5%.28 Fu et al. reported the selective conversion of furfural to cyclopentanone with Cu–Co catalysts with a 67% yield of cyclopentanone.29 Xu's group reported conversion of furfural into cyclopentanone over Ni–Cu bimetallic catalysts at a 62% yield.30 Xiao et al. reported selective hydrogenation of furfural to cyclopentanone over hydrotalcite-based Cu–Ni–Al catalysts with a yield of up to 95.8%.31
Cyclopentanone can undergo condensation with valeraldehyde,32 furfural33,34 or itself.35–38 It can also react with 2-methyl furan through hydroxyalkylation/alkylation,9,39,40 generating C10–C15 oxygen-containing compounds, and then the C10–C15 oxygen-containing compounds can be converted into high-density diesel or jet fuel by hydrodeoxygenation. Aldol condensation of cyclopentanone and furfural by sodium hydroxide in solution free system achieved 2,5-bis(2-furylmethylidene)cyclopentanone yield of 96.0%.41 Aldol condensation of cyclopentanone and furfural in an aqueous solution of sodium hydroxide gave a 2,5-bis(2-furylmethylidene)cyclopentanone yield of more than 95%.33,34 However, the reaction yields a large amount of wastewater and thus was not environmentally benign, additionally, the used sodium hydroxide could not be effectively recycled.
Aldol condensation is an important organic synthetic reaction catalyzed by acid or alkali. It involves transforming of compounds containing active α-hydrogen atoms (such as aldehyde, ketone, carboxylic acid, and ester), nucleophilic addition to obtain β-hydroxyl compounds, and then further dehydration to generate α, β-unsaturated carbonyl compounds. It could take place in homogeneous aqueous (or water/alcohol) solutions15 and biphasic systems.33,42 To simplify the process, new solid base catalysts have also been developed.22,43–46
In this work, fuel precursors 2,5-bis(2-furylmethylidene)cyclopentanone (F2Cp) and 2-(2-furylmethylidene)cyclopentanone (FCp) were obtained from aldol condensation of cyclopentanone and furfural over solid acids catalyst under solvent-free conditions. Nafion exhibited the best performance among investigated catalysts (Nafion, Amberlyst-15, Amberlyst-36, H-USY, ZSM-5, H-β, and SiO2/Al2O3). Furthermore, we also studied the effects of catalyst dosage, reaction temperature, and time on the conversion of furfural and yields of F2Cp and FCp over the Nafion catalyst under solvent-free conditions. We also investigated the stability of the Nafion catalyst. Finally, the reaction mechanism of aldol condensation of cyclopentanone and furfural and the formation mechanism of humins were also proposed.
Experimental
Materials
Nafion resin with a diameter ball of 0.2 mm was provided by JiangSu Success Resin Ltd. Amberlyst-36 and Amberlyst-15 resins were purchased by Sigma Aldrich. H-USY (SiO2/Al2O3 = 12), ZSM-5 (SiO2/Al2O3 = 25), and H-β (SiO2/Al2O3 = 25) zeolites used in this work were provided by Catalyst Factory of Nankai University. SiO2–Al2O3 (SiO2/Al2O3 = 25) was purchased from Qingdao Ocean Chemical Ltd. Furfural (99%) and cyclopentanone (99%) were purchased from Sigma Aldrich. Furfural was purified by vacuum distillation and stored in a refrigerator at 0 °C. F2Cp was prepared following a typical process in the literature.31 FCp produced from the reaction of furfural and cyclopentanone was further separated by column chromatography with silica gel (purchased from Merck) as the stationary phase, and a mixture of ethyl acetate and petroleum ether (at a volume ratio of 1
:
15) was used as the mobile phase. Thin layer chromatography (TLC) was used for detection of FCp, and the collected effluent containing FCp was concentrated through vacuum distillation.
Aldol condensation
The reactions were carried out in a 50 mL batch reactor with a reflex condenser and a magnetic stirrer at atmospheric pressure. The temperature was controlled by a pre-heated oil bath. In a typical reaction, 0.40 g of catalyst, 1.92 g of furfural (20 mmol), and 5.04 g of cyclopentanone (60 mmol) were added to the reactor and then the mixture was stirred at 60 °C for 6 h.
Separation of humins
The crude product in the reactions was then mixed with 200 mL of anhydrous ethanol under refluxing for 30 min. Unreacted furfural, cyclopentanone, and the products of FCp and F2Cp were separated from insoluble residue through filtering at a high temperature (∼78 °C). The residue was treated twice with 200 mL of anhydrous ethanol to completely removed the soluble substances. The residue solid was humins.
Analysis
The concentrations of F2Cp, FCp, and furfural were determined by an Agilent 1260 high performance liquid chromatography (HPLC) system, equipped with a ZORBAXSB-C18 column (4.6 mm × 150 mm, 5 μm) and a refractive index detector (RID). A solution of methanol and water (9
:
1 v/v) was used as the eluent.
The products were verified with a Bruker AVANCE 500 MHz NMR spectrometer, with chloroform-d (99.8% atom D with 0.1% v/v tetramethylsilane (TMS)) from Aldrich was used as the solvent for 1H and 13C NMR sample preparation. Chemical shifts, quoted in ppm, are relative to the internal standards of the singlet at δ = 0 ppm for TMS for 1H NMR and the middle peak of the CDCl3 triplet at δ = 77 ppm for 13C NMR.
Infrared (IR) spectra were measured with a Bruker Vertex 70 Infrared spectrometer using a pressed disc method with potassium bromide. The instrumental resolution was set to at 4 cm−1. The IR spectrum of air was recorded as the background, and then samples were placed in a holder for transmittance measuring. Scan time of 60 s were used for both the background and the samples.
The conversions of furfural and the yields of F2Cp and FCp were calculated by the following formulas:
Results and discussion
Aldol condensation of furfural with cyclopentanone
The aldol condensation of furfural with cyclopentanone was carried out over solid acid catalysts. According to the analysis of HPLC (p S2 in ESI†) and NMR (p S3, S4 in ESI†) spectra, F2Cp (in Scheme 1) was identified as the main product. In addition, FCp (in Scheme 1) was also detected in the reaction mixture. As shown in Scheme 1, FCp was the product of the aldol condensation of furfural with cyclopentanone, and F2Cp was the product of aldol condensation between FCp further with furfural. The NMR spectra (p S3 in ESI†) of F2Cp show the following peaks: 1H NMR (CDCl3-d), δ: 7.80 (s, 2H), 7.56 (s, 2H), 6.90 (t, 2H), 6.75 (m, 2H), 3.28 (t, 4H); 13C NMR (CDCl3-d), δ: 195 (1C), 152 (2C), 144 (2C), 135 (2C), 119 (2C), 116 (2C), 112 (2C), 25 (2C). The F2Cp obtained was in the form of yellow needles crystal. The NMR spectra (p S4 in ESI†) of FCp show the following peaks: 1H NMR (CDCl3-d), δ: 7.71 (s, 1H), 7.37 (d, 1H, J = 4), 6.87 (t, 1H), 6.72 (d, 1H, J = 4), 3.20 (t, 2H), 2.59 (t, 2H), 2.26 (m, 2H); 13C NMR (CDCl3-d), δ: 207 (1C), 152 (1C), 144 (1C), 133 (1C), 118 (1C), 115 (1C), 112 (1C), 37 (1C), 28 (1C), 19 (1C). The FCp was a yellow-brown solid.
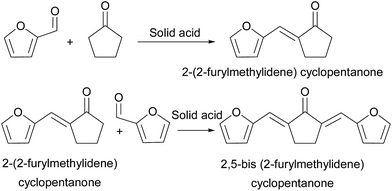 |
| Scheme 1 Reaction route of aldol condensation of furfural and cyclopentanone. | |
The catalytic performances of different solid acids for the aldol condensation of furfural with cyclopentanone are shown Fig. 1, which shows that solid acid catalysts can promote the aldol condensation of furfural with cyclopentanone. Higher yields of F2Cp and FCp could be achieved over Nafion, Amberlyst-15, and Amberlyst-36 resins than under catalysis by H-USY, HZSM-5, H-β, SiO2/AlO3 under the same reaction conditions.
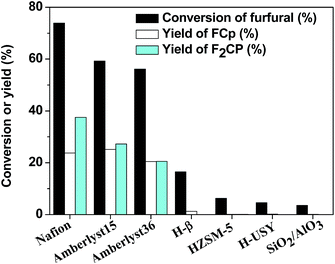 |
| Fig. 1 The aldol condensation of furfural and cyclopentanone over various heterogeneous catalysts. Reaction conditions: 60 °C, 6 h; 1.92 g (20 mmol) furfural, 5.04 g (60 mmol) cyclopentanone, 0.40 g catalyst. | |
The sequence for the yield of F2Cp, FCp over the solid acid catalysts was Nafion > Amberlyst-15 > Amberlyst-36 > H-β, H-USY, ZSM-5, SiO2/Al2O3. This sequence is consistent with that of the Hammett acidity function (−Ho) values of these catalysts (see Table 1). Therefore, the higher catalytic efficiency of Nafion resin can be attributed to the higher strength of acid sites on this catalyst. The higher acid strength of Nafion resin is dependent on by its structure. As we know, Nafion is a perfluorinated sulfonic acid resin,47 while Amberlyst resins are sulfonic-acid-functionalized cross-linked polystyrene.48 The presence of fluorine on the Nafion resin greatly enhances the acid strength of the –SO3H group.
Table 1 Average pore sizes, acid amounts and Hammett acidity function (−Ho) values of the different solid acid catalysts used in the aldol condensation of furfural and cyclopentanonea
Catalyst |
Acid amount (mmol g−1) |
Average pore size (nm) |
−Ho |
According to the information provided by supplier. |
Nafion |
3.0 |
4.0 |
11–13 (ref. 45) |
Amberlyst-15 |
4.7 |
29 |
2.2 (ref. 49) |
Amberlyst-36 |
5.4 |
24 |
2.2–2.65 (ref. 50) |
H-ZSM-5 |
0.43 |
0.5 |
5.6–5.7 (ref. 50) |
H-USY |
0.44–0.48 |
0.7 |
3.0–4.4 (ref. 50) |
H-β |
0.2 |
0.6 × 0.67, 0.56 × 0.56 |
4.4–5.7 (ref. 49) |
H-Y |
0.9 |
0.74 × 0.74 |
−1.5 to 5.6 (ref. 49) |
The influence of catalyst dosage on aldol condensation of furfural and cyclopentanone is shown in Fig. 2. It can be seen that conversion of furfural was increased as the amount of catalyst was raised from 0.2 to 0.5 g. Meanwhile, yields of F2Cp and FCp increased with the catalyst dosage first, and then leveled off. When the catalyst amount of 0.40 g, yields of F2Cp and FCp maximized. Hence, the catalyst amount was 0.40 g in the following parts.
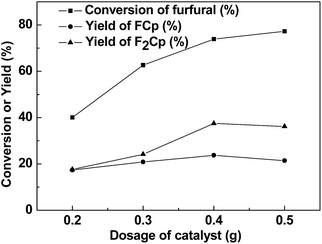 |
| Fig. 2 The effect of the catalyst dosage on the aldol condensation. Reaction conditions: 60 °C, 6 h; 1.92 g (20 mmol) furfural, 5.04 g (60 mmol) cyclopentanone. | |
Temperature is an important parameter for any chemical reaction. Thus, the effect of the reaction temperature on the conversion of furfural, yields of F2Cp and FCp were studied and the results were shown in Fig. 3. The conversion of furfural increased first, and then remained constant as the reaction temperature increased further. Moreover, yields of F2Cp and FCp increased at first with the reaction temperature, and then decreased. Therefore, the chosen reaction temperature was 60 °C.
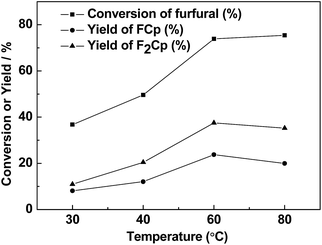 |
| Fig. 3 The effect of reaction temperature on the aldol condensation. Reaction conditions: 0.40 g Nafion catalyst, 6 h; 1.92 g (20 mmol) furfural, 5.04 g (60 mmol) cyclopentanone. | |
The impact of reaction time on the conversion of furfural, yields of F2Cp and FCp was then examined. The experimental results were shown in Fig. 4. It can be seen that conversion of furfural first increased and then remained constant as the reaction time was prolonged from 0.5 to 8 hours. The conversion of furfural was 73.86% at 6 h. Meanwhile, yields of F2Cp and FCp increased at first, and then remained constant. At 6 h, yields of F2Cp and FCp were 37.48% and 23.77%, respectively. Thus, the reaction time of 6 h was better.
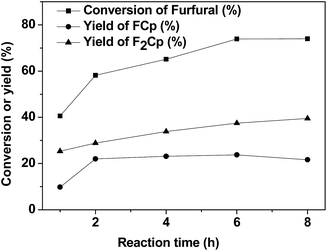 |
| Fig. 4 The effect of reaction time on the aldol condensation. Reaction conditions: 0.40 g Nafion catalyst, 1.92 g (20 mmol) furfural, 5.04 g (60 mmol) cyclopentanone at 60 °C. | |
The stability of Nafion in the aldol condensation of furfural and cyclopentanone was implemented. To eliminate the influence of residues, the catalysts were regenerated with a 10% H2O2 aqueous solution at 80 °C for 2.0 h. Then, the mixture was filtered and the catalyst was dried at 80 °C for 2.0 h after each usage. According to the results shown in Fig. 5, Nafion showed good stability in the aldol condensation of furfural and cyclopentanone. No evident activity change was noticed over this catalyst after it was used 4 times. Considering the excellent catalytic performance and good stability of Nafion resin, we consider it a promising catalyst in future applications.
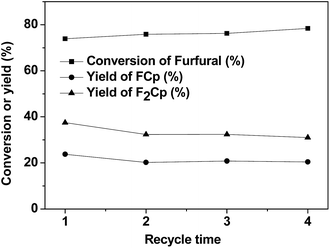 |
| Fig. 5 The recyclability of Nafion resin for the aldol condensation. Reaction conditions: 60 °C, 6 h; 1.92 g (20 mmol) furfural, 5.04 g (60 mmol) cyclopentanone, and 0.40 g of Nafion. | |
Under the optimum conditions (60 °C, 6 hours, and 0.40 g catalyst), aldol condensation of furfural and cyclopentanone on Nafion catalyst in solvent-free conditions gave a conversion of 73.86% for furfural and yields of 37.48% and 23.77% for F2Cp and FCp, respectively. Selectivities of F2Cp and FCp were 50.74% and 32.18%, respectively.
Reaction mechanism of furfural with cyclopentanone
The reaction mechanism of aldol condensation using furfural and cyclopentanone by solid acid catalysis is shown in Scheme 2. Cyclopentanone is first protonated by a proton (H+) over solid acid to form an electron-deficient intermediate (1). The π electron of C
O double bonds is transferred to the electron-deficient atom of oxygen to form carbocation (2). Carbanion and H+ were gained by electron heterolytic formation of alpha C–H σ bond of carbocation. The lone pair electrons of the carbanion are split and transfer to the carbocation, and the C
C bond-containing enol structure (3) is formed. The negatively charged carbon of (3) attacked the C atom of C
O of the same protonated furfural. The π electron of intermediate (4) is transferred to the electron-deficient oxygen of carbonyl. At the same time, the C
C π electrons of intermediate (3) attack the electron-deficient carbon of intermediate (4) to form a C–C bond and the lone pair on the oxygen atom transferred to the adjacent carbon atoms to form C
C gave rise to the structure of the intermediate (5). The intermediate (5) released protons to form intermediate (6). Hydroxyl groups of intermediate (6) are protonated to form intermediate (7) under acidic conditions. Then, one molecule of water is released to form intermediate (8). Meanwhile, the C–H σ bond is transferred and proton is released to form the product FCp.
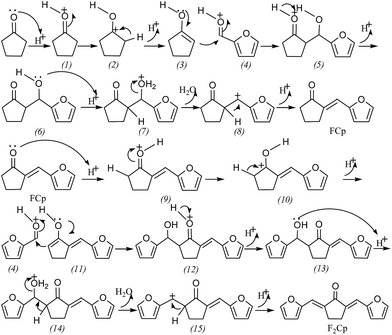 |
| Scheme 2 Reaction mechanism of aldol condensation from furfural and cyclopentanone by solid acid catalysis. | |
The carbonyl of FCp is protonated to obtain intermediate (9), and the π electron of C
O in intermediate (9) transferred to the carbonyl oxygen atom to form a carbon cationic structure (10), which undergoes heterolytic electron transfer to form the enol structure (11). The negative charge of the carbon with a protonated enol structure (11) attacks the protonated carbonyl of furfural in intermediate (4), forming a C–C bond to obtain the intermediate (12). Intermediate (12) releases proton and forms intermediate (13). The intermediate (13) is protonated to form intermediate (14), and then releases a water molecule to form intermediate (15) (σ bond shift). At the same time, proton is removed to form the product F2Cp. This reaction mechanism is similar to that of acetophenone and benzaldehyde under the catalysis of sulfuric acid.51
Formation mechanism of humins
Water is continuously produced from aldol condensation of furfural and cyclopentanone on solid acid conditions. Under these conditions, furfural can be easily polymerized through hydrolysis. The conversion process is shown in Scheme 3. Furfural is first hydrolyzed to produce 5-hydroxy-4,5-dihydrofuran-2-carbaldehyde (I) or 2-hydroxy-2,3-dihydrofuran-2-carbaldehyde (II). The hydrolysis mechanism of furfural is similar to that of 5-hydroxymethyl furfural.52–54 The open ring of intermediates I and II generate 2-oxo pentanedial (III). Isomerization and rearrangement of intermediate III provided 4-hydroxy-5-oxo-4-pentene aldehyde (IV), 2-hydroxy-2-ene glutaraldehyde (V), or 5-hydroxy-2-oxo-4-aldehyde (VI). Then the aldol condensation of IV, V, and VI with furfural forms 4,5-dioxo-6-hydroxy-6-tetrahydrofuran hexanal (VII), 2-oxo-3-tetrahydrofuran methylene pentanedial (VIII), and 2-oxo-4-tetrahydrofuran methylene pentanedial (IX). VII, VIII, and IX will polymerize by themselves or interaction each other to form a polymer with high viscosity (humins). The humins can easily cover the catalyst surface form a membrane. Leading to the active centers of the catalyst are completely isolated from the feedstock (cyclopentanone and furfural). The catalyst subsequently will loss of activity, and therefore the reaction cannot complete thoroughly. Intermediate III can also generate humins through self-condensation or condensation with furfural. This is the reason why, under the optimized conditions, conversion of furfural was 73.86% and the yields of F2Cp and FCp were 37.48% and 23.77%, respectively. Selectivities of F2Cp and FCp were 50.74% and 32.18%, respectively. At the same time, we also found that, during the regeneration process of the catalyst, a layer of thin film formed on the surface of the Nafion ball. It is consistent with formation polymer of hydrolysis reaction.
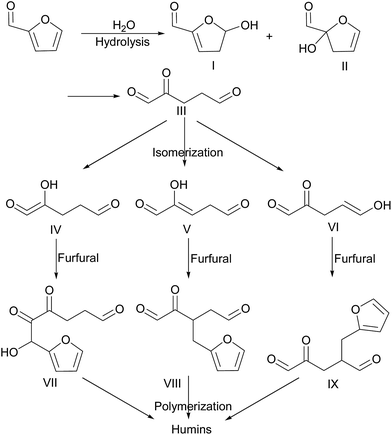 |
| Scheme 3 Formation mechanism of humins. | |
The infrared spectrum of the polymer is shown in Fig. 6. The weak absorption at 3134 cm−1 and 3115 cm−1 belong to the C–H bond stretching vibration of the furan ring. The weak absorption bands at 2877–2957 cm−1 are attributed to CH2 bond stretching vibration owing to polymerization. The weak absorption peak at 1735 cm−1 is due to the stretching vibration of the C
O bonds in aldehyde groups. The strong absorption peaks at 1707 cm−1 and 1681 cm−1 are caused by the stretching vibration of C
O bonds in unsaturated aldehyde and ketone. The strong absorption peaks at 1622 cm−1 and 1604 cm−1 correspond to the C
C stretching vibration and those at 1473 cm−1, 1388 cm−1, and 1348 cm−1 are attributed to the C–H bending vibrations in CH2 bonds. Absorption peaks at 1280 cm−1, 1261 cm−1, 1205 cm−1, and 1161 cm−1 corresponded to C–O bond stretching vibrations, while those at 3134 cm−1, 3115 cm−1, 1622 cm−1, 1604 cm−1, 1485 cm−1, 1161 cm−1, 1020 cm−1, 754 cm−1, and 592 cm−1 are caused by the vibrations of the furan ring.
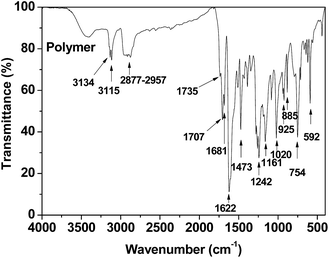 |
| Fig. 6 Infrared spectra of furfural polymers. | |
Conclusions
A series of solid acid catalysts were firstly used for the synthesis of fuel precursors F2Cp and FCp from cyclopentanone and furfural derived from hemicellulose in a solvent free system. Nafion exhibited the best performance among the investigated catalysts (Nafion, Amberlyst-15, Amberlyst-36, H-USY, ZSM-5, H-β, SiO2/Al2O3). The effects of dosage of catalyst, reaction temperature, and time are studied. Under the optimized conditions, conversion of furfural was 73.86%, the yields of F2Cp and FCp were 37.48% and 23.77%, respectively. No deactivation was observed during 4 continuous runs. Mechanism of aldol condensation of furfural and cyclopentanone was proposed in detail. Meanwhile, a certain amount of humins also formed in the reaction process, and the products were characterized using FT-IR spectra.
Acknowledgements
This study was supported by the Education Department of Shaanxi Provincial Government Research Project (No. 16JK1146), the National Natural Science Foundation of China (No. 21503125, 21502109), and the Funds of Research Programs of Shaanxi University of Technology (No. SLGQD13(2)-1).
Notes and references
- G. W. Huber and A. Corma, Chem. Rev., 2006, 106, 4044–4098 CrossRef CAS PubMed
. - C. Zhao, Y. Kou, A. A. Lemonidou, X. Li and J. A. Lercher, Angew. Chem., Int. Ed., 2009, 48, 3987–3990 CrossRef CAS PubMed
. - D. M. Alonso, J. Q. Bond, J. C. Serrano-Ruiz and J. A. Dumesic, Green Chem., 2010, 12, 992–999 RSC
. - M. J. Climent, A. Corma and S. Iborra, Green Chem., 2014, 16, 516–547 RSC
. - C. Zhao and J. A. Lercher, Angew. Chem., Int. Ed., 2012, 51, 5935–5940 CrossRef CAS PubMed
. - T. D. Matson, K. Barta, A. V. Iretskii and P. C. Ford, J. Am. Chem. Soc., 2011, 133, 14090–14097 CrossRef CAS PubMed
. - S. Li, N. Li, G. Li, A. Wang, Y. Cong, X. Wang and T. Zhang, Catal. Today, 2014, 234, 91–99 CrossRef CAS
. - G. Li, N. Li, S. Li, A. Wang, Y. Cong, X. Wang and T. Zhang, Chem. Commun., 2013, 49, 5727–5729 RSC
. - G. Li, N. Li, X. Wang, X. Sheng, S. Li, A. Wang, Y. Cong, X. Wang and T. Zhang, Energy Fuels, 2014, 28, 5112–5118 CrossRef CAS
. - G. Nie, X. Zhang, P. Han, J. Xie, L. Pan, L. Wang and J.-J. Zou, Chem. Eng. Sci., 2017, 158, 64–69 CrossRef CAS
. - J. Q. Bond, D. M. Alonso, D. Wang, R. M. West and J. A. Dumesic, Science, 2010, 327, 1110–1114 CrossRef CAS PubMed
. - D. A. S. Edward, L. Kunkes, R. M. West, J. C. Serrano-Ruiz, C. A. Gärtner and J. A. Dumesic, Science, 2008, 322, 417–421 CrossRef PubMed
. - G. W. Huber, J. N. Chheda, C. J. Barrett and J. A. Dumesic, Science, 2005, 308, 1446–1450 CrossRef CAS PubMed
. - H. Olcay, A. V. Subrahmanyam, R. Xing, J. Lajoie, J. A. Dumesic and G. W. Huber, Energy Environ. Sci., 2013, 6, 205–216 CAS
. - R. Xing, A. V. Subrahmanyam, H. Olcay, W. Qi, G. P. van Walsum, H. Pendse and G. W. Huber, Green Chem., 2010, 12, 1933–1946 RSC
. - I. Agirrezabal-Telleria, J. Requies, M. B. Güemez and P. L. Arias, Appl. Catal., B, 2012, 115–116, 169–178 CrossRef CAS
. - P. Azadi, R. Carrasquillo-Flores, Y. J. Pagán-Torres, E. I. Gürbüz, R. Farnood and J. A. Dumesic, Green Chem., 2012, 14, 1573–1576 RSC
. - E. I. Gürbüz, S. G. Wettstein and J. A. Dumesic, ChemSusChem, 2012, 5, 383–387 CrossRef PubMed
. - Q. N. Xia, Q. Cuan, X. H. Liu, X. Q. Gong, G. Z. Lu and Y. Q. Wang, Angew. Chem., Int. Ed., 2014, 53, 9755–9760 CrossRef CAS PubMed
. - W. Shen, G. A. Tompsett, K. D. Hammond, R. Xing, F. Dogan, C. P. Grey, W. C. Conner, S. M. Auerbach and G. W. Huber, Appl. Catal., A, 2011, 392, 57–68 CrossRef CAS
. - R. M. West, Z. Y. Liu, M. Peter, C. A. Gärtner and J. A. Dumesic, J. Mol. Catal. A: Chem., 2008, 296, 18–27 CrossRef CAS
. - M. Chatterjee, K. Matsushima, Y. Ikushima, M. Sato, T. Yokoyama, H. Kawanami and T. Suzuki, Green Chem., 2010, 12, 779–782 RSC
. - G. Li, N. Li, Z. Wang, C. Li, A. Wang, X. Wang, Y. Cong and T. Zhang, ChemSusChem, 2012, 5, 1958–1966 CrossRef CAS PubMed
. - J. Guo, G. Xu, Z. Han, Y. Zhang, Y. Fu and Q. Guo, ACS Sustainable Chem. Eng., 2014, 2, 2259–2266 CrossRef CAS
. - M. Hronec, K. Fulajtarová and T. Liptaj, Appl. Catal., A, 2012, 437–438, 104–111 CrossRef CAS
. - M. Hronec, K. Fulajtárova and M. Mičušik, Appl. Catal., A, 2013, 468, 426–431 CrossRef CAS
. - M. Hronec, K. Fulajtárová, I. Vávra, T. Soták, E. Dobročka and M. Mičušík, Appl. Catal., B, 2016, 181, 210–219 CrossRef CAS
. - M. Hronec and K. Fulajtarová, Catal. Commun., 2012, 24, 100–104 CrossRef CAS
. - X.-Y. Li, R. Shang, M.-C. Fu and Y. Fu, Green Chem., 2015, 17, 2790–2793 RSC
. - Y. Yang, Z. Du, Y. Huang, F. Lu, F. Wang, J. Gao and J. Xu, Green Chem., 2013, 15, 1932–1940 RSC
. - H. Zhu, M. Zhou, Z. Zeng, G. Xiao and R. Xiao, Korean J. Chem. Eng., 2014, 31, 593–597 CrossRef CAS
. - M. Hasni, G. Prado, J. Rouchaud, P. Grange, M. Devillers and S. Delsarte, J. Mol. Catal. A: Chem., 2006, 247, 116–123 CrossRef CAS
. - M. Hronec, K. Fulajtárova, T. Liptaj, M. Štolcová, N. Prónayová and T. Soták, Biomass Bioenergy, 2014, 63, 291–299 CrossRef CAS
. - M. Hronec, K. Fulajtárova, T. Liptaj, N. Prónayová and T. Soták, Fuel Process. Technol., 2015, 138, 564–569 CrossRef CAS
. - J. Yang, N. Li, G. Li, W. Wang, A. Wang, X. Wang, Y. Cong and T. Zhang, Chem. Commun., 2014, 50, 2572–2574 RSC
. - X. Sheng, N. Li, G. Li, W. Wang, J. Yang, Y. Cong, A. Wang, X. Wang and T. Zhang, Sci. Rep., 2015, 5, 9565 CrossRef CAS PubMed
. - W. Wang, N. Li, G. Li, S. Li, W. Wang, A. Wang, Y. Cong, X. Wang and T. Zhang, ACS Sustainable Chem. Eng., 2017, 5, 1812–1817 CrossRef CAS
. - Q. Deng, G. Nie, L. Pan, J.-J. Zou, X. Zhang and L. Wang, Green Chem., 2015, 17, 4473–4481 RSC
. - X. Zhang, Q. Deng, P. Han, J. Xu, L. Pan, L. Wang and J.-J. Zou, AIChE J., 2017, 63, 680–688 CrossRef CAS
. - Q. Deng, P. Han, J. Xu, J.-J. Zou, L. Wang and X. Zhang, Chem. Eng. Sci., 2015, 138, 239–243 CrossRef CAS
. - Q. Deng, J. Xu, P. Han, L. Pan, L. Wang, X. Zhang and J.-J. Zou, Fuel Process. Technol., 2016, 148, 361–366 CrossRef CAS
. - J. N. Chheda, G. W. Huber and J. A. Dumesic, Angew. Chem., Int. Ed., 2007, 46, 7164–7183 CrossRef CAS PubMed
. - L. Faba, E. Diaz and S. Ordonez, ChemSusChem, 2013, 6, 463–473 CrossRef CAS PubMed
. - J. Yang, N. Li, G. Li, W. Wang, A. Wang, X. Wang, Y. Cong and T. Zhang, ChemSusChem, 2013, 6, 1149–1152 CrossRef CAS PubMed
. - J. Yang, N. Li, S. Li, W. Wang, L. Li, A. Wang, X. Wang, Y. Cong and T. Zhang, Green Chem., 2014, 16, 4879–4884 RSC
. - R. E. O'Neill, L. Vanoye, C. De Bellefon and F. Aiouache, Appl. Catal., B, 2014, 144, 46–56 CrossRef
. - K. A. M. a. R. B. Moore, Chem. Rev., 2004, 104, 4535–4586 CrossRef
. - R. Weingarten, G. A. Tompsett, W. C. Conner and G. W. Huber, J. Catal., 2011, 279, 174–182 CrossRef CAS
. - M. Cadenas, R. Bringué, C. Fité, E. Ramírez and F. Cunill, Top. Catal., 2011, 54, 998–1008 CrossRef CAS
. - J. Jae, G. A. Tompsett, A. J. Foster, K. D. Hammond, S. M. Auerbach, R. F. Lobo and G. W. Huber, J. Catal., 2011, 279, 257–268 CrossRef CAS
. - D. S. Noyce and W. A. Pryor, J. Am. Chem. Soc., 1955, 77, 1397–1401 CrossRef CAS
. - S. K. R. Patil, J. Heltzel and C. R. F. Lund, Energy Fuels, 2012, 26, 5281–5293 CrossRef CAS
. - S. K. R. Patil and C. R. F. Lund, Energy Fuels, 2011, 25, 4745–4755 CrossRef CAS
. - I. van Zandvoort, Y. Wang, C. B. Rasrendra, E. R. H. van Eck, P. C. A. Bruijnincx, H. J. Heeres and B. M. Weckhuysen, ChemSusChem, 2013, 6, 1745–1758 CrossRef CAS PubMed
.
Footnote |
† Electronic supplementary information (ESI) available. See DOI: 10.1039/c7ra02396k |
|
This journal is © The Royal Society of Chemistry 2017 |
Click here to see how this site uses Cookies. View our privacy policy here.