DOI:
10.1039/C7RA00052A
(Paper)
RSC Adv., 2017,
7, 7293-7302
Toward high-performance poly(para-phenylene terephthalamide) (PPTA)-based composite paper via hot-pressing: the key role of partial fibrillation and surface activation
Received
3rd January 2017
, Accepted 12th January 2017
First published on 23rd January 2017
Abstract
The inert surface of para-aramid fibers makes para-aramid fiber-based composites suffer from a poor interfacial interaction and limited physical properties. In this work, the influence of hot-pressing on paper structural properties was explored. Without hot-pressing, in comparison with the fibrid paper (Paper-I), the addition of para-aramid chopped-fiber obviously enhanced mechanical properties, but led to slight damage of the dielectric properties of the fiber/fibrid paper (Paper-II) because of voids and defects. After hot-pressing, it was noteworthy that the increased mechanical properties and dielectric properties of the papers were mainly due to the individual pressing treatment and independent of the individual heating treatment. Interestingly, the combined treatment of heating and pressing shows a synergistic effect and results in an increase of paper compactness especially for Paper-II. Meanwhile, the interfacial interaction between different fibers in the composite papers was greatly improved, which is mainly associated with the partial dissociation into a fibrillar structure and the improved surface activation of para-aramid chopped fibers. Therefore, fiber micro-fibrillation is highly effective for improving internal bonding and optimizing physical properties for para-aramid-based composite papers.
1 Introduction
Polymer-based composites have gained great interest from both the academic community and industrial engineers due to their easy processing and multifunctional properties.1–3 Poly(para-phenylene terephthalamide) (PPTA)-based papers have also achieved extensive applications; they are mostly used as insulation materials and honeycomb-structured materials,4 covering aerospace technologies,5–7 telecommunication, transportation and even weapon manufacturing owing to their exceptional properties including high mechanical strength, good heat resistance, and favorable insulation properties.8–15 In general, conventional aramid paper consists of aramid pulp and chopped fibers and is popular in many high value-added applications.16–18
PPTA fibrid, a newly-developed special product of aramid fibers, is generally manufactured through a precipitation process by applying high shear on the aramid solution in its non-solvent.19,20 PPTA fibrid thus inherits many advantages such as high mechanical strength, good heat resistance and favorable papermaking property.21 Due to its large specific surface area, better flexibility, and dispersion stability in water, PPTA fibrid is suitable for making PPTA paper-based composite and can be used to replace the PPTA pulp.21 Indeed, our previous work demonstrates a successful property optimization including improved papermaking property and enhancement in mechanical strength for aramid chopped fiber/fibrid composite paper in comparison with conventional aramid chopped fiber/pulp composite paper.22,23 However, the aramid fiber/fibrid composite paper still needs further optimization in paper properties including mechanical properties and insulation properties to extend its applications.24–26
Since the chopped fiber surface is smooth and has less chemical reactive groups, changing the inert surface and improving surface activity of the aramid chopped fiber is of great importance.8,27–29 Previous reports have made great efforts including chemical etching by mixed acids,30 ionization, surface irradiation by plasma,31–34 ultrasonic treatment, chemical grafting methods,35–37 and fluorinated modification of the molecular chains38 and other approaches.35,39–41 For instance, phosphoric acid treatment on PPTA showed increasing content of surface functional groups but resulted in a declined mechanical property of PPTA fibers.42–44 Gas plasma treatment on Kevlar fibers caused remarkably improved interfacial shear strength (IFSS) between the fiber and epoxy resin during pull-out tests.31 But the densities of active groups in resultant fibers are still not homogeneous or rich. Recently, Liu and his co-workers have realized direct fluorination of para-aramid fibers which led to surface chain cleavage behavior and even covalent modification on the surface of aramid fibers.41 The direct fluorination process needs complex reaction conditions.45–47 In a word, some approaches cannot directly achieve surface activation in high-efficiency or high density of functional groups without sacrificing the high property or integrity of chemical structure in PPTA fiber, while the others needs special reaction technology and can only be achieved under harsh conditions.48,49 Besides, hot-pressing under appropriate condition has been also demonstrated to significantly enhance the mechanical properties as well as the insulation properties of PPTA-based papers. Obviously, it is an easy and convenient method for modification of PPTA-based papers in comparison with the aforementioned approaches. In addition, hot-pressing also induces some morphological changes for para-aramid fibers and para-aramid fibrids. Unluckily, the reinforcing mechanism of hot-pressing is not clearly elucidated.
Hence, the objective of this work was to systematically investigate the effect of post-treatment through hot-pressing on paper structural properties. For this purpose, two different modes, namely, individual heating or pressing treatment and combined heating/pressing treatment were applied during hot-pressing. The important properties including mechanical properties and insulation properties were discussed. At the same time, we also focused on the reinforcing mechanisms and paper structural changes of para-aramid fiber-based papers with the aid of hot-pressing. Hopefully, the results can give a deep insight into the structure–property relationship of PPTA-based papers during hot-pressing and enrich the knowledge of reinforcing mechanisms for PPTA-based papers.
2 Experimental
2.1 Materials and papermaking process
para-Aramid chopped fiber with average diameters of 12 μm and length of 4–5 mm was purchased from Hebei Guigu Chemical company. para-Aramid fibrid was provided by Teijin Company. The aramid chopped fiber/fibrid composite paper was prepared according to TAPPI standard T 205 sp-95.50,51 As shown in Fig. 1, firstly, to prepare the uniform pulp suspension at 0.1% consistency, a mixture of aramid chopped fiber and fibrid at the mass ratio of 7
:
3 was disintegrated in water via a standard disperser. Then, the aramid chopped fiber/fibrid composite paper was prepared by an ERNST HAAGEBBS-3 sheet formation machine, and the target grammage of produced sample was set as 45 g m−2. To obtain dried chopped fiber/fibrid composite paper, the formed wet-sample was pressed at 0.04 MPa for 3 min and then was dried at 105 °C for 5 min. Subsequently, a hot-pressing machine was employed for post-treating on the composite papers. For comparison, para-aramid fibrid paper was also prepared under the same condition as a reference sample. For simplicity, the reference sample was named as Paper-I and the composite paper was named as Paper-II.
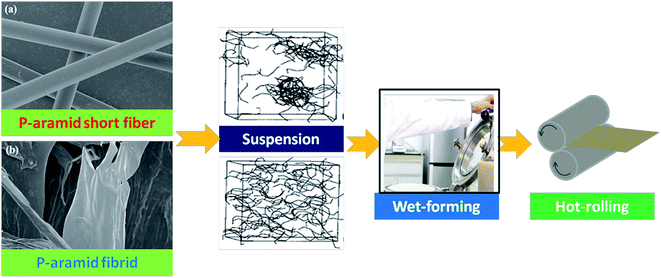 |
| Fig. 1 Sketch of the papermaking process and post-treatment with the aid of hot pressing for PPTA-based papers. | |
2.2 Characterization
The mechanical properties of PPTA-based papers were determined via the measurement of tensile index and tearing index by a L&W SE-062 tensile strength tester and a TMI tearing strength tester according to TAPPI standard T 494 om-88 and T411 om-97, respectively. Before that, the specimens for tensile testing were cut into a rectangular shape, which possesses dimensions of 15 × 100 mm2 with a thickness of ∼0.06 mm. To evaluate the insulation property of aramid chopped fiber/fibrid composite paper, the measurement of electrical breakdown strength was performed on a CS2672D dielectric strength tester according to ASTM D149 standard.
The surface morphologies of aramid chopped fiber/fibrid composite paper with and without post-treatment were characterized by S-4800 field emission scanning electron microscope (SEM) (Hitachi, Japan) with the operation voltage of 3 kV. Prior to analysis, produced samples were coated with the platinum layer to provide the conductivity for impinging electrons. A LEICA super depth field microscope (Germany) was used to observe the fracture surface of original and post-treated PPTA-based papers.
X-ray Photoelectron Spectroscopy (XPS) analysis was carried out using a Kratos ASMA 800 spectrometer (Kratos Analytical Ltd., UK) equipped with Al Kα X-ray source. During the test, the X-ray operation power as 450 W and the vacuum chamber pressure was maintained at the range of 10−8 to 10−9 Torr.
3 Results and discussion
3.1 The influence of heating and pressing on physical property of PPTA-based papers
In order to explore the key parameter in hot-pressing, the effect of individual heating treatment or individual pressing treatment on the mechanical properties and insulation properties were investigated. Fig. 2 shows the representative mechanical properties and insulation properties of two kinds of aramid fiber paper when solely treated either by heating at different temperatures or applying different pressure. Firstly, it can be found that individual heating or pressing treatment can significantly enhance the tensile strength and the tearing strength of the composite paper in comparison with Paper-I. The insulation property of Paper-II is lower than that of Paper-I which is mainly due to defects and decreased paper compactness caused by the introduction of chopped fibers. With changing heating temperature, the insulation property of both Paper-I and Paper-II remains unchanged. Hence, to achieve an overall property, emphasis should be taken on the balance between the mechanical property enhancement and insulation property deduction by using appropriate temperature and/or pressure during hot-pressing. Secondly, the mechanical property and insulation property of Paper-I and Paper-II were compared when concerning temperature increment or pressure increment. It was found that individual heating treatment is indeed in favor of tensile property enhancement, i.e., increasing from ∼15 MPa to ∼35 MPa. But with increasing temperature, it is less effective to further enhance the tensile strength of Paper-I and Paper-II. However, when increasing pressure especially at high pressure value (>0.3 MPa), the tensile strength further increases to a high level of ∼45 MPa while the tearing strength of Paper-II decreases to ∼18 MPa which is still comparable with the value of only heating-treated paper. Interestingly, applying pressure can enhance insulation property remarkably though Paper-II shows a weaker insulation property than Paper-I. In addition, with increasing pressure, the insulation property can be further increased. Overall, the mechanical property improvement and depression of insulation property for Paper-II is insensitive to temperature variation during heating treatment. High pressure along with constant thermal condition is potentially favorable for enhancing the tensile strength and electrical property, that is, a balanced property. It can be concluded that the increased mechanical properties and dielectric properties of both Paper-I and Paper-II were dominated by individual pressing treatment but independent on individual heating treatment.
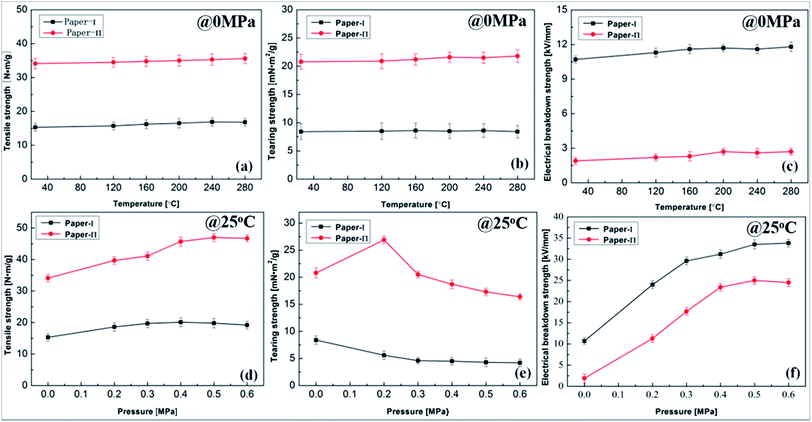 |
| Fig. 2 The effect of individual heating and pressing treatment on the mechanical properties and insulation properties of PPTA-based papers. | |
For a clear comparison, the combined effect of heat and pressure on the mechanical properties and insulation properties of these papers were further investigated. As shown in Fig. 3, two different modes were implemented. The first case is that high pressure is considered as a basic condition and the effect of temperature variation at a fixed pressure of 0.4 MPa was investigated. The tensile strength and dielectric strength of Paper-II begin to be sensitive to temperature variation. With increasing temperature from 40 °C to 260 °C, the tensile strength of Paper-II gradually increases to ∼55 MPa and the dielectric strength of Paper-II also increases from 2 kV mm−1 to 27 kV mm−1. It is noteworthy that the tensile strength and dielectric strength of Paper-II treated by heating at fixed pressure are larger than those of Paper-II treated by individual heating or pressing, showing a great synergistic effect. In addition, the tensile strength and dielectric strength of Paper-I is also enhanced under the same treating condition. The second case is to change pressure at a fixed temperature of 240 °C. Similarly, a further property enhancement was also achieved, that is, Paper-II with tensile strength of ∼55 MPa and dielectric strength of ∼25 kV mm−1 and Paper-I with tensile strength of ∼22 MPa and dielectric strength of ∼37 V mm−1. Though a slight decrease of the tearing strength and the dielectric strength for these PPTA-based papers were observed especially at high pressure, a synergistic effect of heating and pressing on property enhancement of papers was also obvious when changing pressure at fixed temperature.
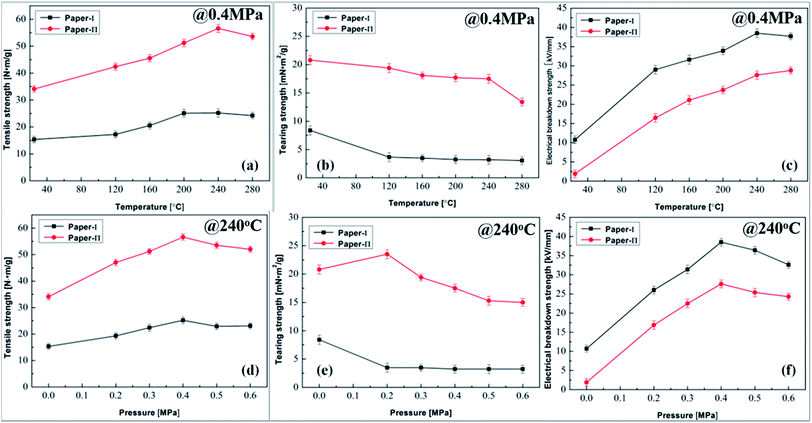 |
| Fig. 3 The combined heating and pressing treatment on the mechanical properties and insulation properties of PPTA-based papers. | |
To present a clear evidence of synergistic effect of heating and pressing, the best performance of Paper-I and Paper-II obtained under different conditions were summarized and compared as can be seen from Fig. 4. For Paper-I, it can be found that it achieves a further increase of 27% in tensile strength and 15% in dielectric strength as well as a comparable tearing strength when treated by combined heating and pressing in comparison with individual pressing-treated case. Correspondingly, Paper-II also achieves a further increase in tensile strength and dielectric strength as well as similar tearing resistance in a same way. Overall, through combined heating and pressing treatment, the synergistic effect endows Paper-II a superhigh performance with tensile strength of 56.6 MPa, tearing strength of 15.0 MPa and dielectric strength of 27.6 kV mm−1, namely a comprehensive increase in comparison with those of Paper-I.
 |
| Fig. 4 Summary of the best performance for PPTA-based paper obtained under different treating conditions: (a) Paper-I; (b) Paper-II. | |
3.2 The influence of hot pressing on paper structures in PPTA-based papers
In the pursuit of high-performance PPTA-based papers, previous experimental and theoretical investigations have pointed out that the fiber–fiber joint and fiber–fibrid interactions play key roles in enhancing paper performance. In order to investigate the effect of hot-pressing process on aramid-based paper structures, morphological changes, fracture surfaces and internal bonding strength of papers after post-treatment via hot-pressing were systematically analyzed. Fig. 5 presents morphological details in Paper-I (control sample) before and after post-treatment. Post-treatment is in great favor for physical connections between different fibrids as can be seen that the surface became smooth and defects were greatly improved.
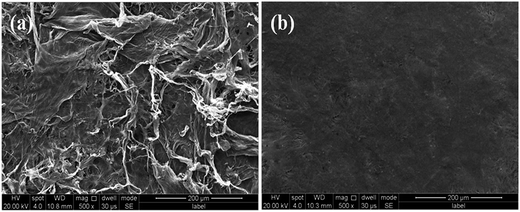 |
| Fig. 5 Morphological changes of Paper-I during heating/pressing treatment: (a) before post-treatment; (b) after post-treatment. | |
Fig. 6 shows morphological details in Paper-II before and after post-treatment. Before post-treatment, Paper-II presents rough surface and porous structure which indicates a loosely-packed network structure with large pores. In addition, the aramid chopped fiber shows a smooth surface and aramid fibrid retains its pristine flexible morphology. Fig. 6a shows several patterns for aramid chopped fibers and aramid fibrids. The aramid fibrid are inclined to deposit on the chopped fiber while the introduction of aramid chopped fiber destructs joint effect between different fibrids, leading to a large quantity of pores and defects in the paper.
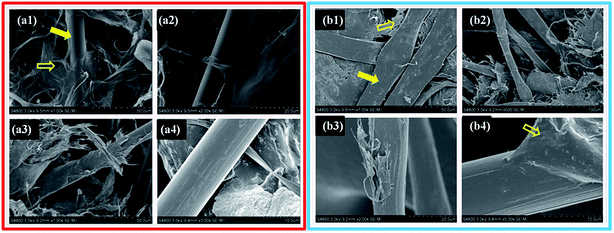 |
| Fig. 6 Morphological changes of Paper-II during the combined heating/pressing treatment: (a1–a4) before post-treatment; and (b1–b4) after post-treatment. Note: solid arrow indicates fibers while hollow arrow represents fibrid. | |
Hence, mechanical performance of Paper-II is strongly depending on the interaction between aramid chopped fiber and aramid fibrid. In this case, Paper-II shows randomly overlapped short fiber along with some fiber surrounded by aramid fibrid mainly due to physical adhesion. After post-treatment as can be seen in Fig. 6b, the treated paper achieves smooth surface with decreased pore size, resulting in increased paper compactness. In addition, the deformed aramid chopped fiber is in favor of interconnection between aramid chopped fiber and aramid fibrid. The aramid fibrid is inclined to wrap closely on the surface of aramid chopped fibers. Therefore, post-treatment favors paper compactness and the interfacial adhesion between aramid chopped fiber and aramid fibrid.
Subsequently, fracture surface of aramid-based papers was examined to roughly estimate interfacial adhesion strength. Optical images for fracture surfaces of these papers can be found in Fig. 7. It was found that the chopped fibers are pulled out easily for Paper-II without post-treatment, while fiber fracture occurs for Paper-II after post-treatment. It indicates greatly enhanced interfacial adhesion strength because of post-treatment, which is advantageous for stress transferring and paper's final performance.
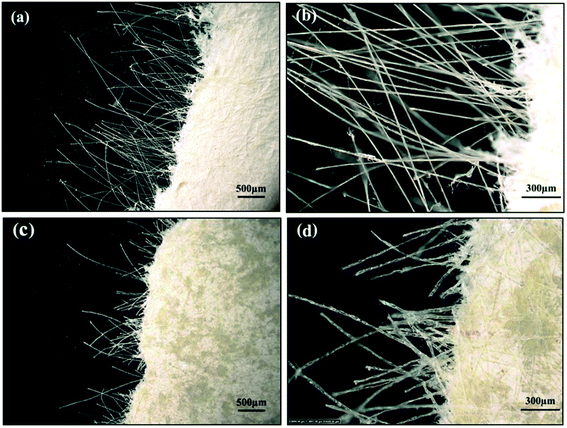 |
| Fig. 7 The fracture surface of Paper-II during the combined heating/pressing treatment: (a) and (b) without post-treatment; (c) and (d) after post-treatment. | |
In order to quantitatively analyze the effect of the combined heating/pressing treatment on internal adhesion, “Scott interlayer bonding strength” was used. Fig. 8 presents interlayer bonding strength of PPTA-based papers as a function of temperature or pressure. In comparison with Paper-I, the introduction of aramid chopped fiber decreases the interlayer bonding strength. As shown in Fig. 8a, with increasing temperature at fixed pressure of 0.4 MPa, interlayer bonding strength of both Paper-I and Paper-II continuously increases to a high level. When increasing pressure at fixed temperature of 240 °C, interlayer bonding strength increase slowly at low pressure but increasing abruptly when the pressure reaches 0.3 MPa. And the interlayer bonding strength gradually reaches to a plateau when further increase pressure to 0.6 MPa. Overall, the interlayer bonding strength is indeed has positive effect on the resultant mechanical properties of aramid fibers. At the same time, the results indicate the possibility of microstructure and chemical changes of chopped fibers and fibrids induced by hot-pressing.
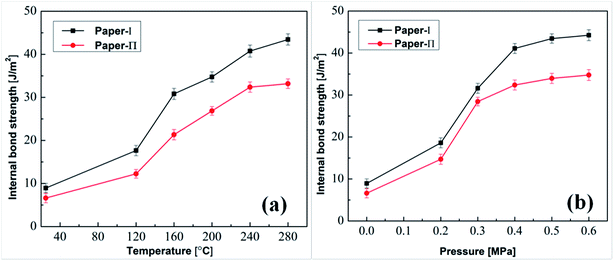 |
| Fig. 8 Interlayer bonding strength of Paper-I and Paper-II under two different treatment conditions: (a) as a function of treatment temperature at a fixed pressure of 0.4 MPa; (b) as a function of treatment pressure at a fixed temperature of 240 °C. | |
3.3 The influence of hot-pressing on chemical structure and microstructures of aramid choped fiber and aramid fibrid
XPS can be used to evaluate the chemical structural changes of aramid chopped fiber and aramid fibrid after the combined heating/pressing treatment. For aramid chopped fiber without treatment (Fig. 9a), there are three peaks indicating –C–C– group (284.9 eV), –C–N– group (286.9 eV) and –C
O group (290.6 eV), respectively. After heating/pressing treatment, a new peak emerges, representing the existence of –C–O– group (287.8 eV). As can be seen in Table 1, the ratio for oxygen-containing groups gradually increases from 7.17% to 31.87% while the ratio for –C–C– group decreases from 68.61% to 30.76% after heat/pressure treatment. This is mainly attributed to that intra-molecular bonding (hydrogen bonding) in aramid chopped fiber is destructed and finally activates the inert surface of aramid chopped fiber. For aramid fibrid, it changes in a totally different way. Before heating/pressing treatment (Fig. 9c), aramid fibrid possesses four different peaks representing –C–C– group (284.6 eV), –C–N– group (285.9 eV), –C–O– group (287.7 eV) and –C
O (288.8 eV), respectively. After heating/pressing treatment on aramid fibrid (Fig. 9d), the peak for –C–O– group disappears. Seen from Table 1, the ratio for –C
O group increases from 11.06% to 17.56%. The increasing number of –C
O group means potential hydrogen-bonding interaction with aramid chopped fiber. Hence, heating/pressing treatment can increase surface activation of aramid chopped fiber and aramid fibrid and thus increasing their interfacial adhesion strength.
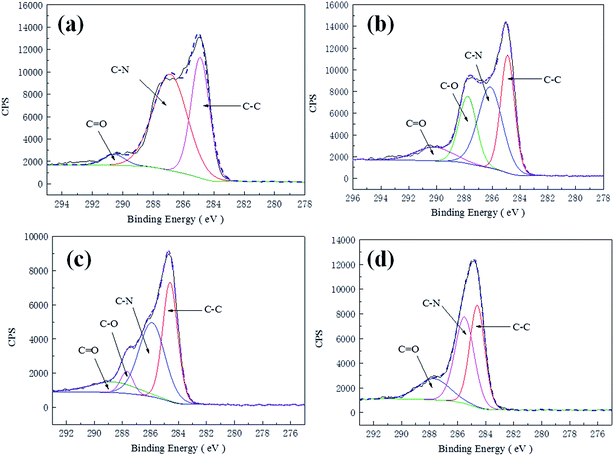 |
| Fig. 9 XPS spectra of aramid chopped fiber and aramid fibrid. (a) Chopped fiber before hot-pressing; (b) chopped fiber after hot-pressing; (c) fibrid before hot-pressing; and (d) fibrid after hot-pressing. | |
Table 1 Surface functional groups of aramid chopped fiber and aramid fibrid before and after the combined heating/pressing treatment
|
The ratio for functional groups [%] |
–C–C– |
–C–N– |
–C–O– |
–C O |
Fiber-before |
68.61 |
24.22 |
— |
7.17 |
Fiber-after |
30.76 |
37.37 |
22.30 |
9.57 |
Fibrid-before |
43.13 |
39.58 |
6.22 |
11.06 |
Fibrid-after |
42.90 |
39.54 |
— |
17.56 |
3.4 The mechanism for the realization of high performance PPTA-based paper via hot-pressing
In order to further explore the reason for mechanical property enhancement in PPTA-based papers, the morphological changes of aramid chopped fiber in related with pressure increment during the combined heating/pressing treatment were presented in Fig. 10. Relying on the intermolecular hydrogen-bonding interaction, molecular chains of PPTA can pack in a same crystalline plane. Due to the weak van der Waals force, lateral pressure can destruct the fiber structure and forming fibrillar structure.16,52,53 For original aramid chopped fiber, it shows a uniform cylindrical form with smooth surface. As mentioned above, Paper-II is strongly sensitive to the pressure especially during the combined heating/pressing treatment. At low pressure, the aramid chopped fiber shows great deformation and becomes ribbon-like films, indicating a flattening process. When the pressure further increases, the aramid chopped fiber starts to crack and gives rise to a large quantity of fibrils, which is a partial dissociation process. At high pressure (such as 0.6 MPa), it can be seen that some fibrils become separated with ultrahigh aspect ratio, i.e., a partial fibrillation process. These fibrils are thus highly effective for mechanical reinforcement. As a result, partial fibrillar structure induced by the combined heating/pressing treatment is in great favor of the resultant mechanical property.
 |
| Fig. 10 Flattening, partial dissociation and partial-fibrillation process for the aramid chopped fiber under the combined heating/pressing treatment with increasing pressure: (a) the pristine aramid chopped fiber; (b) flattened fiber; (c) partial dissociated fiber; (d) partial fibrillated fiber. | |
Fig. 11 summarized the paper structural properties of para-aramid fiber/fibrid composite papers. Two important components, namely, fiber and fibrid, have experienced great changes in morphologies and chemical structures due to hot-pressing especially the combined heating/pressing treatment. It was found that low pressure along with heating treatment induces flattening process, leading to strips of para-aramid fibers with smooth surface. Increased pressure can gradually induce partial dissociation and even partial fibrillation, indicating a high aspect ratio and greatly improved surface activity of aramid fibers. At the same time, fibrids can achieve high surface activity after hot-pressing, thus giving rise to an enhanced interfacial adhesion between aramid fibers and fibrids. Hence, Paper-II can finally achieve a super high mechanical property after hot-pressing. Nevertheless, the existence of pores and defects are bad for the insulation properties. As a result, the dielectric strength of Paper-I is higher than that of Paper-II. With the help of hot-pressing, paper compactness is remarkably increased and thus results in a further increase of insulation properties for both Paper-I and Paper-II. Therefore, Paper-II achieves a comprehensive improvement in mechanical properties as well as insulation properties.
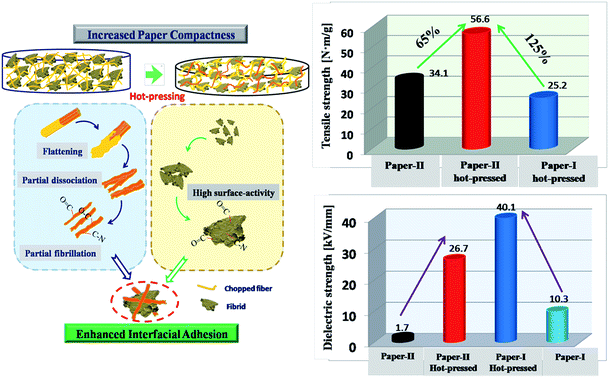 |
| Fig. 11 Schematic profile for improving the overall physical properties of PPTA-based paper with the aid of hot-pressing process. | |
4 Conclusion
In summary, the effect of hot-pressing on mechanical properties and insulating properties of para-aramid-based composite papers were studied. The results showed that hot-pressing is in great favor for enhancement of mechanical properties and insulation properties for both Paper-I and Paper-II. The mechanical properties and insulation properties are independent on individual heating treatment and are mainly dominated by individual pressing treatment. Meanwhile, the combined treatment of heating and pressing caused a synergistic effect, namely, further increasing the mechanical properties and insulation properties for both papers especially for Paper-II. Furthermore, the combined treatment also resulted in an increase of the paper compactness and the interfacial interaction between different fibers, all of which are mainly attributed to the flattening and even partial dissociation into fibrillar structure of para-aramid chopped fibers, and thus giving rise to enhanced surface activation, improved internal bonding and optimized mechanical and insulation properties for para-aramid fiber-based papers.
Acknowledgements
The authors would like to acknowledge the financial support from the National Key Research and Development Plan (2016YFB0303304), State Key Laboratory of Pulp and Paper Engineering (201333), the National Natural Science Foundation of China (Project: 51402180).
References
- J. Gu, C. Liang, X. Zhao, B. Gan, H. Qiu, Y. Guo, X. Yang, Q. Zhang and D. Y. Wang, Compos. Sci. Technol., 2017, 139, 83–89 CrossRef CAS.
- Y. Zhao, Y. Zhu, G. Sui, F. Chen and Q. Fu, Polymer, 2017, 109, 137–145 CrossRef CAS.
- J. Gu, X. Yang, C. Li and K. Kou, Ind. Eng. Chem. Res., 2016, 55, 10941–10946 CrossRef CAS.
- J. Kratz and P. Hubert, Composites, Part A, 2015, 72, 219–227 CrossRef CAS.
- N. Ni, Y. Wen, D. He, X. Yi, T. Zhang and Y. Xu, Composites, Part B, 2016 DOI:10.1016/j.compositesb.2016.01.042.
- J. Gu, X. Yang, Z. Lv, N. Li, C. Liang and Q. Zhang, Int. J. Heat Mass Transfer, 2016, 92, 15–22 CrossRef CAS.
- J. Gu, X. Meng, Y. Tang, Y. Li, Q. Zhuang and J. Kong, Composites, Part A, 2017, 92, 27–32 CrossRef CAS.
- H. F. Zhao, M. Y. Zhang, S. F. Zhang and J. B. Lu, Polym.-Plast. Technol. Eng., 2012, 51, 134–139 CrossRef CAS.
- S. Hayashida, in High-Performance and Specialty Fibers: Concepts, Technology and Modern Applications of Man-Made Fibers for the Future, ed. S. The Society of Fiber and J. Techno, Springer, Japan, Tokyo, 2016, pp. 149–169 Search PubMed.
- H. A. Every, G. J. M. Janssen, E. F. Sitters, E. Mendes and S. J. Picken, J. Power Sources, 2006, 162, 380–387 CrossRef CAS.
- L. R. Yao, W. T. Zhao, S. Q. Xu and Q. L. Sum, in Silk, Protective Clothing and Eco-Textiles, ed. L. Bai and G. Q. Chen, Trans Tech Publications Ltd, Stafa-Zurich, 2013, vol. 796, pp. 290–293 Search PubMed.
- P. Gopal, L. R. Dharani and F. D. Blum, Wear, 1996, 193, 199–206 CrossRef CAS.
- M. Grujicic, W. C. Bell, P. S. Glomski, B. Pandurangan, C.-F. Yen and B. A. Cheeseman, J. Mater. Eng. Perform., 2011, 20, 1401–1413 CrossRef CAS.
- J. A. Mohandesi, A. Sangghaleh, A. Nazari and N. Pourjavad, Comput. Mater. Sci., 2011, 50, 1619–1624 CrossRef CAS.
- J. Gu, N. Li, L. Tian, Z. Lv and Q. Zhang, RSC Adv., 2015, 5, 36334–36339 RSC.
- B. Yang, Z. Q. Lu, M. Y. Zhang, Y. J. Liu and G. D. Liu, J. Appl. Polym. Sci., 2016, 133, 43209–43215 Search PubMed.
- J. Fan, Z. Shi, M. Tian and J. Yin, RSC Adv., 2013, 3, 17664–17667 RSC.
- X. Li, F. Tian, P. Zhou, C. Yang, X. Li, F. Bian and J. Wang, RSC Adv., 2016, 6, 81552–81558 RSC.
- L. Yao, K. Kim and J. Kim, Fibers Polym., 2012, 13, 277–281 CrossRef CAS.
- J. K. Wan, H. Y. Lee, B. Baek and S. C. Yong, Text. Sci. Eng., 2015, 52, 26–34 CrossRef.
- H. F. Zhao, Y. B. Zhu and L. Z. Sha, e-Polymers, 2014, 14, 351–362 CrossRef.
- S. F. Zhang, M. Y. Zhang and K. C. Li, Appita J., 2010, 63, 58–64 CAS.
- S. Zhang, M. Zhang and K. Li, Poly. Bull., 2011, 66, 351–362 CrossRef CAS.
- H. Song, Y. Wang, G. L. Xu and J. Hu, Preparation of phenolic resin for strengthening aramid paper, CRC Press-Taylor & Francis Group, Boca Raton, 2015, vol. 42, pp. 5937–5946 Search PubMed.
- Z. Sun, S. Shi, X. Hu, X. Guo, J. Chen and H. Chen, Composites, Part B, 2015, 77, 38–45 CrossRef CAS.
- J. Gu, C. Liang, J. Dang, W. Dong and Q. Zhang, RSC Adv., 2016, 6, 35809–35814 RSC.
- Y. Rao, A. J. Waddon and R. J. Farris, Polymer, 2001, 42, 5937–5946 CrossRef CAS.
- C. Li, Q. Zhen, Z. Luo and S. J. Lu, J. Appl. Polym. Sci., 2015, 132, 307–315 Search PubMed.
- S. Yang, L. Li, T. Xiao, D. Zheng and Y. Zhang, Appl. Surf. Sci., 2016, 383, 142–150 CrossRef CAS.
- A. Castro-Muñiz, F. Suárez-García, A. Martínez-Alonso and J. M. D. Tascón, J. Colloid Interface Sci., 2011, 361, 307–315 CrossRef PubMed.
- L. X. Xing, L. Liu, Y. D. Huang, D. W. Jiang, B. Jiang and J. M. He, Composites, Part B, 2015, 69, 50–57 CrossRef CAS.
- Y. Y. Chu, X. G. Chen, D. W. Sheel and J. L. Hodgkinson, Text. Res. J., 2014, 84, 1288–1297 CrossRef CAS.
- C. X. Jia, P. Chen, Q. Wang, J. Wang, X. H. Xiong and K. M. Ma, Polym. Compos., 2016, 37, 620–626 CrossRef CAS.
- M. Pykönen, H. Sundqvist, J. Järnström, O.-V. Kaukoniemi, M. Tuominen, J. Lahti, J. Peltonen, P. Fardim and M. Toivakka, Appl. Surf. Sci., 2008, 255, 3217–3229 CrossRef.
- C. X. Wang, M. Du, J. C. Lv, Q. Q. Zhou, Y. Ren, G. L. Liu, D. W. Gao and L. M. Jin, Appl. Surf. Sci., 2015, 349, 333–342 CrossRef CAS.
- X. Qian, R. Zou, Q. OuYang, X. Wang and Y. Zhang, Appl. Surf. Sci., 2015, 327, 246–252 CrossRef CAS.
- L. Luo, Y. Wang, J. Huang, D. Hong, X. Wang and X. Liu, RSC Adv., 2016, 6, 62695–62704 RSC.
- Z. Cheng, P. Wu, B. Li, T. Chen, Y. Liu, M. Ren, Z. Wang, W. Lai, X. Wang and X. Liu, Appl. Surf. Sci., 2016, 384, 480–486 CrossRef CAS.
- H. Zhang, J. Zhang, J. Chen, X. Hao, S. Wang, X. Feng and Y. Guo, Polym. Degrad. Stab., 2006, 91, 2761–2767 CrossRef CAS.
- Y. Y. Sun, Q. Liang, H. J. Chi, Y. J. Zhang, Y. Shi, D. N. Fang and F. X. Li, Fibers Polym., 2014, 15, 1–7 CrossRef CAS.
- J. Gao, Y. Y. Dai, X. Wang, J. Y. Huang, J. Yao, J. Yang and X. Y. Liu, Appl. Surf. Sci., 2013, 270, 627–633 CrossRef CAS.
- L. Z. Sha and H. F. Zhao, Polymer, 2013, 37, 196–203 CAS.
- Z. Jia, Fibers Polym., 2013, 14, 59–64 CrossRef.
- J. H. Kim, N. Alan Heckert, S. D. Leigh, R. L. Rhorer, H. Kobayashi, W. G. McDonough, K. D. Rice and G. A. Holmes, Compos. Sci. Technol., 2014, 98, 93–99 CrossRef CAS.
- Z. Cheng, B. Li, J. Huang, T. Chen, Y. Liu, X. Wang and X. Liu, Mater. Des., 2016, 106, 216–225 CrossRef CAS.
- L. Luo, P. Wu, Z. Cheng, D. Hong, B. Li, X. Wang and X. Liu, J. Fluorine Chem., 2016, 186, 12–18 CrossRef CAS.
- Z. Cheng, B. Y. Li, J. Y. Huang, T. Chen, Y. Liu, X. Wang and X. Y. Liu, Mater. Des., 2016, 106, 216–225 CrossRef CAS.
- J. Lim, J. Q. Zheng, K. Masters and W. W. Chen, International Journal of Impact Engineering, 2011, 38, 219–227 CrossRef.
- D. B. Warheit, K. L. Reed, K. E. Pinkerton and T. R. Webb, Toxicol. Lett., 2002, 127, 259–267 CrossRef CAS PubMed.
- Z. Lu, M. Jiang, M. Zhang and X. Xia, J. Eng. Fibers Fabr., 2016, 11, 1–8 CrossRef PubMed.
- Y. Sun, Y. Wang, G. Xu, F. Cheng and J. Hu, Text. Res. J., 2016, 86, 1533–1542 CrossRef CAS.
- J. M. Zhang, Z. Mousavi, N. Soykeabkaew, P. Smith, T. Nishino and T. Peijs, ACS Appl. Mater. Interfaces, 2010, 2, 919–92653 CAS.
- W. Zhai, H. Liu, Z. Hong, W. Xie and B. Wei, Ultrason. Sonochem., 2017, 34, 130–135 CrossRef CAS PubMed.
|
This journal is © The Royal Society of Chemistry 2017 |
Click here to see how this site uses Cookies. View our privacy policy here.