DOI:
10.1039/C6RA27924D
(Paper)
RSC Adv., 2017,
7, 8034-8050
Tunable auto-combustion preparation of TiO2 nanostructures as efficient adsorbents for the removal of an anionic textile dye†
Received
8th December 2016
, Accepted 18th January 2017
First published on 23rd January 2017
Abstract
We have developed a new route for the synthesis of pure TiO2 nanostructures via a facile auto-combustion method followed by heat treatment. We have tuned the produced phases, morphologies, and crystallite sizes of the nano-sized TiO2 products through an auto-combustion method employing different fuels and various fuel-to-oxidant equivalence ratios, Φc. The as-synthesized products were analyzed by means of FE-SEM, FT-IR, XRD, TEM, BET, and thermal analyses. Interestingly, urea fuel at Φc = 1 generated a pure anatase TiO2 phase (U1) having almost the smallest crystallite size (11.9 nm) and the highest adsorption capacity (135 mg g−1) for the removal of Reactive Red 195 (RR195) dye from aqueous solutions. Moreover, the adsorption data could be described well using the pseudo-second-order kinetic and Langmuir isotherm models. Based on the calculated thermodynamic parameters: ΔH0 (1.343 kJ mol−1), ΔG0 (from −4.630 to −5.031 kJ mol−1), and Ea (18.46 kJ mol−1), the adsorption of RR195 dye on the as-prepared TiO2 nano-adsorbent is an endothermic, spontaneous, and physisorption process, respectively. Moreover, the as-prepared TiO2 adsorbent is a promising candidate for the removal of RR195 textile dye from aqueous media based on its reusability, high stability, and high adsorption capacity.
1. Introduction
Because of the environmental problems that water pollution may cause, a great number of researchers have devoted their efforts to the wastewater treatment research field. One of the serious sources of water pollution is the dying processing included in various industries such as paper, leather, plastic, rubber, and textile. These industries discharge large quantities of organic dyes into the water environment without pre-treatment.1–3 The discharged dyes, including reactive red dye, are non-biodegradable and chemically stable. In addition, these dyes are toxic and carcinogenic owing to the presence of azo groups (–N
N–) in their molecular structures.4 Besides, these dyes cause serious problems to human health such as irritation, respiratory issues chemical burns, ulcers, etc.5,6 Hence, the removal of the organic dyes (especially the textile dyes) from wastewaters is one of the critical necessities for human and environmental safety.
To date, physical, chemical, and biological methods have been proposed for the removal of the dyes from wastewaters. Therefore, several methods have been suggested for this purpose such as membrane separation, coagulation, ultra-sonication, photocatalysis, ozonation, biological treatment, and adsorption.7–14 Among these methods, adsorption was considered to be one of the most efficient techniques for the removal of non-biodegradable contaminants from wastewater owing to its simplicity in operation, high efficiency, economic applicability, scalability, and the availability of numerous adsorbents.15,16 In this vein, various adsorbent materials including natural and synthesized polymers, zeolites, activated carbons, hydrotalcites, and clays have been proposed for treatment of wastewater from textile dyes.1,17–19
Recently, various research groups have devoted their effort to searching for adsorbents with high surface areas, low-cost production, and non-toxic characteristics to the environment. The scientists found their way in nano-sized materials which have been regarded as an important type of adsorbent materials for the removal of heavy metals and organic pollutants from wastewater.2,4,20–23 However, reports on the removal of Reactive Red 195 (RR195) dye from wastewater are still limited.2,20 Besides, searching for the most suitable nano-adsorbent is still a challenge.
Meanwhile, titanium oxide and its composite nanostructures have been proved their efficiency as nano-adsorbents and/or nano-catalysts for the removal of some dyes from wastewater.24,25 So far, various methods have been developed for preparing TiO2 nanostructures such as hydrothermal,26,27 anodic oxidation,28 electrodeposition,29,30 microwave,31 sol–gel,27,32 chemical vapor deposition (CVD),33 and combustion methods.34,35 Among these methods, combustion route has been considered as one of the most efficient routes due to its low-cost production and scalability. However, reports on combustion synthesis of TiO2 nanoparticles are limited.34,35 In addition, combustion synthesis of titanium oxide nanostructures using TiCl4 precursor, tuning the produced TiO2 phase, and employing the produced TiO2 nanostructure as an adsorbent for the removal of Reactive Red 195 (RR195) dye have not been reported so far, to the best of our knowledge.
Therefore, in the present work, we report a facile auto-combustion synthesis of TiO2 nanostructures using a relatively inexpensive TiCl4 precursor, for the first time. The effect of the fuel type and fuel-to-oxidant equivalence ratio on the particle size, morphology, and produced TiO2 phase nanostructures were explored. The products were characterized using various spectroscopic tools. Investigation of the adsorption properties of the products showed high adsorption capacity of the as-synthesized TiO2 nanoparticles for the removal of Reactive Red 195 (RR195) dye (Scheme S1, ESI†), as an anionic textile dye. The kinetics and thermodynamics of the adsorption process, as well as the recyclability of the nano-adsorbent, were studied.
2. Experimental
2.1. Materials and reagents
Titanium tetrachloride (TiCl4), potassium chloride (KCl), sodium chloride (NaCl), urea (NH2CONH2), glycine (NH2CH2COOH), L-alanine (CH3CH(NH2)COOH), and TiO2 nanopowder (Degussa (P25)) were supplied by Sigma-Aldrich Company. Nitric acid (HNO3) was provided from Carlo Erba Company, France. Reactive Red 195 dye (RR195) (C31H19ClN7O19S6Na5; Scheme S1, ESI†) was purchased from Rushabh chemicals industries, India. All other reagents and chemicals were of analytical grade and employed as received without further purification.
2.2. Synthesis of TiO2 nanostructures using different fuels
An auto-combustion method was developed to synthesize TiO2 nanoparticles utilizing three different fuels: L-alanine, glycine, and urea. The produced TiO2 samples are referred to as A, G, and U, respectively. Notably, for the combustion process, the stoichiometric compositions of the redox blends are calculated according to that the total reducing (F) and oxidizing (O) valencies of the fuel and TiO(NO3)2, respectively, verify that Φc = (F/O) = 0.5, 1, 1.5, 2, and 2.5 (where, Φc is the equivalence ratio).8,36 Titanium chloride aqueous solution of a concentration of 2.2 M was prepared by diluting the purchased titanium tetrachloride (TiCl4) in cold HCl aqueous solution (4 M) under nitrogen gas atmosphere. The prepared 2.2 M titanium chloride solution was employed in the subsequent experiments. In a typical experiment: 10 mL of 2.2 M titanium chloride solution (22 mmol, 10 eq.) was diluted in cold bi-distilled water (100 mL). An aqueous ammonium hydroxide solution was then added slowly to a vigorously stirring and cold titanium chloride solution until pH reached 8.5. During this step, white precipitate of TiO(OH)2 was formed. The precipitate (TiO(OH)2) was collected by centrifugation, washed with water, and converted into in situ titanyl nitrate solution (TiO(NO3)2) by adding the least amount of concentrated nitric acid to the white suspension and letting the reaction blend stir at room temperature for 1 h. Solid urea (2.2 g, 36.67 mmol, 6 eq.), as fuel, was added to the titanyl nitrate solution and stirred for 10 min for complete dissolution. In this example, this quantity of the fuel was added so that the calculated Φc was maintained at 1 (i.e. (F/O) = 1). The auto-combustion process was then performed on a hot plate at about 300 °C for 10 min. The produced yellowish precursor was grounded and calcined in a muffle at 500 °C for 1 h to give TiO2 product referred to as U1. Similar experiments were repeated while different quantities of urea were used to have different Φc = (F/O) ratios of 0.5, 1.5, 2, and 2.5, and the produced products were named U0.5, U1.5, U2, and U2.5, respectively. The aforementioned combustion experiment was similarly repeated by employing different quantities of L-alanine and glycine fuels in such a way that Φc = (F/O) = 0.5, 1, 1.5, 2, and 2.5. The products were calcined at 500 °C for 1 h, and they were referred to as A0.5, A1, A1.5, A2, and A2.5 (for L-alanine fuel) and G0.5, G1, G1.5, G2, and G2.5 (for glycine fuel), respectively. Scheme 1 outlines the applied combustion processes.
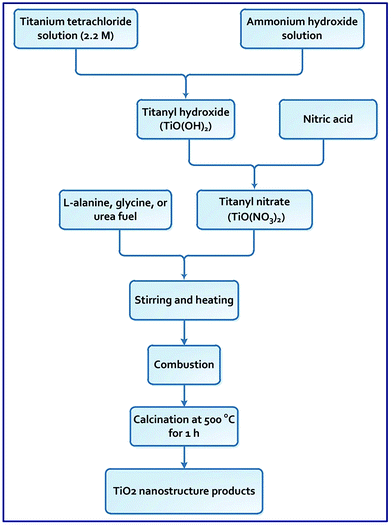 |
| Scheme 1 Schematic representation of the combustion process. | |
2.3. Materials characterization
The phase purity and structure of the as-synthesized products were characterized using powder X-ray diffraction (XRD) patterns collected by 18 kW diffractometer (Bruker; model D8 Advance) with monochromated Cu-Kα radiation (λ = 1.54178 Å). Morphology of the as-prepared materials was identified employing a field emission scanning electron microscope (FE-SEM) connected with a microscope (FE-SEM) (JEOL JSM-6500F) and a high-resolution transmission electron microscope (HR-TEM) (JEM-2100) at 200 kV accelerating voltage. FT-IR spectra of the products in the range of 4000–400 cm−1 were measured on FT-IR spectrometer (Thermo Scientific; model Nicolet iS10) using KBr pellets. Thermal properties of the as-prepared materials were studied using simultaneous thermogravimetric (TGA)/differential thermal analyzer (DTA) (Shimadzu; model TA-60WS, Japan). The samples were thermally studied under an atmosphere of nitrogen gas with 20 °C min heating rate. Platinum crucible and alumina powder reference were used for the measurements of the phase changes and weight losses of the sample, respectively. The UV-vis spectra were recorded on a UV-visible spectrophotometer (Jasco, model v670).
2.4. Adsorption studies
The adsorption properties of the as-synthesized TiO2 products were investigated by performing batch experiments in dark – to avoid the photocatalytic effect – using Reactive Red 195 dye (RR195) as a textile dye pollutant. The adsorption investigation was carried out using nano-sized TiO2 products generated from the combustion reaction using urea fuel at an equivalence ratio, Φc, of 1. In a typical batch adsorption experiment: 0.05 g of TiO2 nano-adsorbent was suspended in 25 mL of RR195 dye solution using a specific initial concentration (C0 = 100 mg L−1) at 25 °C temperature, pH 2, and 400 rpm stirring speed. Notably, pH of the dye solution was first adjusted using HCl and/or NaOH aqueous solutions (0.2 M) then TiO2 nanoparticles were added. The suspension was allowed to magnetically stir; then, at fixed contact time intervals, aliquots of the adsorption media were withdrawn and centrifuged to separate the TiO2 nano-adsorbent. We determined the residual dye concentration in the separated supernatant employing a pre-constructed calibration curve on a UV-vis spectrophotometer for RR195 dye at λmax = 542 nm. We determined the adsorption capacity (qt, mg g−1) of TiO2 adsorbent utilizing eqn (1). We also estimated the dye percent removal efficiency (% R) using eqn (2). |
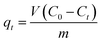 | (1) |
|
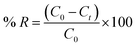 | (2) |
where, C0 (mg L−1) and Ct (mg L−1) are the initial dye concentration and concentration of the dye solution at time t of the adsorption process, respectively. Besides, V (L) and m (g) are the dye solution volume and mass of the TiO2 nano-adsorbent, respectively. Moreover, we have studied the different parameters influencing the adsorption process such as pH (1–10), contact time (5–240 min), initial dye concentration (50–500 mg L−1), temperature (298–318 K), and KCl dose (0.05–0.45 g). We estimated the equilibrium adsorption capacity (qe, mg g−1) of the TiO2 nano-adsorbent using eqn (3). |
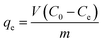 | (3) |
where, Ce (mg L−1) is the equilibrium dye concentration (i.e. the remaining dye concentration in the supernatant at equilibrium). The other terms of eqn (3) have the previously mentioned meaning.
3. Results and discussion
3.1. Auto-combustion synthesis and characterization of TiO2 nanoparticles
In our earlier investigation, we have prepared MgAl2O4 and MgO nanostructures via a combustion method using metal nitrate salts and various fuels.8 We found that the fuel type has a significant influence on the crystallite size of MgAl2O4 and MgO products, but we used only one equivalence ratio (Φc) value. Therefore, in this vein, we have extensively investigated the effect of fuel type and equivalence ratio (Φc) on the combustion of titanyl nitrate (oxidant). The study revealed that the type and quantity of the fuel have a remarkable impact on the product composition, crystal size, and morphology, as it will be shortly discussed. Hence, TiCl4 as a relatively inexpensive material was converted into TiO(NO3)2.37,38 The combustion reactions were performed using the in situ generated TiO(NO3)2 as an oxidizer and L-alanine, glycine, and urea as fuels, separately. Moreover, different fuel-to-oxidant equivalence ratios (Φc): 0.5, 1, 1.5, 2, and 2.5, have been examined to produce the most appropriate TiO2 nanoparticles for the removal of RR195 textile dye from aqueous media. The combustion reactions of TiO(NO3)2 and different fuels: L-alanine, glycine, and urea, separately, at Φc = 1, as a representative example, can be proposed as given in Scheme 2. The ignited and calcined products were identified by means of XRD, SEM, TEM, FR-IR, TGA/DTA, and BET analyses.
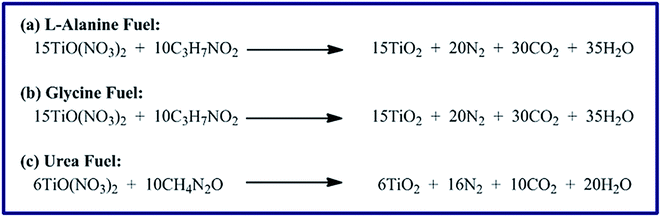 |
| Scheme 2 The proposed combustion reactions of titanyl nitrate with L-alanine, glycine, and urea fuels. | |
3.1.1. XRD investigation. The crystallinity and phase compositions of the combustion synthesized products were identified employing the X-ray diffraction technique. Fig. S1 (ESI†), S2 (ESI†) and (1) exhibit the XRD patterns of the calcined products: (A0.5–A2.5), (G0.5–G2.5), and (U0.5–U2.5), prepared via a combustion process using L-alanine, glycine, and urea fuels, respectively. Inspection of these XRD figures revealed that the fuel and its quantity have a significant influence on the phase composition and crystallinity of the products. Using L-alanine fuel in the combustion process produced pure tetragonal anatase TiO2 product (JCPDS file no. 01-084-1286) at Φc = 0.5 (Fig. S1(a), ESI†), while other Φc values produced tetragonal anatase (JCPDS file no. 01-084-1286) and orthorhombic brookite TiO2 (JCPDS file no. 01-076-1937) phases. It is also observed that the brookite phase became more predominant as the Φc value increased (i.e. Φc > 0.5), as shown in Fig. S1(b–e), ESI.† The average crystallite sizes of the calcined products were determined using the Debye–Scherrer equation (eqn (4)) and tabulated in Table (1).39 |
D = 0.9λ/β cos θB
| (4) |
where, λ, β, and θB symbols are wavelength of the X-ray radiation (nm), the diffraction peak full width at half maximum (FWHM), and angle of the Bragg diffraction, respectively.
Table 1 The produced phases, crystallite sizes, and corresponding maximum adsorption capacities of the TiO2 products as well as the used fuels in the combustion processes
Fuel |
Equivalence ratio, Φc |
Product phasesa |
Sample label |
Crystallite size, nm |
Maximum adsorption capacity, qm (mg g−1) |
Where, A, B, and R stand for anatase, rutile, and Brookite phases of the TiO2 products, respectively, and the adsorption conditions were 300 mg L−1 initial dye concentration, pH 2, temperature 25 °C, and 0.05 g adsorbent dose for this adsorption study. |
L-Alanine |
0.5 |
A |
A0.5 |
13.0 |
77.00 |
1.0 |
A + B |
A1 |
15.8 |
42.00 |
1.5 |
A + B |
A1.5 |
16.0 |
40.00 |
2.0 |
A + B |
A2 |
22.0 |
36.90 |
2.5 |
A + B |
A2.5 |
23.3 |
35.00 |
Glycine |
0.5 |
A |
G0.5 |
13.0 |
52.00 |
1.0 |
A |
G1 |
18.0 |
87.00 |
1.5 |
A |
G1.5 |
20.0 |
65.00 |
2.0 |
A |
G2 |
23.0 |
62.40 |
2.5 |
A |
G2.5 |
24.9 |
62.00 |
Urea |
0.5 |
A |
U0.5 |
11.6 |
132.0 |
1.0 |
A |
U1 |
11.9 |
126.0 |
1.5 |
A + R |
U1.5 |
21.0 |
65.00 |
2.0 |
A + R |
U2 |
30.7 |
51.50 |
2.5 |
A + R |
U2.5 |
68.0 |
39.50 |
However, combustion reactions of TiO(NO3)2 and glycine fuel gave pure tetragonal anatase TiO2 phase at all used fuel-to-oxidant relative equivalence ratio (Φc) values: 0.5, 1.0, 1.5, 2.0, and 2.5. And all the XRD patterns of the products (G0.5–G2.5, Fig. S2, ESI†) could be indexed well to diffraction peaks of pure tetragonal anatase TiO2 with cell constants: a = 3.782 Å, b = 3.782 Å, and c = 9.502 Å (space group I41/amd, JCPDS card 01-084-1286). No other diffraction peaks for other TiO2 phases could be observed. These data are consistent with the reported ones.34 Moreover, the average crystallite size of the calcined products was calculated using eqn (4) and listed in Table 1. The results showed that increasing the Φc values from 0.5 to 2.5 (i.e. increasing the quantity of the glycine fuel) resulted in increasing the crystallite size of the calcined products from 13.0 to 24.9 nm, respectively. This can probably be returned to that increasing the amount of the used glycine fuel in the combustion process may increase the quantity of heat generating from this process. Consequently, this may result in increasing the temperature during the TiO2 particles crystal growth.
On the other hand, employing urea as fuel in the combustion of TiO(NO3)2, produced single tetragonal anatase TiO2 phase (space group I41/amd, JCPDS card 01-084-1286) at Φc values of 0.5 and 1.0 (Fig. 1). The average crystallite sizes of the corresponding calcined products were 11.6 and 11.9 nm, respectively, as presented in Table 1. No other reflections for other TiO2 phases have been detected. Additionally, at higher Φc values (Φc > 1.0), the combustion reaction gave a mixture of anatase (JCPDS card 01-084-1286) and rutile (JCPDS card 01-087-0920) TiO2 phases, as depicted in Fig. 1. Besides, the value of the rutile to anatase phase ratio increased from 46.7
:
53.3 to 89.4
:
10.6 with increasing the Φc values from 1.5 to 2.5, respectively, as shown in Table 1. The average crystallite size was enhanced also with increasing the Φc values (i.e. the quantity of urea fuel). These results can be attributed to that higher values of Φc may result in a higher quantity of heat which can raise the temperature of the system, and this high temperature can consequently convert the anatase phase into the rutile phase.40 These higher temperatures can also enhance the crystallinity of the TiO2 products.40 In addition, the XRD patterns (Fig. 1) have not revealed any peaks for brookite phase in the products: U0.5–U2.5. Thus, the fuel type and fuel-to-oxidant relative equivalence ratio value (Φc) can significantly control both the crystallite size and/or phase of the nanosized TiO2 products, through the combustion route. Moreover, urea fuel can be chosen as the optimum fuel in our study since it generates pure anatase phase with the smallest crystallite size which is appropriate for the present adsorption studies.
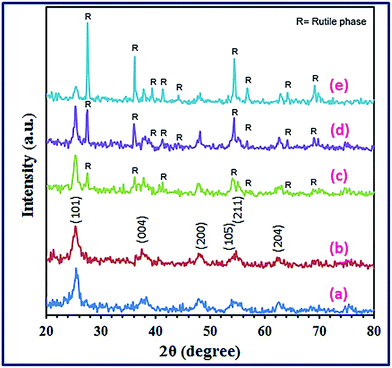 |
| Fig. 1 XRD patterns of the as-synthesized TiO2 products calcined at 500 °C using urea fuel. | |
3.1.2. FT-IR investigation. The chemical structures of the combustion products were investigated using the FT-IR spectra. Fig. 2 exhibits the FT-IR spectra of the combustion products prepared using L-alanine, glycine, and urea fuels at fuel-to-oxidant relative equivalence ratio value of 1.0 (i.e. Φc = 1.0). We focused on the combustion products, before and after calcination, at Φc = 1.0 because this value generated TiO2 products with almost the smallest crystallite size and the most appropriate adsorption properties. The FT-IR spectra of the samples before calcination, Fig. 2(a–c), showed vibrational absorptions at 2900 and 1360 cm−1 which might be attributed to the organic content residues.41 Besides, more peaks appeared in the range of 1490–1016 cm−1 for the combustion product of the glycine fuel (Fig. 2(b)), and this might be due to Ti–O–C and organic content residue.41,42 All the FT-IR spectra of the combustion products before calcination (Fig. 2(a–c)) showed vibrational absorptions in the range of 410–600 cm−1 corresponding to Ti–O–Ti bond.42,43 Additionally, two absorption peaks appeared at ca. 1590 and 3370 cm−1 may be attributed to the bending and stretching vibrations of the adsorbed water molecules.44–47 However, on calcination of the combustion products, Fig. 2(d–f), the vibrational peaks due to the organic residues disappeared. The FT-IR spectra of the calcined products showed one peak at ca. 410–600 cm−1 attributing to Ti–O–Ti bond.42,43 The spectra showed also two vibrational peaks at ca. 1590 and 3370 cm−1 due to bending and stretching vibrations, respectively, of the adsorbed water molecules.
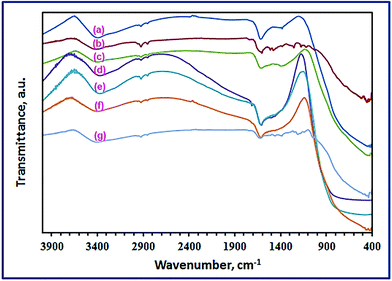 |
| Fig. 2 FT-IR spectra of the as-synthesized TiO2 products before calcination: (a), (b), and (c), for L-alanine, glycine, and urea fuels, respectively, after calcination at 500 °C for the corresponding products (d–f), respectively, and RR195 dye loaded TiO2 nano-adsorbent (g). | |
3.1.3. Morphological investigation. Morphology of the as-synthesized TiO2 nanoparticles calcined at 500 °C (A1, G1, and U1) was studied employing field-emission scanning electron microscope (FE-SEM) and transmission electron microscope (TEM), as displayed in Fig. (3) and (4), respectively. The low and high magnification FE-SEM images of the TiO2 product (A1) generated from L-alanine fuel and presented in Fig. 3(a) and (b), respectively, indicate that the TiO2 product is composed of spherical particles with 1.5 μm diameter. Besides, glycine fuel generated TiO2 product (G1) with irregular flake shapes as shown from its low and high magnification FE-SEM images (Fig. 3(c) and (d)). On the other hand, urea fuel produced TiO2 product (U1) with aggregates of hexagonal, pyramidal, and irregular shapes as shown in low magnification FE-SEM image (Fig. 3(e)). However, high magnification FE-SEM image (Fig. 3(f)) of the product reveals that the aggregates are composed of nanosphere-like particles with an average diameter of ca. 90 nm. Consequently, utilizing different fuels at varying fuel-to-oxidant relative equivalence ratios in the combustion process might produce different quantities of heat and gasses during the combustion process which resulted in TiO2 products with different morphological structures. And this also gave TiO2 products with different crystallite sizes. These results are consistent with the reported data.34 Besides, microstructural investigation of the TiO2 products using transmission electron microscope (TEM), Fig. 4(a–c), indicated that the three fuels produced similar morphologies for the TiO2 particles which were hexagon, sphere, and cube-like structures. The TEM images also revealed the porous structures of the products. The average particle size of the generated TiO2 products: A1, G1, and U1, was 17, 20, and 12 nm, respectively, which was consistent with the results calculated from the XRD data.
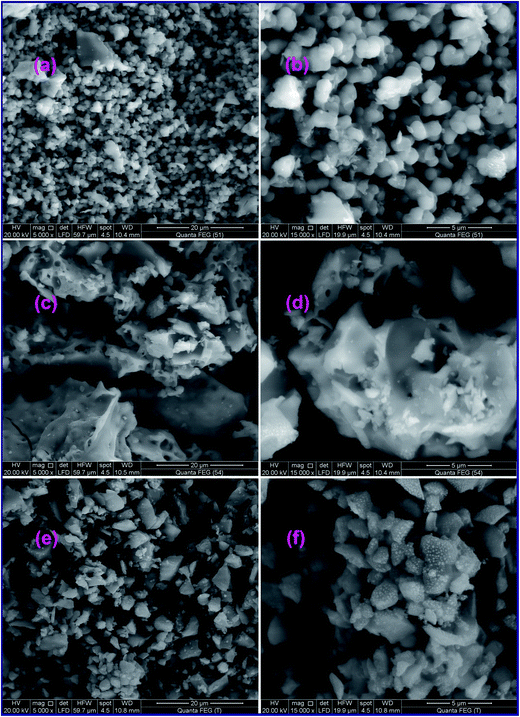 |
| Fig. 3 FE-SEM images of the as-synthesized TiO2 products calcined at 500 °C, using L-alanine (a and b), glycine (c and d), and urea (e and f) fuels. | |
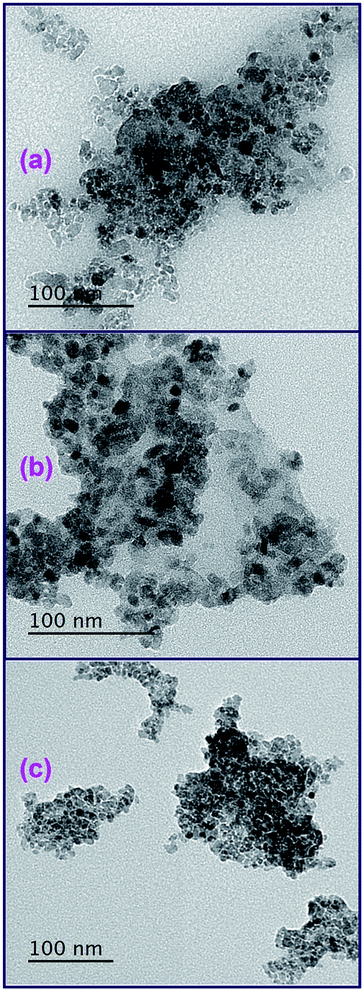 |
| Fig. 4 TEM images of the as-synthesized TiO2 products calcined at 500 °C, using L-alanine (a), glycine (b), and urea (c) fuels. | |
3.1.4. Thermal investigation. Thermal analyses (TG/DTA) of the combustion products generated from the fuels under study at Φc = 1.0, before calcination, are presented in Fig. 5(a–c). Fig. 5(a(i)) displays the TG curve of the combustion product before calcination while L-alanine is used as fuel. This figure reveals two mass loss steps. The first degradation step (mass loss of 7.562%) may be attributed to the removal of physically adsorbed water molecules, and it is detected in the temperature range of 48–300 °C. The second decomposition step (mass loss of 3.074%) observed in the range of 300–650 °C might correspond to decomposition of the remaining L-alanine fuel and carbon residues left from the combustion process. The TG curve (Fig. 5(b(i))) of the combustion product, in the case of glycine fuel, revealed two mass losses. The first one (mass loss of 5.185%) was broad, and it might be due to the elimination of the adsorbed water molecules appeared in the temperature range of 48–225 °C. The second step (mass loss of 7.557%) was also broad, and it might be two overlapped decomposition steps. It was observed in the temperature range of 225–650 °C, and it might be due to the decomposition of the remaining glycine and carbon residues. Thermal decomposition of the combustion product in case of urea fuel revealed two decomposition steps (Fig. 5(c(i))). The first one (mass loss of 5.055%) was detected in the temperature range of 48–175 °C due to the removal of the adsorbed water molecules. The second one (mass loss of 7.013%) was observed in the temperature range of 175–500 °C. This second stage was broad, and it might be two overlapped steps merged together due to the decomposition of the remaining urea fuel and carbon residues generated from the combustion process. The DTA analyses confirmed the results collected from the TG curves. DTA curve, Fig. 5(a(ii)), of the combustion product from the L-alanine fuel showed one endothermic peak at ca. 76.72 °C corresponding the elimination of the adsorbed water. This figure also exhibited one exothermic peak at ca. 451.9 °C attributing to the decomposition of the L-alanine and carbon residues. Fig. 5(b(ii)) shows the DTA curve of the combustion product in case of glycine fuel. This figure showed complex DTA curve with very broad peaks: endothermic one at ca. 77.00 °C, exothermic one at ca. 420.0 °C, and exothermic one at ca. 450.0 °C. These peaks can be attributed to the removal of adsorbed water molecules, decomposition of the remaining glycine residue, and decomposition of the carbon residue, respectively. Finally, Fig. 5(c(ii)) displays the DTA analysis of the combustion product when urea is used as a fuel. This figure reveals three peaks: endothermic peak at ca. 83.52 °C, exothermic peak at ca. 276.6 °C, and exothermic broad peak at ca. 350.0 °C. The first one can be due to the removal of the adsorbed water molecules, the second one may be assigned to the decomposition of some of the remaining urea residue, and the last peak can be attributed to the decomposition of the carbon residue left from the combustion process, respectively. It is noteworthy that decomposition of the residue fuel after the combustion process during the thermal analyses was also reported by others.48
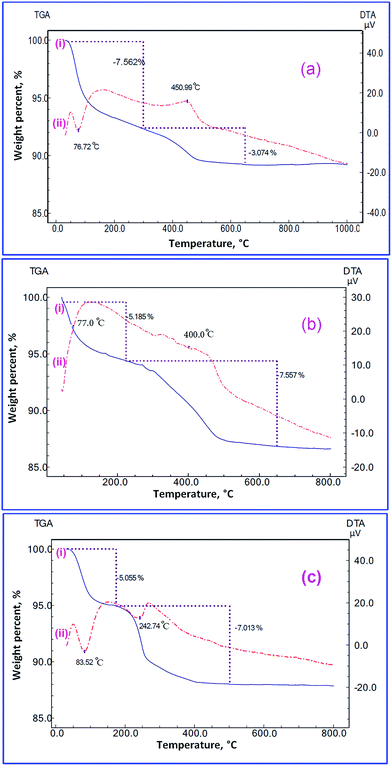 |
| Fig. 5 TG (i), and DTA (ii) analyses of the TiO2 combustion products; using L-alanine (a), glycine (b), and urea (c) fuels, under nitrogen gas. | |
3.1.5. Textural structure and point of zero charge investigation. We investigated the texture properties of only the calcined TiO2 product (U1) prepared using urea fuel at Φc = 1.0 since this fuel gave TiO2 product with almost the smallest crystallite size and the best adsorption properties. Besides, the combustion reactions presented in Scheme 1 reveal that urea fuel generates the largest quantity of gasses; consequently, because of these evolved gasses, TEM study, and the reported data, this fuel can produce the most porous TiO2 product.34 We carried out nitrogen gas adsorption–desorption isotherm measurement for the calcined TiO2 product (U1) as depicted in Fig. S3(a), ESI.† Fig. S3(a)† reveals an adsorption–desorption isotherm with a hysteresis phenomenon. The isotherm is consistent with the type-IV isotherm for the mesoporous materials (i.e. 2–50 nm in size) based on the International Union of Pure and Applied Chemistry IUPAC classification.49 The obtained Barret–Joyner–Halenda (BJH) pore volume and BET surface area for TiO2 product (U1) were found to be 0.180 cm3 g−1 and 115.379 m2 g−1, respectively. Besides, the study exhibited that most of the sample pore volume was occupied with 31.2 nm diameter pores. Moreover, the point of zero charge (pHPZC) of the as-prepared TiO2 product (U1) was estimated because the surface charge of the nanoparticles suspended in a medium is dependent on the pH values of that medium as reported previously.38 The point of zero charge value (pHpzc) of TiO2 nanoparticles was determined using the reported pH drift method2,4,50 where we used TiO2 suspensions in sodium chloride solutions (0.01 M) of various initial pH values in the range of 1.3–11. Then the pHpzc value is the intersection point between the pHinitial − pHfinal and pHinitial = pHfinal curves, as displayed in Fig. S3(b), ESI.† The pHpzc value of the as-prepared TiO2 nanoparticles (U1) was estimated to be around 7.6 which is in good agreement with reported value.51 However, it is worthy to mention that the pHpzc values of the nano-sized metal oxides can vary widely depending on several parameters including chemical and surface modification, crystallite size, and particle transformation.52
3.2. Adsorption properties of the as-prepared TiO2 nano-adsorbent
We investigated the adsorption properties of the TiO2 product (U1) using Reactive Red 195 (RR195) dye as a pollutant and textile dye model. As explained by Nassar et al. the FT-IR spectra can be utilized as an evidence for the adsorption of dyes on adsorbents.2,3,20 Fig. 2(f and g) depicts the FT-IR spectra of the TiO2 adsorbent (U1) before and after RR195 dye adsorption, respectively. It is observed that the FT-IR spectrum of the RR195 dye-loaded TiO2 differs from that of the bare TiO2 before adsorption. The vibrational absorptions appeared at ca. 424, 3364 cm−1 of the pure TiO2 nano-adsorbent (Fig. 2(f)) have been shifted to ca. 406 and 3374 cm−1, respectively, after the adsorption process. Besides, some new absorption peaks appeared upon RR195 dye adsorption at ca. 1004, 1174, 1364, and 1418 cm−1 as shown in the FT-IR spectrum of the RR195-loaded TiO2 (Fig. 2(f)). These new peaks are probably due to the adsorbed RR195 dye molecules onto TiO2 nano-adsorbent. Moreover, several parameters influencing the adsorption properties of the as-prepared nano-adsorbent (TiO2) such as pH, contact time, initial dye concentration, ionic strength, and temperature have been investigated. Moreover, the effect of the used fuel – during the combustion process – on the adsorption capacities of the TiO2 products (A0.5–U2.5) has also been studied as it will be shortly discussed.
3.2.1. Influence of pH. Adsorption media pH is one of the crucial parameters controlling the adsorption efficiency of dye molecules onto adsorbent nanoparticles. This parameter was studied under adsorption conditions: initial pH (1–10), initial dye concentration (C0 = 100 mg L−1), a TiO2 adsorbent dose of 0.05 g, stirring rate of 400 rpm, a temperature of 25 °C, and contact time of 24 h. The results are displayed in Fig. 6(a). The data revealed that the adsorption of RR195 dye was pH dependent, and the maximum adsorption was observed in the pH range of 1–3. Afterward, the dye removal percent decreased slowly by increasing pH up to ca. 6 then it decreased significantly at higher pH values. Therefore, the optimum pH value of the adsorption process of interest was chosen as pH 2; consequently, the other adsorption experiments were performed at pH 2. Moreover, the effect of solution pH on the adsorption of RR195 dye on TiO2 nano-adsorbent could be explained by taking into our account the surface charges of both the TiO2 particles and RR195 dye molecules. Because pHpzc of the as-prepared TiO2 product was estimated to be 7.6, the surface of TiO2 nanoparticles, (MOH), would be positively charged due to their covering with H+ ions (MOH2+). Besides, the anionic dye molecules behave as anionic species (i.e. negatively charged species) causing high electrostatic attraction which results in higher adsorption. While at higher pH values, OH− anions will interact with the TiO2 (MOH) forming deprotonated oxide particles (MO−); consequently, there will be repulsion forces between the similar negatively species (i.e. dye molecules and TiO2 particles). Besides, at higher pH values there will be a competition between the negatively charged dye molecules and OH− anions during the adsorption process. These result in a decrease in the adsorption of the dye molecules at higher pH values. Therefore, the acidic medium is more favorable for the adsorption of RR195 dye on TiO2 nano-adsorbent, and the electrostatic interaction may be the most predominant adsorption mechanism.53 Similar results have been reported in the literature for the adsorption of some dyes.53,54
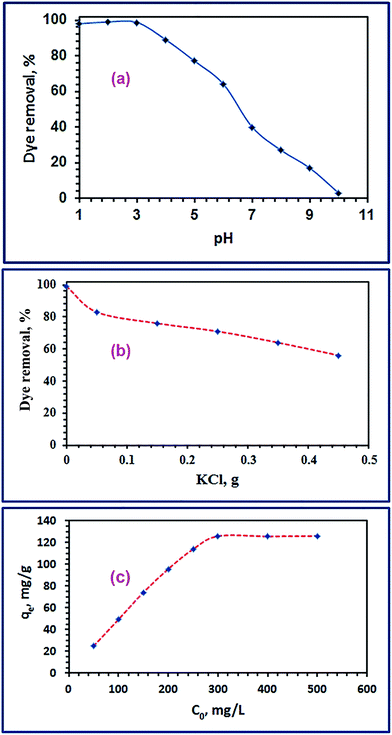 |
| Fig. 6 Effect of pH (a), KCl concentration (b), and initial RR195 dye concentration (c) on adsorption of RR195 dye on TiO2 nano-adsorbent (b). | |
3.2.2. Contact time and adsorption kinetic investigation. The effect of contact time of the adsorption of RR195 dye on the as-prepared TiO2 nano-adsorbent was investigated under the adsorption conditions: initial dye concentrations (50–250 mg L−1), pH 2, temperature of 25 °C, and 0.05 g adsorbent dose. The adsorption capacities (qt, mg g−1) of TiO2 nano-adsorbent for the adsorption of RR195 dye versus the contact time (t, min) were displayed in Fig. 7(a) for various initial dye concentrations. It could be observed that the adsorption was fast in the initial stages; afterward, it increased slowly with increasing the contact time until it reached the equilibrium state (i.e. the plateau behavior). The change in the rate of RR195 dye adsorption at the initial and later stages is probably due to the presence of larger number of active adsorption sites available for adsorption in the beginning of the adsorption process. Then, this number decreased with increasing the contact time by an occupation of the adsorption active sites during the adsorption process. Besides, the slower adsorption rates at longer contact times can be assigned to the slower pore diffusion rate of the RR195 dye molecules into the TiO2 nanoparticles. This behavior is similar to that reported for the adsorption of RB5 dye on ZnO nanoparticles.4 In order to understand the adsorption mechanism, the experimental kinetic data of RR195 dye adsorption on TiO2 adsorbent were examined using pseudo-first-order55 and pseudo-second-order56 models expressed by eqn (5) and (6), respectively. |
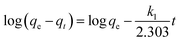 | (5) |
|
 | (6) |
where, qt (mg g−1) and qe (mg g−1) are the adsorption capacity and equilibrium adsorption capacity of TiO2 adsorbent at time t (min) and equilibrium time, respectively. k1 (min−1) and k2 (g mg−1 min−1) are the rate constant of pseudo-first-order adsorption process and pseudo-second-order adsorption process, respectively. Linear plot of log(qe − qt) against t (eqn (5)) was performed for various initial dye concentrations to calculate the qe(cal) and k1 constants for pseudo-first-order model (not shown here). Besides, qe(cal) and k2 constants of the pseudo-second-order model were estimated via plotting of t/qt against t (eqn (6)) for various initial dye concentrations, as presented in Fig. 7(b). The calculated kinetic constants for different initial dye concentrations are tabulated in Table 2. Comparison between regression coefficient (r2) values indicates that the pseudo-second-order model is more valid than the pseudo-first-order model for two reasons. The first one is that the r2 values of the pseudo-second-order model is closer to unity than those of the pseudo-first-order model. The second reason is that the adsorption capacity (qe(cal)) values calculated from the pseudo-second-order model is closer to the experimentally obtained ones compared to those estimated from the pseudo-first-order model. Moreover, using the calculated pseudo-second-order rate constants and adsorption capacities (qe(cal)), the initial sorption rate (h) can be determined using eqn (7) and listed in Table 2.57 The tabulated initial sorption rate values indicated that they increased with enhancing the initial dye concentrations.
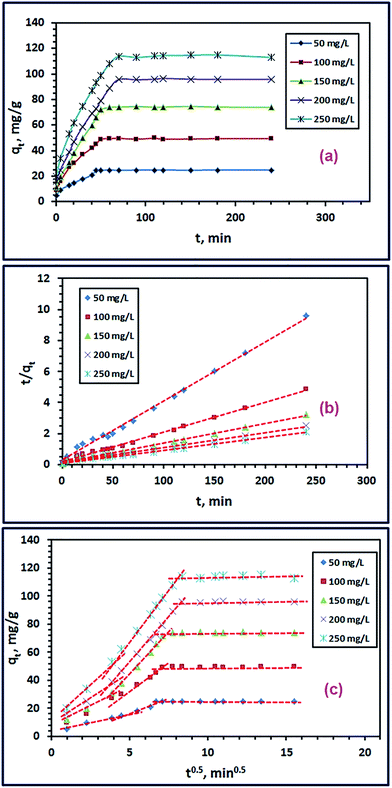 |
| Fig. 7 Effect of contact time at various initial dye concentrations (a), pseudo-second-order (b) and intra-particle diffusion model (c) for the RR195 dye adsorption on TiO2 nano-adsorbent. | |
Table 2 Parameters of the pseudo-second order model for the adsorption of RR195 dye on TiO2 adsorbent at various initial dye concentrations (C0)
Pseudo-second-order model |
C0 (mg g−1) |
K2 [g (mg min)−1] |
qe(cal) (mg g−1) |
r12 |
H [g (mg min)−1] |
qe(exp) (mg g−1) |
50 |
4.90 × 10−3 |
26.23 |
0.996 |
3.369 |
24.90 |
100 |
2.37 × 10−3 |
52.02 |
0.997 |
6.402 |
49.40 |
150 |
1.05 × 10−3 |
79.92 |
0.992 |
6.717 |
74.30 |
200 |
0.590 × 10−3 |
105.3 |
0.991 |
6.720 |
95.80 |
250 |
0.654 × 10−3 |
122.6 |
0.994 |
9.832 |
114.0 |
To investigate the influence of the intra-particle diffusion resistance on the adsorption, the intra-particle diffusion model (eqn (8)) was applied.58
where,
qt (mg g
−1),
t (min),
C (mg g
−1), and
ki (mg (g min
1/2)
−1) are the quantity of the adsorbed RR195 dye at time
t (min), the intercept indicating the boundary layer thickness, and intra-particle diffusion rate constant.
Fig. 7(c) shows the plot of
qt against
t0.5 values, and the corresponding constants are listed in
Table 2.
Fig. 7(c) revealed that the obtained curves were multi-linear plots, and they did not pass the origin. Consequently, the rate-determining step of this adsorption process is not only controlled by the intra-particle diffusion mechanism but also controlled by other mechanisms including film diffusion and bulk diffusion.
59
3.2.3. Influence of ionic strength. Industrial effluents often contain various inorganic salts including KCl, and others, as well as the organic pollutants. These inorganic salts can compete with organic dye molecules for the active adsorption sites of adsorbents during the adsorption process; consequently, this may decrease the adsorption efficiency of the adsorbents. The influence of these competing inorganic ions raises an essential issue since they can control both the electrostatic and non-electrostatic interactions which may be held between the adsorbate and the adsorbent surface.38 We investigated the effect of KCl concentrations on the adsorption of RR195 dye using the as-prepared TiO2 product as an adsorbent under the adsorption conditions: 100 mg L−1 initial dye concentrations, pH 2, temperature of 25 °C, and 0.05 g adsorbent dose. The experimental results depicted in Fig. 6(b) indicate that the dye removal efficiency decreases with increasing the potassium chloride concentration. This is consistent with the conclusion that the adsorption mechanism is mainly based on the electrostatic interactions between the dye molecules and charged surface TiO2 particles.17,38
3.2.4. Initial concentration and adsorption isotherm investigation. The effect of initial dye concentration on the adsorption process was examined using batch techniques under adsorption conditions: 0.05 g TiO2, pH 2, initial dye concentrations (50.0–500 mg L−1), ca. 70 min equilibration time, and at 25 °C temperature. The results are presented in Fig. 6(c). The results indicated that the adsorption capacity of TiO2 adsorbent increased with increasing the initial dye concentration untill it reached the plateau with a maximum value (qm(exp)) of 126.0 mg g−1. It is noteworthy that increasing the adsorbed quantity of the RR195 dye with increasing its initial concentration is probably attributed to overcoming the resistance of the dye molecule mass transfer between the solid and liquid phases at higher dye concentrations during the adsorption process.38,60 Besides, the plateau behavior might be due to the saturation of the limited number of the adsorption sites at high initial concentrations.61Additionally, the experimentally obtained adsorption results were examined using the Langmuir and Freundlich adsorption isotherm models presented in eqn (9) and (10), respectively.
|
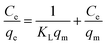 | (9) |
|
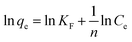 | (10) |
where,
Ce,
qe,
qm, and
KL are the dye equilibrium concentration (mg L
−1), equilibrium adsorption capacity (mg g
−1), maximum adsorption capacity (mg g
−1), and Langmuir constant (L mg
−1), respectively. Besides,
KF and
n are the Freundlich constant which indicates the adsorption capacity and a constant indicating the adsorption intensity, respectively. The two isotherm models were checked by plotting
Ce/
qe against
Ce (
eqn (9),
Fig. 8(a)), and ln
qe versus ln
Ce (
eqn (10),
Fig. 8(b)). The corresponding constants for each model were estimated from the slope and intercept of the relevant straight line, and they were tabulated in
Table 3. The maximum adsorption capacity (
qm(cal)) of TiO
2 adsorbent calculated from the Langmuir model was found to be 127.0 mg g
−1 which is compatible with the experimentally obtained one. On the other hand,
qm(cal) was also determined based on the Freundlich isotherm model according to
eqn (11) as reported by Halsey.
62 |
 | (11) |
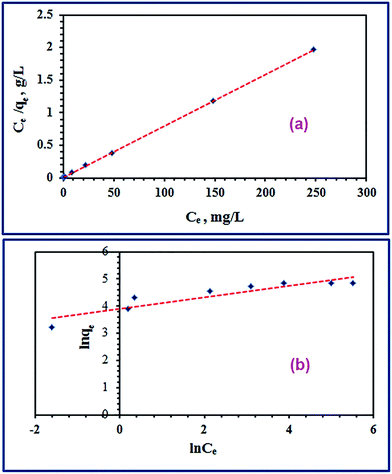 |
| Fig. 8 Langmuir (a) and Freundlich (b) isotherm models for the adsorption of RR195 dye on TiO2 nano-adsorbent. | |
Table 3 Langmuir and Freundlich isotherm constants for the adsorption of RR195 dye on TiO2 adsorbent
Adsorption isotherm model |
Parameters |
Value |
Langmuir |
KL (L mg−1) |
0.641 |
qm(cal) (mg g−1) |
127.0 |
r12 |
0.9990 |
RL |
0.009941–0.09124 |
qe(exp) (mg g−1) at C0 = 300 mg L−1 |
126.0 |
Freundlich |
KF [(mg g−1) (L mg−1)1/n] |
50.13 |
qm(cal) (mg g−1) |
167.3 |
r22 |
0.8349 |
n |
4.732 |
qe,(exp) (mg g−1) at C0 = 300 mg L−1 |
126.0 |
The maximum adsorption capacity (qm(cal)) utilizing the Freundlich isotherm was estimated to be 167.34 mg g−1. Comparison between the tabulated constants in Table (3) for both applied isotherm models exhibited that adsorption of RR195 dye on TiO2 adsorbent followed the Langmuir adsorption isotherm. This is based on the following: (i) the regression coefficient value (r2 = 0.9999) for the Langmuir isotherm model (Fig. 8(a)) higher than that of the Freundlich isotherm model (r2 = 0.8348), and (ii) the maximum adsorption capacity (qm(cal)) calculated from the Langmuir isotherm model is closer to the experimentally determined value than that obtained from the Freundlich isotherm model. Therefore, the obtained results indicate the TiO2 homogenous nature and the RR195 dye monolayer coverage on the surface of the TiO2 nano-adsorbent. In addition, the favorability of the adsorption of RR195 dye on the TiO2 nano-adsorbent was examined using the separation factor constant (RL) derived from the Langmuir isotherm model, as presented in eqn (12).
|
 | (12) |
where,
C0 and
KL are the initial dye concentration (mg L
−1) and Langmuir constant (L mg
−1), respectively. According to the literature, if
RL = 0, 0 <
RL < 1,
RL = 1, or
RL > 1, the adsorption process will be irreversible, favorable, linear, or unfavorable, respectively.
63 The calculated
RL values for different initial dye concentrations were found to be less than one and greater than zero (0.0099–0.091) over the RR195 dye concentration range (50.0–500 mg L
−1), as listed in
Table 3; consequently, the adsorption of RR195 dye on the as-prepared TiO
2 nano-adsorbent is favorable.
3.2.5. Adsorption thermodynamics. The effect of adsorption media temperatures on the adsorption of RR195 dye on the as-prepared TiO2 product was explored in the range of 298–318 K under the adsorption conditions: 0.05 g TiO2, 300 mg L−1 initial dye concentration, 400 rpm stirring rate, and ca. 2 h contact time. The results exhibited that the adsorption capacity of the as-prepared TiO2 adsorbent enhances with increasing the temperature of the adsorption media meaning the endothermic nature of the adsorption process, as shown in Fig. 9(a). Furthermore, the thermodynamic constants can provide information on the energy changes associated with the adsorption process. Therefore, some thermodynamic parameters have been estimated including the enthalpy change (ΔH0), entropy change (ΔS0), and Gibbs free energy change (ΔG0) through using eqn (13) and (14).20 |
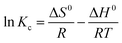 | (13) |
where, R and T are the universal gas constant (8.314 × 10−3 kJ mol−1 K−1) and adsorption medium absolute temperature (K), respectively. Moreover, Kc is the thermodynamic equilibrium constant and the value of this constant must be dimensionless. This is because the fact that the units of ΔG0, R, and T in eqn (15) are kJ mol−1, kJ mol−1 K−1, and K, respectively. Therefore, some approaches have been proposed for the determination of a dimensionless thermodynamic equilibrium constant64–69 |
ΔG0 = RT ln Kc
| (15) |
 |
| Fig. 9 Plot of qe versus T (a), plot of ln(1 − θ) versus 1/T (b), and regeneration efficiency of TiO2 nano-adsorbent for the removal of RR195 dye (c). | |
In our current study, we have calculated the dimensionless thermodynamic equilibrium constant (Kc) using two approaches; the partition constant (Kp) and distribution coefficient constant (Kd).65,70
As reported by Niwas et al. and others,65 the thermodynamic equilibrium constant (Kc) can be represented by eqn (16).
|
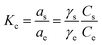 | (16) |
where,
as and
ae are the activities of the adsorbed dye and the equilibrium dye in solution, respectively.
Cs and C
e are the adsorbed concentration of the adsorbate on the adsorbent and the equilibrium concentration of the adsorbate in solutions, respectively. Besides,
γs and
γe are the activity coefficients of the adsorbed dye and dye in solution at equilibrium, respectively. When the solute concentration approaches zero in the solution, the activity coefficient approaches unity, and
eqn (16) reduces into
eqn (17). Therefore the partition coefficient,
Kp, equals in its value to the thermodynamic equilibrium constant (
Kc), and it is in unison with the thermodynamic constant.
|
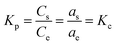 | (17) |
The Kp values (i.e. Kc = Kp in this case) can be obtained by plotting ln(Cs/Ce) versus Cs and extrapolating Cs to zero.70 The ΔH0 and ΔS0 values were estimated from the slope and intercept of the plot of ln
Kc against 1/T. We also calculated ΔG0 value by feeding ΔH0 and ΔS0 values into eqn (14). The calculated thermodynamic parameters are presented in Table (4).
Table 4 Thermodynamic constants for the adsorption of RR195 dye on TiO2 adsorbent from partition and distribution coefficient constants
Method |
T (K) |
Kc |
ΔG0 (kJ mol−1) |
ΔS0 (J mol−1 K−1) |
ΔH0 (kJ mol−1) |
r2 |
Ea (kJ mol−1) |
S* |
Partition constant, Kp (Kp = Kc) |
298 |
6.498 |
−4.630 |
0.02004 |
1.343 |
0.9204 |
18.46 |
9.464 × 10−5 |
308 |
6.557 |
−4.830 |
318 |
6.725 |
−5.031 |
Distribution coefficient constant, Kd (Kc = Kd × 1000) |
298 |
5805.4 |
−21.42 |
0.09113 |
5.737 |
0.7860 |
308 |
5864.2 |
−22.33 |
318 |
6725.1 |
−23.24 |
On the other hand, the thermodynamic equilibrium constant was also derived from distribution coefficient constant (Kd = qe/Ce). The distribution coefficient constant (Kd) can be obtained by plotting ln(qs/Ce) against qs and extrapolating Cs to zero.66 Moreover, the thermodynamic equilibrium constant is dimensionless, hence; there is a unit problem with the Kd constant. Therefore, Milonjić proposed that distribution coefficient constant (Kd) can be converted into the dimensionless thermodynamic equilibrium constant (Kc) by multiplying Kd by 1000.66 The values of ΔH0 and ΔS0 were determined from the slope and intercept of the plot of ln
Kc against 1/T. Where, Kc = Kd × 1000. We also estimated ΔG0 value using eqn (14) by knowing ΔH0 and ΔS0 values. The calculated thermodynamic parameters are tabulated in Table (4). The tabulated thermodynamic values in Table (4) show that the partition coefficient constant is more appropriate than the distribution coefficient for calculating the thermodynamic constants owing to the higher correlation coefficient (r2 = 0.9204) of van't Hoff equation in the case of Kc = Kp on comparing to Kc derived from Kd (r2 = 0.786). It is worthy to mention that both equilibrium constants gave ΔH0, ΔS0, and ΔG0 with same signs.
Based on the thermodynamic parameters calculated from Kc derived from the partition constant, it is indicated that the adsorption process is endothermic and spontaneous due to the positive ΔH0 and negative ΔG0 values, respectively, of the process. Besides, increasing the values of ΔG0 in the negative direction with increasing the temperature indicates the thermodynamic favorability of the adsorption process at higher temperatures. Moreover, it could be concluded that the adsorption process of interest was a physisorption process because the ΔG0 (from −4.630 to −5.031 kJ mol−1) and ΔH0 (1.343 kJ mol−1) values were in the range of (−20)–(0) kJ mol−1 and <40 kJ mol−1, respectively.
In addition, we calculated the activation energy (Ea) of the RR195 dye adsorption on the as-synthesized nano-adsorbent utilizing a modified Arrhenius equation (eqn (18)) related to surface coverage (θ).71,72
|
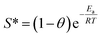 | (18) |
where,
S* (0 <
S* < 1) is an adsorbate/adsorbent function (sticking probability), and it is temperature dependent,
θ = [1 −
Ce/
C0].
C0 and
Ce have the previously mentioned meaning. Substituting of
θ with [1 −
Ce/
C0] in
eqn (18) results in
eqn (19) |
ln(1 − θ) = ln S* + Ea/RT
| (19) |
We calculated the activation energy (Ea) of the adsorption process from the slope and intercept of the plot ln(1 − θ) versus 1/T (Fig. 9(b)). It is worth mentioning that Ea value can indicate whether the adsorption process is physisorption or chemisorption depending on whether the value lies in the range of 5–40 or 40–800 kJ mol−1, respectively.4,73 The activation energy (Ea) value of the adsorption of RR195 dye on the as-prepared TiO2 nano-adsorbent was determined to be 18.46 kJ mol−1. This value indicates the physisorption nature of the adsorption process supporting the previous result concluded from the ΔG0 and ΔH0 values.
3.2.6. Effect of the fuels on the adsorption properties of TiO2 products. We have investigated the influences of combustion fuel and its ratios on the adsorption of the RR195 dye on the calcinated TiO2 products (A1–U2.5) generated from different fuels. We have applied the following adsorption conditions: 0.05 g TiO2, 300 mg L−1 initial dye concentration, 400 rpm stirring rate, 25 °C temperature, and 120 min contact time. The maximum adsorption capacities of the various TiO2 products were estimated and tabulated in Table 1. The results listed in Table 1 indicate that urea fuel generated TiO2 products with the highest adsorption capacities. Moreover, urea fuel with equivalence ratio (Φc) values of 0.5 and 1 generated TiO2 products; U0.5 and U1, with the highest adsorption capacities; 132.0 and 126.0 mg g−1, respectively. However, the TiO2 product U1 was more separable and handful during the adsorption process on comparing to the U0.5 product; consequently, U1 product was chosen as the optimum TiO2 product from the practical point of view.
3.2.7. Reusability of TiO2 nano-adsorbent and comparison with other adsorbents. The efficiency of the as-prepared TiO2 nano-adsorbent was investigated by studying its regeneration and reusability for RR195 dye adsorption. Therefore, the adsorption of the dye of interest on the as-prepared TiO2 nano-adsorbent was achieved under the optimized adsorption conditions; then, we generated the TiO2 nano-adsorbent by either one of the following two approaches: (i) we extracted the adsorbed RR195 dye employing methanol then the adsorbent was washed with methanol and water. The adsorbent was then dried at about 70 °C for 5 h. (ii) The RR195 dye-loaded TiO2 adsorbent was ignited at about 450 °C for 0.5 h. We have repeated this recycling procedure five times, and the obtained results are depicted in Fig. 9(c). The results exhibit that the as-prepared TiO2 product has good reproducibility and high adsorption efficiency even after five cycles of reuse. Moreover, we compared between the maximum adsorption capacity (qm) of the as-prepared TiO2 adsorbent with those of others reported in the literature, and the qm values are presented in Table 5. Additionally, the maximum adsorption capacity (qm) of the commercially available TiO2 product (Degussa (P25)) was experimentally determined under the same optimum adsorption conditions, and it was found to be 55.0 mg g−1. We performed this to verify the effectiveness of the as-prepared TiO2 product as a potential adsorbent for the removal of RR195 dye. In comparison with the listed qm of other reported adsorbents (Table 5), it is clear that the as-prepared TiO2 adsorbent has relatively high qm values. It is noteworthy that the as-prepared TiO2 product (U1) has higher adsorption capacity than that of the commercially available TiO2 (Degussa (P25)). Moreover, MgO adsorbent reported by us elsewhere needed more time and higher temperature in its preparation. Therefore, this comparison and our facile preparation route suggest that the as-synthesized TiO2 product is a possible promising and applicable candidate in the removal of RR195 dye from aqueous media. The results also indicate the long-term use of the as-prepared TiO2 adsorbent for the removal of RR195 dye from aqueous solutions.
Table 5 Comparison between the maximum adsorption capacities of various adsorbents toward RR195 dye removal
Adsorbent product |
Maximum adsorption capacities, qm (mg g−1) |
Reference |
Cone biomass |
7.38 |
74 |
α-Fe2O3 |
20.5 |
20 |
Modified palygorskite with 3-aminopropyl triethoxysilane |
34.24 |
75 |
Commercial TiO2 (Degussa (P25)) |
55.0 |
Present study |
Dehydrated beet pulp carbon |
58.0 |
76 |
TiO2 |
87 |
53 |
CoFe2O4 |
91.7 |
2 |
Wheat bran |
119.1 |
77 |
TiO2 (U1) |
135 |
Present study |
MgO nanoparticles |
207 |
38 |
4. Conclusions
In conclusion, TiO2 nanostructures were successfully synthesized via a facile auto-combustion route using different fuels including L-alanine, glycine, and urea. The results revealed that the fuel type and the fuel-to-oxidant equivalence ratio have a significant influence on the phase, crystallite size, and morphology of the generated TiO2 products. Urea fuel generated almost the smallest crystallite size (11.9 nm) TiO2 nanoparticles with single anatase TiO2 phase at equivalence ratio Φc of 1. The as-prepared TiO2 product generated using urea fuel at Φc = 1 showed the highest adsorption capacity (ca. 135 mg g−1) for the adsorption removal of RR195 textile anionic dye. In addition, the adsorption results could be well described by the pseudo-second-order and Langmuir adsorption isotherm models. Besides, the contribution into the adsorption mechanism did not arise only from the intra-particle diffusion mechanism but aroused also from the bulk diffusion and film diffusion mechanisms. The adsorption of RR195 dye on TiO2 nano-adsorbent was a temperature dependent and the process was a physisorption, endothermic, and spontaneous based on the calculated thermodynamic parameters. Moreover, the as-prepared TiO2 product can be suggested as a promising candidate for the adsorption removal of RR195 dye from aqueous media.
Acknowledgements
The first and second authors are grateful to Benha University, Egypt, for the financial support of the present work.
References
- T. A. Khan, S. Dahiya and I. Ali, Use of kaolinite as adsorbent: equilibrium, dynamics and thermodynamic studies on the adsorption of Rhodamine B from aqueous solution, Appl. Clay Sci., 2012, 69, 58–66 CrossRef CAS.
- M. Y. Nassar and M. Khatab, Cobalt ferrite nanoparticles via a template-free hydrothermal route as an efficient nano-adsorbent for potential textile dye removal, RSC Adv., 2016, 6, 79688–79705 RSC.
- M. Y. Nassar and S. Abdallah, Facile controllable hydrothermal route for a porous CoMn2O4 nanostructure: synthesis, characterization, and textile dye removal from aqueous media, RSC Adv., 2016, 6, 84050–84067 RSC.
- M. Y. Nassar, M. M. Moustafa and M. M. Taha, Hydrothermal tuning of the morphology and particle size of hydrozincite nanoparticles using different counterions to produce nanosized ZnO as an efficient adsorbent for textile dye removal, RSC Adv., 2016, 6, 42180–42195 RSC.
- N. F. Cardoso, R. B. Pinto, E. C. Lima, T. Calvete, C. V. Amavisca, B. Royer, M. L. Cunha, T. H. M. Fernandes and I. S. Pinto, Removal of remazol black B textile dye from aqueous solution by adsorption, Desalination, 2011, 269, 92–103 CrossRef CAS.
- B. Kayan, B. Gözmen, M. Demirel and A. M. Gizir, Degradation of acid red 97 dye in aqueous medium using wet oxidation and electro-Fenton techniques, J. Hazard. Mater., 2010, 177, 95–102 CrossRef CAS PubMed.
- M. Y. Nassar, A. S. Amin, I. S. Ahmed and S. Abdallah, Sphere-like Mn2O3 nanoparticles: facile hydrothermal synthesis and adsorption properties, J. Taiwan Inst. Chem. Eng., 2016, 64, 79–88 CrossRef CAS.
- M. Y. Nassar, I. S. Ahmed and I. Samir, A novel synthetic route for magnesium aluminate (MgAl2O4) nanoparticles using sol–gel auto combustion method and their photocatalytic properties, Spectrochim. Acta, Part A, 2014, 131, 329–334 CrossRef CAS PubMed.
- M. Djenouhat, O. Hamdaoui, M. Chiha and M. H. Samar, Ultrasonication-assisted preparation of water-in-oil emulsions and application to the removal of cationic dyes from water by emulsion liquid membrane: part 2. Permeation and stripping, Sep. Purif. Technol., 2008, 63, 231–238 CrossRef CAS.
- A. B. Fradj, S. B. Hamouda, H. Ouni, R. Lafi, L. Gzara and A. Hafiane, Removal of methylene blue from aqueous solutions by poly(acrylic acid) and poly(ammonium acrylate) assisted ultrafiltration, Sep. Purif. Technol., 2014, 133, 76–81 CrossRef CAS.
- D. Robati, M. Rajabi, O. Moradi, F. Najafi, I. Tyagi, S. Agarwal and V. K. Gupta, Kinetics and thermodynamics of malachite green dye adsorption from aqueous solutions on graphene oxide and reduced graphene oxide, J. Mol. Liq., 2016, 214, 259–263 CrossRef CAS.
- E. Pajootan, M. Arami and N. M. Mahmoodi, Binary system dye removal by electrocoagulation from synthetic and real colored wastewaters, J. Taiwan Inst. Chem. Eng., 2012, 43, 282–290 CrossRef CAS.
- Q. Wu, W.-T. Li, W.-H. Yu, Y. Li and A.-M. Li, Removal of fluorescent dissolved organic matter in biologically treated textile wastewater by ozonation-biological aerated filter, J. Taiwan Inst. Chem. Eng., 2016, 59, 359–364 CrossRef CAS.
- A. Mohammadzadeh, M. Ramezani and A. M. Ghaedi, Synthesis and characterization of Fe2O3–ZnO–ZnFe2O4/carbon nanocomposite and its application to removal of bromophenol blue dye using ultrasonic assisted method: optimization by response surface methodology and genetic algorithm, J. Taiwan Inst. Chem. Eng., 2016, 59, 275–284 CrossRef CAS.
- W. Wang, T. Jiao, Q. Zhang, X. Luo, J. Hu, Y. Chen, Q. Peng, X. Yan and B. Li, Hydrothermal synthesis of hierarchical core–shell manganese oxide nanocomposites as efficient dye adsorbents for wastewater treatment, RSC Adv., 2015, 5, 56279–56285 RSC.
- H. Guo, T. Jiao, Q. Zhang, W. Guo, Q. Peng and X. Yan, Preparation of Graphene Oxide-Based Hydrogels as Efficient Dye Adsorbents for Wastewater Treatment, Nanoscale Res. Lett., 2015, 10, 1–10 CrossRef CAS PubMed.
- Y. S. Al-Degs, M. I. El-Barghouthi, A. H. El-Sheikh and G. M. Walker, Effect of solution pH, ionic strength, and temperature on adsorption behavior of reactive dyes on activated carbon, Dyes Pigm., 2008, 77, 16–23 CrossRef CAS.
- C.-K. Lee, S.-S. Liu, L.-C. Juang, C.-C. Wang, K.-S. Lin and M.-D. Lyu, Application of MCM-41 for dyes removal from wastewater, J. Hazard. Mater., 2007, 147, 997–1005 CrossRef CAS PubMed.
- A. Nematollahzadeh, A. Shojaei and M. Karimi, Chemically modified organic/inorganic nanoporous composite particles for the adsorption of reactive black 5 from aqueous solution, React. Funct. Polym., 2015, 86, 7–15 CrossRef CAS.
- M. Y. Nassar, I. S. Ahmed, T. Y. Mohamed and M. Khatab, A controlled, template-free, and hydrothermal synthesis route to sphere-like [small alpha]-Fe2O3 nanostructures for textile dye removal, RSC Adv., 2016, 6, 20001–20013 RSC.
- M. Y. Nassar and I. S. Ahmed, Template-free hydrothermal derived cobalt oxide nanopowders: synthesis, characterization, and removal of organic dyes, Mater. Res. Bull., 2012, 47, 2638–2645 CrossRef CAS.
- A. Razzaz, S. Ghorban, L. Hosayni, M. Irani and M. Aliabadi, Chitosan nanofibers functionalized by TiO2 nanoparticles for the removal of heavy metal ions, J. Taiwan Inst. Chem. Eng., 2016, 58, 333–343 CrossRef CAS.
- S. Yavari, N. M. Mahmodi, P. Teymouri, B. Shahmoradi and A. Maleki, Cobalt ferrite nanoparticles: preparation, characterization and anionic dye removal capability, J. Taiwan Inst. Chem. Eng., 2016, 59, 320–329 CrossRef CAS.
- T. Kamal, Y. Anwar, S. B. Khan, M. T. S. Chani and A. M. Asiri, Dye adsorption and bactericidal properties of TiO2/chitosan coating layer, Carbohydr. Polym., 2016, 148, 153–160 CrossRef CAS PubMed.
- S. Jafari, B. Tryba, E. Kusiak-Nejman, J. Kapica-Kozar, A. W. Morawski and M. Sillanpää, The role of adsorption in the photocatalytic decomposition of Orange II on carbon-modified TiO2, J. Mol. Liq., 2016, 220, 504–512 CrossRef CAS.
- B. Liu, J. E. Boercker and E. S. Aydil, Oriented single crystalline titanium dioxide nanowires, Nanotechnology, 2008, 19, 505604 CrossRef CAS PubMed.
- N. Erdogan, A. Ozturk and J. Park, Hydrothermal synthesis of 3D TiO2 nanostructures using nitric acid: characterization and evolution mechanism, Ceram. Int., 2016, 42, 5985–5994 CrossRef CAS.
- C. S. Rustomji, C. J. Frandsen, S. Jin and M. J. Tauber, Dye-Sensitized Solar Cell Constructed with Titanium Mesh and 3-D Array of TiO2 Nanotubes, J. Phys. Chem. B, 2010, 114, 14537–14543 CrossRef CAS PubMed.
- T. Frade, M. E. M. Jorge, B. Fernández, R. Pereiro and A. Gomes, A Possible Growth Mechanism for ZnO–TiO2 Composite Nanostructured Films Prepared by Electrodeposition, J. Electrochem. Soc., 2014, 161, D125–D133 CrossRef CAS.
- Y. Wang, Y. He, Q. Lai and M. Fan, Review of the progress in preparing nano TiO2: an important environmental engineering material, J. Environ. Sci., 2014, 26, 2139–2177 CrossRef PubMed.
- K. Ding, Z. Miao, Z. Liu, Z. Zhang, B. Han, G. An, S. Miao and Y. Xie, Facile Synthesis of High Quality TiO2 Nanocrystals in Ionic Liquid via a Microwave-Assisted Process, J. Am. Chem. Soc., 2007, 129, 6362–6363 CrossRef CAS PubMed.
- L. Mai, C. Huang, D. Wang, Z. Zhang and Y. Wang, Effect of C doping on the structural and optical properties of sol–gel TiO2 thin films, Appl. Surf. Sci., 2009, 255, 9285–9289 CrossRef CAS.
- H. Yoshitake, T. Sugihara and T. Tatsumi, Preparation of Wormhole-like Mesoporous TiO2 with an Extremely Large Surface Area and Stabilization of Its Surface by Chemical Vapor Deposition, Chem. Mater., 2002, 14, 1023–1029 CrossRef CAS.
- A. Daya Mani, B. Rama Raju, N. Xanthopoulos, P. Ghosal, B. Sreedhar and C. Subrahmanyam, Effect of fuels on combustion synthesis of TiO2 – Towards efficient photocatalysts for methylene blue oxidation and Cr(VI) reduction under natural sunlight, Chem. Eng. J., 2013, 228, 545–553 CrossRef CAS.
- A. Daya Mani, V. Laporte, P. Ghosal and C. Subrahmanyam, Combustion synthesized TiO2 for enhanced photocatalytic activity under the direct sunlight-optimization of titanylnitrate synthesis, Mater. Res. Bull., 2012, 47, 2415–2421 CrossRef CAS.
- S. R. Jain, K. C. Adiga and V. R. Pai Verneker, A new approach to thermochemical calculations of condensed fuel-oxidizer mixtures, Combust. Flame, 1981, 40, 71–79 CrossRef CAS.
- K. C. Patil, Chemistry of Nanocrystalline Oxide Materials: Combustion Synthesis, Properties and Applications, World Scientific, 2008 Search PubMed.
- M. Y. Nassar, T. Y. Mohamed, I. S. Ahmed and I. Samir, MgO nanostructure via a sol–gel combustion synthesis method using different fuels: an efficient nano-adsorbent for the removal of some anionic textile dyes, J. Mol. Liq., 2017, 225, 730–740 CrossRef CAS.
- R. Jenkins and R. L. Snyder, Introduction to X-ray powder diffractometry, John Wiley & Sons, Inc., New York, 1996 Search PubMed.
- T. Luttrell, S. Halpegamage, J. Tao, A. Kramer, E. Sutter and M. Batzill, Why is anatase a better photocatalyst than rutile? – Model studies on epitaxial TiO2 films, Sci. Rep., 2014, 4, 4043 Search PubMed.
- K. Nakamoto, Infrared and Raman Spectra of Inorganic and Coordination Compounds, Applications in Coordination, Organometallic, and Bioinorganic Chemistry, Wiley, 2009 Search PubMed.
- Y. Tang, S. Fu, K. Zhao, G. Xie and L. Teng, Synthesis of TiO2 nanofibers with adjustable anatase/rutile ratio from Ti sol and rutile nanoparticles for the degradation of pollutants in wastewater, Ceram. Int., 2015, 41, 13285–13293 CrossRef CAS.
- S. N. Karthick, K. V. Hemalatha, H. Seo, D. Ludeman, J.-K. Kim, K. Prabakar and H.-J. Kim, Titanium oxide prepared by polymer gel assisted combustion method for dye-sensitized solar cell, Current Applied Physics, 2011, 11, S127–S130 CrossRef.
- H. M. Aly, M. E. Moustafa, M. Y. Nassar and E. A. Abdelrahman, Synthesis and characterization of novel Cu(II) complexes with 3-substituted-4-amino-5-mercapto-1,2,4-triazole Schiff bases: a new route to CuO nanoparticles, J. Mol. Struct., 2015, 1086, 223–231 CrossRef CAS.
- M. Mostafa, H. M. Saber, A. A. El-Sadek and M. Y. Nassar, Preparation and performance of 99Mo/99mTc chromatographic column generator based on zirconium molybdosilicate, Radiochim. Acta, 2016, 257–265 CAS.
- M. Y. Nassar, A. S. Attia, K. A. Alfallous and M. F. El-Shahat, Synthesis of two novel dinuclear molybdenum(0) complexes of quinoxaline-2,3-dione: new precursors for preparation of α-MoO3 nanoplates, Inorg. Chim. Acta, 2013, 405, 362–367 CrossRef CAS.
- M. Y. Nassar, Size-controlled synthesis of CoCO3 and Co3O4 nanoparticles by free-surfactant hydrothermal method, Mater. Lett., 2013, 94, 112–115 CrossRef CAS.
- R. Venckatesh, K. Balachandaran and R. Sivaraj, Synthesis and characterization of nano TiO2–SiO2: PVA composite – a novel route, Int. Nano Lett., 2012, 2, 15 CrossRef.
- M. Thommes, K. Kaneko, V. Neimark Alexander, P. Olivier James, F. Rodriguez-Reinoso, J. Rouquerol and S. W. Sing Kenneth, Physisorption of gases, with special reference to the evaluation of surface area and pore size distribution (IUPAC Technical Report), Pure and Applied Chemistry, 2015, 1051 CAS.
- M. Ahmaruzzaman and S. Laxmi Gayatri, Batch adsorption of 4-nitrophenol by acid activated jute stick char: equilibrium, kinetic and thermodynamic studies, Chem. Eng. J., 2010, 158, 173–180 CrossRef CAS.
- M. Kosmulski, pH-dependent surface charging and points of zero charge. IV. Update and new approach, J. Colloid Interface Sci., 2009, 337, 439–448 CrossRef CAS PubMed.
- E. M. Hotze, T. Phenrat and G. V. Lowry, Nanoparticle Aggregation: Challenges to Understanding Transport and Reactivity in the Environment
All rights reserved. No part of this periodical may be reproduced or transmitted in any form or by any means, electronic or mechanical, including photocopying, recording, or any information storage and retrieval system, without permission in writing from the publisher, J. Environ. Qual., 2010, 39, 1909–1924 CrossRef CAS PubMed.
- V. Belessi, G. Romanos, N. Boukos, D. Lambropoulou and C. Trapalis, Removal of Reactive Red 195 from aqueous solutions by adsorption on the surface of TiO2 nanoparticles, J. Hazard. Mater., 2009, 170, 836–844 CrossRef CAS PubMed.
- Y. Yang, X. Lin, B. Wei, Y. Zhao and J. Wang, Evaluation of adsorption potential of bamboo biochar for metal-complex dye: equilibrium, kinetics and artificial neural network modeling, Int. J. Environ. Sci. Technol., 2014, 11, 1093–1100 CrossRef CAS.
- Y. S. Ho and G. McKay, The sorption of lead(II) ions on peat, Water Res., 1999, 33, 578–584 CrossRef CAS.
- Y. S. Ho and G. McKay, Pseudo-second order model for sorption processes, Process Biochem., 1999, 34, 451–465 CrossRef CAS.
- F. A. Batzias and D. K. Sidiras, Dye adsorption by prehydrolysed beech sawdust in batch and fixed-bed systems, Bioresour. Technol., 2007, 98, 1208–1217 CrossRef CAS PubMed.
- W. J. Wber and J. C. Morris, Proceedings of the International Conference on Water Pollution Symposium, Pergamon Press, Oxford, New York, 1962 Search PubMed.
- C. Luo, Z. Tian, B. Yang, L. Zhang and S. Yan, Manganese dioxide/iron oxide/acid oxidized multi-walled carbon nanotube magnetic nanocomposite for enhanced hexavalent chromium removal, Chem. Eng. J., 2013, 234, 256–265 CrossRef CAS.
- D. Hu and L. Wang, Adsorption of amoxicillin onto quaternized cellulose from flax noil: kinetic, equilibrium and thermodynamic study, J. Taiwan Inst. Chem. Eng., 2016, 64, 227–234 CrossRef CAS.
- S. M. Husnain, J.-H. Kim, C.-S. Lee, Y.-Y. Chang, W. Um and Y.-S. Chang, Superparamagnetic nalidixic acid grafted magnetite (Fe3O4/NA) for rapid and efficient mercury removal from water, RSC Adv., 2016, 6, 35825–35832 RSC.
- G. D. Halsey, The Role of Surface Heterogeneity in Adsorption, in Advances in Catalysis, ed. V. I. K. W. G. Frankenburg and E. K. Rideal, Academic Press, 1952, pp. 259–269 Search PubMed.
- T. G. Venkatesha, R. Viswanatha, Y. Arthoba Nayaka and B. K. Chethana, Kinetics and thermodynamics of reactive and vat dyes adsorption on MgO nanoparticles, Chem. Eng. J., 2012, 198–199, 1–10 CrossRef CAS.
- Y. Liu, Is the Free Energy Change of Adsorption Correctly Calculated?, J. Chem. Eng. Data, 2009, 54, 1981–1985 CrossRef CAS.
- R. Niwas, U. Gupta, A. A. Khan and K. G. Varshney, The adsorption of phosphamidon on the surface of styrene supported zirconium(IV) tungstophosphate: a thermodynamic study, Colloids Surf., A, 2000, 164, 115–119 CrossRef CAS.
- S. K. Milonjić, A consideration of the correct calculation of thermodynamic parameters of adsorption, J. Serb. Chem. Soc., 2007, 72, 1363–1367 CrossRef.
- X. Zhou and X. Zhou, The Unit Problem In The Thermodynamic Calculation Of Adsorption Using The Langmuir Equation, Chem. Eng. Commun., 2014, 201, 1459–1467 CrossRef CAS.
- P. S. Ghosal and A. K. Gupta, Determination of thermodynamic parameters from Langmuir isotherm constant-revisited, J. Mol. Liq., 2017, 225, 137–146 CrossRef CAS.
- H. N. Tran, S.-J. You and H.-P. Chao, Thermodynamic parameters of cadmium adsorption onto orange peel calculated from various methods: a comparison study, J. Environ. Chem. Eng., 2016, 4, 2671–2682 CrossRef CAS.
- A. A. Khan and R. P. Singh, Adsorption thermodynamics of carbofuran on Sn(IV) arsenosilicate in H+, Na+ and Ca2+ forms, Colloids Surf., 1987, 24, 33–42 CrossRef CAS.
- H. R. Mahmoud, S. M. Ibrahim and S. A. El-Molla, Textile dye removal from aqueous solutions using cheap MgO nanomaterials: adsorption kinetics, isotherm studies and thermodynamics, Adv. Powder Technol., 2016, 27, 223–231 CrossRef CAS.
- M. Ghaedi, A. Hekmati Jah, S. Khodadoust, R. Sahraei, A. Daneshfar, A. Mihandoost and M. K. Purkait, Cadmium telluride nanoparticles loaded on activated carbon as adsorbent for removal of sunset yellow, Spectrochim. Acta, Part A, 2012, 90, 22–27 CrossRef CAS PubMed.
- J. Ma, Y. Jia, Y. Jing, Y. Yao and J. Sun, Kinetics and thermodynamics of methylene blue adsorption by cobalt–hectorite composite, Dyes Pigm., 2012, 93, 1441–1446 CrossRef CAS.
- O. Aksakal and H. Ucun, Equilibrium, kinetic and thermodynamic studies of the biosorption of textile dye (Reactive Red 195) onto Pinus sylvestris L., J. Hazard. Mater., 2010, 181, 666–672 CrossRef CAS PubMed.
- A. Xue, S. Zhou, Y. Zhao, X. Lu and P. Han, Adsorption of reactive dyes from aqueous solution by silylated palygorskite, Appl. Clay Sci., 2010, 48, 638–640 CrossRef CAS.
- A. Y. Dursun and O. Tepe, Removal of Chemazol Reactive Red 195 from aqueous solution by dehydrated beet pulp carbon, J. Hazard. Mater., 2011, 194, 303–311 CrossRef CAS PubMed.
- F. Çiçek, D. Özer, A. Özer and A. Özer, Low cost removal of reactive dyes using wheat bran, J. Hazard. Mater., 2007, 146, 408–416 CrossRef PubMed.
Footnote |
† Electronic supplementary information (ESI) available. See DOI: 10.1039/c6ra27924d |
|
This journal is © The Royal Society of Chemistry 2017 |
Click here to see how this site uses Cookies. View our privacy policy here.