DOI:
10.1039/C6RA27409A
(Paper)
RSC Adv., 2017,
7, 5466-5472
Phytate extraction from coproducts of the dry-grind corn ethanol process
Received
27th November 2016
, Accepted 12th January 2017
First published on 24th January 2017
Abstract
Distiller's dried grains with solubles (DDGS), the major coproduct of dry-grind ethanol production, are being increasingly used in the global market as animal feeds for both energy and protein supplement. DDGS contains high levels of phosphorus in the form of phytate, which cannot be digested by monogastric animals, such as poultry and swines, which in turn produce manure with high levels of phosphorus. Phytate is a highly-valued chemical and can be recovered from DDGS precursors in the downstream processing of dry-grind coproducts. This study was aimed at the utilization of the AG 1-X8 anion exchange resin to remove and purify phytates from thin stillage, and near 100% efficiency of adsorption and over 90% desorption from the resin beads was achieved. The end product showed a similar profile to the standard phytate, and could be precipitated and crystallized as calcium phytate. This process may potentially bring benefits to the parties involved, more revenue to corn ethanol facilities, improved digestibility of animal feeds, and minimized environmental impact, as less manure with a high content of phosphorus is applied to the soil.
Introduction
With the recent expansion of the U.S. corn ethanol industry and fluctuations in the corn and ethanol markets, the coproducts generated from ethanol separation processes are playing a vital role in the overall economic turnout of corn ethanol facilities and are saturating the global markets with feeds for energy and protein replacement.1 In a typical dry-grind processing, corn is directly milled without soaking in water and then enzymes and yeast are sequentially added for the ethanol fermentation.2 This process is characterized for its high versatility and low capital investment. The fermentation broth is then processed by distillation, such that ethanol is separated and the residue is the whole stillage (WS). WS is composed of proteins, fibers, residual sugars, lipids, and other minor components, derived from both the yeast cells and unfermented corn residues.3 WS is centrifuged and separated into two streams: thin stillage (TS), a liquid phase with over 90% of moisture content, and wet distillers grains (WDG), which is the heavy fraction, with a solid content of around 50%. Throughout the several possible procedures found in industrial plants, TS is usually evaporated and concentrated to achieve a lower moisture content, producing industrial “syrup”, often labelled as condensed distillers with solubles (CDS). This syrup is then mixed with the solids present from WDG, and then dried at high temperatures to generate distiller's dried grains with solubles (DDGS).4 In order to increase the shelf life of DDGS for commercialization, the drying process of DDGS is crucial. During the pre-processing of the corn grains the dry-grind process is conducted by physical methods such as hammering, and thus the generated coproducts usually contain detectable levels of starch and impurities.5 There are often additives in this process, such as enzymes and vitamins, which can increase the overall nutritional value of DDGS.6
There has been a growth in the production and commercialization of DDGS due to the rapid expansion of the dry-grind process throughout the ethanol industry. Due to the nutritional value present in DDGS, it quickly gained attention from the markets and in 2015 achieved a significant share, about 23%, of the non-ruminant animal feeding markets, such as poultry and swine industries.7 DDGSs are also an important source of minerals and are known as a feeding material rich in potassium, magnesium, zinc, sulfur, and phosphorus (P).8,9 As regards to P, this nutrient is often regarded as one of the most economic value components in animal feeds. However, Spiehs et al.10 reported too high levels of P in DDGS, with concentrations as high as 10 g of P per kg on dry basis. Such concentration is higher than the requirements of most ruminant animals.6 In DDGS, the largest portion of organic P is found as phytate. This molecule cannot be directly assimilated by non-ruminant animals due to the lack of microbial phytases in their digestive system.11 Feeding non-ruminants with phytate-rich materials, such as DDGS, will further increase the P content in manures, which are often applied as fertilizers by farmers.10 These high levels of P in soil typically exceed the soil binding capacity for phosphates and other forms of P ions, potentially resulting in high levels of P in runoff water. The major environmental impact of such an effect is the eutrophication of surface and underground water bodies.6,12,13
In corn, P is mostly present as inositol-phosphates.14 One molecule of inositol can bind up to six phosphate anions. The fully substituted molecule, inositol-hexaphosphate (IP6), is often referred as phytic acid, or known by its salt name, phytate. According to Ravindran et al.,15 phytate is present in levels ranging from 50% to 80% of the total P present in corn. Phillippy et al.16 evaluated the potential of industrial yeasts for hydrolyzing phytate during ethanol fermentation, and reported that these cells are able to produce phytase. This enzyme is able to degrade phytate to the forms of inositol mono-, bis-, tris-, tetra-, and pentakisphosphates (IP1, IP2, IP3, IP4, and IP5), as well as inorganic phosphate. The global market for phytase has grown significantly over the past years, resolving specific demands for monogastric animals, and its market value reached over 700 million US dollars in 2015.17 However, according to Liu and Han,3 in corn-to-ethanol fermentation systems without exogenous phytase addition, about 40% to 50% of P in the fermentation mash usually remains as phytate.
Several attempts to increase the degradation of phytate throughout or after the fermentation have been recently reported in the literature. Noureddini and Dang18 added phytase from Aspergillus niger to catalyze phytate hydrolysis in WS, whereas Khullar et al.19 proposed a step of incubation with phytase prior to corn saccharification. Despite the environmental problems posed with phytates in the corn ethanol industry, this molecule is often seen as a high-value chemical in the market. Highly employed by some sectors of the food market and textile industries, phytate exhibits strong chelating and preservative properties,20,21 and an excellent inoxidizability,22 being often used as food additive, preservative, and antioxidant. In recent years, the beneficial effects of phytates have been highlighted and explored by the pharmaceutical industry, particularly in the prevention of renal calculi,23 diabetes,24 some types of cancer,25 and Parkinson's disease.26
If phytate could be extracted from DDGS, it will be a win–win situation for both the industrial sector and environmental protection. The industrial process for phytate manufacturing consists of acid extraction from rice bran or cereals, followed by a chemical precipitation step. Strong acids are needed to dissolve phytates in a traditional phytate extraction.27 If phytate was to be recovered from end products, such as DDGS, the low pH of the extracted product would likely make it inappropriate as a feeding material. Ion exchange techniques have been applied to extract P products from liquids.28–30 However, little has been done on phytate extraction from corn ethanol coproducts. This study assayed a particular type of anionic resin, AG 1-X8, and the critical operational conditions to maximize phytate extraction from dry-grind coproducts.
Materials and methods
Sample collection, storage and chemicals
WS, TS, WDG, CDS, and DDGS were obtained from a large-scale dry-grind corn ethanol plant located in the state of Iowa, USA. All samples were stored in the refrigerator at −20 °C prior to use. The AG 1-X8 anion exchange resin (100–200 mesh, chloride form) was purchased from Bio-Rad Co. (Berkeley, CA). All the other chemicals were of analytical grade.
Sample analysis and preparation
All samples were analyzed for moisture content (wet basis), total P, and phytate P. Moisture content was defined as the ratio between the weight loss after drying at 105 °C and the wet weight. For total P determination, samples were dry-ashed, and the colorimetric assay for P was performed in the digests. The samples were analyzed with an adapted molybdate-blue method, based on P test kits (Hach, Loveland, CO). An acid extraction with 1 mol L−1 HCl was performed prior to phytate analysis. In order to precipitate the P salts, the pH of the liquid phases, containing soluble phytates, was changed to neutral by treatment with 1 mol L−1 CaCl2 solution. P salt sediments were then washed, dried and redissolved in 1 mol L−1 HCl, for which analysis on total P and phosphate P by the molybdate-blue method were conducted. Phytate P content was defined as the difference between total P and phosphate P. All chemical analyses were conducted in triplicate.
Batch extraction: adsorption and desorption
The AG 1-X8 resin was equilibrated with 2 mol L−1 HCl, and then washed with distilled water, promoting the pH change to neutral. Then, 10 mL of CDS or TS solution were added to a 25 mL glass vial containing 3 g of the resin. Adsorption efficiency was defined as the ratio between the P concentration in the supernatant and the initial P concentration in the liquid phase. Throughout full factorial experimental design, effect of time, temperature, and pH on adsorption were investigated.
For evaluating desorption, the resin beads were removed by filtration and added to various eluent solutions at different concentrations. These eluents (HCl, NaOH, and NaCl) were intended to elute the retained P anions from the resin beads. Desorption efficiency was calculated as the ratio between P concentration in the supernatant and total P amount adsorbed on the resin beads.
Column extraction – adsorption and desorption
A chromatographic glass column (1.0 cm × 30 cm) was used as support for the AG 1-X8 resin. The resin beads, loaded at different weights, were equilibrated with HCl 2 mol L−1 and washed with distilled water until the pH in the eluted water was neutral. The liquid phase of TS was used as the target solution, which was added sequentially with a loading increment of 10 mL, i.e., each 10 mL of solution added and adsorbed was analyzed in terms of reduction of the P level. Prior to desorption, the resin beads were washed with distilled water for removal of impurities.
For the desorption experiments, the desorption agent solution was loaded sequentially in volumes of 10 mL, i.e., each 10 mL of solution added was analyzed in terms of concentration of P compound. Desorption efficiency was defined as the increment in P concentration over the amount of P adsorbed on the resin beads.
Calcium phytate precipitation and attenuated total reflection Fourier transform infrared spectroscopy (ATR-FTIR) analysis
Phytate precipitation was carried out by adding excess Ca2+, as CaCl2, followed by a pH shift to neutral by the addition of NaOH. The obtained sediments were washed with distilled water and dried at 105 °C until constant weight was obtained.
For the ATR-FTIR analysis, spectra were recorded in the 4000 to 400 cm−1 range on a Thermo Scientific Nicolet iS50 FTIR spectrometer (Waltham, MA) with a built-in diamond ATR. The background used was ambient air. Each test was scanned 32 times with a resolution of 0.24 cm−1. All spectra were normalized. Sodium phytate hydrate from rice (S06880/Pfaltz & Bauer, Waterbury, CT) was used as standard. Sodium phytate samples were obtained using NaCl as the eluting agent, followed by evaporating this solution at 40 °C.
Results and discussion
Moisture content and P analysis
The WS, containing undissolved corn fragments and residual yeast cells, presented a moisture content of 87.94%. During solid–liquid separation of WS, most solids in WS are redirected to WDG. TS had a moisture content of 95.71%, whereas WDG had 49.75%. In CDS, concentrated from TS through series of evaporations, a moisture content of 70.48% was achieved. CDS has a viscous texture, and moisture contents lower than 70% are economically unfeasible,9 mainly due to the increase in suspended solids and osmotic pressure. The dry blend of CDS and WDG was dried to produce DDGS. DDGS samples used in this study presented moisture contents of about 14.92%, within the expected range reported to prevent DDGS from becoming moldy and unusable.31
WS had a total P concentration of 12.02 mg g−1, of which 40% was found to be phytate P, with a concentration of 4.81 mg g−1. After the first solid–liquid separation, the concentrations of total P and phytate P (23.57 mg g−1 and 10.11 mg g−1, respectively) in the TS had doubled, whereas WDG presented much lower concentrations of total P and phytate P (10.21 mg g−1 and 3.27 mg g−1, respectively). The difference was most likely attributed to the fact that more P went to the liquid phase (TS) than the solid phase (WDG) during the solid–liquid separation of WS, which primarily indicates that most P in the streams is soluble.3 The water removal step on TS to produce CDS maintained similar levels of total P (23.77 mg g−1) and showed a slight decrease of phytate P (9.41 mg g−1). Due to the recycling of a TS portion as a backset for the cooking step, the concentrations of both total P and phytate P in DDGS (10.59 mg g−1 and 4.50 mg g−1, respectively) were just a little lower than those of WS.3 Comparing with the literature results,4 similar values were found, particularly for fractions of TS (19.4 mg g−1), CDS (18.8 mg g−1), and WS (11.0 mg g−1) in terms of total P. As shown in Table 1, TS was the stream with the highest moisture content in the downstream processing of dry-grind coproducts.
Table 1 Moisture content, total P, and phytate P in dry-grind coproducts
Sample |
Moisture content (%) |
Total P (mg g−1) |
Phytate P (mg g−1) |
WS |
87.94 ± 0.15 |
12.02 ± 0.60 |
4.81 ± 0.01 |
TS |
95.71 ± 0.13 |
23.57 ± 1.12 |
10.11 ± 0.66 |
WDG |
49.75 ± 0.40 |
10.21 ± 0.53 |
3.27 ± 0.21 |
CDS |
70.48 ± 0.22 |
23.77 ± 0.23 |
9.41 ± 0.34 |
DDGS |
14.33 ± 0.39 |
10.59 ± 0.20 |
4.50 ± 0.15 |
Corn grain presents high phytate levels, with as much as 90% of organic P found as phytate,32 representing overall levels of around 75% of the total P found in the kernel.33 Assuming that the P present in corn is not a limiting factor in the ethanol fermentation, and thus, no extra P is added to the fermentation media, it is observed that phytate levels decrease when comparing ethanol coproducts and corn. Andlid et al.34 attributed this to the expression of a type of phytase enzyme by Saccharomyces cerevisiae during the fermentation. We assumed that the combination of acidic pH, high temperature during processing, and the presence of endogenous phytase in the fermentation tank favor the hydrolysis of the phytate present in corn. Even though phytate levels are decreased on a relative basis, Liu and Han3 described several-fold increase in nutrients during the downstream processing of dry-grind ethanol plants. Thus, phytate, even though is degraded during fermentation, is still found at relative large concentrations due to nutrient increase, as described by Liu and Han.3
Evaluation of phytate extractants
Experiments of phytate extraction with acid or water (Fig. 1) show that phytate concentrations in acid and water extracts from CDS differed by only 6.2% (1026 mg L−1 for the acid extract, and 966 mg L−1 for the water extract), with a significance level of 0.06. Similar results were reported, with 82% of the total P in WS dissolved in the liquid phase.13 Since the majority of phytates in the streams were present as the soluble form, the extraction with strong acids, which brings additional cost and damage to the raw material and barely provides any significant process gain, could be avoided. Thus, the feeding value of the coproducts could be maintained by introducing a mild extraction method.
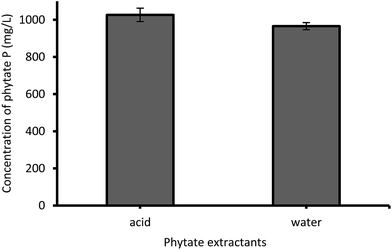 |
| Fig. 1 Phytate extraction from CDS by different extractants. | |
Latta and Eskin,35 and Haug and Lantzsch36 have developed extraction methods for phytate in cereals. Their methods include an acid pretreatment of phytate-rich grains, using dilute HCl, which has proven to dissolve the phytate present in granules into the bulk solution phase. The results of this study showed that most phytate may have already been dissolved in the liquid fraction due to the low pH (4.42) of CDS. In addition, the pH of TS and WS were 4.47 and 4.48, respectively, which meant phytate in TS and WS were likely to be present in its soluble form, as evidenced from the significant increase in concentration of this substance in the liquid phase (TS).
Effect of moisture content on the batch extraction of phytate by anion exchange
Batch extraction of phytate from CDS at different dilutions (Table 2) showed significant variability among samples with different moisture contents (p-value <0.05 for total P and phosphate). Controlling the moisture content of CDS by water addition reflected the concentration of P in the samples. Resin AG 1-X8 showed a better adsorption performance on P solutions with lower concentrations, achieving a 64.51% adsorption of the total P at a moisture content of 95%, whereas only 43.92% of the total P was adsorbed at a moisture content of 75%. Solid–liquid adsorption occurs in four steps: liquid phase mass transfer, interface diffusion between the liquid phase and the exterior surface of the adsorbent, intrapellet mass transfer involving pore diffusion and surface diffusion, and an adsorption–desorption reaction. The increase in viscosity and osmotic pressure effects followed by a decrease in moisture content is hypothesized to be a key factor in the liquid phase mass transfer and on the pore diffusion and surface diffusion processes involved in ion exchange.
Table 2 Effect of moisture content, temperature, time, and pH on P adsorption
Factor |
Level |
Adsorption efficiency (%) |
Phosphate |
Total P |
Moisture content of CDS (%) |
95 |
50.70 |
64.51 |
90 |
46.42 |
59.13 |
85 |
37.70 |
54.47 |
80 |
33.83 |
49.85 |
75 |
31.43 |
43.92 |
Temperature (°C) |
4 |
34.83 |
62.65 |
30 |
38.86 |
64.26 |
40 |
39.53 |
63.02 |
50 |
39.32 |
63.68 |
60 |
38.68 |
63.24 |
Time (min) |
10 |
38.68 |
64.26 |
20 |
39.53 |
64.49 |
30 |
38.89 |
64.39 |
60 |
40.17 |
64.19 |
120 |
38.98 |
64.42 |
1440 |
39.53 |
63.97 |
pH |
1 |
22.85 |
47.01 |
2 |
28.39 |
57.29 |
3 |
31.73 |
59.26 |
4 |
33.54 |
63.09 |
5 |
35.27 |
64.19 |
6 |
39.92 |
64.17 |
The highest adsorption efficiency of phosphate and total P was attained on diluted CDS with 95% moisture content, which was very close to that of TS (95.71%). In this process, approximately 75% of the total P flows into TS after centrifugation of WS.4 If most phytate in TS could be extracted, the final content of phytate in DDGS would be drastically decreased. Furthermore, due to the composition of TS, most residual solids, which are dead yeast cells and small corn residue particles,37 can be separated by a simple filtration, centrifugation or decantation. Therefore, subsequent extraction experiments were focused on TS.
Effect of temperature and time on the batch extraction of phytate by anion exchange
The adsorption efficiency for TS, an extract with high concentrations of total P, presented a constant value of 63.4% for total P (p-value < 0.01) and a desirable lower efficiency of 38.1% for phosphate (p-value < 0.05), across the range of temperatures studied, as shown in Table 2. The robustness of this resin, under the conditions studied, is highly desirable for P extraction because, according to Lee et al.,38 processing of TS in a dry-grind ethanol plant occurs within a narrow range of temperatures close to 70 °C.
The results for adsorption potential were constant at the time range studied (Table 2), from 10 min to 1440 min, achieving a constant value of 64% (p-value < 0.05). These results may suggest that the adsorption equilibrium occurred within 10 min at the conditions studied. Previous chromatographic separations of phytate using similar types of resins and conditions achieved good separation of phytate within 30 minutes (ref. 35) or even with a separation column without control of residence time.36 The high moisture content and the amount of resin in contact with the bulk suspension of stillage allow a high adsorption rate, as predicted by Latta and Eskin.35
Effect of pH on the batch extraction of phytate by anion exchange
The results at the bottom of Table 2 showed better adsorption for both total P and phosphate at higher pH values within the acidic region. At extremely acidic conditions, such as pH 1, 2, and 3, total P was adsorbed at 47.01%, 57.29%, and 59.26%, respectively. Similar to phosphate, the values were 22.85%, 28.39%, and 31.73%. For pH values ranging from 4 to 6, a plateau region was obtained for the adsorption of total P, attaining a circa 63% adsorption on the resin beads. For phosphate, however, there was still an increase in the adsorption within this range with the increment of pH, with values of 33.54%, 35.27%, and 39.92% at pH values of 4, 5, and 6, respectively. The highest P adsorption levels were achieved at higher pH values. Kaufman and Kleinberg39 claimed that one of the most important factors for adsorption in anionic resins was the solution anion electronegativity. Phytate has six protons with pKa values of 2.18, two with pKa of 5.73, and two with pKa equal to 9.21.40 Therefore, a high pH will favor the ionization of phytate by dissociating H+ from the hydroxyls, resulting in an increase of electronegativity in phytate, which in turn will increase the ability of phytate to participate in the anion exchange.39 However, the precipitation that occurs in TS when pH is over 7 would hinder the anion exchange. The resin presented a good adsorption performance when the pH was from 4 to 6 (Table 2). Since the pH of the TS (4.47) was within this range, no pH adjustment was needed before adsorption.
Phytate desorption from the anion exchange resin
NaCl exhibited a better desorption performance on adsorbed phytate at both 0.5 and 1.0 mol L−1 concentrations as compared to HCl and NaOH (Table 3).
Table 3 Effect of various eluents with different concentrations on the desorption efficiency of P
Desorption agent |
Desorption efficiency (%) |
Concentration (mol L−1) |
Phosphate |
Phytate |
Total P |
HCl |
0.5 |
65.96 |
26.15 |
26.15 |
1.0 |
69.96 |
45.39 |
46.24 |
NaCl |
0.5 |
60.47 |
33.87 |
36.24 |
1.0 |
75.00 |
83.69 |
77.33 |
NaOH |
0.5 |
47.73 |
9.66 |
16.35 |
1.0 |
69.40 |
35.55 |
37.34 |
Table 4 shows that the highest desorption efficiency for phytate was obtained when the concentration of NaCl was over 1.5 mol L−1. Thereby, 1.5 mol L−1 NaCl was used as eluent in subsequent column phytate extraction experiments. This can be explained by the displacement of adsorbed phosphorus anions by chloride anions from the eluate solution. The better performance of NaCl as a desorption agent agrees with a previous methodology for phytate extraction from cereal grains, in which Latta and Eskin35 used NaCl to selectively desorb phytate over inorganic phosphate from a similar anion exchange system. Helfferich41 described that NaCl is preferably used as a desorption agent, or even regeneration agent in some conditions, due to its low-toxic potential and low cost.
Table 4 Effect of different NaCl concentrations on the desorption efficiency of P
NaCl concentration (mol L−1) |
Desorption efficiency (%) |
Phosphate |
Phytate |
Total P |
0.05 |
36.15 |
2.68 |
9.44 |
0.10 |
48.97 |
3.09 |
12.43 |
0.25 |
57.81 |
8.21 |
18.17 |
0.50 |
60.47 |
33.87 |
36.24 |
1.00 |
72.39 |
81.96 |
73.97 |
1.50 |
83.98 |
98.52 |
88.26 |
2.00 |
80.60 |
97.50 |
86.87 |
Column extraction
The column extraction results shown in Fig. 2, demonstrate a higher adsorption rate for phytate P than that for phosphate P. One of the most plausible theories could be the higher concentration of negatively charged oxygen atoms in phytate than in phosphate.39 The adsorption efficiency of phytate was sometimes over 100%, and this excessive contribution was probably due to the presence of P in other forms being considered as phytate and also adsorbed on the resin. The scope of the adsorption curve shows a gradual decrease in the adsorption efficiency, explained by saturation of the resin beads with adsorbed ions. The results confirmed this theory since the higher the resin load, the higher the absolute saturation potential was determined to be. This increase might have resulted from the longer adsorption time caused by a higher amount of resin in the column.
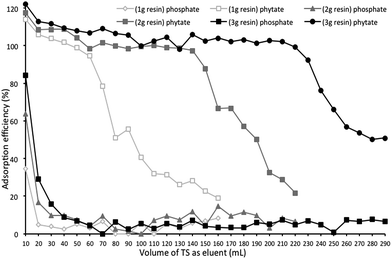 |
| Fig. 2 Adsorption of phosphate and phytate during column extraction. | |
For the column containing 3 g of AG 1-X8 resin, approximately 100% of total phytate and 6.15% of total phosphate in TS were adsorbed, using 220 mL of TS as elution agent. The results also showed a recovery of about 91% of adsorbed phytate using 1.5 mol L−1 NaCl as the desorption agent, which had a total volume of 30 mL (Fig. 3). As a direct consequence of this, the eluate solution showed a significant increase in the concentration of phytate, when compared to its original concentration in the dry-grind coproducts. This increase in the concentration could be conducive to harvest phytate via chemical precipitation.
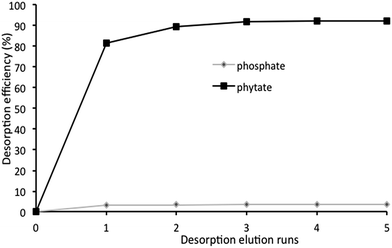 |
| Fig. 3 Desorption of phosphate and phytate during column extraction. | |
ATR-FTIR analysis of extracted phytate
The ATR-FTIR spectra of standard sodium phytate and extracted sodium phytate are shown in Fig. 4. A weak absorption band around 1645 cm−1 and a broad absorption band at 3400 cm−1 (data not shown) were attributed to O–H bonds of the adsorbed water molecules.42 The absorption band around 1398 cm−1 was assigned to the C–O stretching vibration.43 Two bands around 1186 and 496 cm−1 are attributed to the PO43− groups. The bands around 1038, 986, 909, 850 and 793 cm−1 were ascribed to C–O–P vibrations from various types of phytate (IP2–IP6).44 The small shifts in the vibrational bands between the two types of sodium phytate were possibly due to the residual sodium chloride mixed in the extracted one and different types of phytate in the samples.43
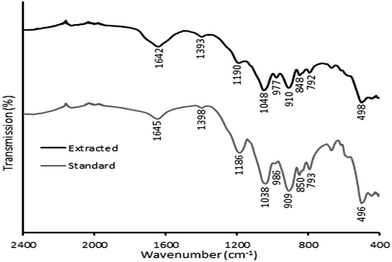 |
| Fig. 4 FTIR spectra of sodium phytate from the extractions and standard sodium phytate from rice bran. | |
Overall yield and significance of the process
Precipitation of phytate with Ca2+ ions does not only remove the chloride ions that are simultaneously desorbed, but also promotes the discoloration by the removal of some organic chromophoric molecules, which phytate could have adsorbed after the elution. From the results, 0.49 g of calcium phytate was yielded as a result of the first 30 mL elution. Based on the results, it was calculated that 0.39 g of P as pure phytate, or the equivalent of 1.85 g of calcium phytate, could be obtained from 1 kg of TS with the optimized conditions of this study.
The approach in this study provided a new method to remove phytate from the coproducts of the dry-grind corn ethanol process. It is expected that this extraction process will not have any significant negative effects on the nutritional value of DDGS as a whole since major nutrients cannot be adsorbed to the column under the conditions studied. For the dry-grind ethanol downstream processing, approximately 75% of the P present in WS is sent to TS.4 Thus, if most phytate in TS could be extracted, final content of P in DDGS would be drastically reduced. Removal of P from ethanol coproducts has been described before by Alkan-Ozkaynak et al.,45 where they used aluminium- and calcium-based coagulants to recover P from TS through a chemical-based separation process, resulting in a sludge that could be applied to agriculture fields. This can provide a feasible solution to the P issue in DDGS, but little value is gained after the sludge is applied to the land. On the other hand, extraction of phytate and generation of calcium phytate can potentially yield additional revenue to the ethanol industry, as well as provide a solution to attenuate environmental concerns regarding the eutrophication of water bodies due to P runoff. Usually, P in soil after manure application moves to groundwater bodies and deep soil layers, potentially damaging the aquatic environment by eutrophication.46 This process may provide a great opportunity for the U.S. ethanol industry because extracting phytate from corn ethanol coproducts can create additional revenue while increasing the feeding value of coproducts and decreasing the P content in animal manure.
Conclusion
With this study, it was proved that it is better to start the extraction of phytate directly from TS since its acid treatment did not result in a significantly larger gain of phytate extraction. The AG 1-X8 resin was proved to be effective within the typical temperature range for TS processing, and the extraction could be accomplished within several minutes. Sodium chloride was proven to be the best desorption agent. Both the AG 1-X8 resin and NaCl have superior specificity for phytate adsorption and desorption over inorganic phosphate. The overall process could yield up to 1.85 g of calcium phytate per kg of TS.
Acknowledgements
This study was partially supported by grants from MnDrive Global Food Ventures and also partially supported by the Nanjing Forestry University (Priority Academic Program Development of Jiangsu Higher Education Institution). Reis's research is supported by CAPES, the Ministry of Education of Brazil, under grant number 13252/13-5.
References
- K. Wang, L. Ou, T. Brown and R. C. Brown, Biofuels, Bioprod. Biorefin., 2015, 9, 190–200 CrossRef CAS.
- P. Luangthongkam, L. Fang, A. Noomhorm and B. Lamsal, Ind. Crops Prod., 2015, 77, 803–808 CrossRef CAS.
- K. Liu and J. Han, Bioresour. Technol., 2011, 102, 3110–3118 CrossRef CAS PubMed.
- A. Alkan-Ozkaynak and K. G. Karthikeyan, J. Environ. Qual., 2012, 41, 1695–1701 CrossRef CAS PubMed.
- H. Zabed, A. N. Boyce, J. N. Sahu and G. Faruq, J. Cleaner Prod., 2017, 142, 4282–4293 CrossRef CAS.
- K. D. Rausch and R. L. Belyea, Appl. Biochem. Biotechnol., 2006, 128, 47–86 CrossRef CAS PubMed.
- Renewable Fuels Association, Ethanol Industry Outlook, 2016, <http://ethanolrfa.org/resources/publications/outlook/>.
- A. Batal and N. Dale, J. Appl. Poult. Res., 2003, 12, 400–403 CrossRef CAS.
- R. L. Belyea, T. E. Clevenger, V. Singh, M. E. Tumbleson and K. D. Rausch, Appl. Biochem. Biotechnol., 2006, 134, 113–128 CrossRef CAS PubMed.
- M. J. Spiehs, M. H. Whitney and G. C. Shurson, J. Anim. Sci., 2002, 80, 2639–2645 CrossRef CAS PubMed.
- G. L. Cromwell, R. D. Coffey, H. J. Monegue and J. H. Randolph, J. Anim. Sci., 1995, 73, 449–456 CrossRef CAS PubMed.
- R. Koelsch and G. Lesoing, J. Anim. Sci., 1999, 77, 63–71 CrossRef CAS PubMed.
- H. Noureddini, M. Malik, J. Byun and A. J. Ankeny, Bioresour. Technol., 2009, 100, 731–736 CrossRef CAS PubMed.
- N. R. Reddy, S. K. Sathe and D. K. Salunkhe, Adv. Food Res., 1982, 28, 1–92 CAS.
- V. Ravindran, W. L. Bryden and E. T. Kornegay, Avian Poultry Biol Rev, 1995, 6, 125–143 Search PubMed.
- B. Q. Phillippy, K. D. White, M. R. Johnston, S. H. Tao and M. R. S. Fox, Anal. Biochem., 1987, 162, 115–121 CrossRef CAS PubMed.
- K. Bhavsar and J. M. Khire, RSC Adv., 2014, 4, 26677–26691 RSC.
- H. Noureddini and J. Dang, Appl. Biochem. Biotechnol., 2009, 159, 11–23 CrossRef CAS PubMed.
- E. Khullar, J. K. Shetty, K. D. Rausch, M. E. Tumbleson and V. Singh, Cereal Chem., 2011, 88, 223–227 CrossRef CAS.
- R. Angel, N. M. Tamim, T. J. Applegate, A. S. Dhandu and L. E. Ellestad, J. Appl. Poult. Res., 2002, 11, 471–480 CrossRef CAS.
- A. Cupisti and K. Kalantar-Zadeh, Semin. Nephrol., 2013, 33, 180–190 CrossRef CAS PubMed.
- A. Marie Minihane and G. Rimbach, Int. J. Food Sci. Technol., 2002, 37, 741–748 CrossRef.
- N. K. Saw, K. Chow, P. N. Rao and J. P. Kavanagh, J. Urol., 2007, 177, 2366–2370 CrossRef CAS PubMed.
- S.-H. Lee, H.-J. Park, H.-K. Chun, S.-Y. Cho, S.-M. Cho and H. S. Lillehoj, Nutr. Res., 2006, 26, 474–479 CrossRef CAS.
- I. Vucenik and A. M. Shamsuddin, Nutr. Cancer, 2006, 55, 109–125 CrossRef CAS PubMed.
- Q. Xu, A. G. Kanthasamy and M. B. Reddy, Toxicology, 2008, 245, 101–108 CrossRef CAS PubMed.
- C. Canan, F. T. L. Cruz, F. Delaroza, R. Casagrande, C. P. M. Sarmento, M. Shimokomaki and E. I. Ida, J. Food Compos. Anal., 2011, 24, 1057–1063 CrossRef CAS.
- J. Lehrfeld, Cereal Chem., 1989, 66, 510–515 CAS.
- J. G. March, B. M. Simonet and F. Grases, J. Chromatogr. B: Biomed. Sci. Appl., 2001, 757, 247–255 CrossRef CAS.
- H.-R. Park, H.-J. Ahn, S.-H. Kim, C.-H. Lee, M.-W. Byun and G.-W. Lee, Food Control, 2006, 17, 727–732 CrossRef CAS.
- R. Bhadra, K. Muthukumarappan and K. A. Rosentrater, ASAE Paper, 2007, 1, 077009 Search PubMed.
- C. D. Boyer, J. C. Shannon, S. A. Watson and P. E. Ramstad, Corn: Chemistry and Technology, 1987, 253–272 Search PubMed.
- P. H. Abelson, Science, 1999, 283, 2015 CrossRef CAS PubMed.
- T. A. Andlid, J. Veide and A.-S. Sandberg, Int. J. Food Microbiol., 2004, 97, 157–169 CrossRef CAS PubMed.
- M. Latta and M. Eskin, J. Agric. Food Chem., 1980, 28, 1313–1315 CrossRef CAS.
- W. Haug and H. J. Lantzsch, J. Sci. Food Agric., 1983, 34, 1423–1426 CrossRef CAS.
- C. Liu, B. Hu, S. Chen and R. W. Glass, Appl. Biochem. Biotechnol., 2007, 137, 875–884 CrossRef PubMed.
- P. H. Lee, J. Bae, J. Kim and W. H. Chen, J. Chem. Technol. Biotechnol., 2011, 86, 1514–1520 CrossRef CAS.
- H. W. Kaufman and I. Kleinberg, Arch. Oral Biol., 1970, 15, 917–934 CrossRef CAS PubMed.
- W. J. Evans, E. J. McCourtney and R. I. Shrager, J. Am. Oil Chem. Soc., 1982, 59, 189–191 CrossRef CAS.
- F. G. Helfferich, Ion Exchange, Courier Corporation, 1962 Search PubMed.
- L. Celi, S. Lamacchia, F. A. Marsan and E. Barberis, Soil Sci., 1999, 164, 574–585 CrossRef CAS.
- K. Ganesan and M. Epple, New J. Chem., 2008, 32, 1326–1330 RSC.
- Z. He, C. W. Honeycutt, T. Zhang and P. M. Bertsch, J. Environ. Qual., 2006, 35, 1319–1328 CrossRef CAS PubMed.
- A. Alkan-Ozkaynak, K. G. Karthikeyan and A. Roa-Espinosa, Trans. ASABE, 2010, 53, 1287–1294 CrossRef CAS.
- X. Zhang, H. Lin and B. Hu, RSC Adv., 2016, 6, 57960–57968 RSC.
|
This journal is © The Royal Society of Chemistry 2017 |
Click here to see how this site uses Cookies. View our privacy policy here.